氧气底吹法(以此为准)
氧气底吹转炉炼钢

[Mn]的氧化反应几乎达到平衡;
底吹转炉吹炼终点钢水残[Mn]比顶吹转炉高;
残[Mn]比顶吹转炉高的原因: 渣中(FeO)含量低于顶吹转炉,而且CO分压(约0.04MPa)低于顶吹转炉0.12MPa,顶吹转炉中的[O]活度高于底吹转炉2.5倍。 此外,底吹转炉喷嘴上部氧压高,Si氧化为SiO2并被石灰粉中CaO所固定,这样MnO的活度增大。
9.2 底吹氧气转炉炼钢法
氧气转炉炼钢车间
01
氧气转炉炼钢车间
单击此处添加文本具体内容,简明扼要的阐述您的观点,以便观者准确的理解您传达的思想。
氧气转炉炼钢车间
底吹转炉炼钢法的发展
酸性底吹空气转炉炼钢法 贝塞麦发明的酸性底吹空气转炉炼钢法只能脱碳,但不能脱磷、脱硫。
碱性底吹空气转炉 1878年,托马斯发明了碱性底吹空气转炉,用石灰造渣,能较好地进行脱磷,炉渣可做磷肥.
细金属管多孔塞式: 图4-12MHP供气元件 图4-13 MHP—D型 图4-14 新的类环缝管式 1—母体耐火材料; 金属砖结构 细金属管型供气元件 2—细金属管;3—集气箱; 4—进气箱
3
由于脱碳速度快,前期渣中氧化铁低,故脱磷是在脱碳基本结束后(即吹炼后期)进行的。脱硫主要是在吹炼后半期高碱度炉渣形成后进行的。
4
吹炼中期: 铁水中碳大量氧化,氧的脱碳利用率几乎是100 % 。而且铁矿石、铁皮分解出来的氧,也被脱碳反应消耗。这体现了底吹氧气转炉良好的熔池搅拌贯穿整个吹炼过程的特点。所以,渣中(FeO))含量低于LD转炉,铁合金收得率高。
”
将Pco取为一个大气压,则可简化为:
由于Kc随温度的变化不大,在炼钢温度范围内为一定值,用M代表则可写出: M =[%C]·[%O] (8—7) M称为碳氧浓度积,它具有化学反应平衡常数的性质,在一定温度和压力下应是一个常数。
《钢冶金学》_第6章 氧气底吹转炉和顶底复合吹炼转炉炼钢

钢冶金学重庆科技学院王宏丹◆氧气底吹转炉炼钢氧气底吹转炉炼钢OBM法和LWS法吹炼高磷铁水时的成分变化Q-BOP法吹炼过程中钢水和炉渣成分的变化Q-BOP法吹炼过程炉渣成分的变化吹炼终点[C]和[O]的关系图终点[C]和[Mn]的关系Q-BOP和LD炉内渣中(FeO)6.2.1 顶底复吹转炉炼钢工艺类型6.2 顶底复合吹炼转炉的冶金特点6.2.2 顶底复吹转炉的底吹供气和供气元件6.2.3 顶底复吹转炉内的冶金反应6.2.4 冶金效果氧气顶底复吹转炉炼钢在复吹转炉中,了解和掌握底吹气体的性质、冶金行为、合理地确定底吹气体比例,选择和控制底吹供气强度,是复吹转炉获得良好的技术经济指标的重要因素。
底吹气体的冶金行为主要表现在三个方面: 强化熔池搅拌,使钢水成分,温度均匀;加速炉内反应,使渣钢反应界面增大,元素间化学反应和传质过程更加趋于平衡;冷却保护供气元件,使供气元件使用寿命延长。
底吹气体底吹O:需用冷却介质来保护供气元件,会与熔2池中碳发生反应,产生较大的搅拌力。
:可不用冷却剂,会与熔池中碳发生反 底吹CO2应搅拌力较强的气体;会使熔池CO分压增加,不利于超低碳钢冶炼。
、Ar和CO:属中性或惰性气体,供入铁 底吹N2水中不参与熔池内的反应,只起搅拌作用。
底吹气体比例在复吹转炉中,底吹气体量的多少决定熔池内搅拌的强弱程度。
,其底吹 在冶炼超低碳钢种时,即使用底吹O2供气量也要达20%左右;对一些具有特殊功能的复吹工艺(如喷石灰粉、煤粉等),其底吹供气量可达40%。
就一般复吹转炉而言,为了保证脱硫、脱气和渣-钢间反应趋于平衡,在吹炼结束前,也要采用较大的底吹供气来搅拌熔池。
底吹供气强度获得最佳搅拌强度,使熔池混合最均匀。
大量实验研究表明,熔池的混匀程度与搅拌强度有关,而搅拌强度受供气量和底吹元件布置影响。
根据吹炼过程调节供气强度。
复吹转炉的特点是能有效地把熔池搅拌与炉渣氧化性有机统一起来,而实现手段就是控制底吹供气强度。
氧气底吹转炉炼铅法
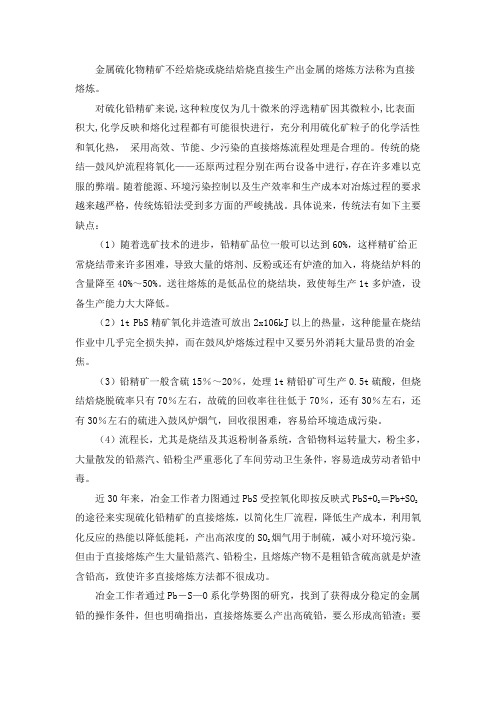
金属硫化物精矿不经焙烧或烧结焙烧直接生产出金属的熔炼方法称为直接熔炼。
对硫化铅精矿来说,这种粒度仅为几十微米的浮选精矿因其微粒小,比表面积大,化学反映和熔化过程都有可能很快进行,充分利用硫化矿粒子的化学活性和氧化热,采用高效、节能、少污染的直接熔炼流程处理是合理的。
传统的烧结—鼓风炉流程将氧化——还原两过程分别在两台设备中进行,存在许多难以克服的弊端。
随着能源、环境污染控制以及生产效率和生产成本对冶炼过程的要求越来越严格,传统炼铅法受到多方面的严峻挑战。
具体说来,传统法有如下主要缺点:(1)随着选矿技术的进步,铅精矿品位一般可以达到60%,这样精矿给正常烧结带来许多困难,导致大量的熔剂、反粉或还有炉渣的加入,将烧结炉料的含量降至40%~50%。
送往熔炼的是低品位的烧结块,致使每生产1t多炉渣,设备生产能力大大降低。
(2)1t PbS精矿氧化并造渣可放出2x106kJ以上的热量,这种能量在烧结作业中几乎完全损失掉,而在鼓风炉熔炼过程中又要另外消耗大量昂贵的冶金焦。
(3)铅精矿一般含硫15%~20%,处理1t精铅矿可生产0.5t硫酸,但烧结焙烧脱硫率只有70%左右,故硫的回收率往往低于70%,还有30%左右,还有30%左右的硫进入鼓风炉烟气,回收很困难,容易给环境造成污染。
(4)流程长,尤其是烧结及其返粉制备系统,含铅物料运转量大,粉尘多,大量散发的铅蒸汽、铅粉尘严重恶化了车间劳动卫生条件,容易造成劳动者铅中毒。
近30年来,冶金工作者力图通过PbS受控氧化即按反映式PbS+O2=Pb+SO2的途径来实现硫化铅精矿的直接熔炼,以简化生厂流程,降低生产成本,利用氧化反应的热能以降低能耗,产出高浓度的SO2烟气用于制硫,减小对环境污染。
但由于直接熔炼产生大量铅蒸汽、铅粉尘,且熔炼产物不是粗铅含硫高就是炉渣含铅高,致使许多直接熔炼方法都不很成功。
冶金工作者通过Pb-S—O系化学势图的研究,找到了获得成分稳定的金属铅的操作条件,但也明确指出,直接熔炼要么产出高硫铅,要么形成高铅渣;要获得含硫低的合格粗铅,就必须还原处理含铅高的直接熔炼炉渣。
氧气底吹转炉炼钢

通过转炉底部的氧气喷嘴,把氧气吹入炉内熔池进行炼钢的方法。
简史?? 氧气底吹转炉始于改造托马斯转炉(见托马斯法)。
西欧富有高磷铁矿资源,用它炼出的生铁含磷高达1.6%~2.0%。
以这种高磷铁水为原料的传统炼钢方法即托马斯法,也即碱性空气底吹转炉法,其副产品钢渣可作磷肥。
对于高磷铁水,托马斯法过去一直是综合技术经济指标较好的一种炼钢方法。
直至20世纪60年代,西欧还存在年产能力约1000万t钢的托马斯炉。
但作为炼钢氧化剂的空气,其中氧气仅占1/5,其余4/5的氮气不仅吸收大量热量,并使钢中氮含量增加,引起低碳钢的脆性。
为此人们一直试图用纯氧代替空气,以改进钢的质量和提高热效率。
但采用氧气后,化学反应区的温度很高,底吹所用氧气喷嘴很快被烧坏。
1965年加拿大空气液化公司为了抑制氧气炼钢产生的大量污染环境的褐色烟尘,试验在氧枪外层通气态或液态冷却剂,取得了预期效果,并同时解决了氧枪烧损快的问题。
1967年联邦德国马克西米利安冶金厂(Maximilianshttte)引进了这项技术,以丙烷为氧喷嘴冷却剂,用于改造容量为24t的托马斯炉,首先试验成功氧气底吹转炉炼钢,取名OBM 法。
1970年法国文代尔一西代尔公司(Wendel—Sidelor?? Co.)的隆巴(Rombas)厂以燃料油为氧喷嘴冷却剂,也成功地将24t托马斯炉改造成氧气底吹转炉,称为LWS法。
随后用氧气底吹氧枪改造的托马斯炉在西欧得到迅速推广,炉容量大多为25~70t,用于高磷铁水炼钢,脱磷仍在后吹期完成,副产品钢渣作磷肥。
1971年美国钢铁公司(U.S.Steel? Corp.)引进COBM法,为了解决经济有效地吹炼低磷生铁和设备大型化问题,在该公司炼钢实验室的30t试验炉上作了系列的中间试验,增加了底部吹氧同时喷吹石灰粉的系统,吹炼低磷普通铁水可在脱碳同时完成脱磷,称为Q—BOP法。
随后,在菲尔菲德(Fairfield)厂和盖里(Gary)厂分别建设了两座200tQ—BOP炉和3座235tQ—BOP炉。
双底吹连续炼铜(中英文)2013.07

氧气底吹炼铜技术Oxygen Bottom BlowingOxygen Bottom Blowing Copper Smelting Technology (SKS)中国恩菲工程技术有限公司China ENFI Engineering Corporation氧气底吹炼铜技术现代炼铜技术Oxygen Bottom Blowing Copper Smelting Technology MODERN SMELTING TECHNOLOGYMODERN SMELTING TECHNOLOGY★诺兰达/特尼恩特炼铜法Noranda/Teniente Smelting Process★奥斯麦特/艾萨炼铜法Ausmelt/ISA Smelting Process★闪速炼铜法Flash Smelting Process★三菱炼铜法Mitsubishi Process★氧气底吹炼铜法SKS Smelting ProcessSKS S lti P★瓦纽科夫/金峰/白银炼铜法Vanukov /Jinfeng/Baiyin Smelting ProcessVanukov/Jinfeng/Baiyin Smelting Process氧气底吹炼铜技术Oxygen Bottom Blowing Copper Smelting Technology 现代炼铜技术MODERN SMELTING TECHNOLOGY 诺兰达/特尼恩特炼铜法(Noranda/Teniente Smelting Process)MODERN SMELTING TECHNOLOGYTENIENTE FURNACE NORANDA FURNACETENIENTE FURNACEMODERN SMELTING TECHNOLOGY诺兰达/特尼恩特炼铜法(Noranda/Teniente Smelting Process)MODERN SMELTING TECHNOLOGY1、诺兰达工艺起源于上个世纪50年代、推广至美国、中国、澳大利亚和智利。
氧气底吹三连炉

氧气底吹三连炉目前,中国已引进世界上最先进的炼铜新工艺有:闪速炉熔炼、艾萨熔炼、奥斯麦特熔炼、诺兰达熔炼等。
国内自主创新的有白银法熔炼、金川合成炉熔炼、东营方圆的氧气底吹熔炼。
后3种都是中国人自己研制的,都具有自主知识产权。
这7种也算世界上较先进的炼铜法。
通过多年的实践,国外的先进技术尚存不足之处,分述如下:1、双闪速炉熔炼法:投资大,专利费昂贵,熔剂和原料先进行磨细再进行深度干燥,需额外消耗能源这不尽合理。
熔炉产出的铜硫需要水碎再干燥再细磨,工序繁杂。
每道工序均难以保证100%回收率,会产生部分机械损失;热态高温铜锍水碎物理热几乎全部损失,水碎后再干燥,再加上炉内大量水套由冷却水带走热量,热能利用也不尽合理。
铜锍水碎需要大量的水冲,增加动力消耗。
破碎、干燥要增加人力和动力的消耗。
这些都是多年来该工艺没有得到大量推广的重要原因。
2、艾萨法和澳斯麦特法均属于顶吹冶炼系列:顶吹都要建立高层厂房,噪音大、高氧浓度低烟气量大、顶吹的氧枪12米长,3天至一周要更换一次,不锈钢消耗量大、投资大、操作不方便。
都用电炉做贫化炉,渣含铜一般大于0.6%不合国情。
3、三菱法的不足4个炉子(熔炼炉、贫化电炉、吹炼炉、阳极炉)自流配置,第一道工序的熔炼炉需要配置在较高的楼层位置,建筑成本相对较高,炉渣采用电炉贫化,弃渣含铜量达0.6%~0.7%,远远高于我国多数大型铜矿开采的矿石平均品位,资源没有得到充分的利用。
4、诺兰达和特尼恩特连续吹炼法,尚在工业试验阶段。
诺兰达是侧吹、要人工打风眼、劳动强度很大、风眼漏风率达10%~15%。
有很大噪音、操作条件不好、冶炼环境不理想。
如果掌握不好容易引起泡沫渣喷炉事故。
综上所述,让我们来寻求新的冶炼工艺,在不断的探索中发现新途径。
氧气底吹炉炼铅、炼铜最早是湖南水口山和中国有色工程设计研究总院共同研发在水口山进行过半工业试验。
首先用于炼铅,产业化取得成功,继这之后,中国有色工程设计研究总院原副院长、总工程师、全国设计大师蒋继穆,用在炼铜上,曾找过多家合作,可是谁都不想吃第一只螃蟹。
氧气底吹连续吹炼技术

氧气底吹连续吹炼技术1. 简介氧气底吹连续吹炼技术是一种在钢铁冶炼过程中使用的先进技术。
它通过在底部喷吹高纯度氧气,使炉料中的杂质被氧化并排出,从而提高钢铁的质量和生产效率。
2. 技术原理氧气底吹连续吹炼技术主要基于以下原理:2.1 氧化反应在底部喷吹高纯度氧气的过程中,氧气与炉料中的杂质发生氧化反应。
例如,硅、锰等元素会与氧气反应生成相应的二氧化物。
这些二氧化物具有较高的挥发性,可以通过熔池表面排出,从而净化钢水。
2.2 温度调控通过调节底部喷吹高纯度氧气的速率和位置,可以控制熔池内部的温度分布。
这对于钢铁冶炼过程非常重要,因为不同温度区域对于不同材质的钢铁有不同的要求。
2.3 连续吹炼氧气底吹连续吹炼技术是一种连续操作的冶炼方法。
与传统的间歇式吹炼相比,连续吹炼可以提高生产效率,并且能够更好地控制钢水的质量。
3. 技术优势氧气底吹连续吹炼技术具有许多优势,包括:3.1 提高钢水质量通过底部喷吹高纯度氧气,可以有效地去除钢铁中的杂质。
这些杂质会影响钢铁的性能和质量,因此去除它们可以提高钢水的质量。
3.2 减少能耗与传统的间歇式吹炼相比,氧气底吹连续吹炼技术可以更好地控制冶炼过程中的温度。
这样可以减少能耗,并且降低生产成本。
3.3 提高生产效率由于是连续操作,氧气底吹连续吹炼技术可以实现无间断地冶炼。
这样可以大大提高生产效率,减少生产时间。
3.4 环保节能氧气底吹连续吹炼技术可以减少冶炼过程中的排放物。
通过去除杂质,可以降低废气和废渣的产生,从而达到环保节能的目的。
4. 应用领域氧气底吹连续吹炼技术在钢铁冶炼领域广泛应用。
它适用于不同规模和类型的冶炼设备,并且可以用于生产各种类型的钢铁产品。
5. 技术发展趋势随着科学技术的不断进步,氧气底吹连续吹炼技术也在不断发展。
未来的发展趋势主要包括以下方面:5.1 自动化控制自动化控制是氧气底吹连续吹炼技术未来发展的关键方向之一。
通过引入先进的控制系统和传感器,可以实现对冶炼过程的实时监测和调控,提高工作效率和产品质量。
铅冶炼氧气底吹资料
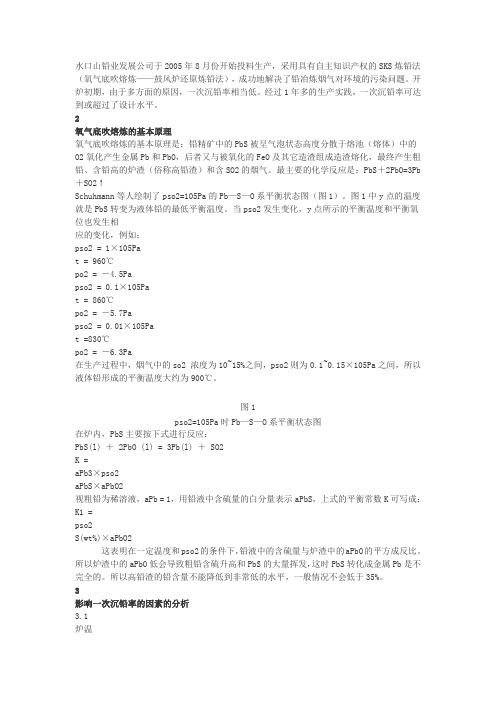
水口山铅业发展公司于2005年8月份开始投料生产,采用具有自主知识产权的SKS炼铅法(氧气底吹熔炼——鼓风炉还原炼铅法),成功地解决了铅冶炼烟气对环境的污染问题。
开炉初期,由于多方面的原因,一次沉铅率相当低。
经过1年多的生产实践,一次沉铅率可达到或超过了设计水平。
2氧气底吹熔炼的基本原理氧气底吹熔炼的基本原理是:铅精矿中的PbS被呈气泡状态高度分散于熔池(熔体)中的O2氧化产生金属Pb和PbO,后者又与被氧化的FeO及其它造渣组成造渣熔化,最终产生粗铅、含铅高的炉渣(俗称高铅渣)和含SO2的烟气。
最主要的化学反应是:PbS+2PbO=3Pb +SO2↑Schuhmann等人绘制了pso2=105Pa的Pb—S—O系平衡状态图(图1)。
图1中y点的温度就是PbS转变为液体铅的最低平衡温度。
当pso2发生变化,y点所示的平衡温度和平衡氧位也发生相应的变化,例如:pso2 = 1×105Pat = 960℃po2 = -4.5Papso2 = 0.1×105Pat = 860℃po2 = -5.7Papso2 = 0.01×105Pat =830℃po2 = -6.3Pa在生产过程中,烟气中的so2 浓度为10~15%之间,pso2则为0.1~0.15×105Pa之间,所以液体铅形成的平衡温度大约为900℃。
图1pso2=105Pa时Pb—S—O系平衡状态图在炉内,PbS主要按下式进行反应:PbS(l) + 2PbO (l) = 3Pb(l) + SO2K =aPb3×pso2aPbS×aPbO2视粗铅为稀溶液,aPb = 1,用铅液中含硫量的白分量表示aPbS,上式的平衡常数K可写成:K1 =pso2S(wt%)×aPbO2这表明在一定温度和pso2的条件下,铅液中的含硫量与炉渣中的aPbO的平方成反比。
所以炉渣中的aPbO低会导致粗铅含硫升高和PbS的大量挥发,这时PbS转化成金属Pb是不完全的。
氧气底吹炼铜过程熔体的流动特性

氧气底吹炼铜过程熔体的流动特性崔志祥;申殿邦;王智;边瑞民;魏传兵【期刊名称】《世界有色金属》【年(卷),期】2013(000)009【总页数】4页(P36-39)【作者】崔志祥;申殿邦;王智;边瑞民;魏传兵【作者单位】东营方圆有色金属有限公司;东营方圆有色金属有限公司;东营方圆有色金属有限公司;东营方圆有色金属有限公司;东营方圆有色金属有限公司【正文语种】中文本文介绍了鼓泡式喷流与射流式喷流的划分条件,论述了底吹熔池熔炼基本属于射流式喷流的范畴。
它有更好的化学反应动力学条件,有更好的节能减排效果,还有更大的生产潜力。
铜的冶炼过程从化学反应的观点看,实质上是氧化除硫、除铁等杂质的过程。
都是以氧气做氧化剂,氧化矿物原料中易被氧化的元素形成的氧化物或造渣,或成气态被除去。
为了给反应物(氧气和矿料)造成有利的反应条件,就形成了各式各样的冶金炉,包括闪速熔炼炉和各种熔池熔炼炉。
熔池熔炼炉又有立式的艾萨炉、奥斯麦特炉、氧气顶吹炉、瓦纽科夫炉和炉渣烟化炉,卧式的则有诺兰达炉、特尼恩特炉、三菱炉和氧气底吹熔炼炉,用做吹炼的P-S转炉也是卧式熔池炉的一种。
在各式各样的炉子中流体的运动特性形式上虽各有不同,但实质上可以分两大类,即鼓泡式熔池熔炼和射流式熔池熔炼。
从风口送入的富氧空气出口线速度较低,修正的弗劳德准数较小,这时气流实际上是以脉冲式喷入熔体中,属于气泡产生体系为鼓泡式熔池熔炼。
当喷嘴出口气体线速度较高,达到或超过音速,修正弗劳德准数较高时,气体以连续稳定的流股状态喷入,称为射流,这样的熔池熔炼为射流式熔池熔炼。
对于喷流性质的区分,有人提出,当氧枪出口气体在工况条件下的气流线速度达到音速,马赫数为1或无限接近于1者为射流式;未达到音速,马赫数小于1者为鼓泡式。
麦克纳兰教授提出鼓泡式射流式的判据是气流线速度是小于或大于400m/s,相当于马赫数约为1.25。
还有以雷诺准数的大小判定,当Re>2100时,气体便形成射流,还有以修正的弗劳德准数及气相与液相密度比来判断,给出了如图1的关系。
氧气底吹熔池熔炼工艺
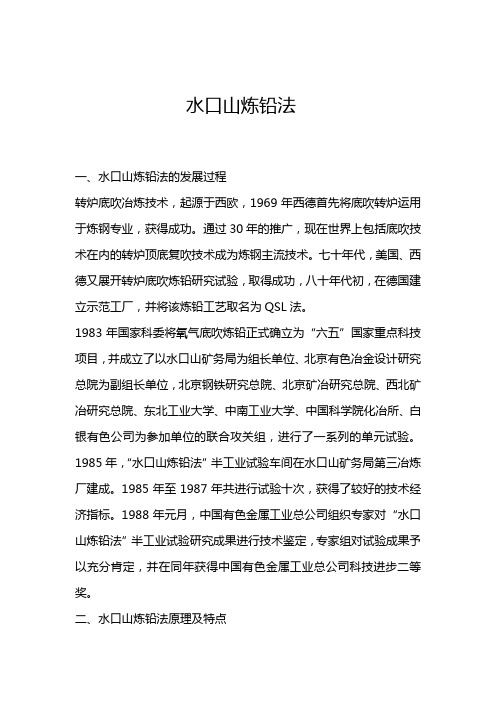
水口山炼铅法一、水口山炼铅法的发展过程转炉底吹冶炼技术,起源于西欧,1969年西德首先将底吹转炉运用于炼钢专业,获得成功。
通过30年的推广,现在世界上包括底吹技术在内的转炉顶底复吹技术成为炼钢主流技术。
七十年代,美国、西德又展开转炉底吹炼铅研究试验,取得成功,八十年代初,在德国建立示范工厂,并将该炼铅工艺取名为QSL法。
1983年国家科委将氧气底吹炼铅正式确立为“六五”国家重点科技项目,并成立了以水口山矿务局为组长单位、北京有色冶金设计研究总院为副组长单位,北京钢铁研究总院、北京矿冶研究总院、西北矿冶研究总院、东北工业大学、中南工业大学、中国科学院化冶所、白银有色公司为参加单位的联合攻关组,进行了一系列的单元试验。
1985年,“水口山炼铅法”半工业试验车间在水口山矿务局第三冶炼厂建成。
1985年至1987年共进行试验十次,获得了较好的技术经济指标。
1988年元月,中国有色金属工业总公司组织专家对“水口山炼铅法”半工业试验研究成果进行技术鉴定,专家组对试验成果予以充分肯定,并在同年获得中国有色金属工业总公司科技进步二等奖。
二、水口山炼铅法原理及特点水口山炼铅法是由我公司独立开发的一权新型专利炼铅工艺。
水口山炼铅法属熔池熔炼范畴,当物料投入炉内,同时完成加热、熔化、氧化、造渣、造锍等过程,具有很高的传质、传热功能;所不同的是,它采用了独特而简单、具有优越冶金动力学功能的设备——水口山熔炼炉。
从熔炼炉顶部加入炉料,底部送入富氧空气搅动熔池,入炉物料在熔池中完成熔炼过程,产出粗铅、高铅渣和烟气,分别从放铅口、放渣口、排烟口排出。
水口山熔炼炉是一个密闭的长圆筒型卧式转炉,钢板外壳内衬铬镁砖,炉身有传动装置,可旋转900,设有加料口、排烟口、放渣口、放铅口,底部装设氧枪,氧枪及其套砖可以更换,端墙燃油烧嘴供开炉和保温使用。
水口山炼铅法是连续熔池熔炼和吹炼过程,它是将含水6~7%的含铅物料和熔剂经混合制粒后,连续、均匀地加入到底部配有射流氧枪的氧气底吹炉中,完成物料的干燥、熔化、氧化造渣、沉铅过程,实现渣铅分离,产出粗铅,烟气和熔炼渣。
9-转炉底吹复吹工艺-2
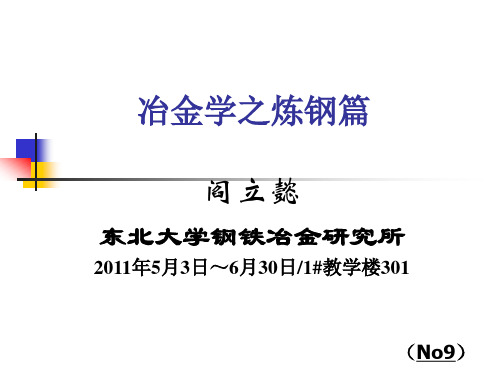
阶段 因素 熔池温度
吹炼前期
低
吹炼中期
中
吹炼后期
高
氧化性 高(>25%) 低(<15%) 中15%~20%)
碱度 脱碳速度 脱磷速度
低
低
中
中
高
高
高
低
低
2020/4/11
东北大学/阎立懿
3
五大工艺制度:
2020/4/11
东北大学/阎立懿
7
4.4.2 氧气底吹转炉结构特点
1)设备概貌
2020/4/11
东北大学/阎立懿
8
2)设备结构特点
炉型与LD转炉相似,但高/径比小于LD转炉的。 底吹转炉的炉身和炉底是可拆卸分开,以满足底吹供气
系统的维护。 炉底上安装有10~20支吹氧喷咀。 没有顶吹氧枪,不需要高厂房,这对生产率不高的平炉
钢水残锰增加、降低Fe-Mn消耗。
2020/4/11
东北大学/阎立懿
14
4)铁的氧化和脱磷反应
底 吹 转 炉 ( FeO ) 低 , 尤 其初期(FeO)低,使得初中 期脱磷不明显,后期(FeO) 提高脱磷显著 ,使脱磷反应比 顶吹转炉滞后进行。
冶 炼 低 碳 钢 时 , ( FeO) 较高,脱磷问题不突出;但冶 炼高碳钢时,因(FeO)较低 影响脱磷。
2020/4/11
东北大学/阎立懿
6
与此同时,法国研制成功与OBM 相似的方法,命名 为LMS法(由三个公司开发的),他们是以液态的燃料 油作为氧气喷嘴的冷却介质,在30吨OBM炉取得了较好 的效果,使得钢中[N]大为降低,炉子寿命大为提高。
氧气底吹炼钢工艺介绍
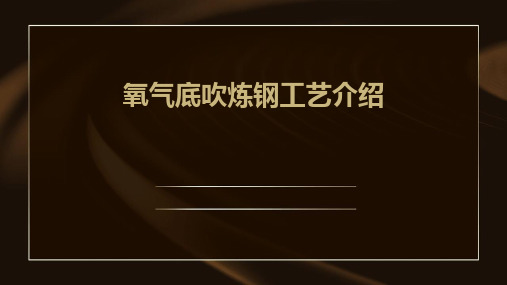
CONTENTS 目录
• 氧气底吹炼钢工艺概述 • 氧气底吹炼钢工艺流程 • 氧气底吹炼钢工艺设备 • 氧气底吹炼钢工艺的应用与优势 • 氧气底吹炼钢工艺的挑战与解决方案 • 未来氧气底吹炼钢工艺的发展趋势
CHAPTER 01
氧气底吹炼钢工艺概述
定义与特点
定义
氧气底吹炼钢工艺是一种炼钢技术, 通过向熔池底部吹入氧气,使熔池中 的铁水与氧气发生反应,从而去除杂 质并提高钢的纯度。
应用领域
01
大型钢厂
适用于大型钢铁企业的炼钢车间 ,可大幅提高生产效率和产品质 量。
特殊钢生产
02
03
环保要求高的区域
适用于生产特殊钢种,如不锈钢 、高强度钢等,满足高端制造业 的需求。
由于氧气底吹炼钢工艺具有较低 的污染物排放,适用于环保要求 高的地区。
工艺优势
01
02
03
高效节能
采用氧气底吹技术,可大 幅提高炼钢效率,降低能 耗。
推动钢铁工业发展
氧气底吹炼钢工艺的广泛应用, 推动了钢铁工业的技术进步和产 业升级,提高了整个行业的竞争 力。
氧气底吹炼钢工艺的历史与发展
历史
氧气底吹炼钢工艺起源于20世纪50年代,经过多年的研究和实践,逐渐发展成熟并得到广泛应用。
发展
随着科技的进步和环保要求的提高,氧气底吹炼钢工艺不断改进和完善,未来的发展方向包括提高产 能、降低能耗、减少污染物排放等方面。
积极开展绿色生产认证,推动氧气底吹炼钢工艺的可持续发展
。
市场前景与展望
市场需求增长
随着全球钢铁工业的发展,对高品质钢材的需求不断增加,为氧气 底吹炼钢工艺提供了广阔的市场空间。
技术优势与竞争力
氧气顶吹转炉炼钢工艺
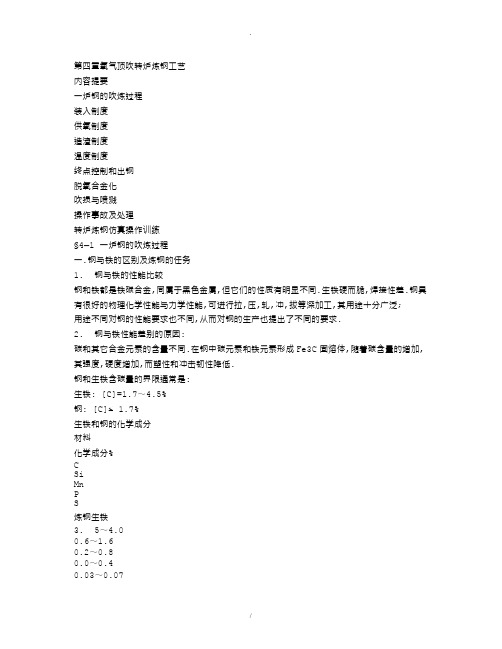
第四章氧气顶吹转炉炼钢工艺内容提要一炉钢的吹炼过程装入制度供氧制度造渣制度温度制度终点控制和出钢脱氧合金化吹损与喷溅操作事故及处理转炉炼钢仿真操作训练§4—1 一炉钢的吹炼过程一.钢与铁的区别及炼钢的任务1.钢与铁的性能比较钢和铁都是铁碳合金,同属于黑色金属,但它们的性质有明显不同.生铁硬而脆,焊接性差.钢具有很好的物理化学性能与力学性能,可进行拉,压,轧,冲,拔等深加工,其用途十分广泛;用途不同对钢的性能要求也不同,从而对钢的生产也提出了不同的要求.2.钢与铁性能差别的原因:碳和其它合金元素的含量不同.在钢中碳元素和铁元素形成Fe3C固熔体,随着碳含量的增加,其强度,硬度增加,而塑性和冲击韧性降低.钢和生铁含碳量的界限通常是:生铁: [C]=1.7~4.5%钢: [C]≤ 1.7%生铁和钢的化学成分材料化学成分%CSiMnPS炼钢生铁3.5~4.00.6~1.60.2~0.80.0~0.40.03~0.07静钢0.06~1.500.1~0.370.25~0.80≤0.045≤0.05沸腾钢0.05~0.27≤0.070.25~0.70≤0.045≤0.054.炼钢的基本任务:⑴脱碳;将铁水中的碳大部分去除,同时随着脱碳的进行,产生大量CO气泡,在CO排出过程中,搅拌熔池促进化渣,同时脱除[H],[N]和夹杂.⑵去除杂质(去P,S和其它杂质);铁水中[P],[S]含量高,而钢中[P]会造成"冷脆",[S]造成"热脆".通常大多数钢种对P,S含量均有严格要求,炼钢必须脱除P,S等有害杂质.⑶去除气体及夹杂物;在炼钢过程中通过熔池沸腾(碳氧反应,底吹惰性气体搅拌)脱除H],[N]和非金属夹杂物.⑷脱氧合金化;在炼钢过程中因为脱碳反应的需要,要向钢液中供氧,就不可避免地使后期钢中含有较高的氧,氧无论是以液体形态还是以氧化物形态存在于钢中都会降低钢的质量,所以必须在冶炼后期或出钢过程中将多余的氧去除掉.在冶炼过程中,铁水中的Si, Mn大部分氧化掉了,为了保证成品钢中的规定成分,要向钢水中加入各种合金元素,这个过程与脱氧同时进行,称为合金化.⑸升温(保证合适的出钢温度).铁水温度一般在1250~1300℃,而钢水的出钢温度一般在1650℃以上,才能顺利浇注成铸坯,因此炼钢过程也是一个升温过程.5.完成炼钢各项任务的基本方法⑴氧化为了将铁水等炉料中的硅,锰,碳等元素氧化掉,可以采用"吹氧"方法,即直接喷吹氧气,或加入其它氧化剂,如铁矿石,铁皮等.⑵造渣为了去除炉料中的P,S等杂质,在炼钢过程中加入渣料(石灰,白云石,熔剂等),形成碱度合适,流动性良好,足够数量的炉渣,一方面完成脱除P,S的任务,同时减轻对炉衬对侵蚀.转炉主要是依靠碳,硅,锰等元素氧化放出等热量,以及铁水的物理热实现升温.⑷加入脱氧剂和合金料通过向炉内或钢包内加入各种脱氧剂和合金料的方法,完成脱氧及合金化的任务.二.金属成分和炉渣成分的变化规律1.Si在吹炼前期(一般在3~4分钟内)即被基本氧化.在吹炼初期,铁水中的[Si]和氧的亲和力大,而且[Si]氧化反应为放热反应,低温下有利于此反应的进行,因此,[Si]在吹炼初期就大量氧化.[Si]+O2=(SiO2) (氧气直接氧化)[Si]+2[O]= (SiO2) (熔池内反应)[Si]+(FeO)=(SiO2)+2[Fe] (界面反应)2(FeO)+(SiO2)=(2FeO·SiO2)随着吹炼的进行石灰逐渐溶解,2FeO·SiO2转变为2CaO·SiO2,即SiO2与CaO牢固的结合为稳定的化合物,SiO2活度很低,在碱性渣中FeO的活度较高,这样不仅使[Si]被氧化到很低程度,而且在碳剧烈氧化时,也不会被还原,即使温度超过1530℃,[C]与[O]的亲和力也超过[Si]与[O]的亲和力,终因(CaO)与(SiO2)结合为稳定的2CaO.SiO2,[C]也不能还原(SiO2).硅的氧化对熔池温度,熔渣碱度和其他元素的氧化产生影响:[Si]氧化可使熔池温度升高;[Si]氧化后生成(SiO2),降低熔渣碱度,熔渣碱度影响脱磷,脱硫;熔池中[C]的氧化反应只有到[%Si]P0.⑵喷嘴前氧压P0:其选用应考虑以下因素:A.氧气流股出口速度要达到超音速(450~530cm∕s),即M=1.8~2.1.B.出口的氧压应稍高于炉膛内气压.通常P0=0.784~1.176MPa.⑶出口氧压P:应稍高于或等于周围炉气的压力.通常P=0.118~0.125MPa.六.枪位及其控制所谓枪位,是指氧枪喷头端面距静止液面的距离,常用H表示,单位是m.目前,一炉钢吹炼中的氧枪操作有两种类型,一种是恒压变枪操作,一种是恒枪变压操作.比较而言,恒压变枪操作更为方便,准确,安全,因而国内钢厂普遍采用.1.枪位的变化范围和规律关于枪位的确定,目前的做法是经验公式计算,实践中修正.一炉钢冶炼中枪位的变化范围可据经验公式确定:H=(37~46)P×D出式中 P——供氧压力,MPa;D——喷头的出口直径,mm;H——枪位,mm.具体操作中,枪位控制通常遵循"高-低-高-低"的原则:⑴前期高枪位化渣但应防喷溅.吹炼前期,铁水中的硅迅速氧化,渣中的(SiO2)较高而熔池的温度尚低,为了加速头批渣料的熔化(尽早去P并减轻炉衬侵蚀),除加适量萤石或氧化铁皮助熔外应采用较高的枪位,保证渣中的(FeO)达到并维持在25~30%的水平;否则,石灰表面生成C2S 外壳,阻碍石灰溶解.当然,枪位亦不可过高,以防发生喷溅,合适的枪位是使液面到达炉口而又不溢出.⑵中期低枪位脱碳但应防返干.吹炼中期,主要是脱碳,枪位应低些.但此时不仅吹入的氧几乎全部用于碳的氧化,而且渣中的(FeO)也被大量消耗,易出现"返干"现象而影响S,P的去除,故不应太低,使渣中的(FeO)保持在10~15%以上.⑶后期提枪调渣控终点.吹炼后期,C-O反应已弱,产生喷溅的可能性不大,此时的基本任务是调好炉渣的氧化性和流动性继续去除硫磷,并准确控制终点碳(较低),因此枪位应适当高些.⑷终点前降枪点吹破坏泡沫渣.接近终点时,降枪点吹一下,均匀钢液的成分和温度,同时降低炉渣的氧化铁含量并破坏泡沫渣,以提高金属和合金的收得率.2.枪位的调节⑴开吹前必须了解的情况A.喷嘴的结构特点及氧气总管氧压情况;B.铁水成分,主要是Si,P,S的含量;C.铁水温度,包括铁水罐,混铁炉或混铁车内存铁情况及铁水包的情况;D.炉役期为多少,是否补炉,相应的装入量是多少,上炉钢水是否出净,是否有残渣;E.吹炼钢种及其对造渣和温度控制的要求;F.上一班操作情况,并测量熔池液面高度.⑵枪位的调节生产条件千变万化,因此具体操作中还应根据实际情况对枪位进行适当的调节.A.铁水温度:若遇铁水温度偏低,应先压枪提温,而后再提枪化渣,以防渣中(FeO)积聚引发大喷,即采用低-高-低枪位操作.铁水温度高时,碳氧反应会提前到来,渣中∑(FeO)降低,枪位可稍高些,以利成渣.B.铁水成分:铁水硅,磷高时,若采用双渣操作,可先低枪位脱硅,磷,倒掉酸性渣;若单渣操作,由于石灰加入量大,应较高枪位化渣.铁水含锰高时,有利于化渣,枪位则可适当低些.C.装入量变化:炉内超装时,熔池液面高,枪位应相应提高,否则,不仅化渣困难而且易烧坏氧枪.D.炉内留渣:采用双渣留渣法时,由于渣中(FeO)高,有利于石灰熔化,因此吹炼前期的枪位适当低些,以防渣中(FeO)过高引发泡沫喷溅.E.供氧压力:高氧压与低枪位的作用相同,故氧压高时,枪位应高些.F.废钢中生铁块多导热性差,不易熔化,应降低枪位,以防吹炼后期没有完全熔化.G.炉龄a 开新炉,炉温低,应适当降低枪位;b 炉役前期液面高,可适当提高枪位;c 炉役后期装入量增加,熔池面积增大,不易化渣,可在短时间内采用高低枪位交替操作以加强熔池搅拌,利于化渣.H.渣料a 石灰质量差和加入量多,则渣量大,枪位应相应提高;b 使用活性石灰成渣快,整个过程枪位都可以稍低些;c 铁矿石,氧化铁皮和萤石用量多时,熔渣容易形成,同时流动性较好,枪位可适当低一些. I.钢种炼高碳钢时,由于脱磷困难,应采用较高的枪位,特别是在吹炼后期.同理,在吹炼含磷很低的钢种时,应采用较高枪位.七.恒压变枪操作的几种模式由于各厂的转炉吨位,喷嘴结构,原材料条件及所炼钢种等情况不同,氧枪操作也不完全一样.现介绍如下几种氧枪操作方式.1.高—低—高的六段式操作开吹枪位较高,及早形成初期渣;二批料加入后适时降枪,吹炼中期炉渣返干时又提枪化渣;吹炼后期先提枪化渣后降枪;终点拉碳出钢.2.高—低—高的五段式操作五段式操作的前期与六段式操作基本一致,熔渣返干时可加入适量助熔剂调整熔渣流动性,以缩短吹炼时间,见下图.3.高一低一高一低的四段式操作在铁水温度较高或渣料集中在吹炼前期加入时可采用这种枪位操作.开吹时采用高枪位化渣,使渣中含(FeO)量达25~30%,促进石灰熔化,尽快形成具有一定碱度的炉渣,增大前期脱磷和脱硫效率,同时也避免酸性渣对炉衬的侵蚀.在炉渣化好后降枪脱高—低—高五段式操作示意图碳,为避免在碳氧化剧烈反应期出现返干现象,适时提高枪位,使渣中(FeO)保持在10~15%,以利磷,硫继续去除.在接近终点时再降枪加强熔池搅拌,继续脱碳和均匀熔池成分和温度,降低终渣(FeO)含量.例:马钢一钢厂95T转炉氧枪操作A.全程枪位:高—低—高式或高—高—低式过程枪位:要力求稳定,尽量少波动,每次动枪波动范围≯200mm.补吹枪位:必须按最低枪位控制(1.1m).B.高枪位:1.7~2.0m;基本吹炼枪位:1.4~1.7m;拉碳枪位:1.2~1.4m;吹炼中,高碳钢拉碳枪位应提高0.1~0.2m.例:马钢一钢厂95T转炉开吹枪位的确定(a)铁水Si>0.70%时渣量大,易喷溅,枪位应比正常情况下低0.1~0.2m;铁水Si ,P含量低,特别是Si1%),P,S较高,或生产优质钢时采用.倒渣时机:这是双渣法操作的关键.选择在渣中含P量最高,含铁量最低的时刻,以获得高脱磷率和低铁损的效果.同时,应在Si已氧化完毕,炉渣已基本化好,P在渣钢之间的分配已接近平衡时进行. 生产实践证明,顶吹转炉在吹炼时间25%左右,复吹转炉为30%左右时倒渣脱磷率最高;若是因铁水硫高而采用双渣法,则应在吹炼10min左右倒渣.注意:倒渣前1分钟适当提枪或加些熔剂改善炉渣的流动性,以便于倒渣操作.3.双渣留渣法定义:将上一炉的终渣(高碱度,高温度和较高(FeO)含量)部分地留在炉内,并在吹炼中途倒出部分炉渣再造新渣的操作方法.特点:初渣早成而前期的去硫及去磷效率高,总去硫率可达60%~70%,总去磷率更是高达95%,适合于吹炼中,高磷铁水.注意:装料时应先加一批石灰稠化所留炉渣,而且兑铁水时要缓慢进行,以防发生爆发性碳氧反应而引起喷溅.若上一炉钢终点碳过低,不宜进行留渣操作.应当指出,顶吹转炉虽能将高磷铁水炼成合格的钢,但技术经济指标较差,与吹炼中,低磷铁水相比,每吨钢的金属料消耗高30~100kg,石灰多用40~100kg,炉龄大幅降低;产量也仅为吹炼低磷铁水时的70%~80%;另外,单渣法生产稳定,操作简单,便于实行计算机控制.因此,对于含硅,磷及硫较高的铁水,入炉前进行预处理使之达到单渣法操作的要求,不仅技术上可行而且工艺上经济合理.七.渣料的加入方法关于渣料的加入,关键是要注意渣料的分批和把握加入的时间.1.渣料分批加入目的:渣料应分批加入以加速石灰的熔化(否则,会造成熔池温度下降过多,导致渣料结团且石灰块表面形成一层金属凝壳而推迟成渣).批次:单渣操作时,渣料通常分成两批:第一批1/2~2/3及白云石全部(冶炼初期炉衬侵蚀最严重);第二批1/2~1/3.2.加料时间⑴第一批渣料在开吹的同时加入.⑵第二批渣料,一般是在硅及锰的氧化基本结束,头批渣料已经化好,碳焰初起的时候(30吨的转炉开吹6 min左右)加入(如果加入过早,炉内温度还低且头批渣料尚未化好又加冷料,势必造成渣料结团难化;反之,如果加入过晚,正值碳的激烈氧化时期,渣中的(∑FeO)较低渣料亦难化.问题的关键是正确判断炉况,头批渣料化好的标志是:火焰软且稳定,炉内发出柔和的嗡嗡声,喷出物为片状,落在炉壳上不粘贴;未化好的情况是:炉口的火焰发散且不稳定,炉内发出尖锐的吱吱声,喷出物是金属火花和石灰粒).有的厂二批料分小批多次加入以利熔化,但最后一小批料必须在终点前3~4分钟加入八.石灰,白云石加入量的确定加入炉内的渣料主要是石灰和白云石,还有少量的萤石或氧化铁皮等熔剂.1.石灰加入量的确定⑴首先根据铁水的硅,磷含量和炉渣碱度计算A.铁水含磷较低([P]<0.3%)时,(kg∕t铁)%CaO有效—石灰中的有效CaO,%CaO有效=(%CaO)石灰-R×(%SiO2)石灰废钢,生铁块也应根据上式计算需补加的石灰量.例:B.铁水含磷较高([P]≥0.3%)时,(kg∕t铁)⑵其次,当加入含(%SiO2)的辅助原料时(如:矿石,白云石萤石,菱镁矿等),应补加石灰. 例: 铁矿石中SiO2的含量为8%,碱度按3.0控制,石灰的有效氧化钙为80%,则每kg矿石补加石灰量 = 8×3.0/80 = 0.3(kg)⑶石灰加入总量废钢中含有一定量的Si,但成分通常不知,一般按每吨废钢补加石灰15~20kg.2.白云石用量的确定白云石的加入量应根据炉渣要求的饱和MgO含量来确定.通常渣中MgO含量控制在8%~10%,除了加入的白云石含有MgO外,石灰和炉衬也会带入一部分.理论用量W(kg/t)=实际加入量W/=W-W灰-W衬3.熔剂的用量萤石用量:尽量少用或不用,部标要求≤4kg/t.矿石用量:铁矿石及氧化铁皮也具有较强的化渣能力,但同时对熔池产生较大的冷却效应,其用量应视炉内温度的高低,一般为装入量的2~5%.4.计算举例例题1:1t金属料中铁水占85%,废钢占10%,生铁块占5%,每T金属料加矿石5kg,萤石3kg,铁水带渣比为0.5%,石灰熔化率为85%,各原材料成分列在下表中.炉渣碱度为3.5.计算:1t金属料所需石灰加入量为多少原料成分铁水废钢生铁块铁水带渣石灰矿石萤石[%Si]0.500.101.40%CaO37.583%SiO2362.56.05.0解:石灰加入量铁水带渣量为:1000×85%×0.5% = 4.25 (kg)铁水带渣带入的SiO2应考虑铁水渣中CaO相当的SiO2量:辅助原料及铁水带渣需补加石灰量(kg))例题2:用轻烧白云石作为调渣剂其成分如下表:原料成分石灰轻烧白云石炉衬%CaO%SiO2%MgO832.54.09502.03777计算条件:终渣成分要求(MgO)=9.66%,渣量为金属装入量的8.2%,炉衬侵蚀量是装入量的0.05%,其它条件同上述例题.解题思路:终渣(MgO)来源:A. 加入的轻烧白云石.C.石灰中的MgO.D.炉衬被侵蚀下来的MgO.⑴计算轻烧白云石加入量由例题1计算的结果是不加轻烧白云石时石灰加入量为68.39kg∕t.石灰带入MgO量:68.39×4.09% =2.80 (kg)炉衬蚀损带入MgO量:1000×0.05%×77%=0.385 (kg)根据1t装入量计算终渣MgO量:1000×8.2%×9.66%=7.92 (kg∕t)⑵计算轻烧白云石需补加石灰量⑶计算轻烧白云石相当的石灰量石灰加入总量= 68.39 - 8.62 + 1.21= 60.98 (kg)例题3:某转炉铁水装入量为100t,铁水含Si:0.4%,P:0.1%.采用单渣法造渣,终渣碱度为3.5,每炉加矿石3000kg,为保证渣中MgO,每炉加轻烧白云石2500kg.已知:石灰:CaO: 91.6% SiO2: 1.6%矿石:SiO2: 8%轻烧白云石:MgO:35% CaO:55% SiO2: 2%计算石灰加入量(单位kg,保留整数).解:⑴计算未加白云石时石灰加入量⑵计算轻烧白云石需补加石灰量⑶计算轻烧白云石相当的石灰量⑷计算石灰加入总量石灰加入总量= 5454+203-1599 = 4085 (kg)九.渣量计算渣量可以用元素平衡法计算.由铁水炼成钢,各元素一部分被氧化,一部分残留在钢中.如果知道某一元素在钢中的数量,该元素其余部分全部进入了熔渣,则通过这个元素在渣中的百分含量,就可以计算出熔渣的数量.Mn和 P两元素,从渣料及炉衬中的来源很少,其数量可以忽略不计.因而可以用Mn或 P的平衡来计算渣量.例:渣量计算(单渣法)装入量 Mn P Fe装 (kg) % kg % kg % kg入铁水28000 0.40 112 0.20 56料废钢4000 0.50 20 0.02 0.8数铁矿石1000 0.30 3 0.10 1.0 56.0 560据小计 135 57.8 560(MnO)% [%Mn] (P2O5)% [%P]终点钢水 0.12 0.03数炉渣 3.30 2.56 2.86 1.25据金属装入量 28000+4000+560=32560kg出钢量(按装入量的90%计算)32560×90%=29304kg钢水中Mn 量 29304×0.12%=35.16kg钢水中P量 29304×0.03%= 8.79kg进入渣中Mn 量 135-35.16=99.84kg进入渣中P量 57.8 - 8.79=49.01kg用Mn 平衡法熔渣占装入量的百分比用P平衡法熔渣占装入量的百分比习题:1名词解释:泡沫渣,单渣法双渣法双渣留渣法2造渣方法如何选择采用双渣法操作时,倒渣的时间应如何掌握3石灰加入量如何计算渣料如何加入4影响石灰溶解的因素有哪些5炉渣严重泡沫化的原因是什么如何控制泡沫渣6.吹炼过程中为什么会出现炉渣"返干"现象§4—5 温度制度氧气转炉的温度制度包括两方面的内容:一是准确控制终点温度,二是恰当控制冶炼过程温度. 温度对于转炉吹炼过程既是重要的热力学参数,又是重要的动力学参数.它既对各个化学反应的反应方向,反应程度和各元素之间的相对反应速度有重大影响,又对熔池的传质和传热速度有重大影响.因此,为了快而多地去除钢中的有害杂质,保护或提取某些有益元素,加快吹炼过程成渣速度,加快废钢熔化,减少喷溅,提高炉龄等,都必须控制好吹炼过程温度.此外,对各钢种都有其要求的出钢温度.出钢温度过低会造成回炉,短锭,包底凝钢及钢锭的各种低温缺陷和废品;过高则会造成跑漏钢,钢锭上涨,粘模及钢锭的各种高温缺陷和废品,并影响炉衬和氧枪的寿命.一.转炉温度控制的目标及温度控制内容1.目标希望吹炼过程中均衡升温,吹炼终点时钢水的温度和化学成分同时命中钢种要求的范围.2.内容⑴确定合适的钢种出钢温度;⑵确定熔池富裕热量的数值,选择冷却剂并确定其冷却效果和加入量;⑶掌握影响熔池温度变化的因素,及进行温度控制操作.二.热量来源与热量支出1.热量来源氧气转炉炼钢的热量来源主要是铁水的物理热和化学热.物理热是指铁水带入的热量,它与铁水温度有直接关系,化学热是铁水中各元素氧化后放出的热量,它与铁水化学成分直接相关. 在炼钢温度下,各元素氧化放出的热量各异,它可以通过各元素氧化放出的热效应来计算确定.例如铁水温度1200℃,吹入的氧气25℃,碳氧反应生成CO时:[C]1473+{O2}298={CO}1473 ΔH1473K= -137520 J/mol则1kg[C]氧化生成CO时放出的热量为137520/12≈11300kJ/kg.现以100kg金属料为例,计算各元素的氧化热能使熔池升温多少.设炉渣量为装入金属料的15%,炉衬吸热为装入金属料的10%,计算热平衡公式如下:Q=∑MCT式中 Q—1kg元素氧化放出的热量,kJ/kg;M——受热金属液,炉衬和炉渣重量,kg;C——各物质比热,已知钢液CL为0.84~1.0kJ/kg·℃,炉渣和炉衬的CS为1.23kJ/ kg·℃.计算在1200℃时C—O反应生成CO时,氧化1kg碳可使熔池温度升高数为:℃1kg元素是100kg金属料的1%,因此,根据同样道理和假设条件,可以计算出其它元素氧化1%时使熔池的升温数.碳完全燃烧生成CO2时其发热量最高,使熔池升温数最大,其次是磷和硅.但是碳大部分没有完全燃烧,因此,在氧气转炉吹炼中采用双流氧枪,可有助于CO进一步燃烧生成CO2,使转炉热效率提高.哪些元素是转炉炼钢的主要热源,不仅要看其热效应大小,还要视其氧化总量的多少而定.例如,在1400℃时,硅氧化0.5%,碳氧化3%,则分别使熔池升温数为71℃和249℃,可见碳氧化产生的总热量要比硅的总热量多得多.2.热量支出热量支出主要包括:钢水物理热;炉渣物理热;炉气物理热;烟尘物理热;渣中金属铁珠物理热;喷溅金属物理热;矿石分解热;废钢物理热(见热平衡表).其中,钢水的物理热约占70%,这是一项主要的支出,熔渣带走的热量大约占10%,它与渣量的多少有关.因此在保证去除P,S的条件下,采用最小的渣量.渣量过大不仅增加渣料的消耗,也增加热量的损失,所以要求铁水进行预处理,这样既可实现少渣操作;同时在吹炼过程中也可减少喷溅,缩短吹炼时间,减少炉与炉的间隔时间,减少热损失,提高转炉的热效率.转炉热效率提高以后,可以提高废钢比.3.转炉炼钢的热平衡指炼钢过程的热量来源与支出之间的平衡关系(见热平衡表).为了准确的控制转炉的吹炼温度,需要知道铁水中各成分氧化反应放出的总热量;这些热量除了把熔池加热到出钢温度外,富余多少热量需要加多少冷却剂这要经过热平衡计算才能得出,具体物料平衡,热平衡计算参看教材中物料平衡与热平衡计算内容.热平衡表的分析:根据转炉吹炼过程中热量的收入与支出,作出热平衡计算列出热平衡表,得出氧气转炉热工特点如下:⑴热量收入主要是铁水的物理热和化学热;⑵尚有大量的富余热量,必须加入冷却剂;⑶元素氧化放热中,C,Si,P都是重要的发热元素,其中碳占有主要地位(占氧化总放热的一半以上).⑷转炉热效率为60~70%左右.转炉总热效率计算公式如下:总热效率=×100%在转炉炼钢过程中,真正有用的热量占整个热量收入的70%左右,在热量的利用上还是有一定潜力的,应努力提高热效率.三.出钢温度的确定出钢温度的高低受钢种,锭型和浇注方法的影响.1.出钢温度的确定依据:⑴保证浇注温度高于所炼钢种凝固温度20~30℃(小炉子偏上限,大炉子偏下限).⑵考虑出钢过程和钢水运输,镇静时间,钢液吹氩时的降温,一般为80~120℃.⑶考虑浇注方法和浇注锭型大小所用时间的降温.2.确定出钢温度T出钢T出钢 =T凝 +△t过热+△T总式中 T凝——钢液的熔点即液相线温度,根据钢种的化学成分而定.T凝=1539-∑△ti×[%i]-7 ℃;△t过热—钢水过热度,℃.即高于熔点的温度值,与钢种,坯型有关.△T总—从出钢→精炼→浇注过程中的温降值.△T总=△t1+△t2+△t3+△t4+△t5△t1—出钢过程温降,℃.△t2—出钢毕至精炼开始之前的温降,℃.△t3—钢水精炼过程温降,℃.△t4—钢水精炼完毕至开浇前的温降,℃.△t5—钢水从钢包至中间包的温降,℃.四.确定冷却剂用量1.冷却剂及其特点转炉炼钢的冷却剂主要是废钢和矿石.比较而言,废钢的冷却效应稳定,而且硅磷含量也低,渣料消耗少,可降低生产成本;但是,矿石可在不停吹的条件下加入,而且具有化渣和氧化的能力.因此,目前一般是矿石,废钢配合冷却,而且是以废钢为主,且装料时加入;矿石在冶炼中视炉温的高低随石灰适量加入.另外,冶炼终点钢液温度偏高时,通常加适量石灰或白云石降温(前两种均不能用).2.各冷却剂的冷却效应冷却效应是指每kg冷却剂加入转炉后所消耗的热量,常用q表示,单位是kJ/kg.⑴矿石的冷却效应:矿石冷却主要靠Fe2O3的分解吸热,因此其冷却效应随铁矿的成分不同而变化,含Fe2O370%,FeO10%时铁矿石的冷却效应为:q矿=1×C矿×△t+λ矿+1×(Fe2O3%×112/160×6456+FeO%×56/72×4247)=1×1.02×(1650-25)+209+1×(0.7×112/160×6456+0.1×56/72×4247)=5360 kJ/kg⑵废钢的冷却效应:废钢主要依靠升温吸热来冷却熔池,由于不知准确成分,其熔点通常按低碳钢的1500℃考虑,入炉温度按25℃计算,于是废钢的冷却效应为:q废=1×[C固(t熔-25)+λ废+ C液(t出-t熔)]=1×[0.7×(1500-25)+272+0.837(1650-1500)]=1430 kJ/kg⑶氧化铁皮的冷却效应:计算方法同矿石,对于50%FeO,40%Fe2O3 的氧化铁皮,其冷却热效应为:q皮=5311 kJ/kg。
底吹氧气转炉炼钢法

Q-BOP和LD炉内渣中(FeO)
• 在低碳范围内,底吹氧气转炉的脱磷并不逊色LD 炉。其原因可归纳为在底吹喷咀上部气体中O2分 压高,产生强制气化,P生成PO(气),并被固体
石灰粉迅速化合为3CaO.P2O5,具有L.P2O5则比较稳定,再还原速度缓慢,尤其是 在低碳范围时,脱磷明显。
• 底吹氧气转炉设有顶吹氧气转炉那样的氧枪,不需要高厂房, 这对生产率不高的平炉改为底吹氧气的转炉十分有利。
3.3.2底吹氧气转炉炉内反应
• 吹炼初期,铁水中 [Si]、[Mn]优先氧化,但 [Mn]的氧化只有30~40%,这与LD转炉吹炼初 期有70%以上锰氧化不同。
• 吹炼中期,铁水中碳大量氧化,氧的脱碳利用 率几乎100%,而且铁矿石、铁皮分解出来的氧, 也被脱碳发应消耗了。这体现了底吹氧气转炉 比顶吹氧气转炉具有熔池搅拌良好的特点。由 于良好的熔池搅拌贯穿整个吹炼过程,所以渣 中的(FeO)被[C]还原,渣中(FeO)含量低于 LD转炉,铁合金收得率高。
• 1971年,美国钢铁公司引进了OBM法,1972年建设了3座200吨底 吹氧气转炉,命名为Q-BOP法(Quiet-BOP)。此后,底吹转炉在 欧洲、美国和日本又得到了进一步发展。
3.3.1底吹氧气转炉结构特点
• 炉身和炉底可差拆卸分开,不同吨位的炉子,在 底吹上安装不同数目的吹氧喷咀,一般为6-22支。 例如230t底吹氧气转炉有18-22个喷咀,150t有 12-18个喷咀。
4 脱硫反应
• 230t底吹转炉吹炼过程中,当熔池中的碳达到 0.8%左右时,[S]达到最低值,说明吹炼初期固 体CaO粉末有一定的直接脱硫能力。但随着炉渣 氧化性的提高,熔池一定回硫,吹炼后期随着流 动性的改善,熔池中[S]又降低。与顶吹相比, 底吹氧转炉具有较强的脱硫能力,特别是炉渣碱 度为2.5以上时表现得更明显。
- 1、下载文档前请自行甄别文档内容的完整性,平台不提供额外的编辑、内容补充、找答案等附加服务。
- 2、"仅部分预览"的文档,不可在线预览部分如存在完整性等问题,可反馈申请退款(可完整预览的文档不适用该条件!)。
- 3、如文档侵犯您的权益,请联系客服反馈,我们会尽快为您处理(人工客服工作时间:9:00-18:30)。
“吹氧造锍多金属捕集技术”创造中国冶金奇迹人民日报记者部主任张平力,记者王明峰
中国冶金史上的一场技术革命正在黄河三角洲滨海城市东营悄然掀起。
由山东方圆有色金属集团公司与中国有色工程设计研究总院共同研制开发的“吹氧造锍多金属捕集技术”点燃了这场革命。
新技术的发明
我国不仅是产铜大国,而且是炼铜大国。
传统炼铜工艺在世界上曾一度领先,现代工艺却没有一席之地。
先秦时期就已出现鼓风炉法炼铜,西汉时用铁从硫酸铜(胆铜)溶液中置换铜。
现在我国使用的炼铜技术几乎都来自国外:11种技术中,引进的6种,未经引进而消化吸收开发的有3种。
自己研发的两种炼铜技术中,只有“氧气底吹法”可与国际先进工艺媲美。
之前,国外先进的吹氧炼铜工艺有顶吹和侧吹两种。
中国有色工程设计研究总院(原北京有色冶金设计研究总院)原副院长兼总工程师、全国工程设计大师蒋继穆经过多年潜心研究,改换顶吹、侧吹送氧位置,将氧气用氧枪从熔炼炉底部送入炉内,并攻克了很多工艺和工程难题,发明了氧气底吹炼铜法。
令同行惊奇的是,这一改变竟为有色冶金技术带来了革命性变化,不仅打破了国内铜冶炼技术由国外长期垄断的局面,还为铜铅和金银等稀有贵金属的综合回收提取开辟了一条新路子。
从顶吹、侧吹到底吹,只是吹氧位置的不同,难道别人就想不到吗?“用氧气底吹法炼铜最早是美国和德国的教授于上世纪70年代末80年代初提出来的,并且做过试验。
”蒋继穆坦言,可是他们在做扩大试验时,大量的工程问题解决不了,后来,只好宣布这个“玩意”不行。
“我们最早用氧气底吹技术试验炼铅。
做完5000吨铅冶炼试验后,就想用这个工艺和装置试验炼铜。
”霜染双鬓的蒋继穆娓娓道来,把思绪带回到了1991年的湖南水口山。
“准备半年的试验炉料(相当于3000吨铜的规模),两个月就‘吃’完了。
可是,炉子一点故障都没有,于是接着弄铜精矿连续试验,一试就开了217天。
”
通过试验,发现底吹较之顶吹、侧吹不只是位置不同,它还具有噪音低,车间操作环境更好的优点。
底吹法用铜锍反复冲洗炉渣,更有利于贵金属的捕集,比其它方法的捕集率可提高1-2%。
再者,有利于V族元素等伴生金属挥发富集于烟尘中而易于综合回收,如As的挥发率大于98%。
与我国引进的澳斯麦特法、艾萨法、诺兰达等熔炼工艺比,氧气浓度更高,可达70%-80%,烟气量更少,SO2浓度更大,硫酸厂规模更小,单位投资更少。
至此,一项达到国际先进水平、具有自主知识产权的铜熔炼新工艺诞生了。
给新技术找“婆家”
半工业试验成功并申请专利后,蒋继穆开始四处给新技术找“婆家”。
“当时有3家,四川绵阳想搞个2万吨的铜厂,山西运城也想搞个2-3万吨的铜厂,江西弋阳想搞个3万吨铜厂。
运城因跟中条山抢资源,省里没批。
绵阳要开发第一家,没有这个胆量。
弋阳和一个香港老板合资,真想上,谈得差不多了,合同也签了,都快要做施工图了,结果发现香港老板是骗子。
3家虽都做过可行性研究报告,但均无果而终。
”
蒋继穆说着,像沉浸在回忆中。
后来推广到中条山冶炼厂。
1992年中条山欲采用自主技术白银炼铜专利建一个
3."5万吨的铜厂。
做完可研报告后,经考察发现环保达不到要求,1994年经北京有色冶金设计研究总院推荐,业主改为购买水口山炼铜专利,但由3000吨规模一下扩大到
3."5万吨,北京院只有七八成把握,因为可研规定,一般火法冶炼研究成果产业化扩大比不应超过10倍。
做完初步设计后,当时厂领导同意,但研究院不敢拍胸脯。
到了1996年,该厂新任领导对“中条山只能消化吸收不能引进”的规定不满,赌气要引进国外技术,于是放弃底吹法,而引进澳斯麦特顶吹炼铜技术。
中条山这一卡不要紧,给后边的推广带来了极为不利影响。
内蒙古赤峰金剑冶炼厂鼓风炉改造项目没有采用氧气底吹法即是一例。
虽然,氧气底吹熔炼技术炼铜屡屡受挫,炼铅却处处开花。
2001年“氧气底吹熔炼——鼓风炉还原炼铅法”试验获得成功,2002年即在国内获得大规模推广。
截至目前,已有11条生产线投产,并于2009年开始走向世界。
而这种炼铜新工艺要想实现产业化,规模生产试验是必由之路,这必须要有厂家来承担试验风险。
可是,为了规避风险,它们宁愿花巨资购买国外技术,也不肯做第一个吃螃蟹的人,导致这么一项好工艺一直待字深闺,十几年无人问津。
方圆勇做“第一个吃蟹人”
正在蒋继穆四处推广新技术的时候,黄河三角洲一名勇敢的“铜匠”——山东方圆有色金属集团公司的董事长崔志祥也在为企业更好地发展寻找出路。
方圆集团是一家以废杂铜为主生产阴极铜起家的民营企业,集金、银等稀贵金属的综合提纯、铜材加工于一体。
短短几年即跻身同行业前列。
随着生产规模从年产1万吨发展到18万吨,原料供应日趋紧张。
为解决这一问题,公司打算往上游发展,于2005年提出上铜冶炼项目。
经过考察,从多金属的伴生矿中不仅可以提炼主体金属铜,还可以提取金、银、铂、钯、硒等稀贵金属。
目前国内采用的传统工艺,因技术装备落后,生产过程复杂,资源综合利用效率低而被淘汰或将被淘汰;采用国外的闪速熔炼法、诺兰达法、三菱法等工艺,仅引进技术专利就需上亿美元,而且此类方法只能用于铜等单一金属的提取,对原料的要求严格,适应性差。
提取其中的伴生贵金属如金、银,国内外均使用湿法冶金的氰化法,流程复杂,环境风险大,金属回收率低。
以上工艺,包括引进的装备技术均不能实现多金属的综合提取,资源流失严重,而且原料的适应性差。
而氧气底吹铜熔炼新工艺利用含金铜锍是稀贵金属良好捕集剂的冶金特性,在单一炉体内实现造锍捕金的全过程,铜回收率大于
97."98%,贵金属回收率大于97%,且原料适应强,能处理复杂矿料,并且吃干榨尽,实现零排放。
不仅较好地解决了我国传统工艺和国外引进技术存在的问题,而且由于是自主知识产权,可省去高昂的许可证费。
运用这种技术,
不仅能提高资源利用率,增加企业经济效益,也符合我国倡导的节能减排、科学发展的要求。
这不正是崔志祥心目中理想的技术吗?他和蒋继穆一拍即合,毅然决然地做了第一个吃螃蟹的人。
“这个工艺具有我国自己的知识产权,是个为国争光的技术,我们有责任有义务使其尽快产业化。
”
新技术实现产业化
“从年产3000吨粗铜的半工业化试验,一下扩大到年产10万吨规模,跨度太大,弄不好数亿元的投资就打水漂了。
”公司技术总监申殿邦说起当初董事长的决定还心有余悸。
难道沉浮商海多年的崔志祥不知道这个风险吗?原来,他这么做自有一番道理。
一方面,基于他对形势的判断和市场的把握,中国工业化和城市化必将带来铜需求量的增长。
即使铜市不好,还可以用这项工艺炼金;另一方面,在国际竞争日趋激烈的今天,他日渐体会到拥有独立自主的知识产权是公司发展的必由选择。
2004年,方圆公司和中国有色工程设计研究总院达成协议,共同合作开发“吹氧造锍多金属捕集技术”。
正如崔志祥说的那样,“誓把盐碱滩,变成铜山、银山和金山!”2005年,公司在4000余亩的海滩上建设第三工业园,主体是10万吨铜/a的“吹氧造锍多金属捕集技术”示范工程。
2008年12月16日,项目正式投产。
一贯低调的崔志祥在新项目的发展上却是高调推进。
“我们要有信心将这个项目做成世界上炼铜和回收金银等有价元素的首选工艺,并把它做成名副其实的国家级示范基地和样板工程。
”
令人欣喜的是,工程自投产至今经不断改进,各工序之间基本实现了平衡生产,主要技术经济指标已达到或超过了原设计目标水平。
然而,崔志祥不满足于此,正依托现有生产线开展连续吹炼试验研究,形成新一代达到国际领先水平的连续炼铜新工艺,为国内铜冶炼企业的技术升级提供引领和示范作用。
目前,国务院已将“吹氧造锍多金属捕集工程技术”作为“促进产业振兴的重点先
进技术”列入国家科技支撑计划。
科技部正着手向全国推广该工艺工程。
正像集团歌词写的那样:
方圆天地任飞旋。
链接:
《我国研发的有色金属铜熔炼新技术成功投入使用》
本报讯记者王明峰报道:
我国自主研发、具有国际先进水平的“吹氧造锍多金属捕集技术”日前在山东方圆有色金属集团公司成功投入使用,为铜和稀贵金属的综合回收提取开辟了一条新路子,填补了有色冶金领域的空白,是中国有色冶金史上的一项创举。