尺寸公差和形位公差
形位公差和尺寸公差的关系
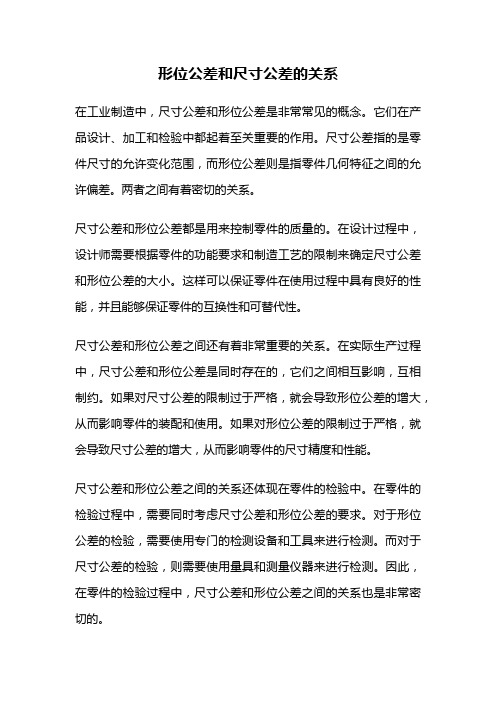
形位公差和尺寸公差的关系
在工业制造中,尺寸公差和形位公差是非常常见的概念。
它们在产品设计、加工和检验中都起着至关重要的作用。
尺寸公差指的是零件尺寸的允许变化范围,而形位公差则是指零件几何特征之间的允许偏差。
两者之间有着密切的关系。
尺寸公差和形位公差都是用来控制零件的质量的。
在设计过程中,设计师需要根据零件的功能要求和制造工艺的限制来确定尺寸公差和形位公差的大小。
这样可以保证零件在使用过程中具有良好的性能,并且能够保证零件的互换性和可替代性。
尺寸公差和形位公差之间还有着非常重要的关系。
在实际生产过程中,尺寸公差和形位公差是同时存在的,它们之间相互影响,互相制约。
如果对尺寸公差的限制过于严格,就会导致形位公差的增大,从而影响零件的装配和使用。
如果对形位公差的限制过于严格,就会导致尺寸公差的增大,从而影响零件的尺寸精度和性能。
尺寸公差和形位公差之间的关系还体现在零件的检验中。
在零件的检验过程中,需要同时考虑尺寸公差和形位公差的要求。
对于形位公差的检验,需要使用专门的检测设备和工具来进行检测。
而对于尺寸公差的检验,则需要使用量具和测量仪器来进行检测。
因此,在零件的检验过程中,尺寸公差和形位公差之间的关系也是非常密切的。
尺寸公差和形位公差是工业制造中非常重要的概念。
它们之间有着密切的关系,相互制约、相互影响。
在设计、加工和检验零件过程中,需要合理地确定它们的大小,以保证零件的质量和性能。
尺寸公差和形位公差关系的公差原则
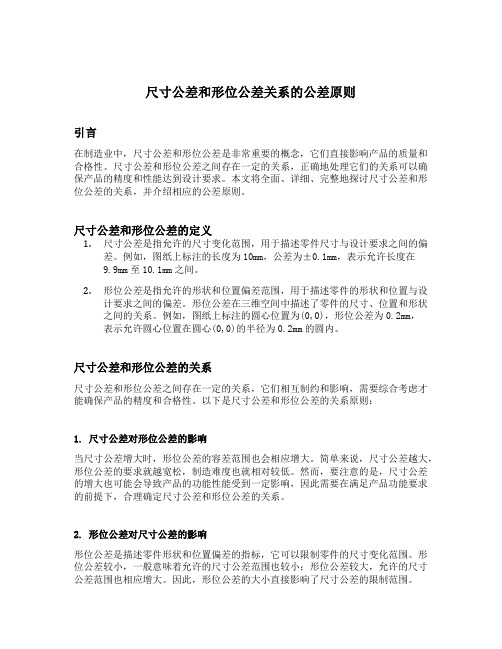
尺寸公差和形位公差关系的公差原则引言在制造业中,尺寸公差和形位公差是非常重要的概念,它们直接影响产品的质量和合格性。
尺寸公差和形位公差之间存在一定的关系,正确地处理它们的关系可以确保产品的精度和性能达到设计要求。
本文将全面、详细、完整地探讨尺寸公差和形位公差的关系,并介绍相应的公差原则。
尺寸公差和形位公差的定义1.尺寸公差是指允许的尺寸变化范围,用于描述零件尺寸与设计要求之间的偏差。
例如,图纸上标注的长度为10mm,公差为±0.1mm,表示允许长度在9.9mm至10.1mm之间。
2.形位公差是指允许的形状和位置偏差范围,用于描述零件的形状和位置与设计要求之间的偏差。
形位公差在三维空间中描述了零件的尺寸、位置和形状之间的关系。
例如,图纸上标注的圆心位置为(0,0),形位公差为0.2mm,表示允许圆心位置在圆心(0,0)的半径为0.2mm的圆内。
尺寸公差和形位公差的关系尺寸公差和形位公差之间存在一定的关系,它们相互制约和影响,需要综合考虑才能确保产品的精度和合格性。
以下是尺寸公差和形位公差的关系原则:1. 尺寸公差对形位公差的影响当尺寸公差增大时,形位公差的容差范围也会相应增大。
简单来说,尺寸公差越大,形位公差的要求就越宽松,制造难度也就相对较低。
然而,要注意的是,尺寸公差的增大也可能会导致产品的功能性能受到一定影响,因此需要在满足产品功能要求的前提下,合理确定尺寸公差和形位公差的关系。
2. 形位公差对尺寸公差的影响形位公差是描述零件形状和位置偏差的指标,它可以限制零件的尺寸变化范围。
形位公差较小,一般意味着允许的尺寸公差范围也较小;形位公差较大,允许的尺寸公差范围也相应增大。
因此,形位公差的大小直接影响了尺寸公差的限制范围。
3. 综合考虑尺寸公差和形位公差为了确保产品的质量和合格性,需要综合考虑尺寸公差和形位公差的关系。
在设计过程中,可以通过优化尺寸公差和形位公差的组合,来实现既满足产品功能要求,又提高零件的制造可行性和成本控制。
公差 形位公差与尺寸公差的关系

Dfe Dfe Dfe DM
+0.025
+
H7
0
-
h6Leabharlann φ40-0.016
最大实体边界
dfe dfe dfe dM
为保证配合性质,用最大实体尺寸控制体外作用尺寸 的公差原则——包容原则
第三章 形位公差与尺寸公差的关系
包容原则
含义—用最大实体边界控制被测要素的实际轮廓 应用—保证配合性质的场合 标注—无形位公差,尺寸公差后加 E
最大实体边界(MMB)
等于最大实体尺寸的边界
第三章 形位公差与尺寸公差的关系
最小实体状态(LMC)
处于极限尺寸 具有最小实体 ——材料最少
最小实体尺寸(LMS) ——保证材料最少极限尺寸
对孔: 最大极限尺寸 DL = Dmax 对轴: 最小极限尺寸 dL = dmin
dfe da da da
0.013
当零件与其他零件配合时,起作用 的尺寸不再是局部实际尺寸,而是 体外作用尺寸
第三章 形位公差与尺寸公差的关系
体外作用尺寸
被测要素的给定长度上,与实际内表面体外相接的最大理想面 或与实际外表面体外相接的最小理想面的直径或宽度
装配过程中起作用的尺寸 实际尺寸与形位误差综合作用的结果 存在于零件上,而不是图纸上
检测合格条件:
⎧⎨⎩dmifn形≤位d≤a
≤ dmax t形位
⎧ ⎨ ⎩
Dmin ≤ Da f形位 ≤
≤ Dmax t形位
0.02
检测方法:—两点法测量
小批量:卡尺、千分尺 大批量: 卡规、塞规
0 -0.033
20
第三章 形位公差与尺寸公差的关系
尺寸公差形位公差表面粗糙度

尺寸公差形位公差表面粗糙度
尺寸公差、形位公差和表面粗糙度是机械制造过程中重要的质量指标。
1. 尺寸公差:是设计者为了控制加工后零件的实际尺寸与理想尺寸之间的误差所规定的标准。
它包括上下偏差(最大和最小极限偏差),通常以尺度(如毫米或英寸)或比例(如千分之一)来表示。
尺寸公差的主要目标是确保每个制造的零件都位于理想的尺寸范围内,从而确保其功能和互换性。
2. 形位公差:是用来控制加工后零件的形状和相对位置的标准。
这包括诸如圆柱度、圆度、平行度、垂直度、同轴度等形状公差,以及位置度、轮廓度和对称度等位置公差。
形位公差的主要目标是确保每个零件的形状和相对位置都符合设计要求,从而确保其使用性能和互换性。
3. 表面粗糙度:是用来描述加工表面微观几何特性的参数,如表面的纹理、峰谷深度和间距等。
它主要影响零件的摩擦性能、密封性能和外观质量等。
表面粗糙度通常通过比较样板或使用仪器进行测量。
对于一些高精度和高质量要求的零件,如液压件、密封件和配合件等,表面粗糙度的控制非常重要。
在机械制造过程中,尺寸公差、形位公差和表面粗糙度的控制都是至关重要的。
它们不仅决定了零件的基本精度和质量,还影响了产品的性能、可靠性和成本。
因此,对于制造者来说,理解并掌握这些概念及其之间的关系是非常重要的。
如需了解更多关于这三者的信息,建议查阅机械制造领域相关书籍或咨询专业人士。
形位公差与尺寸公差

最大实体实效边界 39.9
最大实体要求的两种特殊应用
当给出的形位公差值为零时,则为零形位公差。 此时,被测要素的最大实体实效边界等于最大 实体边界,最大实体实效尺寸等于最大实体尺 寸。 当形位误差小于给出的形位公差,又允许其实 际尺寸超出最大实体尺寸时,可将可逆要求应 用于最大实体要求。从而实现尺寸公差与形位 公差相互转换的可逆要求。此时,在形位公差 框格中最大实体要求的形位公差值后加注 GO “ R ”。
可逆要求(最大实体要求)举例
如图所示,轴线的直线度公差采用可逆的最大实体要求,其含义: 当轴的实际尺寸偏离最大实体尺寸时,其轴的直线度公差增大, 当轴的实际尺寸处处为最小实体尺寸ø 19.7mm,其轴的直线度误 差可达最大值,为t=0.3+0.1=0.4mm。 当轴的轴线直线度误差小于给定的直线度公差时,也允许轴的实 际尺寸超出其最大实体尺寸,(但不得超出其最大实体实效尺寸 20.1mm)。故当轴线的直线度误差值为零时,其实际尺寸可以 0.4 直线度 等于最大实体实效尺寸,即其尺寸公差可达到最大值 Td=0.3+0.1= 0.4mm 。 Ø200-0.3
ø 0 M A
Home
A
可逆要求(最大实体要求)
可逆要求应用于最大实体要求时,被测 要素的实际轮廓应遵守最大实体实效边 界,当其实际尺寸偏离最大 实体尺寸时, 允许其形位误差得到补偿,而当其形位 误差小于给出的形位公差时,也允许其 实际尺寸超出最大实体尺寸,即其尺寸 公差值可以增大,这种要求称之为“可 逆的最大实体要求”,在图样上的形位 公差框格中的形位公差后加注符号M R 。
最大实体实效尺寸(单一要素)
最大实体实效尺寸(关联要素)
最小实体实效状态(尺寸、边界)
尺寸公差、形位公差、表面粗糙度三者的关系
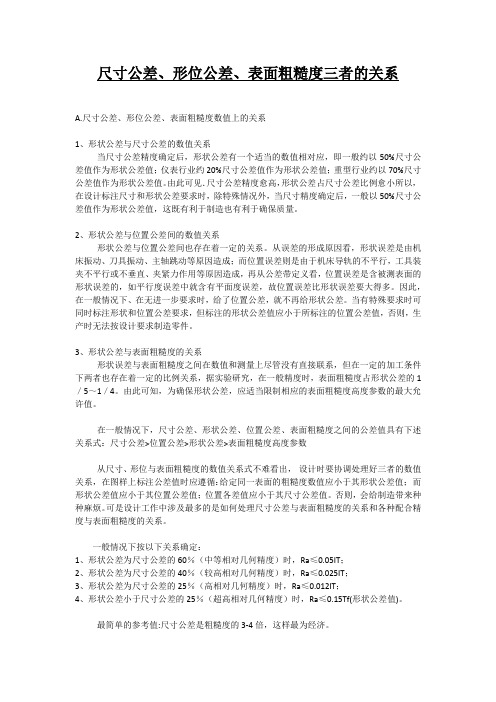
尺寸公差、形位公差、表面粗糙度三者的关系A.尺寸公差、形位公差、表面粗糙度数值上的关系1、形状公差与尺寸公差的数值关系当尺寸公差精度确定后,形状公差有一个适当的数值相对应,即一般约以50%尺寸公差值作为形状公差值;仪表行业约20%尺寸公差值作为形状公差值;重型行业约以70%尺寸公差值作为形状公差值。
由此可见.尺寸公差精度愈高,形状公差占尺寸公差比例愈小所以,在设计标注尺寸和形状公差要求时,除特殊情况外,当尺寸精度确定后,一般以50%尺寸公差值作为形状公差值,这既有利于制造也有利于确保质量。
2、形状公差与位置公差间的数值关系形状公差与位置公差间也存在着一定的关系。
从误差的形成原因看,形状误差是由机床振动、刀具振动、主轴跳动等原因造成;而位置误差则是由于机床导轨的不平行,工具装夹不平行或不垂直、夹紧力作用等原因造成,再从公差带定义看,位置误差是含被测表面的形状误差的,如平行度误差中就含有平面度误差,故位置误差比形状误差要大得多。
因此,在一般情况下、在无进一步要求时,给了位置公差,就不再给形状公差。
当有特殊要求时可同时标注形状和位置公差要求,但标注的形状公差值应小于所标注的位置公差值,否则,生产时无法按设计要求制造零件。
3、形状公差与表面粗糙度的关系形状误差与表面粗糙度之间在数值和测量上尽管没有直接联系,但在一定的加工条件下两者也存在着一定的比例关系,据实验研究,在一般精度时,表面粗糙度占形状公差的1/5~1/4。
由此可知,为确保形状公差,应适当限制相应的表面粗糙度高度参数的最大允许值。
在一般情况下,尺寸公差、形状公差、位置公差、表面粗糙度之间的公差值具有下述关系式:尺寸公差>位置公差>形状公差>表面粗糙度高度参数从尺寸、形位与表面粗糙度的数值关系式不难看出,设计时要协调处理好三者的数值关系,在图样上标注公差值时应遵循:给定同一表面的粗糙度数值应小于其形状公差值;而形状公差值应小于其位置公差值;位置各差值应小于其尺寸公差值。
尺寸公差形位公差、表面粗糙度数值上的关系
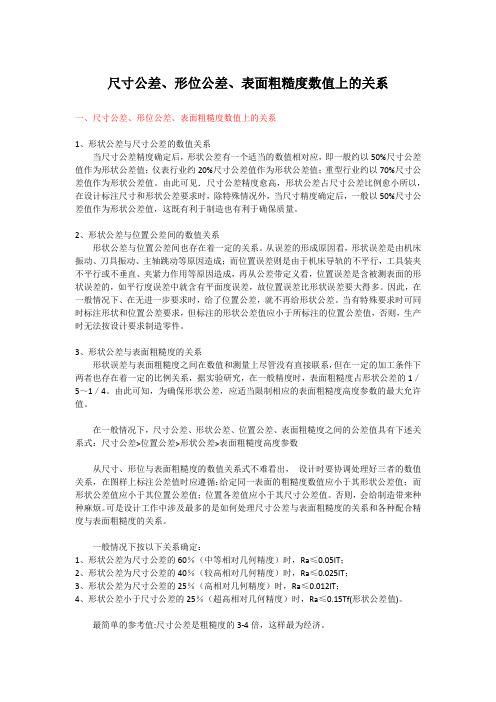
尺寸公差、形位公差、表面粗糙度数值上的关系一、尺寸公差、形位公差、表面粗糙度数值上的关系1、形状公差与尺寸公差的数值关系当尺寸公差精度确定后,形状公差有一个适当的数值相对应,即一般约以50%尺寸公差值作为形状公差值;仪表行业约20%尺寸公差值作为形状公差值;重型行业约以70%尺寸公差值作为形状公差值。
由此可见.尺寸公差精度愈高,形状公差占尺寸公差比例愈小所以,在设计标注尺寸和形状公差要求时,除特殊情况外,当尺寸精度确定后,一般以50%尺寸公差值作为形状公差值,这既有利于制造也有利于确保质量。
2、形状公差与位置公差间的数值关系形状公差与位置公差间也存在着一定的关系。
从误差的形成原因看,形状误差是由机床振动、刀具振动、主轴跳动等原因造成;而位置误差则是由于机床导轨的不平行,工具装夹不平行或不垂直、夹紧力作用等原因造成,再从公差带定义看,位置误差是含被测表面的形状误差的,如平行度误差中就含有平面度误差,故位置误差比形状误差要大得多。
因此,在一般情况下、在无进一步要求时,给了位置公差,就不再给形状公差。
当有特殊要求时可同时标注形状和位置公差要求,但标注的形状公差值应小于所标注的位置公差值,否则,生产时无法按设计要求制造零件。
3、形状公差与表面粗糙度的关系形状误差与表面粗糙度之间在数值和测量上尽管没有直接联系,但在一定的加工条件下两者也存在着一定的比例关系,据实验研究,在一般精度时,表面粗糙度占形状公差的1/5~1/4。
由此可知,为确保形状公差,应适当限制相应的表面粗糙度高度参数的最大允许值。
在一般情况下,尺寸公差、形状公差、位置公差、表面粗糙度之间的公差值具有下述关系式:尺寸公差>位置公差>形状公差>表面粗糙度高度参数从尺寸、形位与表面粗糙度的数值关系式不难看出,设计时要协调处理好三者的数值关系,在图样上标注公差值时应遵循:给定同一表面的粗糙度数值应小于其形状公差值;而形状公差值应小于其位置公差值;位置各差值应小于其尺寸公差值。
形位公差与尺寸公差的关系

形位公差与尺寸公差的关系一、基本概念公差原则的定义定义:处理尺寸公差和形位公差关系的规定。
分类:1、体外作用尺寸单一要素的作用尺寸简称作用尺寸MS。
是实际尺寸和形状误差的综合结果。
在被测要素的给定长度上,与实际内表面(孔)体外相接的最大理想面,或与实际外表面(轴)体外相接的最小理想面的直径或宽度,称为体外作用尺寸,即通常所称作用尺寸。
图例局部实际尺寸和单一要素的体外作用尺寸2、关联要素的体外作用尺寸是局部实际尺寸与位置误差综合的结果。
是指结合面全长上,与实际孔内接(或与实际轴外接)的最大(或最小)的理想轴(或孔)的尺寸。
而该理想轴(或孔)必须与基准要素保持图样上给定的功能关系。
图例关联体外作用尺寸3、体内作用尺寸在被测要素的给定长度上,与实际内表面(孔)体内相接的最小理想面,或与实际外表面(轴)体内相接的最大理想面的直径或宽度,称为体内作用尺寸。
4、最大实体状态(尺寸、边界)最大实体状态(MMC):实际要素在给定长度上具有最大实体时的状态。
最大实体尺寸(MMS):实际要素在最大实体状态下的极限尺寸。
(轴的最大极限尺寸dmax,孔的最小极限尺寸Dmin)边界:由设计给定的具有理想形状的极限包容面。
最大实体边界:尺寸为最大实体尺寸的边界。
5、最大实体实效状态(尺寸、边界)MMVC:在给定长度上,实际要素处于最大实体状态且其中心要素的形状或位置误差等于给出的形位公差值时的综合极限状态。
MMVS:最大实体实效状态下的体外作用尺寸。
MMVS=MMS±t形·位其中:对外表面取“+”;对内表面取“-”dMV =dfe=da+f =dM + t =dmax + tDMV=Dfe=Da-f =DM–t =Dmin- t最大实体实效边界:尺寸为最大实体实效尺寸的边界。
最大实体实效尺寸(单一要素)最大实体实效尺寸(关联要素)6、最小实体实效状态(尺寸、边界)LMVC:在给定长度上,实际要素处于最小实体状态且其中心要素的形状或位置误差等于给出的形位公差值时的综合极限状态,称为最小实体实效状态。
尺寸公差和形位公差关系的公差原则

尺寸公差和形位公差关系的公差原则尺寸公差和形位公差是机械制造中非常重要的两个概念,它们在保证产品质量、提高生产效率、降低成本等方面都起到了关键作用。
本文将从尺寸公差和形位公差的基本概念入手,深入探讨它们之间的关系,总结出尺寸公差和形位公差关系的公差原则。
一、尺寸公差和形位公差的基本概念1. 尺寸公差尺寸公差是指零件各个尺寸之间允许的最大偏离量。
通俗地说,就是指零件实际尺寸与设计要求之间的偏离量。
一般来说,尺寸公差包括上限偏差和下限偏差两种。
2. 形位公差形位公差是指零件各个特定点之间允许的最大偏移量或旋转角度。
通俗地说,就是指零件实际位置与设计要求之间的偏移量或旋转角度。
形位公差可以分为平面形位公差和轴向形位公差两种。
二、尺寸公差和形位公差的关系尺寸公差和形位公差在机械制造中都是非常重要的概念。
它们之间的关系可以从以下几个方面来分析。
1. 形位公差对尺寸公差的影响形位公差可以对零件的尺寸公差产生影响。
一般来说,如果一个零件的形位公差比较大,那么它所允许的偏移量或旋转角度也就比较大,这就会导致其尺寸公差变大。
因此,在进行机械制造时,需要根据设计要求合理设置形位公差,以保证零件的尺寸精度。
2. 尺寸公差对形位公差的影响尺寸公差也可以对零件的形位精度产生影响。
一般来说,如果一个零件的尺寸公差比较大,那么它所允许的偏移量或旋转角度也就比较大,这就会导致其形位精度变低。
因此,在进行机械制造时,需要根据设计要求合理设置尺寸公差,以保证零件的形位精度。
3. 尺寸和形位之间的综合考虑在进行机械制造时,需要综合考虑尺寸公差和形位公差,以确定最终的公差要求。
一般来说,如果一个零件的形位精度要求比较高,那么其尺寸公差就要比较小;反之,如果一个零件的形位精度要求比较低,那么其尺寸公差就可以适当放大。
因此,在进行机械制造时,需要根据具体情况灵活设置尺寸公差和形位公差。
三、尺寸公差和形位公差关系的公差原则根据以上分析,可以总结出以下几个原则:1. 形位精度要求高的零件应该设置较小的尺寸公差。
形位公差和尺寸公差

形状公差和位置公差简称为形位公差(1)形状公差:构成零件的几何特征的点,线,面要素之间的实际形状相对与理想形状的允许变动量。
给出形状公差要求的要素称为被测要素。
(2)位置公差:零件上的点,线,面要素的实际位置相对与理想位置的允变动量。
用来确定被测要素位置的要素称为基准要素。
形位公差是为了满足产品功能要求而对工件要素在形状和位置方面所提出的几何精度要求。
以形位公差带来限制被测实际要素的形状和位置。
形位误差对零件使用性能的影响1.影响零件的功能要求。
2.影响零件的配合性质。
3.影响零件的互换性。
现行国家标准GB/T 1182—1996《形状和位置公差通则、定义、符号和图样表示法》。
GB/T 1184—1996《形状和位置公差未注公差值》。
GB/T 4249—1996《公差原则》。
GB/T 16671—1996《形状和位置公差最大实体要求、最小实体要求和可逆要求》。
GB13319—1991《形状和位置公差位置度公差》。
同轴度:是定位公差,理论正确位置即为基准轴线.由于被测轴线对基准轴线的不同点可能在空间各个方向上出现,故其公差带为一以基准轴线为轴线的圆柱体,公差值为该圆柱体的直径,在公差值前总加注符号“φ”.转载!!!!!!尺寸公差简称公差,是指最大极限尺寸减最小极限尺寸之差的绝对值,或上偏差减下偏差之差。
它是容许尺寸的变动量。
尺寸公差是一个没有符号的绝对值。
极限偏差=极限尺寸-基本尺寸,上偏差=最大极限尺寸-基本尺寸,下偏差=最小极限尺寸-基本尺寸。
编辑本段什么是尺寸公差尺寸公差是指在切削加工中零件尺寸允许的变动量。
在基本尺寸相同的情况下,尺寸公差愈小,则尺寸精度愈高。
尺寸公差等于最大极限尺寸与最小极限尺寸之差,或等于上偏差与下偏差之差。
编辑本段尺寸公差的概念零件在制造过程中,由于加工或测量等因素的影响,完工后的实际尺寸总存在一定的误差。
为保证零件的互换性,必须将零件的实际尺寸控制在允许变动的范围内,这个允许的尺寸变动量称为尺寸公差。
尺寸和形位公差

尺寸与尺寸公差
尺寸公差对外形控制 举例 a. 外部特征如Pin的控制
早期标识
现在标识
一、尺寸与尺寸公差
7)最大实体状态(MMC) a. 特征包含最多材料时的状态(孔径最小,轴径最大); b. 对于外部特征,尺寸处于最大极限尺寸(最大实体尺寸),如下图; c. 对于内部特征,尺寸处于最小极限尺寸(最大实体尺寸),如下图;
一、尺寸与尺寸公差
8)最小实体状态(LMC) a. 特征包含最少材料时的状态(孔最大,轴最小); b. 对于外部特征,尺寸处于最小极限尺寸(最小实体尺寸),如下图; c. 对于内部特征,尺寸处于最大极限尺寸(最小实体尺寸),如下图;
8. 同轴度(REFER ONLY)
公差带是直径为公差值t,且与基准轴线同轴的圆柱面内的区域。
Example 1
d
D
0.1
0.1
基准轴线
被测轴线
表示零件上两对称中心要素保持在同一平面内的状况。
对称度
公差带是距离为公差值t,且相对基准中心平面(或中心线、轴线)对称 配置的两平行平面(或直线)之间的区域。若给定互相垂直的两个方向,则 是正截面为公差值t1 X t2的四棱柱内的区域。
Example 3
圆柱d的轴线必须位于直径为公差值0.05mm,且垂直于基准平面的圆柱面内。 A 0.05 A d 基准平面 圆柱轴线 0.05
表示零件上两要素相对方向保持任意给定角度的正确状况。
7. 倾斜度 (REFER ONLY)
形位公差与尺寸公差的关系
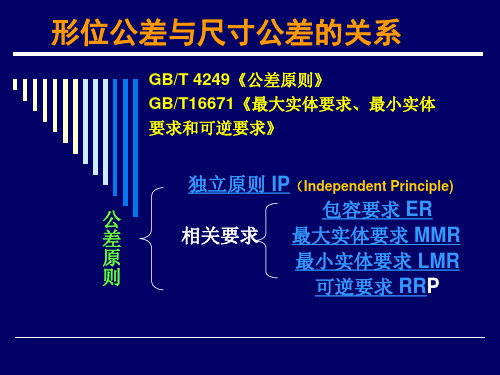
轴类零件形位公差项目的选择
➢ 与支承件结合部位
a、轴颈的圆度或圆柱度。 b、对公共轴线的圆跳动或同
轴度。 c、轴肩对轴线的端面圆跳动
(或垂直度)。
➢与传动件结合部位
a、表面的圆度或圆柱度 b、对公共轴线的圆跳动或同 轴度 c、轴肩对其轴线的垂直度( 或端面圆跳动) d、键槽对其轴线的对称度。
➢形位公差各项目的应用示例:见表2-9~表2-12 ➢形位公差值的选用原则
1、总的原则是在满足零件功能的前提下,选取最经济的公差 值。
形位公差值的确定
2、根据零件的功能要求,考虑加工的经济性和零件的结构、 刚性,按表中数系确定要素的公差值。并考虑以下因素: a)在同一要素上给出的t形状≤t位置。如要求平行的两个表面, 其平面度公差值应小于平行度公差值;
轴类零件形位公差值的确定
齿轮形位公差值的确定
箱体类零件形位公差值的确定
形位公差的未注公差值(GB/T 1184-1996)
为简化制图,对一般机床加工就能保证的形位精度,不必 在图样上注出形位公差,形位未注公差按以下规定执行:
➢ 未注直线度、平面度、垂直度、对称度和圆跳动(表213~表2-16)各规定了H、K、L三个公差等级,在标题栏 或技术要求中注出标准及等级代号。如:“GB/T1184—
➢其它
齿轮类零件形位公差项目的选择
GB10095-1988《齿轮公差》有专门规定:
➢齿轮孔(或轴)的圆度 或圆柱度
➢齿轮键槽对其轴线的对 称度
➢齿轮基准端面对轴线的 垂直度 ➢齿顶圆对轴线的圆跳动
箱体类零件形位公差项目的选择
轴承座孔的圆度或 圆柱度
轴承座孔轴线的同 轴度
形位公差与尺寸公差的关系

外相接的最大理想面的直径或宽度。对于关联要素,该 理想面的轴线或中心平面必须与基准保持图样给定的几 何关系。
dfe= da+ f Dfe=Da-f
f 表示形位误差
dfe da1 da2 da3 dfi
Dfe Da1 Da2 Da3 Dfi
2020/8/2
2020/8/2
返回本章
结束
可逆要求用于最大实体要求
• 标注方法
0.05 M R
20.05(dMV) 20.02(dM)
200-0.03
0.03
2020/8/2
返回本章
0.08
0.07 0.06 0.05
0.03
19.97(d-L0).03 -0.02-0.010 20(dM) 20.02 20.05(dMV)
第四节 形位公差与尺寸公差的关系
定义:机械零件的同一被测要素既有尺寸公 差要求,又有形位公差要求,处理两者之间 关系的原则,称为公差原则。
一.有关术语及定义
1.局部实际尺寸(简称实际尺寸da、Da) 在实际要素的任意正截面上,两对应点之 间测得的距离。
2020/8/2
返回本章
结束
2. 作用尺寸
(1)体外作用尺寸(dfe、Dfe) 在被测要素的给定长度上,
2020/8/2
返回本章
结束
20(dM) 19.97(dL)
0.03
标注
直线度/mm 0.03 0.02
0.01
最大实体边界
19.97(dL) 20(dM)
0 实际尺寸/mm
直线度误差的动 态变动范围
2020/8/2
图4-7包容要求
形位公差和尺寸公差的关系
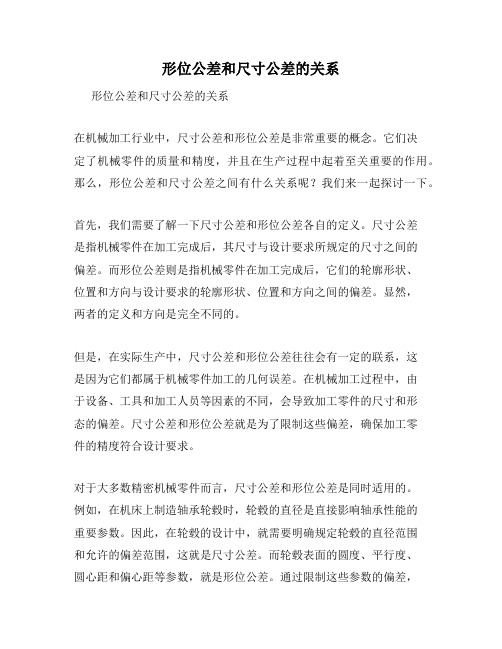
形位公差和尺寸公差的关系形位公差和尺寸公差的关系在机械加工行业中,尺寸公差和形位公差是非常重要的概念。
它们决定了机械零件的质量和精度,并且在生产过程中起着至关重要的作用。
那么,形位公差和尺寸公差之间有什么关系呢?我们来一起探讨一下。
首先,我们需要了解一下尺寸公差和形位公差各自的定义。
尺寸公差是指机械零件在加工完成后,其尺寸与设计要求所规定的尺寸之间的偏差。
而形位公差则是指机械零件在加工完成后,它们的轮廓形状、位置和方向与设计要求的轮廓形状、位置和方向之间的偏差。
显然,两者的定义和方向是完全不同的。
但是,在实际生产中,尺寸公差和形位公差往往会有一定的联系,这是因为它们都属于机械零件加工的几何误差。
在机械加工过程中,由于设备、工具和加工人员等因素的不同,会导致加工零件的尺寸和形态的偏差。
尺寸公差和形位公差就是为了限制这些偏差,确保加工零件的精度符合设计要求。
对于大多数精密机械零件而言,尺寸公差和形位公差是同时适用的。
例如,在机床上制造轴承轮毂时,轮毂的直径是直接影响轴承性能的重要参数。
因此,在轮毂的设计中,就需要明确规定轮毂的直径范围和允许的偏差范围,这就是尺寸公差。
而轮毂表面的圆度、平行度、圆心距和偏心距等参数,就是形位公差。
通过限制这些参数的偏差,可以保证轮毂转动时与其它机械零件的加工精度相匹配。
但是,也有一些机械零件只需要尺寸公差或者形位公差的其中之一。
例如,机械零件的尺寸比形状更为重要,比如常见的螺母、螺栓等,此时只需要给出尺寸公差,而形位公差则可以忽略。
相反,如果对于某些机械零件的形状更为重要,比如发动机活塞、汽缸等,则只需要给出形位公差,而尺寸公差则可由形位公差派生出来。
因此,尺寸公差和形位公差的关系并非固定不变的。
根据不同的机械零件、不同的加工方式以及不同的设计要求,它们之间的联系也会有所不同。
综上所述,尺寸公差和形位公差在机械加工行业中都是非常重要的概念。
它们分别限制了机械零件的尺寸偏差和形态偏差,确保加工零件的精度符合设计要求。
尺寸公差和形位公差关系
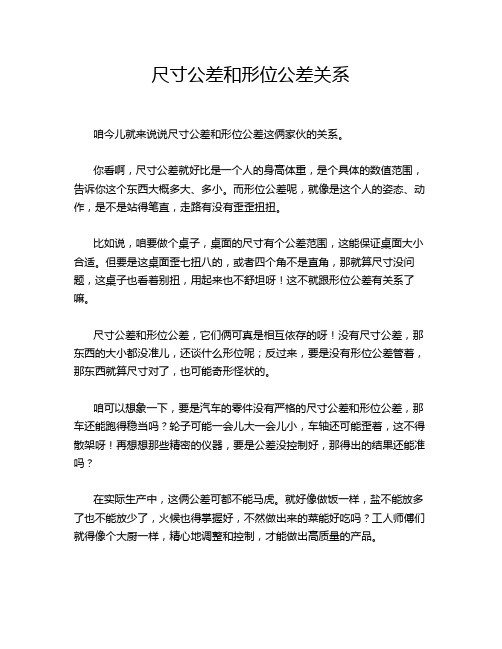
尺寸公差和形位公差关系咱今儿就来说说尺寸公差和形位公差这俩家伙的关系。
你看啊,尺寸公差就好比是一个人的身高体重,是个具体的数值范围,告诉你这个东西大概多大、多小。
而形位公差呢,就像是这个人的姿态、动作,是不是站得笔直,走路有没有歪歪扭扭。
比如说,咱要做个桌子,桌面的尺寸有个公差范围,这能保证桌面大小合适。
但要是这桌面歪七扭八的,或者四个角不是直角,那就算尺寸没问题,这桌子也看着别扭,用起来也不舒坦呀!这不就跟形位公差有关系了嘛。
尺寸公差和形位公差,它们俩可真是相互依存的呀!没有尺寸公差,那东西的大小都没准儿,还谈什么形位呢;反过来,要是没有形位公差管着,那东西就算尺寸对了,也可能奇形怪状的。
咱可以想象一下,要是汽车的零件没有严格的尺寸公差和形位公差,那车还能跑得稳当吗?轮子可能一会儿大一会儿小,车轴还可能歪着,这不得散架呀!再想想那些精密的仪器,要是公差没控制好,那得出的结果还能准吗?在实际生产中,这俩公差可都不能马虎。
就好像做饭一样,盐不能放多了也不能放少了,火候也得掌握好,不然做出来的菜能好吃吗?工人师傅们就得像个大厨一样,精心地调整和控制,才能做出高质量的产品。
有时候我就想啊,这公差就跟人一样,每个人都有自己的特点和局限,但只要在合理的范围内,就能发挥出自己的作用。
而且啊,它们相互配合好了,才能让整个系统正常运转。
你说这尺寸公差和形位公差是不是很重要啊?它们就像一对好兄弟,相互扶持,共同为了产品的质量而努力。
要是其中一个掉链子,那可就麻烦啦!所以啊,咱们可得重视它们,不能小瞧了这看似简单却又极其关键的东西。
总之,尺寸公差和形位公差紧密相连,缺一不可。
只有把它们都抓好了,我们才能制造出完美的产品,让生活变得更加美好呀!。
几何精度设计期末复习重点6-形位公差与尺寸公差
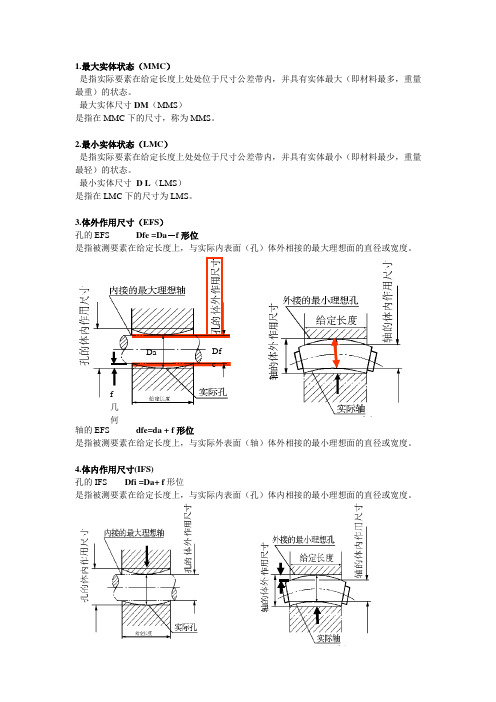
1.最大实体状态(MMC )是指实际要素在给定长度上处处位于尺寸公差带内,并具有实体最大(即材料最多,重量最重)的状态。
最大实体尺寸DM (MMS )是指在MMC 下的尺寸,称为MMS 。
2.最小实体状态(LMC )是指实际要素在给定长度上处处位于尺寸公差带内,并具有实体最小(即材料最少,重量最轻)的状态。
最小实体尺寸 D L (LMS )是指在LMC 下的尺寸为LMS 。
3.体外作用尺寸(EFS )孔的EFS Dfe =Da -f 形位是指被测要素在给定长度上,与实际内表面(孔)体外相接的最大理想面的直径或宽度。
轴的EFS dfe=da + f 形位是指被测要素在给定长度上,与实际外表面(轴)体外相接的最小理想面的直径或宽度。
4.体内作用尺寸(IFS)孔的IFS Dfi =Da+ f 形位是指被测要素在给定长度上,与实际内表面(孔)体内相接的最小理想面的直径或宽度。
Da Df e f几何轴的IFS dfi =da - f 形位是指被测要素在给定长度上,与实际外表面(轴)体内相接的最大理想面的直径或宽度。
5.最大实体实效状态(MMVC)是指实际要素在给定长度上处于MMC ,且其中心要素的 f 形位= t 形位 时综合状态。
最大实体实效尺寸(MMVS)指在MMVC 下的尺寸对轴 dMV= dM + t 形位 dfe=da+ f 形位对孔 DMV= DM –t 形位 Dfe=Da -f 形位6.最小实体实效状态(LMVC)是指实际要素在给定长度上处于LMC ,且其中心要素的f 形位= t 形位时综合状态。
最小实体实效尺寸(LMVS)是指在LMVC 下的尺寸对轴 dLV =dL –t 形位对孔 DLV=DL+t 形位7.边界边界是设计给定的具有理想形状的极限包容面(既包括内表面,也包括外表面) 边界尺寸(BS )是指理想形状的极限包容面的直径或宽度。
(1)最大实体边界(MMB )具有理想形状且边界尺寸(BS )为MMS 的包容面。
尺寸公差与形位公差的关系
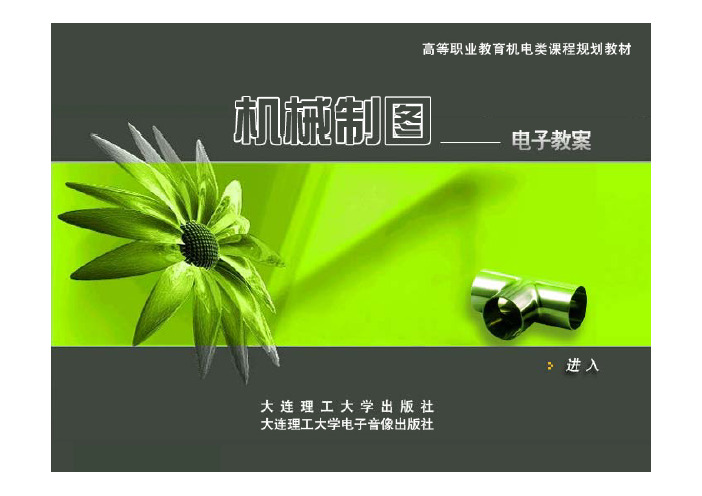
•目的:掌握尺寸公差与行为公差之间关系•重点:公差各项原则难点公差原则的含义•难点:公差原则的含义6.4.4 形位公差与尺寸公差的关系同一个被测要素上,既有尺寸公差又有形位公差要求时,确定尺寸公差与形位公差之间相互关系的原则,称为公差原则。
它分为独立原则和相关要求。
1.有关术语及定义(1)局部实际尺寸(简称实际尺寸)在实际要素的正截面上,两测量点之间测得的距离。
内表面的实际尺寸用D a 表示,外表面的实际尺寸用D a 表示。
(2)体外作用尺寸在被测要素的给定长度上,与实际内表面体外接触的最大理想面或与实际外表面体外接触的最小理想面的直径或宽度。
见图6-37,孔的体外作用尺寸用D f e 表示,轴的体外作用尺寸用D f e 表示。
体外作用尺寸对零件的装配起作用。
图6-37 体外作用尺寸(3)体内作用尺寸在被测要素的给定长度上,与实际内表面体内相接的最小理想面或与实际外表面体内相接的最大理想面的直径或宽度。
如图6-38所示,孔的体外作用尺寸用D f i 表示,轴的体外作用尺寸用d f i 表示。
体内作用尺寸对零件的强度起作用。
6-38 图体内作用尺寸注意:体外作用尺寸和体内作用尺寸是由实际尺寸和形位误差综合形成的,对于每个零件不尽相同。
(4)最大实体状态、最大实体尺寸、最大实体边界实际要素在给定长度上处处位于尺寸极限之内,并具有实体最大时的状态称为实体最大状态,用MMC 表示。
实际要素在最大实体状态下的尺寸称为最大实体尺寸,用MMS 表示。
对于外表面为最大极寸用表内表面为最小极寸用表为最大极限尺寸,用d M 表示,内表面为最小极限尺寸用D M 表示,即D M =d max ,D M =D min 由设计者给定的具有理想形状的极限包容面称为边界。
边界的尺寸为极限包容面的直径或距离。
尺寸为最大实体尺寸的边界称为最大实体边界,用MMB 表示。
(5)最小实体状态、最大实体尺寸、最小实体边界实际要素在给定长度上处处位于尺寸极限之内,并具有实体最小时的状态称为实体最小状态,用LMC 表示。
- 1、下载文档前请自行甄别文档内容的完整性,平台不提供额外的编辑、内容补充、找答案等附加服务。
- 2、"仅部分预览"的文档,不可在线预览部分如存在完整性等问题,可反馈申请退款(可完整预览的文档不适用该条件!)。
- 3、如文档侵犯您的权益,请联系客服反馈,我们会尽快为您处理(人工客服工作时间:9:00-18:30)。
1.完成装配图草图设计
一、图面布置 1)根据传动零件的设计尺寸,同时考虑到传动零件 之间的位置尺寸以及它们距箱体内壁之间的尺寸, 初步估计选用几号图纸。 2)按机械制图的规定在选定的图纸上,绘出外框线 及标题栏,具体尺寸按国家制图标准 3)在图纸的有效面积内,安排三个视图的位置,同 时要考虑编写技术要求和零件明细表所需要的图面 空间,4)根据传动零件(轴、齿轮、蜗杆、蜗轮等) 的设计尺寸,确定并画出传动零件的中心线位置, 绘制传动零件的轮廓线(如齿顶圆、节圆、齿面宽 等)和箱体的內壁线。
二、装配草图绘制第二阶段
在减速器轴系零件设计计算完成之后,轴的结构形 状以及各段长度和直径即已知,同时也初步选定了 所需联轴器和轴承的型号。在装配底图上就可以把 整个轴的结构尺寸绘制出来。 1)绘出轴的结构尺寸后,即可根据轴上各零件的位 置关系,确定出轴的支承位置和轴上传动零件力的 作用位置,进一步计算轴的支承跨距,作轴的强度 校核计算、轴承的寿命验算以及键联接的强度校核 计算。这一阶段的设计往往交叉在计算和绘图的反 复过程中。 2)通过绘制轴的尺寸,还可以核查与传动零件的设 计尺寸有无干涉,做到及时发现问题,及时修改设 计。
外形尺寸,特性尺寸,安装尺寸,配合尺寸
减速器零件的荐用配合参见手册37页 表4-2
尺寸标注参照手册83页图10-1减速Biblioteka 技术特性 参照P37 页技术特性表
零件序号、标题栏和明细表
具体要求按照手册P117页的表11-1的要 求绘制, 零件序号的标注需按照机械制图要求, 参照P38页要求标注。
一般绘图次序是先箱体,后附件;先主体, 后局部;先轮廓,后细节。画图应在三个视图上 协调进行,以能清楚表达箱体结构的视图为主, 兼顾其他视图。
完成装配图设计
• 经过前面几个阶段的设计,完成了装配草图。但 草图上可能还存在有不合理、不协调,甚至错误 的地方。所以在画装配图前,一定要对草图进行 认真检查,经检查、修改无误后,方可动手绘制 装配图。一般是在装配草图的基础上按照国家制 图标准加工完成。也可重新画图。
• 2)对于薄壁零件,在图面上的尺寸小于 2mm(如视孔盖板下的油垫纸板等)的剖 视图,可用全剖涂黑表示。但未剖到的垫 片等则不应该涂黑。涂黑工作应待所有剖 面线画完,且在零件轮廓线加深后再进行, 以保证图面清晰。
• 3)根据教学要求,装配工作图上某些结构 可用简化画法。参照手册P60-63的表
二、零件工作图设计
第三次布置内容
1. 完成装配图草图设计 2. 完成装配图设计 3. 零件工作图设计和绘制 4. 编写设计计算说明书 5. 答辩准备及答辩
• 装配工作图表达了机器总体结构的设计 、 部件的工作原理和装配关系,也表达出各 零件间的相互位置、尺寸及结构形状。它 是绘制零件工作图、进行部件装配、调试 及维护的技术依据。
• 作为完整的装配图,还应标注出必要的尺 寸、编写技术要求、零件序号、明细表和 标题栏等。
装配图尺寸的标注
装配图是组装各零件的依据,图上应标注的尺寸有: 1)特性尺寸:如传动零件的中心距及其偏差。 2)外形尺寸:如减速器的总长、总宽和总高。 3)安装尺寸:如箱体底座的尺寸(包括长、宽、 厚);地脚螺栓孔中心的定位尺寸;地脚螺栓孔的 中心距和直径;减速器的中心高;主动轴与从动轴 外伸端的配合长度和直径等。 4)配合尺寸:如轴与带轮、链轮、齿轮、蜗轮、 联轴器、轴承的配合尺寸;轴承与轴承座孔的配合 尺寸等。标注这些尺寸的同时应标出配合种类与精 度等级。
2、标注尺寸—— 主要径向尺寸和轴向尺寸。
首先应选好基准面,并尽量使尺寸的标注反映加工工
艺的要求;
不允许出现封闭的尺寸链。
对所有的倒角、圆角都应标注无遗,或在技术要求中 说明。
基准面通常选择在传动零件定位面处或轴的端面处
下图为轴类零件长度尺寸的标注示例,图中2为主要基准
面,1为辅助基准面。注意图中键槽位置的标注方法。
编写技术要求——保证减速器的工作性能。
1.对零件的要求 2.对润滑剂的要求 3.对密封的要求 4.对安装调整的要求 5.对实验的要求 6.对包装、运输及外观的要求
减速器技术条件的具体内容可参考手册图10-1
• 完成正式装配工作图应注意下列几点:
• 1)画剖视图时,不同的零件其剖面线的方 向或间距应不同,而同一零件在几个视图 上的剖面线方向和间距都应该相同。
零件工作图是零件制造、检验和制订工艺规程的 基本技术文件。它既要反映出设计意图,又要考虑 到制造的可能性、合理性和经济性。
零件工作图应包括制造和检验零件所需全部 内容。如图形、尺寸及其公差、表面粗糙度、 形位公差、对材料及热处理的说明及其他技 术要求、标题栏等;
零件的基本结构及主要尺寸应与装配图一致, 不应随意更改。如必须更改,应对装配图作 相应的修改。 从装配图拆零件。
➢设计内容: 1、轴 2、齿轮
➢零件工作图的要求:
正确选择和合理布置视图 合理标注尺寸 标注公差及表面粗糙度 编写技术要求 画出零件工作图标题栏
零件工作图设计
零件工作图设计——轴类零件设计要点 (手册P47~48)
轴类零件工作图的设计要点
设计内容:
1、视图
一般只需一个主视图; 在有键槽和孔的地方——增加必要的局部剖面图; 细小结构(如退刀槽、中心孔)——局部放大图。 设计时用3号图纸,比例自定。
三、装配草图绘制第三阶段
减速器装配底图绘制的第三阶段,主要是画 传动零件和支承零件的具体结构尺寸,同时还要 进行部分箱体结构尺寸的绘制。传动零件和支承 零件的具体结构尺寸设计,在轴设计完成之后, 即可参阅教材和指导书有关内容进行经验性设计, 并结合结构的合理性适当修改。
四、装配草图绘制第四阶段
装配底图绘制的第四阶段,主要是针对箱体 及其附件展开的。本课程设计中,有关箱体及其 附件的设计均是经验性设计,可依据指导书提供 的有关资料及数据。本阶段的绘图约占装配底图 绘制工作量的一半。