熔体生长法-直拉法-1
熔体生长法-直拉法-1

25
300 200 25
固 气 气
将硅烷气体导入硅烷分解炉,在一个大气压, 800-900℃的发热硅芯上,硅烷分解并沉积出 高纯多晶硅,分解率达99.6%,主要反应
SiH 4 SiH 2 H 2 49.8kJ / mol SiH 2 Si H 2 SiH 2 H 2 SiH 4
方法:水平区熔法,悬浮区熔法,基座法和焰熔法
熔体生长法—正常凝固法—奇克劳斯基法
硅单晶生长为例(奇克劳斯基法,即提拉法)
材料
Zn
熔点℃ 坩锅材料 气氛
419
拉制速率mmh-1
转动速率 rpm
直 拉 法 制 备 的 晶 体 材 料
GaSb
FeGe2 Bi12GeO20
712
866 930
耐热玻璃 真空 氢气 石墨 铝 真空 铂 氧气 空气
组分
SiH4 SiH3Cl
沸点/℃
-111.8 -30.4
组分
SnCl4 CrO2Cl2
沸点/℃
113 116.7
SiH2Cl2
BCl3 SiCl4 PCl3
8.3
13 57.6 76
VOCl3
AsCl3 TiCl4 PCl5
127
130 136 160
CCl4
POCl3 SiHCl3
77
105.3 31.5
1600 1800o C
2 SiC SiO2 3Si 2CO
用石油焦和木炭作为碳还原剂是为了增加反应物的多孔性,以利 于CO和SiO气体的逸出; 经还原生成的硅熔体从电弧炉的下部流出,很快凝固成块体
制得的冶金级硅,经氯或氧精制后,可得到98~99%的精制冶金硅(MG-Si)
(2)硅片的制备

液相掺杂 ----分凝(segregation)与蒸发
液相掺杂可直接在坩埚内加入杂质元素制造特定电 阻率圆片。(直接掺杂) 对于固相-液相的界面,由于杂质在不同相中的溶解 度不一样,所以杂质在界面两边材料中分布的浓度 是不同的,这就是所谓杂质的分凝现象。 杂质分凝作用的大小描述----分凝系数k,定义为杂 质在固相中的溶解度与杂质在液相中的溶解度之比 k=Cs/Cl
Si + 3HCl → SiHCl3 + H2 Si + 2Cl2 → SiCl4
6
分解 discomposition 氢气易于净化,且在
Si 中 溶 解 度 极 低 , 因 此 , 多 用 H2 来 还 原
SiHCl3 和 SiCl4 ,还原得到的硅就是半导体纯
度的多晶硅。
SiCl4 + 2H2 →Si + 4HCl
酸洗
hydrochlorination
硅不溶于酸,所以粗硅初步
提纯是用 HCl 、 H2SO4 、王水、HF等混酸泡洗至S i 含量99.7%以上。--化学提纯
蒸馏提纯 distillation 利用物质的沸点不同,而在 精馏塔中通过精馏来对其进行提纯 ----物理提纯
先将酸洗过的硅氧化为 SiHCl3或 SiCl4 ,常温下 SiHCl3 (沸点 31.5℃),与 SiCl4( 沸点57.6℃)都是液态,蒸馏 获得高纯的SiHCl3或SiCl4。
目前拉制的单晶硅锭直径已 可达450mm,18英寸。
图2-1直拉法生长单晶硅装置示意图
10
直拉法-Czochralski法(CZ法)
在坩埚中放入多晶硅, 加热使之熔融,用一 个夹头夹住一块适当 晶向的籽晶,将它悬 浮在坩埚上,拉制时, 一端插入熔体直到熔 化,然后再缓慢向上 提拉,这时在液-固界 面经过逐渐冷凝就形 成了单晶。
晶体生长技术
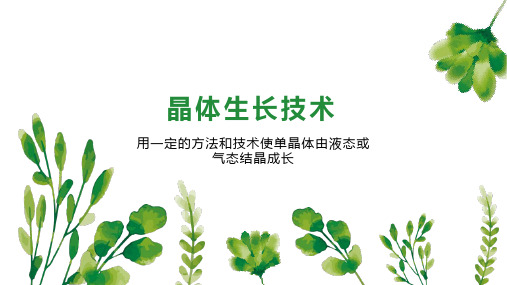
在高温高压下,通过各种碱性或酸性的水溶液使材料溶解而达到过饱和进而析晶的生长晶体方法叫水热生长 法。这个方法主要用来合成水晶,其他晶体如刚玉、方解石、蓝石棉以及很多氧化物单晶都可以用这个方法生成。 水热法生长的关键设备是高压釜,它是由耐高温、高压的钢材制成。它通过自紧式或非自紧式的密封结构使水热 生长保持在200~1000°C的高温及1000~10000大气压的高压下进行。培养晶体所需的原材料放在高压釜内温度 稍高的底部,而籽晶则悬挂在温度稍低的上部。由于高压釜内盛装一定充满度的溶液,更由于溶液上下部分的温 差,下部的饱和溶液通过对流而被带到上部,进而由于温度低而形成过饱和析晶于籽晶上。被析出溶质的溶液又 流向下部高温区而溶解培养料。水热合成就是通过这样的循环往复而生长晶体。
气相外延 材料在气相状况下沉积在单晶基片上,这种生长单晶薄膜的方法叫气相外延法,气相外延有开管 和闭管两种方式,半导体制备中的硅外延和砷化镓外延,多半采用开管外延方式。
液相外延 将用于外延的材料溶解在溶液中,使达到饱和,然后将单晶基片浸泡在这溶液中,再使溶液达到 过饱和,这就导致材料不断地在基片上析出结晶。控制结晶层的厚度得到新的单晶薄膜。这样的工艺过程称为液 相外延。这方法的优点是操作简单,生长温度较低,速率也较快,但在生长过程中很难控制杂质浓度的梯度等。 半导体材料砷化镓的外延层,磁泡材料石榴石薄膜生长,多半用这种方法。
这个方法是指在高温下把晶体原材料溶解于能在较低温熔融的盐溶剂中,形成均匀的饱和溶液,故又称熔盐 法。通过缓慢降温或其他办法,形成过饱和溶液而析出晶体。它类似于一般的溶液生长晶体。对很多高熔点的氧 化物或具有高蒸发气压的材料,都可以用此方法来生长晶体。这方法的优点是生长时所需的温度较低。此外对一 些具有非同成分熔化(包晶反应)或由高温冷却时出现相变的材料,都可以用这方法长好晶体。BaTiO3晶体及 Y3Fe5O12晶体的生长成功,都是此方法的代表性实例,使用此法要注意溶质与助熔剂之间的相平衡问题。
直拉单晶硅

方式称为“自然对流”。自然对流的
程度大小可由格拉斯霍夫常数来判定:
熔体
Gr agT d 3
Vk 2
对于硅而言,α=1.43×10-4℃-1,vk=3 ×10-3cm2/sec,
因此,Gr=1.56 ×104△Td3。此外,Gr的临界值为105,
而根据估计实际的Gr值高达108。除非靠其它的对流方式
籽晶
单晶硅棒
石英坩埚 水冷炉壁 绝热石墨 加热器 石墨坩埚 石墨底盘 石墨轴承 电极
在熔体结晶过程中, 温度下降时,将产生由液态 转变成固态的相变化。为什 么温度下降,会导致相变化 的产生呢?这个问题的答案 可由热力学观点来解释。
一个平衡系统将有最低的自由能,假如一个系统的自由能 G高于最低值,它将设法降低G(即△G < 0)以达到平衡 状态。因此我们可以将△G < 0视为结晶的驱动力。
判断 Bo Ra d 2g
Ma
所以在表面上较大的长晶系统
主要受自然对流控制。而表面张力对流在低重力状态(例
如太空中)及小的长晶系统,才会凸现其重要性。
思考题
1、直拉单晶炉由几大部分组成? 2、什么叫直拉单晶炉的热场 ? 3、直拉单晶炉的合理热场条件是什么? 4、直拉单晶硅的工艺步骤? 5、直拉单晶硅通常选择那些晶体生长方向,为什么? 6、直拉单晶硅中如何实现无位错生长? 7、直拉单晶硅中熔体的对流分哪几种情况,分别用什么 常数来判断其对流的程度?
自然对流、晶轴旋转和坩埚旋转三种方式相互作用对熔体 流动的影响。
表面张力引起的对流
由液体的温度梯度,所造成的
表面张力的差异,而引起的对流形
态,称为表面张力对流。其对流程
度大小可由Marangoni常数来判断
熔体中的晶体生长技术(提拉法)

2020/4/5
低维半导体材料及量子器件
22
2020/4/5
天然石榴石低维半导体材料及量子器件
23
YIG
2020/4/5
低维半导体材料及量子器件
24
YIG
2020/4/5
低维半导体材料及量子器件
25
人工合成GGG
2020/4/5
低维半导体材料及量子器件
26
天然形成的石榴石主要是金属的硅酸盐
48
边界层 厚度的 起伏
温场对称 晶体旋转
温场不对称
生长层的形成
生长 速率 起伏
机械振动
43
6 提拉法生长晶体缺陷的形成与控制
晶体在生长(或降温)过程中所以会产生缺陷, 大体上是由以下几个方面的因素造成的: a 物质条件; b 热力学因素; c 分凝和组分过冷; d 温度分布和温度波动.
2020/4/5
低维半导体材料及量子器件
44
• a物质条件:
包括生长设备的稳定性,有害杂质的影响, 籽晶。
2020/4/5
低维半导体材料及量子器件
28
石榴石生长的主要方法在于原料的区别和 是否考虑掺杂问题,一般生长过程包括以 下几个方面:
a 原料准备 b 保护气氛 c 生长条件 d 掺杂生长 e 晶体的透过率与颜色
2020/4/5
低维半导体材料及量子器件
29
• a 原料准备:Ga2O3(氧化镓)Gd2O3(氧化 钆)经过焙烧,脱水,按照比例配料,混合 后经压机压紧后在1250℃进行固相反应,充 分反应后的原料可供晶体生长使用。
• e 晶体的透过率与颜色:
2020/4/5
低维半导体材料及量子器件
31
纯GGG和掺杂Cr3+
1单晶硅片--(企业标准)

太阳能级单晶硅片1 范围本标准规定了太阳能级单晶硅片的术语和定义、技术要求、试验方法、检验规则、标志、包装、运输和贮存。
本标准适用于太阳能电池用的太阳能级单晶硅片(以下简称单晶硅片)。
2 规范性引用文件下列文件中的条款通过本标准的引用而成为本标准的条款。
凡是注日期的引用文件,其随后所有的修改单(不包括勘误的内容)或修订版均不适用于本标准,然而,鼓励根据本标准达成协议的各方研究是否可以使用这些文件的最新版本。
凡是不注日期的引用文件,其最新版本适用于本标准。
GB/T 2828.1-2003 计数抽样检验程序第1部分:按接收质量限(AQL)检索的逐批检验抽样计划3 术语和定义3.1本产品导电类型为p-型半导体硅片导电类型是指半导体材料中多数载流子的性质所决定的导电特性,本产品导电类型是p-型半导体,其多数载流子为空穴的半导体。
3.2杂质浓度单位体积内杂质原子的数目。
本产品的主要杂质是指氧含量、碳含量。
3.3体电阻率单位体积的材料对于两平行面垂直通过的电流的阻力。
一般来说,体电阻率为材料中平行电流的电场强度与电流密度之比。
符号为ρ,单位为Ω·cm 。
3.4四探针测量材料表面层电阻率的一种探针装置。
排列成一直线、间距相等的四根金属探针垂直压在样品表面上,使电流从两外探针之间通过,测量两内探针的电位差。
3.5寿命晶体中非平衡载流子由产生到复合存在的平均时间间隔,它等于非平衡少数载流子浓度衰减到其始值的1/e(e=2.718)所需的时间。
又称少数载流子寿命,简称少子寿命。
寿命符号τ,单位为μs 。
3.6孪晶在晶体中晶体是两部分,彼此成镜象对称的晶体结构。
连接两部分的界面称为孪晶或孪晶边界。
在金刚石结构中,例如硅,孪晶面为(111)面。
3.7单晶不含大角晶界或孪晶界的晶体。
3.8直拉法(CZ)本产品单晶硅的生长方式为直拉法,其工艺为沿着垂直方向从熔体中拉制单晶体的方法,又称切克劳斯基法,表示符号为CZ。
材料合成与制备第2章材料合成与制备的主要途径

第2章材料合成与制备的主要途径材料合成与制备的方法很多,从材料的物态上看,材料合成与制备的主要途径可以分为三种类型,即:基于液相—固相转变的材料制备;基于固相-固相转变的材料制备;基于气相—固相转变的材料制备。
2.1 基于液相—固相转变的材料制备基于液相—固相转变的材料制备一般可分为两类:一类是从熔体出发,通过降温固化得到固相材料,如果条件适合并且降温速率足够慢可以得到单晶体,如果采用快冷技术可以制备非晶(玻璃态)材料;另一类则从溶液出发,在溶液中合成新材料或有溶液参与合成新材料,再经固化得到固相材料。
2.2.1 从熔体制备单晶材料单晶材料的制备必须排除对材料性能有害的杂质原子和晶体缺陷。
低杂质含量、结晶完美的单晶材料多由熔体生长得到。
熔体生长中应用得最广的方法是直拉法(Czochralski法)生长。
直拉法的特点是所生长的晶体的质量高,速度快。
半导体电子工业所需的无位错Si单晶就是采用这种方法制备的。
图2.l是直拉法晶体生长的示意图。
熔体置于坩埚中,一块小单晶,称为籽晶,与拉杆相连,并被置于熔体的液面处。
加热器使单晶炉内的温场保证坩埚以及熔体的温度保持在材料的熔点以上,籽晶的温度在熔点以下,而液体和籽晶的固液界面处的温度恰好是材料的熔点。
随着拉杆的缓缓拉伸(典型速率约为每分钟几毫米),熔体不断在固液界面处结晶,并保持了籽晶的结晶学取向。
为了保持熔体的均匀和固液界面处温度的稳定,籽晶和坩埚通常沿相反的方向旋转(转速约为每分钟数十转)。
显然,这种旋转使得长成的单晶对转轴有柱面对称性。
高压惰性气体(如Ar)常被通人单晶炉中防止污染并抑制易挥发元素的逃逸。
对易挥发材料也可采用液封技术,即在熔体表面覆盖一层不挥发的惰性液体,如生长GaAs单晶时使用的液封材料是B2O3。
图2.1 直拉法单晶生长示意图1:籽晶;2:熔体;3、4:加热器坩埚下降法又称定向凝固法,也是一种应用广泛的晶体生长技术。
其基本原理是使装有熔体的坩埚缓慢通过具有一定温度梯度的温场,如图2.2所示。
硅锭的拉制方法

硅锭的拉制⽅法硅锭的拉制⽅法1*直拉法Cz (Czochralski )即切克⽼斯基法是⽤的最多的⼀种晶体⽣长技术2*悬浮区熔法:主要⽤于提纯和⽣长硅单晶3*多晶硅浇注法:⽤于制备多晶硅太阳电池所⽤的硅原⽚,它是⼀种定向凝固法,晶体呈现⽚状⽣长过程和结构单晶硅的制法通常是先制得多晶硅或⽆定形硅,然后⽤直拉法或悬浮区熔法从熔体中⽣长出棒状单晶硅。
熔融的单质硅在凝固时硅原⼦以⾦刚⽯晶格排列成许多晶核,如果这些晶核长成晶⾯取向相同的晶粒,则这些晶粒平⾏结合起来便结晶成单晶硅直拉法基本过程原理图⼀个典型cz⽣长炉⽰意图1.引晶:通过电阻加热,将装在⽯英坩埚中的多晶硅熔化,并保持略⾼于硅熔点的温度,将籽晶浸⼊熔体,然后以⼀定速度向上提拉籽晶并同时旋转引出晶体2.缩颈:⽣长⼀定长度的缩⼩的细长颈的晶体,以防⽌籽晶中的位错延伸到晶体中;3.等径⽣长:根据熔体和单晶炉情况,控制晶体等径⽣长到所需长度4.收尾:直径逐渐缩⼩,离开熔体;5.降温:降级温度,取出晶体,待后续加⼯6.最⼤⽣长速度:晶体⽣长最⼤速度与晶体中的纵向温度梯度、晶体的热导率、晶体密度等有关。
提⾼晶体中的温度梯度,可以提⾼晶体⽣长速度;但温度梯度太⼤,将在晶体中产⽣较⼤的热应⼒,会导致位错等晶体缺陷的形成,甚⾄会使晶体产⽣裂纹。
为了降低位错密度,晶体实际⽣长速度往往低于最⼤⽣长速度。
7熔体中的对流:相互相反旋转的晶体(顺时针)和坩埚所产⽣的强制对流是由离⼼⼒和向⼼⼒、最终由熔体表⾯张⼒梯度所驱动的。
所⽣长的晶体的直径越⼤(坩锅越⼤),对流就越强烈,会造成熔体中温度波动和晶体局部回熔,从⽽导致晶体中的杂质分布不均匀等8.⽣长界⾯形状(固液界⾯):固液界⾯形状对单晶均匀性、完整性有重要影响,正常情况下,固液界⾯的宏观形状应该与热场所确定的熔体等温⾯相吻合。
在引晶、放肩阶段,固液界⾯凸向熔体,单晶等径⽣长后,界⾯先变平后再凹向熔体。
通过调整拉晶速度,晶体转动和坩埚转动速度就可以调整固液界⾯形状9.连续⽣长技术:为了提⾼⽣产率,节约⽯英坩埚(在晶体⽣产成本中占相当⽐例),发展了连续直拉⽣长技术,主要是重新装料和连续加料两中技术:- 重新加料直拉⽣长技术:可节约⼤量时间(⽣长完毕后的降温、开炉、装炉等),⼀个坩埚可⽤多次。
最全的材料晶体生长工艺汇总

最全的材料晶体生长工艺汇总提拉法提拉法又称直拉法,丘克拉斯基(Czochralski)法,简称CZ法。
它是一种直接从熔体中拉制出晶体的生长技术。
用提拉法能够生长无色蓝宝石、红宝石、钇铝榴石、钆镓榴石、变石和尖晶石等多种重要的人工宝石晶体。
提拉法的原理:首先将待生长的晶体的原料放在耐高温的坩埚中加热熔化,调整炉内温度场,使熔体上部处于过冷状态;然后在籽晶杆上安放一粒籽晶,让籽晶下降至接触熔体表面,待籽晶表面稍熔后,提拉并转动籽晶杆,使熔体处于过冷状态而结晶于籽晶上,并在不断提拉和旋转过程中,最终生长出圆柱状的大块单晶体。
提拉法的工艺步骤可以分为原料熔化、引晶、颈缩、放肩、等径生长、收尾等几个阶段。
具体过程如示意图。
提拉法晶体生长工艺有两大应用难点:一是温度场的设置和优化;二是熔体的流动和缺陷分析。
下图为提拉法基本的温度场设置以及五种基本的熔体对流模式。
在复杂的工艺条件下,实际生产需要调整的参数很多,例如坩埚和晶体的旋转速率,提拉速率等。
因此实际中熔体的温度场和流动模式也更复杂。
下图是不同的坩埚和晶体旋转速率下产生的复杂流动示意图。
这两大应用难点对晶体生长的质量和效率都有很大影响,是应用和科研领域中最关心的两个问题。
通常情况下为了减弱熔体对流,人为地引入外部磁场是一种有效办法,利用导电流体在磁场中感生的洛伦兹力可以抑制熔体的对流。
常用的磁场有横向磁场、尖端磁场等。
下图是几种不同的引入磁场类型示意图。
引入磁场可以在一定程度上减弱对流,但同时磁场的引入也加大了仿真模拟的难度,使得生长质量预测变的更难,因此需要专业的晶体生长软件才能提供可靠的仿真数据。
晶体提拉法有以下优点:(1)在晶体生长过程中可以直接进行测试与观察,有利于控制生长条件;(2)使用优质定向籽晶和“缩颈”技术,可减少晶体缺陷,获得优质取向的单晶;(3)晶体生长速度较快;(4)晶体光学均一性高。
晶体提拉法的不足之处在于:(1)坩埚材料对晶体可能产生污染;(2)熔体的液流作用、传动装置的振动和温度的波动都会对晶体的质量产生影响。
氧化镓 直拉法

氧化镓直拉法是一种制备单晶氧化镓的方法,其基本原理是在高温下通过化学反应将氧化镓粉末转化为熔体,然后通过拉伸法生长出单晶氧化镓。
具体步骤如下:
1. 准备氧化镓粉末:将高纯度的氧化镓粉末放入高温炉中,加热至一定温度,使其完全转化为熔体。
2. 拉伸法生长:将熔体倒入一个特制的坩埚中,然后通过加热坩埚底部的方式,使熔体在坩埚内上升,并在一定的温度下逐渐形成单晶氧化镓。
在生长过程中,需要通过控制温度和生长速度来控制晶体的质量和尺寸。
3. 切割和抛光:将生长出来的单晶氧化镓取出,进行切割和抛光,以得到所需的形状和尺寸。
氧化镓直拉法的优点是可以制备出高质量的单晶氧化镓,而且生长速度较快,适用于大规模生产。
缺点是需要高温高压的条件,设备成本较高,同时也需要较高的技术水平和经验。
chap.6 硅的晶体生长
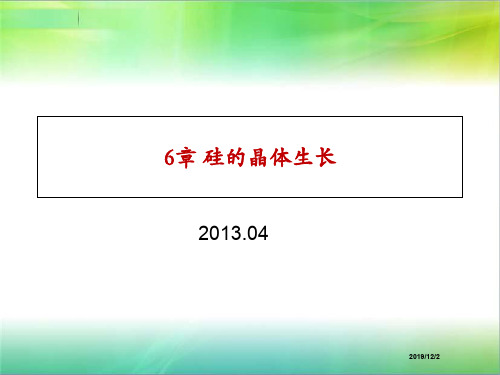
2019/12/2
由自发晶核形成的晶体,一般成为多晶体,极难形成单 晶体。 因此,在拉单晶时,不希望产生自发晶核,要求:人为 加入一个籽晶,同时严格控制熔体中的温度梯度和结晶 界面的“过冷度”,使结晶界面附近以外的熔体处在高 于熔点的过热状态。从而使熔体仅沿籽晶一个晶核结晶, 长大成为单晶体。
95炉技术规格: 拉制晶棒直径 6"、8"或非标 最大装料量: 135kg 适用热场规格: 20";22" 适用石英坩埚规格: 20";22" 最大长晶长度: 2010mm 籽晶轴行程: 3200mm 籽晶提升速度(低): 0~10mm/min 籽晶提升速度(高): 800mm/min 籽晶旋转速度: 0~40rpm 坩埚升降速度(低): 0.000~0.500mm/min 坩埚升降速度(高): 100mm/min 坩埚轴最大承重: <230kg 坩埚转速: 0~20rpm 坩埚升降轴行程: >380mm 设备最大高度: 7300mm 冷却水流量: 280-320L/min 冷却水温度: 最宜15-30度(合适30以下不结冰) 极限真空度: <3mT 真空漏率: <0.4mT/min 籽晶绳材质: 钨质 中炉筒内径: 950mm
6章 硅的晶体生长
2013.04
2019/12/2
1 引言 2 直拉法(CZ法)制备单晶硅 3 MCZ工艺 4 悬浮区熔法(FZ法)制备单晶硅工艺 5多晶硅铸锭制备技术 6 掺杂工艺
2019/12/2
1引言
•单 晶 硅 的 制 备 按 晶 体 生 长 方 法 的 不 同 , 分 为 直 拉 法 (CZ:Czochralski) 、悬浮区熔法(FZ:Float Zone)和外延法。 直拉法、区熔法生长单晶硅棒材,外延法生长单晶硅薄膜。 半导体工业上大约超过75%的单晶硅锭是由CZ法制备的, 1952年Teal和Buehler首次报道了CZ法制备硅单晶,Dash首 次介绍了无位错单晶硅锭的生长技术。
一文看懂氧化镓
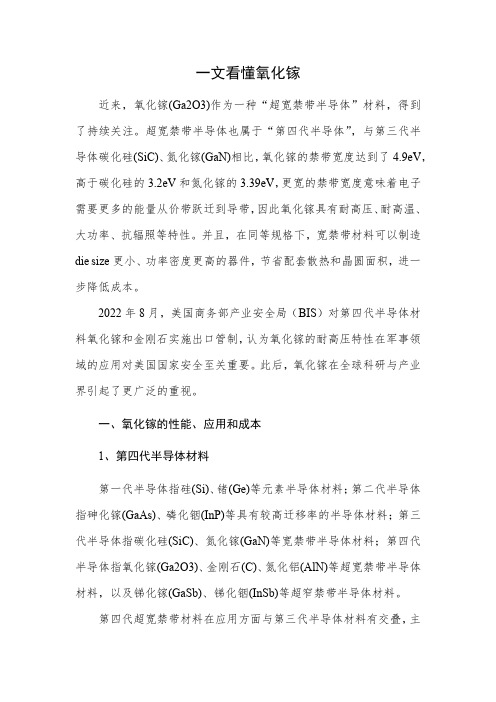
一文看懂氧化镓近来,氧化镓(Ga2O3)作为一种“超宽禁带半导体”材料,得到了持续关注。
超宽禁带半导体也属于“第四代半导体”,与第三代半导体碳化硅(SiC)、氮化镓(GaN)相比,氧化镓的禁带宽度达到了4.9eV,高于碳化硅的3.2eV和氮化镓的3.39eV,更宽的禁带宽度意味着电子需要更多的能量从价带跃迁到导带,因此氧化镓具有耐高压、耐高温、大功率、抗辐照等特性。
并且,在同等规格下,宽禁带材料可以制造die size更小、功率密度更高的器件,节省配套散热和晶圆面积,进一步降低成本。
2022年8月,美国商务部产业安全局(BIS)对第四代半导体材料氧化镓和金刚石实施出口管制,认为氧化镓的耐高压特性在军事领域的应用对美国国家安全至关重要。
此后,氧化镓在全球科研与产业界引起了更广泛的重视。
一、氧化镓的性能、应用和成本1、第四代半导体材料第一代半导体指硅(Si)、锗(Ge)等元素半导体材料;第二代半导体指砷化镓(GaAs)、磷化铟(InP)等具有较高迁移率的半导体材料;第三代半导体指碳化硅(SiC)、氮化镓(GaN)等宽禁带半导体材料;第四代半导体指氧化镓(Ga2O3)、金刚石(C)、氮化铝(AlN)等超宽禁带半导体材料,以及锑化镓(GaSb)、锑化铟(InSb)等超窄禁带半导体材料。
第四代超宽禁带材料在应用方面与第三代半导体材料有交叠,主要在功率器件领域有更突出的应用优势。
第四代超窄禁带材料的电子容易被激发跃迁、迁移率高,主要应用于红外探测、激光器等领域。
第四代半导体全部在我国科技部的“战略性电子材料”名单中,很多规格国外禁运、国内也禁止出口,是全球半导体技术争抢的高地。
第四代半导体核心难点在材料制备,材料端的突破将获得极大的市场价值。
2、氧化镓的晶体结构和性质氧化镓有5种同素异形体,分别为α、β、γ、ε和δ。
其中β-Ga2O3(β相氧化镓)最为稳定,当加热至一定高温时,其他亚稳态均转换为β相,在熔点1800℃时必为β相。
熔体生长法-布里奇曼法和区熔法
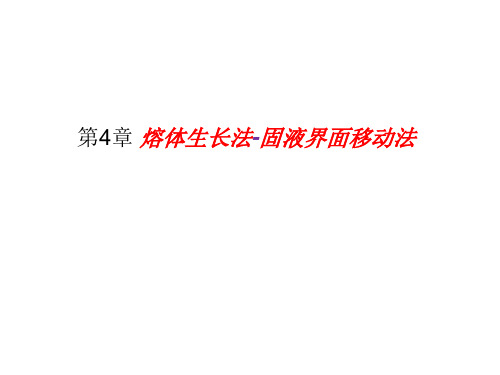
铱 磨沙的二氧化硅 石墨粉 涂的碳或石墨的二氧化硅 厚壁二氧化硅 耐热玻璃 聚四氟乙烯 涂石蜡的不锈刚 聚脂薄膜
以碲锌镉为例介绍垂直布里奇曼法 垂直布里奇曼法
优点:
• 获得化学计量比控制的单晶,成分易控制 • 晶体外形尺寸可控 • 减少污染
缺点:
• 不能生长体积变大的材料 • 晶体和坩锅接触易产生应力和多晶核生长 • 坩锅对材料沾污 • 生长速度慢,周期长 (一个月左右) • 生长过程不能直接观察,晶体缺陷难控制
• 原因:
➢ 在高温下,石英管中的杂质容易扩散到晶体中 ➢ CZT中的Cd在高温下会与石英发生反应,生成硅酸镉
(Cd2SiO4),导致晶体与石英管的粘连,不利于从坩埚中取出
晶体;当晶体的收缩比坩埚大时,二者之间的连接就产生大的应 力,导致位错的增加 ➢ 在晶体生长时引入形核中心,造成径向的形核与生长,严重影响 晶体生长的质量,还可能会引起石英管的开裂
✓凸界面:有利于晶粒的淘汰,使杂质与缺陷向晶体壁 面扩散和延伸
✓凹界面:边缘部分先生长,易形成多晶,杂质易聚集 在晶体内部,对晶体的均匀性和完整性不利,也易产 生内应力
影响固液界面形状的因素
•材料的热导率和结晶潜热是两个主要内因
•坩锅下降速度和温度梯度是两个外因 ;下降速度越 大,固液界面越凸向固体;温度梯度越大,固液界面
开始高,低温炉同时升至615℃;然后将低温炉温炉恒 温于615℃,高温端升至1250 ℃恒温;
• 稼的熔点为29.8 ℃,它在砷化稼熔点的高温区,呈液 态,与低温区提供的砷蒸汽发生发应
• 将砷端的温度控制在使系统中的砷压达到离解压
(0.936个大气压,非常重要),使砷原子溶入液相砷
化稼中,使液相砷化稼,含砷的百分比增加到50%
第四章熔体中晶体生长技术提拉法
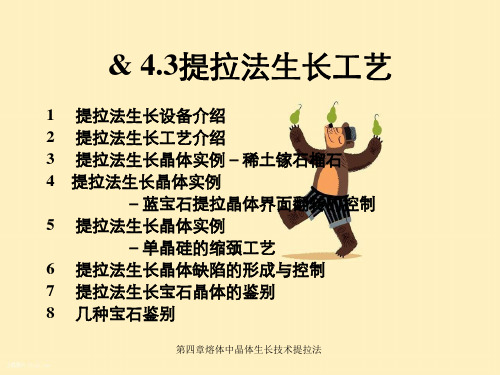
第四章熔体中晶体生长技术提拉法
在这三类稀土石榴石中,稀土铁石榴石(YIG) 不透明,难以用作装饰品;
稀土铝石榴石(YAG)存在折射率不够高,不 易掺质.
第四章熔体中晶体生长技术提拉法
旋转引起条纹
第四章熔体中晶体生长技术提拉法
• d 温度波动和生长层 产生温度波动波动的原因有二 i熔体本身的热流不稳定性造成温度的起伏和振 荡。 ii生长条件的变化 我们把在晶体中溶质浓度的不均匀层称为 生长层(条纹)。生长层是晶体生长,特别是 熔体生长过程中经常出现的微观缺陷之一。
第四章熔体中晶体生长技术提拉法
边界层 厚度的 起伏
温场对称 晶体旋转
稀土镓石榴石(GGG)由于其本身的结构特点, 不但能进行多种形式的掺质,而且通过辐照还可 以形成稳定的色心,使其单晶体呈现绚丽多彩的 漂亮颤色,最适宜作为装饰宝石材料。常用的掺 质元素为:Cr,Co,Ni等过渡族元素氧化物和稀土 Nd,Er的氧化物。
第四章熔体中晶体生长技术提拉法
石榴石生长的主要方法在于原料的区别和 是否考虑掺杂问题,一般生长过程包括以 下几个方面: a 原料准备 b 保护气氛 c 生长条件 d 掺杂生长 e 晶体的透过率与颜色
温场不对称
生长层的形成
生长 速率 起伏
机械振动
温度起伏 籽晶杆 蠕动
熔体非稳 流动
浮力干扰 湍流
加热功率 起伏
压力引起 凝固点的
起伏 第四章熔体中晶体生长技术提拉法
热损耗 起伏
• 7 提拉法生长宝石晶体的鉴别 1.提拉法生长的宝石晶体,由于提拉和 旋转作用,会产生弯曲的弧形生长纹。 或者由于固液界面产生的振动或温 度的波动,可使晶体的溶质浓度分布不 均,因而形成晶体不均匀的生长条纹。
单晶硅生长技术及氧缺陷控制方法2100字

单晶硅生长技术及氧缺陷控制方法2100字摘要:本文介绍了单晶硅的基本概念和用途,并对单晶硅的几种主要制备方法做了简单介绍。
同时结合生产实际经验,对单晶硅中的主要杂质――氧,提出了几种控制方法。
关键词:单晶硅;生长技术;氧缺陷1 单晶硅的概念半导体材料的电学性质和其他物理性质对晶格缺陷以及所含杂质的种类和数量非常敏感。
制作各种半导体器件,尤其是集成电路和大规模集成电路的制作更需要均匀性好的大直径完善单晶。
目前不仅能制造无位错的完善单晶,而且还可以将位错密度控制在一定范围内[1]。
无位错单晶的直径已达到200mm规格化。
2 单晶硅的生长方法生长单晶的方法有很多种,但基本上可分为:从熔体中的生长法、从溶剂的溶液中生长法和气相生长法[2]。
从熔体中生长单晶的方法,根据具体的工艺又分为立式和水平布里支曼法、立式和水平区溶法、直拉法和粉末法等。
立式区熔法又称无坩埚区熔法。
从溶液中生长单晶的方法有溶剂层移动法,液相外延法等。
从气相生长单晶方法,又可分为热分解或氢还原CVE、利用歧化反应的CVE以及分子束外延法等。
体单晶硅的制备主要用直拉法和区溶法。
薄层单晶硅的制备主要用硅的化合物热分解或氢还原的CVE及分子束外延法。
直拉法又称为乔赫拉尔斯基法。
这种方法生长的单晶硅径向杂质分布比较均匀,但纵向分布就差一些。
另外,拉制单晶时熔体直接与石英坩埚接触,会引进一些氧原子及碳沾污。
目前用区熔法能生长直径100mm,长1m以上的单晶硅,这种单晶中纵向杂质分布比较好,但径向分布不如直拉法的单晶。
用气相外延法(如SiH4的热分解或SiCl4氢还原)能够制备质量非常好的薄层单晶,一般器件大多制作在这个外延层中。
气相外延是目前在器件生产中不可缺少的工艺。
为了满足器件对材料的导电类型和电阻率的要求,在直拉法中采用在熔体中掺杂的方法,在无坩埚区熔中采用的掺杂方法有多种。
前些年,我国主要采用溶液掺杂法,最近提出了一些新的行之有效的掺杂方法。
直拉法

缩 颈
生长一定长度的缩小的细长颈的晶体 缩颈的目的就是排位错 位错产生的原因 缩颈的方法
放肩/转肩
放肩:将晶体控制到所需直径 转肩:从放肩转入等径生长 降低温度,降低拉速
等径生长
保持晶体的直径生长 晶体直径要稍大于目标直径以利于滚磨 直径--- 温度,拉速
直径的控制
A (Q Q ) / LV
S L
S
Q
Q
S
单位时间内耗散到环境中的热量
L
单位时间通过熔体传至固液界面的热量
理论值:2.96cm/s (Runyan )
实验值:2.53cm/s
收尾
等径生长完成后,将晶棒直径慢慢缩小至 一尖点再与熔体分离 避免生长界面突然脱离熔体时温度的突变 产生位错和向上滑移 一般要求尾部长度大于一个等径直径
降温
单晶硅生长完成后晶棒需要被逐渐冷却至 常温 原因 方法
硅中的氧
硅中氧的来源 硅中氧的基本性质 氧施主效应 氧沉淀对硅材料和器件的影响 硅单晶的初始状态和氧沉淀 影响氧沉淀的因素
硅中的碳
硅中碳的来源 硅中碳的基本性质 硅中碳的危害 硅中碳的控制
引晶 缩颈 放肩 等径生长 收尾 降温
Czochralski (CZ) Method
Wafer
炉子示意图
直拉法:柴科夫斯基(CZ)法 籽晶 线圈
引晶
通过电阻加热,将装在石英坩埚中的多晶 硅熔化,并保持略高于硅熔点的温度,将 籽晶浸入熔体,然后以一定速度向上提拉 籽晶并同时旋转引出晶体.
蓝宝石晶体主要生长方法和研究现状
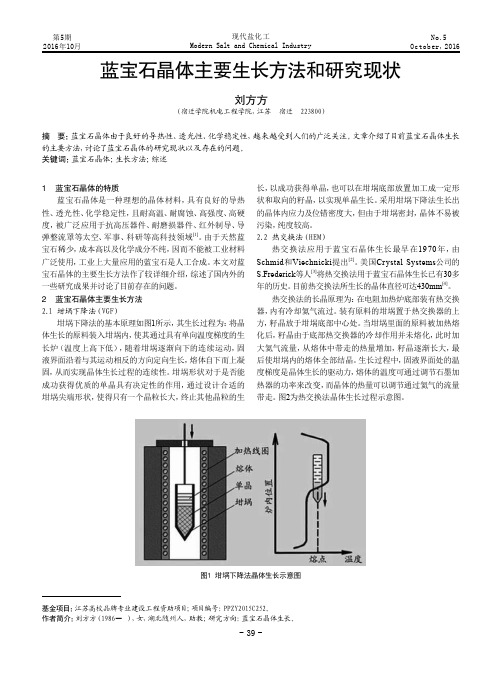
1 蓝宝石晶体的特质蓝宝石晶体是一种理想的晶体材料,具有良好的导热性、透光性、化学稳定性,且耐高温、耐腐蚀、高强度、高硬度,被广泛应用于抗高压器件、耐磨损器件、红外制导、导弹整流罩等太空、军事、科研等高科技领域[1]。
由于天然蓝宝石稀少,成本高以及化学成分不纯,因而不能被工业材料广泛使用,工业上大量应用的蓝宝石是人工合成。
本文对蓝宝石晶体的主要生长方法作了较详细介绍,综述了国内外的一些研究成果并讨论了目前存在的问题。
2 蓝宝石晶体主要生长方法2.1 坩埚下降法(VGF )坩埚下降法的基本原理如图1所示,其生长过程为:将晶体生长的原料装入坩埚内,使其通过具有单向温度梯度的生长炉(温度上高下低),随着坩埚逐渐向下的连续运动,固液界面沿着与其运动相反的方向定向生长,熔体自下而上凝固,从而实现晶体生长过程的连续性。
坩埚形状对于是否能成功获得优质的单晶具有决定性的作用,通过设计合适的坩埚尖端形状,使得只有一个晶粒长大,终止其他晶粒的生长,以成功获得单晶,也可以在坩埚底部放置加工成一定形状和取向的籽晶,以实现单晶生长。
采用坩埚下降法生长出的晶体内应力及位错密度大,但由于坩埚密封,晶体不易被污染,纯度较高。
2.2 热交换法(HEM)热交换法应用于蓝宝石晶体生长最早在1970年,由Schmid 和Viechnicki 提出[2]。
美国Crystal Systems 公司的S.Frederick 等人[3]将热交换法用于蓝宝石晶体生长已有30多年的历史。
目前热交换法所生长的晶体直径可达430mm [4]。
热交换法的长晶原理为:在电阻加热炉底部装有热交换器,内有冷却氦气流过。
装有原料的坩埚置于热交换器的上方,籽晶放于坩埚底部中心处。
当坩埚里面的原料被加热熔化后,籽晶由于底部热交换器的冷却作用并未熔化,此时加大氦气流量,从熔体中带走的热量增加,籽晶逐渐长大,最后使坩埚内的熔体全部结晶。
生长过程中,固液界面处的温度梯度是晶体生长的驱动力,熔体的温度可通过调节石墨加热器的功率来改变,而晶体的热量可以调节通过氦气的流量带走。
第九章 单晶硅制备-直拉法
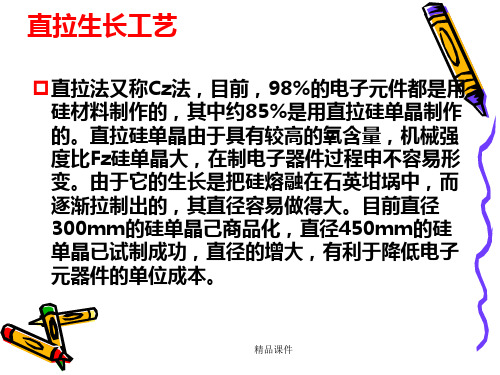
后,升温升拉速进行转肩生长。 转肩完后,调整拉速和温度,使晶体直径偏差维持在
±2mm范围内等径生长。这部分就是产品部分,它的 质量的好坏,决定着产品的品质。 热场的配置、拉晶的速率、晶体和坩埚的转速、气体 的流量及方向等,对晶体的品质都有影响。这部分生 长一般都在自动控制状态下进行,要维持无位错生长 到底,就必须设定一个合理的控温曲线(实际上是功率 控制曲线)。
精品课件
1、CZ基本原理
➢ 在熔化的硅熔液中 插入有一定晶向的籽晶, 通过引细晶消除原生位 错,利用结晶前沿的过 冷度驱动硅原子按顺序 排列在固液界面的硅固 体上,形成单晶。
固液界面过冷度
2 CZ基本工艺
CZ过程需要惰性气体保护! 现有的CZ都采用氩气气氛减压拉晶。
利用通入惰性气体氩气,结合真空泵的抽 气,形成一个减压气氛下的氩气流动。氩 气流带走高温熔融硅挥发的氧化物,以防 止氧化物颗粒掉进硅熔液,进而运动到固 液界面,破坏单晶原子排列的一致性。
1. melting
4. pulling the neck of the crystal
2. temperature stabilisation
5. growth of shoulder
3. accretion of seed crystal
6. growth of body
直拉生长工艺
⑤晶颈生长 硅料熔化完后,将加热功率降至引晶位置,坩埚也置
精品课件
4、 石英坩埚
两个检查步骤
主要检查事项: ➢ 1未熔物; ➢ 2白点和白色附着物; ➢ 3杂质(包括黑点); ➢ 4划伤和裂纹; ➢ 5气泡; ➢ 6凹坑和凸起; ➢ 7坩埚重量。
- 1、下载文档前请自行甄别文档内容的完整性,平台不提供额外的编辑、内容补充、找答案等附加服务。
- 2、"仅部分预览"的文档,不可在线预览部分如存在完整性等问题,可反馈申请退款(可完整预览的文档不适用该条件!)。
- 3、如文档侵犯您的权益,请联系客服反馈,我们会尽快为您处理(人工客服工作时间:9:00-18:30)。
杂质:10%左右的SiCl4以及少许SiH2Cl2 ,SiH3Cl以及其他少许Al, Fe, C ,P, Ca, Ag, Mg, Zn, Ti, Ni, Cr, Cu, As, Sb等氯化物
液封器
三
氯 硅粉干燥器 氢 硅 合 成 螺旋加料器 设 备 示 意 图
列管冷凝器
旋风过滤除尘器 合成炉 计量器
1600 1800o C
2 SiC SiO2 3Si 2CO
用石油焦和木炭作为碳还原剂是为了增加反应物的多孔性,以利 于CO和SiO气体的逸出; 经还原生成的硅熔体从电弧炉的下部流出,很快凝固成块体
制得的冶金级硅,经氯或氧精制后,可得到98~99%的精制冶金硅(MG-Si)
高纯硅的制备:三氯氢硅+精馏+还原
主要副产 物:SiCl4
280 300o C
Si 3SiCl4 2 H 2 4 SiHCl3 SiHCl3 SiCl4 3H 2 2 Si 7 HCl SiH 2Cl2 Si 2 HCl
• 为了减少副产品,要采取以下措施
400-800
10-30
50-100
5-20 5-15 8-16 20-30
10-30
20-50 10-50
Ge
ZnWO4 GaAs
937
1200 1237
石墨 铂
氢气,氮气 60-120
20-50
50-100 10-30
LiNbO3
SrXBa1-XNb2O6
1250
1400 1420
二氧化硅 氩气 铂 氧气 铂 氧气 二氧化硅 氩气 铱 铑 铱 空气 氮气
废 气 淋 洗 塔
氯化氢缓冲罐
粗三氯氢硅储槽
精馏
• 粗三氯氢硅→含有杂质,如硼,磷,铁,铜等的氯 化物,提纯除去这些杂质 • 精镏过程:在塔内被蒸液体的蒸汽→自下向上流动 →升入塔顶→被冷凝成液体→自上而下流动→连续的 气液二相接触→产生传热和传质现象
• 精馏→有效提纯手段,一次全过程,纯度从98% → 9个9或10个9,而且可连续大量生产
熔体生长方法分类
• 正常凝固法
特点:开始生长时,除籽晶外全为熔体,生长时
不再向熔体添加材料,以晶体的长大和熔体的减少 而告终
方法:
晶体提拉法 坩埚移动法 晶体泡生法 弧熔法
• 逐区熔化法
特点:
体系由晶体,熔体和多晶原料三部分组成 体系中存在二个固-液界面,一个界面上发生结晶过 程,另一个界面上发生多晶原料的熔化过程,熔区 向多晶原料移动 熔区体积不变,不断向熔区中添加材料 生长以晶体的长大和多晶原料的耗尽而结束
制备三氯氢硅 工业上常用方法:干燥氯化氢气体和硅粉(粗硅或工业 硅)反应,制得三氯氢硅
工业硅→酸洗→粉碎→选符合粒度要求硅粉(80-120目)→送入 干燥炉→热氮气流干燥→送入沸腾炉 炉底通入适量的干燥HCl(直接合成),进行三氯氢硅合成
酸洗:依次用盐酸,王水(浓盐酸:浓硝酸=3:1),混合酸
这是放热反应,考虑以适当的冷媒,将反应产生的热量带走,反应 温度在280-300℃(温度控制问题) 反应炉中,适量氢气稀释氯化氢气体,提高三氯氢硅的产率,氢气: 氯化氢气体=1:3~5 硅粉与氯化氢,在反应前,充分干燥(水分问题);硅粉粒度在75~ 177um;严格控制硅粉料层厚度及氯化氢流量,这是反应稳定进行 的关键之一,也是产品质量稳定的关键 合成时,加入少量铜,银,镁合金作催化剂,降低合成温度,提高 三氯氢硅产率
75oC冷却 剂出入口
Mg2Si和NH4Cl 混和料储槽 液氨回流柱 液氨加入管 螺旋下料器 硅烷发生器 -30oC冷却 剂出入口 保温层
排渣阀
固体吸附法
• 可用低温精馏和吸附法提纯,硅烷沸点太低,不同低 温精馏,多用分步吸附法提纯 0.4nm分子筛→除去氨气,水,一部分的磷烷,砷烷, 乙炔,硫化氢 0.5nm分子筛→除去余下的氨气,水,磷烷,砷烷, 乙炔,硫化氢,吸附B2H6,Si2H6 13X分子筛→除烷烃,醇等有机大分子 用常温和低温二级活性炭-除B2H6,砷烷,磷烷
• 硅的基本情况 • 高纯硅的制备 • 直拉法生产硅单晶 • 晶锭的处理
硅的基本情况:
Si lattice constant = 5.431Å 5 x 1022 atoms/cm3
I. 第四族元素,具有银白色金属光泽,其 晶体硬而脆 II. 熔体密度比固体大,熔化后体积收缩 10%,具有明显热膨胀及热传导 III. 硅在地壳中含量25.8% ,仅次于氧 IV. 室温下化学性质稳定,不和空气,水和 酸反应,可与强碱,酸作用 V. 高温下与氧,卤素,碳等反应 “diamond” structure VI. 自然界来源:氧化硅和硅酸盐;无单质 The Si Crystal
升高还原温度→还原反应有利;升高温度→生成粗 大,光亮硅粒;温度低,结晶粒度小,呈暗灰色。 温度不可过高→不利于硅向载体沉积;使三氯化硼 和三氯化磷还原→增大硼,磷污染;硅活性大→受 材质污染增大 要控制氢量,氢量太大→浪费,降低产率;氢量太 小→三氯氢硅还原不充分(氢:三氯氢硅=10:1); 不利于P,B挥发析出 高纯多晶硅纯度→用其残留硼,磷含量表示→称为 基硼量,基磷量 我国高纯硅:基硼量≤5×10-11,基磷量≤10-10
气 气 气
25
300 200 25
固 气 气
将硅烷气体导入硅烷分解炉,在一个大气压, 800-900℃的发热硅芯上,硅烷分解并沉积出 高纯多晶硅,分解率达99.6%,主要反应
SiH 4 SiH 2 H 2 49.8kJ / mol SiH 2 Si H 2 SiH 2 H 2 SiH 4
液相从塔顶到塔底→易挥发组分的浓度下降,难挥 发组分浓度增大→最后全是难挥发组分液体 从而达到分离提纯混合液体的目的
三氯氢硅氢还原
精馏的三氯氢硅+高纯氢气=1:(10~20)→送还原炉
1100℃左右,还原反应,制得高纯多晶硅 伴有三氯氢硅热分解和四氯化硅还原 主要反应方程式
SiHCl3 H 2 Si 3HCl
• 硅烷热分解 吸附后的硅烷→经热分解提纯(380℃)
名称
B2H6
状态 分解温度/℃ 名称
气
300 SnH4
状态 分解温度/℃
气
150
(AsH3)X 固
(GaH3)2 液 (InH3)X SiH4 GeH4
110-160
130 >80 >600 340~360
PbH4
AsH3 SbH3 BiH3
气
1100O C
副反应
4 SiHCl3 Si 3SiCl4 2 H 2 SiCl4 2 H 2 Si 4 HCl
热交换器(预冷器)
载体
炉体
尾气回收器
喷头 挥发器
气液分离器
氢还原工艺系统
精镏后SiHCl3→送入挥发器 氢气分二路,一路进还原炉;另一路通入SiHCl3液 体中,使SiHCl3挥发,与直接进入的氢气汇合→经喷 头进入还原炉 氢与SiHCl3的混合气体→连续的进入还原炉→还原反 应,在载体上→沉积出多晶硅 尾气中的SiHCl3需回收→尾气从还原炉底部排出→ 经热交换器预冷→进入尾气回收器→冷凝回收 再经气液分离器→液化的SiHCl3与氢气分离→回收的 SiHCl3 →返回挥发器或精镏再处理 未冷凝的氢气→经过热交换器→送去净化处理→净 化后作还原剂
液氨 30O C
• 硅烷生产过程:
生成的硅皖→液氨回流柱→进入纯化系统→硅皖 带走的氨气在回流器中液化→返回到发生器中 →硅皖中的杂质乙硼烷与氨络合→生成固态络 合物B2H6· 2HN3,在排渣时排除,生成的硅烷不 含硼杂质,这是硅烷法的优点之一
反应产物出口 氨回流冷凝气
硅
烷 气 发 生 系 统
高纯硅的制备:硅烷法+固体吸附法+分解 硅烷的制备
在液氨中,硅化镁和氯化氨反应,生成硅皖
液氨既是溶剂也是催化剂 (日本小松电子株式会社 Komatsu使用此法,原料消耗量大,成本高,危险性大)
1,Mg2Si:NH4Cl=1:3
2,Mg2Si:液氨=1:10,加进液氨Fra bibliotek反应方程式
SiH 4 4 NH 3 2MgCl2 192.5kJ / mol Mg 2 Si 4 NH 4Cl
组分
SiH4 SiH3Cl
沸点/℃
-111.8 -30.4
组分
SnCl4 CrO2Cl2
沸点/℃
113 116.7
SiH2Cl2
BCl3 SiCl4 PCl3
8.3
13 57.6 76
VOCl3
AsCl3 TiCl4 PCl5
127
130 136 160
CCl4
POCl3 SiHCl3
77
105.3 31.5
氧化硅: 一种坚硬,脆性,难熔的无色固体; 1600℃下熔化成粘稠液体,冷却后呈玻璃态; 膨胀系数小,抗酸,可用它做各种器皿
制备粗硅或工业硅
95%-99%的硅称为粗硅或工业硅 是用较纯净石英砂与木炭或石油焦在碳电极的电弧 炉中还原制得的,主要杂质为铁,铝,碳,硼,铜等 主要反应式
SiO2 3C SiC 2CO
方法:水平区熔法,悬浮区熔法,基座法和焰熔法
熔体生长法—正常凝固法—奇克劳斯基法
硅单晶生长为例(奇克劳斯基法,即提拉法)
材料
Zn
熔点℃ 坩锅材料 气氛
419
拉制速率mmh-1
转动速率 rpm
直 拉 法 制 备 的 晶 体 材 料
GaSb
FeGe2 Bi12GeO20
712
866 930