试模模具检查表
模具检查表(新型)(XLS)

模具检查表(新型)
最终检查日: 检查员: 模具番号: 模具品名: 厂家验收 顾客验收 设计担当
分 类
嵌和有无问题 有无防转销 是否打字码 (考虑保养) 是否有火(HRC58~60确认品质)
检 查 项 目 (径 杆 顶管冷却有无问题 顶管高度有无问题 时间差顶杆动作有无问题 (动作量) 孔内径是否用铰刀加工 是否使用了特殊型号(扁形 极细 阶梯 其他) 有无干涉 (径. 间距) 回 导柱是否使用沾火料 程 杆 回程杆的碰面是否良好 回程杆的头部是否倒角 推板上是否有冷却 厚度是否够. 是否会弯 推 分型面是否设计缓冲块或勒聚胺脂块 板 回位弹簧和导柱的位置设计有无问题(因弯曲而动作不良) 在表面按回位弹簧时要在背面把螺丝 角落的镶块要注意斜度的设定和推杆孔的间隙 顶 环式镶块要却认是否有冷却 出 环式镶块的有配管型. 动作时要确认是否有干涉 镶 块 环式镶块顶出时是否会因重量发生平衡不良(支点确认) 动作部位是否使用了无油导套和轴承 顶板和芯子和顶杆导柱位置有无错位 设定的行程能否顺畅动作 是否使用了中荷重的弹簧 早回位弹簧是否能顺畅回位(0面) 100T以上的自动落下无问题否 150T以上自动取出无问题否 有无顶杆回位确认限位(防止滑块和顶杆相互干涉) 有无强制回位的装置(防止滑块和顶杆相互干涉) 顶出有无白化 是否多肉 有无拉着 (顶杆. 导柱) 顶杆眼加工间距是否良好(有无紧) 离型的行程有无问题 动作时使用油缸的时候.构造和轴承是否无问题 是否使用特殊构造(轴承.2段顶出.斜向凸轮) 固定板上是否安装了顶杆孔用的垫片 出荷前顶杆是否清扫好(润滑油.研磨膏) 是否确认了备品的种类荷数量
排气导套是否有台肩或横向顶丝固定侧是否有保护锁块pl面上有突形吊物是否平衡各顶板的螺丝孔处理基准面是否有标记螺丝有无弯曲和龟裂确认部品350t的时候要使其能采取一点吊爱丽思的特别式样吊的平衡是否好挂上钢丝绳时有无干涉物对突出物品的保护是否到位固定板和对各个板上的水嘴的保护热流道模具在换色时型板是否能分离确认为防止各型板丢失是否进行了丝锥处理支脚4的粗细平衡性螺丝是否够深根据模具的重量选择的型号是否合适是否安全周围有无干涉物装卸有无问题有有有ok是否有标牌模具尺寸
模具试模前自检表

否 □
3.吊环孔是否够深.(不少于25mm)
够 □
不 够 □
前后模部份
1.偷料的地方是否做有R角.(R0.5以上)
是 □
否 □
2.水口、分流器的顶针是否平.
平 □
不 平 □
3.分型面经合模、锣入料后,表面是否有披锋.
有 □
没 有 □
4.是否做有排气糟.
有 □
没 有 □
5.水口的走水是否会顺畅、光洁度是否合适.
是 □
否 □
6.料位表面是否平滑.
是 □
否 □
7.一模多穴同样的产品是否有编号.
有 □
没 有 □
8.不可以打编号的产品是否在水口上打上编号.
是 □
否 □
9.攻牙孔的倒角位是否准确.
准确 □
不准确 □
10.攻牙孔的孔径、孔距的尺寸是否准确无误.
准确 □
不准确 □
行 位 部 位
1.行位起止位置是否正确可靠、装配合理、滑动顺畅.
是 □
否 □
2.行位润滑系统是否设立可靠.
是 □
否 □
冷 却 系 统
1.冷却(运水)是否畅通.
是 □
否 □
2.料咀冷却水是否堵好,并无漏水现象.
是 □
否 □
顶 出 系 统
1.顶针、司筒针的高度、方向、位置是否正确及无漏装.
正确 □
不正确 □
2.顶针、斜顶及推板装配是否正确、伸缩顺畅,复位正确可靠.
正确 □
些易遗忘和疏忽之处列于下表以备自检或互查。
型 号:
订 单 号:
开发日期:
项目
内容
检查结果
备注
资 料 复 核
模具试模点检表

工厂 14 28 14
试模实施、问题点提出
检查原料烘干 二次料 记录 添加比例
职
责
检查、跟踪、总结汇报
确认、工时、材料定额确认、问 题点总结 产品检测
确认、试模终止确认 模具调修
模实施、问题点提出
模实施、问题点提出
试模件数 ≈单模重量 准备重量
第四步骤、项目经理检查现场试模人员安排 部门 职 责 姓 名 1 项目经理 组织、检查、跟踪、总结汇报 2 3 技术支持、设备确认、工时、材料定额 生管本部 4 题点总结 5 6 质量技术 产品检测 7 8 技术中心 产品确认、试模终止确认 9 10 工模部 模具调修 11 1ቤተ መጻሕፍቲ ባይዱ 工厂 试模实施、问题点提出 13
试模人员安排及设备\模具点检表
项目名称 监察人姓名 第一步骤、模具点检 点检明细 吊环孔 1 码模槽 2 法兰 3 唧嘴是否防转 4 模具表面及拔模 5 模芯是否有标识 6 复位弹簧是否安装 7 顶出是否顺畅 8 复位是否到位 9 顶棍孔是否符合 10 11 顶针、斜顶、司筒 撑头与板配松 12 13 垃圾钉高度是否一致 14 撑头是否预压0.05 行位是否被限位 15 16 行程保护开关装配 第三步骤、设备点检 点检明细 油路 1 水路 2 电路 3 炮筒温度检查 4 料筒温度检查 5 机嘴检查 6 顶杆 7 检查液压锁模 8 温控箱检查 9 10 11 12 13 OK NO 15 16 17 18 19 20 21 22 23 24 25 26 27 点检明细 问题说明 点检明细 运水是否畅通 17 热流道状况 18 19 模具是否需特别工作原理说明 模具安装方向要求 20 21 22 23 24 25 26 27 28 29 30 31 32 设备备注说明: OK NO 问题说明 1 2 3 4 模具备注说明: 产品名称 调机人姓名 试模时间 试模地点 第二步骤、原料准备-生管本部 原料名称 姓 名 项目经理 试模机台
模具试模前检查表(固态硅胶模具)

序号备注1234567891011121314151617181920日 期:日 期:日 期:模具试模前检查表按照修改模资料中的内容修改模具OK □ NG □OK □ NG □检查结果及处理意见:钳 工:品 质:品质课长:防呆、导向结构是否完善、合理OK □ NG □OK □ NG □是否有漏加工,漏组装部件OK □ NG □OK □ NG □所有通孔背面是否用无头螺丝堵好OK □ NG □OK □ NG □两板易开合无咬死,分型面无间隙OK □ NG □OK □ NG □弹性壁光滑无缺损OK □ NG □OK □ NG □撬模槽、基准角、治具定位销与设计图纸一致OK □ NG □OK □ NG □自拆线光滑平整,无碰伤、无锯齿等缺陷OK □ NG □OK □ NG □导电基无凸点,无刀痕OK □ NG □OK □ NG □刀锣面无明显刀痕,无毛刺,光洁平整OK □ NG □OK □ NG □三角尖刀自拆厚薄均匀,无缺损OK □ NG □OK □ NG □毛刺是否清理干净,是否有明显刀痕OK □ NG □OK □ NG □放电面火花纹一致,无积碳,无麻点不良OK □ NG □OK □ NG □模具是否喷砂,纹路是否均匀OK □ NG □OK □ NG □模具是否清洗干净,筋条、窄缝内是否有砂子OK □ NG □OK □ NG □背孔是否漏打、漏攻牙、位置是否居中OK □ NG □OK □ NG □模号、型号字码、穴号是否正确OK □ NG □OK □ NG □导柱导套深度是否合适OK □ NG □OK □ NG □合页把手螺丝是否锁好OK □ NG □OK □ NG □检 查 内 容钳工自检QC判 定导柱导套是否装对(上模导柱下模导套)OK □ NG □OK □ NG □产品名称穴 数 □修改模客户名称试模次数第 次 □其它(固态硅胶模具)表格编号:模具编号制模组别 □新 模。
注塑模试模前全检表

注塑模试模前全检表
检查日期:
25□OK □NG 26□OK □NG 27□OK □NG 28□OK □NG 29
□OK □NG
接收□ 特采□ 拒收□
注意事项: 1.做好的请在检查状况一栏打“√”,未做好的打“×”。
合模时,回位杆是否可以印到红丹 2.有缺陷的合模,请于备注栏注明原因并请相关主管签字。
3.此表格由各组负责人亲自检查填写(注:负责人不在时,可由其助手填写)。
4.此表格填写完后连同试模单送注塑部,最后由工程存档。
模具主管确认: 模具品管: 模具全检人:
最终判定:
循环水是否按图加工到位模具表面是否有名牌?模具顶板上是否装有垃圾钉?
模具是否有定位圈?。
模具验收标准检查表

有推板顶出的情况,顶杆是否为延迟顶出,防止顶白。 回程杆端面平整,无点焊,胚头底部无垫垫片、点焊。 斜顶在模架上的避空孔是否因太大影响外观。 固定在顶杆上的顶块是否可靠固定,四周非成型部分应加工 3-5 度的
39 斜度,下部周边倒角。 40 制品是否利于机械手取件。 三板模在机械手取料把时,限位拉杆是否布置在模具安装方向的两
外观
更多免费资料下载请进:
好好学习社区
德信诚培训网 各模板是否有零件编号, 编号在基准角符号正下方离底面 10mm 处, 要 12 求同 11 号。 模具配件是否影响模具的吊装和存放,如安装时下方有外漏的油缸、水 13 嘴、预复位机构等,应有支撑腿保护。 支撑腿的安装是否用螺丝穿过支撑腿固定在模架上, 或过长的支撑腿车 14 加工外螺纹紧固在模架上。 模具顶出孔是否符合指定的注塑机,除小型模具外, 原则上不能只用一 15 个中心顶出 (模具长度或宽度尺寸有一个大于 500mm 时) , 顶出孔直径 应比顶出杆大 5-10mm。 定位圈是否可靠固定(一般用三个 M6 或 M8 的内六角螺丝) ,直径一 16 般为¢100 或¢150mm,高出顶板 10mm。如合同有特殊要求,按全同。 17 定位圈安装孔必须为沉孔,不准直接贴在模架顶面上。 重量超过 8000KG 的模具安装在注塑机上时,是否用穿孔方式压螺丝, 18 不得单独压压板。如设备采用液压锁紧模具,也必须加上螺丝穿孔,以 防液压机构失效。 19 20 21 浇口套球 R 是否大于注塑机喷嘴球 R。 浇口套入口直径是否大于喷嘴注射口直径。 模具外形尺寸是否符合指定的注塑机。 安装有方向要求的模具是否在前模板或后模上用箭头标明安装方向, 22 箭头旁应有“UP”字样,箭头和文字均用漏板喷黄色漆,字高 50mm。 模具 模架表面是否有凹坑、锈迹,多余不用的吊环、进出水、气、油孔等 外观 23 及其他影响外观的缺陷。 24 模架各板是否都有大于 1.5mm 的倒角。
模具自检表格

8.不可以打编号的产品是否在水口上打上编号.
行 位 部 位
冷 却 系 统
顶出 系 统
制模 员:
10.攻牙孔的倒角位是否准确. 11.攻牙孔的孔径、孔距的尺寸是否准确无误. 1.行位起止位置是否正确可靠、装配合理、滑动顺畅.
2.行位润滑系统是否设立可靠.
1.冷却(运水)是否畅通.
2.料咀冷却水是否堵好,并无漏水现象.
有□ 没有 □
是□
否□
有□ 没有 □ 准确 □ 不准确 □ 准确 □ 不准确 □
是□
否□
是□
否□
是□
否□
是□
否□
正确 □ 不正确 □
正确 □ 不正确 □
审核:
注:试模前务必认真检查以上的重点,检查完将此表填好,交由文员存档.
目的:
模具自检表
鉴于模具制造周期较长,遗忘之事时有发生;模具试模前亦经常由于一些小疏忽 而导致重上压铸机、试模多次,浪费资源,为避免此类事情的发生,特针对一 些易遗忘和疏忽之处列于下表以备自检或互查。
型 号:
订 单 号:
开发日期:
项目
内容
资 1.模具与图纸尺寸是否合格(计缩水). 料
复 2.有公差的地方是否都准确无误. 核
1.顶针、司筒针的高度、方向、位置是否正确及无漏装.
2.顶针、斜顶及推板装配是否正确、伸缩顺畅,复位正确可 靠.
检查日
试模日
期:
期:
检查结果
备注
合格 □ 不合格 □
准确 □ 不准确 □
准确 □ 不准确 □
是□
否□
够□ 不够 □
有 □ 没有 □
平□ 不平 □
有□ 没有 □
有□ 没有 □
模具设计自检表
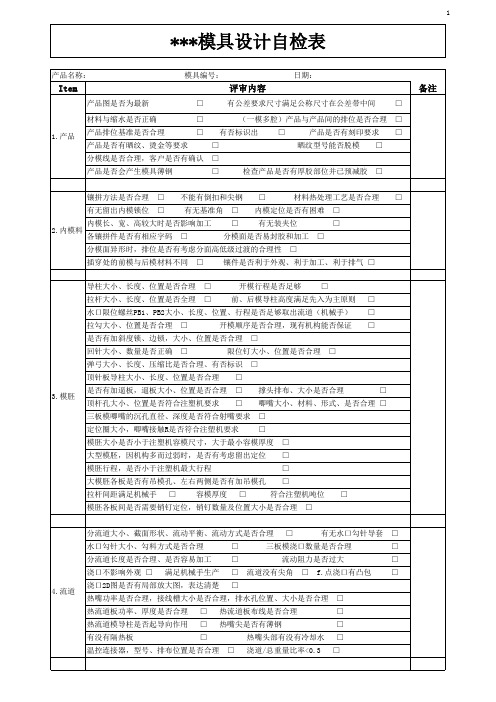
分模线是否合理,客户是否有确认 □
产品是否会产生模具薄钢
□
检查产品是否有厚胶部位并已预减胶 □
备注
镶拼方法是否合理 □ 不能有倒扣和尖钢 □
材料热处理工艺是否合理 □
有无留出内模锁位 □ 有无基准角 □ 内模定位是否有困难 □
内模长、宽、高较大时是否影响加工 □ 有无装夹位
□
2.内模料
各镶拼件是否有相应字码 □
行位限位方式是否合理 □
行位是否需要耐磨板
□
行位弹簧大小、长度、压缩比是否正确 □ 行位是否有加冷却水
□
行位尺寸较大时,是否有导滑槽
□ 是否需要作镶拼件,是否容易加工 □
行位动力机构为油缸时,油缸的缸径、行程、固定方式是否合理 □
行位出模导致产品变形时,是否有行位顶出机构 □
行位是否影响合模 □
行位是否需要延时机构 □
前模抽芯机构之型芯是否影响流道取出 □
抽芯机构复位动作是否合理
□
6.镶件 镶件定位方式是否合理 □
有无可换镶件
□
大镶件有无运水
□
镶件是否易装、拆模
□
顶针、直顶、斜顶出胶位时,是否会夹住产品 □ 顶针类避免与前模面直接碰撞 □
顶针大小、位置、长度是否合理
□
7.顶出 机构
有托顶针、扁顶针、托位避空是否足够,托位是否标准
□
有没有隔热板
□
热嘴头部有没有冷却水 □
温控连接器,型号、排布位置是否合理 □ 浇道/总重量比率<0.3 □
2
1.产品 5.机构
产品图是否为最新
□
有公差要求尺寸满足公称尺寸在公差带中间 □
行位型芯过长时,有否留出定位,防止型芯变形 □ 滑块导向长度大于全长2/3 □
塑胶模具试模查验表样板

20.型腔结构是否与塑胶图一致---------------------□□
21.模仁是否加工完全-----------------------------□□
22.模仁间是否没有缝隙---------------------------□□
23.模具机构运动(合模)是否正常-----------------□□
24.模具上红丹及渣质是否清洗---------------------□□
25.模板污锈是否清洗-----------------------------□□
组长
组立
注:1.以上查检项目由组立人员逐项检查并签名,再由组立组长复检、签名。
4.料道大小是否均匀;合理且光滑-------------------□□
5.停止销是否装置磨平----------------------------□□
6.模具组装时模仁是否做累积公差检测------------□□
7.公母模仁靠破.插破尺寸是否合理----------------□□
8.定位柱,定位块是否有效且正常----------------□□9.特殊配件是否装置------------------------------□□
塑胶模具试模前查检表
组别:_______日期:___Hale Waihona Puke 年___月___日模座编号
塑胶料号
合模料号
查检项目是否
备注
1.定位环是否钻孔攻丝----------------------------□□
2.弹簧长度.压缩回弹是否正常---------------------□□
3.咀嘴是否装置并磨平;并有料沟-------------------□□
模具试模前检查表(塑胶模具)

序号备注1234567891011121314151617181920日 期:日 期:日 期:模具试模前检查表进胶口按图纸开通OK □ NG □OK □ NG □检查结果及处理意见:钳 工:品 质:品质课长:模具运水/油路/气路刻印相关字码,如“IN” “OUT” OK □ NG □OK □ NG □试模前按图面装上限位开关OK □ NG □OK □ NG □滑动部位加润滑油OK □ NG □OK □ NG □按照修改模资料中的内容修改模具OK □ NG □OK □ NG □模仁排气按设计要求加工OK □ NG □OK □ NG □试模前装上锁模片OK □ NG □OK □ NG □后模顶棍孔直径符合图纸OK □ NG □OK □ NG □导套底部开排气OK □ NG □OK □ NG □模仁镶件/镶针/日期章等零件无漏装OK □ NG □OK □ NG □胶塞孔内光滑,口部做R过渡OK □ NG □OK □ NG □模仁省模省到位OK □ NG □OK □ NG □模仁按客户要求蚀纹/蚀字OK □ NG □OK □ NG □流道光滑OK □ NG □OK □ NG □唧嘴球R符合图纸要求OK □ NG □OK □ NG □顶针/斜顶动作顺畅OK □ NG □OK □ NG □行位动作顺畅OK □ NG □OK □ NG □通过20PSI 水压测试不漏水(时限3分钟)OK □ NG □OK □ NG □三板模水口板滑动顺利,水口板易拉开OK □ NG □OK □ NG □检 查 内 容钳工自检QC判 定fit模红丹fit到位OK □ NG □OK □ NG □产品名称穴 数 □修改模客户名称试模次数第 次 □其它(塑胶模具)表格编号:模具编号制模组别 □新 模。
模具检查表

项目名称.产品名称.OK N/A NG 导柱长于斜导柱吗?斜 滑块下有顶针是否加安OK N/A NG A .计量设定为产品20%-OK N/A NG C.射嘴空射压力bar 经过热流道bar 经过主流道bar 经过进胶口bar 3>>流道及流料井是否合理?10>>热流道温度是否有波动? 验证顶针感应开关感应距离是否在0.3-0.5mm? 热流道感应温度是否正常,热流道铭牌标示是否正确? 型腔内部是否有损伤及锈迹,斑点?1>>短射是否平衡?(热流道温度需设定一致)。
检查导柱.斜导柱.斜导柱孔是否有烧伤?4.正常运行后参数的调整3. 模具设定 检查顶出是否平衡.有无杂音及斜顶能否正常顶出?7>>流道是否弹飞?模具检查表A.确认所选的注塑机锁模力是否足够用于试模。
OK NG B.注塑机螺杆直径选择;实际用料量是注塑机螺杆直径的1到3倍。
OK NG 1.机台选择A>>检查模具各组水流量及水流压力是否符合标准。
(水流量为水管直径的0.472以上) 为预防开模时滑块掉落,天侧滑块是否加保护装置? 顶针是否能顶到底?是否有限位装置?A.调整合模低压保护力及保护时间。
B.模具温度正常后测量模具各区域之间的实际温度,偏差是否ok?6>>模具表面是否有料屑?(生产一段时间后再观察一次)2.上机后模具检查B>>模温正常后检查模具型腔有无漏水(如有热流道须在模温正常升温5分钟后才可开启热流道电源).C>>导柱.斜导柱.精定位.耐磨板加黄油润滑. 滑块是否有定位?限位螺丝位置是否合理?D>>模具正常开模后检查以下项目(试动作时首次选用低压安装模式进行) 检查抽芯动作有无异常,抽芯限位开关是否能正常使用? 开合模导柱是否有碰撞声音,开合模阻力是否偏大?检查压力损失,并做各点的压力记录(射胶速度选用机器中速)9>>射速选用高速后的零件是否存在重大缺陷?4>>浇口大小是否合理和一致,有无圆角?5>>流道及零件能否正常脱落?(在不影响模具安全的情况下尽量选用一次顶出)8>>型芯温度是否过高?(注塑过程中测量)B .注塑填充后模具有无风险(如粘模,顶出困难;变形,卡扣筋位断),如一切正常确认一下项目:2>>型腔填充末端及流道是否有排气? NG描述NG描述日期章能否正常转动,版本号是否做镶针? NG描述mm/sbar SI.在保压确定的情况下降低锁模力tonton ℃#N/A℃冷却时间:S 实际周期时间:S 是否用机械手:Remark:短射平衡重量标准小于等于1g ,相差小于10%。
注塑模具试模验收点检表A0
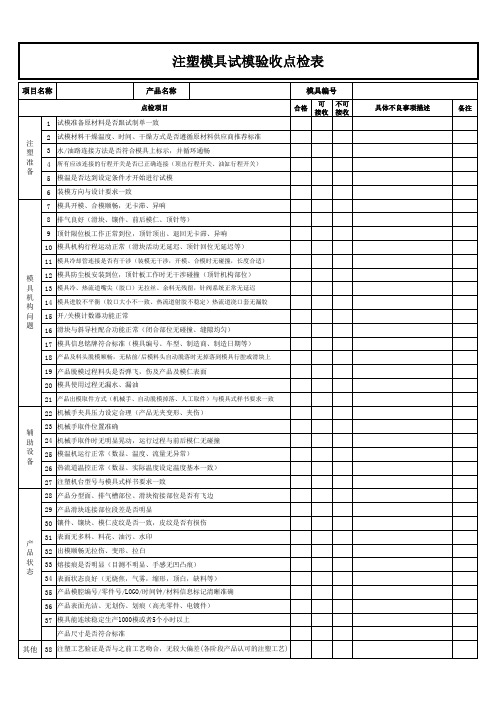
合格
可 接收
不可 接收
其他 38 注塑工艺验证是否与之前工艺吻合,无较大偏差(各阶段产品认可的注塑工艺)
具体不良事项描述
备注
注塑模具试模验收点检表
项目名称
产品名称
点检项目
1 试模准备原材料是否跟试制单一致
2 试模材料干燥温度、时间、干燥方式是否遵循原材料供应商推荐标准 注 塑 3 水/油路连接方法是否符合模具上标示,并循环通畅 准 4 所有应该连接的行程开关是否已正确连接(顶出行程开关、油缸行程开关) 备
5 模温是否达到设定条件才开始进行试模
设 25 模温机运行正常(数显、温度、流量无异常) 备
26 热流道温控正常(数显、实际温度设定温度基本一致)
27 注塑机台型号与模具式样书要求一致
28 产品分型面、排气槽部位、滑块衔接部位是否有飞边
29 产品滑块连接部位段差是否明显
30 镶件、镶块、模仁皮纹是否一致,皮纹是否有损伤
31 表面无多料、料花、油污、水印 产 品 32 出模顺畅无拉伤、变形、拉白
状 33 熔接痕是否明显(目测不明显、手感无凹凸痕) 态
34 表面状态良好(无烧焦,气雾,缩形,顶白,缺料等)
35 产品模腔编号/零件号/LOGO/时间钟/材料信息标记清晰准确
36 产品表面光洁、无划伤、划痕(高光零件、电镀件)
37 模具能连续稳定生产1000模或者5个小时以上
产品尺寸是否符合标准
模具编号
具 13 模具冷、热流道嘴尖(胶口)无拉丝、余料无残留,针阀系统大小不一致、热流道射胶不稳定)热流道浇口套无漏胶
问 15 开/关模计数器功能正常
题 16 滑块与斜导柱配合功能正常(闭合部位无碰撞、缝隙均匀)
17 模具信息铭牌符合标准(模具编号、车型、制造商、制造日期等)
模具检查表(中文版)

3 二次辟空,让位加工是否已完成. 4 斜切刃是否合适. 5 镶件淬火后,是否有开裂现象. 6 硬度是否合格. 7 防止定位销脱落措施是否良好. 8 材质刻印是否清晰. 9 镶件之间的间歇,与挡块之间的间歇是否合适. 10 刀口处是否有破损. 11 堆焊处是否有裂纹. 1 动作是否良好. 斜 2 是否是适时加工. 切 3 切入量是否合适. 4 是否有强制复位装置. 1 废料的排出是否通畅. 2 废料滑槽的形状是否合理. 废 3 废料滑槽是否可收藏在模局内. 4 滑槽与铸件,镶件之间是否有间隙. 5 是否有防止费料飞散措施. 6 废料的落下部位是否有滑槽承接. 料 7 滑槽安装是否合理,有无松动. 8 废料落下部位是否有突起的障碍物. 9 冲孔的落料闭空是否合适. 1 导料架与产品形状是否吻合. 2 导料架是否有调整量 3 导料架的焊接是否良好.(CS焊接NG 样 件 投 装 , 定 位 4 导料架是否用螺钉紧固,补强. 5 是否有防投料错误装置. 6 可动导料架的动作是否良好. 7 接近开关动作是否良好. 8 可动导料架的防松动措施是否良好. 9 产品在浮顶器上是否有晃动现象. 10 浮顶器的行程设定,动作是否良好.
1 样件在上,下模上是否有粘贴抱紧现象.
上升过程中,样件安定性是否良好. 样 2 件 3 防误装置动作是否良好. 的 取 4 产品滑槽的宽度,长度,角度是否合格. 出 5 样件在取出时是否有变形.
5 指形传送棒与模具是否有干涉. 自 动 传 送 装 置 6 防误夹的感应装置的效果是否良好. 7 空站的位置,高度,方向是否良好. 8 空站上样件的安定性是否良好. 9 指形传送棒承接面的形状是否合理. 10 送料杆的内宽是否合适.
成 4 下模面的面接触吻合性是否良好. 5 拉延筋及R角部分的精加工是否良好. 形 6 行程限位块的接触面积是否均匀. 7 形状面及R部份的研磨是否良好. 面 8 形状面及R部份是否有凹陷. 9 堆焊部位是否有咬边,气孔,裂纹. 10 是否有排气孔. 11 压料板的行程限位柱的接触面积是否均匀. 1 动作是否良好. 压 料 板 , 顶 杆 2 样件研配,模具研配是否良好. 3 压料板与切刀,曲刀的间歇是否合理. 4 侧面安全挡销,吊装螺栓的接触面是否均匀. 5 弹簧,聚氨脂橡胶的支撑是否良好, 6 压料板滑动时是否有晃动现象. 1 导滑面的接触是否良好. 导 向 2 是否有滑动拉伤. 3 导柱,导套的防松脱落装置是否良好. 4 加工开始前,导柱或导滑板是否已进入导滑面.
注塑模具试模前检查表

模号:
模具试模前检查表
品名:
客户:
检查日期: 年 月 日 试模日期:
点
检
项
目
点检结果
备注
1.模具顶出机构及回位是否顺畅
YES
NO
2.模具定位环尺寸是否与圖面相符合
YES
NO
3.进料点是否有拋光,避免脫模拉料屑
YES
NO
4.耐磨片及斜頂作动部位是否有油槽
NO
11.平衡块预压量是否依标准研配源自位YESNO12.水路是否畅通,水流量是否正常
YES
NO
13.模具水路是否有测漏水
YES
NO
14.滑块的限位装置功能是否良好,無掉落等問題
YES
NO
15.滑块下方若有顶针,是否有安装微动开关or強制回位
YES
NO
16.滑块行程定位是否正确,斜导柱长度是否与滑块导柱孔对上 YES
YES
NO
29.修模,设变是否已修改完成,并逐项核对检查
YES
NO
质检
部长
YES
NO
课长/组长
钳工担当
23.KO孔位置是否正确,是否可配合试模厂机台规格
YES
NO
24.氮氣缸孔,頂棍孔尺寸避空是否依標準單邊2.0-2.5mm
YES
NO
25.公母模及滑块合模是否有确实,不出毛邊
YES
NO
26.模具是否刻上UP↑标記或強制回位
YES
NO
27.模具P/L安全锁模块是否安装
YES
NO
28.模具碰穿面,插穿面口部毛刺是否去除,成品不致拉傷
模具--模具检查表

模具檢查表
模具名稱
檢查項目內容
判定(打)
合格
不合格
無此項目
模具外觀
1
模具尺寸(L______ x W_______ x H________)
2
定模固定板與動模固定板尺寸是否符合圖面﹖
3
吊環位置是否適當,平衡度是否良好﹖
4
冷卻水路:制作、規格是否符合圖面﹖
接頭處螺牙規格是否符合圖面﹖
2.檢查員必須確實檢查與記錄,如有不確實檢查,經查覺後一律嚴處。
3.不合格者,制模人員重新整理,檢查員重新檢查,並記錄事實。
檢查記錄
核准:
審核:
檢查員:
制模員確認:
WR-09-11-A0
定模部份
動模部份
順暢﹖
14
滑塊
油溝是否制作﹖動作是否順暢﹖
是否熱處理﹖
定位鋼珠效果是否確實﹖
與頂出梢是否有衝突﹖
滑塊動作是否順暢
15
成品取出性是否良好﹖
16
模穴號是否有標示﹖
判定
□合格□不合格
備註說明
1.凡屬於未確認(正式生產)的新模具無論首次試模,或試模後的修改,一律要重新檢查並填此表單。
5
模具上是否標示清楚冷卻回路出入記號﹖
6
油壓缸滑塊是否裝置正常﹖動作順暢﹖
7
微動開關設置:滑塊是否安裝微動開關﹖
頂出板是否安裝微動開關﹖
8
彈簧種類、動作、尺寸是否符合圖面或規格﹖
9
模具編號、名稱是否已標示﹖是否正確﹖
模具內部及動作
10
水路是否貫通流行性良好(空氣測試)﹖
定模部份
動模部份
11
是否漏水、漏油﹖
模具试模前自检表

确认人: 制表: 审核:
日期:
年ቤተ መጻሕፍቲ ባይዱ
月 月
日 日
制表时间: 年 记录编号:
模具试模前自检表
模具编号: 序号 1 2 3 4 5 6 7 8 9 检验内容 水咀是否按图接上,是否有进出水标识,进水IN,出水 OUT,后加顺序号(例如:IN1,OUT1) 进出油咀, 汽咀是否与冷却水区分,并在IN,OUT字 前加上符号[例如(G )汽 ,O(油)] 模板和零件配件是否编号。 外形寸尺是否符合指定的注塑机、顶出孔是否相符。 定位圈是否牢固。(沉进面板表面5~8mm) 模具表面是否有锈迹,凹坑,刀疤等和其它外观不良。 顶针板是否有垃圾钉。 顶针、顶块与滑块干涉是否有预回装置,行程开关。 是否撑头,是否有顶出限位。 模具名称:
判定 是(Y) 否(N)
记录编号:GC-DR-18-A/0 备 注
10 前模板与水口板之间是否有弹弓,辅助开模。 11 顶出是否顺畅、卡滞、异响。 12 滑动部件(顶针除外)是否开油模,是否导滑块。 13 顶杆要求定位的是否定位。 14 回针顶面与PL面是否同时到红丹,且顶针板是否到底。 15 是否进行通水试验,压力4个pa,通水5分钟。 16 流道是否抛光滑。 17 分型面是否有排气槽. 18 模具型腔尺寸是否与图纸相符。 19 前模是否抛光到位。 20 前后模筋位、柱是否无火花纹、刀疤、 倒扣。 21 前后模成型部位是否有倒扣。 22 一模多穴,是否有穴号。 23 型腔和后模是否打上防锈油。 24 锁模块是否安装 25 吊模块是否安装牢固 检验结论: □可试 □不可试 □修正
模具检查表[空白模板]
![模具检查表[空白模板]](https://img.taocdn.com/s3/m/9a62393ab9f3f90f77c61b54.png)
Part Name.产品名称Ass/装配Pos.O.K N.O.K NA Remark/备注1##########2##########3##########4##########5##########6##########7所有顶针是否地有空隙可活动(0.02mm)##########8##########9##########10##########11##########12##########13##########14##########15##########16###17###18###19###20###21222324v2526272829303132333435日期章能否可以转动3637383940414243表单编号:记录保管期限:5年所有工件是否洗干净.前后模固定板是否有码模槽。
计数器是否有安装隧道铲基是否按要求配模与点检前,后模,整体拍照,检查照片是否清析XX-XXX-XX 版本:V02热咀是否会碰穿流道板。
所有运动部件是否有油槽和上油。
所有模仁工件是否有退磁。
整套模具各散件,对应位置字码是否清析明了。
排气引出槽是否有引出符合标准。
水口勾针有没装对,高度是否正确,无后退,在对应位置是否可转动。
检查PL 面。
行位与行位45度角,与前后模封胶位的FIT 模效果验证。
斜顶的高度检查,是否平胶位面。
(顶针要高出胶面0.04mm)检查斜导柱长度,行位不装弹簧是否能退到位。
顶针强行复装置是否配合到位,开合模是否正常。
进胶孔是否有倒扣,积炭,与流道板贴合位是否有错位,反倒扣。
所有铲基,反铲。
耐磨块贴合面是否做R角,油槽是否标准。
环形镶件与前模仁配合位数据是否核对(配合公差在0.00mm到-0.01mm)环形镶件与模仁外形夹口位数据是否核对清(保证夹口公差在0.01mm之内)环形镶件冬菇头精定位与模仁定位槽位置数据核对过。
回针顶面与回针支撑柱是否贴。
垃圾钉与顶针板是否贴合动模组立后必须把所有斜顶打红丹验证封胶位是否到位。
试模前检查表

模具名称 制模组别
胶口、流道、水路、排气、拉料针是否符合工艺要求 客户特殊要求部分: 晒纹 镜面 模具缺陷及加工异常请说明: EDM纹
注:未经检查的模具不能出厂试模,审核人需签字。 检查: 审核: 日期:
打√,不合格项
客
户
试模日期
打×;非检查项在 留空)
产品能否脱模,外观是否有处理 模具螺丝是否锁紧,无漏装 绞牙产品是否可以转动 排气槽大小是否加工合理 导柱是否加工排气 油缸油芯是否顺畅 模具安全保障结构是否有做 模穴号、产品号是否有打 各模胆没用的边角是否倒角 型腔油污是否擦干净喷防锈油 外观外型整洁,无敲打痕迹 模具运水是否通畅,无漏水现象
- 1、下载文档前请自行甄别文档内容的完整性,平台不提供额外的编辑、内容补充、找答案等附加服务。
- 2、"仅部分预览"的文档,不可在线预览部分如存在完整性等问题,可反馈申请退款(可完整预览的文档不适用该条件!)。
- 3、如文档侵犯您的权益,请联系客服反馈,我们会尽快为您处理(人工客服工作时间:9:00-18:30)。
Yes No
供应商检查 对策 Action
星诺奇检查 Yes No
供应商备注:
供应商检 查人 :
检查人 :
项目确认:
生产部确认:
User
第 1 页
2013-8-26
第 2 页ቤተ መጻሕፍቲ ባይዱ
试模模具检查表
星诺奇检查 对策 Action
检查日期 :
检查日期 :
User
第 2 页
2013-8-26
第 1 页
试模模具检查表
试模模具检查表
产品名称PartName: 模具编号Mold No:
开发中模具修模检查: □ 生产中模具修模检查: □
产品编号Part No:
1 2 3 4 5 6 7 8 9 10 11 12 13 14 15
项目 checking items: 如是修模, 是否已完成并提交星诺奇修模报告. 模具带有与模具外形尺寸匹配的起吊块和吊环。 所有大移动部件都要有足够的油槽. 顶出系统运动足够的轻松。 模具打开和闭合过程轻松、安全、平稳。 水管接头是否已按星诺奇(HASCO)标准安装 是否已经测试过冷却系统的渗漏情况(15 bar压力下) 滑块部件可以在用人手操作的情况下运动自如平稳。 模具有足够的排气措施,包括流道系统。 所有模具型芯上都要刻有相应的模穴号及编号,此号码应 与模穴产品号相一致。 模具上所有的非机械式开关(电气、磁性限位)都经过功 能测试并确保能够正常使用。 液压缸头部与模具部件连接处完好,尺寸正确。 所有滑块的运动是否安全可靠(有限位装置及防止脱出装 置)。 热流道系统的电线应被覆盖在模具内部以确保生产情况下 不会被损害。 如有热流道的模具请把加热及感温阻值填写在下表中。 序号 1-2 3-4 5-6 7-8 加热阻值 感温阻值