精益管理专业术语-E系列
精益生产常用工具术语
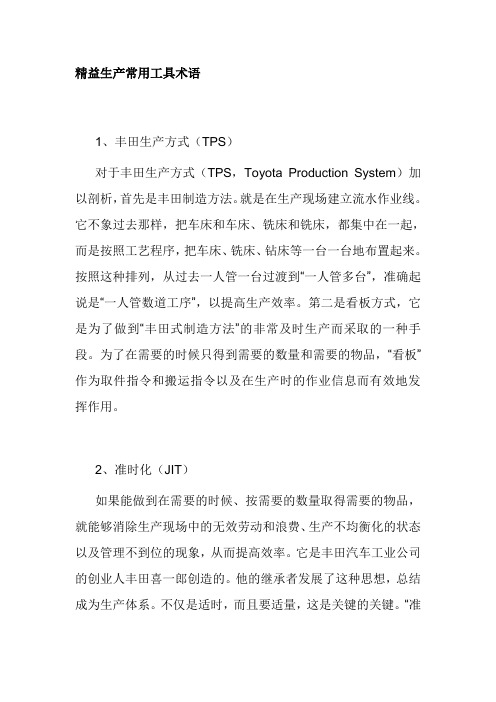
精益生产常用工具术语1、丰田生产方式(TPS)对于丰田生产方式(TPS,Toyota Production System)加以剖析,首先是丰田制造方法。
就是在生产现场建立流水作业线。
它不象过去那样,把车床和车床、铣床和铣床,都集中在一起,而是按照工艺程序,把车床、铣床、钻床等一台一台地布置起来。
按照这种排列,从过去一人管一台过渡到“一人管多台”,准确起说是“一人管数道工序”,以提高生产效率。
第二是看板方式,它是为了做到“丰田式制造方法”的非常及时生产而采取的一种手段。
为了在需要的时候只得到需要的数量和需要的物品,“看板”作为取件指令和搬运指令以及在生产时的作业信息而有效地发挥作用。
2、准时化(JIT)如果能做到在需要的时候、按需要的数量取得需要的物品,就能够消除生产现场中的无效劳动和浪费、生产不均衡化的状态以及管理不到位的现象,从而提高效率。
它是丰田汽车工业公司的创业人丰田喜一郎创造的。
他的继承者发展了这种思想,总结成为生产体系。
不仅是适时,而且要适量,这是关键的关键。
“准时化”(JIT,Just In Time)和下述的“自动化”思想构成了丰田生产方式的两大支柱。
3、自动化(Jidoka)在丰田生产方式中,始终强调必须是带人字旁的“自动化”。
所谓自动化,是将人的智慧赋予机器的意思。
“自动化”这种思想的发端是从丰田公司开山鼻祖--- 丰田佐吉的自动纺织机开始的。
丰田式自动纺织机在经纱断了或纬纱没有了的时候,机器立即停车,也就是装有使机器能判断工作状态好坏的装置。
丰田公司,不仅把这种想法用于机器,而且也扩大到流水线上的操作者。
这就是说,如果发生异常,操作者可以把整个流水线停车。
自动化的优点是,能够防止生产次品,制止过量制造。
此外,还能自动控制生产现场发生的异常现象。
4、目视化管理(VC)在“自动化”(VC,Visual Control)的含义中,包含有这样一种意思,即如果发生异常现象,生产线和机床就立即停车。
精益生产管理常用术语
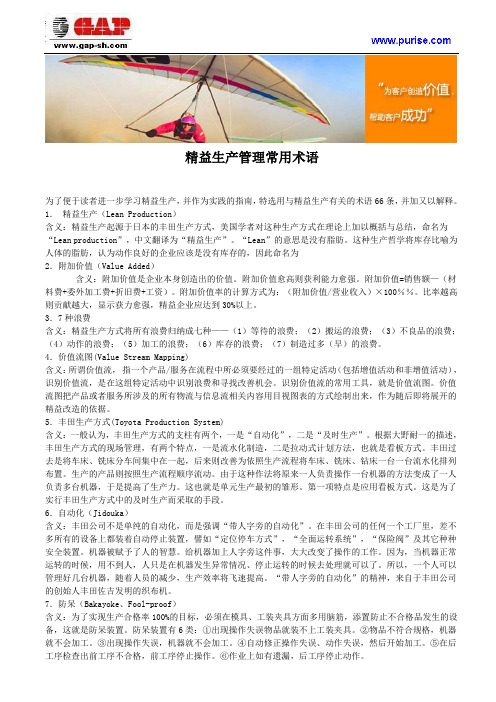
精益生产管理常用术语为了便于读者进一步学习精益生产,并作为实践的指南,特选用与精益生产有关的术语66条,并加又以解释。
1.精益生产(Lean Production)含义:精益生产起源于日本的丰田生产方式,美国学者对这种生产方式在理论上加以概括与总结,命名为“Lean production”,中文翻译为“精益生产”。
“Lean”的意思是没有脂肪。
这种生产哲学将库存比喻为人体的脂肪,认为动作良好的企业应该是没有库存的,因此命名为2.附加价值(Value Added)含义:附加价值是企业本身创造出的价值。
附加价值愈高则获利能力愈强。
附加价值=销售额—(材料费+委外加工费+折旧费+工资)。
附加价值率的计算方式为:(附加价值/营业收入)×100%%。
比率越高则贡献越大,显示获力愈强,精益企业应达到30%以上。
3.7种浪费含义:精益生产方式将所有浪费归纳成七种——(1)等待的浪费;(2)搬运的浪费;(3)不良品的浪费;(4)动作的浪费;(5)加工的浪费;(6)库存的浪费;(7)制造过多(早)的浪费。
4.价值流图(Value Stream Mapping)含义:所谓价值流,指一个产品/服务在流程中所必须要经过的一组特定活动(包括增值活动和非增值活动),识别价值流,是在这组特定活动中识别浪费和寻找改善机会。
识别价值流的常用工具,就是价值流图。
价值流图把产品或者服务所涉及的所有物流与信息流相关内容用目视图表的方式绘制出来,作为随后即将展开的精益改造的依据。
5.丰田生产方式(Toyota Production System)含义:一般认为,丰田生产方式的支柱有两个,一是“自动化”,二是“及时生产”。
根据大野耐一的描述,丰田生产方式的现场管理,有两个特点,一是流水化制造,二是拉动式计划方法,也就是看板方式。
丰田过去是将车床、铣床分车间集中在一起,后来则改善为依照生产流程将车床、铣床、钻床一台一台流水化排列布置。
精益术语-IE
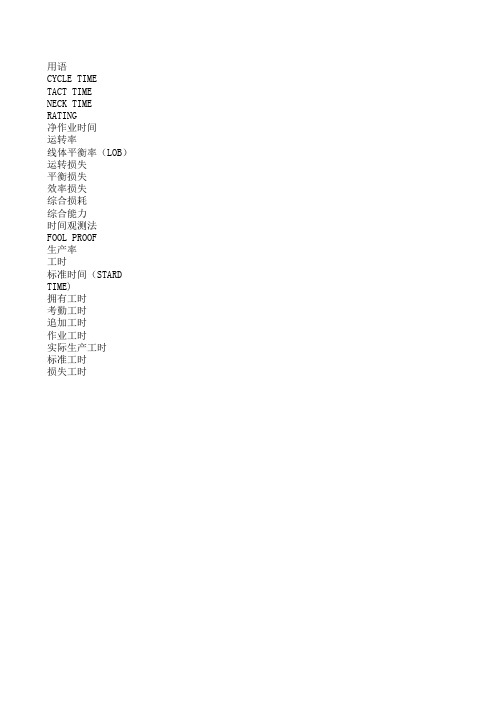
用语CYCLE TIMETACT TIMENECK TIMERATING净作业时间运转率线体平衡率(LOB)运转损失平衡损失效率损失综合损耗综合能力时间观测法FOOL PROOF生产率工时标准时间(STARD TIME)拥有工时考勤工时追加工时作业工时实际生产工时标准工时损失工时详细说明每单位工序中1个循环的作业所需的时间制造一件物品时所需要的实际时间整个工序中1个循环作业时间最长的工序时间作业按标准方法进行时作作业素的快或慢的程度用数字进行换算的时间作业按标准方法进行时所需的最少时间生产产品所需的时间及实际生产中所用的时间之比表示作业人员之间作业要素间平衡程度的值生产产品所需的时间和实际所用的时间之比作业人员之间由于作业量的不公平导致的作业要素时间的不均衡程度的比按标准方法进行作业时需要的最少时间和与实际作业中所用的时间只差的比损耗的总合计按标准方法进行作业时需要的最少时间和与实际生产所用的时间只差的比用秒表观测分析作业人员的作业时间或设备运转的方法作业人员或设备上装上无需小心作业也绝不出错的防止出错装置一般用产量对投入的比人或机器能做的或已做的量用时间来表示熟练程度和技能都达到平均水平的作业人员用正常速度按规定的作业条件和作业方法生产出规定质量的拥有人员的工时实际上没投入到作业的工时(缺勤、休假、出差、支援等)正常出勤工时以外追加作业的工时,即加班,特殊出勤,接受支援等投入到作业中的总工时作业工时中去掉损失工时,实际投入到作业的工时规定的生产中投入到标准时间的合计公式单位工序C/T的和测试次数作业时间(460分)生产数最大的CYCLE TIME很快:125%;快:100%;一般:85%;慢:60%CYCLE TIME*RATING(%)(NECK TIME/TACT TIME)*100(整个工序C/T的和/(NECK TIME*工序数))*100(TACK TIME-NECK TIME)/TACT TIME*100(NECK TIME-CYCLE TIME)/TACT TIME*100(CYCLE TIME -净作业时间/TACT TIME)*100运转损失+平衡损失+效率损失净作业时间/TACT TIME*100OUT PUT/IN PUT业条件和作业方法生产出规定质量的产品一个单位时所需要的时间。
39个精益管理术语,都在这里了...
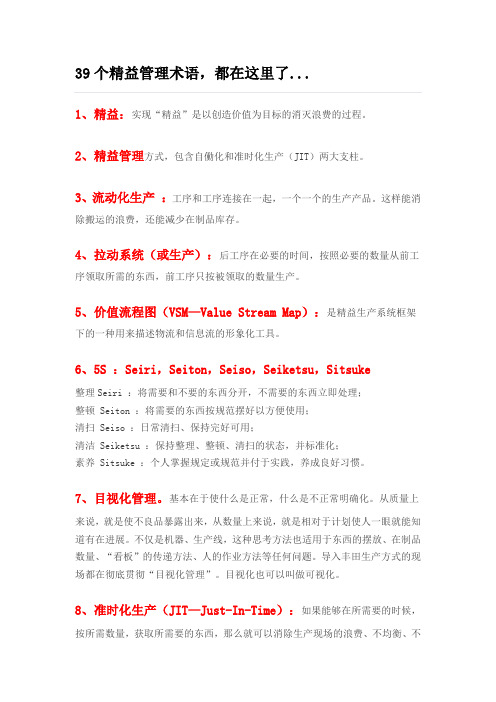
39个精益管理术语,都在这里了...1、精益:实现“精益”是以创造价值为目标的消灭浪费的过程。
2、精益管理方式,包含自働化和准时化生产(JIT)两大支柱。
3、流动化生产:工序和工序连接在一起,一个一个的生产产品。
这样能消除搬运的浪费,还能减少在制品库存。
4、拉动系统(或生产):后工序在必要的时间,按照必要的数量从前工序领取所需的东西,前工序只按被领取的数量生产。
5、价值流程图(VSM—Value Stream Map):是精益生产系统框架下的一种用来描述物流和信息流的形象化工具。
6、5S :Seiri,Seiton,Seiso,Seiketsu,Sitsuke整理Seiri :将需要和不要的东西分开,不需要的东西立即处理;整顿 Seiton :将需要的东西按规范摆好以方便使用;清扫 Seiso :日常清扫、保持完好可用;清洁 Seiketsu :保持整理、整顿、清扫的状态,并标准化;素养 Sitsuke :个人掌握规定或规范并付于实践,养成良好习惯。
7、目视化管理。
基本在于使什么是正常,什么是不正常明确化。
从质量上来说,就是使不良品暴露出来,从数量上来说,就是相对于计划使人一眼就能知道有在进展。
不仅是机器、生产线,这种思考方法也适用于东西的摆放、在制品数量、“看板”的传递方法、人的作业方法等任何问题。
导入丰田生产方式的现场都在彻底贯彻“目视化管理”。
目视化也可以叫做可视化。
8、准时化生产(JIT—Just-In-Time):如果能够在所需要的时候,按所需数量,获取所需要的东西,那么就可以消除生产现场的浪费、不均衡、不合理,提高生产效率。
该思想的开山鼻祖是丰田汽车的创始人-丰田喜一郎,其后继者将此思想展开,概括成为了一个生产体系。
不单是in time, 而是just in time,这是一个重要的关键。
“Just-In-Time”和“自働化”共同形成丰田生产方式的两大支柱。
9、自働化(Jidoka):在丰田的生产方式当中,必须完全是带人字旁的“自働化”。
品质方法中5m1e是指
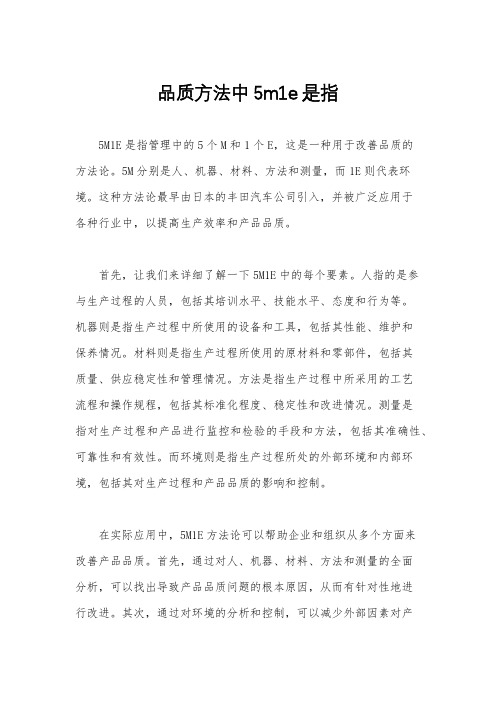
品质方法中5m1e是指5M1E是指管理中的5个M和1个E,这是一种用于改善品质的方法论。
5M分别是人、机器、材料、方法和测量,而1E则代表环境。
这种方法论最早由日本的丰田汽车公司引入,并被广泛应用于各种行业中,以提高生产效率和产品品质。
首先,让我们来详细了解一下5M1E中的每个要素。
人指的是参与生产过程的人员,包括其培训水平、技能水平、态度和行为等。
机器则是指生产过程中所使用的设备和工具,包括其性能、维护和保养情况。
材料则是指生产过程所使用的原材料和零部件,包括其质量、供应稳定性和管理情况。
方法是指生产过程中所采用的工艺流程和操作规程,包括其标准化程度、稳定性和改进情况。
测量是指对生产过程和产品进行监控和检验的手段和方法,包括其准确性、可靠性和有效性。
而环境则是指生产过程所处的外部环境和内部环境,包括其对生产过程和产品品质的影响和控制。
在实际应用中,5M1E方法论可以帮助企业和组织从多个方面来改善产品品质。
首先,通过对人、机器、材料、方法和测量的全面分析,可以找出导致产品品质问题的根本原因,从而有针对性地进行改进。
其次,通过对环境的分析和控制,可以减少外部因素对产品品质的影响,提高生产过程的稳定性和可控性。
此外,通过对5M1E各要素之间的关系和相互影响的分析,可以找出改进产品品质的关键点和突破口,从而更加有效地进行改进和优化。
在实际操作中,应用5M1E方法论需要注意以下几点。
首先,要充分发挥团队的作用,通过团队合作和协作,共同分析和解决产品品质问题。
其次,要注重数据的收集和分析,通过数据来客观评价产品品质的状况和改进效果。
同时,还要注重标准化和持续改进,不断提高产品品质管理的水平和效果。
最后,要注重全员参与,通过全员参与来推动产品品质管理的深入开展和持续改进。
总的来说,5M1E方法论是一种简单而有效的品质改进方法,可以帮助企业和组织从多个方面来提高产品品质。
通过对人、机器、材料、方法、测量和环境的全面分析和改进,可以有效地提高产品品质管理的水平和效果,从而更好地满足客户的需求和要求。
精益生产术语汇总
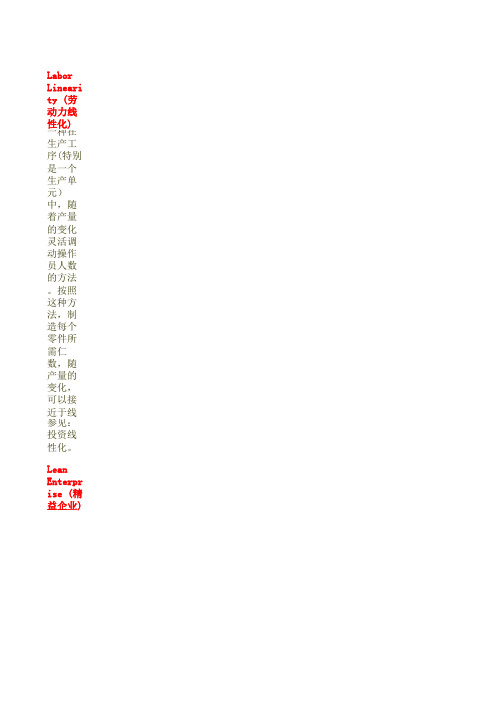
Product ion Analysi s Board (生产分 析 通常板是) 一块置 于生产 工序旁 边的白 板,用 来显示 实际操 作与计 划的对 比 图。例是 一个工 序计划 和实际 产量的 对比。 当实际 产量与 计划不 符时, 问题与 发现的 原因都 记录下 来。
生产分 析板是 一个重 要的可 视化管 理工 具,特 别对那 些刚开 始走向 精益转 化的公 司。然 而,更 重要的 是,生 产分析 板是一 个发现 问题和 解决问 题的工 具,而 不是用 来安排 生产的 工具。 生 参产见分: Plan, Do, Check, Act(计 划,实 施,检 查,行 动)
参见: Heijunk a(均衡 化), Heijunk a Box (生产 均衡 柜), JustIn-Time (及时 生产), PullProduct ion(拉 动生 产), Superma rket (库存
Kaizen Worksho p (改善 研 一系习列会) 的改进 活动, 通常持 续5天, 由一个 小组发 起并实 施 一。个常 见的例 子是在 一周内 创造一 个连续 流工作 单元。 为了实 现这个 目标, 一个持 续改善 小组— —包括 专家、 顾问、 操作 员,以 及生产 线经理 ——进 行分析 、实施 、测 试,以 及在新 的单元
Superma rket Pull System (库存超 市拉动 系 这是统最) 基本、 使用最 广泛的 类型, 有时也 称为“ 填补 ”,或 “a型” 拉动系 统。在 库存超 市拉动 系统 中,每 个工序 都有一 个库存 超市— —来存 放它制 造的产 品。每 个工序 只需要 补足从 它的库
由于每 个工序 都要负 责补充 自己的 库存超 市,因 此每天 工作现 场的管 理就相 对变得 简单起 来,而 且改进 的机会 也就更 明显了 。各个 工序间 库存超 市有一 个缺 点,那 就是每 个工序 必须承 担它所
精益管理专业术语-E系列
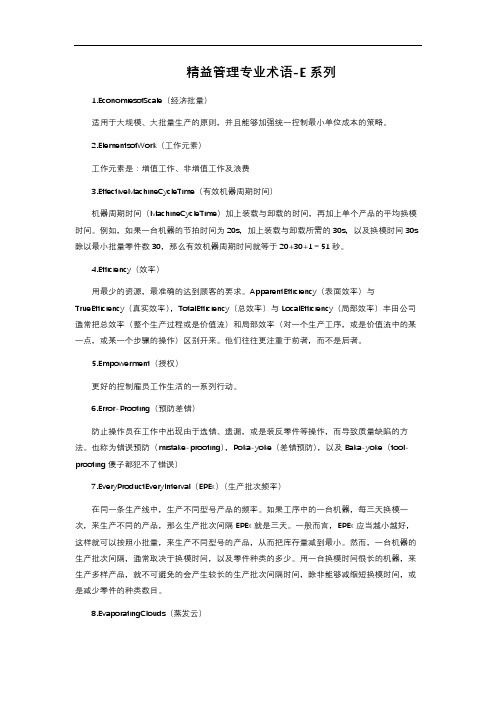
精益管理专业术语-E系列1.EconomiesofScale(经济批量)适用于大规模、大批量生产的原则,并且能够加强统一控制最小单位成本的策略。
2.ElementsofWork(工作元素)工作元素是:增值工作、非增值工作及浪费3.EffectiveMachineCycleTime(有效机器周期时间)机器周期时间(MachineCycleTime)加上装载与卸载的时间,再加上单个产品的平均换模时间。
例如,如果一台机器的节拍时间为20s,加上装载与卸载所需的30s,以及换模时间30s 除以最小批量零件数30,那么有效机器周期时间就等于20+30+1=51秒。
4.Efficiency(效率)用最少的资源,最准确的达到顾客的要求。
ApparentEfficiency(表面效率)与TrueEfficiency(真实效率),TotalEfficiency(总效率)与LocalEfficiency(局部效率)丰田公司通常把总效率(整个生产过程或是价值流)和局部效率(对一个生产工序,或是价值流中的某一点,或某一个步骤的操作)区别开来。
他们往往更注重于前者,而不是后者。
5.Empowerment(授权)更好的控制雇员工作生活的一系列行动。
6.Error-Proofing(预防差错)防止操作员在工作中出现由于选错、遗漏,或是装反零件等操作,而导致质量缺陷的方法。
也称为错误预防(mistake-proofing),Poka-yoke(差错预防),以及Baka-yoke(fool-proofing傻子都犯不了错误)7.EveryProductEveryInterval(EPEx)(生产批次频率)在同一条生产线中,生产不同型号产品的频率。
如果工序中的一台机器,每三天换模一次,来生产不同的产品,那么生产批次间隔EPEx就是三天。
一般而言,EPEx应当越小越好,这样就可以按照小批量,来生产不同型号的产品,从而把库存量减到最小。
oee术语
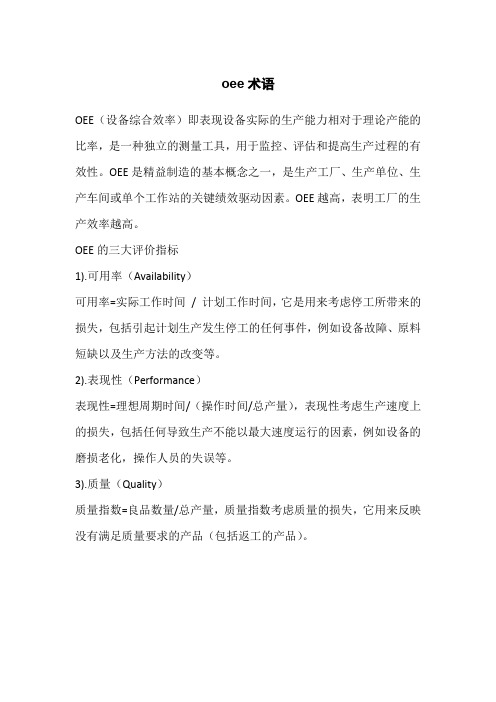
oee术语
OEE(设备综合效率)即表现设备实际的生产能力相对于理论产能的比率,是一种独立的测量工具,用于监控、评估和提高生产过程的有效性。
OEE是精益制造的基本概念之一,是生产工厂、生产单位、生产车间或单个工作站的关键绩效驱动因素。
OEE越高,表明工厂的生产效率越高。
OEE的三大评价指标
1).可用率(Availability)
可用率=实际工作时间/ 计划工作时间,它是用来考虑停工所带来的损失,包括引起计划生产发生停工的任何事件,例如设备故障、原料短缺以及生产方法的改变等。
2).表现性(Performance)
表现性=理想周期时间/(操作时间/总产量),表现性考虑生产速度上的损失,包括任何导致生产不能以最大速度运行的因素,例如设备的磨损老化,操作人员的失误等。
3).质量(Quality)
质量指数=良品数量/总产量,质量指数考虑质量的损失,它用来反映没有满足质量要求的产品(包括返工的产品)。
精益生产单词翻译

精益生产单词翻译OEE(Overall Equipment Effectiveness)--- 全局设备效率OEE = (Running time / Loading time) x (Actual Output / Theoretical output) x (Good Output / Actual out put)世界级企业的全局设备效率OEE为85%或者更好。
大多数企业的设备OEE运行在13% 到40%之间。
Labor Linearity 劳动力线性化一种在生产工序特别是一个生产单元中,随着产量的变化灵活调动操作员人数的方法。
按照这种方法,制造每个零件所需仁数,随产量的变化,能够接近于线性。
Lean Enterprise 精益企业一个产品系列价值流的不一致部门同心协力消除浪费,同时按照顾客要求,来拉动生产。
这个阶段性任务一结束,整个企业立即分析结果,并启动下一个改善计划。
Lean Production 精益生产一种管理产品开发、生产运作、供应商、与客户关系的整个业务的方法。
与大批量生产系统形成对比的是,精益生产强调以更少的人力,更少的空间,更少的投资,与更短的时间,生产符合顾客需求的高质量产品。
精益生产由丰田公司在第二次世界大战之后首创,到1990年的时候,丰田公司只需要用原先一半的人力,一半的制造空间与投入资金,生产相同数量的产品。
在保证质量与提高产量的同时,他们所花费的在产品开发与交货的时间,也远比大批量生产更有效益。
“精益生产”这个术语由MIT国际机动车辆项目的助理研究员John Krafcik于20世纪80年代最先提出。
Lean Logistics 精益物流在沿着价值流的各个公司与工厂之间,建立一个能够经常以小批量进行补给的拉动系统。
我们假设A公司一个零售商直接向顾客销售产品,而且从B公司一个制造商大批量、低频率的补给货物。
精益物流将会在零售商A公司安装一个拉动信号,当他售出若干的货物之后,这个信号就会提示制造商,补充相同数量的货物给A,同时制造商会提示他的供应商补充相同数量的原料或者半成品,以此一直向价值流的上游追溯。
精益术语-IE
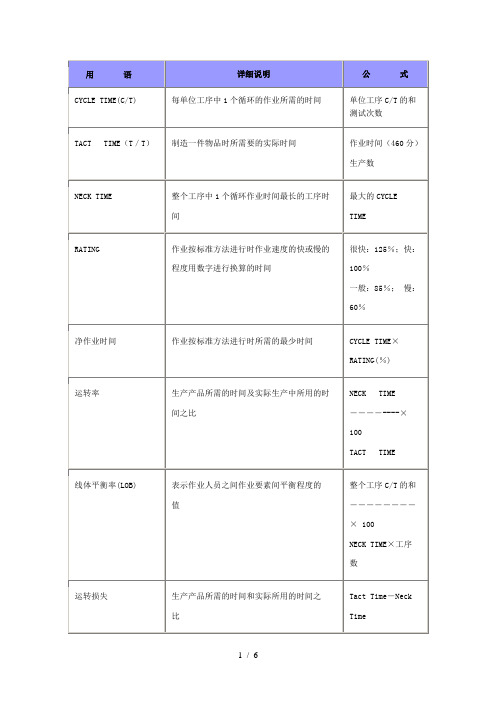
* 作业效率
标准工时
可用工时-损失工时
MTM (Motion-Time Measurement Or Methods-Time Measurement)
所有作业用基本动作来分析,根据指定的基本动作的性格和条件提前给予时间的方法
TMU (time-measurement unit)
给予基本动作的时间值的单位
1分=1.667TMU
1秒=27.8TMU
R.W.F (Ready-Work Facfor)
所有动作分八个基本要素,每执行一个要素动作时根据动作的困难决定W/F数,根据时间表计算净作业时间的方法
1RU=0.001分
基本动作分析法
利用科学家研究出来的17个动作符号测试作业动作时尽量以最小单位来分割的方法
-----------×100
TACT TIME
效率损失
按标准方法进行作业时需要的最少时间和与实际作业中所用的时间之差的比
Cycle Time-净作业时间
-----------×100
TACT TIME
综合损耗
损耗的总合计
运转损失+平衡损失+效率损失
综合能力
按标准方法进行作业时需要的最少时间和与实际生产所用的时间之差的比
很快:125%;快:100%
一般:85%; 慢:60%
净作业时间
作业按标准方法进行时所需的最少时间
CYCLE TIME×RATING(%)
运转率
生产产品所需的时间及实际生产中所用的时间之比
NECK TIME
--------× 100
TACT TIME
线体平衡率(LOB)
表示作业人员之间作业要素间平衡程度的值
精益生产管理中的常见术语(一)
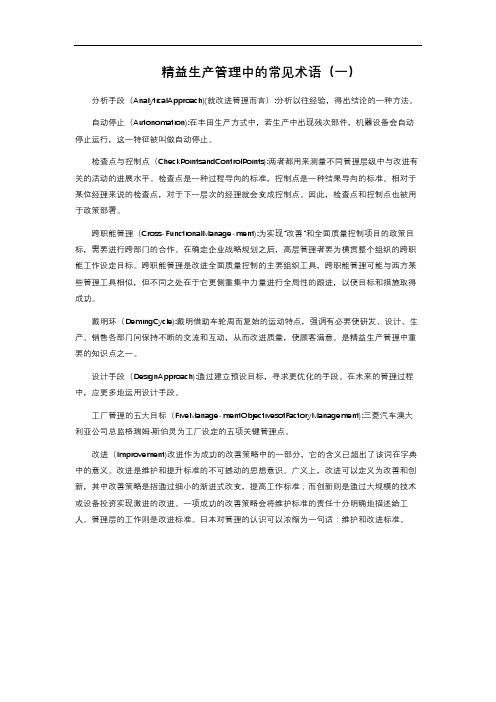
精益生产管理中的常见术语(一)分析手段(AnalyticalApproach)(就改进管理而言):分析以往经验,得出结论的一种方法。
自动停止(Autonomation):在丰田生产方式中,若生产中出现残次部件,机器设备会自动停止运行,这一特征被叫做自动停止。
检查点与控制点(CheckPointsandControlPoints):两者都用来测量不同管理层级中与改进有关的活动的进展水平。
检查点是一种过程导向的标准,控制点是一种结果导向的标准。
相对于某位经理来说的检查点,对于下一层次的经理就会变成控制点。
因此,检查点和控制点也被用于政策部署。
跨职能管理(Cross-FunctionalManage-ment):为实现“改善”和全面质量控制项目的政策目标,需要进行跨部门的合作。
在确定企业战略规划之后,高层管理者要为横贯整个组织的跨职能工作设定目标。
跨职能管理是改进全面质量控制的主要组织工具,跨职能管理可能与西方某些管理工具相似,但不同之处在于它更侧重集中力量进行全局性的跟进,以使目标和措施取得成功。
戴明环(DemingCycle):戴明借助车轮周而复始的运动特点,强调有必要使研发、设计、生产、销售各部门间保持不断的交流和互动,从而改进质量,使顾客满意。
是精益生产管理中重要的知识点之一。
设计手段(DesignApproach):通过建立预设目标,寻求更优化的手段。
在未来的管理过程中,应更多地运用设计手段。
工厂管理的五大目标(FiveManage-mentObjectivesofFactoryManagement):三菱汽车澳大利亚公司总监格瑞姆·斯伯灵为工厂设定的五项关键管理点。
改进(Improvement)改进作为成功的改善策略中的一部分,它的含义已超出了该词在字典中的意义。
改进是维护和提升标准的不可撼动的思想意识。
广义上,改进可以定义为改善和创新,其中改善策略是指通过细小的渐进式改变,提高工作标准;而创新则是通过大规模的技术或设备投资实现激进的改进。
精益生产专业名词解释
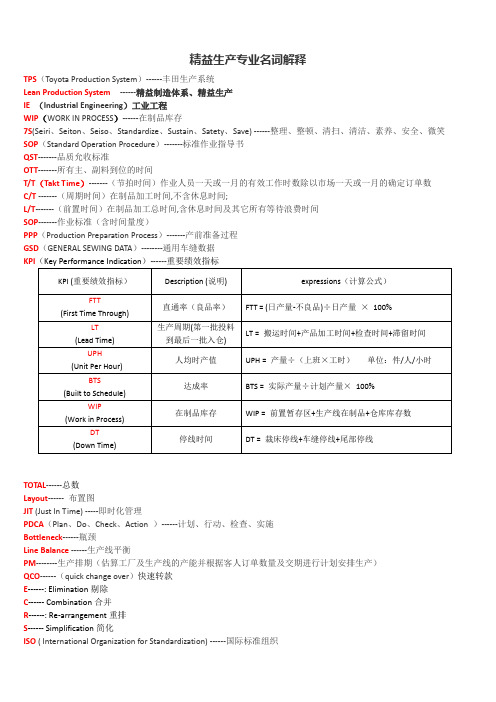
精益生产专业名词解释TPS(Toyota Production System)------丰田生产系统Lean Production System ------精益制造体系、精益生产IE (Industrial Engineering)工业工程WIP(WORK IN PROCESS)------在制品库存7S(Seiri、Seiton、Seiso、Standardize、Sustain、Satety、Save) ------整理、整顿、清扫、清洁、素养、安全、微笑SOP(Standard Operation Procedure)-------标准作业指导书QST-------品质允收标准OTT-------所有主、副料到位的时间T/T(Takt Time)-------(节拍时间)作业人员一天或一月的有效工作时数除以市场一天或一月的确定订单数C/T -------(周期时间)在制品加工时间,不含休息时间;L/T-------(前置时间)在制品加工总时间,含休息时间及其它所有等待浪费时间SOP-------作业标准(含时间量度)PPP(Production Preparation Process)-------产前准备过程GSD(GENERAL SEWING DATA)--------通用车缝数据KPITOTAL------总数Layout------ 布置图JIT (Just In Time) -----即时化管理PDCA(Plan、Do、Check、Action )------计划、行动、检查、实施Bottleneck------瓶颈Line Balance ------生产线平衡PM--------生产排期(估算工厂及生产线的产能并根据客人订单数量及交期进行计划安排生产)QCO------(quick change over)快速转款E------: Elimination剔除C------ Combination合并R------: Re-arrangement重排S------ Simplification简化ISO ( International Organization for Standardization) ------国际标准组织WF (Work factor system) -----工作因素法FMS (Flexible Manufacture System) ------弹性制造系统TPM(Total Production Management)------全面生产管理TQM(Total Quality Management)------全面品质管理QE (quality engineering)------ 品质工程人员QIT(Quality Improvement Team)------ 品质改善小组CAM(Computer-aided-manufacturing)------计算机辅助制造CAD(Computer-aided-design)------计算机辅助设计CAE(Computer-aided-engineering)------计算机辅助工程CAPP(Computer-aided-process planning)------计算机辅助工艺编制BMS(Basic motion study)------基本动作世界研究法ABC分类法------ ABC Classing MethodPC(Production control)------生管QCC(Quality Control Circle)------品管圈QE(Quality Engineering) ------品质工程。
精益管理专业术语
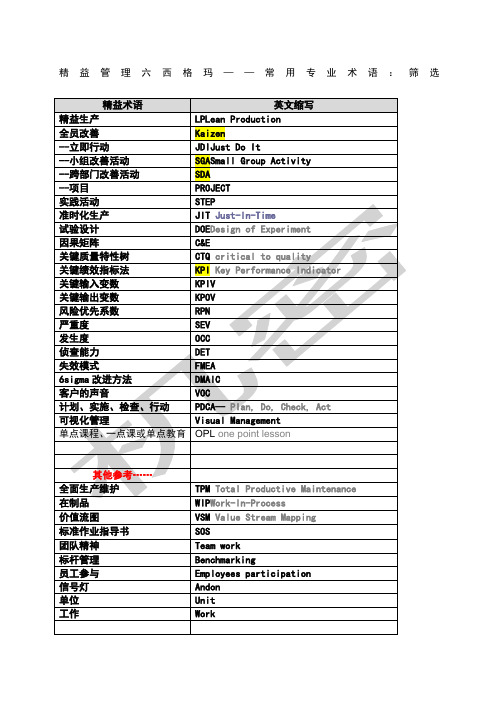
精益管理六西格玛——常用专业术语:筛选根据精益学习情况可随时补充专业术语什么是六西格玛西格玛大写Σ,小写σ是希腊文的字母,其小写“σ”在统计学中称为标准差;在六西格玛方法中,用来表示过程的质量水平,其中4σ=6210 /百万,5σ=230/百万,6σ=3.4/百万;一般企业的产品瑕疵率大约是3~4σ,以4σ而言,相当于每一百万个机会里有6210次误差;如果企业不断改进流程,达到6σ的程度,即在一百万个机会里只找得出3.4个瑕疪,这样的绩效已经近于完美;六西格玛作为流程改进方法论,最早是由摩托罗拉公司的比尔·史密斯于1986年提出,于20世纪90年代通过通用电气公司的实践得以发展和完善;它通过精确的数理统计和分析,找出影响质量的因素并解决问题,力求使产品和服务的质量接近6σ水平;随着实践的经验积累,六西格玛现在已不仅仅是一个衡量业务流程能力的标准和业;;;,5S管理:五个都以“S”开头的相关术语,用来描述可视化控制,及精益生产的现场操作;在日语里这五个术语是:——整理Seiri:从必要的项目¬——工具,零件,材料,文件中分离,并丢弃那些不必要的东西——整顿Seiton:整洁地布置工作区域,把所有东西放到它们应该在的位置上——清扫Seiso:打扫与清洗——清洁Seitetsu:常规性的执行前三个S所导致的清洁——纪律Shitsuke:执行前四个S的纪律Seven Wastes 七种浪费把大规模制造方法的浪费划分成七个主要类别:1.过量生产:制造多于下一个工序,或是顾客需求的产品;这是浪费形式中最严重的一种,因为它会导致其它六种浪费2.等待:在生产周期中,操作员空闲的站在一旁;或是设备失效;或是需要的零部件没有运到等3.搬运:不必要的搬运零件和产品,例如两个连续的生产工序,将产品在完成一个工序后,先运到仓库,然后再运到下一个工序;较理想的情况是让两个工序的位置相邻,以便使产品能够从一个工序立即转到下一个工序4.返工:进行不必要的修正加工,通常是由于选用了较差的工具或产品缺陷而导致生产分析板问题解决板 Production Analysis Board生产控制 Production Control生产准备过程3P Production Preparation Process标准库存 Standard Inventory自动化Jidoka标准化操作Standardized Work标准化操作表Standardized Work Chart标准化操作组合表Standardized Work Combination Table产品系列矩阵Product Family Matrix政策实施Policy Deployment为每个产品做计划PFEP Plan For Every Part单位制造时间Pitch产品的先进先出FIFO First In, First Out停工期 Downtime节拍时间 Takt Time库存超市 Supermarket库存超市拉动系统 Supermarket Pull System拉动生产 Pull Production库存Inventory安全库存Safety Stock:在任何工位上存放的货物原材料,在制品,或成品,用来预防因为上游工序生产能力不足,导致的缺货、断货的问题;通常也称为紧急库存;装运库存Shipping Stock:在价值流末端工厂的库房里,那些已经准备好可以随时下一次出货的产品这些库存通常是装运批量的一部分;在制品WIP Work-in-Process:工厂内各个工序之间的半成品;在精益系统里,标准的在制品数量,是指能够保证价值流在生产单元内,平稳流动所需要的最少的数量;。
品质方法中5m1e是指

品质方法中5m1e是指5M1E是指管理中的5个M和1个E,其中M代表了5个英文单词,分别是Manpower(人力资源)、Machinery(机械设备)、Materials(原材料)、Methods(方法)和Measurement(测量),而E代表了Environment(环境)。
这个概念最初是由日本的丰田汽车公司提出的,是丰田汽车公司在管理实践中的一种重要方法。
首先,我们来了解一下5M1E的具体含义。
在生产过程中,人力资源、机械设备、原材料、方法和测量是非常重要的因素,它们直接影响着产品的质量。
而环境因素则是这些因素之间的相互作用和影响,它也会对产品的质量产生重要的影响。
因此,5M1E方法就是通过对这些因素进行全面的管理和控制,以确保产品的质量达到标准要求。
其次,我们来分别介绍一下5个M和1个E的具体内容。
首先是人力资源,这是指企业中的员工,他们的素质、技能、工作态度等都会直接影响产品的质量。
其次是机械设备,好的机械设备能够提高生产效率,保证产品的质量稳定。
再者是原材料,原材料的质量直接关系到产品的质量,因此对原材料的选择和管理非常重要。
然后是方法,生产过程中的方法和流程对产品的质量也有着重要的影响,因此需要进行科学的管理和控制。
最后是测量,对产品质量的测量和监控是保证产品质量的重要手段。
而环境因素则是指生产环境和外部环境对产品质量的影响,需要进行全面的管理和控制。
在实际应用中,5M1E方法可以帮助企业全面提高产品的质量。
通过对人力资源、机械设备、原材料、方法和测量的全面管理和控制,可以有效地提高产品的质量稳定性和一致性。
同时,对环境因素的管理也能够减少外部因素对产品质量的影响,保证产品质量达到标准要求。
总的来说,5M1E方法是一种非常重要的管理方法,它能够帮助企业全面提高产品的质量。
通过对人力资源、机械设备、原材料、方法和测量的全面管理和控制,以及对环境因素的管理,可以有效地提高产品的质量稳定性和一致性,从而满足客户的需求,提升企业的竞争力。
oo现场IE(精益)
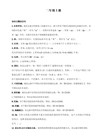
9
放 于 栈 板
10
用 叉 车 运
平均活性指数=
0+3+4+0+3+4+3+4+2+4 10
= 2.7
工程分析
流动数分析
入库累计从月初的保有量开始记录,出库累计从原始点开始 记录,从图中可以看出出库累差距计线和入库累计线的纵向 差距为停滞数量,横向差距为停滞时间 流动数分析图表
数 量 千
8 7 6 5 4 3 2 1
1)发现并消除作业性能底下的损耗时间和非运转损耗时间; 2)测试各种作业方法的优劣后,改善作业方法、工器具、设备等等; 3)评价设计及制造方式的改善程度; 4)作业人员培训的基础水平及评价 5)测试作业人员、监督人员的成果,并进行评价。 6)作好流水线作业等的作业量平衡.
标准时间的应用-计划
1)作为生产计划的基础(制造能力) 2)作为日程计划的基础(制造日程) 3)作为人员计划、加班计划、设备计划的基础 4)作为设定标准成本、成本报价等 5)外协单价的决定
工程分析
工程 着眼点
工程改善着眼点
工程 全部
1)纵观整个工程所需时间,搬运距离及人数 和各工序所需时间,搬运距离与人数时, 将改善的重点放在何处 2) 可省略的工序是哪个 3)有没有可同时进行的工序 4)有没有将工序顺序交换,来减少工序数,时 间,人员的可能性 5)是不是认为现在的工序是最好的工序
精益生产专业名词解释

精益生产专业名词解释TPS(Toyota Production System)------丰田生产系统IE (Industrial Engineering)工业工程WIP(WORK IN PROCESS)------在制品库存7S(Seiri、Seiton、Seiso、Standardize、Sustain、Satety、Save) ------整理、整顿、清扫、清洁、素养、安全、微笑SOP(Standard Operation Procedure)-------标准作业指导书T/T(Takt Time)-------(节拍时间)作业人员一天或一月的有效工作时数除以市场一天或一月的确定订单数C/T -------(周期时间)在制品加工时间,不含休息时间;L/T-------(前置时间)在制品加工总时间,含休息时间及其它所有等待浪费时间MCT------设备自动加工时间(自设备启动开始,到设备完全停止为止)SOP-------作业标准(含时间量度)KPI(Key Performance Indication)------重要绩效指JIT (Just In Time) -----即时化管理PDCA(Plan、Do、Check、Action )------计划、行动、检查、实施Bottleneck------瓶颈Line Balance ------生产线平衡TPM(Total Production Management)------全面生产管理TQM(Total Quality Management)------全面品质管理QE (quality engineering)------ 品质工程人员QIT(Quality Improvement Team)------ 品质改善小组CAM(Computer-aided-manufacturing)------计算机辅助制造CAD(Computer-aided-design)------计算机辅助设计CAE(Computer-aided-engineering)------计算机辅助工程CAPP(Computer-aided-process planning)------计算机辅助工艺编制QCC(Quality Control Circle)------品管圈QE(Quality Engineering) ------品质工程。
质量管理常用术语E

质量管理常用术语E【E】EC Engineer Change 设计变更/工程变更EC Electronic Commerce 电子商务EMC Electric Magnetic Capability 电磁相容EOQ Economic Order Quantity 基本经济订购量ERP Enterprise Resource Planning 企业资源规划ECN Engineering Change Notice 工程变更通知(供货商) ECO Engineering Change Order 工程改动要求(客户) ERS External Reference Spec 外部规格ERP Enterprise Resource Programming 企业资源项目ES Engineering Standard 工程标准E-MAIL Electrical-Mail 电子邮件EAR Engineering Analysis Request 工程分析要求EV Equipment Variation 设备变异ES Engineering Standardization 工程标准Environmental 环境Equipment 设备Effectiveness 有效性Efficiency 效率Element 元素Else 否则Engineering technology 工程技术Entropy 函数Estimated accumulative frequency 计算估计累计数External Failure 外部失效,外部缺陷Event 事件【F】FMEA Failure Mode and Effect analysis 失效模式与效果分析FA Failure Analysis 不良分析FQA Final Quality Assurance 最终品质保证FQC Final Quality control 最终品质控制FAI first article inspection 首件检查FAA first article assurance 首件确认FPIR First Piece Inspection Report 首件检查报告F/T Function Test 功能测试FMS Flexible Manufacture System 弹性制造系统FQC Finish or Final Quality Control 成品质量管理FGI Finished goods Inventory 成品存货FTA Fault Tree Analysis 故障树分析FREQ Frequency 频率FIN Finance 财务Fix OH Fix Overhead 固定管理费用Finance Accounting 财务账目Failure rate 故障率Fact control 事实管理FPY 合格率Full-steer 完全转向function 职能【G】GS General Specification 一般规格GRR Gauge Reproducibility & Repeatability 量具之再制性及重测性判断量测可靠与否Gauge system 量测系统Grade 等级General Affair 总务【H】H/W hardware 硬件H/T High Temperature Test 高温测试HQ Headquarter 总公司HR Human Resource 人力资源部Histogram 直方图Hypothesis testing 假设检定Health meter 体重计Heat press 冲压粘着Hi-tech 高科技【I】IMD Image Management Division 影像管理事业部ITS Information Technology System 计算机部IPQC In Process Quality Control 制程品质控制IQC Incoming Quality Control 来料品质控制IWS International Workman Standard 工艺标准ISO International Standard Organization 国际标准化组织IS Inspection Specification 成品检验规范IE Industrial Engineering 工业工程ID/C Identification Code (供货商)识别码ID Industrial Design 工业设计(外观设计)IS Information System 资讯系统IT Information Technology 系统技术ISAR Initial Sample Approval Request 首批样品认可I/O input/output 输入/输出Improvement 改善Inductance 电感Information 信息Initial review 先期审查Inspection 检验Internal Failure 内部失效,内部缺陷Interested party 相关方Infrastructure 基础设施Inspection 检验【J】JIT Just In Time 实时管理JQE Joint Quality Engineer 客服工程师【L】LCL Lower Control limit 管制下限LQC Line Quality Control 生产线品质控制LQL Limiting Quality Level 最低品质水准L/T Lead Time 前置时间(生产前准备时间)LRR Lot Reject Rate 批退率LSL Lower Size Limit 规格下限L/T Low Temperature Test 低温测试L/N Lot Number 批号LAB Laboratory 实验室LPCL Lower Per-control Limit 前置管制下限Love 爱心Link 连接Life Test 寿命测试Law of large number 大数法则【M】MSA Measurement System Analysis 量测系统分析MPS Mass Production Schedule 量产计划MTF Modulation Transfer Function 调整转换功能MC Material Control 物料控制MVT Mass Verification Test 多项验证测试MIL-STD Military Standard 军用标准MIS Management Information System 管理资讯系统MTBF Mean Time Between Failure 平均故障间隔MAJ Major 主要的MIN Minor 轻微的MIN Minimum 最小值MAX Maximum 最大值MQA Manufacture Quality Assurance 制造品质保证MRP Material Requirement Planning 物料需求计划MRB Material Review Board 物料评审委员会MRB Material Reject Bill 退货单MO Manufacture Order 生产单MFG Manufacturing 制造部MES Manufacturing Execution System 制造执行系统management system 管理体系Materials 物料Measurement 量测management 管理Machine 机械Materials 物料Median 中位数Miss feed 漏送Momentum 原动力Multiplication rule 乘法运算规则。
- 1、下载文档前请自行甄别文档内容的完整性,平台不提供额外的编辑、内容补充、找答案等附加服务。
- 2、"仅部分预览"的文档,不可在线预览部分如存在完整性等问题,可反馈申请退款(可完整预览的文档不适用该条件!)。
- 3、如文档侵犯您的权益,请联系客服反馈,我们会尽快为您处理(人工客服工作时间:9:00-18:30)。
精益管理专业术语-E系列
1.EconomiesofScale(经济批量)
适用于大规模、大批量生产的原则,并且能够加强统一控制最小单位成本的策略。
2.ElementsofWork(工作元素)
工作元素是:增值工作、非增值工作及浪费
3.EffectiveMachineCycleTime(有效机器周期时间)
机器周期时间(MachineCycleTime)加上装载与卸载的时间,再加上单个产品的平均换模时间。
例如,如果一台机器的节拍时间为20s,加上装载与卸载所需的30s,以及换模时间30s 除以最小批量零件数30,那么有效机器周期时间就等于20+30+1=51秒。
4.Efficiency(效率)
用最少的资源,最准确的达到顾客的要求。
ApparentEfficiency(表面效率)与TrueEfficiency(真实效率),TotalEfficiency(总效率)与LocalEfficiency(局部效率)丰田公司通常把总效率(整个生产过程或是价值流)和局部效率(对一个生产工序,或是价值流中的某一点,或某一个步骤的操作)区别开来。
他们往往更注重于前者,而不是后者。
5.Empowerment(授权)
更好的控制雇员工作生活的一系列行动。
6.Error-Proofing(预防差错)
防止操作员在工作中出现由于选错、遗漏,或是装反零件等操作,而导致质量缺陷的方法。
也称为错误预防(mistake-proofing),Poka-yoke(差错预防),以及Baka-yoke(fool-proofing傻子都犯不了错误)
7.EveryProductEveryInterval(EPEx)(生产批次频率)
在同一条生产线中,生产不同型号产品的频率。
如果工序中的一台机器,每三天换模一次,来生产不同的产品,那么生产批次间隔EPEx就是三天。
一般而言,EPEx应当越小越好,这样就可以按照小批量,来生产不同型号的产品,从而把库存量减到最小。
然而,一台机器的生产批次间隔,通常取决于换模时间,以及零件种类的多少。
用一台换模时间很长的机器,来生产多样产品,就不可避免的会产生较长的生产批次间隔时间,除非能够减缩短换模时间,或是减少零件的种类数目。
8.EvaporatingClouds(蒸发云)
一种在约束论中使用的方法,与解决冲突相同。
9.ExternalSetUp(外部设置)
当机器仍然运作时可以做的所有设置动作。