三段一闭路破碎工艺流程解析
破碎流程的计算步骤及方法小结
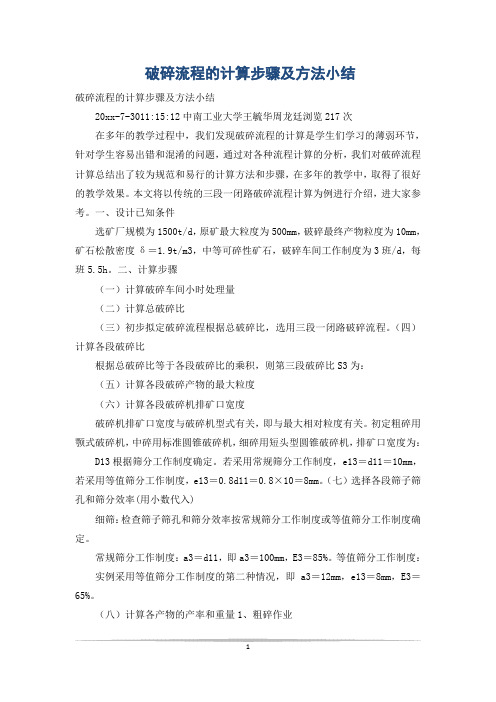
破碎流程的计算步骤及方法小结破碎流程的计算步骤及方法小结20xx-7-3011:15:12中南工业大学王毓华周龙廷浏览217次在多年的教学过程中,我们发现破碎流程的计算是学生们学习的薄弱环节,针对学生容易出错和混淆的问题,通过对各种流程计算的分析,我们对破碎流程计算总结出了较为规范和易行的计算方法和步骤,在多年的教学中,取得了很好的教学效果。
本文将以传统的三段一闭路破碎流程计算为例进行介绍,进大家参考。
一、设计已知条件选矿厂规模为1500t/d,原矿最大粒度为500mm,破碎最终产物粒度为10mm,矿石松散密度δ=1.9t/m3,中等可碎性矿石,破碎车间工作制度为3班/d,每班5.5h。
二、计算步骤(一)计算破碎车间小时处理量(二)计算总破碎比(三)初步拟定破碎流程根据总破碎比,选用三段一闭路破碎流程。
(四)计算各段破碎比根据总破碎比等于各段破碎比的乘积,则第三段破碎比S3为:(五)计算各段破碎产物的最大粒度(六)计算各段破碎机排矿口宽度破碎机排矿口宽度与破碎机型式有关,即与最大相对粒度有关。
初定粗碎用颚式破碎机,中碎用标准圆锥破碎机,细碎用短头型圆锥破碎机,排矿口宽度为: D13根据筛分工作制度确定。
若采用常规筛分工作制度,e13=d11=10mm,若采用等值筛分工作制度,e13=0.8d11=0.8×10=8mm。
(七)选择各段筛子筛孔和筛分效率(用小数代入)细筛:检查筛子筛孔和筛分效率按常规筛分工作制度或等值筛分工作制度确定。
常规筛分工作制度:a3=d11,即a3=100mm,E3=85%。
等值筛分工作制度:实例采用等值筛分工作制度的第二种情况,即a3=12mm,e13=8mm,E3=65%。
(八)计算各产物的产率和重量1、粗碎作业式中:β1-为原矿中小于100mm的粒级含量(用小数代入)。
粗筛筛孔与原矿最大粒度的比值Z1==0.2,从选矿设计手册中图6.3-2,查中等可碎性矿石,得β1=0.31=31%。
破碎的工艺流程
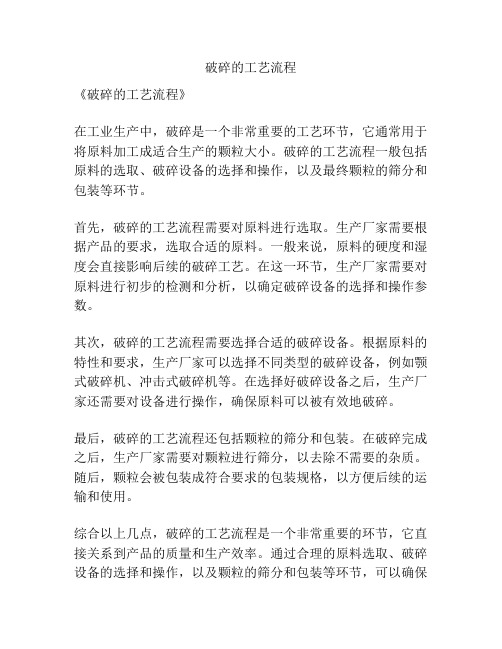
破碎的工艺流程
《破碎的工艺流程》
在工业生产中,破碎是一个非常重要的工艺环节,它通常用于将原料加工成适合生产的颗粒大小。
破碎的工艺流程一般包括原料的选取、破碎设备的选择和操作,以及最终颗粒的筛分和包装等环节。
首先,破碎的工艺流程需要对原料进行选取。
生产厂家需要根据产品的要求,选取合适的原料。
一般来说,原料的硬度和湿度会直接影响后续的破碎工艺。
在这一环节,生产厂家需要对原料进行初步的检测和分析,以确定破碎设备的选择和操作参数。
其次,破碎的工艺流程需要选择合适的破碎设备。
根据原料的特性和要求,生产厂家可以选择不同类型的破碎设备,例如颚式破碎机、冲击式破碎机等。
在选择好破碎设备之后,生产厂家还需要对设备进行操作,确保原料可以被有效地破碎。
最后,破碎的工艺流程还包括颗粒的筛分和包装。
在破碎完成之后,生产厂家需要对颗粒进行筛分,以去除不需要的杂质。
随后,颗粒会被包装成符合要求的包装规格,以方便后续的运输和使用。
综合以上几点,破碎的工艺流程是一个非常重要的环节,它直接关系到产品的质量和生产效率。
通过合理的原料选取、破碎设备的选择和操作,以及颗粒的筛分和包装等环节,可以确保
生产出符合要求的产品。
因此,生产厂家需要在破碎的工艺流程中加强管理和控制,以提高生产效率和产品质量。
黄金选矿中的分段式破碎流程简介
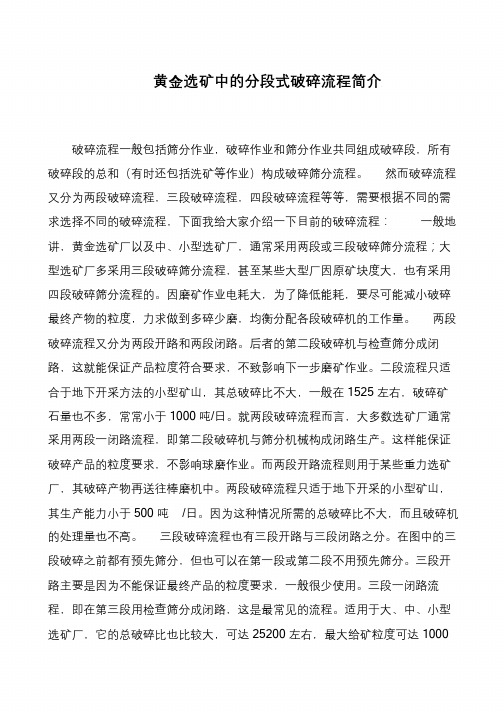
书山有路勤为径,学海无涯苦作舟黄金选矿中的分段式破碎流程简介破碎流程一般包括筛分作业,破碎作业和筛分作业共同组成破碎段,所有破碎段的总和(有时还包括洗矿等作业)构成破碎筛分流程。
然而破碎流程又分为两段破碎流程,三段破碎流程,四段破碎流程等等,需要根据不同的需求选择不同的破碎流程,下面我给大家介绍一下目前的破碎流程:一般地讲,黄金选矿厂以及中、小型选矿厂,通常采用两段或三段破碎筛分流程;大型选矿厂多采用三段破碎筛分流程,甚至某些大型厂因原矿块度大,也有采用四段破碎筛分流程的。
因磨矿作业电耗大,为了降低能耗,要尽可能减小破碎最终产物的粒度,力求做到多碎少磨,均衡分配各段破碎机的工作量。
两段破碎流程又分为两段开路和两段闭路。
后者的第二段破碎机与检查筛分成闭路,这就能保证产品粒度符合要求,不致影响下一步磨矿作业。
二段流程只适合于地下开采方法的小型矿山,其总破碎比不大,一般在1525 左右,破碎矿石量也不多,常常小于1000 吨/日。
就两段破碎流程而言,大多数选矿厂通常采用两段一闭路流程,即第二段破碎机与筛分机械构成闭路生产。
这样能保证破碎产品的粒度要求,不影响球磨作业。
而两段开路流程则用于某些重力选矿厂,其破碎产物再送往棒磨机中。
两段破碎流程只适于地下开采的小型矿山,其生产能力小于500 吨/日。
因为这种情况所需的总破碎比不大,而且破碎机的处理量也不高。
三段破碎流程也有三段开路与三段闭路之分。
在图中的三段破碎之前都有预先筛分,但也可以在第一段或第二段不用预先筛分。
三段开路主要是因为不能保证最终产品的粒度要求,一般很少使用。
三段一闭路流程,即在第三段用检查筛分成闭路,这是最常见的流程。
适用于大、中、小型选矿厂,它的总破碎比也比较大,可达25200 左右,最大给矿粒度可达1000。
破碎工艺流程

破碎工艺流程
《破碎工艺流程》
破碎工艺流程是指将原材料通过不同的破碎设备进行破碎处理,以达到所需的颗粒度和形状的工艺过程。
破碎工艺流程广泛应用于矿山、建筑、化工等行业,是生产过程中不可或缺的工艺环节。
破碎工艺流程的主要设备包括颚式破碎机、冲击式破碎机、圆锥破碎机、锤式破碎机等。
不同的原材料需要选择不同的破碎设备进行处理,比如对于硬度较高的石灰石、花岗岩等硬性材料,通常会选择颚式破碎机进行初步破碎;对于颗粒度要求较高、形状要求较好的材料,则会选择冲击式破碎机进行细碎。
破碎工艺流程的具体流程包括原料的进料、初次破碎、筛分、再次破碎等环节。
在整个流程中,需要根据不同原材料的特性和要求,合理选择破碎设备,并确保设备的正常运转和维护,以保证产量和产品质量。
破碎工艺流程的优化可以提高生产效率、降低能耗、提高产品质量和降低生产成本,因此在实际生产中,对破碎工艺流程的优化是非常重要的一环。
通过对原材料进行科学合理的破碎处理,可以有效提高原料的利用率,降低成本,提高产品的市场竞争力。
总之,破碎工艺流程是生产过程中不可或缺的环节,合理选择
破碎设备并优化破碎工艺流程,对于提高生产效率、降低成本、提高产品质量都具有重要意义。
破碎流程的选择和计算
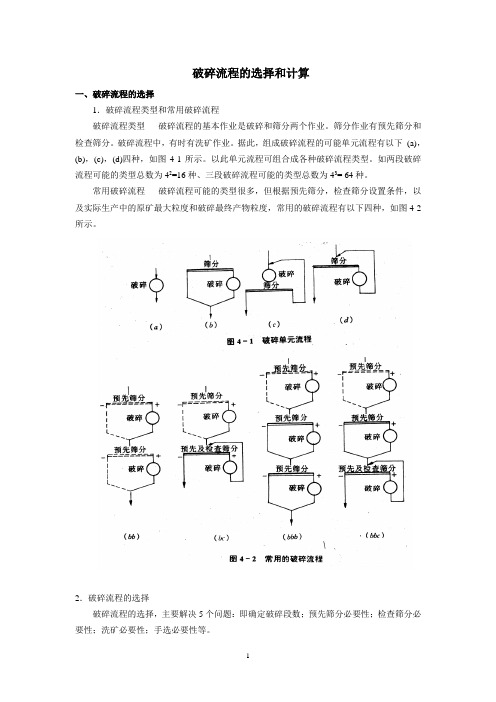
破碎流程的选择和计算一、破碎流程的选择1.破碎流程类型和常用破碎流程破碎流程类型破碎流程的基本作业是破碎和筛分两个作业。
筛分作业有预先筛分和检查筛分。
破碎流程中,有时有洗矿作业。
据此,组成破碎流程的可能单元流程有以下(a),(b),(c),(d)四种,如图4-1所示。
以此单元流程可组合成各种破碎流程类型。
如两段破碎流程可能的类型总数为42=16种、三段破碎流程可能的类型总数为43= 64种。
常用破碎流程破碎流程可能的类型很多,但根据预先筛分,检查筛分设置条件,以及实际生产中的原矿最大粒度和破碎最终产物粒度,常用的破碎流程有以下四种,如图4-2 所示。
2.破碎流程的选择破碎流程的选择,主要解决5个问题:即确定破碎段数;预先筛分必要性;检查筛分必要性;洗矿必要性;手选必要性等。
(1) 破碎段数的确定。
破碎段数取决于原矿最大粒度与破碎最终产物粒度,即取决总破碎比(S)。
总破碎比等于原矿最大粒度(D)除以破碎最终产物粒度 (d)。
即dDS(4-5) (2) 预先筛分的必要性。
水分在破碎时的有害程度,视矿石中矿泥含量而定。
当矿石含泥多,水分高师,采用预先筛分可以减少破碎机的堵塞现象。
生产实践证明,大多数情况下,原矿中均含有一定数量的细粒物料,特别是易碎性矿石,其细粒含量较多,如图4-3所示。
粗碎、中碎排矿产物中,其细粒含量更多,破碎产物的粒度特性曲线总是呈凹型的,如图4-4到图4-9所示。
所以,粗碎、中碎、细碎前的预先筛分总是有利的。
破碎机排矿产物中最大粒度与排矿口宽度之比,称为最大相对粒度Z max 。
排矿产物中,大于排矿口宽度的过大颗粒含量β(%)与最大相对粒度Z max ,如表4-4所示。
表4-4 破碎机排矿产物中过大颗粒含量β(%)与最大相对粒度Z max*闭路时取小值,开路时取大值。
二、破碎流程的计算1. 计算的内容、目的及原理计算内容在破碎筛分作业中,只考虑矿石粒度和粒度组成的变化,不考虑品位和回收率的变化(洗矿、手选除外)。
解析有色金属的选矿流程

解析有色金属的选矿流程有色金属矿的选矿工艺因矿物的可选性能而各异,一般原则流程为破碎筛分-磨矿分级-浮选。
对于向各大有色金属矿石提供球磨机钢球的生产厂家来说,有必要让销售员了解有色金属的选矿流程,才能够为矿山球磨机制定出更加合理的配球方案。
铜、铅、锌矿石,均需经过选矿厂处理,精选出符合有色金属冶炼需要的铜、铅、锌精矿产品。
铝土矿不需进行选矿加工而直接供给氧化铝厂的原料车间配料后,进入氧化铝生产流程。
福山铜矿牙山矿区选矿厂的工艺流程是,破碎采用三段一闭路流程。
磨矿采用一段闭路流程,浮选工艺流程是一次粗选,二次精选,二次扫选,中矿循序返回流程。
精选产品为铜精矿。
孔辛头矿区选矿厂破碎部分采用三段一闭路流程。
磨矿部分采用一段一闭路流程,中矿循序返回流程。
浮选工艺是一粗一精一扫。
浮选产品为铜精矿,浮选尾矿经磁选得铁精矿。
该选厂1972年改为选钼,将浮选工艺改造为一粗二精三扫,选出铜钼混合精矿,经过再磨进入一粗七精二扫分离浮选流程,精选产品为钼精矿,精选尾矿为铜精矿。
香夼铅锌矿铅锌选矿厂,破碎部分采用两段一闭路洗矿破碎流程,即在两段破碎之间设圆筒洗矿机脱泥。
磨矿系统为一段一闭路流程。
浮选工艺流程为铜铅和锌硫分别混合浮选后再行分离的部分混合浮选。
铜铅混合浮选流程为一次粗选三次精选三次扫选,得到铜铅混合精矿。
铜铅分离浮选工艺为一次粗选一次精选二次扫选,分离浮选产品为铜精矿和铅精矿。
在铜铅分离浮选作业中采用了以硫代硫酸钠和硫酸亚铁代替氰化物药剂,实现了无氰化物选矿,消除了公害,也改善了选矿指标。
金岭铁矿和莱芜铁矿的两座铁矿选矿厂,因铁矿原矿石含有伴生的铜钴元素可供综合利用,在选矿工艺中设置了浮选工艺流程,综合回收铜和钴,其产品为铜精矿、钴硫精矿和铜钴混合精矿,是山东铜、钴精矿的主要产地。
三段一闭路破碎工艺流程.
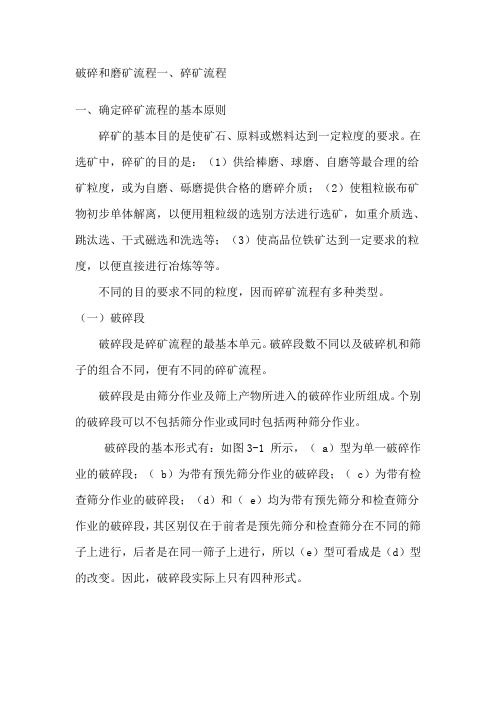
破碎和磨矿流程一、碎矿流程一、确定碎矿流程的基本原则碎矿的基本目的是使矿石、原料或燃料达到一定粒度的要求。
在选矿中,碎矿的目的是:(1)供给棒磨、球磨、自磨等最合理的给矿粒度,或为自磨、砾磨提供合格的磨碎介质;(2)使粗粒嵌布矿物初步单体解离,以便用粗粒级的选别方法进行选矿,如重介质选、跳汰选、干式磁选和洗选等;(3)使高品位铁矿达到一定要求的粒度,以便直接进行冶炼等等。
不同的目的要求不同的粒度,因而碎矿流程有多种类型。
(一)破碎段破碎段是碎矿流程的最基本单元。
破碎段数不同以及破碎机和筛子的组合不同,便有不同的碎矿流程。
破碎段是由筛分作业及筛上产物所进入的破碎作业所组成。
个别的破碎段可以不包括筛分作业或同时包括两种筛分作业。
破碎段的基本形式有:如图3-1 所示,( a)型为单一破碎作业的破碎段;( b)为带有预先筛分作业的破碎段;( c)为带有检查筛分作业的破碎段;(d)和( e)均为带有预先筛分和检查筛分作业的破碎段,其区别仅在于前者是预先筛分和检查筛分在不同的筛子上进行,后者是在同一筛子上进行,所以(e)型可看成是(d)型的改变。
因此,破碎段实际上只有四种形式。
二段以上的破碎流程是不同破碎段的形式的各种组合,故有许多可能的方案。
但是,合理的破碎流程,可以根据需要的破碎段数,以及应用预先筛分和检查筛分的必要性等加以确定。
(二)破碎段数的确定需要的破碎段数取决于原矿的最大粒度,要求的最终破碎产物粒度,以及各破碎段所能达到的破碎比,即取决于要求的总破碎比及各段破碎比。
原矿中的最大粒度与矿石的赋存条件、矿山规模、采矿方法、原矿的运输装卸方式等有关。
露天开采时,主要取决于矿山规模和装矿电铲的容积,一般500~1300 毫米。
井下开采时,主要取决于矿山规模和采矿方法,一般为300~600 毫米。
破碎的最终产物粒度视破碎的目的而不同。
如自磨机的给矿要求!%%& $%% 毫米,进行高炉冶炼的富铁矿的粒度分为500~1300 毫米的两级,棒磨机的合理给矿粒度为300~600 毫米,球磨机合理给矿粒度为300~500毫米。
破碎工艺流程

破碎工艺流程破碎工艺流程是矿石粉碎过程中的重要环节,其作用是将矿石进行碎石,以便进行后续的分选和提炼工作。
下面将介绍一下破碎工艺流程的基本步骤及其各个环节的作用。
首先,矿石经过采矿车辆运输至破碎厂,然后进入破碎机。
破碎机是破碎工艺流程中最重要的设备之一,其作用是将矿石进行粗碎。
矿石进入破碎机后,经过破碎器的旋转锤头或挠性锤片的连续撞击和碰撞,使得矿石分裂、破碎成较小的颗粒。
这些碎石经过排料装置排出破碎机。
接下来,碎石进入振动筛选设备进行筛选。
振动筛选设备采用机械振动方法,使得不同粒度的碎石能够根据其尺寸大小分层排列。
通过筛网的振动,较小的碎石通过筛孔排出,而较大的碎石则被挡在筛网上。
然后,筛选后的碎石进入细碎机。
细碎机的作用是将筛选后的较大的碎石进行进一步的细碎。
在细碎机中,碎石被高速旋转的刀片或者辊子撞击、破碎成更小的砂粒或粉末。
细碎机中的破碎粒度一般比破碎机更小,可以满足不同工艺过程的要求。
最后,细碎后的砂粒或粉末经过磨机进行进一步的磨细。
磨机主要利用研磨介质(如砂、水或钢球等)对砂粒或粉末进行摩擦、碰撞和磨破,从而使其尺寸更细。
磨机通常设有排料装置,将研磨后的细料排出机器。
总的来说,破碎工艺流程主要包括粗碎、筛选、细碎和磨细四个环节。
通过破碎工艺流程的处理,矿石可以被分解成各种粒度的碎石,为后续的分选、提炼和加工提供了便利。
此外,不同的矿石在破碎工艺流程中可能还涉及到其他的处理环节,如洗选、磁选等,以满足特定工艺要求。
需要注意的是,在破碎工艺流程中,破碎机、振动筛选设备、细碎机和磨机等设备的选择和设计应根据矿石的性质和要求来确定。
同时,工艺流程中的操作和设备的维护保养也是非常重要的,可以提高破碎效率,降低能耗,延长设备使用寿命。
总的来说,破碎工艺流程是矿石处理中不可或缺的一环,其步骤包括粗碎、筛选、细碎和磨细等环节,以达到破碎矿石、分选和提炼的目的。
在实践应用中,需要根据矿石的性质和要求来选择和设计相应的设备,并进行合理的操作和维护保养。
磷矿选矿工艺流程
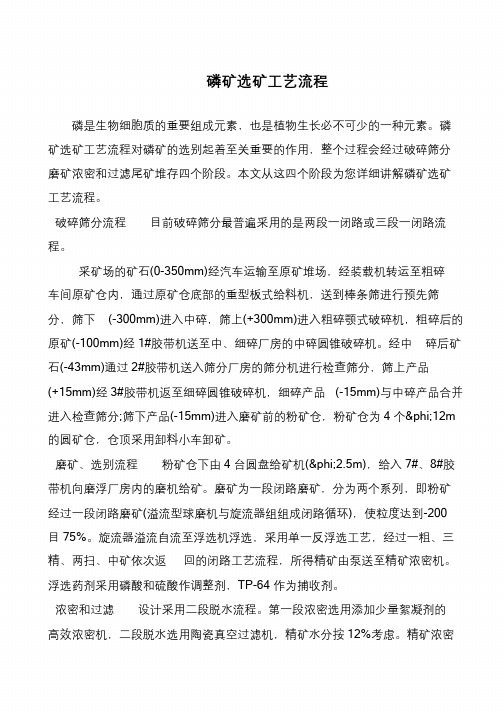
书山有路勤为径,学海无涯苦作舟磷矿选矿工艺流程磷是生物细胞质的重要组成元素,也是植物生长必不可少的一种元素。
磷矿选矿工艺流程对磷矿的选别起着至关重要的作用,整个过程会经过破碎筛分磨矿浓密和过滤尾矿堆存四个阶段。
本文从这四个阶段为您详细讲解磷矿选矿工艺流程。
破碎筛分流程目前破碎筛分最普遍采用的是两段一闭路或三段一闭路流程。
采矿场的矿石(0-350mm)经汽车运输至原矿堆场,经装载机转运至粗碎车间原矿仓内,通过原矿仓底部的重型板式给料机,送到棒条筛进行预先筛分,筛下(-300mm)进入中碎,筛上(+300mm)进入粗碎颚式破碎机,粗碎后的原矿(-100mm)经1#胶带机送至中、细碎厂房的中碎圆锥破碎机。
经中碎后矿石(-43mm)通过2#胶带机送入筛分厂房的筛分机进行检查筛分,筛上产品(+15mm)经3#胶带机返至细碎圆锥破碎机,细碎产品(-15mm)与中碎产品合并进入检查筛分;筛下产品(-15mm)进入磨矿前的粉矿仓,粉矿仓为4 个φ12m 的圆矿仓,仓顶采用卸料小车卸矿。
磨矿、选别流程粉矿仓下由4 台圆盘给矿机(φ2.5m),给入7#、8#胶带机向磨浮厂房内的磨机给矿。
磨矿为一段闭路磨矿,分为两个系列,即粉矿经过一段闭路磨矿(溢流型球磨机与旋流器组组成闭路循环),使粒度达到-200 目75%。
旋流器溢流自流至浮选机浮选,采用单一反浮选工艺,经过一粗、三精、两扫、中矿依次返回的闭路工艺流程,所得精矿由泵送至精矿浓密机。
浮选药剂采用磷酸和硫酸作调整剂,TP-64 作为捕收剂。
浓密和过滤设计采用二段脱水流程。
第一段浓密选用添加少量絮凝剂的高效浓密机,二段脱水选用陶瓷真空过滤机,精矿水分按12%考虑。
精矿浓密。
三段一闭路破碎工艺流程

破碎和磨矿流程一、碎矿流程一、确定碎矿流程的基本原则碎矿的基本目的是使矿石、原料或燃料达到一定粒度的要求。
在选矿中,碎矿的目的是:(1)供给棒磨、球磨、自磨等最合理的给矿粒度,或为自磨、砾磨提供合格的磨碎介质;(2)使粗粒嵌布矿物初步单体解离,以便用粗粒级的选别方法进行选矿,如重介质选、跳汰选、干式磁选和洗选等;(3)使高品位铁矿达到一定要求的粒度,以便直接进行冶炼等等。
不同的目的要求不同的粒度,因而碎矿流程有多种类型。
(一)破碎段破碎段是碎矿流程的最基本单元。
破碎段数不同以及破碎机和筛子的组合不同,便有不同的碎矿流程。
破碎段是由筛分作业及筛上产物所进入的破碎作业所组成。
个别的破碎段可以不包括筛分作业或同时包括两种筛分作业。
破碎段的基本形式有:如图3-1 所示,( a)型为单一破碎作业的破碎段;( b)为带有预先筛分作业的破碎段;( c)为带有检查筛分作业的破碎段;(d)和( e)均为带有预先筛分和检查筛分作业的破碎段,其区别仅在于前者是预先筛分和检查筛分在不同的筛子上进行,后者是在同一筛子上进行,所以(e)型可看成是(d)型的改变。
因此,破碎段实际上只有四种形式。
二段以上的破碎流程是不同破碎段的形式的各种组合,故有许多可能的方案。
但是,合理的破碎流程,可以根据需要的破碎段数,以及应用预先筛分和检查筛分的必要性等加以确定。
(二)破碎段数的确定需要的破碎段数取决于原矿的最大粒度,要求的最终破碎产物粒度,以及各破碎段所能达到的破碎比,即取决于要求的总破碎比及各段破碎比。
原矿中的最大粒度与矿石的赋存条件、矿山规模、采矿方法、原矿的运输装卸方式等有关。
露天开采时,主要取决于矿山规模和装矿电铲的容积,一般500~1300 毫米。
井下开采时,主要取决于矿山规模和采矿方法,一般为300~600 毫米。
破碎的最终产物粒度视破碎的目的而不同。
如自磨机的给矿要求!%%& $%% 毫米,进行高炉冶炼的富铁矿的粒度分为500~1300 毫米的两级,棒磨机的合理给矿粒度为300~600 毫米,球磨机合理给矿粒度为300~500毫米。
常用的破碎筛分流程

书山有路勤为径,学海无涯苦作舟常用的破碎筛分流程一般金属矿选矿厂常采用二段或三段破碎筛分流程。
个别大型选矿厂当处理的原矿块度大时有采用四段破碎流程的。
近年来,由于自磨新工艺的日益发展,破碎筛分流程更为简化了。
一段破碎流程当采用自磨机为磨矿设备时,破碎流程可以大大简化,通常是原矿经过一段粗破碎后(粒度达350~0 毫米)就进入自磨机进行磨矿。
如图1 所示。
对于某些非金属矿如石棉、石灰石或硬度很小,节理较发达的金属矿石,采用反击式破碎机或锤碎机时,也可采用一段破碎流程。
两段破碎流程包括两段幵路破碎如图2(b)或两段一闭路破碎如图2(a)流程。
而后者最为常见。
即第二段破碎机与检查筛分构成闭路,这样就能保证破碎产品的粒度合乎要求。
为下一段磨矿作业创造有利条件。
两段破碎流程只适用于地下采矿法的小型矿山,原矿块度200~400 毫米,产品12~30 毫米,总破碎比不大,破碎矿量也不大。
如图3 为我国某铅锌矿选矿厂所采用的两段一闭路破碎流程。
送到选厂的原矿粒度为200~0 毫米,经筛孔尺寸为50 毫米的格筛筛分之后,筛上产物进入第一段破碎机(400 乘以600 毫米的颚式破碎机)。
第一段破碎产物及格筛筛下产物一同进入筛孔为12 毫米的振动筛,进行第二段破碎的预先筛分,筛上产物进入规格为ψ1200 毫米的中型圆锥式破碎机,其排矿再返回振动筛进行检査筛分,筛下产物(12~0 毫米)送磨矿工段。
当选厂生产规模不大,且第一段破碎机生产能力大大富余的情况下,则可以采用第一段不设预先筛分的两段一闭路破碎流程。
两段开路破碎流程只在某些重选厂把破碎产物直接送棒磨磨矿时采用。
三段破碎流程。
破碎的物理学原理与工艺流程
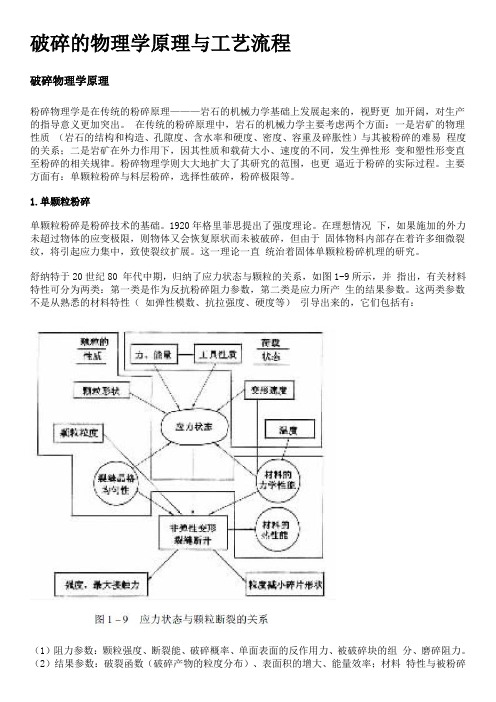
破碎的物理学原理与工艺流程破碎物理学原理粉碎物理学是在传统的粉碎原理———岩石的机械力学基础上发展起来的,视野更加开阔,对生产的指导意义更加突出。
在传统的粉碎原理中,岩石的机械力学主要考虑两个方面:一是岩矿的物理性质(岩石的结构和构造、孔隙度、含水率和硬度、密度、容重及碎胀性)与其被粉碎的难易程度的关系;二是岩矿在外力作用下,因其性质和载荷大小、速度的不同,发生弹性形变和塑性形变直至粉碎的相关规律。
粉碎物理学则大大地扩大了其研究的范围,也更逼近于粉碎的实际过程。
主要方面有:单颗粒粉碎与料层粉碎,选择性破碎,粉碎极限等。
1.单颗粒粉碎单颗粒粉碎是粉碎技术的基础。
1920年格里菲思提出了强度理论。
在理想情况下,如果施加的外力未超过物体的应变极限,则物体又会恢复原状而未被破碎,但由于固体物料内部存在着许多细微裂纹,将引起应力集中,致使裂纹扩展。
这一理论一直统治着固体单颗粒粉碎机理的研究。
舒纳特于20世纪80 年代中期,归纳了应力状态与颗粒的关系,如图1-9所示,并指出,有关材料特性可分为两类:第一类是作为反抗粉碎阻力参数,第二类是应力所产生的结果参数。
这两类参数不是从熟悉的材料特性(如弹性模数、抗拉强度、硬度等)引导出来的,它们包括有:(1)阻力参数:颗粒强度、断裂能、破碎概率、单面表面的反作用力、被破碎块的组分、磨碎阻力。
(2)结果参数:破裂函数(破碎产物的粒度分布)、表面积的增大、能量效率;材料特性与被粉碎物料结构及载荷条件———物料种类、产地和预处理方法;颗粒强度、形状、颗粒的均匀性;载荷强度、载荷速度、载荷次数、施加载荷的工具形状和硬度、湿度等。
舒纳特等人对此进行了较全面的研究,推进了单颗粒粉碎理论的发展。
2.料层粉碎料层粉碎有别于单颗粒粉碎。
单颗粒粉碎是指粒子受到应力作用及发生粉碎事件是各自独立进行的,即不存在粒子间的相互作用。
而料层粉碎是指大量的颗粒相互聚集,彼此接触所形成的粒子群受到应力作用而发生的粉碎现象,即存在粒子间的相互作用。
选矿三段一闭工艺流程
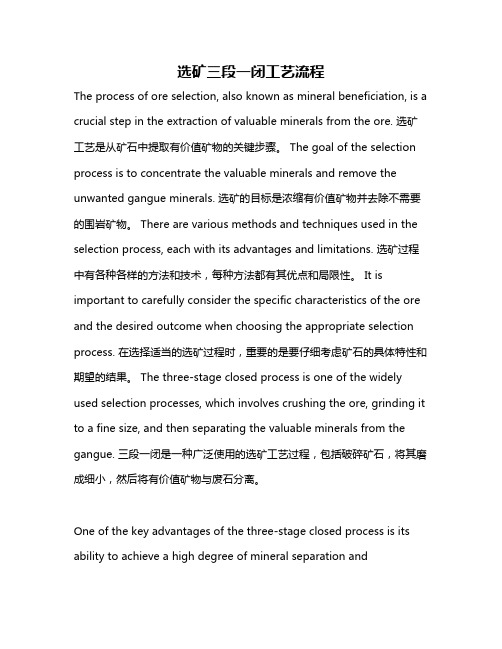
选矿三段一闭工艺流程The process of ore selection, also known as mineral beneficiation, is a crucial step in the extraction of valuable minerals from the ore. 选矿工艺是从矿石中提取有价值矿物的关键步骤。
The goal of the selection process is to concentrate the valuable minerals and remove the unwanted gangue minerals. 选矿的目标是浓缩有价值矿物并去除不需要的围岩矿物。
There are various methods and techniques used in the selection process, each with its advantages and limitations. 选矿过程中有各种各样的方法和技术,每种方法都有其优点和局限性。
It is important to carefully consider the specific characteristics of the ore and the desired outcome when choosing the appropriate selection process. 在选择适当的选矿过程时,重要的是要仔细考虑矿石的具体特性和期望的结果。
The three-stage closed process is one of the widely used selection processes, which involves crushing the ore, grinding it to a fine size, and then separating the valuable minerals from the gangue. 三段一闭是一种广泛使用的选矿工艺过程,包括破碎矿石,将其磨成细小,然后将有价值矿物与废石分离。
三段一闭路破碎厂房设置配置
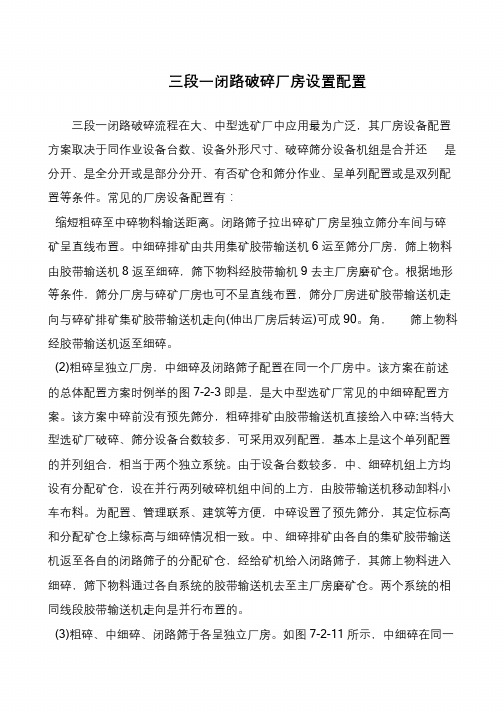
世上无难事,只要肯攀登三段一闭路破碎厂房设置配置三段一闭路破碎流程在大、中型选矿厂中应用最为广泛,其厂房设备配置方案取决于同作业设备台数、设备外形尺寸、破碎筛分设备机组是合并还是分开、是全分开或是部分分开、有否矿仓和筛分作业、呈单列配置或是双列配置等条件。
常见的厂房设备配置有:缩短粗碎至中碎物料输送距离。
闭路筛子拉出碎矿厂房呈独立筛分车间与碎矿呈直线布置。
中细碎排矿由共用集矿胶带输送机6 运至筛分厂房,筛上物料由胶带输送机8 返至细碎,筛下物料经胶带输机9 去主厂房磨矿仓。
根据地形等条件,筛分厂房与碎矿厂房也可不呈直线布置,筛分厂房进矿胶带输送机走向与碎矿排矿集矿胶带输送机走向(伸出厂房后转运)可成90。
角,筛上物料经胶带输送机返至细碎。
(2)粗碎呈独立厂房,中细碎及闭路筛子配置在同一个厂房中。
该方案在前述的总体配置方案时例举的图7-2-3 即是,是大中型选矿厂常见的中细碎配置方案。
该方案中碎前没有预先筛分,粗碎排矿由胶带输送机直接给入中碎;当特大型选矿厂破碎、筛分设备台数较多,可采用双列配置,基本上是这个单列配置的并列组合,相当于两个独立系统。
由于设备台数较多,中、细碎机组上方均设有分配矿仓,设在并行两列破碎机组中间的上方,由胶带输送机移动卸料小车布料。
为配置、管理联系、建筑等方便,中碎设置了预先筛分,其定位标高和分配矿仓上缘标高与细碎情况相一致。
中、细碎排矿由各自的集矿胶带输送机返至各自的闭路筛子的分配矿仓,经给矿机给入闭路筛子,其筛上物料进入细碎,筛下物料通过各自系统的胶带输送机去至主厂房磨矿仓。
两个系统的相同线段胶带输送机走向是并行布置的。
(3)粗碎、中细碎、闭路筛于各呈独立厂房。
如图7-2-11 所示,中细碎在同一。
三段一闭路破碎工艺流程解析
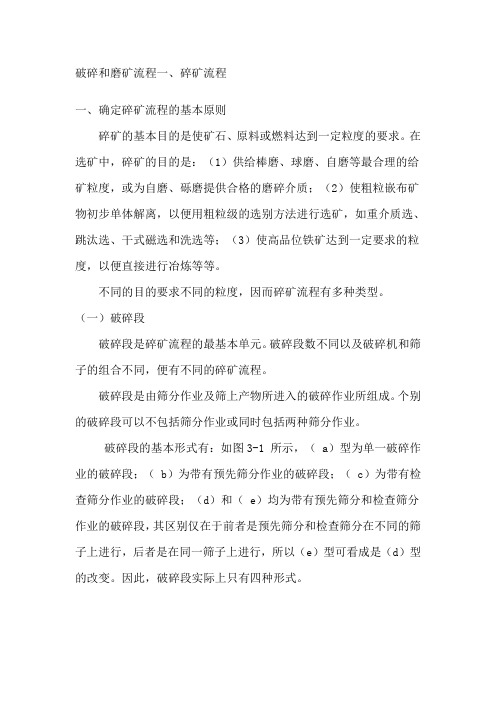
破碎和磨矿流程一、碎矿流程一、确定碎矿流程的基本原则碎矿的基本目的是使矿石、原料或燃料达到一定粒度的要求。
在选矿中,碎矿的目的是:(1)供给棒磨、球磨、自磨等最合理的给矿粒度,或为自磨、砾磨提供合格的磨碎介质;(2)使粗粒嵌布矿物初步单体解离,以便用粗粒级的选别方法进行选矿,如重介质选、跳汰选、干式磁选和洗选等;(3)使高品位铁矿达到一定要求的粒度,以便直接进行冶炼等等。
不同的目的要求不同的粒度,因而碎矿流程有多种类型。
(一)破碎段破碎段是碎矿流程的最基本单元。
破碎段数不同以及破碎机和筛子的组合不同,便有不同的碎矿流程。
破碎段是由筛分作业及筛上产物所进入的破碎作业所组成。
个别的破碎段可以不包括筛分作业或同时包括两种筛分作业。
破碎段的基本形式有:如图3-1 所示,( a)型为单一破碎作业的破碎段;( b)为带有预先筛分作业的破碎段;( c)为带有检查筛分作业的破碎段;(d)和( e)均为带有预先筛分和检查筛分作业的破碎段,其区别仅在于前者是预先筛分和检查筛分在不同的筛子上进行,后者是在同一筛子上进行,所以(e)型可看成是(d)型的改变。
因此,破碎段实际上只有四种形式。
二段以上的破碎流程是不同破碎段的形式的各种组合,故有许多可能的方案。
但是,合理的破碎流程,可以根据需要的破碎段数,以及应用预先筛分和检查筛分的必要性等加以确定。
(二)破碎段数的确定需要的破碎段数取决于原矿的最大粒度,要求的最终破碎产物粒度,以及各破碎段所能达到的破碎比,即取决于要求的总破碎比及各段破碎比。
原矿中的最大粒度与矿石的赋存条件、矿山规模、采矿方法、原矿的运输装卸方式等有关。
露天开采时,主要取决于矿山规模和装矿电铲的容积,一般500~1300 毫米。
井下开采时,主要取决于矿山规模和采矿方法,一般为300~600 毫米。
破碎的最终产物粒度视破碎的目的而不同。
如自磨机的给矿要求!%%& $%% 毫米,进行高炉冶炼的富铁矿的粒度分为500~1300 毫米的两级,棒磨机的合理给矿粒度为300~600 毫米,球磨机合理给矿粒度为300~500毫米。
常规3段1闭路+球磨与半自磨+球磨碎磨流程的方案对比
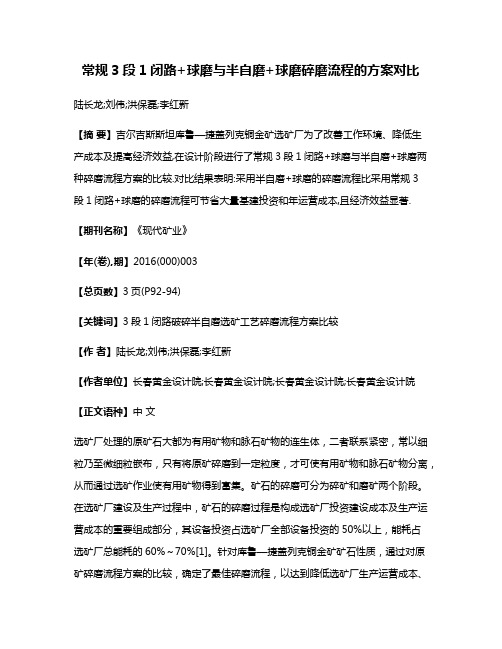
常规3段1闭路+球磨与半自磨+球磨碎磨流程的方案对比陆长龙;刘伟;洪保磊;李红新【摘要】吉尔吉斯斯坦库鲁—捷盖列克铜金矿选矿厂为了改善工作环境、降低生产成本及提高经济效益,在设计阶段进行了常规3段1闭路+球磨与半自磨+球磨两种碎磨流程方案的比较.对比结果表明:采用半自磨+球磨的碎磨流程比采用常规3段1闭路+球磨的碎磨流程可节省大量基建投资和年运营成本,且经济效益显著.【期刊名称】《现代矿业》【年(卷),期】2016(000)003【总页数】3页(P92-94)【关键词】3段1闭路破碎半自磨选矿工艺碎磨流程方案比较【作者】陆长龙;刘伟;洪保磊;李红新【作者单位】长春黄金设计院;长春黄金设计院;长春黄金设计院;长春黄金设计院【正文语种】中文选矿厂处理的原矿石大都为有用矿物和脉石矿物的连生体,二者联系紧密,常以细粒乃至微细粒嵌布,只有将原矿碎磨到一定粒度,才可使有用矿物和脉石矿物分离,从而通过选矿作业使有用矿物得到富集。
矿石的碎磨可分为碎矿和磨矿两个阶段。
在选矿厂建设及生产过程中,矿石的碎磨过程是构成选矿厂投资建设成本及生产运营成本的重要组成部分,其设备投资占选矿厂全部设备投资的50%以上,能耗占选矿厂总能耗的60%~70%[1]。
针对库鲁—捷盖列克铜金矿矿石性质,通过对原矿碎磨流程方案的比较,确定了最佳碎磨流程,以达到降低选矿厂生产运营成本、提高经济效益的目的。
库鲁—捷盖列克铜金矿矿床位于吉尔吉斯共和国西北部的贾拉拉巴德州恰特卡尔区,矿石中主要金属矿物组成为黄铁矿、黄铜矿、毒砂、闪锌矿、磁黄铁矿、辉钼矿、辉铜矿、铜兰、孔雀石、磁铁矿、褐铁矿等。
非金属矿物主要以石英为主,少为长石、云母、绿泥石、方解石等碳酸盐矿物组成。
铜、金为主要目的矿物,矿石工艺类型为少硫化物含金、铜矿石。
原矿采用机车运输,给矿粒度为-600 mm,密度为3.218 t/m3,硬度为8~10,属坚硬矿石。
选矿厂设计处理能力为6 000 t/d,服务年限为14.8 a。
- 1、下载文档前请自行甄别文档内容的完整性,平台不提供额外的编辑、内容补充、找答案等附加服务。
- 2、"仅部分预览"的文档,不可在线预览部分如存在完整性等问题,可反馈申请退款(可完整预览的文档不适用该条件!)。
- 3、如文档侵犯您的权益,请联系客服反馈,我们会尽快为您处理(人工客服工作时间:9:00-18:30)。
破碎和磨矿流程一、碎矿流程
一、确定碎矿流程的基本原则
碎矿的基本目的是使矿石、原料或燃料达到一定粒度的要求。
在选矿中,碎矿的目的是:(1)供给棒磨、球磨、自磨等最合理的给矿粒度,或为自磨、砾磨提供合格的磨碎介质;(2)使粗粒嵌布矿物初步单体解离,以便用粗粒级的选别方法进行选矿,如重介质选、跳汰选、干式磁选和洗选等;(3)使高品位铁矿达到一定要求的粒度,以便直接进行冶炼等等。
不同的目的要求不同的粒度,因而碎矿流程有多种类型。
(一)破碎段
破碎段是碎矿流程的最基本单元。
破碎段数不同以及破碎机和筛子的组合不同,便有不同的碎矿流程。
破碎段是由筛分作业及筛上产物所进入的破碎作业所组成。
个别的破碎段可以不包括筛分作业或同时包括两种筛分作业。
破碎段的基本形式有:如图3-1 所示,( a)型为单一破碎作业的破碎段;( b)为带有预先筛分作业的破碎段;( c)为带有检查筛分作业的破碎段;(d)和( e)均为带有预先筛分和检查筛分作业的破碎段,其区别仅在于前者是预先筛分和检查筛分在不同的筛子上进行,后者是在同一筛子上进行,所以(e)型可看成是(d)型的改变。
因此,破碎段实际上只有四种形式。
二段以上的破碎流程是不同破碎段的形式的各种组合,故有许多可能的
方案。
但是,合理的破碎流程,可以根据需要的破碎段数,以及应用预先筛分
和检查筛分的必要性等加以确定。
(二)破碎段数的确定
需要的破碎段数取决于原矿的最大粒度,要求的最终破碎产物粒度,以及各破碎段所能达到的破碎比,即取决于要求的总破碎比及各段破碎比。
原矿中的最大粒度与矿石的赋存条件、矿山规模、采矿方法、原矿的运输装卸方式等有关。
露天开采时,主要取决于矿山规模和装矿电铲的容积,一般500~1300 毫米。
井下开采时,主要取决于矿山规模和采矿方法,一般为300~600 毫米。
破碎的最终产物粒度视破碎的目的而不同。
如自磨机的给矿要求!%%& $%% 毫米,进行高炉冶炼的富铁矿的粒度分为500~1300 毫
米的两级,棒磨机的合理给矿粒度为300~600 毫米,球磨机合理给矿粒度为300~500毫米。
合理的最终破碎产物粒度,主要取决于工艺的要求和技术经济比较的结果。
确定球磨机的最适宜给矿粒度(即最终破碎产物粒度)时,需考虑破碎和磨矿总的技术经济效果。
破碎的产物粒度愈大,破碎机的生产能力会愈高,破碎费用也愈低;但磨矿机的生产能力将降低,磨矿费用增高。
反之,碎矿的产物粒度愈小,破碎机的生产能力减小,碎矿费用高;但磨矿机的生产能力将提高,磨矿费用可减少。
因此,应综合考虑碎矿和磨矿,选取使总费用最少的粒度,作为适宜的破碎最终产物粒度。
实践证明,磨矿机的最适宜给矿粒度为10~25 毫米。
随着选矿厂的生产规模愈大,缩小磨矿机的给矿粒度,产生的经济效果愈大。
另一方面,确定最终破碎产物粒度时,必须考虑拟选用的破碎机所能达到的实际破碎产物粒度即不得超过允许的排矿口调节范围,以便在设备许可的情况下,获得较小的破碎产物粒度。
每一破碎段的破碎比取决于破碎机的型式,破碎段的类型,所处理旷石的硬度等。
常用破碎机所能达到的破碎比如表 3-1 所示,
处理硬矿石时,破碎比取小值;处理软矿石时、破碎比取大值。
(三)应用预先筛分和检查筛分的确定
预先筛分是在矿石进入该破碎段之前预先筛出合格的粒级,可以减少进入破碎机的矿量,提高破碎机的生产能力;同时可以防止富矿石产生过粉碎。
在处理含水分较高和粉矿较多的矿石时,潮湿的矿粉会堵塞破碎机的破碎腔,并显著降低破碎机的生产能力。
利用预先筛分除掉湿而细的矿粉,可为破碎机造成较正常的工作条件。
因此,预先筛分的应用主要根据矿石中细粒级(小于该段破碎机排矿口宽度的粒级)的含量来决定。
细粒级含量愈高,采用预先筛分愈有利。
研
究证明,技术上和经济上采用预先筛分有利的矿石,其中细粒级的极限含量与破碎机的破碎比有关,其关系如表3-2 所示。
当原矿粒度特性为直线时,在各种破碎比的条件下,其中细粒级的含量均超过了上述极限值(即有利于采用预先筛分的极限含量)。
亦如表3-2所示。
由此可知,当原矿粒度特性为直线时,不管破碎比为多大,采用预先筛分总是有利的。
多数情况下,原矿的粒度特性呈凹形,故破碎前采用预先筛分在经济上都是合算的。
但由于采用预先筛分需要增加厂房高度,当粗碎机的生产能力有富余,或采用直接挤满给矿时,可不设预先筛分。
第二破碎段及第三破碎段给矿中的细粒级含量,主要取决于前一段破碎机的徘矿的粒度特性。
根据实际测定,各种粗碎破碎机和中碎破碎机的产品粒度特性曲线大都是凹形,也就是说细粒占多数,故第二破碎段和第三破碎段采用预先筛分也都是必要的。
只有当选择的中碎机生产能力有富余时,才可考虑中碎前不用预先筛分。
检查筛分的目的是为了控制破碎产品的粒度,并利于充分发挥破碎机的生产能力。
因为各种破碎机的破碎产物中都存在一部分大于排矿口宽度的粗粒级,如短头圆锥破碎机在破碎中等可碎性矿石时,产物中大于排矿口宽。
度的粒级含量达60%,最大粒度为排矿口的2.2~2.7倍;在破碎难碎性矿石时则更甚。
各种破碎机破碎产物中粗粒级(大于排矿口尺寸)含量Z和最大相对粒度(即最大颗粒与排矿
口尺寸之比)如表( 3-3)所示
采用检查筛分后,使不合格的粒级返回破碎机,就如同磨矿机与分级机成闭路循环有利于提高磨矿效率一样,检查筛分对破碎机生产能力的发挥可以改善。
但检查筛分的采用,会使投资增加,并使破碎车间的设备配置复杂化,故一般只在最末一个破碎段采用检查筛分,而且与预先筛分合并构成预先检查筛分闭路循环。
由此得到两点结论:(1)预先筛分在各破碎段均是必要的;检查筛分一般只在最末一个破碎段采用。
(2)破碎段数通常为2~3段。
二、常用碎矿流程
(一)两段碎矿流程
两段碎矿流程有两段开路和两段一闭路两种型式,如图3-2 所示。
两段开路碎矿流程所得的破碎产物粒度粗,只在简易小型选矿厂或工业性试验厂采用,第一段可不设预先筛分。
在这种情况下,当原矿中含泥和水较高时,为使生产能正常进行,小型选矿厂也可采用。
小型选矿厂处理井下开采粒度不大的原矿,并且第二段采用破碎比较大的反击式破碎机时,可采用两段一闭路破碎流程。
(二)三段碎矿流程
三段碎矿流程的基本型式有:三段开路和三段一闭路两种,如图3-3所示。
三段一闭路碎矿流程,作为磨矿的准备作业,获得了较广泛的应用。
不论是井下开采还是露天开采的矿石,只要原矿含泥不高,都能有效地适应。
因此,规模不同的选矿厂都可以采用。
三段开路碎矿流程与三段一闭路流程相比,所得破碎产物粒度较粗,但它可以简化破碎车间的设备配置,节省基建投资。
因此,当磨矿的给矿粒度要求不严和磨矿段的粗磨采用棒磨时,以及处理含水分较高的泥质矿石和受地形限制等情况下,可以采用这种流程。
在处理
含泥含水较高的矿石时,它不致于像三段一闭路流程那样,容易使筛网和破碎腔堵塞。
采用三段开路加棒磨的碎矿流程,不需复杂的闭路筛分和返回产物的运输作业;且棒磨受给矿粒度变化影响较小,排矿粒度均匀,可以保证下段磨矿作业的操作稳定;同时,生产过程产生的灰尘较少,因而可以改善劳动卫生条件。
当要求磨矿产物粒度较粗(重选厂)或处理脆性(钨、锡矿)、大比重(铅矿)矿物时,可采用这一流程。
只有处理极坚硬的矿石和特大规模的选矿厂,为了减少各段的破碎比或增加总破碎比,才考虑采用四段破碎流程。
(三)带洗矿作业的碎矿流程
当原矿含泥( -3 毫米)量超过5-10%和含水量大于5~8%时,细粒级就会粘结成团,恶化碎矿过程的生产条件,如造成破碎机的破碎腔和筛分机的筛孔堵塞,发生设备事故,储运设备出现堵和漏的现象,严重时使生产无法进行。
此时,应在碎矿流程中增加洗矿设施。
增加洗矿设施,不但能充分发挥设备潜力,使生产正常进行。
改善劳动强度,而且能提高有用金属的回收率,扩大资源的利用。
洗矿作业一般设在粗碎前后,视原矿粒度、含水量及洗矿设备的结构等因素而定。
常用的洗矿设备有洗矿筛(格筛、振动筛、圆筒筛)、槽式洗矿机、圆筒洗矿机等。
洗矿后的净矿,有的需要进行破碎,有的可以作为合格粒级。
洗出的泥,若品位接近尾矿品位,则可废弃;若品位接近原矿品位,则需进行选别。
由于原矿性质的不同,洗矿的方式和细泥的处理等不同,因而流程多样,现列举一例。
原矿为矽卡岩型铜矿床,含泥6~11%,含水8%左右,其洗矿流程如图3-4 所示,破碎流程为三段一闭路。
为使破碎机能安全、正常地生产,第一次洗矿在格筛上进行,筛上产物进行粗碎,筛下产物进入振动筛再洗。
第二次洗矿后的筛上产物进入中碎,筛下产物进螺旋分级机分级、脱泥,分级返砂与最终破碎产物合并,分级溢流经浓密机缓冲,脱水后,进行单独的细泥磨矿、浮选。