3-片重超差、粘冲和松片原因及解决方法
(生产管理知识)制剂生产过程中常见问题和处理方法

制剂生产过程中常见问题和处理方法一、质量问题制剂生产过程由于种种原因造成制剂的质量不合格,尤其是在片剂生产中,造成片剂质量问题的因素更多。
现仅对片剂、胶囊剂及注射剂生产中可能产生质量问题的原因及解决方法作介绍。
(一)片剂生产过程中可能发生问题的分析及解决方法1.松片片剂压成后,硬度不够,表面有麻孔,用手指轻轻加压即碎裂,原因分析及解决方法:①药物粉碎细度不够、纤维性或富有弹性药物或油类成分含量较多而混合不均匀。
可将药物粉碎过100目筛、选用黏性较强的黏合剂、适当增加压片机的压力、增加油类药物吸收剂充分混匀等方法加以克服。
②黏合剂或润湿剂用量不足或选择不当,使颗粒质地疏松或颗粒粗细分布不匀,粗粒与细粒分层。
可选用适当黏合剂或增加用量、改进制粒工艺、多搅拌软材、混均颗粒等方法加以克服。
③颗粒含水量太少,过分干燥的颗粒具有较大的弹性、含有结晶水的药物在颗粒干燥过程中失去较多的结晶水,使颗粒松脆,容易松裂片。
故在制粒时,按不同品种应控制颗粒的含水量。
如制成的颗粒太干时,可喷入适量稀乙醇(50%—60%),混匀后压片。
④药物本身的性质。
密度大压出的片剂虽有一定的硬度,但经不起碰撞和震摇。
如次硝酸铋片、苏打片等往往易产生松片现象;密度小,流动性差,可压性差,重新制粒。
⑤颗粒的流动性差,填入模孔的颗粒不均匀。
⑥有较大块或颗粒、碎片堵塞刮粒器及下料口,影响填充量。
⑦压片机械的因素。
压力过小,多冲压片机冲头长短不齐,车速过快或加料斗中颗粒时多时少。
可调节压力、检查冲模是否配套完整、调整车速、勤加颗粒使料斗内保持一定的存量等方法克服。
2.裂片片剂受到震动或经放置时,有从腰间裂开的称为腰裂;从顶部裂开的称为顶裂,腰裂和顶裂总称为裂片,原因分析及解决方法:①药物本身弹性较强、纤维性药物或因含油类成分较多。
可加入糖粉以减少纤维弹性,加强黏合作用或增加油类药物的吸收剂,充分混匀后压片。
②黏合剂或润湿剂不当或用量不够,颗粒在压片时粘着力差。
片剂产生松片,裂片,粘冲与吊冲,片重差异超限的原因及解决办法
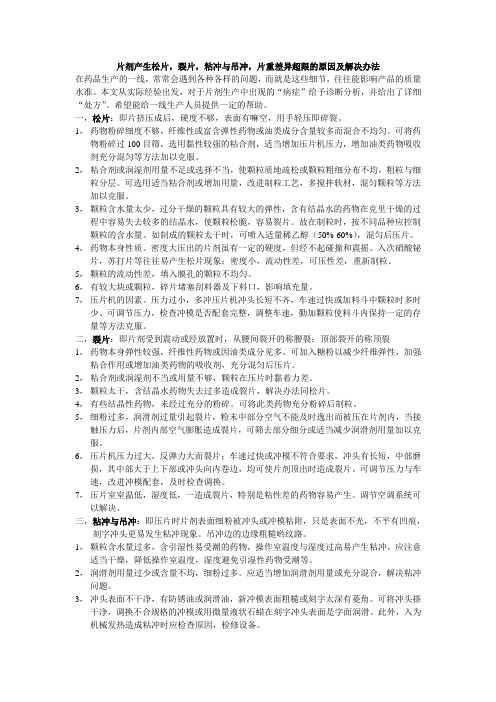
片剂产生松片,裂片,粘冲与吊冲,片重差异超限的原因及解决办法在药品生产的一线,常常会遇到各种各样的问题,而就是这些细节,往往能影响产品的质量水准。
本文从实际经验出发,对于片剂生产中出现的“病症”给予诊断分析,并给出了详细“处方”。
希望能给一线生产人员提供一定的帮助。
一,松片:即片挤压成后,硬度不够,表面有嘛空,用手轻压即碎裂。
1,药物粉碎细度不够,纤维性或富含弹性药物或油类成分含量较多而混合不均匀。
可将药物粉碎过100目筛,选用黏性较强的粘合剂,适当增加压片机压力,增加油类药物吸收剂充分混匀等方法加以克服。
2,粘合剂或润湿剂用量不足或选择不当,使颗粒质地疏松或颗粒粗细分布不均,粗粒与细粒分层。
可选用适当粘合剂或增加用量,改进制粒工艺,多搅拌软材,混匀颗粒等方法加以克服。
3,颗粒含水量太少,过分干燥的颗粒具有较大的弹性,含有结晶水的药物在克里干燥的过程中容易失去较多的结晶水,使颗粒松脆,容易裂片。
故在制粒时,按不同品种应控制颗粒的含水量。
如制成的颗粒太干时,可喷入适量稀乙醇(50%-60%),混匀后压片。
4,药物本身性质。
密度大压出的片剂虽有一定的硬度,但经不起碰撞和震摇。
入次硝酸铋片,苏打片等往往易产生松片现象;密度小,流动性差,可压性差,重新制粒。
5,颗粒的流动性差,填入膜孔的颗粒不均匀。
6,有较大块或颗粒,碎片堵塞刮料器及下料口,影响填充量。
7,压片机的因素。
压力过小,多冲压片机冲头长短不齐,车速过快或加料斗中颗粒时多时少。
可调节压力,检查冲模是否配套完整,调整车速,勤加颗粒使料斗内保持一定的存量等方法克服。
二,裂片:即片剂受到震动或经放置时,从腰间裂开的称腰裂:顶部裂开的称顶裂1,药物本身弹性较强,纤维性药物或因油类成分见多。
可加入糖粉以减少纤维弹性,加强粘合作用或增加油类药物的吸收剂,充分混匀后压片。
2,粘合剂或润湿剂不当或用量不够,颗粒在压片时黏着力差。
3,颗粒太干,含结晶水药物失去过多造成裂片,解决办法同松片。
压片工艺粘冲产生的原因及解决方案

压片工艺粘冲产生的原因及解决方案在压片过程中粘冲分为粘冲和粘连两种方式,粘冲是指粉末颗粒粘附于冲头表面,粘连是指产品粘于冲头表面设计的字母、logo或图案的内部。
该文着重于表述粘冲的原因及解决办法。
当粘冲问题出现的时候,你会听到研发的同事说,我们在实验室阶段采用单冲压片机不粘冲,肯定是压片操作人员操作问题。
当问到压片机操作人员的时候,压片机操作人员会说如果颗粒做的好,我们压片过程中肯定不会出现粘冲问题。
而QA人员会建议检测压片设备是否存在冲模损坏或者冲模是否需要抛光,或者和设备供应商沟通。
但是具体粘冲是来源于压片机还是处方,冲头还是制粒或干燥,或者是操作人员问题,没有一个人可以确定。
一、粘冲的定义粘冲是压片过程中常见问题之一。
当粉末颗粒粘于冲头表面不能形成表面光滑的片时就是出现了粘冲。
下图就是由于粘冲引起的片不合格。
图一是产品粘于上冲表面。
粘连是粘冲的一种,是指颗粒粘于凸出或凹陷的字母和LOGO内部无论是粘冲还是粘连均会导致片不合格。
压片时处方已经配制完成,不能退库,也不能进行重加工,为了保证产品不浪费,压片过程中不得不进行目视监控并手动挑片,这样就会降低生产效率和产品收率。
粘冲可能会出现于压片过程中任何时间段。
经常会在设定压力的时候出现,可能会在压片过程中随机出现,也可能会有规律地出现。
对于一些产品,粘冲具有可预见性,压片机操作人员认为连续压片2个小时不出现粘冲的话就不会出现粘冲。
测定颗粒的水分或者产品的其他性质可以帮助我们预测产品是否粘冲。
尽管有时候混粉性质都符合标准仍然有可能出现粘冲的情况。
事实是,可能在粘冲之前你不知道你的产品到底怎样。
本文提供了一些粘冲的原因及解决方案。
粘冲原因可能和产品、设备、上游工艺或压片机操作有关,也可能是几个因素的综合。
二、粘冲的颗粒可以生产出合格的片当产品第一次压片时,操作人员首先调整片重(通常是通过调节下冲位置,从而改变填充体积,由于松密度不变,片重就得到调节)。
压片机的常见问题及解决方法
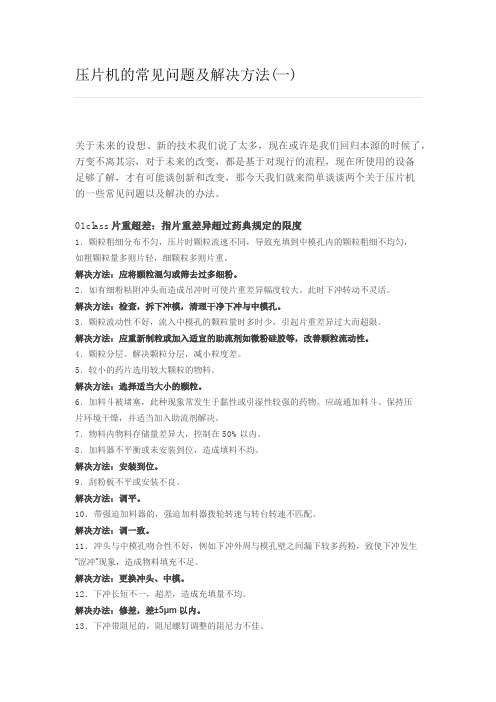
压片机的常见问题及解决方法(一)关于未来的设想、新的技术我们说了太多,现在或许是我们回归本源的时候了,万变不离其宗,对于未来的改变,都是基于对现行的流程,现在所使用的设备足够了解,才有可能谈创新和改变,那今天我们就来简单谈谈两个关于压片机的一些常见问题以及解决的办法。
01class片重超差:指片重差异超过药典规定的限度1.颗粒粗细分布不匀,压片时颗粒流速不同,导致充填到中模孔内的颗粒粗细不均匀,如粗颗粒量多则片轻,细颗粒多则片重。
解决方法:应将颗粒混匀或筛去过多细粉。
2.如有细粉粘附冲头而造成吊冲时可使片重差异幅度较大。
此时下冲转动不灵活。
解决方法:检查,拆下冲模,清理干净下冲与中模孔。
3.颗粒流动性不好,流入中模孔的颗粒量时多时少,引起片重差异过大而超限。
解决方法:应重新制粒或加入适宜的助流剂如微粉硅胶等,改善颗粒流动性。
4.颗粒分层。
解决颗粒分层,减小粒度差。
5.较小的药片选用较大颗粒的物料。
解决方法:选择适当大小的颗粒。
6.加料斗被堵塞,此种现象常发生于黏性或引湿性较强的药物。
应疏通加料斗、保持压片环境干燥,并适当加入助流剂解决。
7.物料内物料存储量差异大,控制在50%以内。
8.加料器不平衡或未安装到位,造成填料不均。
解决方法:安装到位。
9.刮粉板不平或安装不良。
解决方法:调平。
10.带强迫加料器的,强迫加料器拨轮转速与转台转速不匹配。
解决方法:调一致。
11.冲头与中模孔吻合性不好,例如下冲外周与模孔壁之间漏下较多药粉,致使下冲发生“涩冲”现象,造成物料填充不足。
解决方法:更换冲头、中模。
12.下冲长短不一,超差,造成充填量不均。
解决办法:修差,差±5μm以内。
13.下冲带阻尼的,阻尼螺钉调整的阻尼力不佳。
解决方法:重新调整。
14.充填轨道磨损或充填机构不稳定。
解决方法:更换或稳固。
15.追求产量,转台转速过快,填充量不足。
特别是压大片时,要适当降低转速,以保证充填充足。
16.压片机震动过大,结构松动,装配不合理或重新装配;压片机设置压力过大,减小压力。
片剂生产工艺常见问题分析及解决办法
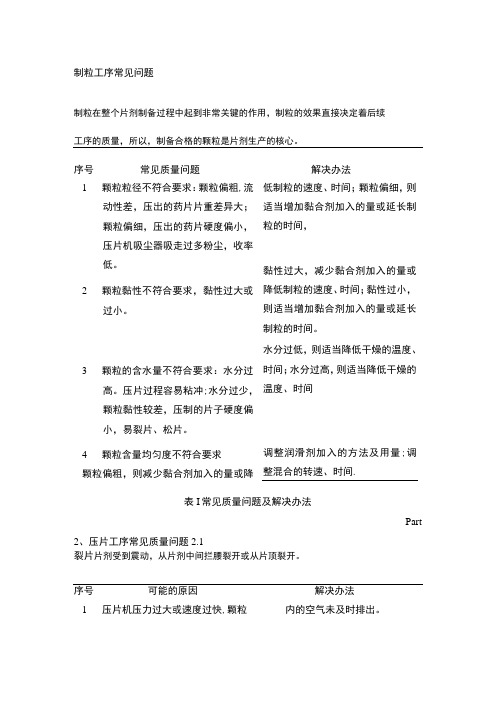
制粒工序常见问题制粒在整个片剂制备过程中起到非常关键的作用,制粒的效果直接决定着后续工序的质量,所以,制备合格的颗粒是片剂生产的核心。
序号常见质量问题解决办法1颗粒粒径不符合要求:颗粒偏粗,流动性差,压出的药片片重差异大;颗粒偏细,压出的药片硬度偏小,压片机吸尘器吸走过多粉尘,收率低。
2颗粒黏性不符合要求,黏性过大或过小。
3颗粒的含水量不符合要求:水分过高。
压片过程容易粘冲;水分过少,颗粒黏性较差,压制的片子硬度偏小,易裂片、松片。
4颗粒含量均匀度不符合要求颗粒偏粗,则减少黏合剂加入的量或降低制粒的速度、时间;颗粒偏细,则适当增加黏合剂加入的量或延长制粒的时间,黏性过大,减少黏合剂加入的量或降低制粒的速度、时间;黏性过小,则适当增加黏合剂加入的量或延长制粒的时间。
水分过低,则适当降低干燥的温度、时间;水分过高,则适当降低干燥的温度、时间调整润滑剂加入的方法及用量;调整混合的转速、时间.表I常见质量问题及解决办法Part2、压片工序常见质量问题2.1裂片片剂受到震动,从片剂中间拦腰裂开或从片顶裂开。
序号可能的原因解决办法1压片机压力过大或速度过快,颗粒内的空气未及时排出。
2处方中油类成分过多,颗粒黏度差。
3环境温度、湿度过低。
4颗粒含水量过少,黏度差一5颗粒粒径差异大或细粉过多,压成的药片上下部硬度强弱不同6黏合剂或润湿剂用量不足,颗粒黏度差适当调低压力或减慢机器速度。
调整处方,替换或增加吸收剂。
适当提高空调系统温、湿度,降低干燥过程的温度或时间可适当过筛部分粗颗粒和细粉。
适当增加黏合剂或润湿剂的用量表2片剂裂开原因及解决办法2.2松片片剂成型后,硬度过低,手指轻轻一捏就碎裂;片剂装袋后,稍加晃动即产生毛边或碎裂现象。
1黏合剂或润湿剂用量不足,2颗粒含水量过少。
3压片机压力过小或运行速度过快。
4有较大团块或颗粒堵塞填粒器及下料口,影响填充量二5冲模长短不一或个别冲模过紧,片剂所受压力不同C6处方中含挥发油成分较多7颗粒流动性差,模孔内填充量不够。
压片过程中如果发生粘冲现象,该怎么解决?

压片过程中如果发生粘冲现象,该怎么解决?在制药生产中,压片是常见的工序。
不过在压片的过程中,很多用户会发现粘冲问题,即粉末颗粒粘附于冲头表面,不能形成表面光滑的片状,使得压片产品不合格。
据了解,针对这种情况,很多用户为了保证产品不浪费,在压片的过程中不得不进行目视监控并手动挑片,但如此一来就会大大降低生产效率和产品收率。
那么,针对这种现象,该怎么解决呢?目前,有行业人士表示,粘冲可能会出现于压片过程中的任何阶段,但粘冲具有可预见性,测定颗粒的水分等性质可以帮助用户预测产品是否粘冲。
粘冲的原因可能和产品、设备、上游工艺或压片机操作有关,也可能是几个因素的综合。
对此,该人士列出了一些粘冲的原因及解决方案,笔者作了简要的梳理。
其一,产品问题。
当产品次进行压片时,操作人员需要先调整片重,再进行片厚的调节。
通过片重、片厚、压片速度、保压时间等因素确定片的硬度。
针对一些压力敏感的颗粒,如果发生粘冲问题,可以快速压几圈硬度很大的片,利用压力使颗粒粘合成片,并把粘在冲上的粉带走。
但需要注意压力的大小,如果超过冲模的负荷可能会导致冲模的损坏甚至断裂。
另外,具备经验的操作人员也可以通过压片机的声音判断是否粘冲。
如存在粘冲现象,可以改变压力设定,如增加压力,减少片厚,降低预压厚度,或者降低压片速度。
其二,设备问题。
用户需要选择正规的冲模设备制造商,因为厂家一般会做一些工作避免粘连、粘冲问题。
有条件的用户也可以定做具有粘连特性的冲模,也改变刻字的高度和角的大小,降低粘冲的风险。
另外,钢材表面的光亮程度也可能发生粘冲。
例如,D2型和440C型钢材比其他型号的钢材含有更多的铬,可以降低粘冲。
同时也可以采用特殊的镀铬涂层,形成高硬度、耐磨的冲模。
不过行业人士也提醒,如果产品本身比较耐磨,镀铬涂层可能很快就会磨光。
其三,空气截留问题。
据了解,压片的过程中可能会把空气吸入冲头的凹面,使得这些空气在片的表面形成松软的区域,发生粘冲情况。
影响片剂质量的主要原因及解决方法
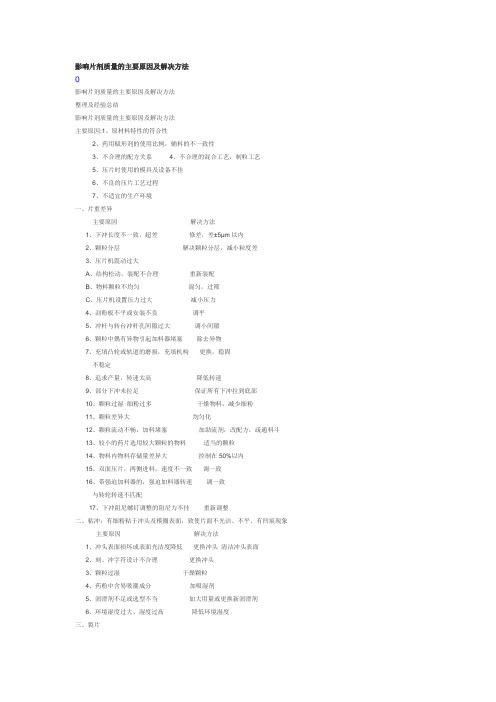
影响片剂质量的主要原因及解决方法影响片剂质量的主要原因及解决方法整理及经验总结影响片剂质量的主要原因及解决方法主要原因:1、原材料特性的符合性2、药用赋形剂的使用比例,辅料的不一致性3、不合理的配方关系4、不合理的混合工艺,制粒工艺5、压片时使用的模具及设备不佳6、不良的压片工艺过程7、不适宜的生产环境一、片重差异主要原因解决方法1、下冲长度不一致,超差修差,差±5μm以内2、颗粒分层解决颗粒分层,减小粒度差3、压片机震动过大A、结构松动,装配不合理重新装配B、物料颗粒不均匀混匀,过筛C、压片机设置压力过大减小压力4、刮粉板不平或安装不良调平5、冲杆与转台冲杆孔间隙过大调小间隙6、颗粒中偶有异物引起加料器堵塞除去异物7、充填凸轮或轨道的磨损,充填机构更换,稳固不稳定8、追求产量,转速太高降低转速9、部分下冲未拉足保证所有下冲拉到底部10、颗粒过湿细粉过多干燥物料,减少细粉11、颗粒差异大均匀化12、颗粒流动不畅,加料堵塞加助流剂,改配方,疏通料斗13、较小的药片选用较大颗粒的物料适当的颗粒14、物料内物料存储量差异大控制在50%以内15、双面压片,两侧进料,速度不一致调一致16、带强迫加料器的,强迫加料器转速调一致与转轮转速不匹配17、下冲阻尼螺钉调整的阻尼力不佳重新调整二、粘冲:有细粉粘于冲头及模圈表面,致使片面不光洁、不平、有凹痕现象主要原因解决方法1、冲头表面损坏或表面光洁度降低更换冲头清洁冲头表面2、刻、冲字符设计不合理更换冲头3、颗粒过湿干燥颗粒4、药粉中含易吸潮成分加吸湿剂5、润滑剂不足或选型不当加大用量或更换新润滑剂6、环境湿度过大、湿度过高降低环境湿度三、裂片主要原因解决方法1、压片时有空气存在于药片当中调整压力、减慢车速、增加预压时间或用有预压的工艺2、冲模磨损严重更换冲模3、黏结剂选型不当或不足更换黏结剂或加量4、颗粒含水量过低增加含水量5、颗粒过细或过粗调整颗粒粒度6、颗粒中油类成分较多加吸油剂7、模具间隙太小、不能顺利排气更换模具四、松片主要原因解决方法1、压力不够增加压力2、受压时间太少、转速快延长受压时间、增加预压、减低转速3、冲头长短不齐调整冲头4、活络冲冲头发生松动进行紧固5、下冲杆掉冲紧固6、黏结剂选型不当或太少更换黏合剂或加量7、颗粒中润滑剂比例不当调节比例8、颗粒太干燥增加颗粒水分9、物料粉碎粒度不够、纤维性或高弹性粉碎粒度过100目筛、加强黏合剂、药物或油类成分多,混合不均吸油剂10、药片压制后,置空气中过久,受潮缩短放置时间五、变色及斑点主要原因解决方法1、颗粒受油脂或其他杂质污染杜绝油脂及杂质污染2、颗粒过硬或含糖品种及有色降低颗粒硬度、有色片剂用片剂颗粒易出现乙醇为润滑剂制粒3、颗粒过大或过小颗粒适宜4、冲模型面出现锈斑清除锈斑5、加料器与转台表面摩擦有金属细粉调节加料器高度随颗粒进入模孔6、冲头与模圈内壁发生摩擦调节模圈致有色金属粉末进入颗粒六、崩解迟缓主要原因解决方法1、黏结剂粘性太强或用量过多,更换黏结剂或降低用量颗粒过硬过粗2、崩解剂选型不当、用量不足更换崩解剂或加量疏水性润滑剂太多降低疏水性润滑剂3、压力过大、片子过硬减低压力七、刻字或线条不清晰主要原因解决方法1、冲模的字符设计、布置不合理更换字符2、冲模型面磨损或破坏更换冲模3、冲模尺寸过大或不够更换冲模4、预压力过大降低预压力粉末直接压片粉末直接压片的应用方法及其注意事项由于粉末直接压片具有较明显的优点,如工艺过程比较简单,不必制粒、干燥,产品崩解或溶出快,成品质量稳定,在国外约有40%的片剂品种已采用这种工艺生产。
压片机粘冲的原因及处理方法
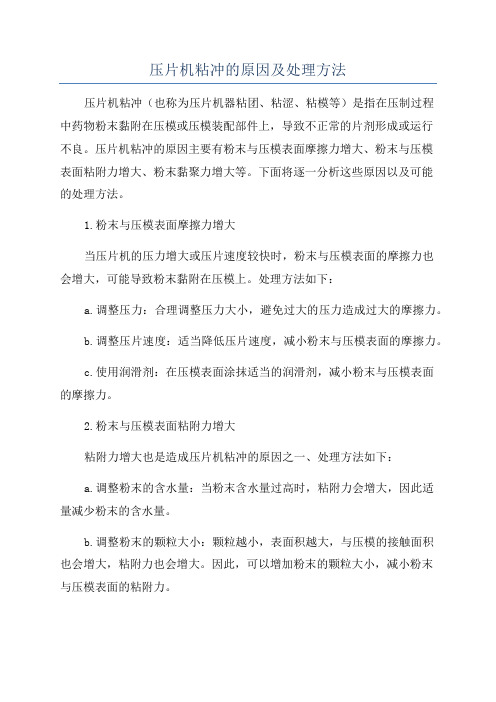
压片机粘冲的原因及处理方法压片机粘冲(也称为压片机器粘团、粘涩、粘模等)是指在压制过程中药物粉末黏附在压模或压模装配部件上,导致不正常的片剂形成或运行不良。
压片机粘冲的原因主要有粉末与压模表面摩擦力增大、粉末与压模表面粘附力增大、粉末黏聚力增大等。
下面将逐一分析这些原因以及可能的处理方法。
1.粉末与压模表面摩擦力增大当压片机的压力增大或压片速度较快时,粉末与压模表面的摩擦力也会增大,可能导致粉末黏附在压模上。
处理方法如下:a.调整压力:合理调整压力大小,避免过大的压力造成过大的摩擦力。
b.调整压片速度:适当降低压片速度,减小粉末与压模表面的摩擦力。
c.使用润滑剂:在压模表面涂抹适当的润滑剂,减小粉末与压模表面的摩擦力。
2.粉末与压模表面粘附力增大粘附力增大也是造成压片机粘冲的原因之一、处理方法如下:a.调整粉末的含水量:当粉末含水量过高时,粘附力会增大,因此适量减少粉末的含水量。
b.调整粉末的颗粒大小:颗粒越小,表面积越大,与压模的接触面积也会增大,粘附力也会增大。
因此,可以增加粉末的颗粒大小,减小粉末与压模表面的粘附力。
c.使用表面处理剂:在压模表面喷涂适当的表面处理剂,减小粉末与压模表面的粘附力。
3.粉末黏聚力增大粉末的黏聚力增大也会导致压片机粘冲。
处理方法如下:a.调整粉末的成分:粉末的成分对黏聚力有着重要影响,可以通过调整粉末的成分来减小黏聚力,例如添加一定量的润滑剂等。
b.调整粉末的粒度分布:不同粒度的粉末会有不同的黏聚力,可以适当调整粉末的粒度分布,使其粒度分布更加均匀。
c.调整粉末的湿度:湿度过高时,粉末的黏聚力会增大,因此可以控制粉末的湿度在适宜的范围内。
除了上述原因和处理方法外a.调整压片机的温度:有些情况下,调整压片机的温度也可以起到减小粉末黏附的效果。
b.更换合适的压模材料:有时候压模的材料也会影响粉末的黏附情况,可以尝试更换合适的压模材料。
c.调整压片参数:适当调整其他压片机参数,如转速、填充度等,来改善粉末黏附问题。
压片机粘冲问题解决方案

粘冲长期压片时经常会发生粘冲,需要预测粘冲的方法以便避免粘冲。
当片剂粉末粘附到冲头表面时就会发生粘冲。
有人通过评估片剂表面的粗糙程度来检测粘冲程度;通过测定刮刀压力来研究是否发生粘冲;研究了各种润滑剂或助流剂的效果,已表明用外加润滑剂可减少粘冲现象;考虑了处理冲头表面,使用硬铬镀层、氮化铬镀层的冲具等进行研究。
有人用专用压片机,用两种方式解决粘冲,一个是压片过程中往冲头上喷微量的硬脂酸镁,还有采用了脱模过程中冲头旋转的方法解决粘冲,有人实际测试过,普通温湿度条件下压VC泡腾片5万片一点问题都没有,主要是脱模的技术是亮点。
《日本药典》(第16版)描述了一种剪切应力法用于评估粉末流动性,目前《日本工业标准》正在研究基于不同测量原理的四种剪切试验。
粘冲指片剂的表面一薄层或一部分粘附到冲头表面或分离的现象,导致片剂表面粗糙不平或有凹痕的现象,对片剂外观产生重大影响,可能在一定程度上不能读取片剂标识(如徽标或产品代码)。
在压片过程中粘冲分为粘冲和粘连两种方式,粘冲是指粉末颗粒粘附于冲头表面,粘连是指产品粘于冲头表面设计的字母、logo或图案的内部。
轻度粘冲难以目测,并且随着压片机的自动化,片剂生产受到严重影响。
引起粘冲的原因有润滑剂用量不足、粘合剂过量、粉末中水分过多,或低熔点药物被压片时产生的摩擦热熔化。
物理化学因素如组成片剂的材料的粒度或结晶度;机械因素如冲头表面的状况或压力;环境因素如温度、相对湿度也可能产生影响。
下面从六个方面来论述粘冲主要原因及解决方案。
1.粘冲的问题是多方面的。
粘冲原因可能和产品、设备、上游工艺或压片机操作有关,也可能是几个因素的综合。
粘冲是压片过程中常见问题之一。
粘冲可能会出现于压片过程中任何时间段。
经常会在设定压力的时候出现,可能会在压片过程中随机出现,也可能会有规律地出现。
对于一些产品,粘冲具有可预见性,压片机操作人员认为连续压片2个小时不出现粘冲的话就不会出现粘冲。
当粘冲问题出现的时候,你会听到研发的同事说,我们在实验室阶段采用单冲压片机不粘冲,肯定是压片操作人员操作问题。
压片机压片过程可能出现的问题及解决办法
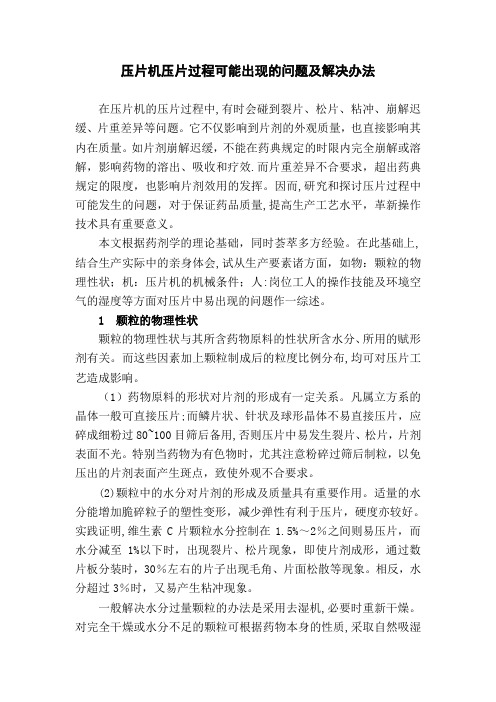
压片机压片过程可能出现的问题及解决办法在压片机的压片过程中,有时会碰到裂片、松片、粘冲、崩解迟缓、片重差异等问题。
它不仅影响到片剂的外观质量,也直接影响其内在质量。
如片剂崩解迟缓,不能在药典规定的时限内完全崩解或溶解,影响药物的溶出、吸收和疗效.而片重差异不合要求,超出药典规定的限度,也影响片剂效用的发挥。
因而,研究和探讨压片过程中可能发生的问题,对于保证药品质量,提高生产工艺水平,革新操作技术具有重要意义。
本文根据药剂学的理论基础,同时荟萃多方经验。
在此基础上,结合生产实际中的亲身体会,试从生产要素诸方面,如物:颗粒的物理性状;机:压片机的机械条件;人:岗位工人的操作技能及环境空气的湿度等方面对压片中易出现的问题作一综述。
1 颗粒的物理性状颗粒的物理性状与其所含药物原料的性状所含水分、所用的赋形剂有关。
而这些因素加上颗粒制成后的粒度比例分布,均可对压片工艺造成影响。
(1)药物原料的形状对片剂的形成有一定关系。
凡属立方系的晶体一般可直接压片;而鳞片状、针状及球形晶体不易直接压片,应碎成细粉过80~100目筛后备用,否则压片中易发生裂片、松片,片剂表面不光。
特别当药物为有色物时,尤其注意粉碎过筛后制粒,以免压出的片剂表面产生斑点,致使外观不合要求。
(2)颗粒中的水分对片剂的形成及质量具有重要作用。
适量的水分能增加脆碎粒子的塑性变形,减少弹性有利于压片,硬度亦较好。
实践证明,维生素C片颗粒水分控制在1.5%~2%之间则易压片,而水分减至1%以下时,出现裂片、松片现象,即使片剂成形,通过数片板分装时,30%左右的片子出现毛角、片面松散等现象。
相反,水分超过3%时,又易产生粘冲现象。
一般解决水分过量颗粒的办法是采用去湿机,必要时重新干燥。
对完全干燥或水分不足的颗粒可根据药物本身的性质,采取自然吸湿或酌喷适宜浓度乙醇,静置或密闭吸湿5小时左右过筛后压片.如含结晶水的药物颗粒,结晶水失去过多时出现的裂片、松片、崩解迟缓等情况则可采用此法解决。
中药片剂粘冲的原因及解决方法

中药片剂粘冲是指中药制剂在生产或使用过程中出现的粘附在包装袋或药瓶内壁上的现象。
这种现象不仅影响了中药品的外观质量,还可能影响药效和药品的服用体验。
中药片剂粘冲的原因各种各样,但主要包括以下几个方面:1. 材料选择:中药片剂制备过程中所使用的原料药材料品质不良、含水量过高、混杂杂质等都会导致制剂粘附。
保证原料品质的稳定性和纯度对避免中药片剂粘冲至关重要。
2. 工艺技术:制剂的生产工艺中,如果烘干温度不够、时间过长或者压片工艺不完善,都可能导致制剂含水量不均匀或者含水过多,从而引起粘附的现象。
3. 包装材料:包装材料的选择和加工质量也是影响中药片剂粘冲的重要因素。
如果包装材料表面不光滑或者容易吸附水分,就容易造成中药片剂的粘附。
针对中药片剂粘冲的问题,可以从以下几个方面着手解决:1. 优化原料选用:对原料的选择要求更加严格,要求供应商提供高纯度、低含水量、无杂质的原料,从源头上杜绝制剂粘冲问题的发生。
2. 改良生产工艺:优化制剂的生产工艺,通过调整烘干温度、时间等参数,确保制剂的含水量均匀且在合适的范围内。
加强粉碎、筛分等步骤的控制,也能有效降低制剂粘冲的发生率。
3. 选用合适的包装材料:选择表面光滑、不易吸附水分的包装材料,并且在加工过程中要控制好包装材料的质量,以确保包装不会成为制剂粘附的隐患。
中药片剂粘冲是一个综合性问题,需要从原料选用、生产工艺到包装材料等多个环节进行全面的控制和管理。
只有全面优化制剂的生产全过程,才能有效避免中药片剂粘冲的问题。
作为写手,我个人认为只有深刻理解和全面掌握中药片剂粘冲的原因和解决方法,才能够更好地指导生产实践。
也需要更加注重原料和生产过程的质量管理,以确保中药片剂的品质和药效。
中药片剂粘冲是一个影响中药品质量的重要问题,对于中药行业来说,如何有效地解决这一问题是至关重要的。
随着中药产业的不断发展,各种新技术、新工艺不断涌现,中药品质管理也面临着新的挑战和机遇。
压片时产生松片,裂片,崩解时限及重量差异问题原因和解决办法
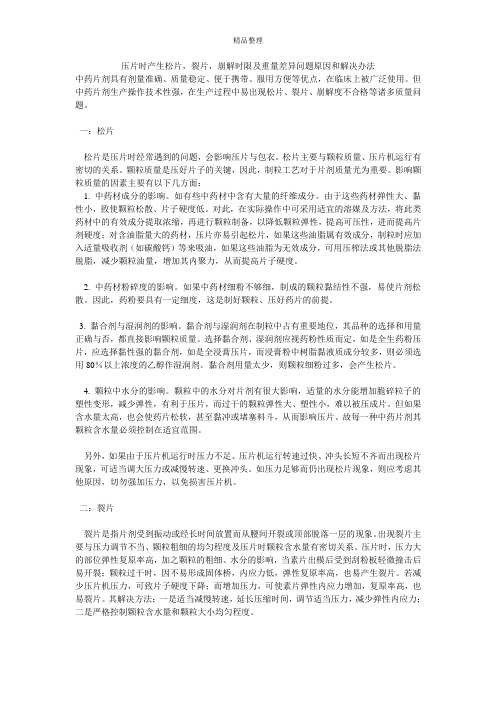
压片时产生松片,裂片,崩解时限及重量差异问题原因和解决办法中药片剂具有剂量准确、质量稳定、便于携带、服用方便等优点,在临床上被广泛使用。
但中药片剂生产操作技术性强,在生产过程中易出现松片、裂片、崩解度不合格等诸多质量问题。
一:松片松片是压片时经常遇到的问题,会影响压片与包衣。
松片主要与颗粒质量、压片机运行有密切的关系。
颗粒质量是压好片子的关键,因此,制粒工艺对于片剂质量尤为重要。
影响颗粒质量的因素主要有以下几方面:1. 中药材成分的影响。
如有些中药材中含有大量的纤维成分。
由于这些药材弹性大、黏性小,致使颗粒松散、片子硬度低。
对此,在实际操作中可采用适宜的溶媒及方法,将此类药材中的有效成分提取浓缩,再进行颗粒制备,以降低颗粒弹性,提高可压性,进而提高片剂硬度;对含油脂量大的药材,压片亦易引起松片,如果这些油脂属有效成分,制粒时应加入适量吸收剂(如碳酸钙)等来吸油,如果这些油脂为无效成分,可用压榨法或其他脱脂法脱脂,减少颗粒油量,增加其内聚力,从而提高片子硬度。
2. 中药材粉碎度的影响。
如果中药材细粉不够细,制成的颗粒黏结性不强,易使片剂松散。
因此,药粉要具有一定细度,这是制好颗粒、压好药片的前提。
3. 黏合剂与湿润剂的影响。
黏合剂与湿润剂在制粒中占有重要地位,其品种的选择和用量正确与否,都直接影响颗粒质量。
选择黏合剂、湿润剂应视药粉性质而定,如是全生药粉压片,应选择黏性强的黏合剂,如是全浸膏压片,而浸膏粉中树脂黏液质成分较多,则必须选用80%以上浓度的乙醇作湿润剂。
黏合剂用量太少,则颗粒细粉过多,会产生松片。
4. 颗粒中水分的影响。
颗粒中的水分对片剂有很大影响,适量的水分能增加脆碎粒子的塑性变形,减少弹性,有利于压片,而过干的颗粒弹性大、塑性小,难以被压成片。
但如果含水量太高,也会使药片松软,甚至黏冲或堵塞料斗,从而影响压片。
故每一种中药片剂其颗粒含水量必须控制在适宜范围。
另外,如果由于压片机运行时压力不足、压片机运行转速过快、冲头长短不齐而出现松片现象,可适当调大压力或减慢转速、更换冲头。
片剂崩解时限等问题总结-20190806

片剂崩解时限等问题总结20190806一、影响片剂的主要原因及解决方法主要原因原村料特性的符合性、药用赋形剂的使用比例,辅料的不一致性,不合理的配方,不合理的混合工艺、制粒工艺,压片时使用的模具及设备不佳,不良的压片工艺过程,不适宜的生产环境2) 粘冲:有细粉枯于冲头及模圈表面致使片面不光洁、不平、有凹痕现象二、粉末直接压片粉末直接压片的应用方法及其注意事项由于粉末直接压片具有较明显的优点,如工艺过程比较简单,不必制粒、干燥,产品崩解或溶出快,成品质量稳定,在国外约有40%的片剂品种已采用这种工艺生产。
a)应用1).用于遇湿、热易变色、分解的药物许多药物对显、热不稳定,如头抱克肟遇湿、热易发生变色,效价降低;雉生素C具有还原性,易空气氧化以致颜色变黄、含量下降,特别是受水分、温度、金属离子等向时更易造成药品变质;氮茶碱遇湿、热均易分解、变色,放出强烈氨臭;利福平对湿、热也不稳定,含量下降,溶出度不合格;维生素81、B2、B6等对湿热、金属离子均不稳定。
这些药物若来用常抛法制粒,因在生产过程中,药物与合剂中的溶接角触,并经高温干燥,必会对产品质量有景知向。
而来用粉末直接压片工艺,所制得的片剥片面光滑,无裂片和粘冲,片重差异小,崩解时限短,经加速试验、留样观察,片剂各项质量指标均无变化。
2).用于酯类、酰胺类等易水解药物因盐酸甲氯芬酯极易水解,采用常规的湿法制粒工艺,因生产过程中加入粘合剂,含有水分,在干燥的高温条件下,药物分解加快,从而影响药品的质量,不仅降低了药物的含量,而且增加了降解产物,使疗效降低,副作用增加。
而采用粉末直接压片工艺生产,避免了与水的接触同时可选用引湿性小的辅料,进一步保证药物在贮藏期间的稳定性。
3).用于溶解度较小或疏水性的药物溶解度小的药物的溶出度受其比表面积和药物成品表面性质的影响较大,通过药剂学方法,选用疏水性辅料,经粉末直接压片后,药品崩解后药物直接从粉末中释放出来分散度增大,溶出加快,相对生物利用度提高4).用于低熔点及产生共熔的复方药物环扁桃酯的熔点为50C〜62℃,常规湿法制粒可造成药物熔化而影响质量;盐酸麻黄素和盐酸苯海拉明的复方制剂,湿法制粒干燥时两者可产生共熔,不易烘干。
片剂制备中可能发生的问题及原因分析
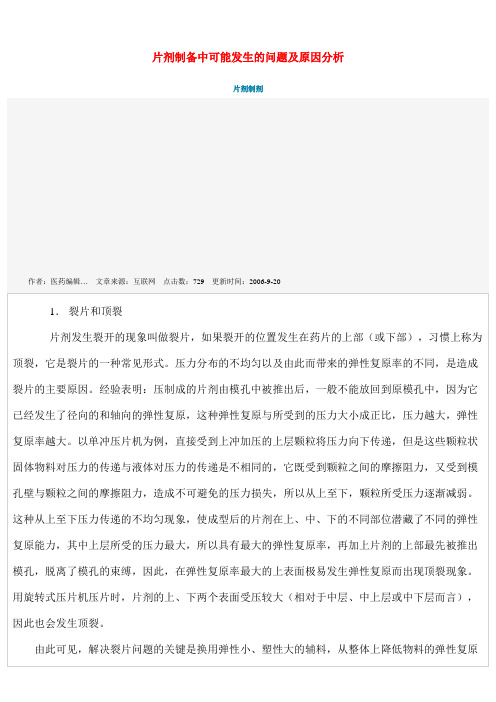
率。
另外,颗粒中细粉太多、颗粒过干、粘合剂粘性较弱或用量不足、片剂过厚以及加压过快也可造成裂片。
2.松片片剂硬度不够,稍加触动即散碎的现象称为松片。
3.粘冲片剂的表面被冲头粘去一薄层或一小部分,造成片面粗糙不平或有凹痕的现象,一般即为粘冲;若片剂的边缘粗糙或有缺痕,则可相应地称为粘模。
造成粘冲或粘模的主要原因有:颗粒不够干燥、物料较易吸湿、润滑剂选用不当或用量不足、冲头表面锈蚀或刻字粗糙不光等,应根据实际情况,查找原因予以解决。
4.片重差异超限即片剂的重量超出药典规定的片重差异允许范围,产生的原因及解决办法是:①颗粒流动性不好,流入模孔的颗粒量时多时少,引起片重差异过大,应重新制粒或加入较好的助流剂如微粉硅胶等,改善颗粒流动性;②颗粒内的细粉太多或颗粒的大小相差悬殊,致使流入模孔内的物料时重时轻,应除去过多的细粉或重新制粒;③加料斗内的颗粒时多时少,造成加料的重量波动也会引起片重差异超限,所以应保持加料斗内始终有1/3量以上的颗粒;④冲头与模孔吻合性不好,例如下冲外周与模孔壁之间漏下较多药粉,致使下冲发生"涩冲"现象,必然造成物料填充不足,对此应更换冲头、模圈。
5.崩解迟缓一般的口服片剂(缓控释片剂、口含片、咀嚼片等特殊片剂除外)都应在胃肠道内迅速崩解,药典中规定了崩解度检查的具体方法及相应的崩解时限。
若某一片剂超过了规定的崩解时限,即称为崩解超限或崩解迟缓。
要对这一问题加以解决,必须对崩解的机理及其影响因素有所了解。
(1)崩解机理简介①有些片剂中含有较多的可溶性成份,遇水后,这些可溶性成份迅速溶解,形成很多溶蚀性孔洞,致使片剂难以继续维持其片状形式而蚀解溃碎即崩解;②有些片剂之所以能固结成片状,与其中的可溶性成份在颗粒间形成"固体桥"有关,当水分透入片剂后,这些"固体桥"溶解,结合力消失,片剂作为一个整体就难以继续存在,从而发生崩解;③有些片剂中含有遇水可产生气体的物质,例如:泡腾片中含有的碳酸氢钠与枸橼酸,遇水后产生二氧化碳气体造成片剂的崩解。
片剂产生松片,裂片,粘冲与吊冲,片重差异超限的原因及解决办法
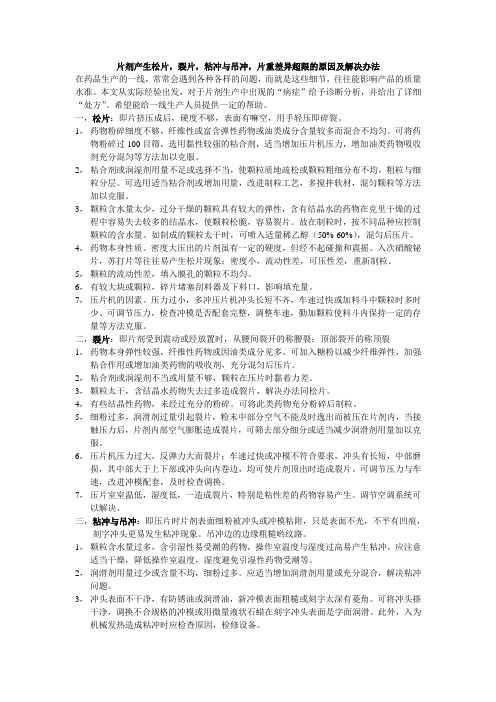
片剂产生松片,裂片,粘冲与吊冲,片重差异超限的原因及解决办法在药品生产的一线,常常会遇到各种各样的问题,而就是这些细节,往往能影响产品的质量水准。
本文从实际经验出发,对于片剂生产中出现的“病症”给予诊断分析,并给出了详细“处方”。
希望能给一线生产人员提供一定的帮助。
一,松片:即片挤压成后,硬度不够,表面有嘛空,用手轻压即碎裂。
1,药物粉碎细度不够,纤维性或富含弹性药物或油类成分含量较多而混合不均匀。
可将药物粉碎过100目筛,选用黏性较强的粘合剂,适当增加压片机压力,增加油类药物吸收剂充分混匀等方法加以克服。
2,粘合剂或润湿剂用量不足或选择不当,使颗粒质地疏松或颗粒粗细分布不均,粗粒与细粒分层。
可选用适当粘合剂或增加用量,改进制粒工艺,多搅拌软材,混匀颗粒等方法加以克服。
3,颗粒含水量太少,过分干燥的颗粒具有较大的弹性,含有结晶水的药物在克里干燥的过程中容易失去较多的结晶水,使颗粒松脆,容易裂片。
故在制粒时,按不同品种应控制颗粒的含水量。
如制成的颗粒太干时,可喷入适量稀乙醇(50%-60%),混匀后压片。
4,药物本身性质。
密度大压出的片剂虽有一定的硬度,但经不起碰撞和震摇。
入次硝酸铋片,苏打片等往往易产生松片现象;密度小,流动性差,可压性差,重新制粒。
5,颗粒的流动性差,填入膜孔的颗粒不均匀。
6,有较大块或颗粒,碎片堵塞刮料器及下料口,影响填充量。
7,压片机的因素。
压力过小,多冲压片机冲头长短不齐,车速过快或加料斗中颗粒时多时少。
可调节压力,检查冲模是否配套完整,调整车速,勤加颗粒使料斗内保持一定的存量等方法克服。
二,裂片:即片剂受到震动或经放置时,从腰间裂开的称腰裂:顶部裂开的称顶裂1,药物本身弹性较强,纤维性药物或因油类成分见多。
可加入糖粉以减少纤维弹性,加强粘合作用或增加油类药物的吸收剂,充分混匀后压片。
2,粘合剂或润湿剂不当或用量不够,颗粒在压片时黏着力差。
3,颗粒太干,含结晶水药物失去过多造成裂片,解决办法同松片。
压片中粘冲的原因与对策
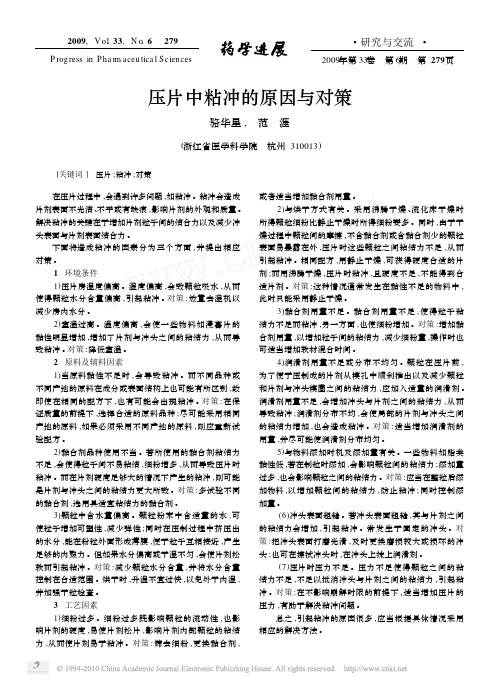
2009,V ol.33,N o.6 279 P rogress in Pha r m aceu tica l Sciences・研究与交流・ 2009年第33卷 第6期 第279 页 压片中粘冲的原因与对策骆华星, 范 涯(浙江省医学科学院 杭州310013)[关键词] 压片;粘冲;对策 在压片过程中,会遇到许多问题,如粘冲。
粘冲会造成片剂表面不光洁、不平或有缺痕,影响片剂的外观和质量。
解决粘冲的关键在于增加片剂粒子间的结合力以及减少冲头表面与片剂表面结合力。
下面将造成粘冲的因素分为三个方面,并提出相应对策。
1 环境条件1)压片房湿度偏高。
湿度偏高,会致颗粒吸水,从而使得颗粒水分含量偏高,引起粘冲。
对策:放置去湿机以减少房内水分。
2)室温过高。
温度偏高,会使一些物料如浸膏片的黏性明显增加,增加了片剂与冲头之间的粘结力,从而导致粘冲。
对策:降低室温。
2 原料及辅料因素1)当原料黏性不足时,会导致粘冲。
而不同品种或不同产地的原料在成分或表面结构上也可能有所区别,故即使在相同的配方下,也有可能会出现粘冲。
对策:在保证质量的前提下,选择合适的原料品种;尽可能采用相同产地的原料,如果必须采用不同产地的原料,则应重新试验配方。
2)黏合剂品种使用不当。
若所使用的黏合剂粘结力不足,会使得粒子间不易粘结,细粉增多,从而导致压片时粘冲。
而在片剂硬度足够大的情况下产生的粘冲,则可能是片剂与冲头之间的粘结力更大所致。
对策:多试验不同的黏合剂,选用具适宜粘结力的黏合剂。
3)颗粒中含水量偏高。
颗粒粉末中含适量的水,可使粒子增加可塑性,减少弹性;同时在压制过程中挤压出的水分,能在粉粒外面形成薄膜,便于粒子互相接近,产生足够的内聚力。
但如果水分偏高或干湿不匀,会使片剂松软而引起粘冲。
对策:减少颗粒水分含量,并将水分含量控制在合适范围。
烘干时,升温不宜过快,以免外干内湿,并加强干粒检查。
3 工艺因素1)细粉过多。
细粉过多既影响颗粒的流动性,也影响片剂的硬度,易使片剂松片,影响片剂内部颗粒的粘结力,从而使片剂易于粘冲。
- 1、下载文档前请自行甄别文档内容的完整性,平台不提供额外的编辑、内容补充、找答案等附加服务。
- 2、"仅部分预览"的文档,不可在线预览部分如存在完整性等问题,可反馈申请退款(可完整预览的文档不适用该条件!)。
- 3、如文档侵犯您的权益,请联系客服反馈,我们会尽快为您处理(人工客服工作时间:9:00-18:30)。
片重超差、粘冲和松片原因及解决方法
一:片重超差的原因及处理如下:
片重超差是指片重差异超过药典规定的限度。
1.颗粒粗细分布不匀,压片时颗粒流速不同,导致填充到中模孔内的颗粒粗细不均匀,如粗颗粒量多则片轻,细颗粒多则片重。
解决方法:应将颗粒混匀或筛去过多细粉,控制粒径分布范围。
2.如有细粉粘附冲头而造成吊冲时可使片重差异幅度较大。
此时下冲转动不灵活,应及时检查,拆下冲模,清理干净下冲与中模孔。
3.颗粒流动性不好,流入中模孔的颗粒量时多时少,引起片重差异过大而超限。
解决方法:应重新制粒或加入适宜的助流剂如微粉硅胶等,改善颗粒流动性。
4.颗粒分层。
解决颗粒分层,减小粒度差。
5.较小的药片选用较大颗粒的物料。
解决方法:选择适当大小的颗粒。
6.加料斗被堵塞,此种现象常发生于粘性或引湿性较强的药物。
应疏通加料斗、
保持压片环境干燥,并适当加入助流剂解决。
7.物料内物料存储量差异大,控制在
50%以内。
8.加料器不平衡或未安装到位,造成填料不均。
9.刮粉板不平或安装不良。
解决方法:调平。
10.带强迫加料器的,强迫加料器拨轮转速与转台转速不匹配。
解决方法:调一致。
11.冲头与中模孔吻合性不好,例如下冲外周与模孔壁之间漏下较多药粉,致使下冲发生“涩冲”现象,造成物料填充不足,对此应更换冲头、中模。
12.下冲长短不一,超差,造成充填量不均。
解决办法:修差,差±5μm以内。
13.下冲带阻尼的,阻尼螺钉调整的阻尼力不佳。
重新调整。
14.充填轨道磨损或充填机构不稳定。
解决方法:更换或稳固。
15.追求产量,转台转速过快,填充量不足。
特别是压大片时,要适当降低转速,以保证充填充足。
16.压片机震动过大,结构松动,装配不合理或重新装配;压片机设置压力过大,减小压力。
二:粘冲的原因及处理如下:
粘冲是指压片时片剂表面细粉被冲头和冲模黏附,致使片面不光、不平有凹痕,
刻字冲头更容易发生粘冲现象。
1.冲头表面损坏或表面光洁度降低,也可能有防锈油或润滑油、新冲模表面粗糙或刻字太深有棱角。
可将冲头擦净、调换不合规格的冲模或用微量液状石蜡擦在刻字冲头表面使字面润滑。
此外,如为机械发热而造成粘冲时应检查原因,检修设备。
2.刻、冲字符设计不合理。
相应更换冲头或更改字符设计。
3.颗粒含水量过多或颗粒干湿不均而造成粘冲。
解决办法:控制颗粒水分在2%~3%左右,加强干粒检查。
4.润滑剂用量不足或选型不当、细粉过多。
应适当增加润滑剂用量或更换新润滑剂、除去过多细粉。
5.原辅料细度差异大,造成混合不均匀或混合时间不当。
解决办法:对原辅料进行粉碎、过筛,使其细度达到该品种的质量要求,同时掌握、控制好混合时间。
6.粘合剂浓度低或因粘合剂质量原因而造成粘合力差,细粉太多(超过
10%以上)而粘冲。
解决办法:用40目的筛网筛出细粉,重新制粒、干燥、整粒后,全批混合均匀,再压片。
7.由于原料本身原因(如具有引湿性)造成粘冲。
解决办法:加入一定量的吸收剂(如加入3%的磷酸氢钙)避免粘冲。
8.环境湿度过大、湿度过高。
降低环境湿度。
9.操作室温度过高易产生粘冲。
应注意降低操作室温度。
三:松片的原因及处理如下:
片剂压成后,硬度不够,表面有麻孔,用手指轻轻加压即碎裂,造成原因分析及解决方法:1.压力不够。
解决方法:增加压力。
然而,对于一些特殊用途的大片要求压力较大,其压力要求达到压片机压力上限或者超出压力上限的,需要定制大压力的相应规格的压片机。
2.受压时间太少、转速快。
相应延长受压时间、增加预压、减低转速。
3.多冲压片机上冲长短不齐。
解决方法:调整冲头。
4.活络冲冲头发生松动。
进行紧固。