冷轧管变形原理
冷轧钢管变形原理
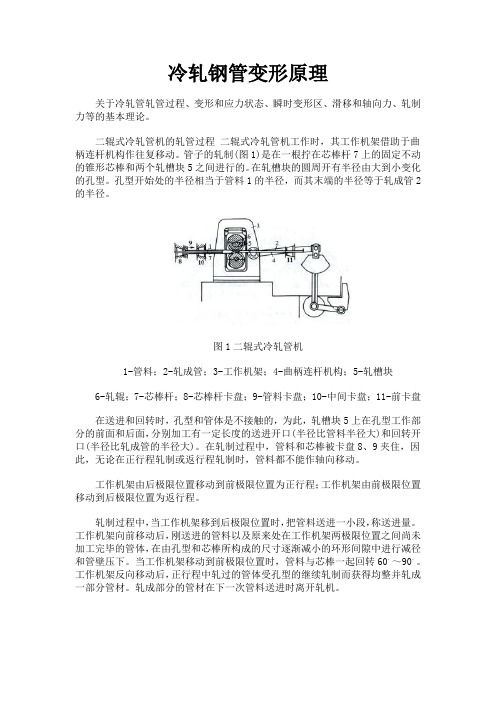
冷轧钢管变形原理关于冷轧管轧管过程、变形和应力状态、瞬时变形区、滑移和轴向力、轧制力等的基本理论。
二辊式冷轧管机的轧管过程二辊式冷轧管机工作时,其工作机架借助于曲柄连杆机构作往复移动。
管子的轧制(图1)是在一根拧在芯棒杆7上的固定不动的锥形芯棒和两个轧槽块5之间进行的。
在轧槽块的圆周开有半径由大到小变化的孔型。
孔型开始处的半径相当于管料1的半径,而其末端的半径等于轧成管2的半径。
图1二辊式冷轧管机1-管料;2-轧成管;3-工作机架;4-曲柄连杆机构;5-轧槽块6-轧辊;7-芯棒杆;8-芯棒杆卡盘;9-管料卡盘;10-中间卡盘;11-前卡盘在送进和回转时,孔型和管体是不接触的,为此,轧槽块5上在孔型工作部分的前面和后面,分别加工有一定长度的送进开口(半径比管料半径大)和回转开口(半径比轧成管的半径大)。
在轧制过程中,管料和芯棒被卡盘8、9夹住,因此,无论在正行程轧制或返行程轧制时,管料都不能作轴向移动。
工作机架由后极限位置移动到前极限位置为正行程;工作机架由前极限位置移动到后极限位置为返行程。
轧制过程中,当工作机架移到后极限位置时,把管料送进一小段,称送进量。
工作机架向前移动后,刚送进的管料以及原来处在工作机架两极限位置之间尚未加工完毕的管体,在由孔型和芯棒所构成的尺寸逐渐减小的环形间隙中进行减径和管壁压下。
当工作机架移动到前极限位置时,管料与芯棒一起回转60。
~90。
工作机架反向移动后,正行程中轧过的管体受孔型的继续轧制而获得均整并轧成一部分管材。
轧成部分的管材在下一次管料送进时离开轧机。
图2多辊式冷轧管机1-柱形芯棒;2-轧辊;3-轧辊架;4-支承板;5-厚壁套筒;6-大连杆;7-摇杆;8-管子多辊式冷轧管机的轧管过程多辊式冷轧管机轧制管材时见(图2),管子在圆柱形芯棒1和刻有等半径轧槽的3~4个轧辊2之间进行变形。
轧辊装在轧辊架3中,其辊颈压靠在具有一定形状的支承板(滑道)4上,支承板装在厚壁套筒5中,而厚壁套筒本身就是轧机的机架,它安装在小车上。
钢管冷轧机工作原理
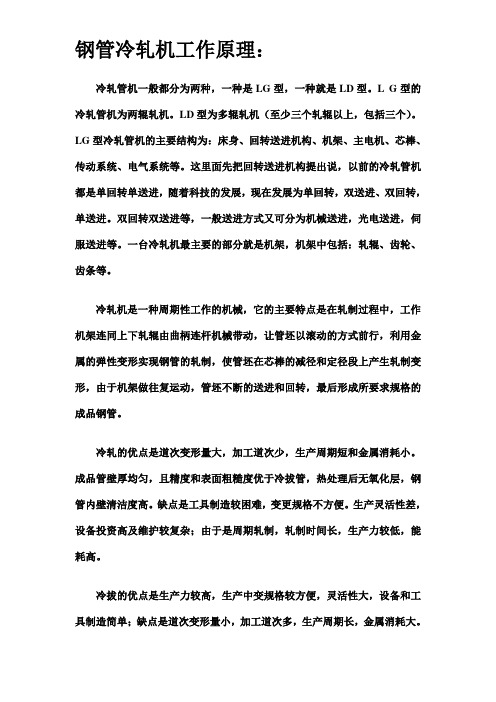
钢管冷轧机工作原理:
冷轧管机一般都分为两种,一种是LG型,一种就是LD型。
L G型的冷轧管机为两辊轧机。
LD型为多辊轧机(至少三个轧辊以上,包括三个)。
LG型冷轧管机的主要结构为:床身、回转送进机构、机架、主电机、芯棒、传动系统、电气系统等。
这里面先把回转送进机构提出说,以前的冷轧管机都是单回转单送进,随着科技的发展,现在发展为单回转,双送进、双回转,单送进。
双回转双送进等,一般送进方式又可分为机械送进,光电送进,伺服送进等。
一台冷轧机最主要的部分就是机架,机架中包括:轧辊、齿轮、齿条等。
冷轧机是一种周期性工作的机械,它的主要特点是在轧制过程中,工作机架连同上下轧辊由曲柄连杆机械带动,让管坯以滚动的方式前行,利用金属的弹性变形实现钢管的轧制,使管坯在芯棒的减径和定径段上产生轧制变形,由于机架做往复运动,管坯不断的送进和回转,最后形成所要求规格的成品钢管。
冷轧的优点是道次变形量大,加工道次少,生产周期短和金属消耗小。
成品管壁厚均匀,且精度和表面粗糙度优于冷拔管,热处理后无氧化层,钢管内壁清洁度高。
缺点是工具制造较困难,变更规格不方便。
生产灵活性差,设备投资高及维护较复杂;由于是周期轧制,轧制时间长,生产力较低,能耗高。
冷拔的优点是生产力较高,生产中变规格较方便,灵活性大,设备和工具制造简单;缺点是道次变形量小,加工道次多,生产周期长,金属消耗大。
钢管冷轧机工作原理

钢管冷轧机工作原理钢管冷轧是一种常见的金属加工工艺,其工作原理主要基于材料塑性变形和金属在加工过程中的力学性能。
钢管冷轧机是一种专用设备,通过连续加工工艺将热轧钢卷或钢板经过一系列冷轧工序加工成所需要的规格尺寸的钢管。
钢管冷轧机主要包括送料系统、轧制系统、切割系统和收卷系统等组成部分。
下面将详细介绍钢管冷轧机的工作原理。
1. 送料系统:钢卷通过送料机构进入钢管冷轧机。
送料机构通常由卷料车、开卷机和导向装置组成。
卷料车将热轧钢卷从卷盘上取出并输送给开卷机,开卷机将钢卷展开成平板,然后由导向装置引导进入轧制系统。
2. 轧制系统:经过展平后的钢卷经过一系列的轧辊,在压下力的作用下经历塑性变形,逐步被轧制成钢管形状。
轧制系统通常由一组上、下两个轧辊和辅助辊组成。
在轧制过程中,通过调整轧辊间隙和轧辊的转速,控制钢材的压下量和形变。
同时,冷却装置也会在轧制过程中对钢材进行冷却,以提高钢材的硬度和强度。
3. 切割系统:经过轧制后,钢管在冷轧机上继续前进,当达到设定长度时,就会通过切割系统将钢管切割成相应的长度。
切割系统通常由切割刀具、送料机构和切割控制装置组成。
4. 收卷系统:切割完成后,钢管经由收卷系统被连续收卷成卷筒状,方便运输和存储。
收卷系统通常由收卷机、收卷装置和卸卷装置组成,通过调整装置的工作方式和张力控制,确保钢管在收卷过程中的平整度和卷取质量。
钢管冷轧机的工作原理主要是通过上述的流程实现的,但在实际生产中,还需要多种辅助设备和控制系统的配合,以确保冷轧过程的稳定性和钢管质量的稳定。
总结:钢管冷轧机通过塑性变形,将热轧钢卷经过一系列的冷轧工序加工成所需的钢管。
其中,送料系统将钢卷引导进入冷轧机,轧制系统通过调整轧辊间隙和转速,实现钢材的塑性变形,切割系统将钢管切割成设定长度,收卷系统将切割完成的钢管连续收卷成卷筒状。
这些步骤的配合与调整,最终决定了钢管的质量和尺寸。
钢管冷轧机在实际生产中已经得到广泛应用,并对钢材加工工艺的提升和钢管质量的改善起到了重要作用。
不锈钢管成型原理.

不锈钢管成型原理.
不锈钢管的成型原理涉及到金属加工工艺和材料特性。
不锈钢
管的成型通常通过冷拔、冷轧、冷拉、冷挤压、热轧等工艺来实现。
这些工艺都是通过对不锈钢材料进行塑性变形来实现管材的成型。
首先,冷拔是将不锈钢坯料在室温下通过模具的拉拔作用,逐
步减小截面积,使得管坯产生塑性变形,最终形成不锈钢管。
冷拔
工艺可以获得高精度、光洁度好的管材。
其次,冷轧是将不锈钢板材或带材通过辊压机在室温下进行轧制,使其产生塑性变形,最终形成管材。
冷轧工艺可以获得尺寸精
度高、表面光洁度好的管材。
冷拉和冷挤压是通过将不锈钢坯料或者管坯在室温下通过模具
的挤压或拉拔来实现管材的成型,这些工艺可以获得高强度、高精
度的管材。
而热轧则是将不锈钢坯料加热至一定温度后进行轧制,由于材
料在高温下的塑性好,可以更容易地进行成型,热轧工艺可以获得
大直径、壁厚的不锈钢管材。
总的来说,不锈钢管的成型原理是通过对不锈钢材料进行塑性变形来实现管材的成型,不同的成型工艺可以获得不同性能和形状的不锈钢管材。
同时,成型过程中还需考虑材料的性能、成型设备的选型和工艺参数的控制等因素。
双排多辊式钢管冷轧变形过程研究

双排多辊式钢管冷轧变形过程研究刘建军刘庆国赖明道樊建成(燕山大学) (宝山钢铁(集团)公司)摘要对双排多辊式轧机冷轧钢管的变形过程进行了详细的分析研究,推导出一个轧制周期内延伸系数的计算公式。
关键词冷轧钢管变形过程STUDY ON DEFORMATION PROCESS OF COLD TUBEROLLINGWITH DOUBLE-SET THREE-ROLLER MILLLIU Jianjun LIU Qingguo LAI Mingdao(Yanshan University)FAN Jiancheng(Baoshan Iron and Steel Corp.)ABSTRACT The deformation process of cold tube rolling withdouble-set three-roller mill is analyzed and studied comprehensively and the calculating formula of elongation coefficient in a rolling cycle is deduced. KEY WORDS cold tube rolling,deformation process1 前言为了结合二辊式和多辊式轧机的优点,给高效率生产高质量、高精度的各种冷轧管材提供一种具有高度可靠性和适应性的冷轧管机,且该轧机具有很强的减径、减壁能力,燕山大学于1993年研制成功了双排多辊式冷轧管机,并在该轧机上轧制出符合国家标准的管材。
为了正确确定变形参数和合理进行轧制工具设计,本文对双排多辊式钢管冷轧时金属的变形过程进行了详细研究。
2 双排多辊式冷轧管机的机头结构双排多辊冷轧管机是一种周期式工作制度的轧机,其机头结构如图1所示,它的变形工具由支承板、轧辊、芯棒组成。
该轧机具有两排轧辊,每排由三个轧辊组成,三个轧辊被布置在与芯棒轴线垂直的平面内,轧辊轴线相互成60°角。
轧管机的工作原理简介

轧管机的工作原理简介1. 轧管机的工作原理简介轧管机是一种用于制造金属管材的机械设备。
它通过将金属材料经过多次轧制,使其形成所需的管材形状和尺寸。
在轧制过程中,轧管机主要通过热轧或冷轧两种不同的工艺来完成。
下面将介绍轧管机的工作原理以及它的关键组成部分。
2. 热轧轧管机的工作原理热轧轧管机主要用于加工高温金属坯料,如钢坯。
它的工作原理可以概括为以下几个步骤:步骤一:物料预热将钢坯通过加热炉等设备进行预热。
这么做的目的是提高钢材的可塑性,使其更容易塑性变形。
步骤二:入口端对齐将预热后的钢坯送入轧管机,通过辊道和辊缝的定位,将钢坯的入口端对齐,以确保轧制的准确度和稳定性。
步骤三:辊道轧制在钢坯进入辊道后,它会被传送到辊缝之间。
辊道上的辊子组按照一定规律布置,当钢坯经过时,辊子组作用下的压力使得钢坯逐渐变薄并改变形状。
这一步骤通常需要多个辊子组的连续作用,以实现所需的深度和形状。
步骤四:尺寸定型经过一系列的轧制后,钢坯的形状和尺寸已经接近最终要求。
此时,进一步通过调整和矫正辊缝间距、辊子组的排布等方式,以确保钢坯的精度和尺寸满足要求。
步骤五:产出经过尺寸定型后,经过轧制的钢坯被切割成所需长度,并通过传送带等方式将成品管材输送到下一个制造环节,如焊接或后续的加工工艺。
3. 冷轧轧管机的工作原理与热轧轧管机相比,冷轧轧管机主要用于加工室温下的金属坯料,如冷轧钢板。
其工作原理与热轧轧管机类似,但有一些区别。
冷轧轧管机不需要对金属坯料进行预热,因为它们已经处于室温下。
在入口端对齐之后,钢坯进入辊道,经过一系列的辊子组轧制,使其形成所需形状和尺寸。
不同之处在于,冷轧过程中对钢板施加的压力较小,以避免在金属坯料加工过程中出现塑性变形不良或其他结构性问题。
冷轧轧管机通常需要进行多次轧制,以逐渐达到所需尺寸和形状。
与热轧相比,冷轧后的成品管材表面更加光滑,并且具有更高的尺寸精度。
4. 轧管机的关键组成部分无论是热轧还是冷轧轧管机,它们都由一些关键组成部分构成,以实现其工作原理。
冷轧基础理论知识
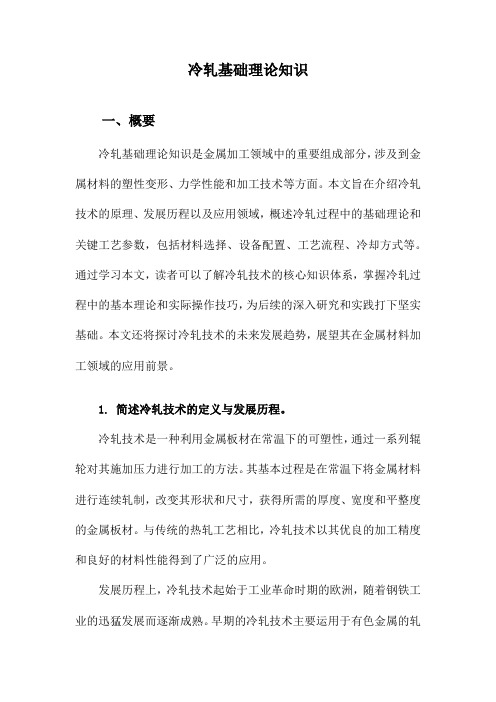
冷轧基础理论知识一、概要冷轧基础理论知识是金属加工领域中的重要组成部分,涉及到金属材料的塑性变形、力学性能和加工技术等方面。
本文旨在介绍冷轧技术的原理、发展历程以及应用领域,概述冷轧过程中的基础理论和关键工艺参数,包括材料选择、设备配置、工艺流程、冷却方式等。
通过学习本文,读者可以了解冷轧技术的核心知识体系,掌握冷轧过程中的基本理论和实际操作技巧,为后续的深入研究和实践打下坚实基础。
本文还将探讨冷轧技术的未来发展趋势,展望其在金属材料加工领域的应用前景。
1. 简述冷轧技术的定义与发展历程。
冷轧技术是一种利用金属板材在常温下的可塑性,通过一系列辊轮对其施加压力进行加工的方法。
其基本过程是在常温下将金属材料进行连续轧制,改变其形状和尺寸,获得所需的厚度、宽度和平整度的金属板材。
与传统的热轧工艺相比,冷轧技术以其优良的加工精度和良好的材料性能得到了广泛的应用。
发展历程上,冷轧技术起始于工业革命时期的欧洲,随着钢铁工业的迅猛发展而逐渐成熟。
早期的冷轧技术主要运用于有色金属的轧制,随着技术的进步,逐渐扩展到黑色金属的轧制领域。
随着材料科学和工艺技术的不断进步,冷轧技术也在不断地发展。
从简单的单机轧制到现代化的连续自动化生产线,从传统的模拟控制到数字化和智能化控制,冷轧技术已经成为现代制造业不可或缺的重要工艺手段。
其发展历程不仅体现了技术的进步,也反映了人类对材料性能的不断追求和探索。
2. 阐述冷轧技术在工业领域中的重要性。
冷轧技术在工业领域中的重要性不言而喻。
随着现代工业的发展,对于材料性能的要求越来越高,而冷轧技术作为一种先进的金属加工技术,能够满足这种高性能的需求。
冷轧过程通过控制金属的塑性变形和再结晶行为,可以显著提高金属的强度和硬度,同时保持良好的韧性和表面质量。
这使得冷轧材料在汽车、航空、建筑、电子等多个行业中得到广泛应用。
在汽车行业,冷轧技术用于生产高质量的钢板和带材,用于制造车身、发动机等关键部件。
17冷轧管材成形原理
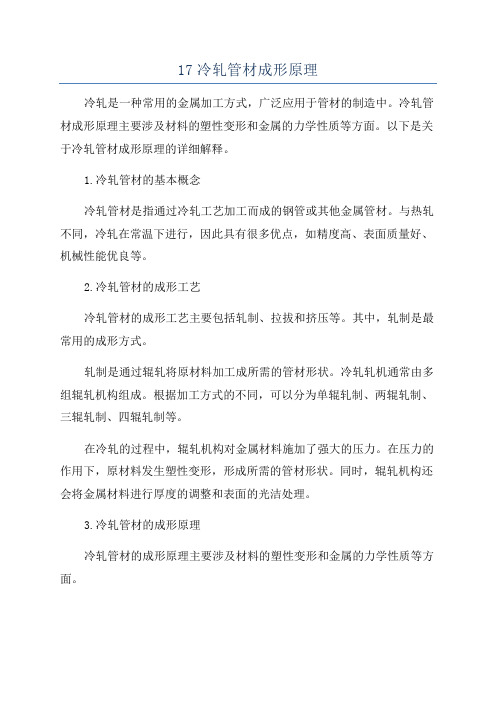
17冷轧管材成形原理冷轧是一种常用的金属加工方式,广泛应用于管材的制造中。
冷轧管材成形原理主要涉及材料的塑性变形和金属的力学性质等方面。
以下是关于冷轧管材成形原理的详细解释。
1.冷轧管材的基本概念冷轧管材是指通过冷轧工艺加工而成的钢管或其他金属管材。
与热轧不同,冷轧在常温下进行,因此具有很多优点,如精度高、表面质量好、机械性能优良等。
2.冷轧管材的成形工艺冷轧管材的成形工艺主要包括轧制、拉拔和挤压等。
其中,轧制是最常用的成形方式。
轧制是通过辊轧将原材料加工成所需的管材形状。
冷轧轧机通常由多组辊轧机构组成。
根据加工方式的不同,可以分为单辊轧制、两辊轧制、三辊轧制、四辊轧制等。
在冷轧的过程中,辊轧机构对金属材料施加了强大的压力。
在压力的作用下,原材料发生塑性变形,形成所需的管材形状。
同时,辊轧机构还会将金属材料进行厚度的调整和表面的光洁处理。
3.冷轧管材的成形原理冷轧管材的成形原理主要涉及材料的塑性变形和金属的力学性质等方面。
在冷轧的过程中,金属材料会发生塑性变形。
塑性变形是材料受到外力作用后,发生形状或体积变化,而不会恢复原状的现象。
这种塑性变形是在金属内部发生的,且伴随着材料的位移、应变和应力等变化。
冷轧管材的成形原理可以通过金属的力学性质来解释。
在冷轧的过程中,金属材料受到辊轧机构施加的压力。
这个压力会产生应变和应力,引起金属材料内部晶粒的位移和重新排列。
同时,冷轧还会改变金属材料的晶体结构。
在冷轧过程中,金属的晶粒会被拉伸、挤压并细化,从而形成细小的晶粒。
这些细小的晶粒会提高冷轧管材的强度和硬度,并改善其机械性能。
4.冷轧管材的应用领域冷轧管材广泛应用于各个领域,如建筑、制造业、交通运输和能源等。
在建筑领域,冷轧管材常用于制作钢结构、钢桁架和管道等,其高强度和良好的韧性使得建筑结构更加牢固和稳定。
在制造业领域,冷轧管材通常用于制作汽车零部件、机械设备和电子产品等。
其尺寸精度高、表面光洁度好等特点,使其能够符合制造业对精密度的要求。
冷轧的原理

冷轧的原理冷轧是一种金属板材或条材加工的方法,其原理是通过在低温条件下对金属进行塑性变形,使得金属材料的尺寸和形状得到调整和改变。
下面将详细介绍冷轧的原理。
冷轧的原理主要可以分为三个方面:金属材料的塑性变形特性、轧制设备和工艺参数的选择以及冷轧过程中可能出现的变形和硬化。
首先,金属材料的塑性变形特性是冷轧的基础。
金属材料的塑性变形主要是通过外力作用下的金属晶体滑移和重结晶来实现的。
当应力作用在金属上时,金属晶体中的滑移系统激活,使得晶体沿着滑移面滑移,继而产生塑性变形。
而在冷轧过程中,由于材料的温度较低,使得滑移速度减慢,晶粒和位错的运动受到限制,从而增加了材料的强度和硬度。
此外,冷轧还可以通过重组晶体结构,消除和修复位错,提高材料的抗变形能力。
其次,轧制设备和工艺参数的选择对于冷轧的效果至关重要。
轧制设备主要包括轧机和辅助设备。
轧机根据材料的形状和规格选择不同的工作方式,如单辊式、双辊式或多辊式。
辅助设备包括冷却系统、润滑系统、张力控制系统等,能够对金属材料的温度、润滑和张力进行控制,以保证冷轧过程的顺利进行。
工艺参数的选择包括轧制速度、轧制压力和轧制温度等。
轧制速度决定了材料的变形速率和变形程度,过高的轧制速度会导致材料的变形不均匀和表面质量的下降;轧制压力可以控制材料的变形量和厚度的变化,过大的轧制压力会导致应变的集中而形成裂纹;轧制温度能够控制材料的强度和硬度,过低的轧制温度会导致材料的可塑性下降,过高的轧制温度会导致材料的回弹和回复能力降低。
最后,冷轧过程中可能出现的变形和硬化是冷轧的关键。
在冷轧过程中,金属材料会受到压力和摩擦力的作用,从而在轧制方向上发生形变。
这种形变可以通过金属材料内部的滑移和变形来实现。
同时,金属材料还会受到塑性变形引起的硬化作用,即材料的硬度和强度逐渐增加。
硬化是由位错的运动和累积引起的,随着冷轧的进行,位错会逐渐堆积形成高密度的晶界,使得金属材料的塑性变形能力减弱。
无缝管冷加工变形原理

1、变形过程和变形区
短芯棒拔制过程
短芯拔制一般使用锥形外模和圆柱形芯棒,也有使用弧形外模和锥形芯棒的, 或在生产过程中两者配合使用。 要实现短芯棒拔制,首先存在一个建立过程的问题。拔制过程的建立一般包括 以下几个阶段:钢管前端进入外模开始减径;钢管内壁和送入的芯棒接触并把它 带入变形区,钢管减壁。这时,芯棒和钢管一起前移,稍后,芯棒被固定不再移 动,钢管在固定的外模与芯棒之间变形和移动,变形过程中进入稳定拔制段。 建立拔制过程中的关键是能否把芯棒带入变形区,芯棒前端的形状是影响芯棒 带入条件的主要因素。芯棒前端倒拔的形状应该保证钢管内壁与芯棒接触时作用 在芯棒上的正压力与摩擦力合力的水平分力朝向拔制方向,为了达到上棕要求, 应把芯棒前端倒成锥形防止弧形,因前一种形状对带入芯棒有利。芯棒前端合适 的倒角与摩擦条件及变形程度有关,一般倒成45度角。 在稳定拔制阶段,钢管的变形过程是减径,继之是减壁,最后是定径。
拔制力
根据上述所知,在拔管时变形量越大则拔制力越大, 拔制应力也随之增 加,所以,由于受上述条件的限制,每道次的变形量存在 一个极限值。为了 增加拔管时的道次变形量,防止拔断,必须降低拔制力。 冷拔钢管时,由于加工硬化的结果,变形后钢管的屈 服极限提高了,而 且加工硬化使屈服极限提高的程度大于使拔应力提高的程 度,这样可以减少 拔断的可能性,从这个意义上讲,加工硬化的结果有利于 增加拔制时的道次 变形量。
短芯棒拔管过程
扩拔
除了减径和减径减壁以外,拔管过程也可用 来进行扩管,即扩大钢管的 直径,扩径时的扩径率一般≦15%~20%,扩径后 钢管的长度有所缩短,壁厚 有所减薄,扩径后钢管的壁厚按以下公式计算:
S1= 1 [√D1 +4(D0-S0)S0-D1] 2
冷轧的原理
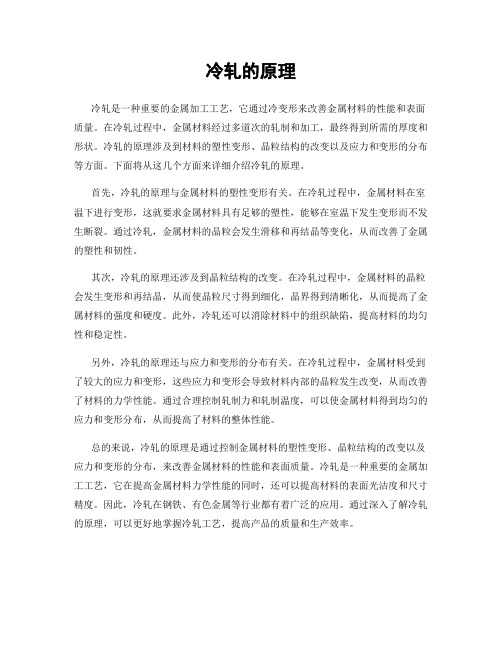
冷轧的原理
冷轧是一种重要的金属加工工艺,它通过冷变形来改善金属材料的性能和表面质量。
在冷轧过程中,金属材料经过多道次的轧制和加工,最终得到所需的厚度和形状。
冷轧的原理涉及到材料的塑性变形、晶粒结构的改变以及应力和变形的分布等方面。
下面将从这几个方面来详细介绍冷轧的原理。
首先,冷轧的原理与金属材料的塑性变形有关。
在冷轧过程中,金属材料在室温下进行变形,这就要求金属材料具有足够的塑性,能够在室温下发生变形而不发生断裂。
通过冷轧,金属材料的晶粒会发生滑移和再结晶等变化,从而改善了金属的塑性和韧性。
其次,冷轧的原理还涉及到晶粒结构的改变。
在冷轧过程中,金属材料的晶粒会发生变形和再结晶,从而使晶粒尺寸得到细化,晶界得到清晰化,从而提高了金属材料的强度和硬度。
此外,冷轧还可以消除材料中的组织缺陷,提高材料的均匀性和稳定性。
另外,冷轧的原理还与应力和变形的分布有关。
在冷轧过程中,金属材料受到了较大的应力和变形,这些应力和变形会导致材料内部的晶粒发生改变,从而改善了材料的力学性能。
通过合理控制轧制力和轧制温度,可以使金属材料得到均匀的应力和变形分布,从而提高了材料的整体性能。
总的来说,冷轧的原理是通过控制金属材料的塑性变形、晶粒结构的改变以及应力和变形的分布,来改善金属材料的性能和表面质量。
冷轧是一种重要的金属加工工艺,它在提高金属材料力学性能的同时,还可以提高材料的表面光洁度和尺寸精度。
因此,冷轧在钢铁、有色金属等行业都有着广泛的应用。
通过深入了解冷轧的原理,可以更好地掌握冷轧工艺,提高产品的质量和生产效率。
钢管的冷拔和冷轧技术

钢管的冷拔和冷轧技术钢管作为一种广泛应用的建筑材料,得到了越来越广泛的应用。
在生产过程中,冷拔和冷轧是两种重要的钢管加工技术。
本文将详细介绍钢管的冷拔和冷轧技术。
一、冷拔技术冷拔是一种机械加工技术,它是通过在常温下拉伸准备好的钢管,从而使其尺寸变小,同时提高其内部品质。
在冷拔过程中,使用的是冷拔机,它可以通过不同的模具生成不同规格和形状的钢管。
1、冷拔机的结构冷拔机主要由内外壳、传动系统、润滑系统和电控系统等组成。
内壳是由负责冷拔成形的模具构成,而外壳则负责支撑内壳和提供轴向力。
传动系统包括电机、减速器等,它们为模块提供动力和速度控制。
润滑系统主要用于减少模具的磨损和提高钢管表面的光洁度。
电控系统负责操作机器人的全过程。
2、冷拔工艺在冷拔的工艺中,首先制造厚壁钢管,然后放入冷拔机内,通过不同大小的模具进行冷拔。
冷拔时,在不同的冷拔通道中进行拉伸,使其焊接接头部分发生塑性变形,从而消除了内部所需。
在冷拔过程中要高度重视冷拔通道的准备工作,通道的尺寸和平整度不仅会影响钢管的尺寸精度,还会影响到钢管的平整度和表面光洁度。
因此,在冷拔通道的准备过程中需要保持高度的认真和负责任。
3、冷拔加工优点与其他钢管加工技术相比,冷拔具有以下优点:(1)提高钢管的尺寸精度;(2)提高钢管的表面光洁度;(3)增加钢管抗拉强度;(4)消除钢管内部应力。
二、冷轧技术冷轧技术是一种通过将钢管置于规定的温度下,使用一定压力来使其尺寸变小的机械加工技术。
与冷拔不同,冷轧是通过将钢管和辊轮轧制机紧密接触,从而达到加工的效果。
去除表面的氧化层。
1、冷轧机的结构冷拧机由传动系统、摆动系统和辊轮组成。
传动系统包括电动机、齿轮、轴承和传动轴等;摆动系统由液压活塞、推杆和底座组成;辊轮由上辊轮、下辊轮、齿轮和轴承等组成。
2、冷轧工艺冷轧工艺的前期工作包括钢管的加热和温度控制。
钢管加热目的是使其达到一定的塑性变形能力。
在冷轧机的轧辊中,一辊轮和下辊轮紧密接触,钢管被挤压固定,同时由于轧辊下压力的作用钢管发生弹性塑性变形,其内部变形。
轧制变形基本原理

1 第四章 轧制变形基本原理金属塑性加工是利用金属能够产生永久变形的能力,使其在外力作用下进行塑性成型的一种金属加工技术,也常叫金属压力加工。
基本加工变形方式可以分为:锻造、轧制、挤压、分为:热加工、冷加工、温加工。
金属塑性加工的优点(1)因无废屑,可以节约大量的金属,成材率较高;(2)可改善金属的内部组织和与之相关联的性能;(3)生产率高,适于大量生产。
第一节 轧钢的分类轧钢是利用金属的塑性使金属在两个旋转的轧辊之间受到压缩产生塑性变形,从而得到具有一定形状、尺寸和性能的钢材的加工过程。
被轧制的金属叫轧件;使轧件实现塑性变形的机械设备叫轧钢机;轧制后的成品叫钢材。
一、根据轧件纵轴线与轧辊轴线的相对位置分类轧制可分为横轧、纵轧和斜轧。
如图1、2、3。
横轧:轧辊转动方向相同,轧件的纵向轴线与轧辊的纵向轴线平行或成一定锥角,轧制时轧件随着轧辊作相应的转动。
它主要用来轧制生产回转体轧件,如变断面轴坯、齿轮坯等。
纵轧:轧辊的转动方向相反,轧件的纵向轴线与轧辊的水平轴线在水平面上的投影相互垂直,轧制后的轧件不仅断面减小、形状改变,长度亦有较大的增长。
它是轧钢生产中应用最广泛的一种轧制方法,如各种型材和板材的轧制。
斜轧:轧辊转动方向相同,其轴线与轧件纵向轴线在水平面上的投影相互平行,但在垂直面上的投影各与轧件纵轴成一交角,因而轧制时轧件既旋转,又前进,作螺旋运动。
它主要用来生产管材和回转体型材。
图1 横轧简图1—轧辊;2—轧件;3—支撑辊图2 纵轧示意图图3 斜轧简图1—轧辊;2—坯料;3—毛管;4—顶头;5—顶杆二、根据轧制温度不同又可分为热轧和冷轧。
所有的固态金属和合金都是晶体。
温度和加工变形程度对金属的晶体组织结构及性能都有不可忽视的影响。
金属在常温下的加工变形过程中,其内部晶体发生变形和压碎,而引起金属的强度、硬度和脆性升高,塑性和韧性下降的现象,叫做金属的加工硬化。
把一根金属丝固定于某一点在手中来回弯曲多次后,钢丝就会变硬、变脆进而断裂,这就是加工硬化现象的一个例子。
冷轧管时管坯断面的变形过程

冷轧管时管坯断面的变形过程嘿,咱今儿就来唠唠冷轧管时管坯断面的变形过程。
你想想啊,那管坯就好比是一块等待雕琢的璞玉,而冷轧这个过程呢,就是那神奇的雕琢之手。
一开始啊,管坯好好地在那儿,它有着自己原本的形状和模样。
可当冷轧这一环节开始后,就像是一场奇妙的冒险之旅开启了。
那力量施加在管坯上,它的断面就开始发生变化啦!就好像一个人原本走在平坦的大路上,突然遇到了山坡,得努力去攀爬,去适应新的地形。
这变形的过程可不是一蹴而就的哟!它是一点一点慢慢来的,就跟我们成长一样,得经历好多阶段呢。
在这个过程中,管坯的断面会逐渐被拉伸、压缩、扭曲,哎呀呀,那场面可真是有趣又神奇。
你说这像不像我们生活中的一些经历呢?有时候我们也会遇到各种各样的挑战,就如同管坯遭遇冷轧一样,我们也得去适应,去改变,去让自己变得更好更强。
你再想想看,要是没有这个变形过程,那能有最终我们看到的那精致的冷轧管吗?肯定不能啊!这就好比是盖房子,没有一砖一瓦的积累,哪来坚固漂亮的大厦呢?在这个变形过程中,每一个细节都至关重要啊!哪怕是一点点的偏差,都可能会影响到最终的成品质量。
这就提醒我们,在做任何事情的时候,都得认真对待每一个小环节,不能马虎大意,对吧?而且啊,这变形过程还需要各种条件的配合呢。
就像是一场精彩的演出,光有主角可不行,还得有配角、灯光、音效等等。
冷轧管时管坯断面的变形也一样,温度啦、压力啦、速度啦,这些都得恰到好处,不然可出不来好的效果。
咱再深入想想,这管坯的变形过程其实也蕴含着一种坚持和努力的精神呢。
它得不断地承受着压力和变化,却始终不放弃,一直努力让自己变成更好的样子。
这不就是我们应该学习的吗?遇到困难不退缩,勇往直前,努力让自己变得更优秀。
总之呢,冷轧管时管坯断面的变形过程可真是一个充满了神奇和挑战的过程啊!它让我们看到了材料的韧性和潜力,也让我们明白了努力和坚持的重要性。
所以啊,我们可得好好地去理解它、研究它,说不定还能从中学到不少人生的道理呢!你说是不是这个理儿?。
材料的冷变形与冷加工

材料的冷变形与冷加工材料的冷变形与冷加工是工程领域中一项重要的技术,它对材料的力学性能和结构特征产生显著的影响。
本文将从冷变形和冷加工的定义、原理、应用以及优缺点等方面进行探讨。
一、冷变形的定义及原理冷变形是指在室温下对材料施加外力,通过塑性变形使材料产生形状和尺寸的改变。
与热变形相比,冷变形不需要进行材料的加热处理,因此可以更加节能、经济和环保。
冷变形的原理是通过塑性变形的过程,使材料的晶体结构发生位错的运动和滑移。
冷变形过程中,外力作用下,材料中的位错被引导并沿特定方向滑移,导致材料发生塑性变形。
二、冷变形的应用冷变形广泛应用于金属材料的加工和制造中。
例如,冷轧是一种常见的冷变形工艺,用于生产薄板和带材;冷拔则常用于制造高精度、高强度的丝材或管材。
此外,冷变形还可以改善材料的力学性能,例如提高材料的硬度、强度和耐磨性等。
同时,冷变形还可以改善材料的表面质量,提高材料的光洁度和精度。
三、冷加工的定义及原理冷加工是指在室温下对材料进行加工,如冷锻、冷镦、冷挤压等。
与热加工相比,冷加工在保持材料性能的同时,更加精确和高效。
冷加工的原理是将材料加工至超过其屈服强度的程度,使材料发生塑性变形。
在冷加工的过程中,材料的晶体结构发生位错滑移以及晶界滑动等变形过程,从而改变了材料的形状和尺寸。
四、冷加工的应用冷加工是金属加工中常用的工艺之一,广泛应用于汽车、机械、电子、航空航天等众多领域。
例如,冷挤压技术可以用于制造高精度的螺纹、螺母和螺柱等零部件;冷镦技术可以用于生产各种螺栓和紧固件。
通过冷加工可以实现对材料性能和结构的优化。
在材料的冷加工过程中,由于晶体结构的变化和位错的堆积,得到的材料具有更高的强度、硬度和韧性,适用于各类高强度构件的制造。
五、冷变形与冷加工的优缺点冷变形和冷加工相对于热变形和热加工具有以下优点:1. 节能环保:冷变形和冷加工无需进行材料的加热处理,相比于热处理能够节约能源并减少环境污染。
金属低温变形技术
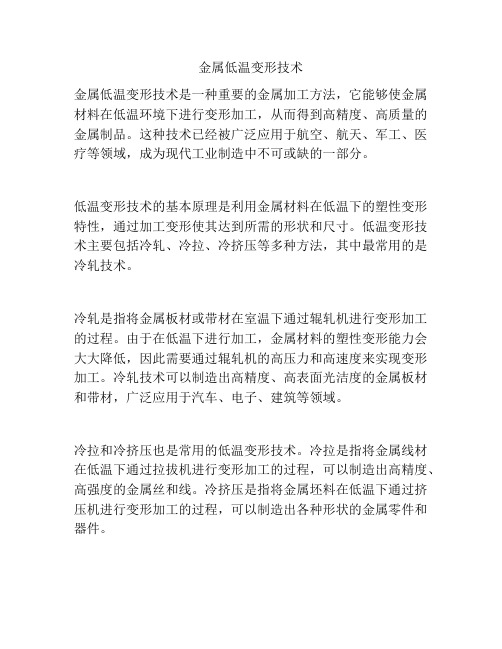
金属低温变形技术
金属低温变形技术是一种重要的金属加工方法,它能够使金属材料在低温环境下进行变形加工,从而得到高精度、高质量的金属制品。
这种技术已经被广泛应用于航空、航天、军工、医疗等领域,成为现代工业制造中不可或缺的一部分。
低温变形技术的基本原理是利用金属材料在低温下的塑性变形特性,通过加工变形使其达到所需的形状和尺寸。
低温变形技术主要包括冷轧、冷拉、冷挤压等多种方法,其中最常用的是冷轧技术。
冷轧是指将金属板材或带材在室温下通过辊轧机进行变形加工的过程。
由于在低温下进行加工,金属材料的塑性变形能力会大大降低,因此需要通过辊轧机的高压力和高速度来实现变形加工。
冷轧技术可以制造出高精度、高表面光洁度的金属板材和带材,广泛应用于汽车、电子、建筑等领域。
冷拉和冷挤压也是常用的低温变形技术。
冷拉是指将金属线材在低温下通过拉拔机进行变形加工的过程,可以制造出高精度、高强度的金属丝和线。
冷挤压是指将金属坯料在低温下通过挤压机进行变形加工的过程,可以制造出各种形状的金属零件和器件。
低温变形技术具有许多优点,如能够提高金属材料的强度和硬度、改善其耐腐蚀性能、提高其表面光洁度等。
但同时也存在一些不足之处,如加工难度大、设备成本高、生产效率低等问题。
因此,在实际应用中需要根据具体情况选择合适的加工方法和设备,并进行充分的技术研究和优化。
总之,低温变形技术是一种重要的金属加工方法,具有广泛的应用前景和发展空间。
随着科技的不断进步和工业制造的不断发展,相信这种技术将会得到更加广泛的应用和推广。
铜管调直方法

铜管调直方法引言铜管是一种常见的金属管材,用于制作各种工业和建筑构件。
然而,在生产和运输过程中,铜管常常会出现弯曲和扭曲的情况,这就需要对铜管进行调直。
铜管调直是一项关键的工艺,它需要合适的方法和设备来实现。
本文将详细介绍铜管调直的方法,并探讨其原理和适用范围。
常见的铜管调直方法1. 冷轧法冷轧法是一种常见的铜管调直方法,它利用冷轧机的作用力将铜管进行调整。
具体步骤如下:1.将弯曲或扭曲的铜管放入冷轧机中。
2.调整冷轧机的辊轴位置,使其与铜管接触。
3.开始启动冷轧机,辊轴的作用力将铜管逐渐调直。
4.根据需要,可以多次进行冷轧调直操作,直到满足要求为止。
冷轧法的优点是调直效果好,能够适应不同直径和弯曲程度的铜管。
然而,该方法需要专业的设备和操作技术,成本较高。
2. 加热调直法加热调直法是另一种常用的铜管调直方法,它利用热力来改变铜管的形状。
具体步骤如下:1.将弯曲或扭曲的铜管放入加热炉中,使其均匀受热。
2.当铜管达到一定温度后,取出并迅速放入调直装置中。
3.调整调直装置的参数,如辊轴间距和压力,使其与铜管接触。
4.开始调整装置,辊轴的作用力将铜管逐渐调直。
5.根据需要,可以多次进行加热调直操作,直到满足要求为止。
加热调直法的优点是可以调整更复杂的弯曲和扭曲形状,适用范围广。
然而,该方法需要高温和高压力,操作过程需要注意安全。
3. 液压调直法液压调直法是一种利用液压力进行调直的方法。
具体步骤如下:1.将弯曲或扭曲的铜管放入液压调直机中。
2.调整调直机的参数,如液压压力和调直方向。
3.启动液压调直机,液压力将铜管逐渐调直。
4.根据需要,可以多次进行液压调直操作,直到满足要求为止。
液压调直法的优点是简单易行,能够快速调直铜管。
然而,该方法适用范围有限,通常只适用于小直径和简单形状的铜管。
铜管调直的原理和适用范围铜管调直的原理是通过外力的作用改变铜管的形状,使之趋于直线。
不同的调直方法基于不同的原理,适用范围也有所不同。
- 1、下载文档前请自行甄别文档内容的完整性,平台不提供额外的编辑、内容补充、找答案等附加服务。
- 2、"仅部分预览"的文档,不可在线预览部分如存在完整性等问题,可反馈申请退款(可完整预览的文档不适用该条件!)。
- 3、如文档侵犯您的权益,请联系客服反馈,我们会尽快为您处理(人工客服工作时间:9:00-18:30)。
冷轧管变形原理deformation theory of cold rolling tube process关于冷轧管轧管过程、变形和应力状态、瞬时变形区、滑移和轴向力、轧制力等的基本理论。
二辊式冷轧管机的轧管过程二辊式冷轧管机工作时,其工作机架借助于曲柄连杆机构作往复移动。
管子的轧制(图1)是在一根拧在芯棒杆7上的固定不动的锥形芯棒和两个轧槽块5之间进行的。
在轧槽块的圆周开有半径由大到小变化的孔型。
孔型开始处的半径相当于管料1的半径,而其末端的半径等于轧成管2的半径。
图1二辊式冷轧管机1-管料;2-轧成管;3-工作机架;4-曲柄连杆机构;5-轧槽块6-轧辊;7-芯棒杆;8-芯棒杆卡盘;9-管料卡盘;10-中间卡盘;11-前卡盘在送进和回转时,孔型和管体是不接触的,为此,轧槽块5上在孔型工作部分的前面和后面,分别加工有一定长度的送进开口(半径比管料半径大)和回转开口(半径比轧成管的半径大)。
在轧制过程中,管料和芯棒被卡盘8、9夹住,因此,无论在正行程轧制或返行程轧制时,管料都不能作轴向移动。
工作机架由后极限位置移动到前极限位置为正行程;工作机架由前极限位置移动到后极限位置为返行程。
轧制过程中,当工作机架移到后极限位置时,把管料送进一小段,称送进量。
工作机架向前移动后,刚送进的管料以及原来处在工作机架两极限位置之间尚未加工完毕的管体,在由孔型和芯棒所构成的尺寸逐渐减小的环形间隙中进行减径和管壁压下。
当工作机架移动到前极限位置时,管料与芯棒一起回转60。
~90。
工作机架反向移动后,正行程中轧过的管体受孔型的继续轧制而获得均整并轧成一部分管材。
轧成部分的管材在下一次管料送进时离开轧机。
图2多辊式冷轧管机1-柱形芯棒;2-轧辊;3-轧辊架;4-支承板;5-厚壁套筒;6-大连杆;7-摇杆;8-管子多辊式冷轧管机的轧管过程多辊式冷轧管机轧制管材时见(图2),管子在圆柱形芯棒1和刻有等半径轧槽的3~4个轧辊2之间进行变形。
轧辊装在轧辊架3中,其辊颈压靠在具有一定形状的支承板(滑道)4上,支承板装在厚壁套筒5中,而厚壁套筒本身就是轧机的机架,它安装在小车上。
工作时,曲柄连杆和摇杆系统分别带动小车和装在工作机架内的轧辊架作往复移动。
由于小车和轧辊架是通过大连杆6和小连杆分别与摇杆7相联结的,所以当摇杆摆动时,轧辊与支承板便产生相对运动。
当辊径在具有一定形状的支承板表面上作往复滚动时,轧辊和圆柱形芯棒组成的环形孔型就由大变小,再由小变大地作周期性改变。
当小车走到后板极限位置时,送进一定长度的管料并将管体回转一个角度。
为了降低返行程轧制时的轴向力以防止两根相邻管料在端部相互切入,一般管料的送进和管体的回转,是当小车在后极限位置时同时进行的。
当小车离开后极限位置向前移动时,孔型逐渐变小,进行轧制,在返行程轧制时获得均整。
冷轧管时金属的变形和应力状态以二辊式冷轧管机轧管为例,在轧管过程中金属的变形过程如图3所示。
送料时工作锥向轧制方向移动一段距离m(送进量),相当于管料的Ⅰ-Ⅰ截面移动相同的距离到了Ⅰ1-Ⅰ1,位置,Ⅱ一Ⅱ的截面移动同一个距离m到了Ⅱ1一Ⅱ1位置(图3a)。
由于在管料送进的时候,工作锥的内表面脱离了芯棒的表面,两者之间形成了一个间隙c,所以,当工作机架前移,工作锥变形时,在变形区中先是减径,然后是压下管壁(图3b),而且在变形和延伸的过程中,工作锥内表面与位于轧槽块前的芯棒之间的间隙不断增大。
同时,工作锥的末端截面移动到Ⅱx一Ⅱx位置。
图3 冷轧管时金属变形在返行程轧制时,由于轧制前管体回转了一个角度,原来处在孔型侧壁的金属转到了孔型顶部,因而工作锥受到了均整,使任何一个横截面形状更圆,壁厚更均匀。
另外,由于变形时其中一部分金属向周向流动的结果,在孔型侧壁和工作锥的内表面管料脱离了芯棒,这样有利于下一次管料送进。
图4 冷轧管变形时的作用力工作机架回到后极限位置Ⅰ时,一个轧制周期结束,轧成管的一段长度为△L T(图3c):△L T=%26pi;S0 (D0-S0)m/%26pi;S T(D T-S T)=%26mu;%26epsilon;m式中%26mu;%26epsilon;为总延伸系数,等于管料截面积与轧成管截面积之比,m为送进量。
总延伸系数%26mu;%26epsilon;和送进量m越大;则△L T越大,反之△L T越小。
冷轧管时,金属是在不断改变着位置和形状的瞬时变形区内变形的。
金属在轧辊的正压力P、芯棒的正压力N,来自轧辊的摩擦阻力T以及来自芯棒的摩擦阻力T1的作用下进行变形(图4)。
若在金属与轧辊接触的变形区中取一单元体,则其径向主应力%26sigma;1、周向主应力%26sigma;2和轴向主应力%26sigma;3均为压应力,所以冷轧管时,金属变形基本应力的应力状态是三向压应力,但在辊缝处(%26phi;角范围内)轴向承受单向拉应力,见图5。
与冷拔管时的二向压一向拉的应力状态相比,这种应力状态更有利于金属塑性的发挥。
图5 冷轧管变形时应力状态沿轧槽分布图a-正行程;b-反行程瞬时变形区的结构无论正行程轧制或返行程轧制,瞬时变形区的出口截面都与工作机架的中心截面相重合。
在二辊式冷轧管机上轧管时,由于进入变形区的管体要先减小直径再减小壁厚,因此,瞬时变形区包括由减径角%26theta;p和压下角%26theta;t构成的两部分(图3b)。
在工作机架的行程中%26theta;p、%26theta;t 的大小是变化的。
%26theta;p与%26theta;t之和构成瞬时变形区总的接触角。
在多辊式冷轧管机上轧管时,行程的开始阶段瞬时变形区由单一的减径区构成,在行程的其他部分,由于这种轧机使用圆柱形芯棒,瞬时变形区可以认为由单一的减壁区构成。
瞬时变形区变形量的确定在一般纵轧过程中,变形区的几何尺寸是不变的。
所以坯料上的任一个截面都可以一直从变形区的入口移动到出口。
变形区进口截面和出口截面的高度差、就是坯料上任一截面连续通过变形区时的压下量,而且是稳定不变的。
但在冷轧管时,进入变形区的和离开变形区的管体截面的尺寸是不断变化的,而且瞬时变形区进口截面和出口截面的高度差也不等于工作锥上进入瞬时变形区的截面在一个轧制行程中的压下量。
因此,冷轧管时,工作锥上的任一截面在一个轧制行程中连续通过不断变化着的瞬时变形区时所达到的变形量是不相同的,而且确定它的大小也是比较复杂的。
在实际计算中,通常是根据各瞬时变形区出口截面的尺寸,确定该截面变形开始时在工作锥上的位置和尺寸,再计算其变形量。
这个变形量称为瞬时变形区变形量。
瞬时变形区变形量的计算一般以下述原则为基础:设某瞬时变形区的出口截面为Ⅰ-Ⅰ(图6),该截面在通过瞬时变形区时所经受的压下量等于它与另一截面Ⅱ一Ⅱ的高度差,而这两个截面之间所包括的金属体积等于送进的金属体积。
图中R x、r x和S x分别为瞬时变形区出口截面的外半径、内半径和壁厚;R%26Delta;x、r%26Delta;x和S%26Delta;x分别为该截面变形前的外半径、内半径和壁厚。
图6 直角坐标中的一段工作锥在冷轧管时,主要变形是在正行程轧制过程中完成的;但是,由于工作机架:轧辊等零部件的弹性恢复和轧制前管体的回转,有的轧机还有送进,因此在返行程轧制时工作锥也有一定的甚至较大的变形。
一般可用下列公式来计算正行程轧制和返行程轧制的壁厚压下量式中%26Delta;S n为正行程轧制时的壁厚压下量;%26Delta;S o为返行程轧制时的壁厚压下量:V y=(R0+r0)/(R x+r x)mS x为送进体积率;R0、r0为管料的外半径和内半径;%26alpha;为锥形芯棒的母线倾斜角;%26gamma;为工作锥母线的倾斜角;K t 为计算返行程轧制时变形量的系数,一般可取K t=0.3~0.4。
一个轧制周期中的壁厚压下量为:瞬时变形区的边界和咬入角为了计算变形时轧辊同轧件的接触面积,必须知道瞬时变形区的前后边界线。
周期式轧制时,瞬时变形区的后边界线(出口一侧的边界线)应是一条空间曲线,但实际上和轧机中心面与工作锥的交线相差不大,故一般把后者作为瞬时变形区的后边界线。
瞬时变形区的前边界线(入口一侧的边界线)是空间曲线,它取决于沿孔型周边的变形区各纵截面上的接触角%26theta;0。
(图7)图7 瞬时变形区的纵截面%26theta;可按下列简化公式计算:式中%26Delta;R x为瞬时变形区中的半径压下量;%26rho;0为轧辊的理想半径;C 为孔型周边上不同点处孔型的高度,R x为瞬时变形区出口截面工作锥的半径。
在孔型的脊部,接触角为:式中%26rho;r为孔型脊部轧辊的半径。
若以瞬时变形区的壁厚压下量%26Delta;S x取代上式中的%26Delta;R x,则可得到确定瞬时变形区前边界线上各点接触角的计算公式。
瞬时变形区的接触面积图8为二辊式和多辊式冷轧管机轧制管子时的变形区及接触面积图示。
文献中有多种计算瞬时变形区接触面积的近似公式。
一种常用的计算二辊式冷轧管机轧管时接触面积的方法如下。
图9为借助于计算接触角%26theta;得到的正行程轧制时瞬时变形区接触表面积的垂直投影和水平投影。
区域OPLMC为总接触表面积的垂直投影;OPRE=F y s为减壁区接触表面积的垂直投影;B1L1M1NM2L2B2=F d x用为总接触表面积的水平投影;C1R1PR2C2=F x s减壁区接触表面积的水平投影。
图8 冷轧钢管时变形区及接触面积图示a-二辊冷轧管机的变形区;b-多辊式冷轧管机变形区;c-正行程的接触面积;d-返行程的接触面积1-塑性和弹性变形区;2-弹性变形区;3-管子;4-芯棒;5-轧辊图9 正行程轧制时瞬时变形区接触面积a-垂直投影;b-水平投影先来确定减壁区接触表面积的水平投影。
由图9可知,减壁区接触表面积的水平投影可分成两部分:F x s=2(F c1p1po +F p1R1P)在孔型脊部C=R x,面积F c1p1po用下式计算具有足够的精确度:式中C为孔槽深,近似为孔槽宽之半。
面积F p1R1P=%26eta;1 1/2(P1P)(R1D),式中%26eta;1为系数,等于0.85。
R1D=(%26rho;0-C min)sin(%26theta;tc-%26theta;tr),C min为孔型周边与工作锥最先接触处轧槽的高度;%26theta;tc为孔型脊部减壁区的接触角;%26theta;tr为孔型周边和工作锥最先接触处减壁区的接触角。
所以计算F x s的公式可写成[取sin(%26theta;tc-%26theta;tr)%26asymp;%26theta;tc-%26theta;tr]:由于孔型侧壁的开口角通常为16。