有史最全-工程图技术要求(适用于工厂出图)
工程图常见技术要求
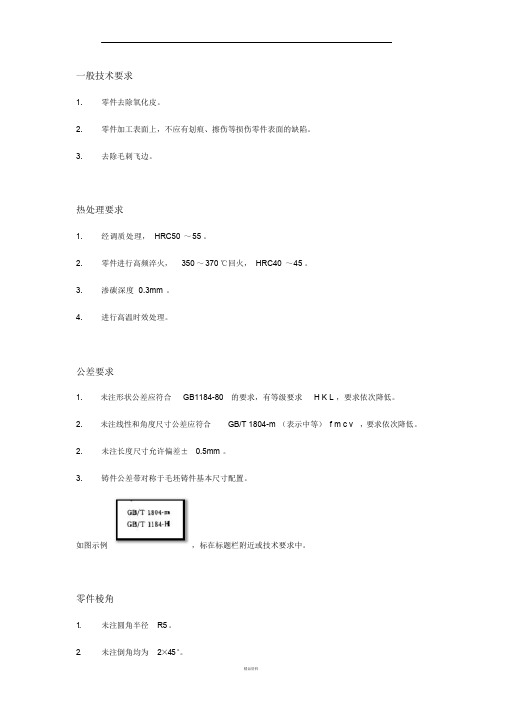
一般技术要求1. 零件去除氧化皮。
2. 零件加工表面上,不应有划痕、擦伤等损伤零件表面的缺陷。
3. 去除毛刺飞边。
热处理要求1. 经调质处理,HRC50 ~55 。
2. 零件进行高频淬火,350 ~370 ℃回火,HRC40 ~45 。
3. 渗碳深度0.3mm 。
4. 进行高温时效处理。
公差要求1. 未注形状公差应符合GB1184-80 的要求,有等级要求H K L ,要求依次降低。
2. 未注线性和角度尺寸公差应符合GB/T 1804-m (表示中等)f m c v ,要求依次降低。
2. 未注长度尺寸允许偏差±0.5mm 。
3. 铸件公差带对称于毛坯铸件基本尺寸配置。
如图示例,标在标题栏附近或技术要求中。
零件棱角1.未注圆角半径R5 。
2.未注倒角均为2×45 °。
3.锐角/尖角/锐边倒钝。
装配要求1. 各密封件装配前必须浸透油。
2. 装配滚动轴承允许采用机油加热进行热装,油的温度不得超过100 ℃。
3. 齿轮装配后,齿面的接触斑点和侧隙应符合GB10095 和GB11365 的规定。
4. 装配液压系统时允许使用密封填料或密封胶,但应防止进入系统中。
5. 进入装配的零件及部件(包括外购件、外协件),均必须具有检验部门的合格证方能进行装配。
6. 零件在装配前必须清理和清洗干净,不得有毛刺、飞边、氧化皮、锈蚀、切屑、油污、着色剂和灰尘等。
7. 装配前应对零、部件的主要配合尺寸,特别是过盈配合尺寸及相关精度进行复查。
8. 装配过程中零件不允许磕、碰、划伤和锈蚀。
9. 螺钉、螺栓和螺母紧固时,严禁打击或使用不合适的旋具和扳手。
紧固后螺钉槽、螺母和螺钉、螺栓头部不得损坏。
10. 规定拧紧力矩要求的紧固件,必须采用力矩扳手,并按规定的拧紧力矩紧固。
11. 同一零件用多件螺钉(螺栓)紧固时,各螺钉(螺栓)需交叉、对称、逐步、均匀拧紧。
12. 圆锥销装配时应与孔应进行涂色检查,其接触率不应小于配合长度的60% ,并应均匀分布。
工程图常见技术要求

一般技术要求1. 零件去除氧化皮。
2. 零件加工表面上,不应有划痕、擦伤等损伤零件表面的缺陷。
3. 去除毛刺飞边。
热处理要求1. 经调质处理,HRC50~55。
2. 零件进行高频淬火,350~370℃回火,HRC40~45。
3. 渗碳深度0.3mm。
4. 进行高温时效处理。
公差要求1.未注形状公差应符合GB1184-80的要求,有等级要求H K L,要求依次降低。
2.未注线性和角度尺寸公差应符合GB/T 1804-m(表示中等)f m c v ,要求依次降低。
2. 未注长度尺寸允许偏差±0.5mm。
3. 铸件公差带对称于毛坯铸件基本尺寸配置。
如图示例,标在标题栏附近或技术要求中。
零件棱角1. 未注圆角半径R5。
2. 未注倒角均为2×45°。
3. 锐角/尖角/锐边倒钝。
装配要求1. 各密封件装配前必须浸透油。
2. 装配滚动轴承允许采用机油加热进行热装,油的温度不得超过100℃。
3. 齿轮装配后,齿面的接触斑点和侧隙应符合GB10095和GB11365的规定。
4. 装配液压系统时允许使用密封填料或密封胶,但应防止进入系统中。
5. 进入装配的零件及部件(包括外购件、外协件),均必须具有检验部门的合格证方能进行装配。
6. 零件在装配前必须清理和清洗干净,不得有毛刺、飞边、氧化皮、锈蚀、切屑、油污、着色剂和灰尘等。
7. 装配前应对零、部件的主要配合尺寸,特别是过盈配合尺寸及相关精度进行复查。
8. 装配过程中零件不允许磕、碰、划伤和锈蚀。
9. 螺钉、螺栓和螺母紧固时,严禁打击或使用不合适的旋具和扳手。
紧固后螺钉槽、螺母和螺钉、螺栓头部不得损坏。
10. 规定拧紧力矩要求的紧固件,必须采用力矩扳手,并按规定的拧紧力矩紧固。
11. 同一零件用多件螺钉(螺栓)紧固时,各螺钉(螺栓)需交叉、对称、逐步、均匀拧紧。
12. 圆锥销装配时应与孔应进行涂色检查,其接触率不应小于配合长度的60%,并应均匀分布。
机械制图工程图技术要求全

机械图纸-技术要求汇总一般技术要求1. 零件去除氧化皮。
2. 零件加工表面上,不应有划痕、擦伤等损伤零件表面的缺陷。
3. 去除毛刺飞边。
热处理要求1. 经调质处理,HRC50~55。
2. 零件进行高频淬火,350~370℃回火,HRC40~45。
3. 渗碳深度0.3mm。
4. 进行高温时效处理。
公差要求1. 未注形状公差应符合GB1184-80的要求。
2. 未注长度尺寸允许偏差±0.5mm。
3. 铸件公差带对称于毛坯铸件基本尺寸配置。
零件棱角1. 未注圆角半径R5。
2. 未注倒角均为2×45°。
3. 锐角/尖角/锐边倒钝。
装配要求1. 各密封件装配前必须浸透油。
2. 装配滚动轴承允许采用机油加热进行热装,油的温度不得超过100℃。
3. 齿轮装配后,齿面的接触斑点和侧隙应符合GB10095和GB11365的规定。
4. 装配液压系统时允许使用密封填料或密封胶,但应防止进入系统中。
5. 进入装配的零件及部件(包括外购件、外协件),均必须具有检验部门的合格证方能进行装配。
6. 零件在装配前必须清理和清洗干净,不得有毛刺、飞边、氧化皮、锈蚀、切屑、油污、着色剂和灰尘等。
7. 装配前应对零、部件的主要配合尺寸,特别是过盈配合尺寸及相关精度进行复查。
8. 装配过程中零件不允许磕、碰、划伤和锈蚀。
9. 螺钉、螺栓和螺母紧固时,严禁打击或使用不合适的旋具和扳手。
紧固后螺钉槽、螺母和螺钉、螺栓头部不得损坏。
10. 规定拧紧力矩要求的紧固件,必须采用力矩扳手,并按规定的拧紧力矩紧固。
11. 同一零件用多件螺钉(螺栓)紧固时,各螺钉(螺栓)需交叉、对称、逐步、均匀拧紧。
12. 圆锥销装配时应与孔应进行涂色检查,其接触率不应小于配合长度的60%,并应均匀分布。
13. 平键与轴上键槽两侧面应均匀接触,其配合面不得有间隙。
14. 花键装配同时接触的齿面数不少于2/3,接触率在键齿的长度和高度方向不得低于50%。
图纸技术要求大全
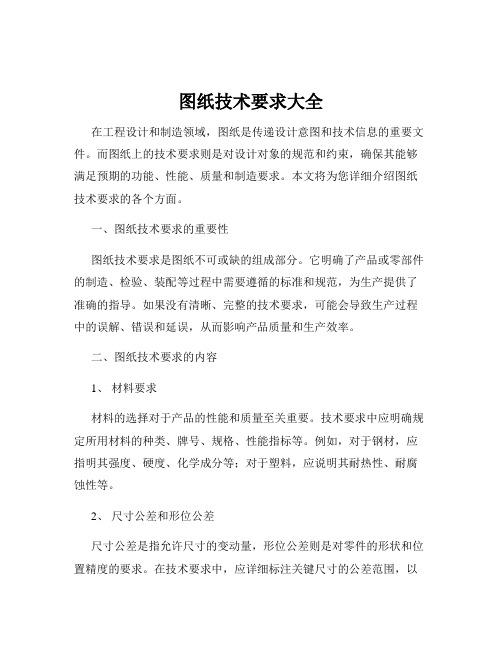
图纸技术要求大全在工程设计和制造领域,图纸是传递设计意图和技术信息的重要文件。
而图纸上的技术要求则是对设计对象的规范和约束,确保其能够满足预期的功能、性能、质量和制造要求。
本文将为您详细介绍图纸技术要求的各个方面。
一、图纸技术要求的重要性图纸技术要求是图纸不可或缺的组成部分。
它明确了产品或零部件的制造、检验、装配等过程中需要遵循的标准和规范,为生产提供了准确的指导。
如果没有清晰、完整的技术要求,可能会导致生产过程中的误解、错误和延误,从而影响产品质量和生产效率。
二、图纸技术要求的内容1、材料要求材料的选择对于产品的性能和质量至关重要。
技术要求中应明确规定所用材料的种类、牌号、规格、性能指标等。
例如,对于钢材,应指明其强度、硬度、化学成分等;对于塑料,应说明其耐热性、耐腐蚀性等。
2、尺寸公差和形位公差尺寸公差是指允许尺寸的变动量,形位公差则是对零件的形状和位置精度的要求。
在技术要求中,应详细标注关键尺寸的公差范围,以及形状(如平面度、圆度)和位置(如平行度、垂直度)的公差要求。
这有助于保证零件之间的配合精度和装配质量。
3、表面质量要求表面质量直接影响产品的外观、耐磨性和耐腐蚀性等。
技术要求中应规定表面粗糙度、表面处理方式(如电镀、喷漆)以及表面缺陷的允许程度。
4、热处理要求对于需要进行热处理的零件,应明确热处理的类型(如淬火、回火、退火)、工艺参数(如温度、时间)以及处理后的性能指标。
5、加工工艺要求这包括加工方法(如车削、铣削、磨削)、加工顺序、切削参数等。
此外,对于一些特殊的加工工艺,如焊接、铸造、锻造等,也应给出相应的技术要求。
6、装配要求如果是装配图,应规定零部件的装配顺序、配合要求、紧固力矩等,以确保装配的正确性和可靠性。
7、检验要求明确检验的方法、量具、检验项目和验收标准。
这有助于保证产品在生产过程中的质量控制。
8、包装和标识要求说明产品的包装方式、防护措施以及标识内容(如产品名称、型号、批次、生产日期等),以便于产品的储存、运输和识别。
工程图常见技术要求
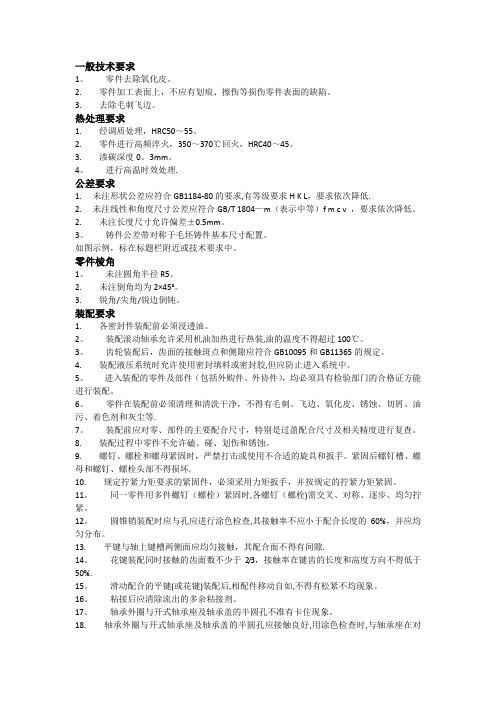
一般技术要求1。
零件去除氧化皮。
2. 零件加工表面上,不应有划痕、擦伤等损伤零件表面的缺陷。
3. 去除毛刺飞边。
热处理要求1. 经调质处理,HRC50~55。
2. 零件进行高频淬火,350~370℃回火,HRC40~45。
3. 渗碳深度0。
3mm。
4。
进行高温时效处理.公差要求1.未注形状公差应符合GB1184-80的要求,有等级要求H K L,要求依次降低.2.未注线性和角度尺寸公差应符合GB/T 1804—m(表示中等)f m c v ,要求依次降低。
2. 未注长度尺寸允许偏差±0.5mm。
3。
铸件公差带对称于毛坯铸件基本尺寸配置。
如图示例,标在标题栏附近或技术要求中。
零件棱角1。
未注圆角半径R5。
2. 未注倒角均为2×45°。
3. 锐角/尖角/锐边倒钝。
装配要求1. 各密封件装配前必须浸透油。
2。
装配滚动轴承允许采用机油加热进行热装,油的温度不得超过100℃。
3。
齿轮装配后,齿面的接触斑点和侧隙应符合GB10095和GB11365的规定。
4. 装配液压系统时允许使用密封填料或密封胶,但应防止进入系统中。
5。
进入装配的零件及部件(包括外购件、外协件),均必须具有检验部门的合格证方能进行装配。
6。
零件在装配前必须清理和清洗干净,不得有毛刺、飞边、氧化皮、锈蚀、切屑、油污、着色剂和灰尘等.7。
装配前应对零、部件的主要配合尺寸,特别是过盈配合尺寸及相关精度进行复查。
8. 装配过程中零件不允许磕、碰、划伤和锈蚀。
9. 螺钉、螺栓和螺母紧固时,严禁打击或使用不合适的旋具和扳手。
紧固后螺钉槽、螺母和螺钉、螺栓头部不得损坏.10. 规定拧紧力矩要求的紧固件,必须采用力矩扳手,并按规定的拧紧力矩紧固。
11。
同一零件用多件螺钉(螺栓)紧固时,各螺钉(螺栓)需交叉、对称、逐步、均匀拧紧。
12。
圆锥销装配时应与孔应进行涂色检查,其接触率不应小于配合长度的60%,并应均匀分布。
13. 平键与轴上键槽两侧面应均匀接触,其配合面不得有间隙.14。
图纸技术要求大全

图纸技术要求大全在工程和制造领域,图纸是至关重要的沟通工具,它能够清晰地传达设计意图和规范,确保产品或项目的顺利实施。
而图纸上的技术要求则是对设计的进一步补充和说明,为生产、加工、检验等环节提供了明确的指导。
下面我们就来详细了解一下图纸技术要求的方方面面。
一、尺寸与公差要求尺寸是图纸中最基本的元素之一,它准确地描述了零件或结构的大小和形状。
在标注尺寸时,需要遵循一定的标准和规范,确保尺寸的清晰、准确和完整。
同时,为了保证零件在制造过程中的互换性和功能性,还需要规定公差。
公差是允许尺寸的变动量,分为尺寸公差和形位公差。
尺寸公差控制零件的尺寸精度,形位公差则控制零件的形状和位置精度。
例如,对于一个圆柱形零件,不仅要规定其直径的尺寸和公差,还要规定圆柱度、同轴度等形位公差要求。
二、材料要求材料的选择直接影响到产品的性能、质量和成本。
在图纸技术要求中,需要明确指定所使用的材料种类、牌号、规格等信息。
例如,对于机械零件,可以指定使用 45 号钢、铝合金等材料,并注明其热处理要求,如淬火、回火等。
对于建筑结构,可能会指定使用混凝土的强度等级、钢材的型号等。
此外,还需要考虑材料的供应情况和成本,选择合适的替代材料方案。
三、表面处理要求表面处理可以提高零件的耐腐蚀性、耐磨性、美观度等性能。
常见的表面处理方法包括电镀、喷涂、氧化等。
在图纸技术要求中,需要明确表面处理的种类、工艺要求和质量标准。
例如,对于需要防锈的零件,可以要求进行镀锌处理,并规定镀层的厚度和质量要求。
对于外观要求较高的零件,可以进行喷漆处理,并指定漆的颜色、光泽度等要求。
四、加工工艺要求加工工艺是将原材料转化为成品的过程,它直接影响到产品的质量和生产效率。
在图纸技术要求中,需要根据零件的结构和功能,规定合理的加工工艺方法和顺序。
例如,对于一个复杂的零件,可能需要先进行铸造或锻造,然后再进行机械加工。
对于有精度要求的孔和轴,可能需要采用磨削加工工艺。
每个机械工程师必备的图纸技术要求大全,你懂多少?
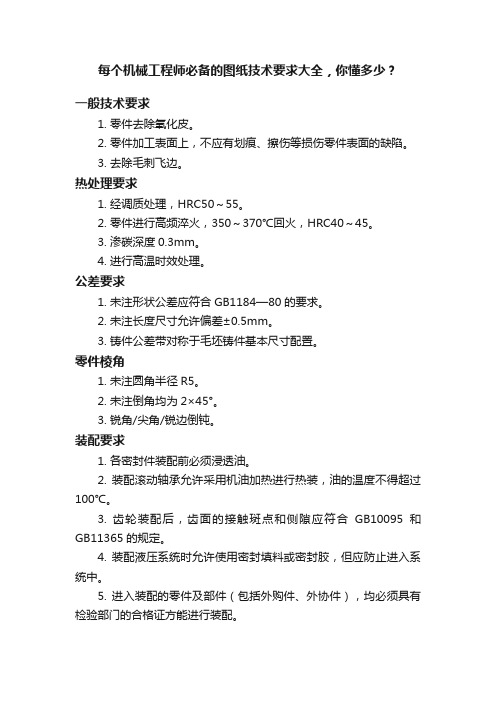
每个机械工程师必备的图纸技术要求大全,你懂多少?一般技术要求1. 零件去除氧化皮。
2. 零件加工表面上,不应有划痕、擦伤等损伤零件表面的缺陷。
3. 去除毛刺飞边。
热处理要求1. 经调质处理,HRC50~55。
2. 零件进行高频淬火,350~370℃回火,HRC40~45。
3. 渗碳深度0.3mm。
4. 进行高温时效处理。
公差要求1. 未注形状公差应符合GB1184—80的要求。
2. 未注长度尺寸允许偏差±0.5mm。
3. 铸件公差带对称于毛坯铸件基本尺寸配置。
零件棱角1. 未注圆角半径R5。
2. 未注倒角均为2×45°。
3. 锐角/尖角/锐边倒钝。
装配要求1. 各密封件装配前必须浸透油。
2. 装配滚动轴承允许采用机油加热进行热装,油的温度不得超过100℃。
3. 齿轮装配后,齿面的接触斑点和侧隙应符合GB10095和GB11365的规定。
4. 装配液压系统时允许使用密封填料或密封胶,但应防止进入系统中。
5. 进入装配的零件及部件(包括外购件、外协件),均必须具有检验部门的合格证方能进行装配。
6. 零件在装配前必须清理和清洗干净,不得有毛刺、飞边、氧化皮、锈蚀、切屑、油污、着色剂和灰尘等。
7. 装配前应对零部件的主要配合尺寸,特别是过盈配合尺寸及相关精度进行复查。
8. 装配过程中零件不允许磕、碰、划伤和锈蚀。
9. 螺钉、螺栓和螺母紧固时,严禁打击或使用不合适的旋具和扳手。
紧固后螺钉槽、螺母和螺钉、螺栓头部不得损坏。
10. 规定拧紧力矩要求的紧固件,必须采用力矩扳手,并按规定的拧紧力矩紧固。
11. 同一零件用多件螺钉(螺栓)紧固时,各螺钉(螺栓)需交叉、对称、逐步、均匀拧紧。
12. 圆锥销装配时应与孔应进行涂色检查,其接触率不应小于配合长度的60%,并应均匀分布。
13. 平键与轴上键槽两侧面应均匀接触,其配合面不得有间隙。
14. 花键装配同时接触的齿面数不少于2/3,接触率在键齿的长度和高度方向不得低于50%。
工程图常见技术要求

一般技术要求1。
零件去除氧化皮。
2。
零件加工表面上,不应有划痕、擦伤等损伤零件表面的缺陷.3. 去除毛刺飞边。
热处理要求1。
经调质处理,HRC50~55.2. 零件进行高频淬火,350~370℃回火,HRC40~45。
3。
渗碳深度0。
3mm。
4。
进行高温时效处理。
公差要求1.未注形状公差应符合GB1184—80的要求,有等级要求H K L,要求依次降低。
2.未注线性和角度尺寸公差应符合GB/T 1804—m(表示中等)f m c v ,要求依次降低。
2. 未注长度尺寸允许偏差±0。
5mm。
3. 铸件公差带对称于毛坯铸件基本尺寸配置。
如图示例,标在标题栏附近或技术要求中。
零件棱角1。
未注圆角半径R5。
2. 未注倒角均为2×45°。
3。
锐角/尖角/锐边倒钝。
装配要求1. 各密封件装配前必须浸透油.2. 装配滚动轴承允许采用机油加热进行热装,油的温度不得超过100℃。
3. 齿轮装配后,齿面的接触斑点和侧隙应符合GB10095和GB11365的规定。
4. 装配液压系统时允许使用密封填料或密封胶,但应防止进入系统中。
5。
进入装配的零件及部件(包括外购件、外协件),均必须具有检验部门的合格证方能进行装配。
6。
零件在装配前必须清理和清洗干净,不得有毛刺、飞边、氧化皮、锈蚀、切屑、油污、着色剂和灰尘等.7. 装配前应对零、部件的主要配合尺寸,特别是过盈配合尺寸及相关精度进行复查。
8。
装配过程中零件不允许磕、碰、划伤和锈蚀。
9。
螺钉、螺栓和螺母紧固时,严禁打击或使用不合适的旋具和扳手。
紧固后螺钉槽、螺母和螺钉、螺栓头部不得损坏。
10. 规定拧紧力矩要求的紧固件,必须采用力矩扳手,并按规定的拧紧力矩紧固。
11. 同一零件用多件螺钉(螺栓)紧固时,各螺钉(螺栓)需交叉、对称、逐步、均匀拧紧。
12。
圆锥销装配时应与孔应进行涂色检查,其接触率不应小于配合长度的60%,并应均匀分布。
13. 平键与轴上键槽两侧面应均匀接触,其配合面不得有间隙.14。
工程图常见技术要求

一般技术要求1. 零件去除氧化皮。
2. 零件加工表面上,不应有划痕、擦伤等损伤零件表面的缺陷。
3. 去除毛刺飞边。
热处理要求1. 经调质处理,HRC50~55。
2. 零件进行高频淬火,350~370℃回火,HRC40~45。
3. 渗碳深度。
4. 进行高温时效处理。
公差要求1.未注形状公差应符合GB1184-80的要求,有等级要求H K L,要求依次降低。
2.未注线性和角度尺寸公差应符合GB/T 1804-m(表示中等)f m c v ,要求依次降低。
2. 未注长度尺寸允许偏差±。
3. 铸件公差带对称于毛坯铸件基本尺寸配置。
如图示例,标在标题栏附近或技术要求中。
零件棱角1. 未注圆角半径R5。
2. 未注倒角均为2×45°。
3. 锐角/尖角/锐边倒钝。
装配要求1. 各密封件装配前必须浸透油。
2. 装配滚动轴承允许采用机油加热进行热装,油的温度不得超过100℃。
3. 齿轮装配后,齿面的接触斑点和侧隙应符合GB10095和GB11365的规定。
4. 装配液压系统时允许使用密封填料或密封胶,但应防止进入系统中。
5. 进入装配的零件及部件(包括外购件、外协件),均必须具有检验部门的合格证方能进行装配。
6. 零件在装配前必须清理和清洗干净,不得有毛刺、飞边、氧化皮、锈蚀、切屑、油污、着色剂和灰尘等。
7. 装配前应对零、部件的主要配合尺寸,特别是过盈配合尺寸及相关精度进行复查。
8. 装配过程中零件不允许磕、碰、划伤和锈蚀。
9. 螺钉、螺栓和螺母紧固时,严禁打击或使用不合适的旋具和扳手。
紧固后螺钉槽、螺母和螺钉、螺栓头部不得损坏。
10. 规定拧紧力矩要求的紧固件,必须采用力矩扳手,并按规定的拧紧力矩紧固。
11. 同一零件用多件螺钉(螺栓)紧固时,各螺钉(螺栓)需交叉、对称、逐步、均匀拧紧。
12. 圆锥销装配时应与孔应进行涂色检查,其接触率不应小于配合长度的60%,并应均匀分布。
13. 平键与轴上键槽两侧面应均匀接触,其配合面不得有间隙。
工程图常见技术要求

一般技术要求1。
零件去除氧化皮.2。
零件加工表面上,不应有划痕、擦伤等损伤零件表面的缺陷。
3。
去除毛刺飞边。
热处理要求1。
经调质处理,HRC50~55.2。
零件进行高频淬火,350~370℃回火,HRC40~45。
3。
渗碳深度0.3mm.4。
进行高温时效处理。
公差要求1.未注形状公差应符合GB1184-80的要求,有等级要求H K L,要求依次降低。
2.未注线性和角度尺寸公差应符合GB/T 1804—m(表示中等)f m c v ,要求依次降低。
2. 未注长度尺寸允许偏差±0。
5mm。
3。
铸件公差带对称于毛坯铸件基本尺寸配置。
如图示例,标在标题栏附近或技术要求中.零件棱角1. 未注圆角半径R5。
2. 未注倒角均为2×45°。
3。
锐角/尖角/锐边倒钝。
装配要求1。
各密封件装配前必须浸透油。
2. 装配滚动轴承允许采用机油加热进行热装,油的温度不得超过100℃.3. 齿轮装配后,齿面的接触斑点和侧隙应符合GB10095和GB11365的规定。
4. 装配液压系统时允许使用密封填料或密封胶,但应防止进入系统中。
5。
进入装配的零件及部件(包括外购件、外协件),均必须具有检验部门的合格证方能进行装配.6。
零件在装配前必须清理和清洗干净,不得有毛刺、飞边、氧化皮、锈蚀、切屑、油污、着色剂和灰尘等。
7。
装配前应对零、部件的主要配合尺寸,特别是过盈配合尺寸及相关精度进行复查。
8. 装配过程中零件不允许磕、碰、划伤和锈蚀。
9。
螺钉、螺栓和螺母紧固时,严禁打击或使用不合适的旋具和扳手.紧固后螺钉槽、螺母和螺钉、螺栓头部不得损坏。
10。
规定拧紧力矩要求的紧固件,必须采用力矩扳手,并按规定的拧紧力矩紧固。
11。
同一零件用多件螺钉(螺栓)紧固时,各螺钉(螺栓)需交叉、对称、逐步、均匀拧紧.12. 圆锥销装配时应与孔应进行涂色检查,其接触率不应小于配合长度的60%,并应均匀分布。
13。
平键与轴上键槽两侧面应均匀接触,其配合面不得有间隙。
工程图常见技术要求
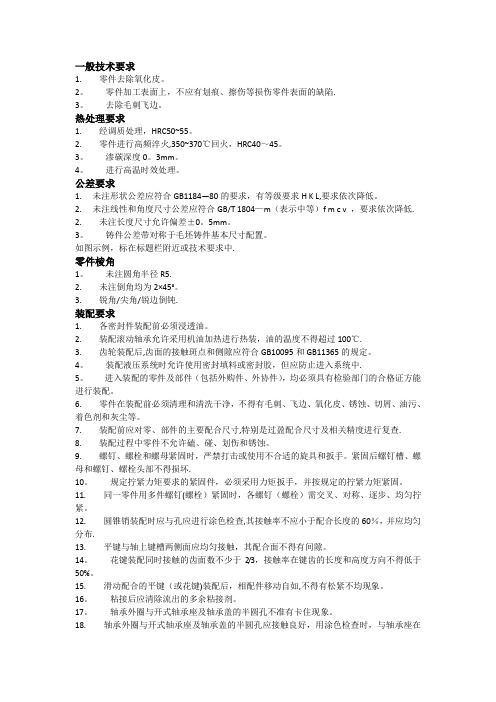
一般技术要求1. 零件去除氧化皮。
2。
零件加工表面上,不应有划痕、擦伤等损伤零件表面的缺陷.3。
去除毛刺飞边。
热处理要求1. 经调质处理,HRC50~55。
2. 零件进行高频淬火,350~370℃回火,HRC40~45。
3。
渗碳深度0。
3mm。
4。
进行高温时效处理。
公差要求1.未注形状公差应符合GB1184—80的要求,有等级要求H K L,要求依次降低。
2.未注线性和角度尺寸公差应符合GB/T 1804—m(表示中等)f m c v ,要求依次降低.2. 未注长度尺寸允许偏差±0。
5mm。
3。
铸件公差带对称于毛坯铸件基本尺寸配置。
如图示例,标在标题栏附近或技术要求中.零件棱角1。
未注圆角半径R5.2. 未注倒角均为2×45°。
3. 锐角/尖角/锐边倒钝.装配要求1. 各密封件装配前必须浸透油。
2. 装配滚动轴承允许采用机油加热进行热装,油的温度不得超过100℃.3. 齿轮装配后,齿面的接触斑点和侧隙应符合GB10095和GB11365的规定。
4。
装配液压系统时允许使用密封填料或密封胶,但应防止进入系统中.5。
进入装配的零件及部件(包括外购件、外协件),均必须具有检验部门的合格证方能进行装配。
6. 零件在装配前必须清理和清洗干净,不得有毛刺、飞边、氧化皮、锈蚀、切屑、油污、着色剂和灰尘等。
7. 装配前应对零、部件的主要配合尺寸,特别是过盈配合尺寸及相关精度进行复查.8. 装配过程中零件不允许磕、碰、划伤和锈蚀。
9. 螺钉、螺栓和螺母紧固时,严禁打击或使用不合适的旋具和扳手。
紧固后螺钉槽、螺母和螺钉、螺栓头部不得损坏.10。
规定拧紧力矩要求的紧固件,必须采用力矩扳手,并按规定的拧紧力矩紧固。
11. 同一零件用多件螺钉(螺栓)紧固时,各螺钉(螺栓)需交叉、对称、逐步、均匀拧紧。
12. 圆锥销装配时应与孔应进行涂色检查,其接触率不应小于配合长度的60%,并应均匀分布.13. 平键与轴上键槽两侧面应均匀接触,其配合面不得有间隙。
工程图常见技术要求

一般技术要求1. 零件去除氧化皮。
2. 零件加工表面上,不应有划痕、擦伤等损伤零件表面的缺陷。
3. 去除毛刺飞边。
热处理要求1. 经调质处理,HRC50~55。
2. 零件进行高频淬火,350~370℃回火,HRC40~45。
3. 渗碳深度0.3mm。
4. 进行高温时效处理。
公差要求1.未注形状公差应符合GB1184-80的要求,有等级要求H K L,要求依次降低。
2.未注线性和角度尺寸公差应符合GB/T 1804-m(表示中等)f m c v ,要求依次降低。
2. 未注长度尺寸允许偏差±0.5mm。
3. 铸件公差带对称于毛坯铸件基本尺寸配置。
如图示例,标在标题栏附近或技术要求中。
零件棱角1. 未注圆角半径R5。
2. 未注倒角均为2×45°。
3. 锐角/尖角/锐边倒钝。
装配要求1. 各密封件装配前必须浸透油。
2. 装配滚动轴承允许采用机油加热进行热装,油的温度不得超过100℃。
3. 齿轮装配后,齿面的接触斑点和侧隙应符合GB10095和GB11365的规定。
4. 装配液压系统时允许使用密封填料或密封胶,但应防止进入系统中。
5. 进入装配的零件及部件(包括外购件、外协件),均必须具有检验部门的合格证方能进行装配。
6. 零件在装配前必须清理和清洗干净,不得有毛刺、飞边、氧化皮、锈蚀、切屑、油污、着色剂和灰尘等。
7. 装配前应对零、部件的主要配合尺寸,特别是过盈配合尺寸及相关精度进行复查。
8. 装配过程中零件不允许磕、碰、划伤和锈蚀。
9. 螺钉、螺栓和螺母紧固时,严禁打击或使用不合适的旋具和扳手。
紧固后螺钉槽、螺母和螺钉、螺栓头部不得损坏。
10. 规定拧紧力矩要求的紧固件,必须采用力矩扳手,并按规定的拧紧力矩紧固。
11. 同一零件用多件螺钉(螺栓)紧固时,各螺钉(螺栓)需交叉、对称、逐步、均匀拧紧。
12. 圆锥销装配时应与孔应进行涂色检查,其接触率不应小于配合长度的60%,并应均匀分布。
图纸及工艺技术要求大全
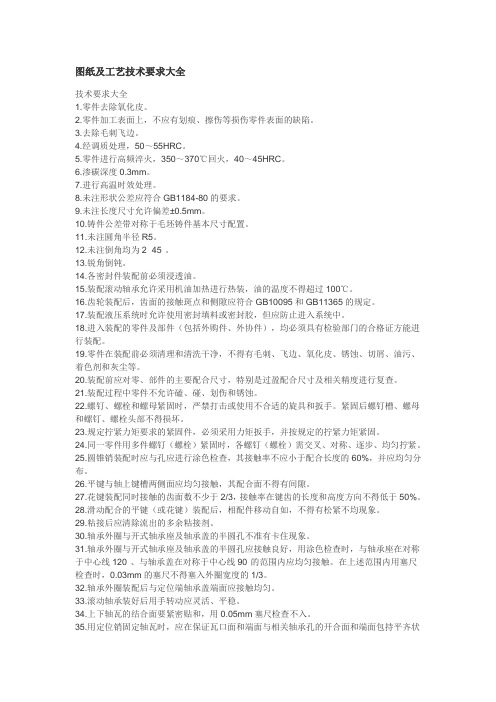
图纸及工艺技术要求大全技术要求大全1.零件去除氧化皮。
2.零件加工表面上,不应有划痕、擦伤等损伤零件表面的缺陷。
3.去除毛刺飞边。
4.经调质处理,50~55HRC。
5.零件进行高频淬火,350~370℃回火,40~45HRC。
6.渗碳深度0.3mm。
7.进行高温时效处理。
8.未注形状公差应符合GB1184-80的要求。
9.未注长度尺寸允许偏差±0.5mm。
10.铸件公差带对称于毛坯铸件基本尺寸配置。
11.未注圆角半径R5。
12.未注倒角均为2×45°。
13.锐角倒钝。
14.各密封件装配前必须浸透油。
15.装配滚动轴承允许采用机油加热进行热装,油的温度不得超过100℃。
16.齿轮装配后,齿面的接触斑点和侧隙应符合GB10095和GB11365的规定。
17.装配液压系统时允许使用密封填料或密封胶,但应防止进入系统中。
18.进入装配的零件及部件(包括外购件、外协件),均必须具有检验部门的合格证方能进行装配。
19.零件在装配前必须清理和清洗干净,不得有毛刺、飞边、氧化皮、锈蚀、切屑、油污、着色剂和灰尘等。
20.装配前应对零、部件的主要配合尺寸,特别是过盈配合尺寸及相关精度进行复查。
21.装配过程中零件不允许磕、碰、划伤和锈蚀。
22.螺钉、螺栓和螺母紧固时,严禁打击或使用不合适的旋具和扳手。
紧固后螺钉槽、螺母和螺钉、螺栓头部不得损坏。
23.规定拧紧力矩要求的紧固件,必须采用力矩扳手,并按规定的拧紧力矩紧固。
24.同一零件用多件螺钉(螺栓)紧固时,各螺钉(螺栓)需交叉、对称、逐步、均匀拧紧。
25.圆锥销装配时应与孔应进行涂色检查,其接触率不应小于配合长度的60%,并应均匀分布。
26.平键与轴上键槽两侧面应均匀接触,其配合面不得有间隙。
27.花键装配同时接触的齿面数不少于2/3,接触率在键齿的长度和高度方向不得低于50%。
28.滑动配合的平键(或花键)装配后,相配件移动自如,不得有松紧不均现象。
工程图常见技术要求

1. 零件去除氧化皮。
2. 零件加工表面上,不应有划痕、擦伤等损伤零件表面的缺陷。
3. 去除毛刺飞边。
热处理要求1. 经调质处理,HRC50~55。
2. 零件进行高频淬火,350~370℃回火,HRC40~45。
3. 渗碳深度。
4. 进行高温时效处理。
公差要求1.未注形状公差应符合GB1184-80的要求,有等级要求H K L,要求依次降低。
2.未注线性和角度尺寸公差应符合GB/T 1804-m(表示中等)f m c v ,要求依次降低。
2. 未注长度尺寸允许偏差±。
3. 铸件公差带对称于毛坯铸件基本尺寸配置。
如图示例,标在标题栏附近或技术要求中。
零件棱角1. 未注圆角半径R5。
2. 未注倒角均为2×45°。
3. 锐角/尖角/锐边倒钝。
装配要求1. 各密封件装配前必须浸透油。
2. 装配滚动轴承允许采用机油加热进行热装,油的温度不得超过100℃。
3. 齿轮装配后,齿面的接触斑点和侧隙应符合GB10095和GB11365的规定。
4. 装配液压系统时允许使用密封填料或密封胶,但应防止进入系统中。
5. 进入装配的零件及部件(包括外购件、外协件),均必须具有检验部门的合格证方能进行装配。
6. 零件在装配前必须清理和清洗干净,不得有毛刺、飞边、氧化皮、锈蚀、切屑、油污、着色剂和灰尘等。
7. 装配前应对零、部件的主要配合尺寸,特别是过盈配合尺寸及相关精度进行复查。
8. 装配过程中零件不允许磕、碰、划伤和锈蚀。
9. 螺钉、螺栓和螺母紧固时,严禁打击或使用不合适的旋具和扳手。
紧固后螺钉槽、螺母和螺钉、螺栓头部不得损坏。
10. 规定拧紧力矩要求的紧固件,必须采用力矩扳手,并按规定的拧紧力矩紧固。
11. 同一零件用多件螺钉(螺栓)紧固时,各螺钉(螺栓)需交叉、对称、逐步、均匀拧紧。
12. 圆锥销装配时应与孔应进行涂色检查,其接触率不应小于配合长度的60%,并应均匀分布。
13. 平键与轴上键槽两侧面应均匀接触,其配合面不得有间隙。
工程图常见技术要求(工程部)

一般技术要求. 零件去除氧化皮。
. 零件加工表面上,不应有划痕、擦伤等损伤零件表面的缺陷。
. 去除毛刺飞边。
热处理要求. 经调质处理,~。
. 零件进行高频淬火,~℃回火,~。
. 渗碳深度。
. 进行高温时效处理。
公差要求1.未注形状公差应符合的要求,有等级要求,要求依次降低。
2.未注线性和角度尺寸公差应符合(表示中等),要求依次降低。
. 未注长度尺寸允许偏差±。
. 铸件公差带对称于毛坯铸件基本尺寸配置。
零件棱角. 未注圆角半径。
. 未注倒角均为×°。
. 锐角尖角锐边倒钝。
装配要求. 各密封件装配前必须浸透油。
. 装配滚动轴承允许采用机油加热进行热装,油的温度不得超过℃。
. 齿轮装配后,齿面的接触斑点和侧隙应符合和的规定。
. 装配液压系统时允许使用密封填料或密封胶,但应防止进入系统中。
. 进入装配的零件及部件(包括外购件、外协件),均必须具有检验部门的合格证方能进行装配。
. 零件在装配前必须清理和清洗干净,不得有毛刺、飞边、氧化皮、锈蚀、切屑、油污、着色剂和灰尘等。
. 装配前应对零、部件的主要配合尺寸,特别是过盈配合尺寸及相关精度进行复查。
. 装配过程中零件不允许磕、碰、划伤和锈蚀。
. 螺钉、螺栓和螺母紧固时,严禁打击或使用不合适的旋具和扳手。
紧固后螺钉槽、螺母和螺钉、螺栓头部不得损坏。
. 规定拧紧力矩要求的紧固件,必须采用力矩扳手,并按规定的拧紧力矩紧固。
. 同一零件用多件螺钉(螺栓)紧固时,各螺钉(螺栓)需交叉、对称、逐步、均匀拧紧。
. 圆锥销装配时应与孔应进行涂色检查,其接触率不应小于配合长度的,并应均匀分布。
. 平键与轴上键槽两侧面应均匀接触,其配合面不得有间隙。
. 花键装配同时接触的齿面数不少于,接触率在键齿的长度和高度方向不得低于。
. 滑动配合的平键(或花键)装配后,相配件移动自如,不得有松紧不均现象。
. 粘接后应清除流出的多余粘接剂。
. 轴承外圈与开式轴承座及轴承盖的半圆孔不准有卡住现象。
- 1、下载文档前请自行甄别文档内容的完整性,平台不提供额外的编辑、内容补充、找答案等附加服务。
- 2、"仅部分预览"的文档,不可在线预览部分如存在完整性等问题,可反馈申请退款(可完整预览的文档不适用该条件!)。
- 3、如文档侵犯您的权益,请联系客服反馈,我们会尽快为您处理(人工客服工作时间:9:00-18:30)。
各类工程图技术要求一、一般技术要求制件去除表面氧化皮;制件不得有划痕、擦伤等损伤零件表面的缺陷;去除毛刺飞边;锐角倒钝;未注倒角均为0.5×45%%d;未注越程槽均为1.2×0.3;表面平整无毛刺;二、未注公差技术要求(金属件)未注公差尺寸的极限偏差按GB/T 1804-m;未注形位公差按GB/T 1184-K;未注长度尺寸允许偏差±0.5;三、表面处理技术要求表面镀白(黑)锌处理;表面喷漆(喷塑)处理;表面发黑处理;表面电泳处理;表面镀铬处理;表面抛光处理;表面滚花,直纹(网纹)m=0.4 GB/T 6403.3;四、热处理技术要求制件氮化450-480HV;制件毛坯须调质处理220-260HB;制件调质处理30-35HRC;制件高频淬火45~50HRC;制件渗碳处理,深度>0.1;制件进行高温回火处理;制件整体淬火40-45HRC;五、铸件技术要求1、压铸件技术要求未注公差尺寸的极限偏差按GB/T 1804-m;未注形位公差按GB/T 1184-K;未注倒角均为0.5×45%%d;未注壁厚2.5;未注筋板1.5~2;未注过渡圆角R0.5-R2;未注脱模斜度≤1%%d;制件饱满光洁、无气孔、缩松、裂纹、夹渣、缺料等缺陷;各脱模顶料推杆压痕均应低于该制件表面0.2;制件要求符合GB/T 15114《铝合金压铸件》标准规定;表面喷漆(喷塑)处理,不得污染到已加工表面;加工表面在表面处理后加工,加工后涂油保护;未注尺寸参照三维造型;制件表面处理及其它要求按客户定;2、砂型铸造技术要求未注铸造圆角R5-10;铸件应彻底清砂,浇冒口应清除平整;铸件需人工时效;铸件不得有砂眼、气孔、缩松、裂纹等缺陷;粗加工后应再次进行人工时效;不加工表面涂底漆;六、冲压件技术要求制件未注公差尺寸的极限偏差按GB/T 15055-m;制件未注形位公差按GB/T 13916-2级;制件不得有裂纹或缺损;制件表面平整,不得有沟痕、碰伤等损坏表面,降低强度及寿命的缺陷;去除边角毛刺;表面处理:七、塑料件技术要求未注公差尺寸的极限偏差按GB/T 14486-MT6级;制件应饱满光整、色泽均匀;无缩痕、裂纹、银丝等缺陷;浇口、溢边修剪后飞边≤0.3,且不得伤及本体;未注壁厚3;未注筋板1.5~2;表面打光(喷砂)处理;未注过渡圆角取R0.3~R1,脱模斜度≤0.3%%d;各脱模顶料推杆压痕均应低于该制件表面0.2;与对应装配结合面外形配合错位≤0.5;制件应进行时效处理;制件机械强度须符合GB 3883.1标准规定;制件腔表面打上材料标记和回收标志;未注尺寸参照三维造型;制件表面处理及其它要求由客户定;八、焊接件技术要求未注公差线性及角度尺寸的极限偏差均按GB/T 19804-B级;未注形位公差按GB/T 19804-F级;焊缝应均匀平整,焊渣清理干净;焊缝应焊透,不得烧穿及产生裂纹等影响机械性能的缺陷;九、各类零、部件技术要求1、齿轮(齿轴)技术要求未注公差尺寸的极限偏差按GB/T 1804-m;未注形位公差按GB/T 1184-K;制件毛坯须调质220~260HB;制件材料的化学成分和力学性能应符合GB/T 3077的规定;齿面接触斑点:按齿高不小于40%,按齿长不小于50%;齿面高频淬火回火至49-52HRC;制件表面不应有锈迹、裂纹、灼伤等影响使用寿命的伤痕及缺陷;最终工序热处理表面不得有氧化皮;2、一般轴芯(无铣齿)技术要求未注公差尺寸的极限偏差按GB/T 1804-m;未注形位公差按GB/T 1184-K;未注倒角均为0.5×45%%d;未注越程槽均为1.2×0.3;制件毛坯须调质220~260HB;尺寸%%c 档车正反两条螺旋槽,螺距10,深0.4;螺纹表面不允许有磕碰、乱扣、毛刺等缺陷;热处理:表面处理:3、包轴毛坯(一次成型)技术要求未注公差尺寸的极限偏差按GB/T 1804-m;未注形位公差按GB/T 1184-K;绝缘层应饱满光洁,无裂纹、气孔、缺料、杂质等缺陷;包轴毛坯:绝缘层%%c 档(注:指冲片配合档)与轴芯间应能承受50Hz,实际正弦波电压2500V历时1min不击穿,其余绝缘层档3750V历时1min不击穿;一次成型:铁芯与轴芯间应能承受50Hz,实际正弦波电压2500V历时1min不击穿,其余绝缘层档3750V历时1min不击穿;4、包轴(加工)技术要求未注公差尺寸的极限偏差按GB/T 1804-m;未注形位公差按GB/T 1184-K;塑层应饱满光洁,无裂纹、气孔、缺料、杂质等缺陷;塑层%%c 档(注:指冲片配合档)与轴芯间应能承受50Hz,实际正弦波电压2500V 历时1min不击穿,其余塑层档3750V历时1min不击穿;制件磨加工后应烘干除水处理;5、转子技术要求未注公差尺寸的极限偏差按GB/T 1804-m;未注形位公差按GB/T 1184-K;绕组接线按转子绕线原理图;绕组绝缘漆应均匀充满绕组并充分固化,漆膜应均匀无气泡或裂痕;云母槽开深0.8~1,槽宽0.6,槽不得残留云母片;绕组冷态绝缘电阻不低于50MΩ;装风叶后校动平衡,其精度应不低于G6.3级;去重不允许有冲片铣穿、残缺现象;铁芯外圆不加工,绝缘漆不得高出铁芯外圆,并不得有明显积瘤;铁芯与轴芯间应能承受50Hz,实际正弦波电压2500V,1min不击穿;绕组与铁芯间应能承受50Hz,实际正弦波电压1250V,1min不击穿;匝间绝缘应能承受1000Hz,峰值为2100V,历时3s不击穿;换向器与轴芯间应能承受50Hz,实际正弦波电压3750V,1min不击穿;应去除铁屑、铜粉、油污等杂质;铁芯外圆应涂透明淡金水防锈处理;6、定子技术要求绕组绕制整齐无松散;引线接头应牢固可靠且充分绝缘;绕组与铁芯间应能承受50Hz,实际正弦波电压1250V历时1min不击穿;匝间绝缘应能承受1000Hz,峰值为2100V,历时3s不击穿;绕组绝缘漆应均匀充满绕组并充分固化,漆膜应均匀无气泡或积瘤;铁芯表面不得有明显绝缘漆;7、定、转子铁芯技术要求未注公差尺寸的极限偏差按GB/T 1804-m;未注形位公差按GB/T 1184-K;冲片叠装应紧密可靠,片间无夹杂,表面及槽无污物和油渍;冲片按同一冲制方向压装;冲片齿槽口整齐与转轴平行,误差不大于0.5;铁芯两端弹开度不大于0.5;8、定、转子冲片技术要求制件未注公差尺寸的极限偏差按GB/T 15055-m;制件未注形位公差按GB/T 13916-2级;制件应表面平整,完整无缺料;尖角处允许用R0.3过渡;制件毛刺不大于0.05(注:高速冲时不大于0.02);制件应不含油脂,剪切油不能用机油;9、绝缘纸技术要求表面不得有划痕、折痕;裁边不起毛;10、换向器技术要求未注公差尺寸的极限偏差按GB/T 1804-m;未注形位公差按GB/T 1184-K;外观完整,表面光滑,应无裂纹、毛刺、锈蚀、气孔、夹杂等缺陷;绝缘电阻:室温下孔与换向片之间大于50MΩ;云母片厚度取0.5;换向片对换向器轴线偏斜度不大于云母片厚度的1/3;介电强度:片间承受频率50Hz,泄露电流为0.1mA,实际正弦波电压600V历时1s不击穿;换向片与孔轴芯间承受频率50Hz,泄露电流为0.25mA,实际正弦波电压3750V历时1min不击穿;试验与检验应符合JB/T 10107《电动工具换向器》标准要求;11、电缆线技术要求电缆线长度尺寸指工具电缆出口至插头的导线部分,不包括插头和插脚;软电缆应符合GB/T 5013《额定电压450V/750V及以下橡皮绝缘电缆》标准要求;聚氯乙烯电缆应符合GB/T 5023《额定电压450V/750V及以下聚氯乙烯绝缘电缆》标准要求;插脚与可触及插头表面的绝缘应能承受50Hz,实际正弦波电压3750V历时1min 不击穿;制件还应符合GB 1002《家用和类似用途单相插头插座型式、基本参数和尺寸》和GB 2099《家用和类似用途插头插座》标准要求;12、开关技术要求未注公差尺寸的极限偏差按SJ/T 10628-7级;除本图要求的外形尺寸、功能、图形、文字外,试验和检验均应符合GB/T 22692《电动工具开关》标准要求;开关的使用性能应保证5万次无故障正常使用;13、电缆护套技术要求未注公差尺寸的极限偏差按GB/T 3672.1-2级;未注形位公差按GB/T 3672.2-M级;制件不得有缺料、破裂等缺陷。
制件应厚度均匀,色泽纯正,外表光洁无污渍、飞边;制件应按JB/T 9605《电动工具电源线护套》进行抗弯试验2万次后不得有裂纹或撕裂等缺陷;制件应能承受50Hz;实际正弦波电压2500V历时1min不击穿;14、碳刷技术要求未注公差尺寸的极限偏差按GB/T 1804-m;未注形位公差按GB/T 1184-K;刷体四边应倒角0.5×45%%d;刷辫与碳刷铜片焊接可靠,刷辫受力均匀,脱线率小于1%,若用锡焊则焊点应不高于铜片表面,且不得用腐蚀性焊剂;刷辫与碳刷体应用铜粉针压深埋固定,埋入深度应≥3;无冲击状态脱出力应≥50N;刷辫应用TSR型软铜绞线;15、电容技术要求未注公差尺寸的极限偏差按SJ/T 10628-7级;外观应无可见损伤,标记清晰;标称电容量最大允许偏差为±20%;试验和检验均应符合GB/T 14472《电子设备用固定电容器第14部分抑制电源电磁干扰用固定电容器》标准要求;16、电感技术要求制件应无可见损伤;标称电感量最大允许偏差为±25%;试验和检验均应符合GB/T 16513《抑制射频干扰固定电感器第2部分试验方法和一般要求的选择》标准要求;17、自锁销轴技术要求未注公差尺寸的极限偏差按GB/T 1804-m;未注形位公差按GB/T 1184-K;未注倒角均为0.5×45%%d;热处理:30-35HRC;表面发黑处理;18、输出轴技术要求未注公差尺寸的极限偏差按GB/T 1804-m;未注形位公差按GB/T 1184-K;未注倒角均为0.5×45%%d;未注越程槽均为1.2×0.3;制件毛坯须调质220~260HB;制件表面不允许有锐边、锈迹、污垢等缺陷;热处理:磨加工前表面发黑处理;19、弹簧技术要求总圈数=有效圈数=展开长度=旋向:热处理:表面处理:制件定型处理;20、含油轴承技术要求制件密度:制件含油率:制件要求无裂纹、缺损等缺陷;制件硬度要求:制件真空渗油(46号机油或防锈油),时间不得少于6分钟21、砂轮罩技术要求制件未注公差尺寸的极限偏差按GB/T 15055-m;制件未注形位公差按GB/T 13916-2级;罩体和罩盖及罩环采用点焊连接,焊点直径%%C5,至少均布5个焊点;22、刨刀组件(含刀轴)技术要求未注公差尺寸的极限偏差按GB/T 1804-m;未注形位公差按GB/T 1184-K;未注倒角均为0.5×45%%d;未注越程槽为1.2×0.3;制作刨刀组件时,配件:刨刀片、垫圈、螺钉和刨刀压板须用托盘天平秤重,两边偏差不得大于0.3克;刨刀部件组装须对刀片进行基本调试;组件须校动平衡,其精度应不低于G6.3级,去重部位为刀轴体的铝体端部,不能破坏周边,并须去净铝末;23、金刚石锯片(烧结)技术要求未注公差尺寸的极限偏差按GB/T 1804-m;锯片基体材料应采用65Mn或不低于65Mn的钢材;锯片基体不得有裂纹、毛刺及锈迹,并允许有工艺孔;锯片基体硬度为37-42HRC;锯齿表面不得有裂纹、哑声及2个以上长、宽大于1的崩刃;锯齿工作面的磨料颗粒应均匀出露,并均匀分布锯片试验和检验应符合GB/T 11270.2《超硬磨料制品金刚石圆锯片第2部分烧结锯片》标准要求;24、硬质合金锯片(焊接)技术要求锯片基体材料应采用65Mn或不低于65Mn的钢材;锯片基体不得有裂纹、毛刺及锈迹,并允许有工艺孔;锯片基体硬度为37-45HRC;锯齿表面不得有裂纹及2个以上长、宽大于1的崩刃;焊缝应饱满,不得有裂纹和孔洞,焊料堆积不得高于锯齿的端面;锯齿焊在基体上的端面对称度不大于0.25;锯片试验和检验应符合GB/T 11270.1《超硬磨料制品金刚石圆锯片第1部分焊接锯片》标准要求;25、砂轮片(角磨用钹形)技术要求砂轮片不应有裂纹;砂轮片表面允许有规则性印痕,外观色泽应均匀;砂轮片试验和检验应符合JB/T 3715《固结磨具修磨用钹形砂轮》标准要求;26、砂轮片(切割机用薄片形)技术要求砂轮片不应有裂纹;砂轮片表面允许有规则性印痕,外观色泽应均匀;砂轮片试验和检验应符合JB/T 6353《固结磨具树脂和橡胶薄片砂轮》标准要求;27、标贴(铭牌、商标)技术要求图线及字体线条应清晰端正;双重绝缘标记应符合GB 3883.1标准要求;字体高度及行距按图纸尺寸规定,字体排列应均匀对称;表面应光洁,不允许有褶皱、卷曲、起皮、脱胶等现象;用酒精擦拭表面至少10次,不得抹去字体或图线;28、包装箱(外箱、彩盒)技术要求瓦楞纸板不应有缺料和薄边,切边应整齐,表面应清洁、平整;在1m的单瓦楞纸板上不应有大于20mm的翘曲;瓦楞纸板交货水分应不大于14%;瓦楞纸板采用淀粉粘合剂或其它同等效果的粘合剂,粘合层的强度应不低于400N/m;钉合瓦楞纸箱应采用宽度1.5mm以上经防锈处理的金属钉线,钉线不应有锈斑、剥层、龟裂等缺陷;单瓦楞纸箱的尺寸公差允许±3mm,双瓦楞纸箱的尺寸公差允许±5mm;瓦楞纸箱摇盖经开合180%%d往复5次,表层和里层均不得有裂缝;十、总装图技术要求技术参数:Hz,V,W,r/min;各装配结合面外形错位≤0.5;外表面不得有磕碰、划伤等损坏现象;齿轮室加入约占空腔2/3容积的2号锂基润滑脂;开关启动灵活无阻滞,通断可靠;机器运转时应性能稳定,火花及振动正常,无异常杂音;整机在校验台上空载运行15min后,测试电缆插头和输出轴之间应能承受50Hz,实际正弦波3750V历时1min的耐压试验不击穿;产品应符合GB 3883.1(可移式:GB13960.1)标准要求;包装应符合JB/T 7587《电动工具产品包装技术条件》标准要求;产品应按出厂检验规规定程序进行出厂检验,全部项目合格才可包装出厂;作为“技术要求”是产品设计者对该产品(零、部件)满足设计要求所提出的支持加工、检验、装配、使用等方面的必要条件,必须制定合理并符合相关标准、法规的要求。