☆☆乘用车制动系统开发设计流程☆☆33页PPT
汽车制动系统精品PPT课件
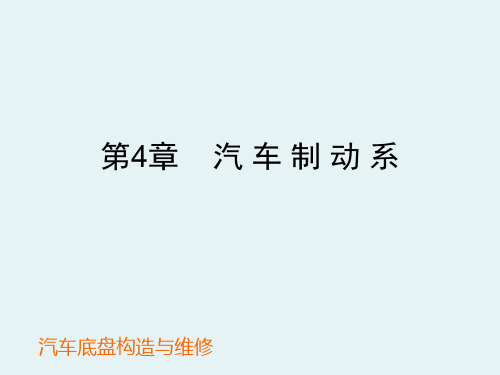
轮旋转方向相反。
汽车底盘构造与维修
这时,制动鼓将该力矩传到车 轮。由于车轮与路面间的附着作 用,车轮对路面作用一个向前制 动力即周缘力Fμ,同时,路面也 对车轮作用于一个向后的反作用 力,即制动力FB。制动力FB由车 轮经车桥和悬架传给车架及车身, 迫使汽作减速或停车。
当放松制动时,油液流回主缸, 在各同位弹簧作用下,制动蹄与 制动鼓又恢复了原来的间隙,从 而制动作用解除。
汽车底盘构造与维修
第二节 车轮制动器
汽车底盘构造与维修
一、鼓式车轮制动器
1.鼓式车轮制动器的结构与工作过程 根据制动时两制动蹄对制动鼓径向力的平衡状况,鼓式车轮 制动器又分为非平衡式、平衡式(单向助势、双向助势)和自动 增力式三种。
汽车底盘构造与维修
汽车底盘构造与维修
①单向自动增力式制动器 两蹄下端都没有固定支点,而是插在连杆n两端开口的直槽 底面上,形成活动连接。后蹄上端固定在支承销上,前蹄上 端在回位弹簧作用下,紧压在轮缸活塞上。
汽车底盘构造与维修
汽车前进制动时,制动缸内的活塞克服回位弹簧的弹力, 将前蹄推出,使其压紧在制动鼓上。由于摩擦力的作用,前蹄 沿制动鼓旋转方向转过一个角度,通过连杆n,以后蹄上端为 支点,又推动后蹄压紧在制动鼓上,进一步增强摩擦力,加大 制动力。此时两蹄均为助势蹄,制动效能较高。
汽车底盘构造与维修
(1)非平衡式车轮制动器 ①基本结构 制动底板用螺栓固定在后桥壳的凸缘上(前桥 茬转问节凸缘上)不能转动;其上部装有制动轮缸或凸轮,下 端装有两个偏心支承销。制动蹄下端圆孔活套在偏心支承销, 上端嵌入制动轮缸活塞凹糟中或顶靠在凸轮上;两制动蹄通过 回位弹簧紧压住轮缸活塞或凸轮;制动鼓与轮毂连接随着车 轮同步旋转。
制动系统介绍ppt演示课件
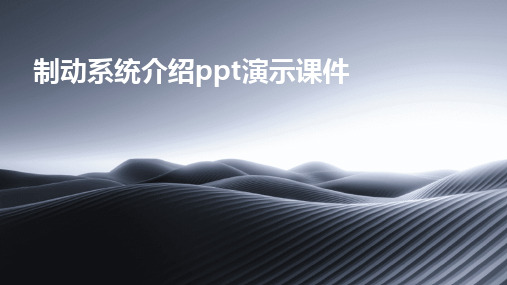
制动系统安全性
制动系统应具有多种安全保护措 施,如防抱死制动系统(ABS)
等,提高车辆行驶安全性。
03
制动系统关键部件介绍
制动器类型及特点
鼓式制动器
具有较大的制动力矩,但 热衰退性能较差,易于磨 损。
盘式制动器
散热性能好,制动效能稳 定,抗热衰退能力强,但 制造成本较高。
制动平顺性
评价制动过程中车辆减速的平顺性,避免急刹车等突兀动作对乘客 造成不适。
05
制动系统故障诊断与排除
常见制动系统故障类型
制动失效
制动踏板行程过大,制动作用迟缓,制动效 能很低甚至丧失,制动距离增长。
制动拖滞
制动后车辆起步困难或行驶无力,制动鼓或 制动盘发热。
制动跑偏
制动时车辆自动向一侧偏驶,无法保持直线 行驶。
评价制动系统使车辆从一定速度减速到完全停止所需的距离,是 制动效能的直观体现。
制动减速度
反映制动过程中车辆速度下降的快慢,是衡量制动效能的重要指 标之一。
制动时间
从驾驶员开始制动到车辆完全停止所需的时间,也是评价制动效 能的重要参数。
制动稳定性评价指标
制动方向稳定性
评价车辆在制动过程中是否保持直线行驶,有无跑偏、侧滑等现 象。
02
制动系统工作原理
制动过程描述
01
02
03
制动踏板操作
驾驶员踩下制动踏板,启 动制动系统。
制动力分配
根据车辆负载、路况等因 素,制动系统自动分配制 动力到各个车轮。
车轮减速
制动器对车轮施加摩擦力, 使车轮减速或停止转动。
制动力产生与传递
制动器工作原理
汽车制动系设计方案PPT(共 45张)
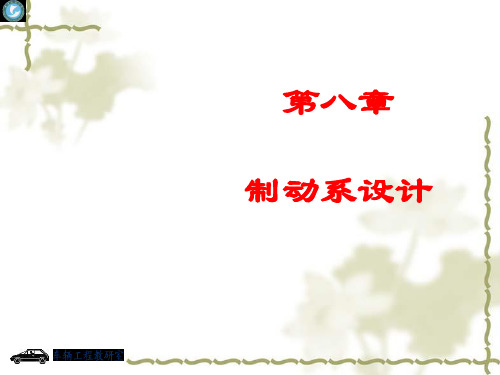
二、制动系的分类:
行车制动装置 驻车制动装置 应急制动装置 辅助制动装置
汽车制动系统图组
三、制动系的设计要求:
1)足够的制动能力; 2)工作可靠 ; 3)不应当丧失操纵性和方向稳定性 ; 4)防止水和污泥进入制动器工作表面; 5)热稳定性良好 ; 6)操纵轻便,并具有良好的随动性 ; 7)噪声尽可能小; 8)作用滞后性应尽可能短; 9)摩擦衬片(块)应有足够的使用寿命; 10)调整间隙工作容易; 11)报警装置 。
(2)制动鼓逆时针旋转时
使鼓向相反的方向转动,唯一 变化的是摩擦力µP 的方向。
制动鼓逆时针旋转
制动蹄上 的摩擦力 有减小作 用在鼓上 的压力的 趋势,这 类蹄为 “松蹄”。
制动鼓逆时针旋转 时的制动力矩曲线
2)解析法 法向力 制动力矩
对于紧蹄 对于松蹄
液力驱动 自锁条件:当 领蹄表面的最大压力
Ⅱ型管路布置特点:
•结构简单,可与传统的单轮缸鼓式制动器配合使用,成本较低; •若后制动回路失效,则一旦前轮抱死即极易丧失转弯制动能力。
•对于采用前轮驱动因而前制动器强于后制动器的轿车,当前制动回路 失效而单用后桥制动时,制动力将严重不足,并且若后桥负荷小于前 轴,则踏板力过大时易使后桥车轮抱死而汽车侧滑。
制动器效能
制动器在单位输入压力或力的作用下所输出的力或力矩。
易
混 制动器效能因数
概 念
在与制输动入鼓力或F0之制比动。盘的作用半径KR上 所M 得到摩擦力(Mμ/R)
制动器效能的稳定性
F0 R
效能因数K对摩擦因数f的敏感性(dK/df)。
1.领从蹄式
每块蹄片都有自己的固定支点,而且两固定支点位于两蹄的同一端 。
双轴汽车的单 个前轮和后来 制动器的比能
制动系详解(有图)ppt课件
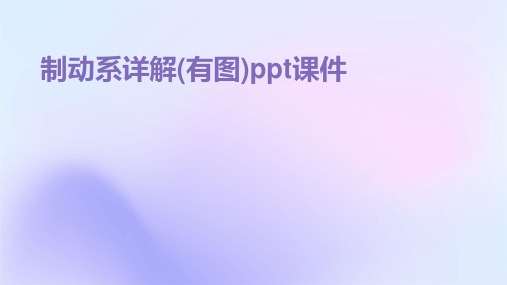
制动管路的维护与保养
检查制动管路连接处是否松动或泄漏,及时紧固或更换 密封件。
检查制动管路是否有老化、裂纹等现象,及时更换受损 管路。
定期清洗制动管路,去除管路内的杂质和油污,确保制 动液流通顺畅。
保持制动管路固定牢靠,避免管路在车辆行驶过程中产 生振动和噪音。
制动液的维护与保养
定期更换制动液,避免制动液 过期或污染导致制动性能下降
04
制动系统的故障诊断与排除
制动失灵的诊断与排除
制动踏板行程过大,制动作用迟缓,制 动效能很低甚至丧失,制动距离增长。
制动主缸、轮缸活塞和缸管磨损或拉伤 ,皮碗老化损坏。
制动踏板自由行程或制动器间隙过大, 制动蹄摩擦片接触不良,磨损严重或有 油污。
制动油压力不足。主要原因是制动主缸 缺油、制动管路破裂、油管接头渗漏、 油路堵塞。
制动系统内有空气。
制动跑偏的诊断与排除
制动时,左右车轮制动效果不一 样,使车轮向一边偏斜,原因如
下
两侧制动器摩擦片摩擦系数不同 ,如一侧摩擦片上有油污等。
两侧制动器摩擦片与鼓(盘)接 触面积差异太大,或一侧摩擦片
损坏严重。
制动跑偏的诊断与排除
01
02
03
04
两侧制动器间隙或摩擦 片磨损程度不一致。
程。同时,也可用于传统汽车的节能改造,降低油耗和排放。
THANKS。
制动器的维护与保养
定期检查
更换磨损件
定期检查制动器的磨损情况,包括摩擦片 厚度、制动盘磨损程度等,确保制动性能 良好。
根据检查结果,及时更换磨损严重的摩擦 片、制动盘等部件,保证制动安全。
清洁与润滑
调整与校准
定期清洁制动器表面的灰尘和油污,保持 其良好的散热性能;同时对制动器的活动 部位进行润滑,确保制动器工作顺畅。
☆☆乘用车制动系统开发设计流程☆☆

联立上式可以得出前后地面制动力与地面附着 系数的关系如下
Fbf m(gB ugh) u ( A B) Fbr m(gA ugh) u ( A B)
对同一车辆来说,上两式中,只有u为变量, 取不同的u值便可得到不同Fbf和Fbr值。这便 是理想制动力分配曲线。
2. 基础制动与制动主缸的联络---轮缸压力与主缸推力
现已知了主缸直径、主缸行程;基础制动系统的压力-减速度曲线,可以推导出主缸推力与制动减 速度曲线。
减速度
轮缸压力 =
主缸压力
轮缸压力
轮缸压力
轮缸推力 =
主缸压力X 活塞面积
主缸压力
主缸压力 主缸活塞推力
踏板杠杆比
3. 制动主缸与人机控制联络 ---主缸行程与踏板行程
insight 均可做为优化工具。
下一张便是2010年所写的一个B21 四连杆 踏板机构优化论文
3.3 制动控制模块布置 目前的制动控制模块主要是ABS 或者ESP(ESC)模块,模块的布置位置并没有严格的要求。但应做到 1. 靠近主缸 2. 液面低于储液罐液面(包括连接主缸-模块的制动管最高点) 3.远离热源 4. 放置淋雨(插接件插接口要防止积水) 5. 尽量放置在纵梁等NVH性能较稳定的部件之上 6. 管路易于安装,本身易于拆装
车辆制动系统开发
汽研院底盘部:李成 2011年5月10日
1. 液压制动系统简介 2. 制动系统开发理论计算 3. 子系统的开发 4. 制动系统零部件的开发 5. 制动系统客观试验 6. 制动系统主观评价
1.液压制动系统简介
液压制动系统是将驾驶人员施加到制动踏板上的 力放大,并助力后反应到制动主缸,由制动主缸建立 起整个制动管路的压力,压力将推动执行机构(制动 器)限制车轮的转动而实现制动。
乘用车制动系统设计

兰州工业学院毕业设计(论文)题目:乘用车制动系统设计院系:汽车工程学院专业:汽车制造与装配技术班级:汽造11班姓名:张百宏学号:201109103145指导老师:李彦晶日期:2013年11月3日摘要汽车制动系是汽车底盘上的一个重要系统,它是制约汽车运动的装置。
其中制动器又是制动系中直接作用制约汽车运动的一个关健装置,是汽车上最重要的安全件。
汽车的制动性能直接影响汽车的行驶安全性。
本论文通过对乘用车制动系统进行细致的分析与了解,首先介绍了汽车制动系统的发展、结构、分类,并通过对鼓式制动器和盘式制动器的结构及优缺点进行分析。
最终确定方案采用液压双回路前盘后鼓式制动器。
除此之外,它还对前后制动器、制动主缸进行设计计算,主要部件的参数选择及制动管路布置形式等的设计过程。
关键字:制动系统;制动器;制动主缸ABSTRACTAutomobile brake system is automobile chassis to an important system, it is restricted by the car of the movement of the device. And the brake is brake system directly effect the automobile sport in a restricted key device, is the most important safety car parts. The automobile braking performance directly influence the car driving safety. First this paper reviewed the automobile braking system development, structure, classification, and through to the drum brake disc brake and the structure of the advantages and disadvantages and analyzed. Ultimately determine the scheme adopts hydraulic double circuit qianpan hougu type brake. In addition, it's still around to brake and brake main cylinder design, calculation of the main parts of parameter selection and brake pipe, the design process of decorate a form, etc.Key words: Braking; Brake drum; Brake disc; Braking cylinder目录摘要 (II)ABSTRACT (III)目录 (1)第一章绪论 (2)1.1汽车制动系的研究的目的和意义.............................................................. 错误!未定义书签。
汽车制动系统设计开发流程教材(PDF 44页)
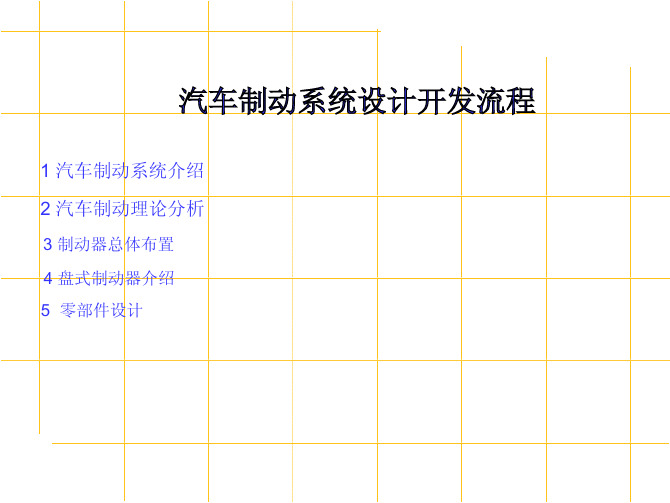
Fbf m(gB ugh) u ( A B)
Fbr m(gA ugh)u (A B)
对同一车辆来说,上两式中,只有u为变量,取不同的u值便可得 到不同Fbf和Fbr值。这便是理想制动力分配曲线,如下页
F 线组是前轮抱死时前后轮地面制动 力的变化关系
h
A
B
Ff mg B ma h (A B) (A B)
Fr mg A ma h (A B) (A B)
a Fb m
假设制动时车轮完全抱死,整车制动力就等于地面附着力
Fbf u Ff Fbr u Fr
u 为地面提供的附着系数
Fb u mg Fbf Fbr Fb
分析可发现,将制动钳后置在制动时施加在轴承上的径 向载荷远小于制动钳前置的情况。
为了减小簧下质量,在赛车上将制动钳与制动盘移至传动轴 内球笼一侧,从而由簧下质量变为簧载质量。这样的好处多方面 的。可以用小的减振器,刚度小的弹簧…
制动盘的布置位置
理想情况是轮胎中线线及制动盘中心还有轴承中心在 y方向重合,这样在制动时在轴承及轮毂上就不会产 生附加的弯矩。
后轮地面制动 力增量(负值)
后轮制动器制 动力增量
前轮制动器制 动力亦地面制
动力增量
R线组
实际制动力分配曲线
关于制动系统理 论,如果在此分析将 占用很大的篇幅,今 后将在制动系统设计 指南中详细分析,在 此就不赘述了!
理想制动力分配曲线
F线组
在附着系数等于0.5的路面上制动,随着制动器 制动力的增加,地面制动力随之上升,当达到实际制 动力与理想制动力的焦点时,前后制动器同时抱死。 此后制动器制动力再增加已无意义。
汽车制动系统设计开发流程
制动系统设计流程
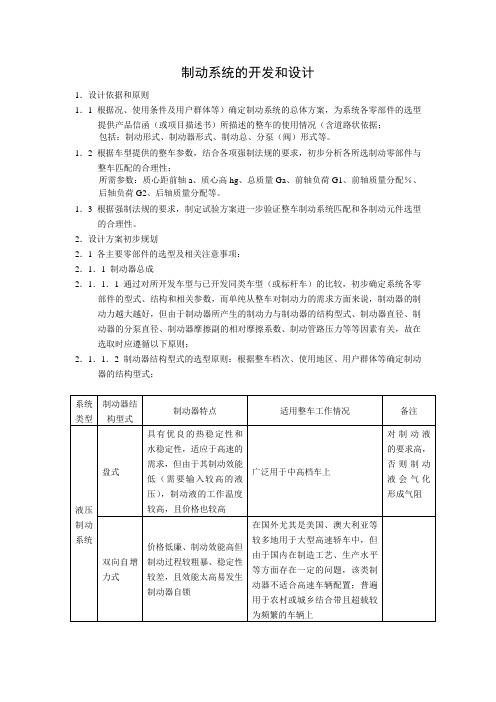
制动系统的开发和设计1.设计依据和原则1.1 根据况、使用条件及用户群体等)确定制动系统的总体方案,为系统各零部件的选型提供产品信函(或项目描述书)所描述的整车的使用情况(含道路状依据;包括:制动形式、制动器形式、制动总、分泵(阀)形式等。
1.2 根据车型提供的整车参数,结合各项强制法规的要求,初步分析各所选制动零部件与整车匹配的合理性;所需参数:质心距前轴a、质心高hg、总质量Ga、前轴负荷G1、前轴质量分配%、后轴负荷G2、后轴质量分配等。
1.3 根据强制法规的要求,制定试验方案进一步验证整车制动系统匹配和各制动元件选型的合理性。
2.设计方案初步规划2.1 各主要零部件的选型及相关注意事项:2.1.1 制动器总成2.1.1.1 通过对所开发车型与已开发同类车型(或标杆车)的比较,初步确定系统各零部件的型式、结构和相关参数,而单纯从整车对制动力的需求方面来说,制动器的制动力越大越好,但由于制动器所产生的制动力与制动器的结构型式、制动器直径、制动器的分泵直径、制动器摩擦副的相对摩擦系数、制动管路压力等等因素有关,故在选取时应遵循以下原则;2.1.1.2 制动器结构型式的选型原则:根据整车档次、使用地区、用户群体等确定制动器的结构型式;2.1.1.3 制动器直径的选型原则:由于制动器的直径与轮辋直径有关,在选型时应根据整车布置及轮辋的要求,考虑制动鼓的散热问题,一般制动鼓与轮辋的间隙应不小于10mm,否则会导致制动器散热不良,引起制动鼓早期龟裂、制动衬片烧结、炭化,大大降低制动器的制动效能;另外,制动器与轮辋的间隙太小,制动过程所产生的热量也将大量传导至轮辋上,对轮胎不利。
2.1.1.4 制动器衬片摩擦系数的确定:由于制动器衬片的摩擦系数是决定制动器制动力的主要原因之一,在同型、同规格的制动器中,制动衬片的摩擦系数越高,制动器所产生的制动力越大,但对于不同结构的制动器来说,并不是摩擦系数越高越好,摩擦系数太高对制动鼓(或盘)的磨损也越大,且对于双向自增力式制动器,摩擦系数越高,制动过程越粗暴,对制动底板、制动蹄铁、制动鼓的刚性要求越高,否则在制动过程中越易产生制动器颤动、整车发抖的现象,故对于摩擦系数的选取根据本人的经验建议:双向自增力式制动器的取0.38左右,其它结构型式的制动器取0.45~0.5左右,盘式制动器取0.35左右。