焊接空心球对接焊缝超声波探伤技术
焊接球节点钢网架焊缝超声波探伤及质量分级法
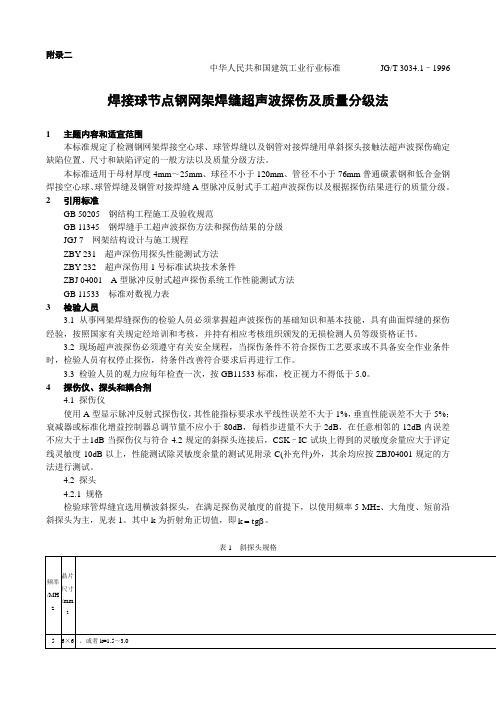
附录二中华人民共和国建筑工业行业标准JG/T 3034.1–1996 焊接球节点钢网架焊缝超声波探伤及质量分级法1 主题内容和适宜范围本标准规定了检测钢网架焊接空心球、球管焊缝以及钢管对接焊缝用单斜探头接触法超声波探伤确定缺陷位置、尺寸和缺陷评定的一般方法以及质量分级方法。
本标准适用于母材厚度4mm~25mm、球径不小于120mm、管径不小于76mm普通碳素钢和低合金钢焊接空心球、球管焊缝及钢管对接焊缝A型脉冲反射式手工超声波探伤以及根据探伤结果进行的质量分级。
2 引用标准GB 50205 钢结构工程施工及验收规范GB 11345 钢焊缝手工超声波探伤方法和探伤结果的分级JGJ 7 网架结构设计与施工规程ZBY 231 超声深伤用探头性能测试方法ZBY 232 超声深伤用1号标准试块技术条件ZBJ 04001 A型脉冲反射式超声探伤系统工作性能测试方法GB 11533 标准对数视力表3 检验人员3.1 从事网架焊缝探伤的检验人员必须掌握超声波探伤的基础知识和基本技能,具有曲面焊缝的探伤经验,按照国家有关规定经培训和考核,并持有相应考核组织颁发的无损检测人员等级资格证书。
3.2 现场超声波探伤必须遵守有关安全规程,当探伤条件不符合探伤工艺要求或不具备安全作业条件时,检验人员有权停止探伤,待条件改善符合要求后再进行工作。
3.3 检验人员的观力应每年检查一次,按GB11533标准,校正视力不得低于5.0。
4 探伤仪、探头和耦合剂4.1 探伤仪使用A型显示脉冲反射式探伤仪,其性能指标要求水平线性误差不大于1%,垂直性能误差不大于5%;衰减器或标准化增益控制器总调节量不应小于80dB,每档步进量不大于2dB,在任意相邻的12dB内误差不应大于±1dB当探伤仪与符合4.2规定的斜探头连接后,CSK–IC试块上得到的灵敏度余量应大于评定线灵敏度10dB以上,性能测试除灵敏度余量的测试见附录C(补充件)外,其余均应按ZBJ04001规定的方法进行测试。
超声波焊缝探伤操作简述

返回
仪器的调校
3)、重复2项操作,依次记录20mm、30mm、40mm、50mm等由 )、重复2项操作,依次记录20mm、30mm、40mm、50mm等由 浅到深的孔的回波,在记录完成所需回波参考点后,一组 DAC曲线制作完成。 DAC曲线制作完成。 4)、按GB11345标准B级,在(DAC主菜单)将评定线、定量 )、按GB11345标准B级,在(DAC主菜单)将评定线、定量 线、判废线分别设定为: DAC-16dB” 线、判废线分别设定为:“DAC-16dB”、“DAC-10dB”、 DAC-10dB” “DAC-4dB”。 DAC-4dB” 5)、在DAC主菜单“曲线选择”设为“定量线”,另外工件表 )、在DAC主菜单“曲线选择”设为“定量线” 面补偿一般要3 4dB,所以“增益校正”应设置为“ 面补偿一般要3、4dB,所以“增益校正”应设置为“3、 4dB” 4dB”。 6)、在保存主菜单保存当前仪器状态设定及DAC曲线到空白的 )、在保存主菜单保存当前仪器状态设定及DAC曲线到空白的 数据集内,记录好该曲线的储存号。
返回
仪器的调校(图)
返回
DAC曲线的制作 DAC曲线的制作(图)
DAC曲线的制作 DAC曲线的制作(图)
返回
探伤操作(图)
返回
探伤操作(图)
返回
探伤操作(图)
返回
缺陷等级分类
返回
焊缝裂纹
超声波探伤操作
质量部
2011.3.23
前 言
探伤目的:检查焊缝是否存在气孔、裂纹、 探伤目的:检查焊缝是否存在气孔、裂纹、 未焊透、未熔合等内部缺陷 使用标准:GB11345-89(适用于钢焊缝手 使用标准:GB11345-89(适用于钢焊缝手 工超声波探伤) 使用仪器:CTS-2020汕头数字超声探伤仪 使用仪器:CTS-2020汕头数字超声探伤仪
超声波检测焊缝的几种常用方法
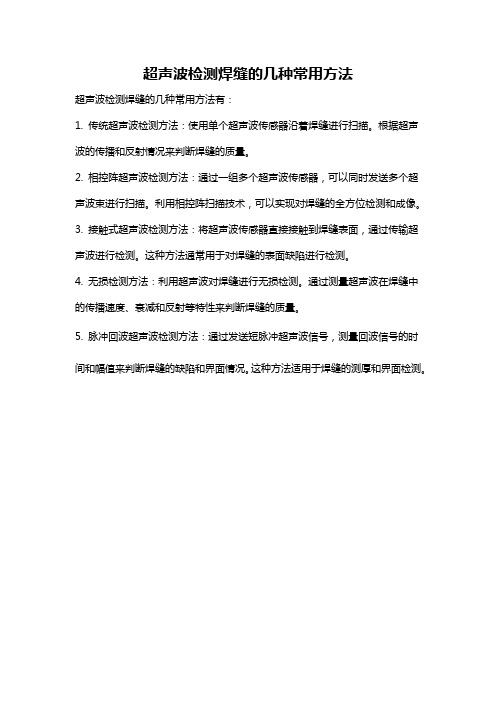
超声波检测焊缝的几种常用方法
超声波检测焊缝的几种常用方法有:
1. 传统超声波检测方法:使用单个超声波传感器沿着焊缝进行扫描。
根据超声波的传播和反射情况来判断焊缝的质量。
2. 相控阵超声波检测方法:通过一组多个超声波传感器,可以同时发送多个超声波束进行扫描。
利用相控阵扫描技术,可以实现对焊缝的全方位检测和成像。
3. 接触式超声波检测方法:将超声波传感器直接接触到焊缝表面,通过传输超声波进行检测。
这种方法通常用于对焊缝的表面缺陷进行检测。
4. 无损检测方法:利用超声波对焊缝进行无损检测。
通过测量超声波在焊缝中的传播速度、衰减和反射等特性来判断焊缝的质量。
5. 脉冲回波超声波检测方法:通过发送短脉冲超声波信号,测量回波信号的时间和幅值来判断焊缝的缺陷和界面情况。
这种方法适用于焊缝的测厚和界面检测。
焊接空心球对接焊缝超声波探伤技术
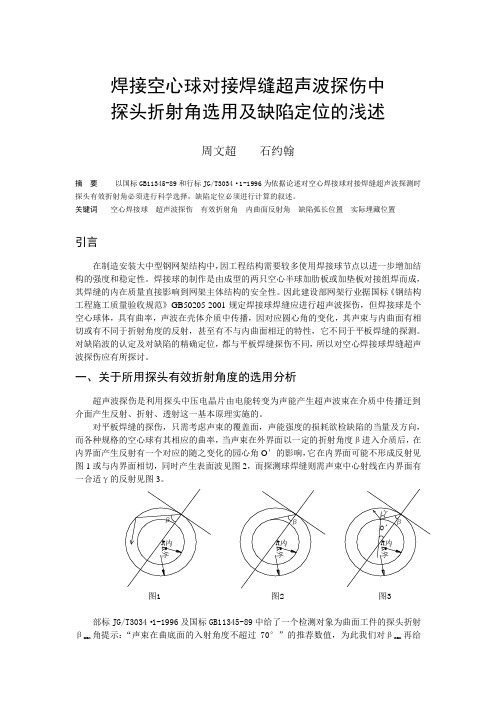
焊接空心球对接焊缝超声波探伤中探头折射角选用及缺陷定位的浅述周文超石约翰摘要以国标GB11345-89和行标JG/T3034·1-1996为依据论述对空心焊接球对接焊缝超声波探测时探头有效折射角必须进行科学选择,缺陷定位必须进行计算的叙述。
关键词空心焊接球超声波探伤有效折射角内曲面反射角缺陷弧长位置实际埋藏位置引言在制造安装大中型钢网架结构中,因工程结构需要较多使用焊接球节点以进一步增加结构的强度和稳定性。
焊接球的制作是由成型的两只空心半球加肋板或加垫板对接组焊而成,其焊缝的内在质量直接影响到网架主体结构的安全性。
因此建设部网架行业据国标《钢结构上一个反射角γ=70°的正弦值,即β有效=sin-1(βmax·sin70°)=sin-1(βmax·0.939)——β3=sin·R内/R外=sin·150/170=61.93°此时β1、β2、β3角度在各自球壳介质内曲面的入射角度都为90°,波型已基本全转换为表面波,沿内曲面表面爬行振动,难以扫查到焊缝的上半部,造成漏检,现用上例三只空心焊接球以不同的折射角βa=61.93°、βb=56.31°入射,在内曲面的入射角γ1、γ2、γ3量值分别为:a:以折射角βa=61.93°为例量值分别为:γ1=sin-1·(R内/R外·sinβa)=sin-1·(210/190·sin61.93°)=77.23°γ2=sin-1·(R内/R外·sinβa)=sin-1·(170/190·sin61.93°)=80.46°γ3=sin-1·(R内/R外·sinβa)=sin-1·(150/170·sin61.93°)=90°β4max=sin-1·R内/R外=sin-1·180/200=64.16°β3max=sin-1·R内/R外=sin-1·160/200=53.13°γ4=sin-1·(R外/R内·sinβ)=sin-1·(200/180·sin56.3°)=67.58°γ3=sin-1·(R外/R内·sinβ)=sin-1·(200/160·sin56.3°)=sin-11.04°(大于90°)从上述计算可知同一角度的探头在同直径球内球面的反射角随壁厚增大而增大,当入角大于90°时将无法与内球面相遇。
超声波探伤检测作业指导书
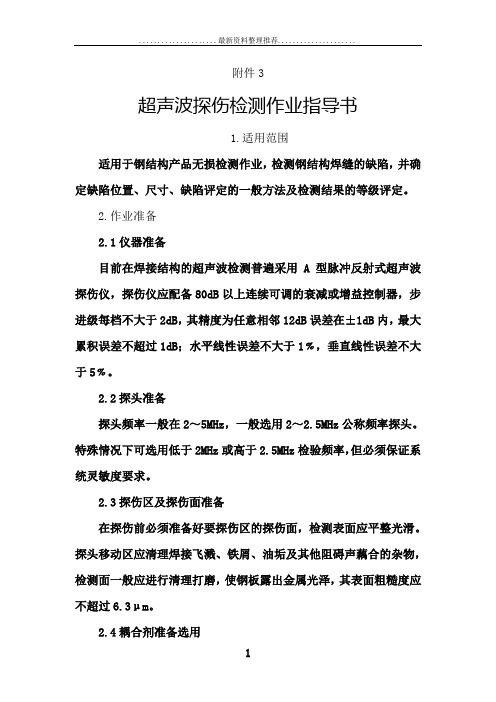
附件3超声波探伤检测作业指导书1.适用范围适用于钢结构产品无损检测作业,检测钢结构焊缝的缺陷,并确定缺陷位置、尺寸、缺陷评定的一般方法及检测结果的等级评定。
2.作业准备2.1仪器准备目前在焊接结构的超声波检测普遍采用A型脉冲反射式超声波探伤仪,探伤仪应配备80dB以上连续可调的衰减或增益控制器,步进级每档不大于2dB,其精度为任意相邻12dB误差在±1dB内,最大累积误差不超过1dB;水平线性误差不大于1﹪,垂直线性误差不大于5﹪。
2.2探头准备探头频率一般在2~5MHz,一般选用2~2.5MHz公称频率探头。
特殊情况下可选用低于2MHz或高于2.5MHz检验频率,但必须保证系统灵敏度要求。
2.3探伤区及探伤面准备在探伤前必须准备好要探伤区的探伤面,检测表面应平整光滑。
探头移动区应清理焊接飞溅、铁屑、油垢及其他阻碍声藕合的杂物,检测面一般应进行清理打磨,使钢板露出金属光泽,其表面粗糙度应不超过6.3μm。
2.4耦合剂准备选用焊缝超声波探伤常用耦合剂有机油、甘油、CMC(化学纤维素)浆糊、润滑脂和水等。
一般工程施工常用的为机油、浆糊两类耦合剂。
当工件表面光洁度较差时,选用声阻抗较大的耦合剂甘油可获得较好的透声性能。
2.5扫描速度调整扫描速度调节由三种方法:①声程比例法:将荧光上时基扫描线长度调整成声程读数,常用CSK-IA试块、半圆试块来调整;②水平比例法:将荧光上时基扫描线长度调整成水平距离读数,常用CSK-IA 或CSK-ⅢA试块来调整;③深度比例法:将荧光上时基扫描线长度调整成水平距离读数,常用CSK-IA试块来调整。
在焊缝探伤中,角度探伤可用声程定位。
但现在焊缝探伤中普遍选用K值探头,板厚小于20mm宜用水平比例法,板厚大于20mm时宜用深度比例法。
2.6距离-波幅曲线(DAC)的绘制2.6.1对于管节点,采用在CSK-ICj试块上实测的直径3mm的横孔反射波幅数据及表面补偿和曲面复测灵敏度修正数据,对于板节点,则采用在CSK-IDj型试块实测的直径3mm横孔反射波幅数据及表面补偿数据。
薄壁小管径焊接球节点焊缝常见缺陷与超声波检测方法
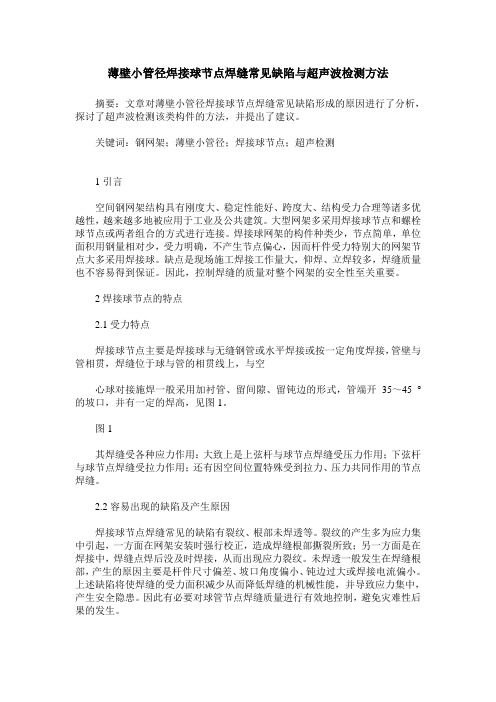
薄壁小管径焊接球节点焊缝常见缺陷与超声波检测方法摘要:文章对薄壁小管径焊接球节点焊缝常见缺陷形成的原因进行了分析,探讨了超声波检测该类构件的方法,并提出了建议。
关键词:钢网架;薄壁小管径;焊接球节点;超声检测1引言空间钢网架结构具有刚度大、稳定性能好、跨度大、结构受力合理等诸多优越性,越来越多地被应用于工业及公共建筑。
大型网架多采用焊接球节点和螺栓球节点或两者组合的方式进行连接。
焊接球网架的构件种类少,节点简单,单位面积用钢量相对少,受力明确,不产生节点偏心,因而杆件受力特别大的网架节点大多采用焊接球。
缺点是现场施工焊接工作量大,仰焊、立焊较多,焊缝质量也不容易得到保证。
因此,控制焊缝的质量对整个网架的安全性至关重要。
2焊接球节点的特点2.1受力特点焊接球节点主要是焊接球与无缝钢管或水平焊接或按一定角度焊接,管壁与管相贯,焊缝位于球与管的相贯线上,与空心球对接施焊一般采用加衬管、留间隙、留钝边的形式,管端开35~45 °的坡口,并有一定的焊高,见图1。
图1其焊缝受各种应力作用:大致上是上弦杆与球节点焊缝受压力作用;下弦杆与球节点焊缝受拉力作用;还有因空间位置特殊受到拉力、压力共同作用的节点焊缝。
2.2容易出现的缺陷及产生原因焊接球节点焊缝常见的缺陷有裂纹、根部未焊透等。
裂纹的产生多为应力集中引起,一方面在网架安装时强行校正,造成焊缝根部撕裂所致;另一方面是在焊接中,焊缝点焊后没及时焊接,从而出现应力裂纹。
未焊透一般发生在焊缝根部,产生的原因主要是杆件尺寸偏差、坡口角度偏小、钝边过大或焊接电流偏小。
上述缺陷将使焊缝的受力面积减少从而降低焊缝的机械性能,并导致应力集中,产生安全隐患。
因此有必要对球管节点焊缝质量进行有效地控制,避免灾难性后果的发生。
3超声波探伤系统的建立3.1探头的选择薄壁小管径(厚度4~8 mm、管径60~159 mm)杆件,曲率大,易造成声束扩散,使灵敏度降低;管壁薄、声程短,有近场干扰、发散严重,且杂波多;探头折射角大,极易产生波型转换;折射角小,一次波无法探测到焊缝根部缺陷。
对接焊接接头超声波检测工艺规程
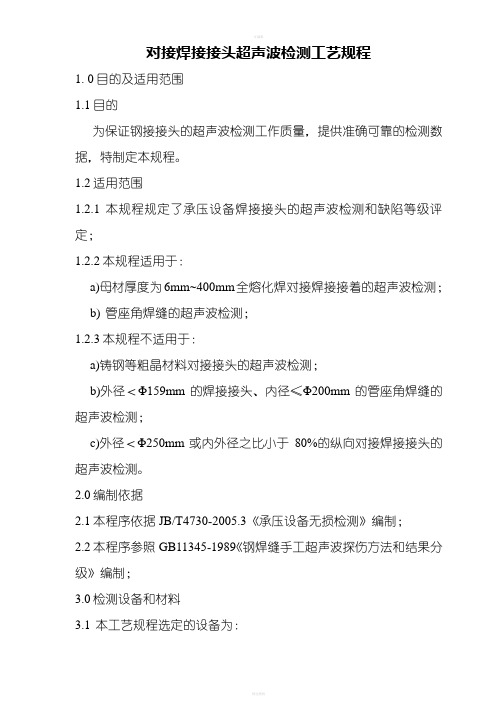
对接焊接接头超声波检测工艺规程1. 0目的及适用范围1.1目的为保证钢接接头的超声波检测工作质量,提供准确可靠的检测数据,特制定本规程。
1.2适用范围1.2.1本规程规定了承压设备焊接接头的超声波检测和缺陷等级评定;1.2.2本规程适用于:a)母材厚度为6mm~400mm全熔化焊对接焊接接着的超声波检测;b) 管座角焊缝的超声波检测;1.2.3本规程不适用于:a)铸钢等粗晶材料对接接头的超声波检测;b)外径<Φ159mm的焊接接头、内径≤Φ200mm的管座角焊缝的超声波检测;c)外径<Φ250mm或内外径之比小于80%的纵向对接焊接接头的超声波检测。
2.0编制依据2.1本程序依据JB/T4730-2005.3《承压设备无损检测》编制;2.2本程序参照GB11345-1989《钢焊缝手工超声波探伤方法和结果分级》编制;3.0检测设备和材料3.1 本工艺规程选定的设备为:数字式A型脉冲接触式超声波检测仪;3.2 为保证超声波检测结果的可靠,超声波检测仪及超声波检测要进行定期校验,必要时可进行随机校验;3.2.1 超声波检测仪和超声波检测用探头的校验方法可依照《数字式超声波检测仪、探头性能测试》程序进行;3.2.2 超声波检测仪和超声波检测用探头的校验的评定标准为:a).水平线性误差值ΔL≯1%;b). 垂直线性误差Δd≯5%;c). 动态范围>26dB。
且保证在达到所检试件最大声程时,其有效灵敏度余量≮10dB;d). 盲区<7mm;e).分辨力F:⑴.直(纵波)探头的分辨力F1≤6mm;⑵.斜(横波)探头的分辨力F2≤6mm。
3.3超声波检测仪和超声波检测用探头的校验周期可依照《数字式超声波检测仪、探头性能测试》程序的要求进行;3.4探头的选用见表1:表1:推荐采用的斜(横波)探头3.5试块试块是超声波检测仪器校准的基准,也是缺陷评定参考基准。
试块的选用必须满足JB/T4730—2005.3标准的要求。
探伤操作规程
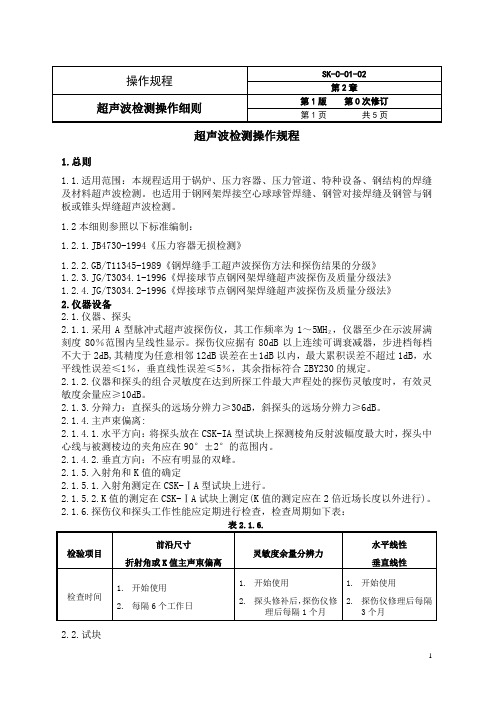
超声波检测操作规程1.总则1.1.适用范围:本规程适用于锅炉、压力容器、压力管道、特种设备、钢结构的焊缝及材料超声波检测。
也适用于钢网架焊接空心球球管焊缝、钢管对接焊缝及钢管与钢板或锥头焊缝超声波检测。
1.2本细则参照以下标准编制:1.2.1.JB4730-1994《压力容器无损检测》1.2.2.GB/T11345-1989《钢焊缝手工超声波探伤方法和探伤结果的分级》1.2.3.JG/T3034.1-1996《焊接球节点钢网架焊缝超声波探伤及质量分级法》1.2.4.JG/T3034.2-1996《焊接球节点钢网架焊缝超声波探伤及质量分级法》2.仪器设备2.1.仪器、探头,仪器至少在示波屏满2.1.1.采用A型脉冲式超声波探伤仪,其工作频率为1~5MHZ刻度80%范围内呈线性显示。
探伤仪应据有80dB以上连续可调衰减器,步进档每档不大于2dB,其精度为任意相邻12dB误差在±1dB以内,最大累积误差不超过1dB,水平线性误差≤1%,垂直线性误差≤5%,其余指标符合ZBY230的规定。
2.1.2.仪器和探头的组合灵敏度在达到所探工件最大声程处的探伤灵敏度时,有效灵敏度余量应≥10dB。
2.1.3.分辩力:直探头的远场分辨力≥30dB,斜探头的远场分辨力≥6dB。
2.1.4.主声束偏离:2.1.4.1.水平方向:将探头放在CSK-IA型试块上探测棱角反射波幅度最大时,探头中心线与被测棱边的夹角应在90°±2°的范围内。
2.1.4.2.垂直方向:不应有明显的双峰。
2.1.5.入射角和K值的确定2.1.5.1.入射角测定在CSK-ⅠA型试块上进行。
2.1.5.2.K值的测定在CSK-ⅠA试块上测定(K值的测定应在2倍近场长度以外进行)。
2.1.6.探伤仪和探头工作性能应定期进行检查,检查周期如下表:表2.1.6.2.2.试块2.2.1.常用JB4730-1994规定的焊缝超声波探伤CSK系列横孔标准试块,GB/T11345-1989ⅡC型试块绘制距离波幅曲线,校核时基线与探伤灵敏度。
焊缝超声波探伤(第二节平板对接焊缝的超声波探伤方法)
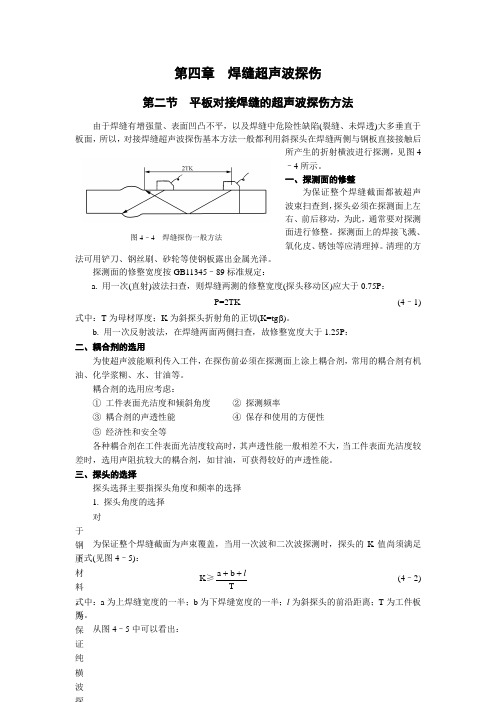
第四章 焊缝超声波探伤第二节 平板对接焊缝的超声波探伤方法由于焊缝有增强量、表面凹凸不平,以及焊缝中危险性缺陷(裂缝、未焊透)大多垂直于板面,所以,对接焊缝超声波探伤基本方法一般都利用斜探头在焊缝两侧与钢板直接接触后所产生的折射横波进行探测,见图4–4所示。
一、探测面的修整为保证整个焊缝截面都被超声波束扫查到,探头必须在探测面上左右、前后移动,为此,通常要对探测面进行修整。
探测面上的焊接飞溅、氧化皮、锈蚀等应清理掉。
清理的方法可用铲刀、钢丝刷、砂轮等使钢板露出金属光泽。
探测面的修整宽度按GB11345–89标准规定:a. 用一次(直射)波法扫查,则焊缝两测的修整宽度(探头移动区)应大于0.75P :P=2TK (4–1)式中:T 为母材厚度;K 为斜探头折射角的正切(K=tg β)。
b. 用一次反射波法,在焊缝两面两侧扫查,故修整宽度大于1.25P : 二、耦合剂的选用为使超声波能顺利传入工件,在探伤前必须在探测面上涂上耦合剂,常用的耦合剂有机油、化学浆糊、水、甘油等。
耦合剂的选用应考虑:① 工件表面光洁度和倾斜角度 ② 探测频率③ 耦合剂的声透性能④ 保存和使用的方便性⑤ 经济性和安全等各种耦合剂在工件表面光洁度较高时,其声透性能一般相差不大,当工件表面光洁度较差时,选用声阻抗较大的耦合剂,如甘油,可获得较好的声透性能。
三、探头的选择探头选择主要指探头角度和频率的选择 1. 探头角度的选择对于钢质材料,为保证纯横波探测,探头的入射角应在第一临界角(27.5°)和第二临界角(57°)之间,即27.5°<α<57°。
国内过去使用的探头均以入射角标称,如、30°、40°、45°、50°、55°等。
近年来,考虑到为使缺陷定位计算方便,故均改用K 值探头(K=tg β)如K=0.8、K=1、K=1.5、K=2、K=2.5、K=3等。
建筑钢结构焊缝超声波探伤实施细则
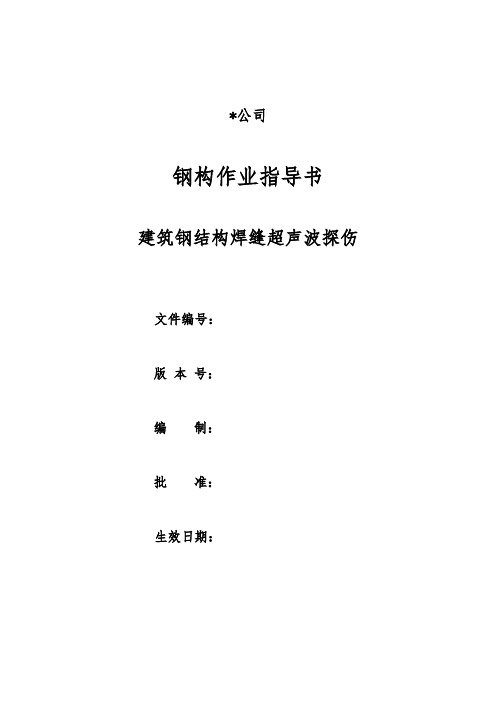
*公司钢构作业指导书建筑钢结构焊缝超声波探伤文件编号:版本号:编制:批准:生效日期:建筑钢结构焊缝超声波探伤实施细则1. 目的为使测试人员在做建筑钢结构焊缝超声波探伤时有章可循,并使其操作合乎规范。
2. 适用范围适用于母材厚度不小于4mm的碳素钢和低合金钢的钢板对接、T型接头、电渣焊接头;适用于母材壁厚不小于3.5mm,管径不于小48mm的螺栓球节点杆件与锥头或封板对接;适用于母材壁度不小于4mm,球径不小于120mm,管径不小于60 mm的焊接空心球及球管焊缝;适用于母材壁厚不小于6mm、支管管径不于小89mm、局部两面角夹不小于30°、支管壁厚外径比小于13%的圆管相贯接节点碳素钢和低合金钢焊接接头焊。
3. 检测依据GB 50205-2001钢结构工程施工质量验收规范JGJ7-2010空间网格结构技术规程JGJ81-2002建筑钢结构焊接技术规程GB 50661-2011 钢结构焊接规范JG/T203-2007钢结构超声波探伤及质量分级法GB/T11345-2013焊缝无损检测超声检测技术、检测等级和评定4.检验方法概述超声波探伤法的原理是利用超声波探伤仪换能器发射的脉冲超声波,通过良好的耦合方式使超声波入射至被检工件内,超声波在工件内传播遇到异质界面产生反射,反射波被换能器所接收并传至超声波探伤仪示波器。
通过试块或工件底面作为反射体调节时基线以确定缺陷反射回波的位置,调整检测灵敏度以确定缺陷的当量大小。
5.人员要求所有从事超声波探伤的检验员应通过有关部门组织的超声波探伤培训、考试并取得相应的执业资格证书,Ⅰ级检验员具有现场操作资格,但必须在Ⅱ级或Ⅲ级人员的指导或监督下进行,Ⅱ级或Ⅲ级人员可以编制超声波探伤工艺规程和工艺卡以及签发审核检验报告。
超声检验人员的视力应每年检查一次,校正视力不得低于1.0。
6.检测器材6.1超声波探伤仪:采用数字A型脉冲反射式超声波探伤仪,频率范围为0.5-10MHz,且实时采样频率不应小于40MHz;衰减器精度为任意相邻12dB的误差在±1dB以内,最大累计误差不超过1dB;水平线性偏差不大于±2%,垂直线性偏差不大于±3%。
焊缝超声波探伤操作步骤
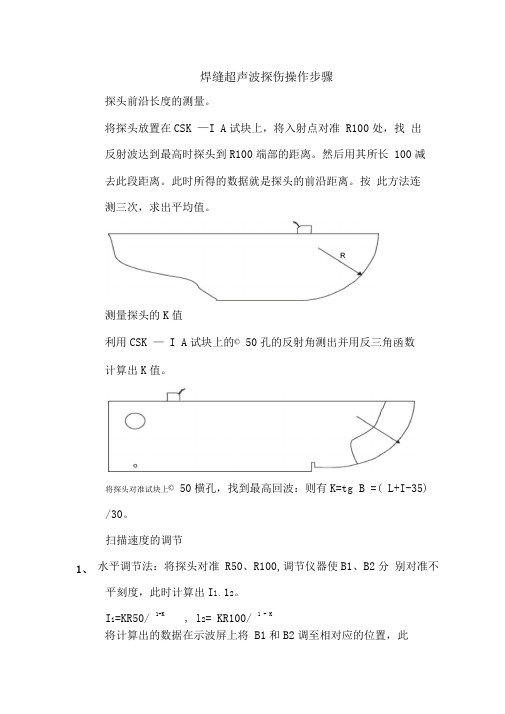
焊缝超声波探伤操作步骤探头前沿长度的测量。
将探头放置在CSK —I A试块上,将入射点对准R100处,找出反射波达到最高时探头到R100端部的距离。
然后用其所长100减去此段距离。
此时所得的数据就是探头的前沿距离。
按此方法连测三次,求出平均值。
测量探头的K值利用CSK —I A试块上的© 50孔的反射角测出并用反三角函数计算出K值。
将探头对准试块上© 50横孔,找到最高回波:则有K=tg B =( L+I-35) /30。
扫描速度的调节水平调节法:将探头对准R50、R100,调节仪器使B1、B2分别对准不平刻度,此时计算出I l、12。
I i=KR50/ 1+K, l2= KR100/ 1 + K将计算出的数据在示波屏上将B1和B2调至相对应的位置,此1、时水平距离扫描速度为1:1。
2、深度调节法利用CSK- I A试块调节,先计算R50、R100圆弧反射波B1、B2对应的纵深di、d2: d i=R50/ 1+K, d2= R100/1+K,然后调节仪器使Bi、B2分别对准水平刻度值d1、d2。
如K=2时,经计算d1二、d2=。
1、将探头置于CSK-皿A试块上,衰减48dB,调增益使深度为10mm的© 1 X 6孔的最高回波达基准60%,记录此时的衰减器读数和孔深,然后分别探测其它不同深度的© 1X6孔,增益不动,调节衰减器将各孔的最高回波调至60%高,记下相应的dB 值和孔深填入表中。
2、以孔深为横坐标,以分贝值为纵坐标,在坐标纸上描点绘出定量线、判废线和评定线,标出I区、H区、皿区,并注明所用探头的频率、晶片尺寸和K值。
3、现以T=30mm举例说明0 1 x 6(dB)52 50 47 44 41 38 0 1 x 6+5(dB)判废线57 55 52 49 46 43 0 1 x 6-3(dB)定量线49 47 44 41 38 35 0 1X 6-9(dB)评定线434138353229|]_1一1 ______ I _________ |_1 02 03 04 050五、调节探伤灵敏度调节探伤灵敏度时,探伤灵敏度不得低于评定线,一般以2倍的壁厚处所对应的评定线dB 值,也就是说在工件60mm 处评 定线所对应的分贝值。
焊缝超声波探伤标准
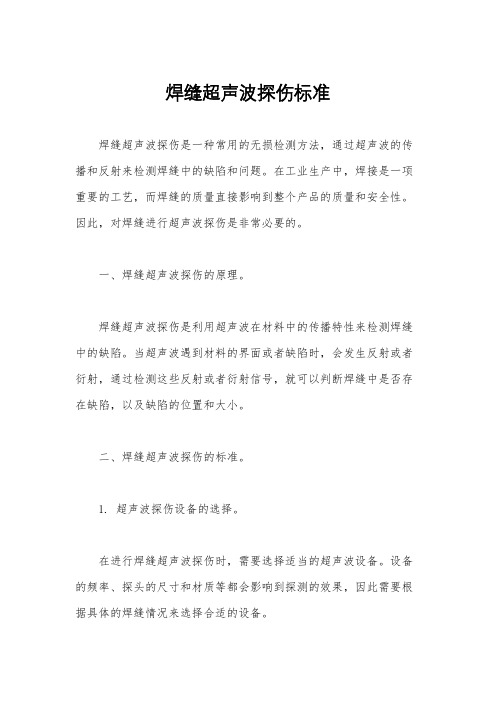
焊缝超声波探伤标准焊缝超声波探伤是一种常用的无损检测方法,通过超声波的传播和反射来检测焊缝中的缺陷和问题。
在工业生产中,焊接是一项重要的工艺,而焊缝的质量直接影响到整个产品的质量和安全性。
因此,对焊缝进行超声波探伤是非常必要的。
一、焊缝超声波探伤的原理。
焊缝超声波探伤是利用超声波在材料中的传播特性来检测焊缝中的缺陷。
当超声波遇到材料的界面或者缺陷时,会发生反射或者衍射,通过检测这些反射或者衍射信号,就可以判断焊缝中是否存在缺陷,以及缺陷的位置和大小。
二、焊缝超声波探伤的标准。
1. 超声波探伤设备的选择。
在进行焊缝超声波探伤时,需要选择适当的超声波设备。
设备的频率、探头的尺寸和材质等都会影响到探测的效果,因此需要根据具体的焊缝情况来选择合适的设备。
2. 探测方法和参数的设定。
在进行焊缝超声波探伤时,需要根据焊缝的类型和要求来设定合适的探测方法和参数。
包括超声波的频率、探头的角度、扫描方式等,这些参数的设定直接影响到探测的准确性和可靠性。
3. 缺陷的判定标准。
针对不同类型的焊缝,需要制定相应的缺陷判定标准。
比如对于焊接接头的缺陷,需要根据相关标准来判断缺陷的大小、形状和位置,以及对产品质量的影响程度。
4. 数据分析和报告。
在进行焊缝超声波探伤后,需要对探测到的数据进行分析,并生成相应的检测报告。
报告中需要包括焊缝的情况描述、探测到的缺陷情况、以及针对缺陷的处理建议等内容。
三、焊缝超声波探伤的应用。
焊缝超声波探伤广泛应用于航空航天、汽车制造、船舶建造、管道工程等领域。
通过超声波探伤,可以及时发现焊缝中的缺陷和问题,保障产品的质量和安全性。
总之,焊缝超声波探伤是一项非常重要的无损检测方法,对于焊接工艺的质量控制和产品质量的保障起着至关重要的作用。
因此,在进行焊缝超声波探伤时,需要严格按照相关标准和要求进行操作,确保探测的准确性和可靠性。
焊接球节点钢网架焊缝超声波探伤

焊接球节点钢网架焊缝超声波探伤焊接球节点钢网架焊缝超声波探伤 2003年1月总第9l期西北建筑与建材2l 焊接球节点钢网架焊缝超声波探伤张宣关(陕西省建筑科学研究院710082)摘要:本文主要探讨空间钢网架结构焊接接头超声波检测的有关技术问题.文中涉及到网架的制作工艺和焊接方法,超声探伤系统的选择,探伤标定和探伤方法,检测结果分析和缺陷评定.同时系统地总结了有关缺陷探测的规律性和特殊性.'近十年以来,空间钢结构在建筑领域的应用越来越广泛,焊接球节点钢网架在大跨空间结构中的应用尤为显着.该类网架在拼装制作过程中,球节点与杆件的焊接是主要的工作内容.除周边及其支座节点外,其余上,下弦每个球节点均与8根杆件焊接相连,因此整个网架的焊缝数量及总长度都很大.球一杆焊缝的质量检验主要是外观检验和超声波探伤无损检验,本文作者根据多年的质量检验工作经验,对该类结构焊缝的超声波探伤作一些探索.一,焊接球网架的拼装工艺和焊接方法大跨网架的制作可分为地面拼装整体吊装和满堂架就位拼装两大类,焊接方法以交直流手工焊为主,杆件端部加工30.,50.焊接坡口,一般不加工钝边.钢材材质主要分为Q235和Q345二类.焊条E4303和E5015.焊接环境温度一般不低于5?,亦不需予热.焊前需对焊口部位100mm 范围内进行打磨除锈,焊条烘干250,300"(22小时.钢球规格通常为中250,500mm,壁厚一般不大于16mm.杆件规格为中60,219mm,壁厚6,16mm.节点及焊接部位如图l,图2所示.图l球节点示意图图2球一管接口示意图西北建筑与建材2003年1月总第91期二,超声仪器扩及探头网架焊缝超声探伤的工作环境为高空和野外,且探伤面只有杆件一侧,因此宜选用重量轻,灵敏度和分辨率高,线性好的超声仪,数字式或模拟式探伤仪均可.根据管件壁厚较小的特点,一般选用带曲面的2.5PK2.5短前沿(1=5mm)A~晶片(6×6或8×8)探头,并结合使用较大晶片(9×9,8×12)探头.根据经验,小前沿探头便于一次波探测根部未熔合及引弧处根部密集气孔缺陷,但由于晶片较小,声束狭窄,有漏检焊缝坡口及层间未熔等缺陷的现象,而大晶片探头能有效地利用二次波检出该类缺陷,为便于操作可选用同K值不同晶片尺寸的两种探头对网架重要受力部位进行细致探测,以防漏检.三,探伤准备1.仪器——-探头系统规定依据GB11345-89(《钢焊缝手工超声波探伤方法和探伤结果分级法》或JBJ/T3034.1(《焊接球节点钢网架焊缝超声波探伤方法及质量分级法》,对所选用的仪器——探头系统进行标定,作距离一波幅曲线.定位方法可选用深度定位或水平定位,一般对管壁大于10mm,宜选用深度定位;管壁小于8mm宜选用水平定位.表面补偿一般为4dB,耦合剂宜选用无蚀害作用的机油或工业浆糊.2.确定探测区域宽度在确定探测区域宽度时,一般以探头三次波加前沿并扩大10,20mm为探测范围,对该范围及焊缝外表面易引起误判的伪缺陷(飞溅,焊瘤及不恰当佘高)进行打磨处理.常见规格管件扫查区域宽度见表l.表1管件规格2I9×16I80×I2I59×10140×8I33×8ll4×6扫查区域宽度(mm)l20ll0l00l008070 四,缺陷探测1.探头扫查方式探伤时探头作锯齿形前后移动的同时不断向右作横向移动,前后扫查探头的夹角为10,15.,锯齿间距不超过探头晶片宽度.发现缺陷后,停止前移, 进行绕射移动和定点转动,同时进行动静态波形分析,对缺陷作综合判断. 2.缺陷定位在采用深度定位标定的情况下,搜索缺陷脉冲峰值,由示波屏直接确定缺陷深度(Z);缺陷的横向位置确定,采用钢直尺从探头前沿进行测量并作有关计算.当采用一次波时:Y=y—Y=y—KZ当采用二次波时:Y=y-y=y-(26一Z)K3.缺陷测长图3探头扫查方式y2003年1月总第9l期西北建筑与建材除?区缺陷和其它经分析判断为危害性缺陷判废外,对于?区和部分I区缺陷需进行指示长度测量,常用半波高度法(6dB法).首先确定缺陷最高脉冲部位,在钢管表作记号,以该点为中心分别向左右两边移动探头,当脉冲下降50%时作记号,左右两边记号之弧长距离作为该单个缺陷的指示长度.当两缺陷间距小于8ram时,将该两缺陷指示长度之和作为单个缺陷的指示长度,依据标准进行评判.在实际工程检测中,会遇到深度方向较长的缺陷,对此类缺陷,前后移动探头,对深度范围进行分析和评定.五缺陷分析通过长期的检测实践,可将钢网架球一管焊缝的焊接缺陷分为以下几类: 1.根部未焊透'该类型缺陷很常见,有效的检测方法为采用短前沿小晶片探头(6×6)一次波法,该探伤方法简单实用,但受管壁厚度影响较大,当6?6时,由于近场区效应,一次波受干扰很大,往往很难判断,此时需采用三次波进行探测,亦可使用较大晶片探头(9×9,8×l0)三次波进行检测. 2.引弧处根部密集气孔当施焊时无引弧板而直接于坡121处起弧时,极易出现密集气孔,该类缺陷的检测与根部未焊透相同.在评定缺陷危害性时,除规范要求外,可参照根部未焊透缺陷,因为该类缺陷一般位于根部l,2ram处,指示长度在l0,15ram,其应力集中程度与根部缺151相近.3.层间夹渣层间夹渣缺陷常发生于板厚深度方向2/3处,形成原因主要为小直径焊条(3.2)打底后清渣不彻底或大直径焊条第一道填充时操作运条不稳定而形成,该类缺陷的检测一般以二次波或小晶片一次波,缺陷指示长度通常为l0,12ram,但有密集现象.4.焊缝中,上部气孔此类缺陷的形成原因主要为焊条烘干不充分和焊接速度偏大,熔池停留时间较短,气体来不及逸出造成.此外电弧电压偏高,电弧过长减弱了药皮造气的保护作用也是原因之一.探伤检测时,以二次波最有效.5.焊缝球表面侧未熔合此类缺陷当球壁厚较大时(6?20mm)极易发生,主要由于球.管散热速度相差较大,球壁温度梯度远大于管壁,当运条不稳焊接时,由于熔池的表面张力较大和结晶速度较快而形成.遇到厚壁球,探伤时对该类缺陷应引起重视,缺陷分布范围为焊缝深度方向?,处.有效的探伤方法为二次波法,该类缺陷的脉冲往往较高,波形尖锐而清晰,波峰位于?区的多.6.焊缝表面气孔该类缺陷较多,主要位于盖面层收弧处,深度2,3mm,呈密集形,探伤时二次波检出率很高,缺陷一般多位于盖面层偏向球方向侧,是否需要处理应进行分析.因球侧焊角高出管壁5,7ram,焊缝承载受力时,其应力密度在该位置已很小,因此该类缺陷对焊缝的等强作用影响较小,可处理亦可不处理,应根据焊缝的受力重要性来评定,亦可采用手动砂轮打磨来消除.六,伪缺陷分析24西北建筑与建材2003年1月总第9l期1.衬环反射波大管一般焊前装有衬环(5=3mm),其作用为保证焊接间隙和充分熔透.当衬环伸出较长,探伤时衬环内壁棱角部位常有反射脉冲.排除该类伪缺陷的办法是探伤前需查清楚坡口角度,计算坡口水平投影长度,探伤时根据缺陷的水平位置可分辨清楚,特别当焊缝整圈都有连续性尖锐脉冲时应引起重视,避免误判.2.根部焊瘤根部焊瘤发生于无衬环的接头中,由间隙较大而形成,脉冲峰值较大,长度有大有小.其排除方法亦采用水平计算定位法.3.焊缝表面咬边表面咬边通过目测可清楚发现,但它易与内部缺陷相混淆.反射波常位于二次波极限位置之前,波形尖锐清晰,当采用水平l:l定位时,通过水平距离测量位置容易确定,而示波屏脉冲位置正好与咬边位置相符.4.表面沟槽焊缝表面的沟槽易引起反射脉冲,其脉冲在示波屏的位置一般已进人三次波段,但通过水平测量可辨析清楚,或用沾油的手指在焊缝表面沾试,根据脉冲是否跳动来判断缺陷真伪.5.耦合剂的反射该类波属于表面波,一般由于耦合剂太多而造成.脉冲外形粗糙,底部较宽,当探头静止时,脉冲仍不断缓慢变化,有经验的探伤人员可立刻判别.6.球内壁反射波该伪缺陷一般发生于小K值探头(K=2.0)一次波且管壁较厚(5?10mm)的焊缝探伤中,此类现象较少见,但时有发生,应引起足够重视,它往往发生于同一规格球一管接头的批量之中.探伤时只需进行水平距离计算即可分辨脉冲所示位置远离焊缝.七,小结焊接钢网架球体曲面角焊缝数量大,且施焊条件差,空间位置有限,缺陷较多,诸因素给超声探伤带来很多困难.结合多年实践经验,本文认为首先应从理论上进行严密的分析,从实践中不断总结经验,归纳总结出一些实用的规律,就可不断提高无损检测的准确性,以确保工程质量,同时应作深人的探索,不断完善具体条件下的探伤方法,总结其规律性,丰富无损检测学科的内容. 【2】【3】【4】参考资料陕西省建设工程质量检测中t~,1990-2000年(《秦俑馆2#坑100m跨球节点网架焊接质量检测报告,(《西安交通大学思源活动中心网架焊接质量检测报告,(《西安城运村网架焊接质量检测报告,张宣关等编劳动人事出版社1998((超声波探伤GB11345—89(《钢焊缝手工超声波探伤方法及探伤结果分级中国机械工业学会焊接学会2001((焊接手册。
焊缝超声波探伤工艺规程
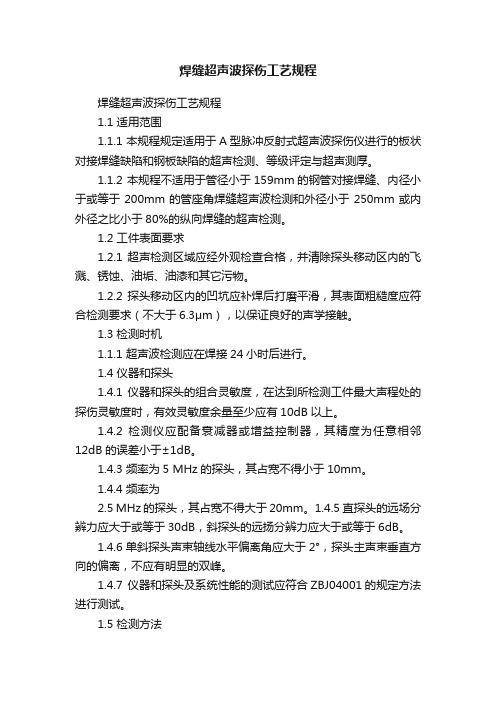
焊缝超声波探伤工艺规程焊缝超声波探伤工艺规程1.1 适用范围1.1.1 本规程规定适用于A型脉冲反射式超声波探伤仪进行的板状对接焊缝缺陷和钢板缺陷的超声检测、等级评定与超声测厚。
1.1.2 本规程不适用于管径小于159mm的钢管对接焊缝、内径小于或等于200mm的管座角焊缝超声波检测和外径小于250mm或内外径之比小于80%的纵向焊缝的超声检测。
1.2 工件表面要求1.2.1 超声检测区域应经外观检查合格,并清除探头移动区内的飞溅、锈蚀、油垢、油漆和其它污物。
1.2.2 探头移动区内的凹坑应补焊后打磨平滑,其表面粗糙度应符合检测要求(不大于6.3μm),以保证良好的声学接触。
1.3 检测时机1.1.1 超声波检测应在焊接24小时后进行。
1.4 仪器和探头1.4.1 仪器和探头的组合灵敏度,在达到所检测工件最大声程处的探伤灵敏度时,有效灵敏度余量至少应有10dB以上。
1.4.2 检测仪应配备衰减器或增益控制器,其精度为任意相邻12dB的误差小于±1dB。
1.4.3 频率为5 MHz的探头,其占宽不得小于10mm。
1.4.4 频率为2.5 MHz的探头,其占宽不得大于20mm。
1.4.5 直探头的远场分辨力应大于或等于30dB,斜探头的远扬分辨力应大于或等于6dB。
1.4.6 单斜探头声束轴线水平偏离角应大于2°,探头主声束垂直方向的偏离,不应有明显的双峰。
1.4.7 仪器和探头及系统性能的测试应符合ZBJ04001的规定方法进行测试。
1.5 检测方法1.5.1 检测时应采用机油、浆糊、甘油和水等透声性好且不损伤检测表面的耦合剂。
1.5.2检测时应扫查工件的整个被检区域,探头的每次扫查复盖率应大于探头直径的15%。
1.5.3 检测时探头的扫查速度不应超过150mm/s,相邻两次探头移动间隔保证至少有探头宽度10%的重叠。
1.5.4 检测时扫查灵敏度至少应比基准灵敏度高6dB。
1.5.5 检测纵向缺陷应进行锯齿形扫查。
建筑钢结构焊缝超声波探伤实施细则D0

钢构作业指导书建筑钢结构焊缝超声波探伤文件编号:版本号:编制:批准:生效日期:建筑钢结构焊缝超声波探伤实施细则1. 目的为使测试人员在做建筑钢结构焊缝超声波探伤时有章可循,并使其操作合乎规范。
2. 适用范围适用于母材厚度不小于4mm的碳素钢和低合金钢的钢板对接、T型接头、电渣焊接头;适用于母材壁厚不小于3.5mm,管径不于小48mm的螺栓球节点杆件与锥头或封板对接;适用于母材壁度不小于4mm,球径不小于120mm,管径不小于60 mm的焊接空心球及球管焊缝;适用于母材壁厚不小于6mm、支管管径不于小89mm、局部两面角夹不小于30°、支管壁厚外径比小于13%的圆管相贯接节点碳素钢和低合金钢焊接接头焊。
3. 检测依据GB 50205-2001钢结构工程施工质量验收规范JGJ7-2010空间网格结构技术规程JGJ81-2002建筑钢结构焊接技术规程GB 50661-2011 钢结构焊接规范JG/T203-2007钢结构超声波探伤及质量分级法GB/T11345-2013焊缝无损检测超声检测技术、检测等级和评定4.检验方法概述超声波探伤法的原理是利用超声波探伤仪换能器发射的脉冲超声波,通过良好的耦合方式使超声波入射至被检工件内,超声波在工件内传播遇到异质界面产生反射,反射波被换能器所接收并传至超声波探伤仪示波器。
通过试块或工件底面作为反射体调节时基线以确定缺陷反射回波的位置,调整检测灵敏度以确定缺陷的当量大小。
5.人员要求所有从事超声波探伤的检验员应通过有关部门组织的超声波探伤培训、考试并取得相应的执业资格证书,Ⅰ级检验员具有现场操作资格,但必须在Ⅱ级或Ⅲ级人员的指导或监督下进行,Ⅱ级或Ⅲ级人员可以编制超声波探伤工艺规程和工艺卡以及签发审核检验报告。
超声检验人员的视力应每年检查一次,校正视力不得低于1.0。
6.检测器材6.1超声波探伤仪:采用数字A型脉冲反射式超声波探伤仪,频率范围为0.5-10MHz,且实时采样频率不应小于40MHz;衰减器精度为任意相邻12dB的误差在±1dB以内,最大累计误差不超过1dB;水平线性偏差不大于±2%,垂直线性偏差不大于±3%。
焊缝超声波探伤标准
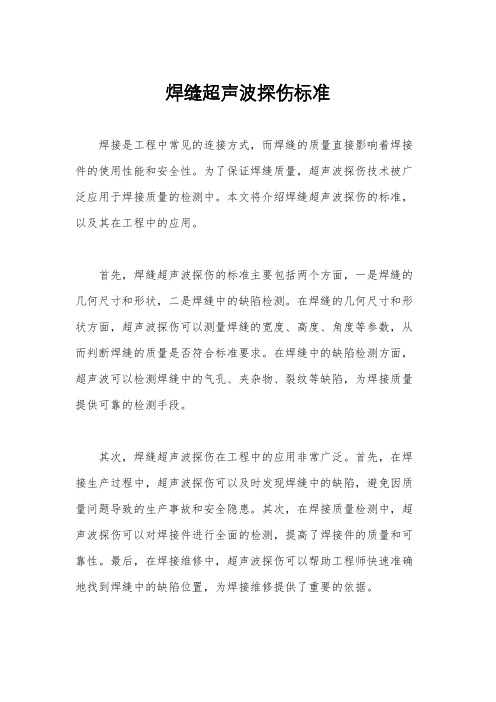
焊缝超声波探伤标准
焊接是工程中常见的连接方式,而焊缝的质量直接影响着焊接件的使用性能和安全性。
为了保证焊缝质量,超声波探伤技术被广泛应用于焊接质量的检测中。
本文将介绍焊缝超声波探伤的标准,以及其在工程中的应用。
首先,焊缝超声波探伤的标准主要包括两个方面,一是焊缝的几何尺寸和形状,二是焊缝中的缺陷检测。
在焊缝的几何尺寸和形状方面,超声波探伤可以测量焊缝的宽度、高度、角度等参数,从而判断焊缝的质量是否符合标准要求。
在焊缝中的缺陷检测方面,超声波可以检测焊缝中的气孔、夹杂物、裂纹等缺陷,为焊接质量提供可靠的检测手段。
其次,焊缝超声波探伤在工程中的应用非常广泛。
首先,在焊接生产过程中,超声波探伤可以及时发现焊缝中的缺陷,避免因质量问题导致的生产事故和安全隐患。
其次,在焊接质量检测中,超声波探伤可以对焊接件进行全面的检测,提高了焊接件的质量和可靠性。
最后,在焊接维修中,超声波探伤可以帮助工程师快速准确地找到焊缝中的缺陷位置,为焊接维修提供了重要的依据。
总之,焊缝超声波探伤标准是保证焊接质量的重要手段,其在
工程中的应用具有重要意义。
通过对焊缝的几何尺寸和形状以及缺
陷的检测,超声波探伤可以有效地提高焊接质量,保障工程安全。
希望本文的介绍能够帮助大家更加深入地了解焊缝超声波探伤标准,并在工程实践中加以应用。
焊缝的超声波探伤资料讲解

超声波的反射、折射、波形转换
在有机玻璃与钢的介面:
第一临界角为α=27.2°,βS=33.3° 第二临界角为α=56.7°,βS=90°
用于焊缝检测的超声波斜探头的入射 角必须大于第一临界角而小于第二临 界角。 我国习惯:斜探头的横波折射角用横 波折射角度的正切值表 示,如K=2
超声波探伤用试块
CSK-IA
超声波探伤用试块
调节:探头的前沿、K值、声速
超声波探伤用试块
CSK-IIIA
距离-波幅(DAC)曲线绘制
三条曲线生成后,按“增益”键,使用方向键调节曲线的高底,使 判废线达到屏幕的80%高度,进入探伤界面,进行探伤检测。
探测灵敏度的选定
➢ 探测灵敏度决定了检测缺陷的能力 灵敏度高,检测缺陷的能力大,探伤时反射的杂波太多,影响缺陷波的
GB11345-89标准规定:检验频率f一般在2-5MHz范围内选 择,
推荐选用2-2.5MHz公称频率检验。
检验等级
•A级检验
采用一种角度的探头在焊缝的单面单侧进行检验,只对允许扫 查到的焊缝截面进行探测.一般不要求作横向缺陷的检验.母材厚度 大于50mm时,不得采用A级检验。
检验等级
• B级检验
➢ 采用二次波探伤,探测面修整宽度为:
S ≥ 2KT+50 (mm)
➢ 采用一次波探伤,探测面修整宽度为:
S≥KT+50 (mm) 式中: K----探头的K值;
T----工件厚度。
P
P
二次波探伤
一次波探伤
耦合剂的选用
- 1、下载文档前请自行甄别文档内容的完整性,平台不提供额外的编辑、内容补充、找答案等附加服务。
- 2、"仅部分预览"的文档,不可在线预览部分如存在完整性等问题,可反馈申请退款(可完整预览的文档不适用该条件!)。
- 3、如文档侵犯您的权益,请联系客服反馈,我们会尽快为您处理(人工客服工作时间:9:00-18:30)。
焊接空心球对接焊缝超声波探伤中
探头折射角选用及缺陷定位的浅述
周文超石约翰
摘要以国标GB11345-89和行标JG/T3034·1-1996为依据论述对空心焊接球对接焊缝超声波探测时探头有效折射角必须进行科学选择,缺陷定位必须进行计算的叙述。
关键词空心焊接球超声波探伤有效折射角内曲面反射角缺陷弧长位置实际埋藏位置
引言
在制造安装大中型钢网架结构中,因工程结构需要较多使用焊接球节点以进一步增加结构的强度和稳定性。
焊接球的制作是由成型的两只空心半球加肋板或加垫板对接组焊而成,其焊缝的内在质量直接影响到网架主体结构的安全性。
因此建设部网架行业据国标《钢结构
上一个反射角γ=70°的正弦值,即β有效=sin-1(βmax·sin70°)=sin-1(βmax·0.939)——
β3=sin·R内/R外=sin·150/170=61.93°
此时β1、β2、β3角度在各自球壳介质内曲面的入射角度都为90°,波型已基本全转换为表面波,沿内曲面表面爬行振动,难以扫查到焊缝的上半部,造成漏检,现用上例三只空心焊接球以不同的折射角βa=61.93°、βb=56.31°入射,在内曲面的入射角γ1、γ2、γ3量值分别为:
a:以折射角βa=61.93°为例量值分别为:
γ1=sin-1·(R内/R外·sinβa)=sin-1·(210/190·sin61.93°)=77.23°
γ2=sin-1·(R内/R外·sinβa)=sin-1·(170/190·sin61.93°)=80.46°
γ3=sin-1·(R内/R外·sinβa)=sin-1·(150/170·sin61.93°)=90°
β4max=sin-1·R内/R外=sin-1·180/200=64.16°
β3max=sin-1·R内/R外=sin-1·160/200=53.13°
γ4=sin-1·(R外/R内·sinβ)=sin-1·(200/180·sin56.3°)=67.58°
γ3=sin-1·(R外/R内·sinβ)=sin-1·(200/160·sin56.3°)=sin-11.04°(大于90°)
从上述计算可知同一角度的探头在同直径球内球面的反射角随壁厚增大而增大,当入角大于90°时将无法与内球面相遇。
综上分析欲对空心钢球焊缝实施超声波探伤,首先对探头的折射角度应进行科学合理的选择,选择中我们引入标准中推荐的内曲面反射角度不大于70°这一推荐值,利用正弦定理得β有效=sin-1R内/R外·0.939(末位数只可省略不宜四舍五入)。
在此,对我认为合理的选择β有效=sin-1R内/R外·0.939进行反证。
仍以图5的R内=160、R外=200的空心焊接球为例进行反推,首先求β有效值
-1-1
则∠O′=sin-1(R外/R内·sinβ)-∠β=∠γ-∠β公式3
又:sin O′/AC=sinβ/R内 AC=R内/sinβ·sin{sin-1(R外/R内·sinβ)-β}=R内/sinβ·sin(γ-β)
在直角△AFC中
FC=AC·cosβ=R内/sinβ·sin{sin-1(R外/R内·sinβ)-β}·cosβ= R内/tgβ·sin (γ-β)
从实际数值计算得知,由(图7)也可以看出FC大于B′C′,这就与常规平板焊缝探测时对波位置的分析有了区别,在对δ厚的平板焊缝探测中,发现反射波的位置在δ处时,我们可以认为是背缝焊角反射,但对壁厚δ的空心焊接球焊缝探测时,发现波的反射在人为标定的δ处时,这绝对是根部或近根部的缺陷反射。
∠ADO=∠FDO=180°-56.3°-11.277°=112.423°
OF = 公式4 = =241.65
EF=R 外-OF=250-241.65=8.35
此时已知缺陷F 点距外表面向圆心8.35mm 处若探测平板焊缝该反射点是在焊缝表面。
E 点的弧长仍需求出:
利用正弦定理先求出∠DOE 的度数,
sin ∠DOE/OF= sin ∠DOE/OF 设∠DOE 为O ”
sinO ”= sin ∠FDO/OF ·DF=sin112.423/241.65·37.2=8.18°
AE 对应的圆心角O AE =∠AOD+∠DOF=11.2778+8.18=19.46°
AE=Φπ/360/∠AOE 公式5
AE=Φπ/360/∠AOE =500·π/360/19.46=84.9
至此,缺陷反射点的位置我们已经知道,它位于入射点(实际操作中入射到探头前沿的弧长可近似认为就是探头前沿距离)起弧长84.9mm 距外表面向圆心8.35mm 处。
综上所述,我们认为空心球对接焊缝的起声波探伤中对缺陷位置的认定绝不等同于常规探测中的认定,它存在一个通过计算确定的过程。
现场操作比较麻烦,目前我们尚未找出简易直观的方法。
在实施检测时,首先应确定该规格空心球所应选用的探头折射角,以免过大,造成根部缺陷漏检,不同规格的焊接球不宜用同一角度探测。
其次宜确定荧光屏上一次反射点和二次反射点的位置及球面上的相应弧长,探测过程中利用模糊概念,先近似评估反射点的位置对超标缺陷再进行计算确定,我们公司做过很多解剖试验,缺陷实际位置与计算误差极小,所以我们认为该方法目前可行。
参考文献
1.水利电力出版社,超声波探伤。
2.GB11345-89钢焊缝手工超声波探伤方法和结果的分析。
3.JG/T3034·1996焊接球节点钢网架焊缝超声波探伤及质量分级法。
FDO
cos OD DF 2-OD DF 22∠•••+423
.112cos 22537.22-22537.222∠•⨯⨯+。