机加工零部件质量检验标准
机加工表面质量标准

安徽铜陵松宝智能装备股份有限公司机加工零件外观检验标准1.范围本标准规定了无任何表面处理一般机加工件(机加工部位)在检验过程中外观可接收的标准。
2. 定义粗糙度:表面光洁程度。
撞伤:工件上的浅坑(人为原因碰撞导致的、非毛坯本身所具有的)。
划痕:浅的沟槽(其他锐利物导致表面划伤的痕迹)。
污渍:工件上的可见的油渍(加工、周转导致的油渍与污渍)。
毛刺:机加工后产生的尖锐突起、飞边等。
3. 外观等级分类3.1 产品分类:A. 一般结构件B. 轴类C. 其他类3.2 部件表面可见程度分类:Ⅰ.经常被注意到的(客户在使用时经常会看到的,正面的)。
Ⅱ.偶尔被注意到的(客户在使用时不经常看到的,侧面和底面的)。
Ⅲ.难以被注意的(只用在安装或维修时才能看到的,内部的)。
4. 职责品质检验负责对送检的零件按本标准进行检验,并判定合格或不合格。
5. 验收标准5.1 机加工件材料应符合图纸要求。
代用材料一律由设计技术员签字认可。
5.2 通用要求5.2.1 工件表面应没有污渍。
5.2.2 工件不得有锐边(以一般手指触摸没有扎手感),不得有毛刺。
5.2.3 表面粗糙度应符合图纸要求。
5.2.4 螺纹孔内不得有切削液,攻丝油等残留(防锈油除外)。
5.2.5 成品工件表面不允许有锈斑,锈迹。
5.3 表面撞伤,划伤判定标准注:表内缺陷数是在 60mmX100mm 范围内。
如物料还需要再进行表面处理,焊接等二次加工的,按不影响使用和二次加工判定。
如遇特殊异常(严重撞伤,明显有损观瞻的)由技术及品管协商处理。
6 包装和保护6.1 供方应采用合适的流转器具装运工件,避免跌落与磕碰。
6.2 如工件的表面要求比较高,应制作专用的流转器具或进行必要的包装。
拟制:审核:批准:。
机械类质量标准“三检、三按”ppt

三、主要内容
1.零部件首件检查
• • • •
• 1.1下列情况必须进行首件检查 1.1.1操作者每个生产班次加工的第一个零件。 对工艺能保证质量的,已连续生产一个班以上的 可以不必每 班做首件检查(特殊情况单位可自行规定)。 1.1.2加工过程中换工、换料、换活加工的第一个零件。 1.1.3改变工艺参数和加工方法(如更换机床,改变零件 的装卡,改变加工部位等)加工出的第一个零件。 1.1.4在调整修理后的设备上加工出的第一个零件。
•
• •
•
•
•
• 2.4 a)工序检查员或操作者发现上道工序或毛料等非本单 位责任的不合格品,由车间通知责任单位认可后,工序检查员 按《不合格品控制程序》进行处置,意见不一致时,由质检科 判决生效。 • b)若粗加工中发现毛料及热处理缺陷,操作者及工序检查员 应及时反馈,待粗加工完毕后,所暴露的问题由责任单位一并 处理。 • c)生产过程中,对上道工序发生的问题,下道工序应该发现, 但未反映继续加工的: • 1)产品本来可以采取措施挽救,因继续加工造成的不合格品, 由加工单位(或下道工序)承担50%的责任; • 2)废品发生工序以后所产生的工时无效。 • 2.5跨车间的质量问题,责任单位必须在半天之内拿出解决 方案并实施,否则,在产单位检查员开具废品票,不再冲票。 • 2.6工序检查员要随时填写工序检查记录 。
1.2 首件检查项目:
• 1.2.1加工的零件与零件生产进程单上的产品图号、名称、 材料、规格是否一致;上下工序的衔接是否符合工艺文件;代 料票是否有技术人员的签字;临时工艺有技术人员的签字认可。 • 1.2.2 加工零件的尺寸、形位公差、表面粗糙度等与产品 图纸、工艺、标准等技术文件的要求是否一致,综合检查零件 是否合格。
机械制造行业质量检验要求

机械制造行业质量检验要求近年来,机械制造行业的发展迅猛,给全球经济发展做出了重要贡献。
然而,由于各类机械产品的质量问题时有发生,严重影响了企业形象和用户体验。
为了确保机械制造行业的质量可靠性,制定和执行一系列质量检验要求势在必行。
本文将从材料、加工工艺、装配、可靠性等多个方面讨论机械制造行业的质量检验要求。
一、材料质量检验要求1. 原材料选择:机械制造的关键材料必须符合相关国家标准,如钢材需要符合GB/T 700或GB/T 1591等相关标准。
对于特殊行业的机械产品,还需要符合特定行业标准,如核电行业需要符合核电材料标准。
2. 材料强度检验:机械零部件的强度是保障其正常工作的基础。
因此,对材料的强度进行测试和评估是必要的,以确保其满足设计要求和使用要求。
常用的材料强度检验方法有拉伸试验、冲击试验、硬度测试等。
3. 材料化学成分检验:机械零部件的材料化学成分对其材料性能和结构性能有重要影响。
因此,对材料进行化学成分检验是必要的。
常用的检验项目包括主要合金元素含量、非金属夹杂物含量、合金相组成等。
二、加工工艺质量检验要求1. 工艺技术规范:机械零部件加工过程中必须依据相应的工艺技术规范进行操作。
工艺技术规范包括加工设备的选择和设置、切削条件的确定、工艺路线的确定等。
对于特殊行业的机械产品,还需要根据特定行业标准进行操作。
2. 加工精度检验:加工精度是机械零部件质量的重要指标之一。
对于关键零部件的加工精度要求较高,需进行尺寸、形状等方面的检验。
常用的加工精度检验方法有三坐标测量、光学投影仪测量等。
3. 工艺过程控制:机械零部件加工过程中的各项参数应进行有效的控制和记录,以确保产品质量的稳定性和可追溯性。
工艺过程控制包括加工设备和工具的定期检验和维护、操作人员技术培训等。
三、装配质量检验要求1. 零部件配合检验:机械零部件的装配配合要求较高,需要进行配合间隙、间隙公差、配合形状等方面的检验。
配合检验可以采用手动装配、测量配合间隙等方法。
机械加工检验标准及规范

机械(金属切削)加工检验标准及规范机械(金属切削)加工检验标准1. 目的2. 范围3. 规范性引用文件4. 尺寸检验原则5. 检验对环境的要求6. 外观的检验7. 表面粗糙度的检验8. 线性尺寸和角度尺寸公差要求9. 形状和位置公差的检验10.螺纹的检验11.检验计划12.判定规则1.目的为了明确公司金属切削加工检验标准,使检验作业有所遵循,特制定本标准。
2. 范围本标准适用于切削加工(包括外协、制程、出货过程)各检验特性的检验。
在本标准中,切削加工指的是:车削加工、铣削加工、磨削加工、镗削加工、刨削加工、孔加工、拉削加工和钳工作业等。
本标准不适用于锻造、钣金、焊接后的检验,其检验标准另行制定。
本标准规定了尺寸检验的基本原则、对环境的要求、外观检验标准、线性尺寸公差要求、形位公差要求、表面粗糙度的检验、螺纹的检验、检验计划和判定准则。
注:本标准不拟对长度、角度、锥度的测量方法进行描述,可参看相关技术手册;形位公差的测量可参看GB/T1958-1980;3. 规范性引用文件下列文件中的条款通过本标准的引用而成为本标准的条款。
GB/T (ISO 2859-1:1989) 计数抽样检验程序第1部分:GB/T 1804- 2000 (ISO2768-1:104989) 一般公差未注公差的线性和角度尺寸的公差GB/T 1184 - 1996(ISO2768-2:1989) 形状和位置公差未注公差值GB/T 1958-1980 形状和位置公差检测规定GB/T 1957-1981 光滑极限量规4. 尺寸检验原则基本原则所用验收方法应只接收位于规定的尺寸验收极限的工件。
对于有配合要求的工件,其尺寸检验应符合泰勒原则,孔或轴的作用尺寸不允许超过最大实体尺寸。
阿贝原则被测量线应处于被测量线或被测量线的延长线上。
最小变形原则为了保证测量结果的准确可靠,应尽量使各种因素的影响而产生的变形为最小。
最短尺寸链原则为保证一定的测量精度,测量链的环节应减到最少,即测量链应最短。
机械加工零件检验标准
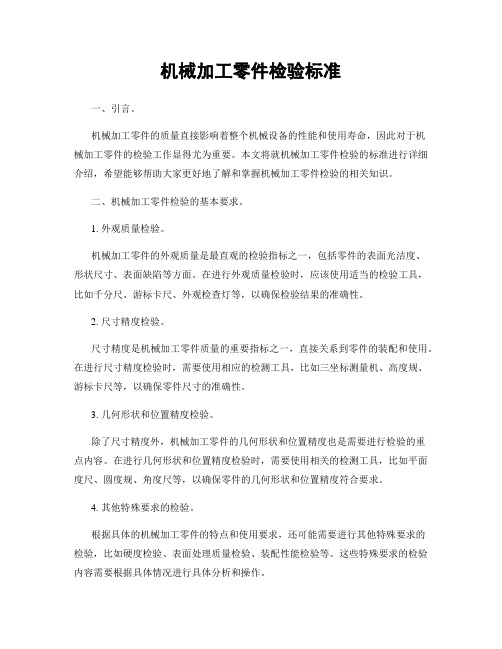
机械加工零件检验标准一、引言。
机械加工零件的质量直接影响着整个机械设备的性能和使用寿命,因此对于机械加工零件的检验工作显得尤为重要。
本文将就机械加工零件检验的标准进行详细介绍,希望能够帮助大家更好地了解和掌握机械加工零件检验的相关知识。
二、机械加工零件检验的基本要求。
1. 外观质量检验。
机械加工零件的外观质量是最直观的检验指标之一,包括零件的表面光洁度、形状尺寸、表面缺陷等方面。
在进行外观质量检验时,应该使用适当的检验工具,比如千分尺、游标卡尺、外观检查灯等,以确保检验结果的准确性。
2. 尺寸精度检验。
尺寸精度是机械加工零件质量的重要指标之一,直接关系到零件的装配和使用。
在进行尺寸精度检验时,需要使用相应的检测工具,比如三坐标测量机、高度规、游标卡尺等,以确保零件尺寸的准确性。
3. 几何形状和位置精度检验。
除了尺寸精度外,机械加工零件的几何形状和位置精度也是需要进行检验的重点内容。
在进行几何形状和位置精度检验时,需要使用相关的检测工具,比如平面度尺、圆度规、角度尺等,以确保零件的几何形状和位置精度符合要求。
4. 其他特殊要求的检验。
根据具体的机械加工零件的特点和使用要求,还可能需要进行其他特殊要求的检验,比如硬度检验、表面处理质量检验、装配性能检验等。
这些特殊要求的检验内容需要根据具体情况进行具体分析和操作。
三、机械加工零件检验的标准。
1. 国家标准。
国家对于机械加工零件的检验工作制定了相关的标准,比如GB/T 1184-1996《精密量规》、GB/T 1184-1996《精密量规》等,这些国家标准是机械加工零件检验工作的重要依据,需要严格遵守和执行。
2. 行业标准。
除了国家标准外,不同的行业还可能制定了针对机械加工零件的检验标准,比如汽车行业的相关标准、航空航天行业的相关标准等,这些行业标准是根据具体行业的特点和要求而制定的,需要根据实际情况进行具体执行。
3. 企业标准。
一些大型企业可能会根据自身的生产特点和质量要求,制定了针对机械加工零件的检验标准,这些企业标准是企业质量管理体系的重要组成部分,需要严格执行和遵守。
机械加工质量控制标准

机械加工质量控制标准在机械制造领域中,机械零部件的质量是至关重要的。
为了确保机械零部件的加工质量,我们需要遵守一定的标准和规范。
本文将介绍机械加工质量控制标准。
一、加工质量要求机械零部件的加工质量要求包括尺寸精度、形位公差、表面质量等方面的要求。
在进行加工之前,需要明确零部件的加工质量要求,并在加工过程中严格控制,以保证最终产品的质量。
1. 尺寸精度尺寸精度是衡量机械零部件加工质量的重要指标之一。
尺寸精度一般分为公差等级,根据零部件的实际要求选择适当的公差等级。
加工过程中需采用合适的加工工艺和设备,保证尺寸精度的达到要求。
2. 形位公差形位公差是衡量机械零部件几何形状和位置精度的指标。
对于要求较高的零部件,需要在制定工艺方案和选择设备时考虑形位公差的控制。
在加工过程中,应严格按照设计要求进行加工,保证形位公差的控制。
3. 表面质量零部件的表面质量对于产品的整体外观和性能有较大的影响。
在机械加工过程中,应注重工艺操作的细节,控制好加工参数和刀具状况,保证零部件的表面光洁度和无明显缺陷。
二、加工工艺要求机械加工工艺是保证零部件加工质量的重要环节。
在加工过程中,应根据零部件的具体要求和材料特性,合理选择加工工艺和设备,并制定相应的操作规程。
1. 工艺路线在制定加工工艺时,需要明确每道工序的加工内容和顺序。
合理的工艺路线可以最大程度地减少加工扭曲和变形,提高零部件的加工精度。
2. 加工方法不同的零部件可能采用不同的加工方法,如车削、铣削、钻削、磨削等。
选择合适的加工方法需要考虑加工效率和加工质量的平衡,确保加工过程中的稳定性和准确性。
3. 刀具选择刀具是机械加工中不可或缺的工具,合适的刀具选择能够有效地提高加工质量。
在选择刀具时,需要考虑加工材料的硬度、表面光洁度等因素,并结合具体的加工操作进行选用。
三、设备要求机械加工设备对于加工质量的控制至关重要。
高精度、稳定性好的设备能够提供良好的加工基础,保证零部件加工质量的稳定性和可靠性。
零部件质量标准及检验规范

零部件质量标准及检验规范页数:共2页第一页加工设备:压刨机、推台锯、覆膜机、切角机、数控雕刻机、立铣机、操作人员要求:需经培训合格熟练掌握设备,性能,安全防护措施及注意事项。
项目质量要求一·作业前检验要求1.板材中间严重分层开裂,凹凸不平,粘压移位等板件不可投入本工序生产。
2.贴皮板面起皱,严重刮伤,开皮,木纹方向不正确板件不可投入本工序生产。
3.刀具不够锋利、损坏缺茬等不能投入本工序生产。
二·立铣、铣型质量标准1.压线铣型MDF材质·立铣:1.各种压线、形状符合工艺图纸和有关技术参数的规定。
2.所有加工面要求平整、顺畅、光滑、转角自然、弧度一致、线条流畅、手摸无起伏坑凹、波浪、刀痕、台阶、缺茬。
3.要求加工无焦黑,无严重起毛、崩裂、加工面无损坏板面现象4.产品必须写有正确单号,字迹工整清晰。
实木材质·铣型:1.活节Φ<1CM允许、死节不允许。
2.肯头、缺茬、焦黑、起毛、崩裂、刀痕、台阶、不允许。
3.尺寸错误不允许。
4.产品必须写有正确单号,字迹工整清晰。
2.各种包类1.铣型:各种包、形状符合工艺图纸和有关技术参数的规定。
2.波浪、缺茬、变形、肯头、凹坑、不允许3.加工面允许少量小于0.2的跳刀痕,(打磨掉,不影响造型美观及尺寸允许)4.包尺寸宽大于200mm 长大于1000mm时:允许公差:±1mm 厚度:±0.5mm5.产品必须写有正确单号,字迹工整清晰。
3.玻璃芯类1.加工面允许少量小于0.2的跳刀狠、波浪纹,(容易打磨掉,不影响造型美观及尺寸允许)2.雕刻:形状符合工艺图纸和有关技术参数的规定。
3.崩边、缺茬、缺皮不允许,尺寸雕刻错误不允许。
4.产品必须写有正确单号,字迹工整清晰。
三·帽头类、制作质量标准1.各种造型、尺寸符合工艺图纸要求。
2.造型做错、尺寸做错不允许3.帽板开料尺寸公差:长:±1mm 宽:±1mm 允许。
机加工检验规范
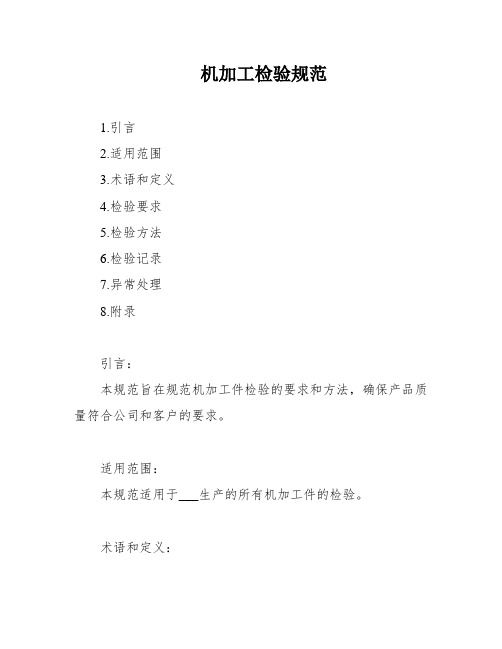
机加工检验规范1.引言2.适用范围3.术语和定义4.检验要求5.检验方法6.检验记录7.异常处理8.附录引言:本规范旨在规范机加工件检验的要求和方法,确保产品质量符合公司和客户的要求。
适用范围:本规范适用于___生产的所有机加工件的检验。
术语和定义:1.机加工件:指在机械设备上通过切削、铣削、钻孔等方式加工成形的零部件。
2.检验:指对机加工件进行各项检测以确保其质量符合要求的活动。
3.合格品:指经过检验符合要求的机加工件。
4.不合格品:指经过检验不符合要求的机加工件。
检验要求:1.外观检验:应检查机加工件的表面是否有明显划痕、裂纹、氧化等缺陷。
2.尺寸检验:应检查机加工件的尺寸是否符合要求。
3.材质检验:应检查机加工件的材质是否符合要求。
4.功能检验:应检查机加工件的功能是否符合要求。
检验方法:1.外观检验:应使用肉眼和放大镜进行检查。
2.尺寸检验:应使用测量工具进行检查,如卡尺、游标卡尺等。
3.材质检验:应使用化学分析仪进行检查。
4.功能检验:应使用相应的设备进行检查,如试验台、模拟器等。
检验记录:1.检验记录应详细记录检验日期、检验人员、检验结果等信息。
2.检验记录应保存至少两年。
异常处理:1.对于不合格品,应及时进行处理,如返工、报废等。
2.对于多次不合格品,应进行原因分析,并采取相应的措施进行改进。
附录:1.机加工件检验报告模板。
2.机加工件检验记录表。
1.目的本文旨在介绍___。
Ltd的产品检验标准,以确保产品质量符合标准要求。
2.范围本检验标准适用于___。
Ltd所有产品的检验,包括但不限于铁路设备、机械零部件等。
3.规范性引用文件本检验标准引用以下文件:GB/T 1804-2000 一般尺寸公差GB/T 1184-1996 钢铁表面缺陷分类和规定GB/T 1167-1983 螺纹检验方法GB/T 3478-1995 机械零部件表面粗糙度的测量和评定GB/T 1800-1996 基本公差制度4.检验条件所有产品在出厂前必须经过以下检验条件:外观检查表面粗糙度检查线性尺寸和角度尺寸公差检查形状和位置公差检查螺纹检查沉孔检查5.包装防护所有产品在出厂前必须进行适当的包装和防护,以确保产品完好无损。
机加工件检验标准
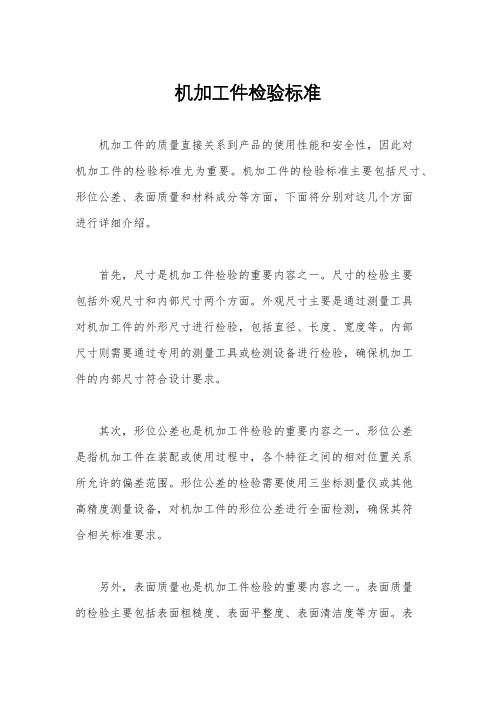
机加工件检验标准机加工件的质量直接关系到产品的使用性能和安全性,因此对机加工件的检验标准尤为重要。
机加工件的检验标准主要包括尺寸、形位公差、表面质量和材料成分等方面,下面将分别对这几个方面进行详细介绍。
首先,尺寸是机加工件检验的重要内容之一。
尺寸的检验主要包括外观尺寸和内部尺寸两个方面。
外观尺寸主要是通过测量工具对机加工件的外形尺寸进行检验,包括直径、长度、宽度等。
内部尺寸则需要通过专用的测量工具或检测设备进行检验,确保机加工件的内部尺寸符合设计要求。
其次,形位公差也是机加工件检验的重要内容之一。
形位公差是指机加工件在装配或使用过程中,各个特征之间的相对位置关系所允许的偏差范围。
形位公差的检验需要使用三坐标测量仪或其他高精度测量设备,对机加工件的形位公差进行全面检测,确保其符合相关标准要求。
另外,表面质量也是机加工件检验的重要内容之一。
表面质量的检验主要包括表面粗糙度、表面平整度、表面清洁度等方面。
表面质量的检验需要使用表面粗糙度仪、平整度测量仪等专用设备,对机加工件的表面质量进行全面检测,确保其符合产品要求。
最后,材料成分也是机加工件检验的重要内容之一。
材料成分的检验需要使用化学分析仪器对机加工件的材料成分进行检测,确保其符合设计要求,以保证产品的使用性能和安全性。
总之,机加工件的检验标准涉及到尺寸、形位公差、表面质量和材料成分等多个方面,需要使用不同的测量工具和检测设备进行全面检验。
只有严格按照相关标准要求进行检验,才能确保机加工件的质量符合产品要求,提高产品的使用性能和安全性。
机加件通用检验标准
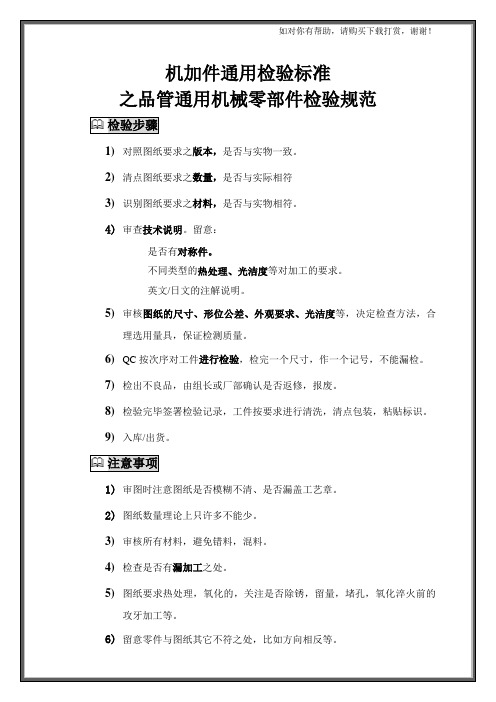
2) 术语和定义 A 级表面:在使用过程中总能被客户看见的部分(如:面壳的正面和顶面,后壳
的顶面,手柄,透镜,按键及键盘正面,探头整个表面等) 。
B 级表面:在使用过程中常常被客户看见的部分(如:面壳的左右侧面,底壳
或后壳的左右侧面及背面等) 。这些表面允许有轻微不良,但是不致引起挑剔客 户不购买产品。
可热处理不锈钢:SUS440C 铁 弗 龙 : PT
黑 赛 钢 : 黑 POM
铁(冷轧板):SPCC 45#钢:SS400、SGD400-D
铬钢:SKD、NAK55、NAK80
外观检视 1) 外观检视条件
——视力:校正视力 1.0 以上 ——目视距离:检查物距眼睛 A 级面 40 ㎝,B、C 距眼睛一臂远。 ——目视角度:45 度~90 度(检查时产品应转动) ——目视时间:A级面 15 秒/面,B、C面 10 秒/面 ——灯光:大于 500LUX 的照明度
钝化膜现象,呈现为区别于周围彩色的白色。
雾状:镀铬、镀镍表面上的模糊、不清晰、不光亮的现象。 颗粒:因材料夹杂物或外来物(如焊渣)的影响而在表面形成的,颜色与正常
表面一致的凸起现象。
挂具印:指电镀、氧化、喷涂等表面处理生产过程中,因装挂用辅助工具的遮
挡而使其与零件相接触的部位产生局部无膜层的现象。
2) 未注公差角度的极限偏差
长度 0~10 10~50
如对你有帮助,请购买下载打赏,谢谢!
公差
±1°
±30′
±20′
±10′
±5′
3) 直线度和平面度的未注公差儿
长度 公差 ≦10 0.02 ﹥10~30 0.05 ﹥30~100 0.1
单位:mm GB 1184-96 ﹥ 100 ~ ﹥ 300 ~ ﹥ 1000 ~ 300 1000 3000 0.2 0.3 0.4 单位:mm GB/T 1184-96
机械零部件检验规范

机械零部件检验规范机械零部件是机械设备的组成部分,它们直接关系到机械设备的整体性能和使用寿命。
因此,对机械零部件进行检验是非常必要的。
机械零部件的检验需要遵循一定的规范,下面将介绍机械零部件检验的规范。
一、机械零部件的检查方法机械零部件的检查方法主要包括外观质量检查、尺寸检查、物理性能检查和化学成分检查。
1. 外观质量检查外观质量检查是对机械零部件表面的缺陷、划痕、气泡、裂纹等进行检查,在机械零部件加工完成后应进行外观合格鉴定。
对于表面有缺陷的机械零部件,应予以拒收。
2. 尺寸检查尺寸检查是对机械零部件的尺寸、形位公差、形状和位置等进行检查。
尺寸检查应使用专业的测量仪器,在采用传统测量方法无法得到很高的精度时,应采用三坐标测量机、光学投影仪等高精度测量设备。
3. 物理性能检查物理性能检查主要对机械零部件的强度、硬度、韧性、耐磨性、耐热性、防腐性等进行检查。
这种检查主要通过对机械零部件进行试验来完成,如拉伸试验、冲击试验、压缩试验和硬度试验等。
4. 化学成分检查化学成分检查是对机械零部件的成分及成分中所含的有害元素进行检查。
机械零部件中所含的有害元素可能会影响机械零部件的性能和使用寿命,因此化学成分检查是必不可少的。
二、机械零部件的检验标准机械零部件的检验标准是机械零部件检验的依据。
机械零部件的检验标准应根据行业的标准、国家标准和地方标准等进行确定。
机械零部件的检验标准应包括以下内容:1. 外观质量要求外观质量应包括机械零部件表面的缺陷、划痕、气泡和裂纹等。
2. 尺寸公差要求尺寸公差应根据机械零部件的用途和要求确定,应符合行业的标准、国家标准和地方标准等规定。
3. 检验方法检验方法应包括机械零部件的外观质量检查、尺寸检查、物理性能检查和化学成分检查等。
4. 数据统计要求数据统计应包括机械零部件的尺寸公差、物理性能指标和化学成分指标的统计。
5. 合格标准合格标准应根据机械零部件的用途和要求确定,应符合行业的标准、国家标准和地方标准等规定。
机械加工件检测标准

机械加工件检测标准1、目的:通过严格执行三检,“首件检验”、“巡回检验”、“完工检验”将检验工件与工序控制紧密结合,对每一工序的质量问题或可能出现的质量问题不放过,不合格品不能转入下工序,从而提高产品质量。
2、适用范围:所有加工件3.检验原则3.1.检验人员必须具有一定的专业知识和实际工作经验,且能满足现行产品对检验工作的各项要求。
3.2.检验人员所用的计量器具必须是经计量部门校验合格并在规定周期内。
3.3.检验人员验收产品前应熟读相关图样和技术文件,了解零件的关键尺寸及装配关系要点。
3.4 检验人员必须严格按照图样和技术文件所规定的要求对零件进行判定。
4.检验依据检测依据按图纸及工艺卡检测5.检测种类:“工序自检”“首件检验”、“巡回检验”、“完工检验”5.1.工序自检:工件完成工序后进行自检,自检合格后在工艺卡进行签字;5.2.首件检验:批量工件必须首件检验后,才能开始加工5.2.1.对首件,根据加工工艺要求,核实首件产品或工件(毛坯)产品的质量特性是否符合要求。
对首批检查的工件,操作者必须做好自检,在操作者缺乏检测手段时,也应对工件外观质量自检,合格后送质量专员检查。
无论在任何情况下,首件检验未经检验合格,不得进行批量生产或继续加工作业。
5.2.2.工作班开始加工的第一个工件;5.2.3.调换操作者后加工的第一个工件;5.2.4. 更换(调整)工艺装备或更换模具后加工的第一个工件;5.2.5.更换材料批(炉)号后加工的第一个工件;5.2.6. 代用材料后加工的第一个工件;5.2.7.检验内容:根据检验标准的要求,核对首件产品的质量特性值是否真正符合要求;对首件检验合格,批准生产加工,首件检验不合格,进行不合格品的处理,同时分析不合格原因,采取改进措施后加工,产品继续首件检验,直至合格为止。
5.3.巡回检验:5.3.1.由检验人员在生产现场,进行日常巡回监督检查,重点监控工序质量和典型零件质量;5.3.2根据检验标准、图纸和工艺的要求、检验、核对巡检产品的质量特性值是否真正符合要求;5.3.3.若巡检某质量特性值不合格,应按《不合格品报告单》处理,同时。
机加工件检验标准

机加工件检验标准机加工件的质量直接关系到产品的使用效果和安全性,因此在生产过程中,对机加工件的质量检验至关重要。
机加工件的检验标准是指对机加工件进行检验时所遵循的一系列标准和规定,其目的是保证机加工件的质量符合要求,达到使用标准。
首先,机加工件的检验标准应包括外观质量、尺寸精度、表面粗糙度、装配性能等方面的要求。
在进行外观质量检验时,应注意检查机加工件是否存在表面缺陷、氧化、变形等情况,以及是否符合设计要求的外观要求。
对于尺寸精度的检验,应根据设计图纸和技术要求,使用相应的测量工具进行检测,确保尺寸精度符合要求。
同时,对于表面粗糙度和装配性能的检验也是非常重要的,这些方面的要求直接关系到机加工件的使用效果和性能。
其次,机加工件的检验标准还应包括检验方法和检验工艺的规定。
在进行机加工件的检验时,应根据不同的材料和工艺要求,选择合适的检验方法和检验工艺。
例如,对于金属材料的机加工件,可以采用金相显微镜、硬度计、三坐标测量仪等设备进行检验,而对于塑料材料的机加工件,则需要采用其他相应的检验方法。
同时,在进行检验时,还应注意检验过程中的环境和条件,确保检验结果的准确性和可靠性。
最后,机加工件的检验标准还应包括检验记录和报告的要求。
在进行机加工件的检验时,应及时记录检验结果和过程,并制作检验报告。
检验记录和报告应包括机加工件的基本信息、检验项目、检验结果、检验人员签名等内容,以便于后续的跟踪和管理。
总之,机加工件的检验标准是保证机加工件质量的重要保障,只有严格按照检验标准进行检验,才能确保机加工件的质量符合要求,达到使用标准。
因此,在生产过程中,应高度重视机加工件的检验工作,严格执行检验标准,确保产品质量和安全性。
机加工件检验标准

机加工件检验标准机加工件是机械制造中常见的零部件,其质量直接影响着整个机械设备的性能和可靠性。
因此,对机加工件的检验标准显得尤为重要。
本文将从机加工件检验的目的、方法和标准三个方面进行探讨。
首先,机加工件检验的目的是为了保证产品质量、满足设计要求、保障使用安全。
在机加工件的生产过程中,通过检验可以及时发现生产过程中的问题,保证产品的质量稳定性;同时,检验也可以确保产品满足设计要求,保障产品的使用性能;最重要的是,检验可以排除产品中的缺陷,保障产品的使用安全,避免因质量问题导致的事故发生。
其次,机加工件的检验方法主要包括外观检查、尺寸测量、材料成分分析、力学性能测试等。
其中,外观检查是最直观的检验方法,通过目视或辅助工具观察产品表面的缺陷、变形、氧化等情况;尺寸测量则是通过测量工具对产品的尺寸进行精确测量,确保尺寸符合设计要求;材料成分分析和力学性能测试则是通过化学分析和实验测试的方式来检验产品的材料成分和力学性能是否符合要求。
最后,机加工件的检验标准主要包括国家标准、行业标准和企业标准。
国家标准是由国家相关部门制定的,具有强制性;行业标准是由行业协会或组织制定的,具有一定的约束力;企业标准则是由企业根据自身生产情况和技术水平制定的,具有一定的灵活性。
在实际生产中,应当严格按照相关标准进行检验,确保产品的质量符合要求。
综上所述,机加工件的检验标准对于保证产品质量、满足设计要求、保障使用安全具有重要意义。
通过科学合理的检验方法和严格执行的检验标准,可以有效地提高产品质量,保障产品的可靠性和安全性,促进机械制造产业的健康发展。
希望各生产企业和相关部门能够重视机加工件的检验工作,确保产品质量,为行业发展做出贡献。
cnc机加工产品检验标准

cnc机加工产品检验标准
制造行业使用cnc机加工制造各种产品,cnc机加工产品检验是重要环节,检验标准必须严格执行,确保产品做到质量上乘。
在cnc机加工过程中,产品被用来制造必须符合一定标准,以确保每个产品的功能和性能。
一般来说,从技术要求角度可以将cnc机加工产品检验标准分为三种:特性要求、表面质量、强度/疲劳强度。
一、特性要求
1、尺寸把握:产品的尺寸精度要求必须符合cnc机加工要求,并与图纸相符,尺寸有相应误差要求,采用尺寸量仪能检测其尺寸及形状。
2、形位公差:检查关节点或夹持件之间形位关系,如果关节点有磨损或移位等影响形位关系的异常情况,应按照图纸规定的公差要求进行检查,使关节点能够正常组装。
3、孔隙公差:主要检查表面上是否存在裂纹、焊接收缩、腐蚀、供料不良、机加工崩角等缺陷,以免影响到使用性能和结构。
二、表面质量
1、表面表现:主要检查产品表面是否存在污染、损坏,有时涂装层表面也可能有锈蚀。
2、表面粗糙度:除了检查表面外,还需要检查表面粗糙度,表面粗糙度越高,表面光洁度也会降低,所以表面粗糙度的检测也很重要。
三、强度/疲劳强度
1、运动状态性能:在cnc机加工过程中,表面涂装要确保运动状态性能,要保证产品可以正常工作,所以涂装对运动状态有较高要求。
2、强度:受力部位针对不同材料实施拉伸试验,检测其强度和强度特性,以确定产品的使用强度。
3、疲劳试验:强度检测之后,还需要进行疲劳试验,主要是模拟实际使用条件下的产品工作性能,以确定该产品的使用寿命。
以上就是cnc机加工产品检验的标准要求,严格按照标准进行检测和检验,以确保产品能够完成正常使用任务,保证使用安全可靠。
机加检验规范

机加检验规范1. 引言机加检验是对机械零部件进行质量检测和性能验证的重要环节。
为了保证机械零部件的质量和可靠性,制定机加检验规范是必要的。
本文档旨在规范机加检验的操作流程和方法,保证机械零部件的质量符合要求。
2. 检验范围机加检验的范围包括但不限于以下几个方面:•尺寸检验:对机械零部件的尺寸进行精确测量,确保满足设计要求。
•材料检验:对机械零部件的材料进行化学成分和力学性能的检测,确保符合规定标准。
•表面质量检验:对机械零部件表面的光洁度、粗糙度等指标进行检测,确保符合要求。
•功能性能检验:对机械零部件的功能进行验证,确保其能够正常工作。
•耐久性检验:对机械零部件的耐久性进行测试,确保其在长时间使用中不会出现问题。
3. 检验设备进行机加检验需要使用一些常见的检验设备,如:•测量仪器:游标卡尺、千分尺、量规等,用于测量尺寸。
•化学分析仪器:扫描电子显微镜、能谱仪等,用于材料的化学成分分析。
•力学性能测试设备:拉力机、冲击试验机等,用于材料的力学性能测试。
•表面质量检测仪器:光学投影仪、粗糙度仪等,用于表面质量的检测。
•功能性能测试设备:液压测试台、载荷测试台等,用于功能性能的验证。
•耐久性测试设备:循环试验机、疲劳试验机等,用于耐久性的测试。
4. 检验流程机加检验的流程一般包括以下几个步骤:1.准备工作:收集机械零部件的相关信息,如图纸、规格要求等。
2.尺寸检验:使用相应的测量仪器对机械零部件的尺寸进行测量,并与设计要求进行比较。
3.材料检验:对机械零部件的材料进行化学成分和力学性能的检测,确保符合规定标准。
4.表面质量检验:使用相应的仪器对机械零部件的表面质量进行检测,如光洁度、粗糙度等。
5.功能性能检验:使用相应的测试设备对机械零部件的功能进行验证,确保其能够正常工作。
6.耐久性检验:使用相应的测试设备对机械零部件的耐久性进行测试,确保其在长时间使用中不会出现问题。
7.检验记录:将检验结果记录下来,并进行分析和汇总,确保检验的完整性和准确性。
机加工零部件质量检验标准
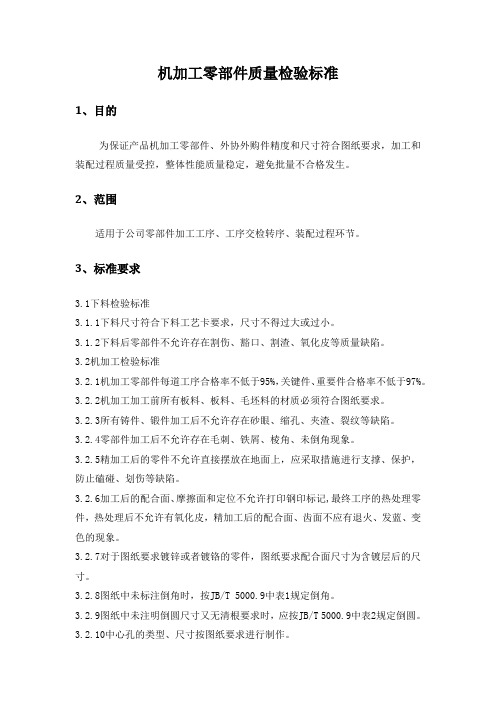
机加工零部件质量检验标准1、目的为保证产品机加工零部件、外协外购件精度和尺寸符合图纸要求,加工和装配过程质量受控,整体性能质量稳定,避免批量不合格发生。
2、范围适用于公司零部件加工工序、工序交检转序、装配过程环节。
3、标准要求3.1下料检验标准3.1.1下料尺寸符合下料工艺卡要求,尺寸不得过大或过小。
3.1.2下料后零部件不允许存在割伤、豁口、割渣、氧化皮等质量缺陷。
3.2机加工检验标准3.2.1机加工零部件每道工序合格率不低于95%,关键件、重要件合格率不低于97%。
3.2.2机加工加工前所有板料、板料、毛坯料的材质必须符合图纸要求。
3.2.3所有铸件、锻件加工后不允许存在砂眼、缩孔、夹渣、裂纹等缺陷。
3.2.4零部件加工后不允许存在毛刺、铁屑、棱角、未倒角现象。
3.2.5精加工后的零件不允许直接摆放在地面上,应采取措施进行支撑、保护,防止磕碰、划伤等缺陷。
3.2.6加工后的配合面、摩擦面和定位不允许打印钢印标记,最终工序的热处理零件,热处理后不允许有氧化皮,精加工后的配合面、齿面不应有退火、发蓝、变色的现象。
3.2.7对于图纸要求镀锌或者镀铬的零件,图纸要求配合面尺寸为含镀层后的尺寸。
3.2.8图纸中未标注倒角时,按JB/T 5000.9中表1规定倒角。
3.2.9图纸中未注明倒圆尺寸又无清根要求时,应按JB/T 5000.9中表2规定倒圆。
3.2.10中心孔的类型、尺寸按图纸要求进行制作。
3.2.11所有内径、外径、轴类加工表面粗糙度必须严格按照图纸制作。
4、职责和要求4.1技术部负责按照产品设计确认产品关键件、重要件并提供清单;负责产品在生产制作过程中图纸尺寸的修改和提供技术支持。
4.2工艺部负责确认关键工序和重要工序并制定工艺文件;负责产品制作过程中加工工艺的指导和工艺文件的制定并监督工作执行情况。
4.3 生产部负责按照最新版设计图纸和工艺文件进行派工,并将图纸和工艺卡一并交给操作者。
操作者在加工前必须熟悉图纸尺寸要求和工艺制作流程要求,熟练掌握本工序所用的工装、夹具和量具的使用,并复检上道工序(如:下料)零部件是否存在尺寸不合格或外观缺陷等质量问题。
航空工业西飞民机零部件的检验标准
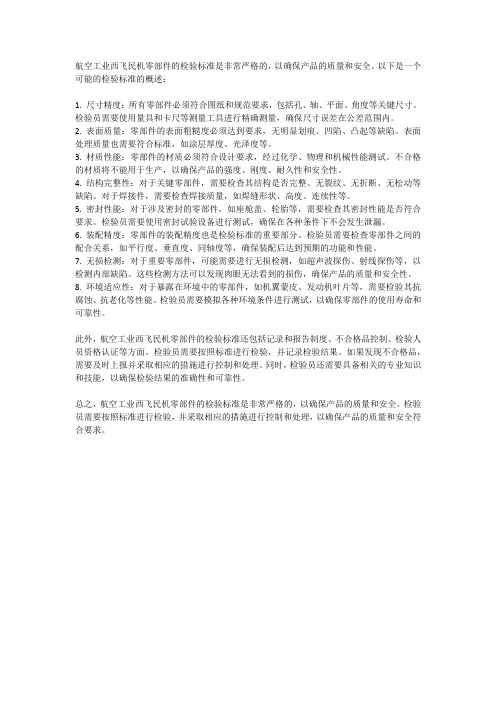
航空工业西飞民机零部件的检验标准是非常严格的,以确保产品的质量和安全。
以下是一个可能的检验标准的概述:1. 尺寸精度:所有零部件必须符合图纸和规范要求,包括孔、轴、平面、角度等关键尺寸。
检验员需要使用量具和卡尺等测量工具进行精确测量,确保尺寸误差在公差范围内。
2. 表面质量:零部件的表面粗糙度必须达到要求,无明显划痕、凹陷、凸起等缺陷。
表面处理质量也需要符合标准,如涂层厚度、光泽度等。
3. 材质性能:零部件的材质必须符合设计要求,经过化学、物理和机械性能测试。
不合格的材质将不能用于生产,以确保产品的强度、刚度、耐久性和安全性。
4. 结构完整性:对于关键零部件,需要检查其结构是否完整、无裂纹、无折断、无松动等缺陷。
对于焊接件,需要检查焊接质量,如焊缝形状、高度、连续性等。
5. 密封性能:对于涉及密封的零部件,如座舱盖、轮胎等,需要检查其密封性能是否符合要求。
检验员需要使用密封试验设备进行测试,确保在各种条件下不会发生泄漏。
6. 装配精度:零部件的装配精度也是检验标准的重要部分。
检验员需要检查零部件之间的配合关系,如平行度、垂直度、同轴度等,确保装配后达到预期的功能和性能。
7. 无损检测:对于重要零部件,可能需要进行无损检测,如超声波探伤、射线探伤等,以检测内部缺陷。
这些检测方法可以发现肉眼无法看到的损伤,确保产品的质量和安全性。
8. 环境适应性:对于暴露在环境中的零部件,如机翼蒙皮、发动机叶片等,需要检验其抗腐蚀、抗老化等性能。
检验员需要模拟各种环境条件进行测试,以确保零部件的使用寿命和可靠性。
此外,航空工业西飞民机零部件的检验标准还包括记录和报告制度、不合格品控制、检验人员资格认证等方面。
检验员需要按照标准进行检验,并记录检验结果。
如果发现不合格品,需要及时上报并采取相应的措施进行控制和处理。
同时,检验员还需要具备相关的专业知识和技能,以确保检验结果的准确性和可靠性。
总之,航空工业西飞民机零部件的检验标准是非常严格的,以确保产品的质量和安全。
机加工国标
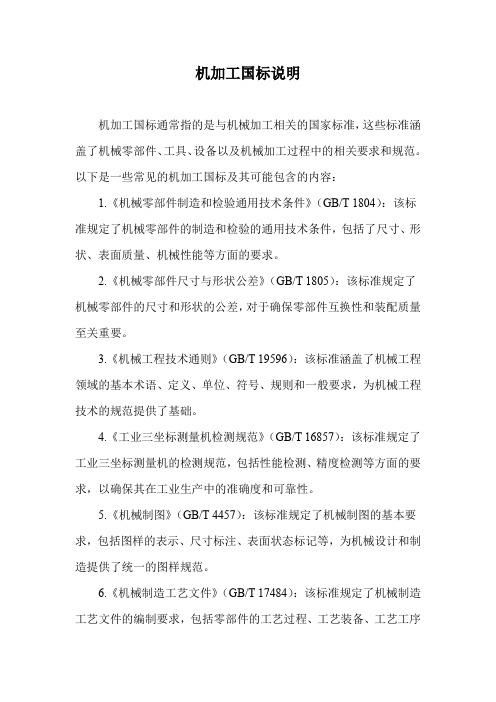
机加工国标说明机加工国标通常指的是与机械加工相关的国家标准,这些标准涵盖了机械零部件、工具、设备以及机械加工过程中的相关要求和规范。
以下是一些常见的机加工国标及其可能包含的内容:1.《机械零部件制造和检验通用技术条件》(GB/T 1804):该标准规定了机械零部件的制造和检验的通用技术条件,包括了尺寸、形状、表面质量、机械性能等方面的要求。
2.《机械零部件尺寸与形状公差》(GB/T 1805):该标准规定了机械零部件的尺寸和形状的公差,对于确保零部件互换性和装配质量至关重要。
3.《机械工程技术通则》(GB/T 19596):该标准涵盖了机械工程领域的基本术语、定义、单位、符号、规则和一般要求,为机械工程技术的规范提供了基础。
4.《工业三坐标测量机检测规范》(GB/T 16857):该标准规定了工业三坐标测量机的检测规范,包括性能检测、精度检测等方面的要求,以确保其在工业生产中的准确度和可靠性。
5.《机械制图》(GB/T 4457):该标准规定了机械制图的基本要求,包括图样的表示、尺寸标注、表面状态标记等,为机械设计和制造提供了统一的图样规范。
6.《机械制造工艺文件》(GB/T 17484):该标准规定了机械制造工艺文件的编制要求,包括零部件的工艺过程、工艺装备、工艺工序等,以确保生产过程的有序进行。
7.《数控机床编程与操作》(GB/T 11887):该标准规定了数控机床编程和操作的基本要求,包括数控机床的坐标系统、指令系统、编程格式等,为数控机床的使用提供了规范。
8.《工具和切削材料加工工艺文件》(GB/T 2423):该标准规定了工具和切削材料加工工艺文件的编制要求,包括工具刀具的选择、切削参数的确定等,以确保工具和切削材料的合理使用。
这些标准在机械加工领域起到了规范和引导作用,有助于提高机械零部件的质量、工艺的规范性和整体的生产效率。
在实际的机械制造和加工过程中,企业和从业人员应当遵循这些国标,确保产品和工艺的合规性和优越性。
- 1、下载文档前请自行甄别文档内容的完整性,平台不提供额外的编辑、内容补充、找答案等附加服务。
- 2、"仅部分预览"的文档,不可在线预览部分如存在完整性等问题,可反馈申请退款(可完整预览的文档不适用该条件!)。
- 3、如文档侵犯您的权益,请联系客服反馈,我们会尽快为您处理(人工客服工作时间:9:00-18:30)。
机加工零部件质量检验标准
1、目的
为保证产品机加工零部件、外协外购件精度和尺寸符合图纸要求,加工和装配过程质量受控,整体性能质量稳定,避免批量不合格发生。
2、范围
适用于公司零部件加工工序、工序交检转序、装配过程环节。
3、标准要求
3.1下料检验标准
3.1.1下料尺寸符合下料工艺卡要求,尺寸不得过大或过小。
3.1.2下料后零部件不允许存在割伤、豁口、割渣、氧化皮等质量缺陷。
3.2机加工检验标准
3.2.1机加工零部件每道工序合格率不低于95%,关键件、重要件合格率不低于97%。
3.2.2机加工加工前所有板料、板料、毛坯料的材质必须符合图纸要求。
3.2.3所有铸件、锻件加工后不允许存在砂眼、缩孔、夹渣、裂纹等缺陷。
3.2.4零部件加工后不允许存在毛刺、铁屑、棱角、未倒角现象。
3.2.5精加工后的零件不允许直接摆放在地面上,应采取措施进行支撑、保护,防止磕碰、划伤等缺陷。
3.2.6加工后的配合面、摩擦面和定位不允许打印钢印标记,最终工序的热处理零件,热处理后不允许有氧化皮,精加工后的配合面、齿面不应有退火、发蓝、变色的现象。
3.2.7对于图纸要求镀锌或者镀铬的零件,图纸要求配合面尺寸为含镀层后的尺寸。
3.2.8图纸中未标注倒角时,按JB/T 5000.9中表1规定倒角。
3.2.9图纸中未注明倒圆尺寸又无清根要求时,应按JB/T 5000.9中表2规定倒圆。
3.2.10中心孔的类型、尺寸按图纸要求进行制作。
3.2.11所有内径、外径、轴类加工表面粗糙度必须严格按照图纸制作。
4、职责和要求
4.1技术部
负责按照产品设计确认产品关键件、重要件并提供清单;负责产品在生产制作过程中图纸尺寸的修改和提供技术支持。
4.2工艺部
负责确认关键工序和重要工序并制定工艺文件;负责产品制作过程中加工工艺的指导和工艺文件的制定并监督工作执行情况。
4.3 生产部
负责按照最新版设计图纸和工艺文件进行派工,并将图纸和工艺卡一并交给操作者。
操作者在加工前必须熟悉图纸尺寸要求和工艺制作流程要求,熟练掌握本工序所用的工装、夹具和量具的使用,并复检上道工序(如:下料)零部件是否存在尺寸不合格或外观缺陷等质量问题。
操作者加工每批次工件时,加工出的第一件产品必须经自检合格后,再主动交给专检人员进行首件检验,经专检人员检验合格后才能继续批量生产。
加工过程中的每件产品操作者应全数进行自检或互检,不得有遗漏。
全部加工完毕后向专检人员进行完工报检,经专检人员全部检验完毕且全部合格后才能转下道工序进行加工。
半成品和成品转运过程中应做好防护,不允许有磕碰或混放。
防护应使用木材、胶皮等软质材料,禁止直接与铁架接触,两层之间也要进行隔开防护,且最上层应用胶皮或棉纱进行遮盖,以防止铁屑等对工件的影响。
操作者在加工过程中发现尺寸、外观等有异常波动时,应立即停止加工并报告专检人员,查找出原因并解决后才能继续生产。
操作者在接收上道工序转来的工件时应进行外观及标识的复验,对不符合转运要求及无上道工序的检验标识时应拒绝接收,对由于外部原因造成的检验标识不清时,应通过专职质检人员进行确认后,再进行处理,严禁接收未经上道工序检验的产品。
生产中如出现回用品且使用回用时需经技术、工艺及质量副总签字同意后放能进行使用,未经允许严禁使用回用品。
装配前应先观察零部件是否有毛刺、铁屑、磕碰、杂物等影响装配质量的缺陷,并将所有零部件清洗干净后在进行装配,装配时严禁使用铁锤敲打已加工表面。
4.4 质检部
专职检验人员在接到操作人员的首件报检后应及时按照图纸及工艺要求进行全尺寸的检验,检验全部合格后做首检标识,并在加工人员处单独存放。
检验不合格的应当面告知加工人员所有的不合格项,加工人员应重新制作并再次进行首件报检,首件报检合格后才能进行批量生产。
首件报检不合格的产品在返修后符合图纸和工艺要求的按合格品处理,在返修后仍达不到要求的按报废处理。
专职检验人员每天应不低于2次对加工人员进行巡检,每次随机抽出1~2件进行全尺寸检验,检验合格后继续生产。
如检验不合格,则生产马上停止,由生产人员配合专职检验人员对两次检验中间加工的工件进行全部检验,检验不合格的工件进行返修或报废处理。
加工人员应重新进行首件报检,合格后在进行批量生产。
生产加工人员每批次加工完毕后进行完工报检,专职检验人员根据新产品研发部下发的关键件、重要件清单对零部件进行全检,其他非关键件、非重要件可根据情况进行抽检,检验全部合格做好合格标识。
不合格的产品应要求工人进行返工或报废处理,所有返工或报废处理的工件应做好明显标识并分开存放,严禁混放。
专职检验人员对每批次各个工序的加工检验情况进行登记,每月月底对加工检验情况进行统计及分析。
专职检验人员在检验中或接到生产加工人员的报告,发现加工质量出现异常波动时,应立即通知加工人员停止生产,并联合工艺、设计和生产等各部门查找原因,并做出改善及预防措施。
专职检验人员检验范围包括:外径、内径、长度、深度、孔距、公法线、硬度、倒角、毛刺、磕碰等图纸要求的尺寸。
5考核
5.1因图纸设计失误造成材料费、工时费等费用,由新产品研发部100%承担。
5.2因工艺文件错误或工艺失误造成的材料费、工时费等费用,由工艺部100%承担。
5.3因派工失误造成的材料费、工时费等费用,由派工员100%承担。
5.4因派工不合理造成的材料费、工时费等费用,由派工员承担50%、操作者承担50%。
5.5因未熟悉图纸和工艺要求及工装量具使用不当造成的材料费、工时费等费用,由操作者100%承担。
5.6因未进行首件交检造成批量不合格的材料费、工时费等由操作者100%承担。
5.7因首件检验不合格造成成批量不合格的材料费、工时费等由操作者承担50%,专职检验人员承担50%。
首件检验合格,完工检验出现不合格的材料费、工时费等由操作者承担。
5.8因转运时未防护造成的不合格的材料费、工时费等由转运人员100%承担。
5.9产品在制作过程中出现异常波动,未进行妥善处理,继续加工的造成的材料费、工时费等损失由操作者承担。
5.10因上道未进行检验下道工序接收并制作,造成的不合格材料费、工时费等损失由接收人承担。
5.11因回用品未经技术、工艺和质量副总同意,进行使用造成的材料费、工时费等由操作者承担。