铸造多晶硅中热施主形成规律
铸造多晶硅中原生杂质及缺陷的研究
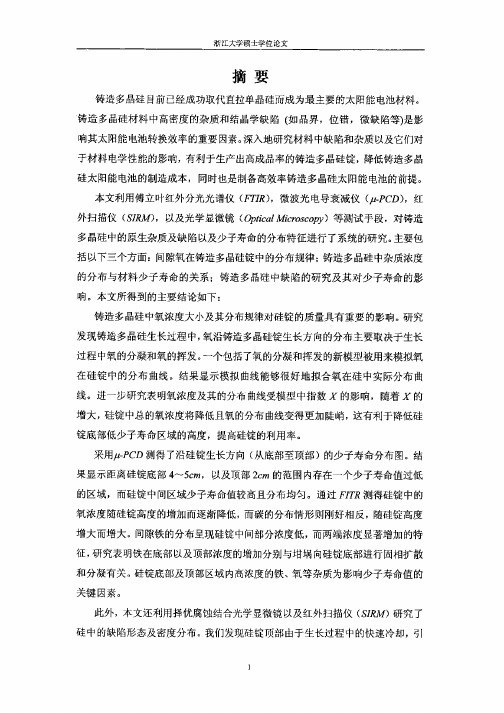
浙江大学硕士学位论文
Ab ta t sr c
C rny a ui sl si n r l d or tl si n h csm l r tle o hs ae m nc sl e o at u t, e r l t ty ai i c n l c a e c o y ai i p n l s c e m ipo vlim tisHg dni o ipri , a ye, o ad a ht oa arl i esy m u tss h o gnc bn n o tc ea . h t f ie u s x c a r n
浙江大学硕士学位论文
起 较大的 应力从而 致了 位错的 热 导 大量 产生 (X m 位错密度大 7 cz 1 0 ) 6 。 体上呈 现
从硅锭底部向硅锭顶部逐渐增加的趋势。 IM 观察到了硅中体缺陷的形态以 S R 及
尺寸大小和密度分布情况。硅锭底部,中部以及顶部处体缺陷平均密度分别为
2 x0 M , x0 m 和1 x0 m . 18 3 8 16 3 . 18 3 8 C . c 5 6 c 左右。
go t d et n G o ar m n bten s u t n epr et dto rwh co . d e et e t i li ad em n l n i i o ge r e w h m ao n x i a a e a oye dsi tn e e alhd T e ye poi w u b a et xgn tb i h b n bi e. o gn fe l e c d ir uo a e s s s t h x r l o d f e
征, 研究表明铁在底部以 及顶部浓度的增加分别与柑祸向硅锭底部进行固相扩散
第七章 铸造多晶硅中的杂质和缺陷
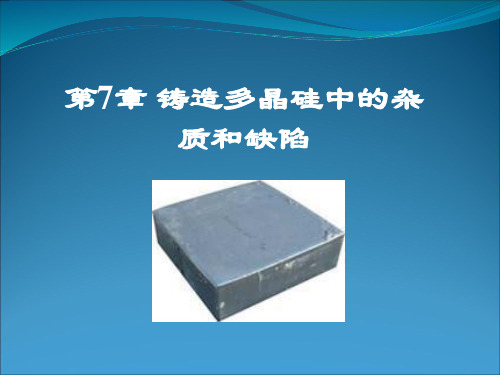
过饱和的间隙氧容易在后续的热处理 工艺中形成复合体与沉淀等。 原生铸造多晶硅中很容易生成氧施主 与氧沉淀,而硅锭底部氧浓度最高, 热处理时间最长,氧施主与氧沉淀的 问题应该是硅锭各部分中最严重的。
铸造多晶硅中原生氧沉淀 的透射电镜照片
第7章 铸造多晶硅中的杂 质和缺陷
铸造多晶硅中的晶界
晶界出现大量的悬桂键,形成界面态,严重影响太阳电 池的光电转换效率。
无金属污染的铸造多晶硅晶界的SEM图像 (a)和EBIC图像(b)
铸造多晶硅中的位错
根据晶体生长方式和过程的不同,铸造多晶硅中的位错 密度约在103~109cm-2左右。
含有高密度位错的铸造多晶硅的光学显微镜照片
a.
p-n结中的金属杂质降低结的反向击穿电压;
b.
金属杂质形成深能级带隙极大地增加p-n结的漏导损耗,
甚至直接导致p-n结变窄;
c.
金属杂质降低氧化诱导生成层错和位错的形成势垒
铸造多晶硅中的金属杂质
金属Cu、Fe、Co在铸造多晶 硅中,自晶体上部(0)到 晶体底部(1)的浓度分布
(直线是根据分凝系数计算的浓 度分布,B的优先分凝系数采用 0.65,Fe的有效分凝系数采用 0.05)
促进其随后氧沉淀生成量。
铸造多晶硅中氧沉淀规律
结果讨论:
铸造多晶硅区别于直拉单晶硅在于,铸造多晶硅中存在较
高密度的位错和晶界等缺陷。而位错和晶界一般可以吸收硅中
过饱和的自间隙硅原子,这降低了铸造多晶硅中氧沉淀的临界 形核半径。另外一方面,由于位错或晶界一般不会影响间隙氧 在硅中的扩散速度,所以,铸造多晶硅中的位错和晶界主要是 通过降低氧沉淀的临界形核半径而促进氧沉淀的生成 。至于原 始氧浓度对氧沉淀的影响,则主要是由于高的原始氧浓度导致 小的氧沉淀临界形核半径,所以高氧样品中氧沉淀生成量较大。
多晶硅铸锭炉的工作原理

多晶硅铸锭炉的工作原理首先,硅料熔融是多晶硅铸锭炉的第一步。
在炉中加入高纯度的硅料,通常是硅块或硅片,然后通过电阻加热或感应加热的方式将硅料加热到熔融温度。
在炉内,硅料中的硅原子由于热能的作用开始振动,并逐渐失去其原子间的结合力。
当硅料的温度达到熔点时,硅原子之间的键强度完全消失,形成了液态硅。
其次,铸锭凝固是多晶硅铸锭炉的第二步。
当硅料熔融后,开始降低温度使其凝固。
凝固过程中,硅原子重新排列并形成了晶体的结构。
在这个过程中,硅原子重新组合并排列成晶格结构,形成了多晶硅。
凝固速度的控制对于提高多晶硅的晶粒度和降低杂质含量非常重要。
通常情况下,在凝固过程中还会控制硅料的搅拌,以避免结晶过程中的杂质团聚。
首先,多晶硅铸锭炉的炉体结构非常重要。
炉体通常由石墨材料制成,可以耐受高温和化学反应。
石墨材料的热传导性能较好,可以加热和散热硅料,确保温度均匀且稳定。
其次,温度控制是多晶硅铸锭炉的关键。
在炉内加热过程中,需要对温度进行精确的控制,以确保硅料能够均匀熔融。
在铸锭凝固过程中,温度的准确控制对于晶体的形成和生长非常重要。
通常通过在炉体中设置多个温度传感器,并通过反馈控制系统来实现温度控制。
最后,搅拌和保护气氛是多晶硅铸锭炉中的重要步骤。
通过搅拌硅料可以改善熔融过程中的均匀性,避免杂质团聚。
此外,为了保护熔融硅料不受氧化的影响,炉内通常需要保持特定的气氛,如氢气或氩气。
总结起来,多晶硅铸锭炉的工作原理包括硅料熔融和铸锭凝固两个主要步骤。
硅料经过加热熔化后,凝固过程中重新排列并形成晶体结构。
在实际操作中,需要考虑炉体结构、温度控制、搅拌和保护气氛等因素的影响。
第十章讲义铸造多晶硅
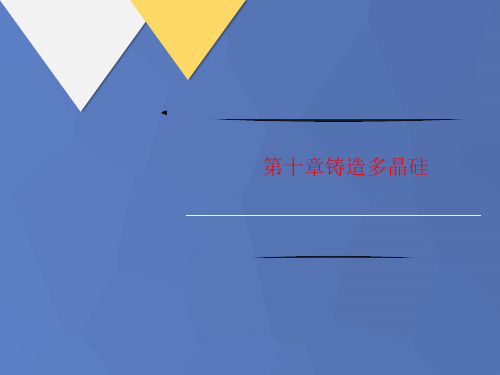
不断挤占单晶硅的市场,成为最有竞争
力的太阳电池材料。21世纪初已占50% 以上,成为最主要的太阳电池材料。
直拉单晶硅为圆片状,而硅片制备 的圆形太阳电池不能有效地利用太阳电 池组件的有效空间,相对增加了太阳电 池组件的成本。如果将直拉单晶硅圆柱 切成方块,制备太阳电池,其材料浪费 就增加,同样也增加了太阳电池组件的 成本。
晶硅,从而降低了太阳电池的光电转换 效率。
铸造多晶硅和直拉单晶硅的比较见表 10.1
自从铸造多晶硅发明以后,技术不 断改进,质量不断提高,应用也不断广 泛。在材料制备方面,平面固液相技术 和氮化硅涂层技术等技术的应用、材料 尺寸的不断加大。
在电池方面,SiN减反射层技 术、氢钝化技术、吸杂技术的开发 和应用,使得铸造多晶硅材料的电 学性能有了明显改善,其太阳电池 的光电转换率也得到了迅速提高。
铸造多晶硅的优缺点
缺
铸造多晶硅具有晶界、高密度的位
错、微缺陷和相对较高的杂质浓度,从 而降低了太阳电池的光电转换效率。
10.1 概述 10.2 铸造多晶硅的制备工艺 10.3 铸造多晶硅的晶体生长
10.1 概述
利用铸造技术制备多晶硅,称为铸 造多晶硅(multicrystalline silicon, mc-Si)。
直熔法
由图可知,硅原材料首先在坩埚中熔 化,坩埚周围的加热器保持坩埚上部温度 的同时,自坩埚的底部开始逐渐降温,从 而使坩埚底部的熔体首先结晶。同样的, 通过保持固液界面在同一水平面并逐渐上 升。使得整个熔体结晶为晶锭。在这种制 备方法中,硅原材料的熔化和结晶都在同 一个坩埚中进行。
直熔法
图10.4 直熔法制备铸造多晶硅用 晶体生长炉的结构
直熔法的冷却方式
铸造多晶硅制备技术的研究进展

(1 Department of Solar Energy Science and Engineering,Xinyu college,Xinyu 338000,
2 Department of Mechnial and Power Engineering!Nanchang Institute of Technology,Nanchang 330099)
tion and the electromagnetic continuous pulling In addition,the purification technique for phosphorus and boron in
metallurgical grade silicon is explained in details,formation and control of grain boundary and dislocation of multicrys—
为了降低坩埚对硅锭的污染。研究者提出了一种改进方 法。在坩埚内壁涂上si。N4膜层,以降低来自坩埚杂质的玷 污。同时.&。N.涂层还能起到一定的润滑脱模作用,因为硅 熔体在高温时与石墨发生反应,加之硅凝固过程中的体膨胀 作用,易造成硅锭与石墨模具的粘连,冷却后难以脱模,使用 si。N|涂层后硅熔体和坩埚内壁不粘结,这样既可以降低凝固 时产生的大量应力又能多次使用坩埚,从而降低了生产成 本。但最近美国的研究者Buonassisi等[2I]通过分析比较了 口-Si3N.涂层与铸造多晶硅中杂质的种类、相对浓度、含有杂 质颗粒的化学态和杂质分布状况及其形成机理后,认为在铸 造多晶体生长时,si。N。涂层中的金属与非金属杂质可能会 污染铸造多晶硅,并提出了相应解决措施:(1)减少mSi。N中 杂质含量;(2)改善口-Si3N的结构质量,使得在晶体生长时口- 鼠N中的分解物降到最低;(3)降低坩埚的表面面积与体积 的比率(如增大坩埚尺寸大小)。 1.2定向凝固法
多晶硅铸锭的晶体生长过程

多晶硅铸锭的晶体生长过程多晶硅铸锭的晶体生长过程在真空熔炼过后,还要经过一个降温稳定,就进入定向凝固阶段。
这个过程既是多晶硅的晶体生长过程,也能够对回收料和冶金法多晶硅料中含有的杂质进行进一步的提纯。
(一)定向凝固与分凝现象硅液中的杂质在硅液从底部开始凝固的时候,杂质趋向于向液体中运动,而不会停留在固体中。
这个现象叫做分凝现象。
在固液界面稳定的时候,杂质在固体中的数量与在液体中的数量的比值,叫做分凝系数。
分凝系数小于1的杂质,在进行定向凝固的时候,都会趋向于向顶部富集。
富集的数量和程度,取决于分凝系数的多少。
一般来说,金属杂质的分凝系数都在10-3以下(铝大约是0.08),所以,定向凝固方式除杂,对于金属杂质比较有效;而硼和磷的分凝系数分别为0.8和0.36,因此,硼和磷的分凝现象就不是太明显。
在定向凝固提纯的同时,考虑硅的长晶工艺,使得定向凝固后的硅能够成为多晶硅锭而直接进行切片,这就是将提纯与铸锭统一在一个工艺流程中完成了。
这也是普罗的提纯铸锭炉的重要提纯手段。
由于含有杂质的硅料和高纯料的结晶和熔液的性质都不太一样,因此,提纯铸锭炉所采用的热场与纯粹铸锭炉的热场是有区别的。
普罗新能源公司目前采用自己研制的提纯铸锭一体化的专利设计,比较成功地解决了这个问题,使得真空熔炼与铸锭是在一次工艺里完成的,既较好地解决了提纯的问题,也圆满地完成了铸锭的要求。
(二)晶体生长过程定向凝固分为以下四个阶段,包括:晶胚形成、多晶生长、顶部收顶、退火冷却。
晶胚形成在熔炼过后,要把硅溶液的温度降低到1440℃左右,并保持一段时间,然后,使坩埚底部开始冷却,冷却到熔点以下6-10℃左右,即1404-1408℃左右。
RDS4.0型的炉体降低底部温度的方法是降低底部功率,和逐渐打开底部热开关的方式。
与常规铸锭炉的提升保温体和加热体方式相比,由于不存在四周先开始冷却然后才逐步到中央的过程,因此,底部温度要均匀得多。
铸锭时,底部红外测温的数据不完全是硅液底部的温度,因为,该测点与坩埚底部的硅液还隔了至少一层坩埚,因此,红外温度仅能参考,还是要根据每台炉子各自的经验数据。
生产多晶硅的工作原理

生产多晶硅的工作原理
多晶硅生产的工作原理主要包括以下几个步骤:
1. 原料准备:首先,将高纯度的硅石通过破碎、磨粉等方式进行预处理,得到符合要求的硅粉。
2. 载体制备:将硅粉与少量添加剂混合,在高温条件下,通过化学反应将硅粉烧结成块状结晶硅,形成多晶硅的基础材料。
3. 铸锭制备:将块状结晶硅通过熔炼、浇铸等方法,将其熔化并倒入特制的铸锭模具中。
在凝固过程中,通过控制温度和冷却速率等参数,使熔态的硅逐渐结晶成为不规则形状的多晶硅铸锭。
4. 晶棒修整:将多晶硅铸锭进行切割,得到多个晶棒。
然后,对晶棒进行粗修整、中修整和精修整等工艺处理,使其尺寸和形状更加精确。
5. 晶棒切片:将修整后的晶棒进行切片,即将晶棒垂直切割成薄片,每片厚度通常为0.2-0.3毫米。
这些薄片即为多晶硅太阳能电池的主要材料。
6. 太阳能电池制造:利用多晶硅薄片制造太阳能电池。
首先,在薄片上形成p-n 结构;然后,通过在片上涂覆导电膜、铝等材料,形成电池电极;最后,进行电池的封装和测试,制成成品太阳能电池。
需要注意的是,多晶硅的生产过程是一个复杂的工序,不同的生产厂家和工艺流程可能会有所不同。
以上仅为一般多晶硅生产的工作原理的简化描述。
定向凝固制备铸造多晶硅的原理及应用综述
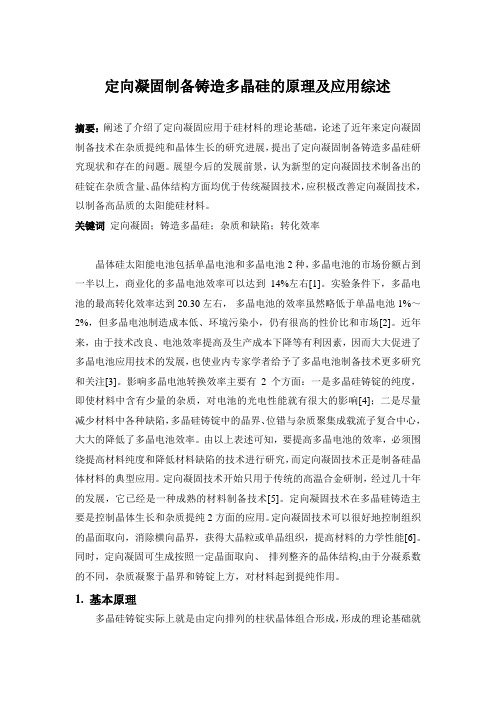
定向凝固制备铸造多晶硅的原理及应用综述摘要:阐述了介绍了定向凝固应用于硅材料的理论基础,论述了近年来定向凝固制备技术在杂质提纯和晶体生长的研究进展,提出了定向凝固制备铸造多晶硅研究现状和存在的问题。
展望今后的发展前景,认为新型的定向凝固技术制备出的硅锭在杂质含量、晶体结构方面均优于传统凝固技术,应积极改善定向凝固技术,以制备高品质的太阳能硅材料。
关键词定向凝固;铸造多晶硅;杂质和缺陷;转化效率晶体硅太阳能电池包括单晶电池和多晶电池2种,多晶电池的市场份额占到一半以上,商业化的多晶电池效率可以达到14%左右[1]。
实验条件下,多晶电池的最高转化效率达到20.30左右,多晶电池的效率虽然略低于单晶电池1%~2%,但多晶电池制造成本低、环境污染小,仍有很高的性价比和市场[2]。
近年来,由于技术改良、电池效率提高及生产成本下降等有利因素,因而大大促进了多晶电池应用技术的发展,也使业内专家学者给予了多晶电池制备技术更多研究和关注[3]。
影响多晶电池转换效率主要有2个方面:一是多晶硅铸锭的纯度,即使材料中含有少量的杂质,对电池的光电性能就有很大的影响[4];二是尽量减少材料中各种缺陷,多晶硅铸锭中的晶界、位错与杂质聚集成载流子复合中心,大大的降低了多晶电池效率。
由以上表述可知,要提高多晶电池的效率,必须围绕提高材料纯度和降低材料缺陷的技术进行研究,而定向凝固技术正是制备硅晶体材料的典型应用。
定向凝固技术开始只用于传统的高温合金研制,经过几十年的发展,它已经是一种成熟的材料制备技术[5]。
定向凝固技术在多晶硅铸造主要是控制晶体生长和杂质提纯2方面的应用。
定向凝固技术可以很好地控制组织的晶面取向,消除横向晶界,获得大晶粒或单晶组织,提高材料的力学性能[6]。
同时,定向凝固可生成按照一定晶面取向、排列整齐的晶体结构,由于分凝系数的不同,杂质凝聚于晶界和铸锭上方,对材料起到提纯作用。
1. 基本原理多晶硅铸锭实际上就是由定向排列的柱状晶体组合形成,形成的理论基础就是定向凝固原理。
关于多晶硅铸锭热场系统
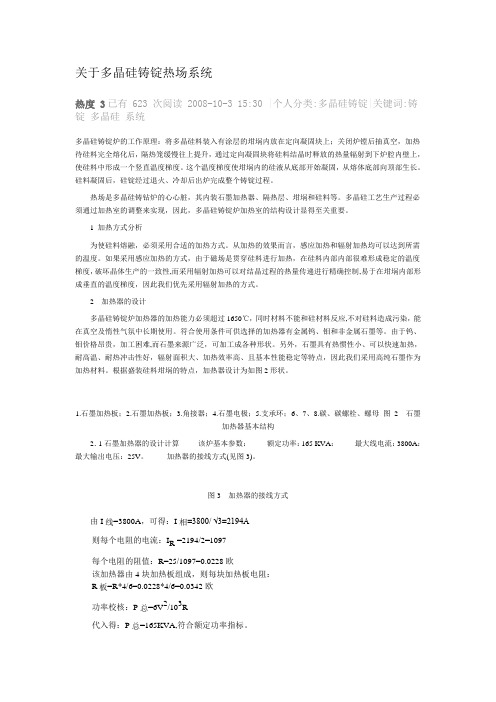
2.3石墨加热器的应力校核
石墨在低温导热性良好,在高温时导热性下降,造成其表面与心部温度差使断面伸长不一致。产生热应力,从而导致石墨加热器损坏,故应计算其产生的热应力。
对于宽度比厚度大得多的板状电热元件:
式中:t中心为电热元件心部温度:t表面为电热元件表面温度,此处取t表面=1540℃
1.石墨加热板;2.石墨加热板;3.角接器;4.石墨电极;5.支承环;6、7、8.碳、碳螺栓、螺母图2石墨加热器基本结构
2.1石墨加热器的设计计算该炉基本参数:额定功率:165 KVA:最大线电流:3800A:最大输出电压:25V。加热器的接线方式(见图3)。
图33800/ √3=2194A
确定隔热层固化碳毡的厚度:
间歇生产的真空电炉,通常隔热层外壁面温度为200~300℃,水冷炉壳内温度为100-150℃,隔热层外表面的辐射换热系数可由下式计算:
(1)
(2)
(3)
tw1为隔热层内壁画温度,此处取tw1=1600℃; tw2为隔热层外壁面温度,此处取tw2=250℃; Q为隔热层散失的总热量,此处已求得Q=3486.OW/m2。将各值代入(5)式,得:故该铸锭炉隔热层固化碳毡厚度取90mm。隔热层组件利用一个方形的小锈钢笼来支撑和固定。
热场是多晶硅铸钻炉的心心脏,其内装石墨加热器、隔热层、坩埚和硅料等。多晶硅工艺生产过程必须通过加热室的调整来实现,因此,多晶硅铸锭炉加热室的结构设计显得至关重要。
1加热方式分析
为使硅料熔融,必须采用合适的加热方式。从加热的效果而言,感应加热和辐射加热均可以达到所需的温度。如果采用感应加热的方式,由于磁场是贯穿硅料进行加热,在硅料内部内部很难形成稳定的温度梯度,破坏晶体生产的一致性,而采用辐射加热可以对结晶过程的热量传递进行精确控制,易于在坩埚内部形成垂直的温度梯度,因此我们优先采用辐射加热的方式。
多晶硅铸锭炉的工作原理

多晶硅铸锭炉的工作原理:将多晶硅料装入有涂层的坩埚内放在定向凝固块上;关闭炉镗后抽真空,加热待硅料完全熔化后,隔热笼缓慢往上提升,通过定向凝固块将硅料结晶时释放的热量辐射到下炉腔内壁上,使硅料中形成一个竖直温度梯度。
这个温度梯度使坩埚内的硅液从底部开始凝固,从熔体底部向顶部生长。
硅料凝固后,硅锭经过退火、冷却后出炉完成整个铸锭过程。
热场是多晶硅铸钻炉的心心脏,其内装石墨加热器、隔热层、坩埚和硅料等。
多晶硅工艺生产过程必须通过加热室的调整来实现,因此,多晶硅铸锭炉加热室的结构设计显得至关重要。
1加热方式分析为使硅料熔融,必须采用合适的加热方式。
从加热的效果而言,感应加热和辐射加热均可以达到所需的温度。
如果采用感应加热的方式,由于磁场是贯穿硅料进行加热,在硅料内部内部很难形成稳定的温度梯度,破坏晶体生产的一致性,而采用辐射加热可以对结晶过程的热量传递进行精确控制,易于在坩埚内部形成垂直的温度梯度,因此我们优先采用辐射加热的方式。
2 加热器的设计多晶硅铸锭炉加热器的加热能力必须超过1650℃,同时材料不能和硅材料反应,不对硅料造成污染,能在真空及惰性气氛中长期使用。
符合使用条件可供选择的加热器有金属钨、钼和非金属石墨等。
由于钨、钼价格昂贵,加工困难,而石墨来源广泛,可加工成各种形状。
另外,石墨具有热惯性小、可以快速加热,耐高温、耐热冲击性好,辐射面积大、加热效率高、且基本性能稳定等特点,因此我们采用高纯石墨作为加热材料。
根据盛装硅料坩埚的特点,加热器设计为如图2形状。
1.石墨加热板;2.石墨加热板;3.角接器;4.石墨电极;5.支承环;6、7、8.碳、碳螺栓、螺母图 2 石墨加热器基本结构2.1石墨加热器的设计计算该炉基本参数:额定功率:165 KV A:最大线电流:3800A:最大输出电压:25V。
加热器的接线方式(见图3)。
图3 加热器的接线方式由I线=3800A,可得:I相=3800/ √3=2194A则每个电阻的电流:I R =2194/2=1097每个电阻的阻值:R=25/1097=0.0228欧该加热器由4块加热板组成,则每块加热板电阻:R板=R*4/6=0.0228*4/6=0.0342欧功率校核:P总=6V2/103R代入得:P总=165KV A,符合额定功率指标。
多晶硅铸锭炉热场
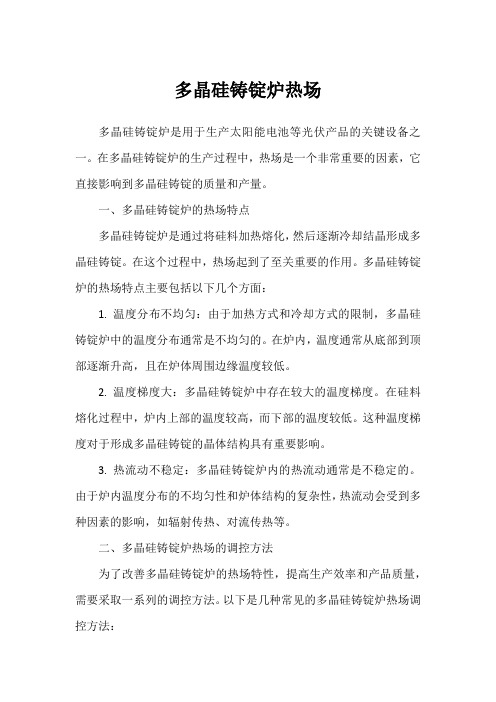
多晶硅铸锭炉热场多晶硅铸锭炉是用于生产太阳能电池等光伏产品的关键设备之一。
在多晶硅铸锭炉的生产过程中,热场是一个非常重要的因素,它直接影响到多晶硅铸锭的质量和产量。
一、多晶硅铸锭炉的热场特点多晶硅铸锭炉是通过将硅料加热熔化,然后逐渐冷却结晶形成多晶硅铸锭。
在这个过程中,热场起到了至关重要的作用。
多晶硅铸锭炉的热场特点主要包括以下几个方面:1. 温度分布不均匀:由于加热方式和冷却方式的限制,多晶硅铸锭炉中的温度分布通常是不均匀的。
在炉内,温度通常从底部到顶部逐渐升高,且在炉体周围边缘温度较低。
2. 温度梯度大:多晶硅铸锭炉中存在较大的温度梯度。
在硅料熔化过程中,炉内上部的温度较高,而下部的温度较低。
这种温度梯度对于形成多晶硅铸锭的晶体结构具有重要影响。
3. 热流动不稳定:多晶硅铸锭炉内的热流动通常是不稳定的。
由于炉内温度分布的不均匀性和炉体结构的复杂性,热流动会受到多种因素的影响,如辐射传热、对流传热等。
二、多晶硅铸锭炉热场的调控方法为了改善多晶硅铸锭炉的热场特性,提高生产效率和产品质量,需要采取一系列的调控方法。
以下是几种常见的多晶硅铸锭炉热场调控方法:1. 加热方式优化:多晶硅铸锭炉的加热方式通常有电阻加热、感应加热等。
合理选择和优化加热方式可以改善炉内温度分布的均匀性,减小温度梯度。
2. 冷却方式控制:多晶硅铸锭炉的冷却方式通常有水冷和气冷两种。
通过调整冷却方式和冷却速度,可以控制炉内的温度梯度和冷却速率,影响多晶硅铸锭的晶体结构和质量。
3. 炉体结构优化:多晶硅铸锭炉的炉体结构对热场的分布和稳定性有着重要影响。
通过改变炉体结构和加强热场的隔离,可以减小炉内温度分布的不均匀性,提高热场的稳定性。
4. 热流动调控:通过优化炉内的热流动方式,可以改善热场的稳定性和温度分布的均匀性。
可以采用流体力学模拟和实验方法来研究和优化炉内的热流动,如调整气体流速、引入局部加热等。
5. 温度监测和控制:在多晶硅铸锭炉中,温度监测和控制是非常重要的环节。
多晶硅生产工艺和反应原理

多晶硅生产工艺和反应原理多晶硅是一种重要的太阳能电池材料,具有高纯度、高晶片质量和较低成本的优点。
多晶硅的生产工艺主要包括硅矿炼制、硅粉冶炼、硅粉还原和硅熔炼等步骤。
其反应原理主要涉及硅矿的还原、氯化和还原等过程。
多晶硅的生产工艺可分为硅矿炼制和硅粉还原两个主要步骤。
硅矿炼制是指从硅矿中提取出硅和非硅物质的工艺。
目前常用的硅矿炼制方法包括硅石和冶金硅炉料两种。
硅石主要是指石英矿和长石矿,常用的炼制方法是先将硅矿进行磨碎和洗选,然后经高温石英石化处理,最后通过水热反应将石英石化为高纯度的硅酸盐溶液,再经过过滤、蒸发结晶等步骤得到硅酸盐固体产物。
冶金硅炉料主要是指含有较高硅含量的矿石,如金山矿、铜渣、废铁渣等,常用的冶炼工艺是将矿石进行焙烧、浸出和萃取等步骤,最终得到较高纯度的硅酸盐溶液。
硅粉还原是指将硅酸盐固体产物还原为硅粉末的工艺。
其主要反应原理是通过还原剂(如木炭、焦炭等)在高温下与硅酸盐反应,生成SiO气体和CO气体,然后进一步反应生成Si和CO2、反应可描述为:SiO2+2C→Si+2CO然而,仅通过硅粉还原很难获得高纯度的多晶硅材料,因为此过程中生成的Si粉末通常包含微量杂质和非晶硅。
为了提高晶片质量和纯度,通常需要进行硅熔炼步骤。
硅熔炼是将硅粉末在真空或惰性气氛下加热,使之熔化成液态硅的工艺。
硅熔炼反应原理是通过向硅粉末中加入硅体和其他掺杂剂,调整硅液中的杂质浓度和晶粒尺寸,以获得纯度较高的多晶硅材料。
硅熔炼通常分为两个阶段进行,首先是预熔阶段,即将硅粉末在较低温度下熔化,然后通过溶液清洁、滤渣等步骤去除杂质,然后再进行主熔阶段,即在高温下继续加热,使硅液达到合适的温度和纯度。
综上所述,多晶硅的生产工艺主要包括硅矿炼制、硅粉还原和硅熔炼等步骤。
反应原理涉及硅矿的还原、氯化和还原等过程。
随着太阳能电池市场的快速发展,多晶硅的生产工艺也在不断改进和优化,以提高生产效率和降低成本。
多晶硅生产工艺和反应原理

多晶硅生产工艺和反应原理1. 引言多晶硅是一种非常重要的半导体材料,广泛应用于电子行业。
本文将介绍多晶硅的生产工艺和反应原理,以帮助读者更好地了解多晶硅的制备过程和原理。
2. 多晶硅生产工艺多晶硅的生产主要通过以下几个步骤完成:2.1 原料准备多晶硅的主要原料是二氧化硅(SiO2),通常以石英砂作为原料。
石英砂首先经过粉碎和洗涤处理,以去除杂质,并获得高纯度的二氧化硅粉末。
2.2 氯化在氯化步骤中,通过将二氧化硅与氯化碳(CCl4)等氯化剂反应,生成气态的四氯化硅(SiCl4)。
SiO2 + 2CCl4 -> SiCl4 + 2COCl22.3 沉积在沉积步骤中,将产生的气态四氯化硅通过化学气相沉积(CVD)或物理气相沉积(PVD)等方法,将其沉积在多晶硅种子(通常为硅棒)上,使其逐渐生长。
2.4 晶体生长在晶体生长步骤中,通过控制温度和压力等条件,使沉积在多晶硅种子上的多晶硅晶体逐渐生长。
在此过程中,多晶硅晶体的结构逐渐完善,并获得所需的形状和尺寸。
2.5 切割和清洗在多晶硅生产的最后阶段,通过机械切割或化学腐蚀等方法将生长得到的多晶硅晶体切割成所需的尺寸和形状。
随后,通过酸洗和高温处理等步骤对多晶硅晶体进行清洗,以去除表面的污染物。
3. 多晶硅生产的反应原理多晶硅的生产过程中涉及到的主要反应是氯化反应和晶体生长反应。
3.1 氯化反应氯化反应是多晶硅生产过程的关键步骤之一。
在氯化反应中,通过将二氧化硅与氯化碳等氯化剂反应,生成气态的四氯化硅。
该反应可用以下化学方程式表示:SiO2 + 2CCl4 -> SiCl4 + 2COCl2氯化反应是一个剧烈的放热反应,同时也是一个可逆反应。
反应中需要控制温度和反应速度,以避免过热和副反应的发生。
3.2 晶体生长反应晶体生长反应是多晶硅生产过程的另一个关键步骤。
在晶体生长反应中,通过将气态的四氯化硅沉积在多晶硅种子上,从而实现多晶硅晶体的生长。
多晶硅生产工艺和反应原理
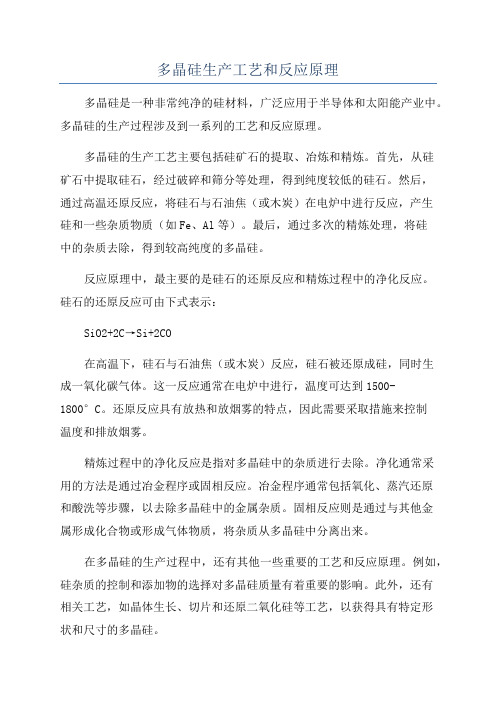
多晶硅生产工艺和反应原理多晶硅是一种非常纯净的硅材料,广泛应用于半导体和太阳能产业中。
多晶硅的生产过程涉及到一系列的工艺和反应原理。
多晶硅的生产工艺主要包括硅矿石的提取、冶炼和精炼。
首先,从硅矿石中提取硅石,经过破碎和筛分等处理,得到纯度较低的硅石。
然后,通过高温还原反应,将硅石与石油焦(或木炭)在电炉中进行反应,产生硅和一些杂质物质(如Fe、Al等)。
最后,通过多次的精炼处理,将硅中的杂质去除,得到较高纯度的多晶硅。
反应原理中,最主要的是硅石的还原反应和精炼过程中的净化反应。
硅石的还原反应可由下式表示:SiO2+2C→Si+2CO在高温下,硅石与石油焦(或木炭)反应,硅石被还原成硅,同时生成一氧化碳气体。
这一反应通常在电炉中进行,温度可达到1500-1800°C。
还原反应具有放热和放烟雾的特点,因此需要采取措施来控制温度和排放烟雾。
精炼过程中的净化反应是指对多晶硅中的杂质进行去除。
净化通常采用的方法是通过冶金程序或固相反应。
冶金程序通常包括氧化、蒸汽还原和酸洗等步骤,以去除多晶硅中的金属杂质。
固相反应则是通过与其他金属形成化合物或形成气体物质,将杂质从多晶硅中分离出来。
在多晶硅的生产过程中,还有其他一些重要的工艺和反应原理。
例如,硅杂质的控制和添加物的选择对多晶硅质量有着重要的影响。
此外,还有相关工艺,如晶体生长、切片和还原二氧化硅等工艺,以获得具有特定形状和尺寸的多晶硅。
总结起来,多晶硅的生产过程涉及到硅矿石的提取、冶炼和精炼等工艺。
其中,硅石的还原反应和净化反应是两个重要的反应原理。
通过这些工艺和反应原理,可以获得高纯度、高质量的多晶硅材料,为半导体和太阳能等产业提供关键的材料基础。
太阳能电池片科普系列-多晶硅铸锭篇

太阳能电池片科普系列——多晶硅铸锭篇中国光伏产业经历了风风雨雨几十年,无论是技术,还是成本都经历了翻天覆地的变化,随着市场对于高效率太阳能电池的需求,多晶硅铸锭工艺也在一丁一点的发生着变化,作为电池片原材料的源头,多晶硅铸锭所扮演的角色也就不言而喻了。
铸锭是将各种来源的硅料高温熔融后通过定向冷却结晶,使其形成硅锭的,硅料被加热完全融化后,通过定向凝固块将硅料结晶时释放的热量辐射到下炉腔内壁上,使硅料中形成一个竖直温度梯度。
这个温度梯度使坩埚内的硅液从底部开始凝固,从熔体底部向顶部生长。
硅料凝固后,硅锭经过退火、冷却后出炉。
一、多晶硅铸锭的主要流程二、喷涂工序1、石英坩埚检查石英坩埚表面——干净无污染、无裂纹,同时内部划痕、凹坑、突起不能超过一定的范围,核对石英坩埚的尺寸(内外部尺寸、上边厚度、底部厚度等),坩埚底部厚度的异常会引起铸锭热场工艺的变化。
2、坩埚涂层坩埚底边和侧边需要预先进行人工刷涂,待涂层凝结过后进行喷枪喷涂,涂层的量是一定的(刷涂次数不限),刷涂的涂层包括氮化硅粉(底部和边部分别为120g、380g)、硅溶胶(60g、150g)、PVA(50g、120g)和纯水(180g、340g),喷涂的涂层中则不需要PVA。
3、检查涂层在喷涂坩埚侧壁的过程中需用挡板遮住坩埚底部,约为侧壁3/4的地方。
喷涂和刷涂过程中要均匀使液体凝聚,涂层必须满足均匀、无气泡、无脱落、无裂缝等条件方为合格。
4、坩埚焙烧将喷好的坩埚放入烘箱内,开始坩埚焙烧,整个过程大概需要30~40小时,先快速升温至设定温度,保持几小时后,自然冷却至合适温度,再开盖冷却。
值得注意的是,坩埚喷涂车间需要保持一定的温度,温度较低环境需在配比涂层时对纯水加热。
原料的杂质浓度会影响铸锭炉的化料时间,铸锭炉在长晶等阶段出现异常,此时铸锭时间可能较一般工艺时间长2-4个小时,底部氮化硅的量太少会导致无法顺利脱模,硅锭底部开裂。
而过量的氮化硅会覆盖住石英砂,从而导致引晶效果不明显,因此要在铸锭中做出适当的调整。
5[1].铸锭多晶硅的生产
![5[1].铸锭多晶硅的生产](https://img.taocdn.com/s3/m/3f60fcc008a1284ac85043bb.png)
5.停炉冷却:把加热功率降低并关闭,让
铸锭硅在炉内自然冷却8~13个小时。方可打 开炉室,取出铸锭硅块,交检验部门进行原 始硅块的初检。 每开一炉的时间(含停炉冷却时间),随 装料量的不等而不同。对装料450公斤的铸锭
硅的生产而言,正常情况下,约需65个小时左
右。
5.3 铸锭硅的外形尺寸
从铸锭炉生产出来的铸锭硅是方形的。装料
Байду номын сангаас
成晶体,并从下往上非常缓慢地长晶,长晶的速度大约为0.2mm/分左右。最后生成一个大晶粒的多晶
铸锭硅来,这个过程大概需要22~27个小时左右。 4.退火处理:坩埚内的液态硅全部结晶成固态后,把炉温控制在稍比熔点低一些,并让硅锭整体 温度保持一致,退火处理3~4个小时,以消除硅锭内部的应力和裂纹,减少位错。
第5节复习题
1、了解铸锭硅生产的简单过程。 2、生产铸锭硅的主要原辅材料有哪些?
3
液体硅
加热器 上炉室 隔热材料
坩埚护板 陶瓷坩埚
热交换台
铸锭硅 下炉室
晶粒的多单晶体的铸锭硅来。见图16。
5.2 铸锭硅的生产过程简介
1.装炉:把铸锭炉室及石墨件清理干净,把 经过氮化硅喷涂及烘烤的方形陶瓷坩埚放置到
石墨底板中间,把多晶硅料和掺杂剂放入到坩
埚中,再用叉车把石墨护板、陶瓷坩埚连同多
图16:铸锭炉室和热场的剖面示意图
1
晶硅料一并装入到铸锭炉中。关闭炉室,给炉室抽真空并通氩气。 2.加热熔化硅料:给炉室内的石墨加热器通电加热。硅的熔点为1416℃,只有在高于此温度的情况 下,硅料才能熔化成液态。从开始加热到硅料全部熔化成液态的时间,一般需要16~21个小时左右。 3.铸锭硅生长:通过缓慢提升隔热系统或缓慢降低坩埚的方法,使下部的液态硅温度降低首先凝固
多晶硅生产工艺和反应原理

多晶硅生产工艺和反应原理多晶硅是一种用于制造太阳能电池板的关键材料。
其制备工艺涉及多个步骤和反应原理。
多晶硅的生产工艺可以概括为以下几个主要步骤:1. 原料准备:多晶硅的主要原料是冶炼硅、矽酸钠和氢氯酸等。
这些原料在制备过程中需要进行精确的配比,以确保最终产品的质量和效能。
2. 冶炼硅的制备:首先,将原料中的冶炼硅与氢氧化钠进行反应,生成硅酸钠溶液。
然后,在高温下将溶液与电解质反应,从中析出粗硅。
这个过程主要是通过液相冶炼和电解两个步骤来完成的。
3. 精炼多晶硅:将粗硅放入电炉中,并在控制温度和环境的条件下进行加热。
通过向炉内加入能与杂质反应的物质(如氯化氢),可以将杂质从硅中去除。
这个过程被称为精炼,其目的是提高多晶硅的纯度。
4. 抽拉和切割:经过精炼的多晶硅会以一定的比例被抽拉成圆柱形的晶棒。
这个晶棒通常被切割成薄片,用于制造太阳能电池板。
切割过程需要高精确度的设备和操作,以确保最终产品的品质。
在多晶硅生产过程中,存在多个反应原理的作用:1. 溶液反应:冶炼硅与氢氧化钠反应形成硅酸钠溶液,这个反应产生了大量的热量。
同时,在高温下进行的电解质反应中,硅酸钠溶液被分解为纯硅和氢氧化钠,从而促使多晶硅的形成。
2. 杂质去除反应:在精炼多晶硅的过程中,通过向电炉中加入氯化氢等物质,可以与多晶硅中的杂质发生反应。
这些杂质会以气体或液体的形式被移出,从而提高多晶硅的纯度。
3. 抽拉和切割反应:在多晶硅被抽拉和切割的过程中,需要使用高精确度的设备和工艺控制,以确保晶棒和切片的质量。
这个过程主要是机械物理反应,通过切割工具对多晶硅进行切割和加工。
总而言之,多晶硅的生产工艺涉及多个步骤和反应原理。
从原料准备、冶炼、精炼到抽拉和切割,每一步骤都是为了提高多晶硅的纯度和形状,以满足太阳能电池板制造的要求。
通过控制反应条件和使用精确的设备,可以实现高质量的多晶硅生产。
多晶硅是一种非常重要的材料,广泛应用于太阳能电池板的制造。
多晶硅材料的热力学性质研究

多晶硅材料的热力学性质研究在当代的材料科学领域内,多晶硅作为一种重要的材料被广泛应用于半导体领域内。
与单晶硅相比,多晶硅具有更高的生产效率、较低的制造成本和更好的机械性能等优点,因此得到了越来越多的关注和研究。
热力学性质是材料科学研究中不可忽视的一部分,它是衡量材料热学性能的核心指标。
对于多晶硅这样的材料,热力学性质的研究不仅可以为材料的生产和应用提供技术指导,还可以为其后续的改进和优化提供科学依据。
一、多晶硅材料的热力学性质介绍热力学性质一般包括热容、热导率、热膨胀系数等,这些性质都是衡量材料能够承受或者释放多少热能的重要指标。
在多晶硅材料中,这些热力学性质的具体表现形式是复杂且多样的,需要通过实验和模拟等手段来进行研究。
在多晶硅材料中,其热容一般与晶界的存在有关,而晶界则是由多晶体的不同晶粒之间所组成的。
同时,多晶硅材料的热导率、热膨胀系数等性质也和晶界以及晶粒的大小等因素密切相关。
二、多晶硅材料的热容研究多晶硅材料的热容是其热力学性质中最为基本的指标之一,也是研究多晶硅材料的热学性质的先决条件。
对于多晶硅材料的热容研究,目前主要的研究方法包括实验测试和模拟计算两种。
实验测试方法一般通过用比热容仪对多晶硅进行测试,以获取其热容值。
而模拟计算则是通过计算多晶硅的晶界能够对其热容产生的影响,从而推测出多晶硅的热容值。
这些研究表明,多晶硅材料的热容值通常会随着晶界的存在而发生变化。
当晶界存在时,热容值会变得更小,因为晶界会抵抗多晶硅材料中热传递的能力。
同时,多晶硅材料的热容值也会随着晶粒大小、晶粒分布等因素而发生变化。
三、多晶硅材料的热导率研究多晶硅材料的热导率是其热力学性质中另一个重要的指标。
在多晶硅材料中,热能传递主要是通过其晶粒直接的热传递完成的。
因此,多晶硅材料的热导率也和其晶粒的大小、晶粒分布、晶界等因素有着密切的关系。
对于多晶硅材料的热导率的研究,研究方法一般包括实验测试和模拟计算两种。
多晶硅生产工艺和反应原理讲解
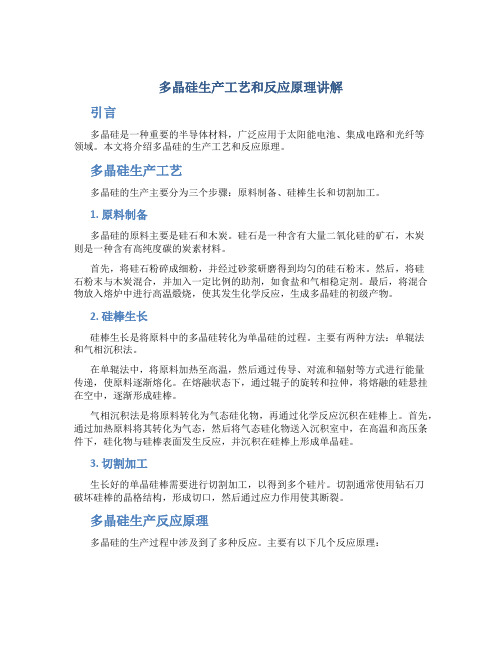
多晶硅生产工艺和反应原理讲解引言多晶硅是一种重要的半导体材料,广泛应用于太阳能电池、集成电路和光纤等领域。
本文将介绍多晶硅的生产工艺和反应原理。
多晶硅生产工艺多晶硅的生产主要分为三个步骤:原料制备、硅棒生长和切割加工。
1. 原料制备多晶硅的原料主要是硅石和木炭。
硅石是一种含有大量二氧化硅的矿石,木炭则是一种含有高纯度碳的炭素材料。
首先,将硅石粉碎成细粉,并经过砂浆研磨得到均匀的硅石粉末。
然后,将硅石粉末与木炭混合,并加入一定比例的助剂,如食盐和气相稳定剂。
最后,将混合物放入熔炉中进行高温煅烧,使其发生化学反应,生成多晶硅的初级产物。
2. 硅棒生长硅棒生长是将原料中的多晶硅转化为单晶硅的过程。
主要有两种方法:单辊法和气相沉积法。
在单辊法中,将原料加热至高温,然后通过传导、对流和辐射等方式进行能量传递,使原料逐渐熔化。
在熔融状态下,通过辊子的旋转和拉伸,将熔融的硅悬挂在空中,逐渐形成硅棒。
气相沉积法是将原料转化为气态硅化物,再通过化学反应沉积在硅棒上。
首先,通过加热原料将其转化为气态,然后将气态硅化物送入沉积室中,在高温和高压条件下,硅化物与硅棒表面发生反应,并沉积在硅棒上形成单晶硅。
3. 切割加工生长好的单晶硅棒需要进行切割加工,以得到多个硅片。
切割通常使用钻石刀破坏硅棒的晶格结构,形成切口,然后通过应力作用使其断裂。
多晶硅生产反应原理多晶硅的生产过程中涉及到了多种反应。
主要有以下几个反应原理:1. 硅石煅烧反应硅石煅烧反应是原料制备中的关键步骤之一。
在高温下,硅石和木炭发生化学反应,生成初级产物。
反应方程式如下所示:SiO2 + 2C → Si + 2CO2. 硅棒生长反应硅棒生长过程中涉及到了两种主要反应:熔融和沉积。
在单辊法中,熔融过程通过能量传递使原料逐渐熔化,生成熔融的硅。
该过程主要包括传导、对流和辐射等方式的能量传递。
在气相沉积法中,硅化物与硅棒表面发生化学反应,并沉积在硅棒上形成单晶硅。
多晶硅铸锭的加热和熔硅过程

多晶硅铸锭的加热和熔硅过程多晶硅铸锭通常分为加热、熔料、⾼温稳定、结晶、退⽕、冷却等六个阶段。
本⽂介绍加热和熔料两个过程。
(⼀)加热准备装好料后,再对炉内进⾏⼀遍检查,即可开炉。
⼀般来说,要先对炉⼦进⾏抽真空。
真空泵逐级打开后,开始通电加温。
抽真空的过程虽然很简单,通常是先打开初级泵(机械、旋⽚或滑阀泵),从⼤⽓抽到2000 Pa以下后,然后再打开罗茨泵,抽真空到10 Pa左右;对于经过清洗的洁净块料,抽真空的顺序只要按照上述步骤进⾏即可。
⼤约在真空度⼩于1000 Pa时,就可以打开加热电源。
在硅料加热时,可以根据经验采⽤恒定功率加热,考虑到硅料的热传导性不佳,⽽RDS3.0 炉型采⽤的是四周加热⽅式,熔化时,是从四周开始熔化,这时,由于测温点在坩埚中部,因此,四周可能已经熔化并到了很⾼的温度,但中间的温度并不⾼,因此,如果采⽤温度设定的控制⽅式,可能功率会加得很⼤。
功率⼤,容易导致坩埚四壁的温度上升,⽽坩埚由于是采⽤⽯英材质的,⼀旦温度超过1600 ℃以上,将很容易与硅发⽣反应,造成坩埚侵蚀;如果温度再上升到1700 ℃,则坩埚会与硅发⽣剧烈反应,导致硅液飞溅,坩埚熔穿。
严重时,硅液甚⾄会溅到炉顶,导致⽯墨件和保温层损坏。
因此,通常熔化阶段应当采⽤功率控制的⽅式,根据理论计算和经验值,使加热功率按照⼀定的设定值进⾏,这样可以保证坩埚温度不会过⾼。
对于RDS4.0型的炉体,由于采⽤底部和顶部加热⽅式,情形会好⼀些,但如果功率过⼤,也同样会在坩埚底部发⽣温度过⾼的情形,只不过,由于顶部和底部都有红外测温,因此,温度不会过⾼。
但如果红外堵塞或者失控,那么,温度过⾼的危险性也是同样存在的。
⽆论是哪种炉型,加热体都在外⾯,因此,硅料内部和外部的温差是始终存在的,这就是为什么在升温⼀段时间,要进⾏⼀下保温,⽬的是让外部的热传到⾥⾯去,避免内外温差过⼤,导致熔化时容易出现意外。
这就是为什么在熔硅的过程中,加热曲线上会有保温的过程。
- 1、下载文档前请自行甄别文档内容的完整性,平台不提供额外的编辑、内容补充、找答案等附加服务。
- 2、"仅部分预览"的文档,不可在线预览部分如存在完整性等问题,可反馈申请退款(可完整预览的文档不适用该条件!)。
- 3、如文档侵犯您的权益,请联系客服反馈,我们会尽快为您处理(人工客服工作时间:9:00-18:30)。
1 实验过程
选取了一批德国拜耳公司所生产的 P 型铸造多 晶硅底部样品( C S 和其他厂家所生长的 P M 一i ) 型单 晶硅样品(Z, C)使用四探针测试样品的原始电阻率, 使用 M R 测试样品的原始氧浓度和碳浓度。原始 数据如表 1 所示:
表 1 实验所用硅片中原始氧, 碳浓度和电阻率大小
样 品类型和编号
取 拉 硅, 代直 单晶 成为最主 太阳 池材料〔1 要的 电 10 , 2
但是与直拉单晶硅太阳电池相比, 铸造多晶硅太阳 电池的转换效率较低。目前, 产业界中直拉单晶硅 太阳电池的转换效率一般在 1一 6 5 1%左右, 而铸造
多晶 硅太阳电池的 转换效率大约在 1一4 究其 3 1%。
…
,. .
, __ 中 令 / ‘宁 : _一 幸 ,
创卜沪甲 . 创巨尹甲
声,
.
.. -一
立立宜立盆。自。 二一二一一一
2 4 0 0
0
6 8 1 0 1 0 10 1 0 0 0 0 2 4 6
的 形成[, 1 7如表 所示。虽然目 1 前对于热施主的形
成机理尚未清楚, 从而提出了很多种热施主模型, 但 是其中一点是大家所肯定的, 那就是硅中间隙氧的
e P to imti , r st a olkR . r holc e l ht , s u o【 ] . vt ars i y t n t o a a s o a d o u
热处理时间/ h
图 1 各种原生晶体硅样品中热施主浓度
随热处理时间的变化曲线
F . u e ot m l o o ettn r s hradnrc cnao i 1 v f g C e o s ri n
v. an t it i r t l e h d e ns p s san lg n f e a e n i i e m e m
C- ( zi S 位错)F, (, F) Z
0
取其中一批样品(, , D. F) A, G, E+ 在 B , , , ,
60 5℃下退火 05, . 以消除原生热施主。然后, h 将这
万方数据
太
阳
能
学
报
2卷 6
些样品和没有经预处理的样品(2 B, D, 预处理和未经过此预处理的各种样品中热施主浓度 A , C, E, 2 2 z 2 我们可以 瓦) 同时进行40 5℃下的退火处理, 保护气氛为氮气。 随热处理时间的变化曲线。从这两个图, 每隔 1 取样测试样品的电阻率, 0 h 记录电阻率的变 发现原生热施主的存在不影响随后热施主形成规 律。所有样品中热施主的浓度都是先随着热处理的 化, 热施主浓度由热处理前后电阻率变化所对应载 时间而增加, 热处理 1 h 3 左右时到达最大值, 0 尔后 流子浓度的差值。 随着热处理的继续进行而迅速降低。但是对于不同 2 结果和讨论 种类的样品, 其中氧沉淀最大生成量显著不同, 在含 碳量低, 无位错和晶界的单晶硅 B 和B 样品中, 1 2 经 由于晶体生长过程中会生成热施主, 而这些热 1h 3 热处理所形成的热施主浓度最大, 0 大约为 11 . 施主可以在 60 5℃下热处理 3mn 0 i消除。表 2 显示 x c-。与此相对比的是相似单晶硅样品 C 16 3 0 m 1 l 所使用硅片中原始热施主的浓度。从该表中可以发 2 其热施主的生成量则最小, 仅为 6 x 现, 在铸造多晶硅底部的样品中存在着高达 1 x 和 C 样品中, . 4 0 c- 1 m 。这两种样品(lB)C,2由于含有不 B,2(lC) 15 ’ 原生热施主, 0 c- 'm 的 这不仅与高浓度的自 间隙 14 3 同的原始氧浓度, 而所生成热施主量的显著不同, 这 氧有关, 还与铸造多晶硅长达 4h 0 左右的晶体生长
原因, 主要在于铸造多晶硅中存在着高密度的缺陷
和高 浓度的 质, 界、 错、 碳等等[。 杂 如晶 位 氧、 3 虽然 ]
清洁的位错或晶界对材料的电学Байду номын сангаас能没有很大的影
响闭, 但是一旦缺陷和杂质相互作用就会显著影响
材料的电学性能, 所以研究铸造多晶硅中缺陷和杂 质的相互作用显得十分必要。 氧和碳是铸造多晶硅中两种非常重要的杂质元 素。关于这两种杂质在直拉单晶硅中性质的研究已 经有几十年的历史, 对它们及其复合体或沉淀相有 了比较深人地理解, 如热施主、 新施主、 氧沉淀、 碳氧
万方数据
4 期
俞征峰等: 铸造多晶硅中热施主形成规律
列样品, 虽然初始氧浓度与 E F , 系列样品中氧浓度 相近, 但是所形成的热施主较低。这表明, 碳会显著
抑制。
的形成规律, 得出以下结论: 1原始氧浓度对热施主形成的影响最大; )
综上所述, 可以发现, 原始氧浓度对热施主形成 规律的影响最大, 其次是碳和位错, 而晶界则几乎没 有影响, 而且氧和位错是促进热施主的形成, 碳则是 抑制作用, 其抑制作用甚至强于位错的促进作用。 当硅片在 0 一 0℃热处理时, 30 50 过饱和的间隙 氧会相互聚集形成热施主以降低化学势。铸造多晶 硅硅锭长时间的生长过程, 同样也是硅锭的热处理 过程。对于铸造多晶硅底部, 一般会经历长达 2 多 0 个热处理退火, 这样就导致较高浓度的原生热施主
B1 C1
D
‘. 1
二M / I
0 0 4 0 2 0 6
,, ,幸
一・ 杏 众 杏二
1 0 4 1 0 2 1 0 6
,1 八」
1 1
6 1 〕 0 川
热处理时间/ h
E
F 1 3
图 2 经 60 5℃热处理 3mn 0 i后各种晶体硅样品 中热施主的浓度随热处理时间的变化
50
无 该 处 理 , 日
F . Crs e ad o o eri l rc c ttn i2 v otr o s na g ue f hm n n o
v. e n t e h d e n s l i r t p s s ana g i t fe a e n l i n i m e m
第2卷 第4 6 期
20 年 8 05 月
阳 能 学 报
E E G A S L R S N C N R I E A I S I A O I
V l 6 N . o. o4 2 , A g 05 ,20 u.
文章编号: 24 0 20 05- %( 5 0 0
铸造多晶硅中热施主形成规律
俞征峰,席珍强, 杨德仁,阀端麟
影响最大。实验还发现, 60 05 退火处理可以消除部分原生热施主,原生热施主对于随后的热施主的形 在 59 . 0 h
成规律没有明显影响。
关健词: 铸造多晶硅;氧; 热施主
中图分类号 T 54 K1 文献标识码 :A
0 引 言
最近, 铸造多晶硅以其较高的性价比已经成功
的变化, 从而揭示热施主的生成规律。
图1 和图 2 分别是在 40 5 ℃下经过 60C mn 5' 3 i 0
其次, 对比样品( lB ) A , , B , 和( lA )虽然在这 2 2 两种晶体硅中含有非常相近的原始氧浓度 , 但是在 铸造多晶硅中所形成热施主最大浓度低于直拉单晶 硅中热施主的最大生成量, 如图 1 和图2 。这表明: 位错, 晶界或碳都可能会抑制热施主的形成。但究 竟是位错, 晶界还是碳主要抑制了热施主的生成? 我们又分别采用了4 种不同的样品研究了其中的热 施主形成规律。样品(lE ) F, 中, E , 和(lF) 虽然 F 2 2 系列的原始样品中含有晶界, 但是其中热施主生成 规律与 E系列样品中热施主形成规律相似, 如图 1 和 2这表明晶界对热施主的形成规律没有明显的 , 影响。同时, 在这两种样品中所形成的热施主浓度 都明显高于 C系列样品中热施主的最大形成浓度, 这表明位错会促进热施主的形成。另外, 对于 D系
M 一 i 凡, C S 人, ) (
[ix 0 sx1 ol 1 [ ] 0 电阻率 17 C "
/ - c 3 / - m c 3 m
1 0 0.
1 0 0.
‘. 1 0
0
/ ,"m a c
, 1
:
0
7
…
4
C- ( zi S 无位错)B, z (, B) C- ( zi S 无位错)C, (GQ) C- ( zi S 位错)D ,l (, ) D C- ( zi S 位错, 晶界)E, (,
F) 2
9 1. 1
4
山. 1
 ̄、
:
甘
复 合体等[。虽然, 5 1 对铸造多晶硅中氧沉淀的形成 规律 一 做了 些研究[1 很少 6, , 但是 人研究 7 铸造多晶 硅
中热施主的形成规律, 特别是晶界、 位错和碳对热施 本实验采用对比方法, 用四探针仪和傅立叶红 外仪(M ) F 研究铸造多晶硅中电阻率和氧、 碳浓度
20
wh p - n m a6 0 0mn 9 f 30 i i t r a e g 5 o t h e n d t r e
.一
・竺
0 1\ 侧 径 州 樱 藕
30 60 90
。
_ _ .. .
.滚
尹 .
样品编号
已
表明原生氧浓度对热施主形成规律的影响最大。
10 5
.. x扩C预 处 理
M 2 10
一.一 A1
・竺 0 1\ 侧 说
一.一 :1 3
目
原生热施主浓度/ ' m 3 / 4 1 c- 0
州 樱 臻
}且 0
60 3a
_ .,. . 声 - .一
, .
_ 声
A1 1 4
时间有关。
表2 各种硅片中原生热施主的浓度
Tb 2 oc ttn s r n ml o nao oa g w t radnr al Cne ri f o h e - e o s it d e n s p s n i r t l h fe a e e m