合成氨原料气醇烃化净化精制新工艺技术
合成氨几种原料气的净化工艺浅析

合成氨几种原料气的净化工艺浅析摘要简述了铜洗、联醇、双甲、醇烃化等几种原料气净化的方法及其特点。
关键词合成氨原料气净化合成氨原料气的净化是生产中至关重要的工序,原料气微量(C0+C02)超高将导致氨合成催化剂中毒而无法运行,目前我国以煤为原料固定层气化的大多数中小氮肥厂采用铜洗法脱除微量(C0+C02)。
传统的铜洗法是一种较为落后的净化工艺,存在着设备多、工艺复杂、操作麻烦而物耗高,又是生产中的主要环境污染源等缺点。
随着耐硫低温变换催化剂的开发和精脱硫技术的发展,近期中小氮肥厂在原料气净化中相继出现各级压力的联产甲醇、甲烷化、双甲和醇烃化工艺替代铜洗净化,这些原料气净化工艺正逐渐完善和成熟,比传统铜洗法具有明显优势。
1 铜洗净化工艺的不足传统的铜洗净化工艺已在中小氮肥厂应用了几十年,现仍然继续在大多数厂中运行。
尽管铜洗净化在各厂运行效果不一,但普遍存在着许多不足。
1.1铜洗是合成氨生产事故的易发工序由于铜洗工艺流程长,设备多,铜液组分受各种因素的影响,各厂铜洗生产都出现过大小不同的事故。
许多厂都出现过微量(CO+CO2) 超高、铜塔带液、设备填料堵塞、铜液成分波动、铜比难调等问题,是事故易发工序。
1.2 铜洗法净化物耗高铜洗在气体净化过程中,铜液要补充氨、铜和酸,铜液在低温下吸收脱除微量而在高温下解吸再生,既消牦热量又消耗冷量(蒸汽和电),铜液在净化过程吸收了(CO+CO2),同时亦溶解了H2有效气体,即使设置了再生回收,仍然存在着气体的损失。
铜洗运行成本各厂水平不一物耗有所差异,但一般不低于50元/tNH3,甚至高达100元/tNH3以上。
1.3 铜洗是生产现场环境较差,污染多的工序铜洗现场的跑冒滴漏是管理难点。
铜液渗漏和再生气排放污染水体和大气,不利企业环保工作的提高。
2 联产甲醇减轻了铜洗净化的生产负荷目前已有相当多的中小氮肥厂于铜洗前增加了联产甲醇工艺,联醇生产不仅增加了企业化工产品,更为重要的是减轻了铜洗净化的负荷,变换和脱碳的生产亦相对变得宽松,其综合效益是明显的。
合成氨工业污染防治技术政策

附件2合成氨工业污染防治技术政策一、总则(一)为贯彻《中华人民共和国环境保护法》等法律法规,防治环境污染,保障生态安全和人体健康,规范污染治理和管理行为,引领合成氨工业生产工艺和污染防治技术进步,促进绿色循环低碳发展,制定本技术政策。
(二)本技术政策所称的合成氨工业是指以煤、天然气、油等为原料生产合成氨和以合成氨为原料生产尿素、硝酸铵、碳酸氢铵以及醇氨联产的生产过程。
(三)本技术政策为指导性文件,提出了合成氨工业污染防治可采取的技术路线和技术方法,包括清洁生产、水污染防治、大气污染防治、固体废物处置和综合利用、鼓励研发的新技术等内容,为合成氨工业环境保护相关规划、污染物排放标准、环境影响评价、总量控制、排污许可等环境管理和企业污染防治工作提供技术指导。
(四)合成氨工业应加大产业结构调整力度,提高产业集中度,因地制宜,按生态环境功能区要求合理布局,加快淘汰技术水平较低的落后产能。
(五)合成氨工业应遵循全过程污染防治的原则,实行清洁生产、末端治理、风险防范的综合防治技术路线。
(六)合成氨生产企业应加强污染物排放全面监控,全面掌握常规及特征污染物排放的特点和规律,健全环境风险防控体系和环境应急管理制度,研发和应用达到更低排放水平的污染防治技术。
二、清洁生产(七)新建以煤为原料的合成氨生产项目应采用水煤浆、干煤粉等加压连续气化工艺;现有采用固定层间歇式煤气化工艺的合成氨生产企业扩建时,应采用加压连续气化工艺。
(八)以天然气为原料的合成氨生产企业应淘汰天然气常压间歇催化转化制气生产工艺。
(九)以无烟块煤为原料采用固定层间歇式煤气化工艺的合成氨生产企业应采用碱液法半水煤气脱硫工艺技术,并配套硫磺回收装置,淘汰氨水液相半水煤气脱硫工艺。
(十)合成氨生产企业应采用一氧化碳低温、宽温耐硫变换及适宜于一氧化碳含量较高情况的等温变换工艺,淘汰一氧化碳常压变换及全中温变换(高温变换)工艺。
(十一)合成氨生产企业应根据生产工艺特点和实际条件选择低温甲醇洗、变压吸附法(PSA法)、聚乙二醇二甲醚法(NHD法)、甲基二乙醇胺法(MDEA法)、碳酸丙烯酯法(PC法)等原料气脱碳技术。
合成氨生产技术(第二版)第六章精炼
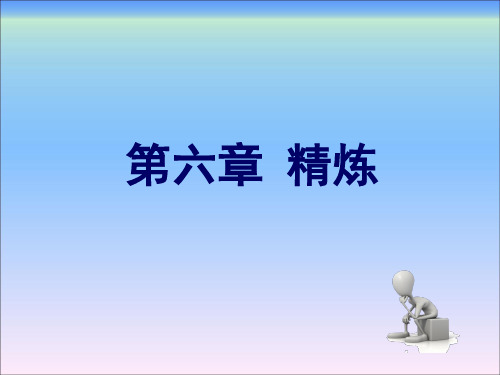
四、铜液的再生
2.再生的操作条件 (1)再生压力 (2)再生温度
四、铜液的再生
(3)再生时间
四、铜液的再生
3.还原操作条件
四、铜液的再生
影响高价铜还原的因素如下 (1)还原温度 (2)高价铜和液相中的C O含量
五、工艺流程
1.再生过程氨的回收 2.再生气的处理 3.能量的回收 4.铜液的清理
五、工艺流程
五、工艺流程
第二节 甲醇化和甲烷化精制工艺及操 作
1 任务 2 生产原理及工艺流程 3 铜洗岗位操作要点
一、任务
甲醇化和甲烷化工段的主要任务有两个:一是净化合成 氨原料气;二是合成甲醇。
二、工艺流程
1.生产原理 (1)甲醇化反应
二、工艺流程
(2)醇烃化反应
二、1图6-7由压缩机五段出口来的气体经油水分离 器,分离器中的油水,由顶部出来再进入铜洗塔底部和 顶部喷淋的铜液在填料上逆流接触,被铜液吸收其中的 有害成分后,经铜液分离器分离铜液雾沫后返回压缩机 六段进口。
三、正常生产操作要点
1.保证铜液质量 2.保证铜洗气净化质量 3.严防铜洗塔带液和回流塔冒液 4.巡回检查
二、工艺流程
(1)甲醇化子系统 (2)醇烃化子系统
三、正常生产操作要点
1.双甲工段开停车 2.系统开车 (1)吹除、排尽 (2)试漏置换 (3)升压置换 (4)系统开车
三、正常生产操作要点
3.系统停车 4.临时停车 5.循环机的开车、停车 (1)双甲循环机的开停车 (2)开车 (3)停车 (4)倒车
四、开停车操作要点
1.正常开车 (1)开车前的准备 (2)开车前的置换 (3)开车 2.停车 (1)短期停车 (2)紧急停车 (3)长期停车
合成氨工艺

合成氨工艺————————————————————————————————作者:————————————————————————————————日期:合成氨工艺流程(1)原料气制备将煤和天然气等原料制成含氢和氮的粗原料气。
对于固体原料煤和焦炭,通常采用气化的方法制取合成气;渣油可采用非催化部分氧化的方法获得合成气;对气态烃类和石脑油,工业中利用二段蒸汽转化法制取合成气。
(2)净化对粗原料气进行净化处理,除去氢气和氮气以外的杂质,主要包括变换过程、脱硫脱碳过程以及气体精制过程。
①一氧化碳变换过程在合成氨生产中,各种方法制取的原料气都含有CO,其体积分数一般为12%~40%。
合成氨需要的两种组分是H2和N2,因此需要除去合成气中的CO。
变换反应如下:CO+H2OH→2+CO2 =-41.2kJ/mol 0298HΔ由于CO变换过程是强放热过程,必须分段进行以利于回收反应热,并控制变换段出口残余CO含量。
第一步是高温变换,使大部分CO转变为CO2和H2;第二步是低温变换,将CO含量降至0.3%左右。
因此,CO变换反应既是原料气制造的继续,又是净化的过程,为后续脱碳过程创造条件。
②脱硫脱碳过程各种原料制取的粗原料气,都含有一些硫和碳的氧化物,为了防止合成氨生产过程催化剂的中毒,必须在氨合成工序前加以脱除,以天然气为原料的蒸汽转化法,第一道工序是脱硫,用以保护转化催化剂,以重油和煤为原料的部分氧化法,根据一氧化碳变换是否采用耐硫的催化剂而确定脱硫的位置。
工业脱硫方法种类很多,通常是采用物理或化学吸收的方法,常用的有低温甲醇洗法(Rectisol)、聚乙二醇二甲醚法(Selexol)等。
粗原料气经CO变换以后,变换气中除H2外,还有CO2、CO和CH4等组分,其中以CO2含量最多。
CO2既是氨合成催化剂的毒物,又是制造尿素、碳酸氢铵等氮肥的重要原料。
因此变换气中CO2的脱除必须兼顾这两方面的要求。
一般采用溶液吸收法脱除CO2。
合成氨原料气醇烃化净化精制新工艺技术

合成氨原料气醇烃化净化精制新工艺技术合成氨是一种重要的化学原料,在农业、化肥生产以及其他领域有广泛的应用。
合成氨的生产过程中,醇烃化是一个关键的步骤,它将醇类原料氧化成氨气。
然而,该过程中也存在着一些问题,如氨气纯度不高、能耗大和废水处理困难等。
为了解决这些问题,研究人员提出了一种新的工艺技术,通过气醇烃化净化和精制的方法来改进合成氨的生产过程。
新工艺技术的主要步骤包括以下几个方面:首先,选择高纯度的醇类原料作为氨气的来源。
一般来说,乙醇和丙醇是合成氨生产中常用的原料,它们具有较高的氨气产率。
在这一步中,可以采用蒸馏等方法从原料中提取纯度较高的醇类化合物。
其次,将醇类化合物经过催化氧化反应得到氨气。
这个步骤的关键在于选择适当的催化剂和反应条件,以提高氨气的产率和纯度。
同时,还需控制反应中的温度、压力和氧化剂的使用量,以减少能耗和废水产生。
接下来,对产生的氨气进行净化处理。
在这一步中,可以采用吸附剂、膜分离或冷凝等方法去除气相中的杂质,如水、氧气和碳氧化物等。
通过这些净化手段,可以提高氨气的纯度,并减少对后续工艺步骤的影响。
最后,对净化后的氨气进行精制处理。
在这一步中,可以利用洗涤和吸附等方法去除氨气中的杂质,如硫化氢和二氧化碳等。
通过精制处理,可以进一步提高合成氨的纯度,并保证其达到工业生产的要求。
总的来说,合成氨原料气醇烃化净化精制新工艺技术为合成氨的生产过程提供了一种可行的改进方法。
该工艺技术通过选择高纯度的醇类化合物原料、优化催化氧化反应条件以及采用净化和精制手段,可以提高氨气的产率、纯度和质量,降低能耗并减少废水处理难题,从而实现合成氨生产过程的可持续发展。
合成氨是一种广泛用于农业、化肥生产和其他领域的化学原料。
目前,最常用的方法是通过醇烃化将醇类原料氧化成氨气。
然而,传统的合成氨工艺存在一些问题,如氨气纯度低、废水处理难题以及能耗较高。
为了解决这些问题,研究人员提出了一种新的合成氨原料气醇烃化净化精制工艺技术。
合成氨原料气的精制陈诚
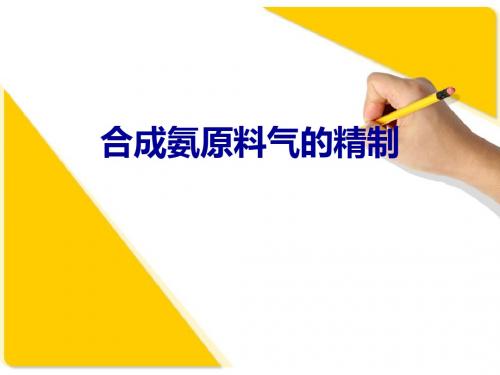
常规甲烷化工艺具有如下特点: 原料气中CO+CO2含量较低,一般不超过0.7%;
反应放热量少,热点温度不超过350℃ ;
反应空速为3000-6000h-1; 反应器为单绝热床; 催化剂为镍系,采用浸渍法或共沉淀法制备; 产品气中CO+CO2含量<2ppm。
二.催化剂主要活性组分
二.工艺流程
变换气经压缩机压缩,用水(或热钾碱溶液等)除去其中大部分CO2 后,再由压缩机加压到12~13MPa送至铜氨液洗涤系统。 气体自铜 氨液洗涤塔(简称铜洗塔)的底部进入,自下而上与塔顶喷淋下来的 铜氨液逆流接触,气体中CO、CO2、H2O和O2等即为铜氨液吸收。 如果洗涤后气体中CO+CO2〈10ml/m3,即可加压后送往氨合成系 统。倘若出铜洗塔气体中的CO2含量较高时,还要经过碱洗塔用氨水 或碱液吸收CO2后,才能达到净化要求。 吸收气体中CO等杂质后 的铜氨液,自铜液塔底部经减压至0.15MPa自动流到铜氨液再生系统 的回流塔3的顶部,与再生器4逸出的气体相遇,捕集其中氨及部分 CO2后,由回流塔底部流至还原器7中。还原器的上下两段均上设有 蒸汽加热管,底部有空气加入管 ,中部有旁通管线(即副线)。铜 氨液首先经过下加热器6加热,随即向上流,经还原器内几层有孔折 板后进入上加热器5。在必要时,可开用旁通管,使部分铜氨液不经 下加热器而直接进入上加热器。铜氨液经还原
金属的甲烷化活性顺序: Ru>Ir>Rh>Ni>Co>Os>Pt>Fe>Mo>Pd>Ag
从原料来源、成本和活性进行综合分析,认为Ni是最适 宜的甲烷化催化剂;
优点 缺点
镍系催化剂
钴系催化剂 钼系催化剂 铁系催化剂
活性高、选择性好
合成氨“双甲”工艺在原料气净化中的优势分析
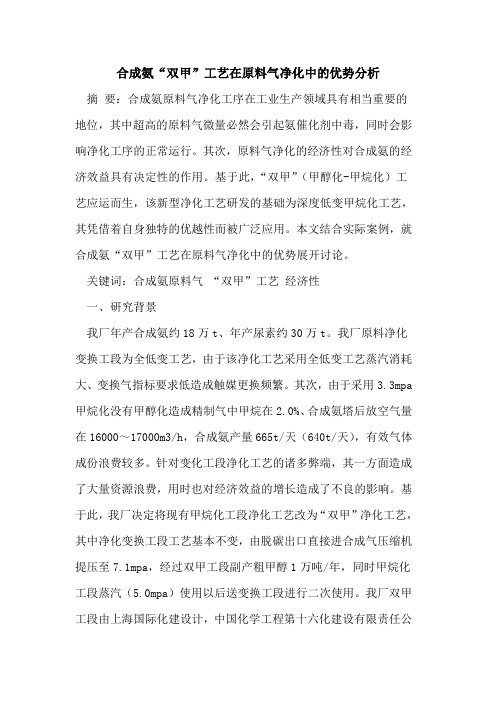
合成氨“双甲”工艺在原料气净化中的优势分析摘要:合成氨原料气净化工序在工业生产领域具有相当重要的地位,其中超高的原料气微量必然会引起氨催化剂中毒,同时会影响净化工序的正常运行。
其次,原料气净化的经济性对合成氨的经济效益具有决定性的作用。
基于此,“双甲”(甲醇化-甲烷化)工艺应运而生,该新型净化工艺研发的基础为深度低变甲烷化工艺,其凭借着自身独特的优越性而被广泛应用。
本文结合实际案例,就合成氨“双甲”工艺在原料气净化中的优势展开讨论。
关键词:合成氨原料气“双甲”工艺经济性一、研究背景我厂年产合成氨约18万t、年产尿素约30万t。
我厂原料净化变换工段为全低变工艺,由于该净化工艺采用全低变工艺蒸汽消耗大、变换气指标要求低造成触媒更换频繁。
其次,由于采用3.3mpa 甲烷化没有甲醇化造成精制气中甲烷在2.0%、合成氨塔后放空气量在16000~17000m3/h,合成氨产量665t/天(640t/天),有效气体成份浪费较多。
针对变化工段净化工艺的诸多弊端,其一方面造成了大量资源浪费,用时也对经济效益的增长造成了不良的影响。
基于此,我厂决定将现有甲烷化工段净化工艺改为“双甲”净化工艺,其中净化变换工段工艺基本不变,由脱碳出口直接进合成气压缩机提压至7.1mpa,经过双甲工段副产粗甲醇1万吨/年,同时甲烷化工段蒸汽(5.0mpa)使用以后送变换工段进行二次使用。
我厂双甲工段由上海国际化建设计,中国化学工程第十六化建设有限责任公司2012年10月安装结束,同年10月30日满负荷生产,运行至今达到了设计要求和效果,满足了工艺要求。
二、“双甲”净化工艺的化学反应机理与工艺流程1.“双甲”净化工艺的化学反应机理2.1来自造气的半水煤气进入洗涤塔除去部分灰尘和冷却降温之后,半水煤气再通过入口水封流至脱硫塔底部,然后半水煤气经塔内填料与钠碱液逆流接触,除去半水煤气内富含的大部分硫化氢,此时需把出口气内的硫化氢质量浓度控制到≤100mg/m3以内,而硫化氢再通过气柜进入电滤器除尘岗位。
合成氨生产的三个过程
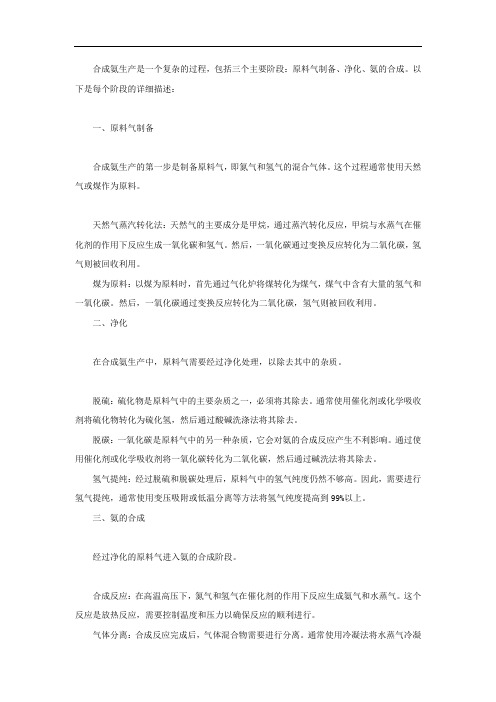
合成氨生产是一个复杂的过程,包括三个主要阶段:原料气制备、净化、氨的合成。
以下是每个阶段的详细描述:一、原料气制备合成氨生产的第一步是制备原料气,即氮气和氢气的混合气体。
这个过程通常使用天然气或煤作为原料。
天然气蒸汽转化法:天然气的主要成分是甲烷,通过蒸汽转化反应,甲烷与水蒸气在催化剂的作用下反应生成一氧化碳和氢气。
然后,一氧化碳通过变换反应转化为二氧化碳,氢气则被回收利用。
煤为原料:以煤为原料时,首先通过气化炉将煤转化为煤气,煤气中含有大量的氢气和一氧化碳。
然后,一氧化碳通过变换反应转化为二氧化碳,氢气则被回收利用。
二、净化在合成氨生产中,原料气需要经过净化处理,以除去其中的杂质。
脱硫:硫化物是原料气中的主要杂质之一,必须将其除去。
通常使用催化剂或化学吸收剂将硫化物转化为硫化氢,然后通过酸碱洗涤法将其除去。
脱碳:一氧化碳是原料气中的另一种杂质,它会对氨的合成反应产生不利影响。
通过使用催化剂或化学吸收剂将一氧化碳转化为二氧化碳,然后通过碱洗法将其除去。
氢气提纯:经过脱硫和脱碳处理后,原料气中的氢气纯度仍然不够高。
因此,需要进行氢气提纯,通常使用变压吸附或低温分离等方法将氢气纯度提高到99%以上。
三、氨的合成经过净化的原料气进入氨的合成阶段。
合成反应:在高温高压下,氮气和氢气在催化剂的作用下反应生成氨气和水蒸气。
这个反应是放热反应,需要控制温度和压力以确保反应的顺利进行。
气体分离:合成反应完成后,气体混合物需要进行分离。
通常使用冷凝法将水蒸气冷凝成液体水,然后通过蒸馏法将氨气从气体中分离出来。
氨的精制:经过气体分离后得到的氨气可能含有其他杂质,如硫化氢、二氧化碳等。
因此,需要进行氨的精制,通常使用化学吸收法或物理吸附法将杂质除去,以提高氨的纯度。
产品储存和运输:经过精制后的氨可以储存在专门的储罐中,也可以通过管道输送到下游用户。
在储存和运输过程中,需要注意安全措施,防止泄漏和事故发生。
总之,合成氨生产是一个复杂的过程,包括原料气制备、净化和氨的合成三个主要阶段。
合成氨原料气净化精制工艺的选择

合成氨原料气净化精制工艺的选择合成氨原料气净化、精制工艺的选择及应用本文系统阐述了近年来合成氨原料气的净化、精制工艺的发展历程。
分别介绍了“双甲工艺”、“醇烃化”及“醇烷化”等不同净化及精制工艺。
从工艺设计、节能降耗及实际案例等方面比较了上述工艺;结果表明:不论是哪种净化、精制工艺,关键的工艺控制点是:将co+co2净化精制至微量级,降低有效氢的损耗,降低生产消耗。
关键词:醇烃化、低能耗、合成氨、净化、精制1概述合成氨原料气的精制工艺,在近20多年的发展历程中展开了革命性的变化,从铜洗脸与深度转换串成甲烷化工艺,首创了“双甲”、“醇烃化”崭新工艺技术,为我国合成氨原料气精制开拓了代莱工艺、装备技术路线,同时也为我国化肥生产装置的大型化、节能环保化、自控化打下了基础。
湖南安淳高新技术有限公司研发、具有自主知识产权的醇烃化(双甲)净化、精制工艺,主要是将合成氨原料气中的co+co2经催化反应脱去,氨合成补充气中的co+co2微量达到≤10ppm的纯氢氮气,使氨合成的催化剂具有更好地活性,提高了反应的合成率和催化剂的运行周期,使生产过程更简便、更节能、更容易实行自控化。
醇烃化(双甲)工艺的应用世界首创,为我国化肥企业的节能减排、扩能增效、快速发展起到了助推作用,化肥企业单套装备从50ktnh3/a发展到今天的500ktnh3/a的生产规模,醇烃化(双甲)精制工艺发挥了重要作用。
2氨制备原料气的净化、精制工艺技术的了解2.1双甲工艺“双甲工艺”(见图1)是甲醇化(二级串并结合)后串联甲烷化(镍催化剂);合成氨生产线脱c来的co+co2约为2.0%~6.0%的氢氮气,经压缩机提高压力进入一级甲醇系统联产粗甲醇,原料气的净化在二级甲醇系统完成,可在中压段或高压段进行,一般入甲烷化塔的co+co2为≤300ppm,有利于合成氨生产的低耗运行。
图1双甲工艺流程示意图2.2醇烃化工艺“醇烃化工艺”(见到图2)就是“双甲工艺”的升级崭新工艺技术,主要就是在精制系统内“催化剂”上的技术创新,具备原料气精制过程中的精制度低、h2耗少、生产管理更方便快捷、催化剂使用寿命短等优势,为我国合成氨生产的大型化、节能环保化、长周期运转奠定了坚石的基础。
合成氨生产企业中的气体精制

合成氨生产企业中的气体精制摘要:对合成氨原料气体精制的几种工艺:醋酸铜氨液精制法、低温甲醇洗串液氮洗涤净化精制法、醇烷化和醇烃化法进行比较,从而对未来合成氨原料气体精制发展方向做出分析判断。
关键词:合成氨铜洗液氮洗醇烷化醇烃化工业生产合成氨原料气在合成氨过程中,因还原态铁触媒对环境气体要求苛刻性,需要将原料气中含氧分子去除至百万分之十的数量级,气体精制就是将原料气中含有的较多的H2O、CO、CO2处理到合成反应要求含量的过程,工业应用精制方法主要有:醋酸铜氨液精制法,低温甲醇洗串液氮洗涤净化精制法,醇烷化和醇烃化精制法。
一、几种精制方法介绍1、醋酸铜氨液精制法醋酸铜氨液精制法,简称“铜洗”法,原理是利用醋酸铜氨液来脱除原料气中的少量CO、CO2,达到精制原料气的目的。
铜氨液吸收CO是在游离氨存在下,依靠低价铜离子进行的,其反应如下:CO(液相)+Cu(NH3)2Ac +NH3?Cu(NH3)3Ac·CO+Q铜氨液吸收CO的作用,先是CO与铜氨液接触被溶解,CO再和低价铜离子作用生成络合物,并放出热量。
铜氨液吸收二氧化碳是依靠铜氨液中的游离氨,反应如下:CO2+2NH3+ H2O?(NH4)2CO3+Q生成的(NH4)2CO3会继续吸收CO2而生成NH4HCO3CO2+(NH4)2CO3+ H2O?2NH4HCO3+Q以上反应都是放热反应,而铜液温度升高,将影响吸收能力。
生成的碳酸铵和碳酸氢氨在温度较低时易于结晶;当铜液中乙酸和氨含量不足时,铜液吸收CO2后又会生成碳酸铜沉淀,这些结晶和沉淀,都将造成设备和管道堵塞,影响生产,所以进入铜洗系统原料气中CO2含量不能太高,并且铜液中应有足够乙酸和氨含量。
吸收了CO和CO2的铜氨液在减压、与再生气逆向接触、加热后,再生彻底的铜氨液继续进行CO和CO2吸收。
2、低温甲醇洗串液氮洗净化精制方法液氮洗涤原理是多组分精馏,是利用合成氨原料气中H2与CO、CH4、Ar 沸点相差较大,通过做功将温度降低到-194℃左右时,将CO、CH4、Ar从气相中溶解到液氮中,达到脱除CO、CH4、Ar等杂质目的,此过程是在液氮洗工序氮洗塔中完成。
合成氨工艺原料气净化方法

摘要:氨合成反应需要高纯度的H2和N2,无论以固体(煤或焦炭)还是用烃类(天然气、石脑油等)为原料获得的原料气中,都含有一氧化碳、二氧化碳、硫化物等不利于合成反应的成分,需要在进入合成塔之前除去,否则将导致氨合成催化剂中毒而无法运行。在多年的实践和探索中,合成氨工艺原料气净化方法不断创新和改进,由原来高污染高能耗的铜洗法发展到如今的高效节能净化技术。本文简述了铜洗、双甲、醇烃化等几种合成氨原料气净化的工艺原理、方法及其特点,对几种净化工艺进行了对比分析。并介绍了新型节能净化技术。
2.3 甲醇甲烷净化工艺法(双甲工艺)
“双甲”工艺,实际上就是合成氨厂将联醇、甲烷化技术引入原料气净化系统,从而省去落 后的铜洗再生工艺。该工艺由两部分组成,在甲醇合成之后,再是传统的甲烷化工艺工序。工艺原理:
甲醇化工艺CO+2H2 = CH3OH CO2+3H2 = CH3OH +H2O;
甲烷化工艺CO+3H2= CH4 +H2O CO2 +4H2=CH4+2H2 O
四.
合成氨厂原料气净化工艺随着时代发展,已从较为落后的铜洗工艺法逐渐发展到 工艺较为先进的醇烃化及醇烷化净化工艺,并不断向节能减排方向发展,如通过增加1台换热器来改进分子筛再生系统,用新增换热器来对系统内氮气进行换热,降低了其他换热器外部供能,从而提高能源利用率,达到节能的效果;合成氨原料气节能净化装置,回收了合成氨原料气中的甲烷,增加了产出,提高了原料利用率,同时有效减少了氨合成工序弛放气的排放量等等。
醇烃化工艺就是醇醚化、醇烃化精制工艺。第一步将双甲工艺中甲醇化催化剂更换成醇醚复 合催化剂,使CO+CO2与H2反应生成甲醇,并随即水解为二甲醚。第二步将双甲工艺的甲烷化催化剂更换为烃化催化剂,使 CO+CO2与H2反应生成低碳烃化物、低碳醇化物,低碳烃化物、低碳醇化物在水冷温度下可冷凝为液相,与气体分离。优点:①脱除CO+CO2的量低且稳定,并能较大幅度地提高联产甲醇的产量;②烃化生产烃类物质,高压常温下冷凝分离;③烃化操作温度较甲烷化低60~80℃,烃化反应床层更易维持自热操作;④烃化催化剂活性温区宽,不易烧结、老化,使用寿命长;⑤烃化催化剂价格便宜;⑥甲醇在烃化塔内无逆反应发生。
新型氨合成工艺技术的特点及比较
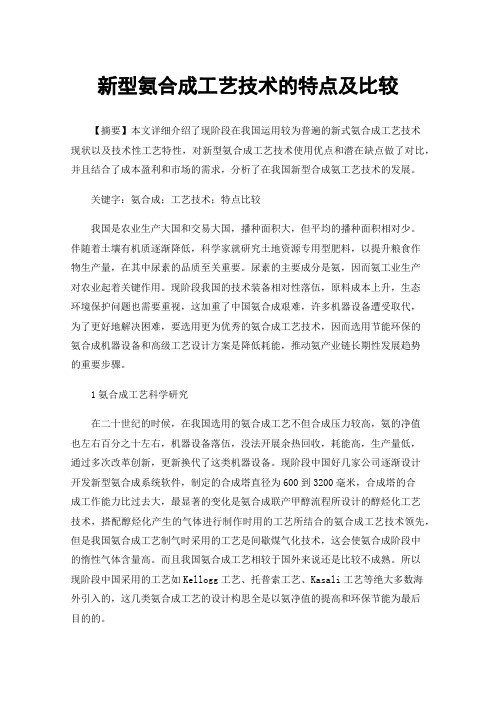
新型氨合成工艺技术的特点及比较【摘要】本文详细介绍了现阶段在我国运用较为普遍的新式氨合成工艺技术现状以及技术性工艺特性,对新型氨合成工艺技术使用优点和潜在缺点做了对比,并且结合了成本盈利和市场的需求,分析了在我国新型合成氨工艺技术的发展。
关键字:氨合成;工艺技术;特点比较我国是农业生产大国和交易大国,播种面积大,但平均的播种面积相对少。
伴随着土壤有机质逐渐降低,科学家就研究土地资源专用型肥料,以提升粮食作物生产量,在其中尿素的品质至关重要。
尿素的主要成分是氨,因而氨工业生产对农业起着关键作用。
现阶段我国的技术装备相对性落伍,原料成本上升,生态环境保护问题也需要重视,这加重了中国氨合成艰难,许多机器设备遭受取代,为了更好地解决困难,要选用更为优秀的氨合成工艺技术,因而选用节能环保的氨合成机器设备和高级工艺设计方案是降低耗能,推动氨产业链长期性发展趋势的重要步骤。
1氨合成工艺科学研究在二十世纪的时候,在我国选用的氨合成工艺不但合成压力较高,氨的净值也左右百分之十左右,机器设备落伍,没法开展余热回收,耗能高,生产量低,通过多次改革创新,更新换代了这类机器设备。
现阶段中国好几家公司逐渐设计开发新型氨合成系统软件,制定的合成塔直径为600到3200毫米,合成塔的合成工作能力比过去大,最显著的变化是氨合成联产甲醇流程所设计的醇烃化工艺技术,搭配醇烃化产生的气体进行制作时用的工艺所结合的氨合成工艺技术领先,但是我国氨合成工艺制气时采用的工艺是间歇煤气化技术,这会使氨合成阶段中的惰性气体含量高。
而且我国氨合成工艺相较于国外来说还是比较不成熟。
所以现阶段中国采用的工艺如Kellogg工艺、托普索工艺、Kasali工艺等绝大多数海外引入的,这几类氨合成工艺的设计构思全是以氨净值的提高和环保节能为最后目的的。
2 合成工艺简介2.1Kellogg氨合成工艺Kellogg氨合成工艺是美国的一项氨合成技术,它意味着全球氨合成技术的专业水准,由卧式径向塔、热壁、氨冷气等构造构成。
合成氨生产原料的比较解读

❖ 1 铜洗法
❖ 醋酸铜氨液洗涤法(简称铜洗)是最古老的方法, 早在1913年就开始应用。铜洗法以其工艺成 熟、操作弹性大,长期在中小型合成氨厂占 据主导地位,但国外早在20世纪60年代就逐 步淘汰这种落后的工艺。
❖ 2.低压甲烷化法 ❖ 原料气甲烷化净化,这是气相中CO+CO2在
催化剂作用下与H2反应转化为CH4而得以净 化,是早期氮肥生产的一种传统气体净化工 艺。
2.以天然气或轻质油为原料制取氢气
该法是在催化剂存在下与水蒸汽反应转化制 气。主要发生下述反应:
CH4+H2O→CO+H2 CO+H2O→CO2+H2 CnH2n+nH2O→nCO+(2n+l)H2 反应在800-820℃下进行。从上述反应可知, 也有部分氢气来自水蒸汽。
❖ 用该法制得的气体组成中,氢气含量可达74%(体 积),其生产成本主要取决于原料价格,我国轻质 油价格高,制气成本贵,采用受到限制。大多数大 型合成氨合成甲醇工厂均采用天然气为原料,催化 水蒸汽转化制氢的工艺。我国在该领域进行了大量 有成效的研究工作,并建有大批工业生产装置。我 国曾开发采用间歇式天然气蒸汽转化制氢工艺,制 取小型合成氨厂的原料,这种方法不必用采高温合 金转化炉,装置投资成本低。以石油及天然气为原 料制氢的工艺已十分成熟,但因受原料的限制目前 主要用于制取化工原料。
甲烷化工艺流程图
中温变换气
脱碳气 气液分离器 甲烷预热器 换热器 甲烷化炉
冷却器
去变换系统
气水分离器
去压缩
❖ 3 甲醇甲烷净化工艺法(双甲工艺)
❖ 所谓“双甲”工艺,实际上就是合成氨厂将 联醇、甲烷化技术引入原料气净化系统,从 而省去落后的铜洗再生工艺。甲烷化工艺能 够控制好(CO+CO2)微量,但对原料气中 (CO+CO2)含量限制较为苛刻,而二者结合起 来形成的“双甲”净化工艺,保持了二者的 优点,弥补了二者的不足。
合成氨工艺

合成氨工艺流程(1)原料气制备将煤和天然气等原料制成含氢和氮的粗原料气。
对于固体原料煤和焦炭,通常采用气化的方法制取合成气;渣油可采用非催化部分氧化的方法获得合成气;对气态烃类和石脑油,工业中利用二段蒸汽转化法制取合成气。
(2)净化对粗原料气进行净化处理,除去氢气和氮气以外的杂质,主要包括变换过程、脱硫脱碳过程以及气体精制过程。
①一氧化碳变换过程在合成氨生产中,各种方法制取的原料气都含有CO,其体积分数一般为12%~40%。
合成氨需要的两种组分是H2和N2,因此需要除去合成气中的CO。
变换反应如下:CO+H2OH→2+CO2 =-41.2kJ/mol 0298HΔ由于CO变换过程是强放热过程,必须分段进行以利于回收反应热,并控制变换段出口残余CO含量。
第一步是高温变换,使大部分CO转变为CO2和H2;第二步是低温变换,将CO含量降至0.3%左右。
因此,CO变换反应既是原料气制造的继续,又是净化的过程,为后续脱碳过程创造条件。
②脱硫脱碳过程各种原料制取的粗原料气,都含有一些硫和碳的氧化物,为了防止合成氨生产过程催化剂的中毒,必须在氨合成工序前加以脱除,以天然气为原料的蒸汽转化法,第一道工序是脱硫,用以保护转化催化剂,以重油和煤为原料的部分氧化法,根据一氧化碳变换是否采用耐硫的催化剂而确定脱硫的位置。
工业脱硫方法种类很多,通常是采用物理或化学吸收的方法,常用的有低温甲醇洗法(Rectisol)、聚乙二醇二甲醚法(Selexol)等。
粗原料气经CO变换以后,变换气中除H2外,还有CO2、CO和CH4等组分,其中以CO2含量最多。
CO2既是氨合成催化剂的毒物,又是制造尿素、碳酸氢铵等氮肥的重要原料。
因此变换气中CO2的脱除必须兼顾这两方面的要求。
一般采用溶液吸收法脱除CO2。
根据吸收剂性能的不同,可分为两大类。
一类是物理吸收法,如低温甲醇洗法(Rectisol),聚乙二醇二甲醚法(Selexol),碳酸丙烯酯法。
合成氨厂净化工段的设计分析

合成氨厂净化工段的设计分析合成氨工艺在整个化工生产领域中具有重要作用。
我国的合成氨生产工艺已经经历一定的发展阶段,但相对于国外,我国在技术方面还存在一定的差距,主要问题体现在生产原料的利用率、合成氨的纯净度上。
基于此,本文将对合成氨工艺进行简单介绍,重点对合成氨厂净化工段的设计进行分析。
标签:合成氨工艺;纯净度;净化工段1 合成氨工艺流程及其特点目前,合成氨工艺流程种类较多,主要有ICI、Kellogg、伍德、Brown以及KBR工艺流程。
各种流程都有自身的优点,同时对原材料和设备的要求情况也有所不同。
ICI工艺流程通过简化工艺流程、提高催化剂效率对生产进行改良;Kellogg工艺流程通过降低炉内负荷,提高操作的稳定性。
现代合成氨工艺受到技术、原料以及生产设备等多种因素影响,呈现出以下发展特点:第一,生产规模逐渐扩大,变为大型生产。
使用大规模生产方式降低了投资、减少了占地面积同时提高了劳动效率;第二,对热能的综合利用。
合成氨工艺流程中会消耗大量的燃料,随着清洁能源的不断开发,合成氨在消耗能源方面的利用率不断提高;第三,自动化程度不断提高。
伴随计算机技术和自动化技术的不断发展,工业生产中自动化程度不断提高,在合成氨工艺中也不例外,自动化程度的提高对生产质量和生产效率有巨大的促进作用。
2 合成氨厂净化工段的设计分析2.1 半脱工序半脱工序是合成氨厂净化工段的首要阶段,根据长期以来工艺方式的筛选工作,决定在办水煤气脱硫方式中采用湿法根脱硫工艺中技术较为成熟可靠的栲胶法,使用这种方式的再生硫颗粒较大,容易分离,并且不容易造成堵塔现象,降低了生产成本,还简化了生产流程。
使用这种方式的净化程度较高,消耗较低,并且在排出液中不会出现氨氮超标等问题,降低对环境的影响。
具体流程分为以下四个步骤:第一,将脱硫装置的生产能力设计为200kt/a氨醇,将塔的直径设置为6000mm,同时在塔体上方提前安装好填料冲洗装置。
各厂工艺简述

合成氨系统工艺情况合成氨系统工艺流程简述:或产品氨合成氨系统分造气工段、脱硫工段、变换工段、变脱工段、碳化工段或脱碳工段、精脱硫工段、粗醇工段、合成工段。
一、造气工段:1、作用:以固体燃料(无烟块煤、焦炭、煤球、煤棒)为原料,空气、水蒸气为气化剂,在高温(1000℃-1200℃)、常压28KPa条件下制取合成氨的原料气(即半水煤气)。
2、生产工艺:主要有固定层间歇气化工艺、固定层富氧连续气化工艺、灰熔聚粉煤气化工艺、恩德炉煤气化工艺、固定流化床粉煤气化工艺、德士古水煤浆气化工艺、壳牌粉煤气化工艺、循环流化床粉煤气化工艺等。
小氮肥一般采用固定层间歇气化工艺和固定层富氧间歇气化工艺,我公司采用的是固定层歇气化工艺。
3、工艺指标:(1)原料煤质量指标:全水份≤6.0% 挥发分≤8.0% 灰分≤14.0% 固定碳≥75.0% 全硫≤0.5%出工段半水煤气指标:CO 29-33% CO26-9% H238-44%N214-17% CH40.5-1% O20.5%4、工艺流程简图:空气(或富氧空气)气柜5、主要反应方程式:C + O2=CO2 + Q 2C + O2=2CO + QCO2+ C=2CO – Q C+ 2H2O(汽)=CO2+ H2 – QC+ 2H2O(汽)=CO+ H2– Q二、脱硫工段:1、作用:脱除半水煤气中的H2S。
2、生产工艺:小氮肥厂一般采用液相法,主要有氨水液相催化法,栲胶氧化法,DDS法等。
我公司有氨水液相法(平陆、稷山),栲胶氧化法(新绛、闻喜、临猗),DDS法(临猗)。
硫磺回收:小氮肥厂一般采用间断熔硫和连续熔硫两种工艺,我公司两种工艺都有,临猗公司采用连续熔硫(邯钢技术),其它公司均为间断熔硫。
3、工艺指标:出口H2S:120~150mg/ m3 (全低变工艺)≤70 mg/ m3 (中串低工艺)4、工艺流程简图:脱硫溶剂半水煤气溶剂再生5、主要反应方程式:氨水法:吸收:NH3+ H2S=NH4HS + Q再生:NH4HS+O2 = NH3+ H2O + Q三、变换工段:1、作用:将半水煤气中的CO,在225-450℃、0.8 MP a或2.0 MP a的条件和催化剂作用下变换为CO2、H2,同时将大部分有机硫转化为无机硫。
合成氨工艺流程简述(word文档良心出品)

合成氨生产工艺简介
一、工艺流程图:
二:流程简述:
无烟块煤经加工成Φ30-100的块状,在造气炉内燃烧并蓄热,后与蒸汽反应生产半水煤气作为合成氨的原料气,原料气经过脱硫后送压缩,经一、二段加压后送变换、变脱,变换气回压缩三进,经三段(或三、四段)加压送脱碳净化后回压缩四进(或五进),经四、五段(或五、六段)加压送甲醇工段,经甲醇工段精制后的甲醇气回压缩,经六段(或七段)加压后送醇烃化工段净化,最后合格的H2、N2气送往合成工段,在一定的温度、压力和催化剂存在的条件下反应生成NH3,用于生产尿素和其他产品。
合成氨原料气醇烃化净化精制新工艺技术
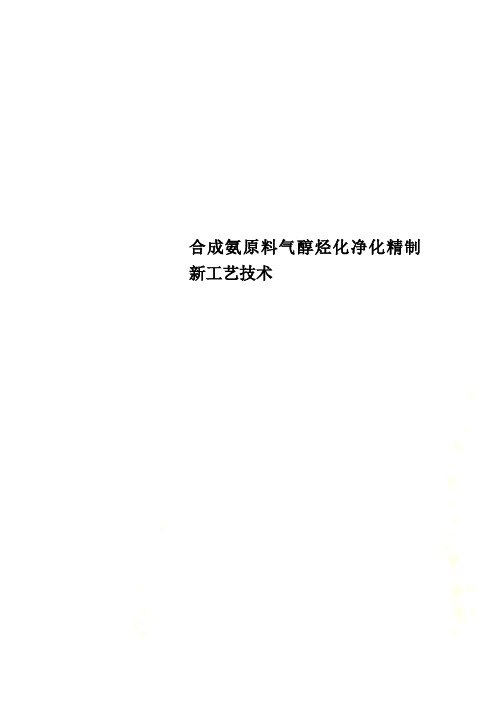
合成氨原料气醇烃化净化精制新工艺技术合成氨原料气醇烃化净化精制新工艺作者/来源:谢定中,卢健(湖南安淳高新技术有限公司,湖南长沙410015)日期: 2006-01-10 点击率:8771 醇烃化工艺开发简况合成氨原料气醇烃化净化精制工艺是双甲工艺的升级技术。
双甲工艺是湖南安淳高新技术有限公司开发成功的原创型技术,该技术于1990年提出,1991年进行工业化,1992年9月第一套工业化装置在湖南衡阳市氮肥厂投产成功,在国际上最早提出,最先进行工业化生产。
1993年4月获国家发明专利,相继又申请了可调节氨醇比的醇烃化专利技术,美、英等权威化学文摘均作了报道。
1994年元月通过化工部科技鉴定,1994年6月国家科委将该项目列入《国家重大科技成果推广计划》项目。
第一套装置至今已正常运行15年,目前这个示范厂的净化精制能力上升到了总氨80kt/a,副产10kt/a 甲醇,工艺投用以来,取得了很好的经济和社会效益。
目前,推广的工艺最大合成氨能力达400kt/a,在全国中、小合成氨厂推广达35家之多。
湖南郴州桥口氮肥厂的双甲工艺被评为国家优秀创新工程,双甲工艺评为1995年度原化学工业部十二大重大科技成果之一,2000年被授予湖南省科技进步一等奖,给予重点推广。
2003年醇烃化工艺获得国家科技进步二等奖。
此工艺开发和发展可分为三个阶段,历时近十五年的开发创新和竭力推广,有着超乎寻常的辛劳,可谓“十年磨一剑”。
技术发展的第一阶段——确认了国产甲烷化催化剂在高压条件下的运行条件。
技术发展之初,当有双甲净化工艺这个创意时,国内的很多厂家已经有了联醇工段,一般为联醇后再串铜洗进行净化精制,由于联醇出口CO和CO2的指标与传统的甲烷化进口气体成分指标不一样,且压力等级也不一样,要将铜洗去掉用甲烷化来替代,必须首先解决进甲烷化炉的进口气体的气体成份问题——一定要使醇后气中CO+CO2总量不超过0.7%,且越低越有利于提高气体的利用率和降低气体的消耗。
- 1、下载文档前请自行甄别文档内容的完整性,平台不提供额外的编辑、内容补充、找答案等附加服务。
- 2、"仅部分预览"的文档,不可在线预览部分如存在完整性等问题,可反馈申请退款(可完整预览的文档不适用该条件!)。
- 3、如文档侵犯您的权益,请联系客服反馈,我们会尽快为您处理(人工客服工作时间:9:00-18:30)。
合成氨原料气醇烃化净化精制新工艺作者/来源:定中,卢健(安淳高新技术, 410015)日期:2006-01-10 点击率:8771 醇烃化工艺开发简况合成氨原料气醇烃化净化精制工艺是双甲工艺的升级技术。
双甲工艺是安淳高新技术开发成功的原创型技术,该技术于1990年提出,1991年进行工业化,1992年9月第一套工业化装置在市氮肥厂投产成功,在国际上最早提出,最先进行工业化生产。
1993年4月获国家发明专利,相继又申请了可调节氨醇比的醇烃化专利技术,美、英等权威化学文摘均作了报道。
1994年元月通过化工部科技鉴定,1994年6月国家科委将该项目列入《国家重大科技成果推广计划》项目。
第一套装置至今已正常运行15年,目前这个示厂的净化精制能力上升到了总氨80kt/a,副产10kt/a甲醇,工艺投用以来,取得了很好的经济和社会效益。
目前,推广的工艺最大合成氨能力达400kt/a,在全国中、小合成氨厂推广达35家之多。
桥口氮肥厂的双甲工艺被评为国家优秀创新工程,双甲工艺评为1995年度原化学工业部十二大重大科技成果之一,2000年被授予省科技进步一等奖,给予重点推广。
2003年醇烃化工艺获得国家科技进步二等奖。
此工艺开发和发展可分为三个阶段,历时近十五年的开发创新和竭力推广,有着超乎寻常的辛劳,可谓“十年磨一剑”。
技术发展的第一阶段——确认了国产甲烷化催化剂在高压条件下的运行条件。
技术发展之初,当有双甲净化工艺这个创意时,国的很多厂家已经有了联醇工段,一般为联醇后再串铜洗进行净化精制,由于联醇出口CO和CO2的指标与传统的甲烷化进口气体成分指标不一样,且压力等级也不一样,要将铜洗去掉用甲烷化来替代,必须首先解决进甲烷化炉的进口气体的气体成份问题——一定要使醇后气中CO+CO2总量不超过0.7%,且越低越有利于提高气体的利用率和降低气体的消耗。
另外要使甲烷化催化剂能在甲醇之后的压力级运行必须有一套可行的工艺条件及设备等来保证。
而当时,国际、国传统镍基甲烷化催化剂的使用压力均在0.3MPa,而当时甲醇催化剂活性压力为13MPa,按工艺布置,甲烷化只能放置在甲醇后,因此,必须要找出甲烷化催化剂在高压下的工况条件。
我公司通过改变工艺条件、流程及设备结构,进行了大量的实验,模索出了一整套甲烷化催化剂在高压条件下的运行条件,于1991年在氮肥厂的40kt/a装置上投产,达到了预期的效果。
技术发展的第二阶段——确定了可调氨醇比的思维模式及工艺条件。
当流程打通后,气体的成分控制、新鲜气的消耗、副产甲醇的量及工艺长久稳定运行的条件等均需要摸索,要求有切实可行的工艺方法及操作工艺指标。
特别是当甲醇市场波动时,氨和副产甲醇的产量配合要自如,且经济性能要好、工艺指标也要先进。
为此我们摸索出了一种可调氨醇比的工艺条件和设备配置方法,达到了醇氨比可在1∶20到1∶1的围进行调整,且可保证工艺运行稳定,净化精制气净化指标不变的目标。
这种工艺方法的更新,使很多厂家获得了十分优厚的效益回报。
技术发展的第三阶段——开发了醇烃化净化精制工艺,代替甲醇甲烷化(双甲)工艺。
众所周知,甲烷化反应主要是将醇后气中少量的CO和CO2与气体中的H2进行合成反应,生成CH4和水,而在氨合成工段CH4为无用的惰性气体,将要在生产过程中放空掉。
因此,我们要求醇后气中CO和CO2尽量低,另外找出一种能使合成后的CH4量生成少的催化剂来替代纯甲烷化的工艺,我们开发了一种价廉的催化剂,称之为醇烃化催化剂,以此来取代甲烷化催化剂。
首次使用是在氮肥厂和化工股份,达到了降低新鲜气消耗约30%的效果。
换言之,利用这种催化剂可将原来采用气态的废气输出方式换成液态,且此物质可回收利用,既降低了有效气体的消耗,又使工艺操作和流程更加简化。
基于此,我们成功地将双甲工艺升级为更加先进、更加节能的醇烃化工艺,此技术一问世,得到了同行的一致认同,成功地获得了国家科技进步二等奖。
不论是双甲工艺还是醇烃化工艺净化精制原料气都比目前很多厂家在用传统的铜洗法和深度低变—甲烷化法净化精制工艺有着比较明显优点。
2 醇烃化工艺技术方案2.1 化学反应2.1.1 甲醇化反应原料气中CO、CO2与H2在一定温度、催化剂作用下生成粗甲醇,经过冷却、分离送入中间贮糟,此工艺类似于合成氨的联醇工艺,但对醇后气的指标要求高,因而要求醇塔要有更高的转化率和更好的热利用率。
本工序主要反应方程式如下主反应CO+2H2 = CH3OH +102.5kJ/molCO2+3H2 = CH3OH+H2O+59.6kJ/mol副反应4CO+8H2 = C4H9OH+3H2O +49.62kJ/mol2CO+4H2 = (CH3)2O+H2O+200.2kJ/mol2CH3OH = (CH3)2O+H2OCO+3H2 = CH4+H2O +115.6kJ/molCO2+H2=CO+H2O-42.9kJ/molnCO+2nH2=(CH2)n+nH2O+Q2.1.2 甲烷化反应经甲醇化工序后的醇后气,含CO+CO2为0.03%~0.3%,经换热后温度达到280℃,进入甲烷化工序,净化气中CO、CO2在催化剂作用下,与H2生成甲烷。
反应方程如下:主反应:CO +3H2 = CH4 + H2O +206.3kJ/molCO2 + 4H2 = CH4 + 2H2O +165.1kJ/mol副反应:O2+2H2=2H2O+C +484.0kJ/mol2CO=CO2+C+172.5kJ/molCO+H2=H2O+C+131.5kJ/molNi+4CO=Ni(CO)4(气)2.2 双甲工艺流程简图及说明2.2.1 双甲工艺的原则流程图1 双甲工艺的原则流程图造气出来的半水煤气经气柜后,进行粗脱硫,使H2S含量<0.07g/m3,加压至0.8MPa,进入中变;中变出来的气体CO含量控制在1.5%~5%,经脱碳,使CO2下降到0.2%~0.5%,再用无硫氨水进行第二次脱硫,将H2S脱除到100×10-6以下;再进行精脱硫,使气体之总硫降到0.1×10-6;气体再入高压机压缩到3.0~13MPa(压力的配置与甲醇的产量大小有关,原则上醇产量高时取较低的压力,反之可取高一点)与醇后气进行换热,温度为200℃,进入甲醇化反应。
从甲醇化塔出来的气体,与新来的气体换热,再水冷至40℃左右,进入醇分,经醇分后CO+CO2达到0.03%~0.3%;去高压机加压至与氨合成相等压力,进入甲烷化系统(或醇烃化系统),反应后的气体CO+CO2≤10×10-6,经换热冷却分离水分后,送往合成系统。
从合成氨系统排出的吹除气及液氨贮罐排出的弛放气,经脱氨后去氢回收装置,利用真空纤维或变压吸附法对气体介质的选择吸附,吸附弛放气中的H2。
H2解吸后,回到系统中,未吸附的气体则排空。
2.2.2 可控制醇氨比的联产甲醇双甲工艺流程(图2)双甲工艺的目的是以净化精制原料气为主,副产甲醇为辅。
但随着市场的变化,产品需求也有变化,即有时醇氨比要大幅度调节。
在甲醇市场好时,醇氨比要求达到1∶3或更高。
此时产醇和精制原料气都是双甲(或醇烃化)工艺的重要任务。
这种条件下我们的流程安排原则上是设置两个甲醇塔,第一个甲醇塔以产醇(尽量放在低压级)为主,第二个醇化塔的目的是净化或深度净化合成氨原料气。
经过第二个塔后CO+CO2含量≤0.3%(这种指标既使新鲜气的消耗不多、又可使热的利用率高、操作方便简捷,后面将专门论述)。
图2 可调氨醇比的双甲流程(醇产量较大)这种安排很灵活,当产甲醇为主,醇氨比很大时,原料气通过两塔,在第一塔中CO与CO2的70%转化为醇;第二塔只把剩余30%的CO与CO2 进行转化,达到既产醇又深度净化的效果,使出醇化系统的CO+CO2总量≤0.3%。
如果甲醇市场需求疲软,工艺以净化精制为主,甲醇是副产品,并使产量尽量少;例如醇氨比达1∶10到1∶20,此时可只用一个醇化塔,这一套醇化系统在运行中可以不启用循环机;以第二醇化塔作为备用塔;当第一塔催化剂活性下降、催化剂老化后,再启用第二塔,同样全过程均可十分方便地控制入甲烷化炉的CO+CO2含量≤0.3%。
第一级甲醇化采用3.0MPa或8.0MPa,第二级甲醇化及甲烷化与氨合成采用12~32MPa压力均可(因地制宜视具体情况确定配置方式)。
第一级仍以产醇为主,即90%的CO与CO2在此压力下转化为粗甲醇,剩余10%的CO与CO2在12~32MPa(或30MPa)压力下转化为甲醇,使CO+CO2含量≤0.3%进入甲烷化,甲烷化后气体中CO+CO2≤10×10-6,送入氨合成。
此流程的优点之一是在低压下合成甲醇,即有占整个原料气6%~10%的气体(CO、CO2和生成甲醇需要的H2),不需加压到更高压力,大大节约了电耗。
优点之二是在3~8MPa压力下甲醇化,可以利用甲醇化反应热副产中压蒸汽,作动力用,背压后蒸汽仍可作为工艺用汽。
优点之三由于甲烷化(或醇烃化)与氨合成等压,可免除工艺气体再过压缩机升压而污染气体这一环节,可以较方便地利用氨合成反应热,维持低成分下(CO+CO2≤0.3%)甲烷化炉(或醇烃化炉)的反应温度,而不必开电炉来维持反应。
对老厂采用醇烃化工艺,高压机没有3~5MPa这一段,而只有7.8MPa、12.5MPa和30MPa等压力段,则分别可以在7.8MPa和12.5MPa压力下进行甲醇化,然后升压至15MPa或32MPa进行甲烷化或醇烃化和氨合成。
这种流程的节能效果也很显著。
这种多级不等压的双甲工艺是我公司因地制宜既有利于生产,又有利于净化和节能的通用设计方法,均有成功的应用实例。
2.2.3 联产甲醇的醇烃化精制流程将甲烷化镍基催化剂改成我公司开发的醇烃化催化剂,则形成可调氨醇比的醇烃化精制流程(图3)。
图3 可调氨醇比的醇烃化原则流程取代双甲工艺的的醇烃化工艺中烃反应有如下几个主要的反应式(2n+1)H2 + nCO →C n H(2n+2) +nH2O (1)2nH2 + nCO →C n H2n +nH2O (2)2nH2 + nCO →CnH(2n + 2)O +(n-1)H2O (3)(3n+1)H2 + nCO2→C n H(2n+2) +2nH2O (4)从反应式可看出,醇后气中CO与CO2在醇烃化催化剂选择作用下,大部分可以生成醇类、多元醇类及非常少量的CH4。
多元醇类物质、醇烃类等物质均可在常温下冷凝为液体,有很好的分离性能,环保性能也很好。
这种物质可作为燃料使用或作为产品来提纯(将其直接送到甲醇精馏岗位提走其中35%的甲醇产品,其余可作为甲醇精馏残液进入燃烧炉烧之)。
无疑,由于醇后气中CO、CO2生成甲烷的量大大减少,送入氨合成后,因甲烷积聚造成的放空量也将减少,由于反应物中生成了高碳的产品,大大减少了原料气的H2消耗,这就是醇烃化工艺的原料气消耗为什么能大幅度下降的基本原理。