1550mm 酸洗轧机联合机组AGC系统组成及改造
1550mm酸轧机组AGC液压压下系统故障分析及处理

2 故 障处理 及其分析
2 . 1 故 障及 其处理
部 脱 m感 应磁 环 ,5号 机 架 操作 侧 A G C液 压 缸 S O N Y磁 尺 磁 杆弯 曲变 形 ,磁 杆 直线 长 度 缩 短 。
这 两 个 磁 杆 均 严 重 黏 接有 沥青 状 同化 油 垢 。分
全 液压 压 下式 AG C控 制 系统 故 障 主要 分 为
定是传感器故 障 ,鉴 于该传感器是嵌于缸 内不
易 更换 ,最终 更换 2个 A G C压下 缸 后 系统 恢 复
正常。 2 . 2 故 障分析
( 1 )将 离 线 A G C缸 拆 解 对 位 移 传 感 器 ( S O N Y 磁 尺 ) 检 查 后 发 现 ,4号 机 架 操 作 侧 A G C液 压缸 S O N Y磁 尺 磁杆 弯 曲 变形 ,磁 杆 端
样 化 验周 期 ,将 每 2个 月 化 验 1次 改 为 1 月 1
次 。确 保 清洁度 保持 在 N A S 5~N A S 6级 。
( 冷 轧板 带厂 马先富 吴 兵 唐水 清 )
查 ,并 检 查 压 下 缸 的 内漏 情 况 ,确认 无故 障后
同样 情形 也 } } 1 现于 5 号轧机的 A G C缸 ,因 而 确
冷轧板带 厂 1 5 5 0 m m酸轧联合 机组设计年 产
能 1 0 0 万 吨 ,于 2 0 0 8 — 0 5投产 ,轧 机采用 5 机 架
连轧 方式 ,均 为 4辊 轧 机 ,采 用 全 液 压 压下 式
5号机架 投 入压下 过程 中操 作 侧位 移偏 差报 警 而 无法 投 入 压 下 。处 理 方 法 :① 对 可 能 影 响压 下
速度 的液 压 阀组 ( 伺 服 阀除 外 )进 行 了逐 一 排
冷连轧AGC缸传感器升级改造
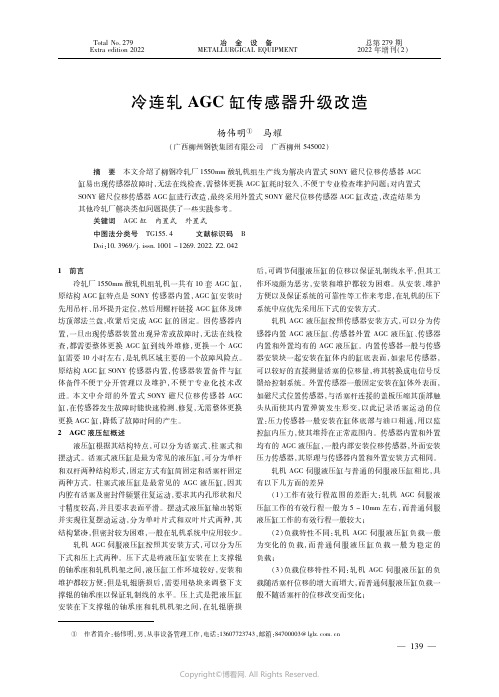
冷连轧AGC缸传感器升级改造杨伟明① 马耀(广西柳州钢铁集团有限公司 广西柳州545002)摘 要 本文介绍了柳钢冷轧厂1550mm酸轧机组生产线为解决内置式SONY磁尺位移传感器AGC缸易出现传感器故障时,无法在线检查,需整体更换AGC缸耗时较久、不便于专业检查维护问题;对内置式SONY磁尺位移传感器AGC缸进行改造,最终采用外置式SONY磁尺位移传感器AGC缸改造,改造结果为其他冷轧厂解决类似问题提供了一些实践参考。
关键词 AGC缸 内置式 外置式中图法分类号 TG155.4 文献标识码 BDoi:10 3969/j issn 1001-1269 2022 Z2 0421 前言冷轧厂1550mm酸轧机组轧机一共有10套AGC缸,原结构AGC缸特点是SONY传感器内置,AGC缸安装时先用吊杆、吊环提升定位,然后用螺杆链接AGC缸体及牌坊顶部法兰盘,收紧后完成AGC缸的固定。
因传感器内置,一旦出现传感器装置出现异常或故障时,无法在线检查,都需要整体更换AGC缸到线外维修,更换一个AGC缸需要10小时左右,是轧机区域主要的一个故障风险点。
原结构AGC缸SONY传感器内置,传感器装置备件与缸体备件不便于分开管理以及维护,不便于专业化技术改进。
本文中介绍的外置式SONY磁尺位移传感器AGC缸,在传感器发生故障时能快速检测、修复,无需整体更换更换AGC缸,降低了故障时间的产生。
2 AGC液压缸概述液压缸根据其结构特点,可以分为活塞式、柱塞式和摆动式。
活塞式液压缸是最为常见的液压缸,可分为单杆和双杆两种结构形式,固定方式有缸简固定和活塞杆固定两种方式。
柱塞式液压缸是最常见的AGC液压缸,因其内腔有活塞及密封件频繁往复运动,要求其内孔形状和尺寸精度较高,并且要求表面平滑。
摆动式液压缸输出转矩并实现往复摆动运动,分为单叶片式和双叶片式两种,其结构紧凑,但密封较为困难,一般在轧机系统中应用较少。
轧机AGC伺服液压缸按照其安装方式,可以分为压下式和压上式两种。
AGC液压系统的组成及维护

Vo1.45 NO.3 June 2016
AGC液 压 系统 的 组成 及 维 护
罗 超
(中色科技股份有限公司 ,河南 洛阳 471039)
摘 要 :文章简要介绍了铝板带轧机 AGC液压 系统 的组 成及其基本工作 原理 ,结 合生产过 程中经常 出现的故障进 行 了
AGC液压系统发生故障除 了元器件质量和使用 不 当外 ,最 主要还 是液 压油 受 到污 染 。AGC液 压 系统 要求油液的清洁度为 NAS 6级 ,即便是很小的污染物 都可能导致液压元器件的卡阻或者相对运动面 的磨 损 ,从而导致液压系统频繁 出现故 障 ,因此保证液压 系统 的清 洁至关 重要 。在 液压 系 统安 装 时 ,需 用 面粉 团清 理油 箱 的每一 个角 落 ,尽 量 清理 掉 制造 和 运 输 过 程 中产生 的所 有异 物 ;液压 管 路需 采 用 不锈 钢 氩 弧 焊 焊 接 ,焊 接后 的不 锈 钢 管 必 须 进 行 认 真 清 理 ,尽 可 能 完 全去 除钢 管 内部 的 附着 物 。通 过 加 油 车 往 油 箱 中 加 油 时一定要 通 过过 滤 滤芯 ,要 摈 弃新 油 或 者看 起 来 没 有杂 质 的油液 就是 干 净 的错 误 观念 。加注 完 成 后 , 最好 用过滤 车连 续循 环 过滤 油 箱 内 的油 液 一段 时 间 , 之后 才能用 泵 站连接 阀台进 行 系 统 内 的循 环 冲洗 ,直 至从 油 箱 中取 出 的油 液 经化 验 后 达 到 NAS 6级 。在 生产过程 中也要避免无谓的加油次数 ,避免新油污染 液压 系统 。在 正 常使 用 过 程 中 ,由于 密 封 件 损 坏 、液 压元 器件 磨损 以及 外来 物 污 染 ,油液 的清 洁度 是 不 断 变 化 的 ,除 了按 要 求更换 滤芯 外 还需 定 期按 液 压 油 指 标 (SH/T0599~1994)的 要 求 对 油 箱 内 油 液 进 行 化 验,不满足要求时需及时进行更换 。
热连轧中AGC控制系统的研究与应用

热连轧中AGC控制系统的研究与应用莱钢1500mm带钢精轧机组由一架立辊和六架平辊轧机组成,即E2、F1~F6。
(E2前设有精除鳞箱用于清除中间坯表面的次生氧化铁皮)。
轧件依次进入立-平-平-平-平-平-平轧机连续轧制。
精轧机架间设有5台液压活套装置(即H1~H5),当轧件依次进入n+1架轧机时,n至n+1架轧机之间的活套依次升起,通过套高调节系统使轧机自动调速,并通过张力调节系统使带钢在微张力、恒张力状态下轧制,轧成所需要的带钢尺寸。
精轧机组F1~F6压下系统为全液压压下,并设有液压AGC自动厚度控制系统和正弯辊装置,用于保证带钢全长范围内的厚度精度及板形要求。
F1~F6工作辊设有轴向窜辊装置,可以控制轧辊凸度并使轧辊磨损均匀,提高轧辊使用寿命。
带钢尾部依次离开各架轧机时,活套装置便自动下降复位。
精轧机架间设有喷水冷却装置,用于控制终轧温度,带钢终轧温度在850℃左右。
精轧机组后设置Χ射线测厚仪和光电式测宽仪,其中测厚仪参与液压监控AGC控制。
AGC控制系统实现1 系统硬件配置根据工艺控制要求本工程自动化总体方案以“集散控制、分层结构”为主要特点,整个自动化系统分为3层。
第1层:现场参数检测与终端执行。
第2层:分散的数据处理、过程控制。
第3层:集中操作监视。
结合本生产线工艺布置和特点,控制系统使用了三套西门子TDC控制器(SIMATIC Tech nology and Drive Control——即工艺和驱动自动化系统),每套TDC控制器中配置4个CP U,下挂3个ET200远程I/O从站。
两台DELL工控机作为上微机监控,负责维护集成历史数据库和提供人机接口,访问TDC中的数据。
精轧生产线控制系统结构图1所示。
图1 1500mm带钢精轧压下网络结构图系统控制功能实现1 APC控制概念所谓APC控制就是在指定的时刻,将被控对象的位置自动地调节到预先给定的目标值上,调节后的位置与目标值之差保持在允许的误差范围内,这个调节过程称为位置自动控制,简称APC。
AGC系统维护技术

AGC系统维护技术一、AGC系统构成一般热轧机液压压下系统(俗称AGC系统)设置两回路供油系统,两个回路的共用部分设有安全卸荷阀,当系统压力出现异常时保护设备不受破坏而直接卸压。
每一回路都由两个单向阀及伺服阀构成,可以单独完成对伺服油缸的位置(或压力)控制。
常规典型的液压压下系统回路图如下:两回路的工作方法:AGC系统两个回路一般都可以独立完成对AGC油缸的位置或压力控制,也可以组合起来控制。
如下图:二、AGC 系统维护要领AGC 系统工作状态的好坏直接影响到轧钢过程的稳定性,影响带钢的质量(成品厚度精度、宽度等)。
经过大量的数据积累及分析大量废钢案例,对AGC 系统的状态把握必须从以下几方面进行:1、 定期作一次液压压下油缸的全行程测试,方法是:分别用#1、#2、#1+#2、#2+#1回路采用手工给定的方式设定伺服阀的开度,两侧油缸同时下压,当其中一个油缸活塞走完全行程时两个油缸活塞位置的差作为液压压下系统同步性好坏的一个评价指标,定义为ds os h h h ∆=-,从需求上讲,该偏差越小越好,考虑到系统各元件的实际状态,确定控制标准为||10h mm ∆≤(该指标为德国SMS 机械供应商及MOOG 伺服阀要求的指标)。
如果两个回路的测试结果都偏差较大,且方向一致,油缸可能存在问题,如果一个回路的测试结果偏差较小、而另一个回路的偏差较大,偏差大的回路的伺服阀存在问题。
测试工具:(专门开发的功能)2、油缸的内泄漏测试。
将F1~F7压到1000吨(一般为零调轧制力),手动强制关断单向阀、伺服阀输出为零,保持10分钟,轧制力的减小量作为衡量油缸(包括单向阀)泄漏的判据,以轧制力的减小量不大于10%作为临界值。
对同一机架两侧轧制力的减小量的差值也可以根据需要规定不能超过一定的百分比值。
说明:该功能也可以在基础自动化系统中开发成自动功能,简化及减少测试,保证测试顺利性及测试数据的可靠性。
3、伺服阀零偏测试两个回路伺服阀零偏测试。
AGC控制系统说明
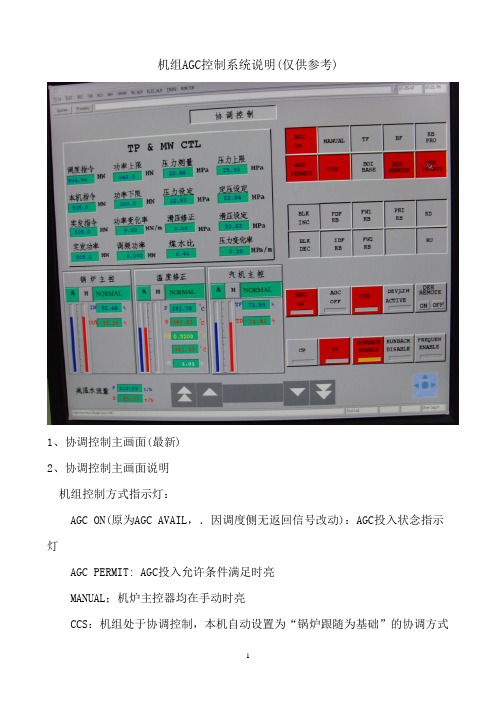
机组AGC控制系统说明(仅供参考)1、协调控制主画面(最新)2、协调控制主画面说明机组控制方式指示灯:AGC ON(原为AGC AVAIL,.因调度侧无返回信号改动):AGC投入状念指示灯AGC PERMIT: AGC投入允许条件满足时亮MANUAL;机炉主控器均在手动时亮CCS:机组处于协调控制,本机自动设置为“锅炉跟随为基础”的协调方式TF:汽机跟随方式,汽机主控投自动且锅炉主控不在自动,汽机调压力BF:锅炉跟随方式,汽机主控自动未投且锅炉主控在自动,锅炉调压力DEH REMOTE;DEH远方控制,汽机调门由DCS汽机主控控制。
DEH PERMIT:DEH允许投REMOTE,信号来自DEHRB PRO:RB动作过程中,RB触发后灯亮,当锅炉主控指令降到位后熄灭BOI BASE:锅炉基础方式,协调控制方式投入情况下,功率变送器损坏,自切为该方式。
异常状态指示灯:BLKINC:闭锁增负荷,包含:给水偏差:给水指令-实测值≥145T/H给水输出100%:任一小机转速≥5700rpm燃料输出偏差:指令-实测值≥22.5T/H燃料输出100%:任一给煤机煤量≥58T/H送风偏差:指令-实测值≥215.8T/H送风输出100%:任一送风机动叶开度≥95%BLK DEC:闭锁减负荷,包含:中间点温度低:中问点温度≤300℃给水偏差:给水指令一实测值≤一145t/h燃料偏差:指令一实测值≤一22.5t/h送风偏差:指令一实测值≤一215.8t/hFDF RB:送风RB,当负荷大于50%,两台送风机运行时一台跳闸。
IDF RB:引风RB,当负荷大于50%,两台引风机运行时一台跳闸。
FWl RB:给水70%RB,当负荷大于70%,两台汽动给水泵运行时一台跳闸,电动给水泵自启。
FW2 RB:给水50%RB,当负荷大于50%,两台汽动给水泵运行时一台跳闸,电动给水泵未自启。
PRI RB:一次风RB,当负荷大于50%,两台送风机运行时一台跳闸。
酸洗连轧联合机组自动穿带系统研究

·技术分析·酸洗连轧联合机组自动穿带系统研究王文广①1 张清东1 周晓敏1 林秀贞2 饶志雄2 顾华中2 李志勇2(1:北京科技大学机械工程学院 北京100083; 2:宝钢股份公司冷轧厂 上海200941)摘要 某1550酸洗连轧联合机组全套由国外引进,拥有世界一流的机电装备和轧制工艺技术。
为了进一步减少此机组的穿带耗时和穿带废料、提高穿带成功率,以扩大机组产能,为其研发了新的自动穿带系统。
研究工作包括建立穿带仿真软件,以离线仿真与现场试验相结合方法设计工艺方案、建立控制数模、整定系统参数,完成在线调试后投入生产使用。
迄今此系统已稳定运行6个多月。
关键词 冷连轧机 穿带 自动控制中图分类号 TG 333.72 文献标识码 AAutom atic Threading -in System for 1550mmCold T andem R olling MillsWang Wenguang Zhang Qingdong Zhou X iaomin(Mechanical Engineering School ,UST Beijing )Lin X iuzhen Rao Zhixiong G u Huazhong Li Zhiy ong(C old R olling Dept ,Baoshan Iron &Steel C o.,Ltd.)ABSTRACT 1550mm C DC M C old T andem M ills is introduced from abroad which have topping mechanical and electrical equipments and rolling mill production technology.In order to save m ore time and material during threading -in process ,im prove success odds of threading -in and enlarge productive capacity of the T andem M ills ,a simulation system is established ,which is used to study threading -in process.Through the combination of simulation and experiment ,the technological program is designed ,threading -in process control m odel is developed and threading system parameter is drawn up.A new Auto Threading -in System was established and have been used in spot.Up to now ,the system have functioned steadily for 6m onths.KE YWOR DS C old T andem M ills Threading -in Automatic regulation1 前言持续寻求扩大机组产能,不仅可以使企业获得更多的效益,也可以拉动企业的技术进步和核心竞争力提升。
北京科技大学科技成果——轧机液压AGC控制系统

北京科技大学科技成果——轧机液压AGC控制系统项目简介液压AGC具有响应速度快、控制精度高的优点,正在取代电动AGC成为当今新建轧机和欲改造轧机的首选技术。
北京科技大学高效轧制国家工程研究中心长期致力于液压AGC在大型工业轧机应用的研究,并在多条带钢连轧机组中取得成功应用,为轧钢技术国产化作出较大贡献。
AGC控制系统由L2过程控制系统和L1基础自动化控制体统组成。
L2级系统主要通过模型自学习完成对液压控制系统参数的缓慢变化造成的厚度偏差进行补偿;L1级系统则完成对实时参数变化造成的厚度偏差进行补偿,同时完成液压APC和液压AFC控制功能。
L2级完成的主要功能包括:轧制负荷分配及优化、辊缝位置基准计算和设定、轧制力预报、温度预报、模型自学习等。
涉及的计算模型包括:轧制力模型、变形抗力模型、残余应变模型、轧制弹跳模型(辊系弹性变形分析、轧机牌坊弹性变形)、板坯温度模型(辐射和对流、高压水、与轧辊接触产生的热传导、塑性功转变为热量引起的温升、摩擦热)、轧辊磨损模型、轧辊热膨胀模型、力矩模型、宽展模型、前滑模型、轧件尺寸计算模型、板形和板凸度模型、板厚控制与板形控制之间的关系、平面形状预测和控制模型等。
由L1级完成的液压AGC主要控制功能包括:液压缸位置控制(HAPC)、电动压下螺丝控制(EAPC)、自动厚度控制(HAGC,根据不同应用场合可以选择:压力AGC、硬度前馈AGC、测厚仪监控AGC、穿带自适应、快速监控AGC、流量AGC和张力AGC等的一种或几种)、补偿AGC(包括轧件宽度补偿、油膜轴承油膜厚度补偿、轧辊热膨胀与磨损补偿、尾部失张补偿、偏心滤波及补偿、伺服阀偏移补偿、穿带冲击补偿、卷取冲击补偿等)、轧辊平行控制(ALC)、自动纠偏、、轧机调零、轧机刚度测量、手动倾斜、事故锁定和卸荷等。
AGC工作方式包括相对AGC控制和绝对AGC控制两种。
该液压AGC系统和板形控制系统一起被评为“九五”国家重点科技攻关计划(重大技术装配)优秀科技成果,并已成功应用于多条轧线,取得了极高的控制精度。
轧机AGC培训资料
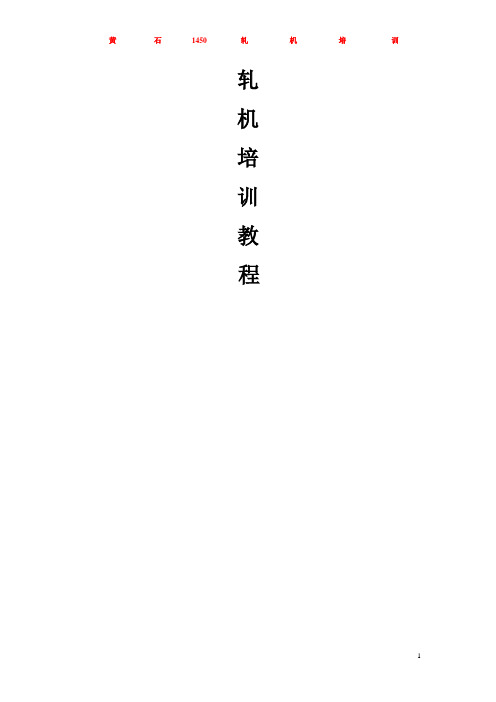
轧机培训教程1450液压AGC控制系统概述一:厚度自动控制原理AGC控制的目的,是借助于辊缝、张力、速度等可调参数,把轧制过程参数(如原料厚度、硬度、摩擦系数、变形抗力等)波动的影响消除,使其达到预期的目标厚度。
而辊缝、张力等参数的调节又是以轧机的弹性曲线和轧件的塑性曲线以及弹塑曲线即P-H图为依据的。
板带轧制过程既是轧件在轧制压力P的作用下产生塑性变形的过程,又是轧机在轧制压力P的作用下产生弹性变形(即所谓弹跳)的过程,二者同时发生,其作用力和反作用力相等而相互平衡。
由于轧机的弹跳,使轧出的带材厚度(h)等于轧辊的理论空载辊缝(So’)再加上轧机的弹跳值。
按照虎克定律,轧机弹性变形与应力成正比,则弹跳值应为P/K,此时h= So’+ P/ K式中:P——轧制力,t;K——轧机的刚度(t/mm),即弹跳一毫米所需轧制力的大小。
上式为轧机的弹跳方程,据此绘成曲线A称为轧机相关性变形式,如图,它近似一条直线,其斜率就是轧机的刚度。
但实际上在压力小时弹跳和压力的关系并非线性,且压力越小,所引起的变形也越难确定,亦即辊缝的实际零位很难确定。
为了消除这一非线性区段的影响,实际操作中可将轧辊预先压靠到一定程度,即压到一定的压力P。
然后将此时的辊缝批示定为零位,这就是所谓“零位调整”。
由图可看出:h= S0+(P-P0)/K式中S0——考虑预压变形的相当空载辊缝另一方面,给轧件一定的压下量(h0-h),就产生一定的压力(P),当料厚(h0)一定,h越小即是压下量越大,则轧制压力也越大,通过实测或计算可以求出对应于一定h值的P 值,在图上绘成曲线B,称为轧件塑性变形线。
B线与A线交点的纵坐标即为轧制力P,横坐标即为板带实际厚度h。
由P-H图可以看出,如果B线发生变形(变为B’),则为了保持厚度h不变,就必须移动压下位置,使A线移到A’,使A’和B’的交点的横坐标不变,亦即须使A线与B线的交点始终在一条垂直线C上。
轧机agc液压循环过滤方案

轧机agc液压循环过滤方案
在轧机的AGC(自动轧制控制)液压系统中,液压循环过滤是非常关键的,它有助于维持系统的稳定性和延长液压元件的使用寿命。
以下是一般的轧机AGC液压循环过滤方案:
过滤器类型:使用高效的过滤器来阻止固体颗粒、杂质和污染物进入液压系统。
过滤器的种类通常包括油泵入口过滤器、系统压力过滤器和油箱回油过滤器。
这些过滤器应该选择适当的微米级别,以确保有效地过滤掉系统中的杂质。
过滤器位置:安装过滤器的位置很关键。
通常,在油箱、油泵入口和系统的关键部位(如液压缸和阀体)都会安装过滤器,以最大程度地防止颗粒进入系统。
过滤器维护:建立定期的维护计划,包括过滤器的更换和清洗。
过滤器的性能随时间逐渐下降,定期更换过滤器有助于维持系统的高效运行。
在线监测系统:安装在线监测系统,可以实时监测液压油的状态,包括污染水平和温度。
一旦发现异常,系统可以提前发出警报,减少设备损坏的风险。
油液质量:使用高质量的液压油,符合系统规格要求。
油液的质量对于液压系统的正常运行至关重要。
压差指示器:在过滤器上安装压差指示器,监测过滤器的压降,一旦达到设定值,即表示过滤器需要更换或清洗。
以上是一般的轧机AGC液压循环过滤的一些建议。
具体的方案可能会根据轧机型号、厂家和应用环境而有所不同,因此建议根据设备的实际情况和制造商的建议进行选择。
柳钢1550mm冷轧带钢厚度控制系统的设计与实现

l 厚度控制基本原理及系统组成
11厚度控制基 本原理 .
厚度控制系统简称为AGC系统, 厚度控制的基本 原理就是在轧制过程 中, 应用测厚仪( 目前用的较多的 是x射线测厚仪 ) 对运行 中的带钢厚度进行连续测量, 然后将厚度实测值与厚度给定值h 进行 比较, 。 得出一
个厚度 偏差 值 , A 传送 到A 控 制系统 进行 数学 将 h GC
作者简介: 勤(97) 黄 17一, 硕士, 电气工程师, 现从事电气 设备
维护及现场施工管理工作 。
机 架 后 设 置 激光 测速 仪检 测带 钢 线速 度 。 () 度 自动控 制部 分 。 为整个 厚 度 自动控 制系 2厚 作
区配置了3 台x射线测厚仪通过Pi b s 网与基础 自 r iu — f DP 动化系统进行数据交换, 同时, 将每台测厚仪的实测值 在人机界面HMI 上显示 出来, 使整个 冷轧厚度控制系 统 响应快速 、 控制精确 、 控制思路 简单明了, 对全线顺 利 投 产 、 产 和早 日达 产起 着 至 关 重 要 的 作 用 。 稳
阐述 了该 系统 的 调 试 过 程 及 实 际应 用 效 果 。
关键 词: 带钢 ; 厚度控 制; 调试
Th s na d Re l a in o e S r ik e s Co t l y t m f 5 mm e De i n ai t f h tpThc n s n r se o 5 0 g z o t i oS 1
统的运算处理部分 , 其主要任务是将测厚仪实测出来
的厚度实测值与厚度给定值进行 比较, 计算出厚度偏
差值 , 并将 厚 度偏 差信 号放 大 , 传送  ̄AG I C系统 的控 制 ]
程序进行运算, 出需要调节 的参数值 。 得 ()执行机构。 3 接收到A C G 系统输出的控制信号后,
1550酸轧机组乳化液系统磁性过滤器的改造

I— — 气 缸 2— — f- 吲 刮 耙 3— — F 阅 刮 耙 4— — 轴 承 座 5— — 曲 机 构
改 造 J
l 磁性 过滤 器结 构示 意图
l 轴 下 轴 刮 把 下 刮把 磁棒 承 承 座
厂
/
…
…
…
黾
~
_{ =|
—
.
一
二~{ :} {
■
-
J
一/ i7,
J 鱼 …
…
。I●
。/ //
//|| | }
l㈡ ||| .
盟
I
^ .
,
I
,l1
n
|
I /¨ .
f/¨ 。 7
1— — 磁 怍 ; 2— — 七 刮 耙 ; 3— — 下 刮 耙 ; 4—— 推 中『: 5— — 挡 铁 ; 6—— 链 轮 、链 条 :7—— 齿 轮 电 机 ; 8— — 滑 块 9—— _Il1柄机 构
2 圆形刮 耙 设计 罔
3 结 语
该 设 计 简 化 了磁 性 过 滤 器 刮污 装 置 的 传 动 机构 ,使 用 更 加 简单 平 稳 。链 轮式 刮 耙 动 作平 稳 ,设 计 、安 装 与维护 具 有 极 (下转 第 62页 )
62
柳 钢 科 技
2018年第 1期
备件让步接收实践
1 前 言
该 批球 阀 阀体 的材 质 ,含 Ni质 量 分 数 为 10%。
在备件基本质量保证 的条件下 ,对备 件的 质量 缺 陷 部 分有 条 件 地接 收 ,双 方 对 备 件 降价 达 成 协 议 ,就 是 备 件 的 让 步 接 收 处 置 。 随 着柳 钢备 件 质 检 工作 的 深 入 ,购买 的 部分 备 件 没 有 达到合 同技术要求 ,但能满足使 用要求 ,经相 关部 门或使 用 单 位 同意 后 可对 该备 件 让 步接 收 , 以利 于 生 产 保 供 。本 文 总 结 柳 钢 实 施 备 件 让 步
轧机厚度自动控制AGC系统说明

轧机厚度自动控制AGC系统使 用 说 明 书中色科技股份有限公司装备所自动化室二零零九年八月二十五日目 录第一篇 软件使用说明书第一章 操作软件功能简介第二章 操作界面区简介第三章 操作使用说明第二篇 硬件使用说明书第一章 接口板、计算机板跨接配置图 第三篇 维护与检修第一章 系统维护简介及维护注意事项第二章 工程师站使用说明第三章 检测程序的使用第四章 常见故障判定方法第四篇 泵站触摸屏操作说明第五篇 常见故障的判定方法附录:第一章 目录第二章 系统内部接线表第三章 系统外部接线表第四章 系统接线原理图第五章 系统接口电路单元图第一篇软 件 说 明 书第一章 操作软件功能简介.设定系统轧制参数;.选择系统工作方式;.系统调零;.显示时实参数的棒棒图、馅饼图、动态曲线;.显示系统的工作方式、状态和报警。
以下就各功能进行分述:1、在轧机靠零前操作手需根据轧制工艺,设定每道次的入口厚度、出口厚度和轧制力等参数。
也可以在轧制表里事先输入,换道次时按下道次按钮,再按发送即可。
2、操作手根据不同的轧制出口厚度,设定机架控制器和厚度控制器的工作方式,与轧制参数配合以得到较理想的厚差控制效果。
3、在泄油状态下,操作手通过在规定状态下对调零键的操作,最终实现系统的调零或叫靠零,以便厚调系统正常工作。
4、在轧制过程中,以棒棒图、馅饼图和动态曲线显示厚调系统的轧制速度、轧制压力、开卷张力、卷取张力、操作侧油缸位置、传动侧油缸位置、压力差和厚差等实时值。
(注意:轧机压靠前操作侧油缸位置、传动侧油缸位置显示为油缸实际移动位置。
轧机压靠后操作侧油缸位置、传动侧油缸位置显示的是辊缝值。
)5、显示系统的工作方式、系统状态和系统报警。
6、系统有两种与传动和测厚仪协调工作模式A.常用数据由厚控AGC发送到传动及测厚仪。
如人口厚度、出口厚度、轧制速度及张力等等。
传动以此为基准值,如调整需通过把手或其他方式加到此基准值上,然后返送回AGC。
新钢1550mm酸轧机组过程控制系统分析及应用

Ab t a t C n tui n n t n f r e s o t l y t L )o 1 5 m D M mi i it d c di i p p r t s s r c : o s t o a df c o r o s nr s m( 2 f 5 0 m C C l s n o u e t s a e.I i itn u i o p c c os e l r n h
L 2控制 系统 的软 件 主要 由两 部分 构 成 : 控制 非
跟踪 、 事件 触发 、 制 规 程 及 各类 设 定 值 计 算 、 产 轧 生
收 稿 日期 :0 1— 3—0 21 0 9
作者简 介: 胡
韬 (9 1 , , 18 一) 男 江西新余人 , 助理 工程师 , 从事冶金设备 一动化软件维护及 开发工作 。
胡 韬 。 小云 王
3 80 ) 3 0 1
( 新余钢铁集 团有 限公 司 , 江西 新余
摘
要 : 介绍了新钢 15m 50 m酸轧机组过程控制系统( 2 的组成及功能, L) 并深入阐述了 L 2系统内部各个进程
间 、2与 L 、2与 L L 】I 3之 间 数 据 流 的 流 向 。现 场 应 用 表 明 , 系 统具 有 良好 的 稳 定 性 、 确性 和灵 活 性 。 该 准
1 概 况
新余 钢铁集 团有 限公 司冷轧 厂 15 r 冷 轧带 50 m a
钢生 产线 于 2 1 0 0年 5月 建成 投产 , 酸洗 一连 轧机 其 组 ( L—T M) 生产 冷 轧 带 钢产 品的 重要 机 组 , P C 是 对 控制 系统 的 自动 化水平 要求 非常 高 。该 机组 引进 了 德 国西 门 子 公 司 的 控 制 系 统 , 为 3级 控 制 ( 1 分 L、
1550UCMW轧机简介

第一章 机型一 机组设置3 1550UCMW三期工程1550酸轧联合机组是中日双方合作制造的一条酸洗-轧机联合机组。
该机组的冷连轧机采用日本日立公司开发的新型UCMW 冷轧机,并采用川崎K-WRS 技术,既能控制各类板形平坦度缺陷,也可以控制带钢的边缘降。
1550mm 冷连轧机组由五个机架组成,五个机架全部为UCMW 机型。
在每一机架的出口都安装有测速仪和张力测量仪,在第一机架的入口和出口处各安装一台测厚仪,在第五机架入口安装一台测厚仪,在第五机架出口安装有两台测厚仪、一台平坦度测量仪和一台边缘降测量仪。
机组的具体设置如图1-6和1-7所示,各机架板形技术配置见表1-3。
UCMW 轧机是一种六辊轧机,如图1-7所示。
++++图1-7 UCMW 轧机S1 S2 S3 S4 S5图1-6 1550UCMW 冷连轧机组示意图(注:*和**都表示该手段参与闭环反馈控制)二主要工艺参数3 1550UCMW1550冷连轧机组的主要工艺参数参见表1-6:三产品定位3 1550UCMW1550UCMW冷连轧机组的产品是以汽车用板为主的冷轧板、镀锌板和中低牌号的电工钢板,也是高技术、高难度、高附加值的产品。
冷轧薄板的钢种有CQ、DQ、DDQ、EDDQ、IF钢及HSLA。
1550冷连轧机组的目标是改变我国汽车制造业依赖进口冷轧汽车板的局面,同时更好的满足家用电器对中低牌号电工钢板和高级家用电路板的需求。
可见,2030机组以普通冷轧板、普通汽车板和镀锌板为基本产品,以轿车用板(尤其O5板)、彩涂板、宽规格板(B>1550)及IF钢为特色产品。
1420机组以镀锡板和薄规格冷轧板为基本产品,以家电外板、DI材及其它优质薄规格冷轧板为特色产品。
1550机组以普通冷轧板、汽车板、镀锌板和中低牌号的电工钢板为基本产品,以轿车用板(尤其O5板、高强钢、超深冲钢板)及IF钢为特色产品。
此外,各机组产品的宽度和厚度不同当然也是各自的优势。
合肥1550冷轧工艺(2011.11.24修改)_(2)--43页-BD

厚度仪,#1轧机入口与出口、#4轧机 出口各装1套,#5轧机出口装有2套, 用于测量带钢的厚度偏差。
速度仪, #2轧机到 #5轧机的出口 各装一个,用于测量带钢速度, 实现秒流量AGC控制 焊缝跟踪仪, #1轧机入口安装一
马钢(合肥)公司 1550 冷轧工艺培训教材 2.2.4 酸轧线工艺流程主要步骤
马钢(合肥)公司 1550 冷轧工艺培训教材
李素薇
2011 年 10 月 21 日
张紧与纠偏装置等)和 3 个活套组成,活套的主要作用就是对应于生产线各段的停机与升降速,适时给各段生产线提供所 需的带钢量或者储存多余的带钢量,以保证带钢在酸槽中的恒速不间断运行。具体来说,就是: 1 号活套,也叫入口活套,位于焊接系统与拉矫破鳞系统之间,作用是当带钢在焊机处停机进行焊接时,将其储存的 活套量供拉矫破鳞系统与酸洗漂洗系统使用,因此 1 号活套的正常使用位置是在“满套” ; 2 号活套,也叫中间活套,位于酸洗漂洗系统与切边剪之间,作用是换规格或换剪刃时,储存来自于酸洗漂洗系统的 多余的钢带量,因此 2 号活套的正常使用位置是在“空套” ; 3 号活套,也叫出口活套,位于切边剪与冷轧机组之间,作用是当切边剪换规格或换剪刃时将其储存的活套量供冷轧 机组使用、当轧机换辊时储存来自于切边剪的多余的钢带量,因此 3 号活套的正常使用位置是在“中套” 。 2.2.3 轧机段工艺流程 在窜列式轧机的入口设有成套的快速反应的高张力张紧装置和双纠偏(CPC)系统,以保证带钢正确喂入轧机,最终 获得更好的辊缝控制和卷取精度。 窜列式轧机由 5 架万能凸度控制轧机(UCM-Mill)组成,自动轧辊更换系统在工作辊 /中间辊换辊时带材可停留在轧 机中,轧机传动系统为工作辊驱动型。 在窜列式轧机的出口设有 1 个转鼓型飞剪、 1 个 carrousel 张力卷取机和 1 个皮带助卷器, 以确保稳定连续的卷取操作, 紧接着的钢卷输出系统由钢卷小车、步进梁式运输机、钢卷称重设备和打捆机组成。 在轧制厚度小于 0.5mm 的产品时,为避免塌卷,将带卷头部轧成较厚的规格。 离线检查站设有 1 个开卷机、1 个检查台,可对带材表面进行离线检查,并可进行表面缺陷的录入、跟踪和追溯,比 如:可检查由于工作辊擦伤带来的带材表面辊印,以确定是哪一架轧机的哪一支辊子产生。 轧机段工艺流程图如下。
1450mm热连轧精轧液压AGC控制系统简介
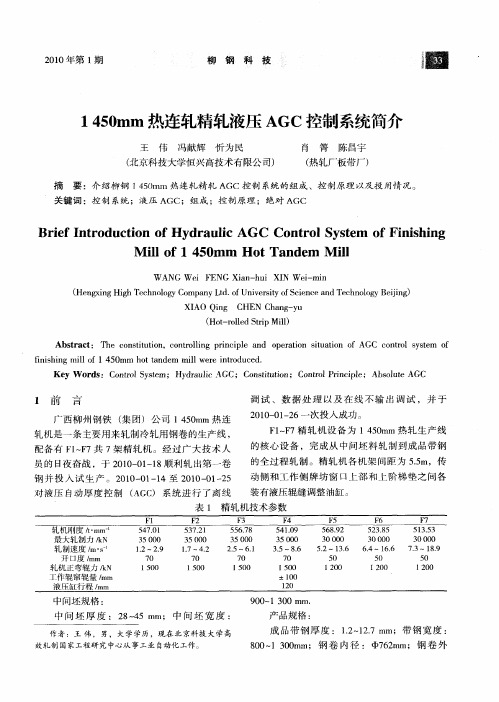
关键 词 :控制 系统 ;液 压 AG C;组 成 ;控 制 原理 ;绝 对 A GC
Bre n r d c i n o d a l ifI t o u to fHy r u i AG C n r lS se fF n s i g c Co t o y t m o i ih n
科 技
2 1 年第 1 00 期
以期 达到 目标 板厚 。在 A C中 , 型 的控制 方式 G 典
是反馈 控制方 式 (IR 。其控制 原理见 图 1 BS A) 。
偏差 调 节量
j
部 ,用 于补 偿 上 支承 辊 和 工作 辊磨 损 后 的位置 变 化 ,减 少 A C 的行 程 ,提 高 轧 机 的控 制 精 G 度 。上 阶梯 垫是 通 过 一个 带 位 置传 感 器 的液 压
21 0 0年第 1 期
柳
钢
科
技
1 5mm 热连轧精轧液压 AGC控制系统简介 0 4
王 伟 冯献辉 忻 为 民 肖 箐 陈 昌宇
( 京科 技大 学恒 兴 高技 术有 限公 司) 北 摘
( 轧厂板 带厂 ) 热
要 :介绍柳 钢 1 5mm 热 连轧精 轧 A 0 4 GC控 制 系统的组 成 、控 制原 理 以及投 用情 况。
柳 钢
径 :ql2 0 m ~ 5 r b 0 r a 20 0 m;最 大卷 重 :2 t a 5 ;钢 卷单 重 :1 . gm ( x。 5 / m ma) 9k 精 轧 压下 厚 度 控制 系 统 包括 上 阶 梯垫 装 置 及 A C系统 。上 阶梯垫 装置 安装 在液 压缸 的下 G
F ~ 7精 轧机 设 备 为 14 0 1F 5 mm热 轧 生 产 线
安钢1550mm冷连轧工程 酸洗段除尘设备投标技术文件
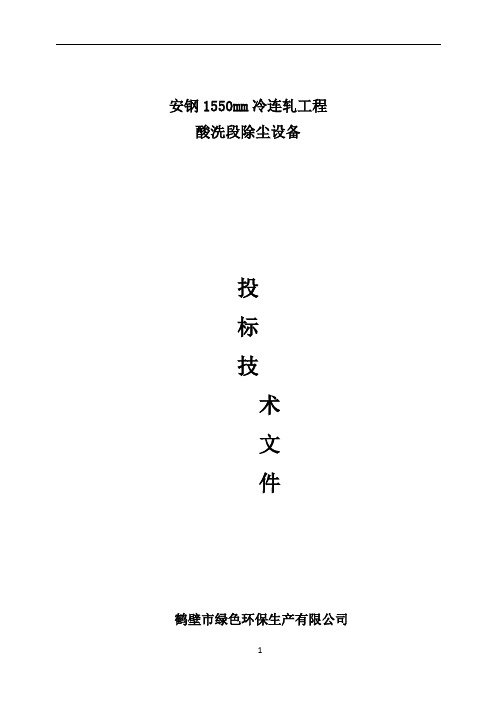
安钢1550mm冷连轧工程酸洗段除尘设备投标技术文件鹤壁市绿色环保生产有限公司2011年7月目录一、概述二、设计原则三、设计、制造、检验、安装及验收标准四、设备技术参数五、除尘器内部气流组织原则六、设备的主要构成及特点七、主要的制作工艺技术说明八、除尘器本体的测量元件与电气控制九、供货、安装范围十、资料交付十一、检验、验收十二、售后服务十三、设备包装、标识、运输方案投标技术文件一、概述安阳钢铁股份有限公司为了更好地满足冷轧板材产品的市场需求,增加公司的经济效益,拟新建1550mm冷轧厂,年产冷轧板材产品120万吨。
新建冷轧厂酸洗段需要二台过滤面积分别为1100、1400㎡的低压脉冲袋式除尘器以及除尘系统的配套设备,与酸连轧生产线中的拉矫机、夹送矫直机等处的捕集尘设施组成一次除尘系统。
安钢冷轧工程指挥部就上述设备组织招投标活动。
鹤壁市绿色环保生产有限公司应招标单位的邀请参加本次招投标。
下面就本公司投标的LCMD-1100型、LCMD-1400两型长袋低压脉冲除尘器与配套设备的技术特点与技术性能进行说明,并对设备设计、制造、安装、供货范围、设备接口、交接界面及技术服务等进行描述。
二、设计原则1、满足招标技术文件中要求的的技术参数值2、耐压强度设计按耐压-10000Pa进行。
并按安阳地区建筑抗震、抗风、抗雪等载荷进行结构设计。
3、除尘器气流组织按低流阻原则进行。
其风道进出口、离线阀等关健部位气流流速按9m/s左右进行设计,烟气流进通道采用圆整降阻技术。
4、除尘器按离线清灰在线检修原则进行设计(同时可在线清灰)。
5、设计制造按招标技术文件的要求执行。
三、设计、制造、检验、安装及验收标准我公司现阶段使用的设计、制造、检验、安装及验收标准如下:我公司现执行的设计、制造、检验、安装及验收标准如与要求执行的标准有出入,以最新标准或高一级标准为准。
四、主要设备技术参数4.1、拉矫机用除尘器1、设备名称:长袋低压脉冲布袋除尘器2、设备型号:LCMD-1100型3、过滤面积:1146m24、处理风量:50310m3/h5、全过滤风速:0.73m/min6、清灰方式:离线(在线)清灰7、烟气温度:≤120℃(长期)≤140℃(瞬时)8、除尘器仓室数:3个9、总脉冲阀数:36个10、仓室进风口规格:1000×50011、入口含尘浓度:≤3g/m312、出口含尘浓度:≤10mg/Nm313、除尘净化效率:>99.8%14、除尘器阻力:≤1500Pa15、滤袋规格:φ130×6000mm16、滤袋数量:468条17、滤袋材质:防水、防油涤纶针刺毡滤料(550g)18、漏风率:≤2%19、喷吹空气压力:0.15~0.25Mpa20、压缩空气气源压力:0.3~0.7Mpa21、除尘器壳体耐压:-10000PaLCMD-1100型除尘器技术设计大纲4.2、夹送矫直机用除尘器1、设备名称:长袋低压脉冲布袋除尘器2、设备型号:LCMD-1400型3、过滤面积:1413m24、处理风量:81500m3/h5、全过滤风速:0.96m/min6、清灰方式:离线(在线)清灰7、烟气温度:≤120℃(长期)≤140℃(瞬时)8、除尘器仓室数:4个9、总脉冲阀数:44个10、仓室进风口规格:1200×60011、入口含尘浓度:≤3g/m312、出口含尘浓度:≤10mg/Nm313、除尘净化效率:>99.8%14、除尘器阻力:≤1500Pa15、滤袋规格:φ130×6000mm16、滤袋数量:572条17、滤袋材质:防水、防油涤纶针刺毡滤料(550g)18、漏风率:≤2%19、喷吹空气压力:0.15~0.25Mpa20、压缩空气气源压力:0.3~0.7Mpa21、除尘器壳体耐压:-10000PaLCMD-1100型除尘器技术设计大纲4.3、螺旋输灰机1)数量:3台(每台除尘器底部一台,集合输灰一台)2)型号:LS315(两台除尘器底部)LS400(集合输灰)3)叶轮直径:315 mm(两台除尘器底部)400 mm(集合螺旋)4)螺旋机长度与输送量:L1=8500mm Q≥18m3/h,L2=10000mm Q≥18 m3/h,L3=14500mm Q≥36m3/h5)驱动电机功率:拉矫机除尘器底部用5.5KW夹送矫直机除尘器底部用7.5KW集合输灰机用11KW螺旋输送机性能参数一览表4.4、斗式提升机1)数量:1台2)型号:TB3153)输送能力:50 m3/h4)提升高度:12 m5)驱动电机功率:11 kW4.5、储灰仓1)数量:1台2)灰仓设计容积:15m33)灰仓设计压力:常压4)灰仓设计温度:常温5)灰仓结构框架:自承式独立结构6)灰仓工作容积:12m37)灰仓直径:Φ2500㎜8)灰仓斗夹角:55度4.6、储灰仓装车系统储灰仓装车系统采用手动插板阀+星型卸灰阀+无尘装车机装车套件1 无尘装车机型号:FZ300a、输送量16—23.5m3/hb、主机功率7.5kWc、垂直送料机功率3kW2 提升机构CD11-1 1台a、起重量1tb、功率3KWc、提升高度6m工作原理:卸灰时,首先将无尘装车机出口降至接近运输车车箱底板处,再开动装车机,打开星形卸灰阀,粉尘通过进料口进入主机输送前移,再通过直管落至卸料车上,逐步形成料堆。
- 1、下载文档前请自行甄别文档内容的完整性,平台不提供额外的编辑、内容补充、找答案等附加服务。
- 2、"仅部分预览"的文档,不可在线预览部分如存在完整性等问题,可反馈申请退款(可完整预览的文档不适用该条件!)。
- 3、如文档侵犯您的权益,请联系客服反馈,我们会尽快为您处理(人工客服工作时间:9:00-18:30)。
1550mm 酸洗轧机联合机组AGC系统组成及改造摘要:本文介绍了马钢(合肥)板材公司1550mm 酸洗轧机联合机组轧机部分辊缝调节机构----AGC系统组成,并对AGC系统单体调试、冷负荷试车、热负荷试车期间发生的故障和事故进行了简要描述,重点介绍了发生事故和故障的原因分析及解决办法。
关键词:AGC 故障改造
马钢(合肥)板材有限责任公司1550mm 酸洗轧机联合机组轧机部分主体由5机架6辊轧机组成。
每台轧机辊缝控制(压下)主要由分别位于轧机操作侧和传动侧牌坊上的AGC液压系统完成。
全线共计10套AGC系统。
1 AGC液压缸组成
AGC液压缸为活塞式,活塞直径Φ760mm,活塞杆直径Φ700mm,最大行程250mm,有效行程245mm,最大轧制力:22000KN,位置阶跃响应时间(达到稳态):25ms(幅值40μ),压下伺服系统响应频率:18-20 Hz(-3db,相移-90ο) ,AGC缸的起动压力0.3 bar,最大工作压力280bar,无位置控制时快速退回:6-8 mm/s,带位置控制时正常调节:2-3 mm/s。
组成:AGC缸本体、磁尺导杆、导杆下降跟随弹簧、导杆与牌坊的连接压盖、磁尺和导杆连接支架、AGC缸行程限位开关等。
2 AGC液压缸阀组
伺服阀块、液控单向阀、溢流阀、换向阀、单向节流阀、压力传感器、控制元件(伺服放大器等)、等元件构成。
伺服阀块安装在缸体外壁上,以减少伺服阀与液压缸之间的管道长度,提高系统响应速度及频率。
压力传感器来监测系统轧制力,对于AGC的内轧制力控制系统提供一个反馈。
3 缸行程检测-p(4)AGC系统在master off 情况下,4#轧机DS侧自行下降,压坏中间辊平衡缸;
(5)2#和5#轧机DS侧磁尺弯曲。
5 问题分析及改善和改造
(1)通过对PLC程序的相关数值的跟踪和现场实验分析,发现发生2#轧机和4#轧机DS侧AGC缸下降,但是位置反馈不变的主要原因是:AGC缸下降,安装磁尺的导杆不下降,从而磁尺没有检测出液压缸的下降行程。
主要是因为AGC缸和牌坊上磁尺导杆的导向孔同心度不好,这样导致导向杆在AGC缸中导向孔内侧面摩擦加大,抵消了弹簧对导向杆的向下推动跟随力。
改造方法:将导向杆与AGC 缸接触的300mm长部位的直径为40mm加工到38mm,改造后此故障解决。
为避免其他导杆也存在类似问题,将1~3架其他4根导杆都进行了加工处理,4~5架的4根导杆将在合适的时间进行改造。
(2)2#轧机WS侧和5号DS侧AGC缸下降,磁尺有相应的反馈,但数值跳跃,线性度不好现象。
经分析只有两种可能:一是伺服阀的开度线性度不好,二是磁尺的磁杆部分有损坏。
经现场分析和试验发现伺服阀没问题,是由于安装单位在安装过程中用砂纸打磨了磁尺磁杆,导致磁杆局部磁性损坏。
更换新磁杆后故障解决。
(3)AGC缸在系统master on(工作准备)状态下,3机架WS 侧突然大幅度下降,将工作辊换辊轨道压坏。
经分析master on时的跟踪曲线和试验发现,master on时的AGC自检1mm时,AGC缸动作,但磁尺未检测到此动作,因此控制系统不断增加伺服阀的开度,导致WS侧AGC缸快速下降,从而使工作辊换辊轨道承受300吨轧制力而受损坏,可以肯定造成事故主要原因仍然和问题1类似,但可以排除问题出现在问题1的部位。
经在现场处理发现,是牌坊固定导杆面加工尺寸出现问题,加工面倾斜0.3mm,导致磁尺导杆倾斜,增加了导向杆在AGC缸中导向孔内侧面摩擦力。
处理方法:现场测绘牌坊固定导杆连接面尺寸偏差,通过增加垫片的方式保证该连接面的水平,从而解决了此次故障。
(4)AGC系统在master off 情况下,4#轧机DS侧自行下降,压坏中间辊平衡缸。
所谓master off就是AGC检修或者长时间停机情况下,AGC缸退回原始位。
为了找出该事故原因,在现场做了大量的试验,但仍然未找到。
为了防止这种事故的再次发生,采取了以下处理方案:首先在HMI上增加AGC缸的工作模式选择(维护模式
和工作模式);其次修改AGC控制程序,在维护模式下将AGC的快抬卸油阀一直得电,通过实验观察检验此改造方案解决了该问题;最后,修改操作规程,要求操作人员在轧机AGC检修或者长时间停机情况下将AGC缸的工作模式选择为维护模式。
对于该故障的根本原因,将在后期的调试和生产过程中进行查找和解决。
(5)对于在调试过程中发现2#和5#轧机DS侧磁尺弯曲事故。
经现场跟踪和分析发现磁尺弯曲发生在AGC缸抬开过程中,主要是由于磁尺安装时未按照要求将非固定端保证540mm,导致在AGC缸下降后磁尺顶端离开磁尺导槽,在磁尺上升时磁尺偏离导槽而被挤弯,在更换备件后正常。
针对该事故,对所有其他8个磁尺安装情况进行了检查和调整,避免了事故的再次发生。
6 结语
通过对故障和事故现象的正确分析和相应的测试实验,加深了对AGC系统的机械、电气和液压系统的理解。
同时,也避免了因AGC 系统发生故障而造成对轧机内设备的损坏,减小了操作和维护工作量,提高了设备作业量,降低了设备维护成本,保证率产品质量。
参考文献
[1] 宁霞,李洪鑫. 热连轧中AGC控制系统的研究与应用[J]. 可编程控制器与工厂自动化. 2006(12)
[2] 李维芳. 我国钢铁行业现状分析与发展方向探索[J]. 经济问题探索. 2004(12)。