船用液压系统串油工艺
液压系统换油操作工艺流程

液压系统换油操作工艺流程
一、液压系统检查与准备
1.确保液压系统处于停止状态
2.准备所需工具和设备
3.确认换油所需油品和滤芯
二、液压系统排油
1.打开液压系统的排油阀门
2.让液压系统中的油完全排空
3.检查并清洁排油阀门
三、液压系统清洗
1.使用清洁剂对液压系统进行清洗
2.冲洗液压管道和油箱
3.确保清洗彻底,无杂质残留
四、更换油品和滤芯
1.加注新的液压油
2.更换液压系统中的滤芯
3.注意新油品牌和型号的匹配
五、液压系统充油
1.关闭排油阀门
2.开始加注新的液压油
3.充满液压系统,并排除气泡
六、液压系统压力测试
1.启动液压系统,检查压力表读数
2.观察系统运行是否正常
3.调整液压系统压力参数
七、系统检查与调试
1.检查液压系统是否有漏油现象
2.检查液压系统各部件工作是否正常
3.调试系统参数,确保系统正常运行。
船舶主辅机燃油管串油工艺
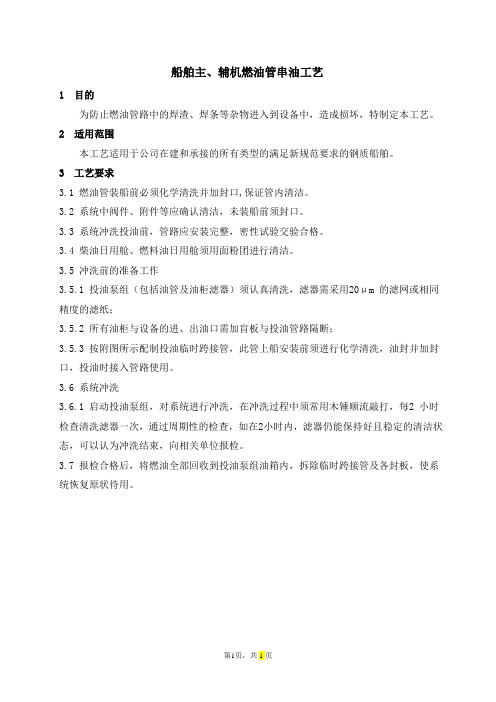
船舶主、辅机燃油管串油工艺
1 目的
为防止燃油管路中的焊渣、焊条等杂物进入到设备中,造成损坏,特制定本工艺。
2 适用范围
本工艺适用于公司在建和承接的所有类型的满足新规范要求的钢质船舶。
3 工艺要求
3.1 燃油管装船前必须化学清洗并加封口,保证管内清洁。
3.2 系统中阀件、附件等应确认清洁,未装船前须封口。
3.3 系统冲洗投油前,管路应安装完整,密性试验交验合格。
3.4 柴油日用舱、燃料油日用舱须用面粉团进行清洁。
3.5 冲洗前的准备工作
3.5.1 投油泵组(包括油管及油柜滤器)须认真清洗,滤器需采用20μm 的滤网或相同精度的滤纸;
3.5.2 所有油柜与设备的进、出油口需加盲板与投油管路隔断;
3.5.3 按附图所示配制投油临时跨接管,此管上船安装前须进行化学清洗,油封并加封口,投油时接入管路使用。
3.6 系统冲洗
3.6.1 启动投油泵组,对系统进行冲洗,在冲洗过程中须常用木锤顺流敲打,每2 小时检查清洗滤器一次,通过周期性的检查,如在2小时内,滤器仍能保持好且稳定的清洁状态,可以认为冲洗结束,向相关单位报检。
3.7 报检合格后,将燃油全部回收到投油泵组油箱内,拆除临时跨接管及各封板,使系统恢复原状待用。
第1页,共1页。
23滑油、液压管道串洗作业指导书
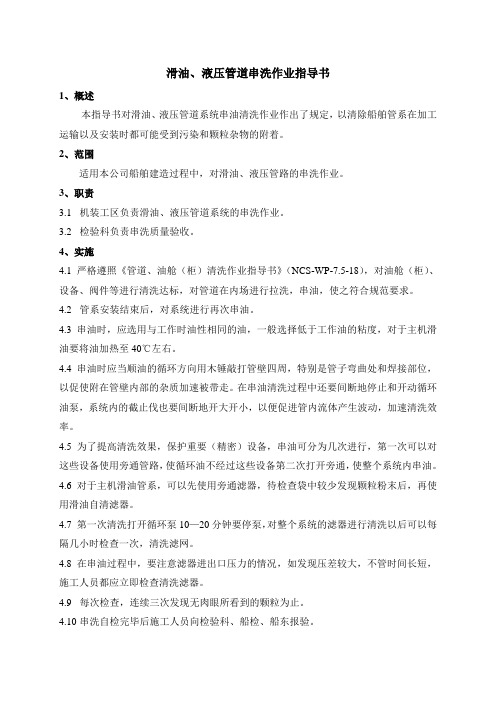
滑油、液压管道串洗作业指导书1、概述本指导书对滑油、液压管道系统串油清洗作业作出了规定,以清除船舶管系在加工运输以及安装时都可能受到污染和颗粒杂物的附着。
2、范围适用本公司船舶建造过程中,对滑油、液压管路的串洗作业。
3、职责3.1机装工区负责滑油、液压管道系统的串洗作业。
3.2检验科负责串洗质量验收。
4、实施4.1严格遵照《管道、油舱(柜)清洗作业指导书》(NCS-WP-7.5-18),对油舱(柜)、设备、阀件等进行清洗达标,对管道在内场进行拉洗,串油,使之符合规范要求。
4.2管系安装结束后,对系统进行再次串油。
4.3串油时,应选用与工作时油性相同的油,一般选择低于工作油的粘度,对于主机滑油要将油加热至40℃左右。
4.4串油时应当顺油的循环方向用木锤敲打管壁四周,特别是管子弯曲处和焊接部位,以促使附在管壁内部的杂质加速被带走。
在串油清洗过程中还要间断地停止和开动循环油泵,系统内的截止伐也要间断地开大开小,以便促进管内流体产生波动,加速清洗效率。
4.5为了提高清洗效果,保护重要(精密)设备,串油可分为几次进行,第一次可以对这些设备使用旁通管路,使循环油不经过这些设备第二次打开旁通,使整个系统内串油。
4.6对于主机滑油管系,可以先使用旁通滤器,待检查袋中较少发现颗粒粉末后,再使用滑油自清滤器。
4.7第一次清洗打开循环泵10—20分钟要停泵,对整个系统的滤器进行清洗以后可以每隔几小时检查一次,清洗滤网。
4.8在串油过程中,要注意滤器进出口压力的情况,如发现压差较大,不管时间长短,施工人员都应立即检查清洗滤器。
4.9每次检查,连续三次发现无肉眼所看到的颗粒为止。
4.10串洗自检完毕后施工人员向检验科、船检、船东报验。
5、记录施工人员应详细记录每次检查的时间和滤网情况,质量记录由检验科和机装工区分别保存。
6、发放发放范围:公司经理层、管理者代表、船舶工程部、质量管理科、检验科、机装工区、内审员。
7、附录:附录一《串洗作业检查记录》(NCS-WP-7.5-14-R01)附录二《施工质量报检单》(NCS-QP-8.2-04-02.1)《专检评语反馈单》(NCS-QP-8.2-04-02.2)附录一格式编号:NCS-WP-7.5-14-R01串洗作业检查记录编号:注:该记录由机装工区保存。
液压油串油工艺流程
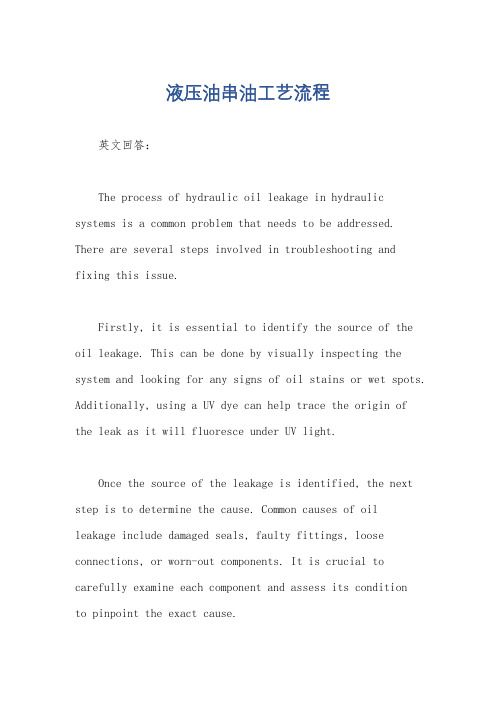
液压油串油工艺流程英文回答:The process of hydraulic oil leakage in hydraulic systems is a common problem that needs to be addressed. There are several steps involved in troubleshooting and fixing this issue.Firstly, it is essential to identify the source of the oil leakage. This can be done by visually inspecting the system and looking for any signs of oil stains or wet spots. Additionally, using a UV dye can help trace the origin of the leak as it will fluoresce under UV light.Once the source of the leakage is identified, the next step is to determine the cause. Common causes of oilleakage include damaged seals, faulty fittings, loose connections, or worn-out components. It is crucial to carefully examine each component and assess its conditionto pinpoint the exact cause.After identifying the cause, the necessary repairs or replacements can be carried out. This may involve replacing damaged seals, tightening loose fittings, or replacing worn-out components. It is important to use the correct tools and follow the manufacturer's instructions to ensure proper installation and prevent further leakage.Once the repairs are completed, it is recommended to conduct a thorough system check to ensure that the leakage has been resolved. This involves running the system and monitoring for any signs of oil leakage. It is also advisable to check the system pressure and temperature to ensure they are within the recommended range.In some cases, additional measures may be taken to prevent future oil leakage. This can include applying sealant or thread tape to fittings, using protective covers or guards for vulnerable components, or implementing regular maintenance and inspection schedules to detect and address any potential issues before they escalate.中文回答:液压系统中液压油串油是一个常见的问题,需要采取措施进行解决。
船舶液压系统投油工艺
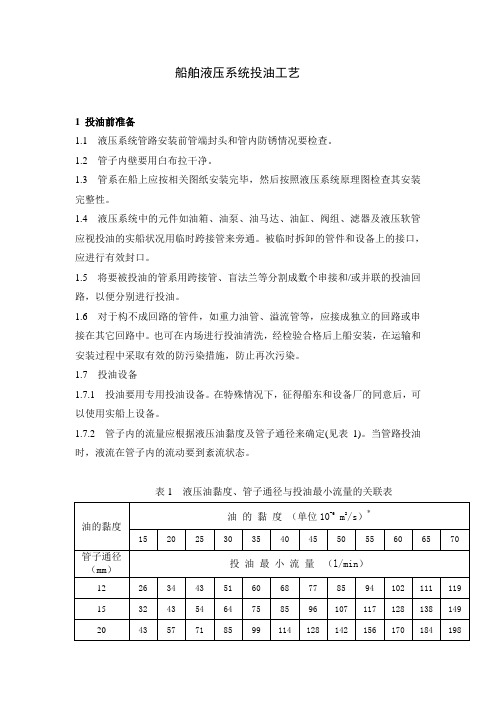
船舶液压系统投油工艺1投油前准备1.1 液压系统管路安装前管端封头和管内防锈情况要检查。
1.2 管子内壁要用白布拉干净。
1.3 管系在船上应按相关图纸安装完毕,然后按照液压系统原理图检查其安装完整性。
1.4 液压系统中的元件如油箱、油泵、油马达、油缸、阀组、滤器及液压软管应视投油的实船状况用临时跨接管来旁通。
被临时拆卸的管件和设备上的接口,应进行有效封口。
1.5 将要被投油的管系用跨接管、盲法兰等分割成数个串接和/或并联的投油回路,以便分别进行投油。
1.6 对于构不成回路的管件,如重力油管、溢流管等,应接成独立的回路或串接在其它回路中。
也可在内场进行投油清洗,经检验合格后上船安装,在运输和安装过程中采取有效的防污染措施,防止再次污染。
1.7 投油设备1.7.1 投油要用专用投油设备。
在特殊情况下,征得船东和设备厂的同意后,可以使用实船上设备。
1.7.2 管子内的流量应根据液压油黏度及管子通径来确定(见表1)。
当管路投油时,液流在管子内的流动要到紊流状态。
表1 液压油黏度、管子通径与投油最小流量的关联表1.7.3 开始投油时使用过滤精度为50μm的回油粗过滤器,投油结束阶段使用过滤精度为5~10μm的回油精过滤器。
1.8 投油用油1.8.1 投油用油的牌号要与对应的液压系统最终所选择使用的液压油牌号一致或在征得船东同意后使用与工作油相兼容的液压油。
1.8.2 经使用过的投油用油,经过精细过滤,取样化验,污染等级达到NAS1638的10级(ISO4406,19/16;GB/T14039-1993,19/16)、水分<0.1%,40℃时黏度与原油样变化≤±(10%~15%),并且无沉淀物,则仍可作投油用油。
3.8.3 投油时,油温应控制在不低于40℃。
最高不许超过65℃。
2 工艺要求2.1 更换干净滤纸后,连续投油2小时,该滤纸应保持恒定的清洁状态。
2.2 投油后取油样进行化验,化验结果应符合液压设备制造厂提出的GB/T14039-1993 《液压系统工作介质固体颗粒污染等级代号》或ISO /DIS4406-1987《液压传动—油液—固体颗粒污染等级代号》或NAS1638-1964《固体颗粒污染等级代号》中的固体颗粒污染等级要求。
船舶管系系统投油工艺

船舶液压管系和系统的清洁工作是一件十分重要而又细致的工作,为减少液压系统实船投油的工作量,确保液压系统投油及效用试验的一次成功,特编制液压管系及系统投油工艺。
本工艺依据CB1102.4—86《船用液压系统通用技术—清洗》部标准编制而成。
本原则工艺用于110M发电机的柴油系统、滑油系统及锚绞液压系统等需要投油的系统,车间应参照本原则工艺要求编制相应的施工工艺。
系统投油包括:管系投油清洗和系统投油清洗二个部份。
通常情况下,管系投油的清洁程度是为系统投油打好了基础。
对于系统简单,管系长度短的润滑系统,例如:滑油系统管系的投油可以采取管系预装、编号、拆回车间内场投油、报检、上船再安装加油后、直接进入效用试验。
一:对液压系统各元件及管系上船安装前的清洁要求:1:系统中全部的液压元件(含阀件、辅件、液压泵站、液压油缸、操纵阀箱等)各油路的进出口必须是清洁的,并确保有效的封口,方可上船进行安装。
2:内场加工制作的管子上船安装之前,应按图纸的要求,经过水压试验合格后、每根管子须经过化学清洗、并对管子内壁采用灌油方法使管子内表面形成完整的油膜、并设置有效的管塞或封口,方可上船安装。
灌油为工作用油,或投油用油(相应牌号的国产油)。
3:所有的封口是液压设备、液压元件以及液压管子确保清洁的重要保证。
因此在生产的全过程中必须确保所有封口是有效的,严禁封口随意拆除,上船安装对接时方可拆除,若封口脱落或有疑问应及时拆检和清洗处理。
4:为减少投油的工作量,管系投油所使用的投油工装及临时跨接管的清洁工作,均按系统元件和管系的清洁要求进行。
二:管系清洗前应具备的条件:1:管系安装完毕,并经系统泵压报验合格后,为减少管系内壁油膜的挥发和锈蚀,应尽快地安排投油的施工。
2:系统的自动控制仪表,如压力表、压力继电器等应上船安装前校验完毕。
3:管系投油清洗可根据需要和方便,设置临时跨接管,将管路短接成一个或数个回路,而不使清洗油流经液压泵站、控制元件和执行元件等。
液压油串油工艺流程
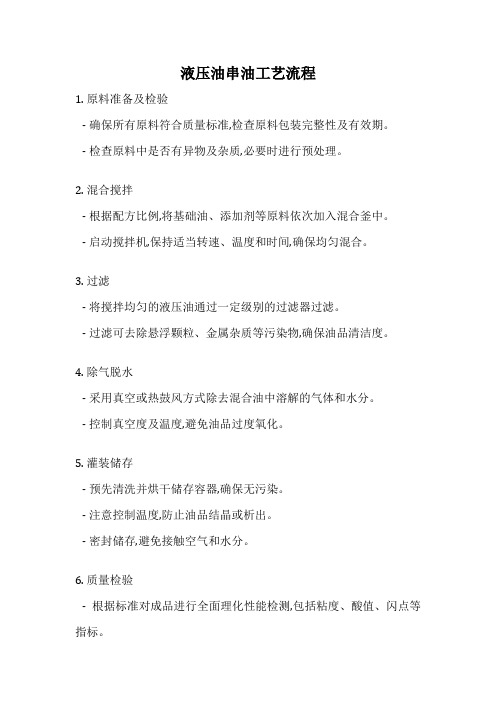
液压油串油工艺流程
1. 原料准备及检验
- 确保所有原料符合质量标准,检查原料包装完整性及有效期。
- 检查原料中是否有异物及杂质,必要时进行预处理。
2. 混合搅拌
- 根据配方比例,将基础油、添加剂等原料依次加入混合釜中。
- 启动搅拌机,保持适当转速、温度和时间,确保均匀混合。
3. 过滤
- 将搅拌均匀的液压油通过一定级别的过滤器过滤。
- 过滤可去除悬浮颗粒、金属杂质等污染物,确保油品清洁度。
4. 除气脱水
- 采用真空或热鼓风方式除去混合油中溶解的气体和水分。
- 控制真空度及温度,避免油品过度氧化。
5. 灌装储存
- 预先清洗并烘干储存容器,确保无污染。
- 注意控制温度,防止油品结晶或析出。
- 密封储存,避免接触空气和水分。
6. 质量检验
- 根据标准对成品进行全面理化性能检测,包括粘度、酸值、闪点等指标。
- 只有符合质量要求的产品方可出厂。
7. 标识和包装
- 对合格产品进行标示,注明产品名称、规格、生产日期和储存条件等信息。
- 采用适当包装形式,防止油品泄漏和受潮。
8. 入库出货
- 将产品入库存储于干燥、阴凉、通风的库房中。
- 严格执行先进先出的出库原则,确保油品新鲜度。
以上是液压油串油的基本工艺流程,在实际生产中还需根据不同产品特性进行适当调整,并严格遵守安全生产操作规程。
船舶液压管路施工与串洗工艺
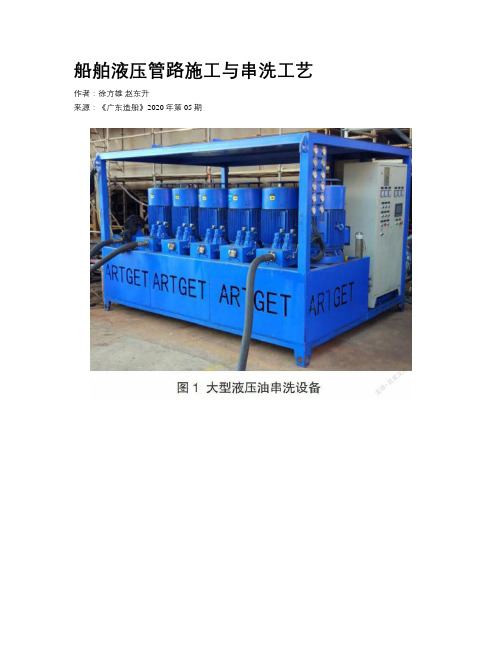
船舶液压管路施工与串洗工艺作者:徐方雄赵东升来源:《广东造船》2020年第05期摘要:液压系统是船舶与海洋工程装备中不可或缺的重要系统之一。
本文重点介绍了液压系统的施工与投油清洗等工艺要领,以防止在设计或施工过程中出现不必要的错误,同时也降低在调试过程中出现因液压系统引起的设备故障,进一步提高施工质量,希望本文能为船舶液压系统的施工及冲洗工艺的改进和发展提供一定的借鉴。
关键词:施工要求;串洗步骤;串洗流量;串洗方法;压力测试中图分类号:U664.8 文献标识码:AConstruction and Flushing Process of Ship Hydraulic PipelineXU Fangxiong, ZHAO Dongsheng( Yiu Lian Dockyards (Shekou) Ltd., Shenzhen 518000 )Abstract: Hydraulic system is an indispensable system in ship and ocean engineering equipment. This paper mainly introduces the construction and oil flushing process of ship hydraulic system so as to prevent the mistakes in the design or construction process, but also reduce the equipment failure during debugging caused by hydraulic system, further improve the quality of construction.Key words: Construction requirements; Flushing steps; Flushing flow; Flushing method; Pressure test1 前言液压系统由下列五个部分组成:动力元件;执行元件;控制元件;辅助元件;液压油。
如何提升船舶滑油及液压油管路串油效率的方案
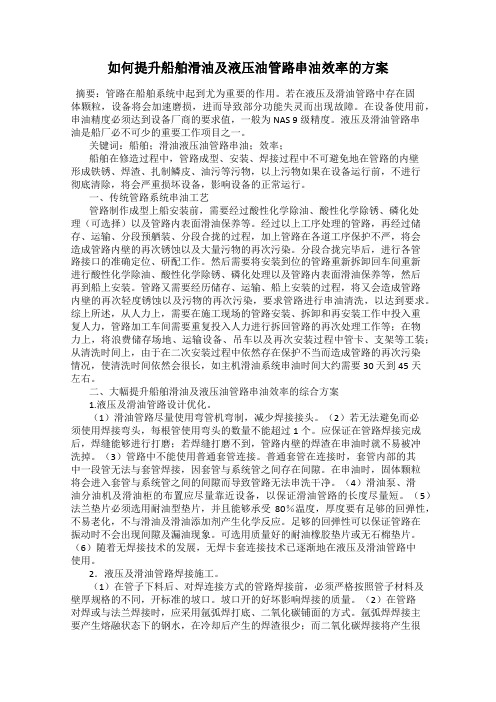
如何提升船舶滑油及液压油管路串油效率的方案摘要:管路在船舶系统中起到尤为重要的作用。
若在液压及滑油管路中存在固体颗粒,设备将会加速磨损,进而导致部分功能失灵而出现故障。
在设备使用前,串油精度必须达到设备厂商的要求值,一般为NAS 9级精度。
液压及滑油管路串油是船厂必不可少的重要工作项目之一。
关键词:船舶;滑油液压油管路串油;效率;船舶在修造过程中,管路成型、安装、焊接过程中不可避免地在管路的内壁形成铁锈、焊渣、扎制鳞皮、油污等污物,以上污物如果在设备运行前,不进行彻底清除,将会严重损坏设备,影响设备的正常运行。
一、传统管路系统串油工艺管路制作成型上船安装前,需要经过酸性化学除油、酸性化学除锈、磷化处理(可选择)以及管路内表面滑油保养等。
经过以上工序处理的管路,再经过储存、运输、分段预舾装、分段合拢的过程,加上管路在各道工序保护不严,将会造成管路内壁的再次锈蚀以及大量污物的再次污染。
分段合拢完毕后,进行各管路接口的准确定位、研配工作。
然后需要将安装到位的管路重新拆卸回车间重新进行酸性化学除油、酸性化学除锈、磷化处理以及管路内表面滑油保养等,然后再到船上安装。
管路又需要经历储存、运输、船上安装的过程,将又会造成管路内壁的再次轻度锈蚀以及污物的再次污染,要求管路进行串油清洗,以达到要求。
综上所述,从人力上,需要在施工现场的管路安装、拆卸和再安装工作中投入重复人力,管路加工车间需要重复投入人力进行拆回管路的再次处理工作等;在物力上,将浪费储存场地、运输设备、吊车以及再次安装过程中管卡、支架等工装;从清洗时间上,由于在二次安装过程中依然存在保护不当而造成管路的再次污染情况,使清洗时间依然会很长,如主机滑油系统串油时间大约需要30 天到45天左右。
二、大幅提升船舶滑油及液压油管路串油效率的综合方案1.液压及滑油管路设计优化。
(1)滑油管路尽量使用弯管机弯制,减少焊接接头。
(2)若无法避免而必须使用焊接弯头,每根管使用弯头的数量不能超过1个。
船舶液压管制作、安装、串油工艺

船舶液压管制作、安装、串油工艺1 概述该工艺对液压系统串油清洗作了规定,以清除船舶管系在加工运输以及安装时都可能受到污染和颗粒杂物的附着。
2 范围适用本公司船舶建造过程中,对液压管路的制作、安装、串油作业。
3 职责由生产组织部门负责组织液压管的具体串油工作,串油须报船东检验认可。
4实施4.1液压管的制作装4.1.1液压管的联接(1)液压管的联接一般有对接、机械联接、法兰联接三种。
(2)采用对接时,应采用氩弧焊打底,二氧化碳焊盖面。
采用法兰联接时,管子应插入法兰。
非通孔法兰时应双面焊接。
(3)焊接完毕后应打磨清除焊接缺陷和焊渣等残附物,打磨时切忌对焊缝的过度打磨。
(4)打磨清渣后按船级社要求对焊缝进行检查并报验。
报验合格后将液压管在车间内场有序连接进行强度试验。
强度试验压力为1.5倍工作压力或按图示压力进行,并报船级社、船东认可。
注意:试验时严禁超压或者带压补焊,试验时如有渗漏,须将压力完全卸放后才能修补。
(5)将强度试验合格的管子拆下装车送外清洗处理。
清洗回厂的管子应进行外观检查是否有锈斑、黄渍等缺陷存在。
清洗合格的管子外表面应涂刷一层防锈底漆,两端端口用厚白帆布或者三防布进行有效的封口。
安装时间较长的管子在封口前还需在管子内壁涂上一层防锈油。
4.2管子的安装4.2.1将需安装的管子吊上船,按零件图或者安装图所示位置将管子大致安放到位。
4.2.2安装一根管子拆除一根管子的封口。
必要时还应用压缩空气对管子内壁进行吹洗。
4.2.3未装妥的管子应及时封口,防止垃圾进入管子。
4.2.3管子安装完毕,检查管子的完整性。
4.3串油前准备工作.4.3.1系统安装完整。
4.3.2系统管路安装后密性试验报验合格。
4.3.2系统管子用临时管将设备、油缸、操作阀箱等设备脱离,系统管路与串油工装接通。
4.3.3振荡器,木榔头,滤纸等附属物件准备到位。
4.4串油4.4.1 启动串油工装串油泵,向系统管路泵油。
4.4.2检查管路是否有漏油现象,如有,立即停泵消除漏油。
SEAWAY工艺:船舶主辅机燃油系统管路串油工艺
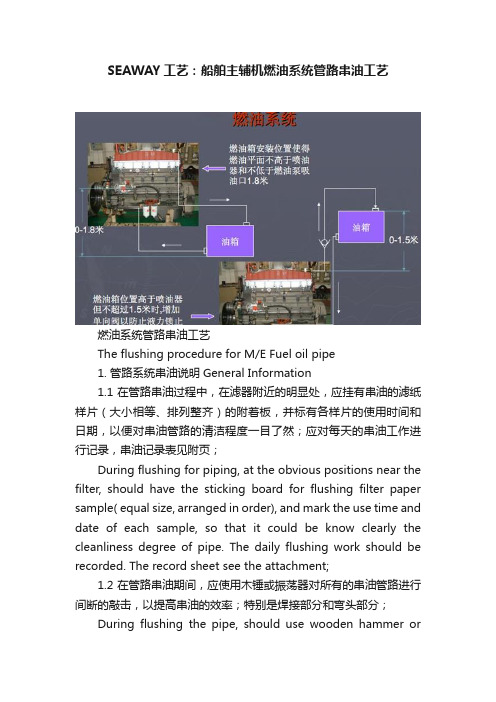
SEAWAY工艺:船舶主辅机燃油系统管路串油工艺燃油系统管路串油工艺The flushing procedure for M/E Fuel oil pipe1. 管路系统串油说明General Information1.1 在管路串油过程中,在滤器附近的明显处,应挂有串油的滤纸样片(大小相等、排列整齐)的附着板,并标有各样片的使用时间和日期,以便对串油管路的清洁程度一目了然;应对每天的串油工作进行记录,串油记录表见附页;During flushing for piping, at the obvious positions near the filter, should have the sticking board for flushing filter paper sample( equal size, arranged in order), and mark the use time and date of each sample, so that it could be know clearly the cleanliness degree of pipe. The daily flushing work should be recorded. The record sheet see the attachment;1.2在管路串油期间,应使用木锤或振荡器对所有的串油管路进行间断的敲击,以提高串油的效率;特别是焊接部分和弯头部分;During flushing the pipe, should use wooden hammer orvibrator to knock all the pipe at intervals.1.3在主辅机燃油系统管路串油过程中,使用临时泵、油柜及滤器;During the flushing of M/E and A/E fuel oil pipe, the temporary pump, oil tank and filter should be used1.4使用柴油对管路进行串油。
船舶管路串油工艺

设计主要内容
• 2、主机串油
• 主机串油:串油就是利用滑油将主机外部的滑 油管道、设备及主机内部冲洗干净。 • 因为在主机及主机机外管道、设备的运输 及安装时,不可避免地会有一些颗粒、焊渣及 杂质进入,在主机动车的时候,它们会对主机 十字头、喷油嘴、轴承、滚轮、气缸壁等造成 损伤。
设计主要内容
• 2、主机串油工艺设计
• 1)主机外部滑油管系清洗 • 2)主机内部滑油管系清洗(除十字头、轴承) • 3)主机内部滑油管系清洗
主机外部滑油管道的清洗
主机内部滑油管道的清洗
主机串油工艺上的优化亮点一
主机串油工艺上的优化亮点二
主机串油工艺上的优化亮点三
谢谢各位老师 祝各位老师 工作顺利,身体健康!!
32500吨散货船主机滑油系统 设计及串油工艺设计
指导老师:李湛、梁榕辉 主讲人:林振豪
1、设计的目的和意义 本设计涉及主机滑油管道的管径的确定、滑 油管道上的设备的计算选型和主机串油工艺设计, 这一设计主要目的在于保证滑油系统满足主机要 求,• 1、主机滑油系统设计
串油
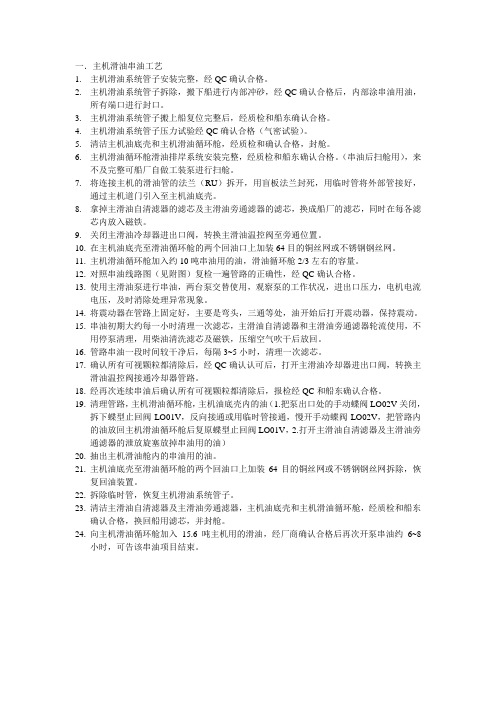
一.主机滑油串油工艺1.主机滑油系统管子安装完整,经QC确认合格。
2.主机滑油系统管子拆除,搬下船进行内部冲砂,经QC确认合格后,内部涂串油用油,所有端口进行封口。
3.主机滑油系统管子搬上船复位完整后,经质检和船东确认合格。
4.主机滑油系统管子压力试验经QC确认合格(气密试验)。
5.清洁主机油底壳和主机滑油循环舱,经质检和确认合格,封舱。
6.主机滑油循环舱滑油排岸系统安装完整,经质检和船东确认合格。
(串油后扫舱用),来不及完整可船厂自做工装泵进行扫舱。
7.将连接主机的滑油管的法兰(RU)拆开,用盲板法兰封死,用临时管将外部管接好,通过主机道门引入至主机油底壳。
8.拿掉主滑油自清滤器的滤芯及主滑油旁通滤器的滤芯,换成船厂的滤芯,同时在每各滤芯内放入磁铁。
9.关闭主滑油冷却器进出口阀,转换主滑油温控阀至旁通位置。
10.在主机油底壳至滑油循环舱的两个回油口上加装64目的铜丝网或不锈钢钢丝网。
11.主机滑油循环舱加入约10吨串油用的油,滑油循环舱2/3左右的容量。
12.对照串油线路图(见附图)复检一遍管路的正确性,经QC确认合格。
13.使用主滑油泵进行串油,两台泵交替使用,观察泵的工作状况,进出口压力,电机电流电压,及时消除处理异常现象。
14.将震动器在管路上固定好,主要是弯头,三通等处,油开始后打开震动器,保持震动。
15.串油初期大约每一小时清理一次滤芯,主滑油自清滤器和主滑油旁通滤器轮流使用,不用停泵清理,用柴油清洗滤芯及磁铁,压缩空气吹干后放回。
16.管路串油一段时间较干净后,每隔3~5小时,清理一次滤芯。
17.确认所有可视颗粒都清除后,经QC确认认可后,打开主滑油冷却器进出口阀,转换主滑油温控阀接通冷却器管路。
18.经再次连续串油后确认所有可视颗粒都清除后,报检经QC和船东确认合格。
19.清理管路,主机滑油循环舱,主机油底壳内的油(1.把泵出口处的手动蝶阀LO02V关闭,拆下蝶型止回阀LO01V,反向接通或用临时管接通,慢开手动蝶阀LO02V,把管路内的油放回主机滑油循环舱后复原蝶型止回阀LO01V,2.打开主滑油自清滤器及主滑油旁通滤器的泄放旋塞放掉串油用的油)20.抽出主机滑油舱内的串油用的油。
串油泵压工艺
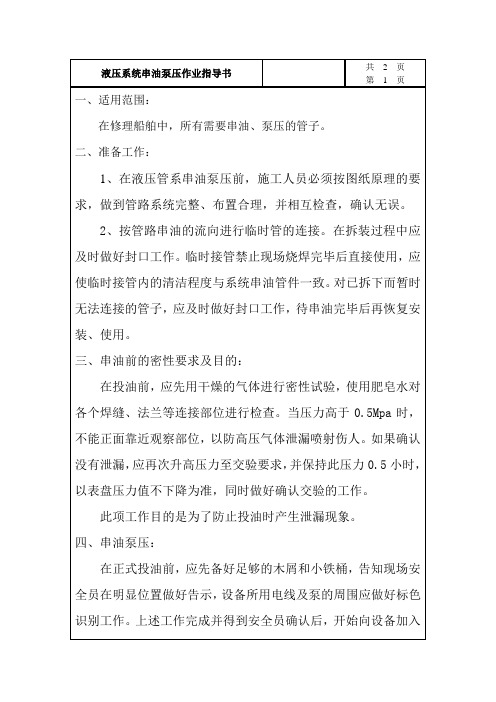
在投油前,应先用干燥的气体进行密性试验,使用肥皂水对各个焊缝、法兰等连接部位进行检查果确认没有泄漏,应再次升高压力至交验要求,并保持此压力0.5小时,以表盘压力值不下降为准,同时做好确认交验的工作。
在串油阶段,应根据管路的粗细、长短等控制好油温及压力,当超出规定的温度时应停止加热或停泵冷却,压力超高时应及时调整。在串油过程中,应不间断地用木制榔头敲击管路,并按规定定时检查、清洁滤器。正向串油12小时后应进行反向串油,直至串油的油样化验合格为止。
五、系统恢复及调试:
在系统恢复阶段,应做好管内残存油液的收集工作。在拆除一根临时管时应马上恢复相应的安装管,禁止一次性拆除所有临时管件,以防垃圾再次进入管内。在整个串油过程中,如有油类垃圾,应及时收集起来,带到车间内专用油类垃圾箱内。
当所有管系完全恢复后,应及时检查管路系统的完整性,特别是阀的方向及连接部位是否紧固等。
液压系统串油泵压作业指导书
共2页
第1页
一、适用范围:
在修理船舶中,所有需要串油、泵压的管子。
二、准备工作:
1、在液压管系串油泵压前,施工人员必须按图纸原理的要求,做到管路系统完整、布置合理,并相互检查,确认无误。
2、按管路串油的流向进行临时管的连接。在拆装过程中应及时做好封口工作。临时接管禁止现场烧焊完毕后直接使用,应使临时接管内的清洁程度与系统串油管件一致。对已拆下而暂时无法连接的管子,应及时做好封口工作,待串油完毕后再恢复安装、使用。
此项工作目的是为了防止投油时产生泄漏现象。
四、串油泵压:
在正式投油前,应先备好足够的木屑和小铁桶,告知现场安全员在明显位置做好告示,设备所用电线及泵的周围应做好标色识别工作。上述工作完成并得到安全员确认后,开始向设备加入
大幅提升船舶滑油及液压油管路串油效率的综合方案
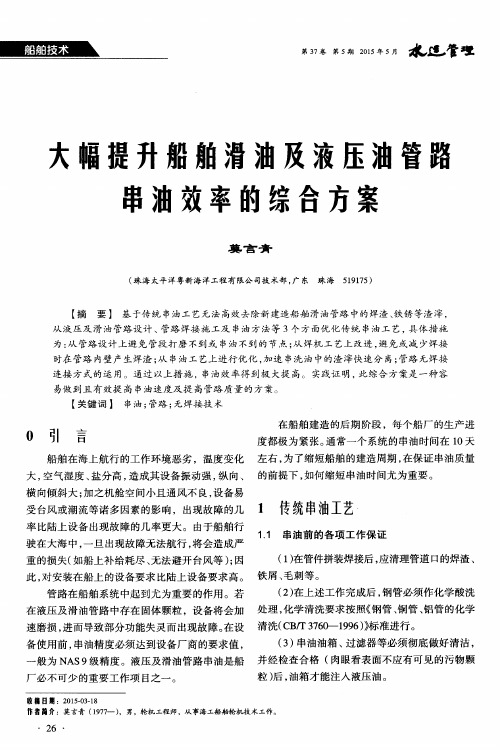
横 向倾 斜大 ; 加之机舱 空间小且通风不 良, 设备 易 受 台风或潮流 等诸多 因素 的影 响 ,出现故 障的几 率 比陆上设备 出现故 障的几率 更大 。由于船舶 行
驶在 大海 中, 一旦 出现故障无法航行 , 将会造 成严 重 的损 失( 如船上补 给耗尽 、 无 法避开 台风等 ) ; 因
1 传统串油工艺
1 . 1 串 油 前 的 各 项 工 作 保 证
( 1 ) 在管件拼装焊接后 , 应清理管道 口的焊渣 、 ( 2 ) 在上述工作 完成后 , 钢管必须作 化学酸洗
毛刺等 。 此, 对安装 在船上 的设备要 求 比陆上设备要 求高 。 铁屑 、 管路在船舶 系统 中起到尤 为重要 的作用 。若 化学清洗要求 按照《 钢管 、 铜管、 铝管 的化学 在 液压及滑油 管路 中存在 固体 颗粒 ,设备将会 加 处理 ,
厂 必不可ቤተ መጻሕፍቲ ባይዱ 的重要 工作项 目之一 。
收稿日期:2 0 1 5 . 0 3 . 1 8
作者简介:莫言青 ( 1 9 7 7 一) ,男,轮机 工程师 , 从 事海工船舶轮机技术工作。
・
2 6 ・
( 4 ) 制造商提供 的动力泵 站油箱 、 过滤器等 必
( 5 ) 在 串油过程 中 , 应定 时清洗及 更换 回油过
须 由供应商检查 确认合格后 方能使用 。
( 5 ) 串油用泵 的工作压力及排量应与系统的工
作压力基本 接近 , 并满足流速 的要求 。
滤 器 的尼龙布 , 以免 过滤器堵塞 。 ( 6 ) 滤 网可用干净 的柴油进行 冲洗 , 冲洗至 肉
眼观察不到颗粒 物再进行使 用 。
( 6 ) 串油 过滤器 的滤 芯为 4 0 0目, 考虑到滤 芯 滤尼龙布 , 效果较好 。 全 损耗系统用 油 ( G B 4 4 3 -1 9 8 9 ) 》 标准, 即残 碳 、
海洋石油水下生产系统液压管线串洗工艺应用探讨
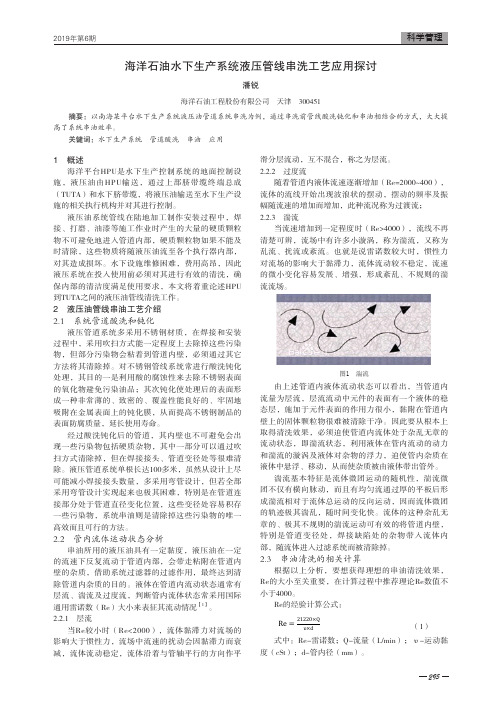
液体中悬浮、移动,从而使杂质被由液体带出管外。
可能减小焊接接头数量,多采用弯管设计,但若全部
湍流基本特征是流体微团运动的随机性,湍流微
采用弯管设计实现起来也极其困难,特别是在管道连
团不仅有横向脉动,而且有均匀流通过厚的平板后形
接部分处于管道直径变化位置,这些变径处容易积存
成湍流相对于流体总运动的反向运动,因而流体微团
一些污染物,系统串油则是清除掉这些污染物的唯一
的轨迹极其湍乱,随时间变化快。流体的这种杂乱无
高效而且ᦹ可DŽ行的方法。
章的、极其不规则的湍流运动可有效的将管道内壁,
2.2 管内流体运动状态分析
特别是管道变径处,焊接缺陷处的杂物带入流体内
串Ϯ͘油ϯ 所І用⊍的⏙液⋫压ⱘ油Ⳍ具݇有䅵一ㅫ定黏度,液压油在一定
幅随流速的增加而增加,此种流况称为过渡流;
液压油系统管线在陆地加工制作安装过程中,焊 2.2.3 湍流
接、打磨、油漆等施工作业时产生的大量的硬质颗粒
当流速增加到一定程度时(Re>4000),流线不再
物不可避免地进入管道内部,硬质颗粒物如果不能及 清楚可辨,流场中有许多小漩涡,称为湍流,又称为
时清除,这些物质将随液压油流至各个执行器内部, 乱流、扰流或紊流。也就是说雷诺数较大时,惯性力
的流速下反复流动于管道内部,会带走粘附在管道内
部,随流体进入过滤系统而被清除掉。
2.3 串油清洗的相关计算
壁的杂质,借助系统过滤器的过滤作用,最终达到清
根据以上分析,要想获得理想的串油清洗效果,
除管道内ṩ杂ᦞ质ԕ的к目࠶的᷀。ˈ液㾱体ᜣ在㧧管ᗇ道⨶内ᜣ流Ⲵ动Ѣ状⋩态通⍇常᭸有᷌ˈZĞ RⲴeབྷ的ሿ大㠣小ޣ至䟽关㾱重ˈ要൘,䇑在计算过程中推荐理论Re数值不
船用液压系统串油工艺

船用液压系统的投油、压力试验一、系统投油前的准备1、准备好一套独立的投油装置,包括油箱、泵、滤器等,考虑到船厂一年四季都有可能施工,最好在投油装置中设置一个加热装置(因船东或设备厂家一般不会同意直接用设备厂家配套的液压泵站来直接投油,所以建议船厂自行购置一套专用的投油装置);2、在头油泵站油箱内注入约适量的的液压油(根据经验:约为整个液压系统用油的80%即可;如油量过多不仅造成船厂的成本浪费,而且不利于系统的投油效率,延长投油时间、影响施工进度);特别需注意投油用液压油牌号和系统用油需一致。
液压油牌号根据系统用途、船舶航区的因素的不同一般选用:ISO VG15、32、 46、68等。
3、准备好50μ、10μ滤芯各若干个。
4、凡是可能引节流或可能被高速的清洗油损坏的液压元件,都应用合适的跨接管来旁通(注意旁通管的压力不能低于系统的试验压力,因后后续的压力实试验也需用旁通管)。
一般来说,系统中的液压元件在设备厂家供货到船厂前已经清洗过并密封好的。
包括油箱、油泵、阀组、油缸、回油滤器等。
5、根据不同系统,用跨接管(可用高压软管或紫铜管)组成一个或多个回路,以达到最好的清洗效果。
要确保回路中没有死路,清洗油最后能流回投油装置。
二、清洗投油步骤1、把用跨接连接的循环回路接入投油装置。
检查油液是否能连续的流经管路并返回投油装置的油箱。
2、投油清洗的油液温度应为50°C~60°C,达到溶解剩余的润滑油的程度。
如油液温度达不到该值,可用投油清洗装置内的电加热器对油液加热,同时注意有叶温度不宜过高。
3、管路清洗投油时,需用木榔头在管路的长度方向上敲打,使粘附在管壁上的杂质脱落(或用管路振动器)。
4、管路清洗投油过程中,每隔数小时需检查并更换滤器中的滤芯。
5、持续清洗投油,直至满足清洁度要求为止。
清洁度的要求可用NAS1638标准的八级或ISO标准的17/14来评估是否达到要求。
6、系统清洗投油时间,以管路长度及管路的污染程度来定。
单点液压系统的串油设计与实践
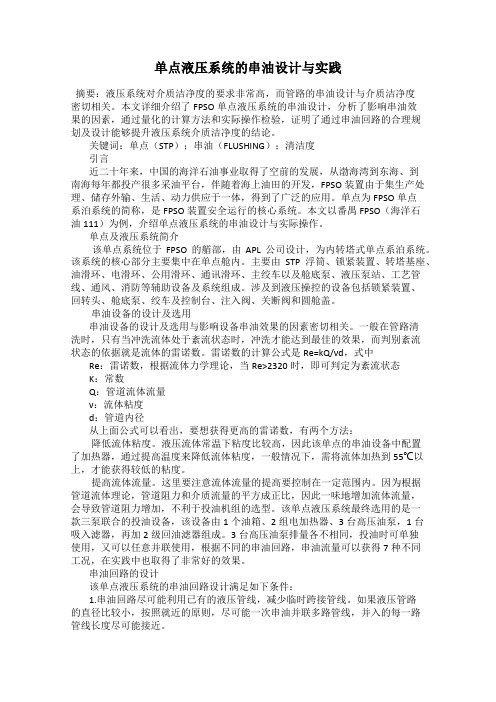
单点液压系统的串油设计与实践摘要:液压系统对介质洁净度的要求非常高,而管路的串油设计与介质洁净度密切相关。
本文详细介绍了FPSO单点液压系统的串油设计,分析了影响串油效果的因素,通过量化的计算方法和实际操作检验,证明了通过串油回路的合理规划及设计能够提升液压系统介质洁净度的结论。
关键词:单点(STP);串油(FLUSHING);清洁度引言近二十年来,中国的海洋石油事业取得了空前的发展,从渤海湾到东海、到南海每年都投产很多采油平台,伴随着海上油田的开发,FPSO装置由于集生产处理、储存外输、生活、动力供应于一体,得到了广泛的应用。
单点为FPSO单点系泊系统的简称,是FPSO装置安全运行的核心系统。
本文以番禺FPSO(海洋石油111)为例,介绍单点液压系统的串油设计与实际操作。
单点及液压系统简介该单点系统位于FPSO的艏部,由APL公司设计,为内转塔式单点系泊系统。
该系统的核心部分主要集中在单点舱内。
主要由STP浮筒、锁紧装置、转塔基座、油滑环、电滑环、公用滑环、通讯滑环、主绞车以及舱底泵、液压泵站、工艺管线、通风、消防等辅助设备及系统组成。
涉及到液压操控的设备包括锁紧装置、回转头、舱底泵、绞车及控制台、注入阀、关断阀和圆舱盖。
串油设备的设计及选用串油设备的设计及选用与影响设备串油效果的因素密切相关。
一般在管路清洗时,只有当冲洗流体处于紊流状态时,冲洗才能达到最佳的效果,而判别紊流状态的依据就是流体的雷诺数。
雷诺数的计算公式是Re=kQ/νd,式中Re:雷诺数,根据流体力学理论,当Re>2320时,即可判定为紊流状态K:常数Q:管道流体流量ν:流体粘度d:管道内径从上面公式可以看出,要想获得更高的雷诺数,有两个方法:降低流体粘度。
液压流体常温下粘度比较高,因此该单点的串油设备中配置了加热器,通过提高温度来降低流体粘度,一般情况下,需将流体加热到55℃以上,才能获得较低的粘度。
提高流体流量。
这里要注意流体流量的提高要控制在一定范围内。
- 1、下载文档前请自行甄别文档内容的完整性,平台不提供额外的编辑、内容补充、找答案等附加服务。
- 2、"仅部分预览"的文档,不可在线预览部分如存在完整性等问题,可反馈申请退款(可完整预览的文档不适用该条件!)。
- 3、如文档侵犯您的权益,请联系客服反馈,我们会尽快为您处理(人工客服工作时间:9:00-18:30)。
船用液压系统的投油、压力试验
一、系统投油前的准备
1、准备好一套独立的投油装置,包括油箱、泵、滤器等,考虑到船厂一
年四季都有可能施工,最好在投油装置中设置一个加热装置(因船东或设备厂家一般不会同意直接用设备厂家配套的液压泵站来直接投油,所以建议船厂自行购置一套专用的投油装置);
2、在头油泵站油箱内注入约适量的的液压油(根据经验:约为整个液压
系统用油的80%即可;如油量过多不仅造成船厂的成本浪费,而且不利于系统的投油效率,延长投油时间、影响施工进度);特别需注意投油用液压油牌号和系统用油需一致。
液压油牌号根据系统用途、船舶航区的因素的不同一般选用:ISO VG15、
32、 46、68等。
3、准备好50μ、10μ滤芯各若干个。
4、凡是可能引节流或可能被高速的清洗油损坏的液压元件,都应用合适
的跨接管来旁通(注意旁通管的压力不能低于系统的试验压力,因后后续的压力实试验也需用旁通管)。
一般来说,系统中的液压元件在设备厂家供货到船厂前已经清洗过并密封好的。
包括油箱、油泵、阀组、油缸、回油滤器等。
5、根据不同系统,用跨接管(可用高压软管或紫铜管)组成一个或多个回
路,以达到最好的清洗效果。
要确保回路中没有死路,清洗油最后能流回投油装置。
二、清洗投油步骤
1、把用跨接连接的循环回路接入投油装置。
检查油液是否能连续的流经
管路并返回投油装置的油箱。
2、投油清洗的油液温度应为50°C~60°C,达到溶解剩余的润滑油的程度。
如油液温度达不到该值,可用投油清洗装置内的电加热器对油液加热,同时注意有叶温度不宜过高。
3、管路清洗投油时,需用木榔头在管路的长度方向上敲打,使粘附在管壁
上的杂质脱落(或用管路振动器)。
4、管路清洗投油过程中,每隔数小时需检查并更换滤器中的滤芯。
5、持续清洗投油,直至满足清洁度要求为止。
清洁度的要求可用NAS1638
标准的八级或ISO标准的17/14来评估是否达到要求。
6、系统清洗投油时间,以管路长度及管路的污染程度来定。
一般需48小
时左右。
7、采集样品油或使用特别的污染显示设备来确认清洗已达到所要求的清洁
度,如船厂无专门的监测仪器,可将油样送至上海的专门的检测机构。
8、清洗投油结束后,将管路中的清洗油完全排空,拆下清洗投油装置,拆
除跨接管,并用螺塞将管子敞开的末端封堵好。
注:清洗工作结束后,应尽快给系统中加满新油。
新油应在系统中进行循环,以确保所有清洁面都能得到良好保护。
三、压力试验(只针对高压管)
完成清洗工作后,系统应准备进行压力试验。
压力:根据系统设计压力
步骤:
1、将高压管路与液压单元、动力单元等断开。
管子末端用螺塞或盖冒封堵
(应确保能承受试验所需的压力)。
2、高压系统的压力试验,应使用一套单独的动力单元来进行。
低压管路不
需要做压力试验。
3、压力试验至少持续5分钟。
4、每个管路都需进行压力试验,发现渗漏应消除后,重新做管路压力试验。
5、压力试验完成后,按液压原理图所示,恢复系统的连接,在恢复系统时,
确保没有污物进入。
6、在拆除螺赛前,请确认管路已经泄压。
8、压力试验需有完整的试验所需数据纪录报告,试验时需有船厂、船检、
船东、设备厂家等代表在场。