特定条件下刀具及切削参数的选择
刀具参数和切削用量选择
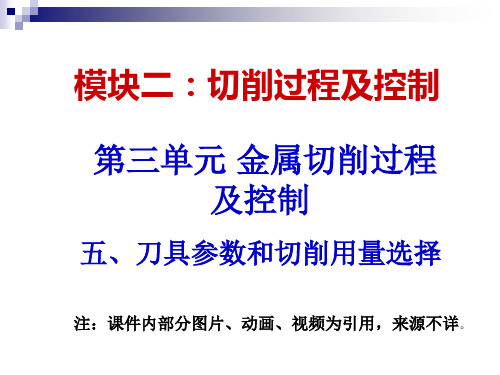
取较大值,如Κr´=30°~45°。
1.5 刃倾角的选择
刃倾角对切削加工的影响:刃倾角λs的正负和大小,影响刀尖部分的
强度、切屑流出的方向和切削分力之间的比值。
2.2 进给量f的确定
粗加工时,进给量的确定主要受切削力的限制, 在刀杆和工件刚度以及机床进给机构强度允许的情况 下,同时考虑工件材料和断屑等问题,应尽量选择较 大值。
精加工时,一般切削力不大,进给量主要受表面 粗糙粗限制,一般根据表面粗糙度的要求来选取,具 体数值参见切削用量手册。
2.3 切削速度v的确定
粗加工时,切削速度v主要受刀具耐用度的限制,由于ap、f的 值比较大,需核算机床电机的功率是否足够。
当切削速度由刀具耐用度确定时,可按下式计算:
C T mapxv
f
yv
kv
当切削速度受机床功率限制或校验机床功率时,可按下式计算:
6104 PEη Fz
m/min
精加工时,ap、f的值都比较小,切削力较小,一般机床电机 功率足够,所以切削速度主要由刀具耐用度决定。
1.4 副偏角的选择
副偏角Κr´的作用: 减小副切削刃、副后刀面和已加工表面之间的摩擦,其大
小会影响已加工表面粗糙度和刀尖部分的强度。 副偏角对切削加工的影响:
减小副偏角Κr´,使刀尖部分体积增大,刀尖强度提高,
残留面积高度降低,但刀具与工件之间的摩擦增加。 副偏角的选择:
副偏角变化幅度不大。一般外圆车刀取Κr´=6°~15°,
2.4 切削用量确定的具体方法和实例
不锈钢加工刀具切削参数

不锈钢加工刀具切削参数一、引言不锈钢是一种常用的材料,应用广泛于各个行业中。
在不锈钢加工中,刀具的选择和切削参数的确定对于加工质量和效率具有重要影响。
本文将从不锈钢加工刀具的选择和切削参数的确定两个方面展开论述。
二、不锈钢加工刀具的选择选择合适的刀具是确保不锈钢加工成功的首要条件。
不锈钢具有较高的硬度和良好的耐磨性,因此在选择刀具时需要考虑以下几个因素:2.1 刀具材料不锈钢加工通常选择硬质合金刀具,因为硬质合金具有较高的硬度和耐磨性,能够在不锈钢的高温和高切削力下保持较好的切削性能。
常见的硬质合金材料有WC-Co、WC-TiC-TaC等。
2.2 刀具形状根据不锈钢加工的具体需求,选择合适的刀具形状是十分重要的。
常见的刀具形状包括平面铣刀、立铣刀、球头铣刀等。
平面铣刀适用于对不锈钢表面进行平整加工,立铣刀适用于进行深度加工,球头铣刀适用于进行轮廓加工等。
2.3 刀具涂层通过刀具涂层可以提高刀具的耐磨性和切削性能,延长刀具的使用寿命。
在不锈钢加工中,常用的刀具涂层有TiN、TiCN、TiAlN等,这些涂层具有良好的耐磨性和热稳定性。
三、不锈钢加工切削参数的确定除了选择合适的刀具外,还需要确定合适的切削参数才能保证加工质量和效率。
切削参数的确定与不锈钢材料的性质、加工要求和刀具特点等因素密切相关。
3.1 切削速度切削速度是切削参数中最重要的一个参数,它决定着切削时刀具与工件之间的相对运动速度。
在不锈钢加工中,切削速度不宜过高,一般建议控制在60-100 m/min之间。
3.2 进给量进给量是指单位切削时间内切削刀具在切削方向上的移动距离。
对于不锈钢加工,进给量要适中,过小会导致加工效率低下,过大则容易导致切削刃磨损过快。
因此,根据具体情况选择合适的进给量十分重要。
3.3 主轴转速主轴转速是指切削时主轴单位时间内旋转的圈数。
选择合适的主轴转速可以保证切削进给率和表面质量。
在不锈钢加工中,一般建议选择较低的主轴转速,以提高刀具寿命和加工质量。
机械加工中的刀具选择与切削参数优化
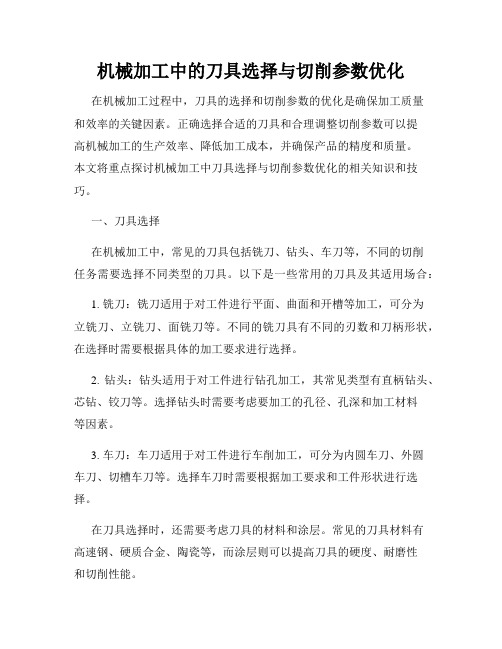
机械加工中的刀具选择与切削参数优化在机械加工过程中,刀具的选择和切削参数的优化是确保加工质量和效率的关键因素。
正确选择合适的刀具和合理调整切削参数可以提高机械加工的生产效率、降低加工成本,并确保产品的精度和质量。
本文将重点探讨机械加工中刀具选择与切削参数优化的相关知识和技巧。
一、刀具选择在机械加工中,常见的刀具包括铣刀、钻头、车刀等,不同的切削任务需要选择不同类型的刀具。
以下是一些常用的刀具及其适用场合:1. 铣刀:铣刀适用于对工件进行平面、曲面和开槽等加工,可分为立铣刀、立铣刀、面铣刀等。
不同的铣刀具有不同的刃数和刀柄形状,在选择时需要根据具体的加工要求进行选择。
2. 钻头:钻头适用于对工件进行钻孔加工,其常见类型有直柄钻头、芯钻、铰刀等。
选择钻头时需要考虑要加工的孔径、孔深和加工材料等因素。
3. 车刀:车刀适用于对工件进行车削加工,可分为内圆车刀、外圆车刀、切槽车刀等。
选择车刀时需要根据加工要求和工件形状进行选择。
在刀具选择时,还需要考虑刀具的材料和涂层。
常见的刀具材料有高速钢、硬质合金、陶瓷等,而涂层则可以提高刀具的硬度、耐磨性和切削性能。
二、切削参数优化切削参数的优化是机械加工中的一个重要环节,它直接影响加工效率和产品质量。
以下是一些常见的切削参数及其优化方法:1. 切削速度:切削速度是指刀具在单位时间内通过工件表面的线速度,它与切削力、刀具寿命和表面质量密切相关。
在选择切削速度时,需要考虑加工材料的硬度、刀具材料和涂层的性能等因素。
一般来说,切削速度适中可以提高加工效率,过高或过低都会对加工效果产生不利影响。
2. 进给速度:进给速度是指工件在单位时间内相对于刀具的移动速度,它与切削力、切屑处理和表面质量密切相关。
在选择进给速度时,需要考虑切削力的大小、切削液的使用和刀具的负荷承受能力等因素。
适当调整进给速度可以改善加工表面的光洁度和减少切削力。
3. 切削深度:切削深度是指刀具在每次切削中与工件接触的距离,它与切削力、切削温度和表面质量有关。
切削参数选择
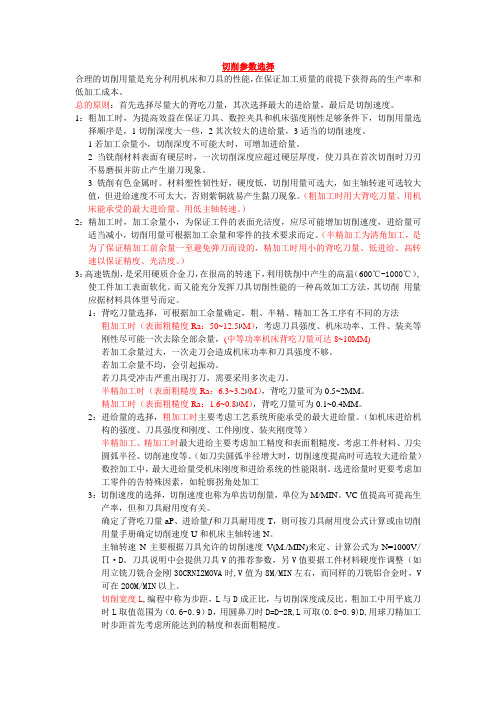
切削参数选择合理的切削用量是充分利用机床和刀具的性能,在保证加工质量的前提下获得高的生产率和低加工成本。
总的原则:首先选择尽量大的背吃刀量,其次选择最大的进给量,最后是切削速度。
1:粗加工时,为提高效益在保证刀具、数控夹具和机床强度刚性足够条件下,切削用量选择顺序是,1切削深度大一些,2其次较大的进给量,3适当的切削速度。
1若加工佘量小,切削深度不可能大时,可增加进给量。
2当铣削材料表面有硬层时,一次切削深度应超过硬层厚度,使刀具在首次切削时刀刃不易磨损并防止产生崩刀现象。
3铣削有色金属时。
材料塑性韧性好,硬度低,切削用量可选大,如主轴转速可选较大值,但进给速度不可太大,否则紫铜就易产生黏刀现象。
(粗加工时用大背吃刀量、用机床能承受的最大进给量、用低主轴转速。
)2:精加工时,加工佘量小,为保证工件的表面光洁度,应尽可能增加切削速度,进给量可适当减小,切削用量可根据加工佘量和零件的技术要求而定。
(半精加工为清角加工,是为了保证精加工前佘量一至避免弹刀而设的,精加工时用小的背吃刀量、低进给、高转速以保证精度、光洁度。
)3:高速铣削,是采用硬质合金刀,在很高的转速下,利用铣削中产生的高温(600℃-1000℃),使工件加工表面软化。
而又能充分发挥刀具切削性能的一种高效加工方法,其切削用量应据材料具体型号而定。
1:背吃刀量选择,可根据加工佘量确定,粗、半精、精加工各工序有不同的方法粗加工时(表面粗糙度Ra:50~12.5µM),考虑刀具强度、机床功率、工件、装夹等刚性尽可能一次去除全部佘量,(中等功率机床背吃刀量可达8~10MM)若加工佘量过大,一次走刀会造成机床功率和刀具强度不够。
若加工佘量不均,会引起振动。
若刀具受冲击严重出现打刀,需要采用多次走刀。
半精加工时(表面粗糙度Ra:6.3~3.2µM),背吃刀量可为0.5~2MM。
精加工时(表面粗糙度Ra:1.6~0.8µM),背吃刀量可为0.1~0.4MM。
3.7切削条件的合理选择

3.7 切削条件的合理选择一、刀具几何参数的合理选择刀具几何参数包含四方面内容:几何角度、刃形、刃面、刃口型式及参数(一)前角的选择1.前角的作用γ↑→变形程度↓→F↓q ↓→θ ↓→T↑振动↓质量↑0刀刃和刀头强度↓散热面积容热体积↓断屑困难在一定的条件下,存在一个合理值对于不同的刀具材料和工件材料,T 随γ的变化趋势为驼峰形。
高速钢的合理前角比Y合金的大。
加工塑材的合理前角比脆材的大2.合理前角的选择原则①粗加工、断续切削、刀材强度韧性低工材强度硬度高,选较小的前角;②工材塑韧性大、系统刚性差,易振动或机床功率不足,选较大的前角;③成形刀具、自动线刀具取小前角;④Aγ磨损增大前角,Aα磨损减小前角(二)后角的选择1.后角的作用α0↑→rn↓锋利、lα↓摩擦F↓→质量↑VB 一定,磨损体积↑→T↑但NB↑刀头强度↓散热体积↓重磨体积↑在一定的条件下,存在一个合理值2.合理后角的选择原则①粗加工、断续切削、工材强度硬度高,选较小后角, 已用大负前角应↑α;②精加工取较大后角,保证表面质量;③成形、复杂、尺寸刀具取小后角;④系统刚性差,易振动,取较小后角;⑤工材塑性大取较大后角,脆材↓α(三)主偏角的选择1.主偏角的作用κr ↓→ac↓aw↑→单位刃长负荷↓→T↑刀尖强度↑散热体积↑,Ra↓Fp↑→变形↑加工精度↓,易振动→Ra↑,T↓在一定的条件下,存在一个合理值2.合理主偏角的选择原则①主要看系统刚性。
若刚性好,不易变形和振动,κr取较小值;若刚性差(细长轴),κr取较大值(90°);②考虑工件形状、切屑控制、减小冲击等,车台阶轴,取90 °;镗盲孔>90 °;κr小切屑成长螺旋屑不易断;较小κr,改善刀具切入条件,不易造成刀尖冲击。
(四)副偏角的选择副偏角的主要作用是形成已加工表面。
副偏角↓→Ra↓刀尖强度↑散热体积↑↑易振动→Ra↑,T↓副刃工作长度↑→摩擦↑Fp在一定条件下,存在一合理值。
刀具及切削参数选择
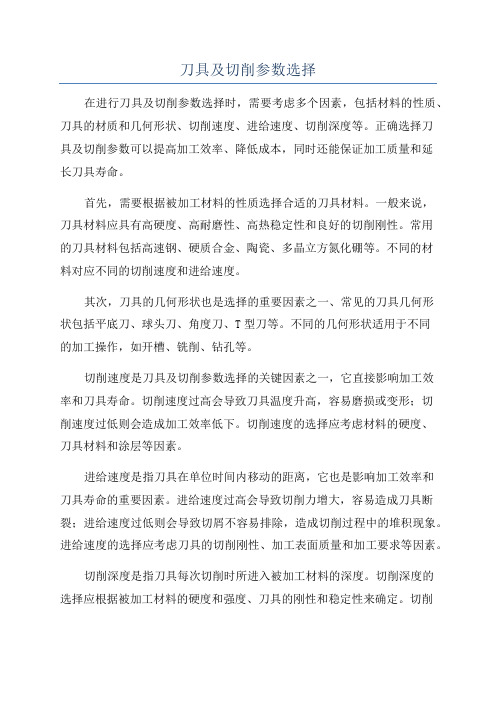
刀具及切削参数选择在进行刀具及切削参数选择时,需要考虑多个因素,包括材料的性质、刀具的材质和几何形状、切削速度、进给速度、切削深度等。
正确选择刀具及切削参数可以提高加工效率、降低成本,同时还能保证加工质量和延长刀具寿命。
首先,需要根据被加工材料的性质选择合适的刀具材料。
一般来说,刀具材料应具有高硬度、高耐磨性、高热稳定性和良好的切削刚性。
常用的刀具材料包括高速钢、硬质合金、陶瓷、多晶立方氮化硼等。
不同的材料对应不同的切削速度和进给速度。
其次,刀具的几何形状也是选择的重要因素之一、常见的刀具几何形状包括平底刀、球头刀、角度刀、T型刀等。
不同的几何形状适用于不同的加工操作,如开槽、铣削、钻孔等。
切削速度是刀具及切削参数选择的关键因素之一,它直接影响加工效率和刀具寿命。
切削速度过高会导致刀具温度升高,容易磨损或变形;切削速度过低则会造成加工效率低下。
切削速度的选择应考虑材料的硬度、刀具材料和涂层等因素。
进给速度是指刀具在单位时间内移动的距离,它也是影响加工效率和刀具寿命的重要因素。
进给速度过高会导致切削力增大,容易造成刀具断裂;进给速度过低则会导致切屑不容易排除,造成切削过程中的堆积现象。
进给速度的选择应考虑刀具的切削刚性、加工表面质量和加工要求等因素。
切削深度是指刀具每次切削时所进入被加工材料的深度。
切削深度的选择应根据被加工材料的硬度和强度、刀具的刚性和稳定性来确定。
切削深度过大会导致切削力增大,容易造成刀具断裂;切削深度过小则会导致加工效率低下。
此外,还需要考虑刀具的冷却方式和切削液的选择。
刀具在切削过程中会产生大量的热量,如果不及时冷却,会导致刀具温度过高,影响刀具寿命。
常见的冷却方式包括气体冷却、液体冷却和固体冷却等。
切削液的选择应考虑被加工材料的性质和切削过程中的润滑和冷却效果。
综上所述,刀具及切削参数选择是一个综合考虑材料性质、刀具几何形状、切削速度、进给速度、切削深度、冷却方式和切削液等多个因素的过程。
刀具及切削参数选择
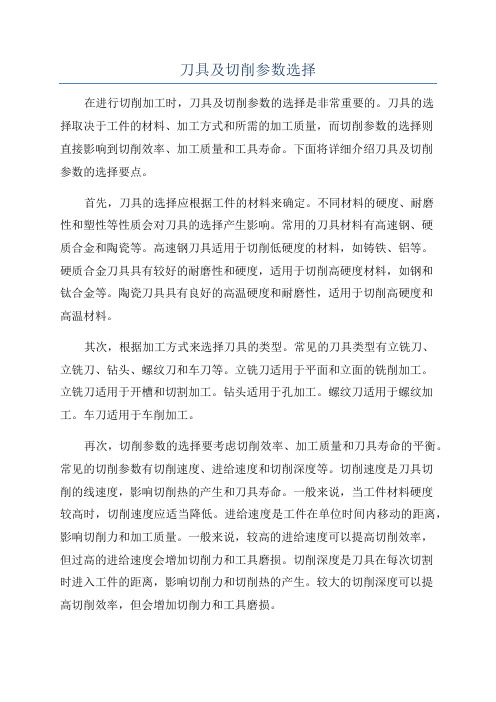
刀具及切削参数选择在进行切削加工时,刀具及切削参数的选择是非常重要的。
刀具的选择取决于工件的材料、加工方式和所需的加工质量,而切削参数的选择则直接影响到切削效率、加工质量和工具寿命。
下面将详细介绍刀具及切削参数的选择要点。
首先,刀具的选择应根据工件的材料来确定。
不同材料的硬度、耐磨性和塑性等性质会对刀具的选择产生影响。
常用的刀具材料有高速钢、硬质合金和陶瓷等。
高速钢刀具适用于切削低硬度的材料,如铸铁、铝等。
硬质合金刀具具有较好的耐磨性和硬度,适用于切削高硬度材料,如钢和钛合金等。
陶瓷刀具具有良好的高温硬度和耐磨性,适用于切削高硬度和高温材料。
其次,根据加工方式来选择刀具的类型。
常见的刀具类型有立铣刀、立铣刀、钻头、螺纹刀和车刀等。
立铣刀适用于平面和立面的铣削加工。
立铣刀适用于开槽和切割加工。
钻头适用于孔加工。
螺纹刀适用于螺纹加工。
车刀适用于车削加工。
再次,切削参数的选择要考虑切削效率、加工质量和刀具寿命的平衡。
常见的切削参数有切削速度、进给速度和切削深度等。
切削速度是刀具切削的线速度,影响切削热的产生和刀具寿命。
一般来说,当工件材料硬度较高时,切削速度应适当降低。
进给速度是工件在单位时间内移动的距离,影响切削力和加工质量。
一般来说,较高的进给速度可以提高切削效率,但过高的进给速度会增加切削力和工具磨损。
切削深度是刀具在每次切割时进入工件的距离,影响切削力和切削热的产生。
较大的切削深度可以提高切削效率,但会增加切削力和工具磨损。
此外,还应考虑冷却润滑剂的选择和使用。
合适的冷却润滑剂可以降低切削热的产生,减小工具磨损,提高加工质量。
综上所述,刀具及切削参数的选择需要考虑工件材料、加工方式和所需加工质量。
合理选择刀具类型和切削参数可以提高切削效率、加工质量和工具寿命。
在实际应用中,还需要根据具体情况进行调整和优化。
高速铣削刀具及切削参数的选择

高速铣削刀具及切削参数的选择摘要:通过等效类比的方法研究了高速铣削刀具选择的一般原则。
推导了球头铣刀的有效直径和有效线速度的计算公式,以此进一步确定转速,通过试验的方法测定了径向铣削深度和每齿进给量对表面粗糙度的影响。
关键词:高速铣削刀具;有效直径;有效线速度;切削参数;表面粗糙度作者:宋志国,宋艳,常州信息职业技术学院0 引言传统意义上的高速切削是以切削速度的高低来进行分类的,而铣削机床则是以转速的高低进行分类。
如果从切削变形的机理来看高速切削,则前一种分类比较合适;但是若从切削工艺的角度出发,则后一种更恰当。
这是因为随着主轴转速的提高,机床的结构、刀具结构、刀具装夹和机床特性都有本质上的改变。
高转速意味着高离心力,传统的7∶24锥柄,弹簧夹头、液压夹头在离心力的作用下,难以提供足够的夹持力;同时为避免切削振动要求刀具系统具有更高的动平衡精度。
高速切削的最大优势并不在于速度、进给速度提高所导致的效率提高;而是由于采用了更高的切削速度和进给速度,允许采用较小的切削用量进行切削加工。
由于切削用量的降低,切削力和切削热随之下降,工艺系统变形减小,可以避免铣削颤振。
1 刀具的选择通常选用图1所示的3种立铣刀进行铣削加工,在高速铣削中一般不推荐使用平底立铣刀。
平底立铣刀在切削时刀尖部位由于流屑干涉,切屑变形大,同时有效切削刃长度最短,导致刀尖受力大、切削温度高,导致快速磨损。
在工艺允许的条件下,尽量采用刀尖圆弧半径较大的刀具进行高速铣削。
图1 立铣刀示意图随着立铣刀刀尖圆弧半径的增加,平均切削厚度和主偏角均下降,同时刀具轴向受力增加可以充分利用机床的轴向刚度,减小刀具变形和切削振动(图2)。
图2 立铣刀受力示意图图3为高速铣削铝合金时,等铣削面积时两种刀具的铣削力对比。
刀具为直径Φ10mm的2齿整体硬质合金立铣刀,螺旋角30度。
刀尖圆弧半径为1.5mm和无刀尖圆弧的两种刀具。
图3 刀尖圆弧半径对铣削力的影响铣削面积同定为a,a p·a e=2.Omm2。
机床刀具的正确选择与使用方法
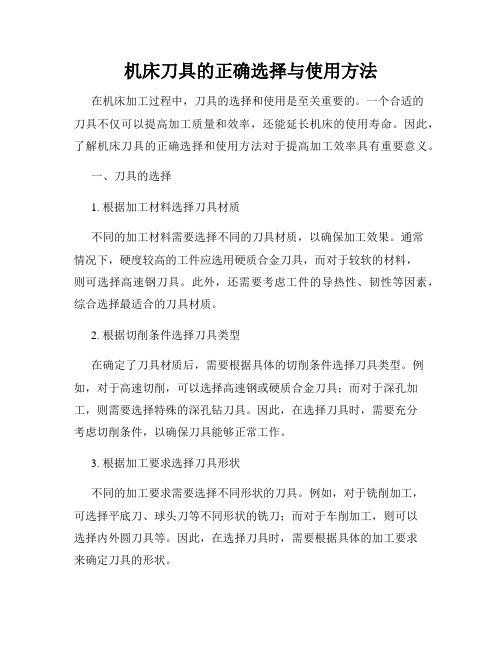
机床刀具的正确选择与使用方法在机床加工过程中,刀具的选择和使用是至关重要的。
一个合适的刀具不仅可以提高加工质量和效率,还能延长机床的使用寿命。
因此,了解机床刀具的正确选择和使用方法对于提高加工效率具有重要意义。
一、刀具的选择1. 根据加工材料选择刀具材质不同的加工材料需要选择不同的刀具材质,以确保加工效果。
通常情况下,硬度较高的工件应选用硬质合金刀具,而对于较软的材料,则可选择高速钢刀具。
此外,还需要考虑工件的导热性、韧性等因素,综合选择最适合的刀具材质。
2. 根据切削条件选择刀具类型在确定了刀具材质后,需要根据具体的切削条件选择刀具类型。
例如,对于高速切削,可以选择高速钢或硬质合金刀具;而对于深孔加工,则需要选择特殊的深孔钻刀具。
因此,在选择刀具时,需要充分考虑切削条件,以确保刀具能够正常工作。
3. 根据加工要求选择刀具形状不同的加工要求需要选择不同形状的刀具。
例如,对于铣削加工,可选择平底刀、球头刀等不同形状的铣刀;而对于车削加工,则可以选择内外圆刀具等。
因此,在选择刀具时,需要根据具体的加工要求来确定刀具的形状。
二、刀具的使用方法1. 切勿超负荷使用刀具刀具在工作时会受到一定的负荷,如果超负荷使用,容易导致刀具磨损过快甚至断裂。
因此,在使用刀具时,需要根据切削条件合理设置切削参数,避免超负荷使用刀具。
2. 定期检查刀具状态刀具在使用过程中会出现磨损,因此需要定期检查刀具状态。
一旦发现刀具磨损严重或者出现其他异常情况,应及时更换或修磨刀具,以确保刀具的正常使用。
3. 注意刀具的保养刀具在使用过程中需要定期进行清洁和保养,以延长刀具的使用寿命。
在清洁时,应使用专用清洁剂擦拭刀具表面,防止刀具受到腐蚀。
同时,在使用完毕后,应将刀具储存在干燥通风的环境中,避免受潮生锈。
总结:正确选择和使用机床刀具对于提高加工效率和质量具有重要意义。
通过根据加工材料选择刀具材质、根据切削条件选择刀具类型、根据加工要求选择刀具形状等方法,能够有效提高刀具的使用效率和寿命。
切削参数的选择
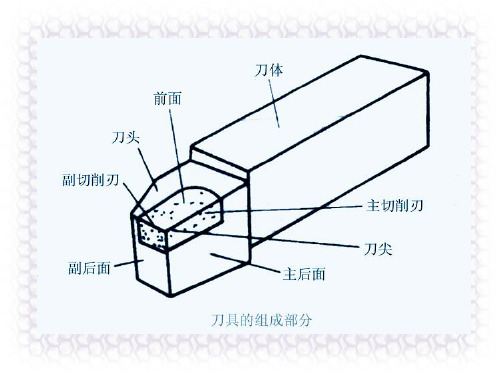
刃。
课堂问题?
2、正交平面参考系各参考面的概念? 基面pr、切削平面ps、正交平面po
❖正交平面参考系时各参考面 : ❖ 基面pr——过切削刃选定点平行或垂直刀
具安装面(或轴线)的平面。 ❖ 切削平面ps——过切削刃选定点与切削
刃相切并垂直于基面的平面。 ❖ 正交平面po——过切削刃选定点同时垂
直于切削平面和基面的平面。
课堂问题?
3、车刀各刀具角度的概念? 前副角偏γ角o、κrˊ后、角刃α倾o、角主λs偏角κr 、
❖ 前角γo——在主切削刃选定点的正交平面 po内,前刀面与基面之间的夹角。
❖ 后角αo——在正交平面po内,主后刀面与 切削平面之间的夹角。
❖ 主偏角κr——主切削刃在基面上的投影与进 给方向的夹角。
❖ 正交平面参考系时各 参考面 :(右图)
❖ 基面pr——过切削刃选 定点平行或垂直刀具安 装面(或轴线)的平面。
❖ 切削平面ps——过切削 刃选定点与切削刃相切 并垂直于基面的平面。
❖ 正交平面po——过切削 刃选定点同时垂直于切 削平面和基面的平面。
正交平面参考系
❖ 对于法平面参考系:
❖ 则由pr、ps、pn三平面组成,其中:
❖ 刀具前角的合理选择,主要由刀具材 料和工件材料的种类与性质决定。
❖ ① 刀具材料
❖ 强度和韧性大的刀具材料可以选择大的前角,而脆性 大的刀具甚至取负的前角。
❖ 下图是不同刀具材料韧性的变化
立方氮化硼刀具 陶瓷刀具 硬质合金刀具
高速钢刀具
❖ ② 工件材料
刀具韧性增强,前角取大
❖ 加工钢件等塑性材料时,切屑沿前刀面流出时和前刀
❖ 刀具几何参数的合理选择:是指在保证加工质量 的前提下,选择能提高切削效率,降低生产成本, 获得最高刀具耐用度的刀具几何参数。
刀具几何参数的合理选择
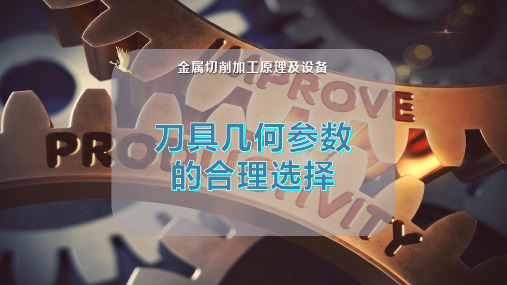
刀具几何参数的合理选择
刀具的几何参数主要包括:刀具角度、前面与后面型式、 切削刃与刃口形状等。
刀具合理几何参数——是指在保证加工质量的前提下, 能够获得最高的刀具寿命,从而达到提高生产效率、降低生 产成本的刀具几何参数。
1.1前角和前面型式的选择
1.前角的选择 增大前角,切削刃锋利,切削变形减小、切削力减小、 切削温度降低、刀具磨损减小、加工表面质量提高。但若前 角过大,刀具刚度和强度降低,散热条件变差,切削温度高, 刀具易磨损或破损,刀具寿命低。总结正、反两方面的影响, 前角应有一个最佳值。 选择前角的原则:“固中求锐”。 (1)按工件材料选—— 切塑性材料时,应选较大前角; 切脆性材料,宜选较小前角。材料强度和硬度越高,前角越 小,有时甚至取负值。 (2)按刀具材料选——高速钢刀具材料的抗弯强度、抗 冲击韧性高,可选取较大的前角;硬质合金材料的抗弯强度 较低、脆性大,故前角应小些;陶瓷刀具材料的强度和韧性 更低、脆性更大,故前角应更小些。
2.根据加工材料选择
加工高强度、高硬度钢时, 为保证刃口强度,应选择较小的 后角;加工塑性材料时宜选择较 大的后角;加工脆性材料时,则 宜选择较小的后角。
1.根据加工精度选择
精加工时,切削用量较小,为了减小摩擦,保证加工表 面质量,宜选择较大的后角;粗加工、强力切削或断续切 削时,为提高刀具强度,后角应较小些。
1.根据加工要求选择——精加工选正值,粗加工选 负值;微量精车、精镗、精刨时,采用大刃倾角 切削。
刃 2.根据工件材料选择——车高硬度、高强度材料时,
倾
取较大的负刃倾角;车削铸铁件时, 择 原
3.根据加工条件选择——切削断续表面、余量不均 匀表面或带冲击振动的切削条件下,通常取负的
如何选择刀具和切削参数
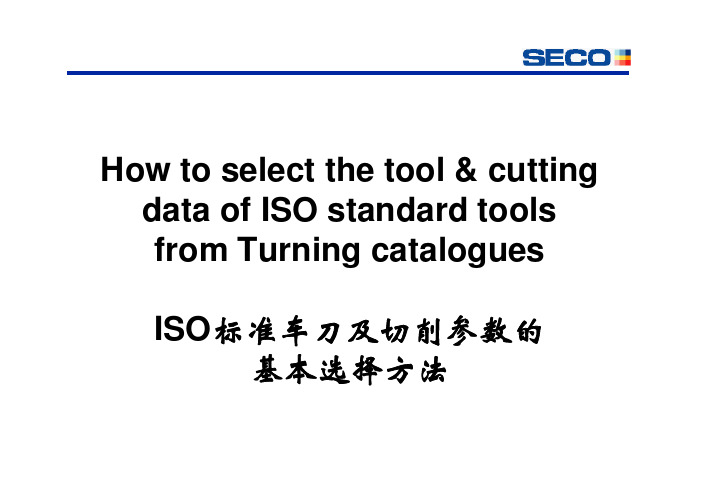
205
6:依切削参数的优化 • 根据刚才选择的刀片,您可以很方便地选得适用的切削参数推荐值。 线速度Vc=200m/min,每齿进给fz=0.25mm/z,因为刀盘直径我们已 经知道是D=100mm,所以转速N=636rpm,刀盘齿数为Z=7,所以实 际的工作进给量F=636*7*0.25=1110mm/min。 实际每转的进给量为Fr=7*0.25=1.75mm>1.5mm的修光刃实际有效 宽度,所以可以预计加工的光洁度不是很好,要提高光洁度您认为应 该采用什么措施? 正确的办法应该是加用修光刃刀片而不是简单地降低每齿进给量。
Plunging Plunging 插铣 插铣
3:确定最适合的首选刀片 • 如我们以加工45钢为例,即山高第4组材料,根据被加工材料在样本的 相应组别中您可以非常容易地找到首选刀片的推荐。 XOMX090308TR-ME06 T350M
4:您也可以在样本中了解 到有关刀盘的其它信息
• 这些信息包括: 刀盘的有效工作直径、杆式 刀的柄直径、刀盘高度、齿 数、重量、盘式刀盘安装孔 径、备用板手、适用的刀柄 规格、安全最大切深等等。
1:确定被加工工件的材料组别 • 依据国际ISO标准的规定,常见的 工件材料被分为六类: 钢件类(P类)--山高组别1-6 不锈钢类(M类)--山高组别7-11 铸铁类(K类)--山高组别12-15 有色金属类(N类)--山高组别16-17 耐热合金类(S类)--山高组别20-22 淬硬钢类(H类)--山高组别7 我们最常用的45号钢为第3 组材料,不 锈钢( 316 )属于第9组材料,铸铁HT25 ( GG25 )属于第12组, 铝合金属于第 16组,钛合金( Ti6Al4V )属于20组,镍 基合金( 718 )属于第22组。
机械制造基础:刀具及切削参数选用
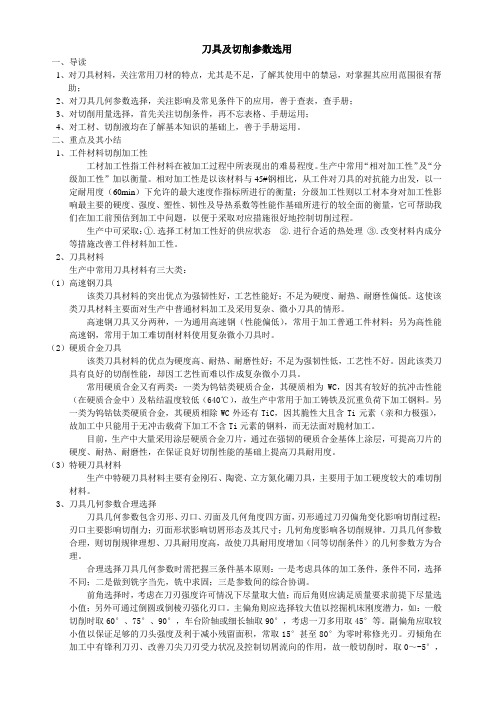
刀具及切削参数选用一、导读1、对刀具材料,关注常用刀材的特点,尤其是不足,了解其使用中的禁忌,对掌握其应用范围很有帮助;2、对刀具几何参数选择,关注影响及常见条件下的应用,善于查表,查手册;3、对切削用量选择,首先关注切削条件,再不忘表格、手册运用;4、对工材、切削液均在了解基本知识的基础上,善于手册运用。
二、重点及其小结1、工件材料切削加工性工材加工性指工件材料在被加工过程中所表现出的难易程度。
生产中常用“相对加工性”及“分级加工性”加以衡量。
相对加工性是以该材料与45#钢相比,从工件对刀具的对抗能力出发,以一定耐用度(60min)下允许的最大速度作指标所进行的衡量;分级加工性则以工材本身对加工性影响最主要的硬度、强度、塑性、韧性及导热系数等性能作基础所进行的较全面的衡量,它可帮助我们在加工前预估到加工中问题,以便于采取对应措施很好地控制切削过程。
生产中可采取:①.选择工材加工性好的供应状态②.进行合适的热处理③.改变材料内成分等措施改善工件材料加工性。
2、刀具材料生产中常用刀具材料有三大类:(1)高速钢刀具该类刀具材料的突出优点为强韧性好,工艺性能好;不足为硬度、耐热、耐磨性偏低。
这使该类刀具材料主要面对生产中普通材料加工及采用复杂、微小刀具的情形。
高速钢刀具又分两种,一为通用高速钢(性能偏低),常用于加工普通工件材料;另为高性能高速钢,常用于加工难切削材料使用复杂微小刀具时。
(2)硬质合金刀具该类刀具材料的优点为硬度高、耐热、耐磨性好;不足为强韧性低,工艺性不好。
因此该类刀具有良好的切削性能,却因工艺性而难以作成复杂微小刀具。
常用硬质合金又有两类:一类为钨钴类硬质合金,其硬质相为WC,因其有较好的抗冲击性能(在硬质合金中)及粘结温度较低(640℃),故生产中常用于加工铸铁及沉重负荷下加工钢料。
另一类为钨钴钛类硬质合金,其硬质相除WC外还有TiC,因其脆性大且含Ti元素(亲和力极强),故加工中只能用于无冲击载荷下加工不含Ti元素的钢料,而无法面对脆材加工。
切削过程具备的条件
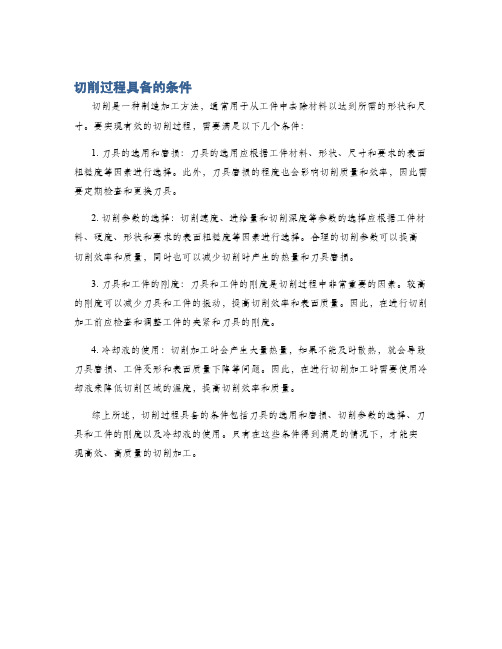
切削过程具备的条件
切削是一种制造加工方法,通常用于从工件中去除材料以达到所需的形状和尺寸。
要实现有效的切削过程,需要满足以下几个条件:
1. 刀具的选用和磨损:刀具的选用应根据工件材料、形状、尺寸和要求的表面粗糙度等因素进行选择。
此外,刀具磨损的程度也会影响切削质量和效率,因此需要定期检查和更换刀具。
2. 切削参数的选择:切削速度、进给量和切削深度等参数的选择应根据工件材料、硬度、形状和要求的表面粗糙度等因素进行选择。
合理的切削参数可以提高切削效率和质量,同时也可以减少切削时产生的热量和刀具磨损。
3. 刀具和工件的刚度:刀具和工件的刚度是切削过程中非常重要的因素。
较高的刚度可以减少刀具和工件的振动,提高切削效率和表面质量。
因此,在进行切削加工前应检查和调整工件的夹紧和刀具的刚度。
4. 冷却液的使用:切削加工时会产生大量热量,如果不能及时散热,就会导致刀具磨损、工件变形和表面质量下降等问题。
因此,在进行切削加工时需要使用冷却液来降低切削区域的温度,提高切削效率和质量。
综上所述,切削过程具备的条件包括刀具的选用和磨损、切削参数的选择、刀具和工件的刚度以及冷却液的使用。
只有在这些条件得到满足的情况下,才能实现高效、高质量的切削加工。
切削参数的选用原则
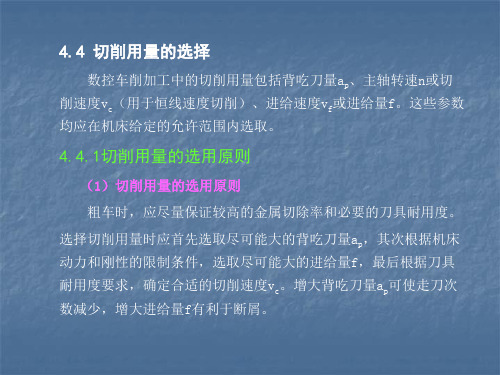
图4-29
切宽槽的走刀路线
小结:1. 数控车削切削用量的选择原则、方法及主要问题
2. 数控车削工序划分和加工顺序安排 3. 确定走刀路线的原则
4. 数控车床常用的走刀路线
作业:
1. 数控车削切削用量的选择原则、方法及主要问题 2. 数控车床常用的走刀路线分析
表4-3 硬质合金刀具切削用量推荐表
粗 加 工 刀具 材料 工件材料 切削速度 (m/min) 220 180 120 80 80 40 120 100 1600 进给量 (mm/r) 0.2 背吃刀量 mm 3 切削速度 (m/min) 260 精 加 工 进给量 (mm/r) 0.l 背吃刀量 mm 0.4 0.4 0.4 0.4 0.4 0.4 0.5 0.5 0.5
圆柱面及圆锥面(粗车掉R42mm圆弧的部分余量),换刀后按总长
要求留下加工余量,然后切断。 第二道工序(见图4-20(c)),用Φ 12mm外圆及Φ 20mm端面
装夹,工序内容有:先车削包络SR7mm球面的30º圆锥面,然后对全
部圆弧表面半精车(留少量精车余量),最后换精车刀将全部圆弧 表面一刀精车成形。
程。
确定走刀路线的总原则:在保证零件加工精度和表面质量的前 提下,尽量缩短走刀路线,以提高生产率;方便坐标值计算,减少
编程工作量,便于编程。对于多次重复的走刀路线,应编写子程序,
简化编程。
数控车床上加工零件时常用的走刀路线: (1)车圆弧的走刀路线分析 实际车圆弧时,需要多刀加工,先将大部分余量切除,最后才 车出所需圆弧。下面介绍车圆弧常用的加工路线。
粗加工
精加工 钻中心孔
2-3
2-6
80~120
120~150 500~800r· -1 min
刀具几何参数与切削用量的合理选择

切削热
合理的刀具几何参数和切 削用量可以降低切削热, 减少因热变形对加工精度 的影响,提高加工效率。
04 实际应用案例分析
案例一
总结词
根据工件材料和加工要求,选择合适的刀具几何参数和切削用量,提高加工效率和表面 质量。
详细描述
在车削加工中,刀具的几何参数如前角、后角和刃倾角对切削力和切削热有显著影响。 前角增大,切削力减小,切削热增加;后角增大,切削热减少,但切削力可能增大。选 择合适的切削用量,如切削速度、进给量和切削深度,可以优化加工效率和表面质量。
刀具主副偏角
主副偏角的大小影响切削层的形状和切削宽度。减小主副 偏角,可减小切削层的截面积,降低切削力,但刀尖强度 减弱。
切削用量对加工质量的影响
1 2
切削速度
切削速度过高可能导致工件表面粗糙度增加或产 生积屑瘤;切削速度过低则可能使切削力增大, 导致刀具磨损。
进给量
进给量过大会导致切削力增大,工件表面粗糙度 增加;进给量过小则可能影响加工效率。
案例四
总结词
根据工件材料、磨料和加工要求,选择合适的刀具几何参数和切削用量,以提高磨削效率和表面质量。
详细描述
在磨削加工中,刀具的几何参数如磨料粒度、结合剂硬度对磨削效率和表面质量有重要影响。磨料粒度越细,表 面粗糙度越低;结合剂硬度越高,磨粒越稳定。选择合适的切削用量,如磨削深度、磨削速度和进给速度,可以 优化磨削效率和表面质量。
谢谢聆听
进给量过小可能导致加 工效率低下,过大则可 能导致加工表面质量下 降。
切削深度的合理选择
01
切削深度影响切削力、切削热和 刀具寿命。
02
选择合适的切削深度可以降低切 削力,减少热量产生,提高刀具
加工中刀具的选择与切削用量的确定

加工中刀具的选择与切削用量的确定在加工过程中,刀具的选择和切削用量的确定是非常重要的。
正确选择合适的刀具和确定合理的切削用量,可以提高加工效率、保证产品质量、延长刀具寿命,降低加工成本。
下面将从加工材料、切削参数和刀具选择等方面探讨加工中刀具的选择与切削用量的确定。
一、加工材料对刀具选择和切削用量的影响在加工过程中,加工材料是选择刀具和确定切削用量的重要依据。
加工材料的硬度、韧性、热导率等性质直接影响了刀具的选择和切削用量的确定。
1. 硬度:对于硬度较高的材料,如钢材,通常需要采用更硬的刀具,例如硬质合金刀具或陶瓷刀具。
同时,由于硬度高的材料切削时容易产生热量,因此需要相应地增加切削用量,以提高切削效率。
2. 韧性:对于韧性较好的材料,如铸铁,切削时容易产生切削力和切削温度较高。
因此,选择耐磨性好、抗冲击性好的刀具,以提高切削质量和刀具寿命。
3. 热导率:热导率高的材料在切削过程中很容易导致刀具温度的升高,因此需要针对这些材料采取相应的散热措施,例如降低切削用量、增加切削冷却液的喷射量等。
二、切削参数对刀具选择和切削用量的影响除了加工材料之外,切削参数也是选择刀具和确定切削用量的重要参考依据。
切削速度、进给量和切削深度等参数的选择直接影响了切削过程的质量和效率。
1. 切削速度:切削速度是切削工件单位时间内通过刀具的线速度。
切削速度的选择取决于刀具材料和工件材料等因素。
对于硬度较高的材料,切削速度较低;而对于韧性较好的材料,切削速度较高。
正确选择切削速度可以保证刀具和工件的寿命。
2. 进给量:进给量是刀具每转一周(或每行进一定距离)切削工件的材料数量。
进给量的选择与刀具的负荷和工件的表面质量有关。
过大的进给量容易导致切削力过大,影响刀具寿命;而过小的进给量则会降低切削效率。
3. 切削深度:切削深度是刀具在单位时间内切削工件的材料厚度。
切削深度的选择取决于工件的材料和加工要求等因素。
较大的切削深度可以提高切削效率,但也会增加切削力和切削温度,影响刀具的使用寿命。
切削参数的选择
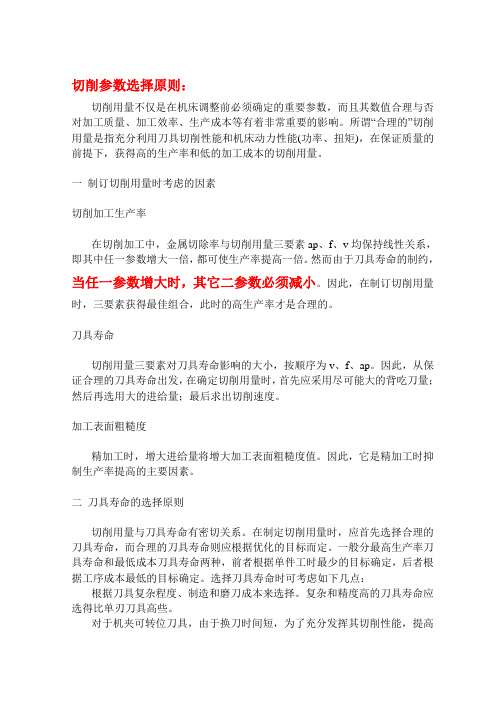
切削参数选择原则:切削用量不仅是在机床调整前必须确定的重要参数,而且其数值合理与否对加工质量、加工效率、生产成本等有着非常重要的影响。
所谓“合理的”切削用量是指充分利用刀具切削性能和机床动力性能(功率、扭矩),在保证质量的前提下,获得高的生产率和低的加工成本的切削用量。
一制订切削用量时考虑的因素切削加工生产率在切削加工中,金属切除率与切削用量三要素ap、f、v均保持线性关系,即其中任一参数增大一倍,都可使生产率提高一倍。
然而由于刀具寿命的制约,当任一参数增大时,其它二参数必须减小。
因此,在制订切削用量时,三要素获得最佳组合,此时的高生产率才是合理的。
刀具寿命切削用量三要素对刀具寿命影响的大小,按顺序为v、f、ap。
因此,从保证合理的刀具寿命出发,在确定切削用量时,首先应采用尽可能大的背吃刀量;然后再选用大的进给量;最后求出切削速度。
加工表面粗糙度精加工时,增大进给量将增大加工表面粗糙度值。
因此,它是精加工时抑制生产率提高的主要因素。
二刀具寿命的选择原则切削用量与刀具寿命有密切关系。
在制定切削用量时,应首先选择合理的刀具寿命,而合理的刀具寿命则应根据优化的目标而定。
一般分最高生产率刀具寿命和最低成本刀具寿命两种,前者根据单件工时最少的目标确定,后者根据工序成本最低的目标确定。
选择刀具寿命时可考虑如下几点:根据刀具复杂程度、制造和磨刀成本来选择。
复杂和精度高的刀具寿命应选得比单刃刀具高些。
对于机夹可转位刀具,由于换刀时间短,为了充分发挥其切削性能,提高生产效率,刀具寿命可选得低些,一般取15-30min。
对于装刀、换刀和调刀比较复杂的多刀机床、组合机床与自动化加工刀具,刀具寿命应选得高些,尤应保证刀具可靠性。
车间内某一工序的生产率限制了整个车间的生产率的提高时,该工序的刀具寿命要选得低些;当某工序单位时间内所分担到的全厂开支M较大时,刀具寿命也应选得低些。
大件精加工时,为保证至少完成一次走刀,避免切削时中途换刀,刀具寿命应按零件精度和表面粗糙度来确定。
切削参数的选择范文

切削参数的选择范文切削参数的选择在机械加工过程中起着至关重要的作用,它直接影响到加工表面的精度、表面质量、加工效率和切削工具的寿命。
正确选择合适的切削参数,能够提高机械加工的质量和效率,降低加工成本。
本文将从不同的角度,详细介绍切削参数的选择。
首先,切削速度是影响切削过程的重要参数之一、切削速度过高容易导致切削温度升高,切削力增大,刀具磨损严重;切削速度过低,则会增加切削时间,降低生产效率。
因此,选择合理的切削速度十分重要。
切削速度的选择需要考虑材料的硬度、切削加工的稳定性以及切削液的能力等因素。
一般来说,对于不同的材料,可以根据经验选择切削速度的范围,并进行试切实验,掌握最佳的切削速度。
其次,进给量是另一个影响切削过程的重要参数。
进给量过大容易导致切削力增大,切削震动,刀具磨损加剧;进给量过小会增加切削时间,降低加工效率。
因此,选择合适的进给量也是非常重要的。
进给量的选择需要根据切削深度、切削宽度、切削力以及切削液的能力来确定。
通常情况下,进给量与切削深度和刀具直径有关,可以根据经验选择合适的进给量,并进行试切实验来确定最佳的进给量。
还有,切削深度也是影响切削过程的重要参数之一、切削深度过大容易导致切削力增大,产生严重的振动和噪音,刀具容易折断;切削深度过小则会增加切削时间,降低加工效率。
因此,选择合适的切削深度同样十分重要。
切削深度的选择需要综合考虑材料的硬度、刀具的刚度和刚度等因素。
一般来说,切削深度和刀具直径有关,可以根据经验选择合适的切削深度,并进行试切实验来确定最佳的切削深度。
此外,切削液的选择也对切削过程产生影响。
切削液可以降低切削温度,减少切削力,延长刀具寿命,提高加工表面的质量。
根据切削液的类型和性能,可以选择合适的切削液。
切削液的选择需要考虑切削材料的特性,切削液的润滑性能和冷却能力等因素。
不同的切削液适用于不同的材料和工艺,选择合适的切削液可以提高加工质量和效率。
最后,要选择适当的刀具和刀具材料。
刀具使用寿命的名词解释

刀具使用寿命的名词解释刀具使用寿命是指刀具在特定条件下能够保持其原有性能和功能的时间。
它是衡量刀具质量和性能的重要指标,也是制造业和加工业中不可忽视的重要要素。
刀具使用寿命的长短直接影响着生产效率、产品质量和成本控制。
一、刀具初次磨刃使用寿命刀具初次磨刃使用寿命也被称为原始刀具寿命,指的是刀具在其初始使用阶段中,能够保持其预期性能和功能的时间。
这一时期的刀具使用寿命通常较长,因为刀具的刃口初始状态较好,磨削边缘清晰锋利,能够有效地完成各种加工任务。
二、刀具寿命的延长方式1. 应用适当的切削参数:合理选择切削速度、进给速度和切削深度,根据材料和加工要求进行调整。
过高的切削速度和进给速度会增加刀具的磨损和损坏风险,过大的切削深度会受到刀具强度和刚性的限制。
2. 选择高品质的刀具材料:刀具材料的选择对刀具寿命有着重要的影响。
高硬度、高韧性和耐磨损的刀具材料能够提供更长的使用寿命。
3. 采用适当的润滑和冷却方式:合理的冷却润滑可以降低刀具的温度,减少磨损和蠕动,提高切削质量和效率。
4. 定期检查和维护刀具:定期检查刀具的磨损和损坏程度,并及时进行维护或更换。
及时更换磨损严重的刀具可以避免切削质量下降和工件受损。
5. 合理存储和保养刀具:刀具在不使用时应存放在干燥、通风的地方,避免接触湿度过高的环境。
在存放和使用时,应注意防护和避免碰撞,以免刀具表面受损。
三、刀具寿命的检测和评价1. 刀具磨损检测:刀具磨损是刀具使用寿命到达一定程度时常见的现象,通常通过观察刃口磨损程度来判断。
常用的方法包括目测法、测量法和光学法。
2. 刀具失效检测:刀具失效是指刀具在使用过程中由于磨损、破损或疲劳等原因导致无法继续使用的情况。
刀具失效通常通过观察刀具表面破损、刃口出现断裂等现象来判断。
3. 刀具寿命评价:刀具寿命的评价主要包括切削时间、产量、切削质量和成本等指标。
通过综合考虑这些指标可以得出刀具的实际寿命和效率。
四、刀具寿命的影响因素1. 材料属性:切削材料的硬度、韧性和切削性能等因素会直接影响刀具的磨损和损坏情况。
- 1、下载文档前请自行甄别文档内容的完整性,平台不提供额外的编辑、内容补充、找答案等附加服务。
- 2、"仅部分预览"的文档,不可在线预览部分如存在完整性等问题,可反馈申请退款(可完整预览的文档不适用该条件!)。
- 3、如文档侵犯您的权益,请联系客服反馈,我们会尽快为您处理(人工客服工作时间:9:00-18:30)。
半精加工: 从φ40mm到φ36mm ,故ap=2mm,由查表 得f=0.3~0.6(mm/r), 取f=0.4,保证Ra=3.2,速度V=50~100m/min, 取v=80m/min,确定主轴转速: ns=1000*v/πd=1000x80/3.14x40=636r/min,从机床 主轴箱查得n为600,, v实=75.36m/min
切削用量大,生热多,,用离子型切 削液或3%-5%乳化液 。 切削液主要作用是减小工件表面粗糙 度值用10%~15%乳化液,采用喷雾法。
精加工
粗加工
组员:
王涛 潘洋 彭峰 宾杰 于浩然 唐超军
刘贝 张雕 何鹏云 周文强 张晓明 侯金鸽
等 级 代号
3
3
1
0
4
4
:优质碳素结构钢,硬度不高,易于切削。
选用硬质合金钢YT类,高速钢性能没有硬 质合金钢好,并且不能用于高速切削。 粗车YT5 精车YT15
r0
a0
a0'
Kr
Kr'ຫໍສະໝຸດ 入s粗加工10
5
5
90
8
-5
精加工
15
8
8
90
5
5
粗车刀图
精车刀图
车床选C6140
粗车 1.选择切削深度:由粗加工从φ48mm到φ40mm,知单边 余量为4mm,故ap =4mm。 2.选择进给量:由查表得f=0.3~0.6(mm/r)。取 f=0.4mm/r。 3.选择切削速度:V=90~110m/s。取v=100m/min , 主轴 转速:ns=1000*v/πd=663r/mm.从机床上查得主转速 n=600r/min, v=nπd,v实=3.14*600*48*10^3=90.432m/min
查表得:单位切削力:Kc=1962(kgf/mm^2) , Kfp=0.96 , KVBFc=1.09 主切削力: Pc=Kc*ap*f*KFc=1962x4x0.4x1.09x0.96=3284.9(N) 切削功率: Pm=Pc*Vc/60000=3284.9x90.432=4.951(kw) 由机床说明书知,C6140机床主电动机功率为7.5kw,取 机床效率为0.8,则: Pm/0.8=4.951/0.8=6.18875(kw)〈PE 机床功率够用,也够半精加工。
要求:
用45钢加工长150mm的台阶轴外
圆,粗加工从Ф48mm到Ф40mm, 半 精加工达Ф36mm,Ra达3.2.
45钢
力学性能:
硬度 <HB> 抗拉强度 延展率% (mpa)
冲 击 韧 相对加 性J 工性Kr
导热系 数 ( W/m* p)
50.2
数值
229(未 处理)
600
16
39
1