对接电阻焊
碰焊(电阻焊)
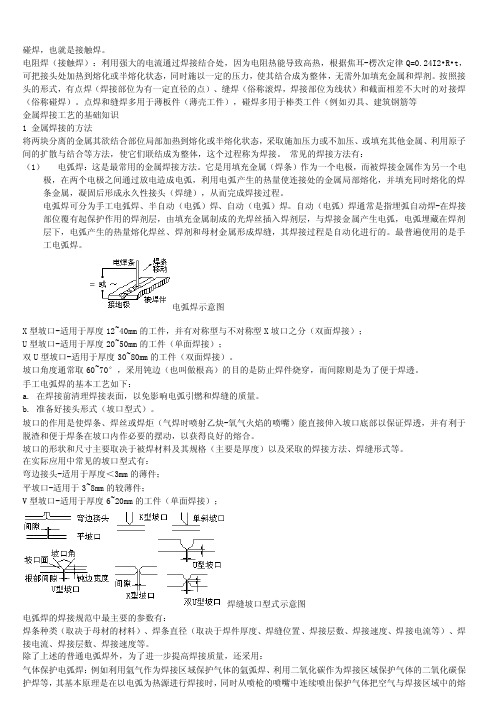
碰焊,也就是接触焊。
电阻焊(接触焊):利用强大的电流通过焊接结合处,因为电阻热能导致高热,根据焦耳-楞次定律Q=0.24I2•R•t,可把接头处加热到熔化或半熔化状态,同时施以一定的压力,使其结合成为整体,无需外加填充金属和焊剂。
按照接头的形式,有点焊(焊接部位为有一定直径的点)、缝焊(俗称滚焊,焊接部位为线状)和截面相差不大时的对接焊(俗称碰焊)。
点焊和缝焊多用于薄板件(薄壳工件),碰焊多用于棒类工件(例如刃具、建筑钢筋等金属焊接工艺的基础知识1 金属焊接的方法将两块分离的金属其欲结合部位局部加热到熔化或半熔化状态,采取施加压力或不加压、或填充其他金属、利用原子间的扩散与结合等方法,使它们联结成为整体,这个过程称为焊接。
常见的焊接方法有:(1) 电弧焊:这是最常用的金属焊接方法。
它是用填充金属(焊条)作为一个电极,而被焊接金属作为另一个电极,在两个电极之间通过放电造成电弧,利用电弧产生的热量使连接处的金属局部熔化,并填充同时熔化的焊条金属,凝固后形成永久性接头(焊缝),从而完成焊接过程。
电弧焊可分为手工电弧焊、半自动(电弧)焊、自动(电弧)焊。
自动(电弧)焊通常是指埋弧自动焊-在焊接部位覆有起保护作用的焊剂层,由填充金属制成的光焊丝插入焊剂层,与焊接金属产生电弧,电弧埋藏在焊剂层下,电弧产生的热量熔化焊丝、焊剂和母材金属形成焊缝,其焊接过程是自动化进行的。
最普遍使用的是手工电弧焊。
电弧焊示意图手工电弧焊的基本工艺如下:a. 在焊接前清理焊接表面,以免影响电弧引燃和焊缝的质量。
b. 准备好接头形式(坡口型式)。
坡口的作用是使焊条、焊丝或焊炬(气焊时喷射乙炔-氧气火焰的喷嘴)能直接伸入坡口底部以保证焊透,并有利于脱渣和便于焊条在坡口内作必要的摆动,以获得良好的熔合。
坡口的形状和尺寸主要取决于被焊材料及其规格(主要是厚度)以及采取的焊接方法、焊缝形式等。
在实际应用中常见的坡口型式有:弯边接头-适用于厚度<3mm 的薄件;平坡口-适用于3~8mm 的较薄件;V 型坡口-适用于厚度6~20mm 的工件(单面焊接);焊缝坡口型式示意图电弧焊的焊接规范中最主要的参数有:焊条种类(取决于母材的材料)、焊条直径(取决于焊件厚度、焊缝位置、焊接层数、焊接速度、焊接电流等)、焊接电流、焊接层数、焊接速度等。
电阻焊原理和焊接工艺完整版

电阻焊原理和焊接工艺完整版电阻焊是指利用电流通过两个接触电极,通过电流在焊接接头上产生的热量,将两个焊接材料加热至熔化状态,然后冷却固化,实现连接的一种焊接方法。
电阻焊可以分为电阻点焊、电阻缝焊和电阻插焊等。
电阻焊的原理是利用焊接接点的电阻加热而焊接材料加热到熔化温度。
焊接接头形成一个电阻,通过焊机施加的电流通过接头,形成焊接接点的电阻加热。
当焊接接头内部电流通过产生的热量超过材料的熔点时,焊接材料开始熔化。
然后通过施加的压力使熔化的焊接材料接触,形成一体化连接。
焊接完成后,断开电流,焊接接头冷却固化,形成强固的连接。
电阻焊的焊接工艺可以从焊材选择、接触电阻、焊接时间、施加压力等多个方面进行控制。
首先,选择合适的焊材能够确保焊接接头的质量。
焊接材料应具备良好的导电性和可焊性。
其次,接触电阻是决定焊接热量的重要因素之一、焊接电极与工件的接触电阻越小,焊接热量就越大。
因此,要采取措施确保接触电阻的稳定和减小接触电阻。
然后,焊接时间是控制焊接热量的另一重要参数。
焊接时间应根据焊接材料的熔点来确定。
焊接时间过短会导致焊接不充分,焊接强度不够;焊接时间过长则容易热损伤焊接接头。
最后,施加的压力也是控制焊接质量的关键。
合适的压力能够保证熔化的焊接材料进一步接触,使焊接接头的凝固过程更加完善。
针对不同焊接材料及材料厚度,电阻焊还可以采用不同的焊接工艺。
例如,电阻点焊广泛应用于金属板材的连接,可以快速、高效地实现金属板材的焊接。
电阻点焊的工艺流程一般包括调整焊机参数、清洁焊接接头、固定焊接接头、施加电流和压力、焊接完成后的冷却和检测等步骤。
电阻点焊的优点是焊接速度快、接头强度高。
此外,电阻焊还有电阻缝焊和电阻插焊等。
总之,电阻焊是利用通过焊接接头的电流加热焊接材料,实现焊接的一种方法。
通过控制焊接材料的选择、接触电阻、焊接时间和施加压力等参数,可以实现高质量的焊接连接。
电阻焊涉及到的焊接工艺可以根据具体的焊接需求进行选择和设计。
电阻点焊操作流程与注意事项

电阻点焊操作流程与注意事项1、电阻点焊机焊接方法——点焊点焊是将焊件装配成搭接接头,并压紧在两柱状电极之间,利用电阻热熔化母材金属,形成焊点的电阻焊方法。
点焊主要用于薄板焊接。
点焊的工艺过程:(1)预压,保证工件接触良好。
(2)通电,使焊接处形成熔核及塑性环。
(3)断电锻压,使熔核在压力继续作用下冷却结晶,形成组织致密、无缩孔、裂纹的焊点。
2、电阻点焊机焊接方法——缝焊(1)缝焊的过程与点焊相似,只是以旋转的圆盘状滚轮电极代替柱状电极,将焊件装配成搭接或对接接头,并置于两滚轮电极之间,滚轮加压焊件并转动,连续或断续送电,形成一条连续焊缝的电阻焊方法。
(2)缝焊主要用于焊接焊缝较为规则、要求密封的结构,板厚一般在3mm以下3、电阻点焊机焊接方法——对焊对焊是使焊件沿整个接触面焊合的电阻焊方法。
4、电阻点焊机焊接方法——凸焊凸焊(projection welding ),是在一工件的贴合面上预先加工出一个或多个突起点,使其与另一工件表面接触并通电加热,然后压塌,使这些接触点形成焊点的电阻焊方法。
凸焊是点焊的一种变形,主要用于焊接低碳钢和低合金钢的冲压件。
板件凸焊最适宜的厚度为0.5~4mm,小于0.25mm时宜采用点焊。
随着汽车工业发展,高生产率的凸焊在汽车零部件制造中获得大量应用。
凸焊在线材、管材等连接上也获得普遍应用。
)在使用点焊机作业过程中的注意事项:1、在作业时,应检查气路及水流量检测开关,确保气路、水冷系统畅通。
气体应保持干燥。
排水温度不得超过40℃,排水量可根据气温调节。
2、严禁在引燃电路中加大熔断器。
3、当控制箱长期停用时,每月应通电加热30min.更换闸流管时应邓热30min。
正常工作的控制箱的预热时间不得小于5min。
4、中频点焊机焊接操作及配合人员必须按规定穿戴劳动防护用品。
5、现场使用的中频点焊机,应设有防雨、防潮、防晒的机棚,并应装设相应的消防器材。
6、当清除焊件焊渣时,应戴防护眼镜,头部应避开敲击焊渣飞溅方向。
电阻对接焊焊接原理
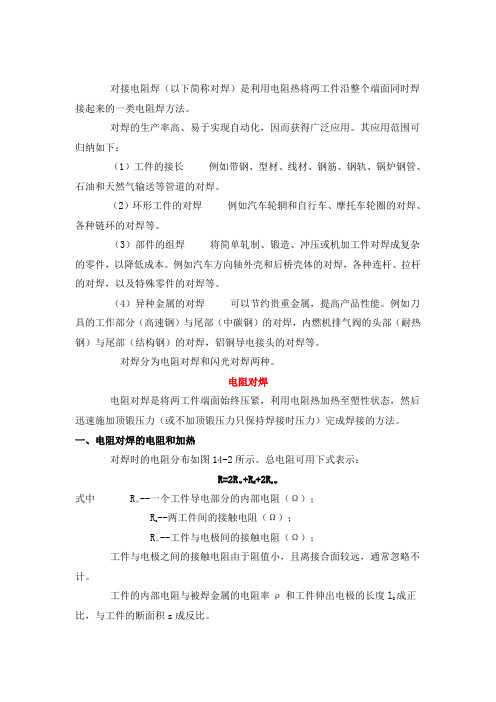
对接电阻焊(以下简称对焊)是利用电阻热将两工件沿整个端面同时焊接起来的一类电阻焊方法。
对焊的生产率高、易于实现自动化,因而获得广泛应用。
其应用范围可归纳如下:(1)工件的接长例如带钢、型材、线材、钢筋、钢轨、锅炉钢管、石油和天然气输送等管道的对焊。
(2)环形工件的对焊例如汽车轮辋和自行车、摩托车轮圈的对焊、各种链环的对焊等。
(3)部件的组焊将简单轧制、锻造、冲压或机加工件对焊成复杂的零件,以降低成本。
例如汽车方向轴外壳和后桥壳体的对焊,各种连杆、拉杆的对焊,以及特殊零件的对焊等。
(4)异种金属的对焊可以节约贵重金属,提高产品性能。
例如刀具的工作部分(高速钢)与尾部(中碳钢)的对焊,内燃机排气阀的头部(耐热钢)与尾部(结构钢)的对焊,铝铜导电接头的对焊等。
对焊分为电阻对焊和闪光对焊两种。
电阻对焊电阻对焊是将两工件端面始终压紧,利用电阻热加热至塑性状态,然后迅速施加顶锻压力(或不加顶锻压力只保持焊接时压力)完成焊接的方法。
一、电阻对焊的电阻和加热对焊时的电阻分布如图14-2所示。
总电阻可用下式表示:R=2Rω+RC+2Reω式中 Rω--一个工件导电部分的内部电阻(Ω);Rc--两工件间的接触电阻(Ω);Rω--工件与电极间的接触电阻(Ω);工件与电极之间的接触电阻由于阻值小,且离接合面较远,通常忽略不计。
工件的内部电阻与被焊金属的电阻率ρ和工件伸出电极的长度l成正比,与工件的断面积s成反比。
和点焊时一样,电阻对焊时的接触电阻取决于接触面的表面状态、温度及压力。
当接触电阻有明显的氧化物或其他赃物时,接触电阻就大。
温度或压力的增高,都会因实际接触面积的增大而使接触电阻减小。
焊接刚开始时,接触点上的电流密度很大;端面温度迅速升高后,接触电阻急剧减小。
加热到一定温度(钢600度,铝合金350度)时,接触电阻完全消失。
和点焊一样,对焊时的热源也是由焊接区电阻产生的电阻热。
电阻对焊时,接触电阻存在的时间极短,产生的热量小于总热量的10-15%。
电阻焊接工艺

电阻焊接工艺电阻焊接是一种常见的金属焊接方法,可以用于连接电路板上的元件和导线。
本文将介绍电阻焊接的基本工艺和注意事项。
电阻焊接步骤1. 准备焊接材料:电阻焊接需要使用焊锡丝、焊锡通量和焊接工具,确保这些工具和材料的质量和使用期限。
2. 检查焊接工具:确保焊接铁头干净,没有氧化或污垢。
如果有需要,清洁铁头以确保良好的接触。
3. 准备焊接区域:清洁焊接区域,防止灰尘和杂质对焊接的干扰。
4. 热熔焊锡:将焊锡丝插入焊接工具,启动热熔功能。
等待焊锡融化并变成液态。
5. 进行焊接连接:将需要连接的元件和导线放置在焊接区域,用热熔的焊锡丝将它们连接在一起。
确保焊接点充分接触和固定。
6. 冷却焊接点:焊接完成后,等待焊接点冷却和固化。
不要移动或扭动焊接点,以免造成损坏。
7. 检查焊接质量:用放大镜检查焊接点的质量,确保焊接点光滑、无裂纹和无断点。
注意事项- 安全操作:进行电阻焊接时,务必佩戴防护眼镜和手套,以防受伤。
- 控制温度:焊接热点的温度应适中,过高可能引起熔化或损坏,过低可能导致焊接不牢固。
- 避免过度焊接:焊接点应尽量避免过度焊接,以免造成电路短路或损坏元件。
- 注意电子元件的极性:在焊接元件时,需要注意元件的极性,确保正确连接。
- 均匀施力:焊接时,应均匀施力,使焊接点处于稳定状态。
结论电阻焊接是一种常见且有效的金属焊接方法。
通过掌握基本的电阻焊接工艺和注意事项,可以确保焊接质量和连接稳固性。
在操作过程中务必保持安全,控制温度,避免过度焊接,并正确连接电子元件。
电阻焊接技术
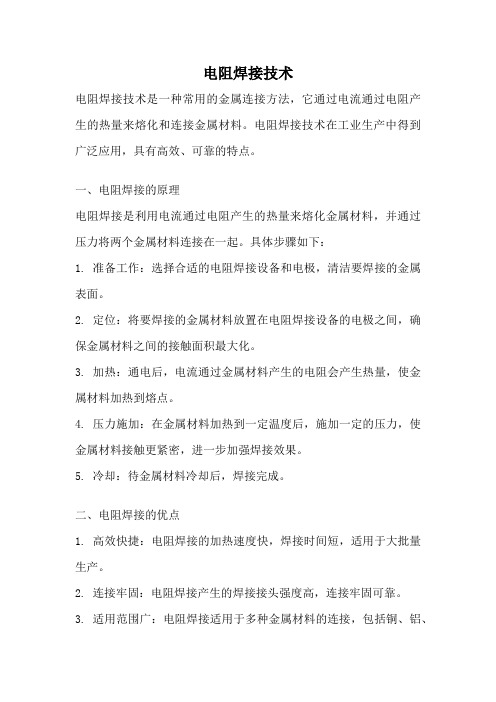
电阻焊接技术电阻焊接技术是一种常用的金属连接方法,它通过电流通过电阻产生的热量来熔化和连接金属材料。
电阻焊接技术在工业生产中得到广泛应用,具有高效、可靠的特点。
一、电阻焊接的原理电阻焊接是利用电流通过电阻产生的热量来熔化金属材料,并通过压力将两个金属材料连接在一起。
具体步骤如下:1. 准备工作:选择合适的电阻焊接设备和电极,清洁要焊接的金属表面。
2. 定位:将要焊接的金属材料放置在电阻焊接设备的电极之间,确保金属材料之间的接触面积最大化。
3. 加热:通电后,电流通过金属材料产生的电阻会产生热量,使金属材料加热到熔点。
4. 压力施加:在金属材料加热到一定温度后,施加一定的压力,使金属材料接触更紧密,进一步加强焊接效果。
5. 冷却:待金属材料冷却后,焊接完成。
二、电阻焊接的优点1. 高效快捷:电阻焊接的加热速度快,焊接时间短,适用于大批量生产。
2. 连接牢固:电阻焊接产生的焊接接头强度高,连接牢固可靠。
3. 适用范围广:电阻焊接适用于多种金属材料的连接,包括铜、铝、铁、不锈钢等。
4. 焊接质量好:由于电阻焊接过程中金属材料加热均匀,焊接接头质量好,焊缝无气孔、夹渣等缺陷。
三、电阻焊接的应用领域1. 汽车制造:电阻焊接广泛应用于汽车制造中,如车身焊接、发动机焊接等。
2. 电子设备:电阻焊接技术用于电子设备的电路板焊接,确保电子元件的连接可靠。
3. 家电制造:电阻焊接用于家电制造,如冰箱、洗衣机等产品的焊接。
4. 金属制品:电阻焊接可用于金属制品的生产,如钣金制品、管道等。
四、电阻焊接的注意事项1. 选择合适的电阻焊接设备和电极,确保设备的稳定性和可靠性。
2. 清洁要焊接的金属表面,确保焊接接头的质量。
3. 控制好焊接温度和焊接时间,避免金属材料过热或焊接不充分。
4. 注意安全,避免电流过大或操作不当导致事故发生。
电阻焊接技术是一种高效、可靠的金属连接方法,广泛应用于工业生产中。
通过电流产生的热量,使金属材料熔化并连接在一起,具有连接牢固、焊接质量好等优点。
对焊机的电阻焊方法.
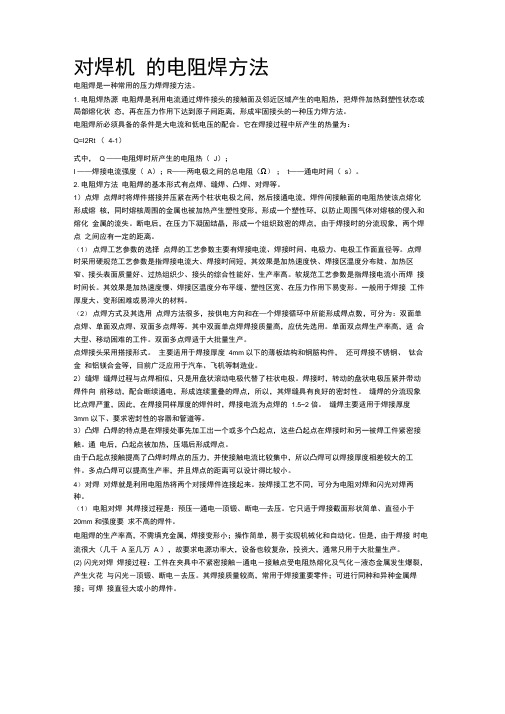
对焊机的电阻焊方法电阻焊是一种常用的压力焊焊接方法。
1. 电阻焊热源电阻焊是利用电流通过焊件接头的接触面及邻近区域产生的电阻热,把焊件加热到塑性状态或局部熔化状态,再在压力作用下达到原子间距离,形成牢固接头的一种压力焊方法。
电阻焊所必须具备的条件是大电流和低电压的配合。
它在焊接过程中所产生的热量为:Q=I2Rt (4-1)式中,Q ——电阻焊时所产生的电阻热(J);I ——焊接电流强度(A);R——两电极之间的总电阻(Ω);t——通电时间(s)。
2. 电阻焊方法电阻焊的基本形式有点焊、缝焊、凸焊、对焊等。
1)点焊点焊时将焊件搭接并压紧在两个柱状电极之间,然后接通电流,焊件间接触面的电阻热使该点熔化形成熔核,同时熔核周围的金属也被加热产生塑性变形,形成一个塑性环,以防止周围气体对熔核的侵入和熔化金属的流失。
断电后,在压力下凝固结晶,形成一个组织致密的焊点,由于焊接时的分流现象,两个焊点之间应有一定的距离。
(1)点焊工艺参数的选择点焊的工艺参数主要有焊接电流、焊接时间、电极力、电极工作面直径等。
点焊时采用硬规范工艺参数是指焊接电流大、焊接时间短,其效果是加热速度快、焊接区温度分布陡、加热区窄、接头表面质量好、过热组织少、接头的综合性能好、生产率高。
软规范工艺参数是指焊接电流小而焊接时间长。
其效果是加热速度慢、焊接区温度分布平缓、塑性区宽、在压力作用下易变形。
一般用于焊接工件厚度大、变形困难或易淬火的材料。
(2)点焊方式及其选用点焊方法很多,按供电方向和在—个焊接循环中所能形成焊点数,可分为:双面单点焊、单面双点焊、双面多点焊等。
其中双面单点焊焊接质量高,应优先选用。
单面双点焊生产率高,适合大型、移动困难的工件。
双面多点焊适于大批量生产。
点焊接头采用搭接形式。
主要适用于焊接厚度4mm 以下的薄板结构和钢筋构件,还可焊接不锈钢、钛合金和铝镁合金等,目前广泛应用于汽车、飞机等制造业。
2)缝焊缝焊过程与点焊相似,只是用盘状滚动电极代替了柱状电极。
电阻焊的焊接方法

电阻焊的焊接方法电阻焊是一种常见的焊接方法,它是利用电阻加热的原理,将两个金属表面加热至熔点,使它们融合在一起。
电阻焊具有焊接速度快、焊接质量高等优点,被广泛应用于各种金属制品的生产中。
本文将介绍电阻焊的工作原理、焊接方法以及注意事项。
一、电阻焊的工作原理电阻焊的工作原理是利用电流通过金属产生的阻力,使金属表面产生高温,从而将金属融化。
具体来说,电阻焊的工作原理如下:1. 电源:电阻焊需要一定的电源来产生电流。
通常使用的电源是变压器,它可以将高电压转换为低电压,从而使电流稳定。
2. 电极:电极是将电流传递到工件上的部件。
电极通常由铜制成,因为铜的导电性能好,能够将电流传递到工件上。
3. 工件:工件是被焊接的金属。
在电阻焊中,工件需要放在电极之间,以便电流能够通过工件产生热量。
4. 热量:当电流通过工件时,会产生热量,热量会使工件表面温度升高,从而将工件熔化。
5. 压力:在工件熔化的同时,需要施加一定的压力,以便使工件中的气泡被挤出,从而保证焊接质量。
二、电阻焊的焊接方法电阻焊的焊接方法主要有以下几种:1. 点焊:点焊是将两个金属表面焊接在一起的常用方法。
在点焊时,电极会在两个金属表面之间施加一定的压力,并通过电流将金属熔化,从而使两个金属表面融合在一起。
2. 缝焊:缝焊是将两个金属板焊接在一起的方法。
在缝焊时,需要将两个金属板的边缘对齐,然后通过电流将金属熔化,最后施加一定的压力,使两个金属板融合在一起。
3. 热压焊:热压焊是将金属和非金属焊接在一起的方法。
在热压焊时,需要将金属和非金属的表面对齐,并通过电流将金属熔化,最后施加一定的压力,使金属和非金属融合在一起。
三、电阻焊的注意事项在进行电阻焊时,需要注意以下几点:1. 电流大小:电流大小会影响焊接的温度和焊接的速度。
如果电流过大,会导致焊接过热,从而影响焊接质量。
如果电流过小,会导致焊接速度过慢,从而影响生产效率。
2. 电极形状:电极的形状会影响焊接的质量。
电阻焊的原理和方法

电阻焊的原理和方法
电阻焊的原理是利用电阻体的电阻产生热量,将工件接触在电阻体两端,通过热量传递使接触部位温度升高,从而实现焊接。
电阻焊的方法包括以下几种:
1. 接触电阻焊:将工件通过电极与电能源相连接,产生电流,电流通过工件和电极形成焊接接点,从而产生热量进行焊接。
2. 间接电阻焊:在两个非焊接接点之间设置导电电极,通过电流的流动产生热量进行焊接。
3. 电流脉冲焊:通过控制电流的脉冲,使工件快速加热和冷却,实现快速焊接,适用于对焊接时间要求高的场合。
4. 电弧电阻焊:电阻焊和电弧焊相结合的焊接方法,同时利用电流和电弧进行焊接,焊接质量更稳定可靠。
5. 电阻点焊:在工件上设定焊接接点,通过电流流过焊点产生热量进行焊接,常用于薄板材料连接。
以上是电阻焊的原理和几种常见的方法,根据实际需求和应用场景可以选择不同的方法进行焊接。
对焊工艺
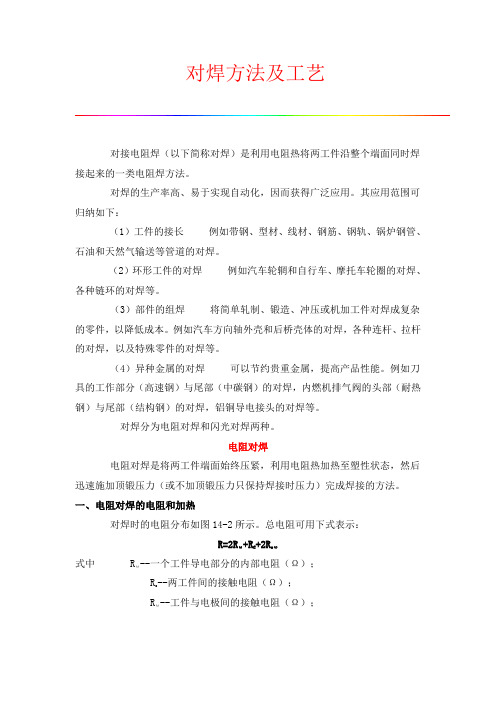
对焊方法及工艺对接电阻焊(以下简称对焊)是利用电阻热将两工件沿整个端面同时焊接起来的一类电阻焊方法。
对焊的生产率高、易于实现自动化,因而获得广泛应用。
其应用范围可归纳如下:(1)工件的接长例如带钢、型材、线材、钢筋、钢轨、锅炉钢管、石油和天然气输送等管道的对焊。
(2)环形工件的对焊例如汽车轮辋和自行车、摩托车轮圈的对焊、各种链环的对焊等。
(3)部件的组焊将简单轧制、锻造、冲压或机加工件对焊成复杂的零件,以降低成本。
例如汽车方向轴外壳和后桥壳体的对焊,各种连杆、拉杆的对焊,以及特殊零件的对焊等。
(4)异种金属的对焊可以节约贵重金属,提高产品性能。
例如刀具的工作部分(高速钢)与尾部(中碳钢)的对焊,内燃机排气阀的头部(耐热钢)与尾部(结构钢)的对焊,铝铜导电接头的对焊等。
对焊分为电阻对焊和闪光对焊两种。
电阻对焊电阻对焊是将两工件端面始终压紧,利用电阻热加热至塑性状态,然后迅速施加顶锻压力(或不加顶锻压力只保持焊接时压力)完成焊接的方法。
一、电阻对焊的电阻和加热对焊时的电阻分布如图14-2所示。
总电阻可用下式表示:R=2Rω+R C+2R eω式中 Rω--一个工件导电部分的内部电阻(Ω);--两工件间的接触电阻(Ω);RcRω--工件与电极间的接触电阻(Ω);工件与电极之间的接触电阻由于阻值小,且离接合面较远,通常忽略不计。
成正工件的内部电阻与被焊金属的电阻率ρ和工件伸出电极的长度l比,与工件的断面积s成反比。
和点焊时一样,电阻对焊时的接触电阻取决于接触面的表面状态、温度及压力。
当接触电阻有明显的氧化物或其他赃物时,接触电阻就大。
温度或压力的增高,都会因实际接触面积的增大而使接触电阻减小。
焊接刚开始时,接触点上的电流密度很大;端面温度迅速升高后,接触电阻急剧减小。
加热到一定温度(钢600度,铝合金350度)时,接触电阻完全消失。
和点焊一样,对焊时的热源也是由焊接区电阻产生的电阻热。
电阻对焊时,接触电阻存在的时间极短,产生的热量小于总热量的10-15%。
电阻焊接工艺
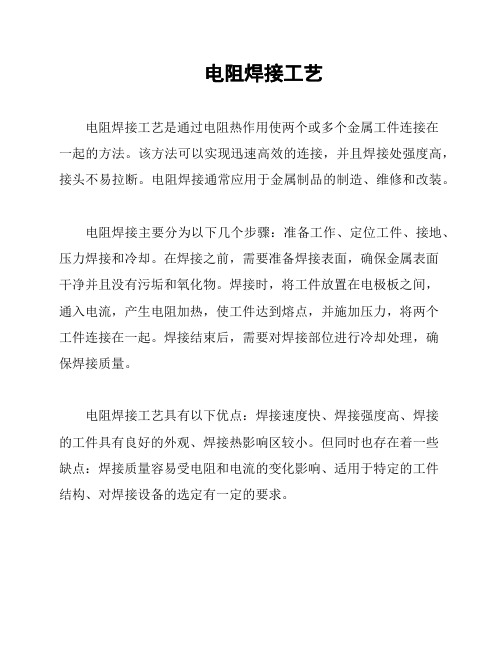
电阻焊接工艺
电阻焊接工艺是通过电阻热作用使两个或多个金属工件连接在
一起的方法。
该方法可以实现迅速高效的连接,并且焊接处强度高,接头不易拉断。
电阻焊接通常应用于金属制品的制造、维修和改装。
电阻焊接主要分为以下几个步骤:准备工作、定位工件、接地、压力焊接和冷却。
在焊接之前,需要准备焊接表面,确保金属表面
干净并且没有污垢和氧化物。
焊接时,将工件放置在电极板之间,
通入电流,产生电阻加热,使工件达到熔点,并施加压力,将两个
工件连接在一起。
焊接结束后,需要对焊接部位进行冷却处理,确
保焊接质量。
电阻焊接工艺具有以下优点:焊接速度快、焊接强度高、焊接
的工件具有良好的外观、焊接热影响区较小。
但同时也存在着一些
缺点:焊接质量容易受电阻和电流的变化影响、适用于特定的工件
结构、对焊接设备的选定有一定的要求。
总之,电阻焊接工艺在工程实践中应用非常广泛。
需要根据具体工件特点和要求来选择焊接工艺和设备,并尽可能降低工件在焊接过程中受到的热影响。
电阻对焊的焊接循环
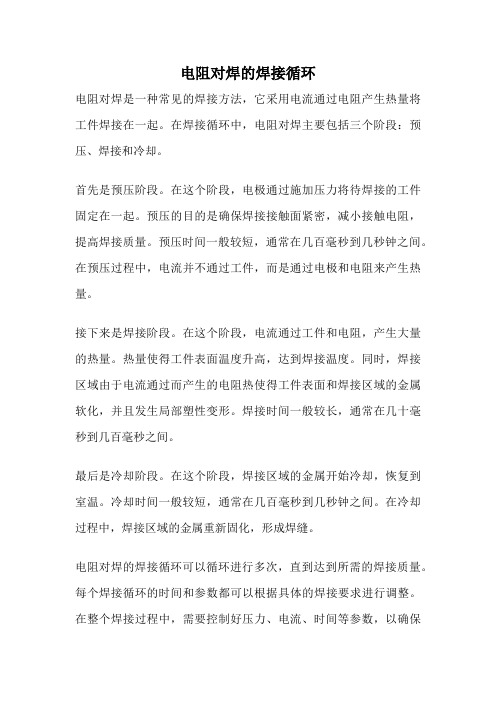
电阻对焊的焊接循环电阻对焊是一种常见的焊接方法,它采用电流通过电阻产生热量将工件焊接在一起。
在焊接循环中,电阻对焊主要包括三个阶段:预压、焊接和冷却。
首先是预压阶段。
在这个阶段,电极通过施加压力将待焊接的工件固定在一起。
预压的目的是确保焊接接触面紧密,减小接触电阻,提高焊接质量。
预压时间一般较短,通常在几百毫秒到几秒钟之间。
在预压过程中,电流并不通过工件,而是通过电极和电阻来产生热量。
接下来是焊接阶段。
在这个阶段,电流通过工件和电阻,产生大量的热量。
热量使得工件表面温度升高,达到焊接温度。
同时,焊接区域由于电流通过而产生的电阻热使得工件表面和焊接区域的金属软化,并且发生局部塑性变形。
焊接时间一般较长,通常在几十毫秒到几百毫秒之间。
最后是冷却阶段。
在这个阶段,焊接区域的金属开始冷却,恢复到室温。
冷却时间一般较短,通常在几百毫秒到几秒钟之间。
在冷却过程中,焊接区域的金属重新固化,形成焊缝。
电阻对焊的焊接循环可以循环进行多次,直到达到所需的焊接质量。
每个焊接循环的时间和参数都可以根据具体的焊接要求进行调整。
在整个焊接过程中,需要控制好压力、电流、时间等参数,以确保焊接质量和稳定性。
电阻对焊具有以下几个优点。
首先,焊接速度快,一般只需要几百毫秒到几秒钟的时间就可以完成一次焊接循环。
其次,焊接接头强度高,焊接质量好,能够满足高强度焊接的需求。
此外,电阻对焊适用于各种金属材料的焊接,如钢、铝、铜等。
最后,电阻对焊设备简单,易于操作和维护,成本较低。
然而,电阻对焊也存在一些局限性。
首先,焊接过程中会产生大量的热量,可能会对工件表面造成一定的热变形。
因此,在进行电阻对焊时,需要对工件进行适当的固定和冷却措施,以避免热变形对焊接质量的影响。
其次,焊接接头的形状和尺寸比较受限制,不适用于焊接复杂形状的工件。
最后,焊接接头的质量主要依赖于焊接参数的控制,对操作人员的要求较高。
总的来说,电阻对焊是一种常见且有效的焊接方法。
基于COMSOL模拟的T形接头对接电阻焊与双面焊的比较
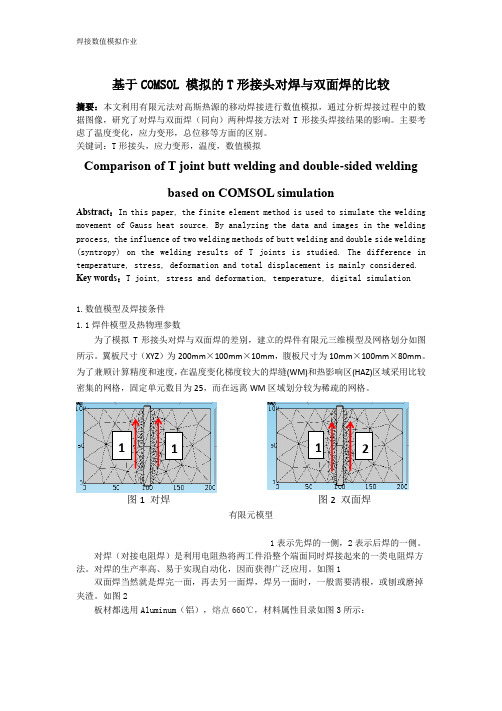
基于COMSOL 模拟的T 形接头对焊与双面焊的比较摘要:本文利用有限元法对高斯热源的移动焊接进行数值模拟,通过分析焊接过程中的数据图像,研究了对焊与双面焊(同向)两种焊接方法对T 形接头焊接结果的影响。
主要考虑了温度变化,应力变形,总位移等方面的区别。
关键词:T 形接头,应力变形,温度,数值模拟Comparison of T joint butt welding and double-sided weldingbased on COMSOL simulationAbstract :In this paper, the finite element method is used to simulate the welding movement of Gauss heat source. By analyzing the data and images in the welding process, the influence of two welding methods of butt welding and double side welding (syntropy) on the welding results of T joints is studied. The difference in temperature, stress, deformation and total displacement is mainly considered. Key words :T joint, stress and deformation, temperature, digital simulation1.数值模型及焊接条件 1.1焊件模型及热物理参数为了模拟T 形接头对焊与双面焊的差别,建立的焊件有限元三维模型及网格划分如图所示。
翼板尺寸(XYZ )为200mm ×100mm ×10mm ,腹板尺寸为10mm ×100mm ×80mm 。
电阻对焊的焊接循环
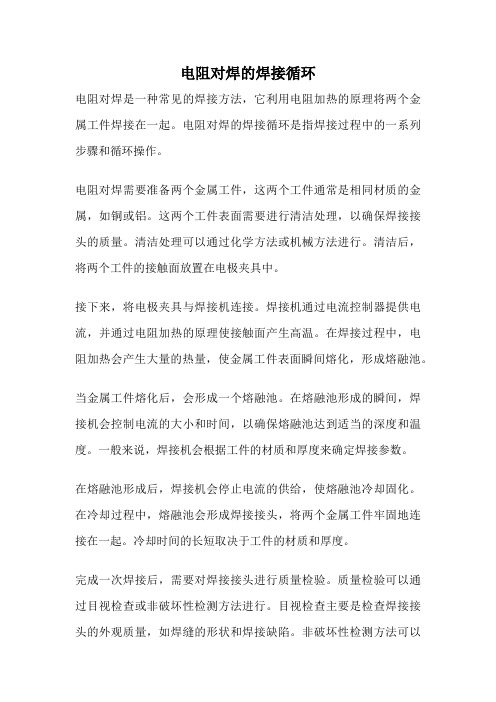
电阻对焊的焊接循环电阻对焊是一种常见的焊接方法,它利用电阻加热的原理将两个金属工件焊接在一起。
电阻对焊的焊接循环是指焊接过程中的一系列步骤和循环操作。
电阻对焊需要准备两个金属工件,这两个工件通常是相同材质的金属,如铜或铝。
这两个工件表面需要进行清洁处理,以确保焊接接头的质量。
清洁处理可以通过化学方法或机械方法进行。
清洁后,将两个工件的接触面放置在电极夹具中。
接下来,将电极夹具与焊接机连接。
焊接机通过电流控制器提供电流,并通过电阻加热的原理使接触面产生高温。
在焊接过程中,电阻加热会产生大量的热量,使金属工件表面瞬间熔化,形成熔融池。
当金属工件熔化后,会形成一个熔融池。
在熔融池形成的瞬间,焊接机会控制电流的大小和时间,以确保熔融池达到适当的深度和温度。
一般来说,焊接机会根据工件的材质和厚度来确定焊接参数。
在熔融池形成后,焊接机会停止电流的供给,使熔融池冷却固化。
在冷却过程中,熔融池会形成焊接接头,将两个金属工件牢固地连接在一起。
冷却时间的长短取决于工件的材质和厚度。
完成一次焊接后,需要对焊接接头进行质量检验。
质量检验可以通过目视检查或非破坏性检测方法进行。
目视检查主要是检查焊接接头的外观质量,如焊缝的形状和焊接缺陷。
非破坏性检测方法可以使用超声波、X射线或涡流检测等技术,对焊接接头进行内部缺陷检测。
如果焊接接头通过质量检验,说明焊接循环完成,焊接工艺顺利进行。
如果焊接接头未通过质量检验,需要重新进行焊接修复或调整焊接参数,再次进行焊接操作。
总的来说,电阻对焊的焊接循环包括准备工件、清洁处理、装夹工件、控制电流加热、熔融池形成、冷却固化、质量检验等步骤。
这个循环过程需要严格控制焊接参数,确保焊接质量。
电阻对焊作为一种常用的焊接方法,被广泛应用于金属加工和制造行业。
它具有焊接速度快、焊接接头牢固等优点,为各种金属制品的生产提供了可靠的焊接解决方案。
电阻焊简介
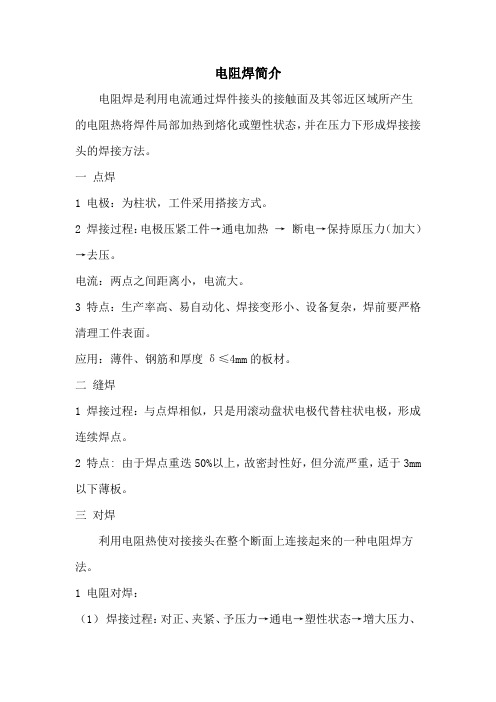
电阻焊简介
电阻焊是利用电流通过焊件接头的接触面及其邻近区域所产生
的电阻热将焊件局部加热到熔化或塑性状态,并在压力下形成焊接接头的焊接方法。
一点焊
1 电极:为柱状,工件采用搭接方式。
2 焊接过程:电极压紧工件→通电加热→ 断电→保持原压力(加大)→去压。
电流:两点之间距离小,电流大。
3 特点:生产率高、易自动化、焊接变形小、设备复杂,焊前要严格清理工件表面。
应用:薄件、钢筋和厚度δ≤4mm的板材。
二缝焊
1 焊接过程:与点焊相似,只是用滚动盘状电极代替柱状电极,形成连续焊点。
2 特点: 由于焊点重迭50%以上,故密封性好,但分流严重,适于3mm 以下薄板。
三对焊
利用电阻热使对接接头在整个断面上连接起来的一种电阻焊方法。
1 电阻对焊:
(1)焊接过程:对正、夹紧、予压力→通电→塑性状态→增大压力、。
电阻点焊焊点接头
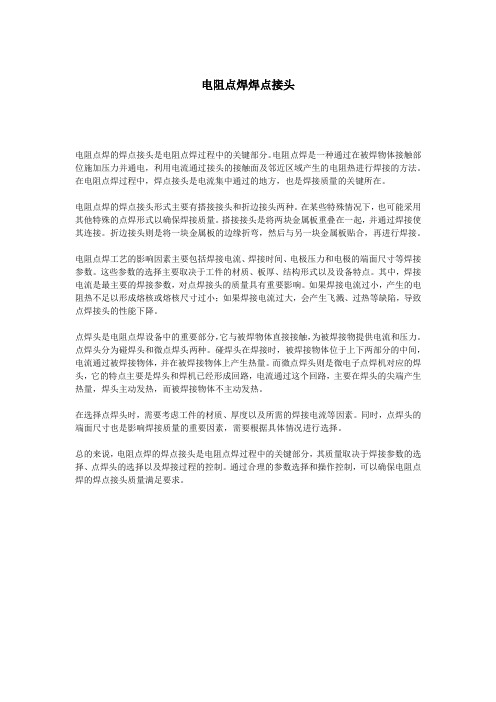
电阻点焊焊点接头电阻点焊的焊点接头是电阻点焊过程中的关键部分。
电阻点焊是一种通过在被焊物体接触部位施加压力并通电,利用电流通过接头的接触面及邻近区域产生的电阻热进行焊接的方法。
在电阻点焊过程中,焊点接头是电流集中通过的地方,也是焊接质量的关键所在。
电阻点焊的焊点接头形式主要有搭接接头和折边接头两种。
在某些特殊情况下,也可能采用其他特殊的点焊形式以确保焊接质量。
搭接接头是将两块金属板重叠在一起,并通过焊接使其连接。
折边接头则是将一块金属板的边缘折弯,然后与另一块金属板贴合,再进行焊接。
电阻点焊工艺的影响因素主要包括焊接电流、焊接时间、电极压力和电极的端面尺寸等焊接参数。
这些参数的选择主要取决于工件的材质、板厚、结构形式以及设备特点。
其中,焊接电流是最主要的焊接参数,对点焊接头的质量具有重要影响。
如果焊接电流过小,产生的电阻热不足以形成熔核或熔核尺寸过小;如果焊接电流过大,会产生飞溅、过热等缺陷,导致点焊接头的性能下降。
点焊头是电阻点焊设备中的重要部分,它与被焊物体直接接触,为被焊接物提供电流和压力。
点焊头分为碰焊头和微点焊头两种。
碰焊头在焊接时,被焊接物体位于上下两部分的中间,电流通过被焊接物体,并在被焊接物体上产生热量。
而微点焊头则是微电子点焊机对应的焊头,它的特点主要是焊头和焊机已经形成回路,电流通过这个回路,主要在焊头的尖端产生热量,焊头主动发热,而被焊接物体不主动发热。
在选择点焊头时,需要考虑工件的材质、厚度以及所需的焊接电流等因素。
同时,点焊头的端面尺寸也是影响焊接质量的重要因素,需要根据具体情况进行选择。
总的来说,电阻点焊的焊点接头是电阻点焊过程中的关键部分,其质量取决于焊接参数的选择、点焊头的选择以及焊接过程的控制。
通过合理的参数选择和操作控制,可以确保电阻点焊的焊点接头质量满足要求。
电阻对接焊焊接原理

对接电阻焊(以下简称对焊)是利用电阻热将两工件沿整个端面同时焊接起来的一类电阻焊方法。
对焊的生产率高、易于实现自动化,因而获得广泛应用。
其应用范围可归纳如下:(1)工件的接长例如带钢、型材、线材、钢筋、钢轨、锅炉钢管、石油和天然气输送等管道的对焊。
(2)环形工件的对焊例如汽车轮辋和自行车、摩托车轮圈的对焊、各种链环的对焊等。
(3)部件的组焊将简单轧制、锻造、冲压或机加工件对焊成复杂的零件,以降低成本。
例如汽车方向轴外壳和后桥壳体的对焊,各种连杆、拉杆的对焊,以及特殊零件的对焊等。
(4)异种金属的对焊可以节约贵重金属,提高产品性能。
例如刀具的工作部分(高速钢)与尾部(中碳钢)的对焊,内燃机排气阀的头部(耐热钢)与尾部(结构钢)的对焊,铝铜导电接头的对焊等。
对焊分为电阻对焊和闪光对焊两种。
电阻对焊电阻对焊是将两工件端面始终压紧,利用电阻热加热至塑性状态,然后迅速施加顶锻压力(或不加顶锻压力只保持焊接时压力)完成焊接的方法。
一、电阻对焊的电阻和加热对焊时的电阻分布如图14-2所示。
总电阻可用下式表示:R=2Rω+R C+2R eω式中 Rω--一个工件导电部分的内部电阻(Ω);--两工件间的接触电阻(Ω);RcRω--工件与电极间的接触电阻(Ω);工件与电极之间的接触电阻由于阻值小,且离接合面较远,通常忽略不计。
工件的内部电阻与被焊金属的电阻率ρ和工件伸出电极的长度l成正比,与工件的断面积s成反比。
和点焊时一样,电阻对焊时的接触电阻取决于接触面的表面状态、温度及压力。
当接触电阻有明显的氧化物或其他赃物时,接触电阻就大。
温度或压力的增高,都会因实际接触面积的增大而使接触电阻减小。
焊接刚开始时,接触点上的电流密度很大;端面温度迅速升高后,接触电阻急剧减小。
加热到一定温度(钢600度,铝合金350度)时,接触电阻完全消失。
和点焊一样,对焊时的热源也是由焊接区电阻产生的电阻热。
电阻对焊时,接触电阻存在的时间极短,产生的热量小于总热量的10-15%。
对接电阻焊工艺
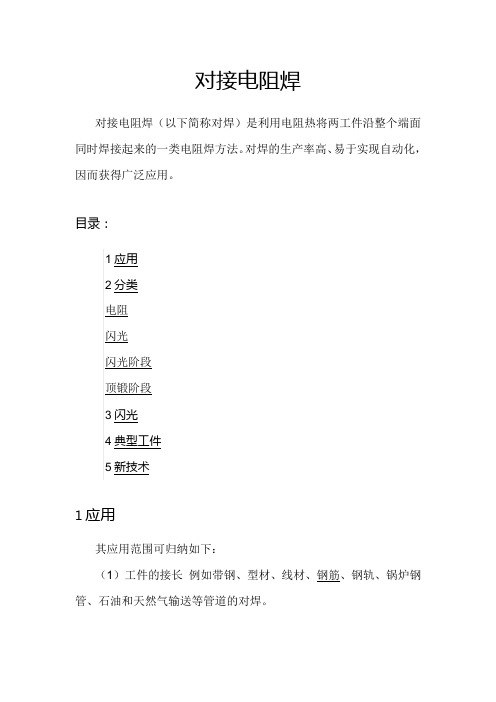
对接电阻焊对接电阻焊(以下简称对焊)是利用电阻热将两工件沿整个端面同时焊接起来的一类电阻焊方法。
对焊的生产率高、易于实现自动化,因而获得广泛应用。
目录:1应用其应用范围可归纳如下:(1)工件的接长例如带钢、型材、线材、钢筋、钢轨、锅炉钢管、石油和天然气输送等管道的对焊。
(2)环形工件的对焊例如汽车轮辋和自行车、摩托车轮圈的对焊、各种链环的对焊等。
(3)部件的组焊将简单轧制、锻造、冲压或机加工件对焊成复杂的零件,以降低成本。
例如汽车方向轴外壳和后桥壳体的对焊,各种连杆、拉杆的对焊,以及特殊零件的对焊等。
(4)异种金属的对焊可以节约贵重金属,提高产品性能。
例如刀具的工作部分(高速钢)与尾部(中碳钢)的对焊,内燃机排气阀的头部(耐热钢)与尾部(结构钢)的对焊,铝铜导电接头的对焊等。
2分类对焊分为电阻对焊和闪光对焊两种。
电阻电阻对焊是将两工件端面始终压紧,利用电阻热加热至塑性状态,然后迅速施加顶锻压力(或不加顶锻压力只保持焊接时压力)完成焊接的方法。
一、电阻对焊的电阻和加热对焊时的电阻分布如图14-2所示。
总电阻可用下式表示:R=2Rω+RC+2Reω式中Rω--一个工件导电部分的内部电阻(Ω);Rc--两工件间的接触电阻(Ω);Rω--工件与电极间的接触电阻(Ω);工件与电极之间的接触电阻由于阻值小,且离接合面较远,通常忽略不计。
工件的内部电阻与被焊金属的电阻率ρ和工件伸出电极的长度l0成正比,与工件的断面积s成反比。
和点焊时一样,电阻对焊时的接触电阻取决于接触面的表面状态、温度及压力。
当接触电阻有明显的氧化物或其他赃物时,接触电阻就大。
温度或压力的增高,都会因实际接触面积的增大而使接触电阻减小。
焊接刚开始时,接触点上的电流密度很大;端面温度迅速升高后,接触电阻急剧减小。
加热到一定温度(钢600度,铝合金350度)时,接触电阻完全消失。
和点焊一样,对焊时的热源也是由焊接区电阻产生的电阻热。
电阻对焊时,接触电阻存在的时间极短,产生的热量小于总热量的10-15%。
电阻焊--对焊
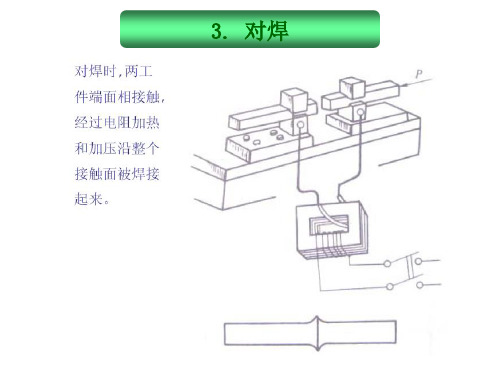
k——考虑钢材性质的系数,对于碳钢、低合金钢,k=1;对于奥氏体 钢,k=1.1; S——焊件的截面积(cm2); υf——闪光速度(cm/s); j——电流密度(A/mm2)。
电阻对焊时Rc、2Rw、R的变化
闪光对焊时rc、2rw、r的变化
动态接触电阻rc较大并在闪光过程中始终存在,随着闪光过程的 进行,零件的接近速度加大、过梁数目和横截面积增大,导致rc减小; 焊件内部动态电阻2rw由于闪光时的加热而增大,但始终小于rc。同 时,由于rc的降低超过2rw的增加,故总电阻r呈下降趋势。顶锻开始 时由于两零件端面相互接触,液态过梁突然消失,因而r急剧下降, 以后的变形规律同于2rw。
头需倒角
电阻对焊接头形式
3、焊接循环
a、等压式
b、变压式
4、电阻对焊接头形成实质
同种金属 结晶化学与热物理性质
再结晶 固相连接
相近的异种金属
结晶化学与热物理 性质相差大的异种金属
扩散
Mo-TU(无氧铜)接头 20钢再结晶接头
5、规范参数
(1)调伸长度l
考虑因素:顶锻时工件的稳定性和向夹钳的散热。
(5)顶锻留量△u
闪光对焊时,考虑两焊件因顶锻缩短而预留的长度称顶锻留量。它 影响液态金属、氧化物的排出及塑性变形程度,通常△u略大些有利, 可根据材料性质、焊件截面尺寸等因素来选择。通常,△u约点总留量 △的20%~30%,其中有电顶锻量约为无电顶锻量的0.5~1.0倍;焊铝 合金时△u值比焊同截面尺寸钢时约大50%。同时,小截面或薄壁铝件 焊接时,为避免过热还应限制其有电顶锻时间不应静夹具或活动夹具中伸出的长度,又称调臵长度。它的作用 是保证必要的留量(焊件缩短量)和调节加热时的温度场,可根据焊件 断面和材料性质选择: A、l=(0.7~1.0)d(d为圆材直径或方材边长); B、l=(4~5)δ(δ为板材厚度,δ=1~4mm); C、异种材料闪光对焊,l的选择见下表:
- 1、下载文档前请自行甄别文档内容的完整性,平台不提供额外的编辑、内容补充、找答案等附加服务。
- 2、"仅部分预览"的文档,不可在线预览部分如存在完整性等问题,可反馈申请退款(可完整预览的文档不适用该条件!)。
- 3、如文档侵犯您的权益,请联系客服反馈,我们会尽快为您处理(人工客服工作时间:9:00-18:30)。
对接电阻焊(以下简称对焊)是利用电阻热将两工件沿整个端面同时焊接起来的一类电阻焊方法。
对焊的生产率高、易于实现自动化,因而获得广泛应用。
其应用范围可归纳如下:(1)工件的接长例如带钢、型材、线材、钢筋、钢轨、锅炉钢管、石油和天然气输送等管道的对焊。
(2)环形工件的对焊例如汽车轮辋和自行车、摩托车轮圈的对焊、各种链环的对焊等。
(3)部件的组焊将简单轧制、锻造、冲压或机加工件对焊成复杂的零件,以降低成本。
例如汽车方向轴外壳和后桥壳体的对焊,各种连杆、拉杆的对焊,以及特殊零件的对焊等。
(4)异种金属的对焊可以节约贵重金属,提高产品性能。
例如刀具的工作部分(高速钢)与尾部(中碳钢)的对焊,内燃机排气阀的头部(耐热钢)与尾部(结构钢)的对焊,铝铜导电接头的对焊等。
对焊分为电阻对焊和闪光对焊两种。
电阻对焊电阻对焊是将两工件端面始终压紧,利用电阻热加热至塑性状态,然后迅速施加顶锻压力(或不加顶锻压力只保持焊接时压力)完成焊接的方法。
一、电阻对焊的电阻和加热对焊时的电阻分布如图14-2所示。
总电阻可用下式表示:R=2Rω+RC+2Reω式中Rω--一个工件导电部分的内部电阻(Ω);Rc--两工件间的接触电阻(Ω);Rω--工件与电极间的接触电阻(Ω);工件与电极之间的接触电阻由于阻值小,且离接合面较远,通常忽略不计。
工件的内部电阻与被焊金属的电阻率ρ和工件伸出电极的长度l0成正比,与工件的断面积s成反比。
和点焊时一样,电阻对焊时的接触电阻取决于接触面的表面状态、温度及压力。
当接触电阻有明显的氧化物或其他赃物时,接触电阻就大。
温度或压力的增高,都会因实际接触面积的增大而使接触电阻减小。
焊接刚开始时,接触点上的电流密度很大;端面温度迅速升高后,接触电阻急剧减小。
加热到一定温度(钢600度,铝合金350度)时,接触电阻完全消失。
和点焊一样,对焊时的热源也是由焊接区电阻产生的电阻热。
电阻对焊时,接触电阻存在的时间极短,产生的热量小于总热量的10-15%。
但因这部分热量是接触面附近很窄的区域内产生的。
所以会使这一区域的温度迅速升高,内部电阻迅速增大,即使接触电阻完全消失,该区域的产热强度仍比其他地方高。
所采用的焊接条件越硬(即电流越大和通电时间越短),工件的压紧力越小,接触电阻对加热的影响越明显。
二、电阻对焊的焊接循环、工艺参数和工件准备1、焊接循环电阻对焊时,两工件始终压紧,当端面温升高到焊接温度Tω时,两工件端面的距离小到只有几个埃,端面间原子发生相互作用,在接合上产生共同晶粒,从而形成接头。
电阻对焊时的焊接循环有两种:等压的和加大锻压力的。
前者加压机构简单,便于实现。
后者有利于提高焊接质量,主要用于合金钢,有色金属及其合金的电阻对焊,为了获得足够的塑性变形和进一步改善接头质量,还应设置电流顶锻程序。
2、工艺参数电阻对焊的主要工艺参数有:伸出长度、焊接电流(或焊接电流密度)、焊接通电时间、焊接压力和顶锻压力。
(1)伸出长度l0 即工件伸出夹钳电极端面的长度。
选择伸出长度时,要考虑两个因素:顶锻时工件的稳定性和向夹钳的散热。
如果l0过长,则顶锻时工件会失稳旁弯。
l0过短,则由于向钳口的散热增强,使工件冷却过于强烈,会增加塑性变形的困难。
对于直径为d的工件,一般低碳钢:l0=(0.5-1)d,铝和黄铜:l0=(1-2)d,铜:l0=(1.5-2.5)d。
(2)焊接电流Iω和焊接时间tω在电阻对焊时,焊接电流常以电流密度jω来表示。
jω和tω是决定工件加热的两个主要参数。
二者可以在一定范围内相应地调配。
可以采用大电流密度、短时间(强条件),也可以采用小电流密度、长时间(弱条件)。
但条件过强时,容易产生未焊透缺陷;过软时,会使接口端面严重氧化、接头区晶粒粗大、影响接头强度。
(3)焊接压力Fω与顶锻压力Fu,Fω对接头处的产热和塑性变形都有影响。
减小Fω有利于产热,但不利于塑性变形。
因此,易用较小的Fω进行加热,而以大得多的Fu进行顶锻。
但是Fω也不能过低,否则会引起飞溅、增加端面氧化,并在接口附近造成疏松。
3、工件准备电阻对焊时,两工件的端面形状和尺寸应该相同,以保证工件的加热和塑性变形一致。
工件的端面,以及与夹钳接触的表面必须进行严格清理。
端面的氧化物和赃物将会直接影响到接头的质量。
与夹钳接触的工件表面的氧化物和赃物将会增大接触处电阻,使工件表面烧伤、钳口磨损加剧,并增大功率损耗。
清理工件可以用砂轮、钢丝刷等机械手段,也可以用酸洗。
电阻焊接头中易产生氧化物夹杂。
对于焊接质量要求高的稀有金属、某些合金钢和有色金属时,常采用氩、氦等保护氛来解决。
电阻对焊虽有接头光滑、毛刺小、焊接过程简单等优点,但其接头的力学性能较低,对工件端面的准备工作要求高,因此仅用于小断面(小于250mm2)金属型材的对接。
闪光对焊闪光对焊可分为连续闪光对焊和预热闪光对焊。
连续闪光对焊由两个主要阶段组成:闪光阶段和顶锻阶段。
预热闪光对焊只是在闪光阶段前增加了预热阶段。
一、闪光对焊的两个阶段1、闪光阶段闪光的主要作用是加热工件。
在此阶段中,先接通电源,并使两工件端面轻微接触,形成许多接触点。
电流通过时,接触点熔化,成为连接两端面的液体金属过梁。
由于液体过梁中的电流密度极高,使过梁中的液体金属蒸发、过梁爆破。
随着动夹钳的缓慢推进,过梁也不断产生与爆破。
在蒸气压力和电磁力的作用下,液态金属微粒不断从接口间喷射出来。
形成火花急流--闪光。
在闪光过程中,工件逐渐缩短,端头温度也逐渐升高。
随着端头温度的升高,过梁爆破的速度将加快,动夹钳的推进速度也必须逐渐加大。
在闪光过程结束前,必须使工件整个端面形成一层液体金属层,并在一定深度上使金属达到塑性变形温度。
由于过梁爆破时所产生的金属蒸气和金属微粒的强烈氧化,接口间隙中气体介质的含氧量减少,其氧化能力可降低,从而提高接头的质量。
但闪光必须稳定而且强烈。
所谓稳定是指在闪光过程中不发生断路和短路现象。
断路会减弱焊接处的自保护作用,接头易被氧化。
短路会使工件过烧,导致工件报废。
所谓强烈是指在单位时间内有相当多的过梁爆破。
闪光越强烈,焊接处的自保护作用越好,这在闪光后期尤为重要。
2、顶锻阶段在闪光阶段结束时,立即对工件施加足够的顶端压力,接口间隙迅速减小过梁停止爆破,即进入顶锻阶段。
顶锻的作用是密封工件端面的间隙和液体金属过梁爆破后留下的火口,同时挤出端面的液态金属及氧化夹杂物,使洁净的塑性金属紧密接触,并使接头区产生一定的塑性变形,以促进再结晶的进行、形成共同晶粒、获得牢固的接头。
闪光对焊时在加热过程中虽有熔化金属,但实质上是塑性状态焊接。
预热闪光对焊是在闪光阶段之前先以断续的电流脉冲加热工件,然后在进入闪光和顶锻阶段。
预热目的如下:(1)减小需用功率可以在小容量的焊机上焊接断面面积较大的工件,因为当焊机容量不足时,若不先将工件预热到一定温度,就不可能激发连续的闪光过程。
此时,预热是不得已而采取的手段。
(2)降低焊后的冷却速度这将有利于防止淬火钢接头在冷却时产生淬火组织和裂纹。
(3)缩短闪光时间可以减少闪光余量,节约贵重金属。
预热不足之处是:(1)延长了焊接周期,降低了生产率;(2)使过程的自动化更加复杂;(3)预热控制较困难。
预热程度若不一致,就会降低接头质量的稳定性。
二、闪光对焊的电阻和加热闪光对焊时的接触电阻Rc即为两工件端面间液体金属过梁的总电阻,其大小取决于同时存在的过梁数及其横断面积。
后两项又与工件的横断面积、电流密度和两工件的接近速度有关。
随着这三者的增大,同时存在的过梁数及其横截面积增大,Rc将减小。
闪光对焊的Rc比电阻对焊大得多,并且存在于整个闪光阶段,虽然其电阻值逐渐减小,但始终大于工件的内部电阻,直到顶锻开始瞬间Rc才完全消失。
图14-5是闪光对焊时Rc、2Rω和R变化的一般规律。
Rc逐渐减小是由于在闪光过程中,随着端面温度的升高,工件接近速度逐渐增大,过梁的数目和尺寸都随之增大的缘故。
由于Rc大并且存在整个闪光阶段,所以闪光对焊时接头的加热主要靠Rc。
三、闪光对焊的焊接循环、工艺参数和工件准备1、焊接循环闪光对焊的焊接循环14-7所示,图中复位时间是指动夹钳由松开工件至回到原位的时间。
预热方法有两种:电阻预热和闪光预热,图中(b)采用的是电阻预热。
2、工艺参数闪光对焊的主要参数有:伸出长度、闪光电流、闪光流量、闪光速度、顶锻流量、顶锻速度、顶锻压力、顶锻电流、夹钳夹持力等。
图14-8是连续闪光对焊各流量和伸出长度的示意图。
下面介绍各工艺参数对焊接质量的影响及选用原则:(1)伸长长度l0 和电阻对焊一样,l0影响沿工件轴向的温度分布和接头的塑性变形。
此外,随着l0的增大,使焊接回路的阻抗增大,需用功率也要增大。
一般情况下,棒材和厚臂管材l0=(0.7-1.0)d,d为圆棒料的直径或方棒料的边长。
对于薄板(δ=1-4mm)为了顶锻时不失稳,一般取l0=(4-5)δ。
不同金属对焊时,为了使两工件上的温度分布一致,通常是导电性和导热性差的金属l0应较小。
表1是不同金属闪光对焊时的l0参考值。
(2)闪光电流If和顶锻电流Iu If取决于工件的断面积和闪光所需要的电流密度jf。
jf的大小又与被焊金属的物理性能、闪光速度、工件断面的面积和形状,以及端面的加热状态有关。
在闪光过程中,随着vf的逐渐提高和接触电阻Rc的逐渐减小,jf将增大。
顶锻时,Rc迅速消失,电流将急剧增大到顶锻电流Iu。