浅述微涡流反应器
微界面反应器工作原理

微界面反应器工作原理
微界面反应器是一种利用微结构技术和微流体技术的化学反应设备,其工作原理主要包括以下几个方面:
1. 微流体控制:微界面反应器通过微流通道的设计和控制,使流体在微尺度下控制流动。
微流体控制能够实现流体的快速混合、加热和冷却等操作,从而提高反应速率和效率。
2. 大比表面积:微界面反应器的微结构和微流通道设计使得反应液体与固体催化剂或界面活性剂之间的接触面积大大增加。
增加接触面积有利于反应物质间的传质和反应速率,从而提高反应效率。
3. 传质控制:微界面反应器中的流体传质过程主要由扩散和对流传质两种方式组成。
微界面反应器的设计可以通过微流通道的尺寸和形状调控扩散和对流传质的比例,从而实现传质过程的控制。
4. 温度控制:微界面反应器由于其微流体特性,使得温度调控更加精确和均匀。
可以通过微热电偶等传感器实时监测温度,并根据需要控制加热或冷却,从而实现对反应温度的精确控制。
总体来说,微界面反应器利用微流体和微结构技术的优势,通过微流体控制、大比表面积、传质控制和温度控制等原理,提高了反应速率和效率,实现了反应过程的精细控制,并在化学合成、催化反应等领域具有广阔的应用前景。
微通道反应器基础知识

一、了解微通道反应器微通道反应器介绍微通道反应器本质上讲是一种连续流动的管道式反应器。
它包括化工单元所需要的混合器、换热器、反应器控制器等。
目前,微通道反应器总体构造可分为两种:一种是整体结构,这种方式以错流或逆流热交换器的形式体现,可在单位体积中进行高通量操作。
在整体结构中只能同时进行一种操作步骤,最后由这些相应的装置连接起来构成复杂的系统。
另一种是层状结构,这类体系由一叠不同功能的模块构成,在一层模块中进行一种操作,而在另一层模块中进行另一种操作。
流体在各层模块中的流动可由智能分流装置控制对于更高的通量,某些微通道反应器或体系通常以并联方式进行操作。
二、微通道反应器的原理微反应器主要是指以表面科学与微制造技术为核心,经过微加工和精密技术制造的一种多通道微结构小型反应器,而微反应器的通道尺寸仅有亚微米和亚毫米级别。
除此以外因为微反应器有优于传统化工设备1-3个数量级的传热/传质特性,所以特别适合做高放热和快速反应的实验。
而微反应器原理想必很多人都想了解一下.微化工技术思想源自于常规尺度的传热机理。
对于圆管内层流流动,管壁温度维持恒定时,由公式(1)可见,传热系数h与管径d成反比,即管径越小,传热系数越大;对于圆管内层流流动,组分A在管壁处的浓度维持恒定时,传质系数kc与管径成反比(公式(2)),即管径越小,传质系数越大。
由于微通道内流动多属层流流动,主要依靠分子扩散实现流体间混合,由公式(3)可知,混合时间t与通道尺度平方成正比。
通道特征尺寸减小不仅能大大提高比表面积,而且能大大强化过程的传递特性。
Nu = hd∕k=3.66(l)Sh = kc∕DAB=3.66 ⑵t=d 2/DAB⑶其中NU为努塞尔数、Sh为谢伍德数、D为扩散系数。
化工过程中进行的化学反应受传递速率或本征反应动力学控制或两者共同控制。
就瞬时和快速反应而论,在传统尺度反应设备内进行时,受传递速辛控制,而微尺度反应系统内由干传递速率呈数量级提高,因此这类反应过程速率将会大幅度提高;如氧碘化学激光器中的激发态氧发生器(氯气用双氧水碱溶液反应)、烧类直接氟化。
涡流反应器及其在即墨市南水厂的应用
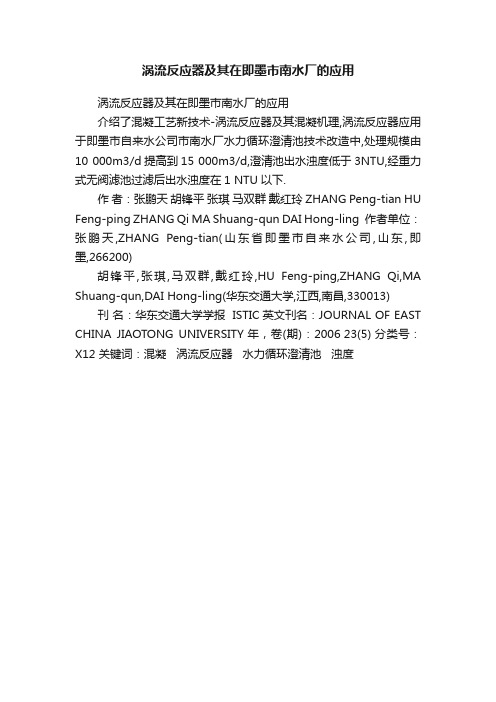
涡流反应器及其在即墨市南水厂的应用
涡流反应器及其在即墨市南水厂的应用
介绍了混凝工艺新技术-涡流反应器及其混凝机理,涡流反应器应用于即墨市自来水公司市南水厂水力循环澄清池技术改造中,处理规模由10 000m3/d提高到15 000m3/d,澄清池出水浊度低于3NTU,经重力式无阀滤池过滤后出水浊度在1 NTU以下.
作者:张鹏天胡锋平张琪马双群戴红玲 ZHANG Peng-tian HU Feng-ping ZHANG Qi MA Shuang-qun DAI Hong-ling 作者单位:张鹏天,ZHANG Peng-tian(山东省即墨市自来水公司,山东,即墨,266200)
胡锋平,张琪,马双群,戴红玲,HU Feng-ping,ZHANG Qi,MA Shuang-qun,DAI Hong-ling(华东交通大学,江西,南昌,330013) 刊名:华东交通大学学报 ISTIC英文刊名:JOURNAL OF EAST CHINA JIAOTONG UNIVERSITY 年,卷(期):2006 23(5) 分类号:X12 关键词:混凝涡流反应器水力循环澄清池浊度。
微涡流絮凝反应器设计原理

微涡流絮凝反应器设计原理微涡流絮凝反应器是一种用于液相混合反应的装置,其设计原理基于微涡流技术。
微涡流技术是一种通过引入微观尺度的涡流场来增强反应的传质和传热效果的方法。
微涡流絮凝反应器利用微涡流技术来提高反应效率和产品质量。
微涡流絮凝反应器的设计原理主要包括两个方面,即微涡流的产生和絮凝反应的进行。
微涡流的产生是通过合理设计反应器的结构来实现的。
在微涡流絮凝反应器内部,通常有多个切向进口,用来引入反应物和溶剂。
这些切向进口会在反应器内部形成旋涡流场,从而产生微涡流。
同时,反应器内部还有一系列的结构设计,如螺旋状结构、分层结构等,用来增加涡流的强度和稳定性。
这些结构的合理设计可以使微涡流得到有效增强,从而提高反应的传质和传热效果。
微涡流絮凝反应器的设计原理还包括絮凝反应的进行。
絮凝是指将微小的悬浮颗粒聚集成较大颗粒的过程。
在微涡流絮凝反应器中,反应物通常是以溶液的形式存在,其中含有微小的悬浮颗粒。
这些微小的悬浮颗粒在微涡流的作用下,会发生聚集和沉降,从而形成较大的絮凝体。
絮凝的过程主要受到两种力的作用,即聚集力和分散力。
聚集力会使颗粒聚集在一起,形成絮凝体,而分散力则会使颗粒分散开来。
微涡流絮凝反应器利用微涡流的流场来增强聚集力,并抑制分散力的作用,从而促进絮凝反应的进行。
通过合理设计微涡流絮凝反应器的结构和调控微涡流的流场,可以实现反应物的快速混合和絮凝反应的高效进行。
微涡流技术可以大大提高反应的传质和传热效果,从而提高反应速率和产品质量。
此外,微涡流絮凝反应器还具有体积小、能耗低、操作简便等优点,适用于多种液相混合反应的领域。
微涡流絮凝反应器的设计原理基于微涡流技术,通过合理设计反应器的结构和调控微涡流的流场来实现反应物的快速混合和絮凝反应的高效进行。
微涡流技术可以大大提高反应的传质和传热效果,从而提高反应速率和产品质量。
微涡流絮凝反应器具有广泛的应用前景,将在化工、生物工程、环境工程等领域发挥重要作用。
微反应器工作原理

微反应器工作原理微反应器是一种在微观尺度下进行化学反应的装置。
它利用微流控技术将反应物料以微滴或薄膜的形式进行加工和流动控制,从而实现反应的快速、高效和精确控制。
微反应器的工作原理主要包括微流控技术、微观尺度和加工控制三个方面。
微反应器利用微流控技术对反应物料进行流动控制。
微流控技术是一种通过微型通道和微型阀门来控制流体的流动的技术。
微反应器中的微流控通道可以精确地控制反应物料的流动速度、流动方向和混合程度,从而实现反应物料的快速混合和反应。
微反应器利用微观尺度来增加反应速度和效率。
由于微反应器中的反应物料以微滴或薄膜的形式存在,相比传统的宏观尺度反应器,微反应器具有更大的比表面积和更短的传质距离。
这使得反应物料能够更快速地进行反应,从而提高反应速度和效率。
微反应器通过加工控制来实现反应的精确控制。
微反应器中的微流控通道和微阀门可以精确地控制反应物料的流动速度和混合程度,从而实现反应的精确控制。
此外,微反应器还可以通过调节温度、压力和反应时间等参数来实现反应条件的精确控制,从而实现对反应产物的选择性合成。
微反应器的工作原理可以通过以下步骤来描述。
首先,反应物料通过进料口进入微反应器中的微流控通道。
然后,根据需要,可以通过微阀门来控制反应物料的流动速度和混合程度。
在微流控通道中,反应物料会快速混合并进行化学反应。
最后,反应产物通过出料口排出微反应器。
微反应器具有许多优点。
首先,由于微反应器可以实现反应物料的快速混合和反应,因此可以大大缩短反应时间,提高反应速度和效率。
其次,微反应器可以实现对反应条件的精确控制,从而实现对反应产物的选择性合成。
此外,由于微反应器的微观尺度和微流控技术的应用,反应物料的用量可以大大降低,从而减少了废物的产生,有利于环境保护。
微反应器在许多领域都有广泛的应用。
例如,微反应器可以用于药物合成、有机合成、催化反应、生物反应等领域。
在药物合成中,微反应器可以实现对药物合成过程的精确控制,从而提高药物的纯度和产率。
微反应器的原理
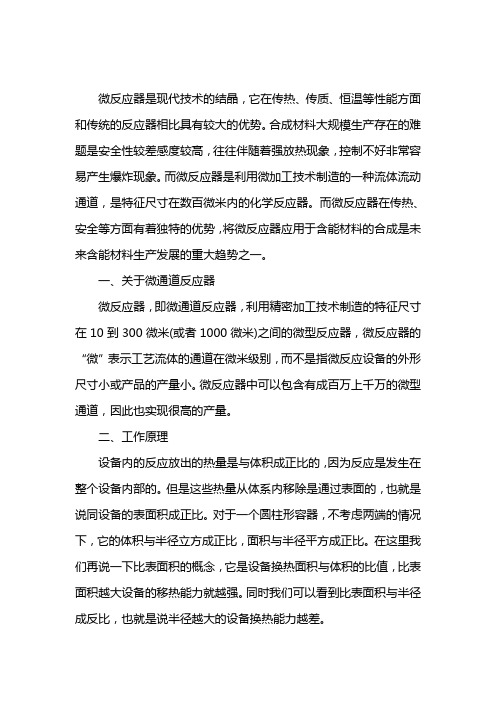
微反应器是现代技术的结晶,它在传热、传质、恒温等性能方面和传统的反应器相比具有较大的优势。
合成材料大规模生产存在的难题是安全性较差感度较高,往往伴随着强放热现象,控制不好非常容易产生爆炸现象。
而微反应器是利用微加工技术制造的一种流体流动通道,是特征尺寸在数百微米内的化学反应器。
而微反应器在传热、安全等方面有着独特的优势,将微反应器应用于含能材料的合成是未来含能材料生产发展的重大趋势之一。
一、关于微通道反应器微反应器,即微通道反应器,利用精密加工技术制造的特征尺寸在10到300微米(或者1000微米)之间的微型反应器,微反应器的“微”表示工艺流体的通道在微米级别,而不是指微反应设备的外形尺寸小或产品的产量小。
微反应器中可以包含有成百万上千万的微型通道,因此也实现很高的产量。
二、工作原理设备内的反应放出的热量是与体积成正比的,因为反应是发生在整个设备内部的。
但是这些热量从体系内移除是通过表面的,也就是说同设备的表面积成正比。
对于一个圆柱形容器,不考虑两端的情况下,它的体积与半径立方成正比,面积与半径平方成正比。
在这里我们再说一下比表面积的概念,它是设备换热面积与体积的比值,比表面积越大设备的移热能力就越强。
同时我们可以看到比表面积与半径成反比,也就是说半径越大的设备换热能力越差。
换热能力这在化工中对工艺的影响也是明显的。
比如说酸碱中和反应,比如说用烧碱中和硫酸。
工厂里做这个操作可能需要半个小时到一个小时的时间,实际上这个反应很快,大概在毫秒级。
但是这个反应放热,必须要把热量移走,因此在工厂里面只能一点一点的把烧碱加到反应釜里,然后反应釜用冷却水冷却。
烧碱的加料速度完全取决于反应釜的移热能力,反应本身可以很快,你可以一下吧烧碱全部加进去,但是放热问题解决不了,溶液会升温甚至沸腾,非常危险。
如果有有一个设备能够瞬间把反应热移走,那么烧碱就可以快速加入,节省大量操作时间。
这就是微通道的意义,我们可以把通道做的很小,然后让一些放热非常强的反应也可以安全快速地进行。
高密度和微涡反应器的原理、功能、优劣、特点和应用

1.高密度反应器1.1高密度反应器简介高密度澄清技术是采用泥渣循环的高密度沉淀处理技术,适用于饮用水生产、污水处理、工业废水处理和污泥处理等领域。
每座高密度沉淀池工艺区域包括凝聚反应区、絮凝反应区、沉淀区、集水区、污泥循环设备、污泥排放设备等,各区域功能如下:(1)反应区反应区分为两个部分:快速混凝搅拌反应池和慢速混凝搅拌反应池。
前者可以使反应池内水流均匀混合,并为絮凝和聚合电解质的分配提供所需的动能;后者可以产生扫粒絮凝,以获得较大的絮状物,达到沉淀区内的快速沉淀。
(2)预沉区/浓缩区为避免冲碎已形成的较大絮状物,已形成的絮状物通过一个较宽的进水口流到沉淀区。
为取得更好的沉淀效果,可在沉淀区内设置异向流斜管,并在集水区内的每个集水槽底部设隔板,把斜管部分分成几个单独的水力区,保证斜管下面的水力平衡。
(3)斜管分离区在逆流式斜管沉淀区沉淀剩余的矾花。
通过固定在清水收集槽下侧的纵向板进行水力分布。
澄清水由一个集水槽系统回收。
絮凝物堆积在澄清池的下部,形成的污泥也在这部分区域浓缩,通过刮泥机将污泥收集起来,循环至反应池入口处,剩余污泥排放。
1.2高密度混凝机理(1)内筒循环和污泥回流产生均质的絮凝体和高密度的矾花水流在内筒和外筒之间循环的独特设计,加大了絮体的水力停留时间;浓缩区上部的污泥回流,增大了反应区中絮体颗粒的碰撞几率。
由此形成的高密度矾花具有优良的絮凝沉降性能和良好的抗冲击性能。
(2)推流式反应池至沉淀池之间的慢速传输絮凝区和沉降区的平稳结合过渡,使絮凝后的水平稳慢速地进入沉降区,大部分絮体在进入斜管前就已经沉降,通过斜管后可进一步降低浊度。
1.3 高密度反应器工艺特点(1) 独特的一体化反应区和水流内筒循环设计,提高了混凝效率。
(2) 增加了污泥回流装置,提高了反应区污泥的絮凝能力。
(3) 絮凝区与沉淀区分离且流速变化平缓,增大了污泥沉降几率。
根据半生产性试验,斜管区上升流速可达6mm/s,超过了斜管沉淀池和机加池,效果更好,占地更小。
反应设备--微反应器剖析共20页文档

▪
30、意志是一个强壮的盲人,倚靠在明眼的跛子肩上。——叔本华
谢谢!
20
▪
26、要使整个人生都过得舒适、愉快,这是
▪
27、只有把抱怨环境的心情,化为上进的力量,才是成功的保证。——罗曼·罗兰
▪
28、知之者不如好之者,好之者不如乐之者。——孔子
▪
29、勇猛、大胆和坚定的决心能够抵得上武器的精良。——达·芬奇
反应设备--微反应器剖析
•
6、黄金时代是在我们的前面,而不在 我们的 后面。
•
7、心急吃不了热汤圆。
•
8、你可以很有个性,但某些时候请收 敛。
•
9、只为成功找方法,不为失败找借口 (蹩脚 的工人 总是说 工具不 好)。
•
10、只要下定决心克服恐惧,便几乎 能克服 任何恐 惧。因 为,请 记住, 除了在 脑海中 ,恐惧 无处藏 身。-- 戴尔. 卡耐基 。
微反应器

基本结构:
微反应器在结构上常采用一种层次结构方式, 它先以亚单元形成单元,再以单元来形成更大 的单元,以此类推。这种特点与传统化工设备不 同 , 它便于微反应器以‘数增放大’的方式 ( 而 不是传统的尺度放大方式),来对生产规模进行 方便的扩大和灵活的调节。
常用材料:
材料的选择取决于介质和工况等因素,如介质的腐蚀性能、操作温 度、操作压力等,且影响着加工方法的选取,因为对于不同材料而言
①小试工艺不需中试可以直接放大:精细化工行业多
数使用间歇式反应器。小试工艺放大到大的反应釜,由于 传热传质效率的不同,工艺条件一般都要通过实验来修改 以适应大的反应器。一般的流程都是:小试→中试→大生
产。而利用微反应器技术进行生产时,工艺放大不是通过
增大微通道的特征尺寸,而是通过增加微通道的数量来实 现的。所以小试最佳反应条件不需要做任何改变就可以 直接进入生产。因此不存在常规反应器的放大难题。
微反应器适合的反应类型:
①放热剧烈的反应; ②反应物或产物不稳定的反应; ③对反应物配比要求很严的快速反应;
④危险化学反应以及高温高压反应;
⑤纳米材料及需要产物均匀分布的颗粒形成反
应或聚合反应。
实例: 一个释放氮气的快速反应
这 是药 物合成中的一个 反应 。反应产 物除了主产 物 外,还 生成氮气。反应 放热剧 烈,一旦温度控制不好, 就会短时间释放大量氮气而引起冲料。
④物料以精确配比瞬间混合:对于那些对反应物料配
比要求很精确的快速反应,如果搅拌不好,就会在局部出现 配比过量,产生副产物,在常规反应器中几乎无法避免,而微 反应器的反应通道一般只有数十微米,可以精确按配比混
合,避免副产物生成。
⑤结构保证安全性:由于换热效率极高,即使反应突然释
日常如何使用微流反应器,方法

日常如何使用微流反应器,方法微流反应器是一种用于微小流体体积反应的设备。
它是一种微型化的化学反应器,通常用于在微流体下进行化学合成、生物学实验和化学反应工艺等领域的研究。
该反应器通常由微量的通道系统和反应室构成,其中反应室通常采用微型或纳米尺度尺寸,以保持高比表面积和高局部浓度的反应物。
微流反应器的主要优点是可以控制和调节反应的温度、压力、物质浓度和反应时间等条件,并且可以在短时间内实现高效的混合和传质,从而提高反应效率和选择性。
此外,反应器还具有体积小、易于自动化和集成化等特点,可以减少废弃物的产生和提高反应的可持续性。
今天,我将向您介绍如何在日常实验中使用反应器。
首先,我们需要准备要使用的微流反应器、化学试剂、溶剂和其他实验器材。
在准备过程中,需要保持实验环境干净整洁,并正确地处理危险废物。
其次,要确保微流反应器的使用程序合理并且严格按照操作说明书的要求执行。
例如,需要控制反应器的温度、流速和压力等操作参数,以确保反应的效果和产物的质量。
此外,需要注意反应器中的反应物含量,过低的反应物含量可能导致反应效率低下,而过高的反应物含量可能会导致副产物的生成。
在使用反应器期间,我们需要不断地观察和记录反应过程中产生的数据。
例如,可以使用吸光光度计或质谱仪等实验仪器来记录反应物浓度、反应速率和产物结构等数据。
同时,我们也需要对反应产物进行分离和提纯,以确保产物质量符合实验要求。
在完成实验后,我们需要及时清理反应器,并正确地处理废弃物和实验器材。
需要注意的是,由于反应器常常涉及有机溶剂和危险废物,因此必须遵守有关安全和环境保护的规定。
总之,有效地使用微流反应器需要我们掌握正确的操作技术和实验方法,严格遵守操作规程,注意安全和环保,以获取高效、快速、高选择性和低副产物的反应结果。
微型化学反应器的研究

微型化学反应器的研究化学反应器是一种将化学反应物质转化成所需反应产物的设备。
在化学工业中,常常需要大规模的反应器,但是特殊的需要则会考虑使用微型尺寸的化学反应器。
微型化学反应器的特点是尺寸小、效率高,能够更快速地完成反应,也可以实现高度集成化的生产。
近年来,微型化学反应器的研究被广泛关注。
由于微米尺寸的反应器具有高效、快速和成本低等优点,因而被认为是未来化工领域重要的研究和发展方向。
微型化学反应器可不仅仅体积小,它的内腔可以在纳米尺度进行流动反应,反应物质更充分,反应速度更快。
同时,微通道反应器还可能存储于硅片中,实现高度集成化并简化反应操作,还可以降低危险品使用的风险,具有高度的安全性。
微型尺寸的化学反应器有很多应用方向,例如药物合成、化学发光、化学传感等领域,可以实现安全、高效、快速的反应过程,减少了反应物质的用量、减轻了环境的污染、降低了成本和风险,并且还能够生产出更加纯净的产物。
因此,对于化学反应的研究和开发有着重要的意义。
微型化学反应器的研究,本质上是一种新的化学反应技术,涉及物理学、化学、机械学等多个学科,需要多方面的技术支持。
目前,关于微型化学反应器的研究一直处于快速发展期,其应用前景也越来越受到重视,这将有助于化学反应技术的创新和进一步发展。
微型化学反应器的研究还在不断深入,除了考虑反应器尺寸之外还需要考虑如何控制反应进程,同时保证反应器在一个较长的时间内可靠的运转,并且达到理想的反应效果。
对于微型化学反应器的控制方法和技术发展也是研究的一个重要方向。
总之,微型化学反应器研究是未来重要的研究方向,它可以实现微观尺寸下的快速、高效,更加纯净的化学反应,有着广泛的应用前景。
随着相关技术的不断发展,微型化学反应器的应用将会日益深入,为化学工业的进一步发展提供强大的支撑力。
微流场 微通道 反应器

微流场微通道反应器什么是微流场微通道反应器?微流场微通道反应器是一种使用微流体技术进行化学反应的装置。
它利用微米级的通道及流场,将反应物料置于微通道内,通过微观尺度下的传质、传热与反应,实现高效、快速的反应过程。
与传统的化学反应器相比,微流场微通道反应器具有体积小、快速、高效、可控性强等特点,被广泛应用于催化反应、有机合成、生物分析等领域。
微流场微通道反应器的工作原理是什么?微流场微通道反应器主要包括微通道结构、进料装置、反应控制装置以及收集装置等组成。
首先,将反应物料通过进料装置引入微通道内,然后利用微通道结构的特殊设计,控制反应物料流动速度、温度、浓度等参数。
由于微通道的尺寸小,流体在通道内的流动速度相对较高,从而促进了传质和传热的强化,提高了反应速率。
与传统的反应器相比,微通道内流体的混合效果更加均匀,反应物料更充分地接触、反应,并大大减少了副反应的产生。
最后,在收集装置中收集反应产物,完成整个反应过程。
微流场微通道反应器与传统反应器的区别有哪些?微流场微通道反应器与传统反应器相比,在尺寸、操作方式、反应速率等方面存在较大的差异。
首先,微流场微通道反应器体积较小,通道内的液体体积也很小,因此需要的反应物料和催化剂的量也相对较少,从而降低了成本。
其次,微流场微通道反应器的反应速率较快,主要得益于微通道的小尺寸,提高了传质和传热效率,使得反应物料在短时间内完成反应过程。
此外,微流场微通道反应器还具有可控性强的优点,通过对微通道结构的设计和调整,可以对反应参数进行精确控制,实现对反应过程的灵活操作。
与传统反应器相比,微流场微通道反应器不仅节省了成本和时间,而且可以提高产物的纯度和收率。
微流场微通道反应器的应用前景如何?微流场微通道反应器作为一种新型的化学反应装置,具有广阔的应用前景。
首先,在催化反应领域,微通道的小尺寸使得催化剂与反应物料接触更充分,降低了传质阻力,提高了反应速率,有利于提高催化反应的效率。
微通道反应器低温制冷机半导体水冷机

微通道反应器低温制冷机半导体水冷机微通道反应器是一种在微观尺度上进行化学反应的装置,它具有小体积、高效率和快速传热的特点。
而在微通道反应器中,温度的控制对于反应的进行起着至关重要的作用。
传统的制冷机往往不能满足微通道反应器对于低温的要求,因此半导体水冷机成为了一个新的解决方案。
本文将会对微通道反应器、低温制冷机和半导体水冷机的原理和应用进行详细的探讨,希望能给读者一个全面的了解。
一、微通道反应器的特点及应用微通道反应器又称为微型反应器,是一种小型化的化学反应装置。
其内部由许多微小的通道组成,使得反应物与催化剂之间的接触面积增大,传热和传质效果显著。
微通道反应器具有下列特点:1.小尺寸:微通道反应器的尺寸通常比传统反应器小很多,可以实现微型化生产。
2.高效率:微通道反应器将传统的反应器中的反应物体系置于微通道中,使其与催化剂之间的接触面积增加,从而提高反应的效率。
3.快速传热:由于微通道反应器内部的微通道尺度较小,故传热速度很快,反应温度可以很快达到。
微通道反应器广泛应用于化学合成、催化剂评价和化学反应动力学等领域,其小尺寸和高效率的特点使其在化工领域有着更广泛的应用前景。
二、低温制冷机的原理和应用低温制冷机是一种用途广泛的制冷设备,其主要原理是通过压缩机将低温制冷剂压缩,使其温度升高,然后通过换热器给环境散热,从而使冷却剂的温度下降。
低温制冷机的应用范围非常广泛,如工业生产中的冷冻设备、医药领域的制药设备、科研实验中的制冷需求等。
在化学反应领域,低温制冷机也扮演着重要的角色,特别是在需要进行低温反应的情况下,低温制冷机是不可或缺的。
低温制冷机通常分为蒸发式和液氮制冷机两种,其中蒸发式制冷机适用于较高温度的制冷需求,而液氮制冷机则适用于极低温度的制冷需求,两者各有优缺点,可根据实际需求进行选择。
三、半导体水冷机的原理和应用半导体水冷机是一种新型的制冷设备,其工作原理是利用半导体材料的P-N结构来实现热电效应,通过电流来控制温度。
新型微流控反应器的设计及其应用研究
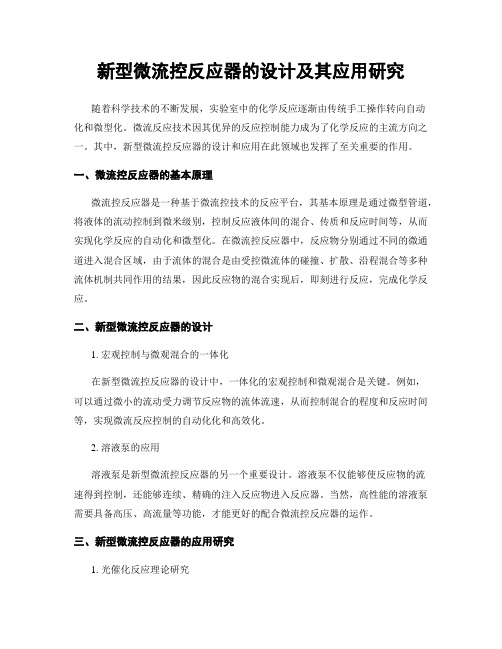
新型微流控反应器的设计及其应用研究随着科学技术的不断发展,实验室中的化学反应逐渐由传统手工操作转向自动化和微型化。
微流反应技术因其优异的反应控制能力成为了化学反应的主流方向之一。
其中,新型微流控反应器的设计和应用在此领域也发挥了至关重要的作用。
一、微流控反应器的基本原理微流控反应器是一种基于微流控技术的反应平台,其基本原理是通过微型管道,将液体的流动控制到微米级别,控制反应液体间的混合、传质和反应时间等,从而实现化学反应的自动化和微型化。
在微流控反应器中,反应物分别通过不同的微通道进入混合区域,由于流体的混合是由受控微流体的碰撞、扩散、沿程混合等多种流体机制共同作用的结果,因此反应物的混合实现后,即刻进行反应,完成化学反应。
二、新型微流控反应器的设计1. 宏观控制与微观混合的一体化在新型微流控反应器的设计中,一体化的宏观控制和微观混合是关键。
例如,可以通过微小的流动受力调节反应物的流体流速,从而控制混合的程度和反应时间等,实现微流反应控制的自动化化和高效化。
2. 溶液泵的应用溶液泵是新型微流控反应器的另一个重要设计。
溶液泵不仅能够使反应物的流速得到控制,还能够连续、精确的注入反应物进入反应器。
当然,高性能的溶液泵需要具备高压、高流量等功能,才能更好的配合微流控反应器的运作。
三、新型微流控反应器的应用研究1. 光催化反应理论研究新型微流控反应器在光催化反应的理论研究中具有广泛应用。
实验研究表明,微流控反应器可以提高光催化反应中反应物的混合程度,促进反应物与光催化剂的连续反应,从而增强反应效率和光催化反应的安全性等。
2. 肿瘤微流控反应器的应用微流反应技术已经被用于肿瘤相关的化学反应。
该技术允许使用微型通道精确定位药物到瘤细胞,并以需要的速度进行分配。
在肿瘤微流控反应器上,反应液体流动速度可以被调整,从而提高药物的渗透程度,提高治疗效果。
四、结论新型微流控反应器的设计和应用研究对化学反应的自动化和微型化具有重要的推动作用。
微通道反应器低温制冷机半导体水冷机
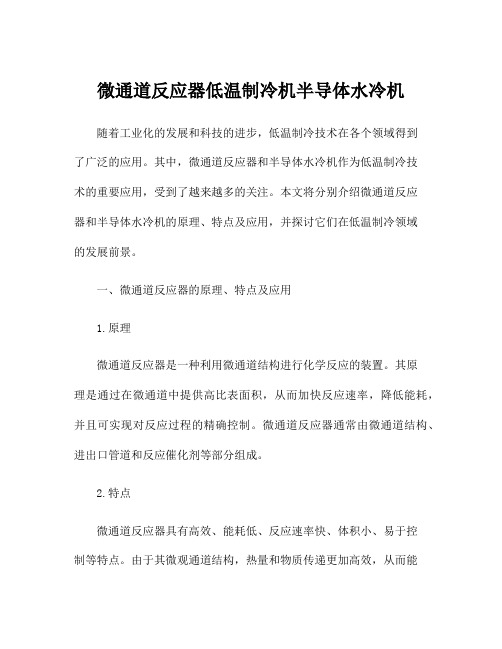
微通道反应器低温制冷机半导体水冷机随着工业化的发展和科技的进步,低温制冷技术在各个领域得到了广泛的应用。
其中,微通道反应器和半导体水冷机作为低温制冷技术的重要应用,受到了越来越多的关注。
本文将分别介绍微通道反应器和半导体水冷机的原理、特点及应用,并探讨它们在低温制冷领域的发展前景。
一、微通道反应器的原理、特点及应用1.原理微通道反应器是一种利用微通道结构进行化学反应的装置。
其原理是通过在微通道中提供高比表面积,从而加快反应速率,降低能耗,并且可实现对反应过程的精确控制。
微通道反应器通常由微通道结构、进出口管道和反应催化剂等部分组成。
2.特点微通道反应器具有高效、能耗低、反应速率快、体积小、易于控制等特点。
由于其微观通道结构,热量和物质传递更加高效,从而能够提高反应的选择性和收率。
同时,微通道反应器的体积小,可实现对大规模化学生产的微型化,从而节约了原材料和空间成本。
3.应用微通道反应器在有机合成、石油化工、生物制药、新能源等领域有着广泛的应用。
在有机合成领域,微通道反应器可用于实现多步反应的连续化,从而提高合成反应的效率和收率。
在生物制药领域,微通道反应器可用于生物催化反应,从而提高药物的纯度和产率。
二、半导体水冷机的原理、特点及应用1.原理半导体水冷机是一种利用半导体材料的热电效应(Peltier效应)进行制冷的装置。
其原理是通过在半导体材料的两侧通入直流电流,从而在材料的两侧产生温差,从而实现对物体的制冷。
半导体水冷机通常由半导体芯片、散热片、电子控制系统等部分组成。
2.特点半导体水冷机具有体积小、制冷速度快、无振动、环保节能等特点。
由于其无机械活动部分,因此不会产生振动和噪音,且具有较长的使用寿命。
同时,半导体水冷机的制冷速度快,对温度的调节和控制更加精确。
3.应用半导体水冷机在光电子元件、电子器件、生物医学、食品保鲜等领域有着广泛的应用。
在光电子元件领域,半导体水冷机可用于激光器、探测器等元件的温控,从而实现器件的稳定工作。
- 1、下载文档前请自行甄别文档内容的完整性,平台不提供额外的编辑、内容补充、找答案等附加服务。
- 2、"仅部分预览"的文档,不可在线预览部分如存在完整性等问题,可反馈申请退款(可完整预览的文档不适用该条件!)。
- 3、如文档侵犯您的权益,请联系客服反馈,我们会尽快为您处理(人工客服工作时间:9:00-18:30)。
浅述微涡流反应器
1 引言
给水处理影响出水水质的因数众多,混凝是最重要的过程也是最难管理的一个环节。
水力絮凝工艺主要有隔板工艺、折板工艺、网格工艺和微涡流工艺。
如表1所示,微涡流工艺具有效率高,且具有安装简单、施工周期短等优点,更重要的是,微涡流工艺反应时间短,在保证处理效果的前提下,不仅可以增大处理能力,还可以降低药耗。
2 涡流反应器
2.1涡流反应器构造特点及优点
微涡流混凝工艺的核心是涡流反应器,其构造特点是:①空心球形结构,直径根据工艺需要确定,内外表面均打毛;②表面开有小孔,孔径和开孔率根据工艺需要确定;③采用ABS塑料材料,容重略大于水,壁厚由结构强度设计确定。
其优点是:①反应时间短,微涡流反应时间紧为6~9min,是传统工艺1/3~1/2;
②絮凝效率高,絮体质量高,有利于提高沉淀效率;③对水质、水量适应能力强;④在出水水质稳定,出水量相同的情况下,较其他工艺减少絮凝剂用量;⑤无方向性,直接投入水中使用,相互堆积不堵塞壁孔,不需要固定安装;⑥可根据进水水质及工艺需求确定反应器的开孔率和开孔孔径;⑦由于反复穿过反应器小孔,水流中会形成大量微小的涡旋;⑧水流冲击作用下,反应器会发生微小旋转,有利于避免积泥现象的出现,也不易被漂浮物堵塞;⑨材料强度好,无毒性,耐腐蚀,抗老化,使用寿命长;⑩工厂化批量注塑生产,改造工程施工期短。
2.2 涡流反应器原理
凝聚效果的好坏取决于水中胶体脱稳的程度和碰撞的机率。
脱稳的程度主要是涉及到最佳投药量问题,碰撞的机率则主要是涉及到水力条件问题。
良好的水力条件对于混凝效果是极其重要的。
它要求水流有适当的紊动程度,为细小的矾花创造最好的相碰接触机会和吸附条件,并防止较大的矾花下沉,同时还要防止已形成的絮凝体破碎。
微涡流絮凝器充分考虑到影响混凝效果的各种水力内在要素,为混凝创造出较优的水力条件,使混凝达到较优的效果。
涡流反应器外形为空心球体,其反应主要原理就是微涡流凝聚,立体接触絮凝。
图1为其混凝作用的示意图。
(1)微涡流凝聚:从混凝动力学可知,推动水中颗粒
相互碰撞的动力主要是由流体运动来进行的。
当水流穿过
微涡流絮凝器壁面的大量孔洞时,在形成一部分小涡旋的同
时也形成无数的微小旋涡。
根据Kolmogoroff局部各向同
性紊流理论可知,紊流中存在各种尺度不等的涡旋。
大涡
旋将能量输送给小涡旋,小涡旋又将能量输送给更小的涡
旋。
大涡旋往往使颗粒作整体移动而不会相互碰撞,而尺
度过小的涡旋其强度往往不足以推动颗粒碰撞,只有涡旋
尺度与颗粒尺寸相近的涡旋才会引起颗粒间相互碰撞。
根图1 涡流反应器混凝作用示意图
据原水的实际情况可选用不同表面开孔直径与开孔率的涡流反应器来控制紊流程度,同时进行不同开孔直径的涡流反应器的安装组合,使其形成微小旋涡的涡旋尺度最大限度地与颗粒直径相近。
这是涡流反应器取得较好混凝效果的技术关键。
众多的微涡旋流动能有效地促进水中微粒的扩散与碰撞。
一方面,混凝剂水解形成胶体在微涡流作用下快速扩散并与水中胶体充分碰撞,使水中胶体快速脱稳;另一方面,涡流形成流层之间较大的流速差,造成了流层中携带微粒的相对运动,同时涡流的旋转作用形成离心惯性力,造成微粒的沿旋涡径向运动,故水中脱稳胶体在微涡流作用下具在更多碰撞机会,因而具有更高的凝聚效率。
(2)立体接触絮凝:当混凝反应区放置了大量的涡流反应器后,由于絮凝器内流速相对较小,大量较大粒径的絮体(矾花)在涡流反应器内积累悬浮于水中。
悬浮絮体(即通常说的泥渣)对水流体中的脱稳胶体产生吸附絮凝作用——即接触絮凝。
与传统接触絮凝澄清池相比涡流反应器具有更高的效率。
其一,传统澄清池内的悬浮絮体内只有一层,而新工艺上向流(即水流垂直向上通过涡流反应器)区每个涡流反应器内都有悬浮絮体,总体积大,形成立体接触絮凝;其二,涡流反应器内絮体成长质量更高,成长过大的絮体在微涡流的作用下会破碎成较小絮体从而保持絮凝能力(絮体过大会使总表面积减小,吸附能力下降),密实度较低的絮体在微涡流的作用下会破碎并重新絮凝成密实度较高的絮体,有利于沉淀分离。
3工程概况
上杭石禾仓水厂投入使用于1998年,取水水源为丰村溪溪水,原水多数时段为低浊度,高浊时期为190NTU左右。
水厂共有2组构筑物,原设计单组供水量为5000m3/d,水厂采用穿孔旋流反应池→斜管沉淀池→普通快滤池过滤处理工艺。
运营初期,出厂水浊度均能达到国家规定的标准(〈3NTU)。
2007年,《生活饮用水卫生标准》的颁布实施;随着时间的推移,水厂原先设计规模已不能满足当地生产和生活用水快速增长的需要;同时运行中还存在如下问题:(1)低温较低时处理效果差;(2)丰水期原水浊度高时水处理效果不稳定,引起出水浊度较高。
经过反复技术讨论和比较,决定对反应池进行改造,在原有构造的基础上增设微涡流混凝工艺。
4工程改造
4.1改造方案
改造过程中水厂原各构筑物外形尺寸基本保持不变,改造主要包括以下三方面:①考虑到丰水期含大量杂质,为了避免积泥和堵塞,将第1格反应池改造成沉砂池;②将2至8格网格反应池改造成微涡旋反应池;③为了解决混合不充分的现象,故将混合器的位置前移到阀门井内。
根据混凝动力学原理,在第2、3格反应池投加开孔孔径为25mm的HJTM2型微涡旋反应器,而从第4格开始同时投加开孔孔径为35mm的HJTM1型涡流反应器,第4、5、6格HJTM1型涡流反应器所占的比例分别为40%、60%、80%,第7、8格全部投加孔径为35mm的HJTM1型反应器,从而满足混凝反应过程中对速度梯度(G值)的要求
4.2微涡流反应时间
从图2中可知:第2、3格在池底以上0.7米处做支撑,放置高度为3.5米;第4、5、6格在池底以上0.75米处做支撑,放置高度为3.4米;第7、8格在池底往上0.8米处做支撑,放置高度为3.3米;第9格作为过渡段,不投加微涡流反应器。
则微涡流反应器的体积为:
V2、3 = 1.0 × 1.0 × 3.5 = 3.5(m3)
V4、.5、6 = 1.0 × 1.0 × 3.4 =3.4 (m3)
V8、7 = 1.0 × 1.0 × 3.3= 3.3(m3)
总体积为:V总=3.5 ×2+ 3.4 ×3+3.3×2 = 23.8 (m3)
微涡流反应时间为:23.8/(5000/24/60)≈ 6.85(min)
根据微涡流反应的设计要求,微涡流反应时间一般要达到6~9min,可以满足微涡旋反应时间要求;此外,原网格反应池总体积为:V2 = 1.0×1.0×4.2×9= 37.8m3,非微涡流反应时间为:(37.8-23.8)/(5000/24/60)=4.03(min),所以,总反应时间为:6.85 + 4.03=10.88 (min),根据经验,反应效果可以保证。
4.3微涡流反应G值及GT值核算
经过现场测算,水流经整个涡流反应器的水损为:
8×(3.5×2+3.4×3+3.3×2)/1000 ≈ 0.19 (m),
则
G=[(1000×0.19)/(60×0.1165×10-3 × 6.85)]1/2 ≈ 63(s-1),
GT=63*6.85*60=2.59*104,
均在传统经典的混凝控制指标(平均G=20~70 s-1,平均GT=1*104 ~1*105 )范围之内。
5 调试运行情况及结果
改造结束后,经过三个月的调试及运行,效果令人满意。
水质较原工艺有明显改善,具体表在:①改造前,反应池基本看不见矾花颗粒,而改造后反应池中生成的矾花清晰,颗粒明显,沉降性能好;②改造后沉淀池主要呈碧绿色,表明沉淀池浑水区明显减小,水质明显改进;③滤池工作周期延长,反冲洗时间缩短(由原来的9min降低为7min,反冲洗水源为水塔供水),反洗水消耗大大降低,表明待滤水浊度降低,且矾花的絮凝质量提高;④滤前水浊度基本保持在3NTU 以下,而出厂水浊度检测均在1NTU以下(多数情况下为0.6NTU左右)。
从表2可知,采用微涡旋混凝工艺后,沉淀出水浊度降低,过滤周期延长(由原来的24小时增加到36小时),冲洗次数减少,反冲洗水量降低。
上杭石禾仓水厂从改造至今已运行3年,3年来水厂一直运行稳定,出厂水浊度基本保持在1.0NTU以下。
6结语
微涡流混凝工艺通过微涡流凝聚和立体接触絮凝,充分利用混凝空间、混凝能量与絮体活性,大大提高了混凝反应效率,缩短了反应时间,在保证出厂水水质的基础上产水量提高了20%,同时节约了大量的反冲洗水量并且使整个净水系统的抗变化适应能力得到大大提高。
所进行的水厂改造实践表明,该工艺可显著改善出水水质,缩短反应时间,降低混凝剂用量,同时施工简单,运行稳定,维护方便,在老水厂改造中具有一定的应用优势。
参考文献:
[1] 严煦世主编.《给水工程》.第四版. 中国建筑工业出版社. 1999.12
[2] 王绍文.惯性效应在絮凝中的动力学作用[J] .中国给排水,1998,14(2):13-16。