复合材料风电叶片的检查保护及维修
风力发电机叶片维修

风力发电机叶片维修
风力发电机叶片维修主要包括以下几个方面:
1. 受损叶片更换:如果叶片受到损坏,需要及时更换。
维修人员会检查叶片的损坏程度,如果只有局部损坏,可以进行修复;如果损坏过于严重,需要更换整个叶片。
2. 叶片表面清洁:风力发电机叶片在运行过程中会积累灰尘、油脂和其它污垢,影响风能的转换效率。
维修人员会使用清洁工具和清洁剂对叶片表面进行清洁,保持其表面光滑。
3. 叶片平衡校正:风力发电机叶片在长期运行过程中可能会出现平衡问题,导致震动和噪音增加。
维修人员会使用专业工具对叶片进行平衡校正,减少其振动和噪音。
4. 叶片涂层维护:叶片表面通常涂有特殊的防风化涂层,用于保护叶片免受风蚀和紫外线辐射的损害。
维修人员会定期检查叶片涂层的状况,如有需要会进行修复或重新涂层。
5. 叶片结构检查:维修人员会对叶片的结构进行检查,确保其没有裂缝、变形或其它潜在问题。
如果发现问题,会及时修复或更换叶片。
总之,风力发电机叶片维修需要由专业的维修人员进行,他们会根据实际情况选择合适的维修方法和工具,确保叶片的正常运行。
风力发电叶片缺陷检测与修复技术研究

风力发电叶片缺陷检测与修复技术研究随着全球对可再生能源的需求不断增长,风力发电已经成为一种受到广泛关注并且得到快速发展的清洁能源形式。
风力发电机的核心部件之一就是叶片,而叶片的缺陷会严重影响发电效率和设备的整体运行性能。
因此,风力发电叶片缺陷检测与修复技术对于提高叶片的质量和延长使用寿命至关重要。
风力发电叶片主要面临以下几种类型的缺陷:磨损、损伤、龟裂和腐蚀。
这些缺陷可能由于设计不当、材料质量问题、自然灾害或长期使用等原因导致。
因此,科学研究人员和工程师们积极探索各种叶片缺陷检测与修复技术,以降低风力发电的成本并提高可靠性。
在叶片缺陷检测方面,目前已经出现了多种方法和技术。
其中,无损检测技术是最为常见的一种。
其基本原理是通过利用声波、电磁波或热辐射等物理信号对叶片进行扫描和分析,以检测叶片表面和内部的缺陷。
例如,超声波检测技术可以通过测量声波在材料中的传播速度和反射情况来检测叶片的内部缺陷。
红外热成像技术则可以通过检测叶片表面的温度分布来发现潜在的龟裂和损伤。
此外,还有X射线检测、磁粉检测和激光扫描等方法都可以用于叶片缺陷的检测。
除了无损检测技术,还有一些新兴的技术也被应用于风力发电叶片缺陷检测中。
例如,机器视觉技术可以利用摄像头和图像处理算法来分析叶片的表面图像,从而检测出表面的缺陷和磨损情况。
这种技术具有高效、快速、非接触等优点,可以提高缺陷检测的准确性和效率。
在叶片缺陷修复方面,目前也有多种修复技术被广泛使用。
对于小型的表面磨损和损伤,常见的修复技术包括抛光、涂层和粘接等。
通过抛光可以去除叶片表面的磨损层,从而恢复其光滑性和表面质量。
涂层技术可以通过在叶片表面施加一层保护性涂层来减轻磨损和腐蚀的影响。
粘接技术则可以用于连接和修补叶片上的小型损伤,例如龟裂和划痕。
对于较大和严重的叶片缺陷,更高级的修复技术则会被应用。
例如,纤维增强复合材料的修复技术可以通过将额外的纤维增强层添加到损伤区域来增加叶片的强度和刚度。
风电机组叶片维护装备的维护保养与更新策略
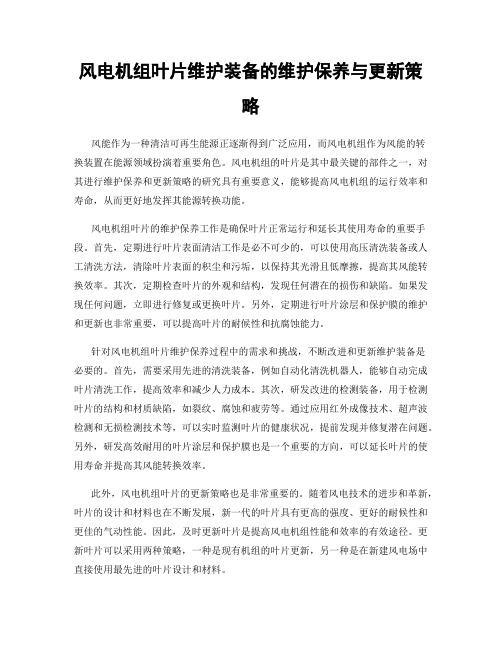
风电机组叶片维护装备的维护保养与更新策略风能作为一种清洁可再生能源正逐渐得到广泛应用,而风电机组作为风能的转换装置在能源领域扮演着重要角色。
风电机组的叶片是其中最关键的部件之一,对其进行维护保养和更新策略的研究具有重要意义,能够提高风电机组的运行效率和寿命,从而更好地发挥其能源转换功能。
风电机组叶片的维护保养工作是确保叶片正常运行和延长其使用寿命的重要手段。
首先,定期进行叶片表面清洁工作是必不可少的,可以使用高压清洗装备或人工清洗方法,清除叶片表面的积尘和污垢,以保持其光滑且低摩擦,提高其风能转换效率。
其次,定期检查叶片的外观和结构,发现任何潜在的损伤和缺陷。
如果发现任何问题,立即进行修复或更换叶片。
另外,定期进行叶片涂层和保护膜的维护和更新也非常重要,可以提高叶片的耐候性和抗腐蚀能力。
针对风电机组叶片维护保养过程中的需求和挑战,不断改进和更新维护装备是必要的。
首先,需要采用先进的清洗装备,例如自动化清洗机器人,能够自动完成叶片清洗工作,提高效率和减少人力成本。
其次,研发改进的检测装备,用于检测叶片的结构和材质缺陷,如裂纹、腐蚀和疲劳等。
通过应用红外成像技术、超声波检测和无损检测技术等,可以实时监测叶片的健康状况,提前发现并修复潜在问题。
另外,研发高效耐用的叶片涂层和保护膜也是一个重要的方向,可以延长叶片的使用寿命并提高其风能转换效率。
此外,风电机组叶片的更新策略也是非常重要的。
随着风电技术的进步和革新,叶片的设计和材料也在不断发展,新一代的叶片具有更高的强度、更好的耐候性和更佳的气动性能。
因此,及时更新叶片是提高风电机组性能和效率的有效途径。
更新叶片可以采用两种策略,一种是现有机组的叶片更新,另一种是在新建风电场中直接使用最先进的叶片设计和材料。
对于现有机组的叶片更新,根据具体条件和经济效益进行评估,选择最合适的替换方案。
考虑到更新叶片可能会影响机组的整体性能和效率,需要进行全面的技术评估和经济分析。
风电叶片的保养与维修技术方案

4,叶根雷击损伤 缺陷描述:1,顺风面叶根轴套雷击损伤,叶片壳体击穿、分层。2,迎风 面叶根尾缘轴套雷击损伤, 叶片壳体击穿、分层
叶片维修从业要求 叶片缺陷产生的原因 叶片维修质量保证
叶片的维修
从事叶片服务的要求
• 门槛低
营业执照,高空作业证
• 专业性强
人员技能,工作经历
• 人为因素大 公司经营理念,人员责任♥
• 安全责任重
安全管理,设备检验
叶片的维修
叶片维修的专业性
叶片的维修
维修
维修案例
1,主梁断裂的维修
a 缺陷描述:叶片SS面距叶根约17m处壳体主梁断裂,并向 尾边横向开裂变形,叶片内部主支架开裂,沿主梁边缘纵向裂纹长7m。
2,尾缘开裂的维修
a,缺陷描述:叶片尾边开裂10m,逆风面玻纤开裂和泡 沫分层7.5m,顺风面泡沫分层9米
3,叶片横向裂纹的维修 a,缺陷描述:叶片横向裂纹。叶片外部距叶跟约9-9.6m,从合模线至前缘 主梁边缘,长度约为1.14m。叶片内部纵向距叶跟9-9.6m,从合模线至主梁边缘 斜向断续开裂,长度为1.0m;
叶片外部+内部检查方法
外部检查方法 平台近距
望远镜/高倍相机远距 高倍相机+平台 无人机近距
质量 较好 一般 一般 较好
叶片质量检查
周期 长 短 短
一般
人工时 台数 16 2台/4人 4 6-8台/4人 6 4-6台/4人 √ 4 3-4台/2人
叶片检查结果输出
• 检查人员不专业
• 检查过程不规范
叶片维修质量保证
专业的人员 专业的设备 专业的材料 专业的工艺 专业的过程控制
叶片的维修
具有专业的技能水平 高效率工作的保证 稳定质量的保证 维修强度的保证 有效的质量监督
复合材料风电叶片的修复技术
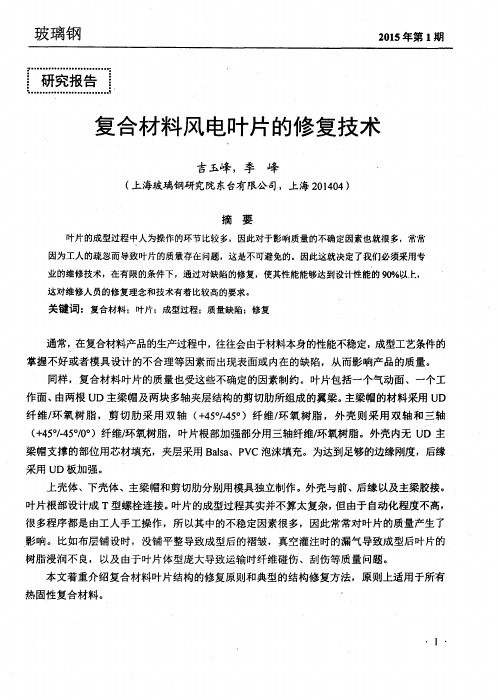
纤维/ 环氧树脂 ,剪 切肋采用双轴 ( + 4 5 o / - 4 5  ̄ )纤维/ 环氧树脂 ,外 壳则采用双轴和三轴
( + 4 5 。 / - 4 5  ̄ / 0 。 )纤维/ 环氧树 脂 ,叶片 根部加 强部分用 三轴 纤维/ 环氧 树脂 。外壳 内无 U D 主 梁帽 支撑 的部位 用芯材填 充,夹层采 用 B a l s a 、P V C泡沫填充 。为达到足够 的边缘刚度 ,后缘 采用 U D板加 强。 上 壳体 、下壳体 、主梁 帽和剪 切肋 分别用 模具独 立制作 。外壳 与前 、后 缘 以及 主梁胶接 。 叶片根 部设计 成 T型螺 栓连接 。 叶 片的成 型过程其 实并不 算太 复杂 , 但 由于 自动化 程度不 高,
2
关键词 :复合材料;叶片;成型过程;质量缺陷;修复
通常 , 在 复合材 料产品的生产过程中,往往会 由于材料本 身的性能不稳 定,成型工艺 条件 的 掌握 不好 或者 模具 设计 的不合 理等 因素而 出现表 面或 内在的缺陷 ,从而 影响产 品 的质量 。 同样 ,复 合材料 叶片 的质 量也受这 些不 确定 的因素制 约 。叶 片包括 一个气 动面 、一个 工 作面 、由两根 UD主 梁帽 及两块 多轴夹 层 结构 的剪 切肋所 组成 的翼 梁 。 主 梁帽 的材料采 用 U D
② 凝胶时 间要合适 ,过长 的凝胶时 间会,过 短的
凝胶时 间会导致 在灌注 过程 中就 出现 固化 ,产品未 能灌透 。 ③放 热峰要 合适 ,过低 的放热 峰会导致 树脂 固化 时间加 长 ,过 高 的放 热峰会 导致 叶片中
其余增 强材料 的老化 ,严重影 响质 量。 由于 V A R T M 技术在风 电市场 上 的应 用 ,成 型效 率越 来越高 ,但也 出现 了由于缩 短时 间及 V A R T M 技术 本身 的原因 ,风 电复合 材料 叶片在 成型过 程 中有 很 多的缺 陷 出现【 ,有些 缺陷 能可见 并修补 ,但一些 缺陷 就 由于 空 间或其他 原 因,无
风力发电叶片维修方案

风力发电叶片维修方案1. 简介风力发电是一种利用风能转换为电能的可再生能源。
在风力发电机中,叶片是最重要的组成部分之一,它们负责捕捉风能并将其转换为机械能以驱动发电机。
然而,由于长时间的运行和自然环境的影响,风力发电叶片可能会出现损坏和磨损。
因此,开发一套维修方案,及时发现和解决叶片问题,是保障风力发电机长期高效运行的关键。
2. 风力发电叶片维修方案2.1 检测和评估在进行风力发电叶片维修之前,首先需要对叶片进行检测和评估,以确定其损坏程度和所需维修的具体方案。
•目视检查:使用无损检测方法,对叶片表面进行目视检查,以寻找明显的损伤,如裂纹、漆面破损等。
•声波检测:使用声波检测装置,对叶片进行声波扫描,检测是否存在内部裂纹和松动。
•照相测量:使用高分辨率相机拍摄叶片表面,并使用计算机软件进行测量和分析,以确定表面平整性、破损程度和变形情况。
•动态测试:当风力发电机处于停机状态时,使用专业仪器对叶片进行动态测试,检测叶片在运行时的振动和变形情况。
2.2 维修方案根据叶片检测和评估的结果,制定相应的维修方案。
以下是常见的风力发电叶片维修方案:•表面修复:对叶片表面进行涂层修复,填补破损和剥落的漆面,提高叶片的防腐性能和表面光滑度。
•裂纹修复:使用专用的充填剂将叶片裂纹处填充,以提高叶片的结构强度和承载能力。
•切割和替换:对严重受损的叶片进行切割和替换,采用新的叶片部件进行更换,确保叶片完整性和性能。
•动态平衡:使用平衡仪对修复的叶片进行动态平衡,以减少振动和噪音,保证风力发电机的稳定运行。
2.3 维修注意事项在执行风力发电叶片维修方案时,需要注意以下事项:•安全:维修过程中,必须遵守相关的安全操作规定和程序,穿戴个人防护装备,确保人员和设备的安全。
•材料和工具:选择符合要求的维修材料和工具,确保维修质量和效果。
•环境保护:在维修过程中,注意环境保护,遵守相关的环境保护法规,正确处置废弃材料和废水。
•记录和报告:维修过程中,及时记录和汇报叶片检测、维修和测试结果,以便跟踪和评估维修效果和维修工作质量。
负责风电叶片维修出厂前的准备工作

负责风电叶片维修出厂前的准备工作
在风电叶片维修出厂前的准备工作中,主要包括以下几个方面:
1. 检查叶片状况:首先需要对风电叶片进行全面检查,包括表面是否有损伤、裂纹、腐蚀等,以及叶片内部结构是否完好。
如果发现有明显的破损或缺陷,需要及时进行修复或更换。
2. 清洗叶片表面:使用适当的清洗剂和工具对叶片表面进行清洗,去除污垢和附着物。
清洗完毕后,需要用清水进行冲洗,确保表面干净。
3. 进行结构强度检测:使用相关仪器对叶片进行结构强度和刚度的检测,以确保其满足设计和安全要求。
同时还需要检查叶片的平衡性,以保证其运行时不产生震动。
4. 进行涂层维修:如果叶片表面有涂层破损或脱落,需要进行相应的修复。
通常采用撬除脱落涂层、修复损伤部位,并重新涂覆防腐、防锈和防风化材料。
5. 进行电缆和连接器检查:对叶片内部的电缆和连接器进行检查和维护,确保其接触良好、防水性能良好。
6. 进行防腐处理:对叶片进行防腐处理,以延长其使用寿命和耐候性。
一般使用专用的防腐涂料进行涂覆,确保涂层完整、耐候性好。
7. 进行封装和包装:在维修完毕后,需要对叶片进行封装和包
装,以保护其免受运输和存储过程中的损坏。
常见的封装和包装方式包括使用防水塑料薄膜、泡沫保护材料等。
总之,风电叶片维修出厂前的准备工作是一个细致入微的过程,需要对叶片进行全面检查和修复,并做好防腐、防震、防水等工作,以确保其良好的运行和使用寿命。
复合材料风机叶片运维及修复

复合材料风机叶片运维及修复叶片是风力发电机的核心部件之一,叶片状态的好坏直接影响到整机的性能和发电效率.。
本文通过对某风电场运行中风机叶片失效分析,提出叶片故障的预控描施及如何做好运维过程管控.。
关键词:故障分析;维护管理;预控办法引言叶片是将风能转化为机械能,通过变桨装置调整桨距角,改变风力发电机组输出功率,实现控制功率输出的目的,叶片维护至关重要,有效的保养和修复能够提高叶片的使用寿命和发电效率.。
一、复合材料叶片简介叶片主材为玻璃纤维增强环氧树脂,叶片结构包括外壳、主梁帽及夹层结构的腹板,主梁帽、腹板、外壳都采用玻璃钢制作而成,叶片由两片外壳粘接而成,中间由腹板支撑,叶片外壳夹层采用轻质的Balsa木、PVC泡沫做成.。
叶片避雷系统由叶尖的铝制接闪器,和中部接闪器,(PS面和SS面分别对称).。
接闪器与铜质导线连接,连接铜导线和铝制部分的电缆采用镀层以防止铝端的电离腐蚀;叶根避雷导线直接连接于人孔盖板的铜连接板上.。
二、复合材料叶片缺陷(1)技术缺陷(1)夹芯结构缺陷或损伤分为外蒙皮缺陷或损伤、芯材缺陷或损伤、外蒙皮加芯材缺陷或损伤、外蒙皮及芯材加内蒙皮贯穿性缺陷或损伤等.。
合模前或合模后叶片内腔人能进入到的位置内蒙皮损伤、内蒙皮加芯材缺陷或损伤可等效为外蒙皮缺陷或损伤、外蒙皮加芯材缺陷或损伤.。
(2)梁帽及后缘UD缺陷及损伤主要指梁帽及后缘发白、褶皱、杂物等缺陷或损伤.。
(3)叶根玻璃钢区域缺胶及损伤主要指包围、发白、撞伤等缺陷或损伤.。
(4)叶片前、后缘缺胶:分为需要修复性缺胶和无需修复性缺胶,前缘修复性缺胶需满足:弦向缺胶位置总长度大于弦向粘接宽度的20%,且长度大于2cm;后缘修复性缺胶需满足:弦向缺胶位置总长度大于弦向粘接宽度的15%,且长度大于2cm.。
(5)腹板缺胶:分为需要修复性缺胶和无需修复性缺胶,腹板缺胶需满足:弦向粘接法兰缺胶宽度大于3cm,且轴向长度大于5cm.。
(6)叶片后缘开裂叶片后缘开裂包括I型后缘结构胶开裂与Ⅱ型后缘结构胶.。
复合材料风电叶片的检查保护及维修
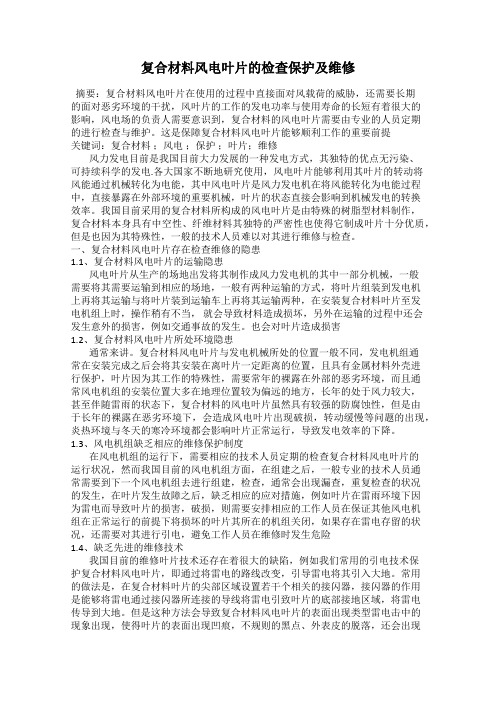
复合材料风电叶片的检查保护及维修摘要:复合材料风电叶片在使用的过程中直接面对风载荷的威胁,还需要长期的面对恶劣环境的干扰,风叶片的工作的发电功率与使用寿命的长短有着很大的影响,风电场的负责人需要意识到,复合材料的风电叶片需要由专业的人员定期的进行检查与维护。
这是保障复合材料风电叶片能够顺利工作的重要前提关键词:复合材料;风电;保护;叶片;维修风力发电目前是我国目前大力发展的一种发电方式,其独特的优点无污染、可持续科学的发电.各大国家不断地研究使用,风电叶片能够利用其叶片的转动将风能通过机械转化为电能,其中风电叶片是风力发电机在将风能转化为电能过程中,直接暴露在外部环境的重要机械,叶片的状态直接会影响到机械发电的转换效率。
我国目前采用的复合材料所构成的风电叶片是由特殊的树脂型材料制作,复合材料本身具有中空性、纤维材料其独特的严密性也使得它制成叶片十分优质,但是也因为其特殊性,一般的技术人员难以对其进行维修与检查。
一、复合材料风电叶片存在检查维修的隐患1.1、复合材料风电叶片的运输隐患风电叶片从生产的场地出发将其制作成风力发电机的其中一部分机械,一般需要将其需要运输到相应的场地,一般有两种运输的方式,将叶片组装到发电机上再将其运输与将叶片装到运输车上再将其运输两种,在安装复合材料叶片至发电机组上时,操作稍有不当,就会导致材料造成损坏,另外在运输的过程中还会发生意外的损害,例如交通事故的发生。
也会对叶片造成损害1.2、复合材料风电叶片所处环境隐患通常来讲。
复合材料风电叶片与发电机械所处的位置一般不同,发电机组通常在安装完成之后会将其安装在离叶片一定距离的位置,且具有金属材料外壳进行保护,叶片因为其工作的特殊性,需要常年的裸露在外部的恶劣环境,而且通常风电机组的安装位置大多在地理位置较为偏远的地方,长年的处于风力较大,甚至伴随雷雨的状态下,复合材料的风电叶片虽然具有较强的防腐蚀性,但是由于长年的裸露在恶劣环境下,会造成风电叶片出现破损,转动缓慢等问题的出现,炎热环境与冬天的寒冷环境都会影响叶片正常运行,导致发电效率的下降。
风力发电场中叶片损伤检测与修复
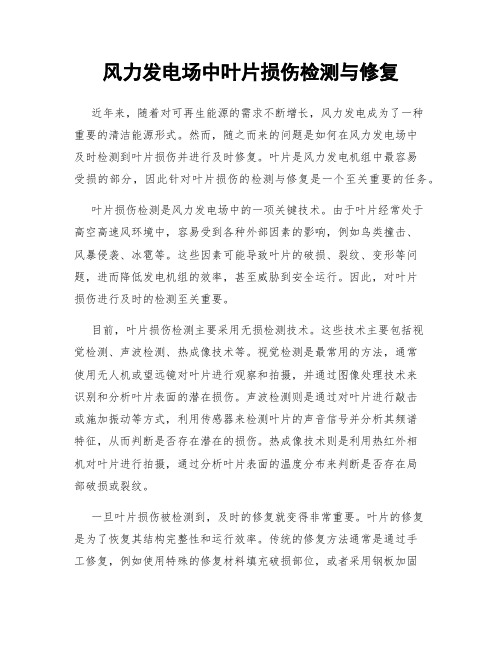
风力发电场中叶片损伤检测与修复近年来,随着对可再生能源的需求不断增长,风力发电成为了一种重要的清洁能源形式。
然而,随之而来的问题是如何在风力发电场中及时检测到叶片损伤并进行及时修复。
叶片是风力发电机组中最容易受损的部分,因此针对叶片损伤的检测与修复是一个至关重要的任务。
叶片损伤检测是风力发电场中的一项关键技术。
由于叶片经常处于高空高速风环境中,容易受到各种外部因素的影响,例如鸟类撞击、风暴侵袭、冰雹等。
这些因素可能导致叶片的破损、裂纹、变形等问题,进而降低发电机组的效率,甚至威胁到安全运行。
因此,对叶片损伤进行及时的检测至关重要。
目前,叶片损伤检测主要采用无损检测技术。
这些技术主要包括视觉检测、声波检测、热成像技术等。
视觉检测是最常用的方法,通常使用无人机或望远镜对叶片进行观察和拍摄,并通过图像处理技术来识别和分析叶片表面的潜在损伤。
声波检测则是通过对叶片进行敲击或施加振动等方式,利用传感器来检测叶片的声音信号并分析其频谱特征,从而判断是否存在潜在的损伤。
热成像技术则是利用热红外相机对叶片进行拍摄,通过分析叶片表面的温度分布来判断是否存在局部破损或裂纹。
一旦叶片损伤被检测到,及时的修复就变得非常重要。
叶片的修复是为了恢复其结构完整性和运行效率。
传统的修复方法通常是通过手工修复,例如使用特殊的修复材料填充破损部位,或者采用钢板加固等手段。
然而,这种修复方法存在一定的局限性,例如需要大量人力和物力,修复效果难以保证等。
近年来,随着材料科学和机器人技术的进步,出现了一些新的叶片修复方法。
其中一种方法是利用复合材料修复叶片。
复合材料具有优异的力学性能和耐久性,可以有效地提高叶片的结构强度和抗风能力。
修复过程可以通过手工施工或者使用机器人进行自动化修复。
另一种趋势是采用3D打印技术进行叶片修复。
3D打印技术可以根据叶片的设计需求来精确打印修复材料,大大提高修复效果和工作效率。
除了及时检测和修复叶片损伤,预防叶片损伤也是非常重要的。
风电机组叶片无损检测技术研究与进展

风电机组叶片无损检测技术研究与进展风电机组叶片在运行时除了承受气动力作用外,还承受重力、离心力等其他力的影响,再加上雨雪、沙尘、盐雾侵蚀、雷击等破坏,使叶片基体及表面容易受到损伤,这些损伤如未及时发现与维修会导致风电机组发电效率下降、停机,甚至发生损毁等事故。
因此,风电机组叶片损伤检测对保障风电机组安全高效运行、降低风电机组寿命周期内发电成本有重大意义。
01风电叶片主要缺陷、损伤类型及损伤原因风电叶片是复合材料设计制作的特殊结构,其内部结构如图1所示。
其损伤主要原因有:1)疲劳损伤。
风力发电机在长期运行中,由于疲劳作用叶片会出现微小裂缝、裂纹和缺陷等,最终导致叶片的断裂或失效。
2)延迟失效。
当叶片被暴露在恶劣环境下,比如高温、低温、潮湿或强风等条件下,其寿命会显著降低,可能会导致延迟失效。
3)冲击损伤。
当叶片受到外部冲击或碰撞时,容易出现破裂、裂纹和断裂等问题。
4)腐蚀损伤。
当叶片表面受到化学物质、海水或大气污染等因素的侵蚀时,会出现腐蚀损伤,导致叶片性能下降或失效。
5)材料老化。
随着使用时间的增加,叶片材料的力学性能逐渐下降,这可能会导致叶片的失效。
图1图1 风电叶片内部结构示意风电叶片局部损伤风电叶片的局部损伤通常指在使用过程中,叶片某些区域出现了裂纹、划痕、腐蚀等问题。
这些损伤可能会影响叶片的性能和可靠性,甚至危及风力发电系统的安全。
1叶片表面裂纹叶片运行进入中期后,叶片表面受疲劳载荷作用容易产生裂纹,尤其是前缘处受拉伸载荷的影响容易产生横向疲劳裂纹(裂纹沿叶展方向为纵向裂纹,垂直于叶展方向为横向裂纹)。
叶片表面裂纹产生的原因有:1)涂层本身耐候性(耐紫外、风沙、雨蚀等)不满足设计要求,整体出现龟裂等;2)涂层底部的复合材料部分存在缺陷,导致叶片运行过程中出现应力集中,裂纹在涂层面上表现出来,如图2和图3所示。
图2 叶片表面横向裂纹图3 叶片表面纵向裂纹2叶片表面或内部分层如果叶片生产制造过程中存在一些区域粘接不良,在长期交变载荷的作用下,叶片表面、前后缘、主梁、腹板等部分可能会发生分层,如图4和图5所示。
复合材料风机叶片运维及修复
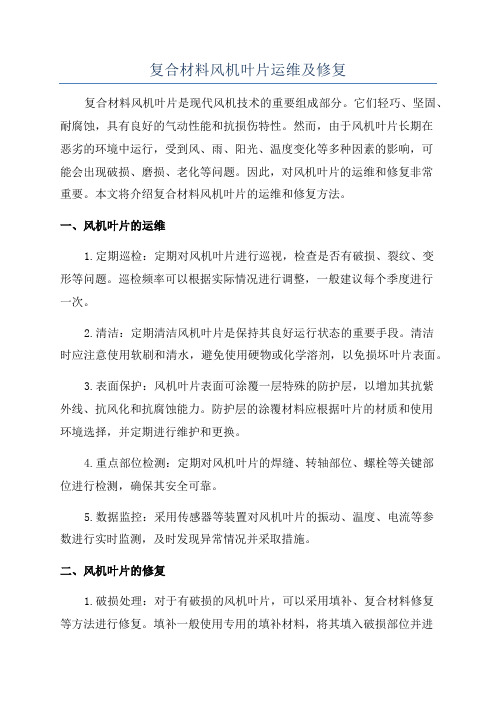
复合材料风机叶片运维及修复复合材料风机叶片是现代风机技术的重要组成部分。
它们轻巧、坚固、耐腐蚀,具有良好的气动性能和抗损伤特性。
然而,由于风机叶片长期在恶劣的环境中运行,受到风、雨、阳光、温度变化等多种因素的影响,可能会出现破损、磨损、老化等问题。
因此,对风机叶片的运维和修复非常重要。
本文将介绍复合材料风机叶片的运维和修复方法。
一、风机叶片的运维1.定期巡检:定期对风机叶片进行巡视,检查是否有破损、裂纹、变形等问题。
巡检频率可以根据实际情况进行调整,一般建议每个季度进行一次。
2.清洁:定期清洁风机叶片是保持其良好运行状态的重要手段。
清洁时应注意使用软刷和清水,避免使用硬物或化学溶剂,以免损坏叶片表面。
3.表面保护:风机叶片表面可涂覆一层特殊的防护层,以增加其抗紫外线、抗风化和抗腐蚀能力。
防护层的涂覆材料应根据叶片的材质和使用环境选择,并定期进行维护和更换。
4.重点部位检测:定期对风机叶片的焊缝、转轴部位、螺栓等关键部位进行检测,确保其安全可靠。
5.数据监控:采用传感器等装置对风机叶片的振动、温度、电流等参数进行实时监测,及时发现异常情况并采取措施。
二、风机叶片的修复1.破损处理:对于有破损的风机叶片,可以采用填补、复合材料修复等方法进行修复。
填补一般使用专用的填补材料,将其填入破损部位并进行打磨和涂层保护。
复合材料修复则是使用与叶片相同或相似的复合材料进行修复,修复后需要进行热处理和表面处理。
2.磨损处理:风机叶片由于长期使用,叶片表面可能会出现磨损现象。
可以采用研磨、喷涂、复合材料修复等方法进行修复。
研磨时应注意选择合适的磨料和磨具,以避免进一步损伤叶片表面。
喷涂和复合材料修复则是在叶片表面形成一层保护性涂层,增加其使用寿命。
3.老化处理:风机叶片长时间使用后可能会出现老化现象,如脆化、黄变等。
可以采用表面处理、喷涂等方法进行修复,恢复叶片的强度和外观。
4.备件替换:如果风机叶片严重破损或老化,修复效果不佳时,可以考虑更换备件。
风电机组的日常检修维护与故障处理

风电机组的日常检修维护与故障处理
风电机组是一种利用风能发电的设备,它能够有效地转化风能为电能,是清洁能源的重要组成部分。
风电机组的日常检修维护与故障处理对于保证其正常运行和延长使用寿命非常重要。
本文将从风电机组的日常检修维护和故障处理两个方面展开讨论。
一、风电机组的日常检修维护
1. 定期检查风叶和轮毂
风叶和轮毂是风电机组的关键部件,定期检查其表面是否有损坏或者积聚物,保证风叶和轮毂的完好无损是保证风电机组正常运行的重要保障。
2. 润滑系统的维护
风电机组中的润滑系统对于减少机械磨损、降低摩擦阻力、提高传动效率非常重要。
定期检查润滑系统的油液是否足够、是否干净,并进行必要的添加和更换。
3. 控制系统和传感器的检修
风电机组的控制系统和传感器是保证风能的高效利用的关键部件,定期检查其工作状态,对于发现故障及时进行修复是非常重要的。
4. 定期清洗和除尘
风电机组的外部表面容易积聚尘土和杂物,定期清洗和除尘有助于保持风电机组的整洁,减少风阻力,提高发电效率。
5. 定期进行机械和电气系统的检修
二、风电机组的故障处理
叶片的损坏往往会导致风能的损失和对其他部件的损坏,因此对于风电机组叶片的故障处理是非常重要的。
一旦发现叶片有损坏,需要及时更换或修复。
风电机组的电气系统是其核心部件,一旦发现电气系统有故障,需要及时处理。
首先需要对故障进行定位,然后进行修复。
润滑系统的故障会导致机械磨损加剧、摩擦阻力增大,影响风电机组的正常运行。
一旦发现润滑系统有故障,需要及时处理,同时对于老化的润滑油进行更换。
风电叶片外观及零部件质量缺陷的维修方案
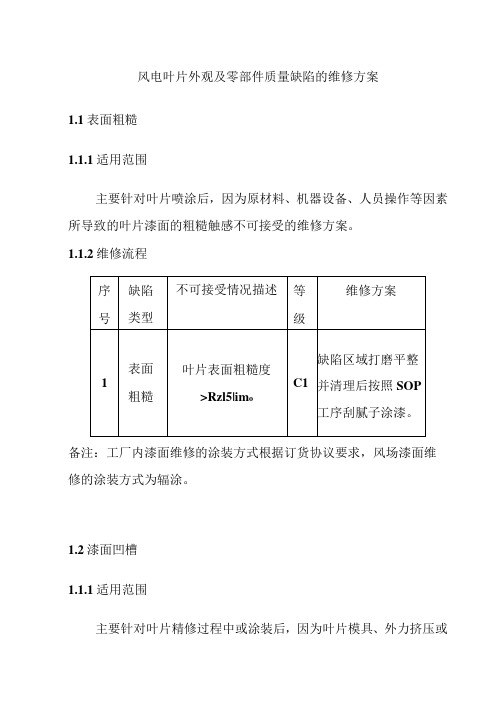
风电叶片外观及零部件质量缺陷的维修方案1.1表面粗糙1.1.1适用范围主要针对叶片喷涂后,因为原材料、机器设备、人员操作等因素所导致的叶片漆面的粗糙触感不可接受的维修方案。
1.1.2维修流程备注:工厂内漆面维修的涂装方式根据订货协议要求,风场漆面维修的涂装方式为辐涂。
1.2漆面凹槽1.1.1适用范围主要针对叶片精修过程中或涂装后,因为叶片模具、外力挤压或修型不到位等因素所致而形成叶片表面凹槽的维修方案。
1.1.2维修流程修合格后按上述维修方案维修。
1.3漆面擦伤1.1.1适用范围主要针对叶片喷涂完毕后,因外力或不可抗或人为因素,导致叶片漆面表面损伤的维修方案。
1.1.2维修流程备注:漆面擦伤伤及玻璃钢时,须先对玻璃钢进行修复,维修合格后按上述维修方案维修。
1.4表面流挂、毛刺、露底1.1.1适用范围主要针对涂装过程中因喷涂、滚涂方法不正确或表面处理不到位所形成的漆面流挂、漆面毛刺、露底的维修方案。
1.1.2维修流程底严重的漆面,彻底打磨,再重新涂装。
1.5标识1.1.1适用范围主要针对叶片出厂前,用于标记叶片基本信息的各类标示不可接受的维修方案,包含标识位置、安全标识、标识喷涂质量、标识的完整性。
1.6颗粒物1.1.1适用范围主要针对叶片喷涂后,出现在叶片壳体表面的颗粒物不可接受的维修方案。
1.1.2维修流程备注说明:(1)漆面颗粒物较密集的区域需要在铲平表面颗粒物后进行面漆喷涂,颗粒物较稀疏的区域直接将表面颗粒物铲平即可。
(2)漆面颗粒物铲除后,漆面无破损的可不需要涂漆,漆面有破损需涂漆。
(3)工厂内漆面维修的涂装方式根据订货协议要求,风场漆面维修的涂装方式为馄涂。
1.7挡板胶流1.7.1适用范围主要针对叶片生产过程中,因为挡板界面保护不当,致使其表面被手糊树脂污染所形成的流痕的维修方案。
1.7.2维修流程主要针对涂层固化后,通过使用漆膜测厚仪对漆层干膜厚度进行检测,涂层干膜厚度不能满足技术要求的情况的维修方案。
风力发电叶片维修

风力发电叶片维修标题:风力发电叶片维修导言:风力发电是一种可再生能源,受到越来越多国家的重视和推广。
风力发电机的叶片是其中一个重要部件,它们承受着巨大的风力冲击和不断的磨损,因此需要定期维修和保养。
本文将介绍风力发电叶片维修的相关知识和方法。
一、叶片维修的重要性风力发电叶片是转化风能为机械能的核心部件,其工作负荷较大,容易受到外界因素的影响而损坏。
叶片的损坏不仅会降低风力发电机的发电效率,还可能导致整个机组的故障。
因此,定期维修和保养叶片对于风力发电的长期稳定运行至关重要。
二、常见的叶片损坏情况1. 表面磨损:受风力冲击和颗粒物的磨损,叶片表面会出现划痕和磨损,降低了叶片的气动性能。
2. 裂纹和断裂:长时间受到风力冲击和振动,叶片可能出现裂纹和断裂现象,严重影响叶片的强度和稳定性。
3. 油漆剥落:叶片表面的油漆可能因为长时间暴露在恶劣的环境中而剥落,导致腐蚀和氧化,进一步加剧叶片的损坏。
三、叶片维修的方法1. 清洁叶片:定期清洁叶片表面的污垢和颗粒物,可以使用软刷和清水进行清洗,注意不要使用过硬的物体刮擦叶片表面,以免造成划伤。
2. 磨损修补:对于叶片表面的划痕和磨损,可以使用砂纸和抛光机进行修补,恢复叶片的光滑度和气动性能。
3. 裂纹修复:对于叶片的裂纹和断裂,需要进行专业的修复。
可以使用环氧树脂胶水和玻璃纤维布进行修复,增强叶片的强度和稳定性。
4. 油漆涂覆:定期对叶片进行油漆涂覆,可以防止叶片腐蚀和氧化。
选择适合的油漆材料,确保其耐候性和耐腐蚀性。
四、叶片维修的注意事项1. 定期检查:定期检查叶片的状况,发现问题及时进行修复,避免小问题演变为大故障。
2. 安全保护:在进行叶片维修时,必须配备合适的安全设备,如安全带、安全绳等,确保工作人员的人身安全。
3. 专业人员:叶片维修需要专业的技术和经验,建议由风力发电厂或专业公司的工程师进行维修。
4. 环保意识:在进行叶片维修时,要注意环境保护,避免污染和对生态环境的破坏。
风电叶片腹板富树脂的维修方案
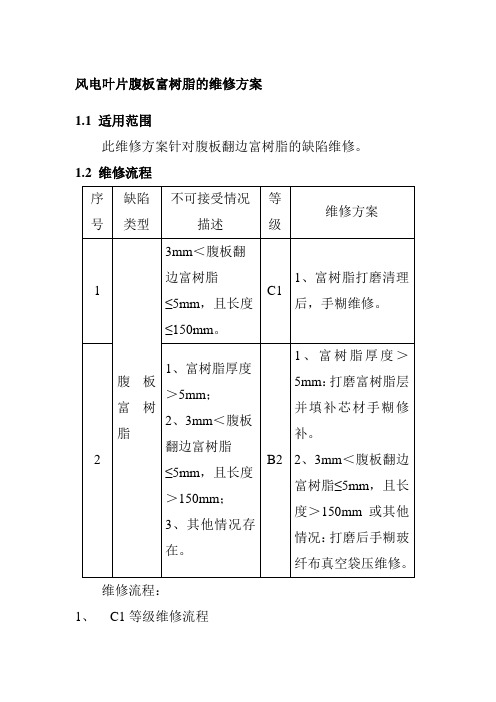
风电叶片腹板富树脂的维修方案1.1 适用范围此维修方案针对腹板翻边富树脂的缺陷维修。
1.2 维修流程维修流程:1、C1等级维修流程缺陷区富树脂清理→玻璃钢层手糊补强→加热固化→维修结果确认。
2、B2等级维修流程(1)富树脂厚度>5mm缺陷区富树脂清理→芯材填补→玻璃钢层手糊补强→抽真空袋压成型→加热固化。
(2)3mm<腹板翻边富树脂≤5mm,且长度>150mm或其他情况缺陷区富树脂清理→玻璃钢层手糊补强→抽真空袋压成型→加热固化。
1.3 维修工序1、C1等级(1)打磨缺陷区域富树脂用圆盘角磨机将缺陷区域富树脂打磨干净,同时将芯材区域表面打磨粗糙面,然后清理干净打磨粉尘,须保证待修面表面为粗糙面,且洁净无粉尘、无异物。
(2)缺陷区玻璃钢层手糊补强在缺陷区域上方手糊铺放双轴织物,按照由小到大或由大到小顺序进行错层铺放,弦向10mm/层错层和轴向50mm/层错层(局部过窄区域20mm/层)进行手糊铺设,原富树脂层区域厚度用糊制布层全部替代。
详细手糊作业要求可参见1.4手糊工艺维修。
(3)加热固化使用加热毯或其他加热方式对维修区域进行加热,保证维修区域完全固化,手糊树脂固化条件为≥60℃,保温3小时;固化要求参见1.4.1.4手糊固化工艺要求。
2、B2等级(富树脂厚度>5mm)(1)打磨清理富树脂将芯材上方的富树脂打磨干净,若间隙或缺失芯材所在区域为空腔,则需要将空腔区域表面打磨粗糙,须保证待修面表面为粗糙面,且洁净无粉尘、无异物。
(2)缺陷区域芯材填补在间隙过大区域准备与间隙或缺失所处的相同规格的芯材(材质、厚度、宽度)填补到间隙或缺失区域,填补后芯材间隙≤2mm。
(3)缺陷区芯材上方玻璃钢层修复在芯材上方按照原布层顺序铺放n+1层布,第n+1层与第n层玻纤布类型相同,按照由小到大或由大到小顺序进行错层铺放,长度方向按照1:50比例错层,弦长方向法兰边侧按照1:20比例错层,芯材上侧按照5cm/层错层,翻边上侧按照1cm/层错层(如下图14所示)。
- 1、下载文档前请自行甄别文档内容的完整性,平台不提供额外的编辑、内容补充、找答案等附加服务。
- 2、"仅部分预览"的文档,不可在线预览部分如存在完整性等问题,可反馈申请退款(可完整预览的文档不适用该条件!)。
- 3、如文档侵犯您的权益,请联系客服反馈,我们会尽快为您处理(人工客服工作时间:9:00-18:30)。
复合材料风电叶片的检查保护及维修
发表时间:2019-09-19T17:26:28.827Z 来源:《当代电力文化》2019年第8期作者:雷山山杨成玲[导读] 风电场的负责人需要意识到,复合材料的风电叶片需要由专业的人员定期的进行检查与维护。
新疆伊犁库克苏河水电开发有限公司新疆伊宁835000摘要:复合材料风电叶片在使用的过程中直接面对风载荷的威胁,还需要长期的面对恶劣环境的干扰,风叶片的工作的发电功率与使用寿
命的长短有着很大的影响,风电场的负责人需要意识到,复合材料的风电叶片需要由专业的人员定期的进行检查与维护。
这是保障复合材料风电叶片能够顺利工作的重要前提关键词:复合材料;风电;保护;叶片;维修风力发电目前是我国目前大力发展的一种发电方式,其独特的优点无污染、可持续科学的发电.各大国家不断地研究使用,风电叶片能够利用其叶片的转动将风能通过机械转化为电能,其中风电叶片是风力发电机在将风能转化为电能过程中,直接暴露在外部环境的重要机械,叶片的状态直接会影响到机械发电的转换效率。
我国目前采用的复合材料所构成的风电叶片是由特殊的树脂型材料制作,复合材料本身具有中空性、纤维材料其独特的严密性也使得它制成叶片十分优质,但是也因为其特殊性,一般的技术人员难以对其进行维修与检查。
一、复合材料风电叶片存在检查维修的隐患
1.1、复合材料风电叶片的运输隐患
风电叶片从生产的场地出发将其制作成风力发电机的其中一部分机械,一般需要将其需要运输到相应的场地,一般有两种运输的方式,将叶片组装到发电机上再将其运输与将叶片装到运输车上再将其运输两种,在安装复合材料叶片至发电机组上时,操作稍有不当,就会导致材料造成损坏,另外在运输的过程中还会发生意外的损害,例如交通事故的发生。
也会对叶片造成损害1.2、复合材料风电叶片所处环境隐患
通常来讲。
复合材料风电叶片与发电机械所处的位置一般不同,发电机组通常在安装完成之后会将其安装在离叶片一定距离的位置,且具有金属材料外壳进行保护,叶片因为其工作的特殊性,需要常年的裸露在外部的恶劣环境,而且通常风电机组的安装位置大多在地理位置较为偏远的地方,长年的处于风力较大,甚至伴随雷雨的状态下,复合材料的风电叶片虽然具有较强的防腐蚀性,但是由于长年的裸露在恶劣环境下,会造成风电叶片出现破损,转动缓慢等问题的出现,炎热环境与冬天的寒冷环境都会影响叶片正常运行,导致发电效率的下降。
1.3、风电机组缺乏相应的维修保护制度
在风电机组的运行下,需要相应的技术人员定期的检查复合材料风电叶片的运行状况,然而我国目前的风电机组方面,在组建之后,一般专业的技术人员通常需要到下一个风电机组去进行组建,检查,通常会出现漏查,重复检查的状况的发生,在叶片发生故障之后,缺乏相应的应对措施,例如叶片在雷雨环境下因为雷电而导致叶片的损害,破损,则需要安排相应的工作人员在保证其他风电机组在正常运行的前提下将损坏的叶片其所在的机组关闭,如果存在雷电存留的状况,还需要对其进行引电,避免工作人员在维修时发生危险1.4、缺乏先进的维修技术
我国目前的维修叶片技术还存在着很大的缺陷,例如我们常用的引电技术保护复合材料风电叶片,即通过将雷电的路线改变,引导雷电将其引入大地。
常用的做法是,在复合材料叶片的尖部区域设置若干个相关的接闪器,接闪器的作用是能够将雷电通过接闪器所连接的导线将雷电引致叶片的底部接地区域,将雷电传导到大地。
但是这种方法会导致复合材料风电叶片的表面出现类型雷电击中的现象出现,使得叶片的表面出现凹痕,不规则的黑点、外表皮的脱落,还会出现不同程度的叶片开裂,在雨水的浸泡下,导致其运转的故障。
二、复合材料风电叶片的检查维修方法
2.1、运输环节的保护
我国目前的复合材料风电叶片的维修检查的方法主要采用观察、使用工具敲试、将涂层打开进行深入内部的观察和维修等,无论其中哪一种检查维修方法,都需要极为专业的检查维护团体与专业的技术人员。
在运输与安装环节,为了避免出现损伤的叶片的行为,则使用专业的技术人员在运输途中通过对叶片的外表进行严谨观察,一旦出现明显的叶片外观损伤与叶片涂层的表面材料出现了刮蹭、损伤,都需要通知相关的叶片制造商与专业的的复合材料风电叶片的维修人员对其进行专业的检查与维修、并对相关的叶片进行拍照,保存资料,对怎样发生事故的原因进行研究,保存,便于以后类似的事故发生之后,进行处理。
2.2、采用先进的检查维修技术
我国传统的检查维修技术,一般在复合材料风电风叶进行检查之时,对其进行拆卸,检查内部,之后对其进行组装,工程量繁琐,极为麻烦,而因为复合材料的外表涂层层数较多、每次的拆卸检查都会对叶片造成损害,在考虑到成本和时间的基础上,采用先进的无损检测设备技术,超声波探测检查技术。
超声波技术它适用于对复合材料其表面下几厘米厚度的区域进行探查,对其能够准确的找到所出现的问题,代替了我国传统的敲击检测方法,能够减少叶片表面的在因为检查维修之时出现的损伤。
还有一种方法称之为错位散斑干涉技术,这种技术主要应用在航空检查与海洋机械之中,它能够在恶劣的环境下对复合材料风电叶片的错位,破损,漏电等情况进行准确定位,代替了传统的人工检查,保障了专业技术人员的人身安全2.3、制定严谨的检查维修制度
在复合材料风电叶片的日常检查维修之中,设立专门的检查制度,对叶片的外边涂层,接口,螺旋仪器,地面引电装置,叶片接电器等等位置进行相关的检查制度设定,;例如对接点器的检查,需要分为三部分:第一部是对其接口处的涂层进行检查,检查复合材料风电叶片与接电器的接口处其表面涂层是否出现脱落。
第二部分则是对其接口处的导电性能进行检查,使用仪器对其导电性能进行检测,一旦发生导电的故障,尽快进行处理。
第三部分则是对整体外部金属的检查,观察是否出现破损,出现后立即更换,保障叶片的正常运行三、结束语
伴随着我国对电力需求的增加,风力发电在因为其高效环保的特点在发电方面所占比重越来越大,本文就目前复合材料风电叶片的维修出现的隐患进行分析,提出了具体的建议参考文献:
[1]当代风电设备技术发展现状及前景 [J].沈德昌.太阳能.2018(04)
[2] 风电叶片全寿命周期性能研究[J]. 唐荆,陈啸,杨科.风能.2017(01)。