精益管理专业术语-F系列
精益生产常用工具术语
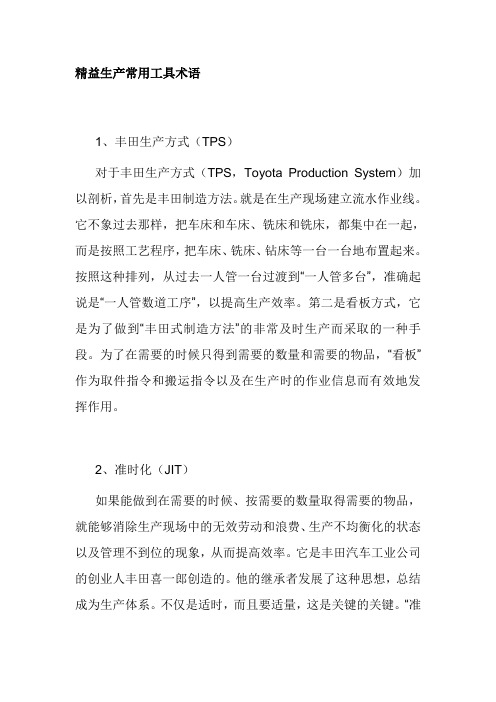
精益生产常用工具术语1、丰田生产方式(TPS)对于丰田生产方式(TPS,Toyota Production System)加以剖析,首先是丰田制造方法。
就是在生产现场建立流水作业线。
它不象过去那样,把车床和车床、铣床和铣床,都集中在一起,而是按照工艺程序,把车床、铣床、钻床等一台一台地布置起来。
按照这种排列,从过去一人管一台过渡到“一人管多台”,准确起说是“一人管数道工序”,以提高生产效率。
第二是看板方式,它是为了做到“丰田式制造方法”的非常及时生产而采取的一种手段。
为了在需要的时候只得到需要的数量和需要的物品,“看板”作为取件指令和搬运指令以及在生产时的作业信息而有效地发挥作用。
2、准时化(JIT)如果能做到在需要的时候、按需要的数量取得需要的物品,就能够消除生产现场中的无效劳动和浪费、生产不均衡化的状态以及管理不到位的现象,从而提高效率。
它是丰田汽车工业公司的创业人丰田喜一郎创造的。
他的继承者发展了这种思想,总结成为生产体系。
不仅是适时,而且要适量,这是关键的关键。
“准时化”(JIT,Just In Time)和下述的“自动化”思想构成了丰田生产方式的两大支柱。
3、自动化(Jidoka)在丰田生产方式中,始终强调必须是带人字旁的“自动化”。
所谓自动化,是将人的智慧赋予机器的意思。
“自动化”这种思想的发端是从丰田公司开山鼻祖--- 丰田佐吉的自动纺织机开始的。
丰田式自动纺织机在经纱断了或纬纱没有了的时候,机器立即停车,也就是装有使机器能判断工作状态好坏的装置。
丰田公司,不仅把这种想法用于机器,而且也扩大到流水线上的操作者。
这就是说,如果发生异常,操作者可以把整个流水线停车。
自动化的优点是,能够防止生产次品,制止过量制造。
此外,还能自动控制生产现场发生的异常现象。
4、目视化管理(VC)在“自动化”(VC,Visual Control)的含义中,包含有这样一种意思,即如果发生异常现象,生产线和机床就立即停车。
精益生产管理常用术语
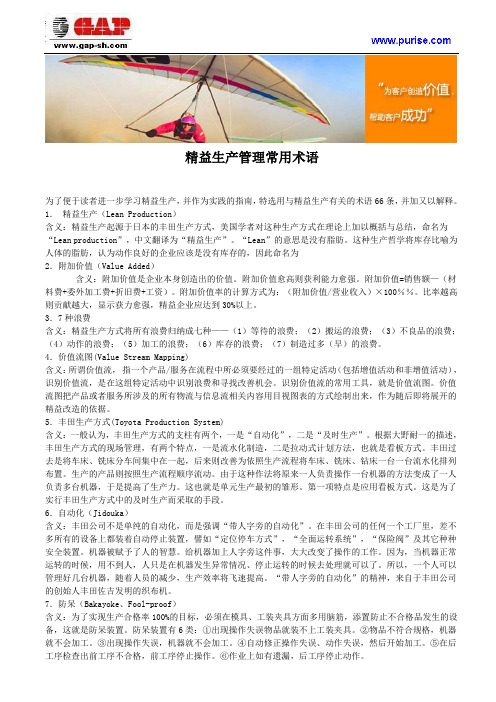
精益生产管理常用术语为了便于读者进一步学习精益生产,并作为实践的指南,特选用与精益生产有关的术语66条,并加又以解释。
1.精益生产(Lean Production)含义:精益生产起源于日本的丰田生产方式,美国学者对这种生产方式在理论上加以概括与总结,命名为“Lean production”,中文翻译为“精益生产”。
“Lean”的意思是没有脂肪。
这种生产哲学将库存比喻为人体的脂肪,认为动作良好的企业应该是没有库存的,因此命名为2.附加价值(Value Added)含义:附加价值是企业本身创造出的价值。
附加价值愈高则获利能力愈强。
附加价值=销售额—(材料费+委外加工费+折旧费+工资)。
附加价值率的计算方式为:(附加价值/营业收入)×100%%。
比率越高则贡献越大,显示获力愈强,精益企业应达到30%以上。
3.7种浪费含义:精益生产方式将所有浪费归纳成七种——(1)等待的浪费;(2)搬运的浪费;(3)不良品的浪费;(4)动作的浪费;(5)加工的浪费;(6)库存的浪费;(7)制造过多(早)的浪费。
4.价值流图(Value Stream Mapping)含义:所谓价值流,指一个产品/服务在流程中所必须要经过的一组特定活动(包括增值活动和非增值活动),识别价值流,是在这组特定活动中识别浪费和寻找改善机会。
识别价值流的常用工具,就是价值流图。
价值流图把产品或者服务所涉及的所有物流与信息流相关内容用目视图表的方式绘制出来,作为随后即将展开的精益改造的依据。
5.丰田生产方式(Toyota Production System)含义:一般认为,丰田生产方式的支柱有两个,一是“自动化”,二是“及时生产”。
根据大野耐一的描述,丰田生产方式的现场管理,有两个特点,一是流水化制造,二是拉动式计划方法,也就是看板方式。
丰田过去是将车床、铣床分车间集中在一起,后来则改善为依照生产流程将车床、铣床、钻床一台一台流水化排列布置。
39个精益管理术语,都在这里了...
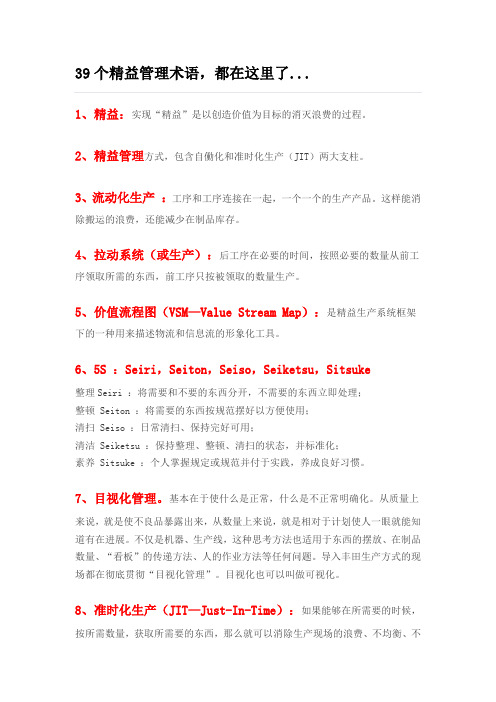
39个精益管理术语,都在这里了...1、精益:实现“精益”是以创造价值为目标的消灭浪费的过程。
2、精益管理方式,包含自働化和准时化生产(JIT)两大支柱。
3、流动化生产:工序和工序连接在一起,一个一个的生产产品。
这样能消除搬运的浪费,还能减少在制品库存。
4、拉动系统(或生产):后工序在必要的时间,按照必要的数量从前工序领取所需的东西,前工序只按被领取的数量生产。
5、价值流程图(VSM—Value Stream Map):是精益生产系统框架下的一种用来描述物流和信息流的形象化工具。
6、5S :Seiri,Seiton,Seiso,Seiketsu,Sitsuke整理Seiri :将需要和不要的东西分开,不需要的东西立即处理;整顿 Seiton :将需要的东西按规范摆好以方便使用;清扫 Seiso :日常清扫、保持完好可用;清洁 Seiketsu :保持整理、整顿、清扫的状态,并标准化;素养 Sitsuke :个人掌握规定或规范并付于实践,养成良好习惯。
7、目视化管理。
基本在于使什么是正常,什么是不正常明确化。
从质量上来说,就是使不良品暴露出来,从数量上来说,就是相对于计划使人一眼就能知道有在进展。
不仅是机器、生产线,这种思考方法也适用于东西的摆放、在制品数量、“看板”的传递方法、人的作业方法等任何问题。
导入丰田生产方式的现场都在彻底贯彻“目视化管理”。
目视化也可以叫做可视化。
8、准时化生产(JIT—Just-In-Time):如果能够在所需要的时候,按所需数量,获取所需要的东西,那么就可以消除生产现场的浪费、不均衡、不合理,提高生产效率。
该思想的开山鼻祖是丰田汽车的创始人-丰田喜一郎,其后继者将此思想展开,概括成为了一个生产体系。
不单是in time, 而是just in time,这是一个重要的关键。
“Just-In-Time”和“自働化”共同形成丰田生产方式的两大支柱。
9、自働化(Jidoka):在丰田的生产方式当中,必须完全是带人字旁的“自働化”。
精益术语

精益术语
三定三要素:定点、定容、定量,场所、方法、标识
三全:全员、全方位、全过程
致胜法宝:
改善,持续改善!
三讲:
讲热情、讲方向、讲方法
三化:
省力化、少人化、自働化
企业文化:
思考、勤奋、忠诚
企业价值观:
1110
企业经营理念:
低成本制造优质产品
四不伤害:
不伤害自己、不伤害他人、不被他人伤害、保护他人不被伤害
四不放过:
事故原因没查清不放过、事故责任者未受到处理不放过、事故责任者和周围群众未受到教育不放过,事故制定切实可行的防范措施未落实不放过
我们的追求:
深入人心的改善哲学,
无处不在的改善文化!。
精益生产术语中英文对照_20150227

序号中文英文1山积图stack diagram2线平衡line balancing3标准作业程序standard operation procedure(SOP) 4客户节拍customer takt time(TT)5节拍cycle time(CT)6换型change over (CO)7前置期lead time8有价值的时间value added time9缓冲buffer10设备综合效率overall equipment efficiency (OEE) 11标准作业票standard work sheet(SWS)12价值流程图value stream mapping (VSM)13价值流设计value stream design(VSD)14批量大小lot size15操作工operator (OP)16多技能工multi-skilled operator17技能矩阵skill metrix18班shift19零件计划plan for every part (PFEP)20防呆poka yoke21牛奶线milkrun22均衡生产leveling23看板Kanban24安灯andon25物料上线点point of use provider (POUP)26先进先出first in first out (FIFO)27在制品库存work in process (WIP)28生产效率productivity29一分钟换模single minute exchange die(SMED) 30持续改善continue improvement(CI)31改善KAIZEN32浪费waste根本原因root cause临时措施temperary action长期措施Long-term action截止日期due date序号No.责任人PIC(person in charge)。
精益生产衡量指标知识

精益生产衡量指标的相关知识精益生产之七个“零”的目标﹕零不良零库存零切换零停滞零故障零伤害零浪费用于业绩度量的三大类指标:基于合格/不合格(计数型数据)的FTY/RTY度量指标;基于缺陷数据(计点型数据)的DPU/DPMO度量指标;基于平均值/标准差(连续型数据)的Z(西格玛水平)。
它们基本覆盖了对产品、服务、商务、管理等所有类型过程的度量。
FPY:First Pass Yield定义为:一次通过率。
(FPY是第一次通过率,一般针对一个工位)(与FTY是一个意思)FTY First Time Yield 首次通过率,就是一次通过检验的合格率,就是第一次就把事情做对,由没有经返工返修就通过的过程输出单位数而计算出的合格率。
生产过程投产1000个单位,第一个子过程产生废品40个单位,返工40个单位,即第一个子过程只有920个单位一次合格。
得到FTY=92%.FTT:First Time Throghut,指首次通过率是指一次性完成一个生产过程并且满足质量要求的零件的百分率,不包括报废,返工,再测试,下线修理或返回。
FTT 用于衡量制造过程的质量。
PFY(process final yield)定义为:最终合格率。
就是过程的最后合格率(不区分是否经过返工)过程最终的合格率通常是指通过检验的合格单位数占过程投产全部单位数的比例。
但是这种质量计算方法不能计算该过程的输出在通过最终检验前发生的返工、返修的损失.(也就是说:将返工后合格的产品也算进合格品率里面去了。
):RTY:Rolled Throughput Yield 当然是全过程通过率了(直通率)。
对一个串行生产过程,假定各过程彼此独立,则其流通合格率等于每个子过程FTY的乘积,表明由这些子过程串联构成的大过程的一次合格率。
一次交验合格率就只看一个环节,而直通率应该把前面环节都考虑。
比如说:一个产品有三个工序来完成,各个环节的合格率都是90%,那么交验合格率应该是90%,而直通率应该是90%*90%*90%=72.9%一般来说交验合格率是指最后一个环节。
品管常用术语

QC: Quality control 品质控制IQC: Incomming quality control 来料品质控制IPQC: In process quality control 制程品质控制FQC: Final quality control 最终品质控制OQC: Outgoing quality control 出货品质控制QA: Quality assurance 品质保证QA: Quality audit 品质稽核QE: Quality engineering 品质工程LQC:Line quality control 生产线品质控制SQA: Source (supplier) quality assurance 供应商品质保证SQC: Statistical quality control 统计品质控制TQC:Total quality control 全面品管DCC: Document control center 文控中心PQA: Process quality assurance 制程品质控制FQA: Final quality assurance 最终品质控制CS: Customer service 客户服务DAS: Defects analysis system 缺陷分析系统FA: Failure analysis 坏品分析CPI:Continuous process improvement 连续工序改善SIP:Standard inspection procedure 检验指导书SOP: Standard operation procedure 作业指导书QCC: Quality control circle 品管圈4M1E: Man\Machine\Material\Method\Environment人/机/料/法/环QCDS: Quality\Cost\Delivery\Service 品质/价格/交期/服务AQL: Acceptable quality level 允收水准IL:Inspection level 检验水平AC: Accept 允收 RE: Reject 拒收CR:Critical 致命的 MA:Major 主要的 MI:Minor 次要的ISO:International organization for standardization 国际标准组织SPC: Statistical Process Control 统计过程控制QSR: Quality system requirements 质量体系要求QS七大手册APQP: Advanced product quality planning and control plan 先期产品质量策划与控制计划FMEA: Potential failure mode and effects analysis潜在失效模式与后果分析MSA: Measurement systems analysis 量测系统分析PPAP: Production part approval process 生产件批准程序QSA: Quality system assessment 质量体系评审TPM:Total prevent maintain 全员预防设备维护Stratification 层别法Check Sheet 查检表QC七大手法Characteristic Diafram 特性要因图Pareto Diafram 柏拉图Seatter Diagram散布图Histogram 直方图Control Chart 管制图。
精益生产管理中的常见术语(一)
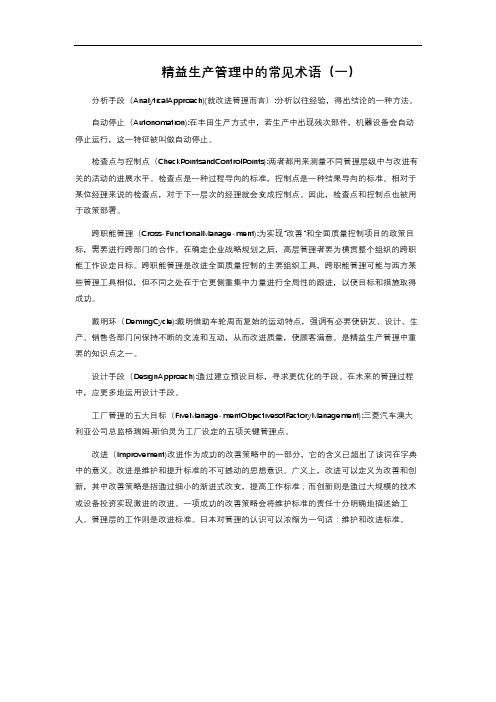
精益生产管理中的常见术语(一)分析手段(AnalyticalApproach)(就改进管理而言):分析以往经验,得出结论的一种方法。
自动停止(Autonomation):在丰田生产方式中,若生产中出现残次部件,机器设备会自动停止运行,这一特征被叫做自动停止。
检查点与控制点(CheckPointsandControlPoints):两者都用来测量不同管理层级中与改进有关的活动的进展水平。
检查点是一种过程导向的标准,控制点是一种结果导向的标准。
相对于某位经理来说的检查点,对于下一层次的经理就会变成控制点。
因此,检查点和控制点也被用于政策部署。
跨职能管理(Cross-FunctionalManage-ment):为实现“改善”和全面质量控制项目的政策目标,需要进行跨部门的合作。
在确定企业战略规划之后,高层管理者要为横贯整个组织的跨职能工作设定目标。
跨职能管理是改进全面质量控制的主要组织工具,跨职能管理可能与西方某些管理工具相似,但不同之处在于它更侧重集中力量进行全局性的跟进,以使目标和措施取得成功。
戴明环(DemingCycle):戴明借助车轮周而复始的运动特点,强调有必要使研发、设计、生产、销售各部门间保持不断的交流和互动,从而改进质量,使顾客满意。
是精益生产管理中重要的知识点之一。
设计手段(DesignApproach):通过建立预设目标,寻求更优化的手段。
在未来的管理过程中,应更多地运用设计手段。
工厂管理的五大目标(FiveManage-mentObjectivesofFactoryManagement):三菱汽车澳大利亚公司总监格瑞姆·斯伯灵为工厂设定的五项关键管理点。
改进(Improvement)改进作为成功的改善策略中的一部分,它的含义已超出了该词在字典中的意义。
改进是维护和提升标准的不可撼动的思想意识。
广义上,改进可以定义为改善和创新,其中改善策略是指通过细小的渐进式改变,提高工作标准;而创新则是通过大规模的技术或设备投资实现激进的改进。
精益生产培训中的精益生产术语

精益生产培训中的精益生产术语很多人不知道应该如何学习精益生产培训,对此总是一头雾水抓瞎。
其实,参加精益生产培训,推行精益生产管理,我们可以先了解一下精益生产的基本知识和理念。
现在,中普咨询精益生产培训公司和大家讲一讲,精益生产咨询培训中的一些精益生产术语。
1、允收品质水准(AQL) Acceptable Quality Level精益生产培训公司,精益生产的产品允收品质水准是顾客与供货商之间的交易运作模式,容许供货商在协议的条件下,交付某一限定比率的不良品。
2、问五次为什么(Ask why five times)精益生产培训五个“为什么”一个发掘问题真正原因的常识原则。
另外精益生产培训中还有“5S”、“5M”等术语。
“5S”是指是指整理(SHIRI)、整顿(SEITON)、清扫(SEISO)、清洁(SEIKETSU)、素养(SHITSUKE)等五个项目,是指在生产现场中对人员、机器、材料、方法等生产要素进行有效的管理,这是日本企业独特的一种管理办法。
3、查核现场(Check gembutsu)精益生产培训提醒,当欲探寻问题的根源时,在现场实地有形的物体加以调查。
4、符合性(Conformance)精益生产培训中用以表示产品或服务能达到相关规格、合约或规则,所要求的一个确定指示或评定。
5、管制图(Control_chart)精益生产培训“管制图”为一个具有上下管制界线的图。
在其图上,绘有一系列的样本或样本组统计量的测定值。
此图通常绘有一条中心线,用以协助侦测所绘之统计值,有否趋向其中之一条管制界线。
6、成本(Cost)在QCD的范畴中,“成本”一词通常系指成本管理,而非削减成本。
成本管理涉及到对各种资源的适度管理,以及消除所有类别的无驮(浪费),在此种方式下,会降低总成本。
7、跨功能(部门)管理(Cross-functional management)在精益生产培训中,这是为达成QCD跨越部门之间的管理活动。
精益术语汇编(Lean Lexicon)

精益术语汇编(Lean Lexicon)Labor Linearity (劳动力线性化)一种在生产工序(特别是一个生产单元)中,随着产量的变化灵活调动操作员人数的方法。
按照这种方法,制造每个零件所需人数,随产量的变化,可以接近于线性。
参见:投资线性化。
Lean Enterprise (精益企业)一个产品系列价值流的不同部门同心协力消除浪费,并且按照顾客要求,来拉动生产。
这个阶段性任务一结束,整个企业立即分析结果,并启动下一个改善计划。
Lean Production (精益生产)一种管理产品开发、生产运作、供应商、以及客户关系的整个业务的方法。
与大批量生产系统形成对比的是,精益生产强调以更少的人力,更少的空间,更少的投资,和更短的时间,生产符合顾客需求的高质量产品。
精益生产由丰田公司在第二次世界大战之后首创,到1990年的时候,丰田公司只需要用原来一半的人力,一半的制造空间和投入资金,生产相同数量的产品。
在保证质量和提高产量的同时,他们所花费的在产品开发和交货的时间,也远比大批量生产更有效益。
(Womack,Jones和Roos1990, P.13)“精益生产”这个术语由MIT国际机动车辆项目的助理研究员John Krafcik于20世纪80年代最先提出。
Lean Logistics (精益物流)在沿着价值流的各个公司和工厂之间,建立一个能够经常以小批量进行补给的拉动系统。
我们假设A公司(一个零售商)直接向顾客销售产品,而且从B公司(一个制造商)大批量、低频率的补给货物。
精益物流将会在零售商(A公司)安装一个拉动信号,当他售出若干的货物之后,这个信号就会提示制造商,补充相同数量的货物给A,同时制造商会提示他的供应商补充相同数量的原料或半成品,以此一直向价值流的上游追溯。
精益物流需要拉动信号(EDI,看板,网络设备,等等),来保证价值流各工序之间的平衡生产,举个例子,用频繁的小批量装运方法,将零售商、制造商、以及供应商,联成一条“送牛奶”的供应链。
精益生产术语
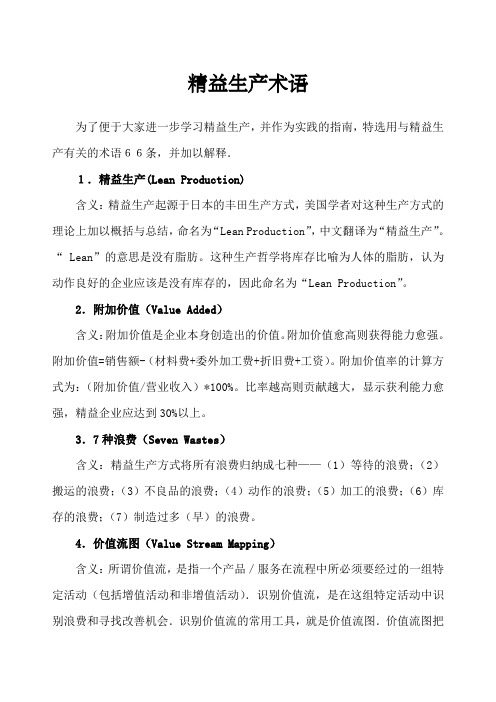
精益生产术语为了便于大家进一步学习精益生产,并作为实践的指南,特选用与精益生产有关的术语66条,并加以解释.1.精益生产(Lean Production)含义:精益生产起源于日本的丰田生产方式,美国学者对这种生产方式的理论上加以概括与总结,命名为“Lean Production”,中文翻译为“精益生产”。
“ Lean”的意思是没有脂肪。
这种生产哲学将库存比喻为人体的脂肪,认为动作良好的企业应该是没有库存的,因此命名为“Lean Production”。
2.附加价值(Value Added)含义:附加价值是企业本身创造出的价值。
附加价值愈高则获得能力愈强。
附加价值=销售额-(材料费+委外加工费+折旧费+工资)。
附加价值率的计算方式为:(附加价值/营业收入)*100%。
比率越高则贡献越大,显示获利能力愈强,精益企业应达到30%以上。
3.7种浪费(Seven Wastes)含义:精益生产方式将所有浪费归纳成七种——(1)等待的浪费;(2)搬运的浪费;(3)不良品的浪费;(4)动作的浪费;(5)加工的浪费;(6)库存的浪费;(7)制造过多(早)的浪费。
4.价值流图(Value Stream Mapping)含义:所谓价值流,是指一个产品/服务在流程中所必须要经过的一组特定活动(包括增值活动和非增值活动).识别价值流,是在这组特定活动中识别浪费和寻找改善机会.识别价值流的常用工具,就是价值流图.价值流图把产品或者服务所涉及的所有物流与信息流相关内容用目视图表的方法绘制出来,作为随后即将展开的精益改造的依据.5.丰田生产方式(Toyota Production System)含义:一般认为,丰田生产方式的支柱有两个,一是"自动化",二是“及时生产”。
根据大野耐一的描述,丰田生产方式的现场管理,有两个特点,一是流水化制造,二是拉动式计划方法,也就是看板方式。
丰田过去是将车床、铣床分车间集中在一起,后来则改善为依照生产流程将车床、铣床、钻床一台一台流水化排列布置。
精益术语(下)

精益术语(下)Inspection (检查)在大批量生产中,专业检验员在制造产品的工序外,检查产品质量的行动。
精益制造商在生产工序中,使用防止错误的设施,并且把质量保证的任务分配给操作员。
如果发现有质量问题,经由质保小组找出问题的源头所在。
这个工序不仅要防止缺陷进入到后续工序,而且要停下来确定原因,并采取纠正措施。
Heijunka Box (生产均衡柜)在固定的时间间隔里,利用看板来平衡产品的型号和数量的工具,称为生产均衡柜。
由于看板槽代表了对材料和信息流的定时,因此看板槽内的每块看板,就代表了生产一种型号产品的一个批量时间(批量时间Pitch =节拍时间×每批次的产品数量)。
例如产品A的批量时间为20分钟,那么每个时间间隔的看板槽里就放一张看板;产品B的批量时间为10分钟,那么每个看板槽里就各放两张看板;产品C的批量时间为40分钟,因此每隔一个看板槽放置一张看板。
产品D和E共用一个生产工序,并且D产品与E产品的需求比例为2:1,因此把D 产品的两张看板分别放在前两个间隔里,而在第三个间隔里放入E产品的一张看板,以此循环下去。
由上文阐述的方法可以看出,生产均衡柜是一个工具,能够在一定时间内,用看板平衡多种产品的混合生产与数量,例如,确保在半小时内,以一个稳定的产品比例,来制造小批量的D和E。
参见:EPEx(每个产品每次间隔),Heijunka(均衡化),Kanban (看板),Material Handling(材料搬运),Paced Withdrawal(有节奏的提取),Pitch(批量时间)。
Heijunka (均衡化)在固定的生产周期内,平衡产品的类型与数量。
这样可以在避免大量生产的同时,有效的满足顾客的需求,最终带来整条价值流中的最优化的库存、投资成本、人力资源以及产品交付期。
举例说明“按照客户需求的产品数量来均衡生产”:假设一个制造商每周都收到500个产品的订单,但是每天收到的订单的产品数量却有着显著的差别:周一要运送200个,周二100个,周三50个,周四100个,周五再运送50个。
管理学精益思想名词解释总结

管理学精益思想名词解释总结精益思想(Lean Thinking)是一种管理理念,由美国麻省理工学院(MIT)所创立,旨在通过消除浪费、提高价值流、追求持续改进来提高组织的效率和竞争力。
下面是对精益思想中常用的名词进行解释和总结。
1. 浪费(Waste):指在生产过程中没有为客户创造价值的活动。
精益思想将浪费分为七大类:运输、库存、动作、等待、过处理、缺陷和不必要运动。
通过消除这些浪费,组织可以提高效率和质量。
2. 价值流(Value Stream):指为了满足客户需求而进行的一系列活动和流程。
精益思想通过对价值流的分析和改进,来优化整个价值创造过程,以减少浪费并提供更高价值的产品或服务。
3. 一体化价值流(Integrated Value Stream):指将供应链中的所有活动和流程整合起来,以实现物质、信息和价值的无缝流动。
精益思想提倡统一敏捷的交付,避免传统的功能分工导致的各种障碍。
4. 短交付周期(Short Lead Time):指从客户下订单到产品交付的时间。
精益思想认为,缩短交付周期可以提高客户满意度、降低库存和降低成本。
5. 好品质(Good Quality):指产品或服务符合客户要求的程度。
精益思想强调通过消除缺陷和提高质量控制来改进品质,并将质量问题视为机会来改进过程。
6. 拉动生产(Pull Production):指根据客户需求来触发生产。
精益思想反对推动生产,即根据预测的需求来生产,而主张建立一个基于实际需求的生产系统。
7. 单件流(One-Piece Flow):指将单个产品从一个工序流到另一个工序,以实现流程的平稳和快速运行。
精益思想认为单件流比批量生产更加高效和质量稳定。
8. 持续改进(Continuous Improvement):指通过不断地寻找问题、分析原因,并采取措施进行改进,来提高组织的效率和质量。
精益思想强调每个员工都应参与到持续改进中,并鼓励工作团队进行反思和学习。
21个精益生产专业术语!一定要记住哦!
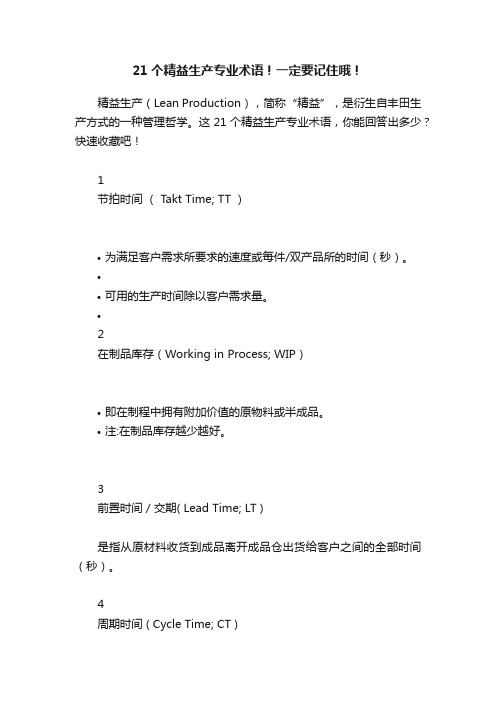
21个精益生产专业术语!一定要记住哦!精益生产(Lean Production),简称“精益”,是衍生自丰田生产方式的一种管理哲学。
这21个精益生产专业术语,你能回答出多少?快速收藏吧!1节拍时间( Takt Time; TT )•为满足客户需求所要求的速度或每件/双产品所的时间(秒)。
••可用的生产时间除以客户需求量。
•2在制品库存(Working in Process; WIP)•即在制程中拥有附加价值的原物料或半成品。
•注:在制品库存越少越好。
3前置时间 / 交期( Lead Time; LT )是指从原材料收货到成品离开成品仓出货给客户之间的全部时间(秒)。
4周期时间 ( Cycle Time; CT )观察测量得出完成一个作业的时间。
更正确的说,是工人完成该工位的工作步骤,并周而复始,到下一个产品开始的时间(秒)。
5总周期时间 ( Total Cycle Time; TCT )某一特定产品的生产速度,等于该产品各工序CT之和。
6每人每时的生产力 (Pairs per People per hour; PPH )是一种衡量生产力和直接劳动力成本的可靠方法,双/人/时。
7及时生产(Just in Time; JIT)下一道工序需要的时候,生产需要的产品和数量。
8首次通过率 ( First Time Through; FTT )计算工件在每一工序成功完成的百分比(不含报废或返工),此为测量首次就能生产无瑕疵的、无须返修的产品的能力。
9转换时间 ( Change Over; CO)介于上一批次A最后一件产品完成的时间与下一批次B第一件产品产出的间隔时间。
说明:B的第1双需为良品,且后续产出的B亦需为连续产出的良品。
10快速切换 ( Quickly Change Over; QCO )在output 之A→B鞋型转换时,仍维持原TT标准之产出即为快速切换之目标。
11先入先出(First in First Out; FIFO)置时间的先后来决定消耗的顺序,先进先出。
精益术语汇编
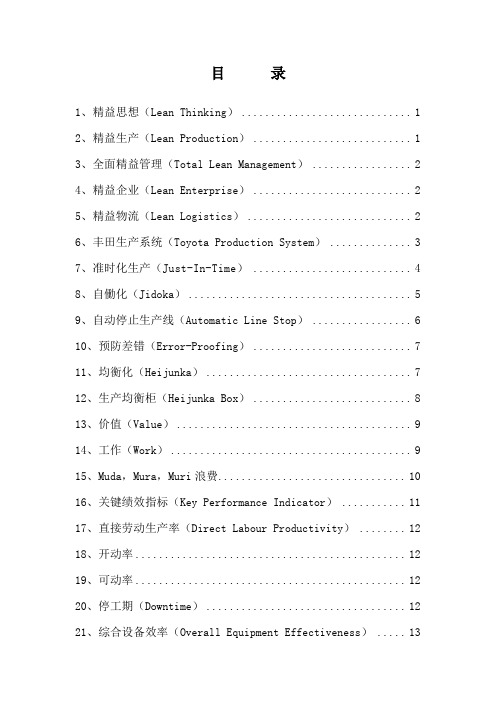
目录1、精益思想(Lean Thinking) (1)2、精益生产(Lean Production) (1)3、全面精益管理(Total Lean Management) (2)4、精益企业(Lean Enterprise) (2)5、精益物流(Lean Logistics) (2)6、丰田生产系统(Toyota Production System) (3)7、准时化生产(Just-In-Time) (4)8、自働化(Jidoka) (5)9、自动停止生产线(Automatic Line Stop) (6)10、预防差错(Error-Proofing) (7)11、均衡化(Heijunka) (7)12、生产均衡柜(Heijunka Box) (8)13、价值(Value) (9)14、工作(Work) (9)15、Muda,Mura,Muri浪费 (10)16、关键绩效指标(Key Performance Indicator) (11)17、直接劳动生产率(Direct Labour Productivity) (12)18、开动率 (12)19、可动率 (12)20、停工期(Downtime) (12)21、综合设备效率(Overall Equipment Effectiveness) (13)22、在制品(Work-In-Process) (14)23、节拍时间(Takt Time) (15)24、周期时间(Cycle Time) (16)25、线平衡率(Line of Balance) (16)26、6M因素法 (17)27、流水线生产(Flow Production) (17)28、ECRS原则 (18)29、PDCA循环 (19)30、换模(Changeover) (21)31、快速换产(Single Minute Exchange of Die) (21)32、七种浪费(Seven Wastes) (25)33、七个零 (26)34、5S (26)35、红牌作战 (29)36、改善(Kaizen) (29)37、改善研习会(Kaizen Workshop) (30)38、三现主义 (30)39、标准化操作(Standardized Work) (31)40、工序能力表(Process Capacity Sheet) (32)41、标准化操作组合表(Standardized Work Combination Table) (32)42、标准化操作表(Standardized Work Chart) (32)43、按订单制造(Build-to-Order) (33)44、产品交付期(Production Lead Time) (33)45、订单交付期(Order Lead Time) (35)46、订单到现金时间(Order to Cash Time) (35)47、批量生产(Batch and Queue) (35)48、生产单元(Cell) (36)49、一个流生产(One Stream Production) (36)50、可视化管理(Visual Management) (37)51、推动生产(Push Production) (37)52、库存超市(Supermarket) (38)53、拉动生产(Pull Production) (38)54、库存超市拉动系统(Supermarket Pull System) (39)55、顺序拉动系统(Sequential Pull System) (39)56、库存超市与顺序拉动混合系统(Mixed Supermarket and Sequential Pull System) (40)57、5W2H分析法 (42)58、5why分析法 (43)59、周转库存 (44)60、安全库存(Safety Stock) (45)61、缓冲库存(Buffer Stock) (45)62、标准库存(Standard Inventory) (46)63、理货(tally) (46)64、PC超市(Process Center) (47)65、价值流图(Value Stream Mapping) (47)66、物料传递员(W/S) (47)67、并行工程(Concurrent Engineering) (47)68、程序分析(Program Analysis) (48)69、看板(KANBAN) (48)70、全面生产维护(Total Productive Maintenance) (50)1、精益思想(Lean Thinking)包括精益生产、精益管理、精益设计和精益供应等一系列思想。
精益术语汇编
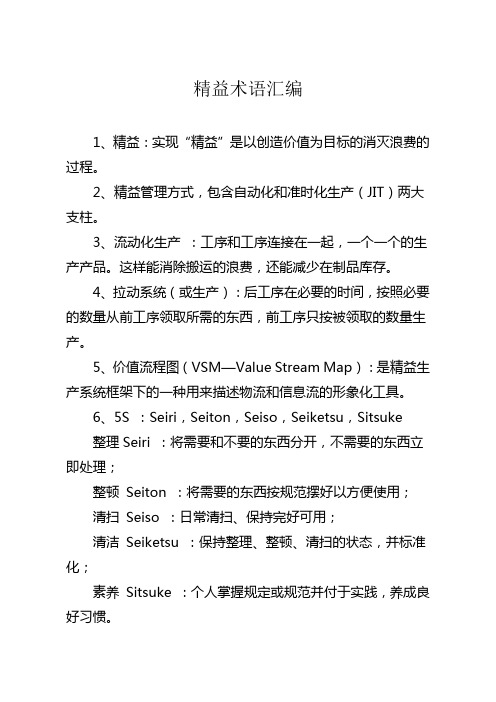
精益术语汇编1、精益:实现“精益”是以创造价值为目标的消灭浪费的过程。
2、精益管理方式,包含自动化和准时化生产(JIT)两大支柱。
3、流动化生产:工序和工序连接在一起,一个一个的生产产品。
这样能消除搬运的浪费,还能减少在制品库存。
4、拉动系统(或生产):后工序在必要的时间,按照必要的数量从前工序领取所需的东西,前工序只按被领取的数量生产。
5、价值流程图(VSM—Value Stream Map):是精益生产系统框架下的一种用来描述物流和信息流的形象化工具。
6、5S :Seiri,Seiton,Seiso,Seiketsu,Sitsuke整理Seiri :将需要和不要的东西分开,不需要的东西立即处理;整顿Seiton :将需要的东西按规范摆好以方便使用;清扫Seiso :日常清扫、保持完好可用;清洁Seiketsu :保持整理、整顿、清扫的状态,并标准化;素养Sitsuke :个人掌握规定或规范并付于实践,养成良好习惯。
7、目视化管理。
基本在于使什么是正常,什么是不正常明确化。
从质量上来说,就是使不良品暴露出来,从数量上来说,就是相对于计划使人一眼就能知道有在进展。
不仅是机器、生产线,这种思考方法也适用于东西的摆放、在制品数量、“看板”的传递方法、人的作业方法等任何问题。
导入丰田生产方式的现场都在彻底贯彻“目视化管理”。
目视化也可以叫做可视化。
8、准时化生产(JIT—Just-In-Time):如果能够在所需要的时候,按所需数量,获取所需要的东西,那么就可以消除生产现场的浪费、不均衡、不合理,提高生产效率。
该思想的开山鼻祖是丰田汽车的创始人-丰田喜一郎,其后继者将此思想展开,概括成为了一个生产体系。
不单是in time, 而是just in time,这是一个重要的关键。
“Just-In-Time”和“自动化”共同形成丰田生产方式的两大支柱。
9、自动化(Jidoka):在丰田的生产方式当中,必须完全是带人字旁的“自动化”。
企业精益质量管理cf
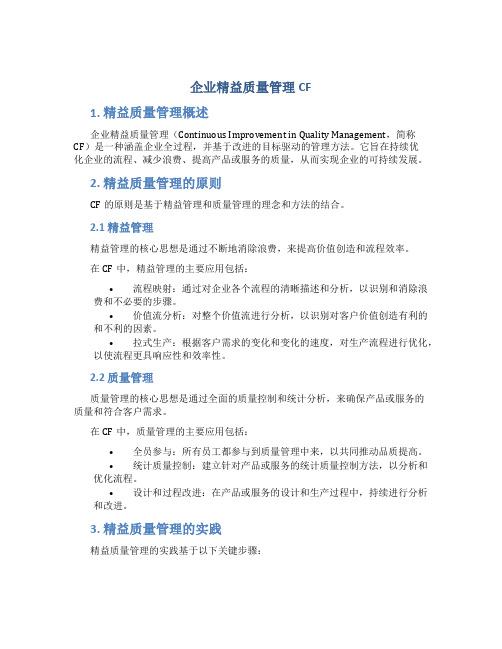
企业精益质量管理CF1. 精益质量管理概述企业精益质量管理(Continuous Improvement in Quality Management,简称CF)是一种涵盖企业全过程,并基于改进的目标驱动的管理方法。
它旨在持续优化企业的流程、减少浪费、提高产品或服务的质量,从而实现企业的可持续发展。
2. 精益质量管理的原则CF的原则是基于精益管理和质量管理的理念和方法的结合。
2.1 精益管理精益管理的核心思想是通过不断地消除浪费,来提高价值创造和流程效率。
在CF中,精益管理的主要应用包括:•流程映射:通过对企业各个流程的清晰描述和分析,以识别和消除浪费和不必要的步骤。
•价值流分析:对整个价值流进行分析,以识别对客户价值创造有利的和不利的因素。
•拉式生产:根据客户需求的变化和变化的速度,对生产流程进行优化,以使流程更具响应性和效率性。
2.2 质量管理质量管理的核心思想是通过全面的质量控制和统计分析,来确保产品或服务的质量和符合客户需求。
在CF中,质量管理的主要应用包括:•全员参与:所有员工都参与到质量管理中来,以共同推动品质提高。
•统计质量控制:建立针对产品或服务的统计质量控制方法,以分析和优化流程。
•设计和过程改进:在产品或服务的设计和生产过程中,持续进行分析和改进。
3. 精益质量管理的实践精益质量管理的实践基于以下关键步骤:3.1. 识别和消除浪费通过流程映射和价值流分析,识别并消除无价值的步骤,以提高流程效率和降低成本。
3.2. 确定并监测关键质量指标通过定义关键质量指标和制定监控计划,以确保产品或服务的质量符合客户需求,并通过统计质量控制方法进行分析和改进。
3.3. 推动全员参与所有员工都参与到质量管理中来,持续地识别和解决问题,以推动过程改进和品质提高。
3.4. 建立和推广质量文化构建一个以质量为中心的企业文化,并持续地推广质量文化,并鼓励员工不断学习和发展。
4. 精益质量管理的效益CF的应用效益包括:•降低成本:通过浪费识别和流程优化,降低企业的成本。
- 1、下载文档前请自行甄别文档内容的完整性,平台不提供额外的编辑、内容补充、找答案等附加服务。
- 2、"仅部分预览"的文档,不可在线预览部分如存在完整性等问题,可反馈申请退款(可完整预览的文档不适用该条件!)。
- 3、如文档侵犯您的权益,请联系客服反馈,我们会尽快为您处理(人工客服工作时间:9:00-18:30)。
精益管理专业术语-F系列
1.FailureModesandEffectsAnalysis(FMEA)(故障模式及危害性分析)
一种结构方法,用于确定潜在故障的严重性以及确定每种潜在故障的根本原因。
2.FeederBuffer(直属缓冲区)
位于非关键链末尾与关键链之间的时间缓冲,有时会被称为关键链直属缓冲区。
3.Feederlines(反馈线)
反馈线就是一个特殊的装配生产线,它允许装配工在主生产线之外执行装配任务。
4.FinishedGoods(成品)
已经加工完毕等待装运的产品。
5.FIFO(先进先出)
一种维持生产和运输顺序的实践方法。
先进入加工工序或是存放地点的零件,也是先加工完毕或是被取出的产品。
这保证了库存的零件不会放置太久,从而减少质量问题。
FIFO是实施拉动系统的一个必要条件。
6.Fixed-PositionStopSystem(固定工位来停止生产)
一种通过在某个固定的位置,停止装配线运转来解决问题的方法。
这类问题通常是指那些已经检测到,但无法在生产周期中解决的问题。
当操作员发现零件、设备、材料供应、安全等方面的问题之后,会拉动一根灯绳或是按动一个信号灯,来提醒管理人员。
管理人员在评估问题之后,决定是否在生产周期结束之前解决问题。
如果问题可以在生产周期内解决,管理人员就会停止信号系统,以保证生产线继续运转,同时进行解决方案;如果不能解决,那么生产线就必须在生产周期完成后来解决问题。
7.FiveWhys(五个“为什么”)
当遇到问题的时候,不断重复问“为什么”,目的要发现隐藏在表面下的问题根源。
1.为什么机器停止工作?
机器超负荷运转导致保险丝烧断了。
2.为什么机器会超负荷运转?
没有能够对轴承进行充分的润滑
3.为什么没有给轴承充分的润滑?
润滑油泵泵送不足
4.为什么泵送不足?
润滑泵的转轴过于陈旧,甚至受损发出了“卡嗒卡嗒”的响声。
5.为什么转轴会破旧受损?
由于没有安装附加滤网,导致金属碎屑进入了油泵。
如果没有反复的追问“为什么”,操作员可能只会简单的更换保险丝或者油泵,而机器失效的情况仍会再次发生。
“五”并不是关键所在,可以是四,也可以是
六、
七、八……关键是要不断的追问,直到发现并消除掉问题的根源。
8.FiveS(5S)
5个以“S”开头的,用来描述可视化控制,及精益生产的现场操作。
日语里这5个术语是:·整理
·整顿
·清扫
·清洁-执行前三个的结果。
·纪律-执行前四个的纪律。
后有人加入第六个“S”安全。
在丰田传统只提4S,不提5S,因为其标准化程度已经很高,且持续审核,强调纪律显得多余了。
9.FlexibleManufacturingSystem(柔性化制造系统)
一种集成的制造能力,以低单位成本生产少量多种类的物品。
柔性化制造系统还有一个特点就是转换时间短,响应时间迅速。
10.Flow(流动)
流动是精益生产的主要目的,也是亨利福特直接传递给丰田的重要概念之一。
福特意识到:理论上说产品应该从原材料到客户一直不间断的保持流动,可以通过一个作为长输送带的上产系统来实现这个理想。
11.FlowChart(流程图)
通过画出过程步骤达到可视化来解决问题的一种工具。
流程变得简单,浪费与过剩都被标识出来。
12.FunctionalLayout(功能性布置)
根据操作类型对机械或步骤进行编排组合的实验
13.FutureRealityTree(FRT)(将来可性度树)
约束理论的思维过程图描述了一个解决方案被通过的过程,都不可避免的要经过严密的逻辑实现想要的结果或者利益。
14.FutureStateMap(未来图)
未来最佳工艺的蓝图,通过帮助设计流程的运作形成实施计划的基础。