乘用车制动系统开发-20140613
2023年乘用车制动系统行业市场研究报告

2023年乘用车制动系统行业市场研究报告乘用车制动系统是汽车的一个重要部件,负责控制汽车的行驶速度和停车。
随着汽车产业的快速发展和市场需求的增加,乘用车制动系统行业也得到了迅猛发展。
下面是一份1500字的乘用车制动系统行业市场研究报告:一、行业概述乘用车制动系统是汽车的重要组成部分,直接影响汽车的安全性能。
整个乘用车制动系统可以分为制动器、制动辅助装置和制动控制装置三个部分。
制动器包括刹车片、制动鼓等,负责制动力的产生和传递;制动辅助装置包括制动液、制动真空助力器等,起到辅助制动的作用;制动控制装置包括制动踏板、制动分泵等,用于控制制动力的大小。
二、市场规模目前,乘用车制动系统市场规模庞大。
根据统计数据显示,2019年全球乘用车制动系统市场规模达到了600亿美元,并且随着汽车产业的不断发展,市场规模还在不断增长。
预计到2025年,全球乘用车制动系统市场规模将突破800亿美元。
三、市场竞争格局乘用车制动系统行业竞争激烈,市场份额主要被少数大型企业掌握。
目前,主要的乘用车制动系统企业包括博世、德尔福、Akebono等。
这些企业凭借其先进的技术、高品质的产品和广泛的市场渠道,占据了乘用车制动系统市场的主要份额。
四、市场发展趋势在未来几年里,乘用车制动系统市场将面临一些新的发展趋势。
首先,随着汽车技术的不断进步,乘用车制动系统将越来越智能化。
例如,电子刹车系统和自动紧急刹车系统等技术的引入,将提高制动系统的安全性能和灵活性。
其次,环保和能源节约将成为乘用车制动系统发展的重要方向。
随着全球汽车尾气排放和能源消耗的问题日益突出,制动能量回收技术等新技术将得到更广泛的应用。
这些新技术可以将制动时产生的能量回收和存储起来,以供其他电子设备使用,从而减少能源的浪费。
此外,汽车市场的增长也将推动乘用车制动系统市场的发展。
尤其是新兴市场的需求增加,将为乘用车制动系统企业带来更多的业务机会和发展空间。
五、市场挑战乘用车制动系统行业面临着一些挑战。
制动系统发展趋势

从汽车出生时起,车辆制动系统在车辆的平安方面就饰演着至关重要的角色.近年来,随着车辆技术的进步和汽车行驶速度的提高,这种重要性暗示得越来越明显.汽车制动系统种类很多,形式多样.传统的制动系统结构型式主要有机械式、气动式、液压式、气—液混合式.它们的工作原理基本都一样,都是利用制动装置,用工作时发生的摩擦热来逐渐消耗车辆所具有的动能,以到达车辆制动减速,或直至停车的目的.陪伴着节能和清洁能源汽车的研究开发,汽车动力系统发生了很年夜的改变,呈现了很多新的结构型式和功能形式.新型动力系统的呈现也要求制动系统结构型式和功能形式发生相应的改变.例如电动汽车没有内燃机,无法为真空助力器提供真空源,一种解决方案是利用电动真空泵为真空助力器提供真空. 汽车制动系统的发展是和汽车性能的提高及汽车结构型式的变动密切相关的,制动系统的每个组成部份都发生了很年夜变动.1 汽车制动系统的组成制动系统主要由下面的4个部份组成:(1)供能装置:也就是制动能源,包括供给、调节制动所需能量以及各个部件,发生制动能量的部份称为制动能源;(2)控制装置:包括发生制动举措和控制制动效果的部件;(3)传动装置:包括把制动能量传递到制动器的各个部件;(4)制动器:发生阻碍车辆运动或者运动趋势的力的部件,也包括辅助制动系统中的部件. 现代的制动系统还包括制动力调节装置和报警装置,压力呵护装置等辅助装置.1.1 供能装置的发展供能装置主要是指制动能源,制动能源有人力制动、伺服制动、动力制动或者上述任两者的结合使用. 人力制动是开始有制动系统时的制动能源,它有机械式制动、液压式制动两种形式.机械式制动主要用于驻车制动系统中,驻车制动系统中要求用机械锁止方法保证汽车在原地停止不动,在任何情况下不至于滑动.液压式制动是通过制动踏板推动制动主缸,进而使制动器进入工作状态.伺服制动兼用人力和发念头作为制动能源,正常情况下制动能量由动力伺服系统供给,动力伺服系统失效时可由人力供给制动能量,这时伺服制动就酿成人力制动.伺服制动可用气压能、真空能(负气压能)以及液压能作为伺服能量,形成各种形式的助力器.动力制动系统的制动能源是发念头所驱动的油泵或者气泵,人力仅作为控制来源,可分为气压制动、气顶液制动、液压制动.其中气压制动是发展最早的一种动力制动系统.它用空气压缩机提供气压,气顶液制动是用气压推动液压举措,发生制举措用.液压制动是目前获得广泛应用的一种制动系统,技术已经非常成熟.目前正在发展的电液复合制动以及电子制动中使用了机电作为制动能源,人力踩制动踏板作为控制来源.1.2控制装置的发展最早的人力制动,通过机械的连接发生制动举措.发展到人力控制制动,通过踩制动踏板启动制动,再由传力装置把制动踏板力传到真空助力器,经过真空助力器的助力扩年夜后,传递到制动主缸发生液压力,然后通过油路把液压力传递到每个轮缸,开始制动.随着清洁能源汽车和电动汽车的研究应用,以及电子技术在汽车上面的广泛应用,制动系统的控制装置也呈现了电子化的趋势,其中电制动完全改变了制动系统的控制和管理,会使汽车制动系统发生革命性的变动,它采纳电子控制,可以更加准确、更高效率地实现制动.1.3传动装置的发展人力制动时代是采纳机械式的传动装置,气(液)压制动是利用气(液)压力和连接管路把制动力传递到制动器.电子制动则是利用制念头电发生制动力直接作用到制动器,它的控制信号来自控制单位(ECU),用信号线传递制动信号和制动力信息.1.4制动器的发展制动器是制动的主要组成部份,目前汽车制动器基本都是摩擦式制动器,依照摩擦副中旋转元件的分歧,分为鼓式和盘式两年夜类制动器. 鼓式制动器又有领从蹄式、双领蹄式、双向双领蹄式、双从蹄式、单向自增力式、双向自增力式制动器等结构型式.盘式制动器有固定钳式,浮动钳式,浮动钳式包括滑动钳式和摆动钳盘式两种型式.滑动钳式是目前使用广泛的一种盘式制动器.由于盘式制动器热和水稳定性以及抗衰减性能较鼓式制动器好,可靠性和平安性也好,而获得广泛应用.可是盘式制动器效能低,无法完全防止尘污和锈蚀,兼做驻车制动时需要较为复杂的手驱念头构,因而在后轮上的应用受到限制,很多车是采纳前盘后鼓的制动系统组成.电动汽车和混合动力汽车上具有再生制动能力的机电,在回收制动能量时起制举措用,它引入了新型的制动器.作为一种新的制动器型式,势必引起制动器型式的变动.电制动系统制动器是基于传统的制动器,也分为盘式电制动器和鼓式电制动器,鼓式电制动器由于制动热衰减性年夜等缺点,将来汽车上会以盘式电制动器为主.2 制动系统的发展趋势已经普遍应用的液压制动现在已经是非常成熟的技术,随着人们对制动性能要求的提高,防抱死制动系统、驱动防滑控制系统、电子稳定性控制法式、主动避撞技术等功能逐渐融人到制动系统傍边,需要在制动系统上添加很多附加装置来实现这些功能,这就使得制动系统结构复杂化,增加了液压回路泄漏的可能以及装配、维修的难度,制动系统要求结构更加简洁,功能更加全面和可靠,制动系统的管理也成为必需要面对的问题,电子技术的应用是年夜势所趋. 从制动系统的供能装置、控制装置、传动装置、制动器4个组成部份的发展历程来看,都分歧水平地实现了电子化.人作为控制能源,启动制动系统,发出制动企图;制动能源来自贮存在蓄电池或其它供能装置;采纳全新的电子制动器和集中控制的电子控制单位(ECU)进行制动系统的整体控制,每个制动器有各自的控制单位.机械连接逐渐减少,制动踏板和制动器之间动力传递分离开来,取而代之的是电线连接,电线传递能量,数据线传递信号,所以这种制动又叫做线控制动.这是自从ABS在汽车上获得广泛应用以来制动系统又一次飞跃式发展. 电液复合制动系统是从传统制意向电子制动的一种有效的过渡方案,采纳液压制动和电制动两种制动系统.这种制动系统既应用了传统的液压制动系统以保证足够的制动效能和平安性,又利用再生制念头电回收制动能量和提供制动力矩,提高汽车的燃料经济性,同时降低排放,减少污染.可是由于两套制动系统同时存在,结构复杂、本钱偏高.结构的复杂性也增加了系统失效和呈现故障的可能性,维护和调养难度增加.3 电制动的优缺点和存在的问题电子制动首先应用到飞机上,目前处于向汽车领域应用的研究和改进阶段,随着技术进步,各种问题会逐步获得解决,电制动系统最终会取代传统的以液压为主的制动控制系统以及电液复合制动系统.电制动或者线控制动(BBW)是未来制动系统发展的方向.电制动器和电制动控制单位、制动力模拟器是其重要组成部份,反馈制动力给制动踏板发生制动感觉.电制动一种可能的结构型式见图4.从结构上,电制动具有其它传统制动无法比力的优点:1)结构简单,系统质量较传统制动系统降低很多,从而减少了整车质量;2)制动响应时间短,提高制动性能,缩短制动距离;3)系统中不存在制动液,维护容易、简单,采纳电线连接,系统的耐久性能良好;4)系统总成的制造、装配、调试、标定更快,易于采纳模块化结构;5)已经开发出具有容错功能的适用于汽车的网络通讯协议如TTP/C,Flex Ray等通讯协议可以应用到电制动系统中.6)易于进行改进和功能的增加,可以并入汽车CAN 通讯网络进行集中管理和共享信息. 对年夜部份人来说,电制动系统是全新的制动系统,它为将来的智能化车辆提供了条件.基于现在的技术条件,要全面应用电制动,还有很多问题需要面对:1)驱动能源问题,采纳电子制动需要较多的电能,一个盘式制动器峰值需要lkW的驱动能量,目前12V的车辆电力系统无法提供这么年夜的能量,未来的车辆动力系统需要采纳高压电,加年夜能源供应,以满足各系统能量的需求,同时解决好高压电的平安问题;2)没计制动系统时必需要考虑的是制动系统的失效问题,电制动不存在主动的备用制动系统,不论是ECU、传感器、还是制动器自己、线束失效,都能使制动系统保证制动的基赋性能,除ECU可以采纳冗余设计外,实现电制动的一个关键技术是相同失效时的信息交流协议如TTP/C等的研究应用;3)实现和汽车底盘其他控制系统的集成,仍有待研究;4)采纳电制动后整车质量有所减少,可是非簧载质量可能会有所增加,这是要注意的;5)制动器在继续制动或高强度制动过程会发生高温,这对机电和传动装置的性能和散热提出了高的要求.6)本钱比原有液压制动系统高,提高电制动系统的性价比是需要解决的问题. 随着技术的进步,上述的各种问题会逐步获得解决.戴姆勒-克莱斯勒汽车公司已经把一种电制动系统——测控一体化制动系统——装置在奔跑乘用车上,它是一种功能强年夜的机电一体化的系统,在汽车运行中,系统感知制动踏板的举措,并把相关信息传递给控制单位,控制单位发出指令给执行器进行各车轮的制动,它可以根据制动踏板的加速度来识别驾驶员是否正在进行紧急制动并做出迅速反应,缩短制动距离,这种系统会增加驾驶者的平安感和舒适感,使停车过程平顺.可以预见不久的将来会有更多的电制动系统获得装车应用.4 结论在车辆模块化、集成化、电子化、车供能源的高压化的趋势驱动下,车辆制动系统也朝着电子化方向发展,很多汽车和零部件厂商都进行了电制动系统的研究和推广,博世、西门子、特维斯等公司已经研制出一些试验功效,电制动系统势必取代传统制动系统,汽车底盘进一步一体化、。
乘用车防抱死制动系统的分析及关键部件的设计

.摘 要ABS 系统可以显著提高或者改善汽车紧急制动时的操作性和稳定性,缩短了制动距离,是 一种越来越得到广泛应用的汽车电子控制产品。
此次毕业设计以小轿车为研究对象,展开对汽车 ABS 系统的研究。
主要完成了以下的工 作:通过对单个车轮的受力分析确定了影响车轮附着系数的主要因素;通过比较电磁式轮速传感器和霍尔效应式传感器的性能优缺点,采用并设计了霍尔效应 式轮速传感器;通过对控制结构的分析设计了以INTEL公司生产的80C196KC单片机为核心的部分实时控 制系统硬件部分;本文通过学习比较只是针对 ABS 控制系统的硬件部分进行设计。
在设计过程中对汽车制 动理论和制动装置有了较为深入的了解, 扩大了自己的知识面,自己解决问题的能力也得到 了较大提高。
关键词:防抱死制动系统 轮速传感器 滑移率ABSTRCTAntiLock Braking System(ABS) is an impotant device to improve the active safety of vehicle.ABS can greatly improve steering control ability during the brake maneuver and shorten stopping distance.It is a kind of more and more widely applied to automotive electronic control products.With the car as the research object,the graduation design on ABS has been carried on.And a series of work were finished:The dynamic situation of wheel was analyzed.Then,the model of hydraulic ABS was built and assured main complication affect the wheeler appendiculate coefficient.By comparing the capabilitu of electromagnetism rotate speed sensor with Houer rotate speed sensor,we chose the later,and have design a sensor of this king.Through the analysis of the structure of control designed for the production of INTEL 80C196KC singlechip microprocessor as the core part of the realtime control system hardware parts.In this paper,based on the knowledge I have mastered,I designed a ABS control system hardware only.I have gotten a indepth understand of motorcare trig theory and equipment. It Widen my knowledge scope,improved my ability of solving problems.Kyewords: electronic control system wheel speed sensor slip rate目录一.防抱死制动系统概述 (4)1.1 ABS 的功能 (4)1.2 ABS 系统在国外发展的历史 (5)1.3 ABS 系统在国内发展的现状 (6)1.4 ABS 系统发展趋势展望 (8)二.ABS 系统控制方式的工作原理 (10)2.1 制动时汽车的运动与受力分析 (10)2.1.1 制动时汽车的受力分析................................................................................... 10 2.1.2 车轮抱死时汽车运动情况.............................................................................. 11 2.2 ABS 的控制方式 (13)2.2.1 车轮滑移率以及其与附着系数的关系........................................................... 13 2.2.2 制动时车轮运动方程...................................................................................... 16 2.3 ABS 的工作原理 (17)2.3.1 ABS 控制过程曲线.......................................................................................... 17 2.3.2 ABS 基本工作原理.......................................................................................... 17 2.3.3 ABS 工作中的反应............................................................错误!未定义书签。
车辆制动系统开发方案
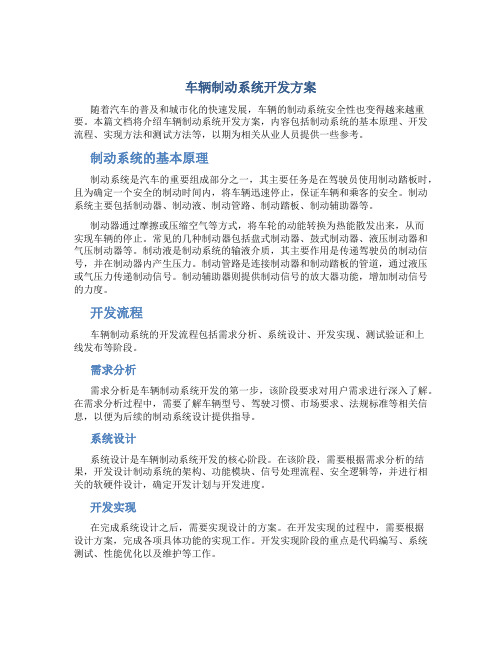
车辆制动系统开发方案随着汽车的普及和城市化的快速发展,车辆的制动系统安全性也变得越来越重要。
本篇文档将介绍车辆制动系统开发方案,内容包括制动系统的基本原理、开发流程、实现方法和测试方法等,以期为相关从业人员提供一些参考。
制动系统的基本原理制动系统是汽车的重要组成部分之一,其主要任务是在驾驶员使用制动踏板时,且为确定一个安全的制动时间内,将车辆迅速停止,保证车辆和乘客的安全。
制动系统主要包括制动器、制动液、制动管路、制动踏板、制动辅助器等。
制动器通过摩擦或压缩空气等方式,将车轮的动能转换为热能散发出来,从而实现车辆的停止。
常见的几种制动器包括盘式制动器、鼓式制动器、液压制动器和气压制动器等。
制动液是制动系统的输液介质,其主要作用是传递驾驶员的制动信号,并在制动器内产生压力。
制动管路是连接制动器和制动踏板的管道,通过液压或气压力传递制动信号。
制动辅助器则提供制动信号的放大器功能,增加制动信号的力度。
开发流程车辆制动系统的开发流程包括需求分析、系统设计、开发实现、测试验证和上线发布等阶段。
需求分析需求分析是车辆制动系统开发的第一步,该阶段要求对用户需求进行深入了解。
在需求分析过程中,需要了解车辆型号、驾驶习惯、市场要求、法规标准等相关信息,以便为后续的制动系统设计提供指导。
系统设计系统设计是车辆制动系统开发的核心阶段。
在该阶段,需要根据需求分析的结果,开发设计制动系统的架构、功能模块、信号处理流程、安全逻辑等,并进行相关的软硬件设计,确定开发计划与开发进度。
开发实现在完成系统设计之后,需要实现设计的方案。
在开发实现的过程中,需要根据设计方案,完成各项具体功能的实现工作。
开发实现阶段的重点是代码编写、系统测试、性能优化以及维护等工作。
测试验证测试验证是车辆制动系统开发的重要环节。
该阶段需要对开发实现阶段的所有功能进行测试,对测试结果进行分析评估,确定是否满足系统要求。
本阶段需要进行全方位的测试,包括单元测试、模块测试、性能测试、压力测试、安全测试、稳定性测试等。
汽车制动系统研究 论文
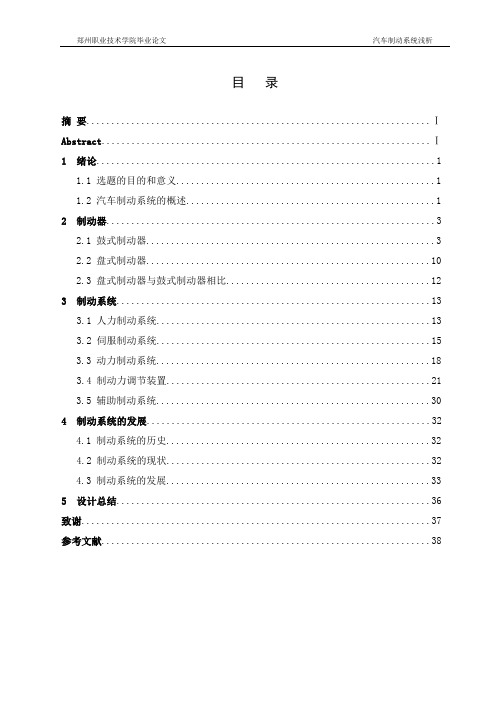
郑州职业技术学院毕业论文汽车制动系统浅析目录摘要 (Ⅰ)Abstract (Ⅰ)1 绪论 (1)1.1 选题的目的和意义 (1)1.2 汽车制动系统的概述 (1)2 制动器 (3)2.1 鼓式制动器 (3)2.2 盘式制动器 (10)2.3 盘式制动器与鼓式制动器相比 (12)3 制动系统 (13)3.1 人力制动系统 (13)3.2 伺服制动系统 (15)3.3 动力制动系统 (18)3.4 制动力调节装置 (21)3.5 辅助制动系统 (30)4 制动系统的发展 (32)4.1 制动系统的历史 (32)4.2 制动系统的现状 (32)4.3 制动系统的发展 (33)5 设计总结 (36)致谢 (37)参考文献 (38)1 绪论1.1 选题的目的和意义汽车制动系统是汽车最重要系统之一,从汽车诞生时起,该系统在车辆的安全方面就扮演着至关重要的角色,特别是近年来,随着车辆技术的进步和汽车行驶速度的提高,这种重要性表现得越来越明显。
汽车制动系统是为了使高速行驶的汽车能减速或停车而设计的。
如果该系统不能正常工作,车上的驾驶员和乘客将受到车祸的伤害,所以分析和研究汽车制动系统具有极其重要的意义,特别是对于汽车专业的毕业生来说,意义更加非凡!1.2 汽车制动系统的概述使行驶中的汽车减速甚至停车,使下坡行驶的汽车速度保持稳定,以及使已停止的汽车保持不动,这些作用统称为汽车制动。
对汽车起到制动作用的力是作用在汽车上,其方向与汽车行驶的方向相反。
作用在行驶汽车上的滚动阻力、上坡阻力、空气阻力都能对汽车起到制动作用,但这些外力的大小都是随机的、不可控制的。
因此汽车上必须装设一系列专门装置,以便驾驶员能根据道路和交通等情况,使外界(主要是路面)对汽车某部分(主要是车轮)施加一定的力,对汽车进行一定程度的强制制动。
这种可控制的对汽车进行制动的外力称为制动力,用于产生制动力的一系列专门装置称为制动系统。
1.2.1制动系统的工作原理以蹄式制动器为列:驾驶员经制动系控制装置,操纵制动器的不旋转元件制动蹄对旋转元件制动鼓(与轮毂连接)制动,从而产生Mτ(制动力矩)。
乘用车制动标准_标协会议
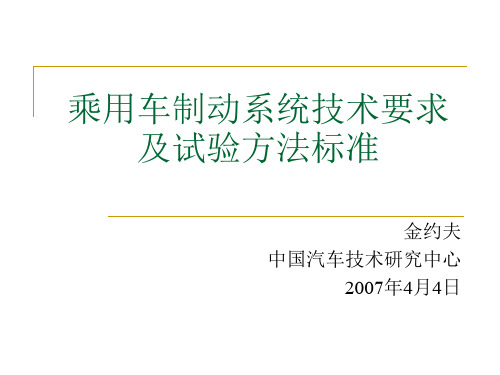
对0-型试验、I-型试验的试验条件、性能要求及关 键的操作程序等各方面作了明确规定;
在车辆基本性能要求方面,不再要求剩余制动性能 并降低了应急制动性能要求的指标,但明确规定仅 利用行车制动系也必须能够达到规定的应急制动性 能。
标准主要技术内容
试验及性能要求
对装有电力再生式制动系和采用电控传输的制动系 在试验条件和操作方面的特殊要求;
s 0.1v v2 150
MFDD 5.8
s 0.1v 0.0060v2 MFDD 6.43
40.00
75
80
85
90
95
100
105
试验车速(km/h)
标准主要技术内容
车型批准和扩展(6.)
“车型”的定义主要针对在制动系统方面进行的车 型批准和扩展,其基本原则是在对制动性能及其测 定方面具有重要影响的车辆部件和参数上不应存在 差异。
国际汽车制动法规
全标委工作文件
谢谢
明确了装有ABS、EBD、电力再生式制动系和电控 传输制动系的附加试验条件。
实施日期
本标准建议实施日期为2008年7月1日; 在生产车自本标准实施之日起12个月后开始执
行本标准; 在此之前,在生产车可在本标准与GB 12676-
1999间选择使用。
后续工作
本标准已经报批 WTO通报 全标委将会组织进行标准宣贯
v=100km/h dm≥5.15m/s2
GB 12676-1999
v=80km/h dm≥5.8 m/s2
v=80%vmax≤160km/h dm≥5.0 m/s2
一只手握住转向盘 (脚控制-行车 +手操纵-驻车)
乘用车制动标准对汽车制动性能的评价

越高,驾驶员需要保持较高的制动作用状态
的时间也越长,制动减速度也不可能保持不
变。从这个角度而言,制动减速度比制动距
离存在更多的优势。
MFDD= (ub2-ue2)
25.92(se-sb)
(式 3)
式 中,ub 为 0.8u0 的 车 速;u0 为 起 始 车
制动试验通常将制动距离和制动减速度 作为评价参数。不管是是欧盟汽车法规、美 国汽车标准都将制动距离作为唯一的评价指 标或重要评价指标之一。
(式 2)
表 1 制动距离要求
制动初速 度(km/h)
空载检验 制动距离 要求(m)
满载检验 制动距离 要求(m)
GB 725850
2017
≤19.0
≤20.0
GB 216702008
TRAFFIC AND SAFETY | 交通与安全
乘用车制动标准对汽车制动性能的评价
蒋一春 夏海峰 宁波梅山卡达克汽车检测有限公司检测部 浙江省宁波市 315000
摘 要:汽车制动性能是汽车安全性的重要评价指标之一,本文主要通过分析我国现有乘用车制动有关标准:GB 7258-2017《机动车运行安全技术条件》、GB 21670-2008《乘用车制动系统技术要求及试验方法》中的 相关要求,对乘用车制动性能进行评价。
的车速,更加贴合正常车辆行驶的制动性能
评价。而 GB 21670-2008 的初始车速为最高
车速的 80%,更偏向于评价车辆在正常行驶
极限车速下的制动性能评价。
3.2 充分发出的平均减速度
从(式 2)看出,不管采取何种方法,除
车辆本身制动性能以外,制动距离主要是受
到试验初速度和制动响应时间的影响,车速
3 制动性能评价指标
乘用车制动标准讲解全部

中国汽车技术研究中心
China Automotive Technology & Research Center
26
标准制定工作历程
n 第二次工作会议
n 中国的参与
q 成立C- WP29专家组 q 派员参加会议
q 日本的启示
n 交通安全环境研究所 n JASIC n 汽车及零部件企业
中国汽车技术研究中心
China Automotive Technology & Research Center
11
目录
n 总体情况介绍 q 国际动态
n WP29 的最新动态
n 制动力分配 n ABS 试验 n 选装衬片试验 n 复合车辆电子控制系统
q 车型批准和扩展
中国汽车技术研究中心
China Automotive Technology & Research Center
22
标准制定工作历程
n 国标计划号 n 20067130-Q-303
中国汽车技术研究中心
China Automotive Technology & Research Center
q 电力再生制动系(RBS)和电控传输制动 q 2005年12月07日
n 天津,与日产
q 2005年12月20日
n 天津,与丰田
q 2005年12月22日
n 武汉,与本田
中国汽车技术研究中心
China Automotive Technology & Research Center
☆☆乘用车制动系统开发设计流程☆☆

联立上式可以得出前后地面制动力与地面附着 系数的关系如下
Fbf m(gB ugh) u ( A B) Fbr m(gA ugh) u ( A B)
对同一车辆来说,上两式中,只有u为变量, 取不同的u值便可得到不同Fbf和Fbr值。这便 是理想制动力分配曲线。
2. 基础制动与制动主缸的联络---轮缸压力与主缸推力
现已知了主缸直径、主缸行程;基础制动系统的压力-减速度曲线,可以推导出主缸推力与制动减 速度曲线。
减速度
轮缸压力 =
主缸压力
轮缸压力
轮缸压力
轮缸推力 =
主缸压力X 活塞面积
主缸压力
主缸压力 主缸活塞推力
踏板杠杆比
3. 制动主缸与人机控制联络 ---主缸行程与踏板行程
insight 均可做为优化工具。
下一张便是2010年所写的一个B21 四连杆 踏板机构优化论文
3.3 制动控制模块布置 目前的制动控制模块主要是ABS 或者ESP(ESC)模块,模块的布置位置并没有严格的要求。但应做到 1. 靠近主缸 2. 液面低于储液罐液面(包括连接主缸-模块的制动管最高点) 3.远离热源 4. 放置淋雨(插接件插接口要防止积水) 5. 尽量放置在纵梁等NVH性能较稳定的部件之上 6. 管路易于安装,本身易于拆装
车辆制动系统开发
汽研院底盘部:李成 2011年5月10日
1. 液压制动系统简介 2. 制动系统开发理论计算 3. 子系统的开发 4. 制动系统零部件的开发 5. 制动系统客观试验 6. 制动系统主观评价
1.液压制动系统简介
液压制动系统是将驾驶人员施加到制动踏板上的 力放大,并助力后反应到制动主缸,由制动主缸建立 起整个制动管路的压力,压力将推动执行机构(制动 器)限制车轮的转动而实现制动。
ECE-R13制动

13号法规M、N和O类车辆制动系统型式认证的统一规定1. 适用范围1.1本法规适用于《关于统一汽车结构的决议》(R.E.3)1)附件7中所定义的M类、N类和O类机动车辆和挂车的制动系1.2本法规不适用于:1.2. 1设计车速低于25km/h的车辆;1.2. 2与设计车速低于25km/h的机动车挂接的挂车;1.2.3 残疾人驾驶的车辆。
1.3 根据本法规适用范围的规定,附件1中所列的设备、装置、方法和条件不包含在本法规内。
2. 定义适用于本法规。
2.1 “车辆认证”是指与制动有关的车型认证2.2 “车型”是指在以下本质方面不存在区别的一类汽车:2.2.1 机动车辆;2.2.1.1车辆种类(按1.1条);2.2.1.2最大总质量,按2.16条;2.2.1.3轴间质量分配;2.2.1.4最大设计车速;2.2.1.5制动装置类型,特别要考虑有无制动装置和其它制动装置,或者有无电动再生式制动系;2.2.1.6 车轴的数目和布置;2.2.1.7 发动机类型;1)R13-H提供了适用于M1类车辆的一套替代要求。
已经签署本法规和R13-H的各协议国应承认根据二者之一进行的认证之间的等效性。
2.2.1.8 变速器档数与档速比;2.2.1.9 主减速比;2.2.1.10 轮胎尺寸。
2.2.2 挂车2.2.2.1 车辆种类(按1.1条);2.2.2.2 最大总质量,按2.16条定义;2.2.2.3 轴间质量分配;2.2.2.4 制动装置类型;2.2.2.5 车轴数目和布置;2.2.2.6 轮胎尺寸。
2.3 “制动系统”是指一些能使行驶车辆逐步减速或停止,或使已经停驶的车辆保持静止状态的零件的组合;这些功能的规定见5.1.2条。
该系统由控制装置、传能装置和制动器本身组成。
2.4 “控制器”是指由驾驶员(或副驾驶员,对挂车而言)直接驱动向传能装置提供制动或控制所需能量的部件。
这些能量可以是驾驶员的体力,也可以是由驾驶员控制的另一种能源的能量,在某些适当的情况下可以是挂车的动能或者是这些不同种类能量的组合。
乘用车制动系统设计-开题报告
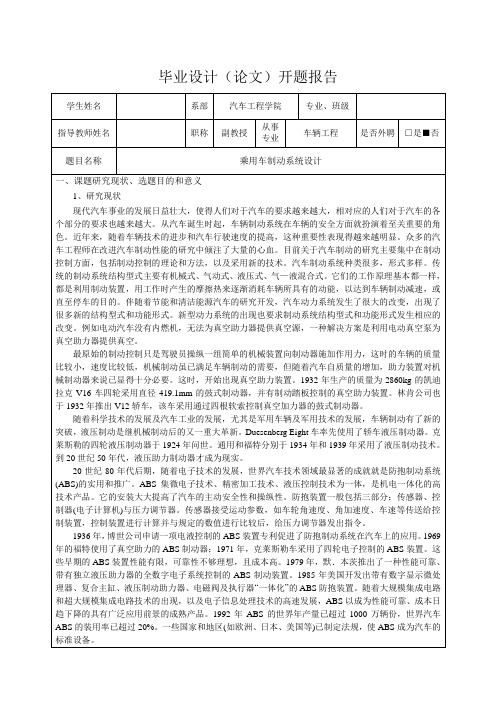
1936 年,博世公司申请一项电液控制的 ABS 装置专利促进了防抱制动系统在汽车上的应用。1969 年的福特使用了真空助力的 ABS 制动器;1971 年,克莱斯勒车采用了四轮电子控制的 ABS 装置。这 些早期的 ABS 装置性能有限,可靠性不够理想,且成本高。1979 年,默.本茨推出了一种性能可靠、 带有独立液压助力器的全数字电子系统控制的 ABS 制动装置。1985 年美国开发出带有数字显示微处 理器、复合主缸、液压制动助力器、电磁阀及执行器“一体化”的 ABS 防抱装置。随着大规模集成电路 和超大规模集成电路技术的出现,以及电子信息处理技术的高速发展,ABS 以成为性能可靠、成本日 趋下降的具有广泛应用前景的成熟产品。1992 年 ABS 的世界年产量已超过 1000 万辆份,世界汽车 ABS 的装用率已超过 20%。一些国家和地区(如欧洲、日本、美国等)已制定法规,使 ABS 成为汽车的 标准设备。
经过了一百多年的发展,汽车制动系统的形式已经基本固定下来。随着电子,特别是大规模、超 大规模集成电路的发展,汽车制动系统的形式也将发生变化。如凯西-海斯(K-H)公司在一辆实验车上 安装了一种电-液(EH)制动系统,该系统彻底改变了制动器的操作机理。通过采用 4 个比例阀和电力电 子控制装置,K-H 公司的 EBM 就能考虑到基本制动、ABS、牵引力控制、巡航控制制动干预等情况,而 不需另外增加任何一种附加装置。EBM 系统潜在的优点是比标准制动器能更加有效地分配基本制动力, 从而使制动距离缩短 5%。一种完全无油液、完全的电路制动 BBW(Brake-By-Wire)的开发使传统的液压 制动装置成为历史。
车辆制动系统设计方案方案发展翻译

车辆制动系统设计方案的发展S.P.JUNG1),KJ.JUN1>,TWPARK 2)*and j.H.YOON3>1)亚洲大学,研究生院机械工程学院,韩国京畿道443-749 2)亚洲大学,机械工程学系,韩国京畿道443-7493),龙仁市器兴,区洞Mabook ,现代摩比斯,80-9 ,韩国京畿道446-912 <2007年5月12出版,2007年11月21日修订)摘要--制动系统有许多部分组成,它包括一个助推器、主缸和卡尺,因此评价汽车制动性能是相当有挑战性的。
通过车辆测试来计算制动力需要很多时间和金钱。
因此,发展一个定性估计车辆制动性能的方法是有益的。
这个研究给出了一个可以分析车辆制动能力,如压力,效率,踏板行程的介绍。
使用该程序可把制动盘温度的增加和各种助推器的性能测试出来。
根据悬挂系统的位移,由配备负荷传感比例阀的车辆的动态特性,可精确地得到阀门压力变化。
因为所有的输入和输出文件都可使用微软的电子表格,轻松完成设计数据管理和数据库建设。
关键词:制动性能,踏板行程,制动力,负载敏感比例阀命名α:减速度,m/s2W DF,W DR:轴载荷转移,kgl :轴距,mmh :重心,mmB F,B R:前方,后方的理想制动力,kgfLP IF,LP IR:车头,车尾的理想线压力,kgf/cm 2LP AF,LP AR:车头,车尾的实际线压力,kgf/cm 2TP F,TP R:车头,车尾的门槛压力,kgf/cm 2C F,C R:前轮,后轮制动恒定,kgf/cm 2P C:阀截止点的压力,kgf/cm 2F pedal :踏板的努力,kgf F0:踏板力损失,kgf:带够,踏板,增压比ηP,ηB:带够,踏板,制动效率F inp,F out:增压器的输入输出力,kgfK:助推器伺服比例R:轮胎半径,mmR Eff :轮胎的有效半径,mmA C : 面积卡尺,EAN P :数字活塞,EABF :制动因数1.引言为了车辆的安全,在各种车辆的驾驶特点中,制动性能应该是首要考虑因素。
制动系统发展趋势

之青柳念文创作从汽车诞生时起,车辆制动系统在车辆的平安方面就饰演着至关重要的脚色.近些年来,随着车辆技术的前进和汽车行驶速度的提高,这种重要性表示得越来越分明.汽车制动系统种类很多,形式多样.传统的制动系统布局型式主要有机械式、气动式、液压式、气—液混合式.它们的工作原理基本都一样,都是操纵制动装置,用工作时发生的磨擦热来逐渐消耗车辆所具有的动能,以达到车辆制动减速,或直至停车的目标.陪同着节能和清洁动力汽车的研究开辟,汽车动力系统发生了很大的改变,出现了很多新的布局型式和功能形式.新型动力系统的出现也要求制动系统布局型式和功能形式发生相应的改变.例如电动汽车没有内燃机,无法为真空助力器提供真空源,一种处理方案是操纵电动真空泵为真空助力器提供真空. 汽车制动系统的发展是和汽车性能的提高及汽车布局型式的变更紧密亲密相关的,制动系统的每一个组成部分都发生了很大变更.1 汽车制动系统的组成制动系统主要由下面的4个部分组成:(1)供能装置:也就是制动动力,包含供给、调节制动所需能量以及各个部件,发生制动能量的部分称为制动动力;(2)节制装置:包含发生制动动作和节制制动效果的部件;(3)传动装置:包含把制动能量传递到制动器的各个部件;(4)制动器:发生阻碍车辆运动或者运动趋势的力的部件,也包含辅助制动系统中的部件. 现代的制动系统还包含制动力调节装置和报警装置,压力呵护装置等辅助装置.1.1 供能装置的发展供能装置主要是指制动动力,制动动力有人力制动、伺服制动、动力制动或者上述任二者的连系使用. 人力制动是开端有制动系统时的制动动力,它有机械式制动、液压式制动两种形式.机械式制动主要用于驻车制动系统中,驻车制动系统中要求用机械锁止方法包管汽车在原地停止不动,在任何情况下不至于滑动.液压式制动是通过制动踏板推动制动主缸,进而使制动器进入工作状态.伺服制动兼用人力和发动机作为制动动力,正常情况下制动能量由动力伺服系统供给,动力伺服系统失效时可由人力供给制动能量,这时伺服制动就变成人力制动.伺服制动可用气压能、真空能(负气压能)以及液压能作为伺服能量,形成各种形式的助力器.动力制动系统的制动动力是发动机所驱动的油泵或者气泵,人力仅作为节制来历,可分为气压制动、气顶液制动、液压制动.其中气压制动是发展最早的一种动力制动系统.它用空气压缩机提供气压,气顶液制动是用气压推动液压动作,发生制动作用.液压制动是今朝得到广泛应用的一种制动系统,技术已经非常成熟.今朝正在发展的电液复合制动以及电子制动中使用了电机作为制动动力,人力踩制动踏板作为节制来历.1.2节制装置的发展最早的人力制动,通过机械的毗连发生制动动作.发展到人力节制制动,通过踩制动踏板启动制动,再由传力装置把制动踏板力传到真空助力器,颠末真空助力器的助力扩展后,传递到制动主缸发生液压力,然后通过油路把液压力传递到每一个轮缸,开端制动.随着清洁动力汽车和电动汽车的研究应用,以及电子技术在汽车上面的广泛应用,制动系统的节制装置也出现了电子化的趋势,其中电制动完全改变了制动系统的节制和管理,会使汽车制动系统发生革命性的变更,它采取电子节制,可以更加准确、更高效率地实现制动.1.3传动装置的发展人力制动时代是采取机械式的传动装置,气(液)压制动是操纵气(液)压力和毗连收路把制动力传递到制动器.电子制动则是操纵制动电机发生制动力直接作用到制动器,它的节制信号来自节制单元(ECU),用信号线传递制动信号和制动力信息.1.4制动器的发展制动器是制动的主要组成部分,今朝汽车制动器基本都是磨擦式制动器,依照磨擦副中旋转元件的分歧,分为鼓式和盘式两大类制动器. 鼓式制动器又有领从蹄式、双领蹄式、双向双领蹄式、双从蹄式、单向自增力式、双向自增力式制动器等布局型式.盘式制动器有固定钳式,浮动钳式,浮动钳式包含滑动钳式和摆动钳盘式两种型式.滑动钳式是今朝使用广泛的一种盘式制动器.由于盘式制动器热和水稳定性以及抗衰减性能较鼓式制动器好,靠得住性和平安性也好,而得到广泛应用.但是盘式制动器效能低,无法完全防止尘污和锈蚀,兼做驻车制动时需要较为复杂的手驱动机构,因而在后轮上的应用受到限制,很多车是采取前盘后鼓的制动系统组成.电动汽车和混合动力汽车上具有再生制动才能的电机,在回收制动能量时起制动作用,它引入了新型的制动器.作为一种新的制动器型式,势必引起制动器型式的变动.电制动系统制动器是基于传统的制动器,也分为盘式电制动器和鼓式电制动器,鼓式电制动器由于制动热衰减性大等缺点,将来汽车上会以盘式电制动器为主.2 制动系统的发展趋势已经普遍应用的液压制动现在已经是非常成熟的技术,随着人们对制动性能要求的提高,防抱死制动系统、驱动防滑节制系统、电子稳定性节制程序、主动避撞技术等功能逐渐融人到制动系统当中,需要在制动系统上添加很多附加装置来实现这些功能,这就使得制动系统布局复杂化,增加了液压回路泄漏的能够以及装配、维修的难度,制动系统要求布局更加简洁,功能更加全面和靠得住,制动系统的管理也成为必须要面临的问题,电子技术的应用是大势所趋. 从制动系统的供能装置、节制装置、传动装置、制动器4个组成部分的发展过程来看,都分歧程度地实现了电子化.人作为节制动力,启动制动系统,发出制动企图;制动动力来自储存在蓄电池或其它供能装置;采取全新的电子制动器和集中节制的电子节制单元(ECU)停止制动系统的整体节制,每一个制动器有各自的节制单元.机械毗连逐渐减少,制动踏板和制动器之间动力传递分分开来,取而代之的是电线毗连,电线传递能量,数据线传递信号,所以这种制动又叫做线节制动.这是自从ABS在汽车上得到广泛应用以来制动系统又一次飞跃式发展. 电液复合制动系统是从传统制动向电子制动的一种有效的过渡方案,采取液压制动和电制动两种制动系统.这种制动系统既应用了传统的液压制动系统以包管足够的制动效能和平安性,又操纵再生制动电机回收制动能量和提供制动力矩,提高汽车的燃料经济性,同时降低排放,减少污染.但是由于两套制动系统同时存在,布局复杂、成本偏高.布局的复杂性也增加了系统失效和出现故障的能够性,维护和调养难度增加.3 电制动的优缺点和存在的问题电子制动首先应用到飞机上,今朝处于向汽车范畴应用的研究和改进阶段,随着技术前进,各种问题会逐步得到处理,电制动系统最终会取代传统的以液压为主的制动节制系统以及电液复合制动系统.电制动或者线节制动(BBW)是未来制动系统发展的方向.电制动器和电制动节制单元、制动力摹拟器是其重要组成部分,反馈制动力给制动踏板发生制动感觉.电制动一种能够的布局型式见图4.从布局上,电制动具有其它传统制动无法比较的优点:1)布局简单,系统质量较传统制动系统降低很多,从而减少了整车质量;2)制动响应时间短,提高制动性能,缩短制动间隔;3)系统中不存在制动液,维护容易、简单,采取电线毗连,系统的经久性能杰出;4)系统总成的制造、装配、调试、标定更快,易于采取模块化布局;5)已经开辟出具有容错功能的适用于汽车的网络通讯协议如TTP/C,Flex Ray等通讯协议可以应用到电制动系统中.6)易于停止改进和功能的增加,可以并入汽车CAN通讯网络停止集中管理和共享信息. 对于大部分人来讲,电制动系统是全新的制动系统,它为将来的智能化车辆提供了条件.基于现在的技术条件,要全面应用电制动,还有很多问题需要面临:1)驱动动力问题,采取电子制动需要较多的电能,一个盘式制动器峰值需要lkW的驱动能量,今朝12V的车辆电力系统无法提供这么大的能量,未来的车辆动力系统需要采取高压电,加大动力供应,以知足各系统能量的需求,同时处理好高压电的平安问题;2)没计制动系统时必须要思索的是制动系统的失效问题,电制动不存在主动的备用制动系统,不管是ECU、传感器、还是制动器自己、线束失效,都能使制动系统包管制动的基赋性能,除了ECU可以采取冗余设计外,实现电制动的一个关键技术是相同失效时的信息交流协议如TTP/C等的研究应用;3)实现和汽车底盘其他节制系统的集成,仍有待研究;4)采取电制动后整车质量有所减少,但是非簧载质量能够会有所增加,这是要注意的;5)制动器在持续制动或高强度制动过程会发生高温,这对电机和传动装置的性能和散热提出了高的要求.6)成本比原有液压制动系统高,提高电制动系统的性价比是需要处理的问题. 随着技术的前进,上述的各种问题会逐步得到处理.戴姆勒-克莱斯勒汽车公司已经把一种电制动系统——测控一体化制动系统——装置在奔驰乘用车上,它是一种功能强大的机电一体化的系统,在汽车运行中,系统感知制动踏板的动作,并把相关信息传递给节制单元,节制单元发出指令给执行器停止各车轮的制动,它可以根据制动踏板的加速度来识别驾驶员是否正在停止告急制动并做出迅速反应,缩短制动间隔,这种系统会增加驾驶者的平安感和舒适感,使停车过程平顺.可以预见不久的将来会有更多的电制动系统得到装车应用.4 结论在车辆模块化、集成化、电子化、车供动力的高压化的趋势驱动下,车辆制动系统也朝着电子化方向发展,很多汽车和零部件厂商都停止了电制动系统的研究和推广,博世、西门子、特维斯等公司已经研制出一些试验成果,电制动系统势必取代传统制动系统,汽车底盘进一步一体化、集成化,制动系统性能也会发生质的飞跃.。
- 1、下载文档前请自行甄别文档内容的完整性,平台不提供额外的编辑、内容补充、找答案等附加服务。
- 2、"仅部分预览"的文档,不可在线预览部分如存在完整性等问题,可反馈申请退款(可完整预览的文档不适用该条件!)。
- 3、如文档侵犯您的权益,请联系客服反馈,我们会尽快为您处理(人工客服工作时间:9:00-18:30)。
助力比,取决于反馈盘 面积比
至此 系统性的匹配工作基本结束。
助力器推杆行程
A B
C
D
Braking System Development
制动系统开发
系统匹配工作结束 确定的参数 1.前后卡钳缸径 2.前后摩擦系数 3.前后有效半径 4. 制动主缸直径 5. 踏板机构杠杆比 6.助力器助力比 7 .助力器尺寸。 带着这些参数接下来该选取合适的零部件或者重新开发零部件,进入子系统布置阶段。
3.子系统的开发---基础制动系统
3.1 前后制动钳的布置 A 圆周方向布置 卡钳在轮辋内圆周布置上,最佳位置为时针4:30 优点: 1.从力学角度分析,这样的布置制动时对轴 承的径向载荷最小。 2.从卡钳冷却角度,这个布置对卡钳迎风也 较好,且降低了质心。 缺点: 1.卡钳位置过低,车轮泥水更容易灌入。 2.对转向节臂的位置影响较大(转向节臂前
Af\Ar : 前后卡钳活塞面积(卡钳为系列化产品,只需参考Benchmark 及轮辋的尺寸来选定一个初始尺寸( 51、54、57…..) Uf\Ur : 前后卡钳摩擦块摩擦系数(0.32-0.4) Ref\Rer: 前后卡钳制动有效半径(根据轮辋及卡钳尺寸,并参考Benchmark,并考虑三化原则设定或选定一 个初始值) R : 车轮滚动半径,一般乘用车前后轮滚动半径都相同。
在附着系数等于0.9的路 面上制动,随着制动器制动力 的增加,超过同步附着系数仍 未有车轮抱死。当实际制动力 与0.9的r线相交后,后轮抱死, 此后前后轮的地面制动力沿0.9 的r线变化,后轮地面制动力有 所减小(重量前移)。前轮地 面制动力按实际制动器制动力 大幅增加,当0.9r线与理想制 动力相交,前轮也抱死,制动 器制动力再增加已无意义。
在 A、 u、 Re、 确定初始值之后,取液压P(0-12Mpa)计算出对应的前后轮制动器制动力 ,并叠加到理想制动力曲线图中。
Braking System Development
制动系统开发 A . 要保证12Mpa时的制动器制动 力大于至少1.0的地面附着力,如 果不满足,可同时增大1.前后轮 缸2.摩擦系数 3. 有效半径(优 先排序)
减速度
轮缸压力
主缸压力
轮缸压力 = 主缸压力
轮缸推力 = 主缸压力X 活塞面积 主缸压力
主缸活塞推力
轮缸压力
3. 制动主缸与人机控制联络 ---主缸行程与踏板行程 目前已知了活塞总行程+ 主缸空行程+助力器空行 程=助力器推杆行程 基于人机工程的要求, 制动踏板的行程有要求 (<=130mm)
A 助力器推杆所需行程
1. 基础制动与制动主缸的联络----卡钳与主缸 现已知卡钳缸径(或需液量)可选出主缸直径(因为主缸为直径-行程系列化产品,行程一般为18+18)
Braking System Development
制动系统开发
2. 基础制动与制动主缸的联络---轮缸压力与主缸推力 现已知了主缸直径、主缸行程;基础制动系统的压力-减速度曲线,可以推导出主缸推力与制动减 速度曲线。
Braking System Development
制动系统开发 3 前后制动钳的布置 B 轴向布置
制动盘中 心尽量靠 近轴承中 心
作用在制动盘上的切向力 轴承附加弯矩
轴承中心
摩擦力力臂
只有将制动盘中心与轴承中心重合,摩擦力力臂才能为0, 轴承才不会有附加弯矩。对轴承寿命有益
Braking System Development
B 制动踏板要求的行程
踏 板 杠 杆 比
Braking System Development
制动系统开发
踏板机构杠杆比的计算要点。
4. 制动主缸与人机控制联络--帮助力 在确定踏板杠杆比之后,踏板的 输出力也已知。
A 踏板输出力
B 主缸所需的推力
帮 助 力 ( 助 力 比 )
Braking System Development
2)前处理,明确转向节用料,网格划分;材料赋予,设计空间非设计空间区分;载荷工况提取(MBD)约 束设置,优化目标设定; 3)提交解算,优化结果解析;
4)模型重建,利用优化结果作为参考CAD 软件重新设计出转向节模型
5)重建模型的验证,CAE 软件将重建的模型进行详细分析;
Braking System Development
3. 前后摩擦块摩擦系数 摩擦块开发重要参数
减速度
4. 管路压力与制动力或制动减速度关系曲线
压力
Braking System Development
制动系统开发
2.2制动系统开发理论计算
原则:车有异,人相同 世面车型千差万别,但对于同一区域的驾驶者却无不同,所以对踏板力,踏板行程这一要求,不同 车辆应有相同的要求。
Braking System Development
制动系统开发
Fbf m( gB ugh) u ( A B)
Fbr m( gA ugh) u ( A B)
Fr
满载理想制动力分配曲线
最理想状况,空满载理想制动 力曲线完全重合。这样空满载同步 附着系数都可以取到最常用附着系 数点,要做到空满载重合,这里需 要做到 1.空满载前后轴荷比例相同(即质 心在整车X 方向位置不变) 2.空满载车辆质心高度相同。
Braking System Development
制动系统开发
2.1 制动系统开发理论计算-基础制动
Fbf u Ff
Fb u m g
h
Fbr u Fr
Fbf Fbr Fb
联立上式可以得出前后地面制动力与地面附着 系数的关系如下
A
B
m g B m a h m g A m a h Ff Fr ( A B) ( A B) ( A B) ( A B)
Braking System Development
制动系统开发
典型工况分析-低附着路面 在附着系数等于0.3的路 面上制动,随着制动器制动 力的增加,当实际制动力与 0.3的f线相交后,前轮抱死, 此后前后轮的地面制动力沿 0.3的f线变化,前轮地面制 动力略有增加(重量前移)。 后轮地面制动力按实际制动 器制动力大幅增加,当0.3f 线与理想制动力相交,后轮 也抱死,制动器制动力再增 加已无意义。
实际制动力分配曲线 R线组
理想制动力分配曲线
F线组
前轮地面制 动力增量
前轮制动器 制动力增量
后轮制动器制动 力亦地面制动力 增量
Braking System Development
制动系统开发
典型工况分析-高附着路面
后轮制动器制 动力增量
实际制动力分配曲线 R线组
理想制动力分配曲线
F线组
后轮地面制动 力增量(负值 )
制动系统开发
4. 助力器的选择 现已确定了助力比以及先前已确定的主缸行程,分析助力器的特性曲线,我们可以选择出合适的助力 器
最大帮助力,取决于助 力器尺寸
助 力 器 输 出 力
对于同一个助力器,助力比和助 力 行程是相互矛盾的,大助力比意味着短 的助力行程, 所以一般的原则是先确定助力比, 再通过行程来决定助力器尺寸(不同助 力器可以有相同的助力比,但最大帮助 力不同)。
空满载理想制动力分配曲 线差异
有乘用车车能做到这两点吗?No
但还是要尽力去做到两条线接近。 方程式赛车勉强可以,且方程 式赛车使用在单一附着系数路面工 作,所以方程式赛车不必匹配ABS 系统。
空载理想制动力分配曲线
Ff
Braking System Development
制动系统开发 实际制动力分配曲线(制动器制动力)
Braking System Development
制动系统开发
4.制动系统零部件的开发
在完成子系统零部件的布置之后,就要开始各零部件的结构设计了。零部件结构设计需要关注材料、工 艺、成本、强度、刚度、模态等等方面。 比如转向节的设计。 在完成了卡钳、制动盘、轴承、轮辋等零部件的布置后,
1)CAD 软件设计出最大轮廓的转向节优化空间;
a Fb m
Fbf m( gB ugh) u ( A B)
Fbr m( gA ugh) u ( A B)
假设制动时车轮完全抱死,整车制动力就等于地 面附着力
对同一车辆来说,上两式中,只有u为变量, 取不同的u值便可得到不同Fbf和Fbr值。这便 是理想制动力分配曲线。
制动系统开发
4.制动系统零部件的开发
设计空间CAD 软件
优化设计前 处理-CAE 软件
优化设计-Hyper Works-Opstruct
模型重建CAD 软件
模型验证CAE 软件
Braking System Development
H 点
踏点
Braking System Development
制动系统开发
3.3 制动控制模块布置 目前的制动控制模块主要是ABS 或者ESP(ESC)模块,模块的布置位置并没有严格的要求。但应做到 1. 靠近主缸 2. 液面低于储液罐液面(包括连接主缸-模块的制动管最高点) 3.远离热源 4. 防止淋雨(插接件插接口要防止积水) 5. 尽量放置在纵梁等NVH性能较稳定的部件之上 6. 管路易于安装,本身易于拆装
置 或者顶置)
Braking System Development
制动系统开发
只有将卡钳布置在4:30位置时 摩擦块对 制 动盘的作用力与合力方向共线反向,合力 最小,轴承载荷最小。
正压力Fz
正压力Fz与地面制动 力Fx的合力
地面制动力Fx=FzXu
Fb平移到轮心处
摩擦块对制动盘的摩 擦力Fb=Fx X Re/Rr
满载理想制动力分配曲线 满载同步附着系数