石墨化增碳剂详细
增碳剂配方

增碳剂配方
增碳剂配方
一、原料:
(1)碳酸钙:60克;
(2)硫酸铵:20克;
(3)碳酸铵:20克;
(4)硫酸钠:20克;
(5)灰垢:30克;
(6)石灰石:20克;
(7)烧碱:20克;
(8)硫黄:10克。
二、配方:
(1)将碳酸钙、硫酸铵、碳酸铵、硫酸钠的总量加入搅拌桶中,搅拌混合均匀,形成基料;
(2)将灰垢、石灰石、烧碱、硫黄以同样的比例混合在基料中,与基料搅拌均匀;
(3)将混合物倒入模具中,经道模压机压制成碳剂;
(4)完成后,将碳剂进行天然烘焙,使之软硬适度,从而使其变得坚实,不易水解。
三、使用方法:
(1)将配制好的碳剂放置在水池中,等待水流经过;
(2)每次添加量为20-30克,每次添加碳剂后,应等待水流完
全透过,以防止碳剂淤积;
(3)用碳剂增碳,可以提高水质,增碳剂用量不宜过多,否则会影响水质。
铸造用增碳剂

煤质增碳剂:灰分、挥发份较高(电炉熔炼已很少用)
优质增碳剂一般指经过石墨化的增碳剂,在高温条件下,碳原子的排 列呈石墨的微观形态,所以称之为石墨化。石墨化可以降低增碳剂中杂质 的含量,提高增碳剂的碳含量,降低硫含量。
2、增碳剂指标
HT250铸件用增碳剂(粒度1-Leabharlann mm):项目固定碳
硫
3.6 避免增碳剂被卷入炉渣 增碳剂一旦被卷入炉渣中,就不能与铁液接触,当然会严重影响增碳效
果。
3、影响增碳剂吸收的因素
3.3 增碳剂粒度 增碳剂粒度是影响增碳剂熔入铁液的主要因素。一般来说,增碳剂的粒
度越小与铁液接触的界面面积就越大,增碳的效率就会越高,但太细的颗粒 已于被氧化且在易于被对流的空气和除尘系统抽走,因此增碳剂尺寸下限不 宜低于1mm。在熔炼铁水材质、过热温度一致的情况下,增碳剂粒度越大越难 以熔化,在电炉中以固态存在的时间就越长,与空气接触的时间也越长,导 致烧损严重,吸收率降低,因此增碳剂的尺寸上限不宜高于4mm。
2.4 氮 氮是衡量增碳剂好坏的一个重要指标。 在灰铁中适量的氮(<150ppm)可使石墨片长度缩短,弯曲程度增加,端
部钝化,长宽比减小,稳定珠光体,细化晶粒组织,提高抗拉强度和硬度。 氮含量过多,阻碍石墨化,增加碳化物稳定性,促进D型石墨的形成,提
高硬度,恶化加工性能,形成氮气孔(>150ppm)。
灰分
指标
≥97.5% ≤0.15%
≤0.3%
挥发分 ≤1%
氮 ≤150ppm
水分 ≤0.5%
2、增碳剂指标
YB/T 192-2001 炼钢用增碳剂
2、增碳剂指标
2.1 固定碳 增碳剂的固定碳不等同于含碳量。 固定碳值根据样品中的水分、挥发份、灰分及硫份计算得出,含碳量可
增碳剂基础要点简明介绍

增碳剂基础要点简明介绍一增碳机制增碳剂通过碳在铁液中的溶解和扩散进行增碳,吸收率取决于增碳剂溶解扩散速度和氧化损耗速度。
二增碳剂的种类增碳剂主要分为石墨化增碳剂和非石墨化增碳剂两大类。
石墨化增碳剂:废石墨电极,石墨电极边角料和碎屑,自然石墨压粒,石墨化焦和碳化硅。
非石墨化增碳剂:沥青焦,煅烧石油焦,乙炔焦炭压粒和煅烧无烟煤。
增碳剂按照铸造用途,材质和使用方法可具体划分为以下:1 按铸造用途分A 球铁增碳剂:C>98.5 S<0.05 主要为石墨化石油焦和石墨化电极。
吸收率高,吸收时间最快。
B 灰铁增碳剂:C>90 S<0.5 主要为非石墨化石油焦和煅煤。
吸收率在85%左右。
C 炼钢增碳剂:C 75-98 主要为煅煤,石墨球和天然石墨碎。
D 特种增碳剂:用于刹车片和包芯线。
一般为0-0.5/0.5-1 mm 石油焦。
2 按照材质分A 冶金焦增碳剂:为冲天炉用大焦B 煅煤增碳剂:多产于宁夏和内蒙C 90-93 S 0.3-0.5 (用于炼钢和灰铁)C 石油焦增碳剂:多产于辽宁,天津和山东C 96-99 S 0.3-0.7 (用于炼钢,灰铁和特种增碳剂)D 石墨化石油焦:多产于山东和河南,以及进口C 98-99.5 S 0.03-0.05 包括石墨化石油焦和石墨化电极(用于球铁)E 天然石墨增碳剂:多产于湖北和山东,C 65-99 (用于炼钢)F 复合材料增碳剂:以石墨粉,焦粉和石油焦为原料人工制造 C 93-97 S0.09-0.73 按照使用方法分主要有熔炼电炉用,保温电炉用,转炉用,冲天炉用,以及铁水包用增碳剂(随流增碳剂)三增碳效果的影响因素1 增碳剂的种类:石墨化增碳剂吸收率高,未经过煅烧的难吸收。
2 增碳剂的颗粒度:A 粒度小,溶解快,损耗大。
大小的选择和炉台直径及容量有关。
100KGS 10mm,500KGS 15mm,1.5T 20mm,20T 30mm。
B 颗粒度分布不均匀的吸收差。
回转炉煅烧增碳剂

回转炉煅烧增碳剂1. 介绍回转炉煅烧增碳剂的概念和作用回转炉煅烧增碳剂是一种用于钢铁生产中的辅助材料,主要用于增加炉料中的碳含量。
它由多种原料混合而成,经过特定的工艺处理后形成颗粒状,方便在回转炉中使用。
回转炉煅烧增碳剂在钢铁冶炼过程中起到了重要的作用,可以提高钢铁的质量和生产效率。
2. 回转炉煅烧增碳剂的原料和制备工艺回转炉煅烧增碳剂的原料主要包括焦炭、石墨、石油焦、木炭等。
这些原料经过破碎、筛分等处理后,按照一定比例混合,再进行加热、煅烧等工艺处理,最终形成所需的颗粒状增碳剂。
制备工艺主要包括以下几个步骤: 1. 原料准备:将焦炭、石墨、石油焦、木炭等原料进行破碎、筛分等处理,确保原料的粒度符合要求。
2. 混合配比:根据所需的成分比例,将不同原料按照一定比例混合。
3. 加热处理:将混合后的原料放入高温炉中进行加热处理,使其达到一定的温度。
4. 煅烧处理:将加热后的原料进行煅烧处理,使其形成颗粒状增碳剂。
5. 冷却和包装:将煅烧后的增碳剂进行冷却,并进行包装,以便于储存和运输。
3. 回转炉煅烧增碳剂的作用机理回转炉煅烧增碳剂在钢铁冶炼过程中的作用主要有两个方面:3.1 增碳作用回转炉煅烧增碳剂中的原料富含碳元素,当增碳剂投入回转炉中时,其碳元素会与炉料中的铁元素进行反应,生成高碳的铁合金。
这样可以增加炉料中的碳含量,提高钢铁的碳含量,使钢铁的强度、硬度等力学性能得到提高。
3.2 清洁作用回转炉煅烧增碳剂中的原料中还含有一定比例的灰分和硫等杂质。
当增碳剂投入回转炉中时,这些杂质会与炉料中的杂质进行吸附、还原等反应,从而减少钢铁中的杂质含量,提高钢铁的纯净度和质量。
4. 回转炉煅烧增碳剂的应用回转炉煅烧增碳剂主要应用于钢铁冶炼过程中。
在回转炉中,增碳剂可以通过喷吹、撒播等方式加入,与炉料一起进行反应。
增碳剂的投入量和投入时间可以根据具体的冶炼工艺和产品要求进行调整。
通过使用回转炉煅烧增碳剂,可以有效提高钢铁的质量和生产效率。
煅煤增碳剂概念

煅煤增碳剂概念煅煤增碳剂概念煅煤增碳剂是一种用于提高钢铁中碳含量的物质。
它通常由石墨或焦炭等原料制成,通过高温处理和加压形成。
在钢铁冶金过程中,它被用作一种添加剂,以达到所需的碳含量。
1. 煅煤增碳剂的分类根据原料不同,煅煤增碳剂可以分为焦炭增碳剂、沥青焦增碳剂、木质素增碳剂等几种。
- 焦炭增碳剂:主要由焦炭或其他高纯度的天然或人工焦制品制成。
具有高纯度、低灰分、低硫分等特点。
- 沥青焦增碳剂:主要由沥青或其他油类物质制成。
具有较高的灰分和硫分,并且易挥发。
- 木质素增碳剂:主要由木材、秸秆等植物纤维素类原料制成。
具有较高的灰分和硫分,并且易挥发。
2. 煅煤增碳剂的作用在钢铁冶金过程中,煅煤增碳剂的主要作用是提高钢铁中的碳含量。
它可以通过以下几种方式实现:- 熔化作用:煅煤增碳剂在高温下熔化,与钢水混合后,可以快速增加钢铁中的碳含量。
- 还原作用:煅煤增碳剂中的焦炭等物质可以还原钢铁中的氧化物,释放出大量的碳。
- 吸附作用:煅煤增碳剂表面具有一定的吸附能力,可以吸附钢铁中的杂质和气体,从而提高钢铁质量。
3. 煅煤增碳剂的使用方法在钢铁冶金过程中,通常将适量的煅煤增碳剂加入到钢水中进行混合。
具体使用方法如下:- 加入时间:一般在转包或转罐前加入。
- 加入方式:可以采用自由落下或压力喷射等方式进行加入。
- 加入量:根据不同需求和生产工艺确定。
4. 煅煤增碳剂的注意事项在使用煅烧增碳剂时,需要注意以下几点:- 保持干燥:煅煤增碳剂易吸潮,在存储和使用过程中需要保持干燥。
- 严禁混用:不同类型的煅煤增碳剂不能混用,否则会影响钢铁质量。
- 控制加入量:加入过多的煅烧增碳剂会导致钢铁中的杂质含量增加,影响钢铁质量。
总结煅烧增碳剂是一种用于提高钢铁中碳含量的物质,主要由焦炭、沥青焦或木质素等原料制成。
它在钢铁冶金过程中起到了重要的作用,能够通过熔化、还原和吸附等方式提高钢铁中的碳含量。
在使用时需要注意保持干燥、严禁混用和控制加入量等事项。
石墨化增碳剂
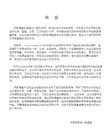
石墨化增碳剂特点
可以降低增碳剂中杂质的含量,提高增碳剂的含量,降低硫、氮含量,增碳效果稳定,碳的吸收率高。
石墨化增碳剂使用方法
在电炉底部放置炉料三分之一后将计算好的产品放置在炉料上,(炉中放一部分料后放增碳剂)然后把剩余炉料按要求放在上面,如上面的炉料较大时应把一些较碎的炉料压在增碳剂上,以防止漂浮影响吸收率。增碳剂加入量是金属量的1-3%,用户也可根据产品生产质量要求自行调整。增碳剂的特点是碳在铁液中吸收效果好,不返渣,使用增增碳剂定义
优质增碳剂一般指经过石墨化得增碳剂,在高温条件下,碳原子的排列呈石墨的微观形态,所以称之为石墨化。
石墨化增碳剂用途
主要用于冶金炼钢增碳和球铁铸造增碳。优质的石墨化增碳剂可用在作耐磨润滑材料、铸造、翻砂、压模及高温冶金材料、原子能工业和国防工业、能防止锅炉结垢、作铅笔芯、颜料、抛光剂、电极等行业。
石墨化增碳剂详细

产品:石墨化增碳剂成分含量:固定碳:≥98.5%灰分:≤0.5%挥发分:≤0.5%硫:≤0.05%水分:≤0.5%氮:≤0.03%(300ppm)生产不同粒度:0mm-0.5mm0.5mm-1mm1mm-5mm5mm-8mm1mm-10mm不同粒度报价不一样,可根据客户要求定制粒度我们工厂采用的是艾奇逊卧式炉锻造,月产量在4000-5000吨针对的客户:钢铁冶炼厂,铸造厂,贸易中间商产品特点:高固定碳,吸收率高,低硫低氮,并在吸收速度上快于同类石墨化增碳剂,且不吸附炉壁,完全吸收无残留,价格低于同类硫低于0.05以下的石墨化增碳剂,性价比高。
吸收率高,根据使用方法吸收率最高能达到90%以上.吸收速度快,比同类石墨化增碳剂吸收速度快,不吸附炉壁,且无残留,炉中增碳吸收速度优势更加明显.硫份低,0.05%以下超高的性价比,综述上述在同类石墨化增碳剂中(硫≤0.05)价格最优优势。
效益影响:石墨增碳剂为您降低成本,提高产品质量。
原材料可增加废钢用量,减少生铁用量或不用生铁,有效避免生铁的遗传性对铸件的影响。
含硫低,稳定可靠,有效节约硫在球化和孕育过程中对合金的不利影响,节省合金费用。
由于熔点低,吸收快,不反渣,可以有效保护和延长炉龄,减少炉衬消耗化学成分纯净:高碳、低硫、微氮,有害杂质少物理形态:外观洁净、无杂质,多孔隙结构,吸收速度快,吸收率高微观形态:晶体度质量优,有效提升铸件铸铁牌号和性能产品性质稳定:增碳效果稳定,吸收效果好,提温效果明显,不返渣包装:25千克/袋,编织袋(内里防水膜),可提供吨袋如需要特殊包装方式等,请致电贮存产品应存放在清洁、干燥的库房内,防止受潮和玷污及踩踏THANKS !!!致力为企业和个人提供合同协议,策划案计划书,学习课件等等打造全网一站式需求欢迎您的下载,资料仅供参考。
石墨球增碳剂

石墨球增碳剂石墨球增碳剂是一种常见的增碳剂,在许多工业领域都有广泛的应用。
本文将介绍石墨球增碳剂的定义、特点、用途以及制备方法。
一、石墨球增碳剂的定义石墨球增碳剂是由石墨粉末和粘结剂混合而成的球状颗粒物。
石墨球增碳剂具有高度的石墨化程度和良好的增碳效果,能够提高钢铁、铸件和合金材料的碳含量,改善其力学性能和工艺性能。
1. 高纯度:石墨球增碳剂采用高纯度的石墨粉末制备而成,具有较高的纯度,能够保证增碳效果的稳定性和可靠性。
2. 球状颗粒:石墨球增碳剂的颗粒形状为球状,具有较好的流动性和分散性,能够均匀地分布在熔体中,提高增碳的均匀性。
3. 耐高温:石墨球增碳剂具有较高的耐高温性能,能够在高温条件下保持其增碳效果,不易烧蚀和熔化。
4. 易于操作:石墨球增碳剂的使用方法简单,可直接投入熔体中,不需要额外的设备和工艺操作。
三、石墨球增碳剂的用途1. 钢铁冶炼:石墨球增碳剂可用于钢铁冶炼过程中的增碳操作,提高钢铁的碳含量,改善其硬度、强度和耐磨性。
2. 铸造工业:石墨球增碳剂可用于铸造工业中的增碳操作,提高铸件的碳含量,改善其铸造性能和机械性能。
3. 合金制备:石墨球增碳剂可用于合金制备过程中的增碳操作,提高合金材料的碳含量,改善其热处理性能和耐腐蚀性能。
四、石墨球增碳剂的制备方法1. 原料准备:将高纯度的石墨粉末和粘结剂按一定比例混合均匀。
2. 成型处理:将混合好的原料进行成型处理,通常采用压制的方式将其压制成球状颗粒。
3. 烧结处理:将成型好的石墨球增碳剂进行烧结处理,使其具有一定的强度和耐高温性能。
4. 表面处理:可对石墨球增碳剂进行表面处理,提高其流动性和分散性。
总结:石墨球增碳剂作为一种常见的增碳剂,具有高纯度、球状颗粒、耐高温和易于操作的特点。
它在钢铁冶炼、铸造工业和合金制备中有广泛的应用,能够提高材料的碳含量,改善其性能。
制备石墨球增碳剂的方法主要包括原料准备、成型处理、烧结处理和表面处理。
增碳剂标准

增碳剂标准1. 什么是增碳剂?增碳剂是一种用于提高金属中碳含量的材料,常见的增碳剂有石墨、石灰石、金属碳酸盐等。
增碳剂的主要作用是提供碳元素,以增加金属的硬度和强度。
2. 增碳剂标准的意义制定增碳剂标准的目的是为了保证增碳剂的质量,确保其能够按照预期的要求提供碳元素。
标准化的增碳剂在生产和应用过程中具有以下重要意义:2.1 保证产品质量增碳剂作为金属冶炼和炼钢的重要原料之一,其质量直接关系到金属产品的质量。
通过制定标准,可以确保增碳剂的成分和性能符合预期,提高金属产品的质量稳定性。
2.2 促进行业发展标准化的增碳剂可以提高行业整体水平,促进技术进步和创新。
通过标准化,可以形成一个统一的市场规则,激发企业竞争力,推动行业健康发展。
2.3 保护环境和人身安全增碳剂在生产和使用过程中可能会产生一些有害物质,如二氧化硫、氮氧化物等。
制定标准可以限制有害物质的排放和使用量,减少对环境和人身健康的影响,保护环境和人身安全。
3. 增碳剂标准的制定过程制定增碳剂标准需要经过一系列的步骤和程序,确保标准的科学性和可操作性。
以下是标准制定的主要步骤:3.1 确定制定标准的需求首先需要明确制定标准的目的和需求,包括产品的用途和适用范围、技术要求、测试方法等。
此步骤需要广泛征求相关利益方的意见和建议。
3.2 收集和分析相关数据收集和分析与增碳剂相关的数据和信息,包括市场需求、前期研究成果、国内外标准等。
通过比较和分析,确定标准的基本要求和技术指标。
3.3 制定初稿在收集和分析数据的基础上,制定初稿。
初稿应包括标准的名称、适用范围、术语和定义、要求和测试方法等内容。
初稿完成后,需要进行内部评审和讨论。
3.4 征求公众意见将初稿公开征求公众意见,接受各方的反馈和建议。
通过公众意见征集,可以获取更广泛的意见和建议,进一步完善标准。
3.5 修改和最终发布根据公众意见和专家建议,对初稿进行修改和完善。
最终确定标准的内容和形式,并进行正式发布和推广。
增碳剂 Carburizing agent(中英文对照)

增碳剂炼钢用增碳剂和铸铁用增碳剂,以及其他一些添加材料也有用到增碳剂,增碳剂属于外加炼钢、炼铁增碳原料。
优质增碳剂是生产优质钢材必不可少的辅助添加剂。
Carburizing agentUsing carburizing agent and cast iron using carburizing agent steel, and other materials are also useful for adding to the carburant carburant is applied, steelmaking, iron carbon materials. High quality carburizing agent is essential to producing high quality steel auxiliary additives.介绍:增碳剂的原料有很多种,生产工艺也各异,有木质碳类,煤质碳类,焦炭类,石墨类等,其中各种分类下又有很多小种类。
优质增碳剂一般指经过石墨化的增碳剂,在高温条件下,碳原子的排列呈石墨的微观形态,所以称之为石墨化。
石墨化可以降低增碳剂中杂质的含量,提高增碳剂的碳含量,降低硫含量。
增碳剂在铸造时使用,可大幅度增加废钢用量,减少生铁用量或不用生铁。
电炉熔炼的投料方式,应将增碳剂随废钢等炉料一起往里投放,小剂量的添加可以选择加在铁水表面。
但是要避免大批量往铁水里投料,以防止氧化过多而出现增碳效果不明显和铸件碳含量不够的情况。
增碳剂的加入量,根据其他原材料的配比和含碳量来定。
不同种类的铸铁,根据需要选择不同型号的增碳剂。
增碳剂特点本身选择纯净的含碳石墨化物质,降低生铁里过多的杂质,增碳剂选择合适可降低铸件生产成本。
Introduction:Carburizing agent there are many kinds of raw materials, production processes are different, there are wooden carbon carbon, coal, coke, graphite, in which all kinds of classification, there are many small species. High quality carburizing agent generally refers to the graphite carbon, under the condition of high temperature, carbon atoms arranged in graphite morphology, so called graphite. Graphite can reduce the content of impurity in recarburizer, increasing carbon content of carburizing agent, reducing sulfur content. Carbon in cast use, can greatly increase the amount of scrap, reduce the amount of pig iron or no iron. Furnace feeding way, should be the carbon with scrap charge to put in, small dose of added the option of adding on the surface of molten iron. But you should avoid large quantities of hot metal in to feed, to prevent oxidation and carbonization of excessive effect is not obvious and castings of carbon content of the insufficient. Carburizing agent dosage, according to other raw material ratio and carbon content to be. Different types of cast iron, according to the needs of different types of carburant. Selection of pure carbon graphite material carburant characteristics, reduces the cast iron excessive impurities, carbon agent selection can reduce the production cost of casting.使用:在冶炼过程中,由于配料或装料不当以及脱碳过量等原因,有时造成钢中碳含量没有达到顶期的要求,这时要向钢液中增碳。
感应电炉炼钢用增碳剂种类与使用方法

增碳剂介绍分炼钢用增碳剂(中华人民共和国黑色冶金行业标准,YB/T 192-2001炼钢用增碳剂)和铸铁用增碳剂,以及其他一些添加材料也有用到增碳剂,譬如刹车片用添加剂,作摩擦材料。
增碳剂属于外加炼钢、炼铁增碳原料。
优质增碳剂是生产优质钢材必不可少的辅助添加剂。
增碳剂的原料有很多种,生产工艺也各异,有木质碳类,煤质碳类,焦炭类,石墨类等,其中各种分类下又有很多小种类。
优质增碳剂一般指经过石墨化的增碳剂,在高温条件下,碳原子的排列呈石墨的微观形态,所以称之为石墨化。
石墨化可以降低增碳剂中杂质的含量,提高增碳剂的碳含量,降低硫含量。
增碳剂在铸造时使用,可大幅度增加废钢用量,减少生铁用量或不用生铁。
电炉熔炼的投料方式,应将增碳剂随废钢等炉料一起往里投放,小剂量的添加可以选择加在铁水表面。
但是要避免大批量往铁水里投料,以防止氧化过多而出现增碳效果不明显和铸件碳含量不够的情况。
增碳剂的加入量,根据其他原材料的配比和含碳量来定。
不同种类的铸铁,根据需要选择不同型号的增碳剂。
增碳剂特点本身选择纯净的含碳石墨化物质,降低生铁里过多的杂质,增碳剂选择合适可降低铸件生产成本。
2碳剂的使用在冶炼过程中,由于配料或装料不当以及脱碳过量等原因,有时造成钢中碳含量没有达到顶期的要求,这时要向钢液中增碳。
常用的增碳剂有增碳生铁、电极粉、石油焦粉、木炭粉和焦炭粉。
转炉冶炼中、高碳钢种时,使用含杂质很少的石油焦作为增碳剂。
对顶吹转炉炼钢用增碳剂的要求是固定碳要高,灰分、挥发分和硫、磷、氮等杂质含量要低,且干燥、干净、粒度适中。
其固定碳组分为:w(C)>96%,挥发分≤1.0%,w(S)≤0.5%,w(水分)≤0.55%,粒度为1一5mm.粒度太细容易烧损,太粗加入后浮在钢液表面,不容易被钢水吸收。
针对感应电炉的颗粒度在0.2-6mm,其中钢和其他黑色金属颗粒度在1.4-9.5mm,高碳钢要求低氮,颗粒度在 0.5-5mm,等等具体需要根据具体的炉型冶炼工件的种类等等细节具体判断和选用。
增炭剂生产工艺
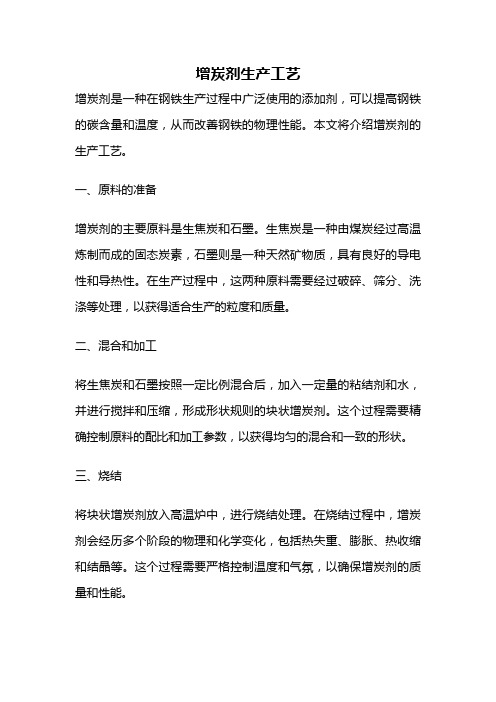
增炭剂生产工艺
增炭剂是一种在钢铁生产过程中广泛使用的添加剂,可以提高钢铁的碳含量和温度,从而改善钢铁的物理性能。
本文将介绍增炭剂的生产工艺。
一、原料的准备
增炭剂的主要原料是生焦炭和石墨。
生焦炭是一种由煤炭经过高温炼制而成的固态炭素,石墨则是一种天然矿物质,具有良好的导电性和导热性。
在生产过程中,这两种原料需要经过破碎、筛分、洗涤等处理,以获得适合生产的粒度和质量。
二、混合和加工
将生焦炭和石墨按照一定比例混合后,加入一定量的粘结剂和水,并进行搅拌和压缩,形成形状规则的块状增炭剂。
这个过程需要精确控制原料的配比和加工参数,以获得均匀的混合和一致的形状。
三、烧结
将块状增炭剂放入高温炉中,进行烧结处理。
在烧结过程中,增炭剂会经历多个阶段的物理和化学变化,包括热失重、膨胀、热收缩和结晶等。
这个过程需要严格控制温度和气氛,以确保增炭剂的质量和性能。
四、包装和存储
经过烧结处理后,增炭剂需要进行包装和存储。
一般采用塑料袋或纸箱包装,并在包装上标注产品名称、规格、生产日期等信息。
在存储过程中,增炭剂需要放置在干燥、通风、无阳光直射的地方,以避免吸湿和氧化。
增炭剂的生产工艺需要精确控制各个环节,从原料准备到烧结处理,再到包装和存储,都需要严格按照工艺要求进行。
只有这样,才能生产出质量稳定、性能优良的增炭剂产品,为钢铁生产提供可靠的支持。
石墨化增碳剂生产工艺
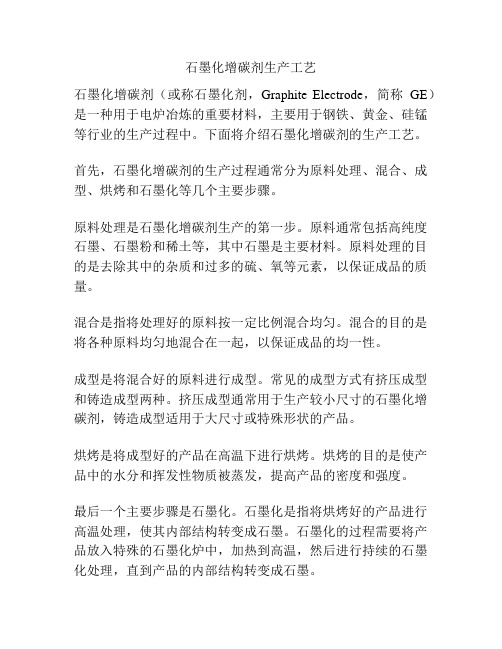
石墨化增碳剂生产工艺石墨化增碳剂(或称石墨化剂,Graphite Electrode,简称GE)是一种用于电炉冶炼的重要材料,主要用于钢铁、黄金、硅锰等行业的生产过程中。
下面将介绍石墨化增碳剂的生产工艺。
首先,石墨化增碳剂的生产过程通常分为原料处理、混合、成型、烘烤和石墨化等几个主要步骤。
原料处理是石墨化增碳剂生产的第一步。
原料通常包括高纯度石墨、石墨粉和稀土等,其中石墨是主要材料。
原料处理的目的是去除其中的杂质和过多的硫、氧等元素,以保证成品的质量。
混合是指将处理好的原料按一定比例混合均匀。
混合的目的是将各种原料均匀地混合在一起,以保证成品的均一性。
成型是将混合好的原料进行成型。
常见的成型方式有挤压成型和铸造成型两种。
挤压成型通常用于生产较小尺寸的石墨化增碳剂,铸造成型适用于大尺寸或特殊形状的产品。
烘烤是将成型好的产品在高温下进行烘烤。
烘烤的目的是使产品中的水分和挥发性物质被蒸发,提高产品的密度和强度。
最后一个主要步骤是石墨化。
石墨化是指将烘烤好的产品进行高温处理,使其内部结构转变成石墨。
石墨化的过程需要将产品放入特殊的石墨化炉中,加热到高温,然后进行持续的石墨化处理,直到产品的内部结构转变成石墨。
整个生产过程中,需要严格控制每个步骤的工艺参数。
如在烘烤过程中,需要控制温度和时间,以保证产品的质量和性能。
同时,生产过程中还需要进行质量检验,以确保产品符合相关的标准要求。
总结来说,石墨化增碳剂的生产工艺包括原料处理、混合、成型、烘烤和石墨化等步骤。
通过严格控制每个步骤的工艺参数和进行质量检验,可以生产出符合要求的石墨化增碳剂产品。
这些产品在电炉冶炼过程中起着重要的作用,推动了相关行业的发展。
增碳剂

增碳剂增碳剂分炼钢用增碳剂(中华人民共和国黑色冶金行业标准,YB/T 192-2001炼钢用增碳剂)和铸铁用增碳剂,以及其他一些添加材料也有用到增碳剂,譬如刹车片用添加剂,作摩擦材料。
增碳剂属于外加炼钢、炼铁增碳原料。
优质增碳剂是生产优质钢材必不可少的辅助添加剂。
增碳剂的原料有很多种,生产工艺也各异,有木质碳类,煤质碳类,焦炭类,石墨类等,其中各种分类下又有很多小种类。
优质增碳剂一般指经过石墨化的增碳剂,在高温条件下,碳原子的排列呈石墨的微观形态,所以称之为石墨化。
石墨化可以降低增碳剂中杂质的含量,提高增碳剂的碳含量,降低硫含量。
增碳剂在铸造时使用,可大幅度增加废钢用量,减少生铁用量或不用生铁。
目前绝大多数增碳剂都适用于电炉熔炼,也有少部分吸收速度特别快的增碳剂用于冲天炉。
电炉熔炼的投料方式,应将增碳剂随废钢等炉料一起往里投放,小剂量的添加可以选择加在铁水表面。
但是要避免大批量往铁水里投料,以防止氧化过多而出现增碳效果不明显和铸件碳含量不够的情况。
增碳剂的加入量,根据其他原材料的配比和含碳量来定。
不同种类的铸铁,根据需要选择不同型号的增碳剂。
增碳剂特点本身选择纯净的含碳石墨化物质,降低生铁里过多的杂质,增碳剂选择合适可降低铸件生产成本随着冶金技术的不断进步,为了适应强化冶炼、优质高效的炼钢技术的要求,在钢包内使用增碳剂作为一种补充手段已被普遍采用。
我厂研制开发的钢水增碳剂具有固定碳含量高,硫磷含量低增碳效果稳定,收得率高等优点,在使用时烟尘较小,不污染生产环境。
是钢水增碳的理想材料。
1、技术指标:成分C% S% 挥发物灰分%指标≥95≤0.5≤0.1≤22、产品特点:固定碳含量高,硫分低,增碳效果稳定,碳的收率高。
3、适用范围:用于各种电炉熔炼铸钢、铸铁的增碳。
4、粒度:常用粒度:0-10mm,或按用户特殊要求供货。
5、使用方法:1)配料时调整碳分,根据含碳量的要求熔化钢(铁)水时,随金属炉料加入电炉中部偏下部位,碳的收率可达90%-95%,增碳剂猛药熔化时不要打渣,否则易裹在非废渣里面,影响碳的收;2)钢(铁)水熔化后,调整碳分,可以加在钢(铁)水表面,通过电炉熔炼时钢(铁)水的涡流搅拌或人工搅拌使碳溶解收,碳的收率在85%左右。
石墨化石油焦增碳剂的生产流程

石墨化石油焦增碳剂的生产流程石墨化石油焦增碳剂是一种用于增碳和改善石墨质能力的关键原料。
它通过一系列的生产流程制备而成。
本文将介绍石墨化石油焦增碳剂的生产流程。
生产石墨化石油焦增碳剂的第一步是石油焦的制备。
石油焦是一种具有高固定碳含量和低杂质含量的石墨质材料。
它是从石油煤焦化过程中生成的副产品。
在焦化过程中,石油原料被加热至高温,使其发生裂解和重组,产生石油焦。
石油焦具有良好的石墨化能力和导电性能,是制备石墨化石油焦增碳剂的理想原料。
第二步是石墨化处理。
石墨化处理是通过对石油焦进行高温处理,使其结构发生变化,增加其石墨化程度。
这一步骤通常在电阻炉中进行,石油焦被置于高温环境中,在缺氧条件下进行热处理。
在高温下,石油焦中的非石墨化碳被热解,石墨化程度得以提高。
通过控制石墨化处理的温度和时间,可以调整石墨化石油焦增碳剂的石墨化程度和导电性能。
第三步是增碳处理。
在这一步骤中,石墨化石油焦增碳剂被与其它原料混合,并进行再次加热处理。
这一步骤的目的是将石墨化石油焦增碳剂中的石墨化碳与其它原料中的非石墨化碳结合,增加石墨化石油焦增碳剂的总碳含量。
增碳处理通常在高温环境下进行,原料与石墨化石油焦增碳剂混合后,经过加热处理,使其结合成为一体。
第四步是粉碎和筛分。
在增碳处理后,石墨化石油焦增碳剂需要经过粉碎和筛分的过程,以获得所需的粒度和均匀度。
粉碎通常使用破碎机进行,将增碳剂块状物料破碎成细粉末。
然后,通过筛分设备,将粉末按照所需的粒度进行筛分,以得到符合要求的产品。
最后一步是包装和贮存。
石墨化石油焦增碳剂经过粉碎和筛分后,需要进行包装和贮存。
一般情况下,石墨化石油焦增碳剂被装入塑料袋或大型容器中,并进行密封,以防止湿气和杂质的侵入。
然后,将包装好的产品存放在干燥的仓库中,以确保其质量和性能不受影响。
石墨化石油焦增碳剂的生产流程包括石油焦的制备、石墨化处理、增碳处理、粉碎和筛分以及包装和贮存等多个步骤。
每个步骤的控制和操作都对最终产品的质量和性能具有重要影响。
一种重利用废石墨电极的多孔高效增碳剂及其制备方法[发明专利]
![一种重利用废石墨电极的多孔高效增碳剂及其制备方法[发明专利]](https://img.taocdn.com/s3/m/2e016b34e97101f69e3143323968011ca300f729.png)
(10)申请公布号(43)申请公布日 (21)申请号 201510288085.2(22)申请日 2015.06.01C21C 7/00(2006.01)(71)申请人铜陵市明诚铸造有限责任公司地址247127 安徽省铜陵市郊区铜山镇竹园新村(72)发明人张蔓青 肖颖(74)专利代理机构安徽合肥华信知识产权代理有限公司 34112代理人方峥(54)发明名称一种重利用废石墨电极的多孔高效增碳剂及其制备方法(57)摘要本发明涉及增碳剂领域,具体涉及一种重利用废石墨电极的多孔高效增碳剂及其制备方法,该增碳剂以废石墨电极作为碳材料,以水玻璃、碳酸氢铵、聚乙二醇400等复合材料制备的粘结剂,这种粘结剂杂质含量低,高温烧制过程中能赋予材料多孔结构,添加的纳米碳管有增效引导作用,加速增碳过程,坯料表面喷涂的硅溶胶干燥后在材料表面粘附硅微粒,促进熔炼液石墨化进程,提高坯料流动性,提高利用率;本发明制备的增碳剂碳含量高,形态性能稳定,流动性好,熔入快,增碳快速,性价比高,有效的提高了金属制品的质量。
(51)Int.Cl.(19)中华人民共和国国家知识产权局(12)发明专利申请权利要求书1页 说明书2页(10)申请公布号CN 104962686 A (43)申请公布日2015.10.07C N 104962686A1.一种重利用废石墨电极的多孔高效增碳剂,其特征在于,该增碳剂由以下重量份的原料制成:废石墨电极50-60、纳米碳管0.8-1、水玻璃0.2-0.5、碳酸氢铵0.1-0.2、玉米秸秆灰0.2-0.3、多孔沸石1-1.5、聚乙二醇400 0.2-0.5、固含量为10-15%的硅溶胶适量、水10-20。
2.如权利要求1所述的一种重利用废石墨电极的多孔高效增碳剂及其制备方法,其特征在于,包含以下步骤:(1)先将废石墨电极投入0.1mol/L的稀盐酸溶液中浸泡30-50min,随后用清水清洗除去酸,再将电极投入5%的乙醇水溶液中,超声清洗5-6h,清洗结束后完全干燥,粉碎成粒径≤0.5mm的颗粒,所得材料备用;(2)将水玻璃、聚乙二醇400、碳酸氢铵投入水中,搅拌至物料完全溶解,随后再投入玉米秸秆灰,高速搅拌混合40-50min,得粘结剂备用;(3)将步骤(1)所得的材料与步骤(2)所得的粘结剂及除硅溶胶外的其它剩余物料混合,高速搅拌均匀后用压球机压坯成型,坯体的粒径为10-20mm,长度为1-5cm,随后将坯体在180-200℃下干燥3-4h,待坯料冷却至70-80℃时,称取与坯料质量比为0.1:1的硅溶胶,将其均匀喷涂在坯料表面,喷涂完毕后恒温放置2-3h,随后自然冷却至室温,即得成品。
石墨化石油焦
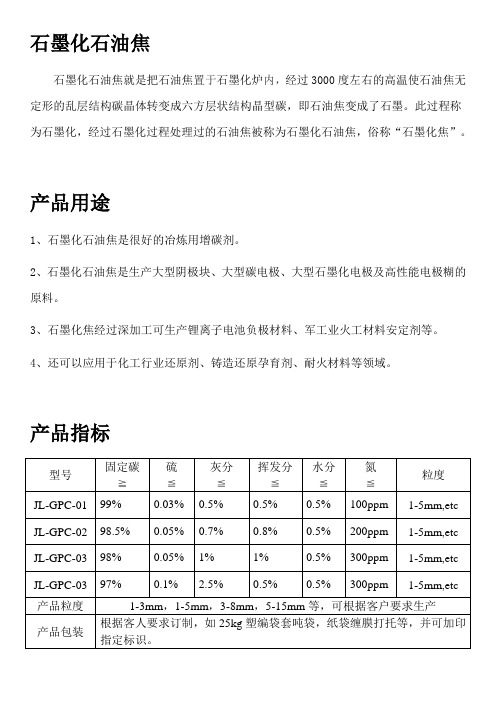
石墨化石油焦
石墨化石油焦就是把石油焦置于石墨化炉内,经过3000度左右的高温使石油焦无定形的乱层结构碳晶体转变成六方层状结构晶型碳,即石油焦变成了石墨。
此过程称为石墨化,经过石墨化过程处理过的石油焦被称为石墨化石油焦,俗称“石墨化焦”。
产品用途
1、石墨化石油焦是很好的冶炼用增碳剂。
2、石墨化石油焦是生产大型阴极块、大型碳电极、大型石墨化电极及高性能电极糊的原料。
3、石墨化焦经过深加工可生产锂离子电池负极材料、军工业火工材料安定剂等。
4、还可以应用于化工行业还原剂、铸造还原孕育剂、耐火材料等领域。
产品指标。
增碳剂的使用方法

增碳剂的使用方法1、炉内投入法:适于在感应炉中熔炼使用,但依据工艺要求具体使用也不尽相同;1在中频电炉熔炼中使用增碳剂,可按配比或碳当量要求随料加入电炉中下部位,回收率可达95%以上;2铁液熔清如果碳量不足调整碳分时,先打净炉中熔渣,再加增碳剂,通过铁液升温,电磁搅拌或人工搅拌使碳溶解吸收,回收率可在90左右,如果采用低温增碳工艺,即炉料只熔化一部分,熔化的铁液温度较低的情况下,全部增碳剂一次性加入铁液中,同时用固体炉料将其压入铁液中不让其露出铁液表面;这种方法铁液增碳可达1.0%以上;2、炉外增碳:1包内喷石墨粉选用石墨粉做增碳剂,吹入量为40kg/t,预期能使铁液含碳量从2%增到3%;随着铁液碳含量逐渐升高,碳量利用率下降,增碳前铁液温度1600℃,增碳后平均为1299℃;喷石墨粉增碳,一般采用氮气做载体,但在工业生产条件下,用压缩空气更方便,而且压缩空气中的氧燃烧产生CO,化学反应热可补偿部分温降,而且CO的还原气氛利于改善增碳效果;2出铁时使用增碳剂可将100—300目的石墨粉增碳剂放到包内,或从出铁槽随流冲入,出完铁液后充分搅拌,尽可能使碳溶解吸收,碳的回收率在50%左右;生产的无烟煤增碳剂具有低硫、低灰,含炭量高易吸收等特点;一、增碳剂的加入时间不能忽视;增碳剂的加入时间若过早,容易使其附着在炉底附近,而且附着炉壁的增碳剂又不易被熔入铁液;与之相反,加入时间过迟,则失去了增碳的时机,造成熔炼、升温时间的迟缓;这不仅延迟了化学成分分析和调整的时间,也有可能带来由于过度升温而造成的危害;因此,增碳剂还是在加入金属炉料的过程中一点一点地加入为好;如在一次加入量过大的情况下,可以结合感应电炉时采用的铁液过热操作结合考虑,保证增碳剂在铁液中的吸收时间10Min,一方面通过电磁搅拌作用使增碳剂充分扩散吸收,保证吸收效果;另一方面可以减少增碳剂中带入的含氮量;二、加入方法上改进不要一次加入,分批加,最后熔化了加一部分,放一部分一包左右铁水到包里,再回冲炉里增碳剂1-2次,然后打渣,加合金;有以下几个方面需要注意的:1.增碳剂比较难吸收没有经过煅烧的2.增碳剂灰分多颗粒分布不均匀3.加入时间太晚4.加入方法不对,采用分层加入;避免铁液镜面又太多渣的时候加入5.尽量别用太多铁锈的材料;三、影响增碳效果的因素1、粒度对吸收率的影响使用增碳剂的增碳过程包括溶解扩散过程和氧化损耗过程;增碳剂的粒度大小不同,溶解扩散速度和氧化损耗速度也就不同,而增碳剂吸收率的高低就取决于增碳剂溶解扩散速度和氧化损耗速度的综合作用;在一般情况下,增碳剂颗粒小,溶解速度快,损耗速度大;增碳剂颗粒大,溶解速度慢,损耗速度小;例如,在110kg高频感应炉中,粒度015~018mm的增碳剂溶解速度很快,在没来得及氧化损耗前大部分已溶解于铁液中,只有少部分损耗掉,因此吸收率高;在60kg感应炉中,炉膛的直径和容量较大,增碳剂粒度015~018mm,相对炉膛的直径和容量太小,损耗速度很快,吸收率低;而粒度116~312mm相对于炉膛直径和容量来说,增碳剂溶解速度较快,损耗速度较慢,溶解占据主导作用,吸收率高〔6〕;因此,增碳剂粒度大小的选择与炉膛直径和容量有关,一般情况下,炉膛的直径和容量大,增碳剂的粒度要大一些;反之,增碳剂的粒度要小一些;2、增碳剂加入量对吸收率的影响在一定的温度和化学成分相同的条件下,铁液中碳的饱和浓度一定;铸铁中碳的溶解极限为〔C%〕=113+010257T-0131〔Si%〕-0133〔P%〕-0145〔S%〕+01028〔Mn%〕T为铁液温度;在一定饱和度下,增碳剂加入量越多,溶解扩散所需时间就越长,相应损耗量就越大,吸收率就会降低;3、饱和浓度一定,温度对增碳剂吸收率的影响从动力学和热力学的观点分析,铁液的氧化性与C-Si-O系的平衡温度有关,即铁液中的O与C、Si 有如下的反应〔7〕:〔Si〕+2〔O〕=SiO2s,〔C〕+〔O〕=COg,SiO2s+2〔C〕=〔Si〕+2COg;ΔG0T=549359-309145T3lg〔Si〕〔C〕2=-27486T+151474平衡温度T随目标C、Si含量不同而变化,如式4所示;依式4可以计算出平衡温度;当铁液成分%为:219~311C、110~112Si时,平衡温度为1380℃左右;铁液在平衡温度以上时,优先发生碳的氧化,C和O生成CO和CO2;这样,铁液中的碳氧化损耗增加;因此,在平衡温度以上时,增碳剂吸收率降低;当增碳温度在平衡温度以下时,由于温度较低,碳的饱和溶解度降低,同时碳的溶解扩散速度下降,因而收得率也较低;因此,增碳温度在平衡温度时,增碳剂吸收率最高;但由于在实验室和生产过程中,铁液温度总会受到诸多因素的影响,所以,实际增碳温度在计算出的平衡温度上加减10℃左右波动;4、铁液搅拌对增碳剂吸收率的影响在增碳剂未完全溶解前,搅拌时间长,吸收率高;搅拌有利于碳的溶解和扩散,减少增碳剂浮在表面被烧损;搅拌还可以减少增碳保温时间,使生产周期缩短,避免铁液中合金元素烧损;但搅拌时间过长,不仅对炉子的使用寿命有很大影响,而且在增碳剂溶解后,搅拌会加剧铁液中碳的损耗;因此,适宜的铁液搅拌时间应以保证增碳剂完全溶解为适宜;5、铁液化学成分对增碳剂吸收率的影响初始碳量每增加0.1%,增碳剂吸收率大约降低1%~2%;硅量每增加0.11%,增碳剂吸收率大约降低3%~4%;硫量每增加0.1%,增碳剂吸收率大约降低1%~2%;锰量每增加0.1%,增碳剂吸收率大约提高2%~3%;由此可见,当铁液中初始碳含量高时,在一定的溶解极限下,增碳剂的吸收速度慢,吸收量少,烧损相对较多,增碳剂吸收率低;当铁液初始碳含量较低时,情况相反;另外,铁液中硅和硫阻碍碳的吸收,降低增碳剂的吸收率;而锰元素有助于碳的吸收,提高增碳剂吸收率;就影响程度而言,硅最大,锰次之,碳、硫影响较小;因此,在实际生产过程中,应先增锰,再增碳,最后增硅;6、增碳工艺对铸铁组织和性能的影响增碳工艺对铸铁组织的影响经过用增碳剂增碳处理后的铸铁,在铁液中生成了大量弥散分布的非均质结晶核心,降低了铁液的过冷度,促使生成以A型石墨为主的石墨组织;同时,由于生铁用量少,其遗传作用大为削弱,因此使A型石墨片分枝发达不易长大,使得石墨短小且均匀;1炉料要求:无油无锈,废钢要求表面不许有过度氧化现象;2一般按每加入100公斤废钢加入增碳剂4公斤准备;3出炉温度控制在1550℃,预计球化降温100℃,手包降温50℃;4第一炉生产时采取在电炉底加入10-20公斤优质铁削;第二炉起生产时采取上一炉剩余铁液20-40公斤;5铁削加入后用塑料口袋装入规定配入的增碳剂放入铁削上;第二炉起在剩余铁液20-40公斤上投入塑料口袋装得增碳剂投入铁液面;6加入碳素小颗粒小于50×50面积废钢50公斤,紧密覆盖整个炉塘;7启动熔化,加入剩余废钢→加配入生铁→加配入回炉铁注意回炉铁的表面粘砂不要过多防止增碳剂与砂粘合影响吸收;8铁液熔化完毕后用覆盖剂覆盖,温度达到1400℃时反复2-3次清理炉渣;9球化处理吊包装入球化剂、硅铁后用优质铁削覆盖表面;10熔炼完毕用优质除渣剂清理炉内液面溶渣2-3次,检测铁液温度1550℃-1600℃;11铁液出炉采用出铁三分之二铁液时,立即在炉嘴处顺流加入二次硅钡孕育剂;12用优质除渣剂清理溶渣;提出了当前对增碳剂的认识存在的误区,以及优质增碳剂的选择;把加增碳剂的熔炼新工艺与传统熔炼只加生铁工艺进行对比,分析了增碳剂对熔炼的影响,说明使用中应当注意的问题,阐明了增碳剂的正确使用方法;关键词:增碳剂;熔炼;一种含碳量很高的黑色或者灰色颗粒或块状的焦碳后续产物,加入到金属冶炼炉里,提高铁液里碳的含量,一方面可以降低铁液里氧的含量,另一方面更重要的是提高冶炼金属或者铸件的力学性能;增碳剂的来源很多,形态各异,根据其加工工艺和成分等不同,价格差异很大;传统的熔炼方式类似冲天炉熔炼:使用生铁、回炉料、废钢、铁合金等作为金属炉料;新的合成铸铁生产工艺:使用废钢作炉料,利用增碳剂来调整铁液的碳当量;后一种生产方式更容易保证优质铁液,同时通过少用或者取代生铁改用废钢大大降低成本;通俗的说,利用增碳剂,我们能用最差的废钢炼出最好的铸件;国外增碳技术已经日趋成熟,国内此项新工艺近几年才开始发展,业内很多人对增碳剂的品质和质量了解不够深入,有些铸造工作者选用增碳剂存在误区;例如混淆增碳剂的固定碳含量和含碳量的含义,固定碳值是根据样品的水分、挥发分、灰分、硫分计算得出的,而含碳量直接测碳仪便可以获得;有些增碳剂的灰分高,含碳量也高,但是它的固定碳值一定不会太理想;还有些铸造工作者片面的从增碳剂的固定碳含量和其物质性质便断定其是否优质,其结果很可能误入歧途,导致购入的增碳剂物不所值;一、增碳剂的选择及其指标性能在冶炼过程中,由于配料或装料不当以及脱碳过量等原因,有时造成钢或铁中碳含量没有达到预期的要求,这时要向钢或铁液中增碳;通常用来增碳的主要物质有无烟煤粉、增碳生铁、电极粉、石油焦粉、沥青焦、木炭粉和焦炭粉;对增碳剂的要求是,固定碳含量越高越好,灰分、挥发分及硫等有害杂质含量越低越好,以免污染钢;铸件的冶炼使用含杂志很少的石油焦经过高温培烧后的优质增碳剂,这是增碳工艺中最重要的环节;增碳剂质量好坏决定了铁液质量的好坏,也决定了能否获得好的石墨化效果;简言之,减少铁液收缩增碳剂起到举足轻重的作用;全废钢电炉熔炼时,优先选用经过了石墨化处理的增碳剂,经过高温石墨化处理的增碳剂,碳原子才能从原来的无序排列变成片状排列,片状石墨才能成为石墨形核的最好核心,以利促进石墨化;因此,我们应该要选用经气体过高温石墨化处理的增碳剂;因为高温石墨化处理时,硫分被生成SO2逸出而降低;所以高品质的增碳剂含硫分很低,ws一般小于0.05%,更好的ws甚至小于0.03%;同时,这也是判断是否经过高温石墨化处理以及石墨化是否良好的一个间接指标;如果选用的增碳剂没经过高温石墨化处理,石墨的形核能力就大大降低,石墨化能力减弱,即使也能达到同样的碳量,但结果完全不一样;所谓增碳剂,就是要在加入后可以有效提高铁液中碳的含量,所以增碳剂的固定碳含量一定不能太低,否则要达到一定的含碳量,就需要加入相比高碳的增碳剂更多的样品,这样无疑增加了增碳剂中其他不利元素的量,使铁液不能获得较好的收益;低的硫、氮、氢元素是防止铸件产生氮气孔的关键,这样就要求增碳剂的含氮量越低越好;增碳剂的其他指标,诸如水分、灰分、挥发分的量越低的固定碳量就越高,所以高的固定碳量,这些有害成分的含量一定不会高;针对不同的熔炼方式、炉型以及熔炼炉的尺寸,选择合适的增碳剂颗粒度也很重要,可以有效提高铁液对增碳剂的吸收速度和吸收率,避免因过小的颗粒度而引起的增碳剂氧化烧损;其粒度最好为:100kg炉小于10mm,500kg炉小于15mm,1.5吨炉小于20mm,20吨炉小于30mm;转炉冶炼中,高碳钢种时,使用含杂质很少的增碳剂;对顶吹转炉炼钢用增碳剂的要求是固定碳要高,灰分,挥发分和硫,磷,氮等杂质含量要低,且干燥,干净,粒度适中;其固定碳C≥96%,挥发分≤1.0%,S≤0.5%,水分≤0.5%,粒度在1-5mm;粒度太细容易烧损,太粗加入后浮在钢液表面,不容易被钢水吸收;针对感应电炉的颗粒度在0.2-6mm,其中钢和其他黑色金属颗粒度在1.4-9.5mm,高碳钢要求低氮,颗粒度在0.5-5mm,等等具体需要根据具体的炉型冶炼工件的种类等等细节具体判断和选用;二、加增碳剂熔炼新工艺对比传统工艺生铁中有许多粗大的过共晶石墨,这种粗大的石墨具有遗传性,熔炼温度低,粗大石墨不易被消除,粗大的石墨从液态遗传到了固态铸铁组织中,一方面降低铸铁所能达到的强度,降低了材料的性能,另一方面使凝固过程中本来应该产生的石墨化析出的膨胀作用削弱,使铁液凝固过程中的收缩倾向增大;在冲天炉熔炼时,尽量降低生铁炉料的用量,使用增碳剂来保证高碳当量,相对提高废钢用量;这样,在高温熔炼的条件下,可以渗碳方式获得活性好,石墨化作用更显着的碳;在铸件上反映出石墨的形态更好,从而有利于提高力学性能,减少收缩倾向,改善加工性能;电炉熔炼时,同样通过低生铁用量甚至零用量,以渗碳方式获得优质铁液;从材质性能上来说,过去那种大比例的生铁用量做法,与同样成分的高废钢用量相比,其力学性能也要低半个牌号;因此,加增碳剂熔炼的新工艺比传统上那种大比例的生铁用量相比无论从成本还是成品性能都要优越;三、增碳剂对熔炼的影响及使用同样的化学成分,采用不同的熔炼工艺、不同配料和配料比,铁液的冶金质量完全不同;获得好的渗碳效果,电炉采用的是增碳技术,冲天炉采用的是高温熔炼技术;增碳剂对熔炼的影响主要有三方面;1.铁液增碳技术,在熔炼过程中特别是电炉熔炼,可以增加石墨晶核;冲天炉熔炼中加入碳化硅还能增加铁液的长效石墨晶核,同时减少铁液氧化;2.增碳是防止或减轻收缩倾向最好的措施;由于铁液凝固过程中的具有石墨化膨胀的作用,因此良好的石墨化会减少铁液的收缩倾向;3.在高的碳量条件下,为获得高强度的灰铸铁铸件,熔炼过程采用全废钢加增碳剂的工艺,使铁液更加纯净,生产的铸件材料性能高;熔炼要用不含油污的干净料,避免产生漏电或浮渣过多的现象;某厂前几炉因使用了油浸废铁屑,使线圈出现电火花,曾认为是炉衬料含铁太高而产生漏电;其实是因为熔炼的铁屑含有油污,容易出现碳沉积;碳积沉部位是在炉衬冷面,甚至沉积到隔热层中,由于炉衬尚未充分烧结,CO渗入炉衬后部,发生CO→C+O2↑反应,生成C沉积在炉衬冷面或隔热材料的气孔中;当产生碳沉积时,会造成炉体接地漏电,造成线圈冒火花;改用纯净料即可避免;另外一个厂因为采购的废钢来源混乱,甚至表层涂附有油漆、石灰、煤等物质,造成浮渣多,在后期除渣工作消耗了大量的人力与物力; 一般认为,铁水温度越高,作用时间越长,碳的吸收率越高;但实际正好相反,在感应电炉内是低温增碳,高温增硅,即在高温时,非但不增碳,反而是降碳,这是因为:①石墨碳主要损失于向炉外大气的气相扩散;②铁水中的氧化性与C-Si-O的平衡有关,铁水中的CO不断地被氧化为CO2,而CO2又会被C还原,反应产生的CO,CO2气体上浮溢出铁水表面,使铁水中的碳含量下降;反应速度与平衡温度有关,而平衡温度又随着碳硅含量的不同而变化;对于球铁原铁水,平衡温度大约为1450℃±20℃,灰铁原铁水约为1400℃±20℃;铁水在平衡温度以上碳的氧化变得剧烈;反应的结果使铁水中的碳不断地被氧化烧损,硅的烧损减少;这时在铁水表面加入的增碳剂使铁水中的增碳和降碳达到平衡;根据以上分析,下面是增碳剂在感应电炉内增碳的正确使用方法:1.使用5T以上的电炉,原料单一稳定,我们推荐分散加入法;根据含碳量的要求,按配料比,将增碳剂与金属炉料随各批料一同加入电炉中下部位,一层金属炉料一层增碳剂,碳的吸收率可达90%-95%,增碳剂在熔化时不要打渣,否则易裹在废渣里,影响碳的吸收;2.使用3T左右中频感应电炉,原料单一稳定,我们推荐集中加入法;在炉内先熔化或剩余少量铁水时,将需配加的增碳剂一次性加在铁水表面,并立即加金属炉料,将增碳剂全部压入铁水中,使增碳剂与铁水充分接触,吸收率在90%以上;3.使用小型中频电炉,原料夹有生铁等高碳物质的,我们推荐增碳剂微调;钢/铁水熔化后,调整碳分,可以加在钢/铁水表面,通过电炉熔炼时钢铁水的涡流搅拌或人工搅拌使本产品溶解吸收,碳的吸收率在93%左右;四、优质增碳剂具备的特性1.颗粒大小适中,孔隙度大,吸收速度快;2.化学成分纯净,高碳、低硫、有害成分极微,吸收率高;3.产品石墨晶体结构好,提高原铁液的形核能力;在孕育中增加球墨铸铁的墨球数量,在电炉铁液中增加石墨晶核;细化、均匀化石墨在铸件中的分布;4.性能优异、稳定;选用合适的增碳剂有助于降低冶炼生产成本,提高冶炼金属及铸件的质量,让冶炼金属厂、铸造。
- 1、下载文档前请自行甄别文档内容的完整性,平台不提供额外的编辑、内容补充、找答案等附加服务。
- 2、"仅部分预览"的文档,不可在线预览部分如存在完整性等问题,可反馈申请退款(可完整预览的文档不适用该条件!)。
- 3、如文档侵犯您的权益,请联系客服反馈,我们会尽快为您处理(人工客服工作时间:9:00-18:30)。
产品:石墨化增碳剂
成分含量:
固定碳:≥%
灰分:≤%
挥发分:≤%
硫:≤%
水分:≤%
氮:≤%(300ppm)
生产不同粒度:
1mm-5mm
5mm-8mm
不同粒度报价不一样,可根据客户要求定制粒度
我们工厂采用的是艾奇逊卧式炉锻造,月产量在4000-5000吨针对的客户:
钢铁冶炼厂,铸造厂,贸易中间商
产品特点:
高固定碳,吸收率高,低硫低氮,并在吸收速度上快于同类石墨化增碳剂,且不吸附炉壁,完全吸收无残留,价格低于同类硫低于以下的石墨化增碳剂,性价比高。
吸收率高,根据使用方法吸收率最高能达到90%以上.
吸收速度快,比同类石墨化增碳剂吸收速度快,不吸附炉壁,且无残留,炉中增碳吸收速度优势更加明显.
硫份低,%以下
超高的性价比,综述上述在同类石墨化增碳剂中(硫≤)价格最优优势。
效益影响:
石墨增碳剂为您降低成本,提高产品质量。
原材料可增加废钢用量,减少生铁用量或不用生铁,有效避免生铁的遗传性对铸件的影响。
含硫低,稳定可靠,有效节约硫在球化和孕育过程中对合金的不利影响,节省合金费用。
由于熔点低,吸收快,不反渣,可以有效保护和延长炉龄,减少炉衬消耗
化学成分纯净:高碳、低硫、微氮,有害杂质少
物理形态:外观洁净、无杂质,多孔隙结构,吸收速度快,吸收率高
微观形态:晶体度质量优,有效提升铸件铸铁牌号和性能
产品性质稳定:增碳效果稳定,吸收效果好,提温效果明显,
不返渣
包装:
25千克/袋,编织袋(内里防水膜),可提供吨袋
如需要特殊包装方式等,请致电
贮存
产品应存放在清洁、干燥的库房内,防止受潮和玷污及踩踏。