粉末冶金原理第六章
材料加工工艺习题【考研】【复习】

《材料加工工艺》考研习题第一章绪论第二章液态金属成形1.金属及合金的结晶包括哪两个基本过程?什么是均质形核和非均质形核?在实际铸造生产中铸造合金结晶的形核是以哪种形核为主,为什么?2.什么是液态金属的充型性能,它与哪些因素有关?铸造合金流动性的好与差对铸件质量有何影响?影响铸造合金流动性的主要因素有哪些?生产中如何采取措施提高铸造合金的流动性?3.铸造合金由液态冷却到室温时要经过哪三个收缩阶段?收缩对铸件质量有什么影响?其收缩大小与哪些因素有关?4.缩孔、缩松是铸件中的常见缺陷之一,哪些因素影响其形成?生产中如何采取措施进行防止?5.什么是铸造应力?铸造应力大小对铸件质量有什么影响?热应力是如何形成的?哪些因素影响其大小?生产中常采取哪些措施来防止和减小应力对铸件的危害?6.铸造合金中的气体主要来源于哪些方面?又以哪些形式存在于铸造合金中?对铸件质量有什么影响?7.铸造合金中的夹杂物是如何分类的?对铸件质有什么影响?如何防止和减小其对铸件的危害?8.湿型粘土砂的主要成分是什么?它有哪些优缺点?适合生产哪些铸件?9.湿型粘土砂的造型方法有哪些?试比较应用震击、压实、射压、高压、气冲和静压等各种造型方法的紧实的砂型紧实度分布(沿砂箱高度方向)。
为什么需要用高密度湿粘土砂型生产铸件?10.树脂自硬砂、水玻璃砂与粘土砂比较有哪些优点?各适用于哪些铸件的生产?11.砂芯的作用是什么?经常使用哪些粘结剂来制芯?常用的制芯工艺有哪些?12.砂型和砂芯涂料的作用是什么?其主要组成有哪些?13.什么是顺序凝固原则?什么是同时凝固原则?各需采用什么措施来实现?上述两种凝固原则各适用于哪些场合?14.铸件的壁厚为什么不能太薄,也不能太厚,而且应尽可能厚薄均匀?为什么要规定铸件的最小壁厚?不同铸造合金要求一样吗?为什么?。
15.为便于生产和保证铸件质量,通常对铸件结构有哪些要求?16.何谓铸件的浇注位置?它是否指铸件上的内绕道位置?铸件的浇注位置对铸件的质量有什么影响?应按何原则来选择?17.试述分型面与分模面的概念?分模造型时,其分型面是否就是其分模面?从保证质量与简化操作两方面考虑,确定分型面的主要原则有哪些?18.试确定图2-116所示铸件的浇注位置及分型面。
粉末冶金原理-中文
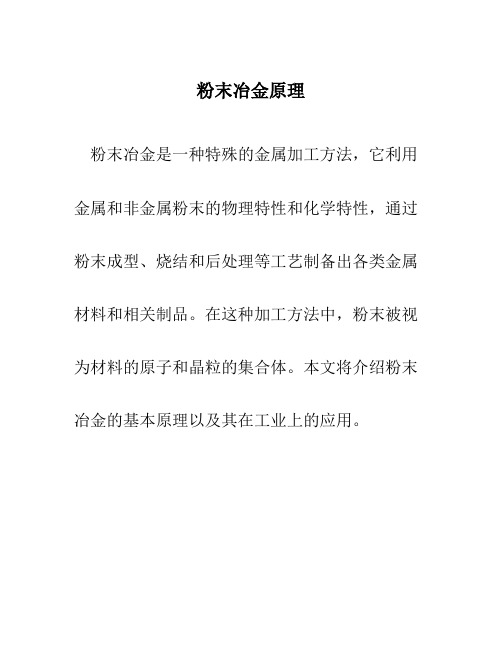
粉末冶金原理粉末冶金是一种特殊的金属加工方法,它利用金属和非金属粉末的物理特性和化学特性,通过粉末成型、烧结和后处理等工艺制备出各类金属材料和相关制品。
在这种加工方法中,粉末被视为材料的原子和晶粒的集合体。
本文将介绍粉末冶金的基本原理以及其在工业上的应用。
粉末冶金的基本原理1.原料选择:粉末冶金的首要任务是选择适当的原料。
原料可以是金属、合金或陶瓷等材料的粉末。
原料的选择应该考虑材料的化学成分、晶体结构、粒子形状和尺寸分布等因素。
2.粉末的制备:粉末的制备是粉末冶金的关键步骤之一。
常见的粉末制备方法包括研磨、机械合金化、溶液沉淀和气相反应等。
不同的制备方法可以获得不同尺寸和形状的粉末。
3.粉末的成型:成型是将粉末转变为所需形状的工艺。
常用的成型方法包括压制、挤出、注射成型和3D打印等。
通过成型,粉末可以被固化成具有一定强度和形状的零件。
4.烧结:烧结是粉末冶金过程中的关键步骤之一。
经过成型的粉末件放入高温环境中,粉末颗粒与颗粒之间发生扩散和结合,形成致密的材料。
烧结温度和时间会影响材料的致密性和力学性能。
5.后处理:烧结后的材料可能需要进行后处理。
常用的后处理方法包括热处理、表面处理和加工等。
通过后处理,可以改善材料的性能和功能。
粉末冶金的应用领域粉末冶金广泛应用于各个领域,包括汽车、航空航天、电子、能源、医疗和军工等。
1.汽车行业:粉末冶金技术在汽车行业中得到广泛应用。
例如,通过粉末冶金可以制备高强度和轻质的发动机零件和齿轮等关键部件,提高汽车的燃油效率和排放性能。
2.航空航天:航空航天行业对材料的要求非常高。
粉末冶金可以制备出具有优异的高温强度和耐腐蚀性能的钛合金和镍基合金等材料,用于制造航空发动机和航天器件。
3.电子:在电子行业中,粉末冶金可以制备具有高导电性和磁导率的材料,例如铜粉末用于制造电子线路板和电磁元件。
4.能源:粉末冶金在能源领域的应用主要集中在制备高温抗氧化和热电材料。
例如,通过粉末冶金可以制备铁素体不锈钢和铬基合金等材料,用于制造高温炉和热交换器等设备。
粉末冶金的原理
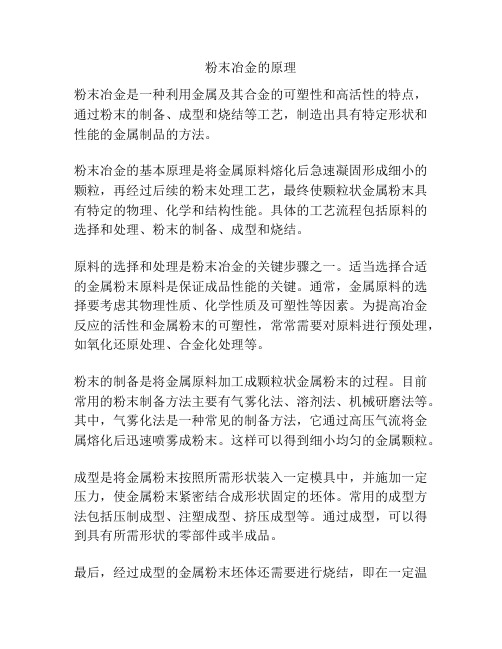
粉末冶金的原理粉末冶金是一种利用金属及其合金的可塑性和高活性的特点,通过粉末的制备、成型和烧结等工艺,制造出具有特定形状和性能的金属制品的方法。
粉末冶金的基本原理是将金属原料熔化后急速凝固形成细小的颗粒,再经过后续的粉末处理工艺,最终使颗粒状金属粉末具有特定的物理、化学和结构性能。
具体的工艺流程包括原料的选择和处理、粉末的制备、成型和烧结。
原料的选择和处理是粉末冶金的关键步骤之一。
适当选择合适的金属粉末原料是保证成品性能的关键。
通常,金属原料的选择要考虑其物理性质、化学性质及可塑性等因素。
为提高冶金反应的活性和金属粉末的可塑性,常常需要对原料进行预处理,如氧化还原处理、合金化处理等。
粉末的制备是将金属原料加工成颗粒状金属粉末的过程。
目前常用的粉末制备方法主要有气雾化法、溶剂法、机械研磨法等。
其中,气雾化法是一种常见的制备方法,它通过高压气流将金属熔化后迅速喷雾成粉末。
这样可以得到细小均匀的金属颗粒。
成型是将金属粉末按照所需形状装入一定模具中,并施加一定压力,使金属粉末紧密结合成形状固定的坯体。
常用的成型方法包括压制成型、注塑成型、挤压成型等。
通过成型,可以得到具有所需形状的零部件或半成品。
最后,经过成型的金属粉末坯体还需要进行烧结,即在一定温度下对金属粉末进行加热处理,使其颗粒之间发生结晶和扩散,相互融合并形成坚固的金属材料。
烧结可以通过自发热烧结、辅助烧结等方法来实现。
烧结过程中,金属粉末之间的氧化物和杂质也会在高温下被还原和挥发。
通过以上的处理工艺,粉末冶金可以制备出具有复杂形状、高强度、良好磨损性能和耐磨性能的金属制品。
由于粉末冶金具有成本低、能耗少、无需后加工等优势,因此在汽车、航空航天、工具等领域得到广泛应用。
材料工程基础-第六章 粉末材料的成形与固结
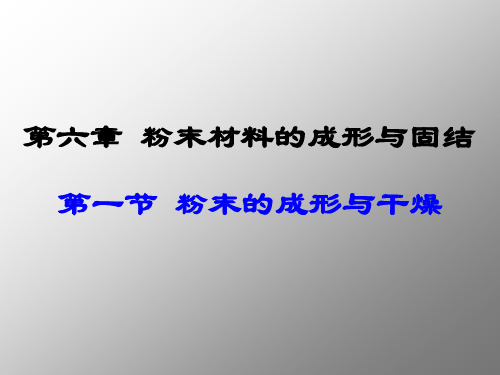
P0—初始接触应力 ρ—相对密度
θ0—(1-ρ) a=[ρ2(ρ-ρ0)]/θ0
成形方法
压力成形
增塑成形
浆料成形
模压成形 三轴压制 等静压成形 高能成形 挤压成形 扎膜成形 楔形压制 注射成形 车坯成形
注浆成形 热压铸成形 流延法成形 压力渗滤 凝胶铸模成形 直接凝固成形
二、压力成形 1、 模压成形
压力成形
增塑成形
挤压成形 扎膜成形 楔形压制 注射成形 车坯成形
浆料成形
二、增塑成形
1、挤压(挤出)成形: 利用压力把具有塑性的粉料通
过模具挤出来成形的,模具的形状就是成形坯体的形状。
单螺杆挤出机示意图
通心粉
➢ 2、轧膜成形(滚压或辊压成形)
将粉体和粘结剂、溶剂等置于置于轧辊上混 炼,使之混合均匀,伴随吹风,溶剂逐步挥发, 形成一层厚膜; 调整轧辊间距, 反复轧制,可制 得薄片坯料。
2、 粉末在压力下的运动行为
成形工艺主要有: 刚性模具中粉末的压制(模压) 弹性封套中粉末的等静压 粉末的板条滚压 粉末的挤压
受力过程的三个阶段
第一阶段:首先粉末颗粒发生重排; 第二阶段:颗粒发生弹塑性变形; 第三阶段:颗粒断裂。
压坯密度与压制压力的关系
在压制过程中,随着压力的增加,粉 体的密度增加、气孔率降低。人们对压 力与密度或气孔率的关系进行了大量的 研究,试图在压力与相对密度之间推导 出定量的数学公式。目前已经提出的压 制压力与压坯密度的定量公式(包括理 论公式和经验公式)有几十种之多,表 中所示为其中一部分。
成形的理论基础 粉末的工艺性能 粉末在压力下的运动行为 成形方法
一、成形的理论基础
1、粉体的堆积与排列
晶胞 BCC
粉末冶金原理简介课件
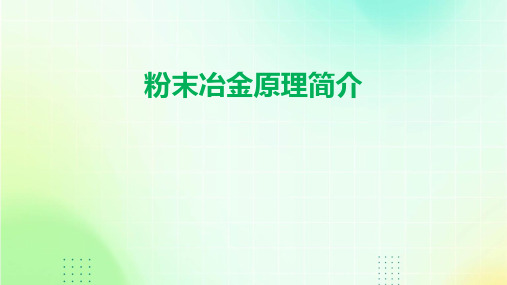
化学共沉淀法
总结词
通过化学反应使金属离子共沉淀形成均匀的金属氧化物或硫化物粉末。
详细描述
化学共沉淀法是一种制备金属粉末的方法,通过化学反应使金属离子共沉淀形成 均匀的金属氧化物或硫化物粉末。在沉淀过程中,控制溶液的pH值和浓度等条 件,使不同金属离子同时沉淀,形成成分均匀的混合物粉末。
喷雾干燥法
定义
粉末烧结是一种通过加热使粉末颗粒 间发生粘结,从而将它们转化为致由烧结和压制烧结。
烧结原理与过程
原理
烧结过程中,粉末颗粒通过表面扩散、粘性流动和塑性变形等机制相互粘结, 形成连续的固体结构。
过程
烧结过程通常包括加热、保温和冷却三个阶段,其中保温阶段是粉末颗粒粘结 的主要阶段。
能源领域
粉末冶金多孔材料可用于制造 燃料电池电极、核反应堆控制 棒等能源相关领域。
医疗器械
粉末冶金材料具有生物相容性 和耐腐蚀性,适用于医疗器械 制造,如人工关节、牙科植入
物等。
粉末冶金的发展历程
01
02
03
早期发展
粉末冶金起源于古代金属 加工技术,如青铜器时代 的铜合金制造。
20世纪发展
随着科技的发展,粉末冶 金在20世纪得到了广泛研 究和应用,涉及领域不断 扩大。
05
粉末冶金材料性能
力学性能
高强度和硬度
粉末冶金材料通过细晶强 化等手段,表现出较高的 硬度和强度,能够满足各 种复杂工况的需求。
良好的耐磨性
由于粉末冶金材料的晶粒 细小且均匀,其耐磨性优 于传统铸造和锻造材料。
抗疲劳性能
由于材料的内部结构均匀 ,可以有效抵抗疲劳裂纹 的扩展,提高零件的寿命 。
特点
粉末冶金具有能够制备传统熔炼 方法难以制备的合金、材料纯度 高、材料性能可调范围广、节能 环保等优点。
粉末冶金学(全套课件325P)

粉末冶金的特点(续2)
1)高合金粉末冶金材料的性能比熔 铸法生产的好。 2)生产难熔金属材料或制品,一般 要依靠粉末冶金法,如钨、钼等 难熔金属。
粉末冶金的不足之处: 粉末成本高 粉末冶金制品的大小和形状受到一定的限制 烧结零件的韧性较差 但是,随着粉末冶金技术的发展,这些问 题正在逐步解决中,例如,等静压成形技术已 能压制较大的和异形的制品;粉末冶金锻造技 术已能使粉末冶金材料的韧性大大提高等等。
0-7 粉末冶金专家—黄培云1
粉末冶金专家—黄培云2 技术职称 : 教授 院 士 : 中国工程院院士 出生日期 : 1917-08-23 出生地点 : 福建 福州 专业领域 : 金属材料 ; 粉末冶金 外 语 : 英语 ; 德语 ; 俄语 ; 日语 通讯地址 : 湖南省长沙市中南工业大学 工作单位: 中南工业大学 职 务: 学术顾问
学和力学性能。
0-3 粉末冶金发展历史 公元3000年前,埃及人已经使用铁粉 公元300年,印度德里铁柱是用大约 6.5t 还原铁粉制成的。 19世纪初,为制铂,粉冶重焕青春 20世纪初,粉末冶金制取W 20世纪40年代,欧洲开始生产Fe粉 汽车工业推动了现代粉末冶金技术的进步 新材料新工艺—金属陶瓷、弥散强化材料、 高速钢、超合金
粉末冶金专家 学 历: —黄培云3
时 间: 1934-1938 学 校: 清华大学 所获学位: 学士 国 别: 中国 时 间: 1941-1945 学 校: 麻省理工学院 所获学位: 科学博士 国 别: 美国
粉末冶金专家—黄培云4
我国粉末冶金学科的主要创始人之一。
创立了著名的粉末压制理论和烧结理论。研制成 功多种用于核、航天、航空、电子等领域的粉末冶 金材料。
粉末冶金专家—黄培云7
粉末冶金原理

粉末冶金原理粉末冶金是一种利用金属粉末或者金属粉末与非金属粉末混合后,再经过压制和烧结等工艺制造金属零件的方法。
在粉末冶金工艺中,粉末的特性和原理起着至关重要的作用。
粉末冶金原理主要包括粉末的制备、成型、烧结和后处理等几个方面。
首先,粉末的制备是粉末冶金的第一步。
金属粉末的制备可以通过机械研磨、化学方法和物理方法等多种途径。
机械研磨是指将金属块或者金属棒经过研磨机械的加工,得到所需的金属粉末。
化学方法则是通过化学反应得到金属粉末,而物理方法则是通过物理手段如电解、喷雾等得到金属粉末。
在粉末冶金中,粉末的制备质量直接影响着最终制品的质量和性能。
其次,成型是指将金属粉末进行成型工艺,使其成为所需形状的工件。
成型方法包括压制成型、注射成型、挤压成型等多种方式。
压制成型是将金属粉末放入模具中,再经过压制机械的加工,使其成为所需形状的工件。
注射成型则是将金属粉末与粘结剂混合后,通过注射成型机械将其注射成型。
挤压成型是将金属粉末放入容器中,再通过挤压机械的作用,使其成为所需形状的工件。
成型工艺的精密度和成型质量对于最终产品的质量和性能至关重要。
接下来,烧结是粉末冶金中的关键工艺。
烧结是指将成型后的金属粉末在高温下进行加热处理,使其颗粒间发生结合,形成致密的金属材料。
烧结工艺的温度、压力和时间等参数对于最终产品的致密度、硬度和耐磨性等性能有着重要影响。
最后,后处理是指对烧结后的金属制品进行表面处理、热处理和精加工等工艺。
表面处理可以提高金属制品的耐腐蚀性和美观度,热处理可以改善金属制品的硬度和强度,精加工则可以提高金属制品的精度和表面质量。
总之,粉末冶金原理是一个复杂而又精密的工艺体系,涉及到材料科学、机械工程、化学工程等多个领域的知识。
通过对粉末的制备、成型、烧结和后处理等环节的深入研究和探索,可以不断提高粉末冶金工艺的精度和效率,为制造业的发展和进步提供更加可靠的技术支持。
粉末冶金原理中文ppt课件
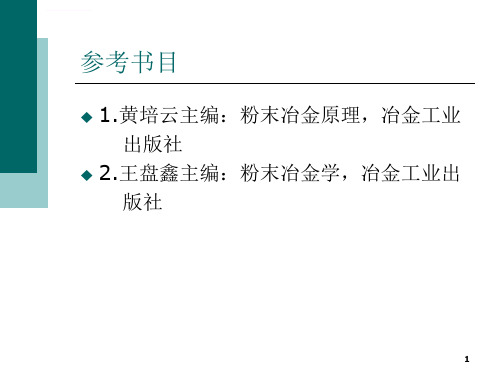
参考书目
1.黄培云主编:粉末冶金原理,冶金工业 出版社
2.王盘鑫主编:粉末冶金学,冶金工业出 版社
1
经 营 者 提 供 商品或 者服务 有欺诈 行为的 ,应当 按照消 费者的 要求增 加赔偿 其受到 的损失 ,增加 赔偿的 金额为 消费者 购买商 品的价 款或接 受服务 的费用
9
经 营 者 提 供 商品或 者服务 有欺诈 行为的 ,应当 按照消 费者的 要求增 加赔偿 其受到 的损失 ,增加 赔偿的 金额为 消费者 购买商 品的价 款或接 受服务 的费用
绪论
➢ 粉末冶金材料和制品的发展方向 ➢ 1、具有代表性的铁基合金,将向大体积的精密制品,高
质量的结构零部件发展。 ➢ 2、制造具有均匀显微组织结构的、加工困难而完全致密
4
经 营 者 提 供 商品或 者服务 有欺诈 行为的 ,应当 按照消 费者的 要求增 加赔偿 其受到 的损失 ,增加 赔偿的 金额为 消费者 购买商 品的价 款或接 受服务 的费用
绪论
粉末冶金工艺的基本工序 1、原料粉末的制备。现有的制粉方法大体可分为两类:
机械法和物理化学法。其中机械法又可分为:机械粉碎和 雾化法;物理化学法又分为:电化腐蚀法、还原法、化合 法、还原-化合法、气相沉积法、液相沉积法以及电解法。 其中应用最为广泛的是还原法、雾化法和电解法。
绪论
1.粉末冶金——是一种利用制取到的金属粉末,或金属粉末与非金 属粉末的混合物作为原料,经过粉末成形和烧结制造金属材料、 复合材料以及各类型制品的工艺过程。粉末冶金法与生产陶瓷有 相似的地方,因此也叫金属陶瓷法。
- 1、下载文档前请自行甄别文档内容的完整性,平台不提供额外的编辑、内容补充、找答案等附加服务。
- 2、"仅部分预览"的文档,不可在线预览部分如存在完整性等问题,可反馈申请退款(可完整预览的文档不适用该条件!)。
- 3、如文档侵犯您的权益,请联系客服反馈,我们会尽快为您处理(人工客服工作时间:9:00-18:30)。
6.1.1 等静压压制的基本原理
(1)压力分布与摩擦力对压坯密度分布的影响 根据流体力 学的原理,压力泵压入钢筒密闭容器内的流体介质,其压强 大小不变并均匀地向各个方向传递。 (2)压制压力与压坯密度的关系 通常,粉末在钢模压制时 常用图6-4所示的曲线定性地描述压制压力与压坯密度的关 系。
6.1.1 等静压压制的基本原理
1.粉浆浇注基本工艺
图6-20 粉浆浇注工艺原理图 a)组合石膏模 b)粉浆浇注入模
c)吸收粉浆水分 d)成形注件
1.粉浆浇注基本工艺
图6-21 粉浆浇注工艺流程图
(2)石膏模具的制造
图6-22 石膏粉粒度与模具吸水能力的关系
2.影响粉浆浇注成形的因素
(1)粉末的粒度 (2)液固比 液固比是指液体与金属粉末的质量比。 (3)粉浆pH值的影响 粉浆pH值的改变直接影响其黏度值和 粉末颗粒的下沉速度。 (4)分散剂及黏结剂的影响 以藻肮酸钠作为分散剂时,其 含量明显地影响粉浆中粉末颗粒的沉降速度。 (5)粉末吸附气体的量的影响 配制粉浆时由于粉末颗粒表 面吸附一层气体而阻碍母液对粉末表面的润湿,浇注时可能 造成气泡及颗粒分布不均等现象,导致注坯质量降低。
2.脱蜡-烧结-热等静压
1)确定合理的烧结压力、温度及时间参数。 2)确定热等静压最大压力、温度及时间。
2.脱蜡-烧结-热等静压
图6-16 烧结-热等静压压制工艺 过程示意图
3.准等静压
图6-18 准等静压工艺过程 a)热石墨粒装模 b)用机械手把热的预成形坯插入石墨粒中 c)用水压机冲头加压 d)清理模具,石墨粒返回再循环使用,取出压坯
图6-1 等静压制原理图 1—排气阀 2—压紧螺母 3—盖顶 4—密封圈 5—高压容器 6—橡皮塞 7—模套 8—压制料 9—压力介质入口
(1)压力分布与摩擦力对压坯密度分布的影响
图6-2 单向和双向压制的压坯密度分布示意图 a)单向压制 b)双向压制
(2)压制压力与压坯密度的关系
图6-3 在等静压下不同直径压坯的密度分布
表6-3 热等静压法与热压法压制制品密度比较
1.热等静压
表6-4 混合粉经热等静压处理得到的Ni-TiC化合物的性质
1.热等静压
图6-14 一种典型的消除碳化物结构中微孔的 热等静压工艺流程
1.热等静压
图6-15 两种分别经过传统的热等静压处理和快速热等静压处理的铁基压坯 a)传统热等静压处理 b)快速热等静压处理
表6-5 不同粒度的不锈钢粉末的最佳液固比
(4)分散剂及黏结剂的影响
图6-23 粉浆的pH值与其粘度的关系 1—粉浆相对密度3.87±0.01,液/固=0.18 2—粉浆相对密度3.79±0.01,液/固=0.19 3—粉浆相对密度3.72±0.01,液/固=0.196
(4)分散剂及黏结ห้องสมุดไป่ตู้的影响
(2)压制压力与压坯密度的关系
图6-5 铜粉水静压制数据的双对数方程图
6.1.2 冷等静压压制
1.湿袋式模具压制 2.干袋式模具压制
1.湿袋式模具压制
图6-7 湿袋式模具压制 1—排气塞 2—压紧螺母 3—压力塞 4—金属密封圈
5—橡皮塞 6—软模 7—穿孔金属套 8—粉末料 9—高压容器 10—高压液体 11—棉花
3.准等静压
图6-19 通过加热和加压小球对装有粉末预成形坯施加准等静压的压制过程
6.2 粉末无压成形
6.2.1 粉浆浇注 6.2.2 冻干铸造法 6.2.3 喷射成形
6.2.1 粉浆浇注
1.粉浆浇注基本工艺 2.影响粉浆浇注成形的因素
1.粉浆浇注基本工艺
(1)粉浆的制取 粉浆是由金属粉末(或金属纤维、陶瓷粉末) 与母液构成的。 (2)石膏模具的制造 一般可按通常的石膏模制造工艺来制 造,但应当重视石膏粉的粒度及其组成。 (3)浇注 为了防止浇注物黏结在石膏模上,浇注前应将涂 料喷涂到石膏模壁上,这种涂料通常称为离型剂,常用的离 型剂有硅油。 (4)干燥 粉浆注入石膏模后,静置一段时间,石膏模即可 吸去粉浆中的液体。
1.热等静压 2.脱蜡-烧结-热等静压 3.准等静压 4.反应性热等静压
6.1.4 热等静压成形
图6-12 热等静压的工艺流程原理图
6.1.4 热等静压成形
图6-13 热等静压制原理 1—压力容器 2—气体压力介质
3—压坯 4—包套 5—加热炉
1.热等静压
表6-2 热等静压制工艺得到的一些材料的密度值
第6章 特殊成形技术
6.1 等静压成形 6.2 粉末无压成形 6.3 粉末挤压成形 6.4 粉末热压成形 6.5 粉末注射成形 6.6 温压成形 6.7 粉末连续成形 6.8 粉末锻造成形 6.9 其他成形技术
6.1 等静压成形
6.1.1 6.1.2 6.1.3 6.1.4
等静压压制的基本原理 冷等静压压制 冷等静压成形工艺 热等静压成形
2.干袋式模具压制
图6-9 干袋式模具压制方式 1—上顶盖 2—螺栓 3—筒体 4—上垫 5—密封垫 6—密封圈 7—套板 8—干袋
9—模芯 10—粉末
2.干袋式模具压制
表6-1 某些弹塑性材料的性质
表6-1 某些弹塑性材料的性质
6.1.3 冷等静压成形工艺
图6-11 冷等静压湿袋工艺
6.1.4 热等静压成形
表6-6 藻肮酸钠与聚乙烯醇配比对不锈钢粉末沉降速度的影响
(5)粉末吸附气体的量的影响
图6-25 浇注法工艺流程图
(5)粉末吸附气体的量的影响
图6-26 流涎法制备构件
6.2.3 喷射成形
1.液体喷射 2.等离子喷射
1.液体喷射
(1)喷射沉积成形工艺的原理及特点 喷射沉积成形是将喷 射沉积与成形技术结合起来将金属或合金加工成半成品或成 品的新工艺。 (2)喷射沉积成形工艺 喷射沉积成形技术根据不同的加工 方式可分为喷射轧制、喷射锻造、离心喷射沉积及喷射涂层 四种。
1.液体喷射
图6-27 喷射成形的装置
(1)喷射沉积成形工艺的原理及特点
图6-28 喷射沉积成形工艺过程图 1—熔融金属 2—熔埚(坩埚) 3—Osprey气体喷嘴 4—沉积物 5—转动轴 6—转动轴套 7—多余的雾化微料
8—旋流器 9—动力矩
(2)喷射沉积成形工艺
1)喷射轧制成形的工艺过程如图6-31所示。 2)喷射锻造是喷射成形领域中较早期发展的工艺之一,其工 艺过程如图6-32所示。 3)离心喷射沉积的工艺过程如图6-33所示。 4)喷射涂层工艺过程如图6-34所示。