固态硅胶模具试模前检查表
模具检查表(新型)(XLS)

模具检查表(新型)
最终检查日: 检查员: 模具番号: 模具品名: 厂家验收 顾客验收 设计担当
分 类
嵌和有无问题 有无防转销 是否打字码 (考虑保养) 是否有火(HRC58~60确认品质)
检 查 项 目 (径 杆 顶管冷却有无问题 顶管高度有无问题 时间差顶杆动作有无问题 (动作量) 孔内径是否用铰刀加工 是否使用了特殊型号(扁形 极细 阶梯 其他) 有无干涉 (径. 间距) 回 导柱是否使用沾火料 程 杆 回程杆的碰面是否良好 回程杆的头部是否倒角 推板上是否有冷却 厚度是否够. 是否会弯 推 分型面是否设计缓冲块或勒聚胺脂块 板 回位弹簧和导柱的位置设计有无问题(因弯曲而动作不良) 在表面按回位弹簧时要在背面把螺丝 角落的镶块要注意斜度的设定和推杆孔的间隙 顶 环式镶块要却认是否有冷却 出 环式镶块的有配管型. 动作时要确认是否有干涉 镶 块 环式镶块顶出时是否会因重量发生平衡不良(支点确认) 动作部位是否使用了无油导套和轴承 顶板和芯子和顶杆导柱位置有无错位 设定的行程能否顺畅动作 是否使用了中荷重的弹簧 早回位弹簧是否能顺畅回位(0面) 100T以上的自动落下无问题否 150T以上自动取出无问题否 有无顶杆回位确认限位(防止滑块和顶杆相互干涉) 有无强制回位的装置(防止滑块和顶杆相互干涉) 顶出有无白化 是否多肉 有无拉着 (顶杆. 导柱) 顶杆眼加工间距是否良好(有无紧) 离型的行程有无问题 动作时使用油缸的时候.构造和轴承是否无问题 是否使用特殊构造(轴承.2段顶出.斜向凸轮) 固定板上是否安装了顶杆孔用的垫片 出荷前顶杆是否清扫好(润滑油.研磨膏) 是否确认了备品的种类荷数量
排气导套是否有台肩或横向顶丝固定侧是否有保护锁块pl面上有突形吊物是否平衡各顶板的螺丝孔处理基准面是否有标记螺丝有无弯曲和龟裂确认部品350t的时候要使其能采取一点吊爱丽思的特别式样吊的平衡是否好挂上钢丝绳时有无干涉物对突出物品的保护是否到位固定板和对各个板上的水嘴的保护热流道模具在换色时型板是否能分离确认为防止各型板丢失是否进行了丝锥处理支脚4的粗细平衡性螺丝是否够深根据模具的重量选择的型号是否合适是否安全周围有无干涉物装卸有无问题有有有ok是否有标牌模具尺寸
模具试前自检记录表

22 頂板導梢,襯套的碰傷,拉傷
23 頂針的碰傷,拉傷
24 回位梢的碰傷,拉摥
25 先行脫模梢的碰傷,拉傷
26 咬切(插破)部的咬傷,拉傷
27 模具尺寸 (外形,夾範本厚度,模具高度,定位環直徑等)ຫໍສະໝຸດ 28 模仁的硬度是否如指定?
確認結果
審核
設計擔當
對策
確認者
工程擔當 鉗工擔當
YX406-03-07
6 開閉器上有無作定位梢定位,位置關係
7 模具圖與入子尺寸有否差異
8 二段頂針,滑塊有否切削油溝
9 組合記號,防呆設置有否 (各入子,頂針等)
10 對模具部品有害的傷痕,生銹有無
11 危 頂險出的部尖上銳方角的有壓無克力板的設置(KEY CAP模具及特別指示的模 12 具)
13 品號,品名是否有刻印在模具天側及操作側的間隔板上
14 刻印內容是否與成品圖面吻合
15 三板模時剝料板的襯套防止脫落螺絲有無?
16 束子塊的合模確認 (平均合到嗎?)
17 咬切插破入子的合模確認 (平均合到嗎?)
18 放電痕跡,刀具痕跡是否殘留,鉗工修除有否?
19 逃氣道有無,深度﹑位置﹑數量適當嗎?
20 分模面是否有去角塌陷現象發生?
21 滑塊部的碰傷,拉傷有無
东莞永翔精密模具有限公司
模具试前自记录表
TRY试模 TOOL NO.模号
TRY试模 TOOL NO.模号
No
確認項目
1 入子的合模及組立上有無不良
2 回位梢長度的確認 (比成品分模面少0.1)
3 頂出部吊杆螺栓確認有無或則回位梢上有加工吊絲穴
4 各範本上的吊環螺絲牙穴有否﹑而且牙徑是否適當
5 頂出杆孔徑 (未滿300噸…φ35,300噸以上…φ40)
试模模具检查表

Yes No
供应商检查 对策 Action
星诺奇检查 Yes No
供应商备注:
供应商检 查人 :
检查人 :
项目确认:
生产部确认:
User
第 1 页
2013-8-26
第 2 页ቤተ መጻሕፍቲ ባይዱ
试模模具检查表
星诺奇检查 对策 Action
检查日期 :
检查日期 :
User
第 2 页
2013-8-26
第 1 页
试模模具检查表
试模模具检查表
产品名称PartName: 模具编号Mold No:
开发中模具修模检查: □ 生产中模具修模检查: □
产品编号Part No:
1 2 3 4 5 6 7 8 9 10 11 12 13 14 15
项目 checking items: 如是修模, 是否已完成并提交星诺奇修模报告. 模具带有与模具外形尺寸匹配的起吊块和吊环。 所有大移动部件都要有足够的油槽. 顶出系统运动足够的轻松。 模具打开和闭合过程轻松、安全、平稳。 水管接头是否已按星诺奇(HASCO)标准安装 是否已经测试过冷却系统的渗漏情况(15 bar压力下) 滑块部件可以在用人手操作的情况下运动自如平稳。 模具有足够的排气措施,包括流道系统。 所有模具型芯上都要刻有相应的模穴号及编号,此号码应 与模穴产品号相一致。 模具上所有的非机械式开关(电气、磁性限位)都经过功 能测试并确保能够正常使用。 液压缸头部与模具部件连接处完好,尺寸正确。 所有滑块的运动是否安全可靠(有限位装置及防止脱出装 置)。 热流道系统的电线应被覆盖在模具内部以确保生产情况下 不会被损害。 如有热流道的模具请把加热及感温阻值填写在下表中。 序号 1-2 3-4 5-6 7-8 加热阻值 感温阻值
模具试模前自检表

否 □
3.吊环孔是否够深.(不少于25mm)
够 □
不 够 □
前后模部份
1.偷料的地方是否做有R角.(R0.5以上)
是 □
否 □
2.水口、分流器的顶针是否平.
平 □
不 平 □
3.分型面经合模、锣入料后,表面是否有披锋.
有 □
没 有 □
4.是否做有排气糟.
有 □
没 有 □
5.水口的走水是否会顺畅、光洁度是否合适.
是 □
否 □
6.料位表面是否平滑.
是 □
否 □
7.一模多穴同样的产品是否有编号.
有 □
没 有 □
8.不可以打编号的产品是否在水口上打上编号.
是 □
否 □
9.攻牙孔的倒角位是否准确.
准确 □
不准确 □
10.攻牙孔的孔径、孔距的尺寸是否准确无误.
准确 □
不准确 □
行 位 部 位
1.行位起止位置是否正确可靠、装配合理、滑动顺畅.
是 □
否 □
2.行位润滑系统是否设立可靠.
是 □
否 □
冷 却 系 统
1.冷却(运水)是否畅通.
是 □
否 □
2.料咀冷却水是否堵好,并无漏水现象.
是 □
否 □
顶 出 系 统
1.顶针、司筒针的高度、方向、位置是否正确及无漏装.
正确 □
不正确 □
2.顶针、斜顶及推板装配是否正确、伸缩顺畅,复位正确可靠.
正确 □
些易遗忘和疏忽之处列于下表以备自检或互查。
型 号:
订 单 号:
开发日期:
项目
内容
检查结果
备注
资 料 复 核
模具试模点检表

工厂 14 28 14
试模实施、问题点提出
检查原料烘干 二次料 记录 添加比例
职
责
检查、跟踪、总结汇报
确认、工时、材料定额确认、问 题点总结 产品检测
确认、试模终止确认 模具调修
模实施、问题点提出
模实施、问题点提出
试模件数 ≈单模重量 准备重量
第四步骤、项目经理检查现场试模人员安排 部门 职 责 姓 名 1 项目经理 组织、检查、跟踪、总结汇报 2 3 技术支持、设备确认、工时、材料定额 生管本部 4 题点总结 5 6 质量技术 产品检测 7 8 技术中心 产品确认、试模终止确认 9 10 工模部 模具调修 11 1ቤተ መጻሕፍቲ ባይዱ 工厂 试模实施、问题点提出 13
试模人员安排及设备\模具点检表
项目名称 监察人姓名 第一步骤、模具点检 点检明细 吊环孔 1 码模槽 2 法兰 3 唧嘴是否防转 4 模具表面及拔模 5 模芯是否有标识 6 复位弹簧是否安装 7 顶出是否顺畅 8 复位是否到位 9 顶棍孔是否符合 10 11 顶针、斜顶、司筒 撑头与板配松 12 13 垃圾钉高度是否一致 14 撑头是否预压0.05 行位是否被限位 15 16 行程保护开关装配 第三步骤、设备点检 点检明细 油路 1 水路 2 电路 3 炮筒温度检查 4 料筒温度检查 5 机嘴检查 6 顶杆 7 检查液压锁模 8 温控箱检查 9 10 11 12 13 OK NO 15 16 17 18 19 20 21 22 23 24 25 26 27 点检明细 问题说明 点检明细 运水是否畅通 17 热流道状况 18 19 模具是否需特别工作原理说明 模具安装方向要求 20 21 22 23 24 25 26 27 28 29 30 31 32 设备备注说明: OK NO 问题说明 1 2 3 4 模具备注说明: 产品名称 调机人姓名 试模时间 试模地点 第二步骤、原料准备-生管本部 原料名称 姓 名 项目经理 试模机台
模具点检表

类别 序号
1 外观检 2
查
检查项目
清洁度
编
号
模具点检表
产品型号
模具名称
检查
静
动
*
*
零件名称 模具编号
检查要领
无切屑、尘砂、油污、杂 物
检查方法
目视 目视
验收
导向装
1
导柱(导套)对底座安装垂直 度
*
置
1
剪切面刃口粗糙度
*
冲裁部
分
2
刃口硬度
*
成型部
1
粗糙度:工作表面无划伤、裂 纹
*
分
2
工作面硬度
*
1
顶出器工作平稳
*
制件投入与 取出
2
制件投入,取出顺利。无干涉
*
1
模具上下模、联接板牢固
*
其它
2
模具各部分无锈蚀
*
<=0.020/100
直角尺
墙面、侧面ຫໍສະໝຸດ 粗糙度标块硬度计粗糙度标块
硬度计
目视 目视
目视 目视
模具试模前检查表(固态硅胶模具)

序号备注1234567891011121314151617181920日 期:日 期:日 期:模具试模前检查表按照修改模资料中的内容修改模具OK □ NG □OK □ NG □检查结果及处理意见:钳 工:品 质:品质课长:防呆、导向结构是否完善、合理OK □ NG □OK □ NG □是否有漏加工,漏组装部件OK □ NG □OK □ NG □所有通孔背面是否用无头螺丝堵好OK □ NG □OK □ NG □两板易开合无咬死,分型面无间隙OK □ NG □OK □ NG □弹性壁光滑无缺损OK □ NG □OK □ NG □撬模槽、基准角、治具定位销与设计图纸一致OK □ NG □OK □ NG □自拆线光滑平整,无碰伤、无锯齿等缺陷OK □ NG □OK □ NG □导电基无凸点,无刀痕OK □ NG □OK □ NG □刀锣面无明显刀痕,无毛刺,光洁平整OK □ NG □OK □ NG □三角尖刀自拆厚薄均匀,无缺损OK □ NG □OK □ NG □毛刺是否清理干净,是否有明显刀痕OK □ NG □OK □ NG □放电面火花纹一致,无积碳,无麻点不良OK □ NG □OK □ NG □模具是否喷砂,纹路是否均匀OK □ NG □OK □ NG □模具是否清洗干净,筋条、窄缝内是否有砂子OK □ NG □OK □ NG □背孔是否漏打、漏攻牙、位置是否居中OK □ NG □OK □ NG □模号、型号字码、穴号是否正确OK □ NG □OK □ NG □导柱导套深度是否合适OK □ NG □OK □ NG □合页把手螺丝是否锁好OK □ NG □OK □ NG □检 查 内 容钳工自检QC判 定导柱导套是否装对(上模导柱下模导套)OK □ NG □OK □ NG □产品名称穴 数 □修改模客户名称试模次数第 次 □其它(固态硅胶模具)表格编号:模具编号制模组别 □新 模。
模具验收标准检查表

有推板顶出的情况,顶杆是否为延迟顶出,防止顶白。 回程杆端面平整,无点焊,胚头底部无垫垫片、点焊。 斜顶在模架上的避空孔是否因太大影响外观。 固定在顶杆上的顶块是否可靠固定,四周非成型部分应加工 3-5 度的
39 斜度,下部周边倒角。 40 制品是否利于机械手取件。 三板模在机械手取料把时,限位拉杆是否布置在模具安装方向的两
外观
更多免费资料下载请进:
好好学习社区
德信诚培训网 各模板是否有零件编号, 编号在基准角符号正下方离底面 10mm 处, 要 12 求同 11 号。 模具配件是否影响模具的吊装和存放,如安装时下方有外漏的油缸、水 13 嘴、预复位机构等,应有支撑腿保护。 支撑腿的安装是否用螺丝穿过支撑腿固定在模架上, 或过长的支撑腿车 14 加工外螺纹紧固在模架上。 模具顶出孔是否符合指定的注塑机,除小型模具外, 原则上不能只用一 15 个中心顶出 (模具长度或宽度尺寸有一个大于 500mm 时) , 顶出孔直径 应比顶出杆大 5-10mm。 定位圈是否可靠固定(一般用三个 M6 或 M8 的内六角螺丝) ,直径一 16 般为¢100 或¢150mm,高出顶板 10mm。如合同有特殊要求,按全同。 17 定位圈安装孔必须为沉孔,不准直接贴在模架顶面上。 重量超过 8000KG 的模具安装在注塑机上时,是否用穿孔方式压螺丝, 18 不得单独压压板。如设备采用液压锁紧模具,也必须加上螺丝穿孔,以 防液压机构失效。 19 20 21 浇口套球 R 是否大于注塑机喷嘴球 R。 浇口套入口直径是否大于喷嘴注射口直径。 模具外形尺寸是否符合指定的注塑机。 安装有方向要求的模具是否在前模板或后模上用箭头标明安装方向, 22 箭头旁应有“UP”字样,箭头和文字均用漏板喷黄色漆,字高 50mm。 模具 模架表面是否有凹坑、锈迹,多余不用的吊环、进出水、气、油孔等 外观 23 及其他影响外观的缺陷。 24 模架各板是否都有大于 1.5mm 的倒角。
模具试模前检查表(塑胶模具)

序号备注1234567891011121314151617181920日 期:日 期:日 期:模具试模前检查表进胶口按图纸开通OK □ NG □OK □ NG □检查结果及处理意见:钳 工:品 质:品质课长:模具运水/油路/气路刻印相关字码,如“IN” “OUT” OK □ NG □OK □ NG □试模前按图面装上限位开关OK □ NG □OK □ NG □滑动部位加润滑油OK □ NG □OK □ NG □按照修改模资料中的内容修改模具OK □ NG □OK □ NG □模仁排气按设计要求加工OK □ NG □OK □ NG □试模前装上锁模片OK □ NG □OK □ NG □后模顶棍孔直径符合图纸OK □ NG □OK □ NG □导套底部开排气OK □ NG □OK □ NG □模仁镶件/镶针/日期章等零件无漏装OK □ NG □OK □ NG □胶塞孔内光滑,口部做R过渡OK □ NG □OK □ NG □模仁省模省到位OK □ NG □OK □ NG □模仁按客户要求蚀纹/蚀字OK □ NG □OK □ NG □流道光滑OK □ NG □OK □ NG □唧嘴球R符合图纸要求OK □ NG □OK □ NG □顶针/斜顶动作顺畅OK □ NG □OK □ NG □行位动作顺畅OK □ NG □OK □ NG □通过20PSI 水压测试不漏水(时限3分钟)OK □ NG □OK □ NG □三板模水口板滑动顺利,水口板易拉开OK □ NG □OK □ NG □检 查 内 容钳工自检QC判 定fit模红丹fit到位OK □ NG □OK □ NG □产品名称穴 数 □修改模客户名称试模次数第 次 □其它(塑胶模具)表格编号:模具编号制模组别 □新 模。
模具动静态检查表--

目视
2 导柱与导套配合间隙 向 3 导板面配合间隙 装 4 滑动导板接触面接合率
▲ 无单边接触,无损伤 大型<0.1,中型<0.08,反侧导板≤
▲
0.01 ▲ ≥85%,分布均匀
5 斜楔机构运动导滑面
▲ 间隙<0.03mm
置
6
各种斜楔机构运动灵活,扒钩间隙合 理
扒钩间隙侧冲0.5~1mm, ▲ 吊冲<0.03mm
目视 目视 目视
5 起吊孔的螺纹规格 检 6 压板槽位置、尺寸及数量
● 按用户和图纸要求 ▲ 按图纸尺寸
目视 直尺
查 7 模具定位键或定位孔 8 空气管接头座及电气安装位置
▲ 按图纸尺寸 ▲ 按图纸尺寸,不能超出模体
直尺 目视
9 闭合高度检查
▲ 按图纸尺寸
卷尺
导 1 导向面粗糙度
●
工作面和导入圆角粗糙度0.8,支承面 粗糙度1.6
︶ 部
11
10°~30°斜面冲裁时,冲孔及修边凸 模处理
工作刃口提前切入深度按2个料厚处 ▲ 理,冲头是否防转
直尺 目视
分 12 刃口切入量
▲ 按图纸规定
直尺
13
退料板与凸模,压料板与凹模的导正 间隙
▲ 间隙0.3~0.5mm
成 1 镶块接缝间隙 形 ︵ 2 工作面粗糙度
拉 延 3 工作表面无缺陷 、
● ≤0.01mm
成 7 凸凹模镶块材料牌号及件号标记
● 打印清晰,无凸起
形 8 上模销孔加丝堵
● 是否防止上模销子松动脱落
、 9 拉延模到底标记
整 形
10
卸料板型面与工件接触面
高于型面 ▲ 0.3mm,工件表 ▲ 是否产生压痕
模具检查表(中文版)

3 二次辟空,让位加工是否已完成. 4 斜切刃是否合适. 5 镶件淬火后,是否有开裂现象. 6 硬度是否合格. 7 防止定位销脱落措施是否良好. 8 材质刻印是否清晰. 9 镶件之间的间歇,与挡块之间的间歇是否合适. 10 刀口处是否有破损. 11 堆焊处是否有裂纹. 1 动作是否良好. 斜 2 是否是适时加工. 切 3 切入量是否合适. 4 是否有强制复位装置. 1 废料的排出是否通畅. 2 废料滑槽的形状是否合理. 废 3 废料滑槽是否可收藏在模局内. 4 滑槽与铸件,镶件之间是否有间隙. 5 是否有防止费料飞散措施. 6 废料的落下部位是否有滑槽承接. 料 7 滑槽安装是否合理,有无松动. 8 废料落下部位是否有突起的障碍物. 9 冲孔的落料闭空是否合适. 1 导料架与产品形状是否吻合. 2 导料架是否有调整量 3 导料架的焊接是否良好.(CS焊接NG 样 件 投 装 , 定 位 4 导料架是否用螺钉紧固,补强. 5 是否有防投料错误装置. 6 可动导料架的动作是否良好. 7 接近开关动作是否良好. 8 可动导料架的防松动措施是否良好. 9 产品在浮顶器上是否有晃动现象. 10 浮顶器的行程设定,动作是否良好.
1 样件在上,下模上是否有粘贴抱紧现象.
上升过程中,样件安定性是否良好. 样 2 件 3 防误装置动作是否良好. 的 取 4 产品滑槽的宽度,长度,角度是否合格. 出 5 样件在取出时是否有变形.
5 指形传送棒与模具是否有干涉. 自 动 传 送 装 置 6 防误夹的感应装置的效果是否良好. 7 空站的位置,高度,方向是否良好. 8 空站上样件的安定性是否良好. 9 指形传送棒承接面的形状是否合理. 10 送料杆的内宽是否合适.
成 4 下模面的面接触吻合性是否良好. 5 拉延筋及R角部分的精加工是否良好. 形 6 行程限位块的接触面积是否均匀. 7 形状面及R部份的研磨是否良好. 面 8 形状面及R部份是否有凹陷. 9 堆焊部位是否有咬边,气孔,裂纹. 10 是否有排气孔. 11 压料板的行程限位柱的接触面积是否均匀. 1 动作是否良好. 压 料 板 , 顶 杆 2 样件研配,模具研配是否良好. 3 压料板与切刀,曲刀的间歇是否合理. 4 侧面安全挡销,吊装螺栓的接触面是否均匀. 5 弹簧,聚氨脂橡胶的支撑是否良好, 6 压料板滑动时是否有晃动现象. 1 导滑面的接触是否良好. 导 向 2 是否有滑动拉伤. 3 导柱,导套的防松脱落装置是否良好. 4 加工开始前,导柱或导滑板是否已进入导滑面.
模具试模前自检表

确认人: 制表: 审核:
日期:
年ቤተ መጻሕፍቲ ባይዱ
月 月
日 日
制表时间: 年 记录编号:
模具试模前自检表
模具编号: 序号 1 2 3 4 5 6 7 8 9 检验内容 水咀是否按图接上,是否有进出水标识,进水IN,出水 OUT,后加顺序号(例如:IN1,OUT1) 进出油咀, 汽咀是否与冷却水区分,并在IN,OUT字 前加上符号[例如(G )汽 ,O(油)] 模板和零件配件是否编号。 外形寸尺是否符合指定的注塑机、顶出孔是否相符。 定位圈是否牢固。(沉进面板表面5~8mm) 模具表面是否有锈迹,凹坑,刀疤等和其它外观不良。 顶针板是否有垃圾钉。 顶针、顶块与滑块干涉是否有预回装置,行程开关。 是否撑头,是否有顶出限位。 模具名称:
判定 是(Y) 否(N)
记录编号:GC-DR-18-A/0 备 注
10 前模板与水口板之间是否有弹弓,辅助开模。 11 顶出是否顺畅、卡滞、异响。 12 滑动部件(顶针除外)是否开油模,是否导滑块。 13 顶杆要求定位的是否定位。 14 回针顶面与PL面是否同时到红丹,且顶针板是否到底。 15 是否进行通水试验,压力4个pa,通水5分钟。 16 流道是否抛光滑。 17 分型面是否有排气槽. 18 模具型腔尺寸是否与图纸相符。 19 前模是否抛光到位。 20 前后模筋位、柱是否无火花纹、刀疤、 倒扣。 21 前后模成型部位是否有倒扣。 22 一模多穴,是否有穴号。 23 型腔和后模是否打上防锈油。 24 锁模块是否安装 25 吊模块是否安装牢固 检验结论: □可试 □不可试 □修正
模具检查表[空白模板]
![模具检查表[空白模板]](https://img.taocdn.com/s3/m/9a62393ab9f3f90f77c61b54.png)
Part Name.产品名称Ass/装配Pos.O.K N.O.K NA Remark/备注1##########2##########3##########4##########5##########6##########7所有顶针是否地有空隙可活动(0.02mm)##########8##########9##########10##########11##########12##########13##########14##########15##########16###17###18###19###20###21222324v2526272829303132333435日期章能否可以转动3637383940414243表单编号:记录保管期限:5年所有工件是否洗干净.前后模固定板是否有码模槽。
计数器是否有安装隧道铲基是否按要求配模与点检前,后模,整体拍照,检查照片是否清析XX-XXX-XX 版本:V02热咀是否会碰穿流道板。
所有运动部件是否有油槽和上油。
所有模仁工件是否有退磁。
整套模具各散件,对应位置字码是否清析明了。
排气引出槽是否有引出符合标准。
水口勾针有没装对,高度是否正确,无后退,在对应位置是否可转动。
检查PL 面。
行位与行位45度角,与前后模封胶位的FIT 模效果验证。
斜顶的高度检查,是否平胶位面。
(顶针要高出胶面0.04mm)检查斜导柱长度,行位不装弹簧是否能退到位。
顶针强行复装置是否配合到位,开合模是否正常。
进胶孔是否有倒扣,积炭,与流道板贴合位是否有错位,反倒扣。
所有铲基,反铲。
耐磨块贴合面是否做R角,油槽是否标准。
环形镶件与前模仁配合位数据是否核对(配合公差在0.00mm到-0.01mm)环形镶件与模仁外形夹口位数据是否核对清(保证夹口公差在0.01mm之内)环形镶件冬菇头精定位与模仁定位槽位置数据核对过。
回针顶面与回针支撑柱是否贴。
垃圾钉与顶针板是否贴合动模组立后必须把所有斜顶打红丹验证封胶位是否到位。
试模前检查表

模具名称 制模组别
胶口、流道、水路、排气、拉料针是否符合工艺要求 客户特殊要求部分: 晒纹 镜面 模具缺陷及加工异常请说明: EDM纹
注:未经检查的模具不能出厂试模,审核人需签字。 检查: 审核: 日期:
打√,不合格项
客
户
试模日期
打×;非检查项在 留空)
产品能否脱模,外观是否有处理 模具螺丝是否锁紧,无漏装 绞牙产品是否可以转动 排气槽大小是否加工合理 导柱是否加工排气 油缸油芯是否顺畅 模具安全保障结构是否有做 模穴号、产品号是否有打 各模胆没用的边角是否倒角 型腔油污是否擦干净喷防锈油 外观外型整洁,无敲打痕迹 模具运水是否通畅,无漏水现象
模具验收检查表
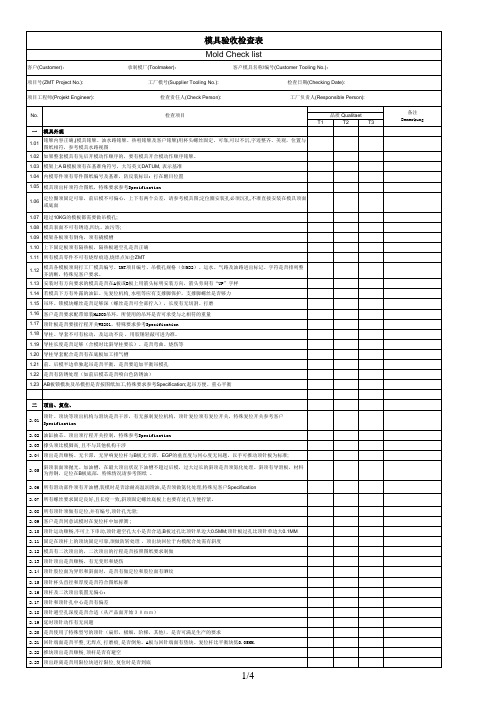
2.06 所有滑动部件须有开油槽,装模时是否涂耐高温润滑油,是否须做氮化处理,特殊见客户Specification 2.07 所有螺丝要求固定良好,且长度一致,斜顶固定螺丝底板上也要有过孔方便拧紧。 2.08 所有顶针须做有定位,并有编号,顶针孔光滑; 2.09 客户是否同意试模时在复位杆中加弹簧 ; 2.10 顶针运动顺畅,不可上下串动,顶针避空孔大小是否合适,B板过孔比顶针单边大0.5MM;顶针板过孔比顶针单边大0.1MM 2.11 固定在顶杆上的顶块固定可靠,须做防转处理 ,顶出块回位于内模配合处需有斜度 2.12 模具有二次顶出的,二次顶出的行程是否按照图纸要求制做 2.13 顶针顶出是否顺畅,有无变形和烧伤 2.14 顶针胶位面为异形和斜面时,是否有做定位和胶位面有晒纹 2.15 顶针杯头直径和厚度是否符合图纸标准 2.16 顶杆及二次顶出装置无偏心; 2.17 顶针和顶针孔中心是否有偏差 2.18 顶针避空孔深度是否合适(从产品面开始30mm) 2.19 延时顶针动作有无问题 2.20 是否使用了特殊型号的顶针(扁形,极细,阶梯,其他),是否可满足生产的要求 2.21 回针端面是否平整,无焊点,打磨痕,是否倒角。A板与回针端面有垫块。复位杆比平衡块低0.05MM. 2.22 推块顶出是否顺畅,顶杆是否有避空 2.23 顶出距离是否用限位块进行限位,复位时是否到底
1.07 超过10KG的模板都需要做吊模孔; 1.08 模具表面不可有锈迹,凹坑、油污等; 1.09 模架各板须有倒角,须有撬模槽 1.10 上下固定板须有隔热板,隔热板避空孔是否正确 1.11 所有模具零件不可有烧焊痕迹,烧焊点知会ZMT 1.12 模具各模板须刻打工厂模具编号、ZMT项目编号、吊模孔规格(如M32)、运水、气路及油路进出标记、字符是否排列整 齐清晰,特殊见客户要求。
模具检查表

静 态 部 份
1、没有此项检查的打/ 2、合格的打O 3、局部合格的打△ 4、不合格的打× / O 第一次检查的填写在1次格内、第二次检查的填写在2次格内,以此内推
自由状态下弹簧不受力 自由状态下手推能略动、用验模剂 、活动块手推能略动、 斜锲 手感、验模剂 检测活动块和驱动器接确面大于80% 驱动器与活动块接确面 大于80% 螺栓孔台阶平底、孔内 每三个螺栓抽检一个螺栓孔内有无 无灰尘、螺栓松紧过程 灰尘铁销、螺栓松紧过程自如,每 自如,定位销松紧合适 螺栓、定位销 目视、手感 三个定位销抽检一个定位销孔有无 、捶击渐进、拔出不毛 灰尘铁削、定位销松紧是否合适、 、上模销孔要有堵头螺 拔出有无拉毛 母 排气有效、上模排气孔 目测拉伸模有无排气孔、排气是否 排气孔 目测 要有防尘措施 通畅、上模排气孔有无防尘装置 模具内大部件起 超过15KG的镶件应有起 目测超过15公斤的镶块有无起吊孔 目测 重 吊孔 配备的顶杆长度及直径 用直尺测量顶杆长度是否与机床匹 符合机床参数、顶杆孔 配、顶杆孔是否与压板槽及上模柄 顶杆及顶杆孔 直尺 的位置与模具的位置度 位置公差超过1MM ±1MM、符合机床参数 压板槽 上下模压板槽位置度± 2MM、位置、宽度及长 度符合机床参数 直尺 用直尺测量压板槽宽度是否符合图 纸要求、与机床是否匹配
仪征赛克工装 装备有限公司
零件号\零件名称 模具检查人 模具制作人 检查项目
模具外观 铭牌 硬度 型面粗糙度 冲裁刀口
模具制作检查表
项目名称 产品名称 工序号\工序名称 检查日期 检查地点
技术要求
检查手段
检查方法
检查非刀口部份是否倒角,模具表 面有无锈迹、无敲击的伤痕,油漆 是否按规定标色涂刷均匀 是否按规定安装在规定的位置 是否符合图纸规定范围 手感平滑、目视有打磨纹理凸模略 留加工痕迹 手感锋利、目视刀口无白线反光、 选择适合的面作基准面测量垂直度 用间隙尺测量镶块与镶块与背托之 间的间隙、用验模剂检查镶块底部 平整度、目视镶块有无按规定标识
- 1、下载文档前请自行甄别文档内容的完整性,平台不提供额外的编辑、内容补充、找答案等附加服务。
- 2、"仅部分预览"的文档,不可在线预览部分如存在完整性等问题,可反馈申请退款(可完整预览的文档不适用该条件!)。
- 3、如文档侵犯您的权益,请联系客服反馈,我们会尽快为您处理(人工客服工作时间:9:00-18:30)。
序号备注
123456789
1011121314151617181920模具编号制模组别 □新 模产品名称穴 数 □修改模客户名称试模次数
第 次 □其它检 查 内 容
钳工自检
QC判 定
导柱导套是否装对(上模导柱下模导套)OK □ NG □OK □ NG □导柱导套深度是否合适OK □ NG □OK □ NG □合页把手螺丝是否锁好
OK □ NG □OK □ NG □背孔是否漏打、漏攻牙、位置是否居中OK □ NG □OK □ NG □模号、型号字码、穴号是否正确OK □ NG □OK □ NG □模具是否喷砂,纹路是否均匀
OK □ NG □OK □ NG □模具是否清洗干净,筋条、窄缝内是否有砂子OK □ NG □OK □ NG □毛刺是否清理干净,是否有明显刀痕OK □ NG □OK □ NG □放电面火花纹一致,无积碳,无麻点不良
OK □ NG □OK □ NG □刀锣面无明显刀痕,无毛刺,光洁平整OK □ NG □OK □ NG □三角尖刀自拆厚薄均匀,无缺损OK □ NG □OK □ NG □自拆线光滑平整,无碰伤、无锯齿等缺陷OK □ NG □OK □ NG □导电基无凸点,无刀痕OK □ NG □OK □ NG □弹性壁光滑无缺损
OK □ NG □OK □ NG □撬模槽、基准角、治具定位销与设计图纸一致OK □ NG □OK □ NG □所有通孔背面是否用无头螺丝堵好OK □ NG □OK □ NG □两板易开合无咬死,分型面无间隙OK □ NG □OK □ NG □品质课长:防呆、导向结构是否完善、合理OK □ NG □OK □ NG □是否有漏加工,漏组装部件OK □ NG □OK □ NG □日 期:
日 期:
日 期:
固态硅胶模具试模前检查表
按照修改模资料中的内容修改模具OK □ NG □
OK □ NG □
检查结果及处理意见:
钳 工:品 质:。