镀通孔
微通孔填充的电镀铜工艺
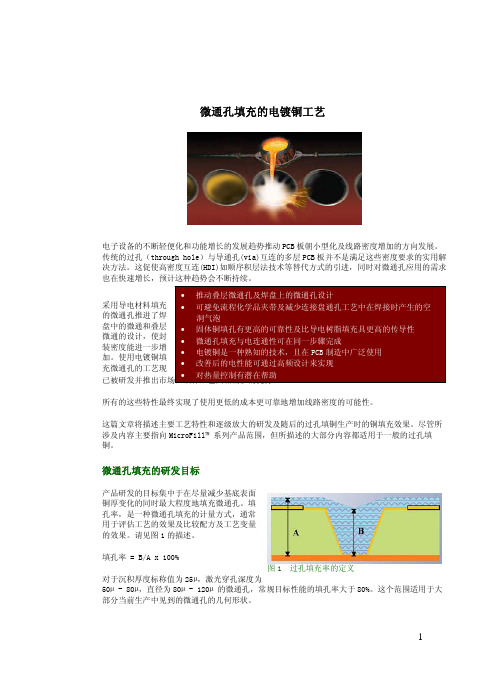
图 6. 硫酸铜浓度与深镀能力之间的关系
流程参数—物理影响
研究的物理工艺参数包括:电流密度、搅 拌、镀层厚度、温度、整流器(DC 或 PPR)及 波形(PPR)。微通孔填充性能的主要影响在下 面描述。
电流密度: 图 7 为电流密度与特定类型微通 孔类型的填孔率之间的关系。一般说来,电 流密度加大对填充率的降低随着微通孔的深 度增加而更明显,当使用更具挑战性的玻璃 增强绝缘基材时,填充率降低会进一步显 著。微通孔填充能力的减弱体现为填充率低 和/或出现空洞。
有关的优化与整流方式相结合,得到了用于直流和 PPR 波形的独特的微通孔填充的产品。
化学组分如下:硫酸铜、硫酸、氯化物,
研究他们彼此间与微通孔填充性能的关系,结果表明主要 的影响来自于硫酸铜的浓度。图 5 已显示浓度对填充效果 的影响。通常表明高一些的浓度可更多地提升微通孔填充 性能。
无机的成分包括二价铜离子(Cu2+),硫酸及氯化物。
硫酸铜是溶液中铜离子的初始来源,在电镀时,溶液中的铜含量通过电镀时在阴阳极间建立起库 仑平衡来维持。阳极通常用与被电镀上去的金属相同的材料制成,并作为离子源,在这里所指的 金属为铜。
硫酸对溶液的整体导电性及减少阳极和阴极间的极化很有效。
氯离子与辅助剂(负载剂)一起作用来减低极性及协助改善沉积表面的高低形貌。使用消耗性的 (铜)阳极时,氯离子有助于阳极的腐蚀,生成均匀及有附着性的阳极膜。
图 7. 不同电流密度对直径为 100µ ,浓度为 80µ 孔的影响。通常低电流密度可改善填孔能 力。
4
溶液搅拌: 这个参数对微通孔填铜有重大影响。图 8 比 较了在微通孔填铜时使用喷嘴或使用冲击电镀进行空气搅 拌效果的不同。很显然,相对于单独的空气搅拌,使用喷 嘴电镀时溶液流直接喷向板很大程度上改善了微通孔填充 的能力及微通孔填充的均匀性。
通孔电镀填孔流程
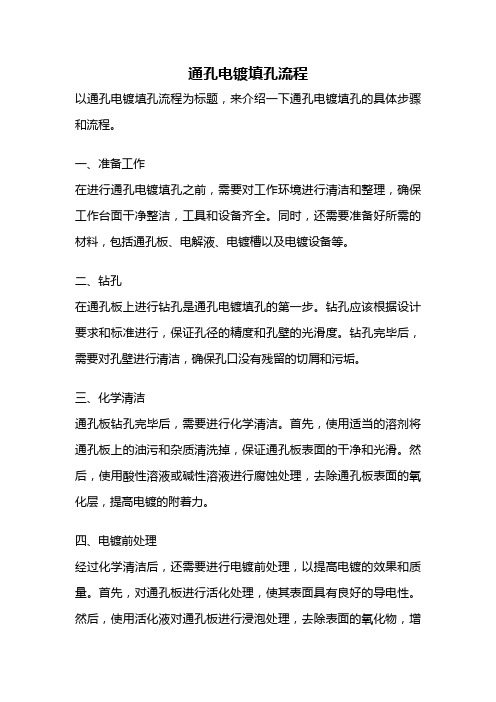
通孔电镀填孔流程以通孔电镀填孔流程为标题,来介绍一下通孔电镀填孔的具体步骤和流程。
一、准备工作在进行通孔电镀填孔之前,需要对工作环境进行清洁和整理,确保工作台面干净整洁,工具和设备齐全。
同时,还需要准备好所需的材料,包括通孔板、电解液、电镀槽以及电镀设备等。
二、钻孔在通孔板上进行钻孔是通孔电镀填孔的第一步。
钻孔应该根据设计要求和标准进行,保证孔径的精度和孔壁的光滑度。
钻孔完毕后,需要对孔壁进行清洁,确保孔口没有残留的切屑和污垢。
三、化学清洁通孔板钻孔完毕后,需要进行化学清洁。
首先,使用适当的溶剂将通孔板上的油污和杂质清洗掉,保证通孔板表面的干净和光滑。
然后,使用酸性溶液或碱性溶液进行腐蚀处理,去除通孔板表面的氧化层,提高电镀的附着力。
四、电镀前处理经过化学清洁后,还需要进行电镀前处理,以提高电镀的效果和质量。
首先,对通孔板进行活化处理,使其表面具有良好的导电性。
然后,使用活化液对通孔板进行浸泡处理,去除表面的氧化物,增加表面活性。
最后,对通孔板进行脱脂处理,去除残留的油污和杂质,确保通孔板表面的干净和光滑。
五、电镀填孔电镀填孔是通孔电镀填孔的关键步骤。
首先,将通孔板放入电镀槽中,将电解液注入槽中,使通孔板完全浸泡在电解液中。
然后,通过电流的作用,将金属离子从电解液中沉积到通孔板的孔壁上,形成金属层。
金属层的形成填满了通孔板的孔壁,实现了通孔的电镀填孔。
六、电镀后处理通孔电镀填孔完成后,还需要进行电镀后处理,以提高填孔质量和表面光洁度。
首先,对填孔后的通孔板进行清洗,去除残留的电解液和金属颗粒。
然后,进行抛光处理,使通孔板表面更加光滑。
最后,对通孔板进行防腐处理,以增加其耐腐蚀性能和使用寿命。
七、质量检验通孔电镀填孔完成后,需要进行质量检验,以确保填孔效果符合要求。
质量检验的内容包括通孔的孔径、孔壁的光滑度以及填孔的完整性等。
通过质量检验,可以判断通孔电镀填孔的质量是否合格,并对不合格的通孔板进行修补或重新制作。
镀通孔制程
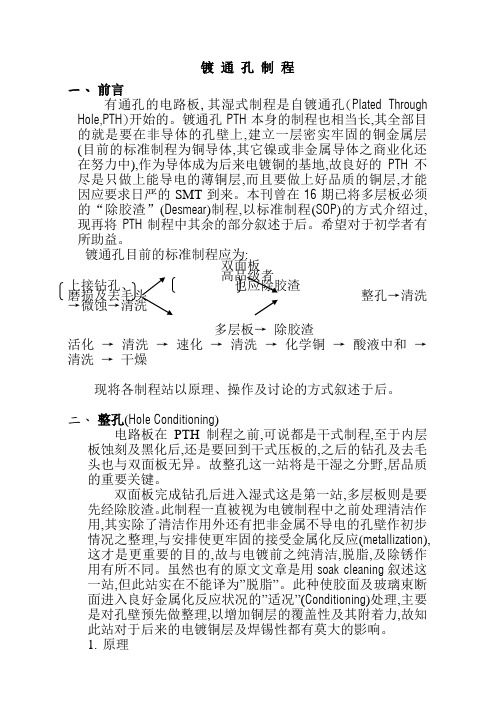
镀通孔制程一、前言有通孔的电路板,其湿式制程是自镀通孔(Plated Through Hole,PTH)开始的。
镀通孔PTH本身的制程也相当长,其全部目的就是要在非导体的孔壁上,建立一层密实牢固的铜金属层(目前的标准制程为铜导体,其它镍或非金属导体之商业化还在努力中),作为导体成为后来电镀铜的基地,故良好的PTH不尽是只做上能导电的薄铜层,而且要做上好品质的铜层,才能因应要求日严的SMT到来。
本刊曾在16期已将多层板必须的“除胶渣”(Desmear)制程,以标准制程(SOP)的方式介绍过,现再将PTH制程中其余的部分叙述于后。
希望对于初学者有所助益。
镀通孔目前的标准制程应为:双面板高品级者上接钻孔、也应除胶渣磨损及去毛头整孔→清洗→微蚀→清洗多层板→除胶渣活化→清洗→速化→清洗→化学铜→酸液中和→清洗→干燥现将各制程站以原理、操作及讨论的方式叙述于后。
二、整孔(Hole Conditioning)电路板在PTH制程之前,可说都是干式制程,至于内层板蚀刻及黑化后,还是要回到干式压板的,之后的钻孔及去毛头也与双面板无异。
故整孔这一站将是干湿之分野,居品质的重要关键。
双面板完成钻孔后进入湿式这是第一站,多层板则是要先经除胶渣。
此制程一直被视为电镀制程中之前处理清洁作用,其实除了清洁作用外还有把非金属不导电的孔壁作初步情况之整理,与安排使更牢固的接受金属化反应(metallization),这才是更重要的目的,故与电镀前之纯清洁,脱脂,及除锈作用有所不同。
虽然也有的原文文章是用soak cleaning叙述这一站,但此站实在不能译为”脱脂”。
此种使胶面及玻璃束断面进入良好金属化反应状况的”适况”(Conditioning)处理,主要是对孔壁预先做整理,以增加铜层的覆盖性及其附着力,故知此站对于后来的电镀铜层及焊锡性都有莫大的影响。
1.原理此一整孔适况处理窍门的被发现也是非常偶然的,早期的业者仍秉持着电镀前处理的观念,认为要将板子做好彻底清洁及活化后,才能去做金属化处理。
PCB的基本知识

PCB的基本知识Solder mask用于生成绿油。
有时候在SMT pin周围就要加入绿油,环径6milSolder paste用于生成钢网。
根据该层来做钢网Drill drawing钻孔图,表示那些地方需要钻孔和孔的大小、孔数。
按X,Y坐标定位而画出整块PCB所需钻孔的位置图,还表示出PTH还是NPTHFlat电镀锡,主要用于非机械孔Assembly drawing装配用。
主要生成装配图并打印出来给焊工看。
不做到板子上Outline主要有三种。
一是板框;二是布线禁止区,一般比板框内缩5mil;三是placement禁止区。
Bare board裸板。
即没有光照腐蚀的板子Daughter board子板Backplane背板互联Conductor trace导线Substrate基底。
Conductor side导线面。
即route sideSolder side焊接面。
即mount sidePattern图形。
比如pin mapping时可以选用图形放置。
即图形化显示Conductive pattern导电图形。
也是图形,但镀锡或者做成铜线Prepreg预浸材料。
在powerpcb的设置中可以看到。
对于四层板,一般是两个双面板之间的材料Bouding layer粘接层Copper-clad surface铜箔面Split裂缝。
比如power plane的壕沟Master drawing布线总图Layout布图设计Layout effecting布线完成率。
主要对自动布线来说Hierarchical design层次设计。
即分层设计。
原理图分层Supporting hole支持孔Plated through hole镀通孔(PTH)孔壁有金属来连接中间层和外层。
和NPTH相反All drilled hole全部钻孔Toaling hole定位孔。
即光学定位孔,对贴片机等有用Landless via hole无连接盘导通孔Pilot hole引导孔Terminal clearance hole端接全隙孔Via-in-pad焊盘中心孔。
电路板湿制程全书
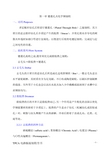
第一章镀通孔及化学铜制程一、功用Purposes多层板经钻孔后即进行镀通孔(Plated Through Hole)之湿制程,其主要目的是去除经钻孔后介质层产生的胶渣(Smear),并使孔壁内非导电的树脂及补强材如玻〇等进行金属化,以便进行后续的电镀层制程,完成层与层之间电性的导通。
二、流程系列Flow Systom镀通孔流程之前,通常须先完成除胶渣之制程:去毛头→除胶渣→镀通孔2.1去毛头Debur去毛头的主要目的是钻孔后所造成孔边残留铜屑(Bur),一般去毛头是以水平滚轮刷磨,其材质有分为尼龙刷、不〇布或陶瓷刷轮,以刷压控制刷磨的强度,另外用于小孔也会以高压水洗及加入少许磷酸或湿润剂于水槽中以求铜面均匀。
2.2除胶渣Desmear除胶渣的目的不单只是除胶渣而已,另一个作用是产生粗化的表面以使化学铜能紧密的附着于介质层上。
胶渣的产生是由于钻孔(机械钻孔或雷射成孔)时,树脂与钻头摩擦产生高热溶解,冷却后附着于表或孔内、孔壁、孔底等处。
2.2.1 去胶渣的四种方法浓硫酸法(sulfuric acid)、重铬酸法(Chromic Acid)、电浆法(Plasma)与〇性高锰酸法(Permanganate)。
A.浓硫酸法:硫酸法由于使用高浓度96~98%硫酸,经7秒冲洗放热处理时间,为保持固定的粗糙度必须一直更新添加新鲜的浓硫酸,操作危险性高,且咬蚀表面光滑无方向性,表面粗糙度无法一致,并不常用。
B.铬酸法:咬蚀速度快,但咬蚀表面无方向性,表面粗糙度无法一致,且目前六价铬为环保局列管毒性化学物质第二类致癌的危险,加上废水处理不容易,已渐渐被淘汰。
C.电浆法:电浆法是将电路板放入真空度为200mbar与功率2000W 高频的电能环境中约20分钟,所用的气体为CF4O2,N2,传统多层板中由于仅以电浆法来去除孔内胶渣效果差,因此多辅以湿制程去胶渣,但目前主要的应用有四:一为通孔与微盲孔除胶渣,由于高纵横比小孔药液循环交换不易,电浆法穿透性好,正好可以解决高纵横比通孔除胶渣的问题。
镀通孔的制造流程
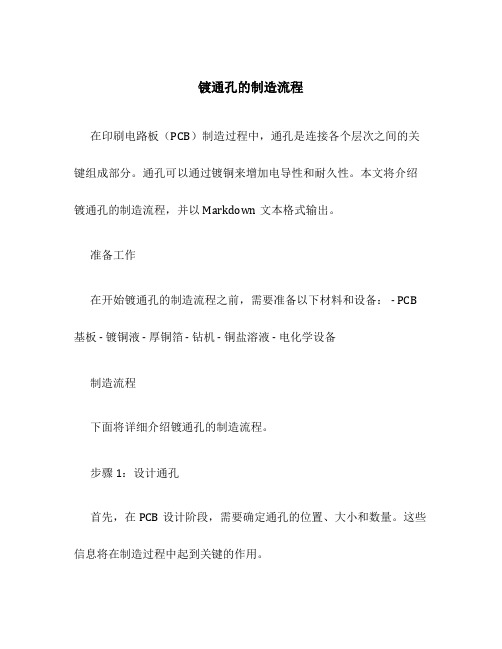
镀通孔的制造流程在印刷电路板(PCB)制造过程中,通孔是连接各个层次之间的关键组成部分。
通孔可以通过镀铜来增加电导性和耐久性。
本文将介绍镀通孔的制造流程,并以Markdown文本格式输出。
准备工作在开始镀通孔的制造流程之前,需要准备以下材料和设备: - PCB 基板 - 镀铜液 - 厚铜箔 - 钻机 - 铜盐溶液 - 电化学设备制造流程下面将详细介绍镀通孔的制造流程。
步骤1:设计通孔首先,在PCB设计阶段,需要确定通孔的位置、大小和数量。
这些信息将在制造过程中起到关键的作用。
步骤2:钻孔在PCB基板上,使用钻机将设计好的通孔位置打孔,以便后续步骤进行电镀。
步骤3:涂覆铜箔为了提高通孔的导电性,需要将铜箔涂覆在PCB基板上。
通常使用厚铜箔进行覆盖。
将铜箔固定在PCB基板的两面,确保通孔周围的区域都有良好的导电性。
步骤4:清洁和脱脂在进行电镀之前,必须确保PCB基板表面的清洁和脱脂。
这可以通过使用特殊的清洁溶液和脱脂剂来完成。
清洁和脱脂的目的是去除表面的污垢和油脂,以提供更好的电镀条件。
步骤5:电解铜涂层将经过清洁和脱脂处理的PCB基板放入装有镀铜液的容器中。
通过电解过程,将铜离子沉积在PCB基板表面的通孔和其他区域上,形成均匀的铜涂层。
电解过程中,需要控制电流和温度,以确保铜涂层的均匀性和精度。
步骤6:清洗和抛光完成铜涂层后,将PCB基板从电解槽中取出,并进行清洗和抛光。
这一步骤的目的是去除镀铜过程中产生的残留物和杂质。
步骤7:涂覆保护层为了保护铜涂层不受外界环境的损害,需要在PCB基板上涂覆一层保护层。
这一层通常是防锈、耐腐蚀的材料,可以防止铜涂层氧化和损坏。
步骤8:最终检查在整个制造流程结束后,需要对PCB基板进行最终检查。
检查的目的是确保通孔和其他部分的质量符合要求。
如果发现任何缺陷或错误,需要进行修正或重新制造。
总结镀通孔是PCB制造中不可或缺的一步。
通过上述的制造流程,可以确保通孔具有良好的导电性和耐久性,从而提高整个PCB的质量和可靠性。
镀通孔
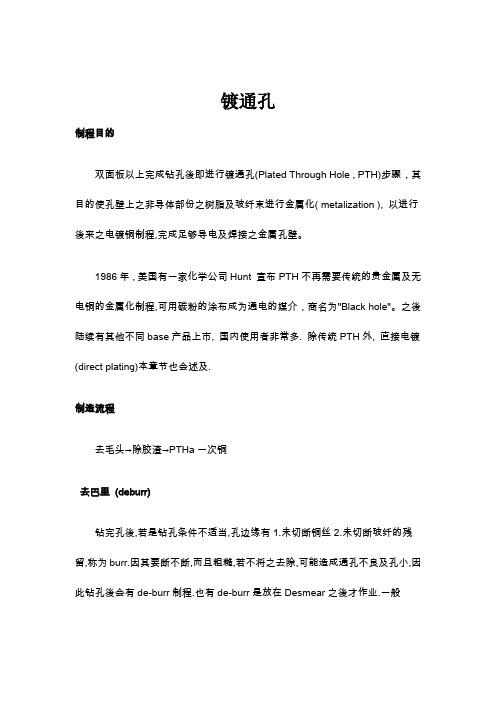
镀通孔制程目的双面板以上完成钻孔後即进行镀通孔(Plated Through Hole , PTH)步骤,其目的使孔壁上之非导体部份之树脂及玻纤束进行金属化( metalization ), 以进行後来之电镀铜制程,完成足够导电及焊接之金属孔壁。
1986年,美国有一家化学公司Hunt 宣布PTH不再需要传统的贵金属及无电铜的金属化制程,可用碳粉的涂布成为通电的媒介,商名为"Black hole"。
之後陆续有其他不同base产品上市, 国内使用者非常多. 除传统PTH外, 直接电镀(direct plating)本章节也会述及.制造流程去毛头→除胶渣→PTHa一次铜去巴里(deburr)钻完孔後,若是钻孔条件不适当,孔边缘有1.未切断铜丝2.未切断玻纤的残留,称为burr.因其要断不断,而且粗糙,若不将之去除,可能造成通孔不良及孔小,因此钻孔後会有de-burr制程.也有de-burr是放在Desmear之後才作业.一般de-burr是用机器刷磨,且会加入超音波及高压冲洗的应用.可参考表.除胶渣(Desmear)A.目的:a. Desmearb. Create Micro-rough增加adhesionB. Smear产生的原因:由於钻孔时造成的高温Resin超过Tg值,而形成融熔状,终致产生胶渣。
此胶渣生於内层铜边缘及孔壁区,会造成.(Poor lnterconnection)C. Desmear的四种方法:硫酸法(Sulferic Acid) 、电浆法(Plasma)、铬酸法(Cromic Acid)、高锰酸钾法(Permanganate).a. 硫酸法必须保持高浓度,但硫酸本身为脱水剂很难保持高浓度,且咬蚀出的孔面光滑无微孔,并不适用。
b. 电浆法效率慢且多为批次生产,而处理後大多仍必须配合其他湿制程处理,因此除非生产特殊板大多不予采用。
c. 铬酸法咬蚀速度快,但微孔的产生并不理想,且废水不易处理又有致癌的潜在风险,故渐被淘汰。
PCB镀通孔发生“空洞”的根本原因和对策
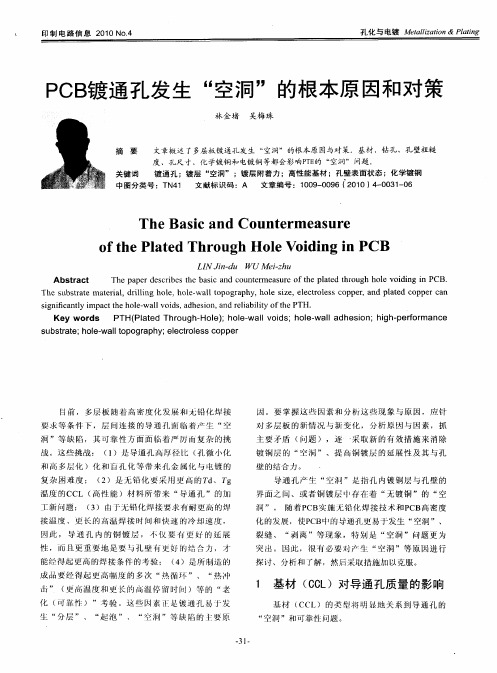
Thes bsr t t ra , rli g h e o e wa lt p g a h ,h l ie lcr ls o pe,a d pltd c p e a u tae mae i l d iln ol,h l — l o o r p y o e sz ,ee to e s c p r n a e o p rc n
洞 ” 。 随 着P CB实施 无 铅 化 焊 接技 术 和 P CB高 密 度
化 的发展 ,使 P B 的导通 孔 更 易于发 生 “ C 空洞 ”、 裂 缝 、 “ 离 ”等 现 象 ,特 别 是 “ 洞 ”问题 更 为 剥 空
性 , 而且 更 重 要地 是要 与孔 壁 何史 好 的 结 台 力 ,才 能经 得起 更 高 的焊接 条 件 的考 验 ; ( )是所 制 造 的 4 成 晶 要 经 得起 更 高幅 度 的多 次 “ 循 环 ”、 “ 热 热冲 击 ” ( 高 温度 和 更 长的 高温 停 留时 问 )等 的 “ 史 老 化 ( 叮靠 性 ) ”考 验 。这 些 素 『 足镀 通 孔 易 于 发 }
界 面 之 问 、或 者铜 镀 层 在 着 “ 镀 铜 ”的 “ f存 无 空
工新 问题 ; ( ) 由 于无 铅 化焊 接 要 求有 耐 更 高 的焊 3
接 温 度 、更 长 的 高温 焊 接 时 间和 快 速 的冷 却 速 度 ,
因此 , 导 通 孔 内 的铜 镀 层 , 小 仪 要 有 更 好 的 延 展
生 “ 分层 ” 、 “ 泡 ” 、 “ 洞 ”等缺 陷 的 丰要 原 起 空
31 .
突 出 。 因此 ,很 有 必 要 对 产 生 “ 洞 ”等 原 因 进 行 空
探 讨 、分 析和 了解 ,然 后采 取措 施加 以 克服 。
PCB钻孔基础介绍
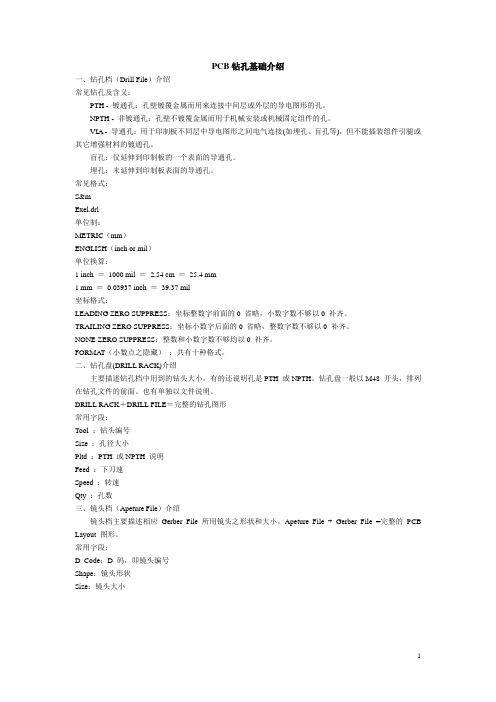
PCB钻孔基础介绍一、钻孔档(Drill File)介绍常见钻孔及含义:PTH - 镀通孔:孔壁镀覆金属而用来连接中间层或外层的导电图形的孔。
NPTH - 非镀通孔:孔壁不镀覆金属而用于机械安装或机械固定组件的孔。
VIA - 导通孔:用于印制板不同层中导电图形之间电气连接(如埋孔、盲孔等),但不能插装组件引腿或其它增强材料的镀通孔。
盲孔:仅延伸到印制板的一个表面的导通孔。
埋孔:未延伸到印制板表面的导通孔。
常见格式:S&mExel.drl单位制:METRIC(mm)ENGLISH(inch or mil)单位换算:1 inch =1000 mil =2.54 cm =25.4 mm1 mm =0.03937 inch =39.37 mil坐标格式:LEADING ZERO SUPPRESS:坐标整数字前面的0 省略,小数字数不够以0 补齐。
TRAILING ZERO SUPPRESS:坐标小数字后面的0 省略,整数字数不够以0 补齐。
NONE ZERO SUPPRESS:整数和小数字数不够均以0 补齐。
FORMA T(小数点之隐藏):共有十种格式。
二、钻孔盘(DRILL RACK)介绍主要描述钻孔档中用到的钻头大小,有的还说明孔是PTH 或NPTH。
钻孔盘一般以M48 开头,排列在钻孔文件的前面。
也有单独以文件说明。
DRILL RACK+DRILL FILE=完整的钻孔图形常用字段:Tool :钻头编号Size :孔径大小Pltd :PTH 或NPTH 说明Feed :下刀速Speed :转速Qty :孔数三、镜头档(Apeture File)介绍镜头档主要描述相应Gerber File 所用镜头之形状和大小。
Apeture File + Gerber File =完整的PCB Layout 图形。
常用字段:D_Code:D 码,即镜头编号Shape:镜头形状Size:镜头大小1。
PCB钻孔的流程、分类和技巧
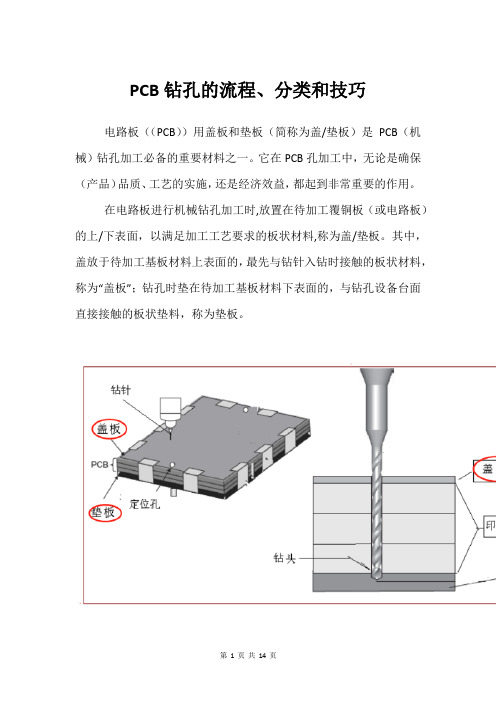
PCB钻孔的流程、分类和技巧电路板((PCB))用盖板和垫板(简称为盖/垫板)是PCB(机械)钻孔加工必备的重要材料之一。
它在PCB孔加工中,无论是确保(产品)品质、工艺的实施,还是经济效益,都起到非常重要的作用。
在电路板进行机械钻孔加工时,放置在待加工覆铜板(或电路板)的上/下表面,以满足加工工艺要求的板状材料,称为盖/垫板。
其中,盖放于待加工基板材料上表面的,最先与钻针入钻时接触的板状材料,称为“盖板”;钻孔时垫在待加工基板材料下表面的,与钻孔设备台面直接接触的板状垫料,称为垫板。
钻孔是PCB制造中最昂贵和最耗时的过程。
PCB钻孔过程必须小心实施,因为即使是很小的错误也会导致很大的损失。
钻孔工艺是PCB制造过程中最关键的工艺。
钻孔工艺是通孔和不同层之间连接的基础,因此钻孔技巧十分重要。
PCB钻孔一、PCB钻孔技术主要有2 种PCB 钻孔技术:机械钻孔和激光钻孔。
PCB钻孔技术1、机械钻孔机械钻头的精度较低,但易于执行。
这种钻孔技术实现了钻头。
这些钻头可以钻出的最小孔径约为6密耳(0.006 英寸)。
机械钻孔的局限性当用于FR4 等较软的材料时,机械钻可用于800 次冲击。
对于密度比较大的材料,寿命会减少到200 计数。
如果PCB 制造商忽视这一点,则会导致出现错误的孔,从而导致电路板报废。
2、激光钻孔另一方面,激光钻可以钻出更小的孔。
激光钻孔是一种非接触式工艺,工件和工具不会相互接触。
激光束用于去除电路板材料并创建精确的孔,可以毫不费力地控制钻孔深度。
激光技术用于轻松钻出受控深度的过孔,可以精确钻出最小直径为2 密耳(0.002”)的孔。
激光钻孔限制电路板由铜、玻璃纤维和树脂制成,这些PCB 材料具有不同的(光学)特性,这使得激光束很难有效地烧穿电路板。
在激光钻孔的情况下,该过程的成本也相对较高。
二、PCB钻孔流程对于PCB(工程师)来说,如果设计电路板,也必须要了解PCB 的制造。
这样才能保证(PCB设计)是可制造,也是可靠的,反过来如果在设计时就注意到制造上的工艺,可以降低成本,并且可以在规定的时间内交付产品。
镀通孔(PTH)孔微蚀处理问题及对策
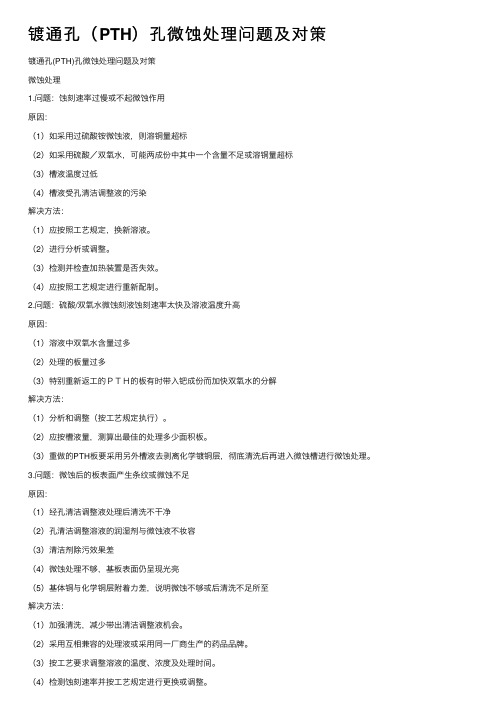
镀通孔(PTH)孔微蚀处理问题及对策
镀通孔(PTH)孔微蚀处理问题及对策
微蚀处理
1.问题:蚀刻速率过慢或不起微蚀作⽤
原因:
(1)如采⽤过硫酸铵微蚀液,则溶铜量超标
(2)如采⽤硫酸/双氧⽔,可能两成份中其中⼀个含量不⾜或溶铜量超标
(3)槽液温度过低
(4)槽液受孔清洁调整液的污染
解决⽅法:
(1)应按照⼯艺规定,换新溶液。
(2)进⾏分析或调整。
(3)检测并检查加热装置是否失效。
(4)应按照⼯艺规定进⾏重新配制。
2.问题:硫酸/双氧⽔微蚀刻液蚀刻速率太快及溶液温度升⾼
原因:
(1)溶液中双氧⽔含量过多
(2)处理的板量过多
(3)特别重新返⼯的PTH的板有时带⼊钯成份⽽加快双氧⽔的分解
解决⽅法:
(1)分析和调整(按⼯艺规定执⾏)。
(2)应按槽液量,测算出最佳的处理多少⾯积板。
(3)重做的PTH板要采⽤另外槽液去剥离化学镀铜层,彻底清洗后再进⼊微蚀槽进⾏微蚀处理。
3.问题:微蚀后的板表⾯产⽣条纹或微蚀不⾜
原因:
(1)经孔清洁调整液处理后清洗不⼲净
(2)孔清洁调整溶液的润湿剂与微蚀液不妆容
(3)清洁剂除污效果差
(4)微蚀处理不够,基板表⾯仍呈现光亮
(5)基体铜与化学铜层附着⼒差,说明微蚀不够或后清洗不⾜所⾄
解决⽅法:
(1)加强清洗,减少带出清洁调整液机会。
(2)采⽤互相兼容的处理液或采⽤同⼀⼚商⽣产的药品品牌。
(3)按⼯艺要求调整溶液的温度、浓度及处理时间。
(4)检测蚀刻速率并按⼯艺规定进⾏更换或调整。
(5)检查及改善微蚀效果并加强后清洗。
通孔镀铜寿命的热应力分析
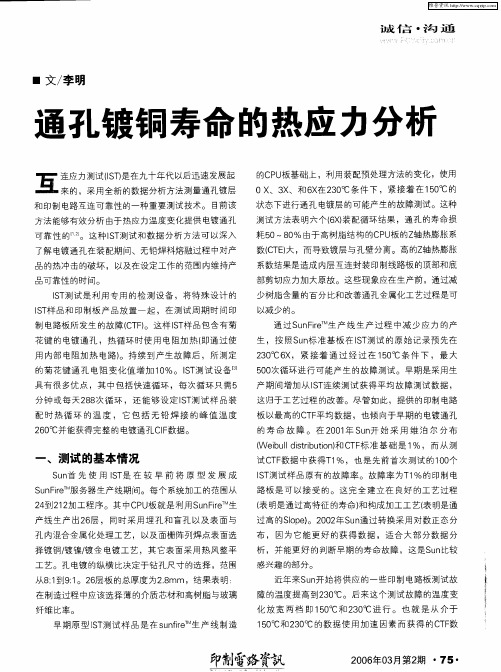
50 0 次循环进行可能产生的故障测试。早期是采用生
产 期 间增 加从 IT S 连续 测 试 获得 平均 故 障测试 数据 ,
这 归于工 艺过程 的改善 。尽 管如此 ,提供 的印制 电路 板 以最 高的C F T 平均 数据 ,也 倾 向于早 期 的电镀通孔
具 有 很 多优点 ,其 中包括 快速 循 环 ,每 次循 环只 需 5 分钟 或每 天 2 8 循 环 ,还 能 够 设定 IT ̄试 样 品 装 8次 S# 0
在 制造过程 中应该 选择 薄的 介质 芯 材和高 树脂 与玻璃
纤 维 比率 。 早 期 原 型 IT ̄试 样 品 是 在 s ni 生 产 线 制造 S# u fe r
印 洛资 制雷 钒
2 60 第期・5 0 年3 2 1 ・ 0 月
维普资讯
可 靠性 的11 种 lT 1 ̄这 S 测试 和 数据 分 析 方法可 以深 入 , 2 了解 电镀 通孔在 装 配期 间、无铅焊 料熔 融过程 中对 产 品的热冲 击 的破 坏 ,以及 在设定 工作 的范围 内维持 产
品可 靠性 的时 间。
数(T ) C E大,而导致镀层与孔壁分离。高的Z 轴热膨胀
系数 结果是造 成 内层 互连 封装 印制线路 板 的顶 部和底 部剪 切应 力加大原 故。这 些现 象应在 生产前 ,通过减 少树 脂含量 的百 分 比和 改善通 孔金 属化工 艺过程是可 以减 少的。
通 过 S n i 生 产 线 生 产 过程 中减 少 应 力 的产 u Fe r
析 ,并能更好 的判断早期的寿命故障 ,这是S n u 比较
感兴 趣 的部 分。
近年来S n u 开始将供应的一些印制 电路板测试故 障的温度提高 ̄2 0C J3 o 。后来这个测试故障的温度变
PCB镀通孔发生_空洞_的根本原因和对策

PCB镀通孔发生“空洞”的根本原因和对策林金堵 吴梅珠摘 要 文章概述了多层板镀通孔发生“空洞”的根本原因与对策。
基材、钻孔、孔壁粗糙度、孔尺寸、化学镀铜和电镀铜等都会影响PTH的“空洞”问题。
关键词 镀通孔;镀层“空洞”;镀层附着力;高性能基材;孔壁表面状态;化学镀铜中图分类号:TN41 文献标识码:A 文章编号:1009-0096(2010)4-0031-06The Basic and Countermeasureof the Plated Through Hole Voiding in PCBLIN Jin-du WU Mei-zhuAbstract The paper describes the basic and countermeasure of the plated through hole voiding in PCB. The substrate material, drilling hole, hole-wall topography, hole size, electroless copper, and plated copper can signi fi cantly impact the hole-wall voids, adhesion, and reliability of the PTH.Key words PTH(Plated Through-Hole); hole-wall voids; hole-wall adhesion; high-performance substrate; hole-wall topography; electroless copper目前,多层板随着高密度化发展和无铅化焊接要求等条件下,层间连接的导通孔面临着产生“空洞”等缺陷,其可靠性方面面临着严厉而复杂的挑战。
这些挑战:(1)是导通孔高厚径比(孔微小化和高多层化)化和盲孔化等带来孔金属化与电镀的复杂困难度;(2)是无铅化要采用更高的T d 、T g 温度的CCL (高性能)材料所带来“导通孔”的加工新问题;(3)由于无铅化焊接要求有耐更高的焊接温度、更长的高温焊接时间和快速的冷却速度,因此,导通孔内的铜镀层,不仅要有更好的延展性,而且更重要地是要与孔壁有更好的结合力,才能经得起更高的焊接条件的考验;(4)是所制造的成品要经得起更高幅度的多次“热循环”、“热冲击”(更高温度和更长的高温停留时间)等的“老化(可靠性)”考验。
镀通孔前段制程中常遇到的问题与解决对策

镀通孔前段制程中常遇到的问题与解决对策镀铜孔制程主要目的是将不导电的孔壁(玻纤与树脂),采用化学铜或其他DP的手段,使之能够导电而完成后续电镀铜。
此段流程一般称为PTH,系指“PTH前制程+化学铜”,更狭义而为业者所常说的PTH,则是专指化学铜以前的各站,但是又不包括更前面的除胶渣Desmear在内。
传统PTH共有四站即:整孔与清洁、微蚀、活化、速化。
以下是镀通孔前段制程所常遇到的问题,就其原因与对策加以整理,以供读者参考与应用。
一、为什么从整孔清洁剂中带至后段槽液的过量泡沫?1.可能原因:整孔槽液在多空的板子中可能带出量太多因应对策:板子出槽后应延长滴水时间(水平连线因有吸液滚轮,故此种问题较少)。
2.可能原因:整孔后水洗不足因应对策:1)检查水洗水是否已流进水洗槽。
2)增加水洗水的流量。
3)在容许的范围内,增加水洗时间或提高水洗温度。
3.可能原因:整孔槽液配制不当,浓度太高因应对策:检查槽液配制程序是否依照供应商的指示。
二、为什么整孔清洁剂槽液中有粒状物体浮游?1.可能原因:非螯合剂(Non-Chalataed)的清洁剂或整孔剂无法完全溶解板子掉落的污染物因应对策:1)加强过滤处理。
2)上游去毛边毛头制程后须以高压喷射的水柱进行强力冲洗。
三、为什么硫酸/双氧水微蚀液的蚀速过快且槽温上升?1.可能原因:双氧水含量可能过高因应对策:分析槽液并调至规格范围内。
2.可能原因:槽液内板子作业面积过大因应对策:1)减少板子的工作量或增加槽液的体积。
2)增设槽外冷却器。
3.可能原因:过多热量导致双氧水分解因应对策:检查加热器会加装冷却器。
4.可能原因:剥除无电铜的重工可能会将底钯层残屑带进入槽液中,进而出现催化作用造成双氧水分解因应对策:另外设线进行重工用的槽液。
四、为什么化学铜与电镀同后孔壁玻纤或树脂上发现有破洞?1.可能原因:清洁整孔剂/活化剂/速化剂/化学铜等槽液成份彼此配合不良因应对策:在实验室中以小槽实验确认其等药水是否匹配,或最好使用药水供应商的PTH全线专用化学品进行试验。
PCB中的通孔设计规则

通孔传统上被分为两组:电镀的(支持的)孔和非电镀的(不支持的)孔。
“支持的”指孔壁上的电镀。
非电镀的或不支持的孔或许有或许没有焊盘,比如安装孔和无孔壁电镀。
这是制造上的术语,可是关于设计而言,孔应当分为被焊接和不被焊接的两类。
关于这些类型中的每一个,被电镀的和不被电镀的分类应当被表记出来。
1、被焊接的. 被电镀的通孔( PLT H)(包含通孔). 不被电镀的通孔( NPTH)2、不被焊接的.被电焊的通孔3、有焊盘和没有焊盘的不被电镀的通孔(NPTH)设计师一定第一知道焊盘能否被确以为被焊接的或不被焊接的。
这个信息帮助工程师决定焊盘的计算是为了焊接仍是为了最小孔环。
假如焊盘没有被焊接,就可以使用标准的环孔并依据组装要求不变。
注意:通孔不过是一个没有焊接的电镀通孔。
在每个组装或许应用中,它不要求利用计算来确认焊盘尺寸,可是要求对最小环孔或能够承载足够电流的最小、最经济的尺寸进行一次较简单的计算。
4、非焊接通孔最小孔环由两个不一样的项构成。
当制造商谈到最小孔环时,指的是标准要求的或是设计师标明的最小孔环外加其自己的孔环要求。
IPC 或其余标准所指定的孔环是印制板达成所要求的最小孔环。
关于一个 0.008 英寸的孔其最小的焊盘直径应当是一个 0.031 英寸。
再次重申,一定要注意这是一个最小值,除非必需,不然就不要使用,介绍的尺寸起码比最小直径大 0.002 英寸。
这些例子的值是鉴于惯例工艺的。
关于外面焊盘孔环起码应当比电镀层厚0.002 英寸(环形的),关于内部焊盘孔环起码应当比电镀厚0.001 英寸。
有效的电镀层厚度是0.0030 英寸。
5、被焊接的通孔除了表面面面积一定要更大,以增强散热来防止出现焊接不良的问题,大部分的规则都合用于被焊接的通孔。
假如可能,为了一致性和便于计算,除非需要简化的焊盘,不然内焊盘应当与外焊盘相同。
其原由是外焊盘被焊接了而内焊盘却没有,被焊接的通孔一定与引脚直径成比率增添,由于更大的引脚要求更多的热量;而为了在引脚和焊盘间平均散热,焊盘一定增大。
PCB缺陷名词解释
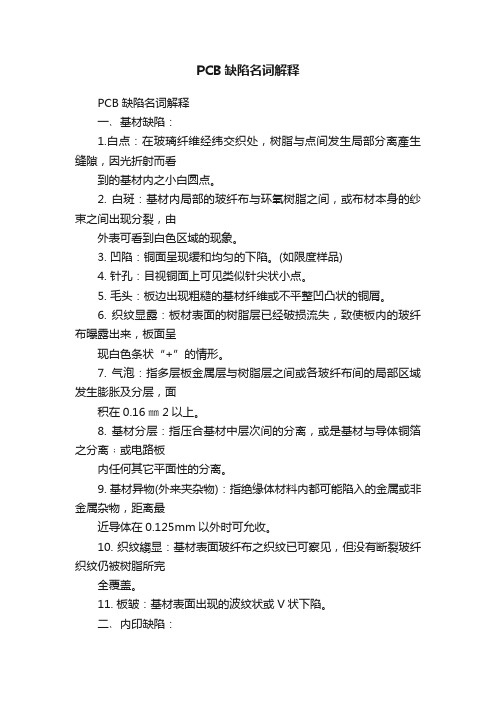
PCB缺陷名词解释PCB缺陷名词解释一﹑基材缺陷:1.白点:在玻璃纤维经纬交织处,树脂与点间发生局部分离產生缝隙,因光折射而看到的基材内之小白圆点。
2. 白斑:基材内局部的玻纤布与环氧树脂之间,或布材本身的纱束之间出现分裂,由外表可看到白色区域的现象。
3. 凹陷:铜面呈现缓和均匀的下陷。
(如限度样品)4. 针孔:目视铜面上可见类似针尖状小点。
5. 毛头:板边出现粗糙的基材纤维或不平整凹凸状的铜屑。
6. 织纹显露:板材表面的树脂层已经破损流失,致使板内的玻纤布曝露出来,板面呈现白色条状“+”的情形。
7. 气泡:指多层板金属层与树脂层之间或各玻纤布间的局部区域发生膨胀及分层,面积在0.16㎜2以上。
8. 基材分层:指压合基材中层次间的分离,或是基材与导体铜箔之分离﹔或电路板内任何其它平面性的分离。
9. 基材异物(外来夹杂物):指绝缘体材料内都可能陷入的金属或非金属杂物,距离最近导体在0.125mm以外时可允收。
10. 织纹縐显:基材表面玻纤布之织纹已可察见,但没有断裂玻纤织纹仍被树脂所完全覆盖。
11. 板皱:基材表面出现的波纹状或V状下陷。
二﹑内印缺陷:1. 显影过度:因曝光能量不足或显影速度过慢使不该显影掉的油墨被显影掉,油墨过缘呈现不平锯齿状。
2. 显影不净:被显影掉油墨的铜面上残留一层很薄的油墨,使铜面无光泽呈现白雾状。
3. 内短:内层因残铜或P.P胶绝缘不良而致使同一层相隔区域间或层间短路。
4. 内断:因内层线路断开,螃蟹脚被咬蚀掉或孔壁与螃蟹脚隔离而造成内层或层与层间断开。
5. 裁板不良:裁板到成型线以内。
6. 内层偏移:内层对位对准度不够,使内层图形向一方偏移。
(如限度样品)7. 板面残胶:板面残留有软性胶状物质。
8. 点状断线:经蚀刻后板面线路上有细小的点状断路。
9. 线细:线径低于客户要求之下限或原稿线径之20%。
10. 线路锯齿:线路局部缺口,凸点交错呈现锯齿状。
11. 刮伤:板面镀层或涂覆层因外力受损,且超过其厚度的20%以上。
通孔电镀铜填孔浅析
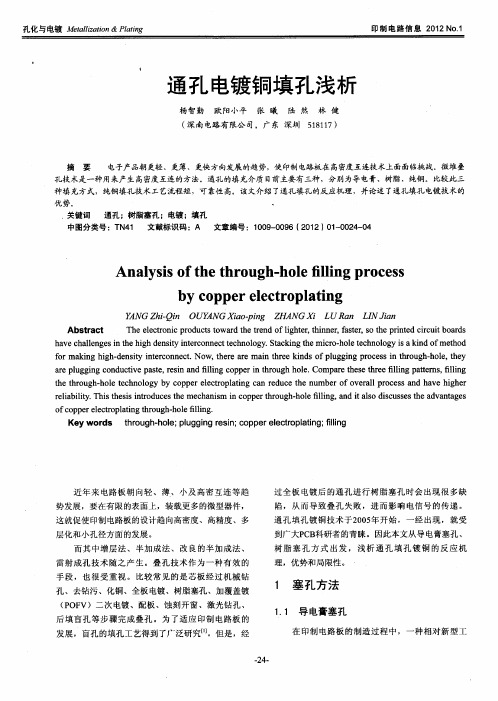
o o p ree to aig t o g - o efli . fc p e lcr plt n h u h h l l r i ng
Ke y wor s t r u h・o e p u g n e i; o p r l c r pa ig f l g d h o g ・ l ; lg ig r s n c p e e t l t ; ln h e o n ii
Ab r t stac Th lcr n cp o u t o r e te d o g tr t i n r a tr S h rn e ic tb a d e ee to i r d c st wa dt r n fl h e, h n e,fse , Ot ep it d crui o r s h i
近 年 来 电路板 朝 向轻 、薄 、小 及 高 密 互连 等 趋
势发 展 ,要在 有 限的表 面上 ,装 载更 多 的微 型器 件 ,
过全 板 电镀 后 的通 孔 进 行树 脂 塞 孔 时 会 出现 很 多缺 陷 , 从而 导 致 叠 孔 失 败 ,进 而 影 响 电信 号 的 传递 。
到广大P B C 科研者的青睐。因此本文从导 电膏塞孔、 树脂 塞孔方 式 出发 ,浅 析通孔 填孔镀 铜 的反应机
理 ,优势 和局 限性 。
1 塞 孔方 法
- 1、下载文档前请自行甄别文档内容的完整性,平台不提供额外的编辑、内容补充、找答案等附加服务。
- 2、"仅部分预览"的文档,不可在线预览部分如存在完整性等问题,可反馈申请退款(可完整预览的文档不适用该条件!)。
- 3、如文档侵犯您的权益,请联系客服反馈,我们会尽快为您处理(人工客服工作时间:9:00-18:30)。
镀通孔7.1製程目的雙面板以上完成鑽孔後即進行鍍通孔(Plated Through Hole , PTH)步驟,其目的使孔壁上之非導體部份之樹脂及玻纖束進行金屬化( metalization ), 以進行後來之電鍍銅製程,完成足夠導電及焊接之金屬孔壁。
1986年,美國有一家化學公司Hunt 宣佈PTH不再需要傳統的貴金屬及無電銅的金屬化製程,可用碳粉的塗佈成為通電的媒介,商名為"Black hole"。
之後陸續有其他不同base產品上市, 國內使用者非常多. 除傳統PTH外, 直接電鍍(direct plating)本章節也會述及.7.2製造流程去毛頭→除膠渣→PTHa一次銅7.2.1. 去巴里(deburr)鑽完孔後,若是鑽孔條件不適當,孔邊緣有1.未切斷銅絲2.未切斷玻纖的殘留,稱為burr.因其要斷不斷,而且粗糙,若不將之去除,可能造成通孔不良及孔小,因此鑽孔後會有de-burr製程.也有de-burr是放在Desmear之後才作業.一般de-burr是用機器刷磨,且會加入超音波及高壓沖洗的應用.可參考表4.1.7.2.2. 除膠渣(Desmear)A.目的:a. Desmearb. Create Micro-rough增加adhesionB. Smear產生的原因:由於鑽孔時造成的高溫Resin超過Tg值,而形成融熔狀,終致產生膠渣。
此膠渣生於內層銅邊緣及孔壁區,會造成P.I.(Poor lnterconnection)C. Desmear的四種方法:硫酸法(Sulferic Acid) 、電漿法(Plasma)、鉻酸法(Cromic Acid)、高錳酸鉀法(Permanganate).a. 硫酸法必須保持高濃度,但硫酸本身為脫水劑很難保持高濃度,且咬蝕出的孔面光滑無微孔,並不適用。
b. 電漿法效率慢且多為批次生產,而處理後大多仍必須配合其他濕製程處理,因此除非生產特殊板大多不予採用。
c. 鉻酸法咬蝕速度快,但微孔的產生並不理想,且廢水不易處理又有致癌的潛在風險,故漸被淘汰。
d. 高錳酸鉀法因配合溶劑製程,可以產生微孔。
同時由於還原電極的推出,使槽液安定性獲得較佳控制,因此目前較被普遍使用。
7.2.2.1 高錳酸鉀法(KMnO4 Process):A.膨鬆劑(Sweller):a. 功能:軟化膨鬆Epoxy,降低Polymer 間的鍵結能,使KMnO4 更易咬蝕形成Micro-rough 速率作用Concentrationb. 影響因素: 見圖7.1c. 安全:不可和KMnO4 直接混合,以免產生強烈氧化還原,發生火災。
d. 原理解釋:(1) 見圖7.2初期溶出可降低較弱的鍵結,使其鍵結間有了明顯的差異。
若浸泡過長,強的鏈結也漸次降低,終致整塊成為低鏈結能的表面。
如果達到如此狀態,將無法形成不同強度結面。
若浸泡過短,則無法形成低鍵結及鍵結差異,如此將使KMnO4咬蝕難以形成蜂窩面,終致影響到PTH的效果。
(2) Surface Tension的問題:無論大小孔皆有可能有氣泡殘留,而表面力對孔內Wetting也影響頗大。
故採用較高溫操作有助於降低Surface Tension及去除氣泡。
至於濃度的問題,為使Drag out降低減少消耗而使用略低濃度,事實上較高濃度也可操作且速度較快。
在製程中必須先Wetting孔內壁,以後才能使藥液進入作用,否則有空氣殘留後續製程更不易進入孔內,其Smear將不可能去除。
B. 除膠劑(KMnO4 ):a. 使用KMnO4的原因:選KMnO4而未選NaMnO4是因為KMnO4溶解度較佳,單價也較低。
b. 反應原理:4MnO4- + C + 4OH- → MnO4= + CO2 + 2H2O (此為主反應式)2MnO4- + 2OH- → 2MnO4= + 1/2 O2 + H2O (此為高PH值時自發性分解反應)MnO4- + H2O → MnO2 + 2OH- + 1/2 O2 (此為自然反應會造成Mn+4沉澱)c. 作業方式:早期採氧化添加劑的方式,目前多用電極還原的方式操作,不穩定的問題已獲解決。
d. 過程中其化學成份狀況皆以分析得知,但Mn+7為紫色, Mn+6為綠色,Mn+4 為黑色,可由直觀的色度來直接判斷大略狀態。
若有不正常發生,則可能是電極效率出了問題須注意。
e. 咬蝕速率的影響因素: 見圖7.3f. 電極的好處:(1).使槽液壽命增長(2).品質穩定且無By-product,其兩者比較如圖7.4:g. KMnO4形成Micro-rough的原因: 由於Sweller造成膨鬆,且有結合力之強弱,如此使咬蝕時產生選擇性,而形成所謂的Micro-rough。
但如因過度咬蝕,將再度平滑。
h. 咬蝕能力也會隨基材之不同而有所改變i. 電極必須留心保養,電極效率較難定出絕對標準,且也很難確認是否足夠應付實際需要。
故平時所得經驗及廠商所提供資料,可加一係數做計算,以為電極需求參考。
C. 中和劑(Neutralizer):a. NaHSO3是可用的Neutralizer之一,其原理皆類似Mn+7 or Mm+6 or Mn+4(Neutralizer)->Mn+2 (Soluable)b. 為免於Pink Ring,在選擇Acid base必須考慮。
HCl及H2SO4系列都有,但Cl易攻擊Oxide Layer,所以用H2SO4為Base 的酸較佳。
c .藥液使用消耗分別以H2SO4及Neutralizer,用Auto-dosing 來補充,維護。
7.2.2.2 .整條生產線的考慮:A.Cycle time:每Rack(Basket)進出某類槽的頻率(時間)B.產能計算:(Working hours / Cycle time)*( FIight Bar / Hoist)*(Racks/Flight Bar)*(SF/Rack)= SF/MonC.除膠渣前Pre-baking對板子的影響:見圖7.5a.由於2.在壓合後己經過兩次Cure,結構會比1,3 Cure更完全,故Baking 會使結構均一,壓板不足處得以補償。
b.多量的氧,氧化了Resin間的Bonding,使咬蝕速率加劇2~3倍。
且使1,2,3 區較均一。
c.釋放Stress,減少產生Void的機會.7.2.2.3. 製程內主要反應及化學名稱:A.化學反應:a .主要反應4MnO4- + 4OH- + Epoxy→ 4MnO4= + CO2↑ + 2H2Ob. 副反應:2MnO4- + 2OH- ←→ 2MnO4= + 1/2O2 + H2O (Side reaction)MnO4= + H2O (CI-/SO4= /Catalize Rx.) → MnO2↓ + 2OH- + 1/2 O2(Precipitation formation)2MnO4= + NaOCI + H2O → 2MnO4- + 2OH- + NaCI4MnO4= + NaS2O8 + H2SO4 → 4MnO4- + 2OH- + 2Na2SO44MnO4= + K2S2O8 + H2SO4 → 4MnO4- + 2OH- + 2K2SO4(For Chemical regeneration type process reaction)2MnO4= + 1/2 O2 + H2O ←→2MnO4- + 2 OH-(Electrolytic reaction: Need replenish air for Oxgen consumption)B.化學品名稱:MnO4- Permanganate NaS2O8 Sodium PersulfateMnO4= Manganate S2O4- SulfateOH- Hydroxide(Caustic) CO2 Carbon DioxideNaOCI Sodium Hydrochloride MnO2Manganese Dioxide7.2.2.4.典型的Desmear Process: 見表7.2.2.5. Pocket Void的解釋:A.說法一:Sweller殘留在Glass fiber中,在Thermal cycle時爆開。
B.說法二: 見圖7.6a.壓板過程不良Stress積存,上鍚過程中力量釋出所致b.在膨漲中如果銅結合力強,而Resin釋出Stress方向呈Z軸方向,當Curing 不良而Stress過大時則易形成a之斷裂,如果孔銅結合力弱則易形成B 之Resin recession,結合力好而內部樹脂不夠強軔則出現c之Pocket voidC﹒如果爆開而形成銅凸出者稱為Pull away7.2.3 化學銅(PTH)PTH系統概分為酸性及鹼性系統,特性依基本觀念而有不同。
7.2.3.1 酸性系統:A.基本製程:Conditioner → Microetch→ Catalpretreatment→ Cataldeposit→ Accelerator→ Electroless DepositB.單一步驟功能說明:a. 整孔Conditioner:1. Desmear後孔內呈現Bipolar現象,其中Cu呈現高電位正電,Glass fiber、Epoxy呈負電2. 為使孔內呈現適當狀態,Conditioner具有兩種基本功能(1)Cleaner:清潔表面(2)Conditioner:使孔壁呈正電性,以利Pd/Sn Colloid負電離子團吸附3. 一般而言粒子間作用力大小如表因而此類藥液系統會有吸附過多或Colloid過多的吸附是否可洗去之顧慮4. Conditioner若Drag In 至Activator槽,會使Pd+離子團降低b. 微蝕Microetch1. Microetching旨在清除表面之Conditioner所形成的Film2. 此同時亦可清洗銅面殘留的氧化物c. 預活化Catalpretreatment1. 為避免Microetch形成的銅離子帶入Pd/Sn槽,預浸以減少帶入2. 降低孔壁的Surface Tensiond. 活化Cataldeposit1. 一般Pd膠體皆以以下結構存在:見圖7.72. Pd2+:Sn2+:Cl- = 1:6:12較安定3. 一般膠體的架構方式是以以下方式結合:見圖7.8當吸附時由於Cl會產生架橋作用,且其半徑較大使其吸附不易良好,尤其如果孔內的Roughness不適當更可能造成問題。
4. 孔壁吸附了負離子團,即中和形成中和電性e. 速化Accelerator1. Pd膠體吸附後必須去除Sn,使Pd2+曝露,如此才能在未來無電解銅中產生催化作用形成化學銅2. 基本化學反應為:Pd+2/Sn+2 (HF)→Pd+2(ad) + Sn+2 (aq)Pd+2(ad) (HCHO)→Pd(s)3. 一般而言Sn與Pd特性不同,Pd為貴金屬而Sn則不然,因此其主反應可如下:Sn+2a Sn+4 + 6F- → SnF6-2 or Sn+2 + 4F- →SnF4-2而Pd則有兩種情形:PH>=4 Pd+2 + 2(OH)- → Pd(OH)2PH<4 Pd+2 + 6F- → PdF6-44. Pd吸附在本系統中本身就不易均勻,故速化所能發揮的效果就極受限制。