带螺纹塑件的脱模机构
机动脱螺纹注塑模结构讲解
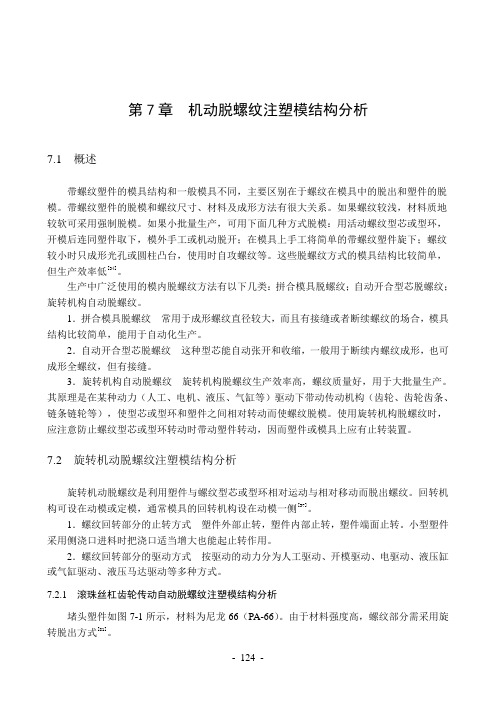
第7章机动脱螺纹注塑模结构分析7.1 概述带螺纹塑件的模具结构和一般模具不同,主要区别在于螺纹在模具中的脱出和塑件的脱模。
带螺纹塑件的脱模和螺纹尺寸、材料及成形方法有很大关系。
如果螺纹较浅,材料质地较软可采用强制脱模。
如果小批量生产,可用下面几种方式脱模:用活动螺纹型芯或型环,开模后连同塑件取下,模外手工或机动脱开;在模具上手工将简单的带螺纹塑件旋下;螺纹较小时只成形光孔或圆柱凸台,使用时自攻螺纹等。
这些脱螺纹方式的模具结构比较简单,但生产效率低[34]。
生产中广泛使用的模内脱螺纹方法有以下几类:拼合模具脱螺纹;自动开合型芯脱螺纹;旋转机构自动脱螺纹。
1.拼合模具脱螺纹常用于成形螺纹直径较大,而且有接缝或者断续螺纹的场合,模具结构比较简单,能用于自动化生产。
2.自动开合型芯脱螺纹这种型芯能自动张开和收缩,一般用于断续内螺纹成形,也可成形全螺纹,但有接缝。
3.旋转机构自动脱螺纹旋转机构脱螺纹生产效率高,螺纹质量好,用于大批量生产。
其原理是在某种动力(人工、电机、液压、气缸等)驱动下带动传动机构(齿轮、齿轮齿条、链条链轮等),使型芯或型环和塑件之间相对转动而使螺纹脱模。
使用旋转机构脱螺纹时,应注意防止螺纹型芯或型环转动时带动塑件转动,因而塑件或模具上应有止转装置。
7.2 旋转机动脱螺纹注塑模结构分析旋转机动脱螺纹是利用塑件与螺纹型芯或型环相对运动与相对移动而脱出螺纹。
回转机构可设在动模或定模,通常模具的回转机构设在动模一侧[37]。
1.螺纹回转部分的止转方式塑件外部止转,塑件内部止转,塑件端面止转。
小型塑件采用侧浇口进料时把浇口适当增大也能起止转作用。
2.螺纹回转部分的驱动方式按驱动的动力分为人工驱动、开模驱动、电驱动、液压缸或气缸驱动、液压马达驱动等多种方式。
7.2.1 滚珠丝杠齿轮传动自动脱螺纹注塑模结构分析堵头塑件如图7-1所示,材料为尼龙66(PA-66)。
由于材料强度高,螺纹部分需采用旋转脱出方式[81]。
注塑模具设计结构篇--注塑模脱模系统的设计培训

29
30
31
4.推块脱模机构 对于端面平直的无孔塑件,或仅带有小孔的塑件,为保证塑件在模具打开 时能留到动模一侧,一般都把型腔安排在动模一侧,如果塑件表面不希望留下 推杆痕迹,必须采用推块机构推推塑件,如图4-86所示。对于齿轮类或一些带 有凸缘的制品,如果采用推杆推出容易变形或者是采用推板推出容易使制品粘 附模具时,也需采用推块作为推出零件。推动推块的推杆如果用螺纹连接在推 块上,则复位杆可以与推杆安装在同一块固定板上,如图4-86(a)所示。如果 推块与推杆无螺纹连接,必须采用图4-86(b)所示的复位方法。推块实际上成 为型腔底板或构成形腔底面大部分,推件运动的配合间隙既要小于溢料间隙, 又不产生过大的摩擦磨损,这就对配合面间的加工,特别是非圆形推块的配合 面提出很高要求,常常要在装配时研磨。
一次推出机构 塑件在推出零件的作用下,通过一次推出动作,就能将塑件全部脱出。 这种类型的脱模机构即为一次推出机构,也称为简单脱模机构。它是最常见 的,也是应用最广的一种脱模机构。一般有以下几种形式。
8
1.推杆脱模机构 (1) 机构组成和动作原理 推杆脱模是最典型的一次推出机构,它结构简单,制造容易且维修方便, 其机构组成和动作原理如图4-76所示。它是由推杆1、推杆固定板2、推板导套 3、推板导柱4、推杆垫板5、拉料杆6、复位杆7和限位钉8等所组成的。推杆、 拉料杆、复位杆都装在推杆固定板2上,然后用螺钉将推杆固定板和推杆垫板 连接固定成一个整体,当模具打开并达到一定距离后,注塑机上的机床推杆将 模具的推出机构挡住,使其停止随动模一起的移动,而动模部分还在继续移动 后退,于是塑件连同浇注系统一起从动模中脱出。合模时,复位杆首先与定模 分型面相接触,使推出机构与动模产生相反方向的相对移动。模具完全闭合后, 推出机构便回复到了初始的位置(由限位钉8保证最终停止位置)。
注塑内螺纹直接脱模结构设计方案

注塑内螺纹直接脱模结构设计方案一、整体思路。
咱们得想个办法,让带有内螺纹的塑料制品在注塑完后,能轻松地从模具里脱模,就像从被窝里钻出来一样容易,而且还不能把这个螺纹给搞坏喽。
二、具体结构设计。
1. 螺纹型芯部分。
首先呢,这个螺纹型芯不能是个死脑筋的结构。
咱们可以把它设计成两段式的。
就像火车有车头和车厢一样。
靠近模具型腔内部的那一段螺纹型芯,咱们可以让它稍微细一点,就像小一号的螺丝。
这一段的螺纹是完整的,用来成型产品的内螺纹。
然后外面再套上一段粗一点的“外套”,这个外套和里面的细螺纹型芯之间要有一定的间隙,这个间隙就像两个好朋友之间保持的小距离,不能太大也不能太小,大概在0.1 0.3毫米左右就行。
这个间隙是为了让里面的细型芯在脱模的时候有活动的空间。
2. 脱模动力装置。
为了让螺纹型芯能从产品里退出来,咱们得给它一个动力呀。
这时候可以在模具上安装一个小型的液压或者气动装置。
想象一下,这个装置就像一个小助手,在脱模的时候轻轻地推一下螺纹型芯。
不过这个推力得控制好,不能太猛,不然会把产品给弄坏的。
一般来说,根据产品的大小和材料的特性,这个推力在50 200牛顿之间比较合适。
另外,还可以在螺纹型芯上连接一个旋转机构。
这个旋转机构就像一个小陀螺,在液压或者气动装置推动螺纹型芯往外退的同时,让它慢慢地旋转。
因为内螺纹嘛,要是光直直地往外退,肯定会卡住的,就像你硬要把拧进去的螺丝直接拔出来一样困难。
这个旋转的速度也不能太快,每分钟大概转个5 10圈就差不多了。
3. 导向和限位结构。
在螺纹型芯的周围,要设置一些导向柱。
这些导向柱就像轨道一样,让螺纹型芯在脱模的时候只能按照规定的方向移动。
就像火车只能在铁轨上跑一样。
导向柱的表面要光滑得像溜冰场一样,这样可以减少摩擦,保证螺纹型芯移动得顺畅。
同时呢,还要有限位装置。
这个限位装置就像一个小警察,告诉螺纹型芯你只能移动到这个位置,不能再往前走了。
这样可以防止螺纹型芯过度脱模,把模具或者产品给损坏了。
螺纹脱模
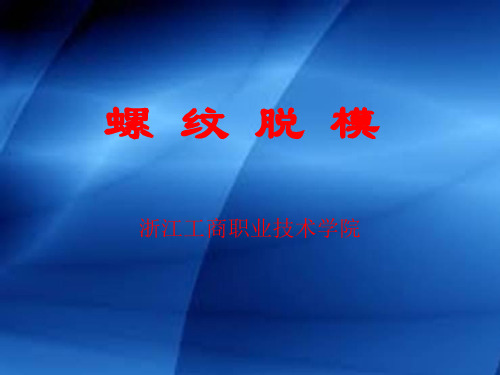
1) 对塑件的要求:由于螺纹表面有沟槽,所以,内螺纹必须 对塑件的要求:由于螺纹表面有沟槽,所以, 由螺纹型芯, 外螺纹必须由螺纹型环成型,而脱模时必 由螺纹型芯, 外螺纹必须由螺纹型环成型, 须从螺纹型芯或螺纹型环上脱出, 须从螺纹型芯或螺纹型环上脱出,两者之间必须作相对转 因此,塑件的外形或端面须有防止转动的花纹或图案, 动,因此,塑件的外形或端面须有防止转动的花纹或图案, 否则难以脱出。 否则难以脱出。 2) 对模具的要求:塑件不能转动,模具应有相应的防转措施 对模具的要求:塑件不能转动, 给予保证。当塑件型腔和螺纹型芯同在动模上时, 给予保证。当塑件型腔和螺纹型芯同在动模上时,型腔可 以保证不使塑件转动。但当型芯和型腔分别处在动、 以保证不使塑件转动。但当型芯和型腔分别处在动、定模 上时,开模后,塑件就离开定模型腔,此时, 上时,开模后,塑件就离开定模型腔,此时,即使塑件外 形有防转花纹也不起作用, 形有防转花纹也不起作用,塑件会留在动模型芯上和它一 起转动而无法脱模,因此在模具上要另设止转机构。 起转动而无法脱模,因此在模具上要另设止转机构。
螺 纹 脱 模
浙江工商职业技术学院
塑件螺纹
很多塑件上带有螺纹, 很多塑件上带有螺纹,螺紋的种类主 要有两大类:内螺纹和外螺纹。 要有两大类:内螺纹和外螺纹。螺纹表面 均带沟槽, 均带沟槽,因此脱模的方式与一般塑件不 它需要有特殊的脱模机构。 同。它需要有特殊的脱模机构。
设计螺纹脱模机构的注意点
设计带螺纹塑件的脱模机构应注意的问题
螺纹脱模方式
带螺纹塑件的脱模方式
对带螺纹塑件的脱模方式主要有以下几种。 对带螺纹塑件的脱模方式主要有以下几种。 1) 手动脱螺纹,这是在塑件成型、开模后,用 手动脱螺纹,这是在塑件成型、开模后, 手工或简单工具将型芯或型环从塑件上旋出。这 手工或简单工具将型芯或型环从塑件上旋出。 类模具的结构简单,易于制造,但劳动强度大, 类模具的结构简单,易于制造,但劳动强度大, 生产效率低。 生产效率低。 2) 强制脱螺纹,这是利用塑件的弹性或型芯的 强制脱螺纹, 弹性,使塑件或型芯与螺纹产生轴向移动, 弹性,使塑件或型芯与螺纹产生轴向移动,强行 将型芯或塑件拉离螺纹而脱模。这类模具结构也 将型芯或塑件拉离螺纹而脱模。 较简单,主要用于螺纹精度要求不高, 较简单,主要用于螺纹精度要求不高,螺紋形状 比较容易脱出的塑件。 比较容易脱出的塑件。
精密螺纹脱模机构

精密内螺纹的脱模方法摘要:本文主要就汽车发动机冷却系统螺纹机构的脱模方式进行探讨,并根据实际生产过程所遇到的问题提出最佳解决方案。
关键字:发动机、冷却系统、脱螺纹机构、2D 、3D汽车发动机冷却水室的经典结构1、汽车发动机冷却水室3D 图及关键位置的2D 图详细2、汽车发动机冷却水室的经典结构的功能分析。
2.1、A 部为下水室的出水口,正常工作时用放水螺塞密封。
螺纹为内螺纹,规格为M14*2.0,螺纹有效长度为12.8mm 。
所以该处必须有脱螺纹机构以及滑块机构,以便螺纹脱模和冷却水通道孔脱模。
同时必须要注意的是螺纹孔需要密封性能很好,所以注塑出来的螺纹尺寸规格必须合格并且尺寸稳定,不能有过大的波动。
冷却水通道侧面有一个φ4mm 的溢水孔,因而螺纹孔的有效长度要准确,若过长则会导致螺塞密封时会封堵住溢水孔,发生机能故障。
3、汽车发动机冷却水室的经典结构的设计方案可行性分析。
3.1、脱螺纹机构设计方案的可行性分析及最终设计方案3.1.1、自动脱螺纹机构的分类3.1.1.1、按动作方式分:①螺纹型芯转动,托板推动产品脱离;②螺纹型芯转动同时后退,产品自然脱离。
3.1.1.2按驱动方式分图1:螺纹机构3D 图 图2:螺纹机构2D 图①油缸+齿条②油马达/电机+链条③齿条+锥度齿轮④来福线螺母螺纹模具要有防转机构保证其定向。
当制品的型腔与螺纹型芯同时设计在动模时,型腔就可以保证不使制品转动,但当型腔不可能与螺纹型芯同时设计在动模时,模具开模后,制品就离开了定模型腔,此时即使制品外形有防转的花纹,也不起作用,塑件会留在螺纹型芯上与之一起运动,变不能脱模,因此,在设计模具时要考虑止转机构的合理设置,比如采用端面止转等方法。
3.1.2、自动脱螺纹机构的动力来源自动脱螺纹机构中的螺纹型芯在开模时或开模后,一面旋转一面将塑件从模具中脱出。
螺纹型芯旋转的动力来源如下:3.1.2.1马达:用变速马达带动齿轮,齿轮再带动螺纹型芯,实现内螺纹脱模。
塑料模具课件_脱模机构
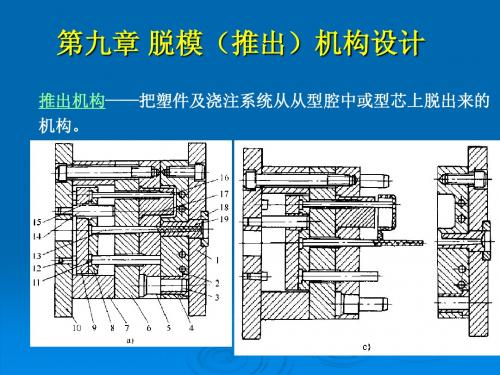
3.模内旋转的脱模方式
(1)螺纹塑件的止转形式
模具设自动脱螺纹机构时塑件外形有止转结构,通常为花纹。
常用模内旋转脱螺纹机构主要有手动脱螺纹和机动脱螺 纹两种。
(2) 手动脱螺纹机构
(3) 机动脱螺纹机构
原理:利用开模时的直线运动,通过齿轮齿条的运动,使 螺纹型芯作回转运动而脱离塑件。 图为,锥齿轮脱螺纹型 芯结构,它用于侧浇口多 型腔模,螺纹型芯只要作 回转运动就可脱出塑件。
p—因塑件收缩对型芯产生的单位正压力(12~20MPa) A—塑件包紧型芯的侧面积(mm2)
F脱= pA(f·cosα-sinα)
总脱模力等于F总=F脱+F大气(大气压力影响:引气、不引气) 以上对脱模力的计算是一种比较粗略的方法。 计算脱模力是为了校核设备的顶出力是否足够,以及校核推出 元件的刚度强度及可靠性。
为减少脱模过程中推件板与型芯之间的摩擦,两者之间留有0.2~ 0.25mm的间隙,并采用锥面配合,以防止推件板 偏斜溢料,锥面 的斜度约取3~5˚左右,图 (b)。
引气装置: 对于大型深腔薄壁容器,推板脱模时 塑件部易形成真空, 使脱模困难,甚至还会使塑件变形或损坏,应在凸模上附设引 气装置,如图(推件板引气)。(推件板不引气)
加粗,增加刚性。
顶盘式推杆:锥面推杆,推出面积较大,适合于深筒形塑件 推出。
b)
c)
d)
2.推杆的固定及配合
(1)推杆的固定
2.推杆的配合
推杆固定板上的孔为d+1mm;推杆台阶部分的直径为
d+5mm;推杆固定板上的台阶孔为d+6mm。推杆与固定 板配合长度为S(一般采用H8/f8配合)
S 可取12~15mm;当d>5mm时, S=(2~3)d (d为推杆直径),配合部分表面Ra=0.8μm。 推杆与塑料接触并与孔经常摩擦,因此多采用热处理后硬度 高的材料制作。推杆材料常用T8A、T10A等碳素工具钢 (50 ~ 54HRC自制推杆)或65Mn (46 ~ 50HRC市场上的 推杆标准件)
塑件螺纹脱模机构设计注意事项
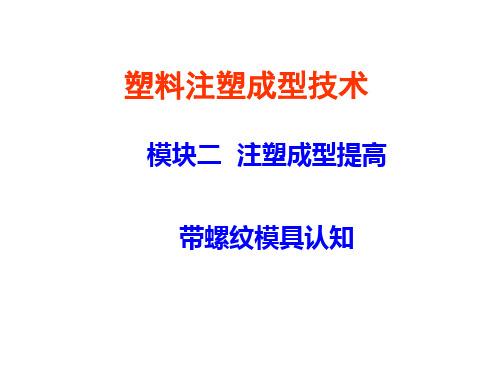
塑件螺纹的脱模方式
②用硅橡胶作螺纹型芯强制脱模 图(a),开模时,在弹簧作用下芯杆l先从硅橡胶螺纹型芯4 中退出,使硅橡胶收缩,再用推杆将塑件推出,(b)。该 因硅橡胶寿命低,仅用于小批量生产。
常用的模具钢材
1.碳素结构钢 45、45Mn、20Mn 有一定强度,切削性能好,热处理变形较大 加工前要正火或调质处理 2.碳素工具钢 T8、T8A、T10、T10A 淬火后有较高的强度与耐磨性,淬火变形大且淬透性 差 淬火后用线切割加工可达较高精度 淬透性、强度、韧性、耐磨性、耐热性好,但加工性 能差,粗加工前要退火处理。
常用的模具钢材
3.合金工具钢 CrWMn:淬火变形很小,淬透性高 9Mn2V:价格低,淬透性、耐磨性不及CrWMn但比T10钢好 Cr12:淬火变形很小、淬透性高、耐磨性 Cr4W2MoV:淬透性、耐磨性不及Cr12,其它性能接近 5CrNiMo:500℃能保持高强度与高韧性 3Cr2W8V:适合氮化处理,耐蚀性好 4.合金结构钢 热处理前具有较好切削性能,热处理后变形小。 20CrMnTi:淬透性、力学性能较高,用于尺寸大的渗碳淬硬件。 40Cr:综合性能很好,但国内Cr资源有限。 40CrMnMo:淬透性、力学性能高,用于强度高韧性好的大截面件。 38CrMoAl:渗氮钢,高硬度、高耐磨性和耐蚀性,尺寸稳定性好。 30CrMnSi:淬透性、强韧性好,用于截面不大而力学性能好的零 件。
塑件螺纹的脱模方式
齿轮轴上加工大升角螺纹,
螺纹脱模结构

螺纹脱模结构
螺纹脱模结构通常用于从模具中取出带有内螺纹的塑件。
以下是一些常见的螺纹脱模结构:
1. 顶出杆:顶出杆可以穿过模具的顶出孔,并插入到塑件的内螺纹中。
当顶出杆被推出时,它会将塑件从模具中带出。
2. 旋钮:旋钮通常用于小型塑件的内螺纹脱模。
它可以通过旋转的方式将塑件从模具中带出。
3. 斜滑块:斜滑块是一种特殊的脱模结构,它可以将塑件从模具中沿着斜向推出。
这种结构通常用于大型塑件的内螺纹脱模。
4. 气动脱模:气动脱模利用气压将塑件从模具中推出。
这种结构适用于自动化生产,可以提高生产效率。
5. 液压脱模:液压脱模利用液压油将塑件从模具中推出。
这种结构适用于大型塑件的内螺纹脱模。
无论选择哪种脱模结构,都需要根据具体的塑件形状、尺寸和生产要求进行选择和设计。
同时,还需要考虑到模具的制造难度和成本等因素。
生产效率低。带螺纹塑件的脱模二
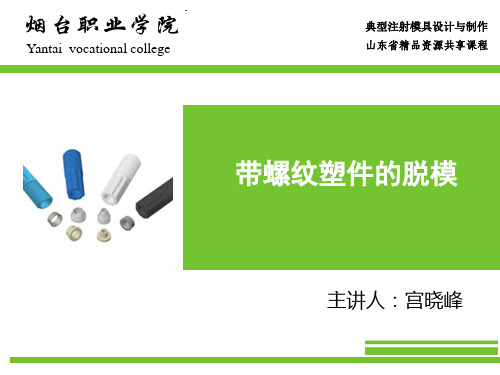
2.利用开合模丝杠脱螺纹的机构
当采用直角式注射机时,可利用 其上开合模丝杠来传递运动。
带螺纹塑件的脱模
带螺纹塑件的脱模
三、机动脱模
3.利用外部动力脱螺纹的机构 用外加液压缸带动齿条侧向运动,使齿轮型芯转动,其行程较大。
带螺纹塑件的脱模
四、拼合型芯或型环脱模方式 (分型抽芯的方式)
• 采用斜滑块或斜导杆的侧向分型或抽芯的方式:外螺纹脱模采用斜滑块 外侧分型;内螺纹脱模采用斜滑块内侧抽芯。
• 特点:脱螺纹机构结构简单、可靠,但在塑件螺纹上存在着分型线。
二、手动脱模
1、模内手动脱螺纹机构
塑件成型后,需先用专用 工具将螺纹型芯脱出,然后再 由推出机构将塑件脱模。
特点:该机构结构简单, 但劳动强度大,生产效率低。
带螺纹塑件的脱模
二、手动脱模 2、带增力齿轮副的模内手动脱螺纹
塑件成型后,摇动与斜齿 轮6相连的手柄,由斜齿轮6 带动斜齿轮5旋转,使螺纹型 芯边旋转边后退,使其从塑件 脱出。
Yantai vocational college
典型注射模具设计与制作 山东省精品资源共享课程
带螺纹塑件的脱模
主讲人:宫晓峰
带螺纹塑件的脱模
带螺纹塑件脱模方式
强制脱模
利用塑件的弹性脱螺纹 利用硅橡胶螺纹型芯脱螺纹
手动脱模 机动脱模
简易手动脱螺纹机构 齿轮副模内手动脱螺纹
齿轮齿条脱螺纹机构 直角注射机脱螺纹机构 推杆轴承旋转式脱出机构
带螺纹塑件的脱模
一、强制脱螺纹 1、利用塑件的弹性脱螺纹
用于制品螺纹的精度要求不高的场合,且螺纹的端面最好 为圆弧形。利用塑料的韧性强制脱螺纹。
带螺纹塑件的脱模
一、强制脱螺纹 2、利用硅橡胶螺纹型芯脱螺纹
浇注系统凝料推出机构

塑料制品成型及模具设计•教学内容4.7.8浇注系统凝料的脱出机构4.7.9 带螺纹塑件的脱模机构•教学目的掌握点浇口式浇注系统凝料的脱出机构和带螺纹塑件的脱模机构的特点、结构、运动原理,了解旋转脱螺纹所需扭矩与功率的计算。
•重点点浇口式浇注系统凝料的脱出机构和带螺纹塑件的脱模机构的特点、结构、运动原理•难点点浇口式浇注系统凝料的脱出机构和带螺纹塑件的脱模机构的特点、结构、运动原理课时:24.7 脱模机构设计4.7.8浇注系统凝料的脱出机构一般来说,普通浇注系统多数是单分型面的二板模具,而点浇口、潜伏式浇口多是双分型面的三板模具。
4.7.8.1 普通浇注系统凝料的脱出机构通常采用侧浇口、直接浇口及盘环形浇口类型的模具,其浇注系统凝料一般与塑件连在一起。
塑件脱出时,先用拉料杆拉住冷料穴,使浇注系统留在动模一侧,然后用推杆或拉料杆推出,靠其自重而脱落。
4.7.8.2 点浇口式浇注系统凝料的脱出机构(1)利用推杆拉断点浇口凝料:如图4-79所示,开模时模具首先沿A-A面分开,流道凝料被带出定模座板8,当限位钉1对推板2限位后,推杆4及推杆5共同将浇注系统凝料推出。
(2)利用侧凹拉断点浇口凝料:分流道末端钻一小斜孔,开模时确保模具先由A-A面分开,点浇口被拉断,流道凝料被中心拉料杆9蜡像型腔板一侧,当限位钉6其作用后,动模与定模型腔板5分开即B-B 分型,中心拉料杆随之失去作用,流道凝料便自动脱落,如图4-80所示。
图4-79 利用推杆拉断点浇口图4-80 利用推杆拉断点浇口图4-81为侧凹拉断点浇口的另一种形式,分流道末端做成斜面,开模时,由于弹簧6的作用,模具首先从A-A面分型,点浇口被拉断,同时拉料杆相对于型芯固定板1移动l距离,继续开模时,型芯固定板1碰到拉料杆2的台阶,拉料杆2则将主流道凝料脱出,随后型腔板(中间板)3将流道凝料从拉料杆2上推出并自动脱落。
图4-81 利用侧凹拉断点浇口的另一种形式(3)利用拉料杆拉断点浇口凝料:如图4-82所示,图4-82(a)为闭模状态,图4-82(b)为开模状态。
螺纹脱模
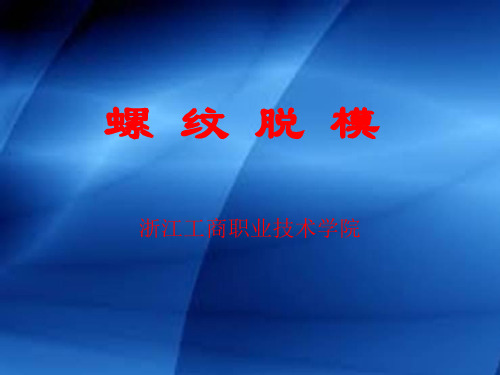
浙江工商职业技术学院
塑件螺纹
很多塑件上带有螺纹, 很多塑件上带有螺纹,螺紋的种类主 要有两大类:内螺纹和外螺纹。 要有两大类:内螺纹和外螺纹。螺纹表面 均带沟槽, 均带沟槽,因此脱模的方式与一般塑件不 它需要有特殊的脱模机构。 同。它需要有特殊的脱模机构。
设计螺纹脱模机构的注意点
设计带螺纹塑件的脱模机构应注意的问题
1) 对塑件的要求:由于螺纹表面有沟槽,所以,内螺纹必须 对塑件的要求:由于螺纹表面有沟槽,所以, 由螺纹型芯, 外螺纹必须由螺纹型环成型,而脱模时必 由螺纹型芯, 外螺纹必须由螺纹型环成型, 须从螺纹型芯或螺纹型环上脱出, 须从螺纹型芯或螺纹型环上脱出,两者之间必须作相对转 因此,塑件的外形或端面须有防止转动的花纹或图案, 动,因此,塑件的外形或端面须有防止转动的花纹或图案, 否则难以脱出。 否则难以脱出。 2) 对模具的要求:塑件不能转动,模具应有相应的防转措施 对模具的要求:塑件不能转动, 给予保证。当塑件型腔和螺纹型芯同在动模上时, 给予保证。当塑件型腔和螺纹型芯同在动模上时,型腔可 以保证不使塑件转动。但当型芯和型腔分别处在动、 以保证不使塑件转动。但当型芯和型腔分别处在动、定模 上时,开模后,塑件就离开定模型腔,此时, 上时,开模后,塑件就离开定模型腔,此时,即使塑件外 形有防转花纹也不起作用, 形有防转花纹也不起作用,塑件会留在动模型芯上和它一 起转动而无法脱模,因此在模具上要另设止转机构。 起转动而无法脱模,因此在模具上要另设止转机构。
带螺纹塑件的脱模
强制脱螺纹
带螺纹塑件的脱模 内侧抽脱螺纹
带螺纹塑件的脱模 螺纹止动
带螺纹塑件的脱模
模内旋转脱螺纹
带螺纹塑件螺纹或外 螺纹的塑件, 螺纹的塑件,为了能 自动卸螺纹在模具内 设有能转动的螺纹型 芯或螺纹型环。 芯或螺纹型环。
带螺纹塑件的脱模机构

带螺纹塑件的脱模机构通常,塑件的内螺纹由螺纹型芯成型,外螺纹由螺纹型环成型,由于螺纹具有侧向凹沟槽,所以带螺纹的塑件需要特殊的脱模机构,即螺纹型芯、型环的脱出机构。
带螺纹塑件的顶出方式可分为三种:强制脱螺纹、活动螺纹型芯与螺纹型环带出脱模、塑件或模具的螺纹部分回转脱模。
1 .强制脱螺纹这种模具结构简单,通常用于精度要求不高的塑件。
( l )利用塑件的弹性强制脱模。
对于聚乙烯、聚丙烯等具有较好弹性的塑件,可采用推件板将塑件从螺纹型芯上强制脱出,如图4 一112 ( a )、(b )所示。
但应避免如图4 一112 (c)所示的圆弧端面作为推动塑件的接触面,否则塑件脱模困难。
( 2 )利用硅橡胶螺纹型芯的弹性强制脱模。
图4 一113 所示为利用硅橡胶螺纹型芯的弹性强制脱模结构。
开模时,由于弹簧的作用,首先退出橡胶螺纹型芯中的芯杆,使橡胶螺纹型芯产生收缩,再在推杆的作用下将塑件推出。
该模具结构简单,但硅橡胶螺纹型芯的寿命短,只适于小批量生产。
2 .活动螺纹型芯与螺纹型环带出脱模当模具不能设计成瓣合模具,或回转脱螺纹结构太复杂时,可将螺纹部分做成活动型芯或型环,随塑件一起脱模,在模外与塑件脱离。
这种模具结构简单,但需要数个螺纹型芯或型环交替使用,并需要预热装置及机外取芯装置。
图4 一114 ( a )所示的螺纹型芯随塑件顶出后,由电动机带动螺纹型芯尾部相配合的四方套筒,使螺纹型芯脱出塑件。
图4 一114 ( b )所示为手动脱螺纹型环形式,当塑件的外螺纹尺寸精度要求较高,不能采用组合螺纹型环时,可用此结构。
开模后螺纹型环随塑件顶出,用专用工具插入螺纹型环的孔,脱出塑件;若将专用工具装于电动机上,则可提高生产效率。
3 .螺纹部分回转的脱模方式这是利用塑件与螺纹型芯或型环相对转动与相对移动脱出螺纹的方式。
回转机构可设在动模或定模上,通常模具的回转机构设在动模一侧。
1 )设计拐纹郎分回转脱模机构的注愈事项(1)对塑件的要求。
- 1、下载文档前请自行甄别文档内容的完整性,平台不提供额外的编辑、内容补充、找答案等附加服务。
- 2、"仅部分预览"的文档,不可在线预览部分如存在完整性等问题,可反馈申请退款(可完整预览的文档不适用该条件!)。
- 3、如文档侵犯您的权益,请联系客服反馈,我们会尽快为您处理(人工客服工作时间:9:00-18:30)。
带螺纹塑件的脱模机构
通常,塑件的内螺纹由螺纹型芯成型,外螺纹由螺纹型环成型,由于螺纹具有侧向凹沟槽,所以带螺纹的塑件需要特殊的脱模机构,即螺纹型芯、型环的脱出机构。
带螺纹塑件的顶出方式可分为三种:强制脱螺纹、活动螺纹型芯与螺纹型环带出脱模、塑件或模具的螺纹部分回转脱模。
1 .强制脱螺纹
这种模具结构简单,通常用于精度要求不高的塑件。
( l )利用塑件的弹性强制脱模。
对于聚乙烯、聚丙烯等具有较好弹性的塑件,可采用推件板将塑件从螺纹型芯上强制脱出,如图4 一112 ( a )、(b )所示。
但应避免如图4 一112 (c)所示的圆弧端面作为推动塑件的接触面,否则塑件脱模困难。
( 2 )利用硅橡胶螺纹型芯的弹性强制脱模。
图4 一113 所示为利用硅橡胶螺纹型芯的弹性强制脱模结构。
开模时,由于弹簧的作用,首先退出橡胶螺纹型芯中的芯杆,使橡胶螺纹型芯产生收缩,再在推杆的作用下将塑件推出。
该模具结构简单,但硅橡胶螺纹型芯的寿命短,只适于小批量生产。
2 .活动螺纹型芯与螺纹型环带出脱模
当模具不能设计成瓣合模具,或回转脱螺纹结构太复杂时,可将螺纹部分做成活动型芯或型环,随塑件一起脱模,在模外与塑件脱离。
这种模具结构简单,但需要数个螺纹型芯或型环交替使用,并需要预热装置及机外取芯装置。
图4 一114 ( a )所示的螺纹型芯随塑件顶出后,由电动机带动螺纹型芯尾部相配合的四方套筒,使螺纹型芯脱出塑件。
图4 一114 ( b )所示为手动脱螺纹型环形式,当塑件的外螺纹尺寸精度要求较高,不能采用组合螺纹型环时,可用此结构。
开模后螺纹型环随塑件顶出,用专用工具插入螺纹型环的孔,脱出塑件;若将专用工具装于电动机上,则可提高生产效率。
3 .螺纹部分回转的脱模方式
这是利用塑件与螺纹型芯或型环相对转动与相对移动脱出螺纹的方式。
回转机构可设在动模或定模上,通常模具的回转机构设在动模一侧。
1 )设计拐纹郎分回转脱模机构的注愈事项
(1)对塑件的要求。
塑件成型后,要从螺纹型芯或螺纹型环上脱出,两者必须作相对运动,为此塑件的外形或端面需有防止转动的措施,否则难以脱出。
为了达到这个目的,塑件的外形或端面需有防止转动的花纹或图案。
( 2 )对模具的要求。
塑件要求止转,模具就要有相应防转机构来保证。
当塑件的型腔与螺纹型芯同时设计在动模上时,型腔就可以保证不使塑件转动。
但是,当型腔不可能与螺纹型芯同时设计在动模上,如型腔在定模,螺纹型芯在动模时,模具开模后,塑件就离开定模型腔,此时,即使塑件外形上有防转的花纹也不起作用,塑件会留在动模型芯上和它一起转动,不能脱模,因此在设计模具时应考虑止转机构。
2 )娘纹回转部分的止转方式
( 1)塑件外部止转。
图4 一115 所示为塑件外部有止转,内部有螺纹的情况。
图4 一115 ( a )所示为外点浇口的情况,型腔在定模,螺纹型芯在动模,螺纹型芯回转使塑件脱出的形式。
图4 一115 ( b )所示为内点浇口的塑件,是型腔在动模,使动模上的塑件回转而脱离螺纹型芯的形
式.这两种脱螺纹形式不使用脱模机构,但在设计时需注意,螺纹型芯与塑件应保留必要的螺扣数(一般为一扣左右),塑件再脱离型腔。
图4 一116 所示为塑件有止转部分的型腔和螺纹型芯同时处于动模的情况,当止转部分长度H 和螺纹部分长度h 相等时,回转结束,塑件可自动落下;当H > h 时,如图4 一116 所示,则要用推杆将塑件顶出型腔。
( 2 )塑件内部止转。
图4 一117 所示为内螺纹塑件在内顶部平面有止转的情况,止转型芯回转并沿轴向移动,使塑件脱离螺纹型芯,设计时需注意,止转型芯上螺纹的螺距和塑件上螺纹
的螺距必须一致,并且塑件脱离螺纹型芯后,顶部平面还和止转型芯连接着,要实现自动脱模还必须考虑其他顶出方法。
图4 一118 所示是外螺纹塑件在内侧有止转的情况,型芯回转带动塑件回转并沿轴向移动,使塑件脱离型腔,再在推杆作用下使塑件脱离型芯。
图4 一119 所示是内螺纹塑件在内侧有止转的情况,型芯回转使螺纹脱开,然后由推件板顶出。
图4 一119 ( a )所示是以推杆将推件板顶起,图4 一119 ( b )所示是使用弹获将推件板顶起。
( 3 )塑件端面止转。
图4 一120 所示是塑件的端面有止转的例子,通过螺纹型芯的回转,推板推动塑件沿轴向移动,使塑件脱离螺纹型芯,再在推杆的作用下使塑件脱离推件板。
小型塑件使用侧浇口时,当螺纹部分脱模后,如果不顶出塑件只顶出浇注系统,也能使之完全脱离型腔,即使塑件的外形不设止转,把浇口适当增大也能起止转作用,但是对于软性塑料浇口,若不够大,则有切断的危险。
3 )娘纹回转邻分的驱动方式
按驱动的动力分为人工驱动、开模运动、电驱动、液压缸或气缸驱动、液压马达等多种方式。
( l )人工驱动。
在设计时必须注意螺纹型芯的非成型端的螺距要与成型端的螺距相等。
如果不等,在脱出螺纹型芯时会将塑件损坏。
图4 一121 所示为模内装有变向机构的手动脱出螺纹型芯的模具机构,当人工摇动螺旋齿轮2 时,与它啮合的斜齿轮3 通过滑键8 的作用使螺纹型芯5 旋转。
由于螺纹型芯凸台处的螺距与成型螺距相等,螺纹型芯旋转的同时相对于塑件向左移动,直到完全脱出塑件内的螺纹部分为止。
当螺纹型芯上的台肩移至A 面,手柄无法继续摇动,然后开启塑模从I 处分型,用推杆(图中未画出)带动推件板4 使塑件脱模,推出距离由定距螺钉7 限制。
( 2 )利用开模运动脱出螺纹。
利用开模时的直线运动,通过齿条齿轮或是丝杆的传动,使螺纹型芯作回转运动而脱离塑件。
螺纹型芯可一边回转一边移动来脱离塑件,也可只作回转运动脱离塑件,还可以通过大升角的丝杆螺母使螺纹型芯回转而脱离塑件。
下面分别介绍。
① 一边回转一边作往复运动。
图4 一122 所示为脱出侧向螺纹型芯的例子。
开模时,齿条导柱1 带动螺纹型芯4 旋转并沿套简螺母3 进行轴向移动,套筒螺母3 与螺纹型芯4 配合处螺纹的螺距应与塑件成型螺距一致,且螺纹型芯上的齿轮宽度应保证在左右移动到两端点时能与齿条导柱的齿形啮合。
图4 一123 所示是多型腔的模具利用开模力退出螺纹型芯的例子.它是通过齿条齿轮来实现一边回转一边自身往复运动的。
② 大升角的丝杠螺母使螺纹型芯回转。
图4 一124 所示是在行星齿轮轴上加工出图示的大升角螺杆5 ,与它配合的固定螺母6 是固定不动的。
开模时,动模4 移动,带动大升角螺杆5 转动,通过大升角螺杆5 使齿轮3 转动而带动螺纹型芯2 转动。
③ 只作回转运动。
对于侧浇口多型腔塑件,螺纹型芯只作回转运动就可以脱出塑件。
如图
4 一12
5 所示,由于螺纹型芯和螺纹拉料钩的旋转方向相反,所以螺纹拉钩需做成反牙螺纹。
( 3 )其他动力源。
图4 一126 所示,是靠液压缸2 (或汽缸)给齿条3 以往复运动,通过齿轮4 使螺纹型芯1 回转的。
图4 一127 所示是靠电动机5 和蜗轮2 、蜗杆1 使螺纹型芯3 回转的。
用液动、气动或电动机为动力源时,都需要控制装置,一般电动机多用于螺纹扣数较多的情况。
4 .脱出螺纹塑件所需扭矩和功率的计算
1 )螺纹塑件产生的包紧力
在螺纹塑件的成型过程中,当浇口冻结,补料停止后,由于塑料熔体冷却收缩,使塑件紧紧包围在螺纹型芯上,形成旋出螺纹型芯阻力,此阻力以扭矩的形式出现。
研究表明,包紧力与塑件厚度有密切关系,为此,将螺纹塑件分为薄壁与厚壁两种情况计算。
( 1 )薄壁螺纹塑件的包紧力。
薄壁螺纹塑件是指t / dm 簇l / 20 的塑件,t 是塑件厚度,mm ; dm 是螺纹中径,mm 。
( 2 )厚壁螺纹塑件的包紧力。
2 )旋出娘纹塑件所需扭矩
螺纹塑件包紧在型芯上,旋出时必须克服包紧力所形成的摩擦扭矩。
3 )旋出娘纹塑件所需功率
作者:汽车模具 。