仪表板注塑工艺
汽车仪表盘装饰面板注塑模设计及其工艺参数优化

汽车仪表盘装饰面板注塑模设计及其工艺参数优化摘要:近年来,汽车领域市场竞争日趋激烈,汽车产品更新换代的速度也逐步加快,汽车厂家为满足市场需求,需要不断推出新的车型或使用新的部件。
在中国汽车制造业发展需求的刺激下,中国汽车模具也迅猛发展,逐渐从中低端向高端市场发展,汽车模具行业面临良好的发展机遇和巨大的发展潜力。
以聚甲基丙烯酸甲酯(PMMA)为薄膜材料,对仪表盘外壳进行模外装饰(OMD)贴膜,采用有限元方法对该成型过程进行模拟仿真,获得了薄膜厚度的分布及其在x、y方向变形分布,分析了影响薄膜成型的因素。
以成型后薄膜厚度平均值的标准偏差及其在x、y 方向变形量的标准偏差同时最小为目标,采用试验设计(DOE)中的正交数组法对其各项工艺参数进行优化分析。
汽车仪表盘装饰面板注塑模设计及其优化工艺也十分重要,本文从优化汽车仪表盘的装饰面板出发,深入探讨装饰面板注塑模设计及其公艺优化参数。
关键词:汽车仪表盘;装饰面板;塑模设计;工艺参数优化;引言汽车仪表板总成是汽车内饰件的重要组成部分,在汽车配件中,所有与仪表板相关的零件统称仪表板总成。
仪表板与副仪表板组成正副仪表板,仪表板总成是汽车最大的一个总成系列。
在汽车内饰件中,仪表板是集安全性,舒适性,与装饰性于一体的部件,汽车仪表板一般分为硬质与软质两种,随着安全气囊的安装,软质仪表板已失去对人的安全性要求,因此只要外观质量得到保证,采用低成本的硬质仪表板是完全可行的。
一、塑件外观要求与结构分析1.1在现代社会,汽车对人们生活的影响越来越大。
随着社会的发展,人们对汽车的要求也越来越高,不仅要求汽车有良好的使用性能,还要求汽车外饰内饰的和谐统一,满足审美要求。
汽车的内饰主要由塑料件构成,因此汽车注塑模具的质量是影响汽车内外饰的重要因素。
模具结构根据汽车仪表板中央装饰件的结构特点与外观要求,模具采用热流道浇注系统。
塑件由于尺寸大,形状复杂,模具分型面高低落差大,熔体填充困难。
仪表台成型工艺简介
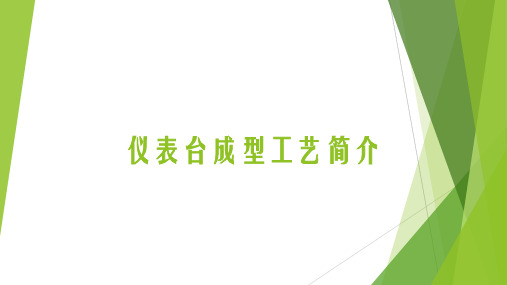
1.06 80~85 6 350 42
(TPU)
四、仪表板表皮的阴模吸塑成型
阴模吸塑成型技术是阳模真空吸塑与搪塑技术的有机结合,它是一种热模成型技术, 即将不带皮纹的热片材(0.8mm TPO表皮+2.0mm泡沬)放置在发泡层与阴模的型腔之间, 通过真空吸附使片材与模具型腔(模具型腔已做出了皮纹)接触成型。冷却时片材收缩, 并与发泡层吸附贴合成型。与传统的成型和复合工艺相比,该工艺不会出现皮纹拉伸现象, 而且可以在一个零件上实现不同的皮纹形式,皮纹均匀、清晰且手感好,与搪塑效果相当。
搪塑表皮一般具有如下优点:由于搪塑表皮的表面花纹是在表皮成型过程中形成的, 因此花纹表面的一致性好;在产品设计上,只要照顾到模具的局部加热性,即可将模具做 成较深的凹陷,甚至做成一定的负角,以加大产品造型设计的裕度;材料成本相对较低。 其缺点是:模具投资大,寿命短(一般模具的质量保证只有20000次表皮寿命);设备投 资大;需要不断地清理模具,导致辅助工时较长。
聚氨酯喷涂仪表板的工艺流程为:注塑成型仪表板骨架→PU喷涂→发泡层 发泡→切割孔和边→焊接主要零件(如需要)→组装相关零件。(高端车型采 用)
一、仪表板的注塑成型
对于全塑的硬质仪表板和发泡仪表板而言,其骨架的注塑成型一般需要使用锁模 力为2000~3000T的注塑机,骨架材料可以采用PC/ABS、SMA或PP+GF,下表对这3 种材料的成型性、成本和使用性能做了比较。片材切割阳模吸塑源自型三、仪表板表皮的搪塑成型
搪塑表皮的制造过程是:首先将带有表面花纹的搪塑模具加热到搪塑表皮的成 型温度,然后将粉箱与搪塑模扣合,使之按设定的程序旋转。当粉料熔化并粘附 于模具表面达到一定厚度后,脱开粉箱。接着,继续加热模具外表面,以使模具 内表面的搪塑表皮得到塑化烧结。最后,快速冷却模具外表面(不喷淋),使表 皮冷却成型。
浅谈仪表板制造工艺

浅谈仪表板制造工艺浅谈仪表板制造工艺作者:浙江众泰汽车技术中心王智仪表板简称“IP(Instrument panel)”,是汽车内饰的重要组成部分。
由于具有得天独厚的空间位置,使得仪表板成为诸多操作功能的载体:驾驶者不仅可通过仪表板了解车辆的基本行驶状态,而且可对风口、音响、空调和灯光等进行控制,从而在确保安全的同时,享受到更多的驾乘乐趣。
近年来,随着技术的不断进步,更多的操作功能被集成到了仪表板中。
显然,为了确保所支撑的各种仪表和零件能够在高速行驶及振动状态下正常工作,仪表板必须具有足够的刚性,而为了减少发生意外时外力对正、副驾驶的冲击,还要求仪表板具有良好的吸能性。
与此同时,出于舒适和审美的要求,仪表板的手感、皮纹、色泽和色调等也日益受到人们的重视。
总之,作为一种独特的内饰部件,仪表板集安全性、功能性、舒适性和装饰性于一身,这些性能的好坏已成为评判整车等级的重要标准之一。
一般,不同的车型所配备的仪表板等级是完全不同的。
根据车型的配置要求,可选择适合的仪表板生产工艺,以达到降低生产成本的目的。
仪表板种类及生产工艺目前,常使用的仪表板主要包括:硬质仪表板、半硬质仪表板、搪塑发泡仪表板、阴模成型仪表板和聚氨酯喷涂仪表板等几种类型。
不同的仪表板,其生产工艺也不尽相同。
一般,硬质仪表板(注塑件)的工艺流程为:注塑成型仪表板本体零件→焊接主要零件(如需要)→组装相关零件;半硬质仪表板(阳模吸塑件)的工艺流程为:注塑/压制仪表板骨架→吸塑成型表皮与骨架→切割孔和边→组装相关零件;搪塑发泡仪表板的工艺流程为:注塑成型仪表板骨架→真空成型/搪塑表皮→泡沬层的发泡处理→切割孔和边→焊接主要零件(如需要)→装配相关零件;阴模成型仪表板(阴模成型及表皮压纹)的工艺流程为:注塑成型仪表板骨架→真空成型/吸塑表面压纹→泡沬层的发泡→切割孔和边→焊接主要零件(如需要)→组装相关零件;聚氨酯喷涂仪表板的工艺流程为:注塑成型仪表板骨架→PU喷涂→发泡层发泡→切割孔和边→焊接主要零件(如需要)→组装相关零件。
仪表板结构反应注射成型工艺优化的开题报告

仪表板结构反应注射成型工艺优化的开题报告一、选题背景和意义随着各种工业制品的使用范围越来越广泛,注塑成型在工业生产中得到了广泛应用。
而注射成型工艺又是注塑成型中最常用的成型工艺方法之一,因其成形速度快、模具寿命长、生产效率高等特点越来越受到工业生产厂家的重视。
但在注塑成型过程中,影响塑料制品质量的因素较多,而掌握优化工艺的方法又较为困难。
然而,我们发现在注射成型工艺中,仪表板的质量问题一直是注射成型加工中的常见问题。
而仪表板质量优劣对于整个汽车内饰的美观度和实用性都有很大的影响。
因此,在当前汽车工业中,如何优化仪表板注射成型工艺以提高仪表板的质量,显得格外重要。
也因此,本文旨在通过优化注射成型工艺,提高仪表板的成形质量。
二、研究内容本文将以汽车仪表板的注射成型工艺为研究对象,重点探讨以下问题:1. 仪表板的成型原理及材料相关知识2. 仪表板注射成型过程中的加工参数控制方法3. 仪表板注射成型模具结构设计及优化方法4. 仪表板注射成型加工过程中的常见问题及其对于成型质量的影响5. 通过优化注射成型工艺,提高仪表板的成形质量三、研究意义本文所探讨的仪表板注射成型工艺的优化方法,可以有效提高汽车仪表板的质量,降低不良率,提升生产效率和生产质量,并有助于提升整个汽车产业链的竞争力。
四、研究方法本文将采用实验室模拟注射成型生产实验,以及计算机仿真和实际汽车仪表板注射成型生产实验两种方法相结合的方式,以对注射成型工艺进行优化,并得到仪表板成型质量的定量评估数据。
五、研究步骤1. 收集仪表板注射成型工艺方面的文献和资料,对相关知识进行深入学习和研究。
2. 设计相关实验方案,建立仪表板注射成型实验模型,并进行成型实验。
3. 根据成型实验结果不断调整加工参数,优化注射成型工艺,比较采用不同工艺参数对成形质量的影响,得到成型质量的定量评估数据。
4. 对比分析注射成型过程中常见问题的成因,总结出影响成型质量的因素,并提出相应的解决方法。
浅谈仪表板制造工艺

环保化:采用环保材料,减少对环境的影 响
集成化:仪表板将集成更多的功能,如导 航、娱乐、通信等
个性化:仪表板将更加个性化,满足不同 消费者的需求
安全性:仪表板将更加注重安全性,如防 撞、防眩光等功能
汇设备,提 高资源利用率, 减少资源浪费
环保认证:通 过环保认证, 提高产品质量 和品牌形象, 满足市场需求
自动化技术:采用自动化生产线,提高生产效率 数字化技术:利用数字化技术,提高生产精度 智能化技术:引入智能化技术,提高生产效率和精度 环保技术:采用环保技术,降低生产过程中的污染和浪费
吸塑工艺:将塑料原料吸 入模具中,通过冷却成型
仪表板制造工艺的特点: 精度高、质量好、生产效 率高
Part Three
塑料原料:聚丙烯、聚碳酸酯等 玻璃原料:钢化玻璃、夹层玻璃等 电子元件:传感器、显示屏等
装饰材料:皮革、织物等 模具:注塑模具、冲压模具等 设备:注塑机、冲压机等
设计原则:满足产品性能和外观要求,提高生产效率 设计方法:采用计算机辅助设计(CAD)和计算机辅助工程(CAE)技术 制造工艺:包括注塑、吹塑、压铸等 质量控制:通过检测和试验,确保模具质量和性能达到要求
装配技术:包括装配顺序、装配方法、装配工具等 检测技术:包括检测方法、检测设备、检测标准等 质量控制:包括质量管理体系、质量控制方法、质量控制标准等 自动化技术:包括自动化装配、自动化检测、自动化质量控制等
Part Five
数字化制造:利用数字化技 术,实现产品设计、生产、 管理等环节的数字化
材料选择:需要选择合适的材料,以满足强度、耐久性和环保要求 工艺技术:需要不断改进工艺技术,以提高生产效率和质量 成本控制:需要降低成本,以提高竞争力 环保要求:需要满足环保要求,以减少对环境的影响 市场需求:需要适应市场需求的变化,以保持竞争力 法规要求:需要满足法规要求,以避免法律风险
浅谈仪表板制造工艺

浅谈仪表板制造工艺引言仪表板是汽车内部的一个重要组件,常见于汽车驾驶舱的前方。
它不仅提供了驾驶员对车辆信息的实时监控,还起到了美化和提升汽车内部整体观感的作用。
在汽车制造过程中,仪表板的制造工艺不仅关乎产品质量和性能的提升,还涉及到制造效率和成本控制等方面的考量。
本文将对仪表板制造工艺进行浅谈。
1. 材料选择仪表板的材料选择是制造工艺的重要一环。
目前,常用的仪表板材料主要有ABS塑料、PVC塑料、PU皮革和真皮等。
其中,ABS塑料是最常见的一种材料,因其具备良好的耐磨性、韧性和抗老化性能而受到广泛应用。
PVC塑料则相对更为廉价,但其抗老化性能较差。
PU皮革和真皮则主要用于高档汽车,具有更好的触感和豪华感,但成本也相应较高。
材料的选择需要综合考虑仪表板的使用环境、车辆定位以及成本等因素。
针对不同的需求,制造商可以选择适合的材料来实现产品的优化设计和提升。
2. 造型设计仪表板的造型设计也是制造工艺的一个重要环节。
一个好的造型设计能够提升仪表板的观感和用户体验。
在设计过程中,需要考虑仪表板的整体结构、弧度、线条和按钮布局等,以及与车辆内部其他组件的协调性。
制造商可以采用计算机辅助设计(CAD)和虚拟样机技术来进行仪表板的设计和仿真。
通过虚拟样机技术,设计师可以在电脑上进行实时的三维模拟和修改,从而提高设计效率和准确性。
3. 注塑工艺注塑工艺是仪表板制造的核心环节之一。
注塑工艺是利用注塑机将熔化的塑料注入到模具中,经过冷却和固化后,得到所需的仪表板零件。
注塑工艺需要注意以下几点: - 模具设计:模具的设计需要考虑零件的结构和尺寸,以及浇口和冷却系统的设置等。
- 材料选择:选择合适的塑料材料,并进行材料的预处理,如干燥、混合和染色等。
- 工艺参数调试:注塑工艺参数的调试需要根据材料的熔融温度、熔体流动性和模具温度等因素进行调整和优化,以确保产品质量。
4. 表面处理表面处理是仪表板制造中不可忽视的一环。
仪表板注塑工艺与模具表面处理工艺的优化对免喷漆硬塑颜色件表面

表板上本体面板表面外观质量和光泽度的影响规律。结果表明:表面处理工艺控制因子对光
泽度的信噪比和均值有较大贡献,注塑工艺控制因子对外观质量评价的信噪比和均值有较大
贡献,而原材料对两者都有影响。对于选用的聚丙烯(PP)注塑仪表板和微网GMGAQ2Q皮纹,
应用由正交列表试验分析出的最优条件进行实际生产,获得了表面外观质量良好的注塑产品。
Process Optimization to tCe Surface Quality of No-painting MIC Part TAO Liang, ZHOU Chen, ZHOU Shu-yuan
( , , , ) Pan Asia Technical Automotive Center Co. Ltd. Shanghai 201206 China
Abstract:In order to lmprove the mold in cclor ( MIC) parts surface quality and reduce the gloss, this paper, on the basis of analysis on light scatte/ng principle, put foavard and verified the method that it can gOectively reduce the gloss by increasing the discrete degree of grain particle size distriVution. At the same Ume, using the orthovonai Ost test design tool was used to further study the infuence law of geain optimieation peocFs, thFpyasticmateiayand inection peocFspaeamFteson thFappFaeancFquayity and gloss of the body panel on the MIC dashboard. The results show that the control fector of suVacc teeatmentpeoceshasageeatconteibution thesignay-to-noiseeatioand mean oJgyos, whiyetheconteoy factor of injection molding process has a great contriVution to the signaOto-noiso ratio and mean of ap pearance evaluation, and the mate/ais have an impact on both. For the selected polypropylene ( PP) injection panel and micro grid GMGA020 grain, the optimum condVions analyzed by orthovonai Ost test weeeappyied o2heac2uaypeoducion, and 2heineecion peoducswih good sueoacequayiyweeeobtained. Key words isu/Vco treatment process & injection process & orthovonai Ost test design & suVacc gloss; suroacequayity
浅谈各种仪表台成型工艺优点与缺点

浅谈各种仪表台成型工艺优点与缺点sino-Andy 仪表台模具2011-02-13浅谈各种仪表台成型工艺优点与缺点仪表台是汽车集安全性,功能性,舒适性与装饰性于一身的部件,在各种配置不同及成型工艺不同的情况下,常见的仪表台成型工艺可分为,注塑成型,阳塑成型,搪塑成型,阴模吸塑成型等多种工艺,在生产工艺上也有不同的成型工艺与优缺点之分,以下为大家介绍以上几种仪表台成型工艺的优点与缺点。
高压注塑主要潜在的产品质量问题因素有:(1)由加强筋位置与模具的浇口设计的尺寸,位置等因素造成的产品表面缩印,引起仪表台产品表面质量。
(2)由于产品结构,材料,周转或摆放不当引起产品变形,造成仪表台的装配困难,面差,缝隙不均匀,造成的外观等不良现象。
(3)由于产品结构,流道的设计,材料的流动性造成产品成型后的熔接痕,造成仪表台产品的外观不良现象。
低压注塑的主要优点:(1)产品成型效率高.(2)面料与骨架不用粘剂。
主要潜在的缺点有,(1)相对与高压注塑模具及设备产品及设备成本高,(2)相对于二次复合工艺的财力啊,面料成本较高。
仪表台阳塑真空吸塑优点:(1)模具投资小,寿命长,(2)产品生产效率高。
(3)设备投资只有搪塑设备的1/3-1/4。
主要潜在的缺点有:(1)由于表面花纹是预制的,花纹损失随着表皮的拉伸度增大而增大,当拉升较大时,细皮纹就会使皮纹消失,粗皮纹就会淡化形成明显的视觉差效果,影响外观。
(2)由于是阳塑真空成型的工艺特征,决定了阳塑加工对产品阴阳角尺寸的局限性,一般R角都要设计在R1.5以上,给产品外观设计带来了局限。
搪塑仪表台的优点:1由于搪塑表皮的表面花纹是在表皮成型过程中形成的,因此花纹面一致性好。
2在产品设计上只要照顾到模具的局部加热性,模具可以做到较深的凹陷,甚至做成一定的负角,使得产品造型设计裕度更大,3材料成本相对较低。
潜在的缺点:1模具投资达,寿命短,一般模具的质量只有20000只表皮的寿命。
仪表外壳注塑模具设计与制作

仪表外壳注塑模具设计与制造如图1所示塑件为某仪表外壳,材料为ABS,壁厚2mm,批量生产。
分析塑件的工艺性能,设计其模具,编制模具零件的加工工艺。
图1 仪表外壳塑件图1 塑件的工艺性分析1.1 塑件的原材料分析ABS 为热塑性塑料,为非结晶性塑料。
综合性能良好,冲击韧性、机械强度较高,尺寸稳定,耐化学性,电性能良好;易于成型和机械加工。
流动性中等,溢边值为0.04mm 左右;吸湿性强,必须充分干燥,表面要求光泽的塑件须经长时间的预热干燥;成型时易取高料温、高模温,但料温过高易分解(分解温度≥250O C )。
结论:该塑料有良好的工艺性能,适宜注射成型,成型前原料要干燥处理。
1.2 塑件的尺寸精度分析此塑件上有三个尺寸有精度要求,分别是34.0066+、26.0046+、018.018-均为MT1~2级塑料件精度,属于中等偏高级的精度等级,在模具设计与制造过程中要严格保证这三个尺寸精度的要求。
其余尺寸均无特殊要求,为自由尺寸,可按MT5级塑料件精度查取公差值。
1.3 塑件表面质量分析该塑件是某仪表外壳,要求外表美观、无斑点、无熔接痕,表面粗糙度可取Ra1.6,而塑件内部没有较高的粗糙度要求。
1.4 塑件结构工艺性分析此塑件外形为方形壳类零件,腔体为8mm 深,壁厚均为2mm ,总体尺寸不大不小,塑件成型性能良好;塑件上有一六边形凸台,要求成型后轮廓清晰,成型它的模具工作零件要用线切割成型,保证六边的尖角;塑件的两边各有一个对称的类三角形凸起标志,高0.2mm ,同样要求轮廓清晰,成型它的模具工作零件可用电火花成型加工,相应的要设计出它的电极。
2 成型设备的选择与模塑工艺参数的编制2.1 计算塑件的体积根据零件的三维模型,利用三维软件直接可查询到塑件的体积为:V1=9563.66mm3,浇注系统的体积:V2=1551.52mm3,一次注射所需的塑料总体积为:V=V1+V2=11115.18 mm3。
(工艺技术)浅谈仪表板制造工艺

浅谈仪表板制造工艺作者:浙江众泰汽车技术中心王智仪表板简称“IP(Instrument panel)”,是汽车内饰的重要组成部分。
由于具有得天独厚的空间位置,使得仪表板成为诸多操作功能的载体:驾驶者不仅可通过仪表板了解车辆的基本行驶状态,而且可对风口、音响、空调和灯光等进行控制,从而在确保安全的同时,享受到更多的驾乘乐趣。
近年来,随着技术的不断进步,更多的操作功能被集成到了仪表板中。
显然,为了确保所支撑的各种仪表和零件能够在高速行驶及振动状态下正常工作,仪表板必须具有足够的刚性,而为了减少发生意外时外力对正、副驾驶的冲击,还要求仪表板具有良好的吸能性。
与此同时,出于舒适和审美的要求,仪表板的手感、皮纹、色泽和色调等也日益受到人们的重视。
总之,作为一种独特的内饰部件,仪表板集安全性、功能性、舒适性和装饰性于一身,这些性能的好坏已成为评判整车等级的重要标准之一。
一般,不同的车型所配备的仪表板等级是完全不同的。
根据车型的配置要求,可选择适合的仪表板生产工艺,以达到降低生产成本的目的。
仪表板种类及生产工艺目前,常使用的仪表板主要包括:硬质仪表板、半硬质仪表板、搪塑发泡仪表板、阴模成型仪表板和聚氨酯喷涂仪表板等几种类型。
不同的仪表板,其生产工艺也不尽相同。
一般,硬质仪表板(注塑件)的工艺流程为:注塑成型仪表板本体零件→焊接主要零件(如需要)→组装相关零件;半硬质仪表板(阳模吸塑件)的工艺流程为:注塑/压制仪表板骨架→吸塑成型表皮与骨架→切割孔和边→组装相关零件;搪塑发泡仪表板的工艺流程为:注塑成型仪表板骨架→真空成型/搪塑表皮→泡沬层的发泡处理→切割孔和边→焊接主要零件(如需要)→装配相关零件;阴模成型仪表板(阴模成型及表皮压纹)的工艺流程为:注塑成型仪表板骨架→真空成型/吸塑表面压纹→泡沬层的发泡→切割孔和边→焊接主要零件(如需要)→组装相关零件;聚氨酯喷涂仪表板的工艺流程为:注塑成型仪表板骨架→PU喷涂→发泡层发泡→切割孔和边→焊接主要零件(如需要)→组装相关零件。
汽车仪表板及其制造工艺介绍

汽车仪表板及其制造工艺仪表板因其得天独厚的空间位置,使愈来愈多的操作功能分布於其中,除反映车辆行驶基本状态外,对风口、音响、空调、灯光等控制也给予行车更多的安全和驾驶乐趣。
因此,在汽车中,仪表板是非常独特的集安全性、功能性、舒适性与装饰性於一身的部件。
首先,它需要有一定的刚性以支撑其所附的零件在高速和振动的状态下保证正常工作;同时又需要有较好的吸能性使其在发生意外时减少外力对正、副驾驶员的冲击。
随着人们对车的理解愈来愈超出其功能,对仪表板的手感、皮纹、色泽、色调也逐渐成为评判整车层级的重要标准。
仪表板通常包含仪表板本体(壳体)、仪表、空调控制系统、风道/风管、出风口、操作面板、开关、音响控制系统、除霜器、除雾器、手套箱、左盖板、饰板等零件。
大部分仪表板还包含:储物盒、驾驶员侧手套箱、扬声器等饰件和时钟、金属加强件、烟灰盒、点烟器、杯托等功能性零件;部分中高档汽车设计有卫星导航系统、手机对讲系统、温度传感系统等高端产品。
仪表板的分类仪表板按安全性可分为无气囊仪表板和附气囊仪表板(针对副驾驶)。
目前国内只有少数中高档次的轿车配备气囊仪表板,随着人们对安全性的重视,客户对附气囊仪表板需求加大,主机厂也将此作为买点之一。
气囊打开在保护乘客的同时,也可能伤害乘客,尤其是儿童。
因此,国际上部分新车型的仪表板气囊已开始加装开关。
为气囊的正常开启,在气囊上方多设计有气囊盖板,在其打开时释放气囊。
但其与仪表板匹配处存在可视装接线,影响整车美观。
为此,近年愈来愈多车型的仪表板设计为无缝气囊仪表板。
既能保证气囊正常开启,又无可视装接线。
仪表板按舒适性可分为硬塑仪表板、吸塑仪表板和半硬泡软质仪表板。
仪表板本体以注塑工艺制成的为硬塑仪表板,因其工艺简单、投资低等优势而被广泛应用,尤其是中低档车。
其中有局部或全部涂装饰漆或软触漆,以改善外观、增加色调或提高质感。
吸塑仪表板是在注塑或压制骨架外吸附并粘结或在注塑时复合表皮,使其外观有皮质感。
汽车仪表外壳注塑工艺及模具设计

汽车仪表外壳注塑工艺及模具设计摘要:随着经济日益发展,塑料制品越来越多,注塑的、吹塑的、挤压成型的,而对于一些改性塑料的应用,有些塑料甚至可以超越部分合金的硬度,在汽车的应用方面,除了塑料轻的原因之外还有很多优良的特性,一些塑料还用于做防火材料,促使成本大大的降低,使国民经济稳定而高速的增长,在生产力的不断提高,工业技术也渐渐的向国外先进技术靠齐,特别是对于一些出口模具,精度要求都可以到达要求,模具设计的好,模具材料选用的好,加工机床先进的,模具的生产时间可以连续生产10几年。
产品的成型离不开注塑机的生产,生产工艺的调试,为达到更好的产品注塑周期和质量要求。
模具是我们提高生产效率的重要因数,提升模具生产产能是每一位工程师的责任,模具设计的好坏直接反馈到模具是否能稳定长时间的生产和日后生产维修是否方便。
关键词:模具;模具设计;注塑;成型一、汽车仪表概述在普通的汽车当中,仪表会涵盖车速里程表、转速表、水温表和燃油表等。
在现代汽车当中,汽车仪表还要安装了稳压设备,专门对仪表电源的电压进行稳定,压制住了波动产生的幅度,确保仪表能够精准的进行显示[1]。
此外,很多仪表的显示皆来自传感设备,根据监测对象产生的变化,对电阻值进行改变,再利用仪表进行表述。
在仪表板当中,最突出的便是车速里程表,能够将汽车的时速显示出来,车速里程表由2个表组成,分别是车速表和是里程表。
二、模具质量正常而言,客户主要从工期、投入以及质量几个角度对模具进行评估。
这里面质量是客户最为关注的一点,这是由于要做出可靠的产品就必须拥有一个可靠的模具。
因此对于模具生产公司来说,如果想要提高其市场竞争力,就必须增强模具的质量。
增强模具质量应当对其生产的所有流程细节进行严格的把控。
模具制造大致要经过制造与设计两个阶段,前者是通过加工、选材、状态、热处理等各种生产流程方面决定着模具的质量;后者则是通过生产可操作性、细节的精准程度、构造的科学程度等影响模具质量。
- 1、下载文档前请自行甄别文档内容的完整性,平台不提供额外的编辑、内容补充、找答案等附加服务。
- 2、"仅部分预览"的文档,不可在线预览部分如存在完整性等问题,可反馈申请退款(可完整预览的文档不适用该条件!)。
- 3、如文档侵犯您的权益,请联系客服反馈,我们会尽快为您处理(人工客服工作时间:9:00-18:30)。
一、实验目的及原理 3. 掌握热塑性塑料注射成型的操作过程
④冷却阶段
冷却阶段: 保压时间到达后,模腔内塑料 熔体通过冷却系统调节冷却到 玻璃化温度或热变形温度以下 ,使塑料制品定型的过程叫冷 却。这其间需要控制冷却的温 度和时间。模具冷却温度的高 低和塑料的结晶性、热性能、 玻璃化温度、制品形状复杂与 否及制品的使用要求等有关。
仪表板注塑工艺 虚拟仿真实验
• 虚拟仿真实验项目脚本文件的格式为PPT, 内容应包括: • 1、所属课程: • 2、项目名称或实验名称: • 3、提供实验指导书(需求说明书)、功能需 求以及素材等。
• 虚拟仿真实验项目内容应包括: • 1、所属课程: 高分子材料成型原理及工艺 • 2、项目名称或实验名称:
一、实验目的及原理 3. 掌握热塑性塑料注射成型的操作过程
⑥开模
开模 开模是注射完毕后,动模在液 压油缸的作用下首先开始低速 后撤,而后快速后撤到最大开 模位置的动作过程叫开模。
一、实验目的及原理 4. 掌握温度、压力等工艺条件对注射制品 质量的影响。
温度对制件的影响 注塑成型的温度通常指料筒温度和模具温度两个方面。成型时,如果塑 料温度偏高:易分解;易产生内应力;熔体的表观粘度降低,流动性好 ,对于温度敏感的塑料尤其如此,充模容易,易溢料、溢边等;收缩率 加大,易产生凹陷;结晶度下降;取向程度下降等。塑料温度偏低:不 易分解;熔体表观粘度大,流动性差,充模困难,易产生充不满、熔接 痕、冷块或僵块等。塑料温度不均:易产生内应力,如在实际模腔中, 各点的温度是不均匀的,熔体的流动属于非等温流动。模温高,利于大 分子热运动,利于大分子的松弛,可以减少厚壁和形状复杂制品可能因 为补塑不足、收缩不均和内应力大的缺陷。但模温高,生产周期长,脱 模困难,是不适宜的。对于结晶型塑料,模温直接影响结晶度和晶体的 构型。
作过程注意事项,突出强调显示,配以文字说明。
(4)鼠标点击实验完成,出现导出工艺数据和思考题。
• 2)列出实验所需要用的设备、仪器、 仪表、工具、样本、模型等,以及操 作使用方法或使用说明书(如相应设 备、仪器、仪表、工具等的图片或录 像等)。
• 3) 提供实验原理、实验目的、实验操作步 骤、实验注意事项等方面的文字介绍。 • 实验指导书
• 3、提供实验指导书(需求说明书)、功能需 求以及素材等。
• 1)教学或实验项目设计及展示形式、实验的方法
和步骤、实验数据分析方法及评分标准、确认需交
互操作的内容和方式方法等。说明如何通过鼠标控
制进行实验仪器的结构学习、操作练习。
• 实验项目设计及展示形式: 以视频、3D动画展示仪表板注塑过程(从启动到顶 出制件) • 实验步骤:以文字、图片展示(按指导书步骤) • 实验数据分析方法及评分标准: 导出工艺设定数据,数据来源于启动前的设定。 评分标准:结合制件外观质量,调整工艺参数;回 答思考题
注意事项:启动注塑机时,必须先打开电热开关,待温 度达到设定值后才能启动马达,否则可能损坏螺杆。
三、实验步骤
步骤4:模式1——手动
• 控制面板图片, 圈示出手动开 关位置
三、实验步骤
步骤5
• 控制面板图片, 圈示出几个动 作按钮
三、实验步骤
步骤6
• 控制面板图片, 圈示出几个动 作按钮
注意事项:按下脱模进按钮顶出制品后,再次合模前一 定要按下脱模退按钮,否则容易损坏脱模油缸。
• 4)提供相关图片素材或示意图、视频(展现 或说明设备的结构、原理、使用过程)等,并 配合必要的说明材料来表达需要实现的效果
仪表板注塑工艺 虚拟仿真实验
仪表板?
• 简介:仪表板是汽 车中非常重要的零 部件,集安全性、 功能性、舒适性和 装饰性于一体。除 了要求有良好的刚 性及吸能性,人们 对其手感、皮纹、 色泽、色调的要求 也愈来愈高。
其各部分组成,详细展示模具(注塑模具仿真视频)
鼠标点击工具,出现工具使用说明图片和文字。
(3)鼠标点击实验步骤,依次按指导书操作步骤出现
设备相关部位,点击鼠标左键进行相应动作的操作。
A、工艺参数的设定,出现设备控制面板,以输入设
定的参数。
B、鼠标点击下一步,逐步显示操作过程。
C、在准备阶段、第一步、第三步、第四步分别出现操
一、实验目的及原理
1.了解塑料注塑成型的基本原理
塑料注塑成型基本原理:利用 塑料的可挤压性和可模塑性 ,首先将松散的粒料或粉状 成型物料从注塑机的料斗送 入高温的机筒内加热熔融塑 化,使其逐渐熔解,并呈粘 流状态,然后在螺杆或柱塞 的高压推动下,以很大的流 速通过料筒前端的喷嘴将熔 体注入到低温闭合的模具中 ,经一段时间保压冷却定型 时间后,开模取出具有一定 形状和尺寸的塑料制件。
一、实验目的及原理
2. 了解注塑机的构成,了解各部分功能
注塑机的基本构成: 本实验使用的注塑机为TD800型注塑机,其基本结构 如下: 注射装置:由料斗、料筒、 加热器、计量装置、螺杆及 其驱动装置、喷嘴等部件组 成,作用是保证定时定量地 把塑料均匀地塑化呈熔融状 态,并以足够的压力和速度 将塑料熔体注入闭合的模具 型腔。 锁模装置:实现模具的开闭 ;成型时提供足够的夹紧力
仪表板?
•
构成:仪表板通常包含仪表板本体(壳体)、仪表、空调控制系统、风道/风管、出风 口、控制面板、开关、音响控制系统、除霜器、除雾器、手套箱、左右下护板等零件。 大部分仪表板还包含:储物盒、副驾驶侧手套箱、扬声器等饰件和时钟、金属加强件、 烟灰盒、点烟器、杯架等功能性零件;部分中高档汽车配备有卫星导航系统、手机对 讲系统、温度传感系统等高端产品。
1.实验设备
设备规格型号
二、实验设备及材料
2.实验材料
ABS
PP
PC
三、实验步骤
步骤1
• 放大圈示出 开关位置
注意事项:物料如果容易吸水,注塑前应进行干燥处理!
三、实验步骤
步骤2
• 控制面板图 片,圈示出T、 P、V设置 • 文字说明如 何设置
三、实验步骤
步骤3
温度等达到设定值后图片
• 放大圈示出马 达开关位置
第四条目的出现后:鼠标点击工艺条件,出现文字说
明和图片(不同参数下的制件缺陷图片)。
(2)鼠标点击实验准备,依次出现实验材料、设备、
工具。
鼠标点击实验材料,出现不同材料以供选择,ABS、
PP、 PC,鼠标右键点击材料显示这些材料的外观
(图片)和特性(文字说明)。
鼠标点击实验设备,出现注射成型来自图片,动画展示一、实验目的及原理 3. 掌握热塑性塑料注射成型的操作过程
①合模
合模 合模是动模前移,快速闭合 。在与定模将要接触时,依 靠合模系统的自动切换成低 压,提供低的合模速度,低 的合模压力,最后切换成高 压将模具合紧。
一、实验目的及原理 3. 掌握热塑性塑料注射成型的操作过程
②注塑阶段
加料斗 料筒
注塑阶段: 模具闭合后,注射机机身前 移使喷嘴与模具贴合。油压 推动与油缸活塞杆相连接的 螺杆前进,将螺杆头部前面 已均匀塑化的物料以规定的 压力和速度注射入模腔,直 到熔体充满模腔为止。
压力对制件的影响 注塑成型时的压力包括注射压力、保压力(型腔压 力)、背压力(塑化压力)。注射压力与注射速度 相辅相成,对熔体的流动和充模具有决定性作用; 保压力和保压时间密切相关,主要影响模腔压力和 最终的成型质量;背压力影响物料的塑化过程、塑 化效果和塑化能力,并与螺杆转速有关。
二、实验设备及材料
螺杆
模具
一、实验目的及原理 3. 掌握热塑性塑料注射成型的操作过程
③保压阶段
保压阶段: 熔体充模完全后,螺杆施加一 定的压力,保持一定的时间, 是为了解决模腔内熔体因冷却 收缩,造成制品缺料时,能够 及时进行补塑,使制品饱满。 保压过程包括控制保压压力和 保压时间,它们均影响制品的 质量。
螺杆将指定的压力应用于聚合物熔体,以便将 更多的塑料装入型腔。
• 确认需交互操作的内容和方式方法等:
(1)鼠标点击实验名称,依次出现实验目的文字说明。
第一条目的出现后:鼠标点击注塑原理,出现注塑动
画,并配以文字说明。
第二条目的出现后:鼠标点击注塑机构成,出现注塑
机原理结构视频讲解,详细展现结构
第三条目的出现后:鼠标点击操作过程,出现动画演
示5个过程,并配以文字说明。
•
零件会继续冷却,直到足够坚硬能够承受顶出
一、实验目的及原理 3. 掌握热塑性塑料注射成型的操作过程
⑤原料预塑化
原料预塑化 制品冷却时,螺杆转动并后退 ,同时螺杆将树脂向前输送、 塑化,并且将塑化好的树脂输 送到螺杆的前部、并计量、储 存,为下一次注射作准备,此 为塑料的预塑化。预塑化是要 求得到定量的、均匀塑化的塑 料熔体。塑化是靠料筒的外加 热、摩擦热和剪切力等而实现 的,剪切作用与螺杆的背压和 转速有关。
仪表板注塑工艺实验
• 3、提供实验指导书(需求说明书)、功能需 求以及素材等。
仪表板注塑工艺实验指导书
一、实验目的 1. 了解塑料注塑成型的基本原理; 2. 了解注塑机的构成,了解各部分功能; 3. 掌握热塑性塑料注射成型的操作过程; 4. 掌握温度、压力等工艺条件对注射制品质量的影响。
二、实验原理 1. 塑料注塑成型基本原理 塑料注塑成型利用塑料的可挤压性和可模塑性, 首先将松散的粒料或粉状成 型物料从注塑机的料斗送入高温的机筒内加热熔融塑化, 使其逐渐熔解, 并呈粘 流状态, 然后在螺杆或柱塞的高压推动下, 以很大的流速通过料筒前端的喷嘴将 熔体注入到低温闭合的模具中, 经一段时间保压冷却定型时间后, 开模取出具有 一定形状和尺寸的塑料制件。 2. 注塑机的基本构成 本实验使用的注塑机为 TD-800 型注塑机,其基本结构如下: 1)注射装置:由料斗、料筒、加热器、计量装置、螺杆及其驱动装置、喷 嘴等部件组成, 作用是保证定时定量地把塑料均匀地塑化呈熔融状态, 并以足够 的压力和速度将塑料熔体注入闭合的模具型腔。 2)锁模装置:实现模具的开闭;成型时提供足够的夹紧力使模具锁紧;开 模时推出模内制件。 3)液压传动和电器控制:实现注塑机的各种动作以及各种工艺参数的调节 和控制。 3. 塑料注塑成型模具的基本组成 注塑模由动模和定模两大部分组成,在注塑成型时,动模与定模闭合,构成 浇注系统和型腔。 本实验注塑模具的主要结构如下: 1)成型部件:作为制件的几何边界,包容之间,完成塑料之间的结构和尺