球团回转窑开炉方案
球团厂(车间)生产线烘炉方案new

天津荣程联合钢铁集团年产150万吨球团生产线烘炉和试生产组织方案天津荣程钢铁150万吨/年氧化球团工程即将竣工,进入回转窑烘炉阶段,为确保烘炉一次成功,保证耐火材料的使用寿命,特制定此烘炉方案。
一、成立烘炉和试生产领导小组组长:副组长:成员:安全负责人:二、烘炉的概念烘炉的目的是把新砌筑的耐火砖和浇注料中大量游离水和部分结晶水缓慢蒸发出来,使耐火材料发生相变以达到炉衬固结并逐渐达到其最高强度。
烘炉时间过短或速度过快都将造成炉衬产生裂纹、剥落或爆裂。
因此,合理的烘炉升温方案是保证耐火材料强度和寿命的关键环节。
同时,烘炉的过程也是投料试生产的过程。
三、烘炉的部位干燥机热风炉、链篦机、回转窑、环冷机、热风管道等所有砌筑、喷涂耐火材料的部位。
四、外围物资、材料、能源供应准备工作1.原料主要负责人:董建存精粉:20000吨皂土:500吨2.煤气主要负责人:苗建志1)引煤气,外围煤气管线(包括高炉煤气管线)完成到指定接点的施工并经试压验收合格。
2)高炉煤气保证按要求的用量和压力供应。
3.水负责人:李志华保证外围接点按时供水并保证所需的水量水压。
4.压缩空气负责人:苗建志保证外围接点按时供气并保证所需的气量气压。
5.低温烘炉燃料和引燃物6.岗位生产工具负责人:李志强包括各岗位日常操作所需工具(部分需加工制作)及设备维护所需一般工具。
7.备件负责人:舒立祥包括易损备件及少量重要设备的大型备件等。
8.润滑油负责人:舒立祥保证设备短时间运转所必须的润滑油。
五、烘炉前工程内部必须完成的工作1.链篦机、回转窑、环冷机等设备已经安装调试完毕,具备试车条件。
2.造球试验成功。
回转窑煤气烘炉前,所有球盘必须成功做完造球试验,确保链篦机上罩温度达到350℃时篦床上铺上生球,以便有效保护链篦机篦床,保证系统可持续升温。
3.各大风机具备正常运转条件主抽风机、回热风机等必须安装调试完毕,经验收合格。
风机试运转应在风管内耐火材料施工完48小时以后进行,以防耐火材料脱落,为保证风系统畅通管道内的杂物应在试车前清理干净。
氧化球团回转窑设计时工艺参数的选择与计算
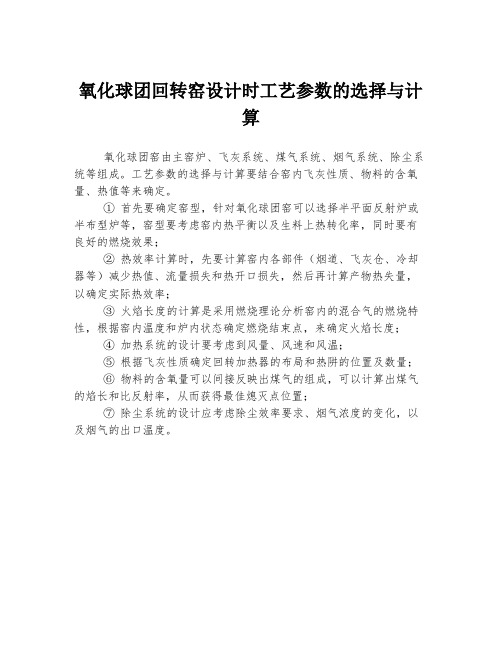
氧化球团回转窑设计时工艺参数的选择与计
算
氧化球团窑由主窑炉、飞灰系统、煤气系统、烟气系统、除尘系统等组成。
工艺参数的选择与计算要结合窑内飞灰性质、物料的含氧量、热值等来确定。
① 首先要确定窑型,针对氧化球团窑可以选择半平面反射炉或半布型炉等,窑型要考虑窑内热平衡以及生料上热转化率,同时要有良好的燃烧效果;
② 热效率计算时,先要计算窑内各部件(烟道、飞灰仓、冷却器等)减少热值、流量损失和热开口损失,然后再计算产物热失量,以确定实际热效率;
③ 火焰长度的计算是采用燃烧理论分析窑内的混合气的燃烧特性,根据窑内温度和炉内状态确定燃烧结束点,来确定火焰长度;
④ 加热系统的设计要考虑到风量、风速和风温;
⑤ 根据飞灰性质确定回转加热器的布局和热阱的位置及数量;
⑥ 物料的含氧量可以间接反映出煤气的组成,可以计算出煤气的焰长和比反射率,从而获得最佳熄灭点位置;
⑦ 除尘系统的设计应考虑除尘效率要求、烟气浓度的变化,以及烟气的出口温度。
回转窑点火方案

回转窑点火方案
余热尾气综合利用400d/T回转窑启动以煤气为介质点火,煤气使用操作必须遵循《煤气安全操作规程》及有关公司规定,为保证回转窑点火安全,特制定本方案。
一、准备工作
1、检查各设备检修时遗留的杂物并清理
2、关闭所有检修门及人孔
3、准备点火棒(2个)
4、对煤气站至回转窑煤气管道进行置换O2<1﹪
二、点火顺序
1、经煤气管道置换合格后,打开盲板阀和电动阀,回转窑当班班长通知调度员回转窑可以接收煤气。
调度员通知煤气站中控工给回转窑供气,回转窑打开窑头放散阀放散至煤气合格。
2、启动高温风机并给定到适当的频率
3、启动一次风机对回转窑内进行吹扫(吹扫10分钟)
4、先将点火棒伸至烧嘴前
5、打开电动阀(开度5﹪),再打开气动阀至点火成功
三、防范措施
点火时,应将煤气管道上的放散阀打开,将管道内的氮气全部排出,直至压力表到达零位时方可送气且放散阀处于打开状态,点
火成功后关闭放散阀。
如一次点火失败,及时关闭煤气阀门,并对窑内吹扫(15分钟)方可再次点火。
回转窑操作方案
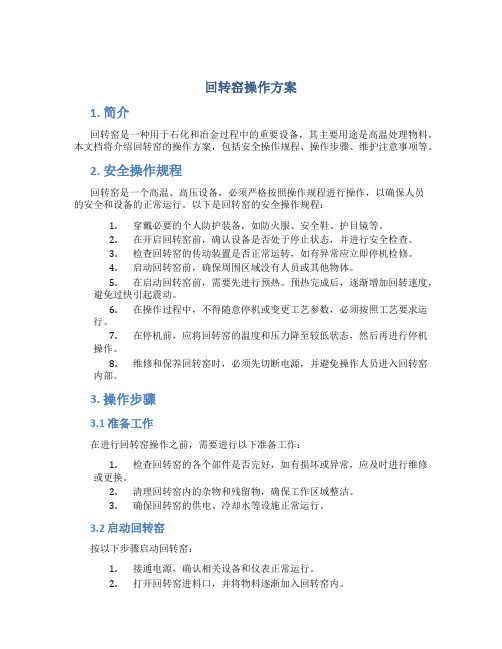
回转窑操作方案1. 简介回转窑是一种用于石化和冶金过程中的重要设备,其主要用途是高温处理物料。
本文档将介绍回转窑的操作方案,包括安全操作规程、操作步骤、维护注意事项等。
2. 安全操作规程回转窑是一个高温、高压设备,必须严格按照操作规程进行操作,以确保人员的安全和设备的正常运行。
以下是回转窑的安全操作规程:1.穿戴必要的个人防护装备,如防火服、安全鞋、护目镜等。
2.在开启回转窑前,确认设备是否处于停止状态,并进行安全检查。
3.检查回转窑的传动装置是否正常运转,如有异常应立即停机检修。
4.启动回转窑前,确保周围区域没有人员或其他物体。
5.在启动回转窑前,需要先进行预热。
预热完成后,逐渐增加回转速度,避免过快引起震动。
6.在操作过程中,不得随意停机或变更工艺参数,必须按照工艺要求运行。
7.在停机前,应将回转窑的温度和压力降至较低状态,然后再进行停机操作。
8.维修和保养回转窑时,必须先切断电源,并避免操作人员进入回转窑内部。
3. 操作步骤3.1 准备工作在进行回转窑操作之前,需要进行以下准备工作:1.检查回转窑的各个部件是否完好,如有损坏或异常,应及时进行维修或更换。
2.清理回转窑内的杂物和残留物,确保工作区域整洁。
3.确保回转窑的供电、冷却水等设施正常运行。
3.2 启动回转窑按以下步骤启动回转窑:1.接通电源,确认相关设备和仪表正常运行。
2.打开回转窑进料口,并将物料逐渐加入回转窑内。
3.启动回转窑的传动装置,逐渐增加回转速度,使物料均匀分布在回转窑内。
4.确保物料在回转过程中可以受到均匀的加热。
3.3 停止回转窑按以下步骤停止回转窑的运行:1.逐渐降低回转窑的回转速度,使其停止运转。
2.关闭回转窑的进料口,停止物料的供给。
3.关闭回转窑的传动装置,并切断电源。
4. 维护注意事项为确保回转窑的正常运行和延长其使用寿命,需要注意以下维护事项:1.定期对回转窑进行清洁,清除内部和外部的积尘和杂物。
2.检查回转窑的传动装置和电气设备,如有异常及时维修或更换。
回转窑的操作范文

回转窑的操作范文回转窑是一种采用回转方式进行石灰窑石灰石煅烧的设备。
它是在工业革命时期出现的一种技术,被广泛应用于石灰生产中。
下面将详细介绍回转窑的操作过程。
首先是准备工作阶段。
在操作开始之前,需要对窑炉进行检查,确保其各项设备工作正常。
同时,需要对石灰石进行质量检测,确保其符合生产要求。
还需要将石灰石送入窑炉内,并根据石灰石的性质和煅烧要求,调整窑炉末端的高度和气室的气体流量。
接下来是点火预热阶段。
点火是启动窑炉运转的关键步骤。
首先,排除窑炉内的氧气,将窑炉内充满惰性气体,例如氮气。
然后,在窑中布设一定数量的点火器,用于将燃料点燃。
通常使用的燃料包括天然气、煤炭和油料等。
在点火时,需要控制好点火器的数量和位置,以保证整个窑炉内的燃料均匀燃烧。
点火成功后,需要进行预热,将窑炉内的温度升至适合煅烧的温度。
正式煅烧阶段是回转窑的核心操作。
在预热结束后,开始加料。
石灰石由进料斗均匀地送入窑炉的上端。
随着窑炉的回转,石灰石逐渐下降到窑炉的下端。
在下降过程中,石灰石会受到靠近窑壁的火焰的直接加热。
这样,石灰石中的结晶水和其他化学结合物逐渐分解,生成石灰石粉末和其它裂解产物。
石灰石粉末会随着回转的窑炉一起向下流动,最终从窑炉底部排出。
在正式煅烧过程中,需要控制窑炉的回转速度、进料速度和气氛气氛的调节。
回转速度的控制可以通过调节电机或变频器来实现,以确保石灰石在窑炉内停留的时间和温度满足生产要求。
同时,还需要根据石灰石的品质和煅烧要求,调节进料速度,保持窑炉内部的热平衡。
此外,还需要根据窑炉内的气氛变化情况,适时调整窑炉顶部和底部的风口开度,以保持窑内的氧气浓度和气氛的稳定。
最后是停窑准备阶段。
当石灰石达到预设煅烧程度后,需要停止进料,并逐渐减小回转速度,让窑炉中的石灰石被完全排出。
同时,为了安全起见,需要将窑炉内的燃气和烟气排出,使其达到安全排放的标准。
以上就是回转窑的操作过程。
通过合理控制窑炉的运转速度、气氛调节和进料速度,可以实现石灰石的高效煅烧,从而生产出高质量的生石灰。
还原炉了炉开炉方案

开炉方案1、开炉前的准备工作1.1开炉所需的物料堆放到规定地方。
(所需的物料见附件1)1.2侧吹还原炉温度达到1000°以上。
1.3所有设备必须进行单体试车,各项指标达到相关技术要求。
单体试车必须有调试记录。
1.4在单体试车完成的基础上,进行联动试车,联动试车模拟实际生产,全部由开炉总指挥下达命令,在主控制室远程控制完成开车和停车。
1.5按照开炉应急预案,实际演练2起突发事故,完成实际应对办法。
1.6在开炉前,由开炉总指挥带队,亲自核查开炉前事项检查表,各项符合要求,发出开炉命令。
1.7开炉使用工具:16磅大锤5把、带堵头堵渣口堵杆4根、清理一、二次风口钎杆各5根,风镐4把,电焊机一台。
1.8开炉前所有岗位操作人员,指挥联络检查人就位(联系方式)2、开炉步骤2.1顶吹炉正常投料,将顶吹炉第一炉渣外排。
2小时后可放出第二批高铅渣进侧吹还原炉;2.2开启烟气风机、循环冷却水、供气、上料等系统运行,操作专用工具齐全到位。
开启二次风机,二次风口送风量根据炉况逐步调节,观察和维持炉顶负压50-80Pa(以炉口没有烟气溢出为准)。
煤粒仓、石灰石仓进到80%料位,并料走到称口。
2.3堵塞好渣口,控制好虹吸铅口最低操作高度。
2.4按开炉加料顺序表完成开炉A: 待炉缸温度升到1000℃,停燃烧器,拆除燃烧器,撤水管、取钢板、炉缸清理。
完成后,从进渣口方向水套口加木材到炉缸平。
B: 装铜水套、进出水管、支撑。
C: 边装水套边投木材,待木材投完完全上火后再投焦炭,第一批焦炭投放量3-4吨。
二层平台投2吨,三层台投2吨。
要求15分钟投完,二层平台从进渣铜溜槽两边、加料口加入。
三层平台从烟道接口两边活动门加入。
待焦炭完全上火后,投粗铅。
D:投第一批粗铅16吨,45分钟内投完。
二层平台投12吨,三层平台投8吨。
要求:二层平台从进渣铜溜槽两边、加料口加入,三层平台从烟道接口两两边投入E:投完第一批铅后,补第二批焦炭2-3吨(10分钟投完)。
回转窑的操作
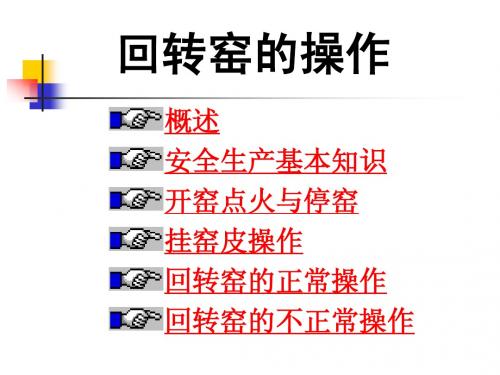
开窑点火与停窑
开窑 点火 停窑
开
窑
对于新建或检修过的回转窑, 在开始运转之前,必须进行检查和 试运转(试车)工作。
开窑前的检查工作 试车 烘窑
开窑前的检查工作
开窑前的检查工作主要包括:窑内情 况检查(对耐火砖的镶砌情况和下料管、 喷煤管的位置检查)和窑外情况检查(对 窑的支承装置、传动装置、密封装置、热 交换装置、冷却装置的检查);最后检查 仪表、操作工具等是否齐全,安全设施是 否完备。
挂窑皮操作
操作时要注意使烧出来的熟料颗粒细小 而均齐,严禁烧大块料,以免砸坏窑皮 在头24小时内为正常下料量的50~70% 为宜,以后每1~2个班增加5~10% 煤喷嘴先适当缩回,再逐步伸到正常位 置。直到窑皮挂好后,即转入正常操作。
回转窑的正常操作
回转窑内情况的判断 回转窑操作控制原则
回转窑内情况的判断
影响“窑皮”形成的因素
生料的化学成分 火焰与窑皮的温度
生料的化学成分
相量多则易形成窑皮, 但又易脱落;反之亦然。一般 不改变生料的化学成分
火焰与窑皮的温度
火焰温度低,液相难以生成,不易挂窑皮; 过高,则会使之脱落。 窑皮温度则应在液相凝固温度附近保持平 衡,才有利于形成窑皮。但窑皮的温度直 接受火焰的温度、火焰的形状的影响,火 焰太短、太急、太粗会侵蚀窑皮,而长火 焰则对窑皮形成有利。故在有利于窑皮形 成条件下尽量缩短火焰
“窑皮”的形成
当物料进入烧成带时,将出现液相,而当液相被物料埋盖后
,不再接受气体的传热,而是将热量传递给窑衬,同时温度 降低,并与窑衬凝固在一起,形成一层窑皮 当这一部分又转到与火焰接触时,只要气体温度不太高,窑 皮就还会烧下来。随着窑皮的加厚,表面温度升高。当达到 液相凝固温度以上时,窑皮便不再形成,并脱落下来,这时 表面温度下降,窑皮继续形成 当新生的窑皮与脱落的窑皮达到平衡时,就保持住一定厚度 的窑皮。
球团回转窑开炉方案

回转窑中修升温方案为了保护窑衬和开机一次成功,特制定此升温方案。
要求各级人员严格按要求落实各项工作,保证升温开机一次成功。
一、升温准备:1、点火前窑衬、环冷机内衬、链蓖机侧墙等验收合格。
2、点火前重点对窑头下料口、窑尾灰斗、链蓖机水平管道、各风箱内和灰斗内的施工积料全部清理干净。
3、柴油站油泵试车正常,主枪清理试喷,油雾化良好。
4、各冷却部位通水、通风正常。
5、各部计量、仪表、电偶及工艺尺寸达到标准要求。
6、制粉系统具备正常生产条件,塔楼提前备好煤粉,并试喷正常。
7、提前联系好5吨烘炉木材和柴油。
8、点火前组织各系统设备的全面试车工作,达到设备稳定运转的条件。
9、点火前各岗位人员全部上岗。
10、点火前做好煤、精矿粉、皂土等原燃料准备,保证开炉的正常需要。
二、烘炉:烘炉时,以窑中热电偶为准,并处于正上方。
为保护窑衬,根据窑衬材质的特性和检修工期的要求,窑衬砌筑完成后,开始进行自然养生1天,然后,进行木柴烘炉24小时,之后回转窑正式点火。
升温安排5天。
三、烘炉操作要求:1、窑衬砌筑完毕后,自然养生1天,养生期间窑门全开,开链蓖机放散。
每两小时转1/4圈。
2、此次链蓖机侧墙、回转窑内衬、环冷机内衬、各热风管道基本为新更换耐火材料。
为保证浇注料中的水分均匀缓慢的充分蒸发,防止水分蒸发过快造成捣打料剥落,对链蓖机、回转窑、环冷机都进行木柴烘炉,时间控制在24小时之内,点位分别为:链蓖机预热段1堆、回转窑窑头1堆、窑内后部间隔均匀放3堆,环冷机三个段各一堆。
木柴烘炉时,各风机蝶阀打开,不开主引风机,关闭窑门,开链蓖机放散。
3、严格按升温制度规定进行升温,设备问题影响时,按时间顺延。
4、木柴烘炉结束后,正式点火时窑中热电偶在正上方,点火8小时后,落链蓖机放散,打开引风、耐热管道上的相应的蝶阀,开主引风机,风量控制在20万米3/小时,电除尘暂不送电,待回转窑停止喷油并达到规定温度时,再启动电除尘。
5、点火22小时内,回转窑每小时转1/3圈,22小时后,用辅机进行连续转窑,窑内高温点在600℃以上时进行主机转窑,窑速0.3转/分。
回转窑操作方案
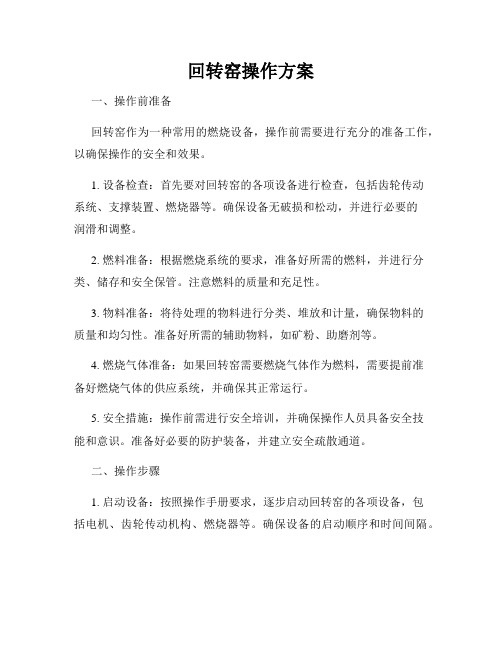
回转窑操作方案一、操作前准备回转窑作为一种常用的燃烧设备,操作前需要进行充分的准备工作,以确保操作的安全和效果。
1. 设备检查:首先要对回转窑的各项设备进行检查,包括齿轮传动系统、支撑装置、燃烧器等。
确保设备无破损和松动,并进行必要的润滑和调整。
2. 燃料准备:根据燃烧系统的要求,准备好所需的燃料,并进行分类、储存和安全保管。
注意燃料的质量和充足性。
3. 物料准备:将待处理的物料进行分类、堆放和计量,确保物料的质量和均匀性。
准备好所需的辅助物料,如矿粉、助磨剂等。
4. 燃烧气体准备:如果回转窑需要燃烧气体作为燃料,需要提前准备好燃烧气体的供应系统,并确保其正常运行。
5. 安全措施:操作前需进行安全培训,并确保操作人员具备安全技能和意识。
准备好必要的防护装备,并建立安全疏散通道。
二、操作步骤1. 启动设备:按照操作手册要求,逐步启动回转窑的各项设备,包括电机、齿轮传动机构、燃烧器等。
确保设备的启动顺序和时间间隔。
2. 加料操作:根据物料的处理要求,通过给料机等设备将物料均匀地加入回转窑内。
控制好物料的进料速度和数量,以避免过载和堵塞的问题。
3. 燃烧操作:根据燃料的种类和特性,通过燃烧器将燃料喷入回转窑内,并调整燃烧器的喷射角度和火焰形态。
控制好燃料的供给量和燃烧温度,以实现理想的燃烧效果。
4. 物料旋转:启动回转窑的旋转装置,使物料在窑内进行均匀的旋转和混合。
根据物料的性质和工艺要求,控制好物料的旋转速度和窑内的倾斜角度。
5. 物料烧结:通过燃烧的热量和窑内的烟气,使物料逐渐烧结和转化为所需的产品。
在烧结的过程中,应监控和调整窑内的温度、压力和气氛,以保证烧结过程的稳定性和产品的质量。
6. 温度控制:根据产品的工艺要求,通过调节供热系统的温度和热量,控制好回转窑内的温度分布。
监测和记录窑内的温度变化,及时调整燃烧和旋转系统,以保持温度稳定。
7. 排出产品:当物料烧结完成后,停止加料和燃烧操作。
通过卸料装置将成品从回转窑中排出,并进行分类、包装和储存。
回转窑点火烘窑方案

回转窑点火烘窑方案1、点火前全系统进行检查确认(系统畅通、封闭完好、阀门到位、翻板灵活)、联动试车,确保设备能正常开起,投料一次成功。
2、原料磨皮带秤、煤磨转子秤、入窑喂料称需标定准确,点火用煤合理,各种原材料储量合理。
3、点火前油枪、油路确保调试良好,火把点燃后放置燃烧器头部再喷油。
点火后,在2小时内将尾温升到150℃左右,此阶段应控制好油量、窑头负压、一次风量、开始尽量少给油,以燃烧良好形成小火焰,无油滴滴到砖面为准,再根据曲线慢慢加油。
点火期间油阀调节必须有专人负责。
4、在尾温达到200℃左右后,以最小给煤量开始油煤混烧,并根据实际情况开启尾排、头排风机。
5、视煤粉燃烧情况开启窑尾排风机,950℃时开启高温风机,窑尾温度达到850℃开启主传动慢转窑,转窑前对各托轮密封进行润滑,窑巡检工要加强对各档托轮瓦的巡检。
点火烘窑时间超过24小时及以上时,为确保一次投料成功,窑尾温度达到650℃时预投料5-8分钟(注:高温风机不拉风),投料量15-20吨,升温过程中确保“慢升温不回头”原则,熟料结粒以细小均齐控制,避免结大块、跑黄料和料子烧流,防止堆“雪人”。
当窑尾温度达到1100℃左右,分解炉出口温度890℃时开始投料。
投料前开启倒库设备,保证拉风后第一时间快速投料,控制一级出口温度400℃以下,初始投料200t/h,窑速0.5r/min,视窑内出料情况提窑速,加料以10t/h梯度,稳定挂窑皮。
不能因窑内温度过高损坏耐火砖,在投料过程中要把握好加料速度,保持窑况稳定使窑投料量达到360-380t/h。
6、升温过程中确保“慢升温不回头”原则,以防耐火材料炸裂、损环。
注意观察窑口、燃烧器、篦冷机等施工部位耐火材料情况。
在烘窑至投料正常期间,烘烤过程如有中断,短时间不能恢复烘烤,按正常冷窑制度进行冷窑,故障排除后按正常烘烤制度重新进行升温;短时间能恢复,做好保温,故障排除后以实际所在温度按烘烤制度升温。
升温过程中,窑头巡检工应勤测胴体温度,防止筒体温度局部过热。
回转窑操作规程
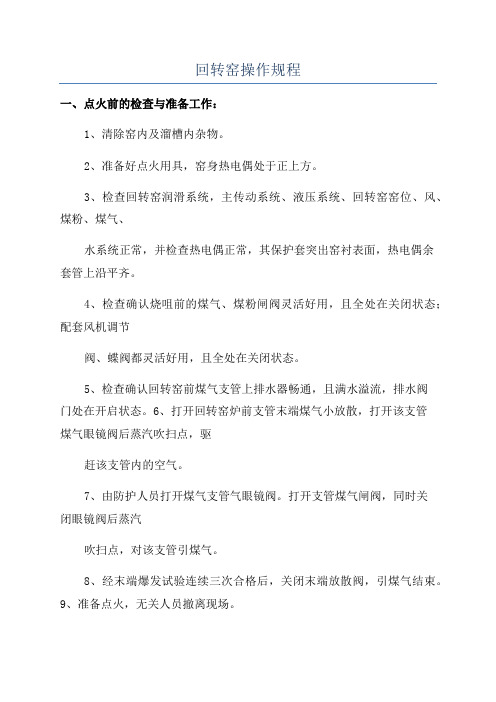
回转窑操作规程一、点火前的检查与准备工作:1、清除窑内及溜槽内杂物。
2、准备好点火用具,窑身热电偶处于正上方。
3、检查回转窑润滑系统,主传动系统、液压系统、回转窑窑位、风、煤粉、煤气、水系统正常,并检查热电偶正常,其保护套突出窑衬表面,热电偶余套管上沿平齐。
4、检查确认烧咀前的煤气、煤粉闸阀灵活好用,且全处在关闭状态;配套风机调节阀、蝶阀都灵活好用,且全处在关闭状态。
5、检查确认回转窑前煤气支管上排水器畅通,且满水溢流,排水阀门处在开启状态。
6、打开回转窑炉前支管末端煤气小放散,打开该支管煤气眼镜阀后蒸汽吹扫点,驱赶该支管内的空气。
7、由防护人员打开煤气支管气眼镜阀。
打开支管煤气闸阀,同时关闭眼镜阀后蒸汽吹扫点,对该支管引煤气。
8、经末端爆发试验连续三次合格后,关闭末端放散阀,引煤气结束。
9、准备点火,无关人员撤离现场。
二、点火操作:1、查看确认回转窑内CO含量为零,且无爆炸混合气体,打开窑尾放散阀。
2、动鼓风机,打开烧咀前的送风一次蝶阀,稍开送风调节阀(开度在5%—10%)达到送风运行正常。
3、燃引火物,送至烧咀前,缓开煤气阀门,引燃煤气,适当调节煤气闸阀,配合调节送风阀,使煤气燃烧正常,达到火焰炽热,无黄焰,且持续稳定.三、回转窑升温操作:1、点火后,要尽快使窑内温度提高,达到正常生产。
2、升温期间要勤观察窑内火焰燃烧情况,将风、煤气、煤粉配合好,达到理想状态。
3、观察电热偶显示屏。
当窑内温度低于200oC时,每小时转窑1/3圈,200~600oC时,每半小时转窑1圈,窑内温度大于600oC时,以回转窑最慢速度连续转窑,如因故不能连续转窑时,每10分钟转1/2圈。
4、点火约4小时升温至900oC时通知窑尾引风机岗位,开引风机。
(引风机也可根据窑内情况提前开)适当调节引风量,使回转窑尽快正常生产。
四、回转窑正常操作:1、转窑正常生产时控制温度:窑头密封罩:~1000oC窑身高温段:1100—1200oC窑尾密封罩:1000—1100oC2、观察固定筛口,有大块及时清除。
回转窑点火烘窑实施细则

回转窑点火烘窑实施细则一、预热器分解炉和窑的煤粉燃烧的细则,具体说明如下:1.烘干材料:柴油、煤粉2.烘干时间:连续烘干144小时左右3.烘干速率:一般温升速度<25℃/小时,升温初期要求速率慢一些,后期可快些,以控制窑尾温度为准。
4.本细则仅考虑了回转窑、预热器和分解炉的烘干,三次风管、篦冷机耐火材料投料后利用余热烘干。
二、升温烘窑1、烘窑升温过程温度控制如下表:温度测点以控制窑尾温度为准,确保砖面温度从常温升至800℃的低温烘烤时间≥72h。
烘窑后期,如遇大雨、暴雨,可开启辅传连续慢转窑。
2、升温曲线如下:3、具体烘窑操作1). 烘窑操作和要求(1). 点火前将三次风阀门开至40%,点火烘窑开始后,在篦冷机用木材烘烤。
(2).用火把点燃燃烧器,将油量调至150-300l/min左右,密切注意窑尾温度变化,和遵守烘窑升温曲线的规定,当窑尾温度小于200℃时,回转窑要每4小时转1/4转,随着窑尾温度的提高,逐渐增加窑的转动次数。
(3).进入烘窑后期阶段,可以转入小开度地打开高温风机和后排风机风门,此时,一级预热器人孔门(四个)则相应关闭。
当C1筒出口温度上升到250℃后,不再调节风门大小,维持到烘窑结束。
(4).在烘烤期间,观察窑头、窑尾密封的运转情况;窑筒体表面温度;托轮的运转情况;窑上、下窜动情况;并进行热态调整。
(5).在烘烤期间,要密切注意预热器分解炉系统各点温度变化情况,要特别注意窑尾和C1筒出口废气温度,严格控制升温速度,防止水分蒸发过快,衬料爆裂。
(6).烘烤期间,是检查窑尾系统密封情况的良好时机,发现有冒黑烟处,应及时封堵。
(7)烘烤结束后,及时排除有关设备内积水,进行设备复位。
(8).检查如未达到烘干要求,应适当延长烘干时间。
(9).待系统烘干结束后,将预热器系统各级旋风筒、上升管道及分解炉顶盖的浇注预留孔封死;将各级排灰阀的平衡杆放下,调整重锤位置,并检查其动作的灵活性。
球团岗位回转窑运行岗位操作规程
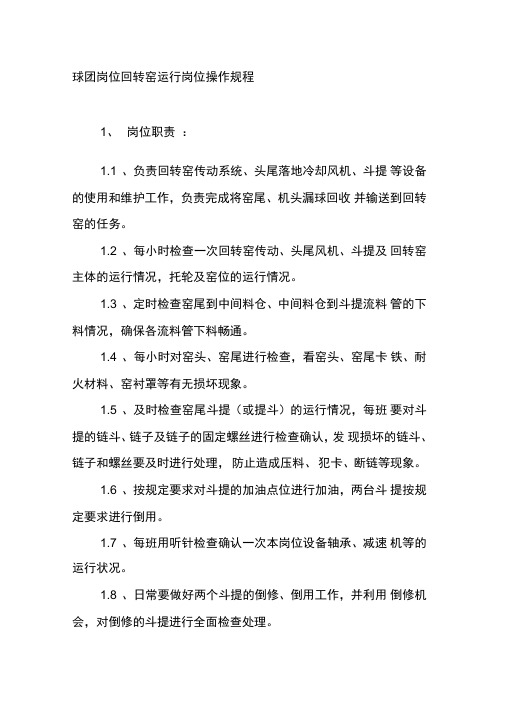
球团岗位回转窑运行岗位操作规程1、岗位职责:1.1 、负责回转窑传动系统、头尾落地冷却风机、斗提等设备的使用和维护工作,负责完成将窑尾、机头漏球回收并输送到回转窑的任务。
1.2 、每小时检查一次回转窑传动、头尾风机、斗提及回转窑主体的运行情况,托轮及窑位的运行情况。
1.3 、定时检查窑尾到中间料仓、中间料仓到斗提流料管的下料情况,确保各流料管下料畅通。
1.4 、每小时对窑头、窑尾进行检查,看窑头、窑尾卡铁、耐火材料、窑衬罩等有无损坏现象。
1.5 、及时检查窑尾斗提(或提斗)的运行情况,每班要对斗提的链斗、链子及链子的固定螺丝进行检查确认,发现损坏的链斗、链子和螺丝要及时进行处理,防止造成压料、犯卡、断链等现象。
1.6 、按规定要求对斗提的加油点位进行加油,两台斗提按规定要求进行倒用。
1.7 、每班用听针检查确认一次本岗位设备轴承、减速机等的运行状况。
1.8 、日常要做好两个斗提的倒修、倒用工作,并利用倒修机会,对倒修的斗提进行全面检查处理。
1.9 、停机检修时,对本岗位的所有设备进行检查,发现问题及时处理。
1.10 、负责本岗位区域的文明生产清理工作,确保区域内无积水、积灰、积油和杂物,设备维护清洁,无油污、机光马达亮。
岗位区域内无跑、冒、滴、漏,发现问题及时进行处理。
2、开停机技术操作规定及方法:2.1 开机前检查2.1.1 回转窑开机前检查:2.1.1 .1、检查回转窑传动系统的油水供给正常,设备周围无人和障碍物。
2.1.1.2 、窑头窑尾密封装置完好,无刮卡现象。
2.1.2 斗提开机前检查:2.1.2.1 、检查电机、减速机、头尾轮轴承符合转动要求,各链斗、链子及固定螺丝完好,没有缺损,斗提内确认无杂物。
2.1.2.2 、检查各下料流槽、中间料仓无杂物,确保下料畅通。
2.2 开停机操作:2.2.1 回转窑:2.2.1.1 、主控室开机接到工长指令T确认设备及周围无人检修、周围无人或障碍物、传动、润滑、冷却系统无误后,将选择开关打到主控开机位置,反馈主控室“可以开机”并在现场监护T运转后反馈主控室。
回转窑开停窑点火操作流程
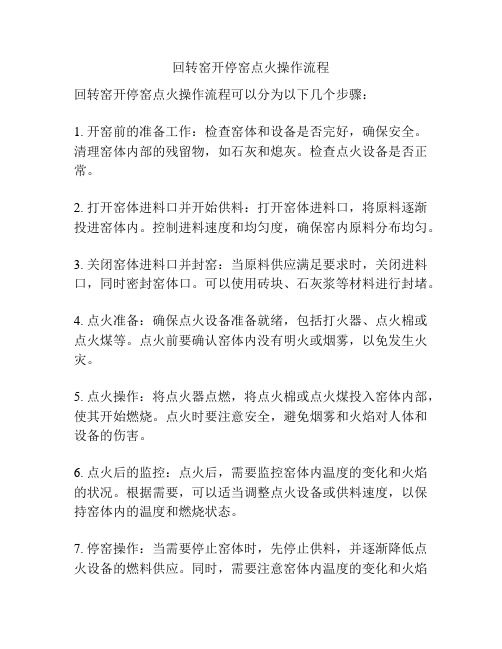
回转窑开停窑点火操作流程
回转窑开停窑点火操作流程可以分为以下几个步骤:
1. 开窑前的准备工作:检查窑体和设备是否完好,确保安全。
清理窑体内部的残留物,如石灰和熄灰。
检查点火设备是否正常。
2. 打开窑体进料口并开始供料:打开窑体进料口,将原料逐渐投进窑体内。
控制进料速度和均匀度,确保窑内原料分布均匀。
3. 关闭窑体进料口并封窑:当原料供应满足要求时,关闭进料口,同时密封窑体口。
可以使用砖块、石灰浆等材料进行封堵。
4. 点火准备:确保点火设备准备就绪,包括打火器、点火棉或点火煤等。
点火前要确认窑体内没有明火或烟雾,以免发生火灾。
5. 点火操作:将点火器点燃,将点火棉或点火煤投入窑体内部,使其开始燃烧。
点火时要注意安全,避免烟雾和火焰对人体和设备的伤害。
6. 点火后的监控:点火后,需要监控窑体内温度的变化和火焰的状况。
根据需要,可以适当调整点火设备或供料速度,以保持窑体内的温度和燃烧状态。
7. 停窑操作:当需要停止窑体时,先停止供料,并逐渐降低点火设备的燃料供应。
同时,需要注意窑体内温度的变化和火焰
的状况,确保窑体内燃烧完全熄灭。
8. 清理工作:在窑体完全冷却后,进行窑体内部的清理工作。
清除残留的物料和灰渣,检查窑体内部设备的状况。
请注意,以上流程仅为一般性描述,实际操作流程可能会因窑体类型、燃烧设备和工艺要求的不同而有所差异。
在进行回转窑开停窑和点火操作过程中,应严格遵守安全操作规程和操作指导,保障人身安全和设备完整性。
球团回转窑工艺流程
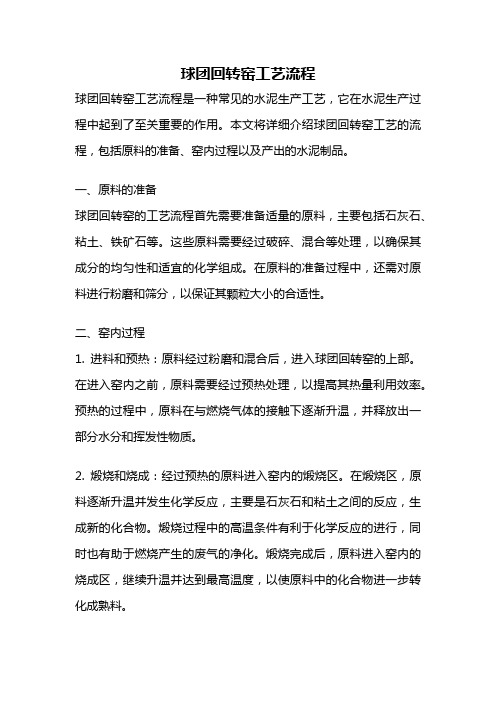
球团回转窑工艺流程球团回转窑工艺流程是一种常见的水泥生产工艺,它在水泥生产过程中起到了至关重要的作用。
本文将详细介绍球团回转窑工艺的流程,包括原料的准备、窑内过程以及产出的水泥制品。
一、原料的准备球团回转窑的工艺流程首先需要准备适量的原料,主要包括石灰石、粘土、铁矿石等。
这些原料需要经过破碎、混合等处理,以确保其成分的均匀性和适宜的化学组成。
在原料的准备过程中,还需对原料进行粉磨和筛分,以保证其颗粒大小的合适性。
二、窑内过程1. 进料和预热:原料经过粉磨和混合后,进入球团回转窑的上部。
在进入窑内之前,原料需要经过预热处理,以提高其热量利用效率。
预热的过程中,原料在与燃烧气体的接触下逐渐升温,并释放出一部分水分和挥发性物质。
2. 煅烧和烧成:经过预热的原料进入窑内的煅烧区。
在煅烧区,原料逐渐升温并发生化学反应,主要是石灰石和粘土之间的反应,生成新的化合物。
煅烧过程中的高温条件有利于化学反应的进行,同时也有助于燃烧产生的废气的净化。
煅烧完成后,原料进入窑内的烧成区,继续升温并达到最高温度,以使原料中的化合物进一步转化成熟料。
3. 冷却和熟料处理:经过烧成后的熟料进入窑内的冷却区,通过冷却气流的流动,熟料逐渐降温。
冷却过程中,熟料的结晶形态逐渐形成,并逐渐凝固成团。
冷却完成后,熟料需要进行破碎和筛分,以得到适合生产水泥的粉状物料。
三、产出的水泥制品经过破碎和筛分后的熟料,即为最终的水泥制品。
水泥制品具有一定的强度和硬度,可以用于建筑材料的生产和施工。
根据需要,水泥制品可以进一步加工,如添加适量的矿渣、石膏等掺合料,以改善水泥的性能和使用效果。
总结:球团回转窑工艺是一种重要的水泥生产工艺,其流程包括原料的准备、窑内过程以及产出的水泥制品。
原料经过破碎、混合、粉磨等处理后,进入窑内进行煅烧和烧成,最终形成熟料。
熟料经过冷却、破碎和筛分后,得到水泥制品,可用于建筑材料的生产和施工。
球团回转窑工艺流程的优点是热量利用率高、燃烧废气净化效果好,但也存在能耗高、对原料成分要求严格等问题,需要进一步改进和优化。
回转窑操作方案
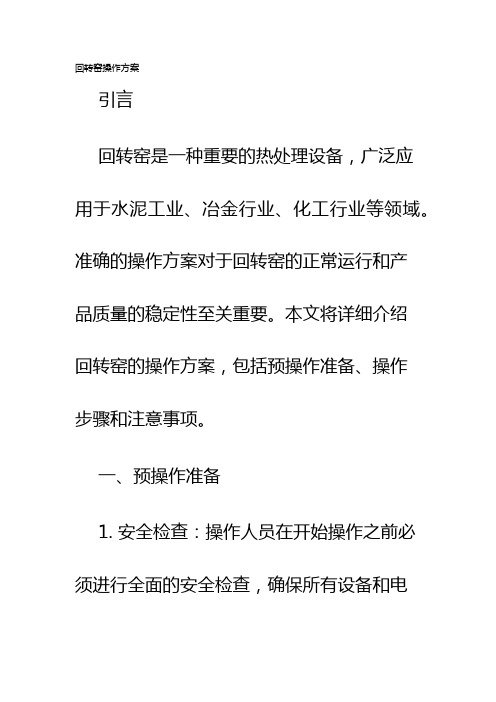
回转窑操作方案引言回转窑是一种重要的热处理设备,广泛应用于水泥工业、冶金行业、化工行业等领域。
准确的操作方案对于回转窑的正常运行和产品质量的稳定性至关重要。
本文将详细介绍回转窑的操作方案,包括预操作准备、操作步骤和注意事项。
一、预操作准备1. 安全检查:操作人员在开始操作之前必须进行全面的安全检查,确保所有设备和电气系统正常工作。
检查各个防护装置的功能是否完好,并确保回转窑周围没有杂物和障碍物。
2. 设备检查:对于回转窑的各个部位,包括传动装置、滚筒、气密性等进行检查,确保各个部位无异常情况。
特别注意回转窑滚筒的磨损情况和承载能力,必要时及时更换。
二、操作步骤1. 开机准备:将回转窑设备的主电源打开,根据操作手册进行调节和设定相关参数。
确保回转窑滚筒的转速和倾角符合操作要求。
2. 上料操作:根据生产计划,将需要处理的原料按照要求进行配料,并通过输送设备将其送入回转窑。
注意保持原料的均匀性,避免出现大块原料或杂质。
3. 启动回转窑:通过仪表板上的操作按钮启动回转窑,确保整个启动过程平稳进行。
根据操作手册上的指示,逐步提高回转窑的转速和倾角。
4. 控制温度:根据生产工艺要求,通过监控回转窑内部的温度变化,及时进行调整。
通过调整燃烧器的喷射位置和燃料供给量来控制炉内的温度。
5. 卸料操作:在生产结束后,根据需要将热处理过的产品从回转窑中卸出。
注意安全,在卸料操作前,确保回转窑内温度降至安全范围,并进行必要的防护措施。
6. 关闭回转窑:在卸出产品后,关闭回转窑设备,将主电源关闭。
三、注意事项1. 安全第一:在操作过程中,必须严格遵守安全规定,佩戴防护设备,不得擅自操作或调整设备。
2. 维护保养:定期检查和维护回转窑设备,及时更换易损件,确保设备的正常运行和寿命。
3. 温度控制:控制回转窑内的温度变化是保证产品质量的关键。
在操作过程中要细心观察温度变化,并及时调整燃烧器和燃料供给量。
4. 原料质量:提前检查原料的质量,避免潜在的问题。
球团链篦机回转窑工艺流程

球团链篦机回转窑工艺流程嘿,朋友们!今天咱来唠唠球团链篦机回转窑工艺流程,这可真是个有趣又重要的玩意儿呢!你想想看,那球团就像一个个小宝贝,得好好地照顾它们,让它们经历一系列神奇的过程,最后变成有用的东西。
先来说说链篦机这一块儿。
就好像是一个大操场,球团们在这儿排好队,开始它们的旅程。
链篦机慢慢地带着它们往前走,就像带着一群小朋友去探险。
在这个过程中,球团们会被加热,就像给它们洗了个温暖的热水澡,让它们变得精神起来。
然后呢,这些热乎乎的球团就来到了回转窑。
回转窑就像是个大魔术箱,球团们一进去,哇塞,各种奇妙的变化就发生了。
它们在里面翻滚、跳跃,被进一步地加工和处理。
这就好比是小宝贝们在学校里学习知识,不断成长和进步。
在回转窑里,温度那可是相当高啊,就跟夏天里的大太阳似的。
但球团们可不怕,它们坚强着呢!它们在里面接受着高温的考验,一点点地变得更加强壮。
经过回转窑的洗礼,球团们就变得不一样啦!它们变得更加坚硬、更加有价值。
这就好像是丑小鸭变成了白天鹅,让人刮目相看。
你说这整个工艺流程是不是特别神奇?就像变魔术一样,把普普通通的球团变成了对我们有用的东西。
咱再想想,如果没有这个工艺流程,那我们好多东西都没办法生产出来啦。
那建筑要用的材料从哪里来?那钢铁厂要用的原料又从哪里来?所以说啊,球团链篦机回转窑工艺流程可真是太重要啦!它就像是一个默默奉献的大功臣,虽然我们平时可能不太注意它,但它却一直在为我们的生活和社会的发展贡献着自己的力量。
我们应该好好珍惜这个工艺流程,好好地维护它,让它能一直为我们服务。
毕竟,它可是我们生活中不可或缺的一部分呢!不是吗?这就是球团链篦机回转窑工艺流程,一个充满魅力和神奇的领域,等着我们去探索和发现!。
回转窑技术方案

回转窑技术方案1. 引言回转窑技术是一种常用于水泥生产过程中的高效能熟料烧成设备。
它利用回转窑转筒的旋转运动,将原料在高温下进行烧结和冶炼,从而产生出高质量的水泥熟料。
本文旨在介绍回转窑技术的原理、特点、优势以及应用范围,为相关从业者提供技术方案的参考。
2. 原理与工艺回转窑是一种长而呈横圆筒形的设备,通常由燃烧装置、回转筒、支撑装置、封堵装置等组成。
其工艺流程包括下列几个步骤:2.1. 原料进料原料以恒定的流量从回转窑的一端进入,并沿着回转筒的轴向逐渐移动。
原料的类型和比例决定了最后产品的特性。
2.2. 预热原料在回转筒中被加热至适宜的升温速率。
这一步骤有助于除去原料中的挥发性成分,提高热效率。
2.3. 煅烧在经过预热后,原料进入到煅烧区域。
高温下,原料中的矿物质发生化学反应并达到烧结状态,形成熟料。
2.4. 冷却熟料从煅烧区域向回转筒的另一端移动,同时被冷却气体吹拂。
冷却气体通过与熟料的热交换,将熟料冷却至环境温度。
2.5. 产品出料冷却后的熟料从回转窑的出料端倾倒出来,并经过粉碎、筛分等工序后,成为最终的水泥产品。
3. 回转窑技术的特点和优势回转窑技术具有以下几个显著的特点和优势:3.1. 高热效率回转窑技术利用燃烧装置产生的高温气流,在整个燃烧和煅烧过程中对原料进行加热。
通过合理的燃烧设备和热交换系统设计,回转窑能够实现高热效率,充分利用燃料的能量,减少热损失。
3.2. 稳定的产品质量回转窑技术能够控制煅烧过程中的温度、气氛和停留时间等参数,确保原料得到充分的煅烧和烧结,从而保证产品质量的稳定。
此外,由于原料在回转筒内的持续运动,实现了热量的均匀分布,避免了产品中的过烧或欠烧等问题。
3.3. 灵活的适应性回转窑技术能够适应多种原料和产品的要求。
在原料的选择和比例调整上具有一定的灵活性,可用于烧制不同种类的水泥熟料。
此外,通过进料端和出料端的设计和调整,回转窑可适应不同生产规模的需求。
3.4. 环保与节能回转窑技术采用了先进的燃烧和热交换技术,能够有效控制燃料的使用量和排放物的含量。
球团矿回转窑工艺流程

球团矿回转窑工艺流程The rotary kiln process in the pellet plant is a crucial and complex operation that plays a significant role in the production of iron ore pellets. This process involves the continuous rotation of a large cylindrical kiln, where iron ore is heated to high temperatures and transformed into pellets. The success of this process is essential tothe overall efficiency and productivity of the pellet plant.球团厂的回转窑工艺是一个至关重要且复杂的操作,它在铁矿球团的生产中起着重要作用。
这一过程涉及将铁矿连续加热至高温,并转变成球团的大型圆筒窑的持续旋转。
这一工艺的成功对球团厂的整体效率和生产力至关重要。
First and foremost, the rotary kiln process requires precise control and monitoring to ensure the quality of the iron ore pellets. Temperature, speed, and airflow are critical parameters that must be carefully regulated to avoid inconsistencies in the pellet formation. Any deviation in these factors can lead to defective pellets and impact the overall production output.首要的是,回转窑工艺需要精确的控制和监测,以确保铁矿球团的质量。
- 1、下载文档前请自行甄别文档内容的完整性,平台不提供额外的编辑、内容补充、找答案等附加服务。
- 2、"仅部分预览"的文档,不可在线预览部分如存在完整性等问题,可反馈申请退款(可完整预览的文档不适用该条件!)。
- 3、如文档侵犯您的权益,请联系客服反馈,我们会尽快为您处理(人工客服工作时间:9:00-18:30)。
回转窑中修升温方案
为了保护窑衬和开机一次成功,特制定此升温方案。
要求各级人员严格按要求落实各项工作,保证升温开机一次成功。
一、升温准备:
1、点火前窑衬、环冷机内衬、链蓖机侧墙等验收合格。
2、点火前重点对窑头下料口、窑尾灰斗、链蓖机水平管道、各风箱内和灰斗内的施工积料全部清理干净。
3、柴油站油泵试车正常,主枪清理试喷,油雾化良好。
4、各冷却部位通水、通风正常。
5、各部计量、仪表、电偶及工艺尺寸达到标准要求。
6、制粉系统具备正常生产条件,塔楼提前备好煤粉,并试喷正常。
7、提前联系好5吨烘炉木材和柴油。
8、点火前组织各系统设备的全面试车工作,达到设备稳定运转的条件。
9、点火前各岗位人员全部上岗。
10、点火前做好煤、精矿粉、皂土等原燃料准备,保证开炉的正常需要。
二、烘炉:
烘炉时,以窑中热电偶为准,并处于正上方。
为保护窑衬,根据窑衬材质的特性和检修工期的要求,窑衬砌筑完成后,开始进行自然养生1天,然后,进行木柴烘炉24小时,之后回
转窑正式点火。
升温安排5天。
三、烘炉操作要求:
1、窑衬砌筑完毕后,自然养生1天,养生期间窑门全开,开链蓖机放散。
每两小时转1/4圈。
2、此次链蓖机侧墙、回转窑内衬、环冷机内衬、各热风管道基本为新更换耐火材料。
为保证浇注料中的水分均匀缓慢的充分蒸发,防止水分蒸发过快造成捣打料剥落,对链蓖机、回转窑、环冷机都进行木柴烘炉,时间控制在24小时之内,点位分别为:链蓖机预热段1堆、回转窑窑头1堆、窑内后部间隔均匀放3堆,环冷机三个段各一堆。
木柴烘炉时,各风机蝶阀打开,不开主引风机,关闭窑门,开链蓖机放散。
3、严格按升温制度规定进行升温,设备问题影响时,按时间顺延。
4、木柴烘炉结束后,正式点火时窑中热电偶在正上方,点火8小时后,落链蓖机放散,打开引风、耐热管道上的相应的蝶阀,开主引风机,风量控制在20万米3/小时,电除尘暂不送电,待回转窑停止喷油并达到规定温度时,再启动电除尘。
5、点火22小时内,回转窑每小时转1/3圈,22小时后,
用辅机进行连续转窑,窑内高温点在600℃以上时进行主机转窑,窑速0.3转/分。
6、烟罩高温点温度达到200℃时,链蓖机以最低机速连续慢转。
7、在升温过程中,尽早实现油煤混喷,根据温度需要,适当减低油压。
四、开机:
1、烟罩温度达到100℃时,由作业长组织原料上料及生球的准备,生球质量达到技术标准要求。
2、烟罩温度350℃时开始链蓖机布料,料厚控制在165±5mm,并同时开启两台耐热风机,烟罩温度到600℃以上时,每10分钟转9个链节,800℃以上时组织开机,机速0.87米/分。
五、开机后加料制度:
本次开机后,采用逐步恢复正产生产进行组织,三天后恢复正常生产,具体要求如下:
1、开机后的第一天:
机速:0.87米/分,料厚165±5mm。
2、开机后的第二天:
①前12小时:
机速:1.2米/分,料厚165±5mm。
②后12小时:
机速:1.4米/分,料厚165±5mm
3、开机后的第三天:
①前12小时:
机速:1.6米/分,料厚175±5mm。
②后12小时:
机速:1.6-1.8米/分,料厚175±5mm
4、开机后的第四天:
机速:1.8-2.0米/分,料厚175±5mm。
②从后12小时开始:按正产生产进行组织。
5、根据具体情况合理调整耐热、引凤风量和窑速,窑速以保证窑尾不倒料为准。
六、其他:
未做说明的严格按工艺技术规程规定执行。
要求升温过程中密切注意窑衬的变化,发现异常立即汇报。