发酵罐制作、安装的说明
小型微生物发酵罐施工方案

小型微生物发酵罐施工方案1. 引言发酵技术是生物工程中的一项重要技术,在医药、食品、化工等领域都有广泛应用。
小型微生物发酵罐是进行微生物发酵实验和小规模生产的重要设备之一。
本文档将详细介绍小型微生物发酵罐的施工方案。
2. 设备选型小型微生物发酵罐的选型需要考虑以下几个方面:•容量:根据实验或生产的需求确定罐体容量。
常见的小型微生物发酵罐容量为5L、10L、20L等。
•材质:选择耐腐蚀、耐高温的材质,常见的材质有不锈钢、玻璃等。
•设备配置:包括搅拌器、温度传感器、气体供给系统等。
根据具体需求选择合适的配置。
3. 施工流程3.1 罐体制作1.根据选定的容量和材质,制作罐体。
如果选择不锈钢材质,需要进行切割、焊接等工艺,保证罐体的密封性和结构强度。
2.罐体表面进行抛光处理,以保证表面平整、无氧化物和细菌。
3.2 设备安装1.安装搅拌器:根据实验需求选择适合的搅拌器,并按照生产厂商提供的安装说明进行安装。
2.安装温度传感器:将温度传感器固定在罐体内部,并与温控系统相连。
3.安装气体供给系统:根据实验需求选择合适的气体供给系统,并将其与罐体连接。
3.3 管路安装1.气体管路:安装气体过滤器、调压器等设备,确保气体供给稳定。
2.水冷系统:根据实验需求选择适合的水冷系统,并安装在罐体外部。
3.电气控制系统:安装电气控制柜,并将各设备的电气接线连接到控制柜。
3.4 系统调试1.检查管路连接是否紧密、气密性是否良好。
2.检查搅拌器、温度传感器、气体供给系统等设备是否正常工作。
3.进行罐体的消毒处理,保证无菌状态。
3.5 系统操作1.根据发酵工艺要求,设置好温度、pH等参数。
2.确保罐体内部气体供给充足。
3.监测发酵过程中的温度、溶氧量等指标,并做好记录。
4. 安全措施•在操作过程中,必须佩戴防护眼镜、手套等个人防护装备,以防发生意外。
•发酵罐周围应保持整洁,避免杂物堆放,以免影响操作。
•发酵罐施工完毕后,应及时进行清洗和消毒,以保证下次使用的安全性。
发酵罐操作规程范文

发酵罐操作规程范文发酵罐是发酵生产中非常重要的设备,其操作规程对于保证生产质量、提高产量具有至关重要的作用。
下面是一份发酵罐操作规程,供参考:一、发酵罐操作前的准备工作1.检查发酵罐设备的机械和电气设备是否正常,确保设备运行无异常。
2.清洁发酵罐内部和外部,确保无残留物质干净。
3.检查发酵罐是否有漏气现象,如果有,及时进行维修。
4.准备好所需的原料、辅料和发酵罐操作所需的其他设备。
二、发酵罐操作规程1.将所需原料按照配方比例加入到发酵罐中。
2.根据发酵工艺要求,将发酵罐内温度、湿度、PH值等参数设定好。
3.启动发酵罐的搅拌设备,确保原料充分混合。
4.启动发酵罐的通风设备,确保发酵罐内空气流通良好。
5.监控发酵罐内温度、湿度、PH值等参数,及时调整。
6.根据发酵工艺要求,定期对发酵罐内的发酵情况进行检查,如有需要进行适当的调整。
7.发酵过程中,要定期清洁发酵罐内部和外部,确保无污物残留。
8.发酵结束后,将发酵罐内的发酵物料转移至下一步工序,清洁发酵罐。
9.对发酵罐进行定期的检修和保养,确保设备运行良好。
10.记录发酵过程的温度、湿度、PH值等参数,并做好数据备份。
三、发酵罐操作注意事项1.注意发酵罐内部压力的变化,确保安全操作。
2.注意发酵罐内的通风情况,确保空气流通。
3.发酵罐操作过程中要及时调整参数,确保发酵工艺正常进行。
4.不得在发酵罐内随意添加物质,防止影响生产质量。
5.禁止在发酵罐操作过程中吸烟、喝酒等行为,确保生产安全。
6.发酵罐操作人员应穿戴好防护装备,确保安全操作。
7.注意发酵罐设备的维护保养,延长设备寿命。
发酵罐制作安装的说明

发酵罐制作安装的说明发酵罐是一种常见的用于发酵蔬菜、水果、酒精、酱料等食品的设备。
下面将详细介绍发酵罐的制作及安装过程。
第一步:准备材料和工具1.发酵罐主体材料:不锈钢、陶瓷、玻璃等。
选择材料时需考虑到食品发酵的特性和食品与材料之间的相容性。
2.发酵罐盖材料:通气性好的材料,如布料或防腐纸。
3.发酵罐配件:气体出口、温度计、发酵罐底部垫片等。
4.工具:锤子、电钻、铁钳、螺丝刀、尺子、刀具等。
第二步:发酵罐制作1.制作罐体:根据所选材料的尺寸要求,将材料切割成合适大小的块状。
2.连接罐体:使用螺丝或焊接将切割好的罐体拼接在一起,确保连接牢固。
3.加工罐盖:根据罐体的形状,制作一个适合的罐盖。
罐盖上需要制作一个通气孔,便于气体排出。
4.安装配件:根据需要,安装气体出口、温度计和底部垫片等配件。
垫片可用于保护发酵罐底部,减少噪音和摩擦。
第三步:发酵罐安装1.选择安装位置:发酵罐需要放置在通风、干燥、避光和无异味的地方,远离热源和可燃物。
2.支架搭建:根据发酵罐的尺寸和重量,搭建一个稳定的支架,确保发酵罐的安全。
3.安装罐体:将制作好的发酵罐放置在支架上,确保罐体稳定,不易倾斜。
4.连接电源:如果需要加热或冷却发酵罐,连接电源,并确保电线走线合理、安全可靠。
5.安装温度计:将温度计插入罐体内部,并确保准确读取温度。
6.测试运行:在安装完成后,运行发酵罐一段时间,观察是否运行正常,温度和通风是否达到预期效果。
第四步:注意事项和维护1.发酵罐使用过程中应保持清洁,避免食品和杂质残留,以免影响发酵效果。
2.定期检查和清洗发酵罐,防止结垢、霉菌和细菌滋生。
3.注意发酵罐的温度控制,避免过高或过低的温度对食品产生不良影响。
4.及时更换或维修罐体和配件,确保发酵罐的正常运行和安全性。
总结:发酵罐的制作和安装是一个涉及材料选择、加工、组装和安装等多个步骤的过程。
在制作和安装过程中,需严格遵守安全操作规程,确保工作环境和设备安全可靠。
发酵罐操作说明

发酵罐操作说明发酵罐是一种用于制造各种发酵食品的设备,如酸奶、啤酒、酸菜等。
本文将为您介绍如何正确操作发酵罐,以确保食品质量和安全。
1. 准备工作在操作发酵罐之前,首先需要做一些准备工作。
确保发酵罐干净卫生,无异味或残留物。
如果是新的发酵罐,应进行清洗和消毒。
确保所有工具和材料都是清洁的,以避免杂菌污染。
2. 食材准备根据所制作的发酵食品的食谱,准备好所需的食材。
确保食材新鲜,并按照食谱的要求进行配比。
记住,发酵食品的质量和味道很大程度上取决于所使用的食材质量。
3. 投料在投料之前,确保发酵罐已经适当设置好。
将发酵罐放在一个稳定的表面上,并确保所有零部件都安装牢固。
将所需的食材倒入发酵罐中,并按照食谱的要求进行操作。
如果需要加入任何发酵剂或酵母,确保按照准确的配方进行投放。
4. 温度控制发酵过程中的温度是非常重要的。
根据食谱的要求,保持罐内的温度在适当的范围内。
有些发酵过程需要较低的温度,而其他一些过程需要较高的温度。
确保根据需要调整发酵罐的温度控制系统。
5. 氧气供应有些发酵过程需要氧气供应,而其他一些过程则需要最小的氧气接触。
根据食谱的要求,决定是否需要开启发酵罐的氧气供应系统。
如果需要,确保氧气供应充足且有稳定的通风。
6. 发酵时间根据食谱的要求,设定适当的发酵时间。
不同的发酵食品需要不同的时间来完成发酵过程。
确保在发酵过程中注意定时,并按照食谱要求适时检查食品的发酵状况。
7. 监控和调整在发酵过程中,应定期监控发酵食品的状态。
注意观察是否有异常情况或异味产生。
如果需要,根据食谱的要求进行调整,如温度、湿度等。
8. 发酵结束当食品达到食谱要求的发酵状态时,即可结束发酵过程。
根据需要,将发酵食品转移到适当的容器中,存放在温度适宜的地方。
确保及时清洁和消毒发酵罐,以准备下一次使用。
总结正确操作发酵罐对于制造高质量的发酵食品至关重要。
请确保罐内整洁卫生、食材新鲜且质量良好、按食谱要求操作、温度和氧气供应适宜、发酵时间准确、监控发酵过程并及时调整。
发酵罐及其附属设备的安装

他应用。所有电源插座都应配有密封盖,不用时
盖上,以防溅水。其他动力源:空气管道入罐前
压力为 0.15~0.20MPa;仪表气源压力为 0.4~ 0.5MPa;蒸汽管道压力为 0.25~0.30MPa。特殊
但相比在房间看着她们愉快的聊天,显然我喜欢阳台。在接近两个小时的
应用还需要配备冷盐水、真空或氮气气源。6.冷
1.安装空间一台 10L 或 30L 的发酵罐,必须
有大小为 2m×2.5m 以上的建筑平面面积,才能
够满足使用和维护的需要。需要的建筑高度,则 根据设备的总高度确定。2.罐体安装罐体安装应
保持水平位置,搅拌轴保持垂直,基础牢靠,以
确保运转时平稳,无震动。3.排气(汽)管道安装
排气(汽)管道在灭菌时有大量蒸汽排放,必须连 接到室外的汽水分离器,不得在室内留排气口,
有水封,一来阻隔臭味,二来可以防止下水道内 的少量蒸汽上泛。小型发酵罐的取样显然我喜欢阳台。在接近两个小时的
一般可不设置地漏,而用塑料桶接料。5.动力配
置除了按设备安装说明书的要求给搅拌马达和
仪器仪表配电外,还要分别配备四孔的 380V 和 两孔、三孔的 220V 备用电源插座,以便维修及其
但相比在房间看着她们愉快的聊天,显然我喜欢阳台。在接近两个小时的
否则在灭菌时可使室内湿度大幅度增加,不利于
设备的维护。有的人贪图方便,将所有排气口与
下水道连接,殊不知这样一来在灭菌时所有下水 道口都将往外冒蒸汽,使室内操作环境恶化,并
降低设备的寿命。4.下水道装配下水道要求在地
面以下,并保持通畅。所有下水道入口即地漏要
却用水的配置冷却用水最好采用可调温循环冷
却无盐水,尽可能不用自来水或冷盐水,这样一 方面可避免在冷却夹套或盘管内结垢,另一方面
发酵罐及其附属设备制作安装工程施工组织设计方案
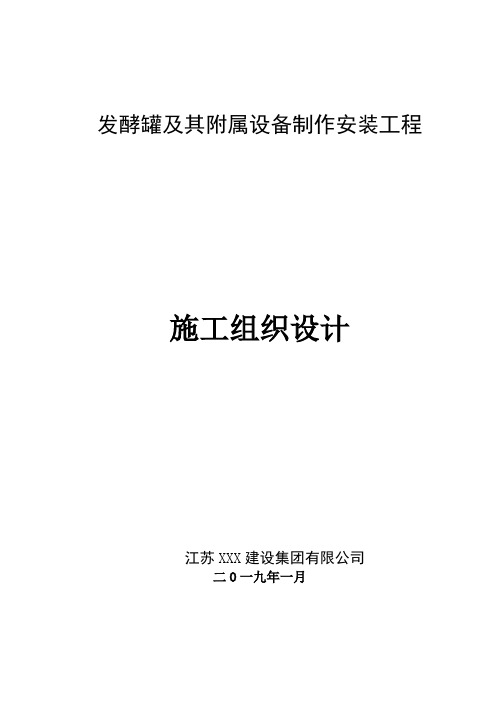
发酵罐及其附属设备制作安装工程施工组织设计江苏XXX建设集团有限公司二O一九年一月目录一、工程概况 (1)二、工期及质量目标 (2)三、施工准备 (2)四、施工组织管理网络 (4)五、施工总体部署 (6)六、主要分部、分项施工方案 (7)七、针对本工程特点采用的特殊措施 (36)八、质量保证措施 (37)九、工期保证措施 (40)十、安全生产施工措施 (44)十一、文明施工管理措施 (48)十二、降低成本、提高经济效益措施 (51)十三、主要施工机械和工具、主要周转材料、劳动力一览表 (52)十四、施工总进度计划 (55)十五、施工总平面布置图 (56)一、工程概况1、编制说明:本施工组织设计是依据XXXX环保有限公司厌氧罐二期项目招标文件、设计施工图纸、安装工程技术规定、施工及验收规范等有关文件资料,结合我公司多年承担大型立式圆筒形钢制焊接储罐和有关餐厨项目厌氧发酵罐及附属设施制作安装工程的施工安装所积累的丰富经验进行编制。
主要解决和阐述涉及本工程的施工组织管理、分部分项工程的施工方法与技术措施、确保工程质量与工程进度措施、创安全生产及文明施工标化管理措施、以及相应的人、财、物力配套计划与投入,目的是确保本工程在科学的管理下,通过有效的预控,有组织、有计划地完成既定的各项指标和工程建设。
2、工程概况:2.1、工程内容:发酵罐及其附属设备制作安装工程。
2.2、施工地点:XXXXX环保产业园。
2.3、工程范围:1)(公称容积:5020m3)厌氧发酵罐1台制作、安装;2)(全容积:~24m3)除砂器(包括钢制支腿)1台制作、安装;3)发酵罐沼气喷嘴1套制作、安装;4)发酵罐加热套筒1套制作、安装;5)发酵罐罐体爬梯、平台与管道支架制作、安装。
包括罐体内壁、内部构件喷砂除锈、防腐,外壁及附属设施除锈、防腐、保温;罐体试水试漏、气密性试验、管道、罐内清理吹扫;罐体外保温圈的焊接以及约定的其他事项。
3、本工程施工应遵循的规范、标准及依据:业主提供的设备图纸设计技术要求及有关技术文件要求GB50128-2014《立式圆筒形钢制焊接储罐施工及验收规范》GB150.1-150.4-2011《压力容器》GB/T985-2008《气焊、手工电弧焊及气体保护焊焊缝坡口的基本形式与尺寸》GB50236-2011《现场设备、工业管道焊接工程施工验收规范》NBT47013.1-13 -2015《承压设备无损检测》JB/T4736-2002《补强圈》GB50205-2008《钢结构施工及验收规范》HGJ299-1991《工业设备、管道防腐蚀工程施工及验收规范》GB/T4272-2008《设备及管道保温技术通则》GB/T8923.1-2011《涂覆涂料前钢材表面处理表面清洁度的目视评定第1部分:未涂覆过的钢材表面和全面清除原有涂层后的钢材表面的锈蚀等级和处理等级》二、工期及质量目标1、工期目标:本工程计划工期85日历天,实际开工日期以建设单位批准的开工日期为准。
发酵罐安全操作规程

发酵罐安全操作规程发酵罐是一种用于进行微生物发酵工艺的设备,安全操作规程对于确保人员和设备的安全至关重要。
以下是一个关于发酵罐安全操作规程的2000字篇幅。
第一章:总则1.1 目的发酵罐安全操作规程的目的是为了确保发酵过程中可以预防和控制危险,保障人员的安全和健康,保护设备的正常运行,降低事故发生的风险。
1.2 适用范围本操作规程适用于所有使用发酵罐进行微生物发酵工艺的工作人员和相关人员。
第二章:基本要求2.1 人员培训2.1.1 所有使用发酵罐的工作人员必须接受相关的安全培训,了解发酵罐的基本操作和安全要求。
2.1.2 操作人员必须具备一定的发酵技术和安全知识,并经过定期培训和考核。
2.2 安全设施2.2.1 发酵罐周围应设有明显的安全警示标识,包括发酵罐的危险性提示、禁止入内提示等。
2.2.2 发酵罐工作区域应设置围栏或其他有效的隔离措施,限制无关人员进入。
2.2.3 发酵罐操作区域应保持干净整洁,无杂物堆放。
2.3 发酵罐设计和安装2.3.1 发酵罐的设计和制造必须符合相关的安全标准和规范。
2.3.2 发酵罐在安装前必须经过严格的检查和测试,确保其正常运行和安全性。
2.4 操作前准备2.4.1 操作人员必须仔细阅读发酵罐的操作说明书,并了解发酵过程中可能遇到的风险和应急处理措施。
2.4.2 在操作前,操作人员必须进行个人防护装备的佩戴,包括防护眼镜、防护手套、工作服等。
第三章:操作流程3.1 发酵罐启动前检查3.1.1 检查发酵罐的电气设备和仪表是否正常运行。
3.1.2 检查发酵罐的液位、温度、压力等参数是否在正常范围内。
3.1.3 检查发酵罐的进料管道和排放管道是否畅通。
3.2 发酵罐运行操作3.2.1 打开发酵罐的供气阀门,保证发酵物质能够正常进行气体交换。
3.2.2 根据工艺要求,加入适量的发酵基质和营养物质。
3.2.3 控制发酵罐的搅拌速度和温度,确保发酵过程进行顺利。
3.3 发酵罐停机操作3.3.1 在停机前,逐步减少发酵罐的搅拌速度和温度。
厌氧发酵罐使用方法说明书

厌氧发酵罐使用方法说明书使用方法说明书一、产品概述本说明书是针对厌氧发酵罐的使用方法进行详细说明,以帮助用户顺利操作和维护设备。
二、设备说明1. 设备名称:厌氧发酵罐2. 设备型号:XXX型号3. 设备尺寸:根据用户需求定制4. 设备重量:根据用户需求定制5. 设备材质:不锈钢三、安装要求1. 设备安装需由专业技术人员进行,确保安装过程符合相关标准和要求。
2. 安装位置应选择通风良好、安全稳定的场所,以保证设备的正常运行。
3. 设备安装完成后,需进行检查和试运行,确保各功能正常。
四、操作步骤1. 打开主控柜电源,确保供电正常。
2. 运行主控系统,在界面上选择相应的操作选项。
3. 根据实际需要,设置温度、压力等相关参数。
4. 加入发酵物料,注意控制投料量和投料时间。
5. 启动设备,等待发酵过程完成。
6. 发酵完毕后,停止设备运行,将发酵物料转移或清理干净。
7. 关闭主控柜电源,确保设备安全。
五、维护保养1. 定期检查设备胶管、阀门等易损件的损耗情况,如有磨损或老化应及时更换。
2. 清洁设备内部,确保无残留物和异味。
3. 定期检查电源线路和电器元件的连接情况,确保设备供电正常。
4. 对设备进行定期润滑,确保机械部件的正常运转。
六、安全注意事项1. 遵守操作规程,不得擅自更改设备参数或操作方式。
2. 使用过程中避免将手或其他物体伸入设备内部。
3. 发现设备异常情况时,及时停止使用并联系售后服务。
4. 在对设备进行维护保养时,应先将电源切断,以确保人身和设备安全。
七、故障排除1. 设备无法启动:检查电源线是否接触良好,确保供电正常;检查控制系统是否故障。
2. 温度过高或过低:检查温度传感器是否损坏,更换并重新设置温度参数。
3. 压力异常:检查压力传感器是否损坏,更换并重新设置压力参数。
八、售后服务1. 本产品提供一年免费保修服务,自购买之日起计算。
2. 在保修期内,如设备出现故障,可联系售后服务人员进行处理。
发酵罐 操作说明书

发酵系统操作规程一、发酵前准备工作(1)检查电源是否正常,空压机、蒸汽发生器和循环水系统是否正常工作。
(2)检查系统上的阀门、接头及紧固螺钉是否拧紧。
(3)开动空压机,用0.15Mpa压力,检查发酵罐、过滤器、管路、阀门等密封性是否良好,有无泄漏。
罐体夹套与罐是否密封(换季时应重点检测),确保所有阀门处于关闭状态。
(4)检查冷却水压、电压、气(汽)压能否正常供应。
进水压维持在0.12Mpa,允许在0.15-0.2Mpa围变动,不能超过0.2Mpa,温度应低于发酵温度10℃以上;电源AC220V±10%,零地分开,频率50Hz,罐体可靠接地;输入蒸汽压力应维持在0.4Mpa,进入系统后通过阀门控制压力为0.12-0.13MPa;空压机压力值0.7Mpa,空气进入压力应控制在0.25-0.30MP(空气初级过滤器的压力值)。
(5)检查电机能否正常运转。
电磁阀能否正常吸合。
二、灭菌1.发酵系统安装好后的初次清洗罐的清洗:种子罐可将罐体上方的法兰卸开,由操作工采用洁净布手动清洗,结束后排尽罐的污水,在多冲洗几遍即可。
发酵罐的清洗可采用自来水管通过手孔向罐体壁冲洗,当水位上升到搅拌轴的第二片叶轮时停止冲洗,开动电机搅拌清洗。
各管路的清洗,可以先采用清水冲洗,再根据相应功能采用相应的清洗介质(清洗管路时应以保护管路中的各种元件为前提),具体步骤可参考“空气管路的灭菌”。
如果发酵系统长时间不用或培养的菌体与上一批次的不相同时,可采用2%NaOH清洗,清洗结束后应对发酵系统灭菌。
2.发酵罐空消(1)空气精过滤器的空消:将所有阀门均关闭,然后微开J3、J4、J5、打开Q9,通过调节J3、J4、J5阀门的开启度保持空气精过滤器上端压力表读数为0.12-0.125Mpa,维持30分钟,空气经过滤器消毒完成。
(2)发酵罐空消:打开G2、J2、G3、J1、J9、Q6、Q7及Q9,通过调节G2和J1阀门的开启度调节发酵罐压力控制在0.12-0.125Mpa,温度121度-125度。
sy3000发酵罐操作使用说明(修订版)

SY3000发酵罐操作使用说明(2007修订版)上海世友信息技术有限公司上海世远生物设备工程有限公司上海交大工业自动化工程研究中心2007年01 月20 日SY3000 发酵罐操作使用说明(2007修订版)目录0、SY-3000发酵罐灭菌与发酵的简要操作步骤一、SY-3000发酵罐配套设备要求二、系统的安装及连接2.1基础安装及电源连接2.2蒸汽连接2.3水管的连接2.4空气连接2.5废水及废气连接2.6SY-3000发酵罐系统的操作步骤三、生物发酵过程灭菌与发酵的操作步骤3.1发酵罐相关管路与阀门3.2蒸汽灭菌操作过程1、开机2、灭菌前准备工作3、蒸汽灭菌1)发酵罐蒸汽灭菌2)空气过滤器、空气管道及空气分布器灭菌3)出料取样阀蒸汽灭菌4、灭菌结束与降温3.3发酵过程的接种1、接种2、控制罐压保持在0.05Mpa左右3、通过控制面板将转速、pH等由手动切换为自动控制四、发酵过程的测量与控制4.1温度的测量与控制1、温度的测量与变送2、发酵罐内发酵液温度的分程控制3、温度智能PID控制算法4、电加热器内装有水位报警器4.2搅拌转速的测量与控制1、转速测量元件2、搅拌电机的控制3、转速控制的算法4、溶氧转速关联控制4.3pH 的校正、测量与控制1、pH电极使用前的水化2、pH值的标定校正1)pH电极的零点校正2)pH电极的斜率校正3)pH电极内的压力3、pH 电极的维护和保养4、pH值的控制4.4溶解氧(DO)的标定、测量与控制1、溶氧测量的电极1)溶氧(DO)测量的电极2)极谱型耐高温溶氧电极的极化2、溶氧(DO)电极测量的标定3、溶氧(DO)的测量4、溶氧(DO)的控制5、溶氧关联控制的操作4.5消泡控制五、下位机控制器的操作5.1键盘及符号说明5.2下位机控制器的操作步骤5.2.1下位机的启动5.2.2下位控制器的设定与操作1、下位机自动控制前的准备2、控制周期Ts的设定3、手动自动操作方式的切换4、手动操作5、自动控制方式的操作5.3推荐的PID参数的最优值六、上位机的操作使用方法说明6.1 上位机软件的安装及IP地址设置6.2 工艺流程操作面板(Process Display Panel)的操作步骤1、打开上位机软件SY-3000E2、上位机的操作步骤●输入此次实验的批号和文件名●进入相应控制和显示操作6.3 仪表校准(Calibration)操作6.4 控制回路(Control loop Display and Set)的设定与操作6.5 变量显示(Display)的操作6.6 动态趋势(X-Y Trend Graphs)的操作6.7 报警显示(Alarms)操作6.8 关联控制(Cascade Control)操作6.9 以电机转速控制的操作过程为例进行说明6.10 界面的结构图七、发酵罐系统的维护、清洗和保养7.1 发酵罐系统的日常检查维护和定期检查维护7.2 发酵罐罐体的清洗、维护和保养7.3 搅拌系统的维护7.4 灭菌空气系统的维护和保养7.5 蒸汽系统的维护和保养7.6 溶氧电极的维护7.7 电磁阀的维护7.8 其它维护八、常见故障与排除方法九、人员培训附录:5、10L玻璃罐管路图及灭菌操作简要说明SY3000 发酵罐操作使用说明(2007修订版)0、SY-3000发酵罐灭菌与发酵的简要操作步骤SY-3000发酵罐系统包括SY-3×××系列的搅拌式发酵罐。
发酵罐使用说明图片

发酵罐的使用1.进水管道(1).锅炉进水管道:蒸汽锅炉电源打开前打开,灭菌区间一直打开,保证锅炉持续供水。
(2).冷凝水循环管道:一直打开,保证水循环,灭完菌后水进入灭菌夹层,冷却降温作用。
2.蒸汽压表:蒸汽压保持在0.4,当蒸汽压为0.4时,打开进蒸汽阀开始通蒸汽。
3.进蒸汽阀:当蒸汽压为0.4时打开,蒸汽进入夹层开始灭菌,灭菌完后关闭。
4.空气控制阀:黑色阀:灭菌完以后,温度降到40度,罐内压为0时,接菌前微开通入一定量的空气,使罐内压力在0.015—0.040 MPa之间。
两个绿色阀:灭绝时微开,1/4圈(蒸汽可以进入管内对进空气管道起灭菌作用)。
灭菌后关闭,冷却后关闭。
5.气压表灭菌后,在上面的气压表显示的气压比下面的气压大。
上面的气压表:显示从外界通入的空气气压下面的气压表:显示管内的气压外界气压比管内气压低,灭完菌以后。
6.罐内气压控制阀门:若管内气压过高,则略开可降低罐内气压(0.115—0.150MPa,不超过0.150MPa)若是在灭菌过成中调过,则在灭完菌开始冷却时关闭,防止外界气压过高水倒流进入灭菌锅通过调节红色的开关控制罐内气压7. 蒸气压表显示进入罐内蒸气压,一般达到0.2为正常,不超过0.38.消泡液加入管道消泡液(一般为植物油)在高温灭菌锅内灭菌,灭菌时容易溢出,需要在灭菌的瓶子下方个铁盒子。
在超菌工作台下安装消泡液的管道。
9.空气控制开关微开可使灭菌锅内的水汽外排,对进入空气的管道进行灭菌。
若是开得太大灭菌锅内的水会大量流出,减少培养量。
10排水阀门黑色的阀门为总阀门:排水排菌液+蓝色阀门:阀门管道要灭菌5-10 分钟,灭菌时关闭总阀门,开启蒸汽阀门,在开启此阀门。
11.管道灭菌阀灭菌快结束时,开启此阀,对排菌管道灭菌5-10分钟12.操作屏幕。
发酵罐操作流程

操作前请认真检查冷水机、空压机、反应器、进出水管、气管情况。
填好使用说明书。
开机:先打开其他单元上的开关,再打开主机背后的开关。
关机:先把控制器上所有单元的参数状态调到off,把进气开关打开后关机;关机时先关控制器后面的开关,再关其他单元上的开关。
灭菌操作1、取下马达,平放于桌上。
罐顶端套上黑色保护帽。
2、由罐上取下温度传感器,该传感器不需要灭菌。
3、取下PH电缆线,盖上红色保护帽;将PH电极要插到底。
务必拧紧电极的上下两个固定螺帽。
PH 电极灭菌前要标定。
PH电极标定:接好电缆后拧开电极的固定螺帽(第一个),将PH电极取出后用去离子水冲洗干净后,轻轻用面纸吸干上面的水后先放入标准溶液4.01中校正,等控制器上数据稳定后在set zero处输入4.01(不管实际数值的微弱差别);输入完闭后从标准液中取出电极,冲洗、吸干后放入7.00的标准溶液中,等控制器上数据稳定后在set span处输入7.00(不管实际数值的微弱差别)。
PH电极校正后不要关控制器。
4、取下DO电缆线,DO电缆接口处用锡箔纸包好后套上黑色帽。
DO电极灭菌完后标定。
DO电极要插到底,拧紧电极的上下两个固定螺帽。
灭菌前要注意溶氧电极里头的保护液是否还有,没有则要进行添加。
5、取下消泡或液位电缆线,将消泡或液位电缆插到底,灭菌后定位到所需要的高度后就不要再压下去。
消泡电极的高度离液面约1.5cm处。
6、拆下发酵罐上和冷凝器上的进、出水管,拆下的同时要用夹子夹住拆下水管的接头处,以防水流出。
7、发酵罐上的过滤器的两端多要用夹子夹死,过滤器的出口处用锡箔包好,所有过滤器的两端多要用夹子夹住。
发酵完毕倒罐后注意检查过滤器是否被打湿,若有则赶快用吸球将其中的液体吹出。
8 、用铁夹夹死收获管上的硅胶管以防在灭菌锅内跑液。
收获管不用时上面一定要卡死不移走。
9、在灭菌前.将发酵罐的六个固定螺帽拧松出气,其他螺帽一定要拧紧!灭菌完后打开高压锅后立刻将其拧紧,注意戴上手套防止被烫伤。
厌氧发酵罐操作说明

厌氧发酵罐操作说明
一、安装操作前准备
1.1安装场地
使用该发酵罐之前,首先需要设置安装场地,建议设置在室外,排空条件好,阳光充足,排水设施完善,并且离家庭等人员尽可能远,以避免安全风险。
1.2熟悉发酵罐使用说明
在安装之前,需要对发酵罐使用说明及外观特征进行熟悉,此外,应仔细检查设备是否有任何损坏或缺陷,保证发酵罐安全运行。
1.3其他准备
预留电源进线,水源,空气源。
二、安装操作步骤
2.1根据现场条件确定安装位置
根据发酵罐使用说明及外观特征,仔细检查发酵罐安装位置,确保发酵罐可以顺利安装、正常使用,并避免安全风险。
2.2安装发酵罐
首先将发酵罐放置在合适的位置,并将发酵罐的固定螺栓用螺丝刀调节至合适的位置,并用冲击扳手将其固定,确保发酵罐可以稳定的安装在现场。
2.3连接电源
将发酵罐的电源进线根据供电状况和现场环境条件,选择合适的插头,连接到电源线上,并用胶带或电缆绑扎,以保证发酵罐安全运行。
2.4连接其他介质(水源、空气源)
将发酵罐的水源管道和空气源管道按照正确的方向连接,确保水源和
空气源可以正常进入发酵罐。
sy3000发酵罐操作使用说明(修订版)

SY3000发酵罐操作使用说明(2007修订版)上海世友信息技术有限公司上海世远生物设备工程有限公司上海交大工业自动化工程研究中心2007年01 月20 日SY3000 发酵罐操作使用说明(2007修订版)目录0、SY-3000发酵罐灭菌与发酵的简要操作步骤一、SY-3000发酵罐配套设备要求二、系统的安装及连接2.1基础安装及电源连接2.2蒸汽连接2.3水管的连接2.4空气连接2.5废水及废气连接2.6SY-3000发酵罐系统的操作步骤三、生物发酵过程灭菌与发酵的操作步骤3.1发酵罐相关管路与阀门3.2蒸汽灭菌操作过程1、开机2、灭菌前准备工作3、蒸汽灭菌1)发酵罐蒸汽灭菌2)空气过滤器、空气管道及空气分布器灭菌3)出料取样阀蒸汽灭菌4、灭菌结束与降温3.3发酵过程的接种1、接种2、控制罐压保持在0.05Mpa左右3、通过控制面板将转速、pH等由手动切换为自动控制四、发酵过程的测量与控制4.1温度的测量与控制1、温度的测量与变送2、发酵罐内发酵液温度的分程控制3、温度智能PID控制算法4、电加热器内装有水位报警器4.2搅拌转速的测量与控制1、转速测量元件2、搅拌电机的控制3、转速控制的算法4、溶氧转速关联控制4.3pH 的校正、测量与控制1、pH电极使用前的水化2、pH值的标定校正1)pH电极的零点校正2)pH电极的斜率校正3)pH电极内的压力3、pH 电极的维护和保养4、pH值的控制4.4溶解氧(DO)的标定、测量与控制1、溶氧测量的电极1)溶氧(DO)测量的电极2)极谱型耐高温溶氧电极的极化2、溶氧(DO)电极测量的标定3、溶氧(DO)的测量4、溶氧(DO)的控制5、溶氧关联控制的操作4.5消泡控制五、下位机控制器的操作5.1键盘及符号说明5.2下位机控制器的操作步骤5.2.1下位机的启动5.2.2下位控制器的设定与操作1、下位机自动控制前的准备2、控制周期Ts的设定3、手动自动操作方式的切换4、手动操作5、自动控制方式的操作5.3推荐的PID参数的最优值六、上位机的操作使用方法说明6.1 上位机软件的安装及IP地址设置6.2 工艺流程操作面板(Process Display Panel)的操作步骤1、打开上位机软件SY-3000E2、上位机的操作步骤●输入此次实验的批号和文件名●进入相应控制和显示操作6.3 仪表校准(Calibration)操作6.4 控制回路(Control loop Display and Set)的设定与操作6.5 变量显示(Display)的操作6.6 动态趋势(X-Y Trend Graphs)的操作6.7 报警显示(Alarms)操作6.8 关联控制(Cascade Control)操作6.9 以电机转速控制的操作过程为例进行说明6.10 界面的结构图七、发酵罐系统的维护、清洗和保养7.1 发酵罐系统的日常检查维护和定期检查维护7.2 发酵罐罐体的清洗、维护和保养7.3 搅拌系统的维护7.4 灭菌空气系统的维护和保养7.5 蒸汽系统的维护和保养7.6 溶氧电极的维护7.7 电磁阀的维护7.8 其它维护八、常见故障与排除方法九、人员培训附录:5、10L玻璃罐管路图及灭菌操作简要说明SY3000 发酵罐操作使用说明(2007修订版)0、SY-3000发酵罐灭菌与发酵的简要操作步骤SY-3000发酵罐系统包括SY-3×××系列的搅拌式发酵罐。
乙醇后发酵罐和酒精发酵罐施工方案

河南天冠30 万吨燃料乙醇有限公司后发酵罐和酒精发酵罐施工方案编制:审核:批准:中国化学工程第十一建设公司南阳项目部2004年3月8日审批栏河南天冠30万吨燃料乙醇有限公司后发酵罐和酒精发酵罐施工方案1编制说明本方案仅适用于河南天冠30万吨燃料乙醇有限公司后发酵罐和酒精发酵罐及其附属内件的制作、安装、检验施工,不包括罐体防腐、保温的施工安排。
2编制依据2.1施工图纸2.2JB/T4735-1997《钢制焊接常压容器》2.3HG20584-1998《钢制化工容器制造技术要求》3工程概况本次现场制作安装的发酵罐共8台,其中后发酵罐2台,酒精发酵罐6台。
全容积为2800m3。
设计温度为100C,设计压力为Mpa,容器类别为常压。
罐内介质为酒精。
发酵罐的主要组成有:罐底、罐壁、罐顶、加强圈、内件。
结构形式全为拱顶罐,罐体为①14.6m*16.5m,罐顶为球冠结构形式。
罐体连接形式为对接,罐顶及罐底板连接形式为搭接。
工程量及技术参数4施方法与施工程序4.1.1这次8台发酵罐需现场建造,发酵罐的预制、安装工作集中在现场进行,内容包括壁板及型钢圈的号料、切割、卷圈、组装、焊接、无损检测、试验。
4.1.2现场安装a.壁板的施工办法采用机械配合倒装法进行。
b.固定顶的施工采用在临时胎具上组装罐顶板。
4.1.3发酵罐的焊接采用手工电弧焊,壁板背面清根采用磨光机打磨。
4.1.4储罐安装之前除地下工程须完工外,其他土建工作诸如道路、管架等工作待罐安装完毕后再进行,保证车辆道路畅通。
4.2施工程序(以后发酵罐为例)施工准备一-材料出库检验一-号料切割一-卷圈一-罐底敷设焊接一-罐底真空实验一-罐体最上层壁板组装焊立缝一-安装顶部连接固定顶加强角钢圈一-设置罐顶组装临时胎具一-安装罐顶板一-罐顶板之间搭接焊缝焊接一-罐顶接管及人孔安装一-上层壁板与包边角钢环向角缝焊接一-临时支架拆除一-吊装用临时抱杆设置一-组装焊接壁板直至最下层壁板一-最下层壁板与罐底角缝先内后外焊接一-> 内件安装一-罐壁上接管安装一-盘梯及顶部平台安装一-煤油试漏一-检查验收5 施工质量要求及保证措施本工程的质量重点是焊接及焊接变形的控制,发酵罐内壁表面平齐。
发酵罐使用说明书说明书

15L发酵罐使用说明书
1.确认使用发酵罐时,至少在灭菌开始前30min打开自来水,确保自来水能够流
进蒸汽发生器,并打开蒸汽发生器进行预加热。
2.按照发酵工艺确定培养基配方,并提前进行搅拌溶解。
3.确认发酵罐的顶盖螺栓已经拧紧,查看电机的电源线是否连接正常,打开发酵
罐开关,通过视灯观察罐内的水是否干净,如若出现浑浊或者水面存在漂浮物,应将水放掉,重新注入自来水进行清洗,并打开搅拌,转速600rpm即可,如果罐的内壁有明显的附着物,应该将发酵罐打开,进行手工清洗。
4.检查发酵罐的PH以及溶氧电极是否正确安装,将溶解好的培养基加入到发酵
罐内,加入2ml消泡剂,并将各补料口及接种口旋紧。
5.待蒸汽发生器的表压稳定后缓慢打开蒸汽管道阀门,然后缓慢打开发酵罐进蒸
汽管道阀门,打开发酵罐下面的放料阀门,将初始的比较脏的蒸汽以及冷凝水排出,在进行空气过滤器的灭菌,灭菌过程中始终注意两个空气滤芯的表压不能超过0.2mpa。
6.在实消过程中,先使用夹套加热,待培养基升温到95度后在通过放料阀使培
养基迅速升温到121度,并尽可能减少冷凝水的生成。
灭菌以及灭菌完成后的降温过程中,通往不锈钢管道的排废水阀门应始终关闭,多余的蒸汽以及温度过高的冷凝水应通过另外的阀门排到水桶内,待冷凝水的温度降下来后再通过不锈钢管道通往水池。
7.接菌完成后,应确保温度、PH、转速在自动控制键位上。
并确保氨水和补料能
流加到罐内,各蠕动泵均能够正常运转,硅胶管道没有破损,诱导过程中氨水和甲醇的量供应充足,当不够时注意添加。
8.培养结束后,将各补料系统以及附属配件清洗干净,并将发酵罐清洗干净,PH
电极放入3mol的Kcl中保存。
发酵罐安装区域的要求

发酵罐安装区域的要求
发酵罐安装区域是一个关键的环节,为了保证发酵过程的顺利进行,以下是对发酵罐安装区域的要求。
一、空间要求
发酵罐安装区域需要有足够的空间来容纳发酵罐及其相关设备。
要确保发酵罐周围有足够的空隙,以便于操作和维护。
此外,还需要合理规划通道,方便人员进出。
二、通风要求
发酵过程中会产生大量的气体,因此发酵罐安装区域需要有良好的通风设备。
通风设备能够及时排除有害气体,保持空气清新,确保工作人员的健康和安全。
三、温度控制
发酵罐安装区域需要有适当的温度控制设备,以确保发酵过程中的温度保持在合适的范围内。
温度过高或过低都会影响发酵效果,因此需要进行严密的温度监控和调节。
四、洁净度要求
发酵罐安装区域需要保持良好的洁净度。
在安装过程中,要防止灰尘和杂质进入发酵罐,以免影响发酵过程。
此外,还需要定期清洁和消毒,以防止细菌和其他有害微生物的滋生。
五、安全设施
发酵罐安装区域需要配备一些必要的安全设施,如紧急停机装置、消防设备等。
这些设施能够在紧急情况下保障工作人员的安全,并及时采取相应的措施来应对突发事件。
六、环境要求
发酵罐安装区域需要保持适宜的环境条件,如光线、湿度等。
光线要充足,以便于操作和观察。
湿度要适宜,以保证发酵过程的正常进行。
以上是对发酵罐安装区域的要求,只有满足这些要求,才能够保证发酵过程的顺利进行。
在安装过程中,要注重细节,确保每一个环节都符合要求,以提高发酵效果和产品质量。
发酵罐安装区域的要求
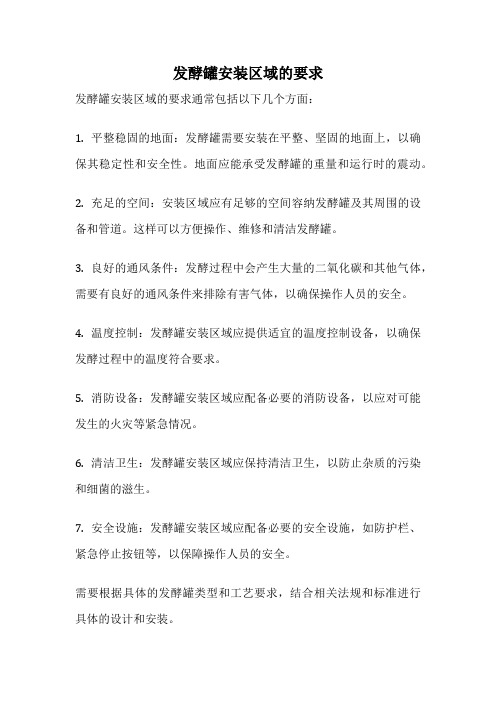
发酵罐安装区域的要求
发酵罐安装区域的要求通常包括以下几个方面:
1. 平整稳固的地面:发酵罐需要安装在平整、坚固的地面上,以确保其稳定性和安全性。
地面应能承受发酵罐的重量和运行时的震动。
2. 充足的空间:安装区域应有足够的空间容纳发酵罐及其周围的设备和管道。
这样可以方便操作、维修和清洁发酵罐。
3. 良好的通风条件:发酵过程中会产生大量的二氧化碳和其他气体,需要有良好的通风条件来排除有害气体,以确保操作人员的安全。
4. 温度控制:发酵罐安装区域应提供适宜的温度控制设备,以确保发酵过程中的温度符合要求。
5. 消防设备:发酵罐安装区域应配备必要的消防设备,以应对可能发生的火灾等紧急情况。
6. 清洁卫生:发酵罐安装区域应保持清洁卫生,以防止杂质的污染和细菌的滋生。
7. 安全设施:发酵罐安装区域应配备必要的安全设施,如防护栏、紧急停止按钮等,以保障操作人员的安全。
需要根据具体的发酵罐类型和工艺要求,结合相关法规和标准进行具体的设计和安装。
- 1、下载文档前请自行甄别文档内容的完整性,平台不提供额外的编辑、内容补充、找答案等附加服务。
- 2、"仅部分预览"的文档,不可在线预览部分如存在完整性等问题,可反馈申请退款(可完整预览的文档不适用该条件!)。
- 3、如文档侵犯您的权益,请联系客服反馈,我们会尽快为您处理(人工客服工作时间:9:00-18:30)。
一、工程简介:工程内容为4只480 M3不锈钢发酵罐制作、安装。
480 M3不锈钢发酵罐直径为Φ5700 mm,总高度达23m,总重量约为38.5吨,不但体积庞大,且单重重,运输困难。
为此,总体上考虑封头、锥体、夹套等部件成型安排在厂内制造,分件运至建设单位厂内罐区现场组焊,筒体在建设单位现场卷制。
二、施工依据及技术质量标准:1、合同;2、设计图纸;3、《压力容器安全技术监察规程》;4、GB150-98《钢制压力容器》;5、HG20584-98《钢制化工容器制造技术规定》;6、GB3274-88《碳素钢和低全金钢热轧中厚钢板和钢带》;7、JB4729-95《旋转压封头》;8、GB/T14976-94《流体输送用不锈钢无缝钢管》;9、JISG4303《不锈钢热轧钢板》;10、GB/14957-94《熔化焊用钢丝》;11、GB4242-84《焊接用不锈钢丝》;12、GB/T983-95《不锈钢焊条》;13、GB4842-84《氩气》;14、JB3223-83《焊条质量管理规程》;15、《锅炉压力容器压力管道焊工考试与管理规则》(国质检锅(2002)109号);16、JB4730-94《压力容器无损检测》;三、施工工艺技术措施和质量控制:1、投产前准备工作:1.1、组织工艺技术人员认真阅读,分析其结构特点,召开技术交底会,充分理解设计意图,做到心中有数,并做好审图记录。
1.2、编制指导生产的制造工艺和焊接工艺,重点交待清楚夹套蜂窝塞焊焊缝的焊接工艺. 1.3、采购质量可靠的SUS304钢板等主材,并选择合格的钢材供应商。
1.4、选择技术过硬的专业施工队伍,配备足够数量的技术熟练的工人,焊工必须是经考试合格的并具有相应资格的有效持证焊工。
2、制造工序流程:3、工艺过程及质量控制:3.1、编制指导生产的工艺:技术工艺人员根据设计图纸、技术标准及现场情况编制指导生产的专业制造、焊接工艺过程卡及检验工艺文件。
3.2、检验人员对钢板和焊材进行入库前的检验和标志移植,确认合格后方可投放生产使用。
3.3、划线下料:对筒节用料钢板进行四边直线度和垂直度检查,若边与边不垂直必须划垂线切割,保证边与边的相互垂直。
并严格掌握筒节坯板的下料长度准确以利环焊缝组装错边量的控制。
3.4、成型:封头坯板下料后,拼接焊缝采用埋弧自动焊。
焊缝检验合格后压制之前,对处于压制面焊缝的余高,应打磨至母材齐平,并对外圆周切割边缘的棱角打磨成过渡小圆弧,防止压制过程中撕裂。
采用先进的旋压成型工艺使封头旋压成型、平边,对拼接焊缝进行1 00%RT检查并应符合III级要求,合格后运送至现场。
锥体采用分片成型后拼接成整体的工艺方法,但与筒节结合的上部轴向过渡园弧,也要旋压成型,以保证质量,工艺上预先安排锥体分为三部分,需旋压部分高度掌握在1m左右(旋压部分的焊缝要求相同),待旋压成型后再组焊成整个锥体。
筒节采用卷板机卷制成型,因筒节直径相对较大,厚度相对较薄,刚性不足,施工中,采用刚性大的内圆辅助工装将其撑圆,保证其圆度。
3.5组对: 纵焊缝组对时控制对口错边量b≤1~1.5mm,(GB150-98标准规定b≤1/4δ,即≤2 mm),对口棱角度≤2.8mm。
两相邻的筒节纵缝应错开,其中焊缝中心线之间的外园弧长应大于筒体厚度的3倍,且不小于100mm,不允许强力组装。
筒体组对后应保证筒壁直线度≤1/10 00mm,且≤13mm。
3.6、产品工艺纪律检查试板:每台罐的第一条纵焊缝焊接时同时将试板焊完,并在得到监理人员确认后方可取下做检查试验(若符合以批代台规定按GB150-98第10.5条规定执行),试板试验合格后方可投入生产。
3.7、纵缝采用埋弧自动焊,。
环缝焊接采用手工电弧焊。
焊条牌号:焊丝为HoCr21Ni10Ti,不锈钢之间的焊接为A102,碳钢之间的焊接为J422,不锈钢与碳钢之间的焊接为A302。
具体焊接工艺参数按焊接工艺卡。
焊工必须是经培圳考核合格并具有相应项目的持证焊工,露天施工时雨天及风速大于10m/s时应采用有效的保护措施,否则,不得施焊。
3.8、RT检测:每条焊缝“T”字部位必须拍一张片,探伤比率≥20%焊缝长度。
若有不合格,则应制订返修工艺,对缺陷部位进行返修,并应在该返修部位延长扩探,扩探长度为该条焊缝的10%,若还不合格则应对该条焊缝进行100%探伤,直至合格。
3.9、将成型后的封头、筒节、锥体内焊缝进行打磨至母材齐平,并不能低于母材,为了加快进度,焊缝磨平应在探伤合格后穿插在各工序间进行。
3.10、夹套板的制作:3.10.1夹套板的制造3.10.2塞焊孔的成型:夹套板材料为3mm厚的进口的SUS304钢板。
塞焊孔采用数控冲床加工,成型后内孔径为Φ30mm,孔深度为13m并呈正三角形排列,对每个孔进行编号,以便焊接和质量检验。
然后,再利用折边机对夹套板四边进行折边。
对成型后的下凹塞焊孔及四周翻边逐个逐块的进行质量检查,主要检查冲压过程中有否撕裂、偏歪及塞焊孔冲压深度的均匀等影响焊接质量的缺陷存在。
若存在这些缺陷,则区别不同情况及时采用相应的补救措施,与内筒组装之前进行修整,保证塞焊孔与筒壁结合处间隙均匀,以保证焊接质量。
其结构如下图:3.10.3夹套板圆弧成型:夹套板的圆弧成型在卷板机上卷制。
采取多次少进给量的卷制工艺进行成形,以保证塞焊孔不变形。
卷制时不断用弧度样板检查成型弧度。
锥体夹套板成形后,应与锥体锥度相符合。
3.11、夹套与筒体、锥体的组焊:将已成型并经检验合格的蜂窝夹套与筒体、锥体点固,清除坡口两侧的渣物、油污等,并保证焊接坡口间隙均匀,确认位置正确,采用手工氩弧焊工艺进行施焊。
先焊塞焊孔,后焊四周边缘,焊接时,施焊部位应采用相对应的水平位置焊接,并保证根部焊透。
蜂窝孔与内筒翻边角焊缝工艺按图纸要求焊接,其工艺参数详见焊接工艺卡。
3.12、夹套板焊缝气压试验及气氨检漏:3.12.1 蜂窝式洒精水冷却夹套试验,夹套内先以0.3MPa压缩空气作试验,在焊缝和窝点用泡剂进行泄漏检查,然后以0.6MPa进行气压试验合格。
3.12.2 氨冷却式夹套试验:该项工序分三步进行:第一,气密性试验,打空气0.3MPa,对塞焊孔组合焊缝、板边角焊缝涂刷肥皂水初步查漏。
查漏方法:以每块夹套板为检查单位,逐排孔进行检查,一经发现问题即用记号笔做上记号,留待泄压后进行补焊;第二步:试漏检查合格后缓慢升压至1.6 MPa保压30分钟,不降压为合格。
第三步,气氨检查,通入1.2MPa气氨,用试纸进行检查,检查方法同第一步,即以每块夹套板为单位,逐排仔细检查,以试纸不变色为合格,注意检查时试纸在每个孔的位置至少停留15秒钟。
此时若发现有漏气现象,必须先做上记号,待整块板的所有孔及板边焊缝全部检查完毕后,放掉氨气用空气彻底置换后方可按返修工艺进行补焊,补焊后再一次通氨检查直至合格。
3.13、夹套管道的组焊:按设计图纸尺寸要求,预先弯制管件,然后与夹套接管组焊。
焊接时采用合理的施焊方法和顺序,并保证单面焊双面成型,根部焊透。
为避免吊装时损坏夹套管件,该部件在设备就位时进行,并必须采取必要的保护措施。
4、设备的内外壁表面处理:4.1、罐体内壁抛光工艺:罐体内表面的抛光处理是制作啤酒发酵罐的关键技术项。
为了消除罐体内表面的粗糙状态,获得较高要求的表面粗糙度(0.6µm)质量,故采用抛光的方法。
由于表面积大,抛光工作量大,表面粗糙度要求高,因此我们选用重庆大学海达砂带磨床公司生产的2MG58400C型罐体抛光机进行抛光,以确保罐体表面要求。
保证罐内粗糙度达到设计要求,并小于0.6µm的表面质量。
4.2、罐体外壁酸洗、钝化及兰点检查法:奥氏体不锈钢制造的容器酸洗、钝化工艺,目的是为了经过酸洗和钝化后的不锈钢表面生成一层无色致密的钝化膜起耐腐蚀作用。
4.2.1 酸洗液配方:硝酸(比重1.42) 20%氢氟酸5%水75%配制时,将硝酸、氢氟酸缓慢加入水中搅匀。
4.2.2 酸洗操作方法和工序:对碳钢工件表面进行保护,刷涂耐酸漆或石腊熔化后热涂于碳钢表面。
4.2.3 将不锈钢工件表面的焊疤、划伤等打磨光滑,并用碱液(肥皂水等)洗去表面油污脏物后清水冲洗干净。
4.2.4 将配制好的酸液用拖把或细沙布、毛巾在工件表面来回反复拖抹,保持工件表面湿润,要求维持湿润的同时用不锈钢钢丝刷在工件表面反复多次拖抹,直至全部表面呈银白色。
特别是焊缝及热影响区处,应反复用不锈钢钢丝刷刷洗。
4.2.5 清水冲洗→肥皂水刷洗→清水冲洗→压缩空气吹干或自然通风晾干。
4.3、钝化液配方:硝酸(比重1.42)5%重铬酸钾2%水93%特别警告:配制时应将硝酸、重铬酸钾缓慢加入水中,并应边加酸边搅拌均匀,切记动作缓慢!禁止:禁止将水加入硝酸中,以免发生危险!4.4、钝化操作方法:将配制好的钝化液用拖把或细纱布、毛巾等在工件表面来回反复拖抹,保持工件表面湿润2~3小时,注意应一直坚持不断地保持表面湿润。
4.5、钝化膜质量检查——“兰点”试验:4.5.1 试验配方:铁氰化钾10克硝酸30克蒸馏水960克4.5.2 检查方法将试液涂于已钝化处理并已清洗干净的工件表面上,30秒后表面无兰点为合格,注意:工件表面每平方米不少于5点,可疑之处应重点检查。
4.6、操作注意事项:4.6.1 配制溶液时应将酸液缓慢倒入水中,并不断地搅拌。
绝对不可将水倒入酸液中。
4.6.2 操作前必须穿戴好劳保用品,操作场所要有良好通风条件。
4.6.3 铁氰化钾,重铬酸钾应由专人保管,按毒品管理办法领用回收。
5、设备的运输、吊装、就位:该分项工程,我公司委托与我单位长期协作的**安装公司,该公司技术过硬,经验丰富.5.1、拖运吊装在制作场地上,把罐体两端垫在额定为40T两铁拖排上,用枕木、钢线索固定罐体在铁拖排上,下摆置铁滚筒及拖板,用5T卷扬机牵引,拖运罐体前进,直至吊装许可位置。
5.2、吊装就位据该厂发酵罐基座,钢管制作数只排列。
采用800×800独立铁拨杆,高度为45米,一次性吊装到位。
该铁拨杆安全负载为45T,垂吊滑组为40T,左右缆风为16T,后缆风为20T同时受用,4台3T-5T卷扬机控制使用,吊装顺序从里向外。
起吊时,先由拨杆、主吊滑车吊起罐体离地50厘米停机,检查受力各点情况。
一切达到预计的要求,即撤掉前铁拖排,扫清任何障碍物及杂物。
然后起吊罐体上半部,徐徐上升,使罐体安装中心垂直轴线,从水平逐步转向垂直,罐后端铁拖排慢慢滚进,直至罐体直立、吊空。
慢慢送至钢管架上,调整水平,就位焊接好,松解吊索,解除。
移吊杆接吊下一只罐,直到吊装完毕。
5.3、设备整体校正:发酵罐就位后,在外壁相隔90°吊垂线二条,检查发酵罐的垂直偏差应≤13mm, 并用经纬仪进行校验,校正过程中,可利用垫斜契铁块进行调正,调正后,对垫铁块进行焊接固定,并紧固地脚螺栓。