消除残余应力的方法
金属复合材料的残余应力消除方法

金属复合材料的残余应力消除方法
1. 热处理法呀,就好像给金属复合材料来一场舒适的“温泉浴”!你想想,把它放进特定温度的环境中,让那些残余应力慢慢跑掉。
比如说汽车的零部件,经过热处理后,就能更稳定可靠啦!
2. 机械拉伸法呢,这就像是给它做个“伸展运动”。
用力拉一拉,让材料舒展一下,残余应力不就减少啦。
像那些金属板材,经常就用这种方法呢!
3. 振动时效法呀,好比给它来个持续不断的“按摩”。
通过振动让残余应力松懈下来。
就好比你累了一天,做个按摩就轻松多了,是不是?像一些大型的金属结构件就特别适合用这个方法呢!
4. 自然时效法,就像是让金属复合材料享受一段“悠闲时光”。
把它放着,慢慢等时间发挥魔力,残余应力就会渐渐消失啦!你看一些不太着急用的金属制品就会用这种哦!
5. 超声冲击法,如同给它来一场“声波洗礼”。
利用超声的力量,冲击掉残余应力。
很多精密仪器的金属部分就靠这个来保障性能呢!
6. 滚压强化法,这不就是给它来个“塑形之旅”嘛!通过滚压让材料更结实,残余应力也随之减少。
像一些轴类零件常用的就是这个办法呀!
7. 豪克能时效法,你可以理解成是给金属复合材料来一个“高级疗养”。
它能有效地消除残余应力,让材料焕发新活力。
一些高质量要求的金属制品就常用这个神奇的方法呢!
我觉得呀,这些方法都各有千秋,具体得根据实际情况来选择,才能让金属复合材料发挥出最佳性能呢!。
(完整版)残余应力产生及消除方法.

残余应力产生及消除方法船舶零件加工后,其表面层都存在残余应力。
残余压应力可提高零件表面的耐磨性和受拉应力时的疲劳强度,残余拉应力的作用正好相反。
若拉应力值超过零件材料的疲劳强度极限时,则使零件表面产生裂纹,加速零件的损坏。
引起残余应力的原因有以下三个方面: ( 一冷塑性变形引起的残余应力在切削力作用下,已加工表面受到强烈的冷塑性变形,其中以刀具后刀面对已加工表面的挤压和摩擦产生的塑性变形最为突出,此时基体金属受到影响而处于弹性变形状态。
切削力除去后,基体金属趋向恢复,但受到已产生塑性变形的表面层的限制,恢复不到原状,因而在表面层产生残余压应力。
( 二热塑性变形引起的残余应力零件加工表面在切削热作用下产生热膨胀,此时基体金属温度较低,因此表层金属产生热压应力。
当切削过程结束时,表面温度下降较快,故收缩变形大于里层,由于表层变形受到基体金属的限制,故而产生残余拉应力。
切削温度越高,热塑性变形越大,残余拉应力也越大,有时甚至产生裂纹。
磨削时产生的热塑性变形比较明显。
( 三金相组织变化引起的残余应力切削时产生的高温会引表面层的金相组织变化。
不同的金相组织有不同的密度表面层金相组织变化的结果造成了体积的变化。
表面层体积膨胀时,因为受到基体的限制,产生了压应力;反之,则产生拉应力。
总之,残余应力即消除外力或不均匀的温度场等作用后仍留在物体内的自相平衡的内应力。
机械加工和强化工艺都能引起残余应力。
如冷拉、弯曲、切削加工、滚压、喷丸、铸造、锻压、焊接和金属热处理等,不均匀塑性变形或相变都可能引起残余应力。
残余应力一般是有害的,如零件在不适当的热处理、焊接或切削加工后,残余应力会引起零件发生翘曲或扭曲变形,甚至开裂,经淬火或磨削后表面会出现裂纹。
残余应力的存在有时不会立即表现为缺陷。
当零件在工作中因工作应力与残余应力的叠加,而使总应力超过强度极限时,便出现裂纹和断裂。
零件的残余应力大部分都可通过适当的热处理消除。
消除残余应力的方法

消除残余应力的方法(金属)-—时效处理消除残余应力的方法(金属)-—时效处理金属工件(铸件、锻件、焊接件)在冷热加工过程中都会产生残余应力,残余应力值高者(单位为Pa)在屈服极限附近构件中的残余应力大多数表现出很大的有害作用;如降低构件的实际强度、降低疲劳极限,造成应力腐蚀和脆性断裂,由于残余应力的松弛,使零件产生变形,大大的影响了构件的尺寸精度。
因此降低和消除工件的残余应力就十分必要了,特别是在航空航天、船舶、铁路及工矿生产等应用的,由残余应力引起的疲劳失效更不容忽视。
目前的针对残余应力的不同处理方法有:自然时效方法和人工时效方法(包括热处理时效、敲击时效、振动时效、超声冲击时效)1、自然时效——适合:热应力(铸造锻造过程中产生的残余应力) 冷应力(机械加工过程中产生的残余应力)焊接应力(焊接过程中产生的应力)自然时效是最古老的时效方法。
它是把构件露天放置于室外,依靠大自然的力量,经过几个月至几年的风吹、日晒、雨淋和季节的温度变化,给构件多次造成反复的温度应力。
再温度应力形成的过载下,促使残余应力发生松弛而使尺寸精度获得稳定。
自然时效降低的残余应力不大,但对工件尺寸稳定性很好,原因是工件经过长时间的放置,石墨尖端及其他线缺陷尖端附近产生应力集中,发生了塑性变形,松弛了应力,同时也强化了这部分基体,于是该处的松弛刚度也提高了,增加了这部分材质的抗变形能力,自然时效降低了少量残余应力,却提高了构件的松弛刚度,对构件的尺寸稳定性较好,方法简单易行,但生产周期长。
占用场地大,不易管理,不能及时发现构件内的缺陷,已逐渐被淘汰。
2、热处理时效——适合:热应力(铸造锻造过程中产生的残余应力)冷应力(机械加工过程中产生的残余应力)焊接应力(焊接过程中产生的应力)热时效处理是传统的消除残余应力方法。
它是将构件由室温缓慢,均匀加热至550℃左右,保温4-8小时,再严格控制降温速度至150℃以下出炉.热时效工艺要求是严格的,如要求炉内温差不大于±25℃,升温速度不大于50℃/小时,降温速度不大于20℃/小时.炉内最高温度不许超过570℃,保温时间也不易过长,如果温度高于570℃,保温时间过长,会引起石墨化,构件强度降低。
残余应力的危害及消除方法

焊接残余应力对构件的危害是1、对结构刚度的影响当外载产生的应力与结构中某区域的残余应力叠加之和达到屈服点时,这一区域的材料就会产生局部塑性变形,丧失了进一步承受外载的能力,造成结构的有效截面积减小,结构的刚度也随之降低。
2、对受压杆件稳定性的影响当外载引起的压应力与残余应力中的压应力叠加之和达到屈服点口。
,这一部分截面就丧失进一步承受外载的能力。
这就削弱了构件的有效截面积,并改变了有效截面积的分布,降低了受压杆件的稳定性。
3、对静载强度的影响没有严重应力集中的焊接结构,只要材料具有一定的塑性变形能力,残余应力不影响结构的静载强度。
反之,如材料处于脆性状态,则拉伸残余应力和外载应力叠加有可能使局部区域的应力首先达到断裂强度,导致结构早期破坏。
4、对疲劳强度的影响残余应力的存在使变载荷的应力循环发生偏移。
这种偏移,只改变其平均值,不改变其幅值。
结构的疲劳强度与应力循环的特征有关,当应力循环的平均值增加时,其极限幅值就降低,反之则提高。
因此,如应力集中处存在着拉伸残余应力,疲劳强度将降低。
5、对焊件加工精度和尺寸稳定性的影响机械加工把一部分材料从焊件上切除时,此处的残余应力也被释放。
残余应力原来的平衡状态被破坏,焊件发生变形,加工精度受影响。
6、对应力腐蚀开裂的影响应力腐蚀开裂是拉伸残余应力和化学腐蚀共同作用下产生裂纹的现象,在一定材料和介质的组合下发生。
应力腐蚀开裂所需的时间与残余应力大小有关,拉伸残余应力越大,应力腐蚀开裂的时间越短。
焊接残余应力消除方法有:利用锤击焊缝区来控制焊接残余应力焊后用小锤轻敲焊缝及其邻近区域,使金属展开,能有效地减少焊接残余应力。
利用预热法来控制焊接残余应力构件本体上温差越大,焊接残余应力也越大。
焊前对构件进行预热,能减小温差和减慢冷却速度,两者均能减小焊接残余应力。
利用“加热减应区法”来控制焊接残余应力焊接时,加热那些阻碍焊接区自由伸缩的部位,使之与焊接区同时膨胀和同时收缩,就能减小焊接应力,这种方法称为“加热减应区法”,加热的部位就称之为“减应区”。
减小或消除焊接残余应力的措施
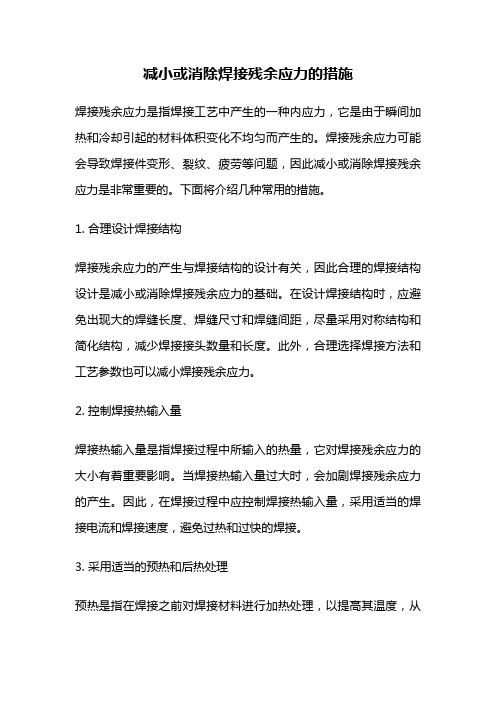
减小或消除焊接残余应力的措施焊接残余应力是指焊接工艺中产生的一种内应力,它是由于瞬间加热和冷却引起的材料体积变化不均匀而产生的。
焊接残余应力可能会导致焊接件变形、裂纹、疲劳等问题,因此减小或消除焊接残余应力是非常重要的。
下面将介绍几种常用的措施。
1. 合理设计焊接结构焊接残余应力的产生与焊接结构的设计有关,因此合理的焊接结构设计是减小或消除焊接残余应力的基础。
在设计焊接结构时,应避免出现大的焊缝长度、焊缝尺寸和焊缝间距,尽量采用对称结构和简化结构,减少焊接接头数量和长度。
此外,合理选择焊接方法和工艺参数也可以减小焊接残余应力。
2. 控制焊接热输入量焊接热输入量是指焊接过程中所输入的热量,它对焊接残余应力的大小有着重要影响。
当焊接热输入量过大时,会加剧焊接残余应力的产生。
因此,在焊接过程中应控制焊接热输入量,采用适当的焊接电流和焊接速度,避免过热和过快的焊接。
3. 采用适当的预热和后热处理预热是指在焊接之前对焊接材料进行加热处理,以提高其温度,从而减小焊接残余应力的产生。
预热可以使材料的温度均匀分布,减少焊接过程中的温度梯度,从而减小焊接残余应力。
后热处理是指在焊接完成后对焊接件进行加热或冷却处理,以消除残余应力。
预热和后热处理的温度和时间应根据具体材料和焊接工艺参数进行合理选择。
4. 采用适当的填充材料和焊接方法填充材料的选择和焊接方法的应用也对焊接残余应力的大小有着重要影响。
合适的填充材料可以改变焊接材料的熔化温度和热导率,从而减小焊接残余应力的产生。
而选择适当的焊接方法,如脉冲焊接、激光焊接等,也可以减小焊接残余应力。
5. 控制焊接过程中的冷却速率焊接过程中的冷却速率也会影响焊接残余应力的大小。
当冷却速率过快时,焊接件表面和内部的温度差异会增大,从而加剧焊接残余应力的产生。
因此,在焊接过程中应控制冷却速率,避免过快的冷却。
减小或消除焊接残余应力是焊接工艺中非常重要的一项任务。
通过合理设计焊接结构、控制焊接热输入量、采用适当的预热和后热处理、选择合适的填充材料和焊接方法,以及控制焊接过程中的冷却速率,可以有效地减小或消除焊接残余应力,提高焊接件的质量和可靠性。
消除焊接残余应力的方法

消除焊接残余应力的方法焊接是一种常见的连接方法,但往往会在焊接过程中产生焊接残余应力。
这些残余应力可以导致焊接材料的变形和裂纹,影响焊接结构的稳定性和强度。
因此,消除焊接残余应力对于确保焊接结构的质量和可靠性至关重要。
下面将介绍几种常见的消除焊接残余应力的方法:1. 预热和后焊热处理:预热是在焊接之前加热焊接材料的方法,可以提高焊接材料的可塑性,降低焊接残余应力的产生。
后焊热处理是在焊接完成后对焊接区域进行加热处理,通过退火、正火或淬火等方法,使焊接结构的组织和性能得到调整和改善,从而减少焊接残余应力。
2. 堆焊:堆焊是在焊接接头上堆积焊条或焊丝,增加焊接材料的体积并形成一定的凸起。
通过堆焊,可以使焊接区域的残余应力分布更均匀,降低焊接接头的变形和残余应力。
3. 振动消除法:振动消除法是利用机械振动的力量来消除焊接残余应力。
通过在焊接过程中施加外力或机械振动,可以改变焊接材料的晶格结构和分子排列方式,使焊接结构中的残余应力得到释放,从而达到消除焊接残余应力的目的。
4. 加工消除法:加工消除法是通过机械或热加工来消除焊接残余应力。
例如,采用热冲压、磨削、切削等方法对焊接结构进行加工,可以改变其形状和尺寸,从而减小残余应力。
5. 冷却消除法:冷却消除法是利用焊接材料的热膨胀系数差异来消除焊接残余应力。
通过在焊接过程中控制焊接材料的冷却速度,可以使焊接结构在冷却过程中产生相应的热应力,从而消除焊接残余应力。
6. 松弛应力消除法:松弛应力消除法是通过施加外力来消除焊接残余应力。
通过对焊接结构施加拉伸、压缩、扭曲等外力,可以使焊接结构的应力场重新分布,降低焊接残余应力。
在实际应用中,常常会按照实际需要,结合不同的方法来消除焊接残余应力。
同时,选择合适的焊接方法、焊接参数和焊接材料也是消除焊接残余应力的重要因素,对于提高焊接质量和可靠性具有重要的影响。
总之,消除焊接残余应力是确保焊接结构质量和可靠性的重要措施之一。
残余应力消除方法的比较
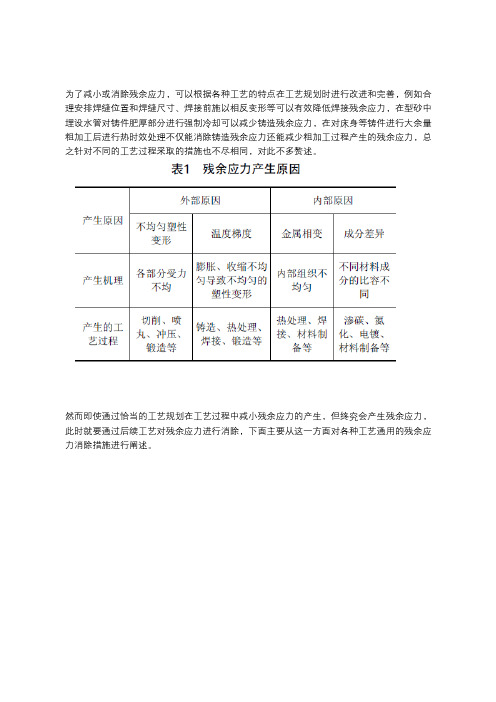
为了减小或消除残余应力,可以根据各种工艺的特点在工艺规划时进行改进和完善,例如合理安排焊缝位置和焊缝尺寸、焊接前施以相反变形等可以有效降低焊接残余应力,在型砂中埋设水管对铸件肥厚部分进行强制冷却可以减少铸造残余应力,在对床身等铸件进行大余量粗加工后进行热时效处理不仅能消除铸造残余应力还能减少粗加工过程产生的残余应力,总之针对不同的工艺过程采取的措施也不尽相同,对此不多赘述。
然而即使通过恰当的工艺规划在工艺过程中减小残余应力的产生,但终究会产生残余应力,此时就要通过后续工艺对残余应力进行消除,下面主要从这一方面对各种工艺通用的残余应力消除措施进行阐述。
采用后续工艺方法来消除或减小工艺过程中所产生的残余应力对工件的不良影响,这种消除残余应力的方法称为时效处理,包括自然时效、热时效以及振动时效。
总体来说,3种方法对于消除各种工艺过程产生的残余应力都是适用的。
自然时效是将工件长时间置于自然条件下使得残余应力释放。
由于自然时效周期长、效率低,难以适应现代生产需要。
热时效是在合适的温度下,对工件进行退火或回火处理,可以很好地起到消除残余应力的目的。
振动时效则是工件在激振器周期性的外力作用下产生共振,使工件内部发生微观变形从而均化、消除工件残余应力。
热时效处理作为传统工艺,能够很好地对工件中残余应力进行消除,并能一定程度上改善材料特性,然而,目前大多数机床制造企业已不具备大型工件热时效处理的设备和条件,导致切削加工等工序中产生的残余应力无法得到很好的消除。
经实验证明,振动时效不仅可消除残余应力,还能削除残余应力峰值、均化残余应力,从而增强零件尺寸稳定性,且工件的材料性能和疲劳寿命都有所提高。
例如,经过振动时效处理的铸件,两个月之后变形量很小,尺寸稳定所需的时间很短。
而且由于振动时效具有节能、环保、高效等特点,同自然时效和热时效相比有显著的优越性。
运用振动时效有助于企业降低成本,提高生产效率,增强产品的竞争力,同时也正是当今资源节约型、环境友好型社会所极力倡导的。
消除残余应力的方法

消除残余应力的方法消除残余应力是指在材料或结构中消除由外力引起的剩余应力,主要通过热处理方法实现。
1. 淬火和回火:淬火是将材料快速冷却到室温以下,使其形成马氏体结构,从而产生较高的表面硬度和残余应力。
回火是将材料在较低温度下加热一段时间,然后冷却,以减轻残余应力。
淬火和回火可以有效地消除大部分残余应力,提高材料的强度和韧性。
2. 热拉伸:热拉伸是通过加热材料到高温,然后进行拉伸,再冷却,以消除残余应力。
热拉伸方法可以使材料在不引起形变的情况下,通过热膨胀来消除应力。
3. 冷加工:冷加工是指通过塑性变形来改变材料的结构和性能,以消除残余应力。
冷加工可以通过压下、弯曲、拉伸、轧制等方式进行,可以有效地减轻残余应力。
4. 喷丸处理:喷丸处理是通过高速飞沙或高压水流冲击材料表面,以消除表面残余应力。
喷丸处理可以有效地改善材料的表面质量和耐蚀性,并减轻残余应力。
5. 超声波处理:超声波处理是将超声波能量传输到材料中,通过超声波的机械振动作用消除残余应力。
超声波处理可以迅速、均匀地改变材料的结构和性能,从而消除残余应力。
6. 磁性退火:磁性退火是通过在材料中施加高频电磁场,使材料的分子磁化方向改变,从而消除残余应力。
磁性退火可以在材料表面产生逆磁场,从而减轻残余应力。
7. 残余应力分析:通过应力测量、有限元分析或光学方法来分析和识别残余应力的分布和特征,从而采取相应的消除措施。
残余应力分析可以帮助确定消除残余应力的最佳方法,并指导材料或结构的设计和制备。
总之,消除残余应力的方法多种多样,可以根据具体情况选择合适的方法。
热处理、热拉伸、冷加工、喷丸处理、超声波处理、磁性退火和残余应力分析是常用的方法,可以有效地消除残余应力,提高材料或结构的性能和可靠性。
如何消除弹簧残余应力

如何消除弹簧残余应力
可用热处理(低温回火、消除应力退火、深冷急热处理)和机械的方法消除弹簧残余应力。
(1)低温退火(消除应力退火)法为了彻底除应力,必须在450Y以上加热。
但是,为了消除应力而又不过多地降低淬火弹簧的硬度,同时提高弹簧的耐磨性,则宜用150~180C的低温回火进行处理。
在100C 的温度下回火,能够消除淬火弹簧残余应力的25左右:在200℃的温度下回火,能够消除淬火弹簧残余应力的50左右:而用600~700C的温度回火。
淬火弹簧残余应力能被完全消除。
这就是消除应力退火法。
保温时间要根据弹簧的厚度确定,一般是按每25.4毫米(1英寸)零件厚度,保湿30分钟计算,冷却速度以每小时200C以下的缓幔冷却较好。
(2) 深冷急热处理法(冷处理急热法)这是消除弹簧表面弹簧残余应力(压应力)的新方法。
如果把淬火产生弹簧残余应力的弹簧进行冷处理,当冷却到一196C(液氮温度)左右后,用蒸气等喷吹,使其急热。
这种由急冷变成急热的处理,可以抵消急冷所产生的应力。
一般如果回火温度高,可用回火消除应力:如果回火温度低(450以下),最好用深冷急热法处理。
(3)喷丸硬化法采用喷丸硬化是为了消除弹簧表面的残余张应力。
因为喷丸硬化产生残余压应力可抵消表面张应力。
(4)机械振动法机械振动法是对有弹簧残余应力的弹簧施以机饿振动以消除应力的方法,其中有名的是Formula 65法。
因为机械振动与由热引起的分子运动具有同样的效果,所以能够消除应力。
这种方
法适合于消除大型弹簧的应力。
消除残余应力有哪些方法

消除残余应力的方法有哪些?残余应力对工件有很大的危害,会使工件发生变形甚至是断裂,而工件一旦发生变形就会对使用精度造成影响,所以消除残余应力就成为很重要的事情。
纵观全球相关领域,消除残余应力的方法大约有四种。
第一种就是自然时效,通过自然放置消除残余应力,这种方法耗时过长,难以适应现代科技及生产需要;第二种是最传统的方法——热时效法,把工件放进热时效炉中进行热处理,慢慢消除残余应力。
但这种方法的缺点也非常的显著,对要求非常严格的工件或者是大型工件都无法用这种方法处理,而且这种方法还带来了大量的污染和能源消耗,随着中国及世界范围内对环保的进一步要求,热时效炉的处理方式马上面临全面退出的境地。
第三种就是利用亚共振来消除残余应力,这种方法虽然解决了热时效的环保问题,但是使用起来相当烦琐。
更令人遗憾的是这种方法只能消除23%的工件应力,无法达到处理所有工件的目的。
第四种就是振动时效消除残余应力,也是聚航科技主要研究的技术之一,是通过机械组装使之形成了一整套消除应力设备,它可以使工件在短时间内达到消除应力的作用,覆盖所有需要消除应力的工件。
用频谱分析优选五个频率以多振型的处理方法达到消除工件应力的目的,所有形状大小的工件都可以使用这种设备完成,将激振器夹在工件上进行振动就可以达到消除应力的效果。
振动时效消除应力相比其他方法有着非常明显的优势,举例来说,15吨左右的热时效炉,燃料多数使用电或天然气,每天开炉一次,时效成本在3000元以上,以每年使用300天计算,仅电或天然气费用每年为90万元。
因为城市环保问题日益严重,热时效炉均远离城区,还要计算运输成本和时间成本。
以上就是消除残余应力方法介绍,如果你对振动时效消除残余应力还有其他的问题,可随时咨询聚航科技。
焊接残余变形的矫正及残余应力的消除

焊接残余变形的矫正及残余应力的消除1.焊接残余变形的矫正方法(1)机械矫正法机械矫正法是利用机械力的作用来矫正变形。
图3—136 所示为工字梁焊后的机械矫正。
低碳钢结构可在焊后直接应用此法矫正。
对于一般合金结构钢的焊接结构,焊后先行消除应力处理,才能进行机械矫正。
否则,不仅矫正困难,而且容易产生断裂。
薄板波浪变形的机械矫正应锤打焊缝区的拉应力段。
因为拉伸应力区的金属经过锤打被延伸了,即产生了塑性变形,从而减小了对薄板边缘的压缩压力,矫正了波浪变形。
在锤打时,必须垫上平锤,以免出现明显的锤痕。
(2)火焰矫正法火焰矫正法是用氧—乙炔火焰或其他气体火焰(一般采用中性焰),以不均匀加热方式引起结构的某部位变形,来矫正原有的残余变形。
具体方法是∶将变形构件的局部(变形处伸长的部分)加热到600~800℃,此时钢板呈褐红色(适宜低碳钢),然后让其自然冷却或强制冷却,使之冷却后产生收缩变形,从而抵消原有的变形。
火焰加热的方式有以下3种∶1)点状加热矫正图3—137 所示为点状加热矫正钢板和钢管的实例。
图3—137a 所示为钢板(厚度在8 mm 以下)波浪变形的点状加热矫正,其加热点直径d一般不小于15 mm。
点间距离L随变形量的大小而变,残余变形越大,/越小,一般在50~100 mm 范围内变动。
为提高矫正速度和避免冷却后在加热处出现小泡突起,往往在加热完1个点后,立即用木锤敲打加热点及其周围,然后浇水冷却。
图3—137b 所示为钢管弯曲的点状加热矫正。
加热温度为800℃,加热速度要快,加热一点后迅速移到另一点加热。
采用同样方法加热并自然冷却1~2次,即能校直。
2)线状加热矫正火焰沿着直线方向移动同时在宽度方向上进行横向摆动,形成带状加热,称为线状加热。
图3—138 所示为线状加热的几种形式。
在线状加热矫正时,加热线的横向收缩大于纵向收缩,加热线的宽度越大,横向收缩也越大。
所以,在线状加热矫正时要尽可能发挥加热线横向收缩的作用。
改善残余应力的方法及特点
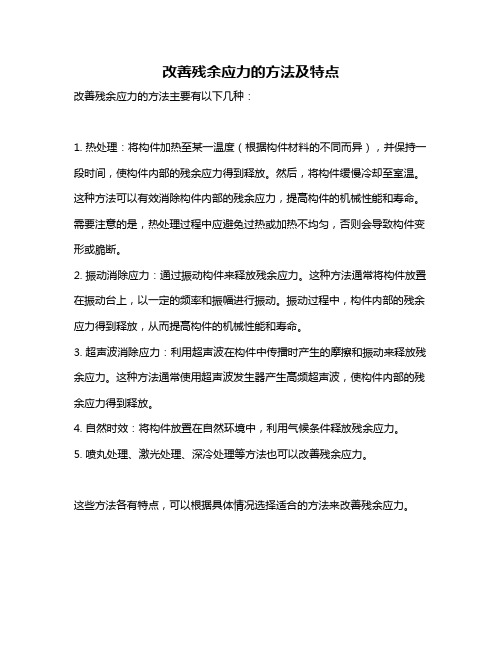
改善残余应力的方法及特点
改善残余应力的方法主要有以下几种:
1. 热处理:将构件加热至某一温度(根据构件材料的不同而异),并保持一段时间,使构件内部的残余应力得到释放。
然后,将构件缓慢冷却至室温。
这种方法可以有效消除构件内部的残余应力,提高构件的机械性能和寿命。
需要注意的是,热处理过程中应避免过热或加热不均匀,否则会导致构件变形或脆断。
2. 振动消除应力:通过振动构件来释放残余应力。
这种方法通常将构件放置在振动台上,以一定的频率和振幅进行振动。
振动过程中,构件内部的残余应力得到释放,从而提高构件的机械性能和寿命。
3. 超声波消除应力:利用超声波在构件中传播时产生的摩擦和振动来释放残余应力。
这种方法通常使用超声波发生器产生高频超声波,使构件内部的残余应力得到释放。
4. 自然时效:将构件放置在自然环境中,利用气候条件释放残余应力。
5. 喷丸处理、激光处理、深冷处理等方法也可以改善残余应力。
这些方法各有特点,可以根据具体情况选择适合的方法来改善残余应力。
消除残余应力的方法
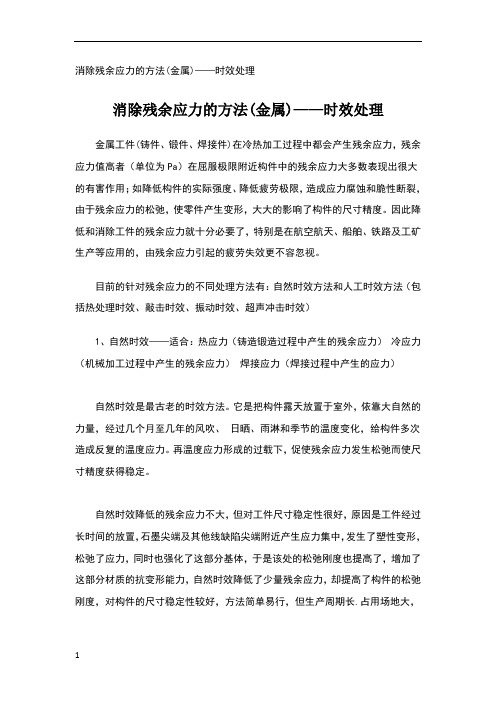
消除残余应力的方法(金属)——时效处理消除残余应力的方法(金属)——时效处理金属工件(铸件、锻件、焊接件)在冷热加工过程中都会产生残余应力,残余应力值高者(单位为Pa)在屈服极限附近构件中的残余应力大多数表现出很大的有害作用;如降低构件的实际强度、降低疲劳极限,造成应力腐蚀和脆性断裂,由于残余应力的松弛,使零件产生变形,大大的影响了构件的尺寸精度。
因此降低和消除工件的残余应力就十分必要了,特别是在航空航天、船舶、铁路及工矿生产等应用的,由残余应力引起的疲劳失效更不容忽视。
目前的针对残余应力的不同处理方法有:自然时效方法和人工时效方法(包括热处理时效、敲击时效、振动时效、超声冲击时效)1、自然时效——适合:热应力(铸造锻造过程中产生的残余应力)冷应力(机械加工过程中产生的残余应力)焊接应力(焊接过程中产生的应力)自然时效是最古老的时效方法。
它是把构件露天放置于室外,依靠大自然的力量,经过几个月至几年的风吹、日晒、雨淋和季节的温度变化,给构件多次造成反复的温度应力。
再温度应力形成的过载下,促使残余应力发生松弛而使尺寸精度获得稳定。
自然时效降低的残余应力不大,但对工件尺寸稳定性很好,原因是工件经过长时间的放置,石墨尖端及其他线缺陷尖端附近产生应力集中,发生了塑性变形,松弛了应力,同时也强化了这部分基体,于是该处的松弛刚度也提高了,增加了这部分材质的抗变形能力,自然时效降低了少量残余应力,却提高了构件的松弛刚度,对构件的尺寸稳定性较好,方法简单易行,但生产周期长.占用场地大,不易管理,不能及时发现构件内的缺陷,已逐渐被淘汰。
2、热处理时效——适合:热应力(铸造锻造过程中产生的残余应力)冷应力(机械加工过程中产生的残余应力)焊接应力(焊接过程中产生的应力)热时效处理是传统的消除残余应力方法。
它是将构件由室温缓慢,均匀加热至550℃左右,保温4-8小时,再严格控制降温速度至150℃以下出炉。
热时效工艺要求是严格的,如要求炉内温差不大于±25℃,升温速度不大于50℃/小时,降温速度不大于20℃/小时。
残余应力 消除机理
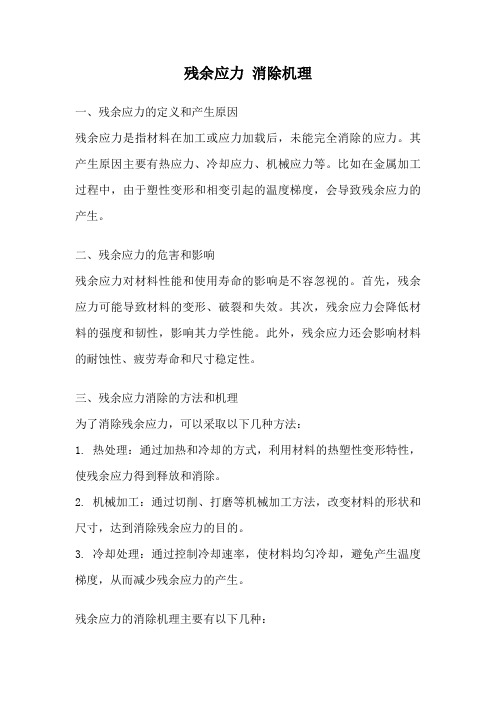
残余应力消除机理一、残余应力的定义和产生原因残余应力是指材料在加工或应力加载后,未能完全消除的应力。
其产生原因主要有热应力、冷却应力、机械应力等。
比如在金属加工过程中,由于塑性变形和相变引起的温度梯度,会导致残余应力的产生。
二、残余应力的危害和影响残余应力对材料性能和使用寿命的影响是不容忽视的。
首先,残余应力可能导致材料的变形、破裂和失效。
其次,残余应力会降低材料的强度和韧性,影响其力学性能。
此外,残余应力还会影响材料的耐蚀性、疲劳寿命和尺寸稳定性。
三、残余应力消除的方法和机理为了消除残余应力,可以采取以下几种方法:1. 热处理:通过加热和冷却的方式,利用材料的热塑性变形特性,使残余应力得到释放和消除。
2. 机械加工:通过切削、打磨等机械加工方法,改变材料的形状和尺寸,达到消除残余应力的目的。
3. 冷却处理:通过控制冷却速率,使材料均匀冷却,避免产生温度梯度,从而减少残余应力的产生。
残余应力的消除机理主要有以下几种:1. 塑性变形:材料在塑性变形过程中,原先存在的残余应力会得到部分或完全释放。
2. 相变:材料的相变过程中,晶体结构的变化会引起残余应力的消除。
3. 热稳定:在高温下,材料的晶体结构会重新排列,从而消除残余应力。
4. 弹性回复:材料在受到外力作用后,会发生弹性变形,在外力去除后,材料会部分或完全恢复原状,从而消除残余应力。
四、残余应力消除的应用领域和意义残余应力消除技术在工程领域有着广泛的应用。
比如在航空航天、汽车制造、电子设备等领域,对材料的残余应力进行有效的消除,可以提高产品的性能和可靠性,减少材料失效的风险。
此外,残余应力消除还可以提高材料的加工性能,减少加工工艺中的变形和破损情况。
总结起来,残余应力消除是一项重要的材料工程技术,对于提高材料的性能和可靠性具有重要意义。
通过合理的方法和机理,可以有效地消除残余应力,保证材料的稳定性和可靠性,提高产品的质量和寿命。
如何消除或减小焊接残余应力

如何消除或减小焊接残余应力焊接残余应力是焊接结束后残留在焊件内的应力,残余应力对焊接结构的强度、腐蚀和尺寸稳定性等使用性能造成影响。
虽然在结构设计时,考虑了残余应力的问题,在工艺上也采取了一定的措施来防止或减小焊接残余应力,但由于焊接应力的复杂性,结构焊接完以后仍然可能存在较大的残余应力。
另外,有些结构在装配过程中还可能产生新的残余应力,这些焊接残余应力及装配应力都会影响结构的使用性能。
常用的消除或减小残余应力的方法,有以下几种。
一、热处理法热处理法是利用材料在高温下屈服点下降和蠕变现象,达到松弛焊接残余应力的目的。
同时,热处理还可改善焊接接头的性能。
生产中常用的热处理法,有整体热处理和局部热处理两种。
1.整体热处理将整个结构件缓慢加热到一定的温度(低碳钢为650℃),并在该温度下保温一定的时间(一般按每mm板厚保温2-4min,但总时间不少于30min),然后空冷或随炉冷却。
整体热处理消除残余应力的效果取决于加热温度、保温时间、加热和冷却速度、加热方法和加热范围,一般可消除60%-90%的残余应力,在生产中应用比较广泛。
2.局部热处理对于某些不允许或不可能进行整体热处理的焊接结构,可采用局部热处理。
局部热处理就是对构件焊缝周围的局部应力很大的区域及其周围,缓慢加热到一定温度后保温,然后缓慢冷却,其消除应力的效果不如整体热处理,它只能降低残余应力峰值,不能完全消除残余应力。
对于一些大型筒形容器的组装环缝和一些重要管道等,常采用局部热处理来降低结构的残余应力。
例如,在铺设热力管道的过程中,焊接结束时常采用氧乙炔焰对焊缝进行局部加热,来降低焊接部位的残余应力。
二、机械拉伸法机械拉伸法是通过不同方式在构件上施加一定的拉伸应力,使焊缝及其附近产生拉伸塑性变形,与焊接时在焊缝及其附近所产生的压缩塑性变形相互抵消一部分,以达到松弛残余应力的目的。
实践证明,拉伸载荷加的越高,压缩塑性变形量就抵消得越多,残余应力消除得越彻底。
减小残余应力的措施
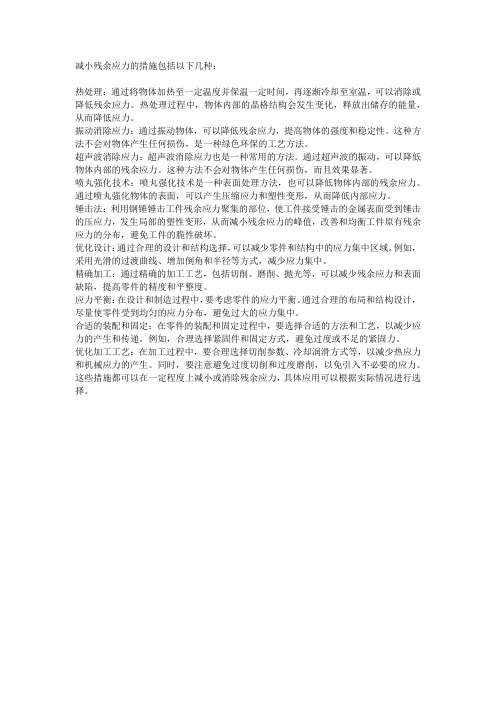
减小残余应力的措施包括以下几种:热处理:通过将物体加热至一定温度并保温一定时间,再逐渐冷却至室温,可以消除或降低残余应力。
热处理过程中,物体内部的晶格结构会发生变化,释放出储存的能量,从而降低应力。
振动消除应力:通过振动物体,可以降低残余应力,提高物体的强度和稳定性。
这种方法不会对物体产生任何损伤,是一种绿色环保的工艺方法。
超声波消除应力:超声波消除应力也是一种常用的方法。
通过超声波的振动,可以降低物体内部的残余应力。
这种方法不会对物体产生任何损伤,而且效果显著。
喷丸强化技术:喷丸强化技术是一种表面处理方法,也可以降低物体内部的残余应力。
通过喷丸强化物体的表面,可以产生压缩应力和塑性变形,从而降低内部应力。
锤击法:利用钢锤锤击工件残余应力聚集的部位,使工件接受锤击的金属表面受到锤击的压应力,发生局部的塑性变形,从而减小残余应力的峰值,改善和均衡工件原有残余应力的分布,避免工件的脆性破坏。
优化设计:通过合理的设计和结构选择,可以减少零件和结构中的应力集中区域。
例如,采用光滑的过渡曲线、增加倒角和半径等方式,减少应力集中。
精确加工:通过精确的加工工艺,包括切削、磨削、抛光等,可以减少残余应力和表面缺陷,提高零件的精度和平整度。
应力平衡:在设计和制造过程中,要考虑零件的应力平衡。
通过合理的布局和结构设计,尽量使零件受到均匀的应力分布,避免过大的应力集中。
合适的装配和固定:在零件的装配和固定过程中,要选择合适的方法和工艺,以减少应力的产生和传递。
例如,合理选择紧固件和固定方式,避免过度或不足的紧固力。
优化加工工艺:在加工过程中,要合理选择切削参数、冷却润滑方式等,以减少热应力和机械应力的产生。
同时,要注意避免过度切削和过度磨削,以免引入不必要的应力。
这些措施都可以在一定程度上减小或消除残余应力,具体应用可以根据实际情况进行选择。
何为残余应力,如何消除

何为残余应力,如何消除
在外力消除后仍保留在金属内部的应力称为残余应力或内应力。
残余应力是由于金属的不均匀变形和不均匀的体积变化造成的。
残余应力按内应力作用范围,可分为宏观内应力(第一类残余应力)、晶界内应力(第二类残余应力)和晶格畸变内应力(第三类残余应力)。
宏观内应力:当金属发送不均匀变形,而物体的完整性又限制这种不均匀变形的自由发展时,在金属物体内大部分体积之间产生互相平衡起来的应力,这种因变形不均匀所出现的应力称为宏观内应力。
晶间内应力:由于金属各晶粒的空间取向不同,在发送变形时,相邻的两个晶粒发生了不均匀变形,两者之间相互制约而产生平衡,阻碍变形的自由发展,变形结束后残留在晶体内形成晶间内应力。
晶格畸变内应力:变形不均匀不仅表现在各晶粒之间,因受其周围晶粒影响不同,在同一晶粒各个部位也存在变形不均匀,产生一定晶格畸变,限制变形的自由发展,变形后残留在晶粒内部形成晶格畸变内应力。
残余应力会导致工作变形、开裂和部分尺寸或形状改变,缩短工件的使用寿命。
为了消除残余应力,一般采用热处理法和机械处理法。
允许退火的金属材料可以采用退火的方法消除残余应力。
消除残余应力的退火一般在较低的温度(低于再结晶温度)下进行,即恢复期,此时残余应力可大部分消除,而不会引起材料强度的降低;在较高温度下退火虽然能彻底消除残余应力,但会造成金属力学性能改变,特别是强度的
降低和制品晶粒的粗化。
机械处理法是在制品的表面在附加一些表面变形,使之产生新的压副应力以抵消制品内的残余应力或尽量减小其数值。
当材料表面有拉伸残余应力时才可以该方法。
例如管棒材的多辊矫直,带材的拉弯矫、张力退火等均是消除残余应力的有效方法。
消减残余应力的方法

消减残余应力的方法
1. 热处理呀,这就像是给材料来个“舒适的温泉浴”。
比如钢铁制品,把它加热到一定温度再慢慢冷却,能有效消减残余应力呢!这样它就不会那么容易变形或开裂啦。
2. 机械拉伸也很棒哦!就好比给材料做个“舒展运动”。
像一些金属板材,对它进行拉伸,把内部的应力给释放出来,是不是很神奇呀?
3. 振动时效可别小瞧呀!这简直是给材料来一场“欢乐的摇摆舞会”。
把工件放在振动台上,让它跟着一起振动,残余应力就被抖落掉啦,你说有趣不有趣?
4. 自然时效虽然慢点,但效果也不错呀!就像是让材料“慢慢修养”。
长时间放置,让残余应力自然地消减,是不是挺神奇哒?你想好要用哪种办法没?
5. 超声冲击也值得一试哟!感觉就像给材料来个“强力按摩”。
特别是一些焊接的地方,用超声冲击一下,残余应力就能大大减少呢!
6. 抛丸强化也很厉害呢!就如同让材料接受一场“激烈的洗礼”。
通过高速弹丸的撞击,既能强化表面又能消减残余应力,这多好呀!
7. 豪克能时效也很牛呀!它仿佛是给材料注入了“神奇能量”。
能快速高效地消减残余应力,真的超厉害的!
我觉得呀,这些方法各有各的好,要根据具体情况来选择合适的,这样才能把残余应力消减得妥妥的!。
- 1、下载文档前请自行甄别文档内容的完整性,平台不提供额外的编辑、内容补充、找答案等附加服务。
- 2、"仅部分预览"的文档,不可在线预览部分如存在完整性等问题,可反馈申请退款(可完整预览的文档不适用该条件!)。
- 3、如文档侵犯您的权益,请联系客服反馈,我们会尽快为您处理(人工客服工作时间:9:00-18:30)。
消除残余应力的方法(金属)——时效处理
消除残余应力的方法(金属)——时效处理
金属工件(铸件、锻件、焊接件)在冷热加工过程中都会产生残余应力,残余应力值高者(单位为Pa)在屈服极限附近构件中的残余应力大多数表现出很大的有害作用;如降低构件的实际强度、降低疲劳极限,造成应力腐蚀和脆性断裂,由于残余应力的松弛,使零件产生变形,大大的影响了构件的尺寸精度。
因此降低和消除工件的残余应力就十分必要了,特别是在航空航天、船舶、铁路及工矿生产等应用的,由残余应力引起的疲劳失效更不容忽视。
目前的针对残余应力的不同处理方法有:自然时效方法和人工时效方法(包括热处理时效、敲击时效、振动时效、超声冲击时效)
1、自然时效——适合:热应力(铸造锻造过程中产生的残余应力)冷应力(机械加工过程中产生的残余应力)焊接应力(焊接过程中产生的应力)
自然时效是最古老的时效方法。
它是把构件露天放置于室外,依靠大自然的力量,经过几个月至几年的风吹、日晒、雨淋和季节的温度变化,给构件多次造成反复的温度应力。
再温度应力形成的过载下,促使残余应力发生松弛而使尺寸精度获得稳定。
自然时效降低的残余应力不大,但对工件尺寸稳定性很好,原因是工件经过长时间的放置,石墨尖端及其他线缺陷尖端附近产生应力集中,发生了塑性变形,松弛了应力,同时也强化了这部分基体,于是该处的松弛刚度也提高了,增加了这部分材质的抗变形能力,自然时效降低了少量残余应力,却提高了构件的松弛刚度,对构件的尺寸稳定性较好,方法简单易行,但生产周期长.占用场地大,不易管理,不能及时发现构件内的缺陷,已逐渐被淘汰。
2、热处理时效——适合:热应力(铸造锻造过程中产生的残余应力)冷应力(机械加工过程中产生的残余应力)焊接应力(焊接过程中产生的应力)
热时效处理是传统的消除残余应力方法。
它是将构件由室温缓慢,均匀加热至550℃左右,保温4-8小时,再严格控制降温速度至150℃以下出炉。
热时效工艺要求是严格的,如要求炉内温差不大于±25℃,升温速度不大于50℃/小时,降温速度不大于20℃/小时。
炉内最高温度不许超过570℃,保温时间也不易过长,如果温度高于570℃,保温时间过长,会引起石墨化,构件强度降低。
如果升温速度过快,构件在升温中薄壁处升温速度比厚壁处快的多,构件各部分的温差急剧增大,会造成附加温度应力。
如果附加应力与构件本身的残余应力叠加超过强度极限,就会造成构件开裂。
热时效如果降温不当,会使时效效果大为降低,甚至产生与原残余应力相同的温度应力(二次应力、应力叠加),并残留在构件中,从而破坏了已取得的热
时效效果。
3、敲击时效(锤击法)——适合:焊接应力(焊接过程中产生的应力)
锤击处理很早被引入焊接领域,初期主要应用于消除焊接变形。
锤击的方法分为,手工锤击法和电锤锤击法。
通过观察分析,认为适当锤击可以消除和减少焊接裂纹,进而推断锤击有消除焊接残余应力的作用,因此在工艺中采用锤击处理,防止焊接裂纹的产生。
一般认为,锤击处理消除焊接残余应力是使被处理金属通过锤击,在体内局部产生一定的塑性伸长,释放焊接过程产生的残余拉伸弹性应变,从而达到释放焊接残余应力的目的。
但由于锤击(特别是手工锤击)的不规范(锤击力的大小、频率、基体的力学性能及锤击区的温度等)及焊接残余应力准确测试的困难,故对于锤击处理与残余应力的关系,至今尚没有一个科学的和系统的研究。
在合适的焊接规范和工艺下,锤击不仅能有效地消除工件焊缝部位的应力,而且能促进热影响区拉伸残余应力的释放,甚至可以获得一定值的压应力。
4、振动时效——适合:热应力(铸造锻造过程中产生的残余应力)冷应力(机械加工过程中产生的残余应力)焊接应力(焊接过程中产生的应力)
振动时效(VSR)就是在激振设备周期性——激振力的作用下在某一频率使金属工件共振,形成的动应力使工件在半小时内进行数万次较大振幅的亚共振振动。
使其内部残余应力叠加,达到一定数值后,在应力最集中处,会超过屈服极限而产生微小的塑性变形,降低该处残余应力,并强化金属基体;而后振动在其余应力集中部分产生同样作用,直至不能引起任何部分塑性变形为止,从而使构件内残余应力降低和重新分布,处于平衡状态,提高材料的强度。
构件在后序安装使用中,因不再处于共振状态,不承受比共振力更大外力作用,振后构件不会出现应力变形。
振动时效也可看作在周期动应力作用下循环应变,金属材料内部晶体位错运动使微观应力增加,达到调节应力稳定构件尺寸的过程。
振动时效,在国外称之为VSR技术,它是Vibratory Stress Reliele的缩写。
它是在激振器的周期性外力(激振力)的作用下,使工件自身产生共振,进而使其内部歪曲的晶格,产生滑移而恢复平衡,提工件的松弛刚度,消除并均化残余应力,使其尺寸稳定。
在以消除残余应力为目的的时效方法中,振动时效可以完全代替热时效。
原机电部等六个部委将振动时效定为第七个五年计化间推广的节能项目,并将此类产品定位替代进口产品,这种振动消除应力技术在国外已有几十年的应用经验。
5、超声冲击——适合:焊接应力(焊接过程中产生的应力)
超声冲击是敲击时效的发展。
超声冲击技术的特点是单位时间内输入能量高,实施装置的比能量(输出能量与装置质量之比)大。
振动处理频率可高达18KHZ-27KHZ,振动速度可达
2m/s-3m/s,加速度高达重力加速度的三万多倍,高速瞬时的冲击能量使被处理
焊缝区的表面温度以极高的速度上升到600℃,又以极快的速度冷却。
这种高频能量输入到焊缝区表面后,使能量作用区的表层金属的相位组织发生一定的变化。
1)使焊缝区的金属表面层内的拉伸残余应力变为压应力,从而能大幅度地提高结构的使用疲劳寿命。
2)表面层内的金属晶粒变细,产生塑性变形层,从而使金属表面层的强度和硬度有相应的提高。
3)改善焊趾的几何形状,降低应力集中。
4)改变焊接应力场,明显减少焊接变形。
注:本文为网站的原创文章,版权归所有。
转载请注明出处。