煤化工项目合成气制甲醇装置总体设计和基础设计技术
年产30万吨合成甲醇项目初步设计说明书
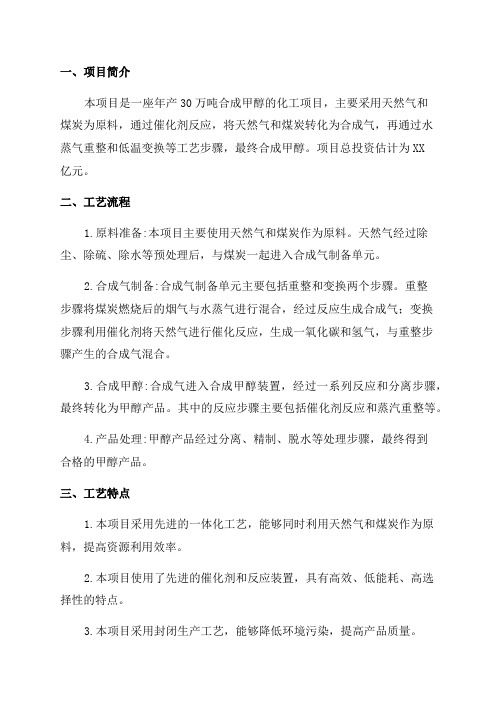
一、项目简介本项目是一座年产30万吨合成甲醇的化工项目,主要采用天然气和煤炭为原料,通过催化剂反应,将天然气和煤炭转化为合成气,再通过水蒸气重整和低温变换等工艺步骤,最终合成甲醇。
项目总投资估计为XX亿元。
二、工艺流程1.原料准备:本项目主要使用天然气和煤炭作为原料。
天然气经过除尘、除硫、除水等预处理后,与煤炭一起进入合成气制备单元。
2.合成气制备:合成气制备单元主要包括重整和变换两个步骤。
重整步骤将煤炭燃烧后的烟气与水蒸气进行混合,经过反应生成合成气;变换步骤利用催化剂将天然气进行催化反应,生成一氧化碳和氢气,与重整步骤产生的合成气混合。
3.合成甲醇:合成气进入合成甲醇装置,经过一系列反应和分离步骤,最终转化为甲醇产品。
其中的反应步骤主要包括催化剂反应和蒸汽重整等。
4.产品处理:甲醇产品经过分离、精制、脱水等处理步骤,最终得到合格的甲醇产品。
三、工艺特点1.本项目采用先进的一体化工艺,能够同时利用天然气和煤炭作为原料,提高资源利用效率。
2.本项目使用了先进的催化剂和反应装置,具有高效、低能耗、高选择性的特点。
3.本项目采用封闭生产工艺,能够降低环境污染,提高产品质量。
4.本项目设计了完善的废物处理装置,实现了废物的资源化利用,减少了对环境的影响。
五、经济效益分析1.本项目年产30万吨甲醇,主要销售给化工企业作为原材料。
根据市场调研和产品定价,预计年销售收入为XX亿元。
2.本项目投资估计为XX亿元,预计投资回收期为X年,静态投资回收率为X%。
3.本项目能够提供大量的就业机会,促进当地经济发展。
六、风险分析1.天然气和煤炭市场价格波动风险。
2.环保政策和法规调整风险。
3.技术创新和市场需求变化风险。
4.合作伙伴风险及市场竞争风险。
七、总结本项目的初步设计说明书详细介绍了年产30万吨合成甲醇的工艺流程、工艺特点、经济效益分析和风险分析等方面。
该项目将利用先进的工艺装置和催化剂,通过合成气制备和反应步骤,将天然气和煤炭转化为合成甲醇,可提供大量就业机会和促进当地经济发展。
煤焦气制甲醇合成工艺装置设计
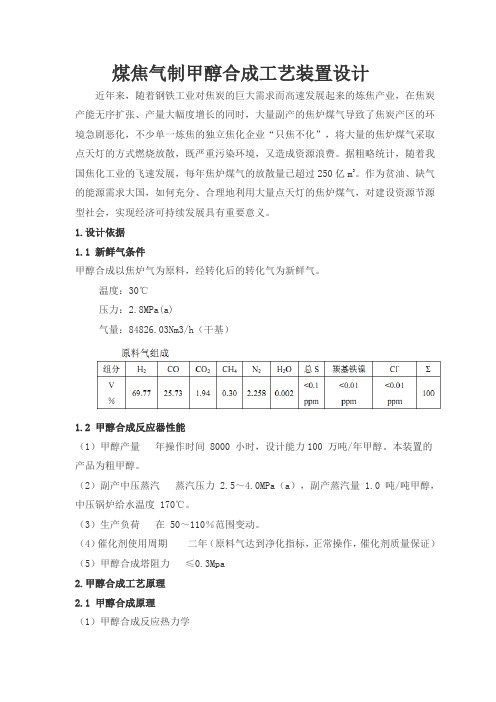
煤焦气制甲醇合成工艺装置设计近年来,随着钢铁工业对焦炭的巨大需求而高速发展起来的炼焦产业,在焦炭产能无序扩张、产量大幅度增长的同时,大量副产的焦炉煤气导致了焦炭产区的环境急剧恶化,不少单一炼焦的独立焦化企业“只焦不化”,将大量的焦炉煤气采取点天灯的方式燃烧放散,既严重污染环境,又造成资源浪费。
据粗略统计,随着我国焦化工业的飞速发展,每年焦炉煤气的放散量已超过250亿m3。
作为贫油、缺气的能源需求大国,如何充分、合理地利用大量点天灯的焦炉煤气,对建设资源节源型社会,实现经济可持续发展具有重要意义。
1.设计依据1.1 新鲜气条件甲醇合成以焦炉气为原料,经转化后的转化气为新鲜气。
温度:30℃压力:2.8MPa(a)气量:84826.03Nm3/h(干基)1.2 甲醇合成反应器性能(1)甲醇产量年操作时间 8000 小时,设计能力100 万吨/年甲醇。
本装置的产品为粗甲醇。
(2)副产中压蒸汽蒸汽压力 2.5~4.0MPa(a),副产蒸汽量 1.0 吨/吨甲醇,中压锅炉给水温度 170℃。
(3)生产负荷在 50~110%范围变动。
(4)催化剂使用周期二年(原料气达到净化指标,正常操作,催化剂质量保证)(5)甲醇合成塔阻力≤0.3Mpa2.甲醇合成工艺原理2.1 甲醇合成原理(1)甲醇合成反应热力学CO、CO2加H2为复合反应体系,CO、CO2均可加H2合成CH3OH,CO与H2除生成CH3OH外,还可生成一系列化合物。
在压力5.0、5.7MPa(a)、温度200~270℃的范围内,求得甲醇、一氧化碳、二氧化碳的平衡组成,分别由下表所示。
(2)甲醇合成催化剂与反应动力学我国甲醇催化剂目前有C307、XNC98等型号,国外催化剂有Katalco51-8、MK121,其物化性能见下表:加氢合成甲醇的动力学方程为:在铜基催化剂上,CO、CO22.2 主要操作条件(1)温度从化学平衡考虑,温度提高,对平衡不利;从动力学考虑,温度提高,反应速率加快。
煤化工项目合成气制甲醇装置总体设计和基础设计技术

神华包头煤化工项目合成气制甲醇装置总体设计和基础设计技术附件合同编号(业主):S K C C*-C-M S-C-06001-00合同编号(承包商):S H-2006-07业主:包头神华煤化工有限公司承包商:华陆工程科技有限责任公司2006年月日目录附件1 工艺描述附件2 设计基础附件3 设计原则、标准和规范附件4 工作范围和服务内容附件5 甲方提供的设计基础资料附件6 设计文件及交付附件7 工作执行计划及重要会议附件8 组织机构及主要人员配备附件9 人工时费附件10 履约保函模板附件1 工艺描述1.1 概述甲方拟在内蒙古自治区包头市九原区工业开发区建设神华包头煤化工项目(以下简称“项目”)。
该项目是以煤为原料生产甲醇,甲醇通过MTO装置转化为烯烃,烯烃聚合生产出聚丙烯和聚乙烯;同时副产硫磺、丁烯、丙烷和乙烷以及C5+等副产品。
合成气制甲醇装置(以下简称“合同装置”)为神华包头煤化工项目的工艺生产装置之一。
本技术附件适用于乙方承担的合同装置基础工程设计工作。
合同装置采用国外甲醇合成技术生产粗甲醇作为MTO装置原料,生产能力折合精甲醇180万吨/年;同时抽出部分粗甲醇采用国内精馏技术(甲醇精馏技术视招标情况也可由甲醇合成专利商提供)生产精甲醇,甲醇精馏规模暂按生产60万吨/年精甲醇考虑,同时预留位置以满足180万吨/年精甲醇生产需要,待甲醇专利技术引进合同签订后确定最终精馏规模。
详见合同装置的方块流程图。
燃料气去界区外合同装置主要由粗甲醇合成单元、甲醇精馏单元、氢气回收单元及产品贮存单元组成。
各单元详细组成如下:粗甲醇合成及制备单元:原料气净化、压缩、甲醇合成、粗甲醇制备、膜分离等;甲醇精馏单元:甲醇精馏、甲醇中间贮罐;氢气回收单元:PSA提纯;产品贮存单元:粗甲醇贮罐、精甲醇贮罐;1.2.1 粗甲醇合成及制备单元1.2.1.1概述本单元拟采用国外技术,详见甲方与国外专利商签订的技术附件。
对于公称能力为180万吨/年合成气制甲醇装置,为充分利用资源,在甲醇合成单元设置膜分离装置,回收合成弛放气中有效气体,该气体一部分可直接返回到联合循环压缩机进口以增产甲醇,另一部分气体进入PSA装置,以提取纯度更高的氢气给下游装置使用。
煤焦气制甲醇合成工艺装置设计
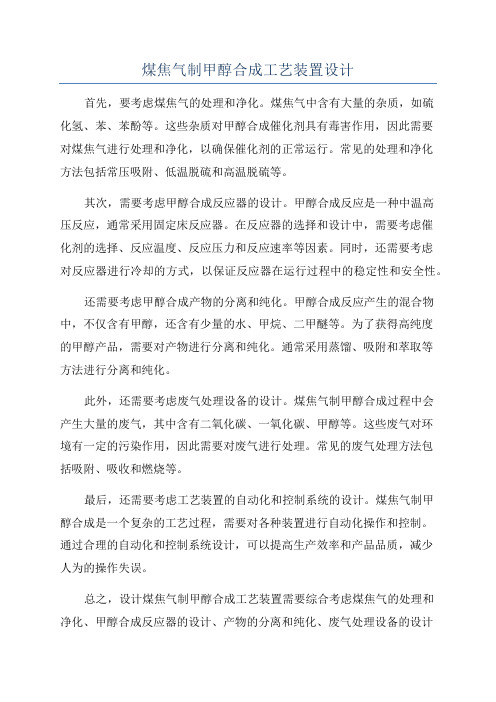
煤焦气制甲醇合成工艺装置设计首先,要考虑煤焦气的处理和净化。
煤焦气中含有大量的杂质,如硫化氢、苯、苯酚等。
这些杂质对甲醇合成催化剂具有毒害作用,因此需要对煤焦气进行处理和净化,以确保催化剂的正常运行。
常见的处理和净化方法包括常压吸附、低温脱硫和高温脱硫等。
其次,需要考虑甲醇合成反应器的设计。
甲醇合成反应是一种中温高压反应,通常采用固定床反应器。
在反应器的选择和设计中,需要考虑催化剂的选择、反应温度、反应压力和反应速率等因素。
同时,还需要考虑对反应器进行冷却的方式,以保证反应器在运行过程中的稳定性和安全性。
还需要考虑甲醇合成产物的分离和纯化。
甲醇合成反应产生的混合物中,不仅含有甲醇,还含有少量的水、甲烷、二甲醚等。
为了获得高纯度的甲醇产品,需要对产物进行分离和纯化。
通常采用蒸馏、吸附和萃取等方法进行分离和纯化。
此外,还需要考虑废气处理设备的设计。
煤焦气制甲醇合成过程中会产生大量的废气,其中含有二氧化碳、一氧化碳、甲醇等。
这些废气对环境有一定的污染作用,因此需要对废气进行处理。
常见的废气处理方法包括吸附、吸收和燃烧等。
最后,还需要考虑工艺装置的自动化和控制系统的设计。
煤焦气制甲醇合成是一个复杂的工艺过程,需要对各种装置进行自动化操作和控制。
通过合理的自动化和控制系统设计,可以提高生产效率和产品品质,减少人为的操作失误。
总之,设计煤焦气制甲醇合成工艺装置需要综合考虑煤焦气的处理和净化、甲醇合成反应器的设计、产物的分离和纯化、废气处理设备的设计以及自动化和控制系统的设计等方面的因素,以实现高效、安全、环保的煤焦气制甲醇合成过程。
合成气制甲醇工艺流程设计与设备选型
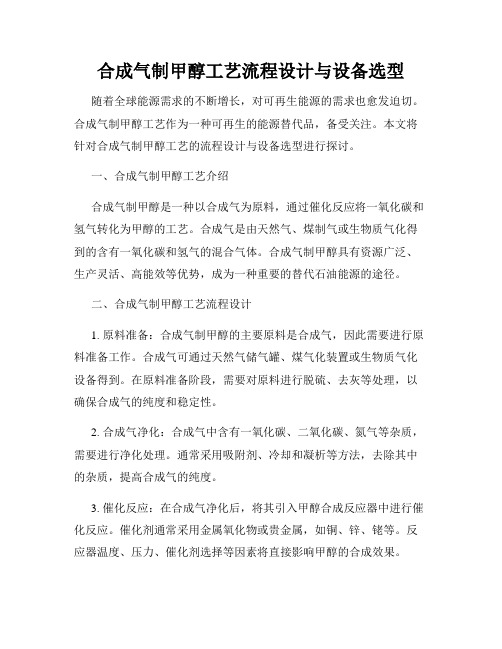
合成气制甲醇工艺流程设计与设备选型随着全球能源需求的不断增长,对可再生能源的需求也愈发迫切。
合成气制甲醇工艺作为一种可再生的能源替代品,备受关注。
本文将针对合成气制甲醇工艺的流程设计与设备选型进行探讨。
一、合成气制甲醇工艺介绍合成气制甲醇是一种以合成气为原料,通过催化反应将一氧化碳和氢气转化为甲醇的工艺。
合成气是由天然气、煤制气或生物质气化得到的含有一氧化碳和氢气的混合气体。
合成气制甲醇具有资源广泛、生产灵活、高能效等优势,成为一种重要的替代石油能源的途径。
二、合成气制甲醇工艺流程设计1. 原料准备:合成气制甲醇的主要原料是合成气,因此需要进行原料准备工作。
合成气可通过天然气储气罐、煤气化装置或生物质气化设备得到。
在原料准备阶段,需要对原料进行脱硫、去灰等处理,以确保合成气的纯度和稳定性。
2. 合成气净化:合成气中含有一氧化碳、二氧化碳、氮气等杂质,需要进行净化处理。
通常采用吸附剂、冷却和凝析等方法,去除其中的杂质,提高合成气的纯度。
3. 催化反应:在合成气净化后,将其引入甲醇合成反应器中进行催化反应。
催化剂通常采用金属氧化物或贵金属,如铜、锌、铑等。
反应器温度、压力、催化剂选择等因素将直接影响甲醇的合成效果。
4. 分离提纯:在甲醇合成反应后,需要进行甲醇的分离和提纯。
通常采用蒸馏、回流和精馏等技术,将甲醇与未反应的气体或杂质分离,得到高纯度的甲醇产品。
三、合成气制甲醇设备选型合成气制甲醇的设备选型是确保工艺顺利进行的重要环节。
在选择设备时,需要考虑以下几个方面:1. 反应器选择:反应器是催化反应的核心设备,对反应效果有着直接影响。
在选择反应器时,需要考虑反应物的流动性、催化剂的服用性和反应温度的控制性等因素。
常见的反应器类型包括固定床反应器、流化床反应器和管式反应器等。
2. 分离设备选择:分离设备是将甲醇与未反应的气体或杂质进行分离的关键设备。
根据甲醇和原料气体的性质和比例,可以选择蒸馏塔、萃取塔和吸附塔等设备。
甲醇气化装置施工方案设计

甲醇气化装置施工方案设计1. 引言甲醇气化装置是将甲醇转化为合成气的重要设备。
本文档旨在设计甲醇气化装置的施工方案,包括施工流程、工期计划、安全措施等内容,确保施工顺利进行并达到预期效果。
2. 施工流程甲醇气化装置的施工流程包括以下几个主要步骤:2.1 设备安装将甲醇气化装置的主要设备进行安装,包括气化炉、热交换器、压力容器等。
根据设备的尺寸和重量,制定相应的安装方案,并配备合适的起重设备和工具。
2.2 配管布置根据设备的工艺流程和布局设计,进行配管布置,包括甲醇进料管道、气体出料管道、冷却水管道等。
在布置过程中,要考虑管道的材料选择、弯头和阀门的安装位置等因素。
2.3 电气接线对甲醇气化装置的电气系统进行接线操作,包括配电箱的安装、控制柜的布线和接线以及仪表的安装与连接等。
确保电气系统的正常运行和设备的安全操作。
2.4 调试测试完成设备安装和电气接线后,进行调试测试工作。
包括气化炉的点火测试、压力容器的压力测试、流量计的校验等。
通过调试测试,确保设备符合设计要求并具备安全可靠的工作状态。
2.5 转场交接完成调试测试后,进行设备的转场交接工作。
包括向运行人员进行设备操作与维护的培训、相关文件的整理和归档等。
确保装置的正常交接和运行。
3. 工期计划根据甲醇气化装置的规模和施工任务,制定工期计划,安排各项施工工作的时间节点。
确保各个施工步骤的衔接和协调。
3.1 施工准备期包括设备准备、工具准备、人员组织等。
在施工准备期,制定详细的工序计划,并进行施工方案的沟通和确认,确保施工的顺利进行。
3.2 施工期根据施工方案,进行设备安装、配管布置、电气接线等施工工作。
在施工期间,要做好施工记录,并及时处理施工中的问题和变化。
3.3 调试测试期在设备安装和施工完成后,进行调试测试工作。
根据测试结果进行必要的调整和修正,确保设备的正常操作和运行。
3.4 转场交接期在调试测试完成后,进行设备的转场交接工作。
向运行人员进行培训,并整理相关文件和资料。
甲醇合成装置工艺流程及关键控制点分析简介
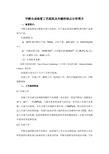
甲醇合成装置工艺流程及关键控制点分析简介一、装置简介:甲醇合成装置是以煤基合成气为原料,生产满足要求的MTO级甲醇产品和氢气产品。
(1)装置能力:a)MTO级甲醇日产量:5500t,小时产量:229.167t(以100%CH3OH 计)。
b)日输出氢气量:15456 Nm3,小时输出量644Nm3,(以99.5% H2计)。
(2)年操作小时:8000小时。
(3)专利技术来源:装置引进英国DPT(Davy Process Technology)公司的工艺包和JMC(Johnson Matthey Catalyst)催化剂。
(4)装置主要由以下几个工艺单元组成:压缩工序、合成工序、精馏工序、氢回收工序、蒸汽冷凝液回收工序、甲醇裂解制氢二、工艺流程简述2.1压缩工序压缩工序合成气压缩机和循环气压缩机。
来自界区(低温甲醇洗)的煤基合成气~30℃、~5.2MPaG,与膜分离来的富氢气混合后,依次进入合成气分离器、合成气压缩机,并在合成气压缩机中增压到~7.8MPaG。
增压后的合成气进入合成气净化预热器,用蒸汽加热并喷入锅炉给水以水解其中的COS,然后进入合成气净化槽,脱除残留的对合成催化剂有毒害的微量组份。
合成气净化槽中装填有净化催化剂。
2.2 合成工序甲醇合成回路由两个串联在一起的蒸汽上升式反应塔组成。
这种串联方式比传统流程在催化剂与设备投资上要更为经济。
甲醇合成塔为径向流反应器,气体通过装填在壳侧的催化剂,发生甲醇合成反应。
反应器内温度由管内上升的蒸汽控制。
副产蒸汽过热后送出界区。
来自合成气压缩机的净化后的合成气分为两股,其中大部分合成气和循环气混合,经过合成回路1号中间换热器加热后,进入1号甲醇合成塔进行甲醇合成反应。
甲醇合成反应在~280℃、~7.46MPaG下,在催化剂的作用下进行,该反应为放热反应。
主要的两个反应如下:CO + 2H2→ CH3OH + QCO2 + 3H2 → CH3OH + H2O + Q反应热副产~2.1MPaG的中压饱和蒸汽,经1号甲醇合成汽包分离后,进入装置内蒸汽总管。
煤制甲醇合成工艺毕业设计方案
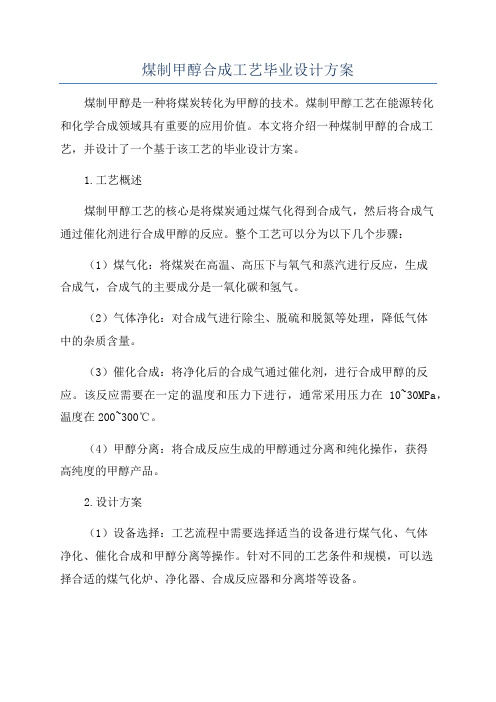
煤制甲醇合成工艺毕业设计方案煤制甲醇是一种将煤炭转化为甲醇的技术。
煤制甲醇工艺在能源转化和化学合成领域具有重要的应用价值。
本文将介绍一种煤制甲醇的合成工艺,并设计了一个基于该工艺的毕业设计方案。
1.工艺概述煤制甲醇工艺的核心是将煤炭通过煤气化得到合成气,然后将合成气通过催化剂进行合成甲醇的反应。
整个工艺可以分为以下几个步骤:(1)煤气化:将煤炭在高温、高压下与氧气和蒸汽进行反应,生成合成气,合成气的主要成分是一氧化碳和氢气。
(2)气体净化:对合成气进行除尘、脱硫和脱氮等处理,降低气体中的杂质含量。
(3)催化合成:将净化后的合成气通过催化剂,进行合成甲醇的反应。
该反应需要在一定的温度和压力下进行,通常采用压力在10~30MPa,温度在200~300℃。
(4)甲醇分离:将合成反应生成的甲醇通过分离和纯化操作,获得高纯度的甲醇产品。
2.设计方案(1)设备选择:工艺流程中需要选择适当的设备进行煤气化、气体净化、催化合成和甲醇分离等操作。
针对不同的工艺条件和规模,可以选择合适的煤气化炉、净化器、合成反应器和分离塔等设备。
(2)催化剂选择:选择适合的催化剂进行甲醇合成反应。
常用的催化剂有铜、锌、锆等金属催化剂,可以考虑使用商业化的催化剂或者开发新的催化剂。
(3)能源消耗和废弃物处理:考虑工艺中的能源消耗和废弃物处理问题。
可以通过优化工艺条件、改善煤气化效率和净化效果等措施来减少能源消耗和废弃物排放。
(4)经济评估:根据工艺设计参数和市场价格,进行经济评估,包括投资成本、运营成本和预期收益等方面。
(5)安全考虑:在工艺设计中要注重安全性,包括压力、温度的控制,设备的安全性和停机维护等方面。
3.结论本文设计了一个基于煤气化和催化合成的煤制甲醇工艺的毕业设计方案。
该方案包括煤气化、气体净化、催化合成和甲醇分离等关键步骤。
通过设备选择、催化剂选择、能源消耗和废弃物处理、经济评估和安全考虑等方面的设计,可以实现高效、经济、安全的煤制甲醇生产。
合成气制甲醇工艺流程设计与节能降耗

合成气制甲醇工艺流程设计与节能降耗合成气制甲醇是一种重要的化工过程,它将合成气(一氧化碳与氢气的混合物)转化为甲醇。
在这个过程中,工艺流程的设计及优化对于提高产量、降低能耗至关重要。
本文将讨论合成气制甲醇的工艺流程设计,并提出一些节能降耗的方法。
一、原料准备合成气制甲醇的原料包括一氧化碳和氢气,因此在工艺流程设计中,首要任务是确保原料的准备充分和稳定。
为了提高合成气的气质,可采取以下措施:1. 原料气体的净化:通过采用特定的催化剂和吸附剂,去除气体中的杂质,如硫化物、硅烷和甲烷等,以提高合成气的纯度。
2. 原料气体的质量控制:采用在线分析技术,对原料气体进行浓度和成分的实时监测,确保原料的稳定供应。
二、催化转化合成气制甲醇的核心过程是催化转化,其中一氧化碳和氢气经过催化剂的作用转化为甲醇。
在工艺流程设计中,需要考虑以下几点:1. 催化剂的选择:选择合适的催化剂,具有高催化活性和选择性,以提高反应效率。
常用的催化剂包括铜、锌、铝等金属催化剂。
2. 催化剂的载体设计:采用合适的载体材料,如氧化铝、硅胶等,提高催化剂的稳定性和寿命。
3. 反应条件的控制:根据催化剂的性质和反应动力学,合理控制反应温度、压力和物质的进料量,以获得最佳的产率和选择性。
三、能源回收与利用为了降低能耗,提高工艺流程的能效,可以采取以下措施:1. 热能的回收利用:将反应过程中产生的热能进行回收,用于供热或发电等用途。
例如,采用热交换器实现废热回收,提高能源利用效率。
2. 废料气体的利用:将反应过程中产生的废料气体进行处理和利用,如利用废料气体中的二氧化碳进行碳捕集和储存,或者作为原料用于其他化工生产过程。
四、设备优化与改进在工艺流程设计中,对设备进行优化和改进,也对节能降耗起到重要作用。
例如:1. 设备的紧密布局和合理设置管道,减少能量损失和压力降低。
2. 采用高效的罐式反应器和分离器,减少反应时间和能耗。
3. 采用先进的自动控制系统,实现工艺参数的智能控制和优化,提高生产效率和稳定性。
年产20万吨煤制甲醇合成工艺初步设计煤化工毕业设计
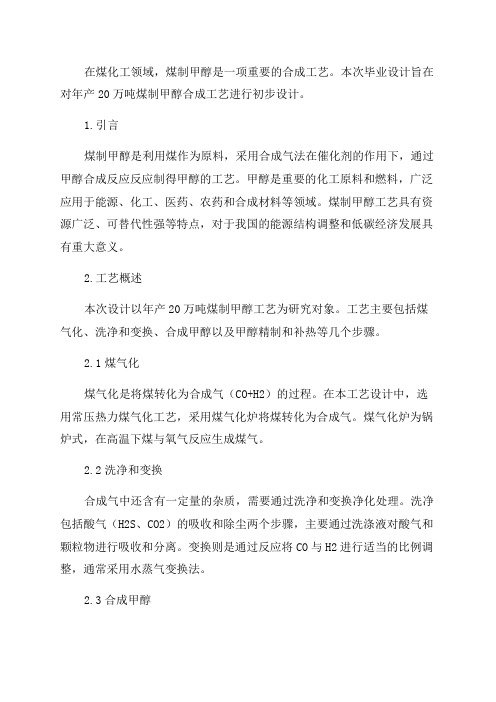
在煤化工领域,煤制甲醇是一项重要的合成工艺。
本次毕业设计旨在对年产20万吨煤制甲醇合成工艺进行初步设计。
1.引言煤制甲醇是利用煤作为原料,采用合成气法在催化剂的作用下,通过甲醇合成反应反应制得甲醇的工艺。
甲醇是重要的化工原料和燃料,广泛应用于能源、化工、医药、农药和合成材料等领域。
煤制甲醇工艺具有资源广泛、可替代性强等特点,对于我国的能源结构调整和低碳经济发展具有重大意义。
2.工艺概述本次设计以年产20万吨煤制甲醇工艺为研究对象。
工艺主要包括煤气化、洗净和变换、合成甲醇以及甲醇精制和补热等几个步骤。
2.1煤气化煤气化是将煤转化为合成气(CO+H2)的过程。
在本工艺设计中,选用常压热力煤气化工艺,采用煤气化炉将煤转化为合成气。
煤气化炉为锅炉式,在高温下煤与氧气反应生成煤气。
2.2洗净和变换合成气中还含有一定量的杂质,需要通过洗净和变换净化处理。
洗净包括酸气(H2S、CO2)的吸收和除尘两个步骤,主要通过洗涤液对酸气和颗粒物进行吸收和分离。
变换则是通过反应将CO与H2进行适当的比例调整,通常采用水蒸气变换法。
2.3合成甲醇通过将洗净和变换后的合成气进入反应器,在催化剂的作用下进行甲醇合成反应。
本设计中选用Cu-Zn-Al催化剂,并采用固定床反应器进行反应。
在适宜的反应温度和压力下,合成气中的CO和H2与催化剂发生反应生成甲醇。
2.4甲醇精制和补热合成甲醇后,通过分离、蒸馏和精制等过程,将甲醇纯化得到符合质量标准的甲醇产品。
同时也需要对合成反应产生的热量进行回收利用,提高热能利用率。
3.工艺流程4.工艺经济分析进行工艺经济分析是评估该工艺可行性的关键环节。
通过对投资、生产能力、原料消耗和产品收益等方面的计算和估算,可以评估工艺的经济效益,为项目决策提供依据。
5.结论本次毕业设计对年产20万吨煤制甲醇合成工艺进行了初步设计,从工艺概述、工艺流程和工艺经济分析等方面对该工艺进行了详细的研究。
煤制甲醇工艺的应用有助于推动我国能源结构调整和低碳经济发展,具有重要的实际意义。
产万吨煤制甲醇生产工艺初步设计
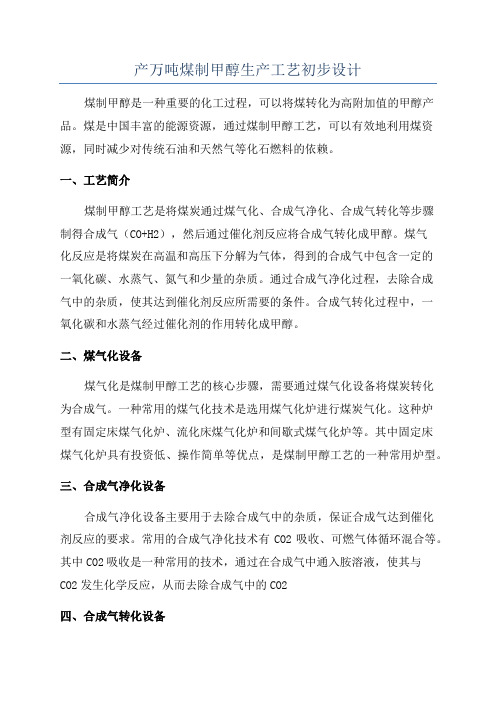
产万吨煤制甲醇生产工艺初步设计煤制甲醇是一种重要的化工过程,可以将煤转化为高附加值的甲醇产品。
煤是中国丰富的能源资源,通过煤制甲醇工艺,可以有效地利用煤资源,同时减少对传统石油和天然气等化石燃料的依赖。
一、工艺简介煤制甲醇工艺是将煤炭通过煤气化、合成气净化、合成气转化等步骤制得合成气(CO+H2),然后通过催化剂反应将合成气转化成甲醇。
煤气化反应是将煤炭在高温和高压下分解为气体,得到的合成气中包含一定的一氧化碳、水蒸气、氮气和少量的杂质。
通过合成气净化过程,去除合成气中的杂质,使其达到催化剂反应所需要的条件。
合成气转化过程中,一氧化碳和水蒸气经过催化剂的作用转化成甲醇。
二、煤气化设备煤气化是煤制甲醇工艺的核心步骤,需要通过煤气化设备将煤炭转化为合成气。
一种常用的煤气化技术是选用煤气化炉进行煤炭气化。
这种炉型有固定床煤气化炉、流化床煤气化炉和间歇式煤气化炉等。
其中固定床煤气化炉具有投资低、操作简单等优点,是煤制甲醇工艺的一种常用炉型。
三、合成气净化设备合成气净化设备主要用于去除合成气中的杂质,保证合成气达到催化剂反应的要求。
常用的合成气净化技术有CO2吸收、可燃气体循环混合等。
其中CO2吸收是一种常用的技术,通过在合成气中通入胺溶液,使其与CO2发生化学反应,从而去除合成气中的CO2四、合成气转化设备合成气转化设备是煤制甲醇工艺的关键设备,通过催化剂的作用将合成气转化为甲醇。
催化剂是合成气转化过程中一个重要的因素,常用的催化剂有铜-锌-铝催化剂和高选择性催化剂等。
催化剂的活性和选择性对甲醇的合成效果具有较大的影响。
五、甲醇分离和纯化设备合成甲醇中常含有杂质和水分,需要进行进一步的分离和纯化。
常用的分离技术有精馏、吸收和萃取等。
甲醇的纯化主要通过精馏等方法,将甲醇中的杂质和水分进行分离,得到高纯度的甲醇产品。
六、废水处理设备煤制甲醇生产过程中会产生大量的废水,其中含有一些有机物和杂质。
为了保护环境,需要对废水进行处理。
以煤为原料的甲醇装置设计方案和运行情况介绍

以煤为原料的甲醇装置设计方案与运行情况介绍刘志臣山东联盟化工股份有限公司摘要:文章总结了山东联盟化工股份有限公司联醇和单醇生产运行情况,重点介绍了10万吨/年单醇系统的主要工段工艺方案的选择和鲁奇低压甲醇合成技术特点,并对系统存在的问题进行了分析和探讨。
前言以无烟煤为原料的中、小氮肥企业,有许多厂实现了联醇生产,在增加了甲醇这种产品的同时,对合成氨生产来说,明显地改善了变换、脱碳、精炼等气体净化工序的工艺条件。
当实现联醇之后,由于变换工段可放宽变换气CO结果(视甲醇产量而定)和入精炼工段CO、CO2的降低,使合成氨生产电耗下降50kwh/tNH3,蒸汽用量减少100kg/tNH3以上,精炼自用氨和副产氨水量减少,生产成本降低,变换、脱碳、精炼的操作更加容易。
有条件的厂甚至实现了热、电、醇、氨四联产,使煤资源得到更充分利用。
当然,对不同的生产厂而言,联醇的作用也不同,有的厂把联醇作为一种气体净化手段;而有的厂靠加大醇氨比,以多产甲醇为目的;多数厂则根据甲醇市场价格的起浮波动来调整醇氨比,以获得最佳的综合经济效益。
近年来,随着甲醇市场的好转,中、小氮肥企业甲醇搞得红红火火,大有"星罗棋布、遍地开花"之势头。
据悉,我国精甲醇生产企业有100多家,发展势头之猛是前所未有的。
从生产规模来看,联醇生产企业其甲醇产量一般较小,多数生产能力在5万吨/年以下。
随着低压甲醇生产技术的日臻成熟,国内不少厂正在兴建10万吨/年、20万吨/年甚至50万吨/年单醇装置。
根据考察和研究,我们认为建设单醇装置最好与合成氨装置联合,以便将甲醇放空气、造气富氮气得到充分回收和利用,并且一些公用设施也可互相补充,使企业获得最佳效益。
山东联盟化工股份有限公司原有合成氨生产能力30万吨/年,联醇生产能力5万吨/年,又在2004年11月建成投产一套10万吨/年单醇装置,将总氨醇能力提高到45万吨/年。
在新建单醇的方案确定中,我们遵循多联产发展的原则,充分考虑了与原有合成氨和联醇装置的配套及公用工程的合理利用,达到减少投资、合理配套、节能降耗、安全环保之目的。
化工专业煤气化制甲醇设计说明
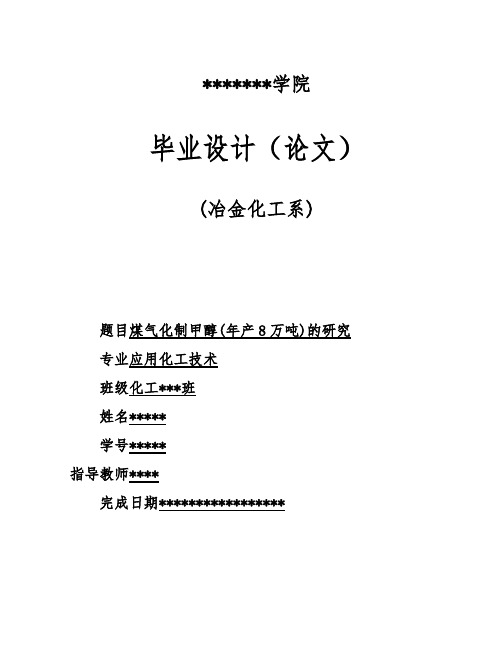
*******学院毕业设计(论文)(冶金化工系)题目煤气化制甲醇(年产8万吨)的研究专业应用化工技术班级化工***班姓名*****学号*****指导教师****完成日期*****************目录前言- 1 -第一章绪论- 2 -1.1煤炭气化的发展-3-1.2新型煤化工容简介-4-1.3煤炭气化在新型煤化工中的应用-4-1.3.1煤炭气化技术- 4 -1.3.2煤制含氧化合物- 4 -第二章煤炭气化原理- 5 -2.1煤炭气化技术-6-2.2原料煤对气化性能的影响-7-2.3气化用煤种的主要特性-7-2.4煤的反应性能-7-第三章煤气化制甲醇- 8 -3.1煤气化制甲醇工艺流程-8-3.2合成气制备-9-3.2.1合成气工艺- 9 -3.2.2 反应设备—气化炉- 9 -3.2.3合成气的净化- 10 -3.3甲醇的制备-11-3.3.1甲醇的性质- 11 -3.3.2甲醇市场现状与展望- 12 -3.3.3合成气制甲醇- 13 -3.3.4低压法合成甲醇的工艺- 13 -3.3.5甲醇合成反应器- 16 -3.4物料衡算-18-第四章结论- 23 -4.1低压法合成甲醇的影响因素-24-4.1.1温度对CH3OH合成的影响- 24 -4.1.2 压力对CH3OH合成的影响- 24 -4.1.3空速对甲醇合成的影响- 24 -4.1.4 氢碳比的控制对甲醇合成的影响- 25 -4.1.5 惰性气体含量对CH3OH合成的影响- 26 -4.1.6甲醇合成催化剂以与催化剂对甲醇合成的影响- 26 - 第五章结束语- 27 -致- 28 -参考文献- 29 -前言中国作为一个煤资源比较丰富,但油资源较为贫乏的国家。
随着节能减排等一系列国家政策的提出,我国越注重对能源的合理、最大化利用。
随着科学技术能力的提高,,合成工艺日趋成熟和完善。
我们也看到了许多方面的技术先进性,所以提出了在煤气化制甲醇的一些工艺流程。
合成气生产甲醇工艺设计流程
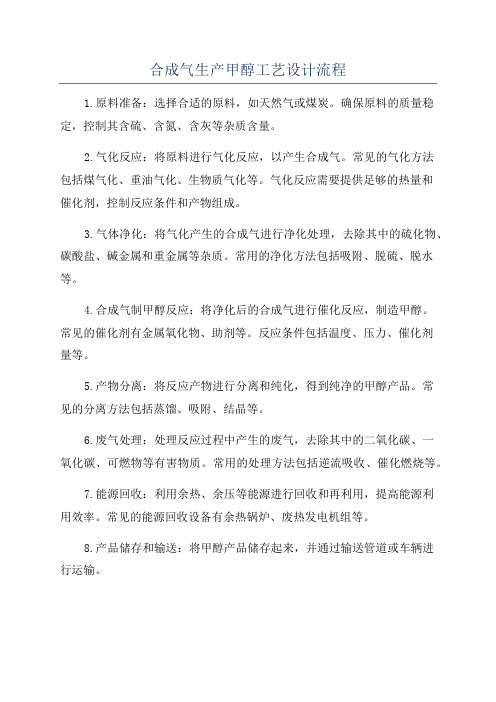
合成气生产甲醇工艺设计流程1.原料准备:选择合适的原料,如天然气或煤炭。
确保原料的质量稳定,控制其含硫、含氮、含灰等杂质含量。
2.气化反应:将原料进行气化反应,以产生合成气。
常见的气化方法包括煤气化、重油气化、生物质气化等。
气化反应需要提供足够的热量和催化剂,控制反应条件和产物组成。
3.气体净化:将气化产生的合成气进行净化处理,去除其中的硫化物、碳酸盐、碱金属和重金属等杂质。
常用的净化方法包括吸附、脱硫、脱水等。
4.合成气制甲醇反应:将净化后的合成气进行催化反应,制造甲醇。
常见的催化剂有金属氧化物、助剂等。
反应条件包括温度、压力、催化剂量等。
5.产物分离:将反应产物进行分离和纯化,得到纯净的甲醇产品。
常见的分离方法包括蒸馏、吸附、结晶等。
6.废气处理:处理反应过程中产生的废气,去除其中的二氧化碳、一氧化碳、可燃物等有害物质。
常用的处理方法包括逆流吸收、催化燃烧等。
7.能源回收:利用余热、余压等能源进行回收和再利用,提高能源利用效率。
常见的能源回收设备有余热锅炉、废热发电机组等。
8.产品储存和输送:将甲醇产品储存起来,并通过输送管道或车辆进行运输。
9.工艺优化和改进:根据实际生产情况,对工艺过程进行优化和改进,提高产量、质量和能源利用效率。
这可以包括改进反应器设计、优化催化剂选择、改进废气处理方法等。
10.安全控制和环境保护:在工艺设计中,要重视安全控制和环境保护。
采取相应的安全措施,防止爆炸、中毒等事故的发生,同时做好废气治理工作,减少对环境的影响。
以上是一个合成气生产甲醇的工艺设计流程,每个步骤都需要详细的操作和技术要点。
在实际生产中,还需要根据具体情况进行具体的工艺优化和改进。
这样才能保证甲醇的生产工艺稳定、高效,并确保产品的质量和环境保护的要求。
【工厂管理】年产10万吨煤合成甲醇工厂设计要点(doc 11页)
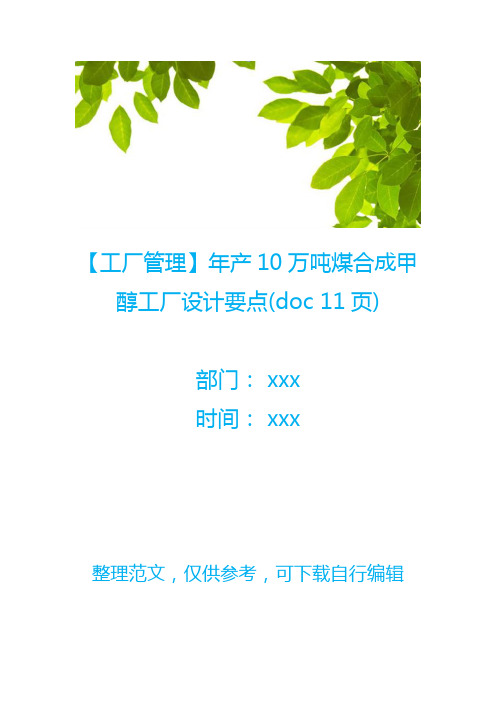
【工厂管理】年产10万吨煤合成甲醇工厂设计要点(doc 11页)部门: xxx时间: xxx整理范文,仅供参考,可下载自行编辑年产10万吨煤合成甲醇工厂设计摘要: 本设计采用CO和H 2为成原料气,中温低压条件下在均温管式反应器中完成甲醇合成。
原料气采用GSP煤气化工艺制得,通过三次脱硫工序和转化反应调节,从而达到甲醇合成最佳碳氢比。
产品粗甲醇经过预塔和主塔三次精馏,最终生产出符合国家一级要求的精甲醇。
设计内容包括厂址选择、物料衡算、能量衡算、主要设备计算与选型、车间平面布置图及立面图、工艺流程图和全厂总平面图。
设计成果为图纸5张,说明书1份,缩写稿1份。
关键词:甲醇,合成,工艺设计The Synthesis Technological Designs of Produces 10,000 TMethyl Alcohol YearlyABSTRACT:The design uses CO and H2 synthesizes the feed gas, Under the middle temperature and low pressure condition, completes the synthesis in the average temperature tubular reactor. The feed gas uses the GSP gasification craft system,Through three desulphurization working procedures and transformed response adjustment, Thus achieves the best carbon hydrogen ratio for the synthesis of methyl alcohol. Through three selective evaporations with the pre-tower and the host tower, The product preliminary methyl alcohol comes to the national level request fine methyl alcohol.The design including factory site choice, mass balance computation, energy balance computation, computation and shaping of main equipment, floor-plan and elevation of workshop, flow chart and entire factory general layout.The results of design are: Blueprint 5, Instruction book1, abridged edition 1.KEY WORDS: Methyl alcohol, Synthesis, Technological design1 概述甲醇是重要的有机化工原料之一,是碳一化学的母体,广泛应用于生产塑料、纤维、橡胶、染料、香料、医药和农药等方面,也是一种重要的有机溶剂,由甲醇延伸的化工产品达数百种,在发达国家其产量仅次于乙烯、丙烯和苯,居第四位。
合成气制甲醇工艺流程设计与催化剂评价
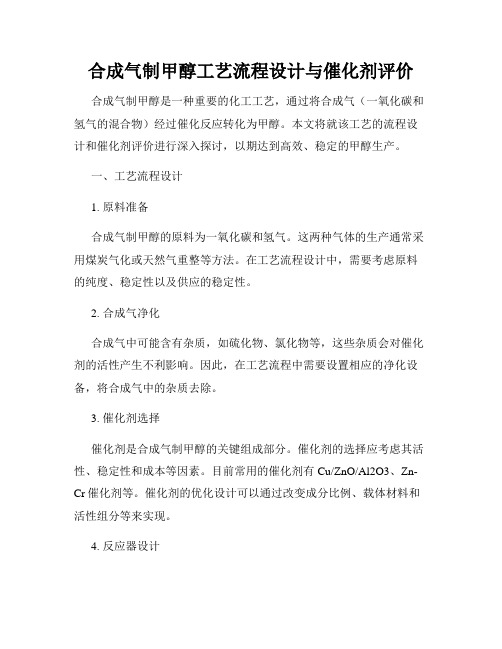
合成气制甲醇工艺流程设计与催化剂评价合成气制甲醇是一种重要的化工工艺,通过将合成气(一氧化碳和氢气的混合物)经过催化反应转化为甲醇。
本文将就该工艺的流程设计和催化剂评价进行深入探讨,以期达到高效、稳定的甲醇生产。
一、工艺流程设计1. 原料准备合成气制甲醇的原料为一氧化碳和氢气。
这两种气体的生产通常采用煤炭气化或天然气重整等方法。
在工艺流程设计中,需要考虑原料的纯度、稳定性以及供应的稳定性。
2. 合成气净化合成气中可能含有杂质,如硫化物、氯化物等,这些杂质会对催化剂的活性产生不利影响。
因此,在工艺流程中需要设置相应的净化设备,将合成气中的杂质去除。
3. 催化剂选择催化剂是合成气制甲醇的关键组成部分。
催化剂的选择应考虑其活性、稳定性和成本等因素。
目前常用的催化剂有Cu/ZnO/Al2O3、Zn-Cr催化剂等。
催化剂的优化设计可以通过改变成分比例、载体材料和活性组分等来实现。
4. 反应器设计反应器是合成气制甲醇过程中完成催化反应的装置。
反应器的设计需要考虑反应器的稳定性、传热效果和转化率等因素。
常见的反应器类型有固定床反应器、流化床反应器和微型反应器等。
5. 分离提纯合成气制甲醇反应产生的产物中,除甲醇外还有一些副产物和未反应物。
分离提纯的过程中需要考虑不同成分的物理性质差异,利用蒸馏、吸附或萃取等方法进行分离。
二、催化剂评价1. 活性评价催化剂的活性是指催化剂在一定条件下促使反应进行的能力。
常用的活性评价方法有甲醇选择性和甲醇转化率等指标。
通过单因素实验和正交实验等方法,评价不同催化剂的活性表现。
2. 稳定性评价催化剂的稳定性是指催化剂在长期使用过程中保持活性的能力。
稳定性评价可以通过寿命测试和循环试验等方法进行。
对于不稳定的催化剂,可以通过改变催化剂成分或制备工艺进行改进。
3. 抗毒性评价合成气中可能含有一些有机硫化物、硫醇等毒性物质,这些物质会对催化剂的活性产生不利影响。
抗毒性评价是评价催化剂在存在毒性物质下的稳定性。
- 1、下载文档前请自行甄别文档内容的完整性,平台不提供额外的编辑、内容补充、找答案等附加服务。
- 2、"仅部分预览"的文档,不可在线预览部分如存在完整性等问题,可反馈申请退款(可完整预览的文档不适用该条件!)。
- 3、如文档侵犯您的权益,请联系客服反馈,我们会尽快为您处理(人工客服工作时间:9:00-18:30)。
神华包头煤化工项目合成气制甲醇装置总体设计和基础设计技术附件合同编号(业主):S K C C*-C-M S-C-06001-00合同编号(承包商):S H-2006-07业主:包头神华煤化工有限公司承包商:华陆工程科技有限责任公司2006年月日目录附件1 工艺描述附件2 设计基础附件3 设计原则、标准和规范附件4 工作范围和服务内容附件5 甲方提供的设计基础资料附件6 设计文件及交付附件7 工作执行计划及重要会议附件8 组织机构及主要人员配备附件9 人工时费附件10 履约保函模板附件1 工艺描述1.1 概述甲方拟在内蒙古自治区包头市九原区工业开发区建设神华包头煤化工项目(以下简称“项目”)。
该项目是以煤为原料生产甲醇,甲醇通过MTO装置转化为烯烃,烯烃聚合生产出聚丙烯和聚乙烯;同时副产硫磺、丁烯、丙烷和乙烷以及C5+等副产品。
合成气制甲醇装置(以下简称“合同装置”)为神华包头煤化工项目的工艺生产装置之一。
本技术附件适用于乙方承担的合同装置基础工程设计工作。
合同装置采用国外甲醇合成技术生产粗甲醇作为MTO装置原料,生产能力折合精甲醇180万吨/年;同时抽出部分粗甲醇采用国内精馏技术(甲醇精馏技术视招标情况也可由甲醇合成专利商提供)生产精甲醇,甲醇精馏规模暂按生产60万吨/年精甲醇考虑,同时预留位置以满足180万吨/年精甲醇生产需要,待甲醇专利技术引进合同签订后确定最终精馏规模。
详见合同装置的方块流程图。
燃料气去界区外合同装置主要由粗甲醇合成单元、甲醇精馏单元、氢气回收单元及产品贮存单元组成。
各单元详细组成如下:粗甲醇合成及制备单元:原料气净化、压缩、甲醇合成、粗甲醇制备、膜分离等;甲醇精馏单元:甲醇精馏、甲醇中间贮罐;氢气回收单元:PSA提纯;产品贮存单元:粗甲醇贮罐、精甲醇贮罐;1.2.1 粗甲醇合成及制备单元1.2.1.1概述本单元拟采用国外技术,详见甲方与国外专利商签订的技术附件。
对于公称能力为180万吨/年合成气制甲醇装置,为充分利用资源,在甲醇合成单元设置膜分离装置,回收合成弛放气中有效气体,该气体一部分可直接返回到联合循环压缩机进口以增产甲醇,另一部分气体进入PSA装置,以提取纯度更高的氢气给下游装置使用。
1.2.1.2膜分离技术(1)工作原理膜分离的基本原理就是利用各气体组分在高分子聚合物中的溶解扩散速率不同,故在膜两侧分压差的作用下导致其渗透通过纤维膜壁的速率不同而分离。
整个膜分离系统基本上无运动部件,控制回路及监控点少,开、停车方便快捷,甚少维修,开工率极高。
(2)流程简述来自甲醇合成工序的弛放气进入膜分离工序,此气体首先进水洗塔以洗去气体中甲醇,然后进入除雾器。
除雾器中装有高效除雾元件,可除去小于1μm的粒子,冷凝的液沫及雾滴被捕集形成液体后通过除雾器底部的阀门排出;从除雾器出来的气体进入一套管式换热器将原料气加热至50︒C,用蒸汽调节阀与温度变送器联合实现原料气温度的调节、指示、报警及联锁;加热过的气体经一管道过滤器进入膜分离器组进行分离,在高压侧得到富氢的渗透气,作为产品气返回压缩机入口,或送到PSA工序进一步提纯;而渗透气并入燃料气管网或直接排往火炬总管。
1.2.2 甲醇精馏单元1.2.2.1概述尽管我国甲醇生产起步较晚,随着生产技术逐年改进和提高,目前甲醇精馏技术掌握了两塔精馏和三塔精馏流程,既可生产GB338-2004优等品甲醇,又可生产(O-M-232K)AA级精甲醇,因此,精馏单元拟采用由国内工程院设计,但考虑到装置的整体优化设计,视具体情况决定是否与合成甲醇单元一起引进。
甲醇精馏有两塔和三塔之分,主要区别在于三塔流程采用两个主精馏塔,一个加压操作(P=0.6-0.7MPa),一个常压操作,利用加压塔塔顶蒸汽冷凝热作为常压塔再沸器的热源,既减少蒸汽消耗,又节约了冷却水,总能耗比两塔精馏低10-20%;由于三塔流程比两塔流程多一个加压主精馏塔及其附属设备,流程变长,投资比两塔流程多30%左右。
从能耗和投资综合考虑,对大型甲醇精馏装置宜采用三塔精馏,为提高甲醇回收率,也可设甲醇回收塔,即3+1流程。
为进一步降低低压蒸汽消耗,提高精甲醇的产品质量,本次60万吨/年甲醇精馏单元拟采用三塔并设回收塔的3+1流程,以提高甲醇收率并平衡整个项目中的低位热能,降低能耗。
1.2.2.2甲醇精馏流程由甲醇合成送来的粗甲醇经过甲醇中间罐区的缓冲后,用泵打入预精馏塔,在该塔进行轻组分的分离。
塔顶蒸馏出的气体经预塔冷凝器将甲醇、水、部分轻组分冷凝,冷凝液进入预塔回流罐,不凝气进轻组分冷却器进一步冷却,出轻组分冷却器的不凝气去燃料气管网作燃料气,冷凝液返回预精馏塔作回流液。
为防止设备腐蚀,在预精馏塔下部加入NaOH稀溶液,以中和合成反应中生成的有机酸,预精馏塔蒸馏需要的热量由预塔再沸器供给。
预精馏塔底部出来的甲醇液由甲醇给料泵加压后送入加压精馏塔,塔顶蒸出的甲醇蒸汽进入冷凝再沸器,甲醇蒸汽冷凝热作为常压精馏塔的热源,出冷凝再沸器的精甲醇液进入加压塔回流罐,一部分精甲醇由加压塔回流泵加压后送入加压精馏塔,其余部分经精甲醇冷却器冷却到40℃送至精甲醇中间罐。
加压精馏塔所需热量由低压蒸汽通过加压塔再沸器提供。
加压精馏塔底部出来的甲醇液送至常压精馏塔下部,蒸出的甲醇蒸汽由常压塔冷凝器冷凝后进入常压塔回流罐,再经常压塔回流泵加压,一部分精甲醇打入常压塔回流,其余部分送至精甲醇中间罐。
精甲醇中间罐的产品化验合格后送去产品甲醇罐区。
常压精馏塔侧线采出的杂醇油冷却后送入杂醇贮槽。
常压精馏塔底排出的含有微量甲醇和其它高沸点醇的水经废液冷却器冷却后,由废液泵送废水处理装置。
1.2.2.3 甲醇中间贮罐中间罐区的作用是检验甲醇产品是否合格。
设计按8小时储存周期考虑,储存量为1812吨,合2264m3,拟设置3个1000m3甲醇储罐,其中2个作为检验罐,1个作为精馏单元进料缓冲罐。
自甲醇精馏工序来的精甲醇,进入甲醇计量罐中。
经检验合格的精甲醇用精甲醇泵升压后送往精甲醇罐区贮存,不合格的甲醇返回到前面重新精馏。
1.2.3 氢气回收单元1.2.3.1 概述为了得到满足下游装置需要的高纯度氢气,本单元拟采用国内成熟的变压吸附技术,以粗甲醇合成单元膜分离工序来的有效气为原料,提取纯度更高的氢气供下游装置使用。
由于目前尚未确定产品氢气的规格要求、用量及有效气的规格、流量等,本流程在设计条件会后确定。
1.2.3.4变压吸附技术(1)工作原理变压吸附(PSA)工艺,利用吸附剂对气体的吸附容量随压力变化而变化的特性,吸附剂在选择吸附的条件下,加压吸附气体中的某些组分,减压脱附这些组分而使吸附剂得到再生,而氢气等组分作为弱吸附组分通过床层达到提纯氢气的目的。
该工艺国内技术成熟、流程简单、投资少、能耗低、自动化程度高、氢回收率高(≥90%,一级)、产品氢气纯度高(≥99.5%)、工业上类似应用业绩很多。
(2)流程简述来自粗甲醇合成单元膜分离工序的富氢气,经流量计计量后送入吸附器,在此气体中含有的CO、CO2及部分CH4等杂质组份被吸附,产品氢气从吸附器顶部出来,经一组压力调节系统将压力调节至要求等级,产品氢气用管道送出界外。
再生阶段,首先将塔内气体从吸附器底部排出(逆放),使其压力降至常压,再利用—台吸附器的顺放气对另一台吸附器自上而下进行冲洗,进一步将吸附器中剩余的杂质组分分离出来。
逆放前期压力较高的解吸气先经解吸气缓冲罐后,再经一组压力调节系统调节压力,与逆放后期及冲洗阶段压力较低的解吸气一起进入解吸气混合罐混和后输出。
整个吸附分离循环过程由计算机控制,全部实现自动化操作,装置弹性大,能适应原料气量和组成的波动。
1.2.4产品贮存单元本装置的产品贮存包括供下游MTO装置用的粗甲醇储罐,甲醇精馏单元生产的精甲醇储罐。
(1)粗甲醇储罐粗甲醇储罐主要向下游MTO装置提供原料甲醇,同时可兼作精馏单元的不合格储罐。
当下游MTO装置临时停车时,甲醇合成工序生产的粗甲醇,进入粗甲醇贮罐中贮存,当下游MTO装置恢复生产时,粗甲醇经粗甲醇泵升压后送往MTO装置;或当精馏单元在开车初期出现不合格产品时,不合格产品可直接经泵送到其中一个储罐,然后再循环到精馏直到达到规格后送到精甲醇储罐。
粗甲醇储罐储存周期按5天考虑,储存量约为30000吨,合38700m3。
为防止物料挥发损失,贮罐拟采用内浮顶式,考虑设置10000m3粗甲醇储罐5个。
贮罐体积和数量可在设计中进一步优化。
(2)精甲醇储罐自精馏单元来的合格精甲醇进入精甲醇储罐储存。
根据业主要求,设计按10天储存周期考虑,储存量为18000吨,合23077m3。
为防止物料挥发损失,该罐拟采用内浮顶式,考虑设置15000m3精甲醇储罐2个。
成品罐的产品经管道输送至成品装车站的装车臂进行槽车灌装,计量方式采用流量计计量。
装车后的产品槽车经火车将产品运往周边市场销售。
1.3 控制方案1.3.1 概述合成气制甲醇装置与煤气化装置将共用一个中央控制室,土建由煤气化装置统一考虑。
1.3.2控制方案合成气制甲醇装置采用先进、可靠、成熟的分散控制系统(DCS)对整个生产过程进行集中监视和自动控制。
所选用的DCS系统是整个工厂管理和控制系统的一部分,实现信息共享,提高全厂的操作管理水平。
合成气制甲醇装置的安全联锁系统由独立于DCS系统的紧急停车系统(ESD)完成。
压缩机组的检测和控制系统包括速度控制、防喘振控制等由压缩机组成套供货,并将重要的运行参数送到DCS系统。
主要的和重要的工艺参数集中到合成气制甲醇装置控制室由DCS系统显示和控制。
不重要的工艺参数及设定点不经常调整的参数,采用就地显示和控制仪表。
必须在现场操作和监视的机组或设备,则在机组或设备附近的现场安装仪表或操作盘,例如压缩机、大型机泵等。
DCS和ESD系统由操作站、控制站、打印机、辅助操作台、通讯总线、外围设备、相关的接口等部分组成。
DCS和ESD系统安装在合成气制甲醇装置的中央控制室,对合成气制甲醇装置的工艺过程进行集中监视,并对重要参数进行分散控制。
对一般的控制参数进行单回路PID反馈控制,部分较重要的参数采用比值控制、串级控制和选择控制,对于特别重要的工艺过程设计复杂控制系统,如甲醇合成的H2/CO比控制、甲醇合成反应器的废锅汽包压力与反应温度的控制、工业在线自动分析数据处理和控制,这些都将在DCS中完成,并可实现优化控制。
本装置的环境特征是易燃、易爆、有毒及气候条件比较恶劣,因此采用本质安全仪表。
另外,设置可燃和有毒气体检测系统,当装置内的可燃和有毒气体浓度超过要求时,发出报警信号。
1.4 技术来源粗甲醇合成(包括膜分离)及制备单元,拟采用国外先进合成技术,引进国外基础工程设计;甲醇精馏单元采用国内技术或国外技术,氢气回收单元(PSA)采用国内先进技术。