不良品在线控制方法
不良品控制程序

不良品控制程序如果“受控文件”章不是红色的,那么此文件未经文控中心受控管制,为无效文件。
对不合格品进行特殊的标识、记录、评价、隔离、处理。
有效的防止不合格品的非预期交付或使用。
适用于于从原材料订货、生产过程中不合格品的制止、处理和掌控。
mrb——是指由生产部、品质部、pmc部主管级以上人员组成的不合格品评审委员会。
4.14.2mrb成员负责不合格品评审,作处理决定。
品质部负责管理产品不当记录的统计分析,并构成报表。
5.1来料检验不合格品控制流程图5.2在制品检验不当Fanjeaux掌控流程图5.3出货检验不良品控制流程图6.1不合格品必须按《产品标识与上溯系统控制程序》的建议不予标识。
6.2判定为拒收的来料不合格批、生产过程中发现的不合格在制品、成品,由iqc、pqc或oqa就各自负责的范围贴挂“不合格”标识,放置在不合格品区,适当的加以标识隔离。
6.3不合格品记录6.3.1来料不合格由iqc记录在【来料检验报告】中,如果整批不合格的必须特别不予标明。
6.3.2制程检验中验出的不能合格在制品,由pqc在【制程不当记录】中记录,叙述不当状况,并维持6.3.3入库或出货检验中抽检的不合格半成品或成品,由oqa在【oqa检验报告】中分类记录,描述不当状况;当整批认定退还时特别标明,有关Fanjeaux管员留存记录。
6.4不合格品评审判定6.4.1来料不合格评审6.4.1.1来料不合格时由iqc将【来料检验报告】交pmc部,全检不合格由pmc部根据订货情况和生产计划作出退款同意。
抽查不合格由pmc明确提出并交mrb委员会展开综合评审。
6.4.1.2mrb成员要按以下原则进行评审:(1)生产部从生产加工和技术的角度,认定不合格的情况对生产加工和产品性能的(2)品质部从客户的观点推论对外观、性能和采用的影响。
(3)物料部从交货计划及供应商的情况推论对订货和交货期的影响。
6.4.1.3mrb成员必须参照以下原则做出决定(1)零散的不能合格来料或生产市场需求对答而来料瑕疵存有关键性影响的来料不合格批,入(2)生产急需、缺陷不可以存在的不合格批,进行全检处理。
生产过程不良品控制与改善管理制度

生产过程不良品控制与改善程序1、目的:规范提高产品合格率,提高工艺可靠性,全面降低生产运营成本。
2、适用范围:本作业程序适用于生产线不良品有关的物流过程和相关部门。
3、引用文件:3.1 JS-COP-804 不合格品控制程序3.2 JS-WI-PM-22 不良品处理作业规范4、定义:来料不良品:在物料进料检验过程中发现不符合零件承认书之要求;在制程中发现不良但属于来料本身劣质和不合格品。
制程不良品:在制造过程中若因加工、组装、测试和包装等作业造成物料的划伤、脱漆、断脚、变形、破裂、坏死等或因产品元器件异常导致不良发生。
5、职责:5.1 生产部: 负责在线不良品(来料和制程)反馈、报废申请及退库作业。
5.2品管部: 负责对不良品的性质判定及甑别材料所属供应商等评审,提供不良品检验报告。
5.3 采购部:负责对不良品处理意见的评审和最终处理决议的执行。
5.4 资材部: 负责不良品帐物管理,并监督、跟进落实相关部门对不良品的处理结果。
6、内容:6.1 生产退料作业6.1.1 产线在生产过程中发现有不良物料时,材料员按来料不良、作业不良区分合理包装存放,再办理退库作业。
6.1.2 物料员按不良属性开出“来料不良退仓单”(属来料不良),或“不良品退库单”(属作业不良、返修拆卸品),并附有品质小票,单据和小票内容必须填写有料号、品名、数量、不良原因、供应商名称,然后交部门主管审核。
6.1.3 物料员将审核好的单据、物料、小票送随线IQC 裁定,IQC 对不良材料裁定其不良属性、供应商是否准确,包装是否合理,有问题的当场纠正,如果是作业不良的应注明处理意见,物料员根据品管裁定的不良属性分别送不良品仓退库。
6.1.4 不良品仓库收到物料员退来的不良品时,一定要核实单据、小票、实物是否一致,三者缺一不可,确认品管部所签署的意见并提供不良品检验报告,依据品管裁定的不良属性区分点收,退货单签字后留白联(仓库联)存底做帐,对描述不清楚、包装不合要求的拒收。
不良品返修控制流程

4.2维修人员必须将当天维修之产品做好《维修记录表》,维修好的产品标识好是维修品,并清点数量,写好相关资料(订单号,电压,数量)转交给老化员。
4.3老化员接受到维修品,必须单独做好记录;老化时间为4个小时。老化好维修品后交由线上检验员,进行外观及性能检测。确认正常后方可随大货包装。
NO.
版本
变更日期
变更内容
页数
制定
审核
1
01
初次发行
品质部
裴春灿
1.目的:
为确保生产品质良好,针对返修品维修部门可以得到全面控制,特制作此工作流程。
2.适用范围:
本程序适用于本公司半成品,成品及外协加的返工、标识、老化、维修报表的记录。
3.2品质部:负责稽核返修过程中出现的异常,及返修品是否依据此程序操作。
4.运作程序:
如何利用精益生产控制不良品出现

如何利用精益生产控制不良品出现简介精益生产(Lean Production),也被称为精益生产系统(Lean Production System),是一种高效的生产管理方法,旨在通过消除浪费和提高价值流程来提高生产效率和产品质量。
本文将介绍如何利用精益生产原则,有效控制不良品的出现。
1. 了解不良品的根本原因要控制不良品的出现,首先需要了解不良品产生的根本原因。
可能的原因包括:•设计缺陷:产品设计不合理或存在缺陷可能导致产品质量问题。
•工艺问题:不完善的生产工艺可能导致不良品的出现。
•操作失误:操作人员的错误操作或管理不当可能导致产品质量问题。
•原材料质量问题:原材料的质量问题可能直接导致产品质量问题。
•设备故障:设备故障或不稳定可能导致产品质量问题。
了解不良品的根本原因是采取有效措施控制不良品的关键。
因此,应该通过详细的调查和分析找到不良品的根本原因。
2. 采用预防性控制措施控制不良品最有效的方法是采取预防性措施。
以下是一些常见的预防性控制措施:2.1 进行全面的产品设计验证在产品设计阶段,应进行全面的产品设计验证工作。
这包括进行样品测试、模拟实验以及详细的设计评审等。
通过验证产品设计的准确性和可行性,可以避免产品质量问题。
2.2 建立完善的生产工艺建立完善的生产工艺,确保每个生产环节都能够按照标准操作。
这包括编制详细的工艺流程和相关的操作规范,对操作人员进行培训和技能提升,以及建立质量控制点进行检查。
2.3 严格的质量管理体系建立严格的质量管理体系,包括质量目标的设定、质量检查和控制的流程、不良品处理的规范等。
通过制定明确的质量标准和控制措施,可以有效避免不良品的出现。
3. 引入精益生产原则精益生产原则是有效控制不良品的重要方法。
以下是一些常见的精益生产原则:3.1 价值流分析通过对整个生产过程进行价值流分析,可以识别出不必要的环节和浪费,从而改进和优化生产过程。
通过优化价值流,可以减少可能导致不良品的因素。
不良品控制方法

不良品控制方法咱平常买东西的时候,都希望到手的是好东西,没谁乐意碰到个残次品。
那在生产过程中,不良品可就像是个调皮捣蛋的小鬼,得好好管管它们!生产线上的事儿,就跟咱过日子一样,得仔细着点儿。
要控制不良品,首先得有双火眼金睛,能在第一时间发现它们。
这就好比咱挑水果,得把那些有疤的、烂了一块儿的给挑出来。
工人师傅们就得时刻保持警惕,不能让不良品蒙混过关。
那怎么能更好地发现不良品呢?这就得靠严格的检验啦!就像老师批改作业一样,得一个一个认真看。
每一道工序结束后,都得来个全面“体检”,不能放过任何一个小毛病。
发现了不良品可不能就这么放着不管呀,得赶紧找原因。
是材料不行?还是工艺出了问题?这就像是医生看病,得找到病根儿才能对症下药。
要是材料的问题,那就得跟供应商好好谈谈,让他们把好材料送来。
要是工艺的问题,那技术人员就得赶紧想办法改进,可不能让同样的问题一再出现。
还有啊,员工的培训也特别重要。
就像学武功,招式得练得熟练了,才能发挥出威力。
员工们得清楚知道怎么做才能减少不良品的产生,要把那些标准和要求都刻在脑子里。
而且大家得互相提醒,互相帮忙,不能一个人马虎了,让不良品钻了空子。
再说说设备吧,这可是生产的好帮手。
但要是设备出了问题,那生产出来的东西能好吗?所以得定期给设备做保养,就像咱给汽车做保养一样。
让设备一直保持良好的状态,才能生产出高质量的产品。
另外啊,生产环境也不能小瞧。
要是车间里脏兮兮、乱糟糟的,那能生产出好东西才怪呢!所以得把车间打扫得干干净净,东西摆放得整整齐齐,这样大家工作起来也舒心,生产效率也能提高不少呢。
咱们控制不良品,不就是为了让客户满意嘛!要是客户收到一堆不良品,那得多生气呀,以后谁还跟咱合作呀!所以咱得把不良品这个小恶魔给死死地管住,让好产品像泉水一样源源不断地流出来。
大家想想,要是咱们生产的东西质量都杠杠的,那咱的口碑不就越来越好啦?客户越来越多,生意越来越红火,那多带劲呀!所以说呀,不良品控制可不是小事儿,咱们都得上点儿心,可别不当回事儿!咱得一起努力,把不良品的数量降到最低,让咱们的产品在市场上所向披靡!这难道不好吗?这肯定好呀!咱们就得这么干!。
不良品控制程序 -回复

不良品控制程序-回复什么是不良品控制程序?如何建立一个有效的不良品控制程序?本文将以这两个问题为主题,详细解答如下。
什么是不良品控制程序?不良品控制程序是在制造过程中用于识别、处理和防止不良品的一套流程和规定。
不良品指的是产品或服务在满足规定要求的方面存在缺陷、不符合要求或无法达到质量标准的情况。
而不良品控制程序的目的在于有效控制不良品的产生,降低不良品率,提高产品或服务的质量。
如何建立一个有效的不良品控制程序?1. 制定明确的质量标准:首先,建立一个明确的质量标准是非常重要的。
质量标准应该包括产品或服务应满足的各项要求,包括技术要求、外观要求、性能要求等等。
这样可以为不良品控制提供一个明确的依据。
2. 设计合理的检验流程:制定一个合理的检验流程是有效控制不良品的关键。
根据产品或服务的特点,确定需要进行的各个检验项目,确定各个环节的责任人和检验标准。
同时,要定期对检验流程进行评估和改进,以确保其持续有效。
3. 建立严格的质量记录体系:建立一套完善的质量记录体系是不良品控制的基础。
每一批产品或服务都应该有相应的记录,包括原材料检验记录、生产过程检验记录、产品抽样检验记录等等。
这样可以及时发现问题和追踪不良品的原因。
4. 培训员工:培训员工是不良品控制的重要环节。
所有参与生产和服务的员工应该接受相应的培训,了解质量标准、检验流程和质量记录要求,增强他们的质量意识和责任心。
5. 建立纠正措施和预防措施:当发现不良品时,要及时采取纠正措施,包括报废、返工、追溯等。
同时,要进行问题分析,找出不良品产生的原因,并采取相应的预防措施,防止类似问题再次发生。
6. 定期进行审核和改进:定期对不良品控制程序进行审核和改进是必不可少的。
通过对过程的评估,发现不足之处,并根据实际情况进行改进,以不断提高控制程序的有效性和适应性。
7. 引入先进的技术手段:随着科技的发展,一些先进的技术手段可以帮助我们更好地控制不良品。
例如,自动化设备、数据分析软件和追溯系统等,都可以提高不良品控制的效率和准确性。
不良品如何管理

生产线的“红盒子”如何使用
为确保生产现场不合格产品能够得到有效的控制,防止非预期的使用或流入客户端,WABCO使
用“红盒子”工具对不良品进行管控,使其能够得到及时有效的标识、隔离、放置、处理。
操作员工发现不合格产品时,需要遵循以下步骤操作:
1、标识:立刻停止生产,将对应的缺陷模式输入EQMS,打印出红标签,并将红标签挂在零件上,不能只将标签放在零件上。
及时地用红标签标识不合格品,防止其混入合格品中,导致客
户投诉。
2、隔离:将不良件放入红盒子中,不能放置到工作站的其他位置,并将不良信息记录到动态柏拉图(Live Pareto)中。
通过此种方式,将不良品有效地隔离。
3、放置不良品传送道有单向门,禁止从不良品滑道的入口处取不良品进行测试、测量等活动。
防止不良品被误取出流入客户端,导致顾客投诉。
4、处理:不良品传送道出口上锁,且处于常闭状态,钥匙由专人统一管理,并定时收取不良件。
只有被授权的拆解分析站人员有权限开锁取出不良品并进行拆解分析。
不合格品管理需要全员参与,严格按照要求执行,避免不合格品的异常处置,保证产品质量,达到顾客满意!。
不良品防止对策

不良品防止对策第三章:提高产品质量控制在制造业中,提高产品质量是防止不良品发生的关键措施之一、通过加强对质量控制的管理和监督,可以有效地降低不良品率,提高产品质量,提升企业的竞争力。
1.设立质量控制部门企业应设立专门的质量控制部门,负责对产品质量进行全面的检测和控制。
该部门应由经验丰富、技术水平高的质量控制人员组成,负责产品的质量规划、质量监控和质量改进工作。
2.建立完善的质量管理体系企业应建立完善的质量管理体系,包括质量目标、质量策划、质量实施、质量评价和质量改进等环节。
通过严格执行质量管理体系,可以有效地控制产品质量,降低不良品率。
3.培训质量控制人员企业应定期组织质量控制人员的培训,提高其质量控制技术和管理水平。
培训内容包括质量检验方法、质量控制工具的应用和质量管理知识等。
通过培训,可以提高质量控制人员的能力和素质,提升产品质量。
4.引入先进的质量检测设备企业应增加投入,引进适用于产品质量检测的先进设备。
这些设备可以提高质量检测的准确性和效率,帮助及早发现产品质量问题,防止不良品的产生。
5.开展供应商管理企业应建立与供应商的合作关系,共同开展供应商管理。
通过对供应商进行质量审核和质量监控,可以确保供应的原材料和零部件符合质量要求,降低因原材料和零部件质量问题引起的不良品。
6.加强工艺控制企业应加强对生产工艺的控制,确保每个生产环节都符合工艺要求。
通过制定和执行严格的工艺标准和工艺流程,可以降低产品的变动性,减少不良品的发生。
7.建立不良品追溯体系企业应建立完善的不良品追溯体系,对不良品进行追溯,找出不良品的原因和责任主体。
通过追溯,可以及时采取措施解决不良品问题,避免不良品的再次发生。
8.定期进行质量检查企业应定期进行质量检查,对生产过程和产品质量进行检测。
通过检查结果,及时发现质量问题,采取纠正措施,确保产品质量符合要求,避免不良品的产生。
9.提高员工的质量意识企业应加强对员工的质量意识教育,强调产品质量的重要性和每个员工的责任。
不良品控制程序
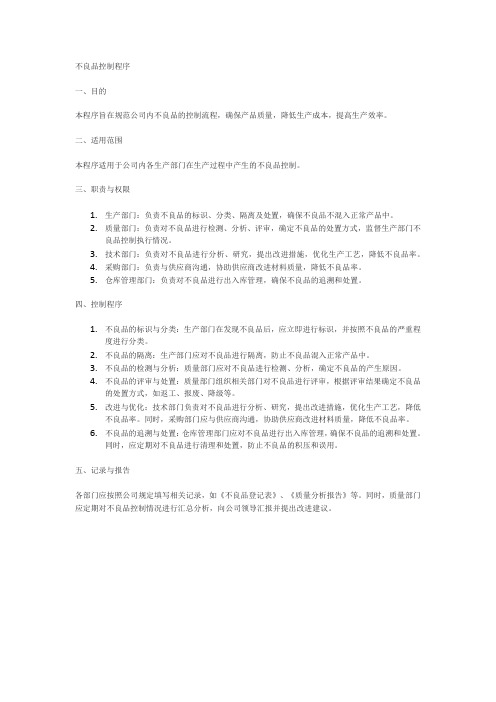
不良品控制程序一、目的本程序旨在规范公司内不良品的控制流程,确保产品质量,降低生产成本,提高生产效率。
二、适用范围本程序适用于公司内各生产部门在生产过程中产生的不良品控制。
三、职责与权限1.生产部门:负责不良品的标识、分类、隔离及处置,确保不良品不混入正常产品中。
2.质量部门:负责对不良品进行检测、分析、评审,确定不良品的处置方式,监督生产部门不良品控制执行情况。
3.技术部门:负责对不良品进行分析、研究,提出改进措施,优化生产工艺,降低不良品率。
4.采购部门:负责与供应商沟通,协助供应商改进材料质量,降低不良品率。
5.仓库管理部门:负责对不良品进行出入库管理,确保不良品的追溯和处置。
四、控制程序1.不良品的标识与分类:生产部门在发现不良品后,应立即进行标识,并按照不良品的严重程度进行分类。
2.不良品的隔离:生产部门应对不良品进行隔离,防止不良品混入正常产品中。
3.不良品的检测与分析:质量部门应对不良品进行检测、分析,确定不良品的产生原因。
4.不良品的评审与处置:质量部门组织相关部门对不良品进行评审,根据评审结果确定不良品的处置方式,如返工、报废、降级等。
5.改进与优化:技术部门负责对不良品进行分析、研究,提出改进措施,优化生产工艺,降低不良品率。
同时,采购部门应与供应商沟通,协助供应商改进材料质量,降低不良品率。
6.不良品的追溯与处置:仓库管理部门应对不良品进行出入库管理,确保不良品的追溯和处置。
同时,应定期对不良品进行清理和处置,防止不良品的积压和误用。
五、记录与报告各部门应按照公司规定填写相关记录,如《不良品登记表》、《质量分析报告》等。
同时,质量部门应定期对不良品控制情况进行汇总分析,向公司领导汇报并提出改进建议。
生产过程不良品控制与改善管理规定

生产过程不良品控制与改善管理规定一、概述不良品是指在生产过程中出现的不符合质量标准要求的产品或材料。
不良品的存在会直接影响产品质量和企业的信誉,因此对于不良品的控制和改善非常重要。
本文将就生产过程中的不良品控制与改善管理进行规定。
二、不良品控制1.产品分类根据产品的不良品情况,将产品分为一类品、二类品和三类品。
一类品是指完全符合质量标准的产品,二类品是指部分符合质量标准的产品,三类品是指完全不符合质量标准的产品。
2.不良品监控对于生产过程中出现的不良品,需要建立相应的监控系统。
通过监控系统,可以及时发现不良品问题,并采取相应的措施进行处理。
3.不良品处理对于出现的不良品,需要采取相应的处理措施。
一类品可以直接销售,二类品需要进行返工,三类品需要报废处理。
4.不良品责任追溯对于不良品的责任,需要进行追溯和调查。
找出造成不良品的原因,并采取措施进行改善。
三、不良品改善管理1.品质培训建立品质培训制度,对员工进行相关知识和技能的培训,提高员工的品质意识和技术水平。
2.不良品分析对于生产过程中出现的不良品,进行分析。
找出不良品的原因,并采取相应措施进行改善。
3.改善措施根据不良品的分析结果,制定相应的改善措施方案。
包括改进生产工艺、调整设备参数等。
4.问题解决针对生产过程中出现的问题,及时进行解决。
建立问题反馈机制,了解员工的问题和意见,并及时处理。
5.持续改善不断对生产过程中的不良品进行监控和改善。
建立持续改善机制,不断提高产品质量水平。
四、总结生产过程中的不良品控制与改善管理是确保产品质量的重要环节。
通过建立相应的监控系统、采取不良品处理措施、追溯责任、进行品质培训、分析与改善不良品,可以有效提高产品质量水平,保证企业的竞争力和可持续发展。
不合格控制程序

不合格控制程序背景在生产过程中,由于各种原因,可能会出现不合格产品。
而这些不合格品如果流入市场,将对消费者的利益和企业的品牌形象造成严重损害。
因此,为了在生产过程中确保产品的质量,企业需要建立一套完善的不合格控制程序。
意义建立不合格控制程序的意义在于,通过监管控制每一个环节,确保生产过程中不合格品的数量最小化。
同时,当发现不合格品的存在时,能够及时采取合理的措施,将不合格产品的数量控制在最小限度内。
步骤不合格控制程序主要包括以下步骤:步骤一:发现不合格品在生产过程中,通过各种手段监控产品的质量,如制定合理的检测方法、检验标准等,确保产品的质量符合要求。
一旦发现任何不合格品,应立即通知相关部门或负责人,以便采取下一步措施。
步骤二:隔离不合格品一旦发现不合格产品,应该对其隔离,以避免其对其他产品造成影响。
可以将不合格品放置在标有“不合格品”标志的专门区域,并通过相应的手段进行密封、锁定或封存。
步骤三:处理不合格品处理不合格品是确保产品质量的重要环节。
处理的方式因产品类型而异,但包括重新制造、修复、销毁或退货等。
应该对不合格品的处理过程进行记录,并确保记录的准确性和完整性。
步骤四:纠正措施当不合格品得到处理后,应对生产过程进行检查和分析,以寻找可能的原因并纠正问题。
应对发现的问题进行跟踪,以确保问题得到持续解决,防止再次发生。
步骤五:持续监测建立不合格控制程序后,应定期进行监测和评估,不断提高程序的有效性和适应性,防止不合格品再次发生。
总结建立不合格控制程序对于企业来说至关重要,不仅可以保证产品的质量,还能保护企业的声誉和市场地位。
只有通过完善的程序和有效的措施,才能确保不合格品的数量最小化,让消费者放心购买企业的产品。
不合格品的控制方法

不合格品的控制方法返工;返修;让步接收;退货;报废;采取纠正预防措施。
1、不合格品控制的目的:防止不合格品的非预期使用或交付。
2、不合格品控制的方法是先识别后控制。
不合格品的控制流程1、识别识别不合格:判断产品合格与否的依据或标准。
—产品标准—客户要求—工艺文件—检验文件—样板—上级的交代与叮嘱2、标识检验状态的标识—标识“待处理”或“不合格”的标识。
—生产班组:不合格的半成品与原材料要标明“待处理”或“不合格”的标识。
—检验员在随机卡、流程卡或“返工单”的相应项目标栏内盖检验章,作为“不合格”标识。
—其作用是:具有可追溯性。
—最终检验:不合格牌标识。
或写明(注明)不合格现象,如(漏包、拉裂、少孔、搞错型号、严重压痕、少工序、用错材料等)。
3、隔离要求:与正常的合格品明确隔离。
—红色胶盘/物料框。
—专门独立的不良品架。
—划分不合格区域,不良品放在不合格品区域内。
—生产区的摆放与其它产品不同,以示区别,然后按要求拉到维修或返工返修区处理。
—定时安排人员到不良品区进行确认与数量的登记4、记录—在规定的检验报告上正确记录不合格产品的型号、批次、检验日期、检验依据、不合格品的数量、检验结果。
—检验报告按规定予审核与批准。
—流程:5、评审当量较大时,或对公司信誉与资金影响大时须评审。
(1)进货检验:经检验主管以上人员签署处置意见(必要时要组织技术部、生产、供应链、相关部门进行评审)。
(2)过程检验:对批量不合格品,质量管理部组织相关部门和相关人员进行评审。
(3)最终检验:质控部负责人审批处置结论,必要时,技术部参与评审。
6、处置包括以下几种:挑选使用、返修、让步接收、报废处理、纠正预防措施。
(1)进货不合格品的处置—退货—让步接收—要求供方采取相关的纠正预防措施—我厂对连续多批不合格,某批大量严重不合格的供方,将安排人员对其审厂并对以后批次加严检验。
(2)过程不合格品的处置过程不合格品的处置方式一般有:返工返修、让步接收与报废等几种。
如何控制不良品流入下道工序

如何控制不良品流入下道工序为满足下一道加工工序及客户对产品的品质需求,从进料到出货每一道工序都必须严格把关尽可能地减少不良品流入下道工序;为控制不良品不流入下道工序,必须要求检验员对产品的检验资料及标准统一明确、检验方法科学合理并正确,要求检验员从一开始就做好做对。
一,来料控制:1.了解来料是用在何种产品的物料及其相应的检验标准。
2.查阅制造通知单,物料申购单,图纸及其它检验资料,确定来料规格型号是否与申购单、检验资料及图纸相符(外观,尺寸,表面处理,规格,.材质,),并了解其装配关系从而更准确地判定来料的合格与否。
3.对检验资料不齐全无法判定的物料必须及时找工程确认并在4小时内给予判定,绝不允许将无法判定的物料入库。
4.不断收集生产过程中所出现的进料异常问题点,并将相关的信息整理记录,作为下批同类物料来料检验的重要检测项目。
5.对于让步接收的产品及时将信息知会各相关工序,让下工序了解异常问题点及时做好特采措施的监控。
6.对所检的良品与不良品做好标识并隔离。
二.产品制程控制:1、对于来料在加工前进行复检,发现异常及时上报或知会I QC经确认后方可加工。
2、检验员对于产品加工的每一个零部件都必须明确其客户检验标准及整机的装配关系。
3、按检验流程完成检验工作;首检、巡检及转序检验并作好相关记录,必须杜绝产品未经检验与良品一起转入下工序.4、对不良品的处理要及时,准确地标识隔离,防止不良品与良品混在一起转序,5、每个检验员平时工作中要对产品品质异常问题点进行收集并记录及上级传达的有关影响产品品质的重要信息要及时知悉并领悟(下工序出现的异常问题点、客诉、设变等)作为后续控制的一个重点项目及对检验标准的更新和完善;6、对于在钣金制程生产出的外观不良影响表面处理需喷涂或外协做特殊处理的产品必须做好标识及隔离并知会下道工序的生产及检验人员,让下道工序了解异常问题点并作重点监控。
精益管理之不良品控制

精益管理之不良品控制提起精益生产治理,人们或许有些生疏,何为精益生产治理?精益生产治理就是对品质追求零PPM(百万分之一)的缺陷率,追求客户100的满足。
以往谈到精益生产治理时往往偏重于介绍精益生产中对生产平准化、物流、看板、标准作业等方面的内容,但是实施精益生产的一个基本前提是不能以牺牲安全和品质为代价去提升绩效。
因此要在整个企业中,非凡是告戒现场生产人员,假如出现百万分之一的不良,意味着送到客户手中就会带来100的不良。
精益生产治理所追求的是在必要的时间生产必要数量的必要产品,假如出现任何不良品,势必造成生产计划和生产治理的混乱。
因此没有品质零缺陷的保证,精益生产中所提出的三个“必要”将无法实现。
实现品质零缺陷,必须坚持“三不”原则,即“不接受不良品、不制造不良品、不流出不良品”。
这是对待不良品的基本原则,也是首先必须保证的原则,是具体保证品质零不良的基础。
不制造不良品——这是每个现场生产人员首先必须保证的,只有不生产不良品才能使得不流出和不接受不良品变为可能。
不流出不良品——作为操作者一旦发现不良品,必须及时停机,将不良品在本工序截下,并且在本工序内完成处置和防止再发生的对策。
不接受不良品——后工序人员一旦发现不良,将立即在本工序实施停机,并就此通知上道工序。
上工序人员需立即停止生产,追查原因,采取对策,控制流出的不良。
精益生产对现场品质控制的方法强调不一定用多么高深的技术和大量高精尖检验设备的投入。
精益生产认为不良的产生往往是治理上的问题,可以通过改变治理方法实现,因此在精益生产治理模式下的现场品质控制方法是简单而实用的,例如:一、让不良品表面化精益生产治理认为任何不良的出现,必定有其内在的原因,只有解决了发生不良的每个原因,才能真正地实现零缺陷,才能让客户真正体会到满足。
假如按照传统的思维和做法由作业者对不合格品自行返工或报废,那么下次还会发生同样的问题。
因此要设置专用的不合格品展示台,不间断地展示不合格品,针对不合格品产生的原因和应采取的对策由现场人员对操作工工逐个分析,提高每个员工的辨别识别能力,转变其对不良的态度。
不良品控制流程

评审结果为同意特 采时办理特采手续
提交纠正预 防措施报告
IPQC对实物进行相应标 识并跟踪后续处理过程, 品质部批准《特采单》
对返工、返修及挑
IPQC向对应生产单 位发出纠正措施单
记录、归档、跟
仓库接收 办理入库
编制:
审核:
记录、归档、跟 踪纠正防错及效
批准:
制造部
根据不合 格项是否 走特采评
XXX汽车传动轴有限公司
不良品控制流程
品质部
IPQC提出产 品不良信息
标识、记录并通知 对生产负责人处理
ห้องสมุดไป่ตู้
提出特采申请
文件编号: 资材部
对不合格 品隔离, 并单独放
返工、返修、挑选
QE负责主导对一般 性不合格品项进行 评审(技术、生产) 对于多次重复性产 生不良邀请后制程 负责人进行评审并 在特采单上签字和
在线不良管制流程

.
目
的
及时、迅速处理,解决生产过程中阻碍生产顺利进行的各种问题,保证生产的正常运行。 2. 适用范围
生产线不良或异常包括物料、工艺、设备、产品功能、作业及其它方面使生产不能顺利 进行的各种因素。 3. 生产线不良或异常处理流程/职责和工作要求
流程
开始 巡线
发现生产
不良品或异常
正制不式现订良开象解或出确决《异认方校常案正
行为报告》
职责
生产、工 程、品检
生产、工 程、品检、SMT 生产、工 程、 品检、 SMT 工程、生 产、开发、品 检
工作要求
监督生产线作业员按工艺文件作业情况; 用样机校正各测试位,并填写样机校位记录表; 检查各仪器设备运行情况; 每小时填写《工序质量日报表》。
组长、领班、物料员、IPQC、工程人员、SMT 管理 人员要有问题意识,及时迅速发现异常或不良,能 预见不良或异常产生的影响和后果。 当单项不良低于 3%时,生产管理要及时将不良品交 修理维修,修理将修好的不良品要贴修理编号,并 从第一 QC 位下机。
修正工艺要求; 重新修订物料规格要求; 修改设计存在的不完善因素。
相关文件 /记录
《样机校位 报告》
《校正行
为报告》
《不合格
品控制程 序》
流程
实施改善方案 问题改善后 NO
的跟进 YES
结束
职责
工作要求
相关文件 /记录
工 程 、 开 根据方案的要求进行评审,经技术和品质评估通过 《纠正措施
工程人员根据问题判断类型(作业、物料、设计) 总不良高于 25%以上时,应勒令停线处理。 参照《不合格品控制程序》运行。
当单项不良超过 3%,在 15 分钟内未能解决时,由 生产线组长、领班、物料员、IPQC、工程人员、SMT 管理人员根据不良或异常状况开出《校正行为报 告》; 组长、领班、物料员、IPQC、工程人员、SMT 管理 人员开出的《校正行为报告》单要如实反映问题, 不得夸大事实。 作业问题应在《校正行为报告》单上描述纠正改善 措施。 设计、物料问题按《不合格品控制程序》执行。
- 1、下载文档前请自行甄别文档内容的完整性,平台不提供额外的编辑、内容补充、找答案等附加服务。
- 2、"仅部分预览"的文档,不可在线预览部分如存在完整性等问题,可反馈申请退款(可完整预览的文档不适用该条件!)。
- 3、如文档侵犯您的权益,请联系客服反馈,我们会尽快为您处理(人工客服工作时间:9:00-18:30)。
发出部门:QC部编号:QC-WI-20111223 版次:1.0 页数:1 OF 2
编写:胥维复核:审批:日期:23/Dec/2011 主题:关于PCBA在线不良品流程控制的规定
1.0目的
加强对在线不良品的控制,确保不良品得到有效的控制,防止不良品混入良品中造成不良流出的质量事件。
2.0适用范围
适用于所有PCBA产品不良品检查控制。
3.0相关文件
《检查与测试记录》/《修理维修记录表》
4.0职责
4.1 LQC负责将不良品挑出并给予明确的标识和区分放置。
4.2 QC组长负责对不良品的统计和及时的反馈在线不良情况。
4.3生产修理负责不良品的及时维修和及时反馈不良原因所在。
4.4 PE负责不良品的分析和在线的控制。
4.5 QC/生产管理员负责对相关人员的培训和对不良品控制流程的管理和监控。
5.0作业程序
5.1 LQC在线检查时,发现有不良品必须及时的标上对应的不良品故障代号,并放入指定的红色不良品胶盆中。
同时做好测试记录。
在测试好的PCBA必须在指定位置标识上对应的测试印章。
5.2 QC组长必须及时的检查和统计LQC检查出的不良品,发现有异常必须及时通知生产、PE及时的处理解决。
并且必须跟踪其改进的效果。
如不能及时解决的应上报部门主管级处理,并根据情况出具相应的CAR要求相关部门改处理。
5.3 生产修理人员应及时的对LQC挑出的不良品进行分析维修,并做好维修报表,发现有严重或同种不良偏多(每小时多余5pcs)时应及时的通知相关管理人员和PE,同时配合PE和生产查出不良原因,以便于生产和品质的及时控制。
同时修理人员将不良品修理好后必须将其不良标识擦洗干净,同时将修好的产品必须从ICT测试位之前放置下线。
(后续的成品修理必须从外观检查位之前下线)。
发出部门:QC部编号:QC-WI-20111223 版次:1.0 页数:2 OF 2
编写:胥维复核:审批:日期:23/Dec/2011 主题:关于PCBA在线不良品流程控制的规定
5.4 PE技术人员应随时的检查生产线不良品情况。
发现有不良应联合生产品质及时的分析处理。
找出不良原因的根本所在,并能从原料、设备、环境、人为等方面给予根本的解决处理。
5.5 生产、QC对应的管理员必须对所属人员针对不良品的控制流程进行相应的培训考核,让所有人员清楚的知道不良品的控制流程及作业方式方法。
同时在日常的工作共给予管理控制,发现有不良情况必须进行再次的培训教育,直至操作人员清楚明白。
同时生产必须对明确的让包装人员知道每种PCBA在线QC不良品记号标识所在及QC 检查合格的标识位置和方式,在包装时必须检查机板必须有QC检查合格的标识和无不良标识的存在。
作业流程:
LQC在线检测发现不良品
LQC标识并放入指定的红
色的不良品胶盆中。
修理人员分析维修
修理OK后,擦拭不良标识
并返回ICT测试工位测试
LQC外观和功能给予重新
测试。