一次法炼胶可行性报告
一次法炼胶可行性报告
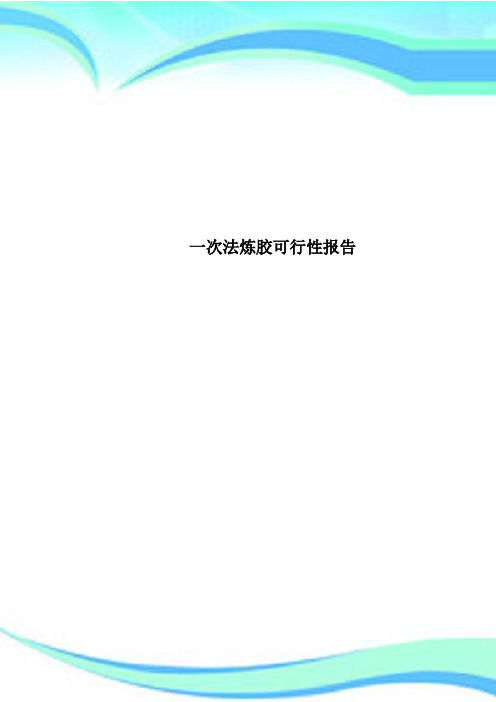
一次法炼胶对密炼机的选型与传统的不一样,传统密炼机(如F370/270、GK-400/255)转子一般都是四棱切线型,填充系数0.75。而一次法炼胶密炼机一般选GE320带有PES3转子,填充系数0.65时的有效容量约208立升与GE590T带有PES5转子串联,填充系数0.36时的有效容量约208立升。
一次法炼胶统工艺炼胶优、劣比较如下。
一、炼胶工艺比较:
传统炼胶工艺:采用密炼机多段混炼,这种加工方法目的是实现橡胶分子链的断裂,主要采用高温氧化裂解,机械剪切为辅。
缺点:分子链分布范围较宽,容易生成大量的炭黑凝胶,影响各种配合剂的分散和物理性能。
一次法炼胶工艺:
采用密炼机一段混炼,在开炼机上加硫磺,这种加工方法大大加强了胶料的机械剪切,弱化了高温氧化裂解的作用。
四、电能消耗比较:
胶料按照传统工艺分析,按照胶料不同,工艺路线如下:胎面胶: 1段,2段,加硫粘合胶料:母胶、1段、2段、加硫以胎面胶为例:1、2段在370,加硫在270,370每车胶料330KG,270每车胶料220KG。1段3分钟,2段2.5分钟,加硫2.5分钟,则1吨胶料耗时:1段3*(1000/330)=9分钟2段2.5*(1000/330)=8.25分钟加硫2.5*(1000/220)=11.4分钟合计:9+8.25+11.4=28.65分钟
三、产能比较:
一次法产能简述:胶料在密炼机内混炼时间以3.5分钟、220公斤/车计算,单日炼胶量为70-80吨终炼胶;按照现行全钢胶料平均段数2.7段计算:一次法单日产能折合为: 终炼胶80吨,母炼胶136吨;合计:216吨;
炼胶实验报告

一、实验目的1. 了解橡胶的基本性质和加工工艺。
2. 掌握炼胶实验的基本步骤和方法。
3. 熟悉炼胶设备的操作和注意事项。
二、实验原理橡胶是一种高分子化合物,具有优异的弹性、耐磨性、耐腐蚀性等特点。
炼胶实验是橡胶加工过程中的重要环节,通过炼胶可以改善橡胶的物理性能,提高橡胶制品的质量。
三、实验材料与仪器1. 实验材料:天然橡胶、炭黑、氧化锌、促进剂、软化剂等。
2. 实验仪器:炼胶机、模具、天平、剪刀、刀具、手套等。
四、实验步骤1. 准备材料:按照配方称取适量的天然橡胶、炭黑、氧化锌、促进剂、软化剂等。
2. 混炼:将天然橡胶放入炼胶机中,启动炼胶机,待橡胶软化后,逐步加入炭黑、氧化锌、促进剂、软化剂等,继续混炼,直至混合均匀。
3. 炼胶:将混炼好的橡胶放入模具中,进行压延、切割、检验等操作。
4. 检验:对炼胶后的橡胶进行物理性能检验,如拉伸强度、撕裂强度、硬度等。
5. 记录实验数据:记录实验过程中的关键数据,如炼胶时间、温度、压力等。
五、实验结果与分析1. 实验结果(1)混炼过程:混炼过程中,橡胶逐渐软化,炭黑、氧化锌、促进剂、软化剂等均匀分布。
(2)炼胶过程:炼胶过程中,橡胶具有良好的可塑性,便于进行压延、切割等操作。
(3)检验结果:炼胶后的橡胶具有良好的物理性能,如拉伸强度、撕裂强度、硬度等。
2. 实验分析(1)混炼过程中,橡胶的软化与温度、压力、时间等因素有关。
温度越高、压力越大、时间越长,橡胶的软化程度越好。
(2)混炼过程中,各种配合剂均匀分布对橡胶的物理性能有很大影响。
炭黑可以提高橡胶的耐磨性、耐热性;氧化锌可以提高橡胶的耐油性、耐水性;促进剂可以提高橡胶的硫化速度;软化剂可以提高橡胶的柔软性。
(3)炼胶过程中的压延、切割等操作对橡胶的物理性能也有一定影响。
适当的压延、切割可以提高橡胶的均匀性、提高橡胶制品的质量。
六、实验结论1. 炼胶实验是橡胶加工过程中的重要环节,通过炼胶可以改善橡胶的物理性能,提高橡胶制品的质量。
(2023)炼胶设备项目可行性研究报告写作范本(一)
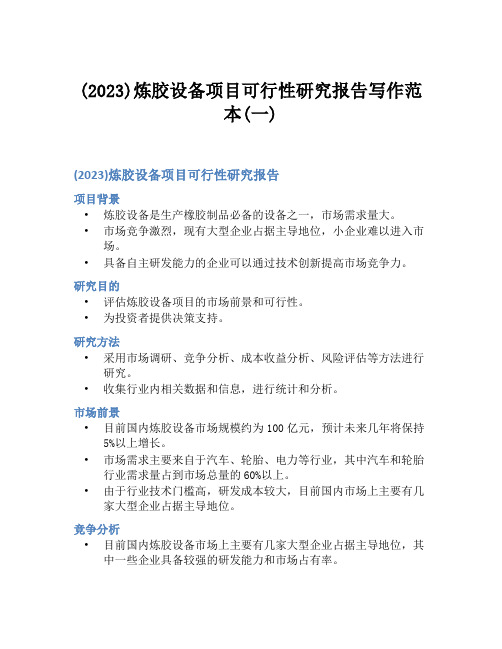
(2023)炼胶设备项目可行性研究报告写作范本(一)(2023)炼胶设备项目可行性研究报告项目背景•炼胶设备是生产橡胶制品必备的设备之一,市场需求量大。
•市场竞争激烈,现有大型企业占据主导地位,小企业难以进入市场。
•具备自主研发能力的企业可以通过技术创新提高市场竞争力。
研究目的•评估炼胶设备项目的市场前景和可行性。
•为投资者提供决策支持。
研究方法•采用市场调研、竞争分析、成本收益分析、风险评估等方法进行研究。
•收集行业内相关数据和信息,进行统计和分析。
市场前景•目前国内炼胶设备市场规模约为100亿元,预计未来几年将保持5%以上增长。
•市场需求主要来自于汽车、轮胎、电力等行业,其中汽车和轮胎行业需求量占到市场总量的60%以上。
•由于行业技术门槛高,研发成本较大,目前国内市场上主要有几家大型企业占据主导地位。
竞争分析•目前国内炼胶设备市场上主要有几家大型企业占据主导地位,其中一些企业具备较强的研发能力和市场占有率。
•相对于大型企业,小企业在技术研发和市场销售方面较为薄弱,难以进入市场。
成本收益分析•炼胶设备的生产成本主要包括研发成本、生产成本、销售成本等。
•相对于大型企业,小企业在研发和生产成本上可能存在较大压力,但通过规模化生产和有效的销售策略可以降低成本。
•由于市场需求量大,经过科学规划和管理,炼胶设备项目在未来几年内可以获得稳定的收益。
风险评估•炼胶设备项目存在技术创新和市场销售风险。
•在研发方面,需要不断提升技术水平和研发能力,以适应市场需求和竞争。
•在市场销售方面,需要制定有效的销售策略,提高产品质量和服务水平。
总结本研究认为,炼胶设备项目具备较大的市场前景和可行性,但存在技术创新和市场销售的风险。
对于投资者来说,可以根据自身实力和资金等条件进行综合考虑,决定是否投资该项目。
建议•针对技术创新风险,建议项目方要加强研发投入,提高研发能力,并且注重知识产权的保护。
•针对市场销售风险,建议项目方要制定有效的销售策略,建立完善的售后服务系统,提高产品质量和服务水平。
炼胶机项目可行性研究报告

炼胶机项目可行性研究报告核心提示:炼胶机项目投资环境分析,炼胶机项目背景和发展概况,炼胶机项目建设的必要性,炼胶机行业竞争格局分析,炼胶机行业财务指标分析参考,炼胶机行业市场分析与建设规模,炼胶机项目建设条件与选址方案,炼胶机项目不确定性及风险分析,炼胶机行业发展趋势分析提供国家发改委甲级资质专业编写:炼胶机项目建议书炼胶机项目申请报告炼胶机项目环评报告炼胶机项目商业计划书炼胶机项目资金申请报告炼胶机项目节能评估报告炼胶机项目规划设计咨询炼胶机项目可行性研究报告【主要用途】发改委立项,政府批地,融资,贷款,申请国家补助资金等【关键词】炼胶机项目可行性研究报告、申请报告【交付方式】特快专递、E-mail【交付时间】2-3个工作日【报告格式】Word格式;PDF格式【报告价格】此报告为委托项目报告,具体价格根据具体的要求协商,欢迎进入公司网站,了解详情,工程师(高建先生)会给您满意的答复。
【报告说明】本报告是针对行业投资可行性研究咨询服务的专项研究报告,此报告为个性化定制服务报告,我们将根据不同类型及不同行业的项目提出的具体要求,修订报告目录,并在此目录的基础上重新完善行业数据及分析内容,为企业项目立项、上马、融资提供全程指引服务。
可行性研究报告是在制定某一建设或科研项目之前,对该项目实施的可能性、有效性、技术方案及技术政策进行具体、深入、细致的技术论证和经济评价,以求确定一个在技术上合理、经济上合算的最优方案和最佳时机而写的书面报告。
可行性研究报告主要内容是要求以全面、系统的分析为主要方法,经济效益为核心,围绕影响项目的各种因素,运用大量的数据资料论证拟建项目是否可行。
对整个可行性研究提出综合分析评价,指出优缺点和建议。
为了结论的需要,往往还需要加上一些附件,如试验数据、论证材料、计算图表、附图等,以增强可行性报告的说服力。
可行性研究是确定建设项目前具有决定性意义的工作,是在投资决策之前,对拟建项目进行全面技术经济分析论证的科学方法,在投资管理中,可行性研究是指对拟建项目有关的自然、社会、经济、技术等进行调研、分析比较以及预测建成后的社会经济效益。
橡胶可行性报告

橡胶可行性报告1. 引言橡胶是一种重要的工业原材料,广泛应用于汽车制造、建筑、家具、电子产品制造等多个领域。
本报告将从市场需求、生产成本和可持续性的角度对橡胶的可行性进行评估,并提供相关发展建议。
2. 市场需求橡胶的市场需求主要受两个因素影响:经济增长和行业发展。
随着全球经济的不断增长,汽车制造、建筑和家具等行业的发展也带动了对橡胶的需求增长。
特别是在汽车制造业中,橡胶的需求量占比较大。
另外,随着电子产品的普及和半导体制造业的发展,橡胶在电子产品制造中的应用也逐渐增加。
因此,橡胶的市场需求前景广阔,具有潜力。
3. 生产成本橡胶的生产成本主要包括原材料成本、能源成本和人工成本。
原材料成本是橡胶生产的主要成本之一,主要取决于橡胶原料的价格。
当前,橡胶原料价格相对较稳定,但由于受到气候变化和天然灾害等因素的影响,价格波动仍存在一定风险。
能源成本是另一个重要的成本因素。
橡胶生产过程中需要大量能源,包括电力和燃料。
能源价格的波动会直接影响橡胶的生产成本。
另外,人工成本也是橡胶生产中的重要成本之一。
在一些发展中国家,人工成本相对较低,但在一些发达国家,人工成本较高。
因此,选择适合的生产地点也会影响橡胶的生产成本。
4. 可持续性考虑随着对可持续发展的关注不断增加,橡胶行业也需要考虑可持续性问题。
橡胶的可持续性主要包括以下几个方面:4.1 环境影响橡胶生产过程中会产生大量废水和废气,对环境造成污染。
此外,橡胶园建设需要大量土地,可能会引发森林砍伐和生态破坏。
因此,橡胶生产应该采取环保措施,减少排放和废物处理的负面影响。
4.2 社会责任橡胶行业需要关注社会责任问题,包括员工福利、劳工权益和生产安全等。
同时,应该遵守当地法律法规,确保生产活动的合法性和合规性。
4.3 可再生能源利用橡胶生产中消耗大量能源,使用可再生能源可以降低对非可再生能源的依赖,减少碳排放和环境污染。
5. 发展建议基于以上分析,为了开展可行的橡胶生产活动,我们提出以下发展建议:5.1 市场调研在决定进入橡胶行业之前,进行充分的市场调研是必要的。
低温一次法炼胶工艺的研究开发和应用进展
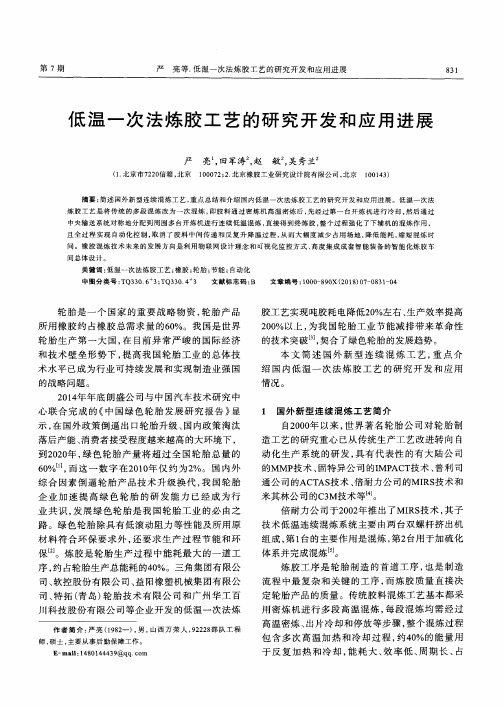
关 键 词 :低 温 一 次 法 炼胶 工 艺 ;橡胶 ;轮 胎 ;节 能 ;自动化 中图 分 类号 :TQ330.6 3;TQ330.4 3 文献 标 志 码 :B 文章 编 号 :1000—890X(2018)07—083卜 O4
轮胎 是 一 个 国家 的 重要 战 略 物 资 ,轮 胎产 品 所用 橡 胶 约 占橡胶 总 需求 量 的60%。我 国是 世界 轮 胎生 产 第 一 大 国 ,在 目前 异 常严 峻 的 国际 经济 和技 术 壁 垒 形 势下 ,提高 我 国轮 胎工 业 的总体 技 术水 平 已成 为行业 可 持续 发展 和实 现制 造业 强 国 的 战略问题 。
混炼胶项目可行性报告
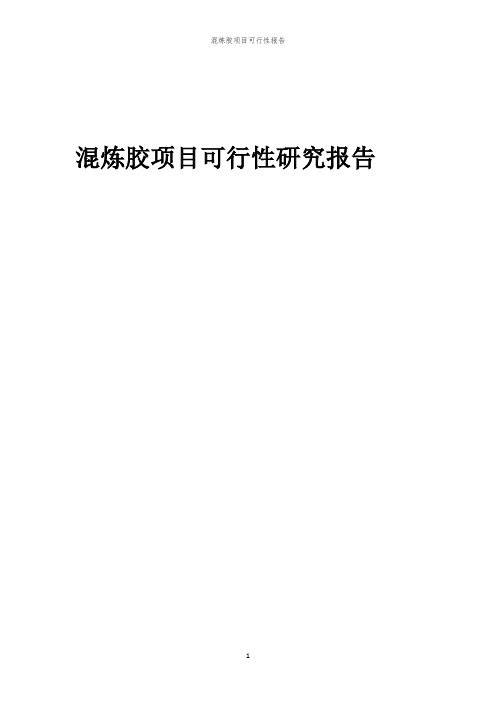
混炼胶项目可行性研究报告目录序言 (5)一、技术方案与建筑物规划 (5)(一)、设计原则与混炼胶项目工程概述 (5)(二)、建设选项 (6)(三)、建筑物规划与设备标准 (7)二、组织架构与人力资源配置 (9)(一)、人员资源需求 (9)(二)、员工培训与发展 (11)三、混炼胶项目基本情况 (13)(一)、混炼胶项目名称及混炼胶项目单位 (13)(二)、混炼胶项目建设地点 (13)(三)、调查与分析的范围 (14)(四)、参考依据和技术原则 (15)(五)、规模和范围 (16)(六)、混炼胶项目建设进展 (16)(七)、原材料与设备需求 (18)(八)、环境影响与可行性 (19)(九)、预计投资成本 (20)(十)、1混炼胶项目关键技术与经济指标 (21)(十一)、1总结与建议 (22)四、法人治理架构 (23)(一)、股东权益与义务 (23)(二)、公司董事会 (24)(三)、高级管理层 (26)(四)、监督管理层 (27)五、市场与供应链管理 (28)(一)、供应链策略 (28)(二)、供应商关系管理 (28)(三)、存货与库存管理 (29)(四)、客户关系管理 (29)(五)、物流与分销策略 (29)六、混炼胶项目进展与里程碑 (30)(一)、混炼胶项目进展 (30)(二)、重要里程碑与进度控制 (31)(三)、问题识别与解决方案 (32)七、技术与研发计划 (33)(一)、技术开发策略 (33)(二)、研发团队与资源配置 (33)(三)、新产品开发计划 (34)八、战略合作与合作伙伴关系 (36)(一)、合作战略与目标 (36)(二)、合作伙伴选择与评估 (37)(三)、合同与协议管理 (38)(四)、风险管理与纠纷解决 (39)九、市场调研与竞争分析 (40)(一)、市场状况概览 (40)(二)、市场细分与目标市场 (41)(三)、竞争对手分析 (43)(四)、市场机会与挑战 (44)(五)、市场战略 (45)十、投资方案 (48)(一)、混炼胶项目总投资构成分析 (48)(二)、建设投资构成 (49)(三)、资金筹措方式 (49)(四)、投资分析 (50)(五)、资金使用计划 (51)(六)、混炼胶项目融资方案 (52)(七)、盈利模式和财务预测 (54)十一、混炼胶项目可行性风险分析 (55)(一)、混炼胶项目风险识别 (55)(二)、风险评估和定量分析 (56)(三)、风险管理计划 (56)(四)、风险缓解策略 (57)十二、战略退出计划 (57)(一)、混炼胶项目退出战略 (57)(二)、潜在退出方式 (58)(三)、退出时机与条件 (59)(四)、投资者回报与退出 (59)十三、环境保护与可持续发展 (60)(一)、环境保护政策与承诺 (60)(二)、可持续生产与绿色供应链 (60)(三)、减少废物和碳足迹 (61)(四)、知识产权保护与创新 (62)(五)、社区参与与教育 (63)十四、社会责任与可持续发展 (64)(一)、社会责任策略 (64)(二)、可持续发展计划 (64)(三)、社会参与与贡献 (65)十五、战略合作伙伴与投资者关系 (65)(一)、投资者关系管理 (65)(二)、战略合作伙伴关系管理 (66)(三)、投资者关系沟通 (66)序言本报告旨在对公司混炼胶项目进行评价分析,旨在提供参考意见和改进建议,帮助企业优化项目管理和提升产品竞争力。
胶的制备实验报告
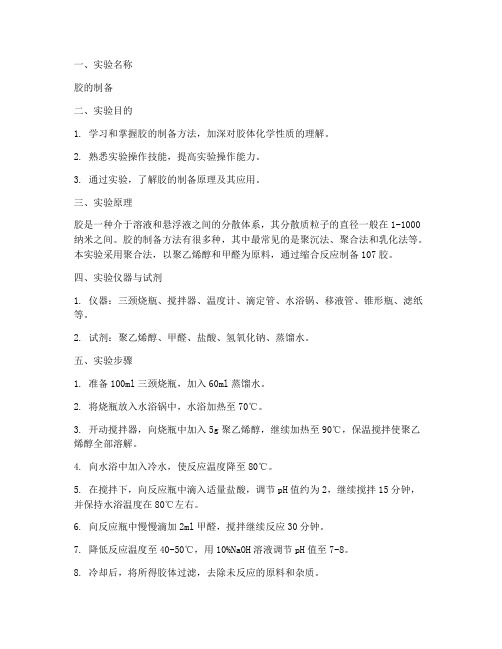
一、实验名称胶的制备二、实验目的1. 学习和掌握胶的制备方法,加深对胶体化学性质的理解。
2. 熟悉实验操作技能,提高实验操作能力。
3. 通过实验,了解胶的制备原理及其应用。
三、实验原理胶是一种介于溶液和悬浮液之间的分散体系,其分散质粒子的直径一般在1-1000纳米之间。
胶的制备方法有很多种,其中最常见的是聚沉法、聚合法和乳化法等。
本实验采用聚合法,以聚乙烯醇和甲醛为原料,通过缩合反应制备107胶。
四、实验仪器与试剂1. 仪器:三颈烧瓶、搅拌器、温度计、滴定管、水浴锅、移液管、锥形瓶、滤纸等。
2. 试剂:聚乙烯醇、甲醛、盐酸、氢氧化钠、蒸馏水。
五、实验步骤1. 准备100ml三颈烧瓶,加入60ml蒸馏水。
2. 将烧瓶放入水浴锅中,水浴加热至70℃。
3. 开动搅拌器,向烧瓶中加入5g聚乙烯醇,继续加热至90℃,保温搅拌使聚乙烯醇全部溶解。
4. 向水浴中加入冷水,使反应温度降至80℃。
5. 在搅拌下,向反应瓶中滴入适量盐酸,调节pH值约为2,继续搅拌15分钟,并保持水浴温度在80℃左右。
6. 向反应瓶中慢慢滴加2ml甲醛,搅拌继续反应30分钟。
7. 降低反应温度至40-50℃,用10%NaOH溶液调节pH值至7-8。
8. 冷却后,将所得胶体过滤,去除未反应的原料和杂质。
9. 将滤液移入锥形瓶中,继续搅拌,直至胶体完全形成。
六、实验结果与分析1. 通过实验,成功制备出107胶,其外观为微黄色或无色透明胶状液体。
2. 实验过程中,pH值的调节对胶的制备至关重要。
若pH值过高或过低,都会影响胶的稳定性。
3. 温度对胶的制备也有一定影响。
过高或过低的温度都会导致胶的凝聚。
七、实验结论本实验通过聚合法成功制备出107胶,验证了实验原理的正确性。
在实验过程中,掌握了实验操作技能,提高了实验能力。
同时,对胶的制备原理及其应用有了更深入的了解。
八、注意事项1. 实验过程中,注意安全,避免甲醛、盐酸等有害物质的吸入和皮肤接触。
- 1、下载文档前请自行甄别文档内容的完整性,平台不提供额外的编辑、内容补充、找答案等附加服务。
- 2、"仅部分预览"的文档,不可在线预览部分如存在完整性等问题,可反馈申请退款(可完整预览的文档不适用该条件!)。
- 3、如文档侵犯您的权益,请联系客服反馈,我们会尽快为您处理(人工客服工作时间:9:00-18:30)。
一次法炼胶可行性报告
随着汽车工业和高速公路的快速发展,对于轮胎新技术的应用和发展提出了很高的要求,为了进一步改进胶料炼胶质量和克服高白炭黑(尤其胎面胶加大白炭黑的用量是发展趋势,它能降低轮胎的滚动阻力,增强干、湿路面的抓着力,节能、减排降低油耗,增强胶料的抗撕裂性,降低胶料生热,减少肩空等。
)含量炼胶硅烷化反应和混炼胶温度高易产生凝胶的技术难题,世界轮胎巨头纷纷不断研究和发展一次法炼胶技术。
其中米其林公司成功开发的OMS 炼胶,又称“一次法连续炼胶系统” 是米其林等公司成功开发的低温混炼系统。
随着一次法连续炼胶新技术进入中国的外资轮胎工厂推广使用,新技术使用对轮胎质量与性能的提高和生产成本的降低起到了决定性的作用。
一次法连续炼胶新技术在激烈的市场竞争中,为轮胎企业提供了提高炼胶质量和降低生产成本的技术平台,在保证胶料质量的前提下提高生产效率,并做到节能和环保,成了各大轮胎企业研究与追求的目标。
如三角集团上了3 套、赛轮1 套、三东聚源轮胎厂1 套、杭橡2 套本月交货、金宇7 月交货、红豆1 套明年初交货、盛泰和万达也准备上。
软控简绍上轮如皋、贵州轮胎、河南好友很快就要上。
一次法炼胶统工艺炼胶优、劣比较如下。
一、炼胶工艺比较:传统炼胶工艺:采用密炼机多段混炼,这种加工方法目的是实现橡胶分子链的断裂,主要采用高温氧化裂解,机械剪切为辅。
缺点:分子链分布范围较宽,容易生成大量的炭黑凝胶,影响各种配合剂的分散和物理性能。
一次法炼胶工艺:
采用密炼机一段混炼,在开炼机上加硫磺,这种加工方法大大加强了胶料的机械剪切,
弱化了高温氧化裂解的作用。
优点:炭黑及配合剂的分散更加均匀,避免炭黑凝胶的产生,提高了胶料的扯断强度、耐磨性和耐疲劳性,减少了粘合胶料的喷霜,提高了粘合胶料的粘性。
一次法炼胶对密炼机的选型与传统的不一样,传统密炼机(如F370/270、GK-400/255)转子一般都是四棱切线型,填充系数0.75。
而一次法炼胶密炼机一般
选GE320带有PES3转子,填充系数0.65时的有效容量约208立升与GE590T带有PES5转子串联,填充系数0.36时的有效容量约208立升。
二、胶料性能比较:
采用低温一次法生产全钢胶料时,由于其设备特点,为了保证硫化剂等的分散效
果,必须对硫化剂进行造粒或者加工成母炼胶形式,否则的话就会造成硫化剂分散不均匀或者生产效率降低(即添加硫化剂后需要延长捣胶时间)。
例如,目前贵州前进全部外购造粒硫化剂(从现场看均为广东泰信公司的产品),但造粒产品与不造粒产品相比,价格要贵1 万元/ 吨左右,扣除造粒用橡胶的影响,原材料价格也要贵2000 元/ 吨左右。
也就是说,一次法低温密炼机混炼一车胎冠胶胶料(其硫黄、促进剂至少需要3kg 以上),配方成本会增加6 元左右,如其它配方也在一次法低温混炼密炼机上生产,则配方成本增加更多(因为大部分配方的硫黄、促进剂用量比胎冠胶配方多)。
以胎冠胶生产为例,一次法混炼每天产量360 车,则每天配方成本增加2000 多元。
所以,如购置一次法低温密炼机,最好同时增加硫化剂造粒设备,以降低轮胎成本。
三、产能比较:
一次法产能简述:胶料在密炼机内混炼时间以3.5 分钟、220 公斤/车计算,单日炼胶量为70-80 吨终炼胶;按照现行全钢胶料平均段数2.7 段计算:一次法单日产能折合为:终炼胶80 吨,母炼胶136 吨;合计:216 吨;
现行F270终炼机台产能88吨,F370母炼机台产能140吨;合计:228吨,概括为:一次法工艺的一条生产线单日产能是一条F270 终炼,一条F370 母炼的总产能的92%。
四、电能消耗比较:
胶料按照传统工艺分析,按照胶料不同,工艺路线如下:胎面胶:1 段,2 段,加硫粘合胶料:母胶、1 段、2 段、加硫以胎面胶为例:1 、2 段在370,加硫在270,370 每车胶料330KG,270 每车胶料220KG。
1 段3 分钟,2段2.5分钟,加硫2.5分钟,则1吨胶料耗时:1段3* (1000/330) =9分钟2 段2.5* (1000/330) =8.25 分钟加硫2.5* (1000/220) =11.4 分钟合计:9+8.25+11.4=28.65分钟
采用低温一次法:采用270密炼机,单车胶料220KG,生产1吨胶料为15.9分钟。
机台装机容量:
采用传统工艺:
生产一吨胶料耗电量:
9*3182/60+8.25*3182/60+11.4*2081/60=1310KWH
采用低温线:
15.9*3933/60=1042KW
综上:生产1吨终炼胎面胶,电能消耗节约268KWH,电能节约比率:(1310-1042)/1310=20%。
(这是按装机容量计算);
实际全年节约电费=80*310*330*20%=94万元/年。
(全钢胶料段数多,而整体线
都采用变频调速,节约电耗应大于这个数,最高可达25%)。
五、人员配置比较:
采用传统工艺,1台255+1台400每班共需要操作人员10人;
采用低温一次法,1条生产线需要操作人员4人;
每天3班,可节约操作人员6*3=18人;
六、物流比较:
6.1、胶料停放周期
传统炼胶工艺从原材料库到终炼胶产成,至少需要两次停放时间,总计需要至
少10小时,加上物流周转和加工时间,理论上至少在12小时。
一次法工艺母炼终炼在一条生产线上完成,没有中间的停放,减少了至少两次的胶料周转运输。
理论上30分钟可以完成终炼胶产成品。
概括为:采用低温线可使原材料缩短至少11小时变为胶料成品。
6.2、周转库区
由于低温线没有中间停放,省掉了大量的周转厂房,以及周转用车和人。
节约用地面积40%二楼可节约1300 m2和大量存胶板。
七、隔离剂用量比较:
一次法炼胶与传统的炼胶,隔离剂用量可节约60%八、投资比较:
总之,一次法炼胶新技术,不但可以降低产品制造成本提高生产效率,而且能保证炼胶产品质量的一致性。
因此一次法连续炼胶新技术是节能环保型的混炼技术,项目具有十分显著的经济效益和社会效益。
但是,采用一次法连续炼胶新技术,前
期设备投资要大得多。
2012420。