影响注塑件强度的几点注塑工艺
注塑成型工艺参数及其影响

注塑成型工艺参数及其影响11209040112 黄卓摘要:塑料材料在生活中所占比例越来越高,而对于其质量的要求也越来越高,注塑成型作为重要的生产手段,对技术的提高也越来越迫切,而注塑成型制品的影响因素较多,但注塑成型加工工艺条件是重要的影响因素之一,下面将会介绍个个工艺参数对于制品性能的影响。
关键词:注塑成型工艺参数一、注塑成型概念传统的模具设计和工艺参数设置主要依赖于设计者的经验和技巧,模具设计的合理性只有靠反复的试模和修模,工艺参数的设置也只能靠反复的试模来进行修改,缺乏科学依据,生产周期长,成本高,质量也难以保证。
而对成型过程进行模拟,在模具制造之前就可发现设计中的问题,使模具设计和工艺参数设置建立在科学的分析基础之上,可缩短生产周期,提高制品质量。
随着对制品质量要求的提高,对成型过程进行预测己经成为设计不可缺少的环节。
因此,建立注塑成型过程熔体在模腔中流动和传热的数学模型,并采用数值仿真方法实现成型过程的模拟具有重要的意义。
由于成型过程的工艺参数直接决定了熔体在模腔中的流动状态,对制品质量有着最直接最深远的影响,因此找到制品成型的最优工艺条件,对成型过程进行工艺控制,是提高塑料制品质量的有效途径。
这是因为,成型过程中,精密的成型机械、合理的模具设计和优良的材料性能只有在合理的成型工艺设置下刁`能体现出来另一方面,成型机械、模具设计和材料性能的缺陷有时可通过合适的成型工艺设置来弥补。
由此可见,注塑成型工艺对制品质量有着至关重要的作用二、注塑工艺条件及其影响1、注塑压力注射压力指的是在注射过程中螺杆顶部或柱塞对于塑料熔体所加载的压力。
它的作用是对于使熔料混合和塑化,螺杆(或柱塞)必须提供克服固体粒子和熔料在料筒和喷嘴中的流动阻力。
使得塑料熔体以一定的速度来充满型腔,在型腔充满熔体后注射压力起到压实的作用。
从而使得塑件致密,并对熔料因冷却而产生的收缩进行补料,从而使塑件保持精确的形状,获得所需要的性能。
塑料注塑性能工艺概括
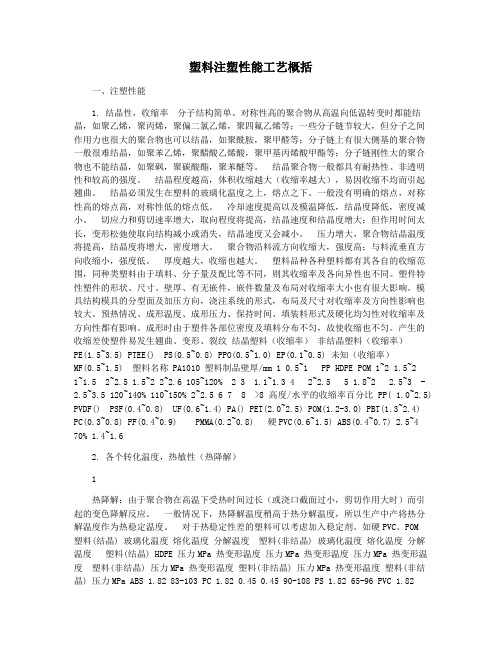
塑料注塑性能工艺概括一、注塑性能1. 结晶性,收缩率分子结构简单、对称性高的聚合物从高温向低温转变时都能结晶,如聚乙烯,聚丙烯,聚偏二氯乙烯,聚四氟乙烯等;一些分子链节较大,但分子之间作用力也很大的聚合物也可以结晶,如聚酰胺,聚甲醛等;分子链上有很大侧基的聚合物一般很难结晶,如聚苯乙烯,聚醋酸乙烯酸,聚甲基丙烯酸甲酯等;分子链刚性大的聚合物也不能结晶,如聚砜,聚碳酸酯,聚苯醚等。
结晶聚合物一般都具有耐热性、非透明性和较高的强度。
结晶程度越高,体积收缩越大(收缩率越大),易因收缩不均而引起翘曲。
结晶必须发生在塑料的玻璃化温度之上,熔点之下。
一般没有明确的熔点,对称性高的熔点高,对称性低的熔点低。
冷却速度提高以及模温降低,结晶度降低,密度减小。
切应力和剪切速率增大,取向程度将提高,结晶速度和结晶度增大;但作用时间太长,变形松弛使取向结构减小或消失,结晶速度又会减小。
压力增大,聚合物结晶温度将提高,结晶度将增大,密度增大。
聚合物沿料流方向收缩大,强度高;与料流垂直方向收缩小,强度低。
厚度越大,收缩也越大。
塑料品种各种塑料都有其各自的收缩范围,同种类塑料由于填料、分子量及配比等不同,则其收缩率及各向异性也不同。
塑件特性塑件的形状、尺寸、壁厚、有无嵌件,嵌件数量及布局对收缩率大小也有很大影响。
模具结构模具的分型面及加压方向,浇注系统的形式,布局及尺寸对收缩率及方向性影响也较大。
预热情况、成形温度、成形压力、保持时间、填装料形式及硬化均匀性对收缩率及方向性都有影响。
成形时由于塑件各部位密度及填料分布不匀,故使收缩也不匀。
产生的收缩差使塑件易发生翘曲、变形、裂纹结晶塑料(收缩率)非结晶塑料(收缩率)PE(1.5~3.5) PTEE() PS(0.5~0.8) PPO(0.5~1.0) EP(0.1~0.5) 未知(收缩率)MF(0.5~1.5) 塑料名称 PA1010 塑料制品壁厚/mm 1 0.5~1 PP HDPE POM 1~2 1.5~21~1.5 2~2.5 1.5~2 2~2.6 105~120% 2 3 1.1~1.3 4 2~2.5 5 1.8~2 2.5~3 - 2.5~3.5 120~140% 110~150% 2~2.5 6 7 8 >8 高度/水平的收缩率百分比 PP( 1.0~2.5) PVDF() PSF(0.4~0.8) UF(0.6~1.4) PA() PET(2.0~2.5) POM(1.2-3.0) PBT(1.3~2.4) PC(0.3~0.8) PF(0.4~0.9) PMMA(0.2~0.8) 硬PVC(0.6~1.5) ABS(0.4~0.7) 2.5~4 70% 1.4~1.62. 各个转化温度,热敏性(热降解)1热降解:由于聚合物在高温下受热时间过长(或浇口截面过小,剪切作用大时)而引起的变色降解反应。
注塑件设计需要注意的问题
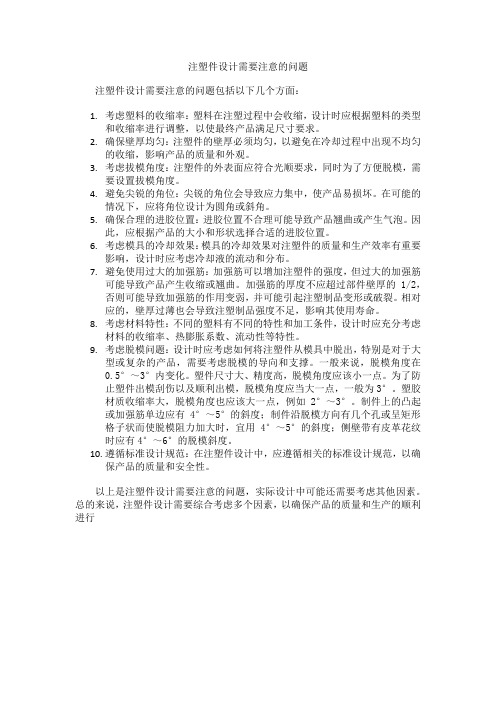
注塑件设计需要注意的问题注塑件设计需要注意的问题包括以下几个方面:1.考虑塑料的收缩率:塑料在注塑过程中会收缩,设计时应根据塑料的类型和收缩率进行调整,以使最终产品满足尺寸要求。
2.确保壁厚均匀:注塑件的壁厚必须均匀,以避免在冷却过程中出现不均匀的收缩,影响产品的质量和外观。
3.考虑拔模角度:注塑件的外表面应符合光顺要求,同时为了方便脱模,需要设置拔模角度。
4.避免尖锐的角位:尖锐的角位会导致应力集中,使产品易损坏。
在可能的情况下,应将角位设计为圆角或斜角。
5.确保合理的进胶位置:进胶位置不合理可能导致产品翘曲或产生气泡。
因此,应根据产品的大小和形状选择合适的进胶位置。
6.考虑模具的冷却效果:模具的冷却效果对注塑件的质量和生产效率有重要影响,设计时应考虑冷却液的流动和分布。
7.避免使用过大的加强筋:加强筋可以增加注塑件的强度,但过大的加强筋可能导致产品产生收缩或翘曲。
加强筋的厚度不应超过部件壁厚的1/2,否则可能导致加强筋的作用变弱,并可能引起注塑制品变形或破裂。
相对应的,壁厚过薄也会导致注塑制品强度不足,影响其使用寿命。
8.考虑材料特性:不同的塑料有不同的特性和加工条件,设计时应充分考虑材料的收缩率、热膨胀系数、流动性等特性。
9.考虑脱模问题:设计时应考虑如何将注塑件从模具中脱出,特别是对于大型或复杂的产品,需要考虑脱模的导向和支撑。
一般来说,脱模角度在0.5°~3°内变化。
塑件尺寸大、精度高,脱模角度应该小一点。
为了防止塑件出模刮伤以及顺利出模,脱模角度应当大一点,一般为3°。
塑胶材质收缩率大,脱模角度也应该大一点,例如2°~3°。
制件上的凸起或加强筋单边应有4°~5°的斜度;制件沿脱模方向有几个孔或呈矩形格子状而使脱模阻力加大时,宜用4°~5°的斜度;侧壁带有皮革花纹时应有4°~6°的脱模斜度。
注塑件熔接痕的影响因素及改进措施
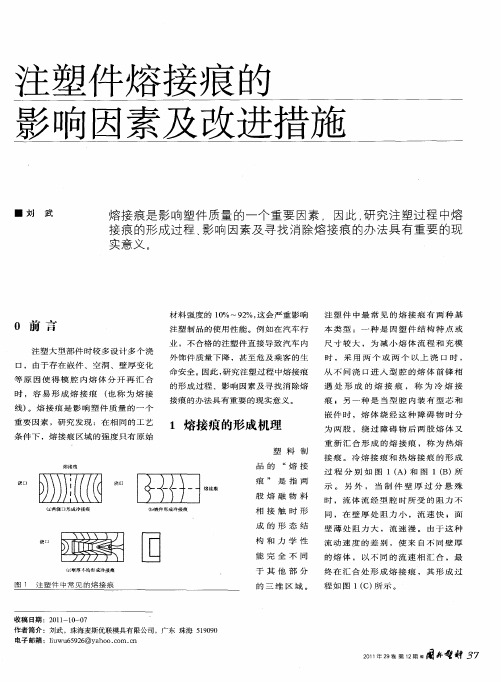
图 2 浇 口位 置 对 塑件 熔 接 痕 的 影 响
这 样 更 有 利 于 物 料 前 端 分 子 的 充 分
熔 合 、 扩 散 和 缠 结 ,从 而 提 高 熔 接
从 而 使 熔 接 痕 强度 得 到提 高 。提 高 保
在 选 定 材 料 、设 置 完 工 艺 参 数 之 后 ,模 具 的 设 计 就 成 了 最 关 键 的 一
评 价 做 了 大 量 研 究 工 作 ,并 提 出 了多
种 解决 方 案 。
21 注 塑工 艺 的影 响 .
211 温 度的影 响 ..
升 高 温 度 可 以 加 速 聚 合 物 的 松 弛 过 程 ,减少 分 子 链缠 结 的 时 间 ,
合 ,增 加 熔 接 痕处 的密度 ,
数 中 , 熔 体 温 度 对 ABS塑 件 熔 接 痕 强度的影响最大 。
注 射 速 度 影 响熔 体 在 型 腔 内的 流
的结 合 强 度 。 塑 件 熔 接 痕 的 产 生 与 浇 口的相 对 位 置 有 着 密 切 关 系 。在 塑 背 后 的 几何 中心 只设 一 个 浇 口 的注 塑 方 法 ,所 制 成 的 塑件 熔 接 痕 强 度 得 到 提 高 。 另 是
注 塑件 熔接痕 的 影 响 因素及 改进 措施
一 刘 武
熔 接 痕 是 影 响 塑件 质 量 的 一 个 重 要 因素 ,因 此 , 究 注 塑 过 程 中熔 研 接痕 的形成过 程 、 响 因素及寻 找消除熔接 痕的办法具 有重要 的现 影 实意 义 。
材 料 强 度 的 1 % ~9 %, 会 严 重 影 响 0 2 这
224 பைடு நூலகம் 腔 、型 芯表 面粗 糙 度 ..
pet加纤材料注塑工艺
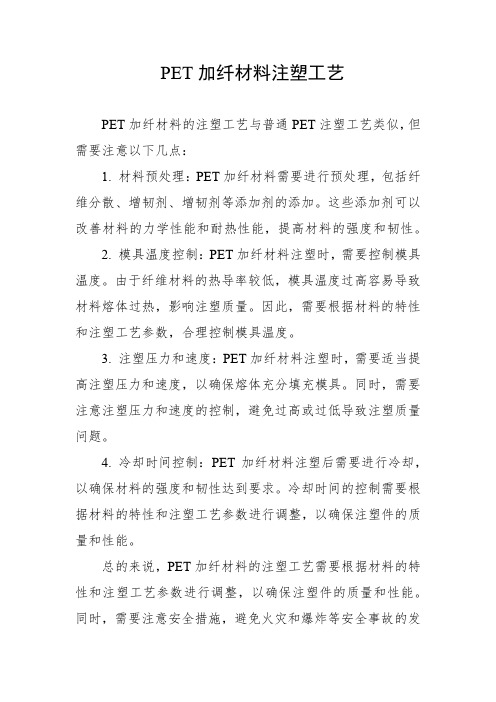
PET加纤材料注塑工艺
PET加纤材料的注塑工艺与普通PET注塑工艺类似,但需要注意以下几点:
1. 材料预处理:PET加纤材料需要进行预处理,包括纤维分散、增韧剂、增韧剂等添加剂的添加。
这些添加剂可以改善材料的力学性能和耐热性能,提高材料的强度和韧性。
2. 模具温度控制:PET加纤材料注塑时,需要控制模具温度。
由于纤维材料的热导率较低,模具温度过高容易导致材料熔体过热,影响注塑质量。
因此,需要根据材料的特性和注塑工艺参数,合理控制模具温度。
3. 注塑压力和速度:PET加纤材料注塑时,需要适当提高注塑压力和速度,以确保熔体充分填充模具。
同时,需要注意注塑压力和速度的控制,避免过高或过低导致注塑质量问题。
4. 冷却时间控制:PET加纤材料注塑后需要进行冷却,以确保材料的强度和韧性达到要求。
冷却时间的控制需要根据材料的特性和注塑工艺参数进行调整,以确保注塑件的质量和性能。
总的来说,PET加纤材料的注塑工艺需要根据材料的特性和注塑工艺参数进行调整,以确保注塑件的质量和性能。
同时,需要注意安全措施,避免火灾和爆炸等安全事故的发
生。
塑胶件注塑工艺关键技术

塑胶件注塑工艺关键技术
塑胶件注塑工艺的关键技术包括以下几个方面:
1.模具设计:模具是注塑工艺的基础,其设计是否合理直接影响到产品的质量和生产效率。
模具设计应根据塑胶件的结构、尺寸、精度要求等因素进行,确保模具的强度、刚度和耐久性。
2.注塑机选择:注塑机是实现注塑工艺的重要设备,其选择应根据生产规模、塑胶类型、制品精度和生产环境等因素进行。
3.原料选择:塑胶原料的种类和品质直接影响到制品的性能和品质,应根据产品要求选择合适的原料,确保生产出的塑胶件符合设计要求。
4.注塑工艺参数控制:注塑工艺参数如注射压力、注射速度、模具温度等对制品的质量和生产效率有很大的影响。
在实际生产中,应根据原料的性能和塑胶件的特点,设置合理的工艺参数。
5.质量控制:在注塑过程中,应对制品进行严格的质量检查,确保其符合设计要求。
常见的质量控制方法包括尺寸测量、外观检查、性能测试等。
6.环境保护:注塑工艺会产生一定的废气、废水和固废等污染物,应采取有效的治理措施,保护环境。
7.人员培训和管理:操作人员的技能和素质对注塑工艺的质量和效率有很大的影响,应对其进行专业的培训和管理,确保其按照规定的要求进行操作和维护设备。
以上是塑胶件注塑工艺的关键技术,在实际生产中,应根据具体情况进行合理的选择和应用,以确保生产出的塑胶件符合设计要求,提高生产效率和质量。
注塑机作业中的注射压力对成型件性能的影响
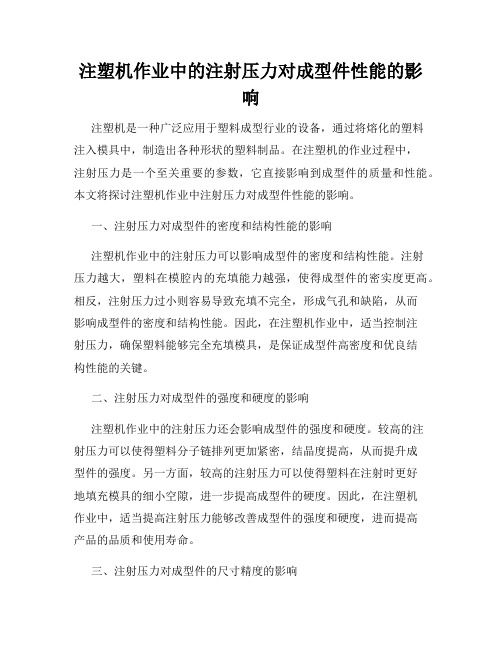
注塑机作业中的注射压力对成型件性能的影响注塑机是一种广泛应用于塑料成型行业的设备,通过将熔化的塑料注入模具中,制造出各种形状的塑料制品。
在注塑机的作业过程中,注射压力是一个至关重要的参数,它直接影响到成型件的质量和性能。
本文将探讨注塑机作业中注射压力对成型件性能的影响。
一、注射压力对成型件的密度和结构性能的影响注塑机作业中的注射压力可以影响成型件的密度和结构性能。
注射压力越大,塑料在模腔内的充填能力越强,使得成型件的密实度更高。
相反,注射压力过小则容易导致充填不完全,形成气孔和缺陷,从而影响成型件的密度和结构性能。
因此,在注塑机作业中,适当控制注射压力,确保塑料能够完全充填模具,是保证成型件高密度和优良结构性能的关键。
二、注射压力对成型件的强度和硬度的影响注塑机作业中的注射压力还会影响成型件的强度和硬度。
较高的注射压力可以使得塑料分子链排列更加紧密,结晶度提高,从而提升成型件的强度。
另一方面,较高的注射压力可以使得塑料在注射时更好地填充模具的细小空隙,进一步提高成型件的硬度。
因此,在注塑机作业中,适当提高注射压力能够改善成型件的强度和硬度,进而提高产品的品质和使用寿命。
三、注射压力对成型件的尺寸精度的影响注塑机作业中的注射压力对成型件的尺寸精度也有很大的影响。
注射压力过大或过小都可能导致成型件的尺寸偏差。
过大的注射压力容易造成过度充填,使得成型件的尺寸放大,而过小的注射压力则容易导致充填不完全,使得成型件的尺寸缩小。
因此,在注塑机作业中,合理控制注射压力,确保注射过程中塑料能够均匀充填模具,是保证成型件尺寸精度的关键。
四、注射压力对成型件的表面质量的影响注塑机作业中的注射压力还会对成型件的表面质量产生影响。
适当的注射压力能够使得塑料在注射过程中充分填充模具的细小凹凸表面,从而得到较为平整和光滑的表面。
相反,注射压力过大则容易使塑料溢出模具缝隙,导致成型件产生毛刺和凹陷。
因此,在注塑机作业中,通过调整注射压力,能够改善成型件的表面质量,提高产品的外观和品质。
注塑件常见成型缺陷及解决方案

注塑件常见成型缺陷及解决方案注塑件常见成型缺陷及解决方案前言在注塑成型加式过程中,可能由于原材料处理不好、塑件或模具设计不合理、操作工没有掌握合适的工艺操作条件,或者因机械方面的原因,常常使塑件产品短射、凹痕、飞边、困气、开裂、翘曲变形等成型缺陷。
本文针对塑件在成型过程中出现的各种注塑缺陷,主要是:短射,困气,发脆,烧焦,飞边,分层起皮,喷流痕,流痕,雾斑(浇口晕),银纹(水花纹),凹痕,熔接痕,成型周期过长,翘曲变形,分析了问题产生的可能原因,从原材料、塑件或模具设计、成型工艺等各方面,提出解决方案。
一.短射短射是指模具型腔不能被完全充满的一种现象。
短射形成原因:1、模温、料温或注塑压力和速度过低2、原料塑化不均3、排气不良4、原料流动性不足5、制件太薄或浇口尺寸太小6、聚合物熔体由于结构设计不合理导致过早固化短射解决方案:材料:选用流动性更好的材料模具设计:1、填充薄壁之前先填充厚壁,避免出现滞留现象2、增加浇口数量和流道尺寸,减少流程比及流动阻力3、排气口的位置和尺寸设置适当,避免出现排气不良的现象注塑机:1、检查止逆阀和料筒内壁是否磨损严重2、检查加料口是否有料或是否架桥工艺条件:1、增大注塑压力和注塑速度,增强剪切热2、增大注塑量3、增大料筒温度和模具温度二.困气困气是指空气被困在型腔内而使制件产生气泡。
困气形成原因:它是由于两股熔体前锋交汇时气体无法从分型面、顶杆或排气孔中排出造成的。
困在型腔内气体不能被及时排出,易导致出现表面起泡,制件内部夹气,注塑不满等现象。
困气解决方案:结构设计:减少厚度的不一致,尽量保证壁厚均匀模具设计:1、在最后填充的地方增设排气口2、重新设计浇口和流道系统工艺条件:1、降低最后一级注塑速度.2、增加模温三.发脆塑件发脆是指制件在某些部位出现容易开裂或折断。
发脆原因:1、干燥条件不适合;使用过多回收料2、注塑温度设置不对3、浇口和流道系统设置不恰当4、熔解痕强度不高发脆解决方案:材料:1、注塑前设置适当的干燥条件2、减少使用回收料,增加原生料的比例.3、选用高强度的塑胶.模具设计:增大主流道、分流道和浇口尺寸注塑机:选择设计良好的螺杆,使塑化时温度分配更加均匀工艺条件:1、降低料筒和喷嘴的温度2、降低背压、螺杆转速和注塑速度3、通过增加料温,加大注塑压力,提高熔解痕强度四.烧焦焦痕是指型腔内气体不能及时排走,导致在流动最末断产生烧黑现象。
影响注塑件强度的工艺因素分析
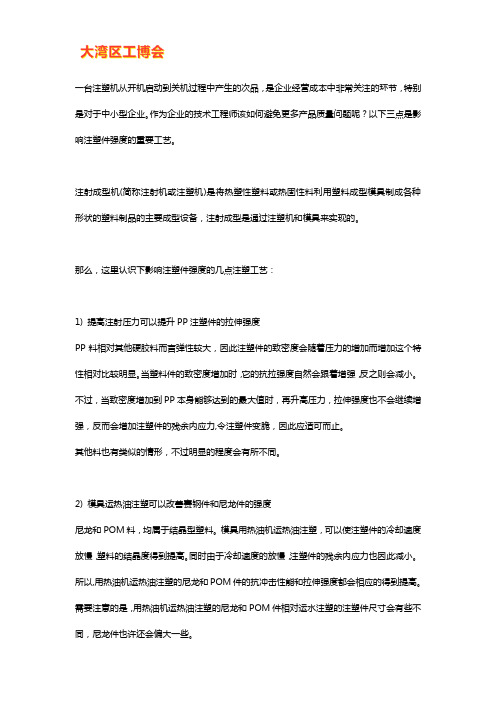
一台注塑机从开机启动到关机过程中产生的次品,是企业经营成本中非常关注的环节,特别是对于中小型企业。
作为企业的技术工程师该如何避免更多产品质量问题呢?以下三点是影响注塑件强度的重要工艺。
注射成型机(简称注射机或注塑机)是将热塑性塑料或热固性料利用塑料成型模具制成各种形状的塑料制品的主要成型设备,注射成型是通过注塑机和模具来实现的。
那么,这里认识下影响注塑件强度的几点注塑工艺:1) 提高注射压力可以提升PP注塑件的拉伸强度PP料相对其他硬胶料而言弹性较大,因此注塑件的致密度会随着压力的增加而增加这个特性相对比较明显。
当塑料件的致密度增加时,它的抗拉强度自然会跟着增强,反之则会减小。
不过,当致密度增加到PP本身能够达到的最大值时,再升高压力,拉伸强度也不会继续增强,反而会增加注塑件的残余内应力,令注塑件变脆,因此应适可而止。
其他料也有类似的情形,不过明显的程度会有所不同。
2) 模具运热油注塑可以改善赛钢件和尼龙件的强度尼龙和POM料,均属于结晶型塑料。
模具用热油机运热油注塑,可以使注塑件的冷却速度放慢,塑料的结晶度得到提高。
同时由于冷却速度的放慢,注塑件的残余内应力也因此减小。
所以,用热油机运热油注塑的尼龙和POM件的抗冲击性能和拉伸强度都会相应的得到提高。
需要注意的是,用热油机运热油注塑的尼龙和POM件相对运水注塑的注塑件尺寸会有些不同,尼龙件也许还会偏大一些。
3) 熔胶速度太快即使180℃注塑也会生胶通常情况下,pvc90度料用180℃注塑,温度已经足够,一般不会出现生胶问题。
但常常是由于未引起操作者注意的原故,或者为了加快生产而有意加快熔胶速度,使得螺杆后退的速度相当快,比如只用了两三秒的时间,螺杆就退到最大熔胶量二分之一以上的位置,PVC 料被加热和搅拌的时间严重不足,造成熔胶温度和混合不均的生胶问题,使得注塑件的强度和韧性都会变得相当的差。
因此,在注塑PVC料的时候,千万要注意不要随便将熔胶转速调到100转/分以上。
注塑成型工艺流程及工艺参数
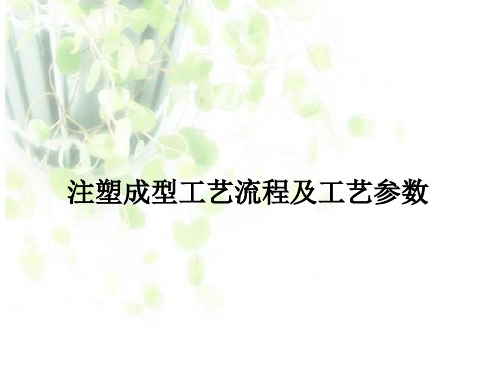
注塑成型工艺流程及工艺参数
塑件的注塑成型工艺过程主要包括填 充——保压——冷却——脱模等4个阶段,这 个阶段直接决定着制品的成型质量,而且这4 个阶段是一个完整的连续过程。
1、填充阶段 1.填充是整个注塑循环过程中的第一步,时间从模
具闭合开始注塑算起,到模具型腔充到大约95%为止 。理论上,填充时间越短,成型效率越高,但是实际 中,成型时间或者注塑速度要受到很多条件的制约。 高速填充。高速填充时剪切率较高,塑料由于剪切变 稀的作用而存在粘度下降的情形,使整体流动阻力降 低;局部的粘滞加热影响也会使固化层厚度变薄。因 此在流动控制阶段,填充行为往往取决于待填充的体 积大小。
ቤተ መጻሕፍቲ ባይዱ
3、冷却阶段
3.熔接痕不仅影响塑件外观,同时由于微观结构的松散,易 造成应力集中,从而使得该部分的强度降低而发生断裂。一 般而言,在高温区产生熔接的熔接痕强度较佳,因为高温情 形下,高分子链活动性较佳,可以互相穿透缠绕,此外高温 度区域两股熔体的温度较为接近,熔体的热性质几乎相同, 增加了熔接区域的强度;反之在低温区域,熔接强度较差。
2、保压阶段
1.保压阶段的作用是持续施加压力,压实熔体,增加塑 料密度(增密),以补偿塑料的收缩行为。在保压过程中, 由于模腔中已经填满塑料,背压较高。在保压压实过程中, 注塑机螺杆仅能慢慢地向前作微小移动,塑料的流动速度 也较为缓慢,这时的流动称作保压流动。由于在保压阶段, 塑料受模壁冷却固化加快,熔体粘度增加也很快,因此模 具型腔内的阻力很大。在保压的后期,材料密度持续增大, 塑件也逐渐成型,保压阶段要一直持续到浇口固化封口为 止,此时保压阶段的模腔压力达到最高值。
1、填充阶段
2. 在流动控制阶段,由于高速填充,熔体的剪切变稀效果往 往很大,而薄壁的冷却作用并不明显,于是速率的效用占了上风。 低速填充。,热传导控制低速填充时,剪切率较低,局部粘度较 高,流动阻力较大。由于热塑料补充速率较慢,流动较为缓慢, 使热传导效应较为明显,热量迅速为冷模壁带走。加上较少量的 粘滞加热现象,固化层厚度较厚,又进一步增加壁部较薄处的流 动阻力。由于喷泉流动的原因,在流动波前面的塑料高分子链排 向几乎平行流动波前。因此两股塑料熔胶在交汇时,接触面的高 分子链互相平行;加上两股熔胶性质各异(在模腔中滞留时间不 同,温度、压力也不同),造成熔胶交汇区域在微观上结构强度 较差。在光线下将零件摆放适当的角度用肉眼观察,可以发现有 明显的接合线产生,这就是熔接痕的形成机理。
注塑工艺及注塑产品常见异常处理

解决办法 更换其他批次原料看是否解决
加强混料时的管控 清洁包装外袋后在加料 使用原料充分清洗炮筒内部
缩水:注塑制件表面(主要发生在塑件壁厚厚的地方、壁厚 改变的地方或者水口的位置)材料堆积区域形成的凹痕。
缩水
产生原因 1、保压压力太低 2、保压时间太短 3、模壁温度太高 4、熔料温度太高 5、模具温度过低
20
熔接痕:塑件表面的一种线状痕迹,系由注射或挤出中若干股流料在 模具中分流汇合,熔料在界面处未完全熔合,彼此不能熔接为一体, 造成熔合印迹。
熔接痕
产生原因 熔料/模具温度太低
浇口太多 浇口太小或堵塞 注射速度太慢 注射压力太小 模具排气不良
解决办法 提高料筒/喷嘴及模具温度 减少浇口或改变浇口位置 增大浇口或清理浇口/流道 提高注射速度或加大浇口尺寸
二、三板模具(二次分型模具)的特点:
• 在定模板和动模板之间有一块模板,在此模板和定 模板之间有水口流道。
• 1、 由于可采用点水口,故不需要对水口位进行后 处理。
• 2、 结构复杂,需分别取出成型品和水口流道。 • 3、 可将浇口置于成型品的任意位置。 • 4、 故障比二板模具多,模具费用也较高。
解决办法 A 降低注射压力或机筒温度B 降低螺杆的旋
转速度或螺杆背压 减少注射时间,减少入料
延长工模冷却时间
延长保压并加强工模冷却
模腔壁再次抛光
产品变形:由于机器设备未调教到位,导致注塑后塑件冷却 后尺寸偏大或者偏小的不良。
产生原因 1.注射压力太大 2.保压时间过长 3.前后模温差太大 4.工模温度过低
• 1、成型零件
• 赋予成型材料形状、结构、尺寸的零件,通常由 型芯(凸模)、凹模型腔以及螺纹型芯、镶块等 构成。
注塑件常见缺陷分析

注塑件常見缺陷分析脱模困难(浇口或塑件紧缩在模具内)一设备方面:顶出力不够。
二模具方面:(1)脱模结构不合理或位置不当。
(2)脱模斜度不够。
(3)模温过高或通气不良。
(4)浇道壁或型腔表面粗糙。
(5)喷嘴与模具进料口吻合不服帖或喷嘴直径大于进料口直径。
三工艺方面:(1)机筒温度太高或注射量太多。
(2)注射压力太高或保压及冷却时间长。
四原料方面:润滑剂不足。
造成注塑制品不满的原因分析造成注塑制品射料不满的主要原因是缺料和注射压力与速度不妥(包括阻力造成压力过于耗损)。
可能由以下几个方面的原因导致而成:1.注塑机台原因:机台的塑化量或加热率不定,应选用塑化量与加热功率大的机台;螺杆与料筒或过胶头等的磨损造成回料而出现实际充模量不中;热电偶或发热圈等加热系统故障造成料筒的实际温度过低;注射油缸的密封元件磨损造成漏油或回流,而不能达到所需的注射压力;射嘴内孔过小或射嘴中心度调节不当造成阻力过大而使压力消耗。
2.注塑模具原因:1.模具局部或整体的温度过低造成入料困难,应适当提高模温;2.模具的型腔的分布不平衡。
制件壁厚过薄造成压力消耗过磊而且充模不力。
应增加整个制件或局部的壁厚或可在填充不足处的附近,设置辅助流或浇口解决。
3.模具的流道过小造成压力损耗;过大时会出现射胶无力;过于粗糙都会造成制件不满。
应适当设置流道的大小,主流道与分流道,浇口之间的过渡或本身的转弯处应用适当的圆弧过渡。
4.模具的排气不良。
进入型腔的料受到来不及排走的气体压力的阻挡而造成充填不满。
可以充分利用螺杆的缝隙排气或降低锁模力利用分型面排气,必要时要开设排气沟道或气孔注塑过程出现气泡现象的解决办法根据气泡的产生原因,解决的对策有以下几个方面:1)在制品壁厚较大时,其外表面冷却速度比中心部的快,因此,随着冷却的进行,中心部的树脂边收缩边向表面扩张,使中心部产生充填不足。
这种情况被称为真空气泡。
解决方法主要有:a)根据壁厚,确定合理的浇口,浇道尺寸。
注塑工艺参数对塑料产品成型的影响
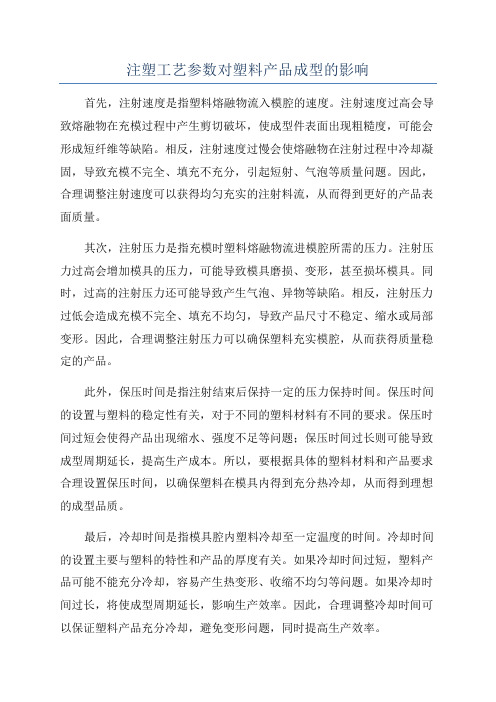
注塑工艺参数对塑料产品成型的影响首先,注射速度是指塑料熔融物流入模腔的速度。
注射速度过高会导致熔融物在充模过程中产生剪切破坏,使成型件表面出现粗糙度,可能会形成短纤维等缺陷。
相反,注射速度过慢会使熔融物在注射过程中冷却凝固,导致充模不完全、填充不充分,引起短射、气泡等质量问题。
因此,合理调整注射速度可以获得均匀充实的注射料流,从而得到更好的产品表面质量。
其次,注射压力是指充模时塑料熔融物流进模腔所需的压力。
注射压力过高会增加模具的压力,可能导致模具磨损、变形,甚至损坏模具。
同时,过高的注射压力还可能导致产生气泡、异物等缺陷。
相反,注射压力过低会造成充模不完全、填充不均匀,导致产品尺寸不稳定、缩水或局部变形。
因此,合理调整注射压力可以确保塑料充实模腔,从而获得质量稳定的产品。
此外,保压时间是指注射结束后保持一定的压力保持时间。
保压时间的设置与塑料的稳定性有关,对于不同的塑料材料有不同的要求。
保压时间过短会使得产品出现缩水、强度不足等问题;保压时间过长则可能导致成型周期延长,提高生产成本。
所以,要根据具体的塑料材料和产品要求合理设置保压时间,以确保塑料在模具内得到充分热冷却,从而得到理想的成型品质。
最后,冷却时间是指模具腔内塑料冷却至一定温度的时间。
冷却时间的设置主要与塑料的特性和产品的厚度有关。
如果冷却时间过短,塑料产品可能不能充分冷却,容易产生热变形、收缩不均匀等问题。
如果冷却时间过长,将使成型周期延长,影响生产效率。
因此,合理调整冷却时间可以保证塑料产品充分冷却,避免变形问题,同时提高生产效率。
总之,注塑工艺参数的设置对于塑料产品的成型质量和性能有着重要的影响。
通过合理调整注射速度、注射压力、保压时间和冷却时间等参数,可以获得质量稳定、表面质量良好的塑料产品。
因此,在注塑生产过程中,应根据具体的塑料材料特性和产品要求,选择合适的工艺参数,以提高注塑成型的质量和效率。
注塑工艺及参数设定

注塑工艺及参数设定首先,注射压力是指在注射过程中,由于塑料熔体注入模腔而产生的压力。
注射压力过大会造成模具过度开合,导致制品尺寸偏大,表面粗糙,甚至可能造成模具损坏;而注射压力过小则会使制品的充填不充分,导致短射或者气孔等缺陷。
注射压力的设定要根据材料的特性和模具的结构来确定。
其次,注射速度是指熔融塑料进入模腔的速度。
注射速度过快会造成破坏模具或者产生气泡等缺陷,而注射速度过慢会使制品的表面产生瑕疵。
注射速度的设定要根据材料的流动性和产品的结构来确定。
保压时间是指塑料在模腔内保持一定压力以保证制品的密实度和尺寸稳定性的时间。
保压时间过长会造成注塑周期延长,产量降低;保压时间过短会导致制品的表面缩短、收缩变形。
保压时间的设定需要根据产品的结构和材料的特性来确定。
保压压力是指在注射结束后,通过保持一定的压力来排除模具内的气体和缩短产品的填充时间的压力。
保压压力过大会导致产品产生变形,甚至可能导致模具损坏;保压压力过小会使得产品的尺寸稳定性降低。
保压压力的设定需要根据产品的形状和材料的特性来确定。
注射温度是指塑料熔融后进入模腔的温度。
注射温度过高会使材料分解、气泡产生、雪花状漏料等缺陷,而注射温度过低会导致进料不良、机器健康下降等不良问题。
注射温度的设定需要根据材料的熔点范围和热稳定性来确定。
冷却时间是指模具中塑料冷却至足够硬度以便脱模的时间。
冷却时间过短会导致产品收缩变形,冷却时间过长会使注塑周期延长。
冷却时间的设定需要根据产品的厚度和材料的热传导性来确定。
除了以上参数外,注塑工艺还包括模具温度、制品质量要求、模腔排气处理、材料干燥要求等各种工艺因素。
正确设置注塑工艺参数能够保证产品质量、提高生产效率和生产效益。
所以在实际生产中,根据产品的特性和要求,合理设定注塑工艺参数是至关重要的。
注塑产品常见问题及改善方法【大全】

注塑成型加工过程是一个涉及模具设计、模具制造、原材料特性和原材料预处理方法、成型工艺、注塑机操作等多方面因素,并与加工环境条件、制品冷却时间、后处理工艺密切相关的复杂加工流程。
因此塑料制品质量的好坏就不单取决于注塑机的注塑精度、计量精度,或是仅仅由模具设计的优劣和模具加工的精度级别决定,通常,它还会受到上述的其他因素的影响和制约。
注塑产品常见问题及解决方案:一、毛刺(或称飞边、溢边、溢料):毛刺的发生是由于熔融注塑树脂从模具分型面上溢出而形成,是成形作业中最恶劣的状态。
特别是当毛刺牢固地粘附在模具分型面上而进行锁模时,会损伤模具分型面.模具由此引起损伤后,重新作业时成形品将会产生新的毛刺。
同时也加剧模具的损坏并导致不能使用。
所以要特别加以注意。
(1)不要使用过高的注射压力(2)提高锁模力(3)妥善保管模具(4)调整注射量、降低温度.二、充填不足(或称成形不足):成形不足是由于熔融注塑树脂尚未完全充满模腔时就已冷却硬化而形成的成形缺陷,主要原因是树脂容量不足、型腔内加压不足、树脂流动性不足、排气效果不好。
在成型机注射量充分的情况下,成形不足的状况仍得不到改善时,应考虑是否注射压力不足或熔融树脂的设定温度偏低。
三、熔接痕(或称结合线):熔接痕是指在成形品表面产生的细线状对合缝痕迹,是由于来自不同方向的熔融树脂前端部分被冷却、在结合处未能完全融合而产生的。
不注意观察时,难以发现。
熔接痕经常发生在模腔内流动的熔融树脂的融合面上。
主要影响外观,对涂装、电镀产生影响。
严重时,对制品强度产生影响,为了保证成形品的质量,应尽量消除此类缺陷。
调整成型条件,提高流动性。
四、凹陷(或称缩坑):凹陷的发生在成形品表面缺陷中最为常见。
它是由成形品热收缩引起体积变化,在壁厚部位形成的缺陷。
凹陷与成形不足相比为程度较轻的缺陷。
常发生于模腔被熔融树脂充满,但保压压力不充分的场合。
五、气泡:气泡易发生于成形品壁厚较厚部位,形成的原因与成形品凹陷完全相同。
注塑件常见原因分析

注塑件常见原因分析
注塑件是制造业中常用的一种零部件,具有成本低、生产效率高、制造周期短等优点。
然而,由于注塑工艺相对复杂,注塑件在生产过程中可能会出现各种问题。
以下是注塑件常见原因分析的一些可能因素。
1.材料问题:
材料的选择对注塑件的质量有着重要的影响。
如果材料本身有缺陷或不符合要求,会导致注塑件出现问题。
例如,材料含水率过高会导致注塑件产生气泡,降低机械性能;材料中添加剂含量不准确会导致注塑件出现色差等问题。
2.模具问题:
模具是注塑件生产过程中的关键因素之一、如果模具设计不合理、加工精度不够或使用寿命较短,可能会导致注塑件尺寸不准确、表面粗糙或产生开裂等问题。
3.注塑工艺问题:
注塑工艺的参数设置直接影响注塑件的质量。
如果温度、时间、压力等参数设定不准确,可能导致注塑件缩水、变形等问题。
例如,加热温度过高会引起熔融物流动性增加、熔胶温度下降过快造成冷料温度过低,导致注塑件表面出现缺陷。
4.操作问题:
5.环境问题:
环境条件也会对注塑件的质量产生一定影响。
如果湿度过高,可能会导致注塑件表面出现气泡;如果温度过低,可能导致注塑件收缩不均匀。
6.质量管理问题:
质量管理是确保注塑件质量的重要环节。
如果企业没有严格的质量管理体系,以及缺乏相关的检测设备和人员,可能会导致注塑件的质量无法得到有效控制。
综上所述,注塑件常见问题的原因分析可以从材料问题、模具问题、注塑工艺问题、操作问题、环境问题和质量管理问题等方面进行考虑。
只有全面分析各种可能因素,并进行相应的改进和优化措施,才能提高注塑件的质量和生产效率。
注塑件常见品质问题及原因分析

注塑件常见品质问题及原因分析注塑件常见品质问题及原因分析、解决方法一、注塑件常见品质问题华缝品技部2014.5.30塑胶件成型后,出现一些不良问题,会影响装配效率或整机性能,与预定的质量标准(检验标准)有一定的差异,不能满足公司的品质要求。
除了加强员工的质量意识培训、对有不良的配件及时处理(比如挑选、加工等);这些缺陷可能是由如下几方面造成:模具、原材料、工艺参数、设备、环境、人员。
现将缺陷问题总结如下:1、色差:注塑件颜色与该单标准色样用肉眼观看有差异,判为色差,在标准的光源下(D65)。
2、注塑不满(缺胶):注塑件不饱满,出现气泡、空隙、缩孔等,与标准样板不符称为缺胶。
3、翘曲变形:塑胶件形状在塑件脱模后或稍后一段时间内产生旋转和扭曲现象,如有直边朝里,或朝外变曲或平坦部分有起伏,如拨叉、加强座等变形,有局部和整体变形之分。
4、熔接痕(纹):在塑胶件表面的线状痕迹,由塑胶在模具内汇合在一起所形成,而熔体在其交汇处未完全熔合在一起,彼此不能熔为一体即产生熔接纹,多表现为一直线,由深向浅发展,此现象对外观和力学性能有一定影响。
如勾盘底部的熔接痕。
5、波纹:注塑件表面有螺旋状或云雾状的波形凹凸不平的表征现象,或透明产品的里面有波状纹,称为波纹。
6、溢边(飞边、披锋):在注塑件四周沿分型线的地方或模具密封面出现薄薄的(飞边)胶料,称为溢边。
7、银丝纹:注塑件表面的很长的、针状银白色如霜一般的细纹,开口方向沿着料流方向,在塑件未完全充满的地方,流体前端较粗糙,称为银丝纹(银纹)。
8、色泽不均(混色):注塑件表面的色泽不是均一的,有深浅和不同色相,称为混色,如505压脚支架,加了不同颜色的水口料后,黑一块白一块,混色。
9、光泽不良(暗色):注塑件表面为灰暗无光或光泽不均匀称为暗色或光泽不良。
10、脱模不良(脱模变形):与翘曲变形相似,注塑件成型后不能顺利的从模具中脱出,有变形、拉裂、拉伤等、称为脱模不良。
塑料件注塑工艺及缺陷解决办法

注塑零件常见缺陷分析与解决方法
6.熔料温度太低 熔料温度太低 解决方法:将料桶加热到仪表设定的温度后还需恒温一段时间才能开机。 如果为了防止熔料分解不得不采取低温注射时,可适当延长注射循环时间, 克服欠注。 7.喷嘴温度太低 喷嘴温度太低 解决方法:在开模时应使喷嘴与模具分离。减少模温对喷嘴温度的影响, 使喷嘴处的温度保持在工艺要求的范围内。或适当提高喷嘴加热温度。 8.注射压力或保压压力不足 注射压力或保压压力不足 解决方法:通过减慢射料螺杆前进速度,适当延长注射时间等方法提高 注射压力。或通过适当提高料温降低熔料黏度,以提高流动性能补救。或通 过适当增加保压时间等方法弥补。 9.注射速度太慢 注射速度太慢 解决方法:适当提高注射速度。 10.塑件结构设计不合理 塑件结构设计不合理 解决方法:在注塑成型时,塑件的厚度应采用1~3mm,大型塑件为3~6mm ,厚度超过8mm或小于0.5mm都对注塑成型不利,设计时应尽量避免。 11.塑料塑化不充分 塑料塑化不充分 解决方法:检查是否有未融化的塑料或杂质。调整背压、适当提高加热 温度及塑化时间、及螺杆转速。
注塑零件常见缺陷分析与解决方法
3.模具排气不良 模具排气不良 解决方法:检查模具排气孔是否被塑料的固化物或其他物体阻塞;在模 具汇料点处增加排气孔,也可通过重新定位浇口,或适当降低锁模力,增大 排气间隙来加速汇料合流。 4.脱模剂使用不当 脱模剂使用不当 在注塑成型中,一般只在螺纹等不易脱模的部分才均匀地涂用少量脱模 剂,原则上尽量减少脱模剂的用量。 5.塑件结构设计不合理 塑件结构设计不合理 解决方法:设计塑件形体结构时,应确保塑件的最薄部位必须大于成型 时允许的最小壁厚,尽可能使壁厚趋于一致。尽量减少嵌件的设计及避免厚 度变化太大。 6.熔接角度太小 熔接角度太小 极限熔接角度一般在135°左右,大于极限熔接角度,熔接痕便消失。 7.塑料的流动性不好 塑料的流动性不好 解决方法:在塑件功能许可范围内,可以考虑改用流动指数(MI)值 较高的塑料。 8.其它原因 其它原因 当使用的原料水分或易挥发物含量太高,模具中油渍未清除干净,模腔 中有冷料或塑料内的纤维填料分布不均,模具冷却系统设计不合理,熔料固 化太快,嵌件温度太低,喷嘴孔设计太小注塑机塑化能力不够,压力损失大 ,都会导致不同程度的熔接痕。
- 1、下载文档前请自行甄别文档内容的完整性,平台不提供额外的编辑、内容补充、找答案等附加服务。
- 2、"仅部分预览"的文档,不可在线预览部分如存在完整性等问题,可反馈申请退款(可完整预览的文档不适用该条件!)。
- 3、如文档侵犯您的权益,请联系客服反馈,我们会尽快为您处理(人工客服工作时间:9:00-18:30)。
1)提高注射壓力可以提升PP注塑件的拉伸強度
PP料相對其他硬膠料而言彈性較大,因此注塑件的致密度會隨著壓力的增加而增加這個特性相對比較明顯。
當塑膠件的致密度增加時,它的抗拉強度自然會跟著增強,反之則會減小。
不過,當致密度增加到PP本身能夠達到的最大值時,再升高壓力,拉伸強度也不會繼續
增強,反而會增加注塑件的殘余內應力令注塑件變脆,因此應適可而止。
其他料也有類似的情形,不過明顯的程度會有所不同。
2)模具邿嵊妥⑺芸梢愿善賽鋼件和尼龍件的強度
尼龍和POM料,均屬于結晶型塑料。
模具用熱油机邿嵊妥⑺埽梢允棺⑺芗的冷卻速度放慢,塑料的結晶度得到提高。
同時由於冷卻速度的放慢,注塑件的殘余內應力也因此減小。
所以
用熱油机邿嵊妥⑺艿哪猃埡POM件的抗沖擊性能和拉伸強度都會相應的得到提高。
需要注意的是,用熱油机邿嵊妥⑺艿哪猃埡POM件相對咚⑺艿淖⑺芗尺寸會有些不同,尼
龍件也許還會偏大一些。
3)熔膠速度太快即使180℃注塑也會生膠
通常情況下,PVC90度料用180℃注塑,溫度已經足夠,一般不會出現生膠問題。
但常常是由於未引起操作者注意的原故,或者為了加快生產而有意加快熔膠速度,使得螺杆后退的速度相當快,比如只用了兩三秒的時間,螺杆就退到最大熔膠量二分之一以上的位置,PVC料被加熱和攪拌的時間嚴重不足,造成熔膠溫度和混合不均的生膠問題,使得注塑件的強度和韌性都會變得相當的差。
因此,在注塑PVC料的時候,千萬要注意不要隨便將熔膠轉速調到100轉/分以上。
如果一定要調得相當快,就要記住將料溫升高5至10℃,或者適當增加熔膠背壓來配合,同時還要注意經常檢查有沒有發生生膠問題,否則极有可能會造成重大的損失。
關於這個問題,因一般人都不會太在意,所以這裡特別提出來提醒生產時必須注意,並且要記得做好檢查功夫。
相反也要注意的是,如果熔膠速度過慢,哪怕是180度注塑PVC90度的料,也會造成燒膠的問題,特別是透明PVC,注塑件上會有許多黑斑和氣紋產生。