金黄庄选煤厂煤泥浮选影响因素分析
金黄庄选煤厂煤泥浮选影响因素分析

金黄庄选煤厂煤泥浮选影响因素分析煤泥浮选是煤炭深度加工过程中一个重要的选矿工艺,它能有效地去除煤炭中的脏杂物,提高煤质的品位和利用价值。
金黄庄选煤厂作为山西省重点骨干企业之一,其煤泥浮选工艺一直受到广泛关注和研究。
本文旨在针对金黄庄选煤厂煤泥浮选影响因素进行深入分析。
煤泥浮选是一种物理化学过程,其实现的关键在于通过给予煤泥浮选药剂,改变其表面性质从而使煤泥与气泡相互作用并发生浮选。
煤泥浮选的影响因素可分为以下几个方面:1. 煤样性质煤的矿物成分、表面性质及颗粒度等都会对煤泥浮选产生重要的影响。
一般来说,煤泥浮选中煤质越好,浮选效果越好。
其中,煤的粒度分布是浮选效果的重要指标之一,一般情况下煤泥的粒度分布应选择在 0.045~0.25mm 的范围内,以获得较好的浮选效果。
2. 浮选药剂浮选药剂是煤泥浮选中必不可少的物质,它包括了捕收剂、起泡剂和调节剂等。
在金黄庄选煤厂的煤泥浮选过程中,多采用了降泡剂、氢氧化钠、乙醇、Q-霉素等药剂。
其中,降泡剂是常用的起泡剂,它能够让气泡形成并吸附于煤泥表面。
但要注意的是,药剂的种类和浓度应根据不同的煤泥类型和处理条件进行合理选择,避免药剂浪费和影响煤泥浮选效率。
3. 浮选环境煤泥浮选环境主要包括了工艺流程、操作参数和水质三个方面。
首先,煤泥浮选的工艺流程应设计合理,确保每一步都能够顺利进行,避免出现工艺瓶颈和环节漏洞。
其次,操作参数的设置应精准可控,主要包括了药剂加入量、溶液 pH 值、气泡尺寸和气泡速度等。
最后,水质对于煤泥浮选也有很大的影响,水质不佳会降低气泡的起泡性能和接触角等,从而影响煤泥的浮选效果。
综上所述,煤泥浮选的影响因素是十分复杂的,需要综合考虑各种因素之间的相互作用,以获取最佳的煤泥浮选效果。
在金黄庄选煤厂的煤泥浮选中,则需要进一步优化浮选工艺流程、合理控制操作参数和加强水质管理,以切实提高煤泥浮选效率和经济效益。
影响浮选机浮选效果的因素

影响浮选机浮选效果的因素
浮选机浮选机主要适用于煤莹石、滑石等有色黑色金属的选别。
在使用过程中如何有效提高浮选机的工作效率,确保浮选机能长时间连续作业,我厂根据数十年的经验,分析哪些因素能影响浮选机浮选效果。
1、混合用药的良好效果是与矿物表面的不均匀性及各种药剂之间的相互作用有关。
矿物表面性质不均匀,氧化程度不一,对不同的捕收剂可能存在有不同的活化区,因而混合用药就可能增加矿物表面捕收剂的覆盖密度,从而改善浮选效果,而各种捕收剂之向的相互作用所产生的共吸附,也可增加药剂的捕收能力,提高浮选指标。
2、气泡的大小对浮选效果有一定影响。
气泡小,则空气弥散的越好,也就增加了气泡表面积及其与矿粒接触的机会,因而对浮选有利,可以改善浮选指标。
但是,如果气泡过小,升浮速度也很小,这样反而有害。
所以,浮选时气泡不能过大,以小为好,但不能过小,否则会影响浮选指标,降低回收率和精矿质量。
3、浮选时不但要求矿物充分单体解离,而且要求有适宜的入选粒度。
矿粒太粗,即使矿物已单体解离,因超过气泡的浮载能力,往往浮不起。
各类矿物的浮选粒度上限不同,如硫化矿物一般为0.2~0.25毫米,非硫化矿物为0.25~0.3毫米,对于一些密度较小的非金属矿如煤等,粒度上限还可以提高。
但是,磨矿粒度过细(如小于0.01毫米)也对浮选不利。
实践证明,各种粒度的浮选行为是有差别的。
矿物粒度太粗和太细都不利于浮选,粗粒和超细粒(矿泥)都具
有许多特殊的物理性质和物理化学性质,它们的浮选行为与一般粒度的矿粒0.001毫米)不同,因此,在浮选过程中要求特殊的工艺条件。
浅谈影响选煤厂煤泥浮选效果的几个关键因素

浅谈影响选煤厂煤泥浮选效果的几个关键因素冯阳【期刊名称】《《选煤技术》》【年(卷),期】2019(000)004【总页数】4页(P53-56)【关键词】矿浆浓度; pH值; 颗粒粒度; 充气量; 气泡尺寸【作者】冯阳【作者单位】山西西山煤电股份有限公司镇城底矿选煤厂山西太原030203【正文语种】中文【中图分类】TD943随着煤炭开采程度的加深和煤炭资源利用率的提高,煤炭生产中细粒煤的含量逐渐增加,使细粒煤的处理成为行业关注的热点。
浮选是细粒煤分选中应用最广泛的方法。
近年来,国内外学者针对影响浮选效果的因素及机理进行了大量的研究。
笔者总结近些年的研究结果,归纳了影响浮选效果的几个关键因素,以为选煤厂优化浮选工艺提供指导借鉴。
1 矿浆性质对浮选的影响浮选精确地说为泡沫浮选,即是利用有用矿物与脉石矿物表面特性差异而进行的物理化学分离过程[1],浮选矿浆中的矿物在经过表面活性剂处理后,强化了矿物之间的表面特性差异,使其更容易被气泡捕集,其中矿浆浓度和溶液pH值会对浮选效果产生影响。
1.1 矿浆浓度对浮选的影响矿浆浓度即矿浆中固体物的含量,杨海昌[2]等研究发现矿浆浓度对浮选效果有一定的影响,当矿浆浓度从60 g/L增加到80 g/L时,浮选可燃体回收率及浮选完善指标的增加幅度很小,并且超过80 g/L还会出现下降的趋势;精矿灰分随着矿浆浓度的增加而增加,当浓度>80 g/L时,精矿灰分曲线增加幅度较大,说明矿浆浓度过大时,浮选不能有效地进行,脉石矿物被有用矿物夹带至泡沫层进行回收,增大了精矿灰分。
在高浓度矿浆条件下,固体物“抱团”凝结,阻碍了药剂与更多固体颗粒接触的机会,从而降低了气泡与固体颗粒接触的概率,使浮选效果变差,故在满足选煤厂正常生产的情况下,应选择浓度较低的矿浆。
1.2 矿浆pH值对浮选的影响矿浆pH值主要影响矿浆中表面活性剂(主要为起泡剂)的活性。
以起泡剂为例,其主要分子结构由亲水的极性基(亲水基)与亲油的非极性基(亲气基)构成:亲水基常由羧酸基、烃基、磺酸基、硫酸基、膦酸基、氨基等组成;亲气基由脂肪族烃基、脂环族烃基和芳香族烃基等组成。
有关煤泥浮选影响因素的分析

中国矿业大学本科生毕业论文姓名:学号:学院:专业:矿物加工工程论文题目:关于煤泥浮选影响因素的研究指导教师:职称:助教2013年 12 月徐州中国矿业大学成人教育学院毕业设计(论文)任务书函授站(点)本部专业年级矿加学生姓名任务下达时期:2013年 9月26日设计(论文)日期:2013年11月20日至 2013年12月25日设计(论文)题目:关于煤泥浮选影响因素的研究设计(论文)专题题目:设计(论文)主要内容和要求:1、查阅国内外文献资料,掌握与课题研究相关研究进展,撰写综述报告,并制定切实可行的研究方案;2、研究煤泥浮选的影响因素,重点说明浮选药剂及浮选的粒度组成对浮选过程的影响3、按照学校规定的格式撰写毕业论文。
字数不少于25000字.指导教师签字:中国矿业大学成人教育学院毕业设计(论文)指导教师评阅书指导教师评语(包含①基础理论及基本技能的掌握;②独立解决实际问题的能力;③研究内容的理论依据和技术方法;④取得的主要成果及创新点;⑤工作态度及工作量;⑥总体评价及建议成绩;⑦存在问题;⑧是否同意答辩等);建议成绩:指导教师签字:年月日中国矿业大学成人教育学院毕业设计(论文)答辩及综合成绩函授站(点) 本部专业年级矿加学生姓名摘要煤泥浮选是利用煤与矸石表面的物理化学性质的差异,并通过添加特定浮选药剂的方法来扩大煤与矸石表面润湿性的差别,在气、固、液三相界面,选择性的富集低灰煤炭,从而实现煤与矸石分离的一种煤泥分选技术。
浮选是煤泥精选最有效、应用最广泛的方法之一。
在精煤产品中约五分之一是通过浮选产生的。
同时煤泥的浮选对选煤厂的煤泥水处理系统起着重要作用。
近年来,煤泥入选量不断增加,精煤质量也需进一步提高,同时仍需改进煤泥水处理方法和减少对环境的污染,因此浮选在选煤中的作用就显得更为重要。
近年来,各国在浮选理论和工艺技术方面的研究工作迅速发展,主要是广泛深入的研究煤的浮选性质,浮选过程的基本行为和作用机理,寻求新的浮选药剂,研制高效大型浮选机,简化浮选工艺系统以及浮选过程的自动检测和控制等。
浮选调节与控制(选煤二班)

(三)药剂量的确定与控制
入料粒度组成变粗,细泥少时:可适当加大人浮煤泥量, 煤浆浓度可调配得高些,此时需较大的加药量,特别是 增加起泡剂的添加量。 人料粒度组成变细,细泥多时:在降低入浮煤浆浓度、 减少入浮煤泥量的同时,应缩减加药量,特别是减少起 泡剂的添加量。
这里所说的加药量是相对比较而言的,从吨煤浮选剂 用量来看,人料粒度组成较粗时,单位用量小;入料粒 度组成较细时,单位用量要增大。
浮选节与控制
讲课人:潘兴谋 班组:选煤二班 时 间:2013年9月27日09:00—11:30
目
录
影响浮选效果的因素
浮选正常主要现象 日常浮选调节依据 浮选机的初步调整 影响因素确定及控制
浮选指标不良的原因分析
一、影响浮选效果的主要因素
• • • • • • 1、入料浓度(80g/l至120g/l); 2、入料粒度组成(0.25-0.075mm); 3、入料流量; 4、刮泡与液位; 5、充气量; 6、药剂制度(加药地点、加药方式、加药量、加药比例、浮选剂与煤浆 接触时间等); • 7、浮选机性能(搅拌强度、矿浆循环量、处理量等); • 8、矿浆液相性质(无机电解质、残余浮选剂、残余絮凝剂、矿浆温度和 PH值等); • 9、浮选流程(准备流程和内部流程)
二、浮选正常主要现象
2至3室,刮入泡沫槽清脆有声,带煤多为粗粒,用手搓 研有很强的“粒度”感觉。
最后一室基本上由虚泡沫组成,气泡大小不等,明显可 见气泡兼并和破灭现象,矿浆表面漂浮着粗糙的泡沫薄 层,泡沫中含高灰细泥较多。
尾矿水因要求的灰分指标及携带的矿物杂资情况不同, 其颜色有黄褐色、灰色、灰黑色之分,基本带泡沫(但 不多),主要是高灰中煤、细泥或粗粒组成。
(三)药剂量的确定与控制
影响浮选的主要因素

目录
• 矿石性质 • 磨矿细度 • 药剂选择与用量 • 充气量与搅拌强度 • 水质与矿浆浓度 • 浮选机与工艺流程
01
矿石性质
矿物组成
矿物种类
不同的矿物具有不同的表面性质和可 浮性,对浮选效果产生影响。例如, 一些矿物表面容易吸附泡沫,而另一 些矿物则难以附着。
矿物共生关系
矿物之间的共生关系也会影响浮选效 果。如果目标矿物与杂质矿物共生紧 密,分离难度会增加。
泥质矿物
某些泥质矿物具有较高的可浮性,容易与目标矿物混淆,对浮选效果产生不良 影响。
02
磨矿细度
磨矿时间
磨矿时间越长,矿石的粒度越细,有利于浮选。但过长的磨矿时间会导致能耗增 加,降低生产效率。因此,需要根据矿石的性质和浮选要求合理选择磨矿时间。
总结词:磨矿时间对浮选效果具有重要影响,合理控制磨矿时间是提高浮选效率 的关键。
总结词:磨矿设备是影响浮选效果的重要因素,选择合适 的磨矿设备是提高浮选效率的关键。
03
药剂选择与用量
捕收剂
捕收剂的选择
捕收剂是影响浮选效果的关键因素之一,需要根据矿物表面的性质选择合适的捕收剂。常用的捕收剂包括黄药、 黑药、白药等。
捕收剂用量
捕收剂的用量对浮选效果也有显著影响。过量的捕收剂可能导致过度的药剂消耗和环境污染,而用量不足则可能 无法充分捕收目标矿物。因此,需要根据实际情况调整捕收剂的用量。
抑制剂
抑制剂种类
抑制剂在浮选过程中用于抑制非目标矿物的活性,提高目标矿物的回收率。常用的抑制剂包括石灰、 水玻璃、淀粉等。
抑制剂用量
抑制剂的用量也需要根据实际情况进行调整,以达到最佳的抑制效果。过量使用抑制剂可能导致目标 矿物受到抑制,降低回收率,而用量不足则可能无法有效抑制非目标矿物。
第五章影响浮选的主要因素
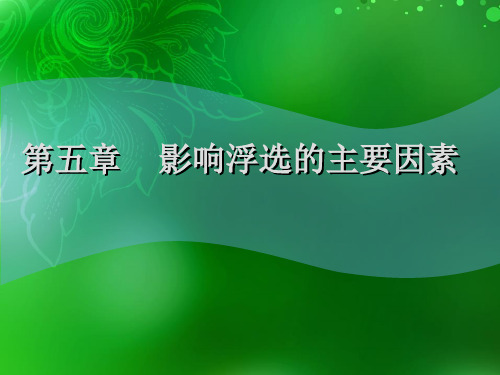
第五章 影响浮选的主要因素
分段加药即把浮选剂分别加在煤浆预处理装置和某个浮选室中。分段加 药适用于较难浮的煤,一般在浮选前加入总量的60-70%,其余的 30-40%加入适当的地点。分段过多不仅增加操作上的麻烦,而且计量 不易准确。
第五章 影响浮选的主要因素
分段加药优点: (1)由于在煤浆预处理装置浮选剂的添加量减少,从而控制了细泥的浮选速度 ,有助于保证精煤质量。 (2)在浮选机内确定一至两个浮选剂添加点,使粗粒表面吸附足够的油类捕收
j (100 Aj ) j Aj
(100 Ar ) Ar
100
(%)
j
100 Ar
Ar Aj Ar
— 浮选精煤灰分,%;
— 浮选入料灰分,%;
— 浮选精煤产率,%。
第五章
影响浮选的主要因素
表2 B选煤厂各生产班的浮选月平均指标
入料 灰分 % 精煤 灰分 % 尾煤 灰分 % 精煤 产率 % 精煤可燃体 回收率 % 精煤非可燃 体回收率 % 浮选完善 指标 %
浮选设备性能对工艺效果影响的因素固定下来。
(2)将浮选机的叶轮转速、浮选剂与煤浆混合搅拌的因素也固定下来。 (3)将捕收剂、起泡剂的单位用量、入浮煤浆浓度、浮选设备的充气量等主 要因素也固定下来,或是通过正交试验确定最优条件。
第五章 影响浮选的主要因素
加煤 搅拌2min,加轻柴油 搅拌2min,加仲辛醇
第五章
影响浮选的主要因素
Ej
j (100 Aj )
100(100 Ar )
100
(%)
浮选精煤的非可燃体混杂率的定义是浮选精煤中的非可燃体占浮选入料中非可 燃体的百分比,则:
j Aj Ew 100 100Ar
第4 浮选因素

第四章煤泥浮选的基本因素煤泥浮选是一个极其复杂的物理化学过程,这一过程包括的因素很多,由于这些因素在浮选过程中相互影响,使得它们的作用更为复杂。
从大的方面说,影响浮选工艺过程的因素很多,可归纳为以下几个主要方面:①矿物的物质组成和化学组成;②矿浆制备;③浮选药剂制度;④浮选机所造成的工作条件;⑤浮选工艺流程。
煤泥浮选影响因素见图4–1所示:图4–1 影响煤泥浮选的工艺因素第一节原煤性质对浮选的影响1.煤的变质程度对浮选的影响按成煤过程中煤的变质程度(或称煤化程度)不同,煤分成不同的煤阶,每个煤阶又分不同煤种。
不同煤阶或煤种具有不同的表面性质和可浮性。
通常,低变质程度的煤具有较高的表面孔隙度和较多的含氧官能团,亲水性较强,可浮性较差;当变质程度增大,煤的排列变得致密,孔隙度降低,表面含氧官能团减少,疏水性增强,在焦煤时可浮性最好;然后,随变质程115度进一步提高,孔隙度又增加,侧链减少,碳链变短,疏水性又降低。
各煤阶的表面疏水性变化也可用接触角的变化来定性说明,即接触角随煤的含碳量增加而增大,在焦煤时达到最大,然后又随含碳量增加而变小,如图4–2。
(a)图4–2各煤阶煤的接触角和孔隙度(a)图4–2各煤阶煤的挥发分、氧、羧基氧和羟基氧的含量(b)L.—褐煤;S.B—次烟煤;H.V.B—高挥发分烟煤;116M.V.B.—中等挥发分烟煤;L.V.B—低挥发分烟煤;A—无烟煤不同煤阶或煤种表面疏水性的变化很难定量解释,目前比较权威和公认的是以煤的工业分析和元素分析的数据为基础的经验式,称为表面成分理论或假说,其要点是认为煤这种不均匀物质由可浮的和不可浮的两组化学成分构成,因此煤的自然可浮性由这两部分的比例所决定,煤表面可浮的成分占优势时,其可浮性变好,反之则变坏。
可浮性成分具有疏水性,非可浮性成分具有亲水性。
按此经验公式计算的可浮性和接触角基本为线性关系。
2.煤的密度组成对浮选的影响通常煤泥中密度越低的部分灰分越低,可浮性越好,所以我国传统上根据煤泥的小浮沉试验来判断煤泥的可浮性及浮选效果。
影响浮选工艺因素

影响浮选工艺的因素有哪些?发布日期:2017-08-15 浏览次数:970影响浮选工艺过程的因素很多,其中较重要的有:磨矿细度、矿浆浓度、浮选时间、药剂制度、矿浆温度、浮选流程、水质、浮选设备类型等。
1、磨矿细度浮选时不但要求矿物单体解离,而且要求适宜的入选粒度。
矿粒太粗,有用矿物尚未单体解离,即使矿物已单体解离,也因其粒度大,重量大,使气泡难以带起或即便带起也易在搅拌时从气泡上脱落。
矿粒太细,不仅增加磨矿费用,而且产生矿泥。
矿泥因其比表面大,且表面活性强而吸附大量浮选药剂或其它矿粒,易恶化浮选过程,使精矿品位和回收率下降,增加药剂消耗。
(1)浮选对细度的要求:①有用矿物基本上达到单体分离;②粗粒单体矿物的粒度,必须小于矿物浮游的粒度上限;③尽可能避免泥化,浮选矿粒的直径小于0.01mm时,浮选指标显著下降,当粒度小于2—5微米时,有用矿物与脉石几乎无法分离。
(2)改善粗粒浮选的措施:①加大充气量,造成较多大气泡或矿浆中析出大量微泡;②适当加强搅拌强度,使矿粒悬浮,提高碰撞几率。
或采用浅槽,减少矿粒脱落几率;③适当增加矿浆浓度;④改进药剂制度。
造成较强疏水性。
(3)改善细粒浮选的措施:①提高分级效率,减少矿泥生成。
一般采用多段破碎、多段闭路磨矿的方法;解质(NaCl、(NH)2SO4等)使脉石矿泥团聚;③分段分批加药,保持矿浆药剂有效浓度;④采用较稀的矿浆浓度;⑤脱泥。
2、矿浆浓度矿浆浓度影响下列工艺指标:(1)回收率。
稀,回收率低;高,回收率高,并达到最大值,超过最大值后,又降低。
主要是充气条件变坏。
(2)精矿质量。
稀,高;浓,低。
(3)药剂用量。
成反比。
(4)浮选的生产能力。
成正比。
(5)浮选时间。
浓,时间长,利于提高回收率和生产能力。
(6)水电消耗。
浓,消耗小。
最适宜的矿浆浓度一般规律是:(1)浮选比重较大的矿物时,采用较浓的矿浆;对比重较小的矿物则用较稀的矿浆;(2)浮选粗粒物料采用较浓的矿浆;而浮选细粒或混状物料则用较稀的矿浆。
第五章影响浮选的主要因素
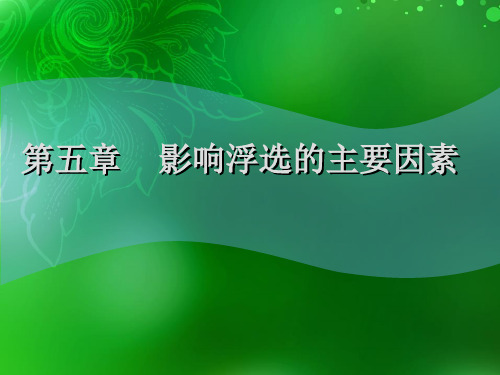
班次
甲
24.48
12.01
71.34
79.02
92.02
39.02
53.00
乙
26.20
11.91
70.08
75.27
89.86
34.22
55.64
丙
25.25
11.48
69.56
75.85
90.08
34.26
55.82
j (100 Aj ) j Aj
(100 Ar ) Ar
100
(%)
j
100 Ar
Ar Aj Ar
— 浮选精煤灰分,%;
— 浮选入料灰分,%;源自— 浮选精煤产率,%。第五章
影响浮选的主要因素
表2 B选煤厂各生产班的浮选月平均指标
入料 灰分 % 精煤 灰分 % 尾煤 灰分 % 精煤 产率 % 精煤可燃体 回收率 % 精煤非可燃 体回收率 % 浮选完善 指标 %
剂,增快其浮选速度,提高可燃体回收率。
(3)以免被细粒级和细泥过多吸附,从而降低了浮选剂用量。
第五章
影响浮选的主要因素
5 浮选流程
煤泥水原则流程 浮选结构流程
5.1 煤泥水原则流程
图4 浓缩浮选原则流程图
第五章
影响浮选的主要因素
煤泥水 (来自于浮选粒度上限控制作业)
煤浆预处理装置
浮选设备
尾煤 澄清浓缩设备
④ 三种浓度之间的换算式:
第五章 影响浮选的主要因素
2.2 结论
一般认为合适的入浮浓度在80g/L左右。 当要求提高分选选择性,降低精煤灰分时,取较低浓度,反之取较高浓度; 当煤泥可浮性差,尤其高灰细泥多时,取较低浓度,反之取较高浓度。 浮选入料浓度的大小,直接影响浮选的生产成本。降低浮选入料浓度固然可以 增强浮选选择性,但浮选剂用量增加,浮选机处理量(按干煤泥计算)下降,电能 消耗(按干煤泥量计算)和稀释水量上升,致使选煤加工成本增加。
影响浮选过程的几种因素

影响浮选过程的几种因素
矿选中的矿浆浓度、原料性质和具体浮选条件都是明显影响各项技术指标和经济指标的
生产过程中,一般遵循大密度、粗粒度的物料的粗作业采用较高浓度,精矿左右采用较低浓度的原则,有利于保证高回收率、高精矿质量和较少药剂量。
矿浆浓度是浮选过程中的重要工艺因素,具体影响如下:
A、精矿质量:矿浆较稀时,精矿质量高;矿浆较浓时,精矿质量随之降低
B、回收率:回收率和矿浆浓度之间有明显的规律性。
矿浆稀时回收率较低,当矿浆浓度逐渐提高并达到最大值,超过最佳的矿浆浓度后回收率又降低。
C、药剂用量:矿降中的药剂浓度适当才能取得好的浮选结果,药剂浓度随矿浆浓度调整。
D、矿浆越浓时,浮选时间越长,浮选机的生产能力增大带来的的是高回收率和水电消耗的加大。
金黄庄选煤厂细煤泥浮选存在问题分析

金黄庄选煤厂细煤泥浮选存在问题分析本文对金黄庄选煤厂细煤泥进行各种相关试验分析,研究结果表明:金黄庄选煤厂浮选入料浓度偏高,浮选环节需进行优化,浮选入料加配稀释水,将浮选入料浓度降至60g/L左右为宜。
關键词:金黄庄选煤厂;细煤泥浮选;分步释放安徽金黄庄矿业有限公司选煤厂是一座矿井型选煤厂,该矿生产的煤泥粒度比较细,且细粒级的灰分较高,各密度级产率和灰分有明显的变化,属于极难选煤泥,浮选精煤很难达到灰分12%以下的产品要求[1]。
1 细煤泥可选性试验1.1 细煤泥现场浮选结果生产现场浮选煤泥浓度经测定通常大于110g/L,通过对浮选入料、精煤和尾煤进行小筛分试验结果如表1所示。
由表1可知:(1)浮选入料筛分结果可以看出入料的粗颗粒较多,结合浮选精煤可知浮选柱对粗颗粒回收效果不佳,尾煤跑粗严重;(2)浮选精煤筛分结果可以看出-0.25mm尤其是-0.045mm有不错的分选效果。
1.2 细煤泥浮沉试验结果由表2可知:-1.8g/cm3密度级以下浮物产率高达78.76%,而灰分只有17.30%;-2.0g/cm3密度级以下浮物产率高达84.38%,而灰分只有19.67%,说明细煤泥解离较好。
2 细煤泥实验室浮选试验试验煤泥水浓度设定为110g/L,采用选煤厂浮选药剂及药剂制度,浮选结果如果表3所示。
由表3可知:(1)从100g/t开始随着药剂量的增加精煤产率和灰分都在逐渐增加,精煤灰分较高;(2)常规浮选机实验结果显示浮选机不能满足其灰分要求。
3 改进方案通过上述分析可知,浮选入料浓度偏高,浮选环节需进行优化,建议更换为矿浆预处理器;浮选入料需加配稀释水,原系统带有配水管,通过现场调试煤泥浮选入料浓度60g/L左右效果较好。
参考文献:[1]孙晋升.金黄庄选煤厂煤泥浮选影响因素分析[J].山东工业技术,2019(10):97.[2]荣国强,吴迪,张友飞,李明.高灰难选煤泥浮选降灰试验研究[J].选煤技术,2018(06):55-59.[3]杨秀秀.影响煤泥浮选工艺效果的主要因素分析[J].选煤技术,2018(04):70-73+77.作者简介:孙晋升(1987-),男,山东枣庄人,本科,助理工程师,生产副厂长,技术副厂长,研究方向:煤泥浮选技术。
影响浮选工艺的因素
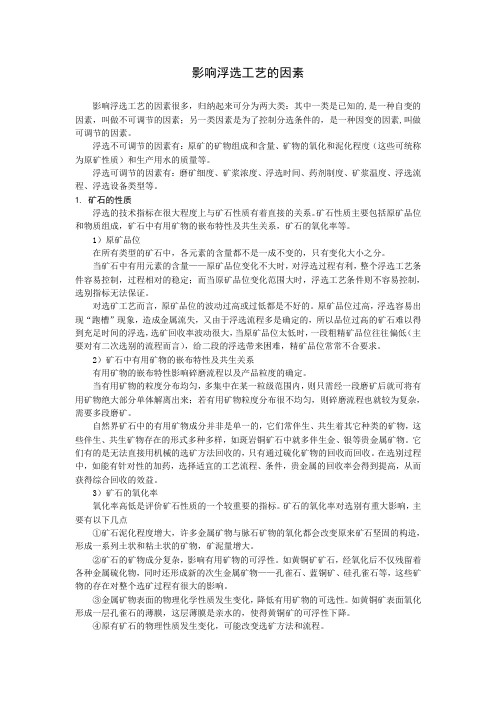
影响浮选工艺的因素影响浮选工艺的因素很多,归纳起来可分为两大类:其中一类是已知的,是一种自变的因素,叫做不可调节的因素;另一类因素是为了控制分选条件的,是一种因变的因素,叫做可调节的因素。
浮选不可调节的因素有:原矿的矿物组成和含量、矿物的氧化和泥化程度(这些可统称为原矿性质)和生产用水的质量等。
浮选可调节的因素有:磨矿细度、矿浆浓度、浮选时间、药剂制度、矿浆温度、浮选流程、浮选设备类型等。
1. 矿石的性质浮选的技术指标在很大程度上与矿石性质有着直接的关系。
矿石性质主要包括原矿品位和物质组成,矿石中有用矿物的嵌布特性及共生关系,矿石的氧化率等。
1)原矿品位在所有类型的矿石中,各元素的含量都不是一成不变的,只有变化大小之分。
当矿石中有用元素的含量——原矿品位变化不大时,对浮选过程有利,整个浮选工艺条件容易控制,过程相对的稳定;而当原矿品位变化范围大时,浮选工艺条件则不容易控制,选别指标无法保证。
对选矿工艺而言,原矿品位的波动过高或过低都是不好的。
原矿品位过高,浮选容易出现“跑槽”现象,造成金属流失,又由于浮选流程多是确定的,所以品位过高的矿石难以得到充足时间的浮选,选矿回收率波动很大,当原矿品位太低时,一段粗精矿品位往往偏低(主要对有二次选别的流程而言),给二段的浮选带来困难,精矿品位常常不合要求。
2)矿石中有用矿物的嵌布特性及共生关系有用矿物的嵌布特性影响碎磨流程以及产品粒度的确定。
当有用矿物的粒度分布均匀,多集中在某一粒级范围内,则只需经一段磨矿后就可将有用矿物绝大部分单体解离出来;若有用矿物粒度分布很不均匀,则碎磨流程也就较为复杂,需要多段磨矿。
自然界矿石中的有用矿物成分并非是单一的,它们常伴生、共生着其它种类的矿物,这些伴生、共生矿物存在的形式多种多样,如斑岩铜矿石中就多伴生金、银等贵金属矿物。
它们有的是无法直接用机械的选矿方法回收的,只有通过硫化矿物的回收而回收。
在选别过程中,如能有针对性的加药,选择适宜的工艺流程、条件,贵金属的回收率会得到提高,从而获得综合回收的效益。
影响浮选过程的因素都有哪些?

影响浮选过程的因素都有哪些?浮选的全名叫做泡沫浮选,是依据各种矿物表面性质的差异,从矿浆中借助于气泡的浮力来选分矿物的过程。
浮选的具体过程就是将一定浓度的矿浆加入各种浮选药剂,在浮选机内经搅拌与充气产生大量弥散气泡。
这时悬浮状态的矿粒与气泡碰撞,一部分可浮性好的矿粒附着在气泡上,上浮至矿液面形成泡沫产品,这就是精矿;不浮矿物留在矿浆内,变成尾矿,从而达到分选的目的。
浮选在进行的过程当中容易受到一些因素的影响,这些因素包括磨矿细度、矿浆浓度、矿浆酸碱度、药剂制度、充气与搅拌、浮选时间、水质等工艺因素。
下面详细介绍下这些影响浮选过程的因素。
一、磨矿细度在浮选中对磨矿细度的要求包括:1、有用矿物基本上单体解离。
2、粗粒单体矿粒粒度,必须小于矿物浮选的粒度上限。
目前,浮选粒度上限,对硫化矿物一般为0.25-0.3毫米;自然硫为0.5-1毫米;煤的粒度上限为1-2毫米。
3、尽可能避免泥化。
当浮选矿粒粒度小于0.01毫米时,浮选指标会显著恶化。
要想得到最合适的磨矿细度必须通过试验和参考生产实践数据来确定。
对于某些矿石,经常采用阶段磨矿与阶段选别流程,避免矿石出现过粉碎,从而及时选出已解离矿粒。
二、矿浆浓度矿浆浓度是影响浮选指标的主要因素之一。
适宜的矿浆浓度要根据矿石性质和浮选条件来确定:浮选比重较大或粒度较粗的矿物应采用较浓矿浆,这样能提高回收率和减少浮选药剂的消耗。
精选作业采用较稀矿浆,这样利于获得高质量的精矿,但有得就有失,在获得精矿的同时,药剂用量、水电消耗以及处理每吨矿石所需的浮选槽容积都要增加,这些都会影响到选矿成本。
三、矿浆的酸碱度矿浆酸碱度指矿浆中OH-与H+的浓度,一般用PH值表示。
各种矿物在使用不同浮选(XKFXJ)剂进行浮选时,都有一个“浮”与“不浮”的PH值,叫做临界PH值。
控制临界PH值,就能控制各种矿物的有效分选。
因此,控制矿浆的PH值,是控制浮选工艺过程的重要措施之一。
四、药剂制度浮选过程中加入药剂的种类和数量、加药地点和加药方式统称为药剂制度,也称药方。
浮选工艺的影响因素

浮选工艺的影响因素
浮选工艺的影响因素有以下几个:
1. 矿石矿物特性:矿石的矿物成分、粒度分布、硬度、密度等特性会影响浮选工艺的选择。
不同矿物具有不同的浮选特性,因此需要根据矿石矿物特性来确定浮选剂和操作条件。
2. 浮选剂选择:浮选剂是浮选过程中的关键因素之一。
浮选剂的选择要考虑到矿石矿物的浮选特性,如选择合适的药剂类型、用量和浓度,以及药剂的pH值、温度等条件。
3. 搅拌条件:搅拌条件对浮选过程的效果有很大的影响。
适当的搅拌可以使浮选剂充分与矿石矿物接触,增加气泡与固体颗粒的接触机会,提高浮选效率。
4. 气体分散条件:气体分散条件也会影响浮选效果。
适当的气体分散可以使气泡均匀地散布在悬浮物中,提高气泡与矿石矿物之间的接触,有利于矿物的浮选。
5. 机械设备:浮选过程中需要使用适当的机械设备,如浮选机、搅拌器等。
设备的设计和性能会直接影响浮选的效果和产量。
6. 水质:水质的影响也是浮选工艺中需要考虑的因素之一。
水质的pH值、硬度以及其中的杂质等会影响浮选剂的效果和矿石矿物的浮选。
综上所述,浮选工艺受到矿石矿物特性、浮选剂选择、搅拌条件、气体分散条件、机械设备和水质等多个因素的影响。
针对不同矿石和浮选目标,需要综合考虑这些因素,选择合适的工艺条件和操作参数。
影响浮选工艺标准的因素

影响浮选工艺的因素影响浮选工艺的因素很多,归纳起来可分为两大类:其中一类是已知的,是一种自变的因素,叫做不可调节的因素;另一类因素是为了控制分选条件的,是一种因变的因素,叫做可调节的因素。
浮选不可调节的因素有:原矿的矿物组成和含量、矿物的氧化和泥化程度(这些可统称为原矿性质)和生产用水的质量等。
浮选可调节的因素有:磨矿细度、矿浆浓度、浮选时间、药剂制度、矿浆温度、浮选流程、浮选设备类型等。
1. 矿石的性质浮选的技术指标在很大程度上与矿石性质有着直接的关系。
矿石性质主要包括原矿品位和物质组成,矿石中有用矿物的嵌布特性及共生关系,矿石的氧化率等。
1)原矿品位在所有类型的矿石中,各元素的含量都不是一成不变的,只有变化大小之分。
当矿石中有用元素的含量——原矿品位变化不大时,对浮选过程有利,整个浮选工艺条件容易控制,过程相对的稳定;而当原矿品位变化范围大时,浮选工艺条件则不容易控制,选别指标无法保证。
对选矿工艺而言,原矿品位的波动过高或过低都是不好的。
原矿品位过高,浮选容易出现“跑槽”现象,造成金属流失,又由于浮选流程多是确定的,所以品位过高的矿石难以得到充足时间的浮选,选矿回收率波动很大,当原矿品位太低时,一段粗精矿品位往往偏低(主要对有二次选别的流程而言),给二段的浮选带来困难,精矿品位常常不合要求。
2)矿石中有用矿物的嵌布特性及共生关系有用矿物的嵌布特性影响碎磨流程以及产品粒度的确定。
当有用矿物的粒度分布均匀,多集中在某一粒级范围内,则只需经一段磨矿后就可将有用矿物绝大部分单体解离出来;若有用矿物粒度分布很不均匀,则碎磨流程也就较为复杂,需要多段磨矿。
自然界矿石中的有用矿物成分并非是单一的,它们常伴生、共生着其它种类的矿物,这些伴生、共生矿物存在的形式多种多样,如斑岩铜矿石中就多伴生金、银等贵金属矿物。
它们有的是无法直接用机械的选矿方法回收的,只有通过硫化矿物的回收而回收。
在选别过程中,如能有针对性的加药,选择适宜的工艺流程、条件,贵金属的回收率会得到提高,从而获得综合回收的效益。
煤泥浮选因素的研究

Page 17
Page 16
关于煤泥浮选影响因素的研究
致
研究概述 研究框架 研究内容 研究结论 写作收获 致 谢
谢
在此特别感谢我的论文指导盖艳武 老师。
其治学严谨、平易近人。在论文的
每一个环节,都对笔者悉心指导和帮 助。提出了很多宝贵的意见,并为论 文的修改和最后的定稿花费了大量心 血。 谨在此致以深深的谢意。
浮选流程内部结构是指浮选循环内部的粗选、精选、扫选 次数以及中矿的处理方式。
Page 15
结论
本文综述了当前煤泥浮选影响因素研究的最新进展,并重 点研究了煤泥粒度组成、浮选药剂、搅拌与充气量、浮选 流程等因素对煤泥浮选效果影响的规律。浮选药剂因素则 重点分析了煤泥浮选最常用的捕收剂、起泡剂和调整剂的 作用原理、常用的药剂种类、在矿浆中的作用及对煤泥浮 选的影响。粒度组成因素则就不同粒级对可浮性的影响和 细泥对浮选效果的影响两个方面进行了重点分析。了解并 掌握这些影响浮选的因素,可使浮选过程顺利进行并达到 最佳的分选效果,从而改善和稳定产品质量,提高生产效 率和经济效益。。
Page 6
第三部分:影响煤泥浮选的自身因素
原煤性质对浮选的影响 粒度特性对浮选的影响 煤浆浓度对浮选的影响
Page 7
原煤性质对浮选的影响
(1)随着煤化程度的增加,煤的天然可浮性先增大后减小 。 (2)通常煤泥中密度越低的部分灰分越低,可浮性越好。 (3)煤颗粒表面显微组分对可浮性影响显著,通常镜质组 分含量越高,煤的可浮性越好。 (4)煤中主要影响其可浮性的矿物质有两类:泥质矿物和 硫化矿物。细泥含量高时,应采用低浓度,高油比,浅刮 泡,一次完的操作制度。
Page 8
粒度特性对浮选的影响
影响浮选选矿和磁选选矿效果的因素

立志当早,存高远影响浮选选矿和磁选选矿效果的因素在选矿中,影响浮选选矿和磁选选矿的因素还是很好总结的,可以分别从以下几个方面来看:影响浮选机浮选效果的因素有:浮选机用药:混合用药的良好效果是与矿物表面的不均匀性及各种药剂之间的相互作用有关。
矿物表面性质不均匀,氧化程度不一,对不同的捕收剂可能存在有不同的活化区,因而混合用药就可能增加矿物表面捕收剂的覆盖密度,从而改善浮选效果,而各种捕收剂之向的相互作用所产生的共吸附,也可增加药剂的捕收能力,提高浮选指标。
气泡特征:气泡的大小对浮选效果有一定影响。
气泡小,则空气弥散的越好,也就增加了气泡表面积及其与矿粒接触的机会,因而对浮选有利,可以改善浮选指标。
但是,如果气泡过小,升浮速度也很小,这样反而有害。
所以,浮选时气泡不能过大,以小为好,但不能过小,否则会影响浮选指标,降低回收率和精矿质量。
影响磁选机磁选效果的重要因素:矿浆浓度:矿浆浓度是影响磁选机磁选效果的重要因素,主要是指分级机溢流浓度大小。
如果矿浆浓度过大,造成分选浓度过高,就会严重影响精矿质量。
因为此时精矿颗粒容易被较细的脉石颗粒覆盖和包裹分选不开,一起选上来使品位降低。
矿浆浓度过小即分选浓度过低,又会造成流速增大选别对间缩短,使一些本来有机会应该上来的细小磁性颗粒,落入尾矿使尾矿品位增高,造成损失。
所以,矿浆浓度要根据需要调整好。
在磁选机处调整主要是靠给矿吹散水的大小来调整,然而最主要的是分级溢流浓度必须根据磁选要求来完成。
给入矿浆浓度最大不能超过35%,一般控制在30%左右,要根据实际情况具体确定。
给矿粒度:影响磁选机磁选效果最重要的因素就是给入磁选的给矿粒度。
给矿粒度的粗细对大部分矿石来说,标志着矿石单体分离度的大小即磁性矿粒与脉石颗粒分离的程度。
如果给入矿石粒度小,说明矿物单体分离度高,。
分析煤泥分级浮尘产生原因及改进方法

分析煤泥分级浮尘产生原因及改进方法1 分级小浮沉试验方法简介1.1 分级小浮沉试验的重要性分级小浮沉试验是指对于粒级为0.5mm以下的煤泥小颗粒进行浮沉分级处理的方法,分级处理浮沉试验方法与其他煤块的处理方法基本类似,它是选择煤层的一项作为基本的工作。
随着现在采煤以及煤炭分层精选处理技术的发展,处理好小浮沉显得尤为重要。
企业可以利用煤泥小浮沉的基本特性来对于煤层的选择性进行评定,也可以根据小浮沉分级处理结果来改进煤泥精选工艺流程。
目前,我国采煤、选煤过程中对于分级精选工艺流程广泛使用,而不进行分级的煤粉颗粒远远达不到工业生产的基本要求,也只有改进分级处理工艺以及细化煤泥小浮沉的基本流程,才能促进我国煤炭相关行业的发展与进步。
1.2 分级小浮沉试验中存在的问题及其形成原因我国GB/T19092-2003有关煤泥浮沉处理试验的方法规定中指出,精选工作人员需要分别对于粒级为0.125~0.25mm以及0.25~0.5mm等的煤粉颗粒进行分级处理,但经过实验人员的重复多次试验发现,粒级为0.25~0.5mm的煤粉浮沉分级处理中存在严重的污染问题。
试验人员在试验结束分离时,进行分离悬浮液以及底部沉淀物质时,会出现一些0.25~0.5mm粒级的煤粉浮沉随之进入分离产物中。
但是对于其他粒级的煤粉颗粒来说,不仅重产物与上层悬浮液体明显分离,而且在倒出分离液体时,煤粉并没有对产物产生污染。
为了改进分级小浮沉试验方法,尽量减少由于试验人员的操作对于结果的影响,我们翻阅国内外有关小浮沉处理方法的文献,并对分级处理试验过程提出一些改进意见,比如试验人员在进行导出上层悬浮液时,要尽量高速稳定地转动离心管,以防备下层沉淀物中的重液对于上层悬浮液的污染。
2 重力力场下的分级小浮沉试验方法2.1 重力小浮沉分级处理的试验准备工作首先,这种方法主要适用于粒级在0.25~0.5mm之间的煤泥小浮沉进行分级处理。
其次,我们在分级处理时,主要采用的四氯化碳、苯等有机化学试剂进行煤泥颗粒分离。
影响浮选工艺因素

影响浮选工艺的因素有哪些?发布日期:2017-08-15 浏览次数:970影响浮选工艺过程的因素很多,其中较重要的有:磨矿细度、矿浆浓度、浮选时间、药剂制度、矿浆温度、浮选流程、水质、浮选设备类型等。
1、磨矿细度浮选时不但要求矿物单体解离,而且要求适宜的入选粒度。
矿粒太粗,有用矿物尚未单体解离,即使矿物已单体解离,也因其粒度大,重量大,使气泡难以带起或即便带起也易在搅拌时从气泡上脱落。
矿粒太细,不仅增加磨矿费用,而且产生矿泥。
矿泥因其比表面大,且表面活性强而吸附大量浮选药剂或其它矿粒,易恶化浮选过程,使精矿品位和回收率下降,增加药剂消耗。
(1)浮选对细度的要求:①有用矿物基本上达到单体分离;②粗粒单体矿物的粒度,必须小于矿物浮游的粒度上限;③尽可能避免泥化,浮选矿粒的直径小于0.01mm时,浮选指标显著下降,当粒度小于2—5微米时,有用矿物与脉石几乎无法分离。
(2)改善粗粒浮选的措施:①加大充气量,造成较多大气泡或矿浆中析出大量微泡;②适当加强搅拌强度,使矿粒悬浮,提高碰撞几率。
或采用浅槽,减少矿粒脱落几率;③适当增加矿浆浓度;④改进药剂制度。
造成较强疏水性。
(3)改善细粒浮选的措施:①提高分级效率,减少矿泥生成。
一般采用多段破碎、多段闭路磨矿的方法;解质(NaCl、(NH)2SO4等)使脉石矿泥团聚;③分段分批加药,保持矿浆药剂有效浓度;④采用较稀的矿浆浓度;⑤脱泥。
2、矿浆浓度矿浆浓度影响下列工艺指标:(1)回收率。
稀,回收率低;高,回收率高,并达到最大值,超过最大值后,又降低。
主要是充气条件变坏。
(2)精矿质量。
稀,高;浓,低。
(3)药剂用量。
成反比。
(4)浮选的生产能力。
成正比。
(5)浮选时间。
浓,时间长,利于提高回收率和生产能力。
(6)水电消耗。
浓,消耗小。
最适宜的矿浆浓度一般规律是:(1)浮选比重较大的矿物时,采用较浓的矿浆;对比重较小的矿物则用较稀的矿浆;(2)浮选粗粒物料采用较浓的矿浆;而浮选细粒或混状物料则用较稀的矿浆。
- 1、下载文档前请自行甄别文档内容的完整性,平台不提供额外的编辑、内容补充、找答案等附加服务。
- 2、"仅部分预览"的文档,不可在线预览部分如存在完整性等问题,可反馈申请退款(可完整预览的文档不适用该条件!)。
- 3、如文档侵犯您的权益,请联系客服反馈,我们会尽快为您处理(人工客服工作时间:9:00-18:30)。
金黄庄选煤厂煤泥浮选影响因素分析
煤泥是煤矿产业中废料处理的一部分,而煤泥浮选是煤泥处理过程中的关键环节之一。
煤泥浮选影响因素的分析对于优化煤泥浮选工艺、提高煤泥浮选效率具有重要的意义。
下
面将从煤泥浮选液性状、煤泥浮选药剂和煤泥颗粒特性三个方面对煤泥浮选影响因素进行
分析。
煤泥浮选液性状是影响煤泥浮选效果的重要因素之一。
煤泥浮选液性状主要包括浮选
液的粘度、浮选液的密度和浮选液的pH值。
浮选液的粘度越大,会使煤泥浮选速度变慢,从而影响浮选效果;浮选液的密度越大,煤泥的沉降速度就越快,从而影响浮选效果;浮
选液的pH值的变化会改变矿浆中煤泥表面的电性质,从而影响煤泥与药剂的吸附和浮选效果。
煤泥浮选药剂是影响煤泥浮选效果的关键因素之一。
浮选药剂主要包括捕收剂、发泡
剂和调整剂。
捕收剂的添加可以增加煤泥与气泡的结合能力,从而提高煤泥浮选率;发泡
剂的添加可以增加气泡的稳定性,从而提高煤泥浮选速度;调整剂的添加可以调控浮选液
的性状,从而优化煤泥浮选条件。
煤泥颗粒特性是影响煤泥浮选效果的重要因素之一。
煤泥颗粒特性主要包括煤泥颗粒
大小、煤泥颗粒形状和煤泥颗粒组成。
煤泥颗粒大小的变化会影响煤泥与气泡的接触机会,从而影响煤泥浮选效果;煤泥颗粒形状的变化会影响气泡在煤泥表面的附着情况,从而影
响煤泥浮选效果;煤泥颗粒组成的变化会影响捕收剂的选择和使用量,从而影响煤泥浮选
效果。
煤泥浮选影响因素主要包括煤泥浮选液性状、煤泥浮选药剂和煤泥颗粒特性三个方面。
在煤泥浮选过程中,合理调控煤泥浮选液性状、选择适当的浮选药剂和优化煤泥颗粒特性
都可以提高煤泥浮选效率,达到资源利用和环境保护的双重目标。