六西格玛管理经典案例
六西格玛管理项目案例
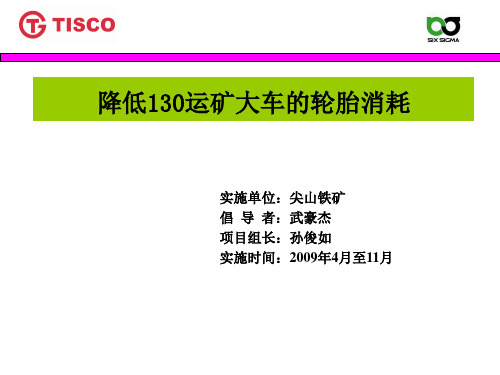
研究日期: 报表人: 产品名称: 其他:
2009年4月28日 杨泰泉 轮胎
检验员与标准
100
90
95.0% 置信区间 百分比
样品 1
2 3 4 5 6 7
测试者 王君山
王君山 王君山 王君山 王君山 王君山 王君山
判定 NG
OK OK OK OK OK NG
标准 NG
NG OK OK OK NG NG
分析:2006年开始,尖山铁矿购入130运矿大车,130运矿大车呈逐年上升的趋势,逐步 取代7548D和7555B。
10
D5 Y的缺陷定义
DMA I C
一、定义、公式 缺陷的定义:
1、磨损—运矿大车在载重行驶过程中胎面与地面摩擦引起的胎面磨平、裂纹、 剥落、掉块、分离、轻微溶胀等现象。
2、刺破——运矿大车在载重行驶过程中由于路面锋利浮石和岩角来回切割引起 的胎侧、胎肩异常划伤或轮胎爆炸现象。
降低130运矿大车的轮胎消耗
实施单位:尖山铁矿 倡 导 者:武豪杰 项目组长:孙俊如 实施时间:2009年4月至11月
项目团队
DMA I C
总倡导者:武豪杰 项目组长:孙俊如
项目发起人:杨忠林
工艺
点检
生产
设备
姓名 郑永泉 姜振望 杨泰泉 刘永政 候效伟 闫四虎
部门 设备能源科 调度室 采矿点检站 运输作业区 筑排作业区 采矿作业区
NG
60
60
2
宋建平
OK
NG
2
宋建平
OK
NG
3
宋建平
OK
OK
3
宋建平
OK
OK
50
50
4
宋建平
六西格玛经典案例

六西格玛经典案例在六西格玛质量管理方法中,通过分析和改进业务流程,以减少缺陷和提高效率,从而实现优秀质量和高度效益。
以下是三个经典的六西格玛案例。
1. Motorola的六西格玛实践Motorola是六西格玛的奠基者之一、20世纪80年代,Motorola采用六西格玛方法,以改进生产过程并提高质量。
在一个以缺陷率而不是零缺陷为标准的产业中,Motorola在一年内将缺陷率从超过三十万个降低到每百万个产品中只有5个。
六西格玛的成功引起了其他公司的注意,并成为其他公司实施质量管理的典范。
2. General Electric(GE)的六西格玛实施GE是六西格玛的早期采用者,它将六西格玛引入公司的各个部门和业务领域。
公司的首席执行官杰克·韦尔奇在1995年将六西格玛作为公司的战略重点。
GE在实施过程中的一个成功案例是其航空发动机业务部门,该部门通过六西格玛方法降低了生产过程中的缺陷率,并提高了航空发动机的性能和可靠性。
GE的成功证明了六西格玛可以在各种行业中实现卓越的结果。
3.美国政府的六西格玛应用六西格玛方法不仅在企业界取得成功,而且在政府部门中也有很好的应用。
美国政府决定在1995年引入六西格玛方法,以提高效率并减少浪费。
例如,美国联邦航空管理局(FAA)使用六西格玛方法改进了飞行管制和管理过程,减少了航班延误和事故。
美国海军也采用了六西格玛方法来改善军舰维护和修理过程,提高了战斗力和减少了成本。
以上是六西格玛的三个经典案例,它们都展示了通过六西格玛方法来实现质量改进和效益提高的潜力。
这些案例证明了六西格玛是一个非常有力的质量管理方法,可以在各个领域带来显著的结果。
无论是在制造业、服务业还是政府部门,六西格玛都能够提供一个可靠的框架来解决质量和效率方面的挑战。
控制案例
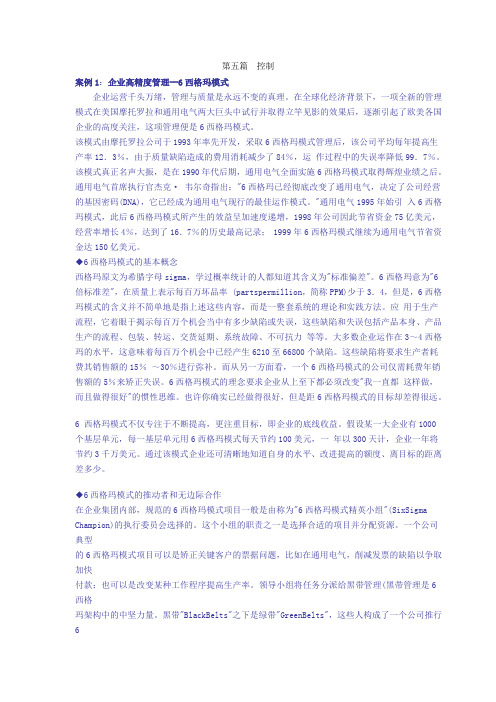
第五篇控制案例1:企业高精度管理--6西格玛模式企业运营千头万绪,管理与质量是永远不变的真理。
在全球化经济背景下,一项全新的管理模式在美国摩托罗拉和通用电气两大巨头中试行并取得立竿见影的效果后,逐渐引起了欧美各国企业的高度关注,这项管理便是6西格玛模式。
该模式由摩托罗拉公司于1993年率先开发,采取6西格玛模式管理后,该公司平均每年提高生产率12.3%,由于质量缺陷造成的费用消耗减少了84%,运作过程中的失误率降低99.7%。
该模式真正名声大振,是在1990年代后期,通用电气全面实施6西格玛模式取得辉煌业绩之后。
通用电气首席执行官杰克·韦尔奇指出:"6西格玛已经彻底改变了通用电气,决定了公司经营的基因密码(DNA),它已经成为通用电气现行的最佳运作模式。
"通用电气1995年始引入6西格玛模式,此后6西格玛模式所产生的效益呈加速度递增,1998年公司因此节省资金75亿美元,经营率增长4%,达到了16.7%的历史最高记录; 1999年6西格玛模式继续为通用电气节省资金达150亿美元。
◆6西格玛模式的基本概念西格玛原文为希腊字母sigma,学过概率统计的人都知道其含义为"标准偏差"。
6西格玛意为"6倍标准差",在质量上表示每百万坏品率 (partspermillion,简称PPM)少于3.4,但是,6西格玛模式的含义并不简单地是指上述这些内容,而是一整套系统的理论和实践方法。
应用于生产流程,它着眼于揭示每百万个机会当中有多少缺陷或失误,这些缺陷和失误包括产品本身、产品生产的流程、包装、转运、交货延期、系统故障、不可抗力等等。
大多数企业运作在3~4西格玛的水平,这意味着每百万个机会中已经产生6210至66800个缺陷。
这些缺陷将要求生产者耗费其销售额的15%~30%进行弥补。
而从另一方面看,一个6西格玛模式的公司仅需耗费年销售额的5%来矫正失误。
6西格玛平安案例

6西格玛平安案例案例1一个半导体簿膜设备制造商在"6-Sigma"实施前的状况是:由于设计研发周期太长,该公司老是不能及时将产品推入市场,而且由于故障率太高,致使售后效劳和维修本钱太高。
售后效劳和维修本钱包括:(1)顾客埋怨、投诉和保修本钱;(2)客户维修本钱;(3)延迟发货和停产损失。
该公司一台设备的平均单价是US$7500K。
该公司希望通过"6-Sigma"的改进运作,能使公司赶上其竞争对手,如Toshiba,Actel,Applied,Material等公司。
该公司的"6-Sigma"运作是从建立"6-Sigma"团队开始的。
核心团队由研发工程、应用工程及可靠性工程组成,其它部门(如市场、制造、财务、质量等)负责支持与协助。
公司的总裁直接领导一个"6-Sigma"负责人,该"6-Sigma"负责人是由公司的副总裁担任。
在"6-Sigma"负责人之下,是"6-Sigma"黑带委员会(包括MBB黑带师、研发总监、技术总监)、"6-Sigma"财务委员会、研发系统1#、研发系统2#、研发系统3#和两个黑带项目团队。
该公司"6-Sigma"的推进步骤如下:由管理高层确定"6-Sigma"的开展计划和管理结构,选定KPI,然后进行管理高层的培训和"6-Sigma"BB培训。
在培训过程中,BB黑带项目也要同时选定和实施,最后是项目的审核。
选定的KPI是:(1)研发周期缩短2个月;(2)生产过渡期合格率由65%提高到80%;(3)减少客户报怨和维修率80%;(4)预计财务回报:通过降低研发周期可创造亿美元(US$350KK);通过提高合格率可创造2亿美元(US$200KK);通过降低维修成本可节约4亿美元(US$400KK)。
六西格玛管理经典案例一个经典的六西格玛案例

六西格玛管理经典案例一个经典的六西格玛案例导读:就爱阅读网友为您分享以下“一个经典的六西格玛案例”的资讯,希望对您有所帮助,感谢您对的支持!一个经典的六西格玛案例黑带大师的笔录—蓝膜效应蓝膜问题三年前我们接到夏新手机一个新产品的订单,为其生产一种新的,非常薄的手机的按键,我们的工程师设计时用了GE---通用电器最新的高拉力硅橡胶来减少厚度,经过样本确认没有问题就转入量产。
但是制造在量产的时候却出现的严重的问题: 经常性100%的按键板在装配热成型后出现硅胶不成熟的现象,轻轻用手指一掐,按键就陷下去,根本无法使用。
要命的是,有时候又会100%OK。
制造工程师做了很多的分析,调节热成型的温度,时间,压力等关键工艺条件来解决,但是缺陷仍然不时出现。
于是产品和过程设计工程师,以及质量工程师做了很多尝试,却无法解决,最后只好请GE美国的材料专家到工厂来协助解决。
三个月过去了,问题没有任何进展.手机商的项目经理很着急,因为一个新款手机的销售周期才6---9个月,我们花在按键板上却已过去了3个多月。
于是夏新给了工厂一个最后期限,只有两个星期的时间,否则他们将撤单。
在这时已经罩不住了,制造经理才只好来找6SIGMA部门,希望我能派BB去解决。
(一般情况下他们都不相信黑带BB能解决问题的,现在也不相信,但是至少BB可以分担他们的责任,呵呵!制造经理此时对于这种缺陷的发生已经快要疯了,他的观点几乎到了唯心的程度,他说:“奥利弗,虽然我也不迷信,但是好像真的有鬼了”。
我派出了两个刚刚结束培训的BB去联手解决,每天我们会花30分钟一起确认进度,工厂的经理们惊奇的发现: 黑带们并没有快速地去假设一些他们认为可能的原因尽快做试验,也没有任何新的人员加入解决问题的团队。
换句话说,人还是这些人,而且BB们先去将整个流程包括他们认为根本无关的工序都问询。
第一天过去后,制造经理忧心忡忡地找我希望我能亲自出马,以期从我身上获得更多信心。
管理学经典案例管理理念
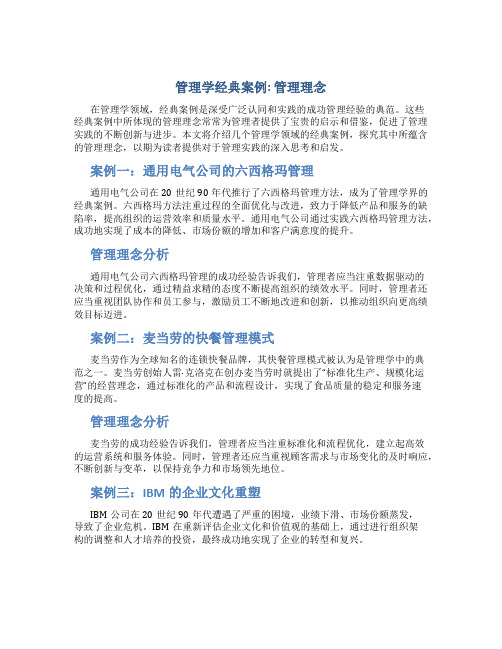
管理学经典案例: 管理理念在管理学领域,经典案例是深受广泛认同和实践的成功管理经验的典范。
这些经典案例中所体现的管理理念常常为管理者提供了宝贵的启示和借鉴,促进了管理实践的不断创新与进步。
本文将介绍几个管理学领域的经典案例,探究其中所蕴含的管理理念,以期为读者提供对于管理实践的深入思考和启发。
案例一:通用电气公司的六西格玛管理通用电气公司在20世纪90年代推行了六西格玛管理方法,成为了管理学界的经典案例。
六西格玛方法注重过程的全面优化与改进,致力于降低产品和服务的缺陷率,提高组织的运营效率和质量水平。
通用电气公司通过实践六西格玛管理方法,成功地实现了成本的降低、市场份额的增加和客户满意度的提升。
管理理念分析通用电气公司六西格玛管理的成功经验告诉我们,管理者应当注重数据驱动的决策和过程优化,通过精益求精的态度不断提高组织的绩效水平。
同时,管理者还应当重视团队协作和员工参与,激励员工不断地改进和创新,以推动组织向更高绩效目标迈进。
案例二:麦当劳的快餐管理模式麦当劳作为全球知名的连锁快餐品牌,其快餐管理模式被认为是管理学中的典范之一。
麦当劳创始人雷·克洛克在创办麦当劳时就提出了“标准化生产、规模化运营”的经营理念,通过标准化的产品和流程设计,实现了食品质量的稳定和服务速度的提高。
管理理念分析麦当劳的成功经验告诉我们,管理者应当注重标准化和流程优化,建立起高效的运营系统和服务体验。
同时,管理者还应当重视顾客需求与市场变化的及时响应,不断创新与变革,以保持竞争力和市场领先地位。
案例三:IBM的企业文化重塑IBM公司在20世纪90年代遭遇了严重的困境,业绩下滑、市场份额蒸发,导致了企业危机。
IBM在重新评估企业文化和价值观的基础上,通过进行组织架构的调整和人才培养的投资,最终成功地实现了企业的转型和复兴。
管理理念分析IBM的成功经验告诉我们,管理者应当注重企业文化的塑造和组织价值观的建立,激发员工的团队合作和创新创造力。
六西格玛改进案例

六西格玛改进案例以六西格玛改进案例为题,列举如下10个案例:1. 生产流程改进案例:在一个制造业公司,生产流程中存在着许多瑕疵品。
为了提高产品质量,该公司采用了六西格玛方法进行改进。
通过分析生产过程中的关键环节,确定了引起瑕疵品的主要原因,并通过改进工艺和设备,减少了瑕疵品的产生率。
2. 供应链管理改进案例:一家零售公司的供应链管理存在着库存过剩和缺货的问题,导致了销售额下降。
为了解决这个问题,该公司运用了六西格玛方法,对供应链中的各个环节进行了优化。
通过提高库存预测的准确性,优化订货策略,以及改进供应商管理,该公司成功解决了库存过剩和缺货问题。
3. 客户投诉处理改进案例:一家电信运营商的客户投诉率较高,影响了公司的声誉。
为了改善客户满意度,该公司运用了六西格玛方法,对客户投诉处理流程进行了改进。
通过提高投诉处理的效率和质量,该公司成功降低了客户投诉率,并提升了客户满意度。
4. 销售流程改进案例:一家保险公司的销售流程存在着繁琐和低效的问题,导致了销售人员的工作效率低下。
为了提高销售业绩,该公司采用了六西格玛方法,对销售流程进行了改进。
通过简化流程、优化销售工具和培训销售人员,该公司成功提升了销售人员的工作效率和销售业绩。
5. 质量管理改进案例:一家制药公司的质量管理体系存在着缺陷,导致了产品质量不稳定。
为了提高产品质量,该公司采用了六西格玛方法,对质量管理体系进行了改进。
通过加强质量控制、改进检验方法和加强员工培训,该公司成功提升了产品质量的稳定性。
6. 项目管理改进案例:一个IT项目存在着进度延误和成本超支的问题,导致了项目无法按时交付。
为了解决这个问题,该公司采用了六西格玛方法,对项目管理进行了改进。
通过优化项目计划、加强资源管理和改进沟通机制,该公司成功提高了项目的进度控制和成本控制能力。
7. 售后服务改进案例:一家家电企业的售后服务存在着响应速度慢和问题解决率低的问题,导致了客户的不满意。
6西格玛课题优秀案例

6西格玛课题优秀案例
六西格玛是一种质量管理方法,旨在通过统计学的方法和工具来降低产品和服务的缺陷率,提高生产效率和降低成本。
下面是一些六西格玛课题的优秀案例:
1. LG 电子的微波炉门泄漏问题:LG 电子在制造微波炉时遇到
了门泄漏问题,这严重影响了产品质量和品牌形象。
通过使用六西格玛方法,LG 电子的团队确定了问题的根本原因,并制定了改进计划,最终成功解决了这个问题。
2. 波音公司的飞机维修成本降低:波音公司使用六西格玛方法来降低飞机的维修成本,通过分析和测量,确定了问题的的根本原因,并采取了一系列措施来减少维修成本。
这项改进不仅降低了公司的运营成本,还提高了飞机的可靠性和安全性。
3. 沃尔玛的库存管理优化:沃尔玛使用六西格玛方法来优化库存管理,通过测量和分析问题,制定了一套优化方案,成功地降低了库存成本和提高了供应链的效率。
4. 通用电气的生产效率提高:通用电气使用六西格玛方法来提高生产效率,通过分析和测量,确定了问题的根本原因,并采取了一系列措施来提高效率,最终提高了公司的盈利能力。
这些案例展示了六西格玛方法在各个领域的应用和成功的结果,不仅提高了产品或服务的质量,还降低了成本和提高了生产效率。
六西格玛管理经典案例

六西格玛管理经典案例
一、六西格玛管理经典案例之一:GE精益实施之路
GE公司,历经几个体系转变期,从企业体系和精益思想的推行,到
用六西格玛管理体系建设精益文化,大力推进GE精益实施。
在实施精益时,GE着重了解和践行客户价值,做到把握核心任务,
以及提高效率、降低成本,这是GE精益思想的本质。
GE整合了一套全面的“六西格玛管理体系”,并在全球范围内实施。
精益实施经历了6个步骤:(1)确定客户要求;(2)确定核心任务;(3)创
建团队;(4)执行;(5)实施管理系统;(6)持续改进。
另外,GE还采取了一系列有效措施来强化精益文化,如GE Vitality Index,持续改进态度等,以不断激发员工的热情,并落实精益思想。
GE精益实施的成功标志着GE有能力将精益理念扎根并落实于企业管
理实践中,让每一个员工充分意识到精益的重要性和必要性。
二、六西格玛管理经典案例之二:印度JCB公司实施精益管理
印度JCB公司是印度最大的出口制造商之一,主要生产破碎机和压路机。
由于全球化竞争日益激烈,JCB公司意识到必须推进精益制造,以提
高生产效率,提升产品质量和减少破费。
因此,JCB公司用六西格玛管理体现实施精益管理。
[6西格玛管理成功案例]成功的例子6篇
![[6西格玛管理成功案例]成功的例子6篇](https://img.taocdn.com/s3/m/89e44bc34793daef5ef7ba0d4a7302768e996f2f.png)
成功的例子篇一:励志小故事成功不在早晚哈兰•山德士是美国肯德基州一家加油站的老板,由于他热情待客、诚信经营,加油站的生意越做越好,每天有很多的车辆来他这里加油。
渐渐地,细心的哈兰•山德士注意到了一个奇特的现象:越是临近中午的时候,来加油的车辆就越多。
看到司机一副饥肠辘辘的样子,他灵机一动:何不利用自己不错的厨艺,在加油站的旁边再开个小餐馆呢?说干就干,山德士的小餐馆很快就开张了,他亲手烹制的炸鸡块深受司机们的欢迎。
一时间,味道独特、口感香软的哈氏炸鸡声名远扬,慕名前来一饱口福的顾客一拨接着一拨。
一段时间之后,哈兰•山德士顺势而起,扩大了餐馆的规模。
那时他刚好40岁。
餐馆的意外成功,不但给山德士带来了比开加油站多出十几倍的财富,还让他成了肯德基州的“名人”。
肯德基州州长为了感谢他在饮食界所做的特殊贡献,向他颁发了上校官衔。
然而,第二次世界大战的突然爆发,让他几乎在一夜之间成了依靠政府救济度日的穷光蛋!由于美国在战时实行汽油配给制,山德士的加油站被迫关闭。
他用巨资扩建的餐馆被一条即将兴建的战时高速公路所“吞没”,全部投资瞬间化为泡影。
这一年,哈兰•山德士已经是一位66岁高龄的老人了。
山德士是个乐观而豁达的老人,虽然遭受灭顶之灾,但并不甘心就此失败。
他冥思苦想,突然想起自己曾经把炸鸡的做法卖给犹他州的一个饭店老板,条件是,对方每卖1只炸鸡就付给自己5美分。
对了,炸鸡的工艺和配方就是最大的无形资产啊!哈兰•山德士如同黑暗中突然遇到一束强光,他决心一试。
于是,他开着一辆破汽车,带着一个塑料桶,再次踏上了创业之路。
从此,人们经常在饭店门口看到山德士老人的身影。
他一家一家地向饭店的老板推销着自己的炸鸡“秘籍”,也一家一家地遭到拒绝,从肯德基州到俄亥俄州,往返数次,历尽艰辛,却一无所获。
无数次的失败,并没有削弱性格倔强的山德士老人的意志,他依然执著地 去推饭店的门。
一天,当山德士老人第N 次走进一家饭店时,老板终于被他说 服了,答应试一试。
六西格玛法在质量管理中的应用实例与分析解读
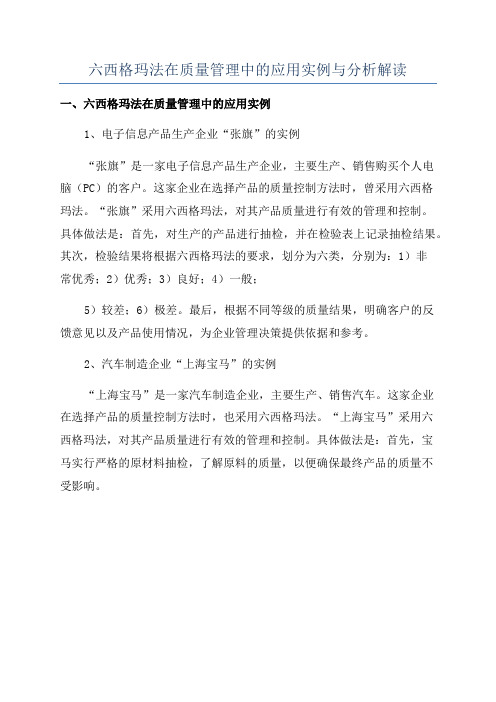
六西格玛法在质量管理中的应用实例与分析解读
一、六西格玛法在质量管理中的应用实例
1、电子信息产品生产企业“张旗”的实例
“张旗”是一家电子信息产品生产企业,主要生产、销售购买个人电
脑(PC)的客户。
这家企业在选择产品的质量控制方法时,曾采用六西格
玛法。
“张旗”采用六西格玛法,对其产品质量进行有效的管理和控制。
具体做法是:首先,对生产的产品进行抽检,并在检验表上记录抽检结果。
其次,检验结果将根据六西格玛法的要求,划分为六类,分别为:1)非
常优秀;2)优秀;3)良好;4)一般;
5)较差;6)极差。
最后,根据不同等级的质量结果,明确客户的反
馈意见以及产品使用情况,为企业管理决策提供依据和参考。
2、汽车制造企业“上海宝马”的实例
“上海宝马”是一家汽车制造企业,主要生产、销售汽车。
这家企业
在选择产品的质量控制方法时,也采用六西格玛法。
“上海宝马”采用六
西格玛法,对其产品质量进行有效的管理和控制。
具体做法是:首先,宝
马实行严格的原材料抽检,了解原料的质量,以便确保最终产品的质量不
受影响。
(六西格玛管理)案例编写济钢测量设备的六西格玛管理
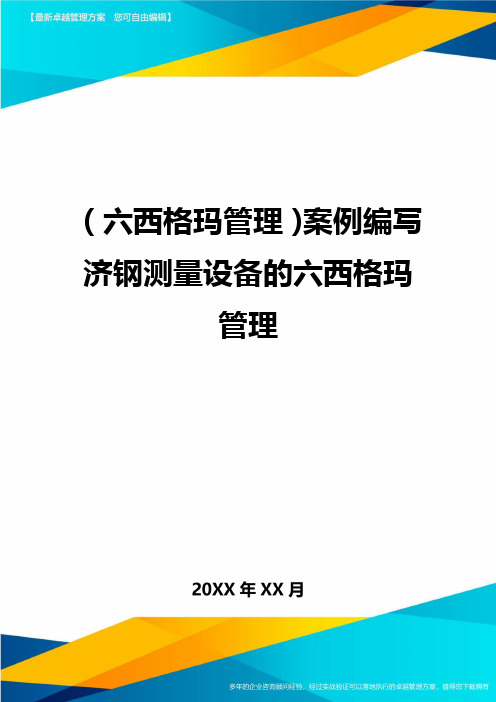
(六西格玛管理)案例编写济钢测量设备的六西格玛管理济钢六西格玛测量设备管理项目壹、济南钢铁集团(股份)公司的发展简介济南钢铁集团(股份)公司(以下简称:济钢)始建于1958年,现有职工42032人,占地面积21214亩,各类测量设备37424台(套),资产总额350亿元,已形成年产1000万吨钢的生产能力的特大型钢铁联合企业,规模位居全国6位,销售收入400多亿,2005年获得全国质量大奖,设有专门的组织机构对于公司内测量设备进行管理,对于公司壹、二级结算和生产重要质量控制点的测量设备实行职能、专业化管理,主要生产工艺有焦化、烧结、球团、炼铁、炼钢、轧钢等。
主要产品有中厚板、圆钢、螺纹钢、角钢、槽钢、球墨铸管、化产品等,现有产品品种187个,产品规格3800个。
2005年全公司生产钢1015万吨、实现销售收入360亿元、利税30亿元、利润18亿元。
长期以来,特别是改革开放以来,济钢坚持以市场为导向,和时俱进,创新发展,制定实施了低成本战略、可持续发展战略、精品战略、出口带动战略、人才战略、信息化推进战略六大战略,加强物质文明建设和精神文明建设,提高核心竞争力,使济钢走上了壹条持续、快速、健康发展的道路。
于企业提高管理水平、确保产品质量、降低能源消耗、做好安全防护及运营管理等工作中,测量设备发挥了重要作用。
二、济钢六西格玛测量设备管理项目的提出1、济钢测量设备管理现状分析济钢现有测量设备五万多台件,设有计量管理处对全厂的测量设备行使管理职能,且负责全公司壹二级测量设备的管理,总公司各二级单位由设备管理部门对所属的三级测量设备进行管理。
于完备的组织体系之下,建立完善了文件化管理体系,形成了大量的三级作业文件和作业指导书,如测量设备点检作业指导书、测量设备确认作业指导书、测量设备维修作业指导书等,明确点检、抢修和日常维修的管理流程,细化了每壹项作业内容和标准。
为确保文件的执行,建立了测量设备运行考核机制,对测量设备按照重要程度不同,规定了具体量化的考核指标,从设备的配备率、运行完好率、故障率和故障时间等进行多维度监督控制。
较完整的六西格玛案例

案例分析过程
确定问题: 明确需要解
决的问题
数据收集: 收集相关数 据包括历史 数据、现状
数据等
分析原因: 分析导致问 题的原因包 括内部原因、 外部原因等
制定解决方 案:根据分 析结果制定 相应的解决
方案
实施解决方 案:按照制 定的解决方 案进行实施
效果评估: 对实施后的 效果进行评 估包括成本、 效率、质量 等方面的改
制造业:提 高产品质量
降低成本
服务业:提 高服务质量 提升客户满
意度
医疗行业: 提高医疗质 量降低医疗
事故
教育行业: 提高教育质 量提升学生
成绩
政府机构: 提高政府服 务效率降低
行政成本
非营利组织: 提高组织效 率降低运营
成本
案例选择标准
问题类型:选择具有代表 性的问题类型如质量、成 本、效率等
确定目标:明确六西 格玛项目的目标和预
期成果
团队建设:组建一支 具备专业知识和技能
的团队
培训与教育:对团队 成员进行六西格玛方
法和工具的培训
数据收集与分析:收 集相关数据并进行深
入分析
改进措施:根据数据 分析结果制定改进措
施
实施与监控:实施改 进措施并监控实施效
果
成果评估:对六西格 玛项目的成果进行评
未来展望
六西格玛将继续在企业中发挥重要作用提高产品质量和效率
六西格玛将与其他管理方法相结合如精益生产、敏捷管理等形成更 加全面的管理体系 六西格玛将在服务行业、政府机构等更多领域得到应用提高服务质量 和效率
六西格玛将继续推动企业创新提高企业竞争力实现可持续发展
推广经验总结
建立六西格玛 团队:选拔具 有专业知识和 技能的员工组
质量管理6Sigma项目案例

6Sigma项目案例一个PCBA工厂波峰焊工序的6Sgma项目改善。
因为波峰焊成为制约PCBA质量的瓶颈。
当前首次通过率为15%,DPMO为30000PPM{种产品每块板焊点数(机会数)为532点}。
2001年9月,该公司成产了一支6Sigma项目改善队伍,其组织结构如下:1.讨论是否选此项目为6Sigma项目。
经小组讨论,大家一致认同此项目为6Sigma项目,理由是:(1)目前焊接DPMO与客户要求存在很大差距,已引起客户强烈投诉。
(2)造成DPMO低的原因不详。
(3)尚未找到改善方法。
(4)实施6Sigma项目改善后可带来大的财务收益和客户满意度的极大提高。
(5)公司人力、物力、财务允许,且技术不是非常复杂。
2.确定项目CTQ关键质量特性。
3.制定6Sigma项目计划书。
4.明确各部门人员职责及其绩效考核方法。
5.确定6Sigma项目所需资源和培训日程。
具体工作分工如下:一、确定项目CTQ及项目Y波峰焊工序是客户特别关注的影响产品品质的关键工序,客户最关注的是焊点一次成功率要高,转化CTQ为焊点的DPMO要小。
故波峰焊点一次成功率为本项目的CTQ,项目Y 衡量CTQ的参数为焊点DPMO。
二、制定6Sigma项目计划书胡伟和张兵根据PCBA焊接状况和已有的DATA制定的6Sigma项目方案如下:6Sigma项目方案三、各成员职责与绩效考核办法续表四、项目资源及培训安排项目资源配置项目培训安排五、项目实施日程安排六、完成Y的测量系统分析本项目中Y的数据为离散二元数据,对其进行分析时需用离散数据的GAGER&R分析进行。
方法:取50块各有一个指定焊点的PCBA,这些焊点有合适焊点、有临界焊点、有不合格焊点,由5个检查员将每块板检查两次,两次之间的时间间隔为一周。
离散数据GAGER&R评估参数:总的一致百分比:用来评估检验员结果一致辞的次数的百分比可重复性百分比:用来评估检验员检查同一部件结果一致的能力可再现性百分比:用来评估多个检验员检验同一部件的结果一致的能力计算公式为:一致百分比=一致的总次数机会的总次数本例计算结果=89%如结果>85%,检验结果可接受。
六西格玛管理案例分析
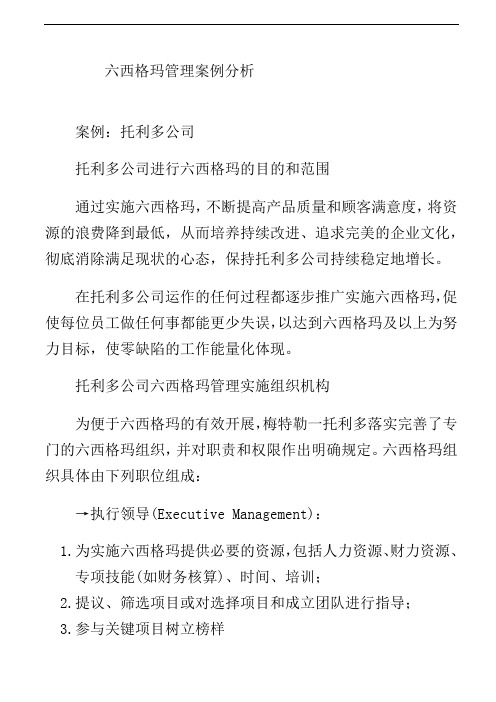
六西格玛管理案例分析案例:托利多公司托利多公司进行六西格玛的目的和范围通过实施六西格玛,不断提高产品质量和顾客满意度,将资源的浪费降到最低,从而培养持续改进、追求完美的企业文化,彻底消除满足现状的心态,保持托利多公司持续稳定地增长。
在托利多公司运作的任何过程都逐步推广实施六西格玛,促使每位员工做任何事都能更少失误,以达到六西格玛及以上为努力目标,使零缺陷的工作能量化体现。
托利多公司六西格玛管理实施组织机构为便于六西格玛的有效开展,梅特勒一托利多落实完善了专门的六西格玛组织,并对职责和权限作出明确规定。
六西格玛组织具体由下列职位组成:→执行领导(Executive Management):1.为实施六西格玛提供必要的资源,包括人力资源、财力资源、专项技能(如财务核算)、时间、培训;2.提议、筛选项目或对选择项目和成立团队进行指导;3.参与关键项目树立榜样→推行委员会(Executive Committee)1.开展六西格玛知识培训;2.负责本公司六西格玛系统的建立;3.统筹本公司六西格玛系统的运作及推进→倡导者(Champion)1.了解六西格玛工具和技术的应用;2.为黑带提供管理、领导、支持;3.检查项目;4.在实施六西格玛战略中致力于降低成本、提高收入和效益→黑带大师(MasterBlackBelt)1.培训六西格玛工具和技术:2.为黑带提供技术支持;3.推动黑带们领导的多个项目;4.为倡导者和执行领导提供咨询帮助;5.作为内部的咨询师、培训教师和专家→黑带,绿带(BlackBelt,GreenBelt)1.寻找应用六西格玛战略和工只的机会,包括内部和外部;2.选择改进项目,制定相应目标和量化指标;3.组建六西格玛项目团队;4.为团队员工提供新战略和工具的正式培训;5.管理并推动、领导项目团队,评价团队成员;6.以培训、案例研究、小规模研讨等形式来传达新的战略和工具;7.按计划完成项目,确保项目效益,并总结推广;8.通过应用六西格玛战略和工具来推销六西格玛。
六西格玛经典案例

六西格玛经典案例1. 引言六西格玛(Six Sigma)是一种质量管理方法,旨在通过降低产品和过程的变异性来提高质量和效率。
这个方法最早由日本公司Toyota引入,并于20世纪80年代由Motorola公司推广到全球。
六西格玛的核心思想是通过收集和分析数据来识别和消除导致质量问题和不必要浪费的根本原因。
在过去的几十年里,许多企业采用了六西格玛来改进其业务流程和产品质量。
本文将介绍几个六西格玛的经典案例,展示六西格玛的强大潜力和实际应用效果。
2. Motorola公司的成功案例Motorola公司在20世纪80年代是最早应用六西格玛的企业之一。
当时,该公司生产的传呼机存在严重的质量问题,导致市场份额大幅下降。
为解决这个问题,Motorola决定采用六西格玛方法来改善产品质量。
Motorola首先对传呼机生产过程进行了详细的调查和数据分析,找出了导致质量问题的根本原因。
然后,他们采取一系列措施来消除问题,如改进生产设备、培训员工和优化生产流程。
结果,Motorola成功地降低了传呼机的缺陷率,提高了产品质量,并重塑了自己在市场上的形象,重新夺回了市场份额。
这个案例显示了六西格玛的实际效果,并证明了通过数据分析和改善措施可以显著提高产品质量。
3. General Electric公司的成本降低案例General Electric(GE)是一个全球性的多元化企业,拥有众多业务部门。
在90年代初,GE公司面临着巨大的竞争压力和成本问题。
GE采用六西格玛方法来降低成本,并在其电力业务部门中开展了一项改进项目。
该项目通过分析电力设备的生产流程,并使用六西格玛工具找出了浪费和低效的环节。
随后,GE采取了一系列措施来改进生产流程,降低成本,如优化设备配置、改进工作流程和培训员工。
通过六西格玛项目的实施,GE成功地降低了电力设备生产的成本,并提高了生产效率。
这个案例证明了六西格玛可以应用于各种行业和业务部门,帮助企业降低成本、提高效率。
六西格玛的成功案例分析
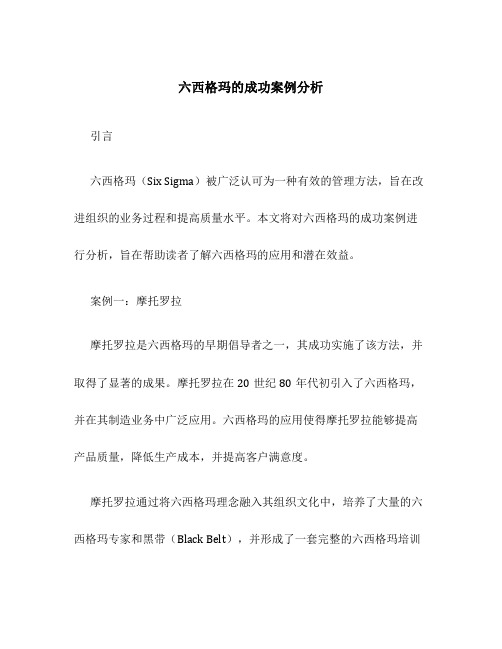
六西格玛的成功案例分析引言六西格玛(Six Sigma)被广泛认可为一种有效的管理方法,旨在改进组织的业务过程和提高质量水平。
本文将对六西格玛的成功案例进行分析,旨在帮助读者了解六西格玛的应用和潜在效益。
案例一:摩托罗拉摩托罗拉是六西格玛的早期倡导者之一,其成功实施了该方法,并取得了显著的成果。
摩托罗拉在20世纪80年代初引入了六西格玛,并在其制造业务中广泛应用。
六西格玛的应用使得摩托罗拉能够提高产品质量,降低生产成本,并提高客户满意度。
摩托罗拉通过将六西格玛理念融入其组织文化中,培养了大量的六西格玛专家和黑带(Black Belt),并形成了一套完整的六西格玛培训和认证体系。
通过推广六西格玛观念和方法,摩托罗拉实现了持续的质量改进,提高了员工的参与度和责任感。
在实施六西格玛后,摩托罗拉的产品质量得到了显著提升,不良品率大幅下降。
通过识别和解决生产过程中的潜在缺陷和变异源,摩托罗拉有效减少了质量问题,提高了产品可靠性。
同时,摩托罗拉通过引入六西格玛的方法和工具,优化了生产流程,降低了生产成本。
摩托罗拉的成功案例证明了六西格玛的有效性和可行性。
通过将六西格玛作为组织文化的一部分,并培养专业的六西格玛人才,组织可以实现质量的持续改进和业务的长期成功。
案例二:通用电气通用电气(GE)是另一个成功应用六西格玛的组织。
GE在20世纪80年代末开始采用六西格玛方法,以提高质量和降低成本。
GE通过六西格玛的实施,将质量管理融入到其核心业务流程中,并将六西格玛作为一种战略工具来推动组织的整体改进。
GE通过六西格玛的应用,实现了巨大的业绩提升。
通过减少产品缺陷和变异性,GE显著降低了质量成本,并提高了产品的可靠性和性能。
六西格玛还促使GE改进了业务流程,提高了效率和生产能力。
通过准确识别和解决问题的方法,GE加强了内部交流和团队合作,提高了员工士气和工作满意度。
GE将六西格玛作为一种战略驱动的改进方法,结合了其他管理理念和工具,如LEAN和业务流程再造。
基于六西格玛管理的银行流程改善案例

基于六西格玛管理的银行流程改善案例六西格玛(Six Sigma)是一种管理方法论,旨在通过降低质量缺陷来提高业务流程的效率和一致性。
在银行业中,六西格玛可以应用于各个业务流程,如开户、贷款审批、客户服务等。
下面是一个基于六西格玛管理的银行流程改善案例。
案例一:贷款审批流程改善问题描述:银行的贷款审批流程存在问题,导致审批时间较长,客户投诉率较高。
1.确定目标:改进贷款审批流程,提高审批效率和客户满意度。
2.收集数据:收集贷款审批的各个环节的数据,包括申请材料收集时间、内部审批时间、客户反馈等。
3.分析数据:根据收集到的数据,分析贷款审批流程中存在的瓶颈和问题,比如申请材料收集不及时、内部审批流程复杂等。
4.改进措施:针对分析结果,提出改进措施,如优化申请材料收集流程,简化内部审批流程等。
5.实施改进:根据改进措施,对贷款审批流程进行改进,并进行试点运行。
6.监控结果:监控改进后的流程效果,比如贷款审批时间的减少、客户投诉率的下降等。
7.标准化改进:如果改进效果良好,将改进后的流程标准化,确保持续的质量改进。
通过六西格玛的方法,银行在贷款审批流程上进行了改进,取得了显著的效果。
贷款审批时间从原来的两周减少到了一周,客户投诉率下降了50%。
这不仅提高了银行的工作效率,还提升了客户体验和满意度。
此外,银行还可以应用六西格玛的方法改进其他业务流程,比如客户服务流程。
在客户服务流程上,银行可以通过分析客户投诉数据,找出问题的根本原因,并提出解决方案。
比如,如果客户投诉主要是因为服务人员的不专业或者服务流程不清晰,银行可以进行培训和制定清晰的服务流程,以提高客户满意度。
总结起来,六西格玛是一种有效的管理方法论,可以帮助银行在各个业务流程上实现质量的持续改进。
通过收集数据、分析问题、制定改进措施并监控结果,银行可以不断提高业务流程的效率和一致性,以提升整体的竞争力和客户满意度。
六西格玛成功(6sigma)案例学习[优秀范文五篇]
![六西格玛成功(6sigma)案例学习[优秀范文五篇]](https://img.taocdn.com/s3/m/51b2a8e3c0c708a1284ac850ad02de80d5d80658.png)
六西格玛成功(6sigma)案例学习[优秀范文五篇]第一篇:六西格玛成功(6sigma)案例学习6sigma成功案例**电子:步伐稳健行走于6σ之路2000年12月,第十届台湾品质奖的颁奖典礼上,在评审“品质不折不扣”的理念下,**电子以多年来致力追求品质的决心与成就,脱颖而出,获得台湾品质奖。
细察**电子追求品质的努力、实践品质的过程,得以知道这个奖得来实至名归。
**电子自1994年起,就在董事长许胜雄的领导下,努力实践6σ(Six Sigma)的品质策略。
何谓6σ?σ在字面上的定义是为统计学上的标准差,简单来说,σ是一个测量品质的标准工具,它代表一种绩效目标,也是一种品质改善的观念。
达到6σ表示每百万次中只会出现3.4个错误,几乎等于零缺点。
σ曾经协助许多世界级企业展现惊人的成绩,它曾经使通用电气(GE)公司迈向营运的高峰,被杰克韦尔奇称许为通用所采用的过最重要的管理措施;也是西方企业力抗日本企业反败为胜的法宝。
提起**电子导入6 σ的原由,**电子副总经理陈乃源表示:“起源于为了满足顾客对品质的要求。
”在未实行6 σ前,**电子所生产的产品错误率颇高,无法达到客户满意,除容易引起顾客的抱怨,相对也缺乏竞争力。
为了提高竞争力,**电子决定导入6 σ。
当时**电子派遣了一批人员到美国接受6σ的训练课程,其中成员包含总经理、数位副总及相关人员,陈乃源也是其中之一。
受训回国后,陈乃源全心投入**电子执行6 σ的架构规划。
陈乃源指出:“实践6 σ的基本原则,是以顾客需求为出发点,一切改善都必须以顾客需求为主,它讲求从制造过程开始改进,而不是看产品产出最后的结果,因为产品事后的修补往往要花费更多的成本。
品质改善最重要的是要从根源做起,也就是在设计时就减少错误的机会。
尤其是在产品生命周期急速缩短的今天,已没有时间让你尝试错误了,也无法再像过去一样等生产过程结束后再统计错误,必须在设计的时候就减少错误的发生,把线上的制程能力及零件的制造能力都计算、考虑进去,让产品合于标准,将制造流程改善,一次就做好,使得后续不至于有错误发生。