PTA装置腐蚀与防护分析
PTA加氢反应器腐蚀风险及有效防范

工厂会使用板焊材料代替。
在这之后,PTA 加氢反应器也在不断发展,人们会基于检查当中发生的问题来进行完善,对反应器的结构进行优化、对其材料进行改进,这使PTA 加氢反应器能够在特殊的环境下使用,使用寿命不断延长、使用效果也不断增强。
2 PTA加氢反应器腐蚀风险2.1 PTA加氢反应器腐蚀机理当加氢反应器处于正常运行条件下的时候,对甲基二甲酸中醋酸与溴离子的浓度都是比较低的,这对加氢反应器衬里的腐蚀也并不严重。
但当溶液当中的卤素离子即溴离子与氯离子质量浓度超过了一定的门槛值之后,就会对加氢反应器奥氏体不锈钢产生点蚀作用。
在实际PTA 反应的过程当中,虽然介质当中卤素离子的浓度比较低,但是在反应过程当中会由于蒸发、沉积等导致离子在加氢反应器的垢下、缝隙等特殊部位产生高浓度沉积,形成一个酸性的环境,进而对加氢反应器的内部产生点坑腐蚀。
尤其是在气液交界处,溶液与氢气都呈翻腾的状态,如果出现溶液阻塞或者偏流问题的话,氢气、对苯二酸钾溶液以及钯炭催化剂这三者所形成的混合物就会产生剧烈的翻腾,不仅会对加氢反应器产生严重的冲刷,同时还会在局部形成气蚀环境,引起对材料的空泡腐蚀,导致加氢反应器内壁的不锈钢材料被破坏,进而腐蚀到材料的内部。
在这之后,腐蚀所形成的孔洞就会吸收溶液当中的卤素离子,使溴离子和氯离子在电泳的作用下自发地向孔洞处移动,进而导致腐蚀日益严重,最终使加氢反应器的衬里材料完全被穿透。
2.2 PTA加氢反应器腐蚀风险如果PTA 加氢反应器遭到腐蚀,就可能会产生一定的风险。
这会导致加氢反应器内衬的材料被彻底地暴露出来,由于内部的碳钢基材在被腐蚀的过程当中并不会发生“自催化”的问题,因此不会在表面处形成比较深和比较明显的坑洞,这种腐蚀并不严重,造成氢气泄漏的可能性也是比较小的。
在实践当中发现,即使加氢反应器的整个衬里完全地被腐蚀掉,对PTA 加氢反应器使用的安全性也并不会产生明显的影响。
因此,在发现加氢反应器的衬里出现穿透腐蚀问题的话,工作人员只需要做好相应的修复,就可以将介质与基材相互隔离,以此来确保加氢反应器整个壳体的安全性。
浅析连续重整装置预处理系统的腐蚀与防护分析

浅析连续重整装置预处理系统的腐蚀与防护分析连续重整装置预处理系统在工业生产中扮演着非常重要的角色,它们用于处理原材料、中间产品和成品,以确保产品质量和生产效率。
这些预处理系统经常受到腐蚀的影响,如果不得当地进行防护分析和腐蚀控制,将会带来严重的后果。
本文将对连续重整装置预处理系统的腐蚀与防护进行分析,为工业生产提供参考和指导。
一、腐蚀的原因分析连续重整装置预处理系统面临着多种腐蚀的危险,主要原因可以归结为以下几点:1. 化学腐蚀:各种化学品在高温、高压条件下容易发生腐蚀作用,而连续重整装置预处理系统中往往使用的就是这类化学品。
2. 电化学腐蚀:系统中存在不同金属之间的接触,在受到潮湿、腐蚀性气体和液体的作用下,会形成电池,导致电化学腐蚀的发生。
3. 热蚀刻蚀:高温、高压条件下,金属表面可能产生热蚀刻蚀现象,加速金属的腐蚀速度。
4. 磨擦腐蚀:系统中存在运动部件,当摩擦副受到化学环境的影响时,会出现磨擦腐蚀现象。
二、防护分析针对连续重整装置预处理系统的腐蚀问题,我们可以采取以下几种防护措施:1. 材料选择:首先要选择耐蚀材料,比如不锈钢、镍基合金等,以减少系统受到腐蚀的影响。
2. 表面处理:采用表面镀层、喷涂等方法,提高金属的耐蚀性。
3. 防护层:在系统表面形成一层防护膜,阻隔化学物质对金属的腐蚀作用。
4. 控制环境:控制系统内部的温度、湿度、气体浓度等环境因素,减少腐蚀的发生。
5. 定期检测:对系统进行定期的腐蚀检测,及时发现问题并进行修复。
三、案例分析某企业的连续重整装置预处理系统遇到了严重的腐蚀问题,导致生产效率下降、产品质量不稳定。
经过对系统的腐蚀和防护进行分析后,采取了以下措施:1. 更换材料:对受腐蚀严重的部件进行了材料更换,选用了耐蚀性更好的不锈钢材料。
通过这些措施的实施,该企业的连续重整装置预处理系统的腐蚀问题得到了有效的控制,生产效率和产品质量得到了提升。
四、结论连续重整装置预处理系统的腐蚀问题是一个需要高度重视的工业生产难题,但通过科学的分析和有效的防护措施,这一问题是可以得到有效控制的。
PTA装置说明、危险因素和防范措施

PTA装置说明、危险因素和防范措施PTA装置的基本概念和结构PTA装置(Percutaneous Transluminal Angioplasty Device),也称为经皮经血管内开放性血管成形术装置。
PTA装置主要由导丝、导管、球囊、支架等部分组成。
其中,导丝主要用于准确定位,导管则是穿透皮肤和血管的介质,而球囊和支架则是治疗器械的重要部分。
PTA装置的使用方法1.术前检查:通过体格检查、影像学检查等方式确定患者的病情,同时对患者的身体状况、过敏史等进行评估。
2.麻醉:根据需要,在局部麻醉、全身麻醉等方面进行选择。
3.穿刺:用导丝指引导管插至患者动脉处。
4.膨胀球囊:将球囊插入狭窄血管内部,然后将球囊逐步膨胀。
5.放置支架:根据病情需要,将支架放置于血管内部。
6.术前整理:完成治疗后,进行伤口处理、检查等工作,确保治疗效果和安全性。
PTA装置使用过程中的危险因素1.内膜损伤:手术操作不当可能导致血管内壁受损,引起出血、血块等问题。
2.血管远端栓塞:球囊膨胀的过程中,可能会将血管内壁软化、释放出血块,进一步形成栓塞。
3.支架脱落:安装支架时,如果操作不当、位置不准确,可能导致支架脱落等问题。
4.手术前后感染:穿刺、手术前后处理不当,可能会导致伤口感染等问题。
PTA装置使用过程中的安全措施1.术前评估:针对患者个体差异性,根据病情和患者身体状况进行评估,确保操作安全。
2.术中监测:术中对患者的心电图、血压、脉搏等进行监测,及时发现异常情况并处理。
3.操作标准化:对操作流程、技术等方面进行规范化管理,确保操作安全。
4.术后护理:对术后伤口进行规范化护理,防止伤口感染等问题的发生。
总结通过以上阐述可知,PTA装置在临床应用中起到了重要的作用。
然而,在操作过程中存在一些潜在的危险因素。
因此,医生在使用PTA装置时需要结合个体化因素、病情综合评估,避免存在的危险因素,并在操作过程中采取有效的安全措施,确保患者的安全和治疗效果。
PTA装置说明、危险因素和防范措施
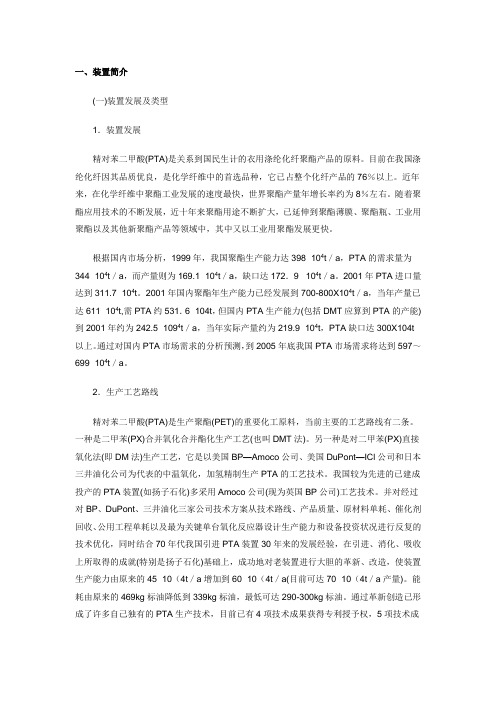
一、装置简介(一)装置发展及类型1.装置发展精对苯二甲酸(PTA)是关系到国民生计的衣用涤纶化纤聚酯产品的原料。
目前在我国涤纶化纤因其品质优良,是化学纤维中的首选品种,它已占整个化纤产品的76%以上。
近年来,在化学纤维中聚酯工业发展的速度最快,世界聚酯产量年增长率约为8%左右。
随着聚酯应用技术的不断发展,近十年来聚酯用途不断扩大,已延伸到聚酯薄膜、聚酯瓶、工业用聚酯以及其他新聚酯产品等领域中,其中又以工业用聚酯发展更快。
根据国内市场分析,1999年,我国聚酯生产能力达398×104t/a,PTA的需求量为344×104t/a,而产量则为169.1×104t/a,缺口达172.9× 104t/a。
2001年PTA进口量达到311.7×104t。
2001年国内聚酯年生产能力已经发展到700-800X104t/a,当年产量已达611×104t,需PTA约531.6×104t,但国内PTA生产能力(包括DMT应算到PTA的产能)到2001年约为242.5×1094t/a,当年实际产量约为219.9×104t,PTA缺口达300X104t 以上。
通过对国内PTA市场需求的分析预测,到2005年底我国PTA市场需求将达到597~699×104t/a。
2.生产工艺路线精对苯二甲酸(PTA)是生产聚酯(PET)的重要化工原料,当前主要的工艺路线有二条。
一种是二甲苯(PX)合并氧化合并酯化生产工艺(也叫DMT法)。
另一种是对二甲苯(PX)直接氧化法(即DM法)生产工艺,它是以美国BP—Amoco公司、美国DuPont—ICl公司和日本三井油化公司为代表的中温氧化,加氢精制生产PTA的工艺技术。
我国较为先进的已建成投产的PTA装置(如扬子石化)多采用Amoco公司(现为英国BP公司)工艺技术。
并对经过对BP、DuPont、三井油化三家公司技术方案从技术路线、产品质量、原材料单耗、催化剂回收、公用工程单耗以及最为关键单台氧化反应器设计生产能力和设备投资状况进行反复的技术优化,同时结合70年代我国引进PTA装置30年来的发展经验,在引进、消化、吸收上所取得的成就(特别是扬子石化)基础上,成功地对老装置进行大胆的革新、改造,使装置生产能力由原来的45×10(4t/a增加到60×10(4t/a(目前可达70×10(4t/a产量)。
PTA装置说明、危险因素和防范措施

PTA装置说明、危险因素和防范措施⼀、装置简介(⼀)装置发展及类型1.装置发展精对苯⼆甲酸(PTA)是关系到国民⽣计的⾐⽤涤纶化纤聚酯产品的原料。
⽬前在我国涤纶化纤因其品质优良,是化学纤维中的⾸选品种,它已占整个化纤产品的76%以上。
近年来,在化学纤维中聚酯⼯业发展的速度最快,世界聚酯产量年增长率约为8%左右。
随着聚酯应⽤技术的不断发展,近⼗年来聚酯⽤途不断扩⼤,已延伸到聚酯薄膜、聚酯瓶、⼯业⽤聚酯以及其他新聚酯产品等领域中,其中⼜以⼯业⽤聚酯发展更快。
根据国内市场分析,1999年,我国聚酯⽣产能⼒达398×104t/a,PTA的需求量为344×104t/a,⽽产量则为169.1×104t/a,缺⼝达172.9× 104t/a。
2001年PTA进⼝量达到311.7×104t。
2001年国内聚酯年⽣产能⼒已经发展到700-800X104t/a,当年产量已达611×104t,需PTA约531.6×104t,但国内PTA⽣产能⼒(包括DMT应算到PTA的产能)到2001年约为242.5×1094t/a,当年实际产量约为219.9×104t,PTA缺⼝达300X104t 以上。
通过对国内PTA市场需求的分析预测,到2005年底我国PTA市场需求将达到597~699×104t/a。
2.⽣产⼯艺路线精对苯⼆甲酸(PTA)是⽣产聚酯(PET)的重要化⼯原料,当前主要的⼯艺路线有⼆条。
⼀种是⼆甲苯(PX)合并氧化合并酯化⽣产⼯艺(也叫DMT法)。
另⼀种是对⼆甲苯(PX)直接氧化法(即DM法)⽣产⼯艺,它是以美国BP—Amoco公司、美国DuPont—ICl公司和⽇本三井油化公司为代表的中温氧化,加氢精制⽣产PTA的⼯艺技术。
我国较为先进的已建成投产的PTA装置(如扬⼦⽯化)多采⽤Amoco公司(现为英国BP公司)⼯艺技术。
PTA装置干燥机加热管腐蚀原因与防护措施
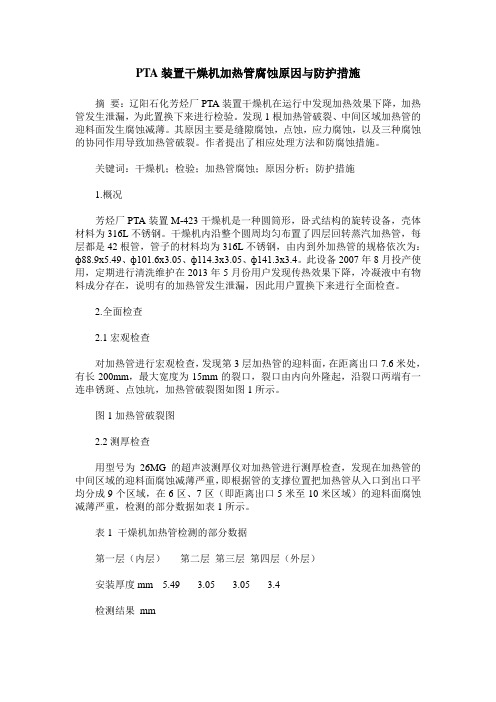
PTA装置干燥机加热管腐蚀原因与防护措施摘要:辽阳石化芳烃厂PTA装置干燥机在运行中发现加热效果下降,加热管发生泄漏,为此置换下来进行检验。
发现1根加热管破裂、中间区域加热管的迎料面发生腐蚀减薄。
其原因主要是缝隙腐蚀,点蚀,应力腐蚀,以及三种腐蚀的协同作用导致加热管破裂。
作者提出了相应处理方法和防腐蚀措施。
关键词:干燥机;检验;加热管腐蚀;原因分析;防护措施1.概况芳烃厂PTA装置M-423干燥机是一种圆筒形,卧式结构的旋转设备,壳体材料为316L不锈钢。
干燥机内沿整个圆周均匀布置了四层回转蒸汽加热管,每层都是42根管,管子的材料均为316L不锈钢,由内到外加热管的规格依次为:ф88.9х5.49、ф101.6х3.05、ф114.3х3.05、ф141.3х3.4。
此设备2007年8月投产使用,定期进行清洗维护在2013年5月份用户发现传热效果下降,冷凝液中有物料成分存在,说明有的加热管发生泄漏,因此用户置换下来进行全面检查。
2.全面检查2.1宏观检查对加热管进行宏观检查,发现第3层加热管的迎料面,在距离出口7.6米处,有长200mm,最大宽度为15mm的裂口,裂口由内向外隆起,沿裂口两端有一连串锈斑、点蚀坑,加热管破裂图如图1所示。
图1加热管破裂图2.2测厚检查用型号为26MG的超声波测厚仪对加热管进行测厚检查,发现在加热管的中间区域的迎料面腐蚀减薄严重,即根据管的支撑位置把加热管从入口到出口平均分成9个区域,在6区、7区(即距离出口5米至10米区域)的迎料面腐蚀减薄严重,检测的部分数据如表1所示。
表1 干燥机加热管检测的部分数据第一层(内层)第二层第三层第四层(外层)安装厚度mm 5.49 3.05 3.05 3.4检测结果mm(6区、7区的迎料面) 1.97 2.132.81 2.89 1.52 1.571.26 1.42 1.89 1.631.31 0.822.13 2.822.903.21材质316L 316L 316L 316L3.腐蚀原因分析主要是缝隙腐蚀;点蚀;应力腐蚀。
PTA装置腐蚀分析及对策探讨

A b s t r a c t : T h e c o r r o s i o n o f s e v e r a l m a j o r e q u i p m e n t s o f P T A p l a n t w a s i n t r o d u c e d . B y a n a l y z i n g t h e c a u s e s o f c o r r o -
从而减轻对尾气用户的腐蚀。 ( 3 ) 稳定生产 , 避免大幅度调节操作参数 , 减少 设 备及 管道受 到热 应力 和交变 应力 的作用 。 ( 4 ) 减少设备 的 高温碱洗 次数。控制碱 洗温 度、 碱洗频率及碱液浓度 , 减轻对设备的腐蚀。 ( 5 ) 在脱离子水罐 、 循环水管线上安装在线 p H 值监测仪 , p H值超过设定参数时 , 及时查找原因 , 加 大排污 , 补充合格水。 ( 6 ) 加强巡 检监 护, 发现腐蚀、 泄漏部位 , 及 时
2 0 0 9 , 2 4 ( 9) : 3 2 - 3 4 .
钛材 、 碳钢衬聚四氟乙烯代替不锈钢材质以及容器 内壁镀 钯 等技 术 , 并 取 得 较好 的效 果 。 在 长期 生 产
Co r r o s i o n a n a l y s i s a nd a nt i c o r r o s i o n d i s c u s s i o n o f PTA pl a n t
ZHAN Yo n g — he, YI N Yu n— h u a
( C h e mi c a l F i b e r F a c t o r y , C N P C U r u m q i P e t r o c h e m i c a l C o m p a n y ,U r u m q i 8 3 0 0 1蚀率。 ( 4 ) 浓度 的影 响 。当乙酸 的质量 分数 升 至 8 5 % 以上 时 , 有较 大腐蚀 性 。
浅谈PTA加氢反应器腐蚀风险及有效防范
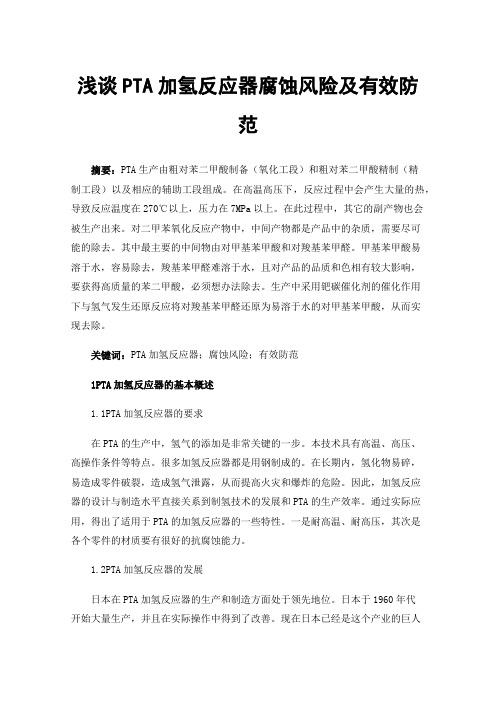
浅谈PTA加氢反应器腐蚀风险及有效防范摘要:PTA生产由粗对苯二甲酸制备(氧化工段)和粗对苯二甲酸精制(精制工段)以及相应的辅助工段组成。
在高温高压下,反应过程中会产生大量的热,导致反应温度在270℃以上,压力在7MPa以上。
在此过程中,其它的副产物也会被生产出来。
对二甲苯氧化反应产物中,中间产物都是产品中的杂质,需要尽可能的除去。
其中最主要的中间物由对甲基苯甲酸和对羧基苯甲醛。
甲基苯甲酸易溶于水,容易除去,羧基苯甲醛难溶于水,且对产品的品质和色相有较大影响,要获得高质量的苯二甲酸,必须想办法除去。
生产中采用钯碳催化剂的催化作用下与氢气发生还原反应将对羧基苯甲醛还原为易溶于水的对甲基苯甲酸,从而实现去除。
关键词:PTA加氢反应器;腐蚀风险;有效防范1PTA加氢反应器的基本概述1.1PTA加氢反应器的要求在PTA的生产中,氢气的添加是非常关键的一步。
本技术具有高温、高压、高操作条件等特点。
很多加氢反应器都是用钢制成的。
在长期内,氢化物易碎,易造成零件破裂,造成氢气泄露,从而提高火灾和爆炸的危险。
因此,加氢反应器的设计与制造水平直接关系到制氢技术的发展和PTA的生产效率。
通过实际应用,得出了适用于PTA的加氢反应器的一些特性。
一是耐高温、耐高压,其次是各个零件的材质要有很好的抗腐蚀能力。
1.2PTA加氢反应器的发展日本在PTA加氢反应器的生产和制造方面处于领先地位。
日本于1960年代开始大量生产,并且在实际操作中得到了改善。
现在日本已经是这个产业的巨人了。
在应用的早期,PTA加氢反应器是以多种高强度的材料为主。
外层一般用铬钼钢板制造,而内层用不锈钢制造。
尽管这种反应器可以达到生产的要求,但是它不能通过超声波探测来探测其内部的问题,从而增加了它的安全性。
20世纪七十年代,采用了锻压和焊接结构,取代了传统的钢板,有些厂家采用了钢板焊接。
从那时起,PTA加氢反应器就一直在发展,并针对存在的问题进行改进,包括对反应器的结构和材质的优化,以保证PTA加氢反应器在特定的环境下运行,使其寿命和运行效率得到了进一步的改善。
《石油炼制常减压装置腐蚀与防腐》范文
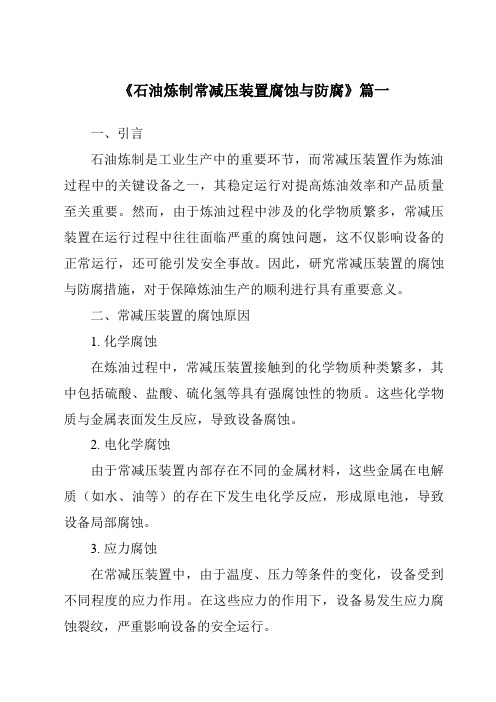
《石油炼制常减压装置腐蚀与防腐》篇一一、引言石油炼制是工业生产中的重要环节,而常减压装置作为炼油过程中的关键设备之一,其稳定运行对提高炼油效率和产品质量至关重要。
然而,由于炼油过程中涉及的化学物质繁多,常减压装置在运行过程中往往面临严重的腐蚀问题,这不仅影响设备的正常运行,还可能引发安全事故。
因此,研究常减压装置的腐蚀与防腐措施,对于保障炼油生产的顺利进行具有重要意义。
二、常减压装置的腐蚀原因1. 化学腐蚀在炼油过程中,常减压装置接触到的化学物质种类繁多,其中包括硫酸、盐酸、硫化氢等具有强腐蚀性的物质。
这些化学物质与金属表面发生反应,导致设备腐蚀。
2. 电化学腐蚀由于常减压装置内部存在不同的金属材料,这些金属在电解质(如水、油等)的存在下发生电化学反应,形成原电池,导致设备局部腐蚀。
3. 应力腐蚀在常减压装置中,由于温度、压力等条件的变化,设备受到不同程度的应力作用。
在这些应力的作用下,设备易发生应力腐蚀裂纹,严重影响设备的安全运行。
三、常减压装置的防腐措施1. 材料选择选用具有良好耐腐蚀性的材料是防止设备腐蚀的有效措施。
例如,可以采用不锈钢、钛合金等耐腐蚀金属材料制造常减压装置的关键部件。
此外,还可以采用非金属材料,如塑料、玻璃等,以增强设备的耐腐蚀性。
2. 表面处理对常减压装置的金属表面进行喷砂、喷涂等处理,可以增强设备的抗腐蚀性能。
例如,喷涂防腐涂料可以形成一层保护膜,隔绝设备与腐蚀性物质的接触。
此外,还可以采用电镀、热浸镀等方法对设备表面进行金属涂层处理,以提高设备的耐腐蚀性。
3. 工艺控制通过优化炼油工艺,降低常减压装置中腐蚀性物质的含量,可以有效减轻设备的腐蚀程度。
例如,可以调整原料油的酸碱度、降低硫化氢的含量等措施来降低设备的腐蚀风险。
此外,还可以采用先进的工艺技术,如催化裂化、加氢裂化等,减少有害物质的生成。
4. 定期检查与维护定期对常减压装置进行检查和维护,及时发现并处理设备的腐蚀问题,是保证设备正常运行的重要措施。
浅析连续重整装置预处理系统的腐蚀与防护分析

浅析连续重整装置预处理系统的腐蚀与防护分析连续重整装置预处理系统在工业生产中起着非常重要的作用,其中腐蚀与防护分析更是不可忽视的一环。
本文将从腐蚀产生的原因、对设备的影响以及防护措施等方面进行浅析,希望对工程技术人员有所帮助。
一、腐蚀产生的原因1.1 环境因素环境因素是导致金属腐蚀的主要原因之一。
比如在化工生产过程中,有很多介质是具有腐蚀性的,如硫化氢、氨气、氯化氢等,这些介质会对金属材料产生腐蚀作用。
1.2 操作条件操作条件也是影响腐蚀的重要因素之一。
比如温度、压力等操作条件对金属设备的腐蚀影响很大。
高温、高压环境下金属材料容易产生腐蚀。
1.3 金属材料金属材料的质量、种类、合金成分等也是影响腐蚀产生的原因。
一些不锈钢、合金钢、耐腐蚀合金等金属材料具有一定的防腐性能,但如果选择不当或者材料质量不过关,也容易产生腐蚀。
1.4 化学因素除了环境、操作条件和金属材料之外,化学因素也是引起腐蚀的重要原因。
比如化学反应、离子浓度、酸碱性等化学因素都会影响金属材料的腐蚀过程。
二、对设备的影响2.1 设备寿命腐蚀会直接影响设备的寿命,加速设备的老化和损坏。
在连续重整装置预处理系统中,各种设备都可能受到腐蚀的侵蚀,包括反应器、换热器、管道、泵阀等设备。
2.2 设备性能腐蚀还会降低设备的性能,影响工艺的稳定性和安全性,甚至引起生产事故。
腐蚀会导致设备表面粗糙度增加、泄漏、磨损等问题,从而影响设备的正常运行。
2.3 经济损失腐蚀不仅会增加设备的维护成本,还可能导致生产中断、产品质量下降、能源消耗增加等问题,给企业带来巨大的经济损失。
三、防护措施3.1 选择合适的材料在设计和选择设备材料时,应根据腐蚀环境和工艺要求,选择适合的材料,如不锈钢、耐腐蚀合金等,以提高设备的抗腐蚀性能。
3.2 表面涂层采用表面涂层技术对设备进行防护,如在金属表面涂覆一层防腐蚀的涂层,可以有效地延长设备的使用寿命。
3.3 防腐措施在工艺设计和操作中尽量采取防腐措施,如控制介质的浓度、温度、压力,减少介质对设备的腐蚀作用。
浅谈PTA装置尾气系统设备的腐蚀和防护
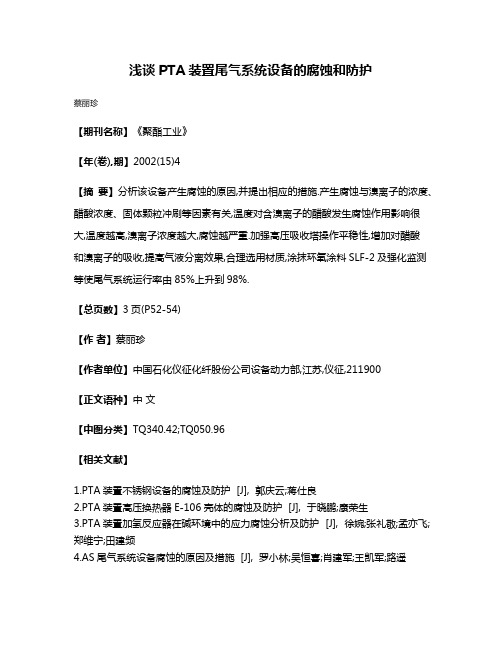
浅谈PTA装置尾气系统设备的腐蚀和防护
蔡丽珍
【期刊名称】《聚酯工业》
【年(卷),期】2002(15)4
【摘要】分析该设备产生腐蚀的原因,并提出相应的措施.产生腐蚀与溴离子的浓度、醋酸浓度、固体颗粒冲刷等因素有关,温度对含溴离子的醋酸发生腐蚀作用影响很大,温度越高,溴离子浓度越大,腐蚀越严重.加强高压吸收塔操作平稳性,增加对醋酸
和溴离子的吸收,提高气液分离效果,合理选用材质,涂抹环氧涂料SLF-2及强化监测等使尾气系统运行率由85%上升到98%.
【总页数】3页(P52-54)
【作者】蔡丽珍
【作者单位】中国石化仪征化纤股份公司设备动力部,江苏,仪征,211900
【正文语种】中文
【中图分类】TQ340.42;TQ050.96
【相关文献】
1.PTA装置不锈钢设备的腐蚀及防护 [J], 郭庆云;蒋仕良
2.PTA装置高压换热器E-106壳体的腐蚀及防护 [J], 于晓鹏;康荣生
3.PTA装置加氢反应器在碱环境中的应力腐蚀分析及防护 [J], 徐婉;张礼敬;孟亦飞;郑维宁;田建频
4.AS尾气系统设备腐蚀的原因及措施 [J], 罗小林;吴恒喜;肖建军;王凯军;路遥
5.PTA装置中冷凝器壳体腐蚀原因分析及防护对策 [J], 张亚明;李美栓;韩成林;马彦忱
因版权原因,仅展示原文概要,查看原文内容请购买。
PTA装置中结晶罐发生应力腐蚀的原因分析
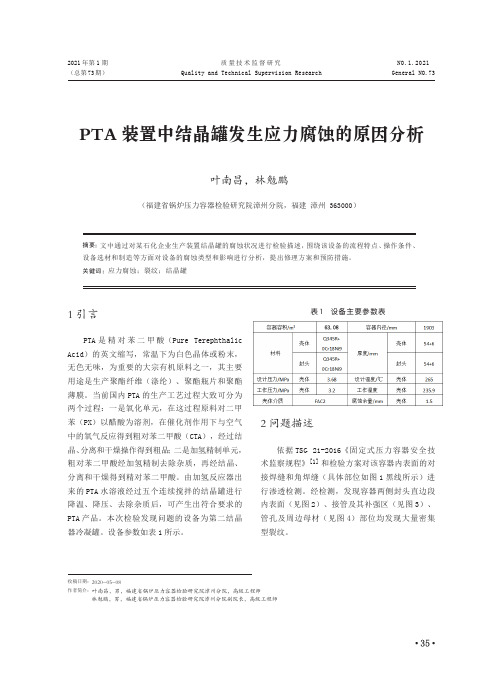
2问题描述依据TSG 21-2016《固定式压力容器安全技术监察规程》[1]和检验方案对该容器内表面的对3.3裂纹微观形态分析3.2腐蚀产物分析左封头正常组织为奥氏体+析出物+形变马氏体,从图6上可以看到晶界已被腐蚀,奥氏体晶界有碳化物析出,且部分碳化物以颗粒状形式在晶界上聚集,并呈现连续的网格状,但晶粒本身未被腐蚀,说明裂纹由材料内部向外表面扩展。
从图7上可以看出,封头与筒体热影响区的金相组织为奥氏体和δ-铁素体;晶界同样被腐蚀,且析出碳化物同样聚集在奥氏体晶界,裂纹呈现沿晶、穿晶扩展两种特征。
由图8可知,筒体母材裂纹处的金相组织为奥氏体、析出物和少量变形马氏体,裂纹也呈沿晶扩展特征。
综合上述金相组织分析,奥氏体晶粒本身未被腐蚀,但晶界有明显腐蚀,同时有碳化物析出,并有少量的碳化物以颗粒状分布于晶粒上,有几处能看到晶粒脱落的凹坑和晶粒脱落。
裂纹呈沿晶分布,在热影响区少量伴有穿晶现象,裂纹源由材料内部向外表面扩展[2]。
4 产生裂纹原因分析根据对材料的腐蚀产物元素分析和金相分析结果可知,该复合板材料的内表面产生了应力腐蚀。
应力腐蚀的产生需要有三个必要条件:一是敏感的金属材料;二是特定的腐蚀介质;三是足够大的拉伸应力。
根据表1所示,该容器的封头材料为Q345R+0Cr18Ni9复合钢板,其中Q345R为容器提供强度,0Cr18Ni9为容器提供防腐蚀作用。
但由于0Cr18Ni9属于非稳定态,常温时碳在奥氏体中的溶解度很小,远低于它的实际含碳量,故而过饱和的碳被固溶在奥氏体中。
查阅相关资料显示奥氏体不锈钢(0Cr18Ni9)在加热温度超过425℃并停留一段时间时,钢中过饱和碳就不断地向奥氏体晶粒边界扩散,与铬元素结合,在晶间形成碳化铬的化合物,这使得晶间形成贫铬区[3]。
这种现象称为敏化作用。
该容器封头制造过程通过960℃热压成型,同时容器整体制造后又进行620℃的消应力热处理,说明该容器的不锈钢材料在制造过程中会发生敏化作用倾向。
《石油炼制常减压装置腐蚀与防腐》
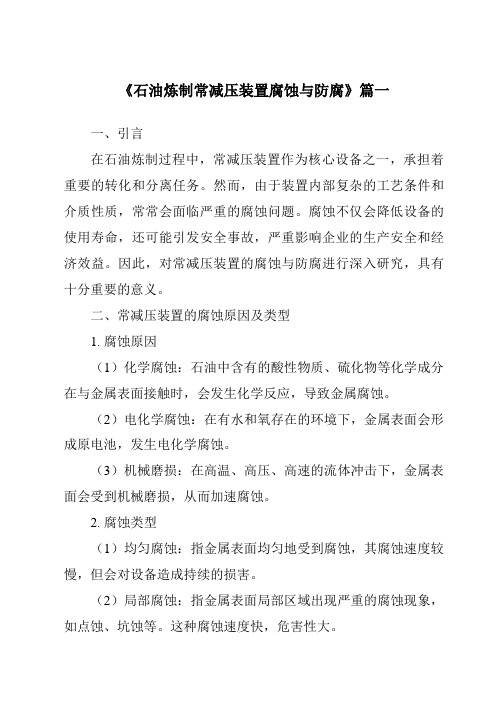
《石油炼制常减压装置腐蚀与防腐》篇一一、引言在石油炼制过程中,常减压装置作为核心设备之一,承担着重要的转化和分离任务。
然而,由于装置内部复杂的工艺条件和介质性质,常常会面临严重的腐蚀问题。
腐蚀不仅会降低设备的使用寿命,还可能引发安全事故,严重影响企业的生产安全和经济效益。
因此,对常减压装置的腐蚀与防腐进行深入研究,具有十分重要的意义。
二、常减压装置的腐蚀原因及类型1. 腐蚀原因(1)化学腐蚀:石油中含有的酸性物质、硫化物等化学成分在与金属表面接触时,会发生化学反应,导致金属腐蚀。
(2)电化学腐蚀:在有水和氧存在的环境下,金属表面会形成原电池,发生电化学腐蚀。
(3)机械磨损:在高温、高压、高速的流体冲击下,金属表面会受到机械磨损,从而加速腐蚀。
2. 腐蚀类型(1)均匀腐蚀:指金属表面均匀地受到腐蚀,其腐蚀速度较慢,但会对设备造成持续的损害。
(2)局部腐蚀:指金属表面局部区域出现严重的腐蚀现象,如点蚀、坑蚀等。
这种腐蚀速度快,危害性大。
三、常减压装置的防腐措施1. 材料选择:选用耐腐蚀、耐高温、耐高压的金属材料,如不锈钢、合金钢等,以降低设备的腐蚀速度。
2. 表面处理:对金属表面进行喷涂、镀层等处理,形成一层保护膜,隔绝介质与金属的接触,从而达到防腐的目的。
3. 工艺控制:通过优化工艺参数,如温度、压力、流速等,减少设备内部介质的腐蚀性。
同时,定期对设备进行清洗和检查,及时发现并处理腐蚀问题。
4. 添加缓蚀剂:在石油中添加缓蚀剂,可以降低介质的腐蚀性,减缓设备的腐蚀速度。
5. 阴极保护:通过使金属设备成为阴极,减少或避免电化学腐蚀的发生。
这种方法常用于大型设备和管道的防腐。
四、实例分析以某石油炼厂为例,该厂常减压装置采用不锈钢材料和合金钢材料制作,同时对设备进行了喷涂和镀层处理。
此外,还通过优化工艺参数、定期清洗和检查设备、添加缓蚀剂等方法来降低设备的腐蚀速度。
经过一系列防腐措施的实施,该厂常减压装置的使用寿命得到了显著提高,减少了维修和更换设备的成本和时间。
PTA装置氧化干燥机壳体腐蚀及对策
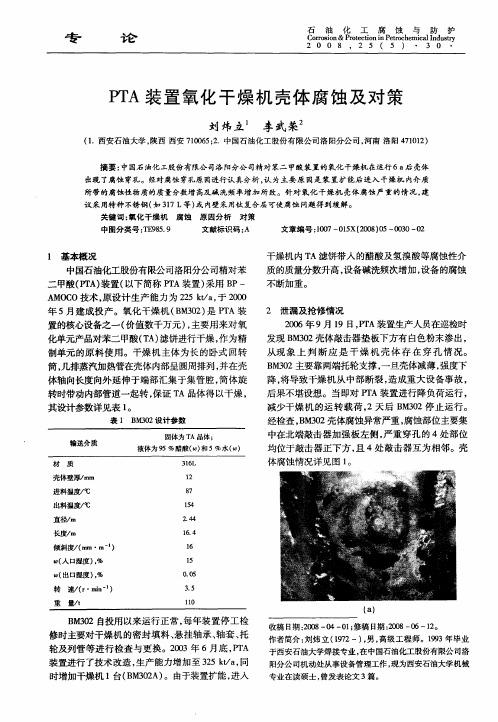
20 06年 9月 1 9日,T P A装 置生产人员 在巡检时 发 现 B 32壳体 敲击器 垫板下 方有 白色 粉末 渗出 , M0
从现 象上 判 断 应 是 干燥 机 壳 体存 在 穿 孔情 况。 B 32主要靠两端托轮支撑 , M0 一旦壳体减薄 , 强度下 降, 将导致 干燥 机 从 中部 断裂 , 成重 大设 备 事故 , 造
刘 炜立 李武荥2
( . 安石 油大学 , 1西 陕西 西安 7 06 ;.中国石油化工股份有限公 司洛 阳分公 司 , 105 2 河南 洛 阳 4 11 ) 70 2 摘要 : 中国石油化 工股份有限公司洛阳分公 司精对笨二 甲酸装 置的氧化 干燥 机在 运行 6a 壳体 后 出现 了腐蚀 穿孔 。经对腐蚀 穿孔 原因进行认真分析 , 为主要 原 因是装 置扩能后 进入干 燥机 内介质 认
m£盯 j
l 基本概况
中国石油化工股 份有 限公司洛 阳分公 司精 对苯 二 甲酸 (T 装置 ( e A) 以下 简称 P A装 置 ) T 采用 B P—
A C MO O技术 , 设 计 生产 能力 为 25 k a 于 20 原 2 t , 0 0 /
干燥机 内T A滤饼带人的醋酸及氢溴酸等腐蚀性介 质 的质 量分数 升高 , 碱洗频次增 加 , 设备 设备 的腐蚀
后果不 堪设想 。 当即对 P A装置 进行 降负荷 运行 , T 减少 干燥 机 的运 转 载 荷 , 后 B 0 2天 M32停 止 运行 。
其设计参数详见表 1 。
表 1 B 3 2 计 参 数 M0 设
质
材 质
液 体 为
慧% 枷)
浅谈PTA装置尾气系统设备的腐蚀和防护

PTA a i ui z fo c ve i ys e f r na f di a n on y ng s t m l i
气 经 仓 顶 除尘 器 1除 尘 后 , 回氮 气 系 统 循 环使 用 。 本 系 统 的输 送 介 质 为 氮 气 , 此 除 输 送 系 统 外 , 因 还 有 一 套 氮气 系 统 。低 压 贮 气 罐 贮 存 的 0 1 a氮 . MP 气 , 压 缩 机 压 缩 成 0 7 MP 经 . a氮 气 贮 存 在 高 压 贮 气
维普资讯
第 4期
山
岚 :T P A粉 料 流 态化 输 送 系 统 简介
① 管道 图例符 号
5 1
图 1 流 态 化 输 送 P A 粉 料 流 程 T
Pr c s ffu d z to o v y ng o TA a i a o e s o i ia i n c n e i f P l frn
SHAN a Ln
( ini e o hmia D s nIstt,ini 0 2 1 C ia Ta j P t c e c l ei ntue Taj 3 0 7 , hn ) n r g i n
Abs r c Th fe t fma n o e a in r me e s o ui ia i n l n it c TA a i o v y n y t m n t t a t: e e c s o i p r to pa a t r ff d z to o g d san e P l frna c n e i g s se o he
PTA装置腐蚀与防护分析
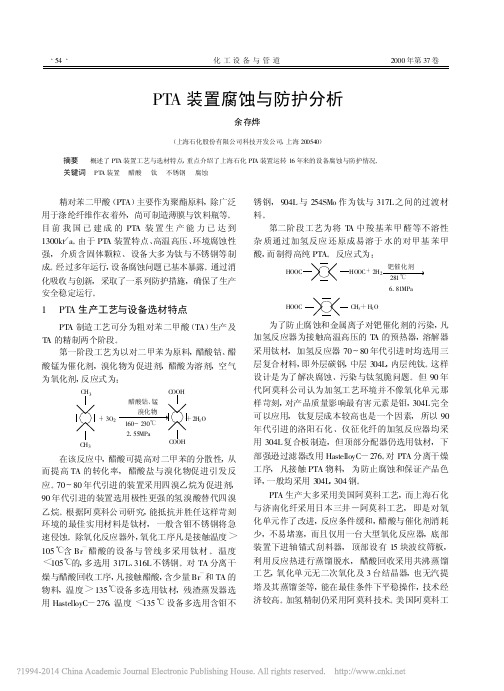
1 PTA 生产工艺与设备选材特点
PTA 制造工艺可分为粗对苯二甲酸(TA)生产及 TA 的精制两个阶段 。
第一阶段工艺为以对二甲苯为原料 , 醋酸钴 、醋 酸锰为催化剂 , 溴化物为促进剂 , 醋酸为溶剂 , 空气 为氧化剂 , 反应式为 :
CH3
COOH
醋酸钴 、锰
+3O2
溴化物
160~ 230℃ 2 .55MPa
精对苯二甲酸 (PTA)主要作为聚酯原料 , 除广泛 用于涤纶纤维作衣着外 , 尚可制造薄膜与饮料瓶等 。 目 前 我 国 已 建 成 的 PTA 装 置 生 产 能 力 已 达 到 1300kt/a 。由于 PTA 装置特点 、高温高压 、环境腐蚀性 强 , 介质含固体颗粒 、 设备大多为钛与不锈钢等制 成 。经过多年运行 , 设备腐蚀问题已基本暴露 。通过消 化吸收与创新 , 采取了一系列防护措施 , 确保了生产 安全稳定运行 。
·56 ·
化 工设 备 与 管 道
2000 年第 37 卷
状焊缝处仍有腐蚀开裂 。后重新设计 、改进结构 , 采 用 317L 作筒体 , 但内壁环焊缝有严重腐蚀 。由于该 设备内壁受到高温浓缩醋酸及残渣颗粒的冲蚀 , 钛 与 317L 均不 是理想 材料 , 建 议象 洛阳石 化采 用 HastelloyC -276 或仪征化纤采用 HastelloyC -22 。 3 .3 非腐蚀性的焊缝损伤
【doc】PTA装置的选材、腐蚀与防护

【doc】PTA装置的选材、腐蚀与防护PTA装置的选材、腐蚀与防护综述?专论石油化工腐蚀与防护2001,18(1)-8- PTA装置的选材,腐蚀与防护余存烨上海石化股份有限公司科技开发公司(上海市200540) 摘要:概述了上海石化F'rA装置运转16年来的设备腐蚀与防护情况,并对引进装置的选材作了评价.关键词:F'rA醋酸钛不锈钢腐蚀精对苯二甲酸(m)主要作为聚酯原料,除广泛用于涤纶纤维作衣着外,尚可制造薄膜和饮料瓶等.为满足人民对合成纤维的需求,国内PTA生产能力正在不断增加:70年代末引进了燕山石化 36kt/a,上海石化225kt/a,80年代引进了扬子石化 450kt/a,济南化纤75kt/a,90年代引进了仪征化纤 250kt/a,洛阳石化225kt/a以及辽阳化纤225kt/a 等.目前国内已建成的PTA装置的生产能力已达到1.5kt/a以上.由于PTA装置的特点(高温高压,环境腐蚀性强,介质含固体颗粒等),设备大多为钛与超低碳不锈钢等材料组成.经过多年的运行,设备腐蚀问题已基本暴露.下文重点叙述上海石化PTA装置运行16年来设备的腐蚀与防护情况,以供国产化及兄弟厂借鉴.1PTA生产工艺与选材特点PTA生产工艺分为两个阶段.第一阶段为对二甲苯氧化生成粗对苯二甲酸(TA);第二阶段为 TA加氢精制生成PTA.第一阶段工艺为以高纯对二甲基苯为原料,醋酸为溶剂,醋酸钻,醋酸锰为催化剂,溴化物为促进剂分别加入到氧化反应器内,在185195?,1MPa 条件下通入空气进行氧化反应,生成纯度为98% 的TA.在该反应工艺中,醋酸浓度达到9o%, 95%,它可提高对二甲苯的分散性,从而提高TA 的转化率.醋酸盐与溴促进引发反应.70,80年代引进的装置采用四溴乙烷作促进剂,9o年代引进的装置选用极性更强的氢溴酸替代四溴乙烷. 根据阿莫柯化学公司的研究,能抵抗并胜任这样苛刻环境的最佳实用材料是钛及其合金,一般含钼不锈钢将急速侵蚀.除氧化反应器外,凡是接触温度太于105~C含溴醋酸的冷凝器,再沸器,容器及管线多采用钛材,温度小于105~C接触含溴醋酸的设备及管线多采用316L,317L不锈钢.9o年代引进的装置还采用904L与254SMO超级不锈钢.随含溴醋酸浓度的变化,而采用不同级~Jrl(含钼量不一) 的钢.个别设备与部件采用Hastelloy一276或C一丝合金.第二阶段工艺为将TA完全溶解于水并送入加氢反应器内,在280?,7MPa,0.7MPa氢分压条件下通过钯炭催化荆作用,使TA中的杂质四羧基苯甲醛与氢反应生成易溶于水的对甲基苯甲酸,分离后得到高纯(99.99%)的PTA,供聚酯生产.阿莫柯公司曾规定PTA产品中金属总含量不允许超过lovg/g.其中Fe 不允许超过2.5g,Mo,Cr, Ni,cu等不允许超过1g.故加氢反应器70,80 年代引进时均采用钛+304L+碳钢三层复合制造,.但到9o年代,阿莫柯公以便优势互补,扬长避短司认为加氢工艺环境并不像氧化单元那样苛刻,304L钢腐蚀率为0.025mm/a,在PTA产品中金属含量小于0.05Vg/g,304L完全可用作反应器内材. 而确认钼是最有害元素,故不宜用316L或含高钼台金.同时考虑钛在280?加氢反应条件下有氢脆危险,三层复合造价较高等因素,所以9o年代引进的装置,如洛阳石化与仪征化纤的加氢反应器均采用304L复合板制造,但反应器顶部的液体分配器仍选用钛材,两只热油加热的进料预热器也选用钛材.此外对接触PTA物料的设备与管线为防止腐蚀和保证产品色泽,一般均采用304L钢. PTA生产大多采用美国阿莫柯工艺,而上海石化与济南化纤采用日本三井一阿奠柯工艺.即对氧化单元作了改进,反应条件缓和,醋酸,催化荆消耗少,不易堵塞,能在最佳条件下平稳操作,技术经济较高.该工艺仅用一台大型氧化反应器,底部装有下进轴锚式刮料器,顶部设有15块波纹筛板,利用反应热进行蒸馏脱水.溶剂醋酸回收采用共沸蒸馏工艺.无二次氧化及3台结晶器,元汽提塔及其蒸馏等.加氢精制仍采用阿奠柯技术.美国阿莫柯工艺,如扬子石化分为二条生产线,各为第1期余存烨.PTA装置的选材,腐蚀与防护?9? 225kt/a;氧化反应器各为3台,共6台;反应温度较高为224qC;控制系统与相应辅助设备亦列三套, 投资大,能耗及原材料单耗较日本三井一阿莫柯工艺略高.9o年代初,中国石化总公司重大装备国产化办公室曾委托上海石化机研所与上海医工院进行过225kt./aPTA装置国产化可行性研究论证. 建议采用日本三井一阿奠柯法225kt/aPTA技术, 以上海石化VIA作样板进行国产化.2PTA装置设备腐蚀与防护上海石化PTA装置经过4年的生产于1988年 l2月完成引进装置的达标任务.从1985年投产一年大检修至今历次现场腐蚀调研及检测,笔者认为,日本三井一阿莫柯法PTA装置设备选材基本上是正确的,大部分设备没有发生严重腐蚀,没有出现较大的生产事故,但某些设备仍发生一些腐蚀与损伤.下面对lO余台曾发生腐蚀或损伤的设备与部件进行分析.2.1氧化单元(TA单元j2.1.1氧化反应器(TD一201)总高28.8m,上段内径4m,高7.95m.有l5层塔盘.为防缝隙腐蚀,该段采用一Pd合金复合钢板;下段内径5.3m,高14.8m,采用钛复合钢板. 由于钛材优良的耐蚀性,至今未发生腐蚀问题.但曾发生反应器半球形封头底部半圆钛管覆盖焊缝损伤,引起泄漏.其原因是由于搅拌器紧固螺母掉下.运转时刮伤焊缝所至.经机修厂在原半圆钛管上再覆盖焊补.使用一年后经检查有粥处裂纹,未焊透与气孔等缺陷,估计是由于只进行单面保护焊及焊前表面处理不彻底等原因造成.后经西北有色院采用铲磨去除原补焊的半圆钛管,再覆盖新的半圆钛管,进行严格的双面保护氩弧焊鲣复,情况较为理想.2.1.2第二薄膜蒸发器(TM一502) 从离心机分离出来的母液送至第一与第二薄膜蒸发器将醋酸蒸发,有机杂质浓缩成残渣,温度为220—260qC,压力0.1MPa.搅拌机采用Haste]lo.yC一276,简体用钛材制作.上下两节简体采用衬钛板唇焊缝,碳钢法兰用C型夹头紧固,因而在简体内壁形成一个环形缝隙.这样在高温,含溴,无水少氧的浓醋酸的作用下发生孔蚀型的缝隙腐蚀,促使氢化,使露于外表的钛唇焊缝开裂,多达5条大裂缝.曾用高分子材料堵漏无效,后在内壁环状缝隙部位实施氩弧焊填充钛丝,以消除漏泄,但施焊部位仍有开裂.后重新设计改进结构.采用317L 钢作简体,经运行几年内壁焊缝腐蚀,明显减薄. 由于蒸发器简体内壁受到浓缩醋酸及残渣颗粒的强列冲刷腐蚀,钛与317L均不是理想材料.建议像洛阳石化采用HastelloyC一276或仪征化纤采用 HastellorC一22.2.1.3反应器冷凝器(TE20lA)氧化反应器顶部出来的废气需经2台冷凝器冷凝,管程温度分别从174qC冷却到155qC,再从 155~C冷却到100~C.管程为钛材,壳体为碳钢.使用情况较好.但其中A台曾由于钛管口焊缝有针孔缺陷,发生含溴醋酸泄漏,使壳体严重腐蚀而更换.为了重新制造冷凝器,充分利用原有数千根钛管,对该冷凝器壳体解体,将结垢钛管进行常温 HNO3+FIF溶液酸洗.结果发现数百根钛管内表面均匀减薄,外表面因结垢程度不一发生了浮雕状腐蚀.为避免酸洗过程腐蚀设备需严格控制HF浓度与清洗时间.2.1.4醋酸蒸馏塔(rr一501)该塔用来把稀醋酸中的水分蒸馏出去,使其达到循环醋酸的浓度返回系统.塔底温度115qC,介质为90%一95%醋酸;塔顶温度9oqC,介质为水及醋酸正丁酯.共用三种材料:上部316L,中部 317L,下部钛复合钢板.317L塔段与钛复合段用法兰连结.经多年运转,该塔内壁不锈钢段一些部位有蚀L,但未构成危害,钛表面光亮,无腐蚀迹像.但塔下部气相进料口,再沸器出料口钛挡板因设计刚度不够,受气流冲击而发生疲劳开裂,后经改进,至今完好.2.1.5离心机(TM一302)共有9台沉降式螺旋卸料离心机,操作温度 105qC,常压,介质为TA,含溴醋酸及水,采用317L 材质.其中最末级三台离心机转鼓腐蚀严重,其上部呈斑坑腐蚀,面积达6o%,蚀深0.3mm.下部呈砂皮状腐蚀,面积达95%.机身内壁也有程度不一的点蚀.尤以碱洗管最严重.已成峰窝状,其中一根曾穿孔更换过.进料管也存在严重点蚀,曾用 254SM0钢制作进料管,使用后检查无明显腐蚀. 也曾用钛材制成筒体的直短管安装于离心机下部, 同时还设计制造并安装一件钛膨胀节,目前运行良好,基本解决了腐蚀与堵料问题.选用254SM0或钛材制造离心机转鼓当然可解决腐蚀问题,但由于加工困难未能实现.目前只有通过轮换使用,以提高运行寿命.2.1.6吸附塔(Tr一1131A,B)及管道石油化工腐蚀与肪护第18卷经反应冷凝后的废气要通过装填90%硅胶和 l0%恬性炭的吸附塔,以脱除水分及有机物,操作温度为160—200?.原设计采用304L,由于含有微量含溴醋酸,促使该塔腐蚀十分严重.尤其是底部构架滤网塌落,塔底蚀穿,每次大检修均需焊补衬里,曾采用254SMO底部焊衬并不太理想.近年扩容(从内径3.8m改为4.2m)后用钛材制造两台吸附塔,通过一年多运行,情况良好.吸附塔的进出口大型不锈钢管道原用304,母材点蚀严重,纵环焊缝发生晶问腐蚀与坑状腐蚀. 后改用316,腐蚀仍严重.经改进工艺后,又改回用304钢.2.1.7回转式干燥机及其螺旋输送机干燥机是把TA中的含摸醋酸及水经蒸汽间接加热,高温循环氮气逆向直接加热蒸发后由氮气带出,螺旋输送机是把湿TA连续送到干燥机迥转筒内.螺旋输送机材质为316L,运转约2年,主轴断裂.邻近处还有多条长裂缝,裂缝均发生在出料端(温度为135?),此外还出现点蚀与均匀腐蚀. 支掌杆和主轴间的焊缝腐蚀也很严重.由于存在物料对螺旋叶片的反作用力及焊接残余应力,使主轴发生应力腐蚀和腐蚀疲劳开裂,所有裂缝全部发生在焊接热影响区上.通过改进设计与焊后消除应力处理,开裂已很少发生.干燥机内径.8m,总长2215m,材料为316L,操作温度135?,在进料段有点蚀,越到出料段,不锈钢越光亮,这是物料干燥后腐蚀性减弱的缘故.2.1.8干燥机循环气鼓风机及其管道,蝶阔离心式鼓风机输送的介质为含摸醋酸的氮气, 流量3Z6ONm3/h,壳体与叶轮均用316L制作.经运转一年,发现壳体下部严重点蚀,叶轮吸气口附近有数片叶片已冲蚀殆尽,后重新焊以新的316叶片,壳体打磨补焊,第二年检修发现腐蚀更为严重, 无法检修,更换新的316L叶轮.为避免与减轻腐蚀,首先是选用了抗冲蚀更好的254Sb10钢;其次是提高进气温度,避免凝液产生,并及时排放凝液; 第三是提高雾沫分离效果,尽量减少循环氮气中含 Hr一的醋酸液滴.经采取上述措施后,情况基本改善.原设计鼓风机进出口316L钢管道(直径12英寸),使用半年,即发生大量穿孔.由于系负压操作,如空气进入系统有爆炸危险,曾用环氧玻璃钢缠绕进行堵漏与加强措施,终因穿孔太多,已全部改成钛管,使用至今.鼓风机吸排气管道上的进出口蝶阔,直径304.8mm,材料SCS14,腐蚀也很严重,全部改用钛阀,使用电好.2.1.9空压机(1?一201)及其中间冷却器多级离心式空气压缩机产生的空气是供氧化反应器需用,流量为731300Nm3/h.转子汽蚀严重, 且有结垢.另外机座下盖密封面腐蚀损坏,需经常清洗与修复.该空压机有一段,二段,三段三个大直径中间冷却器,壳程走空气,管程走冷却水,壳体304,管子316,管板采用碳钢复合304,304复合层朝向壳程侧.管板与管子胀接,再密封焊.由于密封焊的 316焊缝和未被焊缝覆盖的碳钢管板间存在电位差,使得该部位碳钢产生环状电偶腐蚀,部分密封焊缝已脱开,且已腐蚀到胀管部位.曾想用氩弧焊在管板全部堆焊316,但因积水无法施工,后采用环氧涂料覆盖全部管板,并于管箱隔板上加焊锌基或镁基牺牲阳极保护,每次检修更换与涂刷. 2.1.10四溴乙烷管道该管道介质为醋酸加四溴乙烷,原设计采用 316L,投用半年即有9处穿孔,有点蚀,也有均匀腐蚀,腐蚀率达2rmn/a.由于压力较高(原出口压为 1.8MPa),很难堵漏,对生产威胁较大,后改用钛管至今.2.2精制单元(PTA单元)2.2.1加氢反应器(PD一201)反应器容积为33.9m3,规格为~F2100mm× 8400mm,筒体为SGV49(78.5m)+304L(5.5mm)+TP28(2.2ram)--层复合,不锈钢复层的部分焊缝未被钛材覆盖而暴露于工艺介质中.内装3/4筒体高度的恬性炭钯催化剂,由氢压机来的纯氢和由预热器再经溶解器来的TA,从顶部进入,一起通过催化剂床层.反应器顶部进入管,_rA人口管等均为304L制造,管口用相应焊条堆焊.为防催化剂流失,出料口上部装有对称分布的8根带有狭缝金属网的孔管,称Johnson过滤器,由钛制成(洛阳石化用HastelloyC一276),出料管用304L. 经过多年运转,历次腐蚀调研检测发现如下问题:(1)内壁不锈钢焊缝腐蚀.每次检修时总能观察到不锈钢焊缝表面上沉积一层湖蓝色粉末,经鉴定分析是铬的氧化物,这说明不锈钢堆焊层因与钛复层邻接引起电偶腐蚀.(2)不锈钢出料管腐蚀穿孔.1987年因有700t PTA污染被迫停车,经检测发现,反应器下部出料管法兰部(与钛制Johnson过滤器连结),因电偶腐第l期余存烨P2"A装置的选材,腐蚀与肪护蚀穿孔.国外出料管用HastelloyC 一276. (3)不锈钢氢气进口管管口开裂.1993年检修时发现,反应器顶部氢气进口管管口上部开裂. 从金相检测,氢含量测定,硬度测定,证实是氢脆所致.该不锈钢堆焊层金相组织奥化体相当不稳定, 如在一定氢致应力作用下,会促使n转变为马氏体 (.用小角自砂轮打磨后,发现裂缝不深,经染色探伤未发现微裂纹,则用奥312焊条打底补焊, 再用镍基焊丝P12(含Cr21%,Mo9%,Nb2.2%,C0.01%)堆焊修复,经多年使用未发现问题. (4)钛紧固螺母氢脆.曾从反应器一只紧固 Johnson过滤器与304L出料管的钛螺母外表发现有龟裂形貌,取样分析氢量达1600t~g/g,金相观察端面有氢脆裂纹.(5)钛复层吸氢.内壁邻接不锈钢焊缝的钛复层用复膜金相检测发现H针状物,硬度测定较其它部位偏高,尤其是气相部位较严重.但用气动磨头打磨去0.1mm,未发现针状物,这说明吸氢仅表面较浅一层.钛的吸氢是由于在280.CPTA+ 环境中,钛与不锈钢连结,造成不锈钢阳极加速腐蚀与邻近的钛作为阴极吸氢.而在气相部位再加上氢分压条件,阴极析出的氢原子较难转变为氢分子逸出,几乎大部分被活性钛表面吸收,故吸氢严重.2.2.2进料预热器(PE一101D)TA料经过2台蒸汽加热预热器与2台热媒加热预热器,再经溶解器至加氢反应器.腐蚀环境最恶劣的是末台预热器,从215.C加热到280.C.一般钛管及管板l0余年来使用情况良好,但由于管箱采用304L复合,法兰密封面采用308ULC堆焊, 而隔板采用304L外包钛,在这样异种金属结构条件下造成法兰密封面与隔板邻近处严重腐蚀,蚀坑较深.经焊朴修复,不久又产生腐蚀泄漏,每年大修总要焊补.主要原因是设计不合理,若管箱采用钛复合,或隔板栗用304L而不复合钛,可能情况会有所改善.2.23加氢反应器进料调节阀该阀是典型的异金属结构.阀体与导向套为 SCS14不锈钢,阀座,I两杆为钛.经二年使用SCS14 腐蚀严重,紧固的二只316螺丝蚀完,造成钛阀座, 阀杆配合松动无法调节而停车.后通过试验证明在150~C以下时不会发生电偶腐蚀,决定将该阀移至4台进料预热器前,至今使用良好.2.2.4加氢反应器出口调节阀该阀为全钛大型锻造调节阀,日本三井石油规定:氢含量>100tag/g需经脱氢处理.由于该阀处于从6.7MPa减压到4.2MPa,钛阀如吸氢易受到冲击压造成的氢脆开裂.经4年使用后曾对阀体进行金相检测,发现有粗大针状氢化物,曾作真空退火脱氢处理.阀杆可能是Ti一3A1—2.5V钛台金. 阀杆头部采用离子氮化处理,有磨损,需修复. 2.2.5加氢反应器至第一结晶器的管道该管道采用304钢厚壁无缝管弯制成,直径 203.2mm,厚18rmn,介质为VIA,水及反应过剩的少量.温度280.C,压力6.7MPa.由于高温高流速,经二年运转发现内壁熔台线呈现沟状腐蚀,焊肉粗糙疏松,蚀深约1,3mm,母材处有大面积点蚀.日方原设计考虑冲刷减薄量较大,使用一年要更换,但实际使用4,5年才更换.据洛阳石化介绍采用HastelloyB一4,有较高的抗冲蚀性.2.2.6回转式干燥机(PM一4O4)该蒸汽加热干燥机内径~3100mm,总长28000ram,介质为VIA,操作温度135.C,常压操作, 材料用304.运转2年后,在简体中部及蒸汽管外壁发现点蚀,后因点蚀逐渐加重,及蒸汽管因粘结 VIA物料,造成垢下腐蚀与应力腐蚀开裂.经分析有浓缩的d一,cl一是上游设备使用过苛性碱而带来的,最后全部蒸汽管更换成316管,但近年又发生过蒸汽管应力腐蚀开裂.2.2.7离心机(PM一加1)离心机是分离从第五结晶器来的浓度为32% PTA浆料,操作温度151.C,操作压力0.39MPa,转速2100rpm,由304钢制造.该设备一般使用良好, 但经1O余年使用后曾发生过该机内套环整体开裂,外观失去光泽,呈铁灰色,相当脆.经分析认为是不锈钢焊缝及热影响区的晶界贫铬,发生选择性溶解,且在应力与环境中cl一的共同作用下发生应力腐蚀破裂.cI一可能是由于碱洗而带人的,且在内套环局部粘积PTA垢下而浓缩.后内套环采用稳定型奥氏体不锈钢(含焊条),经适当热处理后不再发生开裂.3PTA装置中各类材料的应用评价3.1钛及其台金上海石化PTA装置经过l6年的实际运行,工业纯钛及钛钯台金的大部分设备,尤其在185, 195.C含BT一醋酸的反应器中使用良好,表面光亮或呈各种彩色的氧化膜,未有明显的腐蚀迹象,说明抗高温含溴醋酸均匀腐蚀性能非常优异,对石油化工腐蚀与防护第l8卷280oc,6.7MPaTA溶液环境几乎没有什么腐蚀,是 PTA装置重要设备的理想结构材料.钛的缝隙腐蚀曾是威胁早期钛设备使用的主要问题,但由于 PTA装置所有法兰密封面,塔体与塔板接触处均采用了Ti—Pd合金,杜绝了缝晾腐蚀发生,因此,正是由于优质钛材能大量供应,钛大型设备制造技术 (包括焊接及复合技术,成型加工技术等)的突破, 以及钛腐蚀科学的进展,才能实现PTA工业化生产.PTA装置钛设备预期使用寿命25,30年,是投有问题的.如阿奠柯化学比利时公司最早的 PTA装置,从1969年投资至1996年报道时还在继续运行已达27年,其中的钛设备由于正确设计制造与安装,几乎没有维修的必要.由于钛设备的使用寿命长,虽然投资较高,但企业的综合效益却得到了丰厚的回报.但钛材并不是完善无缺,工业纯钛对残渣蒸发器含溴浓缩醋酸及残渣颗粒的抗冲蚀性能较差,目前设计简体与转子均应采用 HasteUoyC一276或HasteUoyC一22. 钛在高温高压TA+的环境中有吸氢致脆的危险性.但一般说来,工业纯钛在至少含有2% 水分的氢分压及温度在315oc以下不会发生氢脆. 上海石化加氢反应器十余年正常使用足以佐证,顶部钛分配器也未定期更换.发生吸氢主要是由于异金属连结处,特别是与不锈钢接触的钛部位.轧制钛板及钛管的危险性较小,吸氢仅是较浅的表面,但对锻造车制的螺母之类的吸氢脆化是严重的.根据上海石化与阿莫柯比利时公司的经验,钛设备的安全使用关键是制造的质量,特别是应注意钛的焊接.焊接时必须高度清净,完全除去尘土, 湿气与油脂,应慎重控制焊接保护气体.如两面保护,必须有合适的夹具和熟练的焊工进行焊接,严格检验焊接质量.在钛设备加工与维修时应避免铁污染,如在钛反应器内作业时,必须用木制脚手架和铺橡胶垫,而且施工者应穿胶鞋.3.2不锈钢上海石化PTA装置经过l6年运行,一些不锈钢设备腐蚀问题已暴露无遗.主要是点蚀,应力腐蚀以及与钛连结处的电偶腐蚀等.不锈钢点蚀原因是其表面氧化膜被局部破坏,316L,317L钢的含锰量为?2.0%,且有硫?003%,在表面会形成 MIlS夹杂,夹杂处最易成为点蚀的起点.而且该装置氧化单元物料中含Br一,侵蚀性很强,首先把钢表面的MnS蚀去,使氧化膜破坏,产生大蚀孔.在蚀孔内Br一进一步浓缩,点蚀就会向深处发展.而且含溴醋酸不仅会产生点蚀,也同时发生均匀腐蚀.因而危害性较大.为解决点蚀问题主要是提高材质级别,根据抗点蚀的程度可选用904L,254SM0等超级不锈钢,靠增加钼来提高氧化膜的抵抗力. 对特别苛刻的环境,只能选用钛材或镍基合金.当然也可以采用改善工艺环境等措施特别是254SMO(130Cr20Nil8Mo6.1N0.7),由于含钼较高具有相当高的抗点蚀能力,由于含N能阻止金属中间相析出.使用实践证明,在某些场合可代替钛, 可作为钛或HastelloyC一276与316L,317L之间的过渡结构材料.在精制单元,虽然Br一已基本排除,但由于工艺上需碱洗或中和需要,物料中往往带人微量 cl一,而且在不锈钢器壁上容易粘积PTA垢,这样在垢下由于a一的浓缩,会引起以点蚀为起点的应力腐蚀破裂.为此,一是提高材料级别;二是改进结构改善应力条件;三是经常清洗去除沉积的物料垢;四是选用含cl一低的NaOH,或用有机胺中和等.此外,在精制单元280"CTA介质中,钛与不锈钢连结处会发生电偶腐蚀,应在设计中改进,尽可能同一设备中采用同一种材料.如难于避免,应采用过渡层解决,如用Haynes一25合金,或采用改善工艺措施,如移到较低温度环境下使用.在精制单元,根据催化剂与产品色度等工艺要求,尽可能不用含钼不锈钢,而用304L.3.3镍基合金Hast~lloyC一276是HasteUoyC的改进型,它是含16%Mo,16%Cr,5%Fe,4%W的镍基合金.再通过降低c与Si,显着降低了碳化物与F-相析出, 可减少晶间腐蚀,应力腐蚀与缝隙腐蚀,对氧化性介质与还原性介质均具有优异的耐蚀性能,尤其是抗冲蚀性能,在PTA装置中作为残渣蒸发器的结构材料,使用良好.HasteUoyC一22是含22%Ca", 13%Mo,3%W,3%re的镍基合金,低c低si,性能有进一步改进.HastellyB一4是HasteUoyB的改进型,它含68%Ni,28%Mo,15%Fe等,低c低si,该合金主要抗强还原性介质的腐蚀,但不耐氧化性介质腐蚀,一般不宜用于氧化单元,但可用于精制单元不锈钢不耐腐蚀的场合,如加氢反应器至第一结晶器的大13径管道的高温高流速PTA物料的冲蚀环境.(收稿日期12000—03—14)。
PTA第一、二结晶器局部腐蚀情况分析
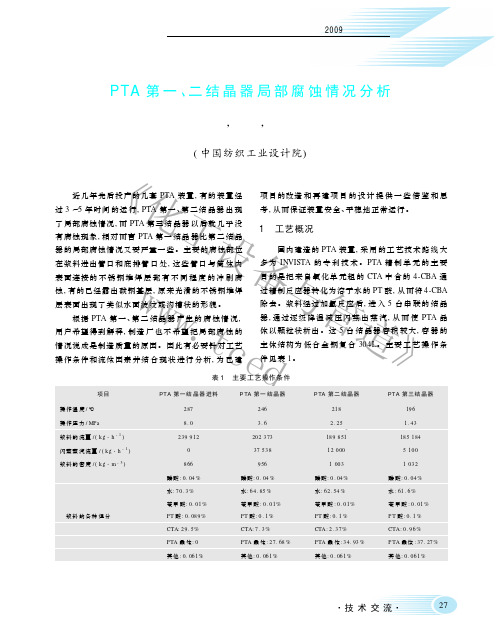
化 质条件要求的。
2.2 工艺操作因素的影响
工 同样的工艺装置, 因工艺操作不当, 其影响是很 设 大的, 设备出现 的腐 蚀情 况也 不同。 比如 因操 作 原
因造成腐蚀介质含量增加; 因操作液位过低造成过
备 量闪蒸蒸汽的产生, 这些都会造成腐蚀情况的发生。
与 在工艺流程里, 从 精制 反应 器 出来 的溶 液进 入 PTA
质经生产实践证明又客观地反映出了问题。在早先 器出现的局部腐蚀情况的分析, 是结合工艺操作条
PTA 装置的精制反应器底部出料管线 ( 进入 PTA 第 件和已建 PTA 装 置 生产 运 行中 发 生的 类 似 情 况 展
一结晶器的) , 该管线 采用 304 无 缝钢 管, 在生 产 过
程中发生严重的冲蚀现象。之后, 该管线材质便设
参考文献
[ 1] 王 非, 林 英. 化 工 设 备 用 钢 [ M] . 北 京: 化 学 工 业 出 版 社 , 2004 .
[ 2] 哈 氏合金 ( Hastelloy alloy) , 宝鸡钛 镍网 技术资 源.
·技 术 交 流·
29
量非常少, 总 含量 不 大 于 0. 15% , 介质 中 没 有 电 解 压溶液进入 PTA 第一结晶器 后快 速发生 闪蒸, 大 量
质的电化学腐蚀环境, 正常操作的情况下不会有引 的蒸汽气泡沿液面与金属界面流动, 形成焦灼带。
起奥氏体不锈钢晶间腐蚀的可能性。
大量的气泡 在 金 属表 面 的 局 部 区 域 反 复 产 生 与 溃
w 结晶器的操作条件就 蕴藏着 介质 冲刷设 备( 尤 其 是
w 管 PTA 第一结晶 器 ) 的 作用。 根 据 工 艺 操 作 条 件, 在
w. 道 结晶器的管口处浆料的流速见表 2。
- 1、下载文档前请自行甄别文档内容的完整性,平台不提供额外的编辑、内容补充、找答案等附加服务。
- 2、"仅部分预览"的文档,不可在线预览部分如存在完整性等问题,可反馈申请退款(可完整预览的文档不适用该条件!)。
- 3、如文档侵犯您的权益,请联系客服反馈,我们会尽快为您处理(人工客服工作时间:9:00-18:30)。
CH3
+2H2 O COOH
在该反应中 , 醋酸可提高对二甲苯的分散性 , 从
而提高 TA 的转化率 , 醋酸盐与溴化物促进引发反
应 。70~ 80 年代引进的装置采用四溴乙烷为促进剂 ,
90 年代引进的装置选用极性更强的氢溴酸替代四溴
乙烷 。根据阿莫科公司研究 , 能抵抗并胜任这样苛刻
环境的最佳实用材料是钛材 , 一般含钼不锈钢将急
4 不锈钢设备腐蚀与防护
4 .1 点腐蚀 氧化单元有 9 台沉降式螺旋卸料离心机 , 操作
温度 105℃, 介质为 TA , 含 Br-醋酸与水 , 材料采用 317L 。其中最末级三台离心机转鼓腐蚀特别严重 , 其 上部呈斑坑腐蚀 , 面积达 60 % , 下部呈砂皮状腐蚀 , 面积达 95 %。机体内壁也发生点蚀 。曾用 254SMo 制 作进料管 , 钛材制作离心机下部直短管与膨胀节 , 基 本解决了这些零部件的腐蚀问题 。设想用钛或 254SMo 制作离心机转鼓 , 但由于加工问题 , 很难实 现 。 目前只有通过轮换使用 , 减缓腐蚀 。
腐蚀性虽小, 但已构成氢脆危险 。在 >100℃的分离干燥 工序设备中 , 由于 PTA 物料因生产工艺需要 , 碱洗与 中和难免带入微量 Cl-, 不锈钢有可能发生应力腐蚀 破裂 。
3 钛设备的腐蚀与防护
3.1 氢脆 以加氢反应器为例 , 其筒体为 SGV49(78.5mm)
+304L(5 .5mm)+TP28(2.2mm)三层复合 , 但内壁的 不锈钢复合层的焊缝未被钛所复盖 , 而暴露于工艺介 质中 。经过 10 余年运转 , 邻接不锈钢焊缝的钛复层用 复膜金相检测发现有 TiH2 针状物 , 硬度测定较其它部 位高 , 尤其是气相部位较严重 , 但用气动磨头打去 0.1mm , 未发现针状物 , 这说明吸氢仅表面较浅一层 , 钛的吸氢是由于在 280℃ TA +H2 环境中钛与不锈钢 连结 , 造成不锈钢阳极加速腐蚀 , 钛作为阴极吸氢乃 至氢化 , 而在气相部位再加上在氢分压条件下 , 阴极 析出的氢原子较难转变为氢分子逸出 , 几乎大部分被 钛表面吸收 , 故吸氢严重 。曾从反应器液相部分一只 紧固钛制强逊过滤器与 304L 出料管的钛螺母外表发 现有龟裂形貌 , 取样分析氢含量达 1600ppm , 金相观察 端面有氢脆裂纹 。一般说来 , 工业纯钛在至少含有 2% H2O 的氢分压下 , 温度在 315℃以下不会发生氢脆 。上 海石化加氢反应器 10 余年来安全正常运转足以作 证 。发生吸氢主要是与不锈钢邻接的钛部位 , 轧制钛 板及钛管危险性较小 , 吸氢仅是较浅的表面 , 但对锻 材车制的螺母之类吸氢脆化是严重的 。 3.2 缝隙腐蚀
1 PTA 生产工艺与设备选材特点
PTA 制造工艺可分为粗对苯二甲酸(TA)生产及 TA 的精制两个阶段 。
第一阶段工艺为以对二甲苯为原料 , 醋酸钴 、醋 酸锰为催化剂 , 溴化物为促进剂 , 醋酸为溶剂 , 空气 为氧化剂 , 反应式为 :
CH3
COOH
醋酸钴 、锰
+3O2
溴化物
160~ 230℃ 2 .55MPa
反应器冷凝器管程走高温醋酸废气 , 壳程走冷 却水 , 管程用钛 , 壳程用碳钢制造 。一般没有腐蚀问 题 , 使用良好 。但其中一台可能由于钛管口焊缝存在 隐性针孔 , 发生含溴醋酸漏入壳程 , 导致碳钢壳体严 重腐蚀而更换 。 3 .4 疲废劳断裂
醋酸蒸馏塔下部气相进料口 , 再沸器出料口钛 档板 , 固引进时设计刚度不够 , 受气流交变冲击 , 而 发生疲劳断裂 , 档板掉到塔底 。后对拉筋加粗修复 , 至今完好 。
在引进设备时基本上已考虑了防钛缝隙腐蚀的设 计 。如氧化反应器上部有 15 层塔盘 , 醋酸蒸馏塔下部 也有多层塔盘 , 由于塔壁与塔盘接触有缝隙 , 故该部 位塔体及塔板均采用了 Ti -Pd 合金 。接管 、人孔法兰 密封面均衬上 Ti -Pd 合金 。但对第二薄膜蒸发器却考 虑不周 , 虽然搅拌器采用 HastelloyC -276 , 筒体选用 钛 。上下两筒体采用衬钛板唇焊缝 , 碳钢法兰用 C 型 夹头紧固 , 因而在筒体内壁形成一个环形缝隙 , 这样 在 220~ 260℃含溴少氧缺水浓醋酸的作用下发生缝 隙腐蚀 , 促使氢化氢脆 , 最终导致钛唇焊缝多次开裂 泄漏 , 曾用高分子合金修补堵漏失败 , 后在内壁环状 缝隙处施行氩弧焊填充钛丝以消除泄漏 , 但不久环
用 HastelloyC -276, 温度 <135 ℃ 设备多选用含钼不
锈钢 , 904L 与 254SMo 作为钛与 317L 之间的过渡材
料。
第二阶段工艺为将 TA 中羧基苯甲 醛等不溶性
杂 质通过加氢反应 还原成易溶于 水的对甲基 苯甲
酸 , 而制得高纯 PTA。 反应式为 :
HOOC
钯催化剂 HOOC +2H2 281 ℃
精制单元设备大多处于高温 TA 或 PTA 腐蚀环 境 。280 ℃下的 TA 溶液呈还原性 , 对不锈钢有不大的 腐蚀性 , 约 0.02mm/a 。但在与钛混合结构中 , 与钛邻 接的不锈钢腐蚀加速 , 温度增高 , 影响更大 。如 150 ℃ 时 , Ti/SCS14, 不锈钢腐蚀率为 0.0019mm/a , 而 280 ℃ 时 , 则达到 0.0582mm/a , 即增大了 30 倍 。 在 280 ℃, 6.72MPa 的 TA +H2(0.49 ~ 0.685MPa 氢分压)环境 中, 304L 腐蚀率为 0 .762mm/a, 钛腐蚀率为 0 .0025mm/a,
精对苯二甲酸 (PTA)主要作为聚酯原料 , 除广泛 用于涤纶纤维作衣着外 , 尚可制造薄膜与饮料瓶等 。 目 前 我 国 已 建 成 的 PTA 装 置 生 产 能 力 已 达 到 1300kt/a 。由于 PTA 装置特点 、高温高压 、环境腐蚀性 强 , 介质含固体颗粒 、 设备大多为钛与不锈钢等制 成 。经过多年运行 , 设备腐蚀问题已基本暴露 。通过消 化吸收与创新 , 采取了一系列防护措施 , 确保了生产 安全稳定运行 。
PTA 生产大多采用美国阿莫科工艺 , 而上海石化 与济南化纤采用日本三井 —阿莫科工艺 , 即是对氧 化单元作了改进 , 反应条件缓和 , 醋酸与催化剂消耗 少 , 不易堵塞 , 而且仅用一台大型氧化反应器 , 底部 装置下进轴锚式刮料器 , 顶部设有 15 块波纹筛板 , 利用反应热进行蒸馏脱水 , 醋酸回收采用共沸蒸馏 工艺 , 氧化单元无二次氧化及 3 台结晶器 , 也无汽提 塔及其蒸馏釜等 , 能在最佳条件下平稳操作 , 技术经 济较高 。加氢精制仍采用阿莫科技术 。美国阿莫科工
干燥机循环 N2 气系统不锈钢设备及管路均发 生不同程度的点蚀 , 还有缝隙腐蚀 、焊缝腐蚀与冲蚀 等 。这个系统材料大多使用 316L 。如干燥机回转筒 及蒸汽加热管与螺旋输送机的进料部位 , N2 冷凝器 管子与管板间 、输送 N2 的鼓风机及其进出口管道与 蝶阀等均发生以点蚀为主的腐蚀 。这个系统由于循 环 N2 气中有含 Br-醋酸液滴 , 或是某些部位易于沉 积含 Br-醋酸冷凝液 , 是造成腐蚀的主要原因 。鼓风 机由于冲蚀严重已改用 254SMo , 其进出口管道由于 多处蚀穿 , 蝶阀由于严重蚀损 , 已均改用钛制 。
经氧化反应冷凝后的废气要通过装填硅胶与活 性炭的两台吸附塔 , 以脱除水分与有机物 , 操作温度 为 160~ 200℃, 引进时设计采用 304L , 由于含有微量
含 Br-醋酸 , 促使该塔腐蚀十分严重 , 尤其底部构 架 , 滤网塌落 , 而且底部也点蚀穿孔 , 每次检修均需 焊补衬里 , 曾采用 254SMo 底部焊补并不太理想 , 近 年决定扩容改造 (从 3 .8m 改为 4.2m), 有钛制造 了两台吸附塔 , 已使用一年多 , 情况良好 。
PTA 装置国产化可行性论证研究 , 拟采用日本三井 —阿莫科法 225kt/aPTA 技术 , 以上海石化 PTA 装置 作样板 , 进行国产化 , 发展民族工业 。
2 PTA 装置腐蚀环境分析
从上海石化 PTA 装置生产工艺与 1985 年至今 历次检修腐蚀检测可知 , 其主要腐蚀介质有两种 , 一 是氧化单元含溴醋酸 , 二是精制单元高温对苯二甲 酸。 2.1 含溴醋酸
·56 ·
化 工设 备 与 管 道
2000 年第 37 卷
状焊缝处仍有腐蚀开裂 。后重新设计 、改进结构 , 采 用 317L 作筒体 , 但内壁环焊缝有严重腐蚀 。由于该 设备内壁受到高温浓缩醋酸及残渣颗粒的冲蚀 , 钛 与 317L 均不 是理想 材料 , 建 议象 洛阳石 化采 用 HastelloyC -276 或仪征化纤采用 HastelloyC -22 。 3 .3 非腐蚀性的焊缝损伤
样苛刻 , 对产品质量影响最有害元素是钼 , 304L 完全 可以应用 , 钛复层成本较高也是一个因素 , 所以 90 年代引进的洛阳石化 、 仪征化纤的加氢反应器均采 用 304L 复合板制造 , 但顶部分配器仍选用钛材 , 下 部强逊过滤器改用 HastelloyC -276 。对 PTA 分离干燥 工序 , 凡接触 PTA 物料 , 为防止腐蚀和保证产品色 译 , 一般均采用 304L , 304 钢 。
·54 ·
化 工设 备 与 管 道
2000 年Байду номын сангаас 37 卷
PTA 装置腐蚀与防护分析
余存烨
(上海石化股份有限公司科技开发公司 , 上海 200540)
摘要 概述了 PTA 装置工艺与选材特点 , 重点介绍了上海石化 PTA 装置运转 16 年来的设备腐蚀与防护情况 。 关键词 PTA 装置 醋酸 钛 不锈钢 腐蚀
速侵蚀 。除氧化反应器外 , 氧化工序凡是接触温度 > 105 ℃含 Br-醋酸的设备与 管线多采用钛材 。 温度
<105℃的 , 多选用 317L 、316L 不锈钢 。对 TA 分离干