生产偏差处理的七个阶段【最新版】
生产偏差处理的流程

生产偏差处理的流程一、对事件的报告1•事件观察者发现了任何有可能引发偏差的事件后,应撰写偏差事件报告;或立即向主管报告,由主管或相关人员随后撰写生产偏差事件报告。
2.发起者应进行初步调査并立即采取纠正措施。
(1)立即釆取以下措施(但不仅限于此),以减少事件对生产物料/设备/区域/工艺/程序等的负面影响:停止生产:GMP相关活动的恢复和继续需质量部的批准。
调查结束前,问题原辅料、包材、中间体或成品应清楚地贴上待验标签或通过在软件系统中控制其待验状态。
任何怀疑有问题的设备、仪器、系统应安放在一个安全的条件下,调查结束后方可使用,如必要,需贴上明显的标签。
通知相关部门人员(如批记录审阅/释放,生产操作,药师药政和技术服务)。
(2)进行范围影响评佔,在生产偏差事件报告中对报告事件应作详细描述(如涉及范圉、持续时间、严重性)3.确定唯一生产偏差的跟踪号。
4.生产偏差事件应记录以下项Ll (包括但不限于):(1)产品名称、批号(2)发现日期/报告日期(3)事件发生日期(4)其他相关调查(5)事件描述,包括如何发现、在何处发现(6)事件发现者和/或报告者(7 )所有受影响的生产物料/设备/区域/方法/方法/程序(8)其他相关记录(9)事件分类(10)立即采取的措施二、偏差事件报告评估1•发起部门经理、主管或其代理人负责对事件报告进行评估,确保有关事件的详细内容包含其中,如评估时发现不够详尽,需要立即通知撰写者,撰写者需尽快补充。
2.质量部过程检查负责人最终评估事件报告,确保包括事件的详细内容包含其中。
如审阅者发现不够详尽,需要通知撰写者,撰写者需尽快补充。
3.质量部在调查相关部门人员的协助下,评估是否有受事件影响的批次、系统或区域没有在事件报告中报告,如果有,应将它们处于待验状态。
4•质量部同样需评估过去一段时间(如:一个月)是否发生类似事件。
如发生过,过去事件的事件报告号需记录。
如果当前事件是一定时间内多次发生,即使符合只报告事件条件,该事件应山质保部评估以确认是否需进入偏差调查程序。
偏差处理程序

码第1错误!未指定书签。
页一、目的:任何偏差均应依照本程序进行调查,以便准确、及时地进行处理,提出改进措施,避免再次发生。
二、适用范围:本公司与生产和质量相关的任何偏差均依照此程序进行管理。
三、责任者:1.公司品管部负责该文件的起草与修订,品管部、生产技术部负责该文件审核,质量副总负责该文件的批准。
2.公司所有与生产、质量活动有关的部门负责执行该程序,公司品管部负责对执行情况进行监督。
四、内容1.定义1.1偏差:与已批准的影响产品质量的有关工艺、标准、规定、条件等不相符合的任何情况,它包括药品生产的全过程和各种影响因素。
如:物料取样、储存、化验结果超标,生产工艺偏差,设备故障,计量校验结果超标等。
1.2关键偏差:可能影响产品的质量、安全性、功效及注册情况的偏差。
1.3非关键偏差:不影响产品的质量、安全性、功效及注册情况的偏差。
2.偏差分类2.1设备/设施:包括与生产或实验室设备和设施相关的不符合事件。
如动力运行故障、设备、仪器故障;对设备/设施/系统的监测未能如期执行或监测结果超标等;清洁检查结果不合格。
2.2人员/实施:包括违反SOP或工艺规程进行操作等。
2.3文件/记录:填写/修改不规范,也包括批记录因污染、损坏需要更换,未经批准修改工艺参数等。
2.4产品/物料:原辅料或包装材料检验不合格,原辅料或包装材料虽检验合格,但在使用过程中发现异常,可能导致物料报废或产品返工。
如需反馈供应商,以期进一步调查与改进。
产品检验不合格。
2.5检验发生的不符合事件:超标结果(OOS):任何检验结果不符合已批准的质量标准、检验方码第2错误!未指定书签。
页法或程序,应先执行《QC超标、超常检验结果的处理程序》,在确认物料或产品不合格后,执行本程序。
2.6校验:使用了未通过校验和校验过期的检测仪器,或在校验中发现的不符合情况。
2.7其它3.偏差举例3.1所有拒收的批次。
3.2所有超过收率范围的批次,例如,由于设备故障造成的超额损失。
生产偏差处理的流程

生产偏差处理的流程一、对事件的报告1.事件观察者发现了任何有可能引发偏差的事件后,应撰写偏差事件报告;或立即向主管报告,由主管或相关人员随后撰写生产偏差事件报告。
2.发起者应进行初步调查并立即采取纠正措施。
(1)立即采取以下措施(但不仅限于此),以减少事件对生产物料/设备/区域/工艺/程序等的负面影响:停止生产:GMP相关活动的恢复和继续需质量部的批准。
调查结束前,问题原辅料、包材、中间体或成品应清楚地贴上待验标签或通过在软件系统中控制其待验状态。
任何怀疑有问题的设备、仪器、系统应安放在一个安全的条件下,调查结束后方可使用,如必要,需贴上明显的标签。
通知相关部门人员(如批记录审阅/释放,生产操作,药师药政和技术服务)。
(2)进行范围影响评估,在生产偏差事件报告中对报告事件应作详细描述(如涉及范围、持续时间、严重性)3. 确定唯一生产偏差的跟踪号。
4. 生产偏差事件应记录以下项目(包括但不限于):(1)产品名称、批号(2)发现日期/报告日期(3)事件发生日期(4)其他相关调查(5)事件描述,包括如何发现、在何处发现(6)事件发现者和/或报告者(7)所有受影响的生产物料/设备/区域/方法/方法/程序(8)其他相关记录(9)事件分类(10)立即采取的措施二、偏差事件报告评估1.发起部门经理、主管或其代理人负责对事件报告进行评估,确保有关事件的详细内容包含其中,如评估时发现不够详尽,需要立即通知撰写者,撰写者需尽快补充。
2. 质量部过程检查负责人最终评估事件报告,确保包括事件的详细内容包含其中。
如审阅者发现不够详尽,需要通知撰写者,撰写者需尽快补充。
3.质量部在调查相关部门人员的协助下,评估是否有受事件影响的批次、系统或区域没有在事件报告中报告,如果有,应将它们处于待验状态。
4. 质量部同样需评估过去一段时间(如:一个月)是否发生类似事件。
如发生过,过去事件的事件报告号需记录。
如果当前事件是一定时间内多次发生,即使符合只报告事件条件,该事件应由质保部评估以确认是否需进入偏差调查程序。
偏差处理流程

偏差处理流程偏差处理流程是指在组织中发生问题或偏差时,组织采取的一系列措施来及时纠正并防止再次发生类似问题的过程。
偏差处理流程的目标是保持组织的正常运作,提高工作效率,增强组织的竞争力。
偏差处理流程通常包括以下几个步骤:1. 发现和报告偏差:组织成员需要时刻关注工作流程和结果,及时发现可能存在的偏差。
一旦发现偏差,应当及时向上级或相关部门报告,确保问题得到及时处理。
2. 偏差验证和确认:上级或相关部门接到偏差报告后,需要对偏差进行验证和确认。
通过对工作过程和数据进行分析,确定是否存在偏差,并对偏差进行评估,以确定对组织的影响程度。
3. 制定纠正措施:针对确认的偏差,上级或相关部门需要制定相应的纠正措施。
纠正措施应当具体、明确,并根据问题的本质和影响程度确定优先级和时限。
4. 实施纠正措施:上级或相关部门需要组织相关人员对纠正措施进行具体实施。
这可能涉及到调整工作流程、加强培训和沟通、修正错误数据等操作,以确保纠正措施能够有效地解决问题。
5. 监督和评估:在纠正措施实施后,上级或相关部门需要对纠正措施的执行情况进行监督和评估。
这可以通过定期报告、现场检查、绩效评估等方式进行。
监督和评估的目的是确保问题得到有效解决,并防止类似问题再次发生。
6. 改进措施的制定:通过监督和评估,可以发现纠正措施的不足之处或新的潜在风险。
上级或相关部门可以根据监督和评估的结果,制定改进措施,进一步提升组织的管理水平和工作效率。
总结来说,偏差处理流程是组织中非常重要的一环,它能够帮助组织及时发现和解决问题,确保组织的正常运作。
偏差处理流程需要各级管理者和相关人员密切合作,及时报告和处理问题,以确保问题得到有效解决。
同时,偏差处理流程也需要不断进行监督和评估,以及时发现并解决执行中存在的问题,确保流程的有效性和持续改进。
在实际操作中,组织可以根据自身需求和特点,对偏差处理流程进行个性化的调整和优化,以提高流程的适用性和实施效果。
偏差处理程序
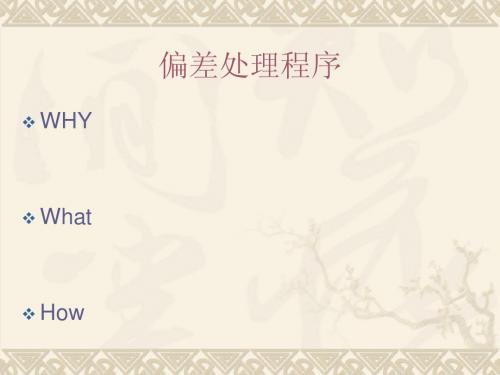
偏差记录 隔离 报告 偏差事件的分级和评估 偏差事件的调查 偏差时间的终审 纠正及预防措施的追踪、关闭
偏差记录
物料接收,储存,使用,生产过程的设备运行,工 艺参数,控制标准,公用系统运行,校验等任何 发生异常或偏差时,偏差发生的部门应及时记 录涉及偏差的所有细节,并将相关物料隔离开 来. 若需要采取不使情况进一步恶化的必要工作, 可采用必要的应急措施,事后应将所采取的措 施填写在,偏差事件处理单中,交部门经理和 QA确认.
偏差事件的调查
QA组织和协调偏差事件发生部门对偏差事件进行调 查,有关责任部门应指定调查员负责进行偏差事件根 源的调查,并完成相应调查报告交QA,由QA汇总并完 成最终调查报告. 调查员对上述各方面的调查结果进行汇总分析,确定 根源或最有可能的原因,时限为20个工作日.若超过, 需在偏差事件处理单上注明原因. 纠正及预防措施的确认,最后调查报告交QA经理/质 量副总/总经理审批.
关键/严重偏差需要进行调查与记录。如有必 要,关键/重要偏差的调查还必须扩展到其他 可能受影响的批次。在批产品放行前,关键/ 严重偏差的调查必须完成并确定对产品质量 已无影响。
偏差事件的管理
偏差事件的处理时限:终审原则上应自发生之日起30个工作 日内完成;特殊事件,例如:需要与经营部进行沟通,则审 批时间可根据需要延迟 偏差事件的处理台账管理:QA要对每个偏差事件基本信息 登记在“偏差处理台账”中。 偏差事件月度回顾:QA每月要对偏差事件进行统计,确认 偏差事件的调查完成情况、审核批准完成情况及偏差事件的 分类、分析。 偏差时间年度回顾:QA每年初对上年发生的偏差事件进行 趋势分析、纠正预防措施完成情况及实施效果分析,分析结 果向公司管理层报告 偏差时间的编号原则:按DN+(5位)年流水号编号,如 DN-06001,即06的第一个偏差事件。
偏差处理流程范文

偏差处理流程范文偏差处理流程是一种管理工具,可用于处理项目或组织中出现的偏差或问题。
偏差是指计划与实际之间的差异,可能导致项目无法按时完成、产生额外的成本或质量问题。
因此,采用适当的偏差处理流程可以帮助及时发现和解决偏差,确保项目能够按计划顺利进行。
下面是一个常见的偏差处理流程,包括以下几个步骤:1.偏差识别:首先需要对项目或组织进行全面的评估,以确定是否存在偏差。
这可能包括与项目计划和目标的比较、与过去的类似项目的对比,以及与利益相关者的交流。
通过这些手段,可以尽早发现潜在的偏差并确定其严重程度。
2.偏差原因分析:一旦确认了偏差,下一步是进行原因分析。
这可以通过使用根本原因分析工具如鱼骨图、5W1H分析(谁、何时、何地、何种原因、为什么及如何等)或因果图等,以尽量准确地找出造成偏差的根本原因。
确切地了解偏差的原因有助于解决问题并采取适当的纠正措施。
3.处理计划制定:基于偏差原因分析的结果,制定处理计划。
该计划应包括明确的目标、所需的资源、负责人和时间表等。
处理计划应既可行又可实施,并与项目或组织的整体目标相一致。
4.更新项目计划:在确定了处理计划后,需要将其及时更新到项目计划中。
这包括更新关键的时间表、成本估计和资源分配等信息,以确保项目的整体规划能够适应处理计划的变化。
5.推广计划执行:执行处理计划是将计划变为现实的过程。
在执行过程中,需要确保各项计划都按时、按要求得到落实。
这可能需要协调不同利益相关者的合作、分配和管理资源以及确保沟通顺畅。
6.监控和控制:在处理计划执行的同时,需要进行监控和控制以保证其有效性。
这可以通过定期的进度报告、成本效益分析和质量评估等方式进行。
通过监控和控制,可以及时发现并解决潜在的问题,并调整计划以适应项目的实际情况。
7.记录和报告:在整个偏差处理流程中,记录和报告是非常重要的。
记录所有的偏差识别、原因分析和计划制定过程,并定期向相关方进行报告。
这不仅有助于追溯和审核,还可以为以后的项目或组织提供宝贵的经验教训。
偏差处理流程

偏差处理流程一、偏差识别。
首先,我们需要建立偏差识别的机制,包括设立偏差识别的标准和方法。
可以通过设立质检点、监控设备运行状态、定期进行数据分析等方式,及时发现偏差的存在。
同时,还需要对可能引起偏差的因素进行分析和排查,以便更快地找出偏差的根源。
二、偏差分析。
一旦发现偏差,就需要进行偏差分析。
偏差分析是为了找出偏差的成因,确定偏差的影响范围,并对偏差进行分类和评估。
在偏差分析中,需要收集相关数据和信息,进行对比和验证,找出偏差的具体原因。
同时,还需要评估偏差对产品质量和生产效率的影响,以便确定处理偏差的优先级和紧急程度。
三、偏差处理。
在偏差分析的基础上,我们需要制定偏差处理方案。
偏差处理方案应包括对偏差的具体处理措施、责任人、处理时限和效果评估等内容。
对于一些常见的偏差,可以建立偏差处理的标准流程,以便更快地进行处理。
在处理偏差的过程中,需要及时沟通和协调各相关部门和人员,确保偏差得到有效处理。
四、偏差预防。
除了对已发生的偏差进行处理外,我们还需要进行偏差预防工作。
偏差预防包括对偏差的根本原因进行分析和处理,改进生产工艺和管理方法,提高设备和人员的技术水平等。
通过偏差预防工作,可以减少偏差的发生,提高生产效率和产品质量。
五、偏差记录和总结。
最后,我们需要对偏差处理的过程进行记录和总结。
偏差记录应包括偏差的发生时间、原因、处理过程和效果评估等内容。
通过偏差记录和总结,可以为今后的偏差处理工作提供经验和参考,不断改进偏差处理的流程和方法。
综上所述,偏差处理流程是一个系统工程,需要全员参与,注重细节和数据分析,以确保偏差得到及时、有效地处理。
只有不断完善偏差处理流程,才能提高企业的生产效率和产品质量,赢得客户的信任和支持。
希望以上内容能够对您有所帮助,谢谢阅读。
偏差处理流程
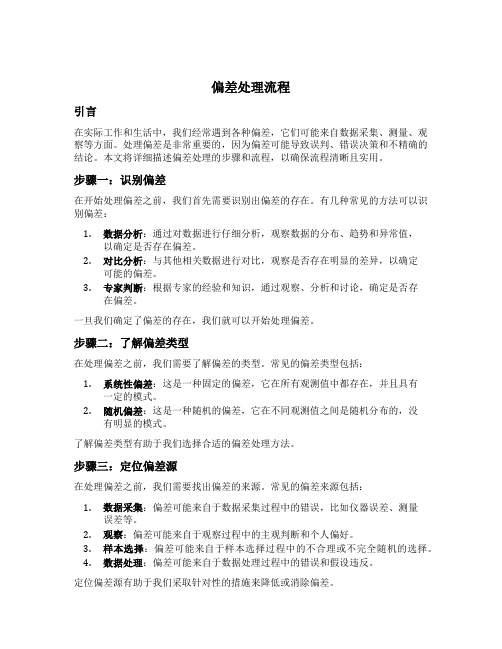
偏差处理流程引言在实际工作和生活中,我们经常遇到各种偏差,它们可能来自数据采集、测量、观察等方面。
处理偏差是非常重要的,因为偏差可能导致误判、错误决策和不精确的结论。
本文将详细描述偏差处理的步骤和流程,以确保流程清晰且实用。
步骤一:识别偏差在开始处理偏差之前,我们首先需要识别出偏差的存在。
有几种常见的方法可以识别偏差:1.数据分析:通过对数据进行仔细分析,观察数据的分布、趋势和异常值,以确定是否存在偏差。
2.对比分析:与其他相关数据进行对比,观察是否存在明显的差异,以确定可能的偏差。
3.专家判断:根据专家的经验和知识,通过观察、分析和讨论,确定是否存在偏差。
一旦我们确定了偏差的存在,我们就可以开始处理偏差。
步骤二:了解偏差类型在处理偏差之前,我们需要了解偏差的类型。
常见的偏差类型包括:1.系统性偏差:这是一种固定的偏差,它在所有观测值中都存在,并且具有一定的模式。
2.随机偏差:这是一种随机的偏差,它在不同观测值之间是随机分布的,没有明显的模式。
了解偏差类型有助于我们选择合适的偏差处理方法。
步骤三:定位偏差源在处理偏差之前,我们需要找出偏差的来源。
常见的偏差来源包括:1.数据采集:偏差可能来自于数据采集过程中的错误,比如仪器误差、测量误差等。
2.观察:偏差可能来自于观察过程中的主观判断和个人偏好。
3.样本选择:偏差可能来自于样本选择过程中的不合理或不完全随机的选择。
4.数据处理:偏差可能来自于数据处理过程中的错误和假设违反。
定位偏差源有助于我们采取针对性的措施来降低或消除偏差。
步骤四:消除或控制偏差在定位了偏差源之后,我们可以采取一系列措施来消除或控制偏差,具体措施取决于不同的偏差类型和偏差来源。
下面是一些常见的偏差处理方法:1.校正:针对系统性偏差,我们可以进行校正来消除或降低偏差。
校正可能包括调整仪器、修改测量方法、修正数据处理算法等。
2.控制:针对随机偏差,我们可以采取控制措施来减少偏差的影响。
GMP生产偏差及偏差管理

GMP生产偏差及偏差管理1偏差Deviation偏差是指与批准的工艺、程序、说明、规范或既定标准不同的任何意外事件。
偏差可能发生在药品的制造、包装、取样和测试过程中。
例如化工工艺中,对温度的控制没有限制在规定的范围内,或者投料的时间超过了规定的时间上限,或者某个反应没有按照要求进行氮气保护等等不一而足。
偏差按照严重程度的递减次序可分为关键偏差、重大偏差(major deviation)和轻微偏差(minor deviation)三种类型。
具体划分标准不同的机构可能有着不同的操作流程。
通常来说,关键偏差是那些会影响关键工艺参数(CPPs, critical process parameters)、设备或仪器的质量,或者具有直接的患者安全风险或危及生命的偏差情况。
重大偏差会影响产品的质量、安全性或功效,但可能不会对患者产生直接影响。
轻微偏差会影响公用事业、设备、材料、组件或文档,但不会影响产品质量或产品的物理状态。
值得注意的是,很多机构如今在偏差的分类和命名上有不同的操作手段,例如将偏差分为“计划偏差”(planned deviation)与“非计划偏差”(unplanned deviation),颇有些司法体系中“一级谋杀罪”(预谋杀人等)与“二级谋杀罪”(有杀人的故意,但其杀人行为并非经预谋或计划)的意味。
他们将计划偏差称为偏差,而把非计划轻微偏差叫做incident(事件)。
其实非计划偏差的主题词已经是“偏差”了,所以它的本质就是偏差。
而如果偏差是计划中的,也就是说,在偏差发生之前就已经预计到了它的出现,那么这个所谓的“计划偏差”就应该属于”change (工艺变化)“。
在GMP 中,不应将任何内容声明为”事先计划的偏差”,那是“变化”,而偏差是计划外的。
所谓的“计划偏差”这个古怪的称谓,它大多存在于许多年前的公司中,而没有在任何地方进行正式定义。
EMA 的一份文件中首次使用了“计划偏差planned deviation”一词。
偏差处理标准管理规程
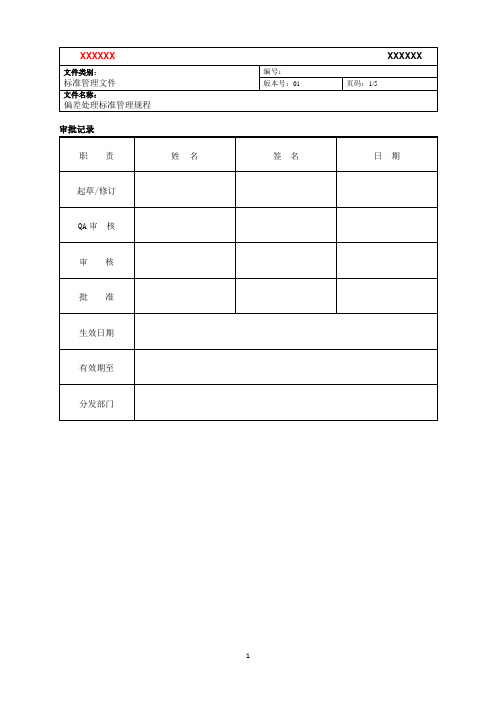
审批记录1目的建立偏差处理管理规程,及时、规范处理偏差,确保产品质量。
2范围适用于研发活动过程中偏离工艺规程或管理要求的偏差。
比如任何偏离生产工艺、质量标准、检验方法、操作规程等,都属于偏差范畴。
4参考文件及文献4.1《药品生产质量管理规范》(2010年修订版)5术语5.1偏差:指偏离已批准的程序(指导文件)、标准或方案的任何情况,如任何偏离生产工艺、物料平衡限度、质量标准、检验方法、操作规程等,均称为偏差。
6内容6.1偏差分类6.1.1根据偏差对药品质量影响程度的大小,将偏差分为以下3类。
6.1.1.1微小偏差:不足以影响产品质量,调查后只需做好相关记录并说明原因,采取纠正措施,必要时可采取预防措施。
6.1.1.2中等偏差:属较重大的偏差,该类偏差可能对产品的质量产生实际或潜在的影响。
必须进行深入的调查,查明原因,采取纠正措施进行整改,必要时可采取预防措施。
6.1.1.3重大偏差:该类偏差可能对产品的质量、安全性或有效性产生严重的后果,必须按规定的程序进行深入调查,查明原因,并提出纠正及预防措施。
6.1.2为了方便对偏差进行定义和参照,对微小偏差、中等偏差、重大偏差分别予以举例说明,具体的案例清单包括但不限于表中的例子。
6.2偏差实施原则6.2.1生产工艺:小试阶段不进行偏差管理;中试阶段需要按此文件进行偏差管理。
6.2.2工艺验证阶段和检验方法转移阶段产生的偏差,按照GMP车间的管理要求进行偏差管理,研发团队参与偏差调查过程,偏差处理完毕后,研发QA需保留偏差处理单复印件。
若仅仅是检验数据有异常,按照《检验异常结果调查管理规程》进行处理。
6.2.3稳定性考察:临床批、验证批、注册批次稳定性考察(影响因素试验、加速试验、长期稳定性考察试验)偏离方案要求的(比如:时间节点偏移、检验项目遗漏等)需进行偏差管理。
6.2.4实验室检验异常:按照《检验异常结果调查管理规程》进行处理,确定为样品原因引起的,临床批、验证批次和注册批启动偏差,其他批次不启动偏差。
生产过程偏差处理程序
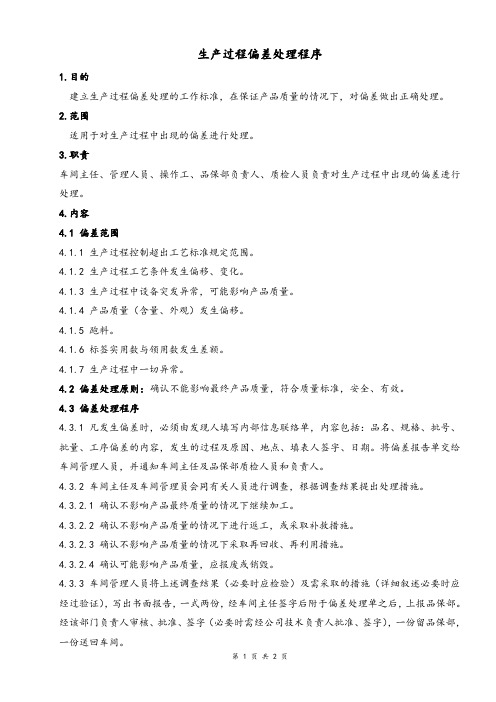
生产过程偏差处理程序1.目的建立生产过程偏差处理的工作标准,在保证产品质量的情况下,对偏差做出正确处理。
2.范围适用于对生产过程中出现的偏差进行处理。
3.职责车间主任、管理人员、操作工、品保部负责人、质检人员负责对生产过程中出现的偏差进行处理。
4.内容4.1 偏差范围4.1.1 生产过程控制超出工艺标准规定范围。
4.1.2 生产过程工艺条件发生偏移、变化。
4.1.3 生产过程中设备突发异常,可能影响产品质量。
4.1.4 产品质量(含量、外观)发生偏移。
4.1.5 跑料。
4.1.6 标签实用数与领用数发生差额。
4.1.7 生产过程中一切异常。
4.2 偏差处理原则:确认不能影响最终产品质量,符合质量标准,安全、有效。
4.3 偏差处理程序4.3.1 凡发生偏差时,必须由发现人填写内部信息联络单,内容包括:品名、规格、批号、批量、工序偏差的内容,发生的过程及原因、地点、填表人签字、日期。
将偏差报告单交给车间管理人员,并通知车间主任及品保部质检人员和负责人。
4.3.2 车间主任及车间管理员会同有关人员进行调查,根据调查结果提出处理措施。
4.3.2.1 确认不影响产品最终质量的情况下继续加工。
4.3.2.2 确认不影响产品质量的情况下进行返工,或采取补救措施。
4.3.2.3 确认不影响产品质量的情况下采取再回收、再利用措施。
4.3.2.4 确认可能影响产品质量,应报废或销毁。
4.3.3 车间管理人员将上述调查结果(必要时应检验)及需采取的措施(详细叙述必要时应经过验证),写出书面报告,一式两份,经车间主任签字后附于偏差处理单之后,上报品保部。
经该部门负责人审核、批准、签字(必要时需经公司技术负责人批准、签字),一份留品保部,一份送回车间。
4.4 车间按批准的措施组织实施。
措施实施过程要在车间管理人员和品保部质检人员的控制下进行,并详细记入批记录,同时将偏差处理单及调查报告和处理措施报告附于批记录之后。
4.5 相关事宜:若调查发现有可能与本批次前后生产批次的产品有关联,则必须立即通知品保部负责人,采取措施停止相关批次的放行。
GMP生产过程偏差处理规定

页码:文件编号:生效日期: 再版日期:第1页/共2页SMP-PM-01004-1标准管理规程STANDARD MANAGEMENT PROCEDURESubject题目:生产过程偏差处理规定Issued by颁发部门:质量部Written by起草人:Date日期:Dept. Head Approval 部门主管审核:Date日期:QA Director Approval QA 主管审核:Date日期:Approved by批准:Date日期:Dispense分发:总经理、质量部、生产部、商务部、行政人事部、财务部1.目的建立生产过程偏差处理规定,在保证产品质量的前提下,对偏差做出正确处理。
2.适用范围适用于生产过程中的偏差。
3.责任者生产部负责人、车间主任、工艺员、相关工序操作工、班组长、现场QA、QA主管、质量部负责人4.内容4.1.生产过程中可能出现的偏差:4.1.1.物料平衡超出收率的合格范围;4.1.2.生产过程时间控制超出工艺规定范围;4.1.3.生产过程工艺条件发生偏移、变化;4.1.4.生产过程中设备发生异常,可能影响产品质量;4.1.5.产品质量发生偏移。
4.2.生产过程中偏差处理程序4.2.1.发现偏差时,发现人及时查找原因,采取措施,使偏差控制在规定的范围内;并立即报告其上级。
页码:文件编号:生效日期: 再版日期:第2页/共2页SMP-PM-01004-1标准管理规程STANDARD MANAGEMENT PROCEDURESubject题目:生产过程偏差处理规定Issued by颁发部门:质量部4.2.2.偏差发现人在采取措施仍不能将偏差控制在规定范围内时,应立即停止生产;所涉及的物料由现场QA贴上SMP-QM-01006-1-R-003《在控物料》标示。
4.2.3.发现人填写SMP-PM-01004-1-R-001《偏差处理记录》二份,写明品名、批号、规格、批量、工序、偏差的内容,发生的过程及原因、地点、填表签字、日期;并交给工艺员,通知生产部及质量部负责人。
GMP偏差处理管理程序

偏差处理管理程序1.目的本文件规定了产品生产全过程和各经营工作中出现偏差的处理程序及要求,以加强对偏差的反馈处理,促进生产和经营工作正常进行。
2.范围及职责本文件适用于产品生产检验工作的全过程和各经营工作系统出现的偏差。
在出现偏差时各部门应严格按此文件执行,本文件正式执行前由各部门经理负责培训本部门员工。
3.定义偏差:在生产、经营工作中不论什么原因所发生的偏离标准(包括物料标准、质量标准、工作标准等);违反各项规程、规定的一切不正常现象,均为偏差。
如:生产操作、产品检验、设备运行、产品销售、物资采购等各方面。
根据在生产、经营工作中发生偏差的现象,将其分为以下四类:3.1物品管理工作中的偏差,如:物料的采购、验收、储存保管、领用发放,包括生产过程中的中间产品、半成品、成品,检验用试剂,留样等各类物品的管理。
3.2仪器、设备、公用系统使用,操作运行中的偏差,如:各部门仪器,设备的使用、操作,空调制水系统的运行,作业环境洁净度、温湿度控制等。
3.3产品生产、检验中的偏差,如:工艺规程、工艺参数、检验规程的制定、执行,产品质量、收率偏离标准的现象等。
3.4业务工作中的偏差,如:工作差错、失误以及违反管理制度规定的工作现象。
4. 处理程序出现偏差应立即进行处理,根据不同类别采取不同的处理程序。
4.1物品管理过程中出现的偏差4.1.1物资部库管员在到货验收时发现不合格,及经质量检定部门判定不合格时,按照《不合格物料的管理办法及处理程序》进行处理。
4.1.2 各物品使用管理部门的库管员,对其所管理的物品同样要做好入库物品品名、规格、数量等验收,记录等工作,如发现不符有权拒绝入库。
4.1.3由于仓库贮存条件达不到物料的贮存条件或发生突然变化时,库管员应及时通知本部门领导和设备部、质保部,由质保部组织分析原因,可能产生的影响和解决措施,设备部负责具体的处理解决工作。
对库存物品需进行复检的,由质检部负责物品检验。
4.1.4各物品库管员应经常检查所保管物品情况,如:发现物品数量、质量等方面发生偏差,应及时报告本部门领导和质保部。
生产过程偏差处理规定

生产过程偏差处理规定生产过程中的偏差是指实际产出与理论产出之间的差异。
在任何生产过程中,由于机器设备、人力资源、原材料和环境等各种因素的影响,都有可能导致生产过程中出现一定程度的偏差。
为了保证产品质量和生产效率,企业需要建立和执行一套科学、合理的生产偏差处理规定。
一、偏差的分类根据偏差的性质和产生的原因,可以将生产过程中的偏差分为系统偏差和偶然偏差两类。
系统偏差是指一种长期或永久性的偏差,由于生产过程中的固有缺陷或长期使用导致的。
偶然偏差是指一种暂时性的偏差,通常是由于一些突发因素引起的,例如操作失误、设备故障等。
二、建立偏差处理规定的目的建立偏差处理规定的主要目的是为了确保产品质量的稳定性和符合相关法规的要求,同时提高生产效率,控制成本。
通过科学合理的偏差处理规定,可以有效地处理生产过程中的偏差,防止偏差进一步扩大,确保产品的质量可控。
三、偏差处理规定的内容1.偏差的监测与记录:建立偏差监测体系,定期对生产过程中的偏差进行监测和记录,包括偏差类型、偏差大小、偏差发生的时间和地点等信息。
通过对偏差的监测与记录,可以清楚了解偏差的产生原因和趋势,为制定有效的偏差处理措施提供依据。
2.偏差的评估与分析:对监测到的偏差进行评估和分析,确定其对产品质量和生产效率的影响程度。
通过评估和分析,可以确定处理偏差的紧急性和重要性,为偏差处理措施的制定和实施提供指导。
3.偏差处理措施的制定和实施:根据偏差的评估和分析结果,制定相应的偏差处理措施。
偏差处理措施可以包括调整生产工艺参数、更换设备、培训操作人员等。
在制定和实施偏差处理措施时,要充分考虑产品质量和生产效率的要求,确保偏差能够得到有效地控制和处理。
4.偏差处理结果的监测与追踪:对实施偏差处理措施的效果进行监测和追踪,确保偏差得到有效地控制和处理。
如果偏差处理措施没有达到预期效果,可以对措施进行调整或再次制定新的偏差处理措施,直到偏差得到有效地控制和处理为止。
药厂偏差处理的流程
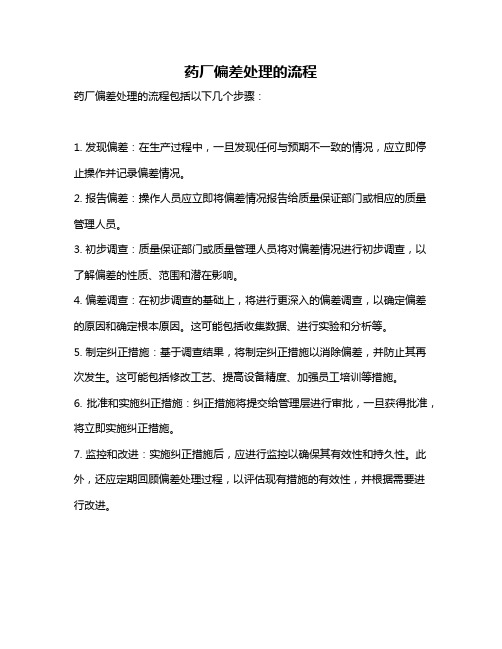
药厂偏差处理的流程
药厂偏差处理的流程包括以下几个步骤:
1. 发现偏差:在生产过程中,一旦发现任何与预期不一致的情况,应立即停止操作并记录偏差情况。
2. 报告偏差:操作人员应立即将偏差情况报告给质量保证部门或相应的质量管理人员。
3. 初步调查:质量保证部门或质量管理人员将对偏差情况进行初步调查,以了解偏差的性质、范围和潜在影响。
4. 偏差调查:在初步调查的基础上,将进行更深入的偏差调查,以确定偏差的原因和确定根本原因。
这可能包括收集数据、进行实验和分析等。
5. 制定纠正措施:基于调查结果,将制定纠正措施以消除偏差,并防止其再次发生。
这可能包括修改工艺、提高设备精度、加强员工培训等措施。
6. 批准和实施纠正措施:纠正措施将提交给管理层进行审批,一旦获得批准,将立即实施纠正措施。
7. 监控和改进:实施纠正措施后,应进行监控以确保其有效性和持久性。
此外,还应定期回顾偏差处理过程,以评估现有措施的有效性,并根据需要进行改进。
8. 记录和报告:在整个偏差处理过程中,应详细记录相关信息,包括偏差的性质、调查结果、采取的纠正措施、实施效果等。
这些记录应定期报告给相关部门和管理层。
请注意,以上流程仅供参考,具体流程可能因药厂而异。
此外,偏差处理还涉及一些法规要求和行业标准,药厂应遵循相关法规和标准的要求进行操作。
生产过程偏差处理规定
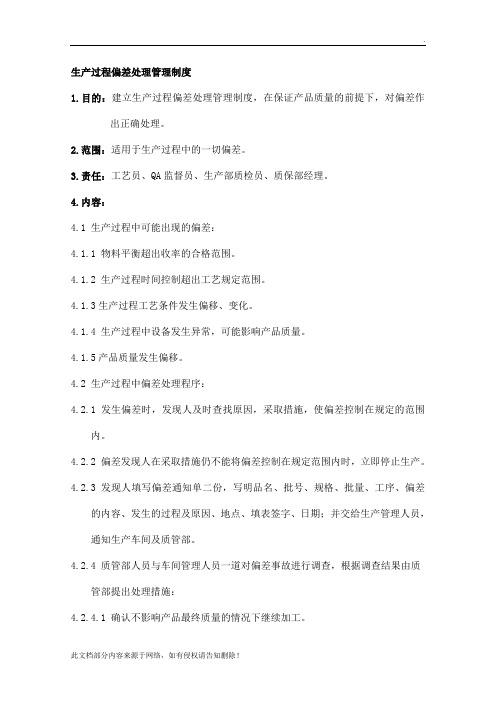
生产过程偏差处理管理制度1.目的:建立生产过程偏差处理管理制度,在保证产品质量的前提下,对偏差作出正确处理。
2.范围:适用于生产过程中的一切偏差。
3.责任:工艺员、QA监督员、生产部质检员、质保部经理。
4.内容:4.1 生产过程中可能出现的偏差:4.1.1 物料平衡超出收率的合格范围。
4.1.2 生产过程时间控制超出工艺规定范围。
4.1.3生产过程工艺条件发生偏移、变化。
4.1.4 生产过程中设备发生异常,可能影响产品质量。
4.1.5产品质量发生偏移。
4.2 生产过程中偏差处理程序:4.2.1 发生偏差时,发现人及时查找原因,采取措施,使偏差控制在规定的范围内。
4.2.2 偏差发现人在采取措施仍不能将偏差控制在规定范围内时,立即停止生产。
4.2.3 发现人填写偏差通知单二份,写明品名、批号、规格、批量、工序、偏差的内容、发生的过程及原因、地点、填表签字、日期;并交给生产管理人员,通知生产车间及质管部。
4.2.4 质管部人员与车间管理人员一道对偏差事故进行调查,根据调查结果由质管部提出处理措施:4.2.4.1 确认不影响产品最终质量的情况下继续加工。
4.2.4.2 确认不影响产品质量的情况下进行返工,或采取补救措施。
4.2.4.3 确认影响产品质量,则报废或销毁。
4.2.5 车间管理人员将调查结果及需采取的措施,记录于偏差通知单上,上报质管部。
4.2.6质量保证部门认真审核偏差调查结果及需采取的措施,最后批准、签字,一份送回生产车间,一份留质保部。
4.2.7生产车间按批准的措施组织实施。
在实施过程中要在生产管理人员和质保部监督员的监控下进行,并记入批记录,同时将偏差通知单附于批记录之后。
4.2.8如调查发现有可能与本批前后生产批次的产品有关联,则必须立即通知质保部负责人,采取措施停止相关批次的放行,直到调查确认与之无关方可放行。
附:偏差通知单。
- 1、下载文档前请自行甄别文档内容的完整性,平台不提供额外的编辑、内容补充、找答案等附加服务。
- 2、"仅部分预览"的文档,不可在线预览部分如存在完整性等问题,可反馈申请退款(可完整预览的文档不适用该条件!)。
- 3、如文档侵犯您的权益,请联系客服反馈,我们会尽快为您处理(人工客服工作时间:9:00-18:30)。
生产偏差处理的七个阶段
第一阶段:对事件的报告
1. 事件观察者发现了任何有可能引发偏差的事件后,应撰写偏差事件报告;或立即向主管报告,由主管或相关人员随后撰写生产偏差事件报告。
2. 发起者应进行初步调查并立即采取纠正措施。
(1)立即采取以下措施(但不仅限于此),以减少事件对生产物料/设备/区域/工艺/程序等的负面影响:
停止生产:GMP相关活动的恢复和继续需质量部的批准。
调查结束前,问题原辅料、包材、中间体或成品应清楚地贴上待验标签或通过在软件系统中控制其待验状态。
任何怀疑有问题的设备、仪器、系统应安放在一个安全的条件下,调查结束后方可使用,如必要,需贴上明显的标签。
通知相关部门人员(如批记录审阅/释放,生产操作,药师药政和
技术服务)。
(2)进行范围影响评估,在生产偏差事件报告中对报告事件应作详细描述(如涉及范围、持续时间、严重性)
3. 确定唯一生产偏差的跟踪号。
4. 生产偏差事件应记录以下项目(包括但不限于):
(1) 产品名称、批号
(2) 发现日期/报告日期
(3) 事件发生日期
(4) 其他相关调查
(5) 事件描述,包括如何发现、在何处发现
(6) 事件发现者和/或报告者
(7) 所有受影响的生产物料/设备/区域/方法/方法/程序
(8) 其他相关记录
(9) 事件分类
(10) 立即采取的措施
第二阶段:偏差事件报告评估
1. 发起部门经理、主管或其代理人负责对事件报告进行评估,确保有关事件的详细内容包含其中,如评估时发现不够详尽,需要立即通知撰写者,撰写者需尽快补充。
2. 质量部过程检查负责人最终评估事件报告,确保包括事件的详细内容包含其中。
如审阅者发现不够详尽,需要通知撰写者,撰写者需尽快补充。
3. 质量部在调查相关部门人员的协助下,评估是否有受事件影响的批次、系统或区域没有在事件报告中报告,如果有,应将它们处于待验状态。
4. 质量部同样需评估过去一段时间(如:一个月)是否发生类似事
件。
如发生过,过去事件的事件报告号需记录。
如果当前事件是一定时间内多次发生,即使符合只报告事件条件,该事件应由质保部评估以确认是否需进入偏差调查程序。
第三阶段:偏差事件报告批准
1.质量部负责人是事件报告的批准人,利用质量分析工具审核和评估事件报告,以确认以下事实:
(1)问题得到了充分和适当的评估
(2)结论合乎逻辑并有调查资料支持
(3)建议的行动得到落实
(4)确定了根本原因
2.质量部根据以下原则将事件报告分类,并在规定的工作日内完成事件报告的评估和批准。
对分类基本原理、所有支持资料或信息,应清楚地描述。
(1)无需根本原因调查事件,及次要生产偏差。
次要生产偏差一般
对生产物料/设备/区域/工艺/程序影响很小或没有影响。
在决定是否需要调查时,应考虑事件本身及周围环境。
一般包括:已知根本原因和纠正预防措施已确认但未完成实施的重复发生事件或已知根本原因、应采取的措施在相关SOP中已有规定的事件。
必须有证据那些特定生产偏差其性质较轻,相关过程或区域完全在控制当中。
(2)如事件属于主要生产偏差或严重生产偏差,需进入调查程序。
第四阶段:主要生产偏差或严重生产偏差的调查
1.总则:调查组长应拥有足够的知识实施调查、确定参与调查相关专家的需求;调查组长根据实际情况决定由技术部、工程部、生产部门等专家组成的调查小组人员。
质量部、技术支持部门和涉及部门人员一般是调查组的成员。
2.调查过程:
(1)确定事件的背景:调查应该包括技术和/或过程的信息,以便清楚阐明和容易理解所有后续的调查部门,该部分必须包括以下内容:
描述调查事件相关的正常操作
描述在调查事件中怎样的作业、与正常作业有无区别
提供相关支持性文件(如设备、设施程序的标准)
(2)通过确定涉及的所有生产物料/设备/区域/工艺等,决定受影响的范围。
评估包括相同产品其他批次、其他可能受影响的产品、一些类似发生情况的分析。
(3)排除或涉及生产物料/设备/程序等方面的原因。
第五阶段:根本原因分析及纠正预防措施的制定
1.数据资料收集
2.数据资料分析
3.分析事实数据、记录和相关的文件,资料可能包括:批记录、设备记录、培训记录、变更控制、调查报告(历史的、第三方的、客户投诉)、校验和维护保养记录和日志、技术或验证报告、环境记录、产品投诉历史、以前鉴定的纠正预防、拒绝批次、通过面谈和观测过
程收集的资料
4.根本原因确定
记录最有可能的根本原因
附上确定和排除这些原因相应的支持文件和收集的资料;
挑战最有可能的根本原因及确保所有相关的数据资料支持结论;
如果原因不确定,需要记录所有可能的原因并进行趋势分析。
5.生产偏差根本原因分类举例:
(1)物料
供应商/合同商问题
规格或测试方法需审阅/修订/删除
物料未反映出本身原有的特性
不适当的物料储存条件(2)设备
维护工作不充足
故障
校准程序,标准或频率不恰当报废,需替代品
设备/设施的设计问题
供应商问题
设备软件问题
(3)工艺方法
工艺步骤/控制参数需要改进
规格或测试方法需要审核/修订/删除标示材料/包装设计需审核/修订
处方需审核/修订
直接接触药品的容器等需要审核(4)文件
文件管理系统
要求使用的文件版本错误
(5)人员
岗位操作问题
特定任务或程序没有培训
培训计划/课程/不足够
工作要求需更明确的说明
6. 根本原因分析结束后,对照根本原因调查结果,调查组长应与成员一起共同确定纠正预防措施。
第六阶段:调查报告的审核和批准
1、相关部门负责人应审核批准调查报告。
2、质量受权人负责最后审核批准主要偏差和重要偏差。
3、审核人和批准人应确保调查是合理的,并确认调查的范围、深度、根本原因和适当的纠正/预防措施。
4、仅可能记录所有的附件和引用的文件。
第七阶段:最终处理
根据调查和纠正预防措施的结果、调查组的最终处理建议、各部门审核意见,质量管理负责人/受权人应作最后批准,并决定有问题的物料、批次、设备、区域或方法的最终处理,记录决定的理由,必要时,定期进行偏差回顾。