汽车电器DFMEA-组合仪表系统装置
内外饰DFMEA-31 汽车仪表板出风口总成
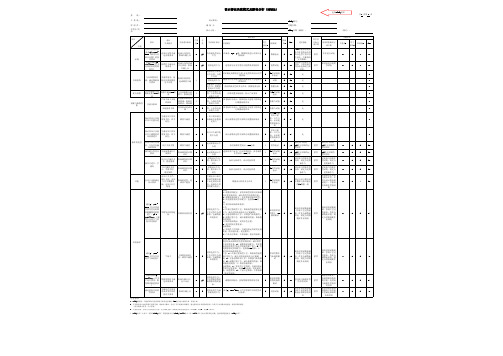
系 统 :子 系 统 :设计职责:零 部 件 :编 制 人:车型年/项目:
核心小组 :
3、严重度等级、分类与严重度对应关系、发生频度等级、探测度等级分别见附表一中图表1,图表2、图表3、图表4。
4“DFMEA清单”中每个“零部件DFMEA编号”需超链接至对应DFMEA的sheet表中,每个sheet表右上角中需附带返回键,返回键需超链接至“DFMEA清单”。
(修订):
1、DFMEA编制时,严格按照每个因素的填写说明进行编制,RPN值已输入函数关系,直接生成。
2、只有修改设计才能降低严重度等级,增加设计确认、验证工作只能减少探测度,通过修改设计来消除或控制一个或多个失效模式的起因、机理来降低频度。
一种失效模式仅有一个严重度。
关键日期:
DFEMA日期(编制):
设计潜在失效模式及影响分析(DFMEA)
共1 页第 1 页
DFMEA编号:。
汽车车身饰件DFMEA-上装饰件系统
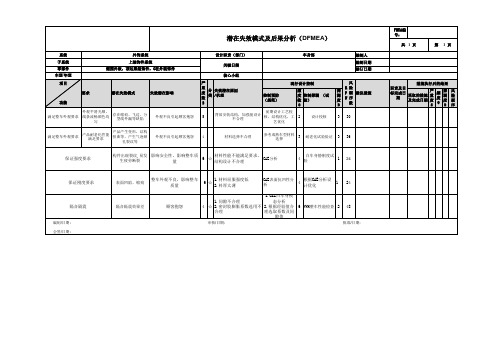
FMEA编 号:
共 1页
第 1页
措施执行后的结果
职责及目
标完成日 期
采取的措施 及完成日期
严 重 度 S
频 度 O
探 测 度 D
风 险 顺 序
表面凹陷、缩痕
整车外观不良,影响整车 质量
6
☆
1.材料屈服强度低 2.料厚太薄
CAE表面抗凹性分 析
4
根据CAE分析设 计优化
1
24
隔音隔震效果差
顾客抱怨
1.CAE白车身模
1.间隙不合理
态分析
4 ☆ 2.密封胶膨胀系数选用不 2.根据经验值合
合理
理选取系数及间
隙值
审核/日期:
6 NVH整车性能检查
2 48 批准/日期:
潜在失效模式及后果分析(DFMEA)
系统 子系统 零部件 车型/年型
项目
外饰系统 上装饰件系统 侧围外板,顶边梁装饰件,C柱外装饰件
要求
潜在失效模式
失效潜在影响
功能
满足整车外观要求
外观平滑光顺, 线条流畅颜色均
匀
存在缩痕、飞边、分 型线外漏等缺陷
外观不良引起顾客抱怨
设计职责(部门)
车身部
关键日期
核心小组
产品产生变形,结构 扭曲等,产生气泡锁
孔裂纹等
外观不良引起顾客抱怨
4
材料选择不合理
参考成熟车型材料 选择
3
耐老化试验验证
3
36
保证强度要求
构件出现裂纹,易发 生疲劳断裂
影响安全性,影响整车质 量
6
☆
材料性能不能满足要求, 结构设计不合理
CAE分析
4
白车身静刚度试 验
汽车电器DFMEA-车载终端

。
使用; 天线设计需要阻抗匹
配; 通信模块增加屏蔽 罩,增强抗干扰能
力;
4
线束加屏蔽。
性能测试 性能测试 性能测试
2 20 3 54 3 72
Box升级中断后无法
远程升级中断后无 法正常工作
远程升级中断后T-Box总 成无法正常工作
重新连接升级,导 致T-Box总成无法继 续升级且无法正常
死。
T-Box远程升级支持 断电重连后继续进行 软件后续升级的升级 方式,且升级成功前 旧版本软件依然可以 正常工作(软件回滚)
。
3
B
电池管理方案失效;电 池质量差
优化电池管理方案, 禁止过充过放;电池 充放电技术指标达标
2
1、给T-Box设定休眠
T-Box总成因涉及到国 条件,T-Box总成在
标数据上传功能,故需 KEYOFF&接收不到整
B
接常电;在接常电的情 车CAN报文后进入休
况下如无判断条件,则
眠模式。
3
无法正常进入休眠模式 2、TBOX符合休眠网
。
络管理规范
升级测试 性能测试 性能测试
3 54 2 32 2 24
T-Box自检功能失效
自检功能失效
不能正常自检导致 无法进入正式工作 6
状态
B
CPU故障,自检出现卡死 审核电气原理、技术
6
工作。
1. 不符合国家要求
(断电前10min的信
后备电池失效
整车异常断电后,不能 将数据传输到平台
息上报到平台) 2. 不能上报异常事
8
件
T-Box总成无法进入 休眠模式
T-Box总成在整车休眠后 未进入休眠模式
DFMEA-汽车空调 - 系统
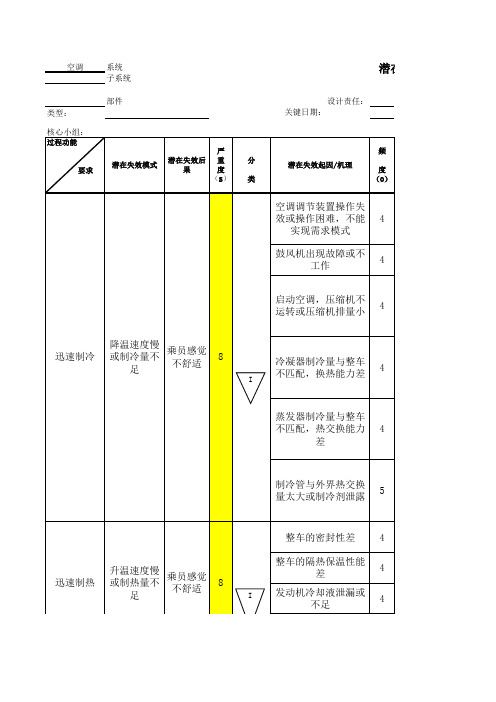
3
90
样件装车 试验验证
项目组
对安装结构和功 能部件进行优化
更换滤网
及时清理
4
72
FMEA编号: 页码: 第 页 编制人: FMEA日期(编制):
潜在失效模式及后果分析 (系统FMEA)
共
页
(修订)
现行设计控制
预防
探测
风 探 险 R 测 顺 P 度 序 N (D) 数
措施执行结果 建议措施 责任及目标完 成日期
采取的措施
要求厂家进行密封 加强出厂进行密 性实验,并出具相 封性试验 关报告
2
48
3D设计改进
CFD
2
32
3D设计改进
CFD
2
32
要求厂家进行相关 对鼓风机进行噪 实验,并出具报告 声试验
2
32
要求厂家进行相关 对压缩机进行噪 实验,并出具报告 声试验
2
32
3D设计改进
进行零部件性能 试验,检查接插 件安装情况
I
蒸发器芯体密封性差 冷凝器密封性能差 制冷剂循环不畅,连 接管路接头密封性能 差
4
由于风道结构造成噪 音大
4
噪音小
大于70dB(A)
不符合法
4
由于风道结构造成噪 音大
4
噪音小
大于70dB(A)
不符合法 规
4
N
鼓风机运转时噪音太 大
4
压缩机运行稳定性 差,噪音大
4
操纵方便
乘员操纵 空调装置操 不方便, 纵手感差或 产生抱怨 操纵失效 。
4
4
4
迅速制冷
8
I
冷凝器制冷量与整车 不匹配,换热能力差
DFMEA 仪表板总成

不能通过法 不能有效阻燃 规
4
F 选用材料质 量差
安装牢固可靠
翘出
影响整车品 质,不美观
3
I
安装卡扣松 脱
4
方案讨 论
失效模式及后果分析 (设计FMEA)
编制人: FMEA日期(编制):
FMEA编号NO: 页码: 第 1 页
共 1 页
(修订)
现行设计控制
探测
风 探 险 R 测 顺 P 度 序 N (D) 数
仪表板
系统 子系统
潜在失效模式及后果分析 (设计FMEA)
设计责任: 关键日期:
仪表板总成 部件 年度车型/车辆类型: 核心小组:
项目 潜在失效模式 潜在失效后果 严 重 度 (S)
频 分 类 潜在失效起因/ 机理 度 (O)
现行设计控制
功能
预防
装饰
卡脚断裂
仪表板易松 动,产生噪 音
3
I
卡脚结构设 计薄弱。
装饰
表面有缩痕
影响外观品 质
3
I
产品料厚不 均匀或有料 厚突变现象
3
置物
杂物盒周边 杂物盒变形, 间隙不均 错位 匀,影响美 观 不能通过法 规Biblioteka 2I产品变形
杂物盒 4 背面加 加强筋 选用通 过法规 4 要求材 质 选用通 过法规 4 要求材 质
R
无刺激性气味
有刺激性气味
4
选用材料质 量差
满足阻燃要求
卡脚后 3 面加加 强筋
置物
杂物盒关闭不 杂物盒无法 紧 正常使用
3
I
杂物盒抠手 卡接量太少
4
方案讨 论
装饰
仪表板前缘与 装配困难 钣金等干涉
汽车车身饰件DFMEA-仪表板总成

点之前,仪表板腰线
以上零部件,突出高度
≤3.2,且小于宽度的
突出高度有问题;
一半,倒角要求;
接触圆角太小;
圆角:前排座椅H点之
CAS及A面评审:
★
刚性支架位置在接触区 前,仪表板腰线以上
域;
零部件,R≥3.2;
2
数据审核: CAE分析、头碰试
2
40
仪表板零件材料选择导 刚性支架位置:覆盖
验实验
致结构刚度过大
★
距离偏小;
比例推荐值10:80:10.
◆出风方向。格栅导向 2.空调除霜风道总面
距离偏小;
积大于等于15000cm2.
2
总布置校核; CAE分析; DV验证试验 PV验证试验
3
54
95%;侧玻璃除霜要
◆开口面积。空调出口
求:25分钟后看清
及各除霜风道风量分配
左外后视镜
不合理;
30分钟后看清右外
◆开口面积。空调出口
组合仪表炫目
合仪表,影响驾 驶安全性和舒适
8
☆
侧窗玻璃直接照射在组 1 在校核DVD屏目时, 合仪表可视区域造成炫 要校核屏目反光问
3
3
72
性。
目;
题,要校核阳光照射
到屏目的范围,不能
超过60%,
驾驶员无法看清
安全法 规
防炫目要 求
仪表板总成零件部 造成反光炫目
光亮件反光炫目
驾驶视野,影响 驾驶安全性和舒
系统 子系统 零部件
内饰系统 仪表板系统 仪表板总成
年型/车型
项目 功能
要求
严 重 潜在失效模式 失效潜在影响 度 数 S
车辆容易燃烧,
汽车空调系统设计DFMEA案例分析

汽车空调系统设计DFMEA案例分析DFMEA简介DFMEA(Design Failure Mode and Effects Analysis,设计失效模式与影响分析)是一种常用的质量管理工具,用于在产品设计阶段识别并解决潜在的失效模式及其影响。
本文将以汽车空调系统设计为案例,探讨如何应用DFMEA来提高汽车空调系统设计的安全性和可靠性。
一、设计失效模式与影响分析(DFMEA)DFMEA是一种以系统化和有序方式对产品设计进行评估和分析的方法。
它的主要目的是识别可能的失效模式、评估其严重程度以及制定相应的纠正和预防措施。
下面我们将根据DFMEA的步骤,对汽车空调系统进行案例分析。
1. 制定DFMEA团队与范围首先,确定参与DFMEA的团队成员,包括汽车空调系统设计的工程师、质量控制专家、测试工程师等。
明确DFMEA的范围和目标,以汽车空调系统各个子系统为分析对象。
2. 识别失效模式对汽车空调系统设计进行全面的分析,列举可能的失效模式。
比如,制冷剂泄漏、温度控制失效、空调系统过热等。
3. 确定失效模式的可能原因针对每个失效模式,分析其潜在的原因,如设计不当、材料选择不当、制造工艺缺陷等。
以制冷剂泄漏为例,可能的原因包括密封件老化、接口松动等。
4. 评估失效的严重程度对每个失效模式进行严重程度评估,考虑其对汽车空调系统性能、安全性和可靠性的影响。
以温度控制失效为例,可能导致车内温度无法调节,对车内乘客的舒适度产生较大影响。
5. 确定控制措施针对每个失效模式确定相应的预防和纠正措施,以减少失效概率和降低失效的严重程度。
比如,在设计阶段增加密封件的检测和更换计划,严格控制安装过程中的接口紧固力矩。
6. 跟踪执行和评估效果实施控制措施后,跟踪其执行情况,并对效果进行评估。
通过实际数据的反馈,不断优化和改善汽车空调系统的设计。
二、汽车空调系统DFMEA案例分析以下是针对汽车空调系统的DFMEA案例分析,以帮助读者更好地理解DFMEA方法的应用。
DFMEA表(新版DFMEA-总装结构)

3L
尺寸链的计算 2 尺寸检验
3L
尺寸链的计算 2 尺寸检验
3L
尺寸链的计算 2 尺寸检验
3L
尺寸链的计算 2 尺寸检验
3L
尺寸链的计算 2 尺寸检验
3L
轴套设计 安装尺寸要 格,客户不满
求
意
6
控制臂总 成
保证产品的 安装尺寸要
求
安装尺寸不合 格,客户不满 意
零部件分析
零部件 要素(项
目/接 口)
零部件的功 能,要求,预 期输出及特性
失效原因
壳体
零件的尺寸设 计满足要求
尺寸设计不当
轴套
零件的尺寸设 计满足要求
尺寸设计不当
控制臂
零件的尺寸设 计满足要求
公司名称: 制造地址: 顾客名称: 车型/项目:
项目: FMEA开始日 FMEA修订日 跨职能团
设计潜在失效模式及影响分析 FMEA编号: 过程职责: 保密级别:
版本号:
页 码:
第
页,共
页
编制者/日期:
批准/日期:
范围定义:(针对具体产品详细说明) 1、产品适用车型: 2、客户针对此项目的特别要求:含技术要求、法律合规性、目录和标准零件 3、明确设计控制权及客户对接部门: 4、FMEA团队及会议机制: 5、FMEA完成步骤时间节点及要求:
尺寸设计不当
压装盖 板
零件的尺寸设 计满足要求
尺寸设计不当
齿环
零件的尺寸设 计满足要求
尺寸设计不当
齿型连 接套
零件的尺寸设 计满足要求
尺寸设计不当
O型圈*2
零件的尺寸设 计满足要求
尺寸设计不当
启动准备工作:(针对具体产品详细说明) 1、顾客要求转化清单: 2、FMEA的边界分析证据:设计框图、边界图、示意图、图纸、3D模型 3、类似设计经验教训:物料清单、风险评估、FMEA、防错要求、可制造性和可装配性设计、质量功能展开、质量/可靠性 历史(内部、零公里、现场失效、保修和索赔) 4、技术新颖性、创新程度、设计复杂性、人员和系统安全、网络物理系统 5、产品设计和使用的工况环境情况说明:
汽车电器_车身控制系统_DFMEA
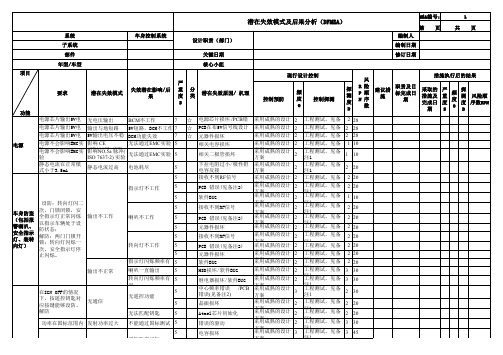
整,壁厚过厚,导致零 型工艺,将零件
件整体缩水变形
的加强筋骨布局 3
测量检查
2 24
由于材料特性造成注塑 将前框和后壳内 A样件验证,尺寸
成型时易出现变形 增加加强筋
测量检查
选用的材料不合理
根据技术协议, 3 高低温实验验证 5 50 选用合理的材料
控制模块装配后,零件
未压到线路板,起不到
Z方向的固定作用
5
静态电流在正常模 静态电流过高 电池耗尽 式小于3.5mA
5
5
指示灯不工作
5
车身防盗 (包括报 警喇叭、 安全指示 灯、装转 向灯)
设防:转向灯闪二 次、门锁闭锁,安 全指示灯正常闪烁 输出不工作 以指示车辆处于设 防状态; 解防:两门门锁开 锁;转向灯闪烁一 次、安全指示灯停 止闪烁。
输出不正常
3D数模模拟装配 3 A样件试装后验证 5 60
控制模块装配后,零件
与后壳装配的卡扣设计
零件的加强筋骨不完 依据塑胶件的成
A样件验证,尺寸
整,壁厚过厚,导致零 型工艺,将零件
件整体缩水变形
的加强筋骨布局 3
测量检查
2 24
由于材料特性造成注塑 将前框和后壳内 A样件验证,尺寸
成型时易出现变形 增加加强筋
在IGN OFF的情况 下,按遥控钥匙对 应按键能够设防、 解防
无通信
5
5
喇叭不工作
5
5
5
转向灯不工作
5
5
指示灯闪烁频率有 5
误喇叭一直输出
5
转向灯闪烁频率有 5 误
5 无遥控功能
5
无法匹配钥匙
5
功率在国标范围内 发射功率过大 不能通过国标测试 5
汽车电器DFMEA-电机控制器

系统
/
子系统
/
零部件
/
车型年/项
目
核心小组
潜在失效模式与影响分析
(设计FMEA)
性能/外观满足 客户要求,符 合安全性和法 律法规,易与 设计职责 生产装配。
关键日期
FMEA编号 共 1 页,第 1 页
编制人 FMEA日
期(原
项目 功能
要求
潜在失效模式
失效潜在影响
严重度 (S)
失效潜在原因
控制 预防
完成日期 采取的措施 严重度 发生度 探测度 完成日期
RPN
线路板设计
及关键元器
件选择
电压/电流参数
IGBT模块选型合 低,功率损耗
理
大,开关特性
影响控制器性能
6
选型不合理
重新选型,参考同 类产品设计
2
设计评审,元件 规格书参数
5
60
差,温升快
IGBT驱动芯片及 无隔离,驱动/关
电源选型合理
断能力差
4
48
求,接头符合防
水要求
接头不防水
影响控制器寿命 7
接头选型不合理
重新选型,调整机 壳接口设计
2
设计评审,样机 试装
4
56
控制器机壳
结构设计 机壳承受10KPa 压强不变形
抗压能力差
客户不满意退货
6
机壳材料选型不合 重新调整,参考同 理,壁厚设计太薄 类产品设计
3
机壳机械强度测 试
4
72
机壳防尘防水能 有效保护线路板
影响控制器性能
6
选型不合理
重新选型,参考同 类产品设计
2
设计评审,元件 规格书参数
汽车电器DFMEA-DC
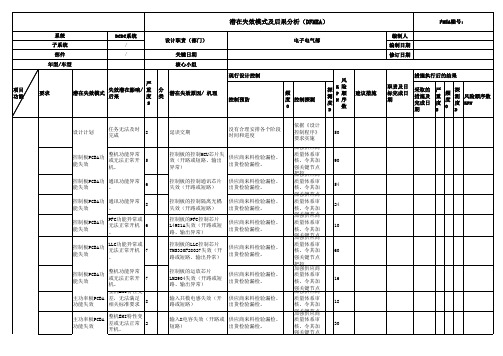
能失效
。
8
控制板PCBA功 能失效
PFC功能异常或 无法正常开机 6 。
控制板PCBA功 能失效
LLC功能异常或 无法正常开机 7 。
控制板PCBA功 能失效
整机功能异常 或无法正常开 机。
7
整机EMI特性变
主功率板PCBA 差,无法满足
功能失效
相关标准要求
8
。
主功率板PCBA 功能失效
整机EMI特性变 差或无法正常 2 开机。
主功率板PCBA 功能失效
LLC功能异常或 无法正常开机 7 。
主功率板PCBA 功能失效
LLC功能异常或 无法正常开机 8 。
主功率板PCBA 功能失效
LLC功能异常或 无法正常开机 2 。
输入Y电容失效(开路或 供应商来料检验漏检、
短路)
出货检验漏检。
加强供应商 质量体系审 核、令其加
18
辅助电源变压器失效 (开路或短路)
质量体系审 核、令其加
54
强加关强键 供节应点商
控制板的控制隔离光耦 供应商来料检验漏检、 失效(开路或短路) 出货检验漏检。
质量体系审 核、令其加
24
控制板的PFC控制芯片 L4981A失效(开路或短 路、输出异常)
供应商来料检验漏检、 出货检验漏检。
强加关强键 供节应点商 质量体系审 核、令其加 强加关强键 供节应点商
项目 功能
系统 子系统
部件 年型/车型
DCDC系统 / /
设计职责(部门)
关键日期 核心小组
要求
严
潜在失效模式
失效潜在影响/ 后果
重 度
S
分 类
潜在失效原因/ 机理
汽车电器DFMEA-开关系统装置

及试验
加验强证设
计方案
2 12 的评审
及试验
开验发证控
3 42
制及耐 久试验
验证
安装可靠 性
装配稳定 性
开关触点 电压稳定
性
插接端子 可装配性
插片可装 配性
防尘稳定 性
耐电流强 度稳定性 耐光稳定
性
耐温性
长期使用 可靠性
开关安装困难
顾客不满
5
开关失灵 电压降过大
部分功能失效顾客 抱怨
4
开关灵敏性降低, 顾客不满意
与行程有关的尺寸公 差设计不合理;回位
部件设计不合理
回位部件设计不合理
潜在失效模式及后果分析(DFMEA)
电子电气部
现行设计控制
控制预防
频
度
控制探测
O
设计评审
4
样件检测
数模验证
2
样件检测
数模验证
2
样件检测
数模验证
2
样件检测
设计评审
3
型式试验
设计评审
2
型式试验
设计评审
3
样件检测
设计评审
2
样件检测
数模验证
项目
功能 外观 外观 外观 外观 防水性 金属外观 操纵力
操纵感
行程 回位可靠
性
系统 子系统
部件 年型/车型
开关系统 / /
设计职责(部门)
关键日期 核心小组
要求
潜在失效模式
失效潜在影响/后果
严 重分 度类 S
潜在失效原因/ 机理
按钮及开关主表面变形
外观不协调,顾客不 满意
4
开关装车后,按钮与安装 外观不良,顾客不满
汽车电器DFMEA-灯具系统装置
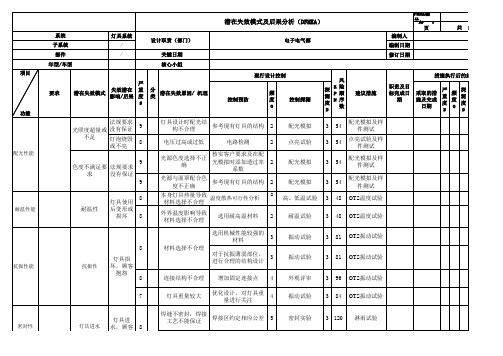
3 28 样件测试
按照制定的标
2
24
准进行检验, 并到客户处确
认
2 36 外观检测
审核:
批准:
共1页
后的结果 风险顺序数 RPN
项目 功能 配光性能 耐温性能 抗振性能 密封性
系统 子系统
部件 年型/车型
灯具系统 / /
设计职责(部门)
关键日期 核心小组
要求
严
潜在失效模式
失效潜在 影响/后果
重 度
S
分 类
潜在失效原因/ 机理
潜在失效模式及后果分析(DFMEA)
电子电气部
编制人
FMEA编 号第: 1
页
编制日期
修订日期
共1页
现行设计控制
3 81 OTS振动试验 3 81 OTS振动试验 3 96 OTS振动试验
7
灯具重量较大
优化设计,对灯具重 量进行关注
4
振动试验
3 84 OTS振动试验
灯具进水
灯具进 水,顾客 8
抱怨
焊缝不密封,焊接 工艺不能保证
焊接区约定相应公差
5
密封实验
3 120 淋雨试验
密封性
抗应力特 性
抗腐蚀性 能
耐紫外线 性
控制预防
频
度
控制探测
O
风
探 测 度 D
R险 P顺 N序
数
建议措施
措施执行后的结果
职责及目 标完成日
期
采取的措 施及完成
日期
严 重 度 S
频 度 O
探 测 度 D
法规要求 光照度超量或 没有保证
9
不足
灯泡烧毁 或不亮
汽车电器DFMEA-线束系统装置

风
探 测 度 D
R险 P顺 N序
数
建议措施
措施执行后的结果
职责及目 标完成日 期
采取的措施及完 成日期
严 重 度 S
频 度 O
探 测 度 D
风险顺序数 RPN
功能不起作用,车辆 熄火
10
VCU、控制模块等关键接插 关键零部件的插件厂家及
件接触不良(振动、环境恶 型号采用供应商指定的插 3
劣)
接件厂家及型号
系统 子系统
部件 年型/车型
线束系统 / /
设计职责(部门)
关键日期 核心小组
项目 功能
要求
潜在失效模式
严
失效潜在影响/后果
重 度
S
分 类
潜在失效原因/ 机理
潜在失效模式及后果分析(DFMEA)
电子电气部
编制人 编制日期 修订日期
FMEA编号: #NAME?
现行设计控制 控制预防
频 度 控制探测 O
7
无固定或固定不合适 断路
按照线束设计指导规范进 行线束布置及固定
4
试装
2 56
按照线束设计指导规范进 行线束布置及固定
4
路试搭载
2 56
与运动件干涉
按照线束设计指导规范进 行设计线束固定及走向布 1 置
路试搭载试 装
3 21
与动态件相连,分支余量不 根据动态件的行程,线束
够
分支长底做相应的预留
3
路试搭载试 装
3 21
配电盒极柱端子不防错
配电盒极柱型式、极柱大 小采用防错装置或标识
3
台架实验
2 48
压降过大(端子锈蚀、镀层 、导线线径过小)
汽车车身饰件DFMEA-组合仪表罩总成

☆
撞距离要求
100mm
驶员造成更多伤
组合仪表罩总成视野
组合仪表罩 总成不可遮 挡仪表可视
区域
组合仪表在视野 可视范围内不被 遮挡,视野清晰
仪表视野遮挡
看不清仪 表,影响驾 驶员安全性
和舒适性
8
☆
可靠耐久性/可靠性/环 境条件/温度湿度
组合仪表罩 总成
高温变形翘曲, 轮廓和曲面歪斜 仪表板系统及其 、高温接合面分 子系统需要在 离、高温气泡、 95%的车辆使用 粉化、渗出、缩 温度和湿度条件 孔、高温纹理消 下功能可靠 失、高温装饰层 膨胀、高温变形 、功能失效低温
间隙定义不合理
相互配合结构符合BP 规范IP-11021
数据评审/设 3 计校核/实车 2
验证
1、节点审
核,M2节点
3
仪表板系统对M1数据进
3
行评审确认
组合仪表罩总成卡子 卡紧力不够,卡口结 构未按照数据调整到
位
1、概念设计时,此项 校核不充分 2、设计评审
设计时未考虑组仪表 设计时做好组合仪表 罩总成单独拆卸空间 罩单独拆DMU校核
齐
灰边
怨
4
☆
组合仪表罩总成 组合仪表罩总成
与组合仪表配合 与组合仪表间隙
规避摩擦异响
不合理
间隙小产生 摩擦异响
4
☆
组合仪表罩 总成满足紧 固良好的要
求
组合仪表罩总成 禁锢良好
组合仪表罩总成 禁锢不良,组合
仪表罩易晃动
舒适度不 佳,影响内 饰质量评价
4
☆
组合仪表罩 总成
组合仪表罩总成 在不拆卸仪表板 条件下具备维修
要求
组合仪表罩要拆 卸仪表板才能维
DFMEA

40
机绕组 对机壳 的工频
2500V的耐压限值的工 频正弦耐电压试验,无 击穿现象,漏电流≤
无法满足工频 耐压要求
使用中,耐压 达不到,电机 性能受影响
7
耐电压 100 mA。
*
电机设计不 依照GB/T18488.1合理 2015标准设计
使用安规综 3 合测试仪检 2 42
测
ISG电 ISG电机绕组能耐受
电机设计不 依据技术协议,设 合理 计电机
电机设计不 依据技术协议,设 合理 计电机
*
电机设计不 依照GB/T18488.1合理 2015标准设计
*
电机设计不 依照GB/T18488.1合理 2015标准设计
1 委外检测 4 20
1 委外检测 4 20
1 委外检测 4 20
3 电桥检测 2 30
3 电桥检测 2 30
机控制 器安装
Φ14(mm)
孔径
产品名称
产品型号 项目工程师
审核
类别
编制日期 日期 批准
NO 修订日期 版本
① 变更 ② 履历 ③
④ ⑤
修订内容
修订人
严管
潜在失效模式
潜在失效后果
重 度
制 特
(S) 性
失效的潜在 原因/机理
现行过程控制
控制预防
频度 (O)
控制探测
探 风险 测 顺序 度数 (D) RPN
建议措施
改善措施效果确认
负责
采取的措 施
严重度(S)
频度 (O)
探测 度(D)
RPN
过压或欠压
电机控制器无 法工作,电驱 8 动无法工作
*
供电系统出 现问题
- 1、下载文档前请自行甄别文档内容的完整性,平台不提供额外的编辑、内容补充、找答案等附加服务。
- 2、"仅部分预览"的文档,不可在线预览部分如存在完整性等问题,可反馈申请退款(可完整预览的文档不适用该条件!)。
- 3、如文档侵犯您的权益,请联系客服反馈,我们会尽快为您处理(人工客服工作时间:9:00-18:30)。
表盘颜色不符合用户要 求
用户不满意
6
表盘上报警符号及显示 汽车在行驶时,驾
符号的形状不符合用户 驶员难以读取仪表 6
要求
指示值
B
油墨的颜色选用不当
B
表盘上报警符号的形状 设计不合理
规定油墨的颜色标 3 准,并印制样件确 2 36
认
依据用户的产品功 3 能规范的要求制作 2 36
效果图确认
LCD漏白光
项目
功能
前框、面 板:
为仪表的 外观装饰 提供适当
的面; 保护仪表 免受天气 等外部原
因的干 扰;为仪 表中表盘
的固定
指针组 合:指示 各仪表的 正确数值
系统 子系统
部件 年型/车型
组合仪表系统 / /
设计职责(部门)
关键日期 核心小组
要求
潜在失效模式
严
失效潜在影响/后果
重 度
分 类
S
潜在失效原因/ 机理
面板的阻燃性能差 用户装配尺寸超差
影响车辆的安全行 驶
面板与汽车前围贴 合不紧凑
9 A ( D ) 未采用正确的材料
6
B
面板曲率设计不合理
面板表面有折光 面板的透明度差
影响产品指示的可 视性
6
影响产品外观和产 品的指示的可视性
5
前框与面板焊接不可靠 仪表得不到保护 6
B
面板曲率设计不合理
B
选用的材料不合理
固定LCD
调节按钮 和调节 杆:
调整时间 的设置和 里程模式
转化
导光支架尺寸和线路板 的电子元器件之间发生
干涉
装配困难,元器件 受损
5
导光支架上与PCB板配 B 合的端面结构设计不合
理
线路板与导光支架装反 (线路板的正面——即 与后壳无法装配 6
LED焊接面朝下)
导光支架上固定线路板 B 的左、右定位柱的尺寸
潜在失效模式及后果分析(DFMEA)
电子电气部
控制预防
现行设计控制
频
度
控制探测
O
风
探 测 度 D
R险 P顺 N序
数
3
2 54
采用绘图软件中的
2
干涉检查的功能对 产品的装配图进行
2
24
干涉分析
2
2 24
2
2 20
2 耐振动性试验 3 36 2 耐振动性试验 3 36
2
4 48
依据步进电机的图 纸,
3 将指针轴孔径控制 2 36 在Φ0.975±0.005 (mm)
对称的形式
将导光支架上固定
3
调节按钮的圆槽端 面加高即低于表盘
2
36
装配面0.2mm
采用绘图软件中的 干涉检查的功能并 3 和PCB小组联合对产 2 36 品的装配图进行干
涉分析
将LCD导光支架上增 加防错的定位措施 3 ——即将左、右定 2 36 位柱的位置设计为
不对称的行驶
采用绘图软件中的
2
干涉检查的功能, 对产品的装配图进
是对称的
调节按钮的根部漏光
影响产品的外观质 量
6
导光支架上固定调节按 B 钮的圆槽端面的高度过
低,导致漏光
LCD指示失效,出现丢字 段等现象
驾驶员无法读取信 息、给驾驶员错误
的信息
6
B
导光支架用于支撑LCD 的部分结构设计不合理
LCD导光支架与线路板装 LCD上的显示内容颠
反(左、右颠倒)
倒,导致返工
6
LCD导光支架上的左、 B 右定位柱的尺寸是对称
的
调节功能失效
转换模式不可靠 6
B
调节杆上与PCB匹配处 倒勾尺寸不合理
采用绘图软件中的 干涉检查的功能并 3 和PCB小组联合对产 2 30 品的装配图进行干
涉分析
将导光支架上增加 防错的定位措施— 2 —即将左、右定位 2 24 柱的位置设计为不
汽车在行驶时,驾 驶员难以读取仪表
指示值
9
A(D)
表盘上报警符号的形状 设计不合理
依据用户的产品功能 规范的要求制作效果
图确认
3
符合客户要求
2 54
表盘与导光支架之间发 生干涉
生产装配困难
5
B
表盘装配孔的中心位置 及内径尺寸设计不合理
采用绘图软件中的
3
干涉检查的功能对 产品的装配图进行
2
30
干涉分析
器件之间发生干涉
受损
6
B
后壳上支撑PCB板的结 构设计不合理
采用绘图软件中的
3
干涉检查的功能, 对产品的装配图进
2
36
行干涉分析
3
在后壳中设置散热 孔
2
36
采用绘图软件中的 干涉检查的功能并 2 和PCB小组联合对产 3 36 品的装配图进行干
涉分析
MCU处理能力受限
后续扩展功能无法 增加
7
EMI/EMC不合格 电源反接试验不合格
2
24
行干涉分析
后壳: 保护仪表 免受天气 外部原因 的干扰;
为线路 板,前框 组合的支
撑件
MCU
电源模块
用户装配尺寸超差
用户装配困难 6
零件上装车定位孔的孔 B 径尺寸及位置尺寸设计
不合理
因电子元器件长期工作 发热,导致电子元器件 产品的功能失效 6
失效
B
后壳未设计散热孔(不 利于散热)
后壳和线路板的电子元 装配困难,元器件
影响产品的外观质 量,用户不满意
6
表盘上与LCD匹配的窗 B 口尺寸同LCD显示区域
尺寸一致
将表盘上与LCD匹配
2
的窗口尺寸缩小— —即比LCD显示区域
3
36
尺寸小1.0mm
表盘上报警符号的位置 不符合用户要求
用户不满意
5
B
报警符号的位置设计不 合理
驾驶员无法读取信 显示符号之间互相串光 息、给驾驶员错误 6
的信息
B
பைடு நூலகம்
导光支架中各灯室之间 的厚度过小(1.2mm)
依据产品功能规范 3 的要求制作效果图 2 30
确认
3
灯室间的厚度控制 在1.5mm~2.0mm
2
36
导光支 架:对表 盘、指针 的照明、 报警和指 示符号的 显示起导 光作用; 为表盘、 显示片、 LCD、调 节杆等零 件的支撑
件
LCD导光 支架:
前框凸台设计不合理,
造成焊接质量差 面板配合端面设计不合
B
理
零件材料不合理
指针与步进电机轴配合 产品的指示功能失
松
效
6
B
指针轴孔尺寸(Φ 0.99)及公差不合理
指针的照明效果不好
汽车在夜间行驶 时,驾驶员难以准 6 确读取仪表指示值
指针臂的内部导光面的 倾斜角度不合理(20
°) B
指针臂选用的材料不合 理
仪表容易受外界干
扰;同时会影响其 他电子部件无法工
7
1、保作险烧毁
2、TVS烧毁,后续
出现高压仪表存在 7
烧毁的可能性
仪表工作不正常
仪表出现闪屏、小 计里程丢失、时间 8
日期复位,黑屏
1、设计初期对仪表
1、设计初期MCU选型余 所需采集的信号进行
量不足 2、整车需求变化大
依据设计手册和 同类产品的设计结 3 构,将导光面的倾 2 36 斜角度控制在45°
±1°
2
3 36
标盘: 指示汽车 行驶状态
导光支
指针臂颜色不符合用户 要求
用户不满意
6
B
油墨的颜色选用不当
规定油墨的颜色标 3 准,并印制样件确 2 36
认
表盘上的报警符号(如
单位标识km/h、充放电 、低电量、温度、冷却 液位、左转向、右转向 、远光灯、)的形状不