炼油厂停工大修时的超级清洗技术
油管清洗新工艺及方法研究

摘要在油田生产中使用的管具很多,包括油管、套管等等。
油井作业结束后,油管和套管或多或少会沾满油污、水垢和氧化合物,影响下一次的使用。
若继续使用,则会是油田生产时间增加而影响到经济效益。
据考证,一个年产200万吨的小型油田,每年需要修复的油管约17万根,每根油管约500元,可以看出如果不修复,这将大大增加油田开发成本。
油田开发过程中引入了油管等管具的清洗流程,从而提高其经济效益。
油管的清洗方法也很多,主要的有加热清洗、化学剂清洗、物理清洗三大类。
从以往的清洗经验得知,加热清洗和化学清洗对环境的影响很大且效率不高。
为了改善清洗效率和质量,将高压水射流清洗技术引入了油田生产中。
高压水射流清洗在清洗过程中,对环境没有污染,对污垢的清洗能力较强,是一项理想的新型清洗技术。
在油田清洗中引入高压水射流清洗技术后,清洗时间明显缩短,清洗质量改善。
本文将对高压水射流清洗技术的一系列流程进行研究,基本包括清洗理论的研究、水射流清洗工艺等方面。
在充分理解其工作机理的基础上,找出影响水射流清洗的效率问题,并提出改善途径。
通过合理匹配清洗系统参数,提高清洗效率和质量,并在计算流体流动力学(CFD)对所选参数的清洗效果进行模拟。
模拟结果表明参数匹配基本合理,可以满足清洗要求。
关键词:油管;油管清洗;高压水射流;清洗工艺;数值模拟AbstractIn oilfield has used in production, including the tube coiled many, casing, etc.After the oil operation, tubing and casing more or less oily, scale and oxygen compounds, affecting the next use. If you continue to use, it will be time to increase oil production affects the economic benefits. According to research, an annual output of 2000000 tons of small oil fields, pipeline needs to be repaired every year about 17 million, the pipeline of about 500 yuan each, can be seen that if not repaired, it will greatly increase the oil field development costs.In oilfield development process has introduced the pipe tube cleaning process, thus improve their economic benefits. Cleaning method is also a lot of tubing, and they are heated cleaning, chemical cleaning, physics clean three categories. Learned from previous experience of cleaning, washing and chemical cleaning of heating a great impact on the environment and inefficient.In order to improve the efficiency and quality, cleaning of high pressure water jet cleaning technology introduced in oilfield production. High pressure water jet cleaning in the cleaning process, no environmental pollution, dirt cleaning ability, is an ideal new cleaning technology. Introduced in the oilfield cleaning high pressure water jet cleaning technology, cleaning time was shortened to improve cleaning quality.This article will high-pressure water jet cleaning technology to study a series of processes, the basic theoretical research, including cleaning, water jet cleaning process and so on.In the full understanding based on the working mechanism, affecting water jet cleaning efficiency, and put forward improving ways. Through the rational matching cleaning system parameters, improve the efficiency and quality, and clean in computational fluid flow mechanics (CFD) selected parameters to simulate the cleaning effect. Simulation results show that the basic parameters matching rational, can satisfy cleaning requirements.Keywords: tubing; pipe cleaning; high pressure water jet cleaning technology; numerical simulation目录摘要 (i)Abstract (ii)目录 (iii)1绪论 (1)1.1目前国内外油管清洗现状 (1)1.1.1国内现状 (1)1.1.2国外现状 (2)1.2目前油管清洗方法 (2)1.2.1化学剂清洗技术 (2)1.2.2中频感应加热清洗技术 (4)1.2.3高压水射流清洗技术 (5)1.2.4综合评价 (5)1.3研究内容及研究思路 (6)1.3.1研究内容 (6)1.3.2研究思路 (8)2高压水清洗技术理论 (9)2.1高压水射流基础知识 (9)2.1.1水的物理性质 (9)2.1.2高压水射流 (9)2.1.3水射流清洗机理 (11)2.2水射流结构 (12)3水射流清洗工艺 (14)3.1水射流清洗工艺 (14)3.1.1移动式高压水射流清洗 (14)3.1.2喷头自旋进给 (15)3.1.3管具旋转喷嘴进给 (16)3.1.4清洗的条件 (17)3.2水力参数及装置机械参数计算 (18)3.2.1水力参数计算 (18)3.2.2机械参数计算 (19)3.3清洗效率 (20)3.3.1影响清洗效率的因素 (20)3.3.2提高清洗效率的途径 (21)4射流系统参数优选 (23)4.1压力和流量 (23)4.2高压软管 (23)4.2.1高压软管规格选择 (23)4.2.2高压软管沿程损失计算 (25)4.3高压泵 (25)4.3.1高压泵基本参数 (25)4.3.2高压泵的选型 (26)4.4驱动机 (26)4.5喷嘴 (27)4.5.1喷嘴当量直径的选择 (27)4.5.2喷嘴参数计算及选型 (29)5喷嘴流场数值模拟 (30)5.1计算流体动力学控制方程 (30)5.2模型建立及边界条件 (33)5.2.1计算模型 (33)5.2.2计算边界条件 (34)5.3计算结果分析 (35)6结论 (37)致谢 (38)参考文献 (39)1绪论1.1目前国内外油管清洗现状1.1.1国内现状国内大庆、江汉等油田,从70年代后期开始研究旧油管修复工艺技术,并建立了简单的修复流水线。
炼油厂停工大修时的超级清洗技术

炼油厂停工大修时的超级清洗技术【摘要】介绍了炼油厂原油、重油换热系统实施超级清洗的原理及过程,实践表明清洗效果良好,大大降低了装置操作人员的劳动强度以及换热设备再次清理费用,缩短了停工检修时间。
【关键词】炼油超级清洗换热系统1.前言随着原油性质变差、生产周期延长,重油部分结垢非常严重,传统的停工前的清油程序,往往只能将轻组分清除,重质油垢等无法去除,系统中的油泥、渣油等也不可能清除干净。
同时每次装置停工换热设备吹扫都会耗费大量蒸汽仍吹扫不干净,操作人员消耗体力大等问题比较突出。
为此,在停工检修过程中,对原油、重油换热系统(脱前换热器、脱后换热器、常压炉前换热器、减压渣油换热器和循环回路内所有的设备和管线等)进行了超级清洗,取得了满意效果。
2.超级清洗原理超级清洗技术是使用装置专用油溶性清洗剂,以催化柴油做为清洗溶剂,利用现有装置的设备(加热炉、换热器、泵、罐、塔等循环系统)对重油系统的热交换器、管线、塔、罐等进行在线清洗。
使清洗液在一定的温度下,按照装置生产流程使清洗液在设备内整体循环。
专用清洗剂中的渗透剂和分散剂,可以溶解分散高温产生的油焦质、沥青质和残留的油污等,具有强大的溶解、清洁能力,同时防止清洗过程中发生再次油相沉积,创造良好的检修环境。
超级清洗选用LWY-11油溶性清洗剂,清洗原理示意如下:①含清洗剂的载体与油污接触;②清洗剂向油污内渗透;③清洗剂与油污内的金属接触,分散金属与油污的结合,软化油污;④油污被软化、分散,从而被溶解除去;⑤重质油随清洗剂载体流动而清除出设备。
图-1 清洗油垢示意图3.实施过程3.1清洗范围常减压装置原油、重油系统(脱前换热器、脱后换热器、常压炉前换热器、减压渣油换热器和循环回路内所有的设备和管线等)。
3.2 清洗方法3.2.1采用催化柴油做载体,加入LWY-11清洗剂在装置设备内密闭循环清洗。
3.2.2使用现有装置的设备(机泵、塔等)对系统的热交换器及其管线等进行循环清洗。
油井超导热洗技术及对产量影响

油井超导热洗技术及对产量影响陈建宏杨伟娟杨继锋王明王健长庆油田分公司第三采油厂吴起作业区,陕西延安 717600摘要:采用常规热力清蜡方法易导致油层堵塞和卡井躺井事故,为弥补常规方法的不足,研究出一种低压力小排量的热力清蜡技术。
该技术的原理是利用热洗车加热热载体(油或水),通过油套环空缓慢注入井筒,其热能以热传递方式向油管内传递,提高油管内壁的温度,蜡受热熔化而被液流带出地面。
关键词:低压;小排量;热力清蜡;现场应用中图分类号:TE358.2 文献标识码:A 文章编号:1671-5799(2015)17-0044-021 目前存在井筒问题油井结蜡现象一直制约着油井的正常生产,尽管人们采用多种方法综合清蜡,但仍未从根本上解决油井的结蜡问题。
下强磁防蜡器不适应深抽井和间歇性出油井,且磁场范围有限,磁体易破碎卡杆卡井;化学药剂含有机氯根;电热带和热化学清蜡成本高,效率低,推广应用受限制;抽油杆自动清蜡装置因强度有限易破碎卡井;大排量热洗井清蜡技术在使用范围上有较大的局限性,经改进后的热油清蜡车在洗井液出口温度和输液泵的泵压上和以往的旧型车相比有大幅度提高[1],这种常规热洗井方式具有排量大、压力高和升温快的特点,对地层能量高、供液充足的油井是适应的。
2 超导热洗清蜡的基本原理超导热力清蜡是利用热能提高液流和沉积表面的温度,从而熔化沉积于井筒中的蜡。
抽油井超导热力清蜡技术是热力清蜡类型中的一种新方法,其原理是利用热洗车加热热载体(油或水),通过油套环空缓慢注入井筒,热载体在油套环空流动时,其热能以热传递方式向油管内传递,提高油管内壁的温度。
一方面,由油套环空流下的热载体,主要以吸附方式顺套管内壁或油管外壁下流(类似自由落体),由于热载体温度高于井筒内物质的温度,不同物体间产生热交换,即温度高的热载体的热能传导至温度低的管材及油管内物质,蜡受热熔化而被液流带出地面。
另一方面,热载体受重力作用向下流至泵抽管柱进油口(筛管或十字叉),增加泵抽生产管柱的供液量,油井泵效提高,油管内液流流速增大,加大了油流向上携带蜡的能力。
全清洗技术(RFC技术)1

济南瑞东实业有限公司Jinan Ruidong Industry Co.,Ltd炼化装置全清洗RFC技术介绍二OO八年五月炼化装置停工全清洗RFC技术化学清洗是通过无机或有机的溶剂溶解、络合、转化及其他作用使垢物从设备表面脱离的技术。
随着技术革新和新型清洗剂的出现,通过有机清洗剂清除石油化工设备内的污油的清洗技术可以大大解决停工检修的工作量,和传统停工检修相比,通过清洗可缩短停工时间,且清洗时温度、压力低,对设备的损害小,清洗后排放的废液通过蒸馏、焦化装置回炼,或者加入破乳剂即可分离,能有效回收资源,减少环境污染。
随着石化企业的技术发展和管理进步,人员素质逐步提高,企业员工越来越精简。
同时,精简的人员能够确保装置的安稳运行,但对于传统的停工检修由于工作量较大,比较困难。
在国外已经频繁应用于常减压、焦化、催化等装置停工过程中。
即装置停工退油后经过适当的处理,交清洗公司进行化学清洗,清洗结束可直接交检修公司检修。
济南瑞东实业有限公司是一家专业清洗公司,有十多年的经验,开发了具有国内领先的装置全清洗技术炼化装置停工全清洗RFC技术(分为水基与油基),为石化企业做更多的服务。
一、清洗机理全清洗过程主要分成五步,主要分为浸透、分散、溶解的过程,如图-1。
1、含清洗剂的载体与油污接触;2、清洗剂向油污内渗透;3、清洗剂与油污内的金属接触,将金属从油污中剥离,软化油污;4、油污被软化、分散,从而被溶解除去;5、重质油随清洗剂载体流动而清除出设备。
图1 清洗效果机理二、全清洗的分类全清洗以载体的不同分为水基和油基两种。
水基全清洗即以水作为溶剂载体的清洗技术。
清洗剂溶解在水溶液中,在一定的温度(90~125℃)、流量下在设备系统内循环。
在清洗过程中,主要观察载体的颜色、粘度、油含量等指标,当上述指标基本稳定时结束,一般循环24小时左右结束。
污水排放需破乳、油水分离后外送。
油基全清洗即以油作为溶剂载体的清洗技术。
一般以FCC柴油作为溶剂载体,清洗剂溶解在FCC柴油中,在一定的温度(130±10℃)、流量下在设备系统内内循环。
FeS学清洗剂在炼油装置停工安全中的应饪

就会 自燃 烧毁 设备, 造成 原油炼制设 备停 工检 修中的重大事故 。因此 , 消除F S e 成了 上 是 对 传 统 清洗 法地 改 进 , 清 洗 的 过 程 间 , 理 的 安 排 了化学 清洗 。 照停 工 过 程 在 合 按 含硫 原 油加 工 设 备 停工 检 修 的 第 一 道 必 需 中 , 入 适 当的 钝 化 剂 成 分 , 设 备 中 残 存 对 设 备 进行 了传 统 的 退 油 、 汽 吹 扫 、 温 加 与 蒸 高 的 硫化 亚 铁 发 生 钝 化 反 应 , 而 完 全 消 除 蒸煮工亭, 从 在蒸塔进行之 后进行洗塔时, 加 的安 全 工 序 。 人F C 硫化 亚铁化学 清洗剂清洗 , Z 一1 因为 胜 利 油 田 石油 化 工 总 厂是 一 个 燃 料 型 硫 化 亚 铁 自燃 的 危害 。 此 时 塔 内 构 件上 附 着 的 大部 分油 泥 已被 高 的炼 油企 业 , 工 原 油 的 硫 含 量 在 08 加 .%左
铁(e ) F S 的形式出现 。 炼油装置经过长 周期 的 运 行 后 , 量 油 泥 、 e 等污 垢 沉 积 在 大 及F S 塔 、 器 、 线等 设 备 内部 , 容 管 当进 入 设 备 停 工检修阶段 , 不采取 有效预防措施 , e 若 FS 遇空气会 迅速 发生氧 化反应 , 当反 应 剧 烈
主 要 高 温 清 除 法 , 采 用 高 温 蒸 汽 和 热 水 即 对 设备 进 行 较 长 时 间 地 吹 扫 清 洗 。 装 置 但 停 工 时 清 除 法 不 仅 要 进 行 较 长 时 间 的 蒸 汽 、 压 水 冲 洗 , 序 烦 琐 , 且 不 能 完 全 高 工 而 除 掉 硫 化 亚 铁 , 备 打开 后 , 防止 硫 化 亚 设 为 铁 自燃 , 需 要 由设 备顶 部 打 水 冷 却 1— 4 速 低 , 面 腐 蚀 生 成 的 F S 难 被 物 料 带 还 2 2 表 e很 小 时 以 上 , 急需 施 工 抢 修 的 设 备 影 响 了 走, 对 每次检 修过程 中上述填 料和换热 器都 施 工 进 度 。 外 , e 遇 水 和 空气 后 , 生 会 发生 硫化 亚 铁 自燃 现 象 , 要用 冷水 进 行 此 FS 产 需 对 不 锈 钢 设 备 危 害 极 大 的 连 多 硫 酸 , 害 冷 却 。 损 了 设 备 使 用寿 命 。 为 了 有 效 、 速 地 将 常 减 压 装 置 设 备 快 石 化 总 厂 采 用的 F S 学 清 冼 剂 , 际 内 集 结 的 硫 化 亚 铁 处 理 干 净 , 短 汽 对 管 线 和 设 备 吹 扫 , 后用 水 进 的 流 动 , 部 分 污 垢 从设 备 表 面 冲 洗 剥 离 然 使 胜 利 油田石 化 总 厂利 用型硫 化 亚铁 清洗 剂对 行 冲 洗 。 样 处 理 后可 以 清 除 管 壁 上 部 分 下 来 , 污垢 清除 干净 。 这 使
石油化工设备油垢焦垢化学清洗技术
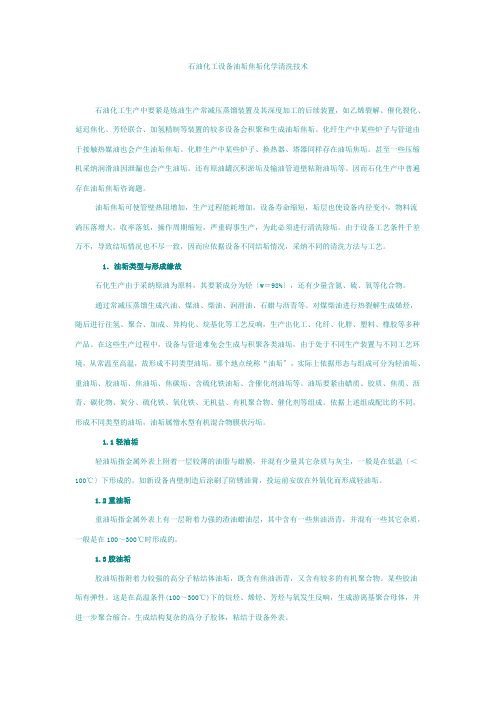
石油化工设备油垢焦垢化学清洗技术石油化工生产中要紧是炼油生产常减压蒸馏装置及其深度加工的后续装置,如乙烯裂解、催化裂化、延迟焦化、芳烃联合、加氢精制等装置的较多设备会积聚和生成油垢焦垢。
化纤生产中某些炉子与管道由于接触热媒油也会产生油垢焦垢。
化胖生产中某些炉子、换热器、塔器同样存在油垢焦垢。
甚至一些压缩机采纳润滑油因泄漏也会产生油垢。
还有原油罐沉积淤垢及输油管道壁粘附油垢等。
因而石化生产中普遍存在油垢焦垢咨询题。
油垢焦垢可使管壁热阻增加,生产过程能耗增加,设备寿命缩短,垢层也使设备内径变小,物料流淌压落增大,收率落低,操作周期缩短,严重碍事生产,为此必须进行清洗除垢。
由于设备工艺条件千差万不,导致结垢情况也不尽一致,因而应依据设备不同结垢情况,采纳不同的清洗方法与工艺。
1.油垢类型与形成缘故石化生产由于采纳原油为原料,其要紧成分为烃〔w=98%〕,还有少量含氮、硫、氧等化合物。
通过常减压蒸馏生成汽油、煤油、柴油、润滑油、石蜡与沥青等。
对煤柴油进行热裂解生成烯烃,随后进行往氢、聚合、加成、异构化、烷基化等工艺反响,生产出化工、化纤、化胖、塑料、橡胶等多种产品。
在这些生产过程中,设备与管道难免会生成与积聚各类油垢,由于处于不同生产装置与不同工艺环境,从常温至高温,故形成不同类型油垢。
那个地点统称“油垢〞,实际上依据形态与组成可分为轻油垢、重油垢、胶油垢、焦油垢、焦碳垢、含硫化铁油垢、含催化剂油垢等。
油垢要紧由蜡质、胶质、焦质、沥青、碳化物、炭分、硫化铁、氧化铁、无机盐、有机聚合物、催化剂等组成。
依据上述组成配比的不同,形成不同类型的油垢,油垢属憎水型有机混合物膜状污垢。
1.1轻油垢轻油垢指金属外表上附着一层较薄的油脂与蜡膜,并混有少量其它杂质与灰尘,一般是在低温〔<100℃〕下形成的。
如新设备内壁制造后涂刷了防锈油膏,投运前安放在外氧化而形成轻油垢。
1.2重油垢重油垢指金属外表上有一层附着力强的渣油蜡油层,其中含有一些焦油沥青,并混有一些其它杂质,一般是在100~300℃时形成的。
油管修复清洗的工艺优化及设备改造

油管修复清洗的工艺优化及设备改造摘要:在油田生产中使用的管具很多,包括油管、套管等等。
油井作业结束后,油管和套管或多或少会沾满油污、水垢和氧化合物,影响下一次的使用。
若继续使用,则会是油田生产时间增加而影响到经济效益。
随着油田开采的进入后期,降本增效是油田发展的主线,油管作为油田开采的重要、常用管材,提高油管修复效率是采油厂降本增效的一项重要措施,提高油管的修复质量,保证油井的正常生产,延长检泵周期,减少作业返工,降低作业费用。
通过制定合理清洗系统参数,提高清洗效率和质量,并在清洗过程中进行可视化过程控制杜绝违章行为,减少隐患存在,做到零违章,无隐患的目标,在环保方面根据国际标准对处理污水进行实施监控,达到合格的排放标准。
关键词:油管;油管清洗;自动化;清洗工艺;安全;环保1 绪论1.1 目前国内油管清洗现状1.1.1国内现状大庆、胜利、长庆等油田,从70年代后期开始研究旧油管修复工艺技术,并建立了简单的修复流水线。
90年代以后,油管在油田生产中所占的成本比例逐年提高,为了降低采油成本,提高开发效益,各油田逐步重视旧油管的修复利用,相继建设了油管修复流水线,加大了旧油管检测与修复力度。
目前国内外油田油管修复流水线一般包括:清洗-通径-探伤-车扣-试压等五个主要工序。
目前国内采用的比较先进的方式为高压水射流清洗及中频加热清洗等。
高压水射流清洗具有自动化程度高、节约能源、油污清洗较为彻底,但是存在设备维护费用高,核心部件(如密封件、阀、喷头等)易损坏等问题,且对于严重结蜡的油管及油管中的丝扣、卡箍等位置难以达到理想的清洗效果;同时,目前广泛采用的油管射流清洗中使用的水压力较高,对泵及其他辅助设备提出了更高的要求,而且,较高的喷射压力形成的噪音污染严重影响工作环境,因此对射流系统及核心元器件进行设计优化,在不影响清洗效率的情况下降低水压力。
由此可见,新的油管清洗技术有待研究。
而目前使用的较先进的清洗技术,即自动化清洗技术更需要优化,向安全、环保、高效、节能等方面发展,以改善目前油管修复技术在清洗方面的现状。
炼化企业全厂检修停工经验分享

炼化企业全厂检修停工经验分享1实现密闭吹扫,重油装置实现柴油清洗后吹扫。
先后两次组织相关人员赴天津石化和济南分公司学习大检修,并重点学习密闭吹扫。
学习完成后,从系统到装置,参照两家兄弟单位做法进行了流程完善和改进。
停工实践的结果证明是有效的,实现了安全、环保、无异味、低噪声停工。
结合停工过程,值得固化的经验有:1.重油装置用轻油置换清洗后,再用蒸汽吹扫,既容易吹扫干净,又节约蒸汽。
如常减压用直储柴油清洗后,清洗油退至原油罐,柴油组分未浪费,且不影响航煤生产,一举多得。
经统计,停工吹扫蒸汽预计在3.2万吨,实际使用量较计划减少0.45万吨左右,吹扫蒸汽使用峰值(200t∕h)较计划值(320t∕h)低120t∕h02.各装置吹扫时要分系统进行,各系统间要紧密衔接,吹扫时间要较常规吹扫适当延长。
如装置各系统全面展开,会造成系统压力低,而且后部有背压,更不容易吹扫干净。
3.密闭吹扫时,出装置前要冷凝,避免高温介质进入罐区或气柜。
本次所有密闭吹扫项目均是开工期间增上,因此只能互相借用,大部分能够实现冷凝后出装置,没有问题。
如3#加氢装置新增一条放空罐D-401至分储塔塔顶空冷A-201前吹扫线,在各个系统吹扫时,装置关闭放空罐至低压瓦斯系统阀门,投用A-201,无法冷凝的蒸汽经过A-201及E-201后,温度降至30℃左右,装置间断将温度不高的放空系统不凝气排入低压瓦斯系统,解决了外排气温度高的问题;7月5日11:00至12:25,两套常减压柴油顶线,经过3#加氢边界跨不合格线进9#罐区,3#加氢控制界区温度不超50°C,G905涨约100吨油,未把大量蒸汽带进罐区。
2网络统筹到位,公用工程平衡控制。
本次停工以连续重整、3#催化、渣油加氢为核心,以蒸汽平衡、瓦斯平衡、氢气平衡为控制要点,最终结果表明,此方案可控,为较优化方案。
结合公司停工网络,三大平衡分解到小时,并重点关注停工过程中关键控制点,制定更加详细和具体措施;与装置逐一对接、重复推演、不断优化,在整个停工过程中,三大系统运行平稳,满足装置需求。
重质油垢化学清洗技术

重质油垢化学清洗技术
简介
炼油厂和化工厂的塔盘、换热器、罐及管线表面,运行中由于各种原因会积聚大量重质油垢,这些油垢炭化程度高,清除困难。
常州清立环能化工科技有限公司研制的重质油垢清洗剂,利用特殊的清洗技术和清洗工艺,对其进行化学转型后可有效清除。
该技术不需拆除设备和机械除垢,可大大降低检修难度和加快检修进度。
技术特点
1.清洗工艺简单,不需对流程作调整,不需拆除设备;
2.清洗液具有极强的渗透能力,能穿过污垢表面的微小间隙进入污垢内部;
3.当清洗液进入污垢内部后,与之发生反应,使分子量较大的重质油垢,转型成为分子量较小的物质而被乳化分散到清洗液中;
效果
1.重质油垢清除率:>90%;
2.清洗后可直接密封进入投运状态。
过滤芯清洗前过滤芯清洗后
过滤芯清洗后检测过滤芯清洗后检测。
炼油厂停工检修开工用能优化案例之四

炼油厂停中工国检石油修化开工工股份用有能限优公司化安案庆例分公之司四
2019年
中国石油化工股份有限公司安庆分公司
• 目录
一、停开工准备
二、停工过程控制 三、开工实施情况
中国石油化工股份有限公司安庆分公司
四、五大类装置停开工用能情况
五、降低停开工检修用能消耗经验及不 足
出排放申请,安环部根据化验分析结果决定污水去向。若提升泵站污 水含油量高,应申请安排吸油作业。
返回目录
中国石油化工股份有限公司安庆分公司 7、公用工程准备
• 蒸汽系统 在大修前和各作业部对接,对停开工期间各装置蒸汽耗量进行预算,把数据精确到天
。根据总供热量和主装置停中开国工节石点油,化科学工安股排份热电有机限、公炉停司开安时庆间和分次公序司,编制热
600
400
200
0
总供热能力
总供热量
炼油板块耗汽量
返回目录
中国石油化工股份有限公司安庆分公司
• 氮气系统
在大修前,同各作业部对接,编制了“停工大修期间氮气用量一览表”,根
据预算合理安排两套空中分国装置石停油、化开工工节股点份,提有前限做公好液司氮安采庆购计分划公。司
在停、开工过程中,克服G20峰会前期危化品禁运等困难,维持液氮储槽高液 位运行。在液氮设备停役期间,搭建临时管线,将安庆曙光公司氮气通过供 氢管线输送进厂,满足储运球罐氮封需求。整个停、开工过程,氮气系统整 体受控。
返回目录
中国石油化工股份有限公司安庆分公司
• 清洗污水排放安排 各作业部严格按照清洗方案,清洗结束后联系检验中心做好排放污水
分析,主要分析项目有pH值、COD、氨氮含量、含油量。
炼油厂大罐清洗方案

炼油厂大罐清洗方案一、装置停工、开工、检修介绍1.装置简介催化裂化是炼油工业中重要的二次加工过程,催化裂化工艺是指原料油(减压蜡油及减压渣油)在高温催化剂的作用下发生催化裂化反应生成裂解油气,并通过吸收、解吸、精馏等手段将裂解油气分离为干气、液态烃、稳定汽油、轻柴油、重柴油、回炼油、油浆的过程2.开、停工范围催化裂化装置含反应、分馏、稳定、脱硫、三机组、气压机等单元。
因二催化装置较催化装置晚停工70小时,所以脱硫系统较其它系统晚停70小时。
3.开停工、检修时间进度3.1停工时间:2008年5月15日0:00~2008年5月18日0:00。
3.2开工时间: 2008年6月1日0:00~2008年6月5日12:00。
4.开、停工主要程序及主要检修项目4.1停工主要程序4.1.1停工准备4.1.2降温降量4.1.3切断进料停气压机4.1.4转卸催化剂4.1.5装大盲板全面扫线4.1.6加装各界区盲板4.2开工主要程序4.2.1全面大检查4.2.2管线吹扫试压,两器气密试验,分馏冷油运4.2.3两器升温,分馏引油循环,吸收稳定建立三塔一器循环4.2.4沉降器赶空气,拆大盲板,分馏塔进油4.2.5装催化剂,转催化剂,建立两器流化4.2.6反应进油,开气压机4.3主要检修项目4.3.1机组检修、1#、2#气压机大修、3#增压机大修,烟机东侧风线、蒸汽线换管;润滑油泵出口管线配回油箱线;安全阀增加下手阀;机组蓄能器检验3个。
4.3.2再生器检修,再生器内构件检查修复(旋分器、分布板、分布管、仪表引压管等);人孔拆装;催化剂清扫等项目。
4.3.3反应器、沉降器检修,沉降器内构件检查修复(旋分器、环形档板、提升管、喷嘴、仪表引压管等);人孔拆装等项目;提升管出口封头改法兰盖连接。
4.3.4三旋及烟道检,内构件检查修复(旋分器);人孔拆装等项目。
4.3.5外取热及汽包检修,拆装人孔DN700 2个;检查处理隐蔽项目;管束抽装配合修补衬里(待定)。
水冲洗在炼化装置停工中的应用

1 前言众所周知,炼化企业停工检修时,装置退油吹扫的效果,尤其重质油设备能否处理干净,对检修质量起决定性作用,常减压装置作为炼化龙头,有着油品密度重、粘度大,以及装置换热流程长等特点。
停工退油吹扫难度大,很难达到预期效果,对安全环保影响巨大。
蒸汽吹扫是行业公认的处理工艺流程内油品的主要操作手段,但由于全厂性停工期间蒸汽压力不足,造成吹扫不彻底。
全部采用蒸汽吹扫处理设备存油,存在蒸汽使用量大,成本居高不下,不利于践行集团公司降本增效的理念;在蒸汽吹扫的过程中不可避免的出现携带油气的蒸汽及携带污油的冷凝水的排放,不利于践行绿色化工的理念;同时使用蒸汽扫线要反复多次憋压操作,装置定员少,员工劳动强度大;流程复杂,蒸汽管线带水,容易出现水击,造成设备管线移位损伤等诸多不利因素,因此急需一种创新思路,在这种情况下水冲洗停工成为必然。
2 装置执行全面的停工水冲洗2.1 环保停工的意义环保已经成为今天我们经济可持续发展的一个决定性的关键,随着中国的经济发展,环境问题一直是举国上下关注的焦点,频发的自然灾害、雾霾等屡治不禁的污染,已经严重影响了人们的生活。
在“绿水青山,就是金山银山”的前提下,总公司提出了“绿色环保停工”要求,要求做到“气不上天、油不落地”的停工总要求。
为了实现这个目标,就要改进原有的蒸汽停工方案,杜绝油气污染天空、脏油污染环境。
改变我们的思想,创新思路,安全环保停工势在必行。
如今密闭吹扫,密闭排放等多种全新的停工方案在近几年中不断出现,鉴于此,结合本装置的特点,急需寻求一种新的停工方法,以达到减少对环境的污染,实现绿色环保停工的目的。
2.2 电脱盐系统的水顶油成功经验的借鉴电脱盐罐在常减压装置中起到油水分离,脱盐脱水的重要作用。
主要特点有:介质密度大、粘度大、温度高。
当装置进行停工操作时,由于电脱盐罐温较高,退油泵容易抽空,每次停工都要提前处理,通过冷油置换或切除降温,停工时间长和,影响装置正常生产。
某炼油厂清罐污油净化技术应用总结
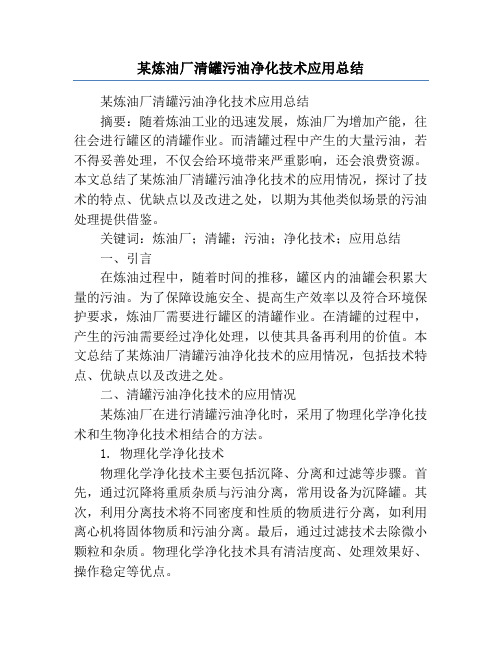
某炼油厂清罐污油净化技术应用总结某炼油厂清罐污油净化技术应用总结摘要:随着炼油工业的迅速发展,炼油厂为增加产能,往往会进行罐区的清罐作业。
而清罐过程中产生的大量污油,若不得妥善处理,不仅会给环境带来严重影响,还会浪费资源。
本文总结了某炼油厂清罐污油净化技术的应用情况,探讨了技术的特点、优缺点以及改进之处,以期为其他类似场景的污油处理提供借鉴。
关键词:炼油厂;清罐;污油;净化技术;应用总结一、引言在炼油过程中,随着时间的推移,罐区内的油罐会积累大量的污油。
为了保障设施安全、提高生产效率以及符合环境保护要求,炼油厂需要进行罐区的清罐作业。
在清罐的过程中,产生的污油需要经过净化处理,以使其具备再利用的价值。
本文总结了某炼油厂清罐污油净化技术的应用情况,包括技术特点、优缺点以及改进之处。
二、清罐污油净化技术的应用情况某炼油厂在进行清罐污油净化时,采用了物理化学净化技术和生物净化技术相结合的方法。
1. 物理化学净化技术物理化学净化技术主要包括沉降、分离和过滤等步骤。
首先,通过沉降将重质杂质与污油分离,常用设备为沉降罐。
其次,利用分离技术将不同密度和性质的物质进行分离,如利用离心机将固体物质和污油分离。
最后,通过过滤技术去除微小颗粒和杂质。
物理化学净化技术具有清洁度高、处理效果好、操作稳定等优点。
2. 生物净化技术生物净化技术是将微生物应用于污油的处理中,通过微生物的代谢活动降解污染物。
其中最常用的是生物降解和生物吸附技术。
生物降解利用微生物分解有机物质,通过合理调控菌群和提供适宜生境来加速降解过程。
生物吸附则是利用微生物细胞表面的吸附作用去除污染物。
生物净化技术具有处理效率高、成本低、环境友好等特点。
三、技术的优缺点与改进之处1. 物理化学净化技术的优缺点与改进物理化学净化技术在清罐污油处理中具有清洁度高、效果好的优点,但其所需的设备和运行成本较高。
此外,处理过程中的一些化学药剂可能会对环境产生污染。
为了改进该技术,可以引入新型的分离设备和替代性药剂,提高净化效率和环境友好性。
550万装置停工化学清洗处理方案

550万装置停工化学清洗处理方案摘要: 550万常减压装置主要生产半成品或者为炼油厂重整装置,航煤加氢装置、柴油加氢装置、催化裂化装置、润滑油装置、延迟焦化等装置提供原料。
装置做好检修为长周期运行奠定基础是重中之重。
由于2023年装置到了4年检修时期,为了达到装置绿色检修、节能检修的目的,特做出化学清洗方案,对装置检修按期完成显得格外重要。
关键词:常减压清洗停工检修流程一、装置简介兰州石化公司550万吨/年常减压蒸馏装置由中国石化工程建设公司设计,于2009年11月建成投产。
设计年加工能力为550万吨(年开工时间为8400小时),为燃料型常减压装置。
二、清洗目的根据兰州石化公司的安排,装置准备2023年6月份开始停工检修。
为了保证检修工作的安全顺利进行,拟在各装置实施清洗技术服务,以消除硫化亚铁自燃问题并消除设备内带有的恶臭类气味,确保检修人员和设备的安全,缩短装置停工检修时间,减少装置停工能耗及费用。
此次清洗技术服务采用济南某公司生产的高效复配钝化清洗剂、水基清洗剂进行清洗技术服务。
清洗剂由渗透剂、螯合剂、分散剂等复配制得的。
本品用于炼油或化工设备的检修开放前清洗系统中硫化亚铁和除去硫化氢、硫醇、氨等化合物。
清洗剂不含重金属等对污水处理有毒成分,清洗结束后,产生废液不会对污水处理造成影响。
产品高效、无毒、无腐蚀,不会造成二次污染。
三、清洗方式3.1水基清洗(1)加注水基清洗剂循环清洗①系统水退油合格后,清洗人员分别从P102入口排凝、P105入口排凝、P114入口排凝处连接注剂设备。
②装置操作人员分别从P101水线、P102水线、P105水线、P114水线继续补新鲜水,建立重油部位大循环以及三塔各侧线闭路水循环,清洗过程中新鲜水补水量需要满足各侧线外送循环量,维持各侧线正常循环。
③装置操作人员点常压炉,系统水循环温度升温至80±5℃(循环流程中温度最低温度要求),装置操作人员维持清洗流程的正常运行。
全清洗技术

问题的提出: 问题的提出: 重油系统停工处理较为困难,如常减压 渣油、催化油浆、焦化重油等系统,特 别是换热系统
传统的处理方式: 传统的处理方式: 蒸汽吹扫、机械清洗或者其它简单的清洗 处理 传统处理的问题 • • • • • 吹扫不彻底、不干净 机械清洗强度大、工作量大 停工时间长,影响停工检修时间 消耗大,如蒸汽、人员 成本高
特点 • • • • 清洗能力强 无废水、废液产生 设备腐蚀减少、操作人员负担减轻 装置检修工期缩短、费用减低
应用范围 • 清洗装置:主要有常减压、催化裂化、 重油加氢、焦化等装置,以及其他有 重油、用常规方法难清洗的系统、装 置及设备。 • 清洗范围:可进行全装置、全系统清 洗,也可以部分清洗。
清洗机理
机理说明 • 含清洗剂的载体与油污接触; • 清洗剂向油污内渗透; • 清洗剂与油污内的金属接触,将金 属从油污中剥离,软化油污; • 油污被软化、分散,从而被溶解除 去; • 重质油随清洗剂载体流动而清除出 设备。
• 重质油随清洗剂载体流动而清除出设备。
清洗剂性能指标
外观 密度(),g.cm-3 PH值 闪点(开口℃) 机械杂质 水中溶解状况 气味 淡黄色,透明,自由流动液体 0.95±0.05 7~8 > 无 乳状液 淡清香味
包装及保质期 180kg铁皮桶包装,避光阴凉、 密闭储存,保质期一年。
服务 由于各企业加工量和原油组分的不 同,以及装置系统大小和设备尺寸 的差异,我公司努力做好“售前、售 中、售后”服务,为客户提供“保姆式 ”交钥匙服务,其中包括技术咨询、 现场技术指导,直到客户满意为止。
结束
用量
• 用量可根据装置加工的原料性 质、加工量、生产运行周期等 确定,一般为系统藏量的 1.5~2.5%。
炼油厂换热器中重质油垢的化学清洗

炼油厂换热器中重质油垢的化学清洗
文年英
【期刊名称】《石油炼制》
【年(卷),期】1990(000)003
【摘要】以油浆、渣油、原油、重柴油等为介质的重质油所生成的污垢,主要成分为高聚物以及难溶的胶质,粘度较大、憎水,难以清除.自投产以来,每次大修时,均得用钢钎捅或高压蒸汽吹扫,但管壁上仍粘附1~1.5mm左右的胶质无法清除.我们研制的化学清洗剂配方,清洗操作简单、成本低、安全性好、除垢率高.1987~1988年两次采用此配方对常减压蒸馏装置的油浆端、原油端、渣油端进行串联式的循环清洗6h后,再用新鲜水冲洗至pH=7.拆开检查结果,只要管束未堵死,管壁上再无油垢、胶质等杂物.
【总页数】2页(P66-67)
【作者】文年英
【作者单位】无
【正文语种】中文
【中图分类】TE965.07
【相关文献】
1.螺旋板式换热器油垢的化学清洗 [J], 杨智强;葛晶儒;张丹阳
2.焦化厂粗苯工段换热器焦油垢化学清洗 [J], 郭信忠
3.化学清洗法在新建炼油厂中压蒸汽管网清洗中的应用 [J], 黄少敏
4.发电厂板式换热器化学清洗中氨基磺酸的运用研究 [J], 陈庚;陈钰
5.煤焦油垢的化学清洗——我厂造气车间换热器的结垢清洗 [J], 侯忠德
因版权原因,仅展示原文概要,查看原文内容请购买。
炼油厂清洗方案

炼油厂储油罐清洗技术方案、储油罐设备概况_、方案编制依据三、清洗前的预备工作四、清洗步骤及工艺流程五、清洗施工进度表六、清洗质量标准七、清洗废液处理八、清洗工程安全措施九、清洗工程工程治理十、交工验收容积序号 油罐编号 金属材质 3 (m )数量上次使用 时间 备注 使用年 限 前言:随着石油工业的进展,使用的油罐数量和容积都在增加,目前 大型油罐的容积一般在 1X 10 i也有直径 80m 高达 20m 的特大型 油罐。
为防止使用时间过长、油罐破损而导致石油泄漏,需定期对油罐进 行开放检查。
油品在油罐中的储存过程中,在油罐底部就会沉积出淤渣〔或 称油泥〕,清洗油罐的主要目的是去除附着在罐壁上的及沉积在底部 的油泥,由此可保证成品油的质量,并延长油罐的使用寿命。
一、储油罐设备概况1、 清洗范围油罐清洗工程量清单上述油罐中,分别标出哪些是在用油罐;哪些是闲置油罐,清洗后再利用;哪些是制造安装的油罐;哪些油罐是清洗后换装 另外品种的油,不同状况在清洗时要承受不同措施。
本次清洗工程,不行能全部油罐放空。
可能放空局部油罐清 洗,请业主方尽量供给具体状况,便于施工方配置施工机械设备 及人员、施工进度等。
2、 业主方清洗质量要求m 53、清洗施工期限二、方案编制依据HG/T2387—2023《工业设备化学清洗质量标准》HG20232《脱脂工程施工及验收规章》JB8526--1997《高压水射流清洗作业安全标准》JB/T8093--1999《高压水射流设备》UL1776--1995《高压清洗机安全标准》GB8978 污水综合排放标准甲方供给的清洗工作量清单三、清洗前的预备工作1、清洗工程技术人员赴现场具体了解油罐的油垢状况、构造和材质,并对油罐的人孔、出油口、排污口了解清楚。
是否有泄露或堵塞等缺陷,阀门开关是否敏捷,如有上述问题应实行有效措施预先处理。
2、与业主方协商为油罐清洗供给水源、电源、压缩空气、蒸汽等。
- 1、下载文档前请自行甄别文档内容的完整性,平台不提供额外的编辑、内容补充、找答案等附加服务。
- 2、"仅部分预览"的文档,不可在线预览部分如存在完整性等问题,可反馈申请退款(可完整预览的文档不适用该条件!)。
- 3、如文档侵犯您的权益,请联系客服反馈,我们会尽快为您处理(人工客服工作时间:9:00-18:30)。
炼油厂停工大修时的超级清洗技术
【摘要】介绍了炼油厂原油、重油换热系统实施超级清洗的原理及过程,实践表明清洗效果良好,大大降低了装置操作人员的劳动强度以及换热设备再次清理费用,缩短了停工检修时间。
【关键词】炼油超级清洗换热系统
1.前言
随着原油性质变差、生产周期延长,重油部分结垢非常严重,传统的停工前的清油程序,往往只能将轻组分清除,重质油垢等无法去除,系统中的油泥、渣油等也不可能清除干净。
同时每次装置停工换热设备吹扫都会耗费大量蒸汽仍吹扫不干净,操作人员消耗体力大等问题比较突出。
为此,在停工检修过程中,对原油、重油换热系统(脱前换热器、脱后换热器、常压炉前换热器、减压渣油换热器和循环回路内所有的设备和管线等)进行了超级清洗,取得了满意效果。
2.超级清洗原理
超级清洗技术是使用装置专用油溶性清洗剂,以催化柴油做为清洗溶剂,利用现有装置的设备(加热炉、换热器、泵、罐、塔等循环系统)对重油系统的热交换器、管线、塔、罐等进行在线清洗。
使清洗液在一定的温度下,按照装置生产流程使清洗液在设备内整体循环。
专用清洗剂中的渗透剂和分散剂,可以溶解分散高温产生的油焦质、沥青质和残留的油污等,具有强大的溶解、清洁能力,同时防止清洗过程中发生再次油相沉积,创造良好的检修环境。
超级清洗选用LWY-11油溶性清洗剂,清洗原理示意如下:
①含清洗剂的载体与油污接触;
②清洗剂向油污内渗透;
③清洗剂与油污内的金属接触,分散金属与油污的结合,软化油污;
④油污被软化、分散,从而被溶解除去;
⑤重质油随清洗剂载体流动而清除出设备。
图-1 清洗油垢示意图
3.实施过程
3.1清洗范围
常减压装置原油、重油系统(脱前换热器、脱后换热器、常压炉前换热器、减压渣油换热器和循环回
路内所有的设备和管线等)。
3.2 清洗方法
3.2.1采用催化柴油做载体,加入LWY-11清洗剂在装置设备内密闭循环清洗。
3.2.2使用现有装置的设备(机泵、塔等)对系统的热交换器及其管线等进行循环清洗。
3.3 清洗步骤及工艺要求
3.3.1 隔断清洗系统外的设备
装置退油后,清洗系统流程以外的设备关闭阀门或加装盲板,打开电脱盐罐副线阀。
3.3.2 导入柴油、置换
①通过现有工艺流程向常减压装置内输送催化柴油,开始进行柴油置换操作。
②柴油置换流程:
装置使用催化柴油对清洗系统进行开路清洗,用柴油置换装置内残存介质(置换柴油及后期循环清洗后柴油回到污油罐区以备回炼)。
流程图如下:
图-2 800万吨/年常减压超级清洗清柴油置换流程示意图
③在柴油置换过程中,注意切换跨线、副线,并联换热器分组置换。
④置换结束
采样分析柴油进装置处和出装置口柴油密度的对比来检测清洗系统柴油的置换程度,当两处的柴油密度值相差在3%以内时,柴油置换合格,结束置换流程,转为循环清洗流程。
3.3.3 注剂
①系统柴油清洗循环建立好,将清洗剂注入到循环柴油里。
②注剂时时间控制
清洗剂缓慢均匀注入,总加注时间控制在2小时左右。
③注剂结束时,用约一桶(200L)柴油将注剂设备以及注剂管线内的清洗剂压送到系统里。
3.3.4 闭路循环清洗
①循环清洗流程
打开开工循环线,关闭去污油罐阀门,柴油改为闭路循环。
整体闭路循环回路与柴油置换流程相同,仅将减压渣油冷却器E140出口利用开工循环线转到脱前换热器入口形成闭路循环。
减三线循环是利用减三线泵P116经过E123A-D/E303→E125A/B→E120后返回减压塔,清洗液落至减三线集油箱后在经过减三线泵P116形成循环回路。
图-3 800万吨/年常减压超级清洗清洗整体循环清洗流程示意图
图-4 800万吨/年常减压超级清洗清洗减三线循环清洗流程示意图
②循环清洗时,将减压渣油冷却器E140冷却进水关闭。
③柴油在循环清洗过程中的温度调整
清洗过程用常压加热炉F101、减压加热炉F102作热源,注剂完成后温度则提高至110-130℃。
正式清洗循环阶段保持清洗循环液温度为110-130℃。
④循环动力
清洗循环可通过泵P103、P111、P118、P116等来进行。
3.3.5 清洗操作
①保持温度在110-130℃,对系统循环清洗不少于18小时。
②为了提高清洗效果,在所有热交换器清洗一段时间后,对脱盐罐前、后并联的热交换器组,采用并联热交换器轮流清洗。
③循环清洗阶段循环流量尽可能增大,循环液体的流量将取决于循环回路中使用泵的能力,因此回路中的机泵流量尽可能的调节至最大。
3.3.6清洗终点判定
在清洗循环过程中,随着清洗剂渗透到粘稠的油垢内,使其软化。
软化的油垢被溶解到清洗柴油内,使清洗的载体柴油颜色逐渐变黑。
通过采样分析柴油颜色的变化情况来判定清洗的进展状况。
清洗过程中定时(每小时)在同一采样点采集清洗的柴油,用色差仪进行分析循环液变化的L值,施工初期进入到系统的柴油L值约为90.0左右,随着清洗时间的进行,滤纸L值会逐渐降低,当L值趋于稳定时停止清洗循环。
表-1 清洗过程循环液L值记录表。