瑞士布勒冷室压铸机
真空压铸工艺
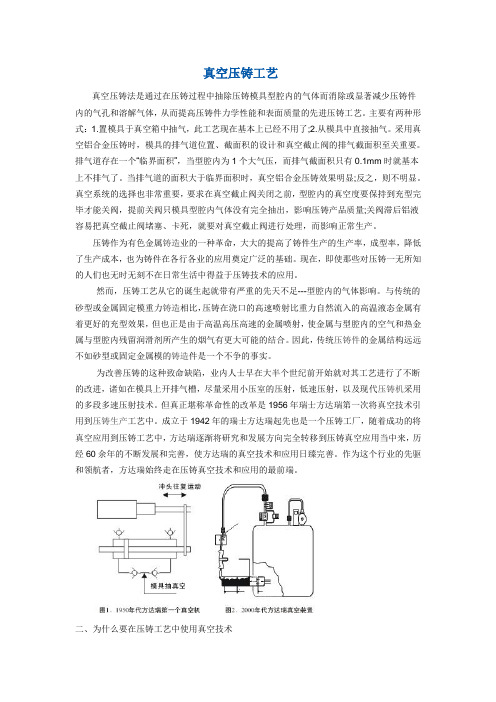
真空压铸工艺真空压铸法是通过在压铸过程中抽除压铸模具型腔内的气体而消除或显著减少压铸件内的气孔和溶解气体,从而提高压铸件力学性能和表面质量的先进压铸工艺。
主要有两种形式:1.置模具于真空箱中抽气,此工艺现在基本上已经不用了;2.从模具中直接抽气。
采用真空铝合金压铸时,模具的排气道位置、截面积的设计和真空截止阀的排气截面积至关重要。
排气道存在一个“临界面积”,当型腔内为1个大气压,而排气截面积只有0.1mm时就基本上不排气了。
当排气道的面积大于临界面积时,真空铝合金压铸效果明显;反之,则不明显。
真空系统的选择也非常重要,要求在真空截止阀关闭之前,型腔内的真空度要保持到充型完毕才能关阀,提前关阀只模具型腔内气体没有完全抽出,影响压铸产品质量;关阀滞后铝液容易把真空截止阀堵塞、卡死,就要对真空截止阀进行处理,而影响正常生产。
压铸作为有色金属铸造业的一种革命,大大的提高了铸件生产的生产率,成型率,降低了生产成本,也为铸件在各行各业的应用奠定广泛的基础。
现在,即使那些对压铸一无所知的人们也无时无刻不在日常生活中得益于压铸技术的应用。
然而,压铸工艺从它的诞生起就带有严重的先天不足---型腔内的气体影响。
与传统的砂型或金属固定模重力铸造相比,压铸在浇口的高速喷射比重力自然流入的高温液态金属有着更好的充型效果,但也正是由于高温高压高速的金属喷射,使金属与型腔内的空气和热金属与型腔内残留润滑剂所产生的烟气有更大可能的结合。
因此,传统压铸件的金属结构远远不如砂型或固定金属模的铸造件是一个不争的事实。
为改善压铸的这种致命缺陷,业内人士早在大半个世纪前开始就对其工艺进行了不断的改进,诸如在模具上开排气槽,尽量采用小压室的压射,低速压射,以及现代压铸机采用的多段多速压射技术。
但真正堪称革命性的改革是1956年瑞士方达瑞第一次将真空技术引用到压铸生产工艺中。
成立于1942年的瑞士方达瑞起先也是一个压铸工厂,随着成功的将真空应用到压铸工艺中,方达瑞逐渐将研究和发展方向完全转移到压铸真空应用当中来,历经60余年的不断发展和完善,使方达瑞的真空技术和应用日臻完善。
冷室压铸机技术教程(力劲版)

***冷室压铸机技术教程(力劲版)第一章卧式冷室压铸机的构成与工作原理压力铸造(简称压铸)是将熔化的金属,在高压作用下,以高速填充至型(模)具型腔内,并使金属在此压力下凝固而形成铸件的一种方法。
高压、高速是压铸法与其他铸造方法的根本区别,也是最重要的特点。
压力铸造是所有铸造方法中生产速度最快的一种方法,填充初始速度在0.5~70m/s 范围,生产效率高。
用压铸机能压铸出从简单到相当复杂的各种铸件,压铸件重量可从几克到几十千克不等,并能实现压铸生产的机械化和自动化,压铸产品广泛应用于汽车、航空航天、电讯器材、医疗器械、电气仪表、日用五金等,如图1-1所示为压力铸造工程示意图。
图1-1压力铸造工程示意图压铸机分为热室压铸机和冷室压铸机两大类。
热室压铸机与坩埚连成一体,其压室浸于金属熔液中,压射部件安装在熔炉坩埚的上面;冷室压铸机的压室与坩埚是分开的,压铸时,从熔炉的坩埚或保温炉中取出液体金属浇入压室后进行压铸,冷室压铸机适应于压铸各种有色合金和黑色金属。
用压铸机压铸具有如下工作特点:1)操作工序简单,生产效率高,容易实现自动化。
2)压铸可以代替部分装配,且原材料消耗少,能节省装配工时。
3)卧式冷室压铸机一般设有偏心和中心两种浇注位置,可供压铸型(模)设计时选用。
4)金属液在浇道中流动时转折少,有利于发挥增压的作用,提高压铸件质量。
5)压铸件力学性能好,以铝合金、镁合金为例(见表1-1)说明。
6)互换性好,便于维修。
7)压铸产品轮廓清晰,压铸薄壁、复杂零件以及花纹、图案、文字等,能获得很高的清晰度。
8)压铸设备投资高,一般不宜于小批量生产。
表1-1铝合金、镁合金不同铸造方法力学性能注:①W Cu 、W Al 分别表示Cu 、Al 的质量分数。
如图1-2所示为全自动镁合金卧式冷室压铸机在压铸生产时其设备配备图,其中压铸机是压铸生产的主导设备,其他各设备也都起着不可缺少的作用图1-2是力劲机械厂有限公司生产的全自动化镁合金卧式冷室压铸机压铸生产时其设备配备图图1-2压力生产设备图1--定量输送泵2--压铸机3--型(模)具加热器4--喷涂装置5--取件机械手6--熔化炉7--预热炉8--边角料传送带9--压边机10--压铸件传送带11--废品传送带第一节卧式冷室压铸机压铸原理如图1-3所示,压铸型(模)合型(模)后,金属液3浇入压室2中,压射冲头1向前推进,将金属液经浇道7压入型腔6中,冷却凝固成型。
真空压铸工艺
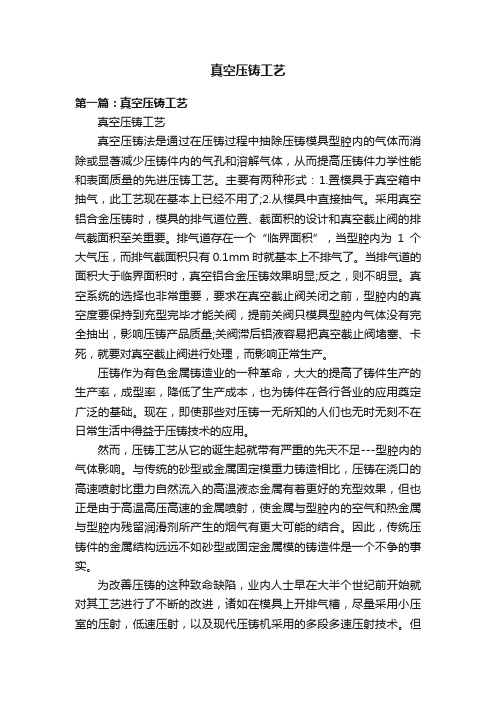
真空压铸工艺第一篇:真空压铸工艺真空压铸工艺真空压铸法是通过在压铸过程中抽除压铸模具型腔内的气体而消除或显著减少压铸件内的气孔和溶解气体,从而提高压铸件力学性能和表面质量的先进压铸工艺。
主要有两种形式:1.置模具于真空箱中抽气,此工艺现在基本上已经不用了;2.从模具中直接抽气。
采用真空铝合金压铸时,模具的排气道位置、截面积的设计和真空截止阀的排气截面积至关重要。
排气道存在一个“临界面积”,当型腔内为1个大气压,而排气截面积只有0.1mm时就基本上不排气了。
当排气道的面积大于临界面积时,真空铝合金压铸效果明显;反之,则不明显。
真空系统的选择也非常重要,要求在真空截止阀关闭之前,型腔内的真空度要保持到充型完毕才能关阀,提前关阀只模具型腔内气体没有完全抽出,影响压铸产品质量;关阀滞后铝液容易把真空截止阀堵塞、卡死,就要对真空截止阀进行处理,而影响正常生产。
压铸作为有色金属铸造业的一种革命,大大的提高了铸件生产的生产率,成型率,降低了生产成本,也为铸件在各行各业的应用奠定广泛的基础。
现在,即使那些对压铸一无所知的人们也无时无刻不在日常生活中得益于压铸技术的应用。
然而,压铸工艺从它的诞生起就带有严重的先天不足---型腔内的气体影响。
与传统的砂型或金属固定模重力铸造相比,压铸在浇口的高速喷射比重力自然流入的高温液态金属有着更好的充型效果,但也正是由于高温高压高速的金属喷射,使金属与型腔内的空气和热金属与型腔内残留润滑剂所产生的烟气有更大可能的结合。
因此,传统压铸件的金属结构远远不如砂型或固定金属模的铸造件是一个不争的事实。
为改善压铸的这种致命缺陷,业内人士早在大半个世纪前开始就对其工艺进行了不断的改进,诸如在模具上开排气槽,尽量采用小压室的压射,低速压射,以及现代压铸机采用的多段多速压射技术。
但真正堪称革命性的改革是1956年瑞士方达瑞第一次将真空技术引用到压铸生产工艺中。
成立于1942年的瑞士方达瑞起先也是一个压铸工厂,随着成功的将真空应用到压铸工艺中,方达瑞逐渐将研究和发展方向完全转移到压铸真空应用当中来,历经60余年的不断发展和完善,使方达瑞的真空技术和应用日臻完善。
尊敬的国内外压铸界同仁:

布勒设备工程(无锡)有限公司自1860年至今,瑞士布勒集团一直是全世界范围内高效生产系统和工程解决方案的技术合作伙伴,其广博的业务领域包括: 谷物加工、工程产品和金属压铸工业。
布勒提供的成套设备和综合性工程是其在开发、设计和工艺支持领域数十年专用技术的积累和结晶。
目前布勒集团在世界各地已经拥有40家分公司和80多个分支机构。
布勒设备工程(无锡)有限公司(简称中国布勒)是瑞士布勒控股股份有限公司于2002年初在中国成立的独资企业。
中国布勒作为布勒集团接近与服务于中国客户的直接窗口,协调布勒所有国产产品和进口产品在中国境内的销售和服务,并参与研发、测试、承接工程、制造和供应全套设备。
它下设北京、长春和深圳三个办事处,进一步贴近客户。
布勒压铸有限公司是经济的、非传统的、新型压铸技术的领跑者,致力于改善压铸质量,是一个全套系统的供应商-基于实时控制压铸机新技术的解决方案。
机器锁模力由260T到4200T。
布勒压铸有限公司在挑战新技术中积累的丰富经验确保项目的顺利运行。
主导世界的专家们帮助您解决以下工艺中遇到的问题:铝压铸、传统工艺、真空压铸工艺、挤压铸造,、半固态铸造/触变铸造和镁压铸。
2005年3月初布勒压铸有限公司生产基地于无锡正式成立,这将标志着布勒公司与中国压铸行业紧密合作的新篇章。
米勒万家顿(上海)有限公司米勒万家顿是德国的一家著名机械设备制造公司,于 1863年由米勒先生创建,1981年同万家顿公司合并,成为上市公司,并于2001年收购了德国埃尔福特成型技术公司,是目前世界上规模最大,技术最先进的成型设备制造公司。
现有员工人数 2500余,年销售额超过 4 亿欧元。
米勒公司制造的第一台压铸机是在 1923 年,世界上第一台压铸镁合金的冷室压铸机也出自米勒公司,公司最大压铸机的合模力达到 5500吨,堪称世界第一。
米勒公司的OptiCast 型冷室压铸机配备有独特的压射系统,能确保压铸机的压射速度最快,建压时间最短,是行业公认的名牌压铸机,广泛应用于汽车行业,是德国和欧洲压铸行业的首选设备。
冷室压铸机1000T主要技术参数表

锁模行程
模板尺寸
哥林柱间距内尺寸
哥林柱直径
压模厚度(最小最大)
kN
mm
mm
mm
mm
mm
1300
350
650×652
435×435
80
170-500
Injection Unit射料部分
Working Pressure
CastingForce
Intensifier
CastingStroke
PlungerTipPenetration
Tie Bar Dlameter
DIe Heigeht(Min/Max)
锁模力
锁模行程
模板尺寸
哥林柱间距内尺寸
哥林柱直径
压模厚度(最小最大)
kN
mm
mm
mm
mm
mm
10000
880
1620×1620
1030×1030
200
450-1150
Injection Unit射料部分
Working Pressure
CastingForce
Intensifier
CastingStroke
PlungerTipPenetration
ShotPosition
PlungerDiameter
ShotWeight
Foundry pressure
CastingArea
MaxCastArea(ASSUME PRESSURE400kg/sp.cm)
油箱容量
机身尺寸(连机械手)
出机重量(连机及机械手)
Litre
(lxWxh)m
kg
400
4300×1300×2500
第二节 卧式冷室压铸机的构成

第二节卧式冷室压铸机的构成,它由柱架、机架、压射、液压、电气、润滑、冷却、安全防护等部件组成。
按机器零、部件组成的功能分类,我们将卧式冷室压铸机分成合型(模)、80卧式冷室压铸机为例进行结构分析。
图1-5 卧式冷室压铸机构成图过滤器 4--冷却器 5--压射回油油箱 6--曲肘润滑油泵 7--主油箱 8--机架 9--电动机 10--电箱 11--合型(模)油路板组件 12--合开型(模)液压缸15--锁型(模)柱架 16--型(模)具冷却水观察窗 17--压射冲头 18--压射液压缸 19--快压射蓄能器20--增压蓄能器 21--增压油路板组件 22--压射油路板组件(模)动作和锁紧型(模)具、顶出产品的作用。
它主要由定型座板、动型座板、拉杠(哥林柱)、曲肘机构、顶出机构、调型(模)机构等组成。
图1图1-6 合模装置结构简图1--调型(模)液压马达 2--尾板 3--曲肘组件 4--顶出液压缸 5--动型座板 6--拉杆 7--定型座板 8--拉杠螺母9--拉杠压板 10--调型(模)大齿轮 11--动型座板滑脚 12--调节螺母压板 13--调节螺母 14--合开型(模)液压缸点以将合型(模)液压缸的推力放大16~26倍,与液压式合型装置相比,高压油消耗减小、合型液压缸直径减小、泵的功率相应减小。
如图1-7所示,在合型(模)运动过程中,动型座板移动速度由零很快升到最大值,以后又逐渐减慢,随着曲肘杆逐渐伸直至终止时,合型速度为零,机速转慢至零,非常符合机器整个运动设计要求。
图1-7 曲肘部分结构简图1--合开型(模)液压缸 2--钩铰 3--长铰 4--动型座板一直线时,机构处于自锁状态,此时,可以撤去合型(模)液压缸的推力,合型(模)系统仍然会处于合紧状态。
、速度、行程或位置,所涉及的几个概念解释如下。
板对型(模)具形成的锁紧力。
金液注入型(模)具型腔时,模板对型(模)具形成的最终锁紧力。
国内外挤压铸造技术发展概况

!E B ;7*
%/%2?2& ?/-
自行车受力件 曲柄, 方向轴, 车架接头。 其他
荷兰 78(+9: ;*9<(+: 等多家公司用满料筒挤压铸造 工艺, 为福特汽车公司开发生产了质量为 5& 34 的 ,%/& 铝合金的下曲轴箱, 为通用汽车公司生产了质量为 2 34 的 ,%-$ = >$ 铝合金的后上控制杆, 上述生产设备均为 合模力 5 1 / 万 3’ 的压铸机。国外用布勒公司压铸机设 备开发出的挤压铸造产品有: 滑轮、 皮带轮、 发动机支 架、 托架、 连杆、 雪车离合器等。 在我国大批量生产的品种主要是摩托车铝轮毂, 各 种汽车铝活塞, 摩托车前叉及刹车系统零件, 液压及气 压系统泵体, 阀体及其他耐压件, 压力锅及炊具, 压缩机 件, 自行车件, 光学镜架件, 以及铜轴套等。但我国由于 受到挤压铸造设备吨位及设备功能的限制, 使大型铸件 (%- 1 -$ 9@) 以上汽车 和某些形状复杂的铸件如 5? 英寸 铝轮、 汽车十字梁等的开发受到了制约, 与国外有一定 的差距。目前, 我国正开发的产品主要有汽车转向节、 空调压缩机涡旋盘, 以及小型发动机零件等。
综
述
特种铸造及有色合金
’""’年第’期
国内外挤压铸造技术发展概况
中国兵器工业第五二研究所宁波分所 摘 要 齐丕骧!
概述了近几年来国内外挤压铸造技术发展。重点评述了在挤压铸造设备、 挤压铸造产品以及在合金材料、 复合
材料、 半固态加工以及模具设计等方面的发展情况。
关键词:挤压铸造
中图分类号: !"#$% & #
第八届中国国际压铸展览会综述

铸机 ,其 压射 曲线 可多段设 置 ,合模 和压射独 立控制 ,
保证压射 的稳定性 ,同时有单槽 或双槽 炉供客户 选择 , 双 槽 炉 进 一 步 提 高 了 金 属 液 的 洁 净 度 ; 展 出 的 Q ai s6 0 u l at 4 冷室压铸 机结合 了原来米 勒万 家顿的压射 c
DC 0 JMX系列伺 服压铸 机 ,该机 在压 射 阶段 有 1 个 8 0— 0
废 气 过滤 系统 ,不但 可 以对单 一位置 压铸 机进 行除尘 过 滤 ,还 可 以对 整 个工 厂 抽 出废 气再 进 行 中央过 滤 , 过滤后 的洁净 空气 可达 到室 内排放标 准 ,所 以使其 回
具厚 度调 整方 便快捷 ,模 具不 平行 度及模 具热 膨胀 自
办 和承 办单 位 致 开幕 词 、德 国纽 伦 堡 会展 服 务 公 司 、
香港 压铸 及铸造业 总会 、欧洲镁 合金协 会 、力劲 ・ 上海
一
达机 械公 司代表 分别致辞 。 本届展 会 比历届 规模 都要 大 ,展 出总面积 达 到 了
DON G a mi LI Ho - h o , Xin— ng, U ng c a CAO n 2 Ya g
(. AW on r o, t. hn cu 3 0 2 Ji, h a 1F F u dyC . d, a gh 10 6 ,in C i ; L C n l n 2 S eyn sac stt f o n r, hn ag1 02 , i n g C ia . h n ag erhI tue F u dy S eyn 10 2 La i , h ) Re ni o on n
Ke r s dec s n c ie dec s n i; i at g e ii o ywo d : i at gma hn ; i at gde dec si ; x b t n i i n h i
Al_Si_Cu_Zn压铸铝合金的显微组织及拉伸性能
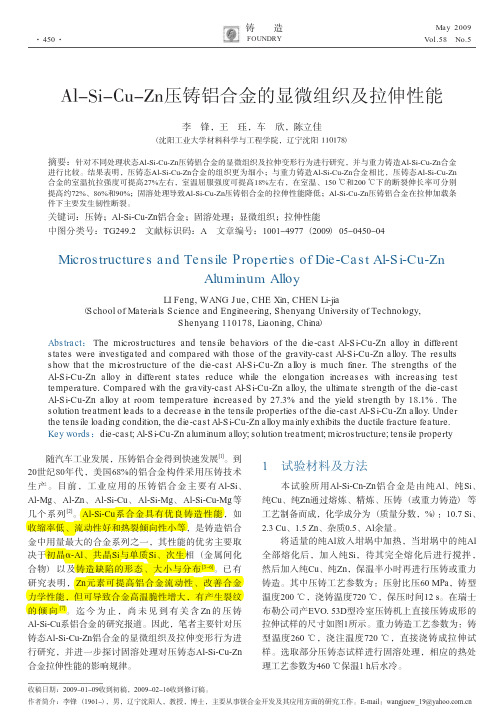
··随汽车工业发展,压铸铝合金得到快速发展[1]。
到20世纪80年代,美国68%的铝合金构件采用压铸技术生产。
目前,工业应用的压铸铝合金主要有Al-Si 、Al-Mg 、Al-Zn 、Al-Si-Cu 、Al-Si-Mg 、Al-Si-Cu-Mg 等几个系列[2]。
Al-Si-Cu 系合金具有优良铸造性能,如收缩率低、流动性好和热裂倾向性小等,是铸造铝合金中用量最大的合金系列之一,其性能的优劣主要取决于初晶α-Al 、共晶Si 与单质Si 、次生相(金属间化合物)以及铸造缺陷的形态、大小与分布[3-6]。
已有研究表明,Zn 元素可提高铝合金流动性、改善合金力学性能,但可导致合金高温脆性增大,有产生裂纹的倾向[7]。
迄今为止,尚未见到有关含Zn 的压铸Al-Si-Cu 系铝合金的研究报道。
因此,笔者主要针对压铸态Al-Si-Cu-Zn 铝合金的显微组织及拉伸变形行为进行研究,并进一步探讨固溶处理对压铸态Al-Si-Cu-Zn 合金拉伸性能的影响规律。
1试验材料及方法本试验所用Al-Si-Cn-Zn 铝合金是由纯Al 、纯Si 、纯Cu 、纯Zn 通过熔炼、精炼、压铸(或重力铸造)等工艺制备而成,化学成分为(质量分数,%):10.7Si 、2.3Cu 、1.5Zn 、杂质0.5、Al 余量。
将适量的纯Al 放入坩埚中加热,当坩埚中的纯Al 全部熔化后,加入纯Si ,待其完全熔化后进行搅拌,然后加入纯Cu 、纯Zn ,保温半小时再进行压铸或重力铸造。
其中压铸工艺参数为:压射比压60MPa ,铸型温度200℃,浇铸温度720℃,保压时间12s 。
在瑞士布勒公司产EVO.53D 型冷室压铸机上直接压铸成形的拉伸试样的尺寸如图1所示。
重力铸造工艺参数为:铸型温度260℃,浇注温度720℃,直接浇铸成拉伸试样。
选取部分压铸态试样进行固溶处理,相应的热处理工艺参数为460℃保温1h 后水冷。
压铸培训-压铸机结构及原理完美版资料

下面以力劲机械厂有限公司生产的DCC280卧式冷室压铸机为例,说明压射机构的工作原理. 增压油路板组件-- 21 压射机构是将金属液压入型(模)具型腔进行充填成形的机构。 下面以力劲机械厂有限公司生产的DCC280卧式冷室压铸机为例,说明压射机构的工作原理. 压射机构是将金属液压入型(模)具型腔进行充填成形的机构。 下面以力劲机械厂有限公司生产的DCC280卧式冷室压铸机为例,说明压射机构的工作原理. 合开模液压缸-- 12 增压蓄能器-- 20 它主要由压射液压缸组件、压射室(入料筒)、冲头(锤头)组件、快压射蓄能器组件、增压蓄能器组件组成,它的结构性能对压铸 过程中的铸造压力、压射速度、增压压力及时间等起着决定性作用,并直接影响铸件的轮廓尺寸、力学性能、表面质量和铸件的致密 性。 模具冷却水观察窗--16 C1、C2 压射腔 C3 增压腔 C4 回程腔 A1、A2、A3 通道 按机器零、部件组成的功能分类,我 C1、C2 压射腔 C3 增压腔 C4 回程腔 A1、A2、A3 通道 11--合模油路板组件 压铸合金选择要求不仅仅是物理性质和机械性质及化学成分,而且还有合金内在的特性以及他们对压铸生产的作用,可能的加工和最 终的表面处理 压射油路板组件-- 22
压射液压缸-- 18 快压射蓄能器-- 19
增压蓄能器-- 20 增压油路板组件-- 21 压射油路板组件-- 22
压射机构及工作原理 压射机构是将金属液压入型(模)具型腔进行充填成形的机构。它主要由压射液压缸组件、 压射室(入料筒)、冲头(锤头)组件、快压射蓄能器组件、增压蓄能器组件组成,它的 结构性能对压铸过程中的铸造压力、压射速度、增压压力及时间等起着决定性作用,并直 接影响铸件的轮廓尺寸、力学性能、表面质量和铸件的致密性。下面以力劲机械厂有限公 司生产的DCC280卧式冷室压铸机为例,说明压射机构的工作原理. 在整个压射运动过程中,慢速、快速及增压的快慢和时间长短都可以通过安装在油路集成 板上的控制油阀调节
2015年模压成型专用机械设备行业概况
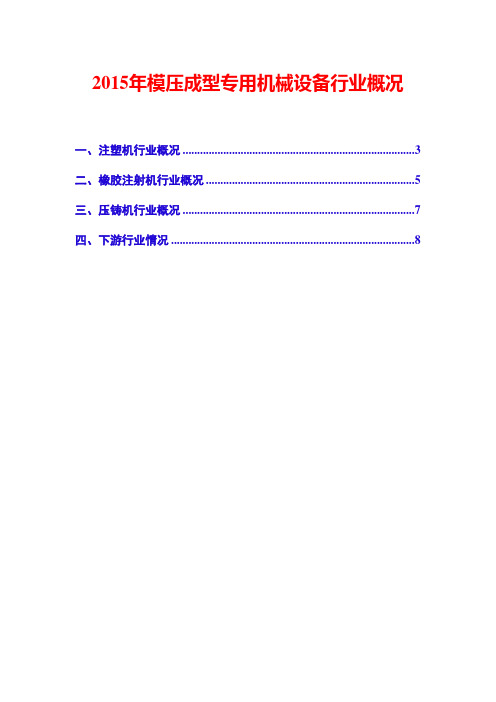
2015年模压成型专用机械设备行业概况
一、注塑机行业概况 (3)
二、橡胶注射机行业概况 (5)
三、压铸机行业概况 (7)
四、下游行业情况 (8)
模压成型装备,是指采用模压成型工艺,将高分子材料或轻合金材料成型为制品的装备,主要包括高分子材料模压注射成型设备、轻合金模压成型设备和橡胶平板硫化机等。
在结构上,模压成型装备由合模机构、注射机构、液压传动系统、电气控制系统、机架部件、安全门部件组成;在性能上,模压成型装备具备速度、压力、温度、位臵、时间等诸多变量的自动化控制,并具有网络管理、远程监控、多重安全监控及报警功能;在技术发展趋势上,模压成型装备的主要技术发展方向包括节能技术、高速高效生产技术、自动化技术和智能化、网络化控制技术。
装备制造业是为国民经济各行业提供技术装备的战略性产业,是各行业产业升级、技术进步的重要保障和国家综合实力的集中体现。
高端装备制造作为我国“十二五”期间重点扶持的战略性新兴产业,将推动中国从“制造大国”向“制造强国”的转型。
近年来,我国机械装备制造业规模发展迅速,已超过日本和美国,成为全球机械装备制造第一大国。
2013 年我国机械工业主营业务收入已达20.4 万亿元,同比增长13.8%,规模稳居世界第一。
在规模扩大的同时,我国重大技术装备自主化取得了较大突破,并向大型化、高参数化发展,部分产品的效率已接近世界先进水平,对国民经济各行业的保障能力明显增强。
模压成型装备作为机械装备。
国内压铸周边设备简介

第五届中国国际压铸展览会评述由中国机械工程学会、机械工业生产力促进中心主办,中国机械工程学会铸造分会、铸造行业生产力促进中心承办的第五届中国国际压铸展览会于2006年6月28日—7月1日在上海国际展览中心隆重举行。
本届国际压铸展览会内容十分丰富,展品面广,技术含量高,参展企业具有典型性和代表性。
来自中国、德国、瑞士、意大利、日本、韩国、西班牙、美国、加拿大、中国香港和中国台湾等11个国家和地区的150余家压铸供应商、采购商和压铸件生产商,在近10 000 m2展场上展出了当今世界一流的压铸工业的相关产品,展品涵盖压铸机、熔炼及保温炉、周边设备、模具及辅助设备、原辅材料、压铸件、检测设备、铸件清理设备等产品和技术,展览会还吸引了一些专业媒体和行业组织前来参展。
本届展览会吸引了大批海内外压铸界专业人士前来参观,在3天半的展期内,参观展览会的专业观众量超过5 000人次。
1 压铸机本届展览会中,压铸机展台大部分在展馆一楼,是整个展览会中展出规模最大、最受关注的部分,有28家国内外压铸机厂商参展,展出压铸机20余台。
这28家国内外压铸机展商基本代表了压铸机生产、销售的主流,也是在中国压铸市场上最活跃的部分。
展出的20台压铸机均是各厂商在中国市场的主推产品之一,它们既设计、制造精良,又各具特色。
由于压铸市场对优化压铸工艺及压铸生产过程的稳定性和高效率的需要,新型压铸机普遍采用了高性能压射系统和实时控制技术。
在新型压铸机中,可视化操作界面、PLC电控系统、电液比例及电液伺服控制、多点压射速度设置和过程监控等技术已成主流。
下面介绍压铸机参展商展出的主要压铸机及其主要技术特点。
德国富来公司在本届展会上展出了125 t的FCH 125M镁合金热室压铸机和220 t的FCC 200卧式冷室压铸机,两台压铸机均由富来(上海)压铸机有限公司组装生产。
富来(上海)压铸机有限公司作为德国富来集团的全资子公司,采用德国原厂零部件组装生产更适合中国用户的热室(FCH-Z系列)、冷室(FCC系列)及镁合金(FCH-M系列)压铸机,各压铸机性能与质量不变,但价格大幅度降低。
300C冷室压铸机说明书

LX300C冷室压铸机说明书300C 冷室压铸机安全事项一、防止电击1、整机必须接地良好;2、严禁简化安全保护装臵;3、漏电开关应该配臵合适的熔断器;4、经常检查主电源线的外壳是否损坏或破裂,如果有破损,必须立即更换;5、接通电源之前,所有的电箱及接线盒必须关闭;6、开机后禁止接触电器零件;7、维护和保养之前,必须断开总电源,在断开总电源之后,必须等待五分钟,让电容器放电,避免出现严重的电器危险事件。
二、防止烧伤1、穿防护服装,防护服应罩住身体的所有裸露部份,并应能防止火花及铁渣进入人体;2、按下燃烧机起动按钮时,严禁燃烧机喷火咀朝向自己或他人;3、避免加入有油、水的合金进入熔炉。
三、保持通风良好1、安装排气扇。
2、在熔炉上面加烟罩,把废气排出室外。
1目录第一章前言3第二章本机技术参数41、300T冷室压铸机技术参数表42、模板尺寸图5第三章本机器的用途和特点7第四章压铸机的安装和开机前准备81、安装前准备82、运输及安装步骤113、注意事项114、开机前的准备12第五章电气系统工作原理与功能说明131、电气系统工作特性142、LX280操作箱按钮功能说明153、主电箱内部电气元件说明16第六章安全防护、安全操作及维护171、安全防护装臵172、机器的安全操作173、机器安全操作注意事项184、定期维护195、定期检查事项20第七章冷室压铸机的调试方法22第八章冷室压铸机常见的故障及处理方法25第九章280T 抽芯使用说明262300C 冷室压铸机第一章前言感谢贵公司选购使用本公司冷室压铸机。
衷心希望本公司冷室压铸机为贵公司生产带来突飞猛进的发展。
当购买冷室压铸机后,请仔细阅读本说明书,它会使贵公司很快了解冷室压铸机的结构、性能,并掌握其操作调教,以便能迅速投产使用。
本公司冷室压铸机采用日本及德国先进液压元件,配有专为冷室压铸机设计的工业电脑,速度快、周期短、操作方便、性能稳定、安全可靠。
为了使贵公司在维护保养上的方便,说明书后面提供了维护保养和易损件等资料。
中国压铸业发展历程与进步
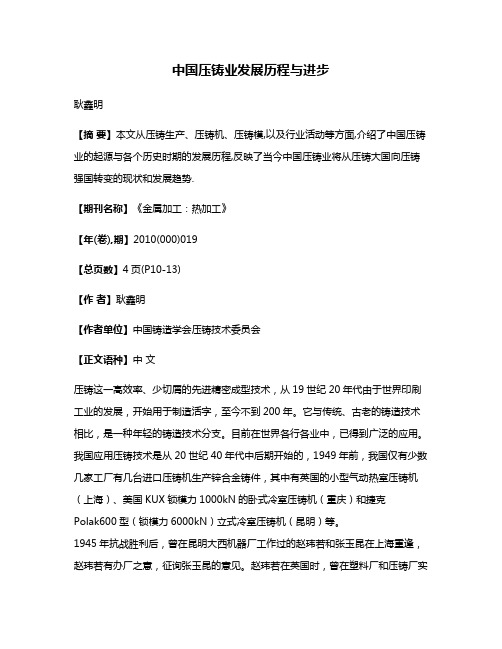
中国压铸业发展历程与进步耿鑫明【摘要】本文从压铸生产、压铸机、压铸模,以及行业活动等方面,介绍了中国压铸业的起源与各个历史时期的发展历程,反映了当今中国压铸业将从压铸大国向压铸强国转变的现状和发展趋势.【期刊名称】《金属加工:热加工》【年(卷),期】2010(000)019【总页数】4页(P10-13)【作者】耿鑫明【作者单位】中国铸造学会压铸技术委员会【正文语种】中文压铸这一高效率、少切屑的先进精密成型技术,从19世纪20年代由于世界印刷工业的发展,开始用于制造活字,至今不到200年。
它与传统、古老的铸造技术相比,是一种年轻的铸造技术分支。
目前在世界各行各业中,已得到广泛的应用。
我国应用压铸技术是从20世纪40年代中后期开始的,1949年前,我国仅有少数几家工厂有几台进口压铸机生产锌合金铸件,其中有英国的小型气动热室压铸机(上海)、美国KUX锁模力1000kN的卧式冷室压铸机(重庆)和捷克Polak600型(锁模力6000kN)立式冷室压铸机(昆明)等。
1945年抗战胜利后,曾在昆明大西机器厂工作过的赵玮若和张玉昆在上海重逢,赵玮若有办厂之意,征询张玉昆的意见。
赵玮若在英国时,曾在塑料厂和压铸厂实习过,两位老友商量究竟从何人手。
由于当时上海还没有压铸企业,最后商定,选择以办压铸厂作为发展方向。
那时,压铸技术资料奇缺,赵玮若手里只有一本刊物上的压铸机图片,是一台小型热室压铸机。
由于结构比较简单,就确定参照仿制。
这第一台热室压铸机,合模和压射全部手动。
坩埚熔化锌合金是采用火油喷灯加热。
场地是租借上海市江苏路久丰搪瓷厂的一间闲置厂房。
从图样设计、制造木模、铸件翻砂、机械加工、设备安装以及试模工作,都是在这间简陋的旧厂房中进行。
当时,选择国外压铸的锌合金锁具作为产品样品,全部仿制,只是商标改为“狗头牌”,并按此设计模具,由于缺乏经验,试摸数十次压不成型,后经改进模具内浇道,终于压铸成功。
1947年.在镇宁路华山路口选定厂址,修建厂房,添置刨床、车床等加工设备。
热室压铸机与冷室压铸机有的区别

压铸是在压铸机上进行的金属型压力铸造,是目前生产效率最高的铸造工艺。
压铸机分为热室压铸机和冷室压铸机两类。
热室压铸机自动化程度高,材料损耗少,生产效率比冷室压铸机更高,但受机件耐热能力的制约,目前还只能用于锌合金、镁合金等低熔点材料的铸件生产。
当今广泛使用的铝合金压铸件,由于熔点较高,只能在冷室压铸机上生产。
压铸的主要特点是金属液在高压、高速下充填型腔,并在高压下成形、凝固,压铸件的不足之处是:因为金属液在高压、高速下充填型腔的过程中,不可避免地把型腔中的空气夹裹在铸件内部,形成皮下气孔,所以铝合金压铸件不宜热处理,锌合金压铸件不宜表面喷塑(但可喷漆)。
否则,铸件内部气孔在作上述处理加热时,将遇热膨胀而致使铸件变形或鼓泡。
此外,压铸件的机械切削加工余量也应取得小一些,一般在0.5mm左右,既可减轻铸件重量、减少切削加工量以降低成本,又可避免穿透表面致密层,露出皮下气孔,造成工件报废。
压铸机一般分为热压室压铸机和冷压室压铸机两大类。
冷压室压铸机按其压室结构和布置方式分为卧式压铸机和立式压铸机(包括全立式压铸机)两种。
热压室压铸机(简称热空压铸机)压室浸在保温溶化坩埚的液态金属中,压射部件不直接与机座连接,而是装在坩埚上面。
这种压铸机的优点是生产工序简单,效率高;金属消耗少,工艺稳定。
但压室,压射冲头长期浸在液体金属中,影响使用寿命。
并易增加合金的含铁量。
热压室压铸机目前大多用于压铸锌合金等低熔点合金铸件,但也有用于压铸小型铝、镁合金压铸件。
冷室压铸机的压室与保温炉是分开的。
压铸时,从保温炉中取出液体金属浇入压室后进行压铸随着我国汽车、摩托车、家电等工业的迅速发展,工业产品的外形在满足性能要求的同时,变得越来越复杂,而这些产品的制造商不开模具,这就要求模具制造行业以最快的速度、最低的成本、最高的质量生产出模具。
- 1、下载文档前请自行甄别文档内容的完整性,平台不提供额外的编辑、内容补充、找答案等附加服务。
- 2、"仅部分预览"的文档,不可在线预览部分如存在完整性等问题,可反馈申请退款(可完整预览的文档不适用该条件!)。
- 3、如文档侵犯您的权益,请联系客服反馈,我们会尽快为您处理(人工客服工作时间:9:00-18:30)。
一种新型的锁模力为1100-1250t的冷室压铸机,通过长时间的生产考验后得到了开发。
该机在控制系统、调节系统以及监控系统等方面,皆达到了当代的各种要求。
—通过现代的计算机数控系统(CNC),将生产过程的控制系统及监控系统联成一体,以便高效率地生产出优质压铸件;—辅助时间短暂、生产节奏快;—高度稳定地生产及就绪进行生产;—容易操作;—拥有周密的人身保护和设备防护措施。
1合模系统的设计1 .1机械设计拥有安装在坚实机架上的、具有特色的、最大开模行程及较大模具开档的、液压驱动的曲肘系统。
对各铰结点、曲肘座板、拉杠以及动定模墙板等机器受力元件,均按最高强度进行设计,使机器达到高度的可靠性和长的使用寿命。
由于零件遭到破坏(如拉杠断裂)所造成的停机损失,事关重大,不可低估。
采用合适的防护罩,并且精心地设计关键的承载部位,可以有效地防护在恶劣的铸造环境中、使承载处避免遭受污染和锈蚀。
考虑到模具运动时所产生的速度和推力,对曲肘机构的几何尺寸,按最佳方案进行设计,动模安装板在开合时,其动作尤为快速、平稳。
所选择的思路,包括:模具高度调节机构、液压紧固拉杠,以及在定模安装板上液压驱动拉杠螺母、抽出或送进一根或两根上部拉杠等,皆按快速全自动化原则来进行设计。
考虑到抽出拉杠的方案是为了明显地减少模具的安装时间,到目前为止,也的确大大地节约了换模时间。
另一方面,不可低估的附带的好处是同时可以避免在拆卸和再紧固极为沉重的拉杠螺母时所存在的危险。
模具高度的快慢调整,取用两种速度,容许迅速、精确地调整模具高度。
对于大偏心的模具而言,有可能(在一定范围内)采用后部位的拉杠螺母,来个别地调整拉杠的予加载荷。
1.2安全多方面的安全装置,符合当代所制订的、严格的安全规范。
所要注意的一个现实情况,即在曲肘系统的危险工作范围内,都由顶部护板及两侧护门围护着,使在其周围进行确有实效的防护。
设在两侧的安全栅网,包括固定的和活动的两个部分组成。
活动安全栅网,确保完全贴近推出部位。
活动安全栅网,是借助一种特殊的电气一机械键盘所操纵的安全开关进行连锁;换言之,即除非机器停下,否则就无法打开此安全门。
模具范围内的防护,是通过两道侧面的安全门。
气动安全门控制系统,可使安全门快速移动。
特别是当安全断路杆受到推动时,即可迅速完成安全门的关闭动作。
当模具采用抽芯油缸时,必然突出在外部,但是安全门仍在周围移动。
此外,上部安全门的导杆可以快速抽出,以便更换模具。
采用可以相互监控的限位开关,以校正安全门的位置。
2液压系统机器液压系统的特点是设计简单明了,而且易于维修,具备了高度的可靠性。
设计时己考虑采用不燃液压油HFC:PIHFD进行运转。
2. 1油箱油箱与机器底板分开安装。
为了排除振动与噪声,油箱承托在橡皮底座上。
有鉴于此,油箱是可以移动的。
为了液压油的稳定,要求有长的回油管路。
油箱内装有导向板隔板,还带有较大横截面积的、处于下部位置的吸油管滤油器和低压检测系统,以对泵的吸油腔室,起到保护作用。
油箱是根据德意志联邦共和国铸造专家协会(VDG)所发表的6322所规定的指标进行设计。
2.2泵组:压力和流量的控制系统液压系统的心脏部分,包括一对安装在两个侧面上的驱动系统。
每台驱动系统,皆配备有一对内啮合齿轮泵,这些泵以设计简洁、高的效率和长的寿命而著称于世。
每台泵可以以两种不同的流量进行运转。
随着每台泵的开动或停顿以及液压油无压流回油箱等等,最多可选用15种流量,以便能够最佳地控制模具合模结束时所有的动作(其中包括抽芯系统的动作在内),以适应各方面的需求。
回路图(图1)设计简单,但是绝对保证压力不存在相互干扰。
保证稳定的液压油的流量,也从而保证了生产中的稳定性。
这种类型的回路,之所以具有极高的效率乃是由于流量直接由泵产生,不存在由于流量控制阀(包括比例控制阀)在能量转换时所产生的无效热量所带来的损耗。
图1数字式的速度控制系统及比例压力控制阀冲头直接受来自蓄能器系统压力的驱动(冲头的回程运动除外),这就是说,各种泵的作用,只用作蓄能器的充压之用,这就清楚地表明了,采用高压泵是有利于蓄能器快速充压的。
对于个别动作所要求的压力级别,实质上受控于一种无磁滞的比例压力控制阀。
因此,一定的流量和压力是按每个动作的需要而定。
2 .3过滤器和热交换回路为了保证液压系统的顺利运转,特别要注意液压油的过滤和冷却。
当采用二次回路作液压油的冷却和过滤时,可以获得以下的优点:—液压油通过最佳状态下、连续精细地过滤,所产生的故障少,并延长液压系统元件的使用寿命。
—连续的液流要通过热交换器,因此,可用较小的水量来达到较好的冷却效率。
—如果操作条件差,有可能加接外部加热系统。
此外,这种系统的特色,是对过滤元件采用了有受到污染的防护措施;油箱油位探针(予报警及最低油位);以及液压油温度监控系统。
根据所采用的液压油粘度一温度特性,有可能总的安排7个温度测定点。
2 .4合模控制系统动模安装板运动过程中各个阶段,如开始动作、快速运动、模具的保护动作、合拢、缓冲、中停、模具停止运动等等,皆由双通阀作最佳控制。
液压合模系统的特色、按标准化设计,.以一种电一液停止合模的安全装置,作为阻止非常规合模运动的安全保护。
2. 5抽芯装置的液压系统对于抽芯装置而言,由于考虑了某些技术上的要求,现已发展了一种按标准型号设计的液压系统,可以实现多样化的配置方案。
根据实际生产要求,可以采用不同种类阀的尺寸。
此外,抽芯装置的程序也可以随意编排(图2)。
图2具备各种特色的抽芯装置,根据需要采用阀的大小尺寸3新型的压射装置新型的经过通盘重新设计的卧式冷室压射装置的性能,具备以下各种特色:3.1机械设计方面新型的压射系统,紧凑、简明,拥有一种先进的液压系统模块以及快速接通的垂直式压力增压器。
压室由一架坚固的导滑支架所支撑,根据压射位置的需要,可在垂直方向进行调整。
压室的确可以紧固在所选定的位置上。
此外,锁紧装置也使压室不致有任何错位。
供垂直调整压室的导滑轨道,全部由一只移动式护罩所覆盖,并与独立的中心润滑系统相连接。
当压室由于磨损而需要更换,有必要将压室从压射系统中移开时,可以不必拆卸定模,由此可以显著地减少停机时间。
此外,在冲头杆上有一种快换接头,可以进一步缩短安装时间。
另外,在压射系统中配备有一套在各种转换点中、供作检测冲头行程和监控冲头运动的装置。
3. 2液压系统压射装置的液压系统,按照当前技术发展水平的设计思想,采用全部集中在模块内的双通道内装式控制阀,并且与一种新型的压力增压控制系统相结合。
特别值得强调的优点是采用了比例控制阀,使阀快速接通,使操作简单而方便。
此外,按照最佳尺寸设计横截面积,以达到最大的压射能量。
活塞式蓄能器和压力增压器中,装置有一个充液制动装置,并且当充液完成后,有一个开关使泵断开。
为安全计,凡是存在于蓄能器的压力,在机器停止运转时,处于卸载状态。
3. 3新型的压力增压系统压力增压器最初直接用氮气充气。
为了达到快速建立压力而无压力峰值出现的要求,增压器的活塞按最轻的重量进行设计,并由适当的并经表面处理过的新材料所制成。
基本的受压力控制的增压系统(图3),带有分开的、独立的压力蓄能器装置,其用意乃是为了使最终增压阶段的压力值,在增压时,气体的压力能得到适当地控制。
图3基本上受压力所控制的增压系统气体的压力是通过活塞式蓄能器、按一定容积气体的压缩和膨胀来进行控制。
所要求的压力,受到设在活塞式蓄能器液压一侧的比例压力控制阀所控制。
气体温度的波动,可能引起有害的压力波动会自动地消失,其结果是达到了高度的生产过程的稳定性。
为了使增压器在动作之前,要求有稳定的压力值,则要求消除压力峰值。
此外,在有决定性的、最后建压阶段的压力,不会受到由于有任何压力控制阀、处于波动状态下所带来的影响。
按照自然规律,在高速运动的系统中,压力冲击峰是无法避免的,然而,可以通过减轻增压器件的质量、在气体的直接作用下,可以大大地降低到最小值。
3. 4操作程序所有的受到速度调节的各种动作(除增压外),都会受到压射阀某一阶段动作的影响,这种阀直接受控于蓄能器。
某些主要动作,依靠分开设置的先导控制阀来起作用,以取得最佳的工作状态。
各个压射级别产生的步骤如下:第一级:以抛物线压射(Parashot)作为开始压射阶段、借助比例流量控制阀、作递增地或部分递增地先导控制,其动作系在微型计算机内,根据数字控制信号,采用步进电动机控制。
第二级:从第一级向第二级转换是可以调节的,即可中断,也可以均衡地按等加速度进行。
实现速度控制系通过一个电一液比例执行机构,它是直接在微处理机内,根据先进的信号数据处理进行设计的。
操作过程中参数的变化,如冲头磨擦阻力增加、液压油的温度波动等等,都可能导致所预定的第二级速度的变化,皆可立即由微机记录,并且纠正下一阶段的循环动作。
第三级:压力增压的加载大小,根据需要,或者通过压力或者通过行程启动,其操作方式可以在控制屏上进行预选。
以行程位置作为三级压射启动时,通过行程测量系统,从所预定的行程位置上,可以得出清晰的启动信号。
然而,也可以用压力来控制进行启动,它们处于交接状态,也就是说,如果行程的选点不够准确,或者在浇注时,熔融金属的容量过大的情况下,则在启动时,可用压力控制信号,产生三级增压,反应则可更快些。
此外,通过一种辅助阀来实现行程控制,有可能起到节流作用,这种动作状态,存在下列优点:(1)增压器系在慢速的、受控状态下向前运行,其所允许的由于勺料的定量不够准确所出现的误差,较之在全部接通状态下会更大。
(2)增压器的向前运行,发生在加速运动之中,因此,对第二级速度的影响是微小的。
在这里不用说也明白,从采用增压器这一点上,总会由于时间延时阀而受到滞后。
此外,最终的挤压压力,可在液压控制箱上,按1:2.2的比例迅速地进行调节,而不需要变化氮气的充气。
推出余料:速度和推出压力可以分别调节,使余料从模具中平稳地推出。
4控制系统现代的、复杂的压铸生产系统,导致于需要现代化的控制系统,这里不仅是对于机器和周围的设备而言,而且也是对于压铸过程及其监控而言,皆属如此。
这些控制系统必须具有某些特征,如可靠性、安全性、容易操作以及连续地进行监控,其中也包括联机过程中误差的识别,以保证生产厂有最大的适用性。
新近开发的计算机数控(CNC),调节系统及监控系统,实质上包括两个部分,称之为:—有实效的"Datacess”控制系统,连同机器以及外围设备的控制屏。
一“Processtrol”压铸过程检测及监控系统。
4. 1 "Datacess”控制系统这种控制系统的主要特点如下:(1)采用最佳的现代电子控制硬件,以满足复杂的压铸系统的要求;(2)把最新的压铸技术考虑在内的软件集成化;(3)使操作人员容易了解、简化的操作系统,通过直观的显示装置,取得生产中的信息;(4)诊断装置系统的集成化,以简单明了的文本、指出95%所有的可能的误差根源。