[推荐]刀具切削参数
加工中心硬质合金刀具切削参数表经典

0.06 -0.025--0.047 高速推荐侧刃切削
1500 -0.025--0.047 高速推荐侧刃切削
13000 -0.025--0.047 高速推荐侧刃切削
60 -0.025--0.047 高速推荐侧刃切削
0.81 -0.025--0.047 高速推荐侧刃切削
刀具直径
E6 E6 E6 E6 E6 E6 E8 E8 E8 E8 E8 E8 刀具直径
0.06 -0.025--0.047 高速推荐侧刃切削
1500 -0.025--0.047 高速推荐侧刃切削
13000 -0.025--0.047 高速推荐侧刃切削
60 -0.025--0.047 高速推荐侧刃切削
0.81 -0.025--0.047 高速推荐侧刃切削
高速切削 刀具精度
侧刃切削
15 -0.025--0.047 高速推荐侧刃切削
侧刃切削
0.2-0.3 4
1200 2950 50 0.783 0.2-0.3
6 1300 2800 50 0.783 侧刃切削
0.25-0.5 8
1500 1750 60 1.087 0.25-0.5 10 1500 2000 60
高速切削 刀具精度
侧刃切削
9
-0.025--0.047 高速推荐侧刃切削
0.06 -0.025--0.047 高速推荐侧刃切削
1500 -0.025--0.047 高速推荐侧刃切削
13000 -0.025--0.047 高速推荐侧刃切削
60 -0.025--0.047 高速推荐侧刃切削
0.81 -0.025--0.047 高速推荐侧刃切削
9
-0.025--0.047 高速推荐侧刃切削
常用刀具的切削参数
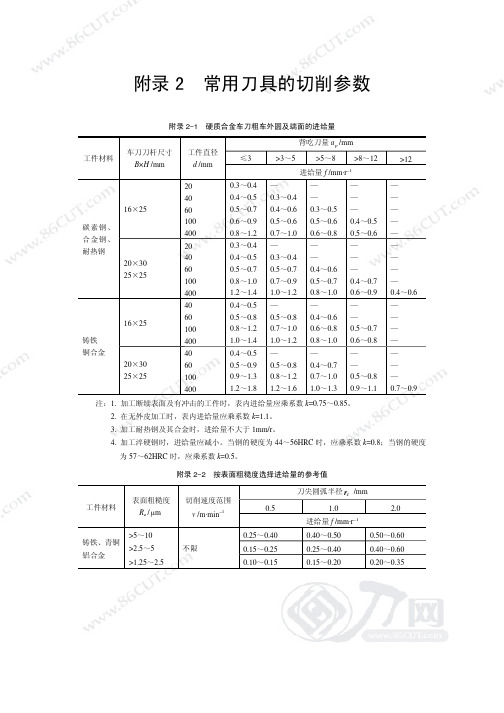
附录2 常用刀具的切削参数附录2-1 硬质合金车刀粗车外圆及端面的进给量背吃刀量p a /mm≤3 >3~5 >5~8 >8~12>12工件材料车刀刀杆尺寸 B ×H /mm工件直径 d /mm 进给量f /mm·r –116×2520 4060 100 400 0.3~0.4 0.4~0.5 0.5~0.7 0.6~0.9 0.8~1.2 — 0.3~0.4 0.4~0.6 0.5~0.6 0.7~1.0 — — 0.3~0.5 0.5~0.6 0.6~0.8 — — — 0.4~0.5 0.5~0.6 — — — — — 碳素钢、合金钢、耐热钢20×30 25×2520 40 60 100 400 0.3~0.4 0.4~0.5 0.5~0.7 0.8~1.0 1.2~1.4 — 0.3~0.4 0.5~0.7 0.7~0.9 1.0~1.2 — — 0.4~0.6 0.5~0.7 0.8~1.0 — — — 0.4~0.7 0.6~0.9 — — — — 0.4~0.6 16×254060 100 400 0.4~0.5 0.5~0.8 0.8~1.2 1.0~1.4 — 0.5~0.8 0.7~1.0 1.0~1.2 — 0.4~0.6 0.6~0.8 0.8~1.0 — — 0.5~0.7 0.6~0.8 — — — — 铸铁 铜合金20×30 25×2540 60 100 4000.4~0.5 0.5~0.9 0.9~1.3 1.2~1.8— 0.5~0.8 0.8~1.2 1.2~1.6— 0.4~0.7 0.7~1.0 1.0~1.3— — 0.5~0.8 0.9~1.1— — — 0.7~0.9 注:1. 加工断续表面及有冲击的工件时,表内进给量应乘系数k =0.75~0.85。
常用刀具的切削参数

常用刀具的切削参数1.钻头:钻头是一种旋转式刀具,通常用于在硬材料上钻孔。
切削速度是指钻头每分钟旋转圈数,一般以转/分钟(RPM)为单位。
切削速度的选择将受到材料类型和钻头直径的影响。
对于大型孔径和脆性材料,较低的切削速度可能更合适。
进给量是指每转刀具在轴向(沿钻孔方向)上移动的距离。
进给量的选择将受到钻头直径和材料类型的影响。
较大直径的钻头可能需要较大的进给量。
切削深度是指钻头在一次进给中的轴向深度。
如果切削深度太大,可能会导致钻头断裂或切削不洁净。
切削深度的选择还将受到材料类型和钻头直径的影响。
2.铣刀:铣刀是一种回转和前进运动刀具,常用于平面加工、开槽和切割。
切削速度是指铣刀每分钟旋转圈数,同样以转/分钟(RPM)为单位。
切削速度的选择将受到材料类型、铣刀材料和刀具直径的影响。
进给量是指铣刀在工件表面上移动的距离。
较大的进给量将导致更高的切削速度,但也可能影响切削表面的质量。
切削深度是指铣刀在一次运动中与工件表面的最大距离。
切削深度的选择将受到材料类型和铣刀直径的影响。
3.车刀:车刀是一种在工件上进行旋转切削的刀具,常用于车削和车削加工。
切削速度是指车刀每分钟旋转圈数,仍然以转/分钟(RPM)为单位。
切削速度的选择将受到材料类型、车刀材料和刀具直径的影响。
进给量是指车刀在工件上移动的距离。
较大的进给量可以提高生产效率,但也可能影响切削表面的质量。
切削深度是指车刀与工件表面的最大距离。
切削深度的选择将受到材料类型和车刀直径的影响。
4.锯片:锯片是一种用于切割材料的刀具,常用于金属、木材和塑料加工。
切削速度是指锯片每分钟旋转圈数,仍然以转/分钟(RPM)为单位。
切削速度的选择将受到材料类型、锯片材料和刀具直径的影响。
进给量是指锯片在工件上移动的距离。
较大的进给量可以提高切割速度,但也可能导致切割表面质量的下降。
切削深度是指锯片与工件表面的最大距离。
切削深度的选择通常由锯片的直径和材料类型确定。
数控车床刀片切削参数

数控车床刀片切削参数
数控车床刀片的切削参数包括以下几个方面:
1. 等效切削速度(Vc):数控车床刀片的等效切削速度是指刀具在进行切削时对工件表面每分钟实际移动的线速度。
等效切削速度与切削材料、刀具材料、转速和进给速度等因素有关。
2. 进给速度(F):进给速度是指工件在切削过程中每分钟所移动的距离,即工件进给速率。
进给速度与刀具的几何形状、切削材料和刀具材料等有关。
3. 切削深度(Ap):切削深度是指刀具在进行切削时,每次切削所能切掉的工件材料厚度。
切削深度与刀具材料、刃数、切削参数等参数有关。
4. 切削宽度(Ae):切削宽度是指刀具在每次切削时所能切削的工件材料的宽度。
切削宽度与刀具材料、刃数、切削参数等参数有关。
5. 转速(n):转速是指数控车床刀具所使用的高速旋转的速度。
转速与切削材料、刀具材料、等效切削速度等因素有关。
6. 切割力(Fc):切割力是指数控车床刀具在切削时对工件及刀具的作用力。
切割力与切削材料、刀具材料、切削参数等参数有关。
切削参数表(车刀)
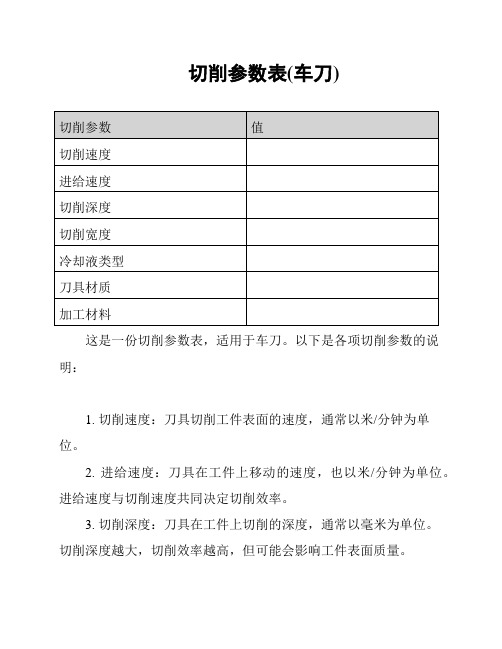
切削参数表(车刀)
这是一份切削参数表,适用于车刀。
以下是各项切削参数的说明:
1. 切削速度:刀具切削工件表面的速度,通常以米/分钟为单位。
2. 进给速度:刀具在工件上移动的速度,也以米/分钟为单位。
进给速度与切削速度共同决定切削效率。
3. 切削深度:刀具在工件上切削的深度,通常以毫米为单位。
切削深度越大,切削效率越高,但可能会影响工件表面质量。
4. 切削宽度:刀具在工件上切削的宽度,同样以毫米为单位。
切削宽度也是影响切削效果和工件表面质量的重要参数。
5. 冷却液类型:在加工过程中使用的冷却液的类型,根据加工材料和切削条件选择适合的冷却液。
6. 刀具材质:车刀的刀具材质,根据加工材料和切削条件选择合适的刀具材料。
7. 加工材料:要加工的工件材料,根据工件材料选择适当的切削参数。
以上是切削参数表的内容,根据具体的加工需求和条件,调整这些参数可以获得更好的切削效果。
记得根据实际情况进行测试和调整参数,以确保安全和高效的切削操作。
刀具及切削参数选择
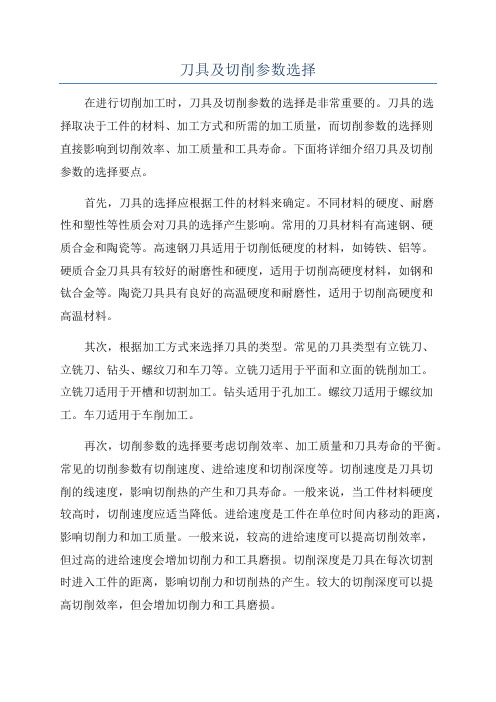
刀具及切削参数选择在进行切削加工时,刀具及切削参数的选择是非常重要的。
刀具的选择取决于工件的材料、加工方式和所需的加工质量,而切削参数的选择则直接影响到切削效率、加工质量和工具寿命。
下面将详细介绍刀具及切削参数的选择要点。
首先,刀具的选择应根据工件的材料来确定。
不同材料的硬度、耐磨性和塑性等性质会对刀具的选择产生影响。
常用的刀具材料有高速钢、硬质合金和陶瓷等。
高速钢刀具适用于切削低硬度的材料,如铸铁、铝等。
硬质合金刀具具有较好的耐磨性和硬度,适用于切削高硬度材料,如钢和钛合金等。
陶瓷刀具具有良好的高温硬度和耐磨性,适用于切削高硬度和高温材料。
其次,根据加工方式来选择刀具的类型。
常见的刀具类型有立铣刀、立铣刀、钻头、螺纹刀和车刀等。
立铣刀适用于平面和立面的铣削加工。
立铣刀适用于开槽和切割加工。
钻头适用于孔加工。
螺纹刀适用于螺纹加工。
车刀适用于车削加工。
再次,切削参数的选择要考虑切削效率、加工质量和刀具寿命的平衡。
常见的切削参数有切削速度、进给速度和切削深度等。
切削速度是刀具切削的线速度,影响切削热的产生和刀具寿命。
一般来说,当工件材料硬度较高时,切削速度应适当降低。
进给速度是工件在单位时间内移动的距离,影响切削力和加工质量。
一般来说,较高的进给速度可以提高切削效率,但过高的进给速度会增加切削力和工具磨损。
切削深度是刀具在每次切割时进入工件的距离,影响切削力和切削热的产生。
较大的切削深度可以提高切削效率,但会增加切削力和工具磨损。
此外,还应考虑冷却润滑剂的选择和使用。
合适的冷却润滑剂可以降低切削热的产生,减小工具磨损,提高加工质量。
综上所述,刀具及切削参数的选择需要考虑工件材料、加工方式和所需加工质量。
合理选择刀具类型和切削参数可以提高切削效率、加工质量和工具寿命。
在实际应用中,还需要根据具体情况进行调整和优化。
直径600-700粗镗刀切削参数

直径600-700粗镗刀切削参数粗镗刀是一种广泛用于金属加工中的切削工具,常用于修整孔内壁,提高孔的尺寸精度和表面质量,下面将就直径为600-700的粗镗刀切削参数进行详细介绍。
1.切削速度:粗镗刀的切削速度是指一分钟内切削刀具切削表面的线速度,常用单位为m/min。
切削速度需要根据工件材料的硬度和加工精度要求来确定,通常的切削速度为10-30m/min。
2.进给量:进给量是指粗镗刀在一次切削中,每转给定转数切削刃前进的距离,通常用mm/r来表示。
进给量的选择需要综合考虑工件材料的硬度、刀具材料、切削速度等因素。
一般情况下,进给量过大会导致切削过重,刀具易磨损,进给量过小则会导致加工时间过长。
3.主轴转速:主轴转速是粗镗刀切削时主轴的转速,单位为r/min。
主轴转速一般需要根据切削速度和切削直径来选择,较高的主轴转速可以提高生产效率,但过高的主轴转速也会增加刀具磨损和切削温度。
4.切削深度:切削深度是指粗镗刀每次切削刃在孔内切削的深度,通常用mm来表示。
切削深度需要根据工件材料的硬度、刀具的刚性以及加工精度要求来确定,一般情况下,切削深度不宜过大,以免导致加工质量下降和刀具过早磨损。
5.冷却液:在进行粗镗刀切削中,冷却液是非常重要的辅助工具。
它可以帮助降低切削温度,减小刀具磨损,提高加工表面质量。
常用的冷却液有水溶液、油溶液等,选择合适的冷却液需要根据工件材料以及具体的切削情况来确定。
以上是关于直径600-700的粗镗刀切削参数的详细介绍。
在实际应用中,还需要根据具体的加工要求、刀具的选择以及工件材料的情况等因素进行合理的调整和综合考虑,以达到最佳的切削效果。
常用刀具的切削参数

常用刀具的切削参数刀具切削参数是指在切削过程中,对刀具进行设置和调整的一系列参数。
这些参数包括切削速度、进给速度、切削深度、切削角度等,它们的选择和调整直接影响到切削效果和刀具寿命。
下面是常用刀具的切削参数的一些介绍:1. 切削速度(Cutting Speed):切削速度是指刀具在切削过程中移动的速度,一般用单位时间内刀具切削的长度来表示。
切削速度的选择取决于工件材料的硬度和切削材料的种类。
一般来说,硬度较高的材料需要较低的切削速度,而硬度较低的材料则可以使用较高的切削速度。
2. 进给速度(Feed Rate):进给速度是指刀具在切削过程中每分钟进给到工件上的距离。
进给速度的选择取决于工件的材料和切削操作的要求。
较低的进给速度可以获得更好的切削质量,而较高的进给速度可以提高生产效率。
3. 切削深度(Depth of Cut):切削深度是指刀具切削时每次切削进入工件的深度。
切削深度的选择需要考虑工件材料的硬度和切削工具的强度。
一般来说,较硬的材料需要较小的切削深度,而较软的材料则可以选择较大的切削深度。
4. 切削角度(Cutting Angle):切削角度是指刀具切削刃与工件表面之间的夹角。
切削角度的选择取决于工件材料的硬度和切削操作的要求。
一般来说,较硬的材料需要较大的切削角度,而较软的材料则可以选择较小的切削角度。
5. 切削液(Cutting Fluid):切削液是在切削过程中起冷却、润滑和清洁作用的液体。
切削液的选择取决于切削材料的种类和切削条件的要求。
常见的切削液有切削油、切削液和切削蜡等。
6. 切削力(Cutting Force):切削力是指切削过程中刀具对工件施加的力。
切削力的大小受到切削参数的影响,包括切削速度、进给速度、切削深度和切削角度等。
合理选择切削参数可以降低切削力,提高切削效率和刀具寿命。
7. 切削温度(Cutting Temperature):切削温度是指刀具和工件在切削过程中产生的热量。
45钢刀具切削参数
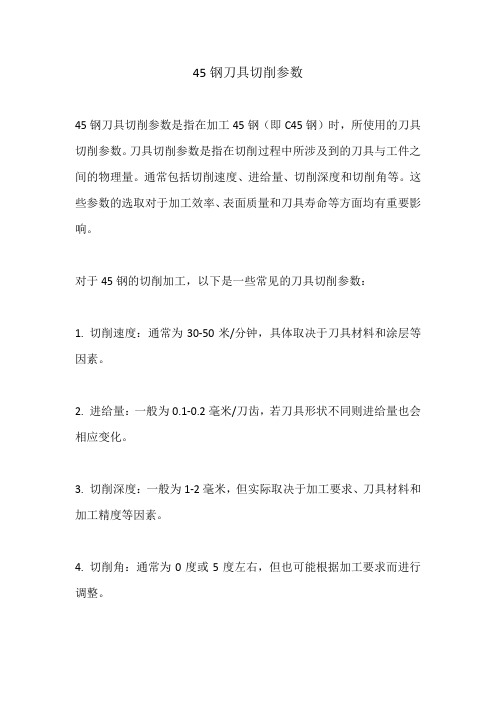
45钢刀具切削参数
45钢刀具切削参数是指在加工45钢(即C45钢)时,所使用的刀具切削参数。
刀具切削参数是指在切削过程中所涉及到的刀具与工件之间的物理量。
通常包括切削速度、进给量、切削深度和切削角等。
这些参数的选取对于加工效率、表面质量和刀具寿命等方面均有重要影响。
对于45钢的切削加工,以下是一些常见的刀具切削参数:
1. 切削速度:通常为30-50米/分钟,具体取决于刀具材料和涂层等因素。
2. 进给量:一般为0.1-0.2毫米/刀齿,若刀具形状不同则进给量也会相应变化。
3. 切削深度:一般为1-2毫米,但实际取决于加工要求、刀具材料和加工精度等因素。
4. 切削角:通常为0度或5度左右,但也可能根据加工要求而进行调整。
在选择刀具切削参数时,需要考虑刀具材料、涂层、刀具形状、加工要求等因素,以使切削过程顺利进行,且达到最佳的加工效果。
同时,也需要注意切削参数的合理性,避免切削参数过高或过低,导致刀具寿命的缩短或加工效率的降低。
CBN刀具的切削参数

CBN刀具的切削参数作者单位:郑州华菱超硬材料有限公司一,CBN刀具切削参数的制定方法:粗加工时,应尽量保证较高的金属切除率和必要的刀具耐用度,故一般优先选择尽可能大的切削深度ap,其次选择较大的进给量f,最后根据刀具耐用度要求,确定合适的切削速度。
精加工时,首先应保证工件的加工精度和表面质量要求,故一般选用较小的进给量f和切削深度ap,而尽可能选用较高的切削速度υc。
1,切削深度ap的选择1)切削深度应根据工件的加工余量来确定。
粗加工时,除留下精加工余量外,一次走刀应尽可能切除全部余量。
当加工余量过大,工艺系统刚度较低,机床功率不足,刀具强度不够或断续切削的冲击振动较大时,可分多次走刀。
切削表面层有硬皮的铸锻件时,应尽量使ap大于硬皮层的厚度,以保护刀尖。
2)半精加工和精加工的加工余量一般较小时,可一次切除,但有时为了保证工件的加工精度和表面质量,也可采用二次走刀。
3)多次走刀时,应尽量将第一次走刀的切削深度取大些,一般为总加工余量的2/3~3/4。
4)在中等功率的机床上、粗加工时的切削深度可达8~10mm,半精加工(表面粗糙度为Ra6.3~3.2μm)时,切削深度取为0.5~2mm,精加工(表面粗糙度为Ra1.6~0.8μm)时,切削深度取为0.1~0.4mm。
2,进给量f的选择切削深度选定后,接着就应尽可能选用较大的进给量f。
粗加工时,由于作用在工艺系统上的切削力较大,进给量的选取受到下列因素限制;机床—刀具—工件系统的刚度,机床进给机构的强度,机床有效功率与转矩,以及断续切削时刀片的强度。
半精加工和精加工时,最大进给量主要受工件加工表面粗糙度的限制。
工厂中,进给量一般多根据经验按一定表格选取(详见车、钻、铣等各章有关表格),在有条件的情况下,可通过对切削数据库进行检索和优化。
3,切削速度υc的选择在切削深度ap选定以后,可在保证刀具合理耐用度的条件下,用计算的方法或用查表法确定切削速度υc的值。
刀具切削参数表

对长度与直径比(l/d)超过5倍的刀具在加工中应降低转速与进给率,并减少吃
倍数(l/d) 参数比例 转数S 进给率F Ar(切深)
1-5倍 100% 100% 100%
6倍 70% 70% 70%
7倍 60% 60% 60%
8-10倍 50%↓ 50%↓ 50%↓
6.球刀加工时应根据工件不同要求进行参数选择,参阅《模具加工工艺规范》
0.1
外观型腔面平坦部位尽可能避免采用球刀光刀,避开零切削区。方法:采用圆鼻刀或球 加工方式优选 机床选用最底限 电蚀及数控工艺选用 筋加工方式 等高铣 II级精度 优先电蚀 优先数控 II级精度 优先电蚀 优先数控
7.刀具夹持部分最小长度与刀具直径比例原则:
序号 1 2 3 4 刀具直径 Φ 20-Φ 32 Φ 10-Φ 20 Φ 5-Φ 10 Φ 3-Φ 5
切削线速度 主轴转速 进给速度 金属去除率 端铣飞刀计算 N=Vc*1000/(p*Dc) rpm Vf=fz*N*Zn mm/min Q=ap*ae*Vf/1000 CM3
Vc=p*Dc*N/1000 m/min(切削线速度可参考刀具商
端铣飞刀计算
Dc刀具切削位置直径 ap轴向切削深度(可参考刀具商推荐值) ae 径向切削深度(可参考刀具商推荐值) Fz每齿进给量(可参考刀具商推荐值) Zn刀具齿数 以32日立飞刀为例计算
*895*.4=716
*1342* .2=536.8 *N *Zn mm/min
De*N/1000 m/min
*1000/(p*De) rpm
√ap(Dc2-ap) N*Zn mm/min
Dc*N/1000 m/min (可参考刀具商推荐值)
1000/(p*Dc) rpm
切削参数表(切割工具)

切削参数表(切割工具)1. 简介本文档旨在提供有关切削工具的切削参数表,以帮助用户在使用切割工具时了解和选择合适的切削参数。
2. 切削参数说明切削参数是指在使用切割工具时需要考虑的一些主要因素。
以下是常见的切削参数及其说明:2.1 刀具类型刀具类型是指所使用的切割工具的种类。
常见的刀具类型有:高速钢刀具、硬质合金刀具、多齿刀具等。
不同类型的刀具适用于不同的切削任务,选择适合的刀具类型可以提高工作效率和切割质量。
2.2 刀具材料刀具材料是指刀具的制作材料。
常见的刀具材料有:钢、硬质合金、陶瓷等。
不同的刀具材料具有不同的硬度、耐磨性和耐热性,选择适合的刀具材料可以延长刀具寿命并提高切割精度。
2.3 刀具直径刀具直径是指刀具的直径尺寸。
刀具直径大小直接影响到切削过程中的切削力、切削速度和切削表面质量。
通常情况下,刀具直径越大,切削力越大,切削速度越慢,但切削表面质量更好。
2.4 刀具齿数刀具齿数是指刀具上的齿片数量。
刀具齿数的选择应根据具体的切割任务和切削材料来确定。
通常情况下,刀具齿数越多,切削速度越快,但同时也会增加刀具的磨损,需要更频繁地更换刀具。
2.5 切削速度切削速度是指刀具在切割过程中的线速度。
切削速度的选择应根据切割工件的材料和切割任务来确定。
选择合适的切削速度可以提高切割效率和切割质量。
2.6 进给量进给量是指工件在单位时间内的切削进给量。
进给量的选择应根据具体的切割任务和切削材料来确定。
进给量过大可能导致刀具磨损加剧,进给量过小可能影响切削效率。
3. 切削参数表样例注:以上数据仅供参考,具体的切削参数需根据实际情况进行调整和选择。
4. 总结切削参数表是选择合适的切削工具时的重要参考依据。
根据不同的切割任务和切削材料,合理选择刀具类型、刀具材料、刀具直径、刀具齿数、切削速度和进给量等切削参数,可以提高工作效率和切割质量。
刀具基本切削参数表
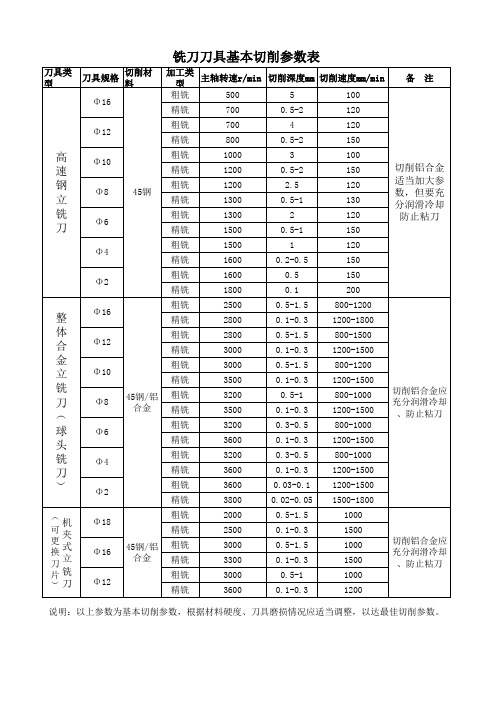
120
防止粘刀
精铣
1500
0.5-1
150
粗铣
1500
1
120
精铣
1600
0.2-0.5
150
粗铣
1600
0.5
150
精铣
1800
0.1
200
粗铣
2500
0.5-1.5
800-1200
精铣
2800
0.1-0.3
1200-1800
粗铣
2800
0.5-1.5
800-1500
精铣
3000
0.1-0.3
1200-1500
说明:以上参数为基本切削参数,根据材料硬度、刀具磨损情况应适当调整,以达最佳切削参数。
刀具类 型
高 速 钢 立 铣 刀
整 体 合 金 立 铣 刀 (
球 头 铣 刀 )
(机
可 更 换 刀
夹 式 立
片铣
)刀
刀具规格
切削材 料
Φ16
Φ12
Φ10
Φ8
45钢
Φ6
Φ4
Φ2
Φ16
Φ12
Φ10
Φ8
45钢/铝 合金
Φ6
Φ4
Φ2
Φ18
Φ16
45钢/铝 合金
Φ12
铣刀刀具基本切削参数表
加工类 型
主轴转速r/min
1500 1000 1500 1000
切削铝合金应 充分润滑冷却 、防止粘刀
精铣
3600
0.1-0.3
1200
说明:以上参数为基本切削参数,根据材料硬度、刀具磨损情况应适当调整,以达最佳切削参数。
铣刀刀具基本切削参数表
常用刀具的切削参数

附录2 常用刀具的切削参数附录2-1 硬质合金车刀粗车外圆及端面的进给量背吃刀量p a /mm≤3 >3~5 >5~8 >8~12>12工件材料车刀刀杆尺寸 B ×H /mm工件直径 d /mm 进给量f /mm·r –116×2520 4060 100 400 0.3~0.4 0.4~0.5 0.5~0.7 0.6~0.9 0.8~1.2 — 0.3~0.4 0.4~0.6 0.5~0.6 0.7~1.0 — — 0.3~0.5 0.5~0.6 0.6~0.8 — — — 0.4~0.5 0.5~0.6 — — — — — 碳素钢、合金钢、耐热钢20×30 25×2520 40 60 100 400 0.3~0.4 0.4~0.5 0.5~0.7 0.8~1.0 1.2~1.4 — 0.3~0.4 0.5~0.7 0.7~0.9 1.0~1.2 — — 0.4~0.6 0.5~0.7 0.8~1.0 — — — 0.4~0.7 0.6~0.9 — — — — 0.4~0.6 16×254060 100 400 0.4~0.5 0.5~0.8 0.8~1.2 1.0~1.4 — 0.5~0.8 0.7~1.0 1.0~1.2 — 0.4~0.6 0.6~0.8 0.8~1.0 — — 0.5~0.7 0.6~0.8 — — — — 铸铁 铜合金20×30 25×2540 60 100 4000.4~0.5 0.5~0.9 0.9~1.3 1.2~1.8— 0.5~0.8 0.8~1.2 1.2~1.6— 0.4~0.7 0.7~1.0 1.0~1.3— — 0.5~0.8 0.9~1.1— — — 0.7~0.9 注:1. 加工断续表面及有冲击的工件时,表内进给量应乘系数k =0.75~0.85。
加工中心刀具切削参数
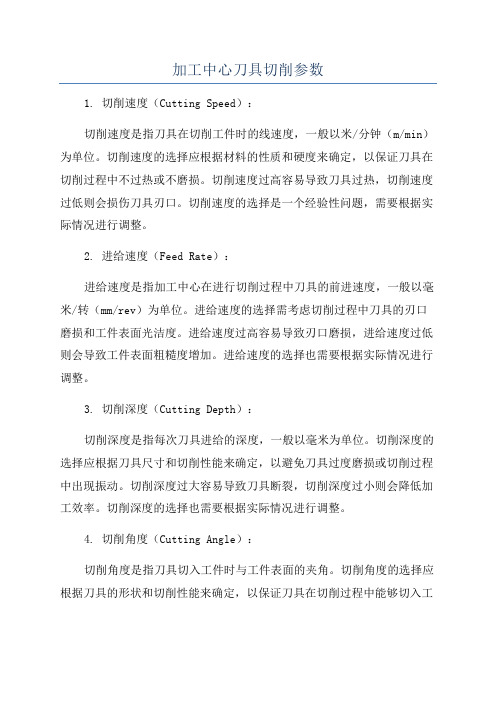
加工中心刀具切削参数1. 切削速度(Cutting Speed):切削速度是指刀具在切削工件时的线速度,一般以米/分钟(m/min)为单位。
切削速度的选择应根据材料的性质和硬度来确定,以保证刀具在切削过程中不过热或不磨损。
切削速度过高容易导致刀具过热,切削速度过低则会损伤刀具刃口。
切削速度的选择是一个经验性问题,需要根据实际情况进行调整。
2. 进给速度(Feed Rate):进给速度是指加工中心在进行切削过程中刀具的前进速度,一般以毫米/转(mm/rev)为单位。
进给速度的选择需考虑切削过程中刀具的刃口磨损和工件表面光洁度。
进给速度过高容易导致刃口磨损,进给速度过低则会导致工件表面粗糙度增加。
进给速度的选择也需要根据实际情况进行调整。
3. 切削深度(Cutting Depth):切削深度是指每次刀具进给的深度,一般以毫米为单位。
切削深度的选择应根据刀具尺寸和切削性能来确定,以避免刀具过度磨损或切削过程中出现振动。
切削深度过大容易导致刀具断裂,切削深度过小则会降低加工效率。
切削深度的选择也需要根据实际情况进行调整。
4. 切削角度(Cutting Angle):切削角度是指刀具切入工件时与工件表面的夹角。
切削角度的选择应根据刀具的形状和切削性能来确定,以保证刀具在切削过程中能够切入工件并顺利进行切削。
切削角度对切削力和刀具寿命有着显著的影响。
切削角度的选择也需要根据实际情况进行调整。
5. 切削液(Cutting Fluid):切削液是指在切削过程中用于冷却刀具和工件的液体。
切削液可以有效降低切削温度、减少切削力和刃口磨损,提高加工质量和刀具寿命。
切削液的选择应根据加工材料和切削性能来确定,以保证切削效果的最佳化。
综上所述,加工中心刀具切削参数是切削加工中的重要参数,对于加工质量和效率具有重要意义。
在实际操作中,需要根据材料性质、刀具特点和切削要求来灵活调整这些参数,以达到最优的加工效果。
- 1、下载文档前请自行甄别文档内容的完整性,平台不提供额外的编辑、内容补充、找答案等附加服务。
- 2、"仅部分预览"的文档,不可在线预览部分如存在完整性等问题,可反馈申请退款(可完整预览的文档不适用该条件!)。
- 3、如文档侵犯您的权益,请联系客服反馈,我们会尽快为您处理(人工客服工作时间:9:00-18:30)。
[推荐]刀具切削参数
刀具切削参数
切屑量:刀具每个刀槽切去材料的量
进料速率:刀具每个刀刃进入工件的速率——英寸/每分
英寸/每分(IPM):刀具每分钟内进入工件的线形距离,用英寸表示。
切削深度(DOC):端铣刀沿轴向方向进入部件表面后的深度。
使用电脑数控机器铣削时,通常以Z轴方向为标准。
英寸/每转(IPR):刀具每转的进料速率。
以英寸为单位,刀具的进料速率可以用它来计算。
I.P.R.=切削量x刀槽数
毫米/每转(MMPR):刀具每转的进料速率。
以米制为单位,刀具的进料速率可以
用它来计算。
M.M.P.R.=切削量x刀槽数
米/每分(MPM):端铣刀的切削速度,这种米制单位在所有地区均适用。
该单位表示刀具穿过部件的速率。
转/每分(RPM):刀具接轴的运行速率,这个值可用MPM或SFPM单位计算而得。
表面英尺/每分(SFPM):这是美国使用的端铣刀切削速率的单位。
它表示刀具在一个给定位置每分钟转过的周长,用英尺来表示。
使用刀具时要选择合适的切削速度、进料速度以及切削深度
购买者在使用端铣刀时一定要注意以下参数:
SFPM:刀具表面切削速率
切屑量:刀具每个刀槽切去材料的量
切削深度:根据具体的部件选择
注意:切削深度不要超过刀具槽深,切的太深会有损刀具。
如果需要切的更深时,就换一个直径再大一些的刀具,要始终保
持刀具直径和切削深度的比例为1:1
切削宽度:最大不要超过刀具直径的2/3。