现场改善IE案例
现场IE改善案例分析--生产线平衡分析改善案例
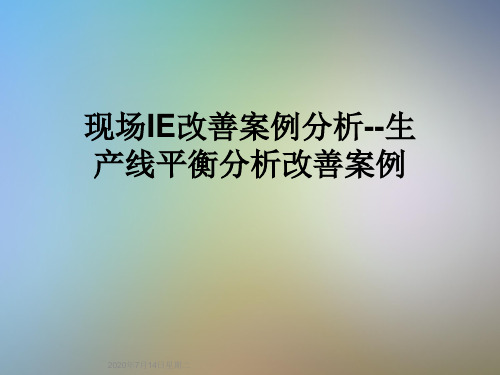
生产线平衡定义
对生产的全部工序进行均衡,调整作业 负荷和工作方式,消除工序不平衡和工 时浪费,实现“一个流”。
出料
入料
平衡生产线的意义
通过平衡生产线可以综合应用到程序分析、动作分析 、layout分析,搬动分析、时间分析等全部IE手法,提 高全员综合素质
在平衡的生产线基础上实现单元生产,提高生产应变 能力,对应市场变化实现柔性生产系统
(4) 4种增值的工作
站在客户的立场上,有四种增值的工作
1、使物料变形 2、组装 3、改变性能 4、部分包装
物料从进厂到出厂,只有不到 10% 的时间是增值的!
工序
符 号
内容
作业内容
分类
加工 作业
○
加工 作业
■产生附加价值的工序及作 业
卖得掉
检查
□
数量检查 ■虽然有必要,但需要进行 品质检查 改善的工序及作业
现场IE改善案例分析--生 产线平衡分析改善案例
2020年7月14日星期二
内容安排
一、线平衡定义 二、生产线平衡分析方法 三、B值、F值的定义与计算 四、线平衡案例分析
一、线平衡定义
生产线平衡定义
什么是生产线平衡
生产线平衡是指构成生产线各道工序所需的 时间处于平衡状态,作业人员的作业时间尽 可能的保持一致,从而消除各道工序间的时 间浪费,进而取得生产线平衡。
减少人手(1)
將工序3里的工作时 间分配至工序2﹑4 及5之內﹐从而工序 3里的人手可调配其 它生产线去
可行性﹕須工序 2﹐4及5內均有足夠 时间接受额外工作。
ቤተ መጻሕፍቲ ባይዱ
生产线平衡-例3﹕减少人手(2人)
降低线体速度,减少生产产量
工作時間
现场IE知识
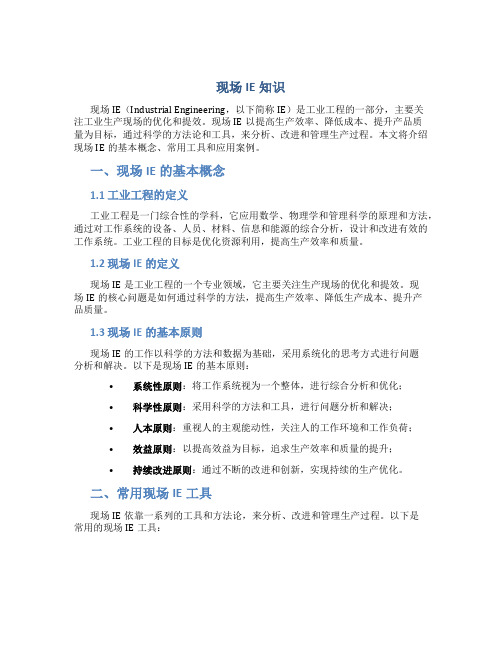
现场IE知识现场IE(Industrial Engineering,以下简称IE)是工业工程的一部分,主要关注工业生产现场的优化和提效。
现场IE以提高生产效率、降低成本、提升产品质量为目标,通过科学的方法论和工具,来分析、改进和管理生产过程。
本文将介绍现场IE的基本概念、常用工具和应用案例。
一、现场IE的基本概念1.1 工业工程的定义工业工程是一门综合性的学科,它应用数学、物理学和管理科学的原理和方法,通过对工作系统的设备、人员、材料、信息和能源的综合分析,设计和改进有效的工作系统。
工业工程的目标是优化资源利用,提高生产效率和质量。
1.2 现场IE的定义现场IE是工业工程的一个专业领域,它主要关注生产现场的优化和提效。
现场IE的核心问题是如何通过科学的方法,提高生产效率、降低生产成本、提升产品质量。
1.3 现场IE的基本原则现场IE的工作以科学的方法和数据为基础,采用系统化的思考方式进行问题分析和解决。
以下是现场IE的基本原则:•系统性原则:将工作系统视为一个整体,进行综合分析和优化;•科学性原则:采用科学的方法和工具,进行问题分析和解决;•人本原则:重视人的主观能动性,关注人的工作环境和工作负荷;•效益原则:以提高效益为目标,追求生产效率和质量的提升;•持续改进原则:通过不断的改进和创新,实现持续的生产优化。
二、常用现场IE工具现场IE依靠一系列的工具和方法论,来分析、改进和管理生产过程。
以下是常用的现场IE工具:2.1 工作测量工作测量是现场IE的基础工具之一,它主要用于衡量工作的时间和劳动强度。
常见的工作测量方法有时间测量和运动研究法,这些方法能够帮助IE工程师识别生产过程中的瓶颈和改进机会。
2.2 生产布局生产布局是指不同设备和资源之间的空间安排。
合理的生产布局能够缩短物料和信息的传递路径,减少物料和信息的流动时间,提高生产效率。
常见的生产布局方法有流水线布局、U型布局和细胞制造布局等。
ie工程现场改善方案

ie工程现场改善方案一、引言:随着工程行业的发展,越来越多的企业开始关注工程现场的改善问题。
IE工程作为一种管理和优化工程现场生产的方法,不仅可以提高生产效率,降低成本,还可以改善工作环境,提升员工工作满意度。
本文将以某工程现场为例,提出IE工程现场改善方案,以期为类似的工程现场提供参考。
二、现状分析:某工程现场是一家制造企业的生产基地,主要生产零部件和组件。
然而,该工程现场存在一些问题,例如生产效率低,物料管理混乱,工艺流程不够合理,员工工作负荷过重,工作环境较差等。
这些问题不仅影响了企业的生产和经营,也影响了员工的工作体验和生活质量。
因此,为了解决这些问题,需要对工程现场进行改善。
三、IE工程现场改善方案:1. 进行价值流分析:通过价值流分析,了解生产流程的瓶颈和浪费,找到生产效率低下的原因。
针对分析结果,制定相应的改善计划,优化生产流程。
2. 实施5S管理:建立起规范的物料管理和生产环境,包括整理、整顿、清扫、清洁、素养。
通过5S管理,提高现场的整体效率和安全性。
3. 设计并实施标准化作业程序:为每个工序制定标准化的作业程序,规范生产操作。
通过标准化作业程序,提高生产质量和效率。
4. 应用作业分析技术:通过作业分析,评估员工的工作强度和负荷,合理安排员工的工作任务,避免过重的工作负荷。
5. 实施人机工程学改善:对工作环境进行改善,包括工作高度、工作台面、照明等,提高员工的舒适度和安全性。
6. 建立绩效评价体系:建立合理的绩效评价体系,鼓励员工参与工程现场改善工作,激发员工的工作动力和创造力。
7. 进行员工培训:针对工程现场的改善方案,对员工进行相关的培训,提高员工的技能和素质,增强员工的工程现场管理意识。
8. 建立改善持续改进机制:建立持续改进的机制,定期对工程现场进行检查和评估,及时发现和解决问题,保持工程现场的良好状态。
四、改善效果评估:通过实施上述的IE工程现场改善方案,预计可以取得以下改善效果:1. 生产效率提高:通过价值流分析和优化生产流程,提高生产效率,减少浪费。
IE工艺流程现场改善

IE工艺流程现场改善IE(Industrial Engineering)工艺流程的现场改善是指通过分析、优化和改善生产流程,提高生产效率和质量,并减少资源浪费和成本的过程。
下面是一个1200字以上的IE工艺流程现场改善的详细说明。
一、背景介绍随着经济的发展和竞争的加剧,生产企业迫切需要提高生产效率和质量,以降低成本并提升竞争力。
IE工艺流程现场改善是一个重要的手段,通过对工艺流程的分析、优化和改善,可以实现生产效率和质量的提升。
二、IE工艺流程现场改善的目标1.提高生产效率:通过分析生产流程,优化工艺环节,减少工作时间和非价值增加时间,提高生产效率。
2.提高质量:通过控制和优化生产流程,减少产品次品率和不良品率,提高产品质量。
3.减少资源浪费:通过优化生产流程,减少不必要的等待时间和运输时间,降低能源和原材料的浪费。
4.降低成本:通过优化生产流程,减少生产时间和不良品率,降低人力和设备成本。
三、IE工艺流程现场改善的步骤1.数据收集:收集和整理与工艺流程相关的数据,包括生产时间、生产工艺、产品质量等。
2.工艺分析:对工艺流程进行详细的分析,理解每一个环节的工作内容和操作步骤,确定工艺流程中存在的问题和瓶颈。
3.优化方案设计:根据工艺分析的结果,设计合理的优化方案,包括减少非价值增加时间、改进工作方法和工具、优化生产顺序等。
4.实施改善方案:根据优化方案,对工艺流程进行改善实施。
可能涉及到更新设备、调整工作流程、培训操作人员等。
5.数据分析:对改善后的工艺流程进行数据分析,比较改善前后的生产效率和质量,并评估改善效果。
6.持续改进:根据数据分析的结果,不断优化工艺流程,实现持续改进。
四、IE工艺流程现场改善的应用案例以家汽车生产企业的焊接工艺流程为例,进行IE工艺流程现场改善:1.数据收集:收集焊接工艺流程的相关数据,包括焊接时间、焊缝质量、焊接设备使用率等。
2.工艺分析:分析焊接工艺流程,发现存在焊接时间过长、焊接设备闲置率高、焊缝质量不稳定等问题。
现场改善IE案例
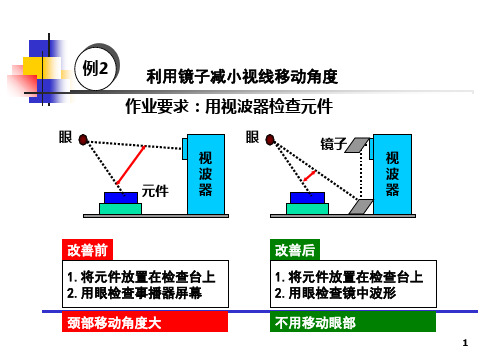
例17
辅助工具的应用
镊子
薄小零件
薄小零件
波纹板
改善前 用镊子把薄小零件夹起来 薄小零件易滑动
改善后 把薄小零件放在波纹板上
零件相对固定,夹取容易
17
例18
固定夹具 需长时间固定对象物时,可利用固定夹具
改善前
左手拿起螺栓, 右手将螺母拧上
改善后
左右手同时进行下述动作: 将螺栓放在固定夹具上, 再将螺母拧上
改善后 零件有序、对称放置, 双手同时、按顺序工作
12
例13
尽量缩小作业区域
传送带 工件 作业台
人
传送带 工件
人
★良好的照明有助于提高作业效率 ★适当的通风、正常的温度和湿度可以减轻疲劳 ★加强清扫和整理、合适的工作服可以避免工伤
13
例14
容器和器具
方形箱子
漏斗状/托盘状箱子
、、、、、、、、、
零件 过滤网 脏屑
9
例10
工具
改变材料和工具的存放状态
弹
夹
簧
工件
改善前
改善后
工具未固定
工具固定
取放距离不定
便于作业
10
例11பைடு நூலகம்作业场所的钳子放置
钳子
改善前 钳子放在桌子上, 拿起后要在手里倒一下
握法要调整
改善后 钳子放在漏斗状支架中
免去握法调整
11
例12 零件左右对称布置,便于双手作业
改善前
零件放置杂乱, 随即选择零件进行组装
14
例15
漏斗形容器的利用
加压
轴套 方形容器
改善前 从箱子中取轴套, 移动距离长,不好拿
漏斗形容器出口
现场改善及ie手法

THANK YOU
感谢聆听
时间研究
通过观察和测量作业人员完成某项任务所需的时间,制定合理的时 间标准。
作业标准化
将最优的作业方法和流程标准化,确保所有作业人员都能按照统一 的标准进行操作,提高生产效率和产品质量。
标准作业程序(SOP)制定
编写详细的标准作业程序,明确每一步骤的操作规范和要求,为作 业人员提供明确的指导。
生产线平衡与布局优化
运用各种计划和控制手段,确 保生产系统按照预定目标高效 运行。
IE手法在现场改善中的应用
流程优化
通过分析和改进工作流程,消除浪费、提高效率 。例如,减少不必要的操作步骤、简化工作流程 等。
设备改善
对生产设备进行改进和优化,提高设备效率和可 靠性。例如,采用自动化设备、改进设备维护计 划等。
物料管理
意义
现场改善是企业提高竞争力、实现可持续发展的重要手段之一。 通过现场改善,企业可以不断提高产品质量、降低生产成本、提 高生产效率、增强员工士气,从而赢得更多的市场份额和客户信 任。
现场改善的目标与原则
目标
现场改善的主要目标是提高生产效率、降低生 产成本、提高产品质量、增强员工士气等,以
实现企业的整体经营目标。
现场改善及IE手法
目
CONTENCT
录Hale Waihona Puke • 现场改善概述 • IE手法简介 • 现场改善的步骤与方法 • IE手法在现场改善中的具体应用 • 现场改善的实践案例 • 现场改善的挑战与对策
01
现场改善概述
现场改善的定义与意义
定义
现场改善是一种通过优化工作流程、提高工作效率和质量、降低 成本等方法,对生产现场进行持续改进的管理方法。
IE现场改善专案报告

2015年10月 2015年11月 2015年12月
李自岳/ 刘庆鹤
付国华/ 张文雅
计划 执行
2016年1月
付国华
IE
计划 执行
李自岳/ 刘庆鹤
赵永强
计划 执行
李自岳/ 刘庆鹤
赵永强
计划 执行
李自岳/ 刘庆鹤
赵永强
计划 执行
李自岳/ 刘庆鹤
赵永强
计划 执行
李自岳/ 刘庆鹤
赵永强
计划 执行
李自岳/ 刘庆鹤
一.成立背景及课题选定
1.2 课题选定之订单分析
根据10月份产能分析得,该型号订单量占公司总订订量的34.8%。
二.改善计划及目标设定
2.1 改善计划
内容
冲压A903车间LAYOUT布置
效果确认
A903改善48米流水线作业 改为30米作业(41人)
流程改善(山积表/平衡率 /IE七大手法)
A903改善(41人改为36 人,产能不变)
TT:22.4s
12
12
8
2 2
TT:19s
五.效果确认
5.1 各项指标数
41人
生
产
人
36人 数
:
减
少
改善前
改善后
5
人
400
350
面
300 200
220
积 :
减
100
少
13
0
0
改善前 改善后 M²
生 产 人 数 : 减 少 5 人
流 水 60
线 50
长 40
度 30
: 20
减 少
18
10 0
米
48米 改善前
IE工业工程改善案例

生产实习目的1.通过实习了解工业工程领域的知识的应用背景。
2.深入了解企业中工业工程各种基本知识和原理的实际应用情况,巩固和加深对知识的理解,并加以整合,提高综合分析问题和解决问题的能力。
3.了解实习企业的生产管理的基本情况,发现存在的问题并提出解决方案。
4.掌握提案改善的一般流程及具体做法,在团队中(或个人)如何完成一个提案从提出到发表的全流程,为毕业后的实操奠定坚实基础。
5.学习企业管理人员,工程技术人员对企业的高度责任感,对工作尽职尽责,勇于改革,不断进取创新的奉献精神。
实习任务从数据统计得出的各类产品装配各工件装配 SPT ,及拉平衡状况分析表,及原因分析与改善建议。
装配部部门简介装配部,作为车模生产的最后一道工序,肩负着车模成品的组装和包装的全部生产过程。
装配部现有六条生产线和一条样办组装线。
常用的设备有:钻床,电批,手啤机,风批,烙铁,高周波,封口机等。
为了更好的完成各种的生产任务,装配部引入了精益生产工艺流程。
精益生产是目前工业界公认最佳的一种生产组织体系和方式。
通过合理的排拉,达到合理生产,提高效率和质量的目的。
例子一:DCP1/25 货车,按流程标准可分成:车身半品( 10人),车身组合(16人),内座组合(4人),车底组合(11人),成品组装(7人)和包装(9人)共六个小组(57人)来完成。
每个小组会有一次或以上的自检。
例子二:YTB002 1/42莱茵之星单层客车按流程标准可分成:内座组装(12人),车底组装(9人),车身组装(20人),成品包装(6人)共四个小组(47人)来完成,在其中也加入了多少的自检。
装配车间平面分布图装配生产线平衡改善过程 了解产品组装工艺 对U 型拉进行工时测定,得到统计数据 从统计数据分析U 型拉平衡状况 识别瓶颈工位,找出不平衡的原因 运用平衡改善法则(ECRS 法则)、动作经济原则等方法制定改善方案 将改善方案告知组长或装配主任,实施现场改善 改善效果分析总结平衡改善法则-ECRS 法则简介 符号 名称说明E 取消Eliminate 对于不合理、多余的动作或工位给予取消 C 合并Comebine 对于无法取消又是必要的,看是否可以合并以达到省时、简化的目的 R重排Rearrange 经过取消、合并后,可再根据“何人”“何时”“何处”三个提问后进行重排S简化Simplify 经过取消、合并、重排后的必要工位,应考虑能否采用最简单的方法或设备替代,以节省人力和时间以上ECRS法则,具体可通过下列图片来说明生产中如何运用改善:装配线平衡典型案例数据统计时间:2012/8/2-2012/8/3 U拉序号:U24、U25产品编号:53072(太空车)组装部分:成品和包装改善方案提出时间:2012/8/2改善方案实施时间:2012/8/3改善前各工位组装工艺工位序号 组装工艺SPT(秒)人数设备1 双花轴装进轮子*2,再用啤机压紧 9.5 1 手啤机2 再装入太同车下壳,再用压紧轮子*2 11 1 手啤机3 太空车上壳+太空车下壳组件 6 14 太空车身打螺丝13 1 电动批5 太空车上壳表面粘贴蓝色标签1 8 16 太空车上壳表面粘贴蓝色标签2 8 17 太空车上壳表面粘贴蓝色标签3 8 18 太空车半品装太空车雷达 6 1 抹布9 清洁位,车身抹洗面水 9 1 抹布10 检查位,擦拭车身 10 111 太空车成品装进胶袋 6 112 胶袋粘透明胶纸,并最终装进外箱8 1此款产品的装配线由U25、U24两个U型拉组成,工位分布如下图所示:平衡率=各工序的作业时间/(瓶颈工位时间*人数)=(9.5+11+6+13+8+8+8+6+9+10+6+8)/(13*12)=65.71%平衡损失率=1-平衡率=34.29%改善前装配线工位平衡图改善措施从统计数据分析这条装配线,可以发现瓶颈工位是工位4。
精选现场IE改善案例分析

扑克牌游戏规则
1、每个分厂安排4个人(厂长、工艺、作业长、班长) 2、小组内部自己安排4个人的工作 3、要求是将52张扑克牌按同一花色、从大到小的排成一排 4、时间最少的小组获胜 5、开始和结束计时以固定的人员手敲桌子为准 6、游戏开始由工作人员将牌洗好
评分标准
1.2.3.4名分别100.80.60.40分错 一张牌,扣10分
电装7人线标准工时
请 计 算 平 衡 率
6、生产线平衡分析的方法
1、确定对象与范围 2、用作业分析把握现状 3、测定各工程的净时间 4、制作速度图标 5、计算平衡 6、分析结果,制定改善方 案
7、改善瓶颈岗位
(1)改善的4大原则
1)减少动作次数 2)同时使用双手 3)缩短移动距离 4)使动作变得轻松
4、工时测定分析(蓝色为作业的时间红色为失去平
衡的时间)
5、生产线平衡的计算
生产平衡率(%)=各工程净时间总计/(时间最长工程*人 员数)*100%
如上图表中,生产线平衡率=1505/(90*19)*100%=88% 不平衡率%=100%-平衡率(%) 对生产线来说,不平衡率越小越好,一般控制5%-13%之间,
(2)IE动作改善的4原则:
• ECRS原则 1.Eliminate —取消 2、Combine —合并 3、Rearrange —重排 4、Simplify —简化
(3)ECRS法运用图示简介
生产线平衡—例1:缩短生产节拍
提升生产速度,维持人手不变
缩短生产节拍 将工序2里一部 分可抽离的时间 转至3工序里, 以缩短整体的生 产节拍
至少要控制在15%以下
• 请大家观看电子分厂电装3人柔性线视频
1、一边看一边测试,最后计算平衡率 2、计算一下线小时理论产量 3、提出提升线平衡的思路方法
《IE现场优化改善》课件

未来企业应进一步拓展IE现场优化改 善的领域,加强与其他管理方法的融 合,实现更高效、更灵活、更智能的 生产模式。
谢谢观看
《IE现场优化改善》PPT课件
目录
• IE现场优化改善概述 • IE现场优化改善方法 • IE现场优化改善案例分析 • IE现场优化改善的未来发展 • 结论与建议
01
IE现场优化改善概述
定义与目标
定义
IE现场优化改善是一种通过系统地分析和改进生产现场的布局、操作流程、设 备及工装夹具等,以提高生产效率、降低成本、提升质量的管理方法。
费,提升产品质量和客户满意度。
动作分析
01
动作分析的定义
通过对作业过程中动作的分析和研究,寻找最优的动作方法和顺序。
02
动作分析的工具
动素分析、动作经济原则。
03
动作分析在IE现场优化中的应用
通过动作分析,消除多余和无效的动作,提高作业效率和生产线的平衡
,降低成本和浪费,提升产品质量和客户满意度。
制定标准、宣传培训、执行落实、检查考 核、持续改进。
通过5S管理,优化现场布局,提高作业效 率和生产线的平衡,减少浪费和不良品, 保障员工安全和健康。
流程优化
流程优化的定义
对现有流程进行分析、改进和优化,提高流程效率和效果。
流程优化的原则
明确目标、关注瓶颈、整体优化、持续改进。
流程优化的方法
流程图绘制、流程分析、流程改进、流程再造。
时间研究
时间研究的定义
通过对作业过程中所需时间的分析和研究,制定标准作业时间。
时间研究的工具
时间测量表、工作抽样。
时间研究在IE现场优化中的应用
通过时间研究,制定合理的生产计划和排程,提高生产效率和产能,降低成本和浪费,提 升产品质量和客户满意度。
电子厂IE改善案例分享
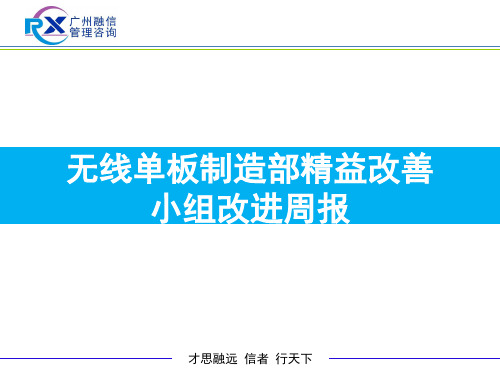
才思融远 信者 行天下
项目背景概要
课题:无线双密度模块全流程一个流 目标: 1、双密度模块综合直通率提升46%,由88%提升到93.5%; 2、双密度模块综合加工周期降低63%,由13.5天降低到5天; 3、模块产出能力由400块/天提升到600块/天,提升50%。
直通率改善目标 94% 92% 90% 88% 86% 84% 现状 目标 88% 93.50%
天 15 10 5 0
加工周期改善目标
13.5
5
现状
目标
才思融远 信者 行天下
无线双密度价值流程图(现状)
Question(问题点) 1、单板用原材料的物流现状:自动物流中心-生产中心二级库-电装生产现场 2、模块/整机用原材料的物流现状:自动物流中心-生产中心二级库-生产现场 3、单板发料周期长 4、发料及备料环节等待时间长 5、SMT工序不能分开备料,双面加工机时长焊接不能跟线一个流运作 6、插件与SMT工序CT相差大,中间存在堆板,不能做到一个流 7、装配工位贴条码,中间转运距离长,且批量作业等待时间长 8、单板FT环节无标准作业,堆板严重,在制量大
才思融远 信者 行天下
内容提要
改善目标 本周完成的主要改善工作 改善前后对比 存在的主要问题 下一步工作思路及计划
才思融远 信者 行天下
本周完成的主要改善工作
• •
1、GM52DPAU产能提升; 2、 DTRU操作质量问题改善;
•
• •
3、 CDMA2000送检周期缩短;
4、软件加工车间加工周期改善; 5、无线ICT TS设备产出率提升项目;
改 善 后(After)
问题点.着眼点(problem) :补焊第一工位需去除辅助边及 锉平毛刺
【精益教材】第2节:现场改善IE七大手法(下)
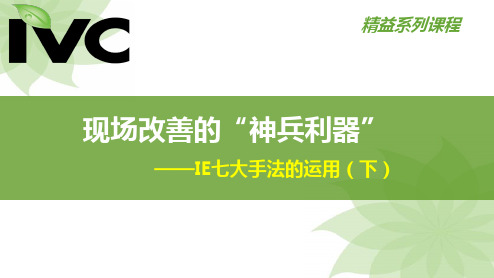
现场改善的“神兵利器”
——IE七大手法的运用(下)
上节课程回顾
1、IE七大手法是什么?七大手法口诀? 答:“走(流)动的五个人抽双防烟” 流程法、动改法、五五法、人机法、抽查法、双手法、防呆法
2、防呆法的十大原则是什么?举例说明。 答:断根—隔离—警告—保险—相符—缓和—层别—
顺序—自动—复制。
流程程序图的分类
2、人型流程程序图
它是以人为研究对象,对他/她完成所有 工序的整个过程进行记录分析。
案例(发料):
工作内容:仓库发料员发料 开始:发料员坐在工作台旁 结束:发料员发完料坐到工作台旁
流程法的分析技巧
1个不忘:动作经济原则 4大原则:ECRS(取消、合并、重排、简化) 5个方面:加工、搬运、储存、检验、等待 5W1H技术:What/Where/When/Who/Why/How 6大步骤:选择、记录、分析、建立、实施、维护
案例:对制粒某机器作业率进行观测,估计该机器停机率为25%,需要观测
精度的绝对误差为0.01,可靠度为95%,求需观测的次数。(查表得正态分 布下的Z值为1.96)
答﹕P=0.25, 1-P=0.75, Z=1.96, E=0.01 由公式, n=P(1-P)Z2/E2 =0.25X0.75X1.962/0.012 =7203次
95.45%的可靠度,就是说实现预定 的抽样资料中有95.45%以上落入2 σ 的范围,仅有4.55%的误差。
抽查法的步骤
正态分布曲线
[P(1 P )] n
P-观测时间发生率 n-观测次数
抽查法的步骤
2、绝对精度和相对精度
使用抽查法时,会存在误差,所允许的误差用精确度来衡量。 精确度又分为绝对精确度E和相对精确度S
ie工程现场改善方案

IE工程现场改善方案背景为了提高生产工艺的效率以及质量,IE工程师在现场经常需要进行改善工作,包括但不限于:•流程简化•设备优化•人力调配•物料管控然而,在实际实施改善计划时,IE工程师经常会遇到各种问题和挑战,例如:•各部门间合作不充分,难以落实具体的改善计划•质量不稳定,改善后效果难以持续•信息化程度不够,难以获取有效的数据支持决策因此,我们需要一套完整的IE工程现场改善方案,以应对上述问题和挑战。
方案策略规划首先,我们需要制定一份长远的IE工程改善规划,以确保改善工作能够落地并且取得长期效果。
具体而言,我们需要:•分析现有工艺和流程,并确定潜在的改善点•制定改善目标,确定改善计划的具体方向和重点•制定改善计划的时间表,并确定各阶段的关键节点•确定改善计划所需的资源,包括人力、物力、财力等•构建长期的改善监测机制,以确保改善效果能够持续并得到反馈团队建设IE工程师需要与各部门紧密合作,共同落实改善计划。
因此,我们需要构建一个高效的改善团队,以提高协作效率和决策质量。
具体而言:•确定改善团队的组成和角色分配•建立团队的工作流程和协作机制,包括但不限于会议、报告、工作安排等•建立改善团队的绩效考核体系•为团队成员提供专业培训和技能提升机会,以保证团队的知识和能力的提升改善实施改善实施是IE工程的核心工作之一。
我们需要有系统的方法来确保改善工作能够取得实质性的效果。
具体而言:•确定改善点,并制定具体的改善方案•确定改善所需的资源,并进行预算和计划•制定有效的实施计划和时间表,并做好实施前的准备工作,包括但不限于游程活动、人员调配、设备安排等•推动实施,确保改善方案能够落地并取得实际效果•建立改善监测体系,并及时收集、分析和反馈改善成效,以便为后续的调整和改进提供依据信息化支持信息化支持是现代IE工程的重要组成部分。
我们需要建立起完善的信息化平台,以支持IE工程师的工作和决策。
具体而言:•建立数据收集和分析平台,以支持IE工程师进行改善分析和决策•建立项目管理平台,以支持项目的治理、监测和分析•建立交流平台,以支持改善团队之间的互动和协作•建立知识库和培训平台,以支持IE工程师的培训和技能提升结论IE工程现场改善方案是一个系统性的工作,需要涉及到规划、团队建设、实施和信息化支持等多个方面。
工业工程(IE)现场改善方法_图文(精)

3、用以比较改善前及改善后之差异情形
基本符号和应用符号
①加工:表示直接改变制品的物理和化学性质或处于分解装配中。
A35第五道加工工序
A制品的第3道加工工序
以加工为主,同时检验
直径3/8吋
②搬运:表示材料从一处移到另一处。
或
③检验:进行数量或质量的检验。表示数量检验表示质量检验表示数量和质量同时检验,以质量检验为主
•在纸上采用适当的间隔分开人与机,作出垂线。最左方为工人操作时的动作单元及垂线,在此垂线上按所取的时间比例,由上向下记录工人每一动作单元所需时间。当工人操作时用实线(或其它方式表示,空闲用虚线(或其它方法表示,机器同样。•待人与机器的操作时间均已记录之后,在此图的下端将工人与机器的操作时间、空闲时间及每周期人工时数予以统计,供分析时参考。
联合作业分析研究对象:两个或两个以上操作者所进行的分析联合作业分析研究目的:发掘空闲与等待时间,使工作平衡,減少周期時間,获得最大的机器利用率。
联合作业分析研究工具:联合作业图
联合作业图的构成:表头、图表、统计。示例
联合作业图的特点:机器的作业情况画在图表的最左栏
操作者的作业情况画在图表的右栏
利用联合作业图分析的基本原则:
工作A工作A工作A
工作B
工作B
工作B
4h4h
4h
3h
3h
3h 1h
等待
8h 7h
使各个对象的工作进度协调,取消空闲和等待时间,缩短周期。
结论:
1消除工作中的等待,可以有效的缩短工作的周期时间
2如果有多项工作,则同时开展工作,周期时间最短
人机操作图的构成
•以适当的线段的长短代表时间比例。
改善案例(八大浪费)

制造过多/过早
浪
费
制造过多/过早造成浪费: ☆ 造成在库 ☆ 计划外/提早消耗 ☆ 有变成滞留在库的风险 ☆ 降低应对变化的能力
浪
费
多余动作 增加强度降低效率
常见的12种浪费动作: ① 两手空闲 ② 单手空闲 ③ 作业动作停止 ④ 动作幅度过大 ⑤ 左右手交换 ⑥ 步行多
动作
⑦ 转身角度大 ⑧ 移动中变换动作 ⑨ 未掌握作业技巧 ⑩ 伸背动作 ⑾ 弯腰动作 ⑿ 重复/不必要动作
啟動開關獨立地防止地面易
01
備碰﹑觸發生工業安全﹐且
02
人須彎腰按動開關易疲勞
03
將啟動開關定置在控制面板上
04
保障安全且人不須彎腰按動開
05
關動作經濟化
06
IE手法三﹕防呆法
01
手動固定工件產生品質無
03
利用治具定位精度准﹐品質
02
保障﹑精度不准
04
高﹐效率得到提升
IE手法三﹕防呆法
01
準確掌握生產活動的實際狀態﹔ 盡快地發現浪費﹑不合理﹑不可靠的地方﹔ 對生產活動的改善和標準化進行系統的管理﹒
02
從來沒有這樣做過; 人家已經用過了不行; 這個方法已經用了10年; 我們現在已經做的夠好; 這個方法不適合我們; 老板不會感興趣﹔ 他們都說不可能﹔
4.現場IE活動的21種抵抗情緒(1)
個個方法行不通﹔ 沒有預算﹔ 那是件遙遠的事情﹔ 這事情超過我們的權限﹔ 不是我的工作﹔ 沒有時間﹔ 客戶不會接受﹔
《IE现场优化改善》课件
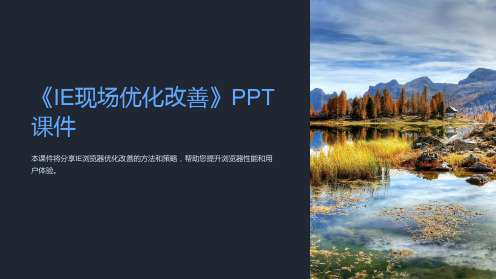
本课件将分享IE浏览器优化改善的方法和策略,帮助您提升浏览器性能和用 户体验。
IE浏览器性能瓶颈分析
缓慢的页面加载速度
分析可能的原因,如网络连接、脚本问题等,提 供解决方案。
响应时间过长的问题
介绍如何从前端和后端两个方面进行优化,以减 少响应时间。
高CPU和内存占用
提供禁用Windows错误报 告的方法,以减少对浏览 器性能的影响。
3 可行性和风险
讨论禁用Windows错误报 告的可行性和相关风险, 以供用户做出决策。
升级IE版本提升性能
1 最新版本的优势
说明升级IE的好处,包括性能改进、安全性增强和新功能。
2 平滑升级策略
提供平滑升级IE的策略,以避免因升级而引起的兼容性问题。
3 应用兼容性测试
介绍如何进行应用兼容性测试,以确保升级后的IE能够正常运行。
启用GPU加速
什么是GPU加速?
解释GPU加速的概念和原理, 以及如何启用GPU加速来提升 浏览器性能。
3
管理插件更新
建议定期检查插件更新,并清除不需要 的旧版本插件。
禁用兼容性视图
什么是兼容性视图? 为什么要禁用? 禁用兼容性视图的方法
解释兼容性视图的作用和影响,并提供禁用方法。
描述禁用兼容性视图的好处,包括提高网页显示 的准确性和性能。 指导用户如何在IE浏览器中禁用兼容性视图。
优化IE设置
Internet选项
探讨导致浏览器资源消耗过高的因素,并给出优 化建议。
闪烁和卡顿的界面
讨论界面闪烁和卡顿的原因,提供解决方案来改 善用户体验。
IE缓存及过期机制
浏览器缓存
解释浏览器缓存的基本原理和使 用建议,以加速页面加载。
IE改善案例之一如何解决生产线堆积(doc 15页).
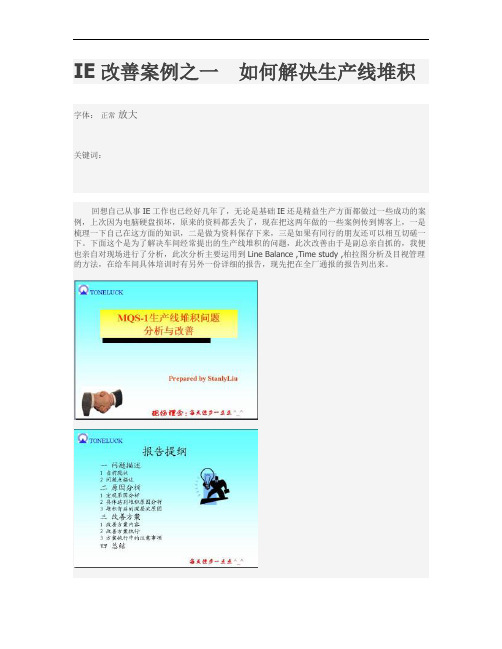
IE改善案例之一如何解决生产线堆积字体:正常放大
关键词:
回想自己从事IE工作也已经好几年了,无论是基础IE还是精益生产方面都做过一些成功的案例,上次因为电脑硬盘损坏,原来的资料都丢失了,现在把这两年做的一些案例传到博客上,一是梳理一下自己在这方面的知识,二是做为资料保存下来,三是如果有同行的朋友还可以相互切磋一下。
下面这个是为了解决车间经常提出的生产线堆积的问题,此次改善由于是副总亲自抓的,我便也亲自对现场进行了分析,此次分析主要运用到Line Balance ,Time study ,柏拉图分析及目视管理的方法,在给车间具体培训时有另外一份详细的报告,现先把在全厂通报的报告列出来。
- 1、下载文档前请自行甄别文档内容的完整性,平台不提供额外的编辑、内容补充、找答案等附加服务。
- 2、"仅部分预览"的文档,不可在线预览部分如存在完整性等问题,可反馈申请退款(可完整预览的文档不适用该条件!)。
- 3、如文档侵犯您的权益,请联系客服反馈,我们会尽快为您处理(人工客服工作时间:9:00-18:30)。
例8
使用身体最佳部位
手的移动
手指→手→前臂→上臂
→肩→躯干→腰部
使作业位置高度达到最佳状态: ★坐在椅子上,前臂水平伸出时
——高度约60cm
★臂肘防灾作业台上,眼睛平视 进行组装零部件,作业者不弯 腰——高度约85cm
●缩短手臂的移动距离 ●尽可能不动全臂 ●只做凭前臂、手腕或手指即 可完成的动作 ●尽可能将零件、工具放在手 够得着的近处 ●减少屈身、弯腰等躯干动作
13
例13
传送带 工件 作业台
尽量缩小作业区域
传送带 工件
人 人
★良好的照明有助于提高作业效率
★适当的通风、正常的温度和湿度可以减轻疲劳
★加强清扫和整理、合适的工作服可以避免工伤
14
例14
容器和器具
方形箱子
漏斗状/托盘状箱子
零件 过滤网 、、、、、、、、、
脏屑
15
例15
加压
漏斗形容器的利用
轴套
方形容器
漏斗形容器出口
改善前 从箱子中取轴套, 改善后 从漏斗形容器出口取轴套 取用方便
16
移动距离长,不好拿
例16
辅助工具的应用
小零件 手指
小零件
作业台
海绵垫 改善后 小零件放在海绵垫上 取用更容易
改善前 小零件放在作业台上, 用指尖拿起来 取用时小零件易滑掉
★工具、设备的把手做成易握、易抓的形状
8
例8 眼睛的移动 眼睛→颈部→躯干 ●尽可能将零件、工具 放在看得见的近处
9
例9
减小移动距离 作业要求:将盖板固定在产品上
传送带
产品 人 改善前 盖板放在一边, 取到盖板后固定在产品上 手移动40cm 改善后 盖板放在传送带上, 取到盖板后固定在产品上 手移动15cm
10
人
例10
工具
改变材料和工具的存放状态
例1
将工具固定减少动作数量
元件 焊料 基板
作业要求:
将元件焊在基板上
电烙铁
改善前
改善后
左手 右手 1.取材料 (等待) 2.拿焊料 拿电烙铁 3.焊接 4.放焊料 放电烙铁 5.材料入箱 (等待)
每次都要取放电烙铁
左手 右手 1.取材料 拿焊料 2.焊接 3.材料入箱 拿焊料
将电烙铁固定在工作台前
1
例6
双手同时反向和对称移动
非协调性动作 协调性动作
左手 右手 左手 右手
左手
左手
右手
左手
右手
材料工具不对称,肩部或躯干要移动, 易失去平衡,易疲劳
容易做到
不能做到
能,但不协调
6
例7
使用双手可同时完成动作的夹具
改善前 左手拿垫圈, 右手握夹使之弯折90°
改善后 双手将垫圈插入专用夹具, 用手指使之弯折90° 双手协调动作
合 格
改善前 分别在两处盖章
改善后 只要盖1次章
动作多,盖章位置难确定
动作少,盖章位置易确定
3
例4
双手同时作业
小零件
小零件
固定作业
改善前 左手拿零件 右手将零件固定 单手作业
改善后 左手拿零件并将之固定 右手同时进行相同作业 对称作业
4
例5
双手同时作业
改善前 一件一件地检查
改善后 一次检查两件
5
例2
利用镜子减小视线移动角度 作业要求:用视波器检查元件
眼 视 波 器
眼
镜子
元件
视 波 器
改善前 1.将元件放置在检查台上 2.用眼检查事播器屏幕
改善后 1.将元件放置在检查台上 2.用眼检查镜中波形
颈部移动角度大
不用移动眼部
2
例3
将两个以上动作合并 作业要求:盖日期印和合格印
定位
日 期
合 格
日 期
★利用夹具、导轨等限定运动路线 ★利用夹具、导轨等使定位更容易
19
例19
利用重力和其它力取送材料 利用斜槽缩短完成品搬运的距离
60cm 20cm
作业台
工件箱
其它力:磁力、气压、油压、弹力、点滴装置
20
例20
利用重力和机械力取送材料 利用斜架缩短搬运的距离
60cm
21
17
例17
辅助工具的应用
镊子 薄小零件
薄小零件
波纹板
改善前 用镊子把薄小零件夹起来 薄小零件易滑动
改善后 把薄小零件放在波纹板上 零件相对固定,夹取容易
18
例18
固定夹具
需长时间固定对象物时,可利用固定夹具
改善前
改善后 左右手同时进行下述动作: 将螺栓放在固定夹具上, 再将螺母拧上
左手拿起螺栓, 右手将螺母拧上
弹 簧
夹
工件
改善前 工具未固定
改善后 工具固定 便于作业
11
取放距离不定
例11
作业场所的钳子放置
钳子
支 架 改善前 改善后 钳子放在漏斗状支架中
钳子放在桌子上, 拿起后要在手里倒一下 握法要调整
免去握法调整
12
例12
零件左右对称布置,便于双手作业
改善前 零件放置杂乱, 随即选择零件进行组装
改善后 零件有序、对称放置, 双手同时、按顺序工作