☆☆乘用车制动系统开发设计流程☆☆
公路机动车底盘:乘用车制动系统的设计与优化
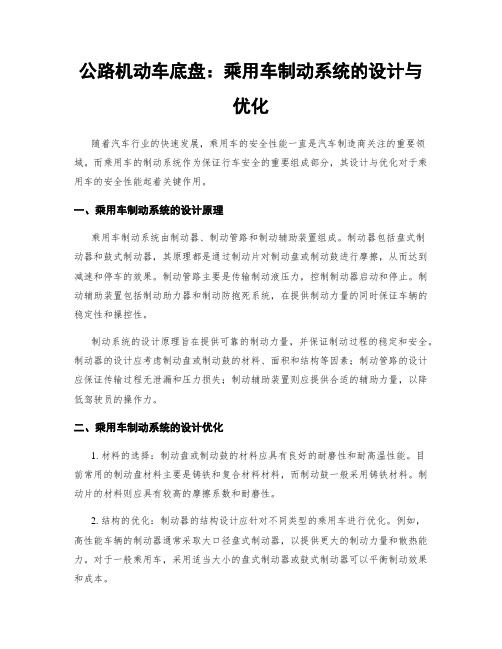
公路机动车底盘:乘用车制动系统的设计与优化随着汽车行业的快速发展,乘用车的安全性能一直是汽车制造商关注的重要领域。
而乘用车的制动系统作为保证行车安全的重要组成部分,其设计与优化对于乘用车的安全性能起着关键作用。
一、乘用车制动系统的设计原理乘用车制动系统由制动器、制动管路和制动辅助装置组成。
制动器包括盘式制动器和鼓式制动器,其原理都是通过制动片对制动盘或制动鼓进行摩擦,从而达到减速和停车的效果。
制动管路主要是传输制动液压力,控制制动器启动和停止。
制动辅助装置包括制动助力器和制动防抱死系统,在提供制动力量的同时保证车辆的稳定性和操控性。
制动系统的设计原理旨在提供可靠的制动力量,并保证制动过程的稳定和安全。
制动器的设计应考虑制动盘或制动鼓的材料、面积和结构等因素;制动管路的设计应保证传输过程无泄漏和压力损失;制动辅助装置则应提供合适的辅助力量,以降低驾驶员的操作力。
二、乘用车制动系统的设计优化1. 材料的选择:制动盘或制动鼓的材料应具有良好的耐磨性和耐高温性能。
目前常用的制动盘材料主要是铸铁和复合材料材料,而制动鼓一般采用铸铁材料。
制动片的材料则应具有较高的摩擦系数和耐磨性。
2. 结构的优化:制动器的结构设计应针对不同类型的乘用车进行优化。
例如,高性能车辆的制动器通常采取大口径盘式制动器,以提供更大的制动力量和散热能力。
对于一般乘用车,采用适当大小的盘式制动器或鼓式制动器可以平衡制动效果和成本。
3. 制动力的分配:对于前置驱动或四驱车辆,制动力的分配应考虑前后轴之间的平衡。
前轴制动力过大或过小都会影响车辆的操控性和稳定性。
4. 制动管路的优化:制动管路的设计应降低管路的压力损失和泄漏风险。
采用高质量的制动软管、合适的管径和优化的布置可以有效提高制动系统的性能。
5. 制动辅助装置的改进:制动助力器应提供合适的助力力量,根据车速和制动力量的需求进行调整,从而保证驾驶员的操控感和制动的稳定性。
防抱死系统可以通过不断调整制动力量,防止车轮锁死,提高制动过程的控制性和稳定性。
汽车底盘部分制动系统设计开发指南

5、制动部分设计指南 5.1简要说明5.1.1 内容概括● 制动系统包括行车制动系统,驻车制动系统,应急制动系统;行车制动:使行驶中的汽车减速甚至停车,使下坡行驶的汽车的速度保持稳定的一套装置 ; 驻车制动:使已停使的汽车驻留原地不动的一套装置;应急制动:在行车制动系统部分失效或完全失效的情况下保证汽车仍能实现减速或停车的一套装置; ● 制动系统的开发流程:5.1.2适用范围适用于所有奇瑞公司所开发的车型.5.1.3 设计目的合理设计汽车的制动系统,其目的在于:在满足国家法规要求的同时,具有良好的舒适性,满足用户的要求.5.1.4 零件结构图制动系统主要分为三部分:1行车制动系统:包括基础制动器,真空助力器,制动管路,踏板,2.驻车制动系统,包括驻车操纵机构总成,制动拉索,驻车制动器3.压力调节装置包括包括ABS控制器总成或比例阀,ABS传感器等,5.2设计构想5.2.1 设计原则5.2.1.1 制动系统的功能要求●行车制动必须保证驾驶员在行车过程中能控制机动车安全、有效地减速和停车。
行车制动必须是可控制的,且必须保证驾驶员在其座位上双手无须离开方向盘(或方向把)就能实现制动; 驻车制动应能使机动车即使在没有驾驶员的情况下,也能停在上、下坡道上。
驾驶员必须在座位上就可以实现驻车制动。
●制动效能要满足法规要求●有良好的制动稳定性●驾驶感好(包括踏板力,踏板行程)●有良好的热衰退性能(通过AMS试验来验证,详见试验部分)5.2.1.2 制动系统的顾客要求在满足制动性能的前提下,还应该满足舒适性要求,如:操作方便,行车制动在产生最大制动效能时的踏板力,对于乘用车不应大于230N ;手握力不应大于 250 N,除了这些力的要求,尽量避免有制动点头,制动时摩擦片尖叫等不良现象,同时在行车制动系统失效的情况下,还应具有应急制动的功能.5.2.1.3 制动系统的性能要求制动系统性能要满足法规GB/T12676要求,GB/T12676等同于欧洲法规ECER13-09,ECER13H-00及美国法规FMVSS 1355.2.2 制动系统设计计算5.2.2.1 ●决定制动系统关键参数的因素:详见下表●计算过程汽车制动时,地面作用于车轮的切线力称为地面制动力Fxb,它是使汽车制动而减速行驶的外力。
汽车制动系统设计说明书
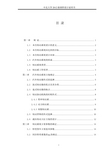
目录第一章绪论 (1)1.1 本次制动系统设计的意义 (2)1.2 本次制动系统应达到的目标 (2)1.3 本次制动系统设计内容 (3)1.4 汽车制动系统的组成 (3)1.5 制动系统类型 (3)1.6 制动系工作原理 (3)第二章汽车制动系统方案确定 (4)2.1 汽车制动器形式的选择 (5)2.2 鼓式制动器的优点及其分类 (6)2.3 盘式制动器的缺点 (8)2.4 制动驱动机构的结构形式 (8)2.4.1 简单制动系 (9)2.4.2 动力制动系 (9)2.4.3 伺服制动系 (10)2.5 制动管路的形式选择 (10)2.6 液压制动主缸方案的设计 (12)第三章制动系统主要参数的确定 (14)3.1 轻型货车主要技术参数 (14)的确定 (14)3.2 同步附着系数的3.3 前、后轮制动力分配系数 的确定 (15)3.4 鼓式制动器主要参数的确定 (16)3.5 制动器制动力矩的确定 (18)3.6 制动器制动因数计算 (19)3.6.1 制动器制动因数计算 (19)3.6.1 制动器制动因数计算 (20)3.7 鼓式制动器零部件的结构设计 (21)第四章液压制动驱动机构的设计计算 (24)4.1 制动轮缸直径d的确定 (24)的计算 (25)4.2 制动主缸直径d4.3 制动踏板力F (26)P4.4 制动踏板工作行程Sp (26)第五章制动性能分析 (27)5.1 制动性能评价指标 (27)5.2 制动效能 (27)5.3 制动效能的恒定性 (27)5.4 制动时汽车的方向稳定性 (28)5.5 前、后制动器制动力分配 (28)5.5.1 地面对前、后车轮的法向反作用力 (29)5.6 制动减速度j (29)5.7 制动距离S (29)5.8 摩擦衬片(衬块)的磨损特性计算 (30)5.9 汽车能够停留在极限上下坡角度计算 (32)第六章总结 (33)参考文献 (34)一.绪论汽车工业是一个综合性产业,汽车工业的生产水平,能够代表一个国家的整个工业水平,汽车工业的发展,能够带动各行各业的发展,进而促进我国工业生产的总体水品。
车辆制动系统开发方案
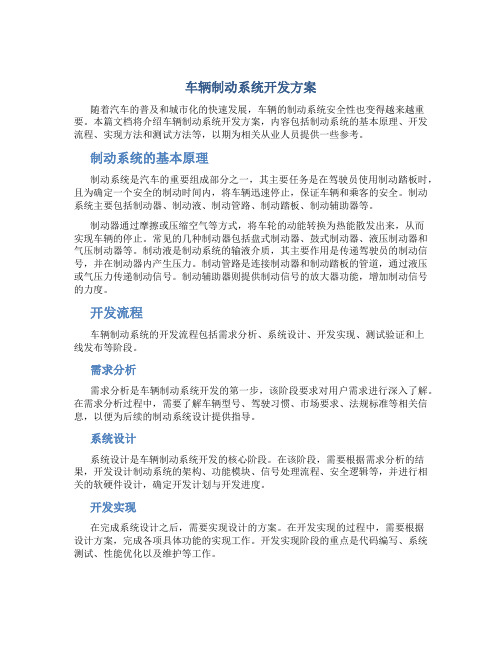
车辆制动系统开发方案随着汽车的普及和城市化的快速发展,车辆的制动系统安全性也变得越来越重要。
本篇文档将介绍车辆制动系统开发方案,内容包括制动系统的基本原理、开发流程、实现方法和测试方法等,以期为相关从业人员提供一些参考。
制动系统的基本原理制动系统是汽车的重要组成部分之一,其主要任务是在驾驶员使用制动踏板时,且为确定一个安全的制动时间内,将车辆迅速停止,保证车辆和乘客的安全。
制动系统主要包括制动器、制动液、制动管路、制动踏板、制动辅助器等。
制动器通过摩擦或压缩空气等方式,将车轮的动能转换为热能散发出来,从而实现车辆的停止。
常见的几种制动器包括盘式制动器、鼓式制动器、液压制动器和气压制动器等。
制动液是制动系统的输液介质,其主要作用是传递驾驶员的制动信号,并在制动器内产生压力。
制动管路是连接制动器和制动踏板的管道,通过液压或气压力传递制动信号。
制动辅助器则提供制动信号的放大器功能,增加制动信号的力度。
开发流程车辆制动系统的开发流程包括需求分析、系统设计、开发实现、测试验证和上线发布等阶段。
需求分析需求分析是车辆制动系统开发的第一步,该阶段要求对用户需求进行深入了解。
在需求分析过程中,需要了解车辆型号、驾驶习惯、市场要求、法规标准等相关信息,以便为后续的制动系统设计提供指导。
系统设计系统设计是车辆制动系统开发的核心阶段。
在该阶段,需要根据需求分析的结果,开发设计制动系统的架构、功能模块、信号处理流程、安全逻辑等,并进行相关的软硬件设计,确定开发计划与开发进度。
开发实现在完成系统设计之后,需要实现设计的方案。
在开发实现的过程中,需要根据设计方案,完成各项具体功能的实现工作。
开发实现阶段的重点是代码编写、系统测试、性能优化以及维护等工作。
测试验证测试验证是车辆制动系统开发的重要环节。
该阶段需要对开发实现阶段的所有功能进行测试,对测试结果进行分析评估,确定是否满足系统要求。
本阶段需要进行全方位的测试,包括单元测试、模块测试、性能测试、压力测试、安全测试、稳定性测试等。
乘用车设计流程

二、概念设计阶段
2.1.3 汽车的布局
FF缺点
FF的驱动轮附着利用率较小,上坡时驱动轮的附着力会减
小;前轮的驱动兼转向结构比较复杂,引擎和传动系统集 中在引擎舱内,布局拥挤,局限了采用大型引擎的可能性。 这是大型轿车不采用FF的主要原因。针对这个问题,近年 来出现了纵置引擎的FF布局(以前FF的引擎都是横置的),
2.1.3 汽车的布局
以电视机为例,所有电视机的内部结构大多相差无几,
大致上都为立方体,造型所要提供的功能也不多。
汽车的内部结构复杂,使用功能的要求很严格(如乘 员/载货的空间、人体工程学要求等),这些构成了很多 在造型设计过程中必须遵循的条件。因此,汽车造型设 计师必须具备很清晰明确的布局观念,才能设计出具有
2.1.3 汽车的布局
一、何谓布局?
这里所讲的布局,是指如何安排一部汽车的各个组成
部分在整车中所处的相对位置,即全车的整体布局。布 局方案一般是由总工程师决定的,但对于车身造型设计 师,很好地理解甚至具备确定总体布局的能力也十分重 要,这是因为与其他工业产品相比,汽车构造的复杂多
变性要大得多。
二、概念设计阶段
安放了大型的水平对向12缸引擎,使其后轮距远大于前轮
距,这就需要以特别的造型设计来配合。在操控性方面, 轮距越大,转向极限和稳定性也会提高,很多高性能跑车 车身叶子板都向外抛,就是为了尽量扩大轮距。
二、概念设计阶段
2.1.2 尺寸参数的确定
7、离地距
离地距即车体最低点与地面的距离。后驱车的离地最低点
产品规划 设计任务书
乘用车制动系统开发资料

Braking System Development
制动系统开发
2.1 制动系统开发理论计算-基础制动
Fbf u Ff
Fb u m g
h
Fbr u Fr
Fbf Fbr Fb
联立上式可以得出前后地面制动力与地面附着 系数的关系如下
A
B
m g B m a h m g A m a h Ff Fr ( A B) ( A B) ( A B) ( A B)
制动系统开发
4.制动系统零部件的开发
设计空间CAD 软件
优化设计前 处理-CAE 软件
优化设计-Hyper Works-Opstruct
模型重建CAD 软件
模型验证CAE 软件
Braking System Development
Braking System Development
制动系统开发
4.制动系统零部件的开发
在完成子系统零部件的布置之后,就要开始各零部件的结构设计了。零部件结构设计需要关注材料、工 艺、成本、强度、刚度、模态等等方面。 比如转向节的设计。 在完成了卡钳、制动盘、轴承、轮辋等零部件的布置后,
1)CAD 软件设计出最大轮廓的转向节优化空间;
Braking System Development
制动系统开发 3 前后制动钳的布置 B 轴向布置
制动盘中 心尽量靠 近轴承中 心
作用在制动盘上的切向力 轴承附加弯矩
轴承中心
摩擦力力臂
只有将制动盘中心与轴承中心重合,摩擦力力臂才能为0, 轴承才不会有附加弯矩。对轴承寿命有益
Braking System Development
制动系统开发
4. 助力器的选择 现已确定了助力比以及先前已确定的主缸行程,分析助力器的特性曲线,我们可以选择出合适的助力器
☆☆乘用车制动系统开发设计流程☆☆

联立上式可以得出前后地面制动力与地面附着 系数的关系如下
Fbf m(gB ugh) u ( A B) Fbr m(gA ugh) u ( A B)
对同一车辆来说,上两式中,只有u为变量, 取不同的u值便可得到不同Fbf和Fbr值。这便 是理想制动力分配曲线。
2. 基础制动与制动主缸的联络---轮缸压力与主缸推力
现已知了主缸直径、主缸行程;基础制动系统的压力-减速度曲线,可以推导出主缸推力与制动减 速度曲线。
减速度
轮缸压力 =
主缸压力
轮缸压力
轮缸压力
轮缸推力 =
主缸压力X 活塞面积
主缸压力
主缸压力 主缸活塞推力
踏板杠杆比
3. 制动主缸与人机控制联络 ---主缸行程与踏板行程
insight 均可做为优化工具。
下一张便是2010年所写的一个B21 四连杆 踏板机构优化论文
3.3 制动控制模块布置 目前的制动控制模块主要是ABS 或者ESP(ESC)模块,模块的布置位置并没有严格的要求。但应做到 1. 靠近主缸 2. 液面低于储液罐液面(包括连接主缸-模块的制动管最高点) 3.远离热源 4. 放置淋雨(插接件插接口要防止积水) 5. 尽量放置在纵梁等NVH性能较稳定的部件之上 6. 管路易于安装,本身易于拆装
车辆制动系统开发
汽研院底盘部:李成 2011年5月10日
1. 液压制动系统简介 2. 制动系统开发理论计算 3. 子系统的开发 4. 制动系统零部件的开发 5. 制动系统客观试验 6. 制动系统主观评价
1.液压制动系统简介
液压制动系统是将驾驶人员施加到制动踏板上的 力放大,并助力后反应到制动主缸,由制动主缸建立 起整个制动管路的压力,压力将推动执行机构(制动 器)限制车轮的转动而实现制动。
乘用车制动系统设计

兰州工业学院毕业设计(论文)题目:乘用车制动系统设计院系:汽车工程学院专业:汽车制造与装配技术班级:汽造11班姓名:张百宏学号:201109103145指导老师:李彦晶日期:2013年11月3日摘要汽车制动系是汽车底盘上的一个重要系统,它是制约汽车运动的装置。
其中制动器又是制动系中直接作用制约汽车运动的一个关健装置,是汽车上最重要的安全件。
汽车的制动性能直接影响汽车的行驶安全性。
本论文通过对乘用车制动系统进行细致的分析与了解,首先介绍了汽车制动系统的发展、结构、分类,并通过对鼓式制动器和盘式制动器的结构及优缺点进行分析。
最终确定方案采用液压双回路前盘后鼓式制动器。
除此之外,它还对前后制动器、制动主缸进行设计计算,主要部件的参数选择及制动管路布置形式等的设计过程。
关键字:制动系统;制动器;制动主缸ABSTRACTAutomobile brake system is automobile chassis to an important system, it is restricted by the car of the movement of the device. And the brake is brake system directly effect the automobile sport in a restricted key device, is the most important safety car parts. The automobile braking performance directly influence the car driving safety. First this paper reviewed the automobile braking system development, structure, classification, and through to the drum brake disc brake and the structure of the advantages and disadvantages and analyzed. Ultimately determine the scheme adopts hydraulic double circuit qianpan hougu type brake. In addition, it's still around to brake and brake main cylinder design, calculation of the main parts of parameter selection and brake pipe, the design process of decorate a form, etc.Key words: Braking; Brake drum; Brake disc; Braking cylinder目录摘要 (II)ABSTRACT (III)目录 (1)第一章绪论 (2)1.1汽车制动系的研究的目的和意义.............................................................. 错误!未定义书签。
制动系统设计流程
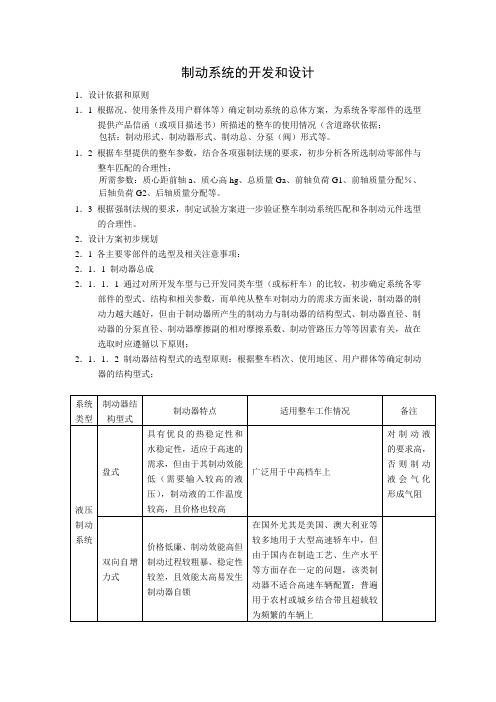
制动系统的开发和设计1.设计依据和原则1.1 根据况、使用条件及用户群体等)确定制动系统的总体方案,为系统各零部件的选型提供产品信函(或项目描述书)所描述的整车的使用情况(含道路状依据;包括:制动形式、制动器形式、制动总、分泵(阀)形式等。
1.2 根据车型提供的整车参数,结合各项强制法规的要求,初步分析各所选制动零部件与整车匹配的合理性;所需参数:质心距前轴a、质心高hg、总质量Ga、前轴负荷G1、前轴质量分配%、后轴负荷G2、后轴质量分配等。
1.3 根据强制法规的要求,制定试验方案进一步验证整车制动系统匹配和各制动元件选型的合理性。
2.设计方案初步规划2.1 各主要零部件的选型及相关注意事项:2.1.1 制动器总成2.1.1.1 通过对所开发车型与已开发同类车型(或标杆车)的比较,初步确定系统各零部件的型式、结构和相关参数,而单纯从整车对制动力的需求方面来说,制动器的制动力越大越好,但由于制动器所产生的制动力与制动器的结构型式、制动器直径、制动器的分泵直径、制动器摩擦副的相对摩擦系数、制动管路压力等等因素有关,故在选取时应遵循以下原则;2.1.1.2 制动器结构型式的选型原则:根据整车档次、使用地区、用户群体等确定制动器的结构型式;2.1.1.3 制动器直径的选型原则:由于制动器的直径与轮辋直径有关,在选型时应根据整车布置及轮辋的要求,考虑制动鼓的散热问题,一般制动鼓与轮辋的间隙应不小于10mm,否则会导致制动器散热不良,引起制动鼓早期龟裂、制动衬片烧结、炭化,大大降低制动器的制动效能;另外,制动器与轮辋的间隙太小,制动过程所产生的热量也将大量传导至轮辋上,对轮胎不利。
2.1.1.4 制动器衬片摩擦系数的确定:由于制动器衬片的摩擦系数是决定制动器制动力的主要原因之一,在同型、同规格的制动器中,制动衬片的摩擦系数越高,制动器所产生的制动力越大,但对于不同结构的制动器来说,并不是摩擦系数越高越好,摩擦系数太高对制动鼓(或盘)的磨损也越大,且对于双向自增力式制动器,摩擦系数越高,制动过程越粗暴,对制动底板、制动蹄铁、制动鼓的刚性要求越高,否则在制动过程中越易产生制动器颤动、整车发抖的现象,故对于摩擦系数的选取根据本人的经验建议:双向自增力式制动器的取0.38左右,其它结构型式的制动器取0.45~0.5左右,盘式制动器取0.35左右。
乘用车开发流程

乘用车开发开发流程•概念设计服务项目市场定位分析* L4 Z/ G! i" 、初期总布置设计整车动力性、经济性分析和计算7…造型设计指导书参考样车分析供应商平台调查…成本分析…编制产品描述书1. 市场定位…从消费者调查、市场调研、竞争对手分析及企业制造能力分析来确定产品的市场定位。
初期总布置% O. U2 X4 ~9 2……根据客户需求,选定各分总成,初步确定整车基本参数,在此基础上完成人体布置和各类运动分析,视野分析,手触及空间分析和仪表可视性分析等。
该过程借助三维设计软件模拟完成,分析出现的问题反馈到模型中进行调整,这样经过多次调整,使所设计的汽车满足现代汽车高水平的驾驶操作性、乘坐舒适性和居住性等要求。
3整车动力性、经济性分析和计算进行整车初步动力性和经济性计算,分析整车性能满足产品定量目标的程度并进行必要的调整。
4确定造型设计方向- }0 m# A4 s5 l) Y z% D3 确定初步外部尺寸、整车技术参数、造型风格和内部配置。
…5参考样车分析品8 X3 r& & k; " R3 8 对参考样车进行分析研究,确定其优势和不足,结合市场情况提出所开发产的目标定位。
6供应商平台调查9 s- T$ ]-J6 对潜在的供应商进行货源可行性评估,评价他们在满足质量、供货能力及开发水平的前提下提供总成和部件的能力。
识别价格及质量具有相对竞争力的供应商,以满足产品定位的要求。
将所有涉及该过程的开发伙伴协调在一起,整合资源满足用户最大需求。
在供应商和制造者之间建立信息沟通,提升整个汽车生产链运作的效率,并增进更高层面上的技术创新。
7成本分析确定各系统和整车的目标成本。
编制产品描述书描述书作为产品开发的依据文件,将所要开发的产品项目的背…+Q8景、目标、车型规划、总成选择、装备、进度等进行详细描述。
…g&?•汽车造型分析造型设计任务书, y) o: t. A' 12收集和整理相关资料并进行样车准备3工程与造型的契合确定设计理念,提出设计方案& E1 X3 U) F0 P4 L+k45阶段评审6初步草图设计方向性评审. D/ {, G+ Q9 o2 i78细化效果图草图设计9设计评审效果图设计9 F5 M# t" A* z! W10效果图评审, B3 {- @2 b1 S" 1112 效果图修改及提交13根据客户的意见修改效果图14效果图批准进入零部件造型的细节设计阶段8 F+ F# v) L615•三维造型…三维造型室以评审通过的效果图为依据构建及渲染三维数字模型。
车辆制动系统方案毕业设计

车辆制动系统方案毕业设计一、引言随着汽车行业的发展,车辆安全问题越来越受到人们的关注。
而车辆制动系统作为车辆最重要的安全保障之一,其性能的稳定和可靠直接影响车辆行驶的安全。
因此,本文将研究一种车辆制动系统方案,对其进行系统设计,并在实际驾驶过程中进行测试验证,以达到优化车辆制动系统性能的目的。
二、方案设计本方案设计的车辆制动系统分为三个部分:制动控制部分、制动执行部分以及传感反馈部分。
1. 制动控制部分制动控制部分采用可编程控制器(PLC)作为控制核心,通过传感器采集车速、制动踏板行程等参数,来实时控制制动器的工作,进而控制车辆的制动。
2. 制动执行部分制动执行部分采用气动式制动器,将制动控制部分发送的控制信号转换为气源控制信号,通过阀门的控制实现制动器的工作,进而实现车辆的制动。
3. 传感反馈部分传感反馈部分主要由传感器组成,包括制动踏板行程传感器、制动器传感器等,通过采集数据并传输给制动控制部分进行处理,从而实现对制动系统的实时监测和反馈。
三、实验结果分析1. 实验方法在本次实验中,我们通过实验台模拟车辆行驶状态,对所设计的车辆制动系统进行测试。
在测试过程中,我们对比了原有制动系统和新设计的制动系统的刹车距离、制动灵敏度等指标差异,并通过数据对比来对所设计的方案进行分析。
2. 实验结果在测试中,我们发现采用所设计的车辆制动系统后,车辆的刹车距离、制动灵敏度等指标得到了显著的提升。
在同样的行驶路线下,新设计的制动系统刹车距离相比原有制动系统减少了近30%,同时制动灵敏度得到了明显的提高。
四、结论本文根据车辆制动系统的需求,设计了一种新的车辆制动系统方案,并在实验中对其进行了有效性验证。
通过测试数据分析,我们发现所设计的车辆制动系统在刹车距离、制动灵敏度等指标上得到了显著的提升,同时也保证了车辆的安全性和可靠性,可为未来的车辆制动系统的研究和应用提供一定的参考价值。
中型客车制动系统设计开发思路及方法

Desgn r s ar h i e e c
窒
中型客 车制动 系统设计 开发 思路及方法
白红 波
( 陕西德 仕汽 车部 件< 团> 限责 任 公司 陕 西 集 有 西安 70 0 ) 12 0
摘
要 :随着 高速 公 路 的迅速 发展 和车 速 的提 高 以及 车流 密度 的 日益增 大 ,为 了保 证行 车 安全 ,汽 车制
《 B 16 6 1 9 G 2 7- 9 9汽 车制 动系 统结 构 、性能 和试验 方
种 变 形车 。这些 车在 重 心位 置 、轴距 、载荷 分 配做 了变 目前 国 内在制 定 系 统 方面 ,有两 个 强 制性 标 准 , 一是
成 了许 多 故 障 。本 文 是 基 于此 背 景 下提 出 , 以一款 7 法 》 ( 以下简称 GB 166 ,在 汽车 制动 系统 结构 、性 2 7 )
动 系 的工 作可靠 性 显得 日益 重要 。也只 有制 动性 能 良好 、制 动 系工作 可靠 的汽 车 ,才 能充 分发 挥其 动力
性 能 。这里 主要 叙述 中型客 车制动 系 统 的设计 开发 思路 、主 要制 动参数 的确 认及 校核 、协 调方 法 、试 验 的重要 性 。
关键 词 :整 车sg de sa e ho f e um a y t m e i n i a nd m t dso di M busbr kes se
g o brkig e f r a c a r l bl o r to o he r k n s t m ,a gve u l ly o t d n m i od a n p ro m n e nd ei e pea in f t b a i g yse c n i f l a p a t i s ya c p ro m a e e f r nc .Th s ri l a ny d s rb s he e i n i e s h o i ain n c e k o e m an b a ig i atce m i l e c ie t d sg d a ,t e c nf m r t a d h c f t i r n o h k
汽车制动系统的设计及仿真

汽车制动系统的设计及仿真任务书1.设计的主要任务及目标汽车制动器是制动系中最重要的一个部件,是制动系统中用以产生阻碍汽车运动或运动趋势的力的部件。
凡是利用固定元件与旋转元件工作表面的摩擦而产生制动力矩的制动器都成为摩擦制动器。
摩擦制动器可分为鼓式和盘式两大类。
前者的摩擦副中的旋转元件为制动鼓,其工作表面为圆柱面;后者的旋转元件则为圆盘状的制动盘,以端面为工作表面。
2.设计的基本要求和内容(1)了解汽车制动系统的工作过程。
(2)熟悉汽车制动系统的设计过程和设计参数。
(3)结合汽车制动性能要求设计汽车制动器。
(4)结合三维建模软件,并实现制动器的运动仿真。
3.主要参考文献[1] 王望予.汽车设计[M].北京:机械工业出版社,2004[2] 余志生.汽车理论[M].北京:机械工业出版社,2003[3] 陈家瑞.汽车构造[M].北京:机械工业出版社,2003[4] 林秉华.最新汽车设计实用手册[M],黑龙江:黑龙江出版社,2005[5] 张尉林.汽车制动系统的分析与设计[M].北京:机械工业出社,20024.进度安排注:一式4份,系部、指导教师各1份、学生2份:[毕业设计]及答辩评分表各一份汽车制动系统的设计及仿真摘要:汽车的制动系是汽车行车安全的保证,许多制动法规对制动系提出了许多详细而具体的要求,这是我们设计的出发点。
从制动器的功用及设计的要求出发,依据给定的设计参数,进行了方案论证。
对各种形式的制动器的优缺点进行了比较后,选择了浮动钳盘的形式。
这样,制动系有较高的制动效能和较高的效能因素稳定性。
随后,对盘式制动器的具体结构的设计过程进行了详尽的阐述。
选择了简单液压驱动机构和双管路系统,选用了间隙自动调节装置。
在设计计算部分,选择了几个结构参数,计算了制动系的主要参数,盘式制动器相关零件的设计计算。
关键词: 制动器,同步附着系数,制动盘,制动钳Automobile brake system design and simulationAbstracts:The braking system in a vehicle guaranteed the safety of driving .Many rules and regulations have been made for the braking system in detail, which is the starting of our design.Firstly, I demonstrate the project on the base of the function of the brake, And analysis their strong point and shortcomings .I choose the form of front-disked. In this way, the braking system have higher braking efficiency and high stability of the performance factors. Subsequently, the specific structure of the disc brake design was elaborated in detail.I designed the hydraulic drive system and two-pipe system and selected clearance automatic adjusting device.In the calculate part .I chosen several structural parameters, calculated the main parameters of the braking system drive mechanism.Key words:disc brakes,synchronous attachment coefficient,brake disc,brake caliper目录1 绪论 (1)1.1 课题研究的目的及意义 (1)1.2制动系统研究现状 (1)1.3课题设计思路 (3)2制动系统概述 (4)2.1制动系的类型 (4)2.2汽车制动系统组成 (4)2.3 制动器的组成 (5)2.4 制动器的要求 (5)2.5 制动器的种类 (7)3 汽车参数计算 (14)3.1汽车的基本参数 (14)3.2 制动系的主要参数及其选择 (15)3.3 盘式制动器的结构参数与摩擦系数的确定 (16)3.4 制动衬块的设计计算 (18)3.5 摩擦衬块磨损特性的计算 (19)4 制动器主要零件的结构设计 (21)4.2 制动钳 (21)4.4 摩擦材料 (21)4.5 盘式制动器间隙的调整方法及相应机构 (22)4.6 制动驱动机构的结构型式选择与设计计算 (22)结论 (25)参考文献 (26)致谢 (27)附录 (28)1 绪论1.1 课题研究的目的及意义汽车的设计与生产涉及到许多领域,其独有的安全性、经济性、舒适性等众多指标,也对设计提出了更高的要求。
汽车制动系统设计开发流程教材(PDF 44页)
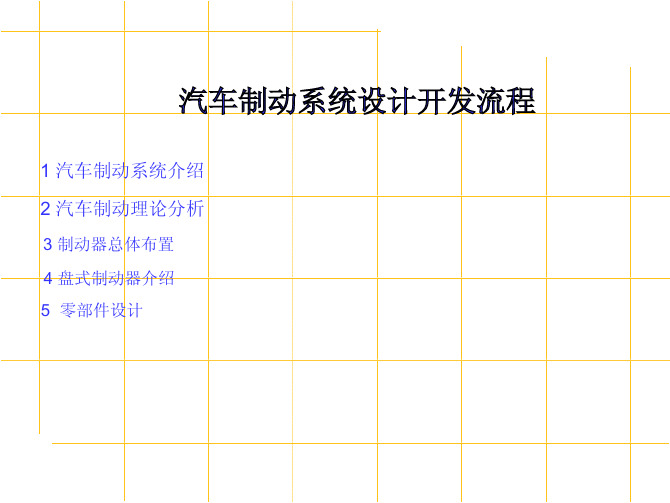
Fbf m(gB ugh) u ( A B)
Fbr m(gA ugh)u (A B)
对同一车辆来说,上两式中,只有u为变量,取不同的u值便可得 到不同Fbf和Fbr值。这便是理想制动力分配曲线,如下页
F 线组是前轮抱死时前后轮地面制动 力的变化关系
h
A
B
Ff mg B ma h (A B) (A B)
Fr mg A ma h (A B) (A B)
a Fb m
假设制动时车轮完全抱死,整车制动力就等于地面附着力
Fbf u Ff Fbr u Fr
u 为地面提供的附着系数
Fb u mg Fbf Fbr Fb
分析可发现,将制动钳后置在制动时施加在轴承上的径 向载荷远小于制动钳前置的情况。
为了减小簧下质量,在赛车上将制动钳与制动盘移至传动轴 内球笼一侧,从而由簧下质量变为簧载质量。这样的好处多方面 的。可以用小的减振器,刚度小的弹簧…
制动盘的布置位置
理想情况是轮胎中线线及制动盘中心还有轴承中心在 y方向重合,这样在制动时在轴承及轮毂上就不会产 生附加的弯矩。
后轮地面制动 力增量(负值)
后轮制动器制 动力增量
前轮制动器制 动力亦地面制
动力增量
R线组
实际制动力分配曲线
关于制动系统理 论,如果在此分析将 占用很大的篇幅,今 后将在制动系统设计 指南中详细分析,在 此就不赘述了!
理想制动力分配曲线
F线组
在附着系数等于0.5的路面上制动,随着制动器 制动力的增加,地面制动力随之上升,当达到实际制 动力与理想制动力的焦点时,前后制动器同时抱死。 此后制动器制动力再增加已无意义。
汽车制动系统设计开发流程
乘用车制动设计及仿真

乘用车制动设计及仿真一、引言制动系统是汽车安全的核心组成部分之一。
乘用车制动系统不仅要满足对车辆的制动需求,同时要保证乘客和行人的安全。
本文将介绍乘用车制动设计的基本原理,并通过仿真分析验证制动系统的性能。
二、乘用车制动设计原理乘用车制动设计的目标是实现快速而稳定的制动效果。
制动系统的设计包括制动器、液压系统和控制系统三个方面。
2.1 制动器乘用车主要采用盘式制动器,包括刹车片、刹车盘和刹车钳。
制动器的设计应考虑以下几个因素:•刹车片材料:刹车片材料应具有良好的摩擦性能和耐磨性能,同时要考虑制动过程中的热膨胀和热衰减。
•刹车盘材料:刹车盘材料应具有良好的导热性能和耐热性能,以便快速散热,防止制动衰减。
•刹车钳设计:刹车钳应能够确保刹车片与刹车盘之间的紧密接触,避免制动时的失效。
•刹车片与刹车盘的接触面积:接触面积越大,制动效果越好,但也会增加制动器的负荷和成本。
2.2 液压系统液压制动系统通过液压力将制动力传递给刹车片和刹车盘。
液压系统的设计应考虑以下几个因素:•制动液的选择:制动液应具有高沸点和低压缩性,以保证制动时的稳定性和可靠性。
•主缸设计:主缸应能够通过踏板的力量产生足够的液压力,以便实现快速制动。
•助力器设计:助力器可以增加制动力,并减小制动力所需的踏板力量。
•刹车管路设计:刹车管路应保证液压力的传递和分配的稳定性,避免制动衰减。
2.3 控制系统控制系统主要包括制动控制单元(ECU)和制动系统的传感器。
制动控制单元接收传感器的信号,并根据车辆的速度、制动力和转向角等信息,控制制动系统的工作。
三、乘用车制动仿真制动仿真是评估和优化制动系统性能的重要方法。
通过仿真分析,可以预测制动系统的工作状态、制动力的分布和制动距离等参数,并优化设计方案。
制动仿真可以分为双端和单端仿真。
双端仿真是指通过在车辆和制动器之间建立模型,模拟制动系统的工作过程。
单端仿真是指通过在制动器上建立模型,模拟刹车片和刹车盘之间的接触状态和摩擦力。
汽车开发设计作业流程及各阶段工作内容
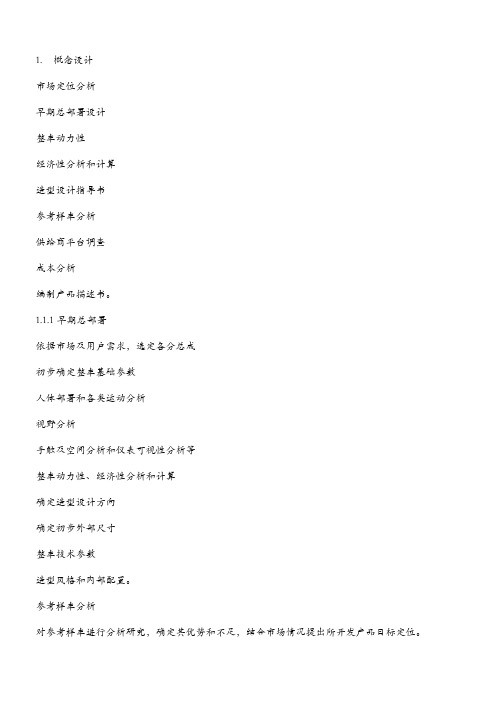
1.概念设计市场定位分析早期总部署设计整车动力性经济性分析和计算造型设计指导书参考样车分析供给商平台调查成本分析编制产品描述书。
1.1.1早期总部署依据市场及用户需求,选定各分总成初步确定整车基础参数人体部署和各类运动分析视野分析手触及空间分析和仪表可视性分析等整车动力性、经济性分析和计算确定造型设计方向确定初步外部尺寸整车技术参数造型风格和内部配置。
参考样车分析对参考样车进行分析研究,确定其优势和不足,结合市场情况提出所开发产品目标定位。
供给商平台调查对潜在供给商进行货源可行性评定评价她们在满足质量、供货能力及开发水平前提下提供总成和部件能力识别价格及质量含有相对竞争力供给商,以满足产品定位要求。
在供给商和制造者之间建立信息沟通成本分析确定各系统和整车目标成本。
编制产品描述书描述书作为产品开发依据文件,将所要开发产品项目标背景、目标、车型计划、总成选择、装备、进度等进行具体描述。
1.2团体一支有着丰富汽车理论知识和设计经验优异团体,熟知中国汽车配套资源及现有车型。
以敏锐眼光洞察中国汽车市场,能很好把握中国汽车发展时尚。
1.3市场定位从消费者调查、市场调研、竞争对手分析及,企业制造能力分析来确定产品市场定位。
2.汽车造型分析造型设计任务书搜集和整理相关资料并进行样车准备工程和造型契合确定设计理念,提出设计方案阶段评审初步草图设计方向性评审细化效果图草图设计设计评审效果图设计效果图评审效果图修改及提交依据用户意见修改效果图效果图同意进入零部件造型细节设计阶段团体要求:含有锐意创新精神,透过设计表面来了解设计本身所代表设计师对生活形态和消费心理了解,给予设计更多实际意义。
高雅艺术品味、丰富设计经验、全方面汽车相关专业知识和衍生材料学、流体力学、热能学、人体工程学、社会学、环境保护学等众多方面知识。
对消费者及成本了解和极富魅力创意思维使她们不停推陈出新,发明出更符合国际趋势和品牌定位作品。
设计部门负担整车造型、总体部署及整车集成,内容涵盖了从美学表面质感、动感、内外饰创意、计算机辅助曲面设计到产品外型最终数据公布。
汽车制动系统设计程序的开发
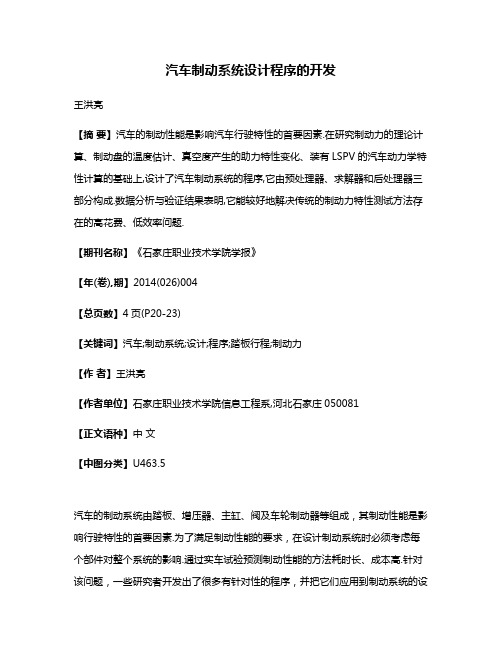
汽车制动系统设计程序的开发王洪亮【摘要】汽车的制动性能是影响汽车行驶特性的首要因素.在研究制动力的理论计算、制动盘的温度估计、真空度产生的助力特性变化、装有LSPV的汽车动力学特性计算的基础上,设计了汽车制动系统的程序,它由预处理器、求解器和后处理器三部分构成.数据分析与验证结果表明,它能较好地解决传统的制动力特性测试方法存在的高花费、低效率问题.【期刊名称】《石家庄职业技术学院学报》【年(卷),期】2014(026)004【总页数】4页(P20-23)【关键词】汽车;制动系统;设计;程序;踏板行程;制动力【作者】王洪亮【作者单位】石家庄职业技术学院信息工程系,河北石家庄050081【正文语种】中文【中图分类】U463.5汽车的制动系统由踏板、增压器、主缸、阀及车轮制动器等组成,其制动性能是影响行驶特性的首要因素.为了满足制动性能的要求,在设计制动系统时必须考虑每个部件对整个系统的影响.通过实车试验预测制动性能的方法耗时长、成本高.针对该问题,一些研究者开发出了很多有针对性的程序,并把它们应用到制动系统的设计中.如,文献[1]设计了一种计算制动力分配的理论与试验方法;文献[2]开发了多个ABS系统(防抱死系统),以确保转向安全;文献[3]利用轮胎有限元法研究了汽车的制动距离;文献[4]利用轮胎动力学模型,估计了制动力与路面摩擦系数的关系;文献[5]开发出了一种计算半挂汽车列车制动性能的程序;文献[6]研究了踏板力作用在制动装备上的效果;文献[7]根据减速度和踏板力的变化来预测车辆的制动性能.而大多数基于程序设计的验证方法并没有考虑汽车制动过程中产生的制动盘温度上升以及助力器压力的变化,因而,程序模拟的结果与实际试验得到的结果有较大的出入.本文针对通过试验来确定汽车制动力特性存在的计算成本高、周期长等问题,提出一种能对汽车制动压力、制动效率以及踏板行程等进行定性分析的程序设计方法.1 理论计算1.1 制动力的计算在汽车制动过程中,相对于汽车静止时,汽车前桥的载荷增加,后桥的载荷减少.汽车减速时的动态载荷分配情况如图1所示.图1 轴的动载荷分配图具体载荷满足下式:其中,W 表示整车的重力,WDF表示前轮承受的重力,WDR表示后轮承受的重力,h表示重心的高度,lR和lF分别为重心到前后轴的距离,l为轴距,g为重力加速度,α为车辆加速度.考虑轴载荷后的理想制动力为:其中,BF和BR为前后轮的制动力.道路最大理想制动力为:其中,LPIR和LPIF分别为前后轮的总制动力,TPF和TPR分别为前后轮的制动力矩,CR和CF为比例系数.实际制动压力就是由施加到轮缸上的压力得到的车轮制动力.轮缸阀的特性决定制动力的大小.由于汽车在制动过程中载荷向前转移,因而前轮制动力大于后轮制动力.图2给出了比例阀的工作特性.文件均为MS-EXCEL格式,输出数据也以MS-EXCEL格式保存.图2 比例阀管路压力特征曲线2.2 求解器该程序利用预处理器的输入数据计算出汽车的制动性能,根据减速度和踏板力进行分析.计算加速度主要考虑汽车的载荷分配、制动力、制动压力、制动距离等因素.该程序中,加速度的变化范围为0g~1.2g(1g的加速度相当于承受一倍于自身体重的负荷),步长为0.01g.根据减速度获得实际制动力的流程如图3所示.踏板力与减速度、管路压力和踏板行程有关.计算流程如图4所示.代表初始速度,ρ为制动盘密度,V 为制动盘体积,c为盘的比热,Q为总摩擦热,g为重力加速度. 1.3 真空度产生的助力特性变化作用在制动踏板上的制动力通过助力器变大.考虑到制动踏板力的损失情况、踏板传动比及传动效率,助力器的输入作用力为:Finp=(FPedal-F0)γPηP,其中,Fpedal为踏板力,F0 为制动损失力,γp为传动比,ηp为传动效率.1.4 装有LSPV的汽车动力学特性计算感载比例阀(LSPV)控制汽车传递到车轮的制动压力,该制动压力由后桥载荷的变化量确定.装有p阀的汽车实际制动力保持不变且与汽车的质量无关;而装有LSPV的汽车随着汽车质量的变化调整实际制动力.2 制动系统程序开发由三部分构成:第一部分为预处理器,在得到汽车及零部件输入设计参数之前,将数据输入到程序并计算制动盘和助力器特性;第二部分为求解器,用来分析所有数据;第三部分为后处理器,用于输出图形、对话框及文本文件等数据.2.1 预处理器输入数据包括前/后/驻车制动数据、助力器数据、主缸数据、阀的数据及所需流体数据.所有输入1.2 制动盘的温度估计汽车制动过程中,机械能转换为热能,其中有部分热能增加了制动盘的温度.盘的温度上升影响盘的摩擦系数,并改变汽车的制动性能.温度上升方程图3 由输入减速度计算制动压力与管路压力的流程图图4 由输入踏板力计算减速度的流程图2.3 后处理器使用后处理器,可以将输出文件以MS-EXCEL格式自动打印出来.3 数据分析及验证根据制动踏板力绘制出减速度曲线、管路压力分配曲线及踏板行程曲线,如图5所示,它同时显示了踏板力、助力器输入/输出力以及管路压力之间的关系.可以重叠绘制多条曲线并改变坐标轴设置.每根坐标轴会根据每条曲线的最大值自动调整.所有数据可以以文本文件形式查看,通过在对话框输入数值来验证乘用车和商用车的制动性能.部分输出图形如图6所示.图5 四轴图图6 输出结果图当汽车分别处于满载及轻载时,力分配和压力分配曲线分别代表理想与实际制动力曲线.当踏板力从10N变化到700N时,通过管路压力显示制动压力.同制动压力曲线一样,当助力器工作、停止以及汽车满载、轻载时,管路压力的变化也可以通过曲线表示.所有的数据都可以定量验证,且容易分析,图形与输入数据能够实时更新,可以方便地设计有效的制动系统.表1给出了一些由本设计程序计算得到的估计值与实车测试值.他们之间误差产生的一个主要原因是发动机进气管不能自动反馈真空助力压力的变化.本程序没有考虑外界流入真空助力器以及由真空助力器流到发动机进气管的空气压力.表1所示误差受发动机转速与汽车车速的影响.由表1可知,估计值与实测值的最大误差为6.6%,因此所开发的程序可以较合理地预测汽车的制动性能.表1 估计值与试验值对比制动特性加速度/(m/s2)踏板力/N 常规估计测试误差/%普通行程制动力 6 3<12N<60N 96N 52N 97N 54N 1.0 3.8踏板行程 6 3<62mm<43mm 48.0mm 36.7mm 51mm 37mm 6.3 0.8最大行程 200 500<75mm<95mm 75.2mm 88.6mm 70.2mm 87.1mm 6.6 1.74 结论本文开发了一种评价汽车制动系统性能的程序,建立了制动性能设计数据库.该程序能方便地确定制动性能的影响因素,如制动力、制动压力、制动效率及LSPV动态特性.制动系统部件的设计数据和制动特性采用 MS-EXCEL文件管理,制动系统的每个组件都可以插入或独立于整个系统中.参考文献:[1]LIMPERT R.制动器的设计与安全[M].华盛顿:美国机动车工程师协会,1999:293-350.[2]GATT M E.美国联邦机动车安全标准[M].华盛顿:美国国家公路交通安全管理局,2005:75-105.[3]CHOI J,JEON D,CHO J,et al.轮胎制动性能估计使用有限元方法[M].首尔:韩国汽车工程师学会,2004:1523-1528.[4]HONG D,HUH.估计轮胎的制动力和道路轮胎与路面之间摩擦系数来控制车轮的滑移面[M].首尔:韩国机械工程师学会,2004:517-523.[5]SUH M,KWON S,PARK Y.半挂汽车列车制动系统设计程序的开发[M].首尔:韩国汽车工程师学会,2001:108-120.[6]KIM H,LIM Y.对汽车制动踏板力特性的研究[M].首尔:韩国汽车工程师学会,2002:241-258.[7]JUNG I,LEE S.开发的汽车制动性能分析程序动态特性的考虑[M].首尔:韩国汽车工程师学会,2004:175-181.。
汽车制动系统的设计与制造

汽车制动系统的设计与制造第一章:引言在现代社会,汽车被广泛应用于人们的日常生活和工作之中,它们承载着人们的出行和运输任务。
汽车制动系统是汽车的重要组成部分之一,其作用是保证汽车在运行过程中能够承受起停车和制动的力量,确保人们的出行安全。
本文通过对汽车制动系统的设计和制造的研究,探讨了制动系统的重要性,对其制造和设计提出了一些建议和改进,旨在为汽车制造业的可持续发展做出积极贡献。
第二章:汽车制动系统的原理汽车制动系统的主要原理是将动能转化为热能。
当车辆运动时,它会获得动能,制动系统通过制动力来消耗这些动能,转化为热能散发出去,从而使车辆停下来。
制动系统的关键是能够在短时间内产生强大的制动力,并且对其施加的力要足够均匀和稳定,以保证车辆在制动过程中的稳定性和安全性。
第三章:汽车制动系统的设计汽车制动系统的设计应当从以下几个方面考虑:1. 制动力的大小和稳定性。
制动力的大小应根据车辆的重量和车速等因素确定,同时制动力的稳定性关系到车辆是否能够稳定停车,因此需要在设计过程中进行精细的计算和检测。
2. 制动器的类型和材质。
制动器的类型包括盘式制动器和鼓式制动器,而制动器材质的选择需要考虑到材质的耐磨性和耐高温性等性能。
3. 制动油的选用。
制动油需要具备高沸点和不易吸湿等性能,以保证制动系统的效果和使用寿命。
4. 制动系统的辅助装置。
制动系统的辅助装置包括制动盘、制动鼓、制动器等部件,这些部件的选用和安装需要保证制动力的稳定和均匀,同时需要对其进行定期检测和维护。
第四章:汽车制动系统的制造汽车制动系统的制造需要考虑到以下因素:1. 生产工艺。
汽车制动系统的生产需要考虑到各个部件之间的配合和协作,以保证制动系统的性能和质量。
2. 材料选择。
制动系统涉及到的材料种类繁多,包括金属、橡胶、塑料等材料,而材料的选用需要考虑到其强度和耐磨性等因素,以保证制动系统的效果和寿命。
3. 制造流程的优化。
制造过程中需要对制造流程进行优化和改进,以提高生产效率,同时降低生产成本和产品中的缺陷率。
- 1、下载文档前请自行甄别文档内容的完整性,平台不提供额外的编辑、内容补充、找答案等附加服务。
- 2、"仅部分预览"的文档,不可在线预览部分如存在完整性等问题,可反馈申请退款(可完整预览的文档不适用该条件!)。
- 3、如文档侵犯您的权益,请联系客服反馈,我们会尽快为您处理(人工客服工作时间:9:00-18:30)。
汽研院底盘部:李成 2011年5月10日
Braking System Development
AERI Chassis Department
1. 液压制动系统简介
2. 制动系统开发理论计算 3. 子系统的开发 4. 制动系统零部件的开发 5. 制动系统客观试验 6. 制动系统主观评价
前轮制动器制 动力亦地面制 动力增量
Braking System Development
AERI Chassis Department
基础制动匹配完成之后我们可以锁定如下参数 1. 前后制动钳缸径(系列化卡钳中选定) 有了前后制动钳缸径,可进一步活的卡钳所需液量曲线(一般由供应 商试验得出)
2. 前后制动有效半径 有效半径是制动盘设计的重要参数之一
实际制动力分配曲线(制动器制动力)
Fbf
4 ( p pt f ) Af u f Re f R
4 ( p pt r ) Ar ur Re r Fbr R
Fbf :前轮制动器制动力 Fbr : 后轮制动器制动力 p: 制动管路压力,抱死压力控制在12Mpa以下,
Braking System Development
AERI Chassis Department
4. 助力器的选择 现已确定了助力比以及先前已确定的主缸行程,分析助力器的特性曲线,我们可以选择出合适的助力器
最大帮助力,取决于助 力器尺寸
助 力 器 输 出 力
对于同一个助力器,助力比和助力 行程是相互矛盾的,大助力比意味着短 的主力行程, 所以一般的原则是先确定助力比, 再通过行程来决定助力器尺寸(不同助 力器可以有相同的助力比,但最大帮助 力不同)。
置 或者顶置)
Braking System Development
AERI Chassis Department
正压力Fz
正压力Fz与地面制动 力Fx的合力
只有将卡钳布置在4:30位置时 摩擦块对制 动盘的作用力与合力方向共线反向,合力 最小,轴承载荷最小
地面制动力Fx=FzXu
Fb平移到轮心处
摩擦块对制动盘的摩 擦力Fb=Fx X Re/Rr
助力比,取决于反馈盘 面积比
至此 系统性的匹配工作基本结束。
助力器推杆行程
A B
C
D
Braking System Development
AERI Chassis Department
系统匹配工作结束 确定的参数 1.前后卡钳缸径 2.前后摩擦系数 3.前后有效半径 4. 制动主缸直径 5. 踏板机构杠杆比 6.助力器助力比 7 .助力 器尺寸。 带着这些参数接下来该选取合适的零部件或者重新开发零部件,进入子系统布置阶段。
在 A、 u、 Re、 确定初始值之后,取液压P(0-12Mpa)计算出对应的前后轮制动器制动力 ,并叠加到理想制动力曲线图中。
Braking System Development
AERI Chassis Department
Ff
A . 要保证12Mpa时的制动器制动 力大于至少1.0的地面附着力,如 果不满足,可同时增大1.前后轮缸 2.摩擦系数 3. 有效半径(优先排 序)
Braking System Development
AERI Chassis Department
3 前后制动钳的布置 B 轴向布置
制动盘中 心尽量靠 近轴承中 心
作用在制动盘上的切向力 轴承附加弯矩
轴承中心
摩擦力力臂
只有将制动盘中心与轴承中心重合,摩擦力力臂才能为0, 轴承才不会有附加弯矩。对轴承寿命有益
Ptf\Ptr : 前后卡钳启动压力(选定初始卡钳之后,此参数可询问供应商或假设一个初始值(0.5bar左右)
Af\Ar : 前后卡钳活塞面积(卡钳为系列化产品,只需参考Benchmark 及轮辋的尺寸来选定一个初始尺寸( 51、54、57…..) Uf\Ur : 前后卡钳摩擦块摩擦系数(0.32-0.4) Ref\Rer: 前后卡钳制动有效半径(根据轮辋及卡钳尺寸,并参考Benchmark,并考虑三化原则设定或选定一 个初始值) R : 车轮滚动半径,一般乘用车前后轮滚动半径都相同。
Braking System Development
AERI Chassis Department
1.液压制动系统简介
液压制动系统是将驾驶人员施加到制动踏板上的 力放大,并助力后反应到制动主缸,由制动主缸建立 起整个制动管路的压力,压力将推动执行机构(制动 器)限制车轮的转动而实现制动。
Braking System Development
1. 基础制动与制动主缸的联络----卡钳与主缸 现已知卡钳缸径(或需液量)可选出主缸直径(因为主缸为直径-行程系列化产品,行程一般为18+18)
Braking System Development
AERI Chassis Department
2. 基础制动与制动主缸的联络---轮缸压力与主缸推力 现已知了主缸直径、主缸行程;基础制动系统的压力-减速度曲线,可以推导出主缸推力与制动减 速度曲线。
满载理想制动力分配曲线
U=1.0
满载同步附着系数
空载同步附着系数
B . 在满足A 的前提下,不断的调节前 后1.轮缸直径,2有效半径,3摩擦系数( 尽量取中值)来调节实际曲线斜率,终 极目标是让空载同步附着系数落在( 0.4-0.6)满载落在(0.7-0.9) 可分别取 中值0.5 0.8 为什么? Ff
实际制动力分配曲线 R线组
理想制动力分配曲线
F线组
前轮地面制 动力增量
前轮制动器 制动力增量
后轮制动器制动 力亦地面制动力 增量
Braking System Development
AERI Chassis Department
典Hale Waihona Puke 工况分析-高附着路面后轮制动器制 动力增量
实际制动力分配曲线 R线组
a Fb m
Fbf m( gB ugh) u ( A B)
Fbr m( gA ugh) u ( A B)
假设制动时车轮完全抱死,整车制动力就等于地 面附着力
对同一车辆来说,上两式中,只有u为变量, 取不同的u值便可得到不同Fbf和Fbr值。这便 是理想制动力分配曲线。
Braking System Development
AERI Chassis Department
顺带提及轴承轴向布置
车轮中心 轴承中心
垂向力弯矩
侧向力弯矩
Rdyn
+ A
F
+
FR
- A
Rdy
n
F
+
FR
Fy Fz
当轴承中心位于车轮中心内侧(轴承负偏距)转向时的侧 向力及正压力所产生的弯矩可以相互抵消一部分,对轴承 有益。一般取偏距量5-10mm 不可过大,否侧转向时内侧 车轮工况恶化。
减速度
轮缸压力
主缸压力
轮缸压力 = 主缸压力
轮缸推力 = 主缸压力X 活塞面积 主缸压力
主缸活塞推力
轮缸压力
3. 制动主缸与人机控制联络 ---主缸行程与踏板行程 目前已知了活塞总行程+ 主缸空行程+助力器空行 程=助力器推杆行程 基于人机工程的要求, 制动踏板的行程有要求 (<=130mm)
A 助力器推杆所需行程
这样的同步附着系数在空载时后轮岂不是很容易抱死?ABS 工作岂不是很频繁?
回答:确实如此,但有两点需要明确,1 不能为了空载的舒适性而牺牲满载的安全性;2 一般 乘用车(尤其前驱的车辆)空载时前轴载荷远大于后轴载荷,此时后轮的抱死压力很低,就是 说空载时及时ABS 对后轮起作用,它的工作负荷也很轻。对它的寿命影响不大。
Braking System Development
AERI Chassis Department
Fbf m( gB ugh) u ( A B)
u(0 1.0)
Fbr m( gA ugh) u ( A B)
Fr
满载理想制动力分配曲线
最理想状况,空满载理想制动力 曲线完全重合。这样空满载同步附 着系数都可以取到最常用附着系数 点,要做到空满载重合,这里需要 做到 1.空满载前后轴荷比例相同(即质 心在整车X 方向位置不变) 2.空满载车辆质心高度相同。
B 制动踏板要求的行程
踏 板 杠 杆 比
Braking System Development
AERI Chassis Department
踏板机构杠杆比的计算要点。
4. 制动主缸与人机控制联络--帮助力 在确定踏板杠杆比之后,踏板的 输出力也已知。
A 踏板输出力
B 主缸所需的推力
帮 助 力 ( 助 力 比 )
空满载理想制动力分配曲 线差异
有乘用车车能做到这两点吗?No
但还是要尽力去做到两条线接近。 方程式赛车勉强可以,且方程式 赛车使用在单一附着系数路面工作 ,所以方程式赛车不必匹配ABS 系 统。
空载理想制动力分配曲线
Ff
Braking System Development
AERI Chassis Department
3. 前后摩擦块名义摩擦系数 摩擦块开发重要参数
减速度
4. 管路压力与制动力或制动减速度关系曲线
压力
Braking System Development
AERI Chassis Department
2.2制动系统开发理论计算-人机工程
原则:车有异,人相同 世面车型千差万别,但对于同一区域的驾驶者却无不同,所以对踏板力,踏板行程这一要求,不同 车辆应有相同的要求。
Braking System Development