制氢装置转化炉简介
制氢装置转化炉受力分析与改进

制氢装置转化炉受力分析与改进制氢装置转化炉是制取氢气的核心设备之一,其性能直接影响着制氢效率。
转化炉受力分析与改进是提高制氢效率的重要手段之一。
本文将对制氢装置转化炉进行受力分析并提出改进方案。
1.受力情况转化炉在工作过程中受到气体压力和温度的双重影响。
气体在管道中流动时会对管道壁产生一定的压力,转化炉内的气体压力也会导致转化炉壁产生一定的压力。
同时,高温下转化炉内壁受热膨胀的影响也会使其产生一定的应力。
2.应力分析根据力学原理可得,转化炉壁内应力主要由气体压力和膨胀力两部分组成。
(1)气体压力造成的应力当氢气通过管道流动时,其产生的压力会直接作用于管道壁上。
设管道内径为d,压力为p,壁厚为t,则管道内侧壁面所受合力F1为:F1=πd²/4×p壁面受力应变ε1为:ε1=F1/Et其中E为管材弹性模量,t为管道壁厚。
(2)膨胀力引起的应力高温下转化炉内壁受热膨胀,产生的膨胀力也会对转化炉壁产生一定的应力。
设转化炉壁温度变化量为ΔT,线性膨胀系数为α,壁面面积为A,则壁面受力F2为:F2=αΔTA3.应力评估根据受力分析,可得转化炉内壁应力分为两部分:气体压力引起的应力和膨胀力引起的应力。
对于圆筒形转化炉壁,可采用轴对称的应力平衡原理求解。
当壁面处于沿径向的应力状态时,转化炉壁上的应力σ可表示为:σ=(πd²/4)(p+αΔT)/t根据以上公式可计算出转化炉壁受力状态与应力大小,从而为改进提供依据。
二、改进方案1.加强壁面支撑转化炉内壁受到的气体压力和膨胀力较大,若壁体支撑不足,则会导致其变形,使壁体应力增大,加速壁体疲劳寿命的降低。
因此,加强转化炉壁面支撑是一项必要的改进措施。
改进方案一:在转化炉内部设置支撑结构,加强其骨架,防止转化炉壁体过度变形。
采用这种方案可以防止壁面扭曲、折叠和膨胀等问题,从而减少壁面应力,提高转化炉的使用寿命和可靠性。
改进方案二:采用加厚壁体或改变材料等方式增强壁面强度。
天然气制氢关键设备:水蒸气转化炉
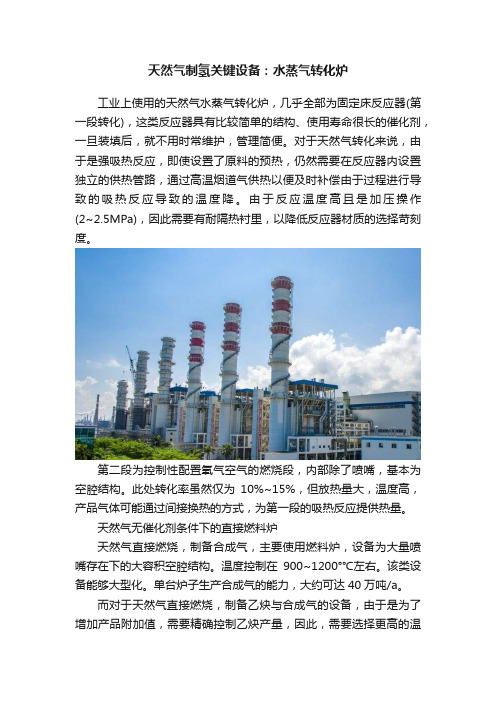
天然气制氢关键设备:水蒸气转化炉工业上使用的天然气水蒸气转化炉,几乎全部为固定床反应器(第一段转化),这类反应器具有比较简单的结构、使用寿命很长的催化剂,一旦装填后,就不用时常维护,管理简便。
对于天然气转化来说,由于是强吸热反应,即使设置了原料的预热,仍然需要在反应器内设置独立的供热管路,通过高温烟道气供热以便及时补偿由于过程进行导致的吸热反应导致的温度降。
由于反应温度高且是加压操作(2~2.5MPa),因此需要有耐隔热衬里,以降低反应器材质的选择苛刻度。
第二段为控制性配置氧气空气的燃烧段,内部除了喷嘴,基本为空腔结构。
此处转化率虽然仅为10%~15%,但放热量大,温度高,产品气体可能通过间接换热的方式,为第一段的吸热反应提供热量。
天然气无催化剂条件下的直接燃料炉天然气直接燃烧,制备合成气,主要使用燃料炉,设备为大量喷嘴存在下的大容积空腔结构。
温度控制在900~1200°℃左右。
该类设备能够大型化。
单台炉子生产合成气的能力,大约可达40万吨/a。
而对于天然气直接燃烧,制备乙炔与合成气的设备,由于是为了增加产品附加值,需要精确控制乙炔产量,因此,需要选择更高的温度,对于空气与天然气的接触,混合结构要求苛刻。
目前最大设备为单系列每年1万~1。
5万吨乙炔。
由于乙炔气在初次产品气中的含量约8%,而合成气约80%。
因此,相当于该炉子每年能够生产合成约15万吨/a。
由于以乙炔气为最大生产目标,该装置的结构为混合段、燃烧段、淬冷段及排液段组成。
需要控制燃料反应在毫秒级发生,同时需要利用冷的介质与蒸汽或水,在极短时间内,将含乙炔的高温气体淬冷,避免其进一步反应,生成碳或合成气。
天然气与空气在催化剂下的催化反应,尚未工业化,目前仍然处于实验室硏究阶段,使用固定床设备,尚未考虑过程中催化剂积炭及反应强放热导致的工程问题。
同时,在规模不大的自热式或热平衡式转化中,有硏究者使用微通道反应器,通过精细控制催化剂涂层及设置换热结构,希望达到减少反应器体积,减少危险气体的瞬时流量与存放问题,提高过程安全度。
提高转化炉热效率降低单耗
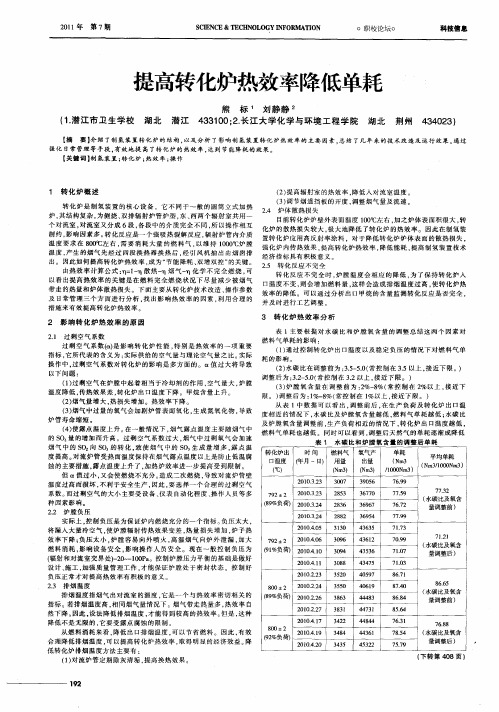
2 影 响转 化炉 热 效 率 的原 因
3 转 化炉 热 效 率 分 析
表 1主 要 根 据 对 水 碳 比 和 炉 膛 氧 含 量 的 调 整 总 结 这 两 个 因 素 对 21 过 剩 空气 系数 . 燃 料 气 单耗 的影 响 : 过 剩 空 气 系 数 ㈧ 是 影 响 转 化 炉 性 能 , 别 是 热 效 率 的 一 项 重 要 特 ( ) 过控 制 转 化 炉 出 口温 度 以及 稳 定 负 压 的情 况 下 对 燃 料 气 单 1通 指 标 , 所代 表 的含 义 为 : 际供 给 的空 气 量 与 理 论 空气 量 之 比 。 际 它 实 实 耗的影响。 操作中 , 过剩 空 气 系 数 对 转 化 炉 的 影 响 是 多 方 面 的 。q值 过 大 将 导 致 () 2 水碳 比在 调 整 前 为 :.— .( 35 5 常控 制 在 35以上 , 近 下 限 。) O . 接 以下 问 题 : 调 整 后 为 :.— .( 32 5O 常控 制 在 3 . 2以上 . 近 下 限 。 ) 接
炉 管 寿命 缩 短 。 及 炉 膛 氧含 量 调 整 前 , 产 负荷 相 近 的情 况 下 , 化 炉 出 口温 度 越 低 , 生 转 () 4 使露 点 温 度 上 升 。 一般 情 况 下 , 气 露点 温度 主 要 随 烟 气 中 在 烟 燃 料气 单 耗 也 越 低 。 同 时 可 以看 到 , 整 后 天 然气 的单 耗 逐 渐 成 降低 调 的 S 的增 加 而 升 高 。 过 剩 空 气 系 数 过 大 , 气 中 过 剩 氧 气 会 加 速 O量 烟 表 1 水 碳 比和 炉膛 氧 含量 的 调 整 盾 单 耗 烟 气 中 的 S 2 S 的 转 化 , 使 烟 气 中 的 S 成 量 增 多 , 点 温 o向 致 O生 露 转化炉出 时间 燃料气 氢气产 单耗 度提高。 对流炉管受热面温度保持在烟气露点温度以上是 防止低温腐 口温度 ( 年月 一日) 用量 出量 (m N3 平均单耗
烃类转化制氢装置中废热锅炉的简介

烃类转化制氢装置中废热锅炉的简介锅炉是指利用各种燃料、电或者其他能源,所将承装的液体加热到一定的参数,并具有一定压力的密闭设备。
制氢装置共有3个废热锅炉,以下以转化废热锅路为例进行介绍。
制氢锅炉属于中压(3.8-6.0)、中型(20-75t/h)、自然循环、蒸汽、卧式锅壳式火管锅炉。
一.锅炉的结构1.废锅和汽包锅炉吸热部分,并将热量传递给水的受热面系统,是锅炉中贮存或输送锅炉水或蒸汽的密闭受压元件。
由管束和壳程组成,管束内走转化气,壳程是水汽混合物。
2.下降管、上升管下降管的作用是把汽包里的水输送到废锅,上升管是把废锅产出的水汽输送到汽包,使有足够大的循环量,以保证转化废锅受热面金属能够得到可靠冷却,达到安全运行的目的。
3.安全附件、自控装置锅炉的安全附件包括安全阀、压力表、水位表、温度计。
锅炉自控装置包括水调节阀、高低水位报警装置、低水位连锁保护装置、超温超压报警装置、燃烧调节装置、点火熄火保护装置等。
A.安全阀蒸汽锅炉一般选用全启式、带手柄不密封的弹簧安全阀。
对于蒸发量大于0.5t/h的锅炉至少在汽包最高位置安装两个或两个以上的安全阀,应每年对安全阀校验一次,并有铅封、标签、效验报告。
B.压力表压力表一般不能低于2.5级的弹簧式压力表,与汽包蒸汽空间直接相连。
C.流量计锅炉进水,汽包出口蒸汽对流量计没有特殊要求,全部可采用孔板流量计。
4.排污装置锅炉运行时,炉水所含各种杂质不断析出。
为此设有定期排污、连续排污、下降管排污系统把集聚在锅炉底部的高浓度钙镁化合物和泥垢、磷酸根漂浮物排出。
都是用的是快开式排污阀。
二.锅炉的工作过程从理论上讲锅炉的工作可分为三个连续进行的过程,即放热-传热-吸热1.高温转化气放热。
2.高温转化气通过管壁将热量传递给工质。
传热情况的好坏取决于受热面积的布置及其内部是否结生水垢和转化气流速等因素。
3.水吸收热量变为热水或蒸汽的过程。
将水加热的目的是要得到一定参数(温度和压力)的热水或水蒸气,供生产和生活使用。
制氢装置转化炉简介
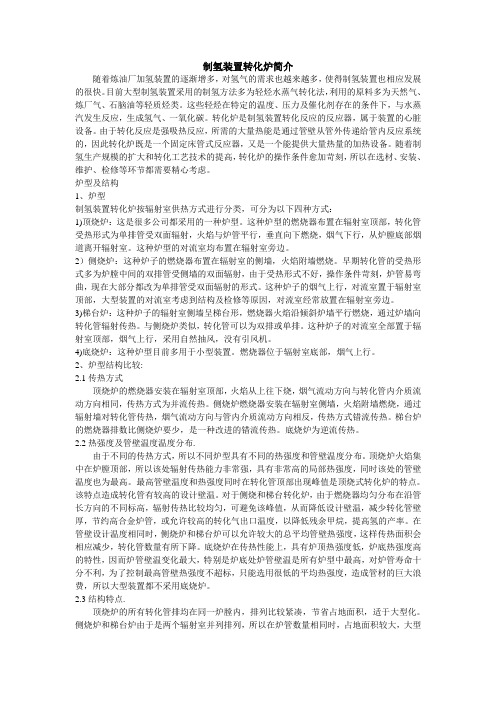
制氢装置转化炉简介随着炼油厂加氢装置的逐渐增多,对氢气的需求也越来越多,使得制氢装置也相应发展的很快。
目前大型制氢装置采用的制氢方法多为轻烃水蒸气转化法,利用的原料多为天然气、炼厂气、石脑油等轻质烃类。
这些轻烃在特定的温度、压力及催化剂存在的条件下,与水蒸汽发生反应,生成氢气、一氧化碳。
转化炉是制氢装置转化反应的反应器,属于装置的心脏设备。
由于转化反应是强吸热反应,所需的大量热能是通过管壁从管外传递给管内反应系统的,因此转化炉既是一个固定床管式反应器,又是一个能提供大量热量的加热设备。
随着制氢生产规模的扩大和转化工艺技术的提高,转化炉的操作条件愈加苛刻,所以在选材、安装、维护、检修等环节都需要精心考虑。
炉型及结构1、炉型制氢装置转化炉按辐射室供热方式进行分类,可分为以下四种方式:1)顶烧炉:这是很多公司都采用的一种炉型。
这种炉型的燃烧器布置在辐射室顶部,转化管受热形式为单排管受双面辐射,火焰与炉管平行,垂直向下燃烧,烟气下行,从炉膛底部烟道离开辐射室。
这种炉型的对流室均布置在辐射室旁边。
2)侧烧炉:这种炉子的燃烧器布置在辐射室的侧墙,火焰附墙燃烧。
早期转化管的受热形式多为炉膛中间的双排管受侧墙的双面辐射,由于受热形式不好,操作条件苛刻,炉管易弯曲,现在大部分都改为单排管受双面辐射的形式。
这种炉子的烟气上行,对流室置于辐射室顶部,大型装置的对流室考虑到结构及检修等原因,对流室经常放置在辐射室旁边。
3)梯台炉:这种炉子的辐射室侧墙呈梯台形,燃烧器火焰沿倾斜炉墙平行燃烧,通过炉墙向转化管辐射传热。
与侧烧炉类似,转化管可以为双排或单排。
这种炉子的对流室全部置于辐射室顶部,烟气上行,采用自然抽风,没有引风机。
4)底烧炉:这种炉型目前多用于小型装置。
燃烧器位于辐射室底部,烟气上行。
2、炉型结构比较:2.1传热方式顶烧炉的燃烧器安装在辐射室顶部,火焰从上往下烧,烟气流动方向与转化管内介质流动方向相同,传热方式为并流传热。
02转化炉

采用小直径的转化炉管
内径一般只有71mm。空速高,阻力降大, 动力损耗大。
竖琴管顶烧方箱炉结构简图
5.2.4梯台炉特点(Foster Wheeler炉型)
辐射室外型为梯台型,火焰沿倾斜炉 墙平行燃烧。火嘴倾斜向上的为正梯 台炉,反之为倒梯台炉。其优点是可 以分段控制火焰。目前在我国尚未推 广此炉型。
2.1 烃类蒸汽转化的化学反应式
2.1.1气态烃蒸汽转化反应式 CH4+H2O=CO+3H2 -206.4kJ/mol CH4+2H2O=CO2+4H2 -165.3kJ/mol CO +H2O=CO2+H2 41.2kJ/mol CO2+ CH4=2CO+2H2 -247.3kJ/mol CnH2n+2(多碳烃) + nH2O →nCO + (2n+1)H2 -Q 2.1.2液态烃(CnHm)蒸汽转化反应式 CnHm + nH2O → nCO + (n+m/2)H2 -Q (2-1) CO+3H2 → CH4+H2O 206kJ/mol (2-2) CO +H2O → CO2+H2 41.2kJ/mol (2-3)
(制氢)转化炉讲议
1. 概
述
烃类蒸汽转化炉(管式转化炉、制氢 转化炉)是以烃类为原料,用蒸汽转 化法生产合成氨原料气和氢气。炼油 厂的制氢炉、甲醇厂的制氢转化炉和 合成氨厂的一段转化炉等都属于烃类 蒸汽转化炉。转化炉是蒸汽转化工艺 中的关键设备之一。
2. 烃类蒸汽转化的基本原理
转化反应原理:用水蒸汽作氧化剂与 合格的烃类为原料,通过转化催化剂 床层,在高温下,水蒸汽与烃类发生 裂解反应,生成H2、CO、CO2。是 强度吸热反应。 通过变换工艺和提纯 工艺可以得到氢气。所用烃类原料主 要是天然气,亦可用丙烷、丁烷、液 化石油气及轻石脑油。
制氢转化炉烘炉

转化炉(F1002)烘炉1 烘炉目的转化炉(F1002)炉墙及E1001内衬,是用耐火砖混凝土等筑砌而成,里面含有大量的水份。
通过烘炉,可将炉墙中吸附水和结晶水慢慢脱除,以避免在使用过程中因水份急剧蒸发而引起炉墙衬里破坏。
通过烘炉,了解炉管的热膨胀情况,掌握炉子的温度调节、E1001使用性能及锅炉系统的热态操作。
2 烘炉具备的条件2.1 装置冲洗、吹扫合格,系统气密试验合格。
2.2 C1001A/B单机试车合格,负荷试车正常,处于备用状态;P1003A/B、P1004A/B单机试车合格,P1001、P1005标定完毕,负荷试车正常,处于备用状态。
2.3各岗位主要仪表具备投用条件。
2.4 废热锅炉系统建立水循环。
2.5 冷N 2循环时发现问题均已解决,转化炉负压力表已装好,炉区清理各种易燃易爆物品,备好消防器材。
3 转化炉点火前应具备的条件3.1 用氮气置换燃料气系统至各火嘴小阀前,由F1002顶放空管放空。
采样分析合格(O2<0.5%)后,引燃料气至火嘴小阀前。
3.2 启动F1002烟道风机,打开烟道挡板,抽20分钟后炉膛采样作爆炸分析,合格后,调整烟道挡板至合适开度.使炉膛保持合适的负压(-2~-5mmH 2O),F1002就可点火。
3.4 把E1001全部连入系统。
4 升温烘炉4.1 升温速度见表,升温曲线见图。
升温曲线图4.2 低温烘转化炉(F1002)点燃F1001火咀,按升温曲线要求使F1002升温。
但要控制F1001自身的温升≯50℃/h,出口温度≯380℃。
同时兼顾各反应器的入口温度,防止温度过高损坏反应器。
当F1001无法使F1002继续升温,或者F1002炉膛已达到120℃,并经过恒温,即可进行F1002点火。
4.3 F1002点火升温点燃F1002火嘴应按下列顺序:先两边后中间。
同时要使炉子两侧点燃的火嘴对称,避免炉管单侧受热。
初始阶段,火焰尽量小些,以避免局部温升过快,以后可根据升温曲线的要求及时增减火嘴。
提高制氢转化炉热效率的有效措施
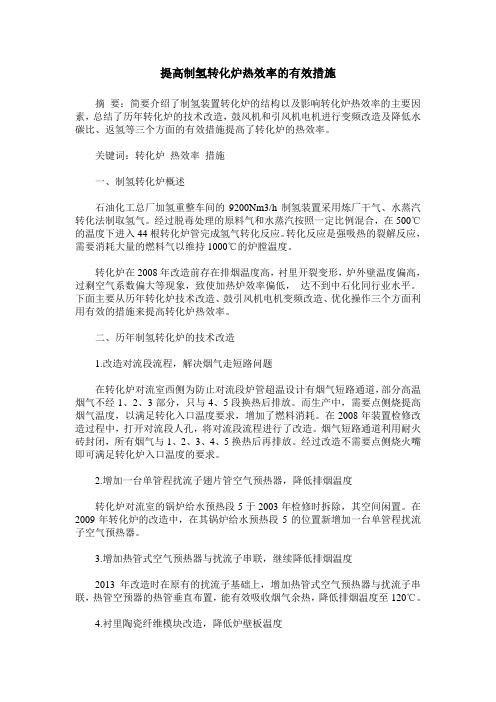
提高制氢转化炉热效率的有效措施摘要:简要介绍了制氢装置转化炉的结构以及影响转化炉热效率的主要因素,总结了历年转化炉的技术改造,鼓风机和引风机电机进行变频改造及降低水碳比、返氢等三个方面的有效措施提高了转化炉的热效率。
关键词:转化炉热效率措施一、制氢转化炉概述石油化工总厂加氢重整车间的9200Nm3/h制氢装置采用炼厂干气、水蒸汽转化法制取氢气。
经过脱毒处理的原料气和水蒸汽按照一定比例混合,在500℃的温度下进入44根转化炉管完成氢气转化反应。
转化反应是强吸热的裂解反应,需要消耗大量的燃料气以维持1000℃的炉膛温度。
转化炉在2008年改造前存在排烟温度高,衬里开裂变形,炉外壁温度偏高,过剩空气系数偏大等现象,致使加热炉效率偏低,达不到中石化同行业水平。
下面主要从历年转化炉技术改造、鼓引风机电机变频改造、优化操作三个方面利用有效的措施来提高转化炉热效率。
二、历年制氢转化炉的技术改造1.改造对流段流程,解决烟气走短路问题在转化炉对流室西侧为防止对流段炉管超温设计有烟气短路通道,部分高温烟气不经1、2、3部分,只与4、5段换热后排放。
而生产中,需要点侧烧提高烟气温度,以满足转化入口温度要求,增加了燃料消耗。
在2008年装置检修改造过程中,打开对流段人孔,将对流段流程进行了改造。
烟气短路通道利用耐火砖封闭,所有烟气与1、2、3、4、5换热后再排放。
经过改造不需要点侧烧火嘴即可满足转化炉入口温度的要求。
2.增加一台单管程扰流子翅片管空气预热器,降低排烟温度转化炉对流室的锅炉给水预热段5于2003年检修时拆除,其空间闲置。
在2009年转化炉的改造中,在其锅炉给水预热段5的位置新增加一台单管程扰流子空气预热器。
3.增加热管式空气预热器与扰流子串联,继续降低排烟温度2013年改造时在原有的扰流子基础上,增加热管式空气预热器与扰流子串联,热管空预器的热管垂直布置,能有效吸收烟气余热,降低排烟温度至120℃。
4.衬里陶瓷纤维模块改造,降低炉壁板温度转化炉墙及炉顶砖结构损坏严重,造成炉墙钢板表面温度严重超温,经测试炉壁钢板表面温度100℃,局部的温度甚至达到120℃,严重影响转化炉的热效率。
转化炉讲议

采用小直径的转化炉管
内径一般只有71mm。空速高,阻力降大, 动力损耗大。
竖琴管顶烧方箱炉结构简图
5.炉型及结构
5.1炉型
制氢转化炉按辐射室供热方式及外型 分,可分为四种类型。 单管型顶烧方箱炉(I.C.I型) 竖琴管顶烧方箱炉(Kellogg型) 侧烧箱式炉(Topsфe型) 梯台炉(Foster Wheeler型)
5.2主要炉型特点及结构
5.2.1单管型顶烧方箱炉特点(I.C.I炉型) 顶烧
方箱型
辐射段为方箱型,管排紧凑、数目增减灵活, 占地少,炉宽不受产量限制,适宜大型化。
对流段设置在炉侧
安装拆修方便,但占地较大。
茂名分公司联合二车间 6×104m3/h制氢装置的转化炉就 是与此类型相似的炉子。
I.C.I型转化炉结构简图
茂名分公司6×104m3/h制氢装置的转化炉
炉膛尺寸为长(18.22)×宽(14.25)×高(25), 六排炉管,每排54根,共324根。炉顶设置七 排燃气燃烧器,每组16个,共112个。 炉管规格为ф123×10×14500,装载转化催 化剂32.4m3,炉子热负荷97.088MW,管外壁 最高温度为950º C,操作压力3.1MPa,炉管 材质为ZG40Ni35Cr25Nb(HP-40Nb),下猪 尾管和下集气管材质为Incoloy-800。
※燃烧器(WR-I)
制氢转化炉操作指南

制氢转化炉操作指南制氢转化炉操作指南一、前言本操作指南旨在提供制氢转化炉的详细操作方法,以确保操作人员能够正确、安全地使用该设备。
请在使用前仔细阅读本指南,并按照指南的要求进行操作。
二、设备概述1.制氢转化炉是一种用于将化学原料转化为氢气的设备,具有高效、节能的特点。
2.转化炉由炉体、燃烧器、进料口、出料口、废气排放口等组成。
三、安全注意事项1.操作人员必须熟悉转化炉的使用方法,并遵守相关安全规定。
2.在操作转化炉前,请确保设备正常运行,无损坏或泄漏等情况。
3.确保操作人员都佩戴适当的个人防护装备,如手套、防护眼镜等。
4.在操作过程中,严禁离开操作岗位,如有特殊情况需离开,请事先关闭炉体和燃烧器,并通知相关人员。
5.操作结束后,应及时清理转化炉周围的杂物,保持设备清洁。
四、操作步骤1.开机准备a.检查炉体和燃烧器是否正常,如有异常情况,请及时通知维修人员。
b.打开进料口,根据需要加入适量的化学原料。
c.打开燃烧器,调节火焰大小,使其能够提供足够的热量。
2.开始操作a.将化学原料缓慢地加入转化炉,避免产生冲击和溢出。
b.观察炉内温度和压力的变化,并及时调整燃烧器的火焰强度。
c.根据工艺要求,控制转化炉的温度和时间。
3.操作结束a.停止加料,并将燃烧器调至最小火焰。
b.关闭炉体和燃烧器,并等待转化炉冷却后进行下一步操作。
五、附件本文档附带以下附件:1.转化炉操作记录表:用于记录每次操作的详细信息。
2.转化炉维护检查表:用于定期检查维护转化炉设备的情况。
六、法律名词及注释1.安全规定:指根据国家相关法律法规和行业标准制定的安全操作规范。
2.防护眼镜:用于保护操作人员的眼睛免受化学物质或碎片的伤害。
3.化学原料:指用于制氢转化炉的化学反应的起始物质。
4.工艺要求:指制氢转化炉在操作过程中需要遵循的工艺要求,包括温度、压力等。
制氢转化炉模块化制造及质量控制简介

5
转化炉 转化炉系统介绍Introduction for reformer system 系 统
转化炉系统包括以下内容 reformer system include the following 序号 Item 6 7 转化炉系统 Reformer system 风机 fan 空气预热器 air pre-heater 详细内容 Detail 鼓风机、引风机 air blower and draft fan
2
炉管系统 Reformer tube system
转化炉 转化炉系统介绍Introduction for reformer system 系 统
转化炉系统包括以下内容 reformer system include the following 序号 Item 转化炉系统 Reformer system 详细内容 Detail 包括纤维制品(纤维毯、纤维板、纤维模块、纤维带等)、耐 火砖及浇注料 Including refractory fiber product(fiber blanket、 fiberboard、fiber modules、fiber ribbon .etc)、 refractory brick and castable refractory
项目进度统计分析系统 (PSS)
项目文件控制 (DC) 项目周报/月报系统(/Monthly Report)
项目进度评审会议(PRM)
转 化 炉 3、转化炉车间模块化制造质量控制措施 3、Quality control measures for Modular manufacturing in 系 统 workshop
制氢装置转化炉受力分析与改进
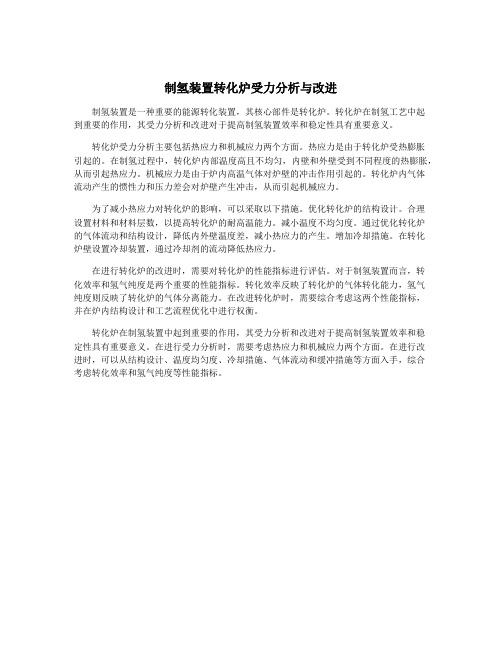
制氢装置转化炉受力分析与改进制氢装置是一种重要的能源转化装置,其核心部件是转化炉。
转化炉在制氢工艺中起到重要的作用,其受力分析和改进对于提高制氢装置效率和稳定性具有重要意义。
转化炉受力分析主要包括热应力和机械应力两个方面。
热应力是由于转化炉受热膨胀引起的。
在制氢过程中,转化炉内部温度高且不均匀,内壁和外壁受到不同程度的热膨胀,从而引起热应力。
机械应力是由于炉内高温气体对炉壁的冲击作用引起的。
转化炉内气体流动产生的惯性力和压力差会对炉壁产生冲击,从而引起机械应力。
为了减小热应力对转化炉的影响,可以采取以下措施。
优化转化炉的结构设计。
合理设置材料和材料层数,以提高转化炉的耐高温能力。
减小温度不均匀度。
通过优化转化炉的气体流动和结构设计,降低内外壁温度差,减小热应力的产生。
增加冷却措施。
在转化炉壁设置冷却装置,通过冷却剂的流动降低热应力。
在进行转化炉的改进时,需要对转化炉的性能指标进行评估。
对于制氢装置而言,转化效率和氢气纯度是两个重要的性能指标。
转化效率反映了转化炉的气体转化能力,氢气纯度则反映了转化炉的气体分离能力。
在改进转化炉时,需要综合考虑这两个性能指标,并在炉内结构设计和工艺流程优化中进行权衡。
转化炉在制氢装置中起到重要的作用,其受力分析和改进对于提高制氢装置效率和稳定性具有重要意义。
在进行受力分析时,需要考虑热应力和机械应力两个方面。
在进行改进时,可以从结构设计、温度均匀度、冷却措施、气体流动和缓冲措施等方面入手,综合考虑转化效率和氢气纯度等性能指标。
天然气制氢装置转化炉介绍
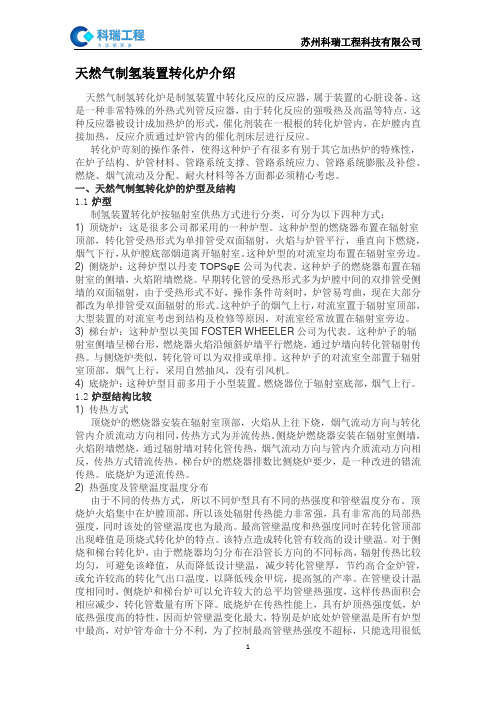
天然气制氢装置转化炉介绍天然气制氢转化炉是制氢装置中转化反应的反应器,属于装置的心脏设备。
这是一种非常特殊的外热式列管反应器,由于转化反应的强吸热及高温等特点,这种反应器被设计成加热炉的形式,催化剂装在一根根的转化炉管内,在炉膛内直接加热,反应介质通过炉管内的催化剂床层进行反应。
转化炉苛刻的操作条件,使得这种炉子有很多有别于其它加热炉的特殊性,在炉子结构、炉管材料、管路系统支撑、管路系统应力、管路系统膨胀及补偿、燃烧、烟气流动及分配、耐火材料等各方面都必须精心考虑。
一、天然气制氢转化炉的炉型及结构1.1 炉型制氢装置转化炉按辐射室供热方式进行分类,可分为以下四种方式:1) 顶烧炉:这是很多公司都采用的一种炉型。
这种炉型的燃烧器布置在辐射室顶部,转化管受热形式为单排管受双面辐射,火焰与炉管平行,垂直向下燃烧,烟气下行,从炉膛底部烟道离开辐射室。
这种炉型的对流室均布置在辐射室旁边。
2) 侧烧炉:这种炉型以丹麦TOPSφE公司为代表。
这种炉子的燃烧器布置在辐射室的侧墙,火焰附墙燃烧。
早期转化管的受热形式多为炉膛中间的双排管受侧墙的双面辐射,由于受热形式不好,操作条件苛刻时,炉管易弯曲,现在大部分都改为单排管受双面辐射的形式。
这种炉子的烟气上行,对流室置于辐射室顶部,大型装置的对流室考虑到结构及检修等原因,对流室经常放置在辐射室旁边。
3) 梯台炉:这种炉型以美国FOSTER WHEELER公司为代表。
这种炉子的辐射室侧墙呈梯台形,燃烧器火焰沿倾斜炉墙平行燃烧,通过炉墙向转化管辐射传热。
与侧烧炉类似,转化管可以为双排或单排。
这种炉子的对流室全部置于辐射室顶部,烟气上行,采用自然抽风,没有引风机。
4) 底烧炉:这种炉型目前多用于小型装置。
燃烧器位于辐射室底部,烟气上行。
1.2炉型结构比较1) 传热方式顶烧炉的燃烧器安装在辐射室顶部,火焰从上往下烧,烟气流动方向与转化管内介质流动方向相同,传热方式为并流传热。
天然气制氢工艺及设备简介
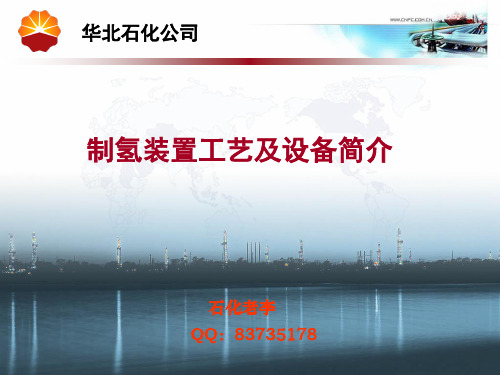
主要产品:
合格氢气
用氢单位:
渣油加氢、加氢裂化、柴油加氢、硫磺等
一、装置概述
技术路线:
造气部分引进Technip公司低能耗蒸汽转化制氢技术 吸附部分采用成都华西工业气体有限公司PSA净化工艺
技术特点:
技术先进、成熟可靠、灵活节能
转化炉的 参数特点:
三高:高转化入口温度、高转化出口温度、高碳空速 一低:低水碳比 特点:代表当今较先进的制氢技术水平。
炉型结构比较
工况的适应
顶烧炉上部供热较多,转化管采用抗积碳性能好的催化剂 时,可以很好的和转化反应相匹配,在反应最激烈处能供给 最多的热量,燃料放热分布与反应吸热分布较协调。但炉管 纵向温度不能调节,在操作末期或催化剂积碳时,上部反应 较少,管内介质温度升高很快,造成转化炉管的管壁温度升 高,对炉管寿命有影响,设计管壁温度也需要较大的裕量。 侧烧炉和梯台炉可以根据需要调节沿炉管长度方向受热的 负荷,对不同工况的适应情况较好。
原料气升 压及精制
转化
三、工艺过程
原料气升 预转化 压及精制
自系统管网来的干气经压缩机升压 后,与自界区来的天然气混合进入装置, 混合后原料压力4.0MPa(G)。
进入脱硫部分的原料气,首先经过钴钼加氢反应器,在钴钼 精制后的原料气,按水碳比 催化剂的作用下发生氢解反应,把有机硫转化为无机硫,有机氯 2.3mol/mol与工艺蒸汽混合,再经转化 转化为氯化氢。然后,加氢后的原料气通过脱硫反应器床层,在 炉对流段中原料/蒸汽预热段预热至 加氢反应器氯化氢与氧化钠反应,生成氯化钠,在脱硫反应器氧 470℃,进入预转化反应器。预转化反 化锌与硫化氢发生反应,生成硫化锌,达到脱氯、脱硫的目的。 应器为一绝热反应器,在催化剂的作用 精制后的气体中硫含量小于0.1ppm,进入预转化部分。
制氢装置简介

Co,MoO3
氧化锌脱硫 催化剂 转化催化剂 转化催化剂 中变催化剂
T-305
Z-417 Z-418 B113
ZnO,MgO
Ni,Al2O3 Ni,Al2O3 Fe2O3, Cr2O3
制氢装置主要设备(转化炉)
名称
炉型 辐射室数量 辐射室尺寸 炉管数量(根数/排×排)
数值
顶烧 1个 20000×10000×25000mm 共240根:(60根/排)×4
炉管尺寸(内径×外径×长) φ100×φ125.6×14510 mm 12000mm 炉管加热长度 920度 设计承受最高温度
制氢装置主要设备(转化炉)
名称 设计压力/实际压力 催化剂装填高度 催化剂装填总体积 烧嘴数量个数及分布 (个/排×排) 辅助烧嘴个数及位置 燃料
数值 3.25/2.9MPa 12000mm 22.6 m3 (16/排)×5
制氢装置催化剂装填的影响
由于催化剂装填高度高,装填精度要求高,因此 要求催化剂强度高,无破碎,无粉尘,防止出现炉 管压降偏差大,架桥等情况。由于装填问题导致炉 管压降偏差大,容易偏流,造成局部炉管积炭, 形成热管,出现热管需要停工烧炭,烧炭后热管 无法消失,则停工换剂,防止烧坏炉管。
制氢装置催化剂的装填 催化剂装填保证工艺气平均分配,在炉管中无 堵塞或架空现象,各炉管压降偏差不大于±5%, 充分发挥催化剂整体性能,装填时将称量好的催化 剂通过漏斗装入细布袋中,布袋一端系以长尼龙绳, 另一端折起10厘米,提着绳轻轻将袋子放入管底,然 后提起袋子,使催化剂落入管内,布袋提起高度小于1 米,全部装完一袋要震动炉管,测量床层高度,相差5 厘米为正常,超过要卸出重装.依次装2,3……,直至 装完.装完后测量阻力降,在偏差5%内正常,偏差大 的卸出重装.
- 1、下载文档前请自行甄别文档内容的完整性,平台不提供额外的编辑、内容补充、找答案等附加服务。
- 2、"仅部分预览"的文档,不可在线预览部分如存在完整性等问题,可反馈申请退款(可完整预览的文档不适用该条件!)。
- 3、如文档侵犯您的权益,请联系客服反馈,我们会尽快为您处理(人工客服工作时间:9:00-18:30)。
一、概述随着炼油厂加氢装置的逐渐增多,所需要的氢气也越来越多,使得制氢装置相应的发展很快。
目前大型工业装置采用的制氢方法均为烃类水蒸汽转化法,利用的原料主要有天然气、炼厂气、石脑油等轻质烃类。
这些烃类在特定的温度、压力以及催化剂存在的条件下与水蒸汽发生反应,生成氢气及一氧化碳。
烃类化合物的水蒸汽转化反应是一个复杂的反应平衡系统,高分子烃类先裂解或转化成甲烷,最终与水蒸汽进行转化反应。
大体上可用下列反应式表达:CnHm + 2H2O → Cn-1Hm-2 + CO2 + 3H2 – QCH4 + 2H2O = CO2 + 4H2 – QCO2 + H2 = CO + H2O - Q转化炉是制氢装置中转化反应的反应器,属于装置的心脏设备。
这是一种非常特殊的外热式列管反应器,由于转化反应的强吸热及高温等特点,这种反应器被设计成加热炉的形式,催化剂装在一根根的转化炉管内,在炉膛内直接加热,反应介质通过炉管内的催化剂床层进行反应。
转化炉苛刻的操作条件,使得这种炉子有很多有别于其它加热炉的特殊性,在炉子结构、炉管材料、管路系统支撑、管路系统应力、管路系统膨胀及补偿、燃烧、烟气流动及分配、耐火材料等各方面都必须精心考虑。
二、炉型及结构1.炉型制氢装置转化炉按辐射室供热方式进行分类,可分为以下四种方式:1)顶烧炉:这是很多公司都采用的一种炉型。
这种炉型的燃烧器布置在辐射室顶部,转化管受热形式为单排管受双面辐射,火焰与炉管平行,垂直向下燃烧,烟气下行,从炉膛底部烟道离开辐射室。
这种炉型的对流室均布置在辐射室旁边。
2)侧烧炉:这种炉型以丹麦TOPSφE公司为代表。
这种炉子的燃烧器布置在辐射室的侧墙,火焰附墙燃烧。
早期转化管的受热形式多为炉膛中间的双排管受侧墙的双面辐射,由于受热形式不好,操作条件苛刻时,炉管易弯曲,现在大部分都改为单排管受双面辐射的形式。
这种炉子的烟气上行,对流室置于辐射室顶部,大型装置的对流室考虑到结构及检修等原因,对流室经常放置在辐射室旁边。
3)梯台炉:这种炉型以美国FOSTER WHEELER公司为代表。
这种炉子的辐射室侧墙呈梯台形,燃烧器火焰沿倾斜炉墙平行燃烧,通过炉墙向转化管辐射传热。
与侧烧炉类似,转化管可以为双排或单排。
这种炉子的对流室全部置于辐射室顶部,烟气上行,采用自然抽风,没有引风机。
4)底烧炉:这种炉型目前多用于小型装置。
燃烧器位于辐射室底部,烟气上行。
2.炉型结构比较传热方式顶烧炉的燃烧器安装在辐射室顶部,火焰从上往下烧,烟气流动方向与转化管内介质流动方向相同,传热方式为并流传热。
侧烧炉燃烧器安装在辐射室侧墙,火焰附墙燃烧,通过辐射墙对转化管传热,烟气流动方向与管内介质流动方向相反,传热方式错流传热。
梯台炉的燃烧器排数比侧烧炉要少,是一种改进的错流传热。
底烧炉为逆流传热。
热强度及管壁温度温度分布由于不同的传热方式,所以不同炉型具有不同的热强度和管壁温度分布。
顶烧炉火焰集中在炉膛顶部,所以该处辐射传热能力非常强,具有非常高的局部热强度,同时该处的管壁温度也为最高。
最高管壁温度和热强度同时在转化管顶部出现峰值是顶烧式转化炉的特点。
该特点造成转化管有较高的设计壁温。
对于侧烧和梯台转化炉,由于燃烧器均匀分布在沿管长方向的不同标高,辐射传热比较均匀,可避免该峰值,从而降低设计壁温,减少转化管壁厚,节约高合金炉管,或允许较高的转化气出口温度,以降低残余甲烷,提高氢的产率。
在管壁设计温度相同时,侧烧炉和梯台炉可以允许较大的总平均管壁热强度,这样传热面积会相应减少,转化管数量有所下降。
底烧炉在传热性能上,具有炉顶热强度低,炉底热强度高的特性,因而炉管壁温变化最大,特别是炉底处炉管壁温是所有炉型中最高,对炉管寿命十分不利,为了控制最高管壁热强度不超标,只能选用很低的平均热强度,造成管材的巨大浪费,所以大型装置都不采用底烧炉。
结构特点顶烧炉的所有转化管排均在同一炉膛内,排列比较紧凑,节省占地面积,适于大型化。
侧烧炉和梯台炉由于是两个辐射室并列排列,所以在炉管数量相同时,占地面积较大,大型化有一定的困难。
顶烧炉的燃烧器数量较少,密集排列在炉顶,燃料配管及空气配管相应简化,但炉顶结构比较复杂。
侧烧炉燃烧器数量较多,分布在辐射室侧墙,燃料配管及空气配管较多。
对工况的适应情况顶烧炉由于在上部供热较多,所以在转化管内采用抗积碳性能好的催化剂时,可以很好的和转化反应相匹配,在反应最激烈处能供给最多的热量,燃料放热分布与反应吸热分布较协调。
但炉管纵向温度不能调节,在操作末期或催化剂积碳情况下,由于上部反应较少,管内介质温度升高很快,造成转化炉管的管壁温度升高,对炉管寿命有影响,设计管壁温度也需要取较大的裕量。
侧烧炉和梯台炉可以根据需要调节沿炉管长度方向受热的负荷,对不同工况的适应情况较好。
操作情况顶烧炉的燃烧器都集中在炉顶,造成炉顶的操作条件比较恶劣,由于炉顶的温度非常高,炉顶布置又非常紧密,正常操作过程中调节燃烧器有一定难度。
侧烧炉和梯台炉的燃烧器均布置在侧墙,操作条件和缓,对正常操作好处较大。
但侧烧炉由于燃烧器数量较多,点火时花费的时间比顶烧炉要长。
三、转化管系1.转化管系流程中压蒸汽与原料气混合后进对流室的原料预热段预热,然后出对流室,经过转油线至辐射室顶部的上集合管,从上集合管分配进入各上猪尾管,再经过上猪尾管进入装有催化剂的转化管进行转化反应,转化反应完毕的转化气从转化管底部经下猪尾管导出,下猪尾管与下集合管相连,在下集合管内汇集的转化气被送至与下集合管直接相连的工艺气废热锅炉发生蒸汽并降温。
某些出口操作温度较高的转化炉没有下猪尾管,转化管直接与下集合管连接。
2.转化管系零件上集合管上集合管是进气总管,主要用来将进料分配至各支管,根据原料预热温度的不同,上集合管可以采用铬钼钢、304、321等材质。
上猪尾管上猪尾管是进气支管,除了用来分配进料外,主要作用是吸收转化管和上集合管以及转油线的膨胀,所以要求材料的塑性要好,主要采用奥氏体不锈钢304、321等材质。
其管径主要有φ25、φ32等规格。
转化管该管直接置于炉膛内加热,由于要求良好的耐高温及抗高温蠕变性能,所以采用离心浇铸耐热合金管,早期的材质主要为HK40,后来又发展为HP40,这些年又出现了一系列新的改进型钢种。
下猪尾管主要用来吸收下集合管的膨胀,采用的材质主要为Alloy 800H。
下集合管根据装置规模的不同,下集合管有热壁和冷壁两种形式。
热壁下集合管的材质主要为Alloy 800H,冷壁下集合管的内壁为耐高温的衬里材料,外壁由于温度较低,可以采用普通碳钢或低合金钢。
3.转化管系的膨胀与补偿由于装置的大型化,制氢转化炉管路系统的热膨胀问题越来越突出。
大量的热膨胀问题要通过尾管和弹簧支吊架等热膨胀吸收元件和预留有足够的热膨胀空间来解决。
下集合管的膨胀下集合管的膨胀分为分集合管的纵向膨胀和总集合管的水平膨胀。
对于每排炉管分集合管较短的情况,分集合管和总集合管均可采用热壁管,分集合管的纵向膨胀和总集合管的水平膨胀所形成的转化管和集合管之间的相对位移可由下尾管吸收。
转化管直接与下集合管相连时,下集合管的膨胀量可以通过安装前对转化管进行一定的冷拉量来吸收。
对于每排炉管根数较多,分集合管较长的情况,可以通过以下途径解决管路系统的膨胀问题:1)采用冷壁的总集合管,分集合管的出口设在中部并通过总集合管引出。
这样热壁分集合管的膨胀量比从端部引出减少至原来的二分之一。
2)采用复合式分集合管,既将整根热壁集合管分成若干根口径较小的小热壁集合管,进一步减少热壁管的膨胀,并节约高合金热壁管的投资。
3)采用带尾管的全冷壁集合管。
4)采用不带尾管的全冷壁集合管。
从经济性来看,以上以上方案的优劣次序为:不带尾管的全冷壁集合管,带尾管的全冷壁集合管,复合式分集合管,冷壁总集合管热壁分集合管,全热壁集合管。
不带尾管的全冷壁集合管主要用于转化气出口温度大于880℃的情况。
因为在该工况下,Cr20Ni32材质的尾管的热态许用应力为9MPa以下。
为满足二次应力的强度要求,在880℃以上的高温下要求较长的尾管,为满足一次应力的强度要求,长的尾管和低的许用应力导致繁杂的甚至是无法实现的支撑结构。
但不带尾管的全冷壁集合管催化剂的装卸都得通过转化管顶端法兰完成,当催化剂积碳时,从顶端真空吸出催化剂是有困难的。
当某根转化管发生泄露时,也无法通过同时卡死上下尾管的方式将泄露转化管切除。
转化管和转油线的膨胀为减少转化管底部和下集合管的位移差,减少高合金下尾管的长度,节约投资,转化管一般采用底部支撑,向上膨胀的方式。
同样为减少转化管顶部和上集合管的位移差,减少上尾管的长度,转油线也采用底部支撑,向上膨胀的方式。
与转油线相连的上集合管则由弹簧吊架悬挂,并随上升的膨胀向上移动。
转化管尽管采用底部支撑,但为减小转化管底部的轴向压应力,防止转化管弯曲,在转化管顶部增设弹簧吊架。
上集合管的膨胀上集合管除随转油线向上移动以外,还沿轴向膨胀。
转化管向上膨胀、上集合管随转油线向上移动以及沿轴向膨胀所形成的转化管与上集合管的位移差由上尾管补偿。
四、对流室管系对流室管系主要用来预热原料、发生及过热反应用的蒸汽、回收烟气中的余热等等。
不同的工艺方案采用的对流室管系的布置方式略有不同,主要有原料/蒸汽混合过热段、蒸汽过热段、蒸汽发生段、燃烧用空气预热段。
五、转化炉主要工艺参数1.水碳比水碳比是指反应进口气体中水蒸汽分子数与烃类原料中碳原子数的比,常以S/C 表示,它表征了转化操作所耗蒸汽的量。
工业上采用的水碳比要比按化学平衡计算值大。
在一定条件下,水碳比越高,甲烷平衡含量越低。
但水碳比越高,过剩蒸汽量则越大,辐射室热负荷也越大,增大了装置无用的燃料消耗。
水碳比和原料种类、催化剂类型、下游路线的选择以及经济因素有关,天然气原料的水碳比较低,石脑油原料的水碳比较高。
目前制氢装置的水碳比大概在至之间。
2.压力烃类蒸汽转化是体积增大的可逆反应,所以压力增加,逆反应随着增加。
但为了减少压缩功、强化后续设备的生产以及为使结构紧凑等等,目前的蒸汽转化仍然是加压蒸汽转化。
转化炉操作压力和下游设备的要求(如变压吸附等)、原料供应压力、转化管设计温度、转化管材料有关,目前制氢装置的操作压力大概在左右。
3.出口温度烃类蒸汽转化是吸热反应,温度增加,反应向正方向移动,残余甲烷平衡含量下降。
转化管出口温度与操作压力、转化管设计温度、转化管材料以及经济因素有关,制氢装置的转化出口温度在780℃至900℃之间。
4.原料预热温度原料预热温度即是入转化管的温度,提高原料预热温度可降低辐射室热负荷,减少燃料消耗,但原料预热温度和原料类型、管路材料、以及经济因素有关,采用天然气为原料时可以采用较高的预热温度,采用石脑油为原料时,由于原料会裂解,所以不宜采用太高的预热温度。