基于应变模态的车轴动应力仿真计算
基于模态应力恢复的有限元疲劳分析法_张林波

第15卷增刊计算机辅助工程 V ol. 15 Supp1. 2006年9月COMPUTER AIDED ENGINEERING Sep. 2006 文章编号:1006-0871(2006)S1-0202-03基于模态应力恢复的有限元疲劳分析法张林波,黄鹏程,柳杨,瞿元(奇瑞汽车有限公司乘用车工程研究院,安徽芜湖 241009)摘要:结合实例介绍基于模态应力恢复的有限元疲劳分析法及分析流程,它是一种综合MSC Nastran, MSC Adams及MSC Fatigue的疲劳寿命集成化仿真方法,非常适合汽车零部件的有限元疲劳分析.关键词:模态;应力恢复;有限元;疲劳;汽车中图分类号:O241.82;U461.7 文献标志码:AFEM-based Fatigue Analysis Using ModalStress Recovery MethodZHANG Linbo, HUANG Pengcheng, LIU Yang, QU Yuan (Passenger Vehicle Product Development, Chery Automobile Co., Ltd., Wuhu Anhui 241009, China)Abstract: The FEM-based fatigue analysis method and procedure are described through an example. The method is an integrated fatigue simulation method using MSC Nastran,MSC Adams and MSC Fatigue together, which is useful to the fatigue analysis for automobile components.Key words: mode shape; stress recovery; fatigue; finite element; automobile0 引言随着行业竞争加剧,通过加快产品研发速度、降低产品成本、提高产品可靠性的手段提高产品竞争力,已经为各企业所认可. 疲劳分析是一个重要途径,在产品研发中得到越来越多的应用. 汽车零部件疲劳分析方法主要有静态(或准静态)、动态、随机振动疲劳分析等,对于给定的问题,应根据结构所受载荷及其动态特性不同,判断并选择正确的疲劳分析方法. 静态(准静态)疲劳分析方法的应力时间历程采用线性静态叠加法计算,并应用Miner 准则进行疲劳分析,计算效率很高,因而在汽车零部件的疲劳分析上得到广泛应用. 但由于静态(或准静态)疲劳分析方法忽略动态因素,当结构的固有频率与外载荷的频率接近时,计算结果存在很大误差.本文采用模态应力恢复方法计算动态应力时间历程,并进行有限元疲劳分析. 它是一种结合MSC Nastran,MSC Adams及MSC Fatigue等几种软件的疲劳寿命集成化分析方法. [1]在汽车动力学仿真过程中,有多种方法可以考虑零部件的柔性,MSC Adams采用模态综合法,该方法由于能够大规模减少自由度,因而与常规的瞬态应力计算方法相比,能够显著提高计算效率. 此外,MSC Nastran,MSC Adams,MSC Adams与MSC Fatigue之间有良好的数据接口,使得疲劳寿命集成化分析方法具有很好的可操作性和效率.1 模态应力恢复方法简介基于模态应力恢复的有限元疲劳分析方法主要收稿日期;2006-06-29;修回日期:2006-07-06作者简介:张林波(1973- ),男,吉林靖宇人,副研究员,博士,研究方向为汽车强度和耐久性,(E-mail) zhanglinbo@增刊 张林波,等:基于模态应力恢复的有限元疲劳分析法 203 应用模态综合技术,此外,路面文件的编制也非常重要.1.1 模态综合技术自20世纪60年代以来,国内外对于大型复杂结构系统的动力分析方法进行了大量研究,其目标主要在于通过缩减大型复杂结构的动力模型的自由度,来达到兼顾分析精度及计算效率的目的. 模态综合技术方法就是在这种背景下提出的一种特别有效的减缩自由度的方法. 模态综合法有多种理论及计算方法,MSC Adams 采用的是Craig-Bampton 方法,它是基于运动学的观点来构造结构的Ritz 基. [2-4]首先将结构划分为若干子结构,子结构内部的任一点位移,可以写出如下形式:0B B CN I I Ix p x p x p ⎡⎤⎡⎤⎡⎤===⎢⎥⎢⎥⎢⎥ΦΦ⎣⎦⎣⎦⎣⎦Φ (1) 式中,Bx 是边界自由度,Ix 是内部自由度,CΦ是约束模态,NΦ是保留的低阶主模态,Bp 和Cp 是对应于主模态的广义坐标,Φ为对应于广义坐标的变换矩阵. 柔性体的运动方程可以写成如下形式:00BB BN B NB NN I BB B B NN I I m m p p p mm p k p p ⎡⎤⎡⎤+=⎢⎥⎢⎥⎣⎦⎣⎦⎡⎤⎡⎤⎡⎤+==⎢⎥⎢⎥⎢⎥⎣⎦⎣⎦⎣⎦&&&&&&M K f f (2)式中:BB BI T T IB II mm M m m m ⎡⎤==⎢⎥⎣⎦ΦΦΦΦ (3) BBBI T T IBII k k k kk ⎡⎤==⎢⎥⎣⎦K ΦΦΦΦ(4)=f F Φ (5)M ,K 和f 分别为广义质量阵、广义刚度阵和模态坐标系下的载荷矢量,而F 为物理坐标系下的载荷矢量.1.2 路面文件的编制道路表面对于理想平面的偏离称为路面不平度,它具有影响车辆动力性、行驶质量和路面动力载荷3者的数值特征. 通常把路面相对基准平面的高度沿道路走向长度的变化,称为路面不平度函数. 本报告将路面不平度函数称为路面谱,并且将其在Adams 中的描述文件称为路面文件.按照国标GB7031-86《车辆振动输入——路面不平度表示方法》,路面不平度位移功率谱密度拟合表达式采用下式:()()00wd d n G n G n n −⎛⎞=⎜⎟⎝⎠n >0 (6)式中:0n 为参考频率,00.1n =m -1;()0d G n 为路面不平度系数,m 3;()d G n 为路面不平度,m 3;w 为频率指数,经验值w =2.通过离散频域路面的X 方向的x 值,就可以得到空间频域下随机路面Y 方向的值. 根据上述方法计算得到的E 级路面不平度曲线见如图1. 路面谱确定后,可以很方便的根据理论方法计算出疲劳分析所需要的载荷谱.图 1 E 级路面不平度曲线2 分析流程基于模态应力恢复的有限元疲劳分析方法的主要分析流程如下:(1) 生成模态中性文件MSC Nastran 可以采用残余结构、超单元或者部件超单元3种方法之一生成MSC Nastran 和MSC Adams 数据交换文件——模态中性文件(*.mnf ),在MSC Adams 中作为一个柔性部件进行动力学仿真. 包括大的刚体运动在内的多体动力学分析都可以引入柔体.(2) 建立含有柔体的多体动力学模型,按要求选取典型工况进行动力学仿真. 一般选取动力学系统中刚性相对较弱并且其应力变化是设计所关心的零部件作为柔体.(3) 输出载荷数据,用MSC Nastran 进行应力恢复计算,得到应力时间历程数据.(4) 用MSC Fatigue 进行疲劳寿命分析.3 应用实例以某车型前悬架系统中上控制臂的疲劳分析为例,动力学模型如图2所示,为了计算方便,仅将上控制臂用柔体代替(见图3). 为了提高分析精度并减少自由度数量,上控制臂用6面体划分网格(见图4).204 计算机辅助工程2006年图 2 整车动力学模型图 3 前悬系统局部图 4 上控制臂有限元模型根据某典型路面形状编制成MSC Adams能够输入的路面文件,进行刚柔耦合多体动力学仿真,柔体连接点共有3个,因此得到每个点6个方向共18个载荷时间历程,图5为控制臂与转向节连接点z向载荷. 图6为某时刻控制臂上的应力分布图,总的疲劳寿命如图7所示,最小寿命为8 400 000次,满足设计要求.图 5 控制臂与转向节连接点z向载荷图 6 上控制臂某时刻的应力分布图 7 控制臂疲劳寿命云图4 结论基于Craig-Bampton子结模态综合法,利用MSC Adams,MSC Nastran和MSC Fatigue对汽车零部件进行疲劳寿命预测是一种行之有效的疲劳寿命集成化分析方法. 由于采用子结构模态综合技术,分析模型自由度大规模缩减,因而可以极大地提高分析效率. 该方法为汽车零部件的疲劳分析提供了方便快捷的途径.参考文献:[1] 周传月. 郑红霞. MSC Fatigue疲劳分析应用与实例[M]. 北京:科学出版社, 2005.[2] DAKIN J. HEYES P. FERMER M. et al. Analytical Methods for Durability in Automotive Industry–Engineering Process, Past, Present andFuture[R]. SAE Paper 2001-01-4074.[3] ZHANG Y, XIAO P, PALMER T et al.. Vehicle Chassis/Suspension Dynamics Analysis – Finite Element Model vs. Rigid Body Mdoel[R]. SAEPaper 980900[4] YOON J, KYE K. Suspension Abuse Test Simulation Using Modal Stress Recovery[R]. SAE Paper 2004-01-0776(编辑 吴彦生)。
基于虚拟仪器的车辆零部件应力测试及疲劳强度分析系统
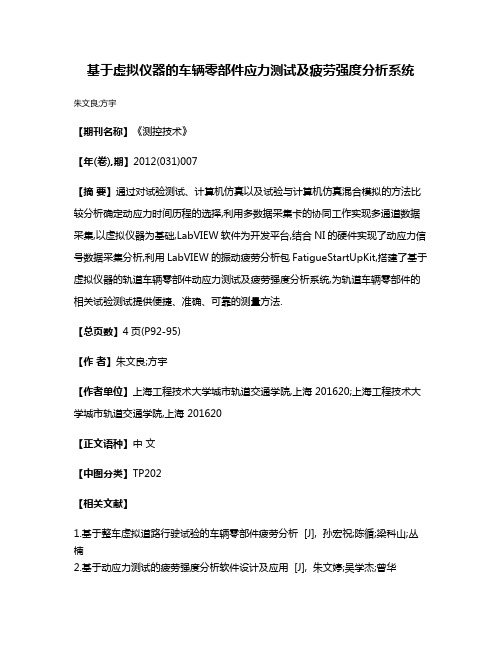
基于虚拟仪器的车辆零部件应力测试及疲劳强度分析系统朱文良;方宇
【期刊名称】《测控技术》
【年(卷),期】2012(031)007
【摘要】通过对试验测试、计算机仿真以及试验与计算机仿真混合模拟的方法比较分析确定动应力时间历程的选择,利用多数据采集卡的协同工作实现多通道数据采集,以虚拟仪器为基础,LabVIEW软件为开发平台,结合NI的硬件实现了动应力信号数据采集分析,利用LabVIEW的振动疲劳分析包FatigueStartUpKit,搭建了基于虚拟仪器的轨道车辆零部件动应力测试及疲劳强度分析系统,为轨道车辆零部件的相关试验测试提供便捷、准确、可靠的测量方法.
【总页数】4页(P92-95)
【作者】朱文良;方宇
【作者单位】上海工程技术大学城市轨道交通学院,上海 201620;上海工程技术大学城市轨道交通学院,上海 201620
【正文语种】中文
【中图分类】TP202
【相关文献】
1.基于整车虚拟道路行驶试验的车辆零部件疲劳分析 [J], 孙宏祝;陈循;梁科山;丛楠
2.基于动应力测试的疲劳强度分析软件设计及应用 [J], 朱文婷;吴学杰;曾华
3.基于有限元的门座起重机结构强度分析及应力测试 [J], 陈敏;黄国健;吴粤平;王强;刘柏清;王新华
4.基于无线应力测试的锁环式快开盲板强度分析 [J], 别锋锋;王俊尧;都腾飞;张仕佳
5.基于确定性规则波法的CALM系统锚链疲劳强度分析 [J], 梁凯;王亚琼;马超;刘天
因版权原因,仅展示原文概要,查看原文内容请购买。
轨道几何不平顺对高速列车车轴动应力的影响
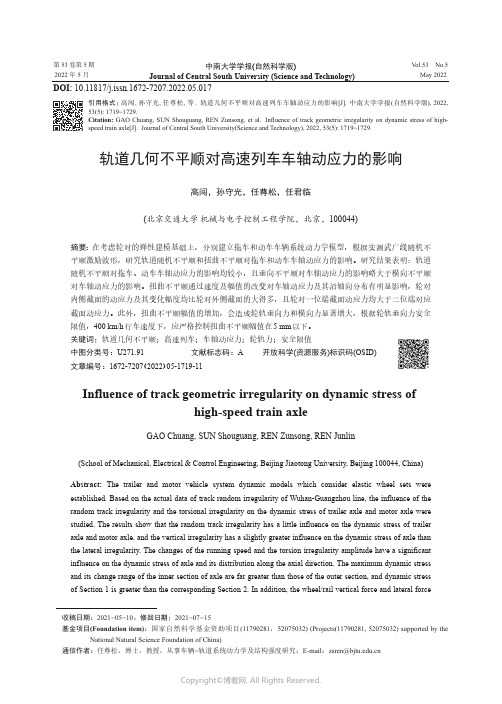
第53卷第5期2022年5月中南大学学报(自然科学版)Journal of Central South University (Science and Technology)V ol.53No.5May 2022轨道几何不平顺对高速列车车轴动应力的影响高闯,孙守光,任尊松,任君临(北京交通大学机械与电子控制工程学院,北京,100044)摘要:在考虑轮对的弹性建模基础上,分别建立拖车和动车车辆系统动力学模型,根据实测武广线随机不平顺激励波形,研究轨道随机不平顺和扭曲不平顺对拖车和动车车轴动应力的影响。
研究结果表明:轨道随机不平顺对拖车、动车车轴动应力的影响均较小,且垂向不平顺对车轴动应力的影响略大于横向不平顺对车轴动应力的影响。
扭曲不平顺通过速度及幅值的改变对车轴动应力及其沿轴向分布有明显影响,轮对内侧截面的动应力及其变化幅度均比轮对外侧截面的大得多,且轮对一位端截面动应力均大于二位端对应截面动应力。
此外,扭曲不平顺幅值的增加,会造成轮轨垂向力和横向力显著增大,根据轮轨垂向力安全限值,400km/h 行车速度下,应严格控制扭曲不平顺幅值在5mm 以下。
关键词:轨道几何不平顺;高速列车;车轴动应力;轮轨力;安全限值中图分类号:U271.91文献标志码:A开放科学(资源服务)标识码(OSID)文章编号:1672-7207(2022)05-1719-11Influence of track geometric irregularity on dynamic stress ofhigh-speed train axleGAO Chuang,SUN Shouguang,REN Zunsong,REN Junlin(School of Mechanical,Electrical &Control Engineering,Beijing Jiaotong University,Beijing 100044,China)Abstract:The trailer and motor vehicle system dynamic models which consider elastic wheel sets were established.Based on the actual data of track random irregularity of Wuhan-Guangzhou line,the influence of the random track irregularity and the torsional irregularity on the dynamic stress of trailer axle and motor axle were studied.The results show that the random track irregularity has a little influence on the dynamic stress of trailer axle and motor axle,and the vertical irregularity has a slightly greater influence on the dynamic stress of axle than the lateral irregularity.The changes of the running speed and the torsion irregularity amplitude have a significant influence on the dynamic stress of axle and its distribution along the axial direction.The maximum dynamic stress and its change range of the inner section of axle are far greater than those of the outer section,and dynamic stress of Section 1is greater than the corresponding Section 2.In addition,the wheel/rail vertical force and lateralforce收稿日期:2021−05−10;修回日期:2021−07−15基金项目(Foundation item):国家自然科学基金资助项目(11790281,52075032)(Projects(11790281,52075032)supported by theNational Natural Science Foundation of China)通信作者:任尊松,博士,教授,从事车辆−轨道系统动力学及结构强度研究;E-mail :**************.cnDOI:10.11817/j.issn.1672-7207.2022.05.017引用格式:高闯,孙守光,任尊松,等.轨道几何不平顺对高速列车车轴动应力的影响[J].中南大学学报(自然科学版),2022,53(5):1719−1729.Citation:GAO Chuang,SUN Shouguang,REN Zunsong,et al.Influence of track geometric irregularity on dynamic stress of high-speed train axle[J].Journal of Central South University(Science and Technology),2022,53(5):1719−1729.第53卷中南大学学报(自然科学版)increase significantly with the increase of torsional irregularity amplitude.According to the safety limit of the wheel/rail vertical force,the torsional irregularity amplitude should be strictly controlled below5mm at the speedof400km/h.Key words:track geometric irregularity;high-speed train;dynamic stress of axle;wheel/rail force;safety limit轨道不平顺是列车产生振动响应的主要原因,严重的轨道不平顺会加剧轮轨间冲击振动,引起车轮和轨道损伤、噪声。
基于模态应力恢复的汽车零部件虚拟疲劳试验方法

s h i d c t st a e vru lft e ts meh d c n b c me a f c ie me n n v h ce d s n u n i ae tt i a a g t t o a e o n e e t a si e i l e i . h h t i u e v g
[ btat B sdo nt e m n oa aa s , eil m l—oydnmc n tu f peii A s c] ae nf i—l et dl nl i fxbe utbd ya is dfi ele rd tn r ie e m ysl i a ag i co
对汽车零部件进行疲劳寿命试验是保证汽车安 全的关键环节 , 传统疲劳试验方法是利用样车在试 车 场或道 路上进 行道路 试验 , 期长 、 费大 。 近年 周 耗 来, 基于计算机仿真的虚拟疲劳试验的出现 , 使得设 计人员在产品开发初期 即可进行疲劳寿命分析 , 得
到相对可 靠 的零部 件 预 测 寿命 , 大 大缩 短 了开 发 既
பைடு நூலகம்
关 键词 : 汽车零 件 ; 态应 力恢复 ; 模 疲劳 寿命 ; 虚拟 样机
Vi u lF t u e tMeh d frAuo P rsB s d o d lSr s c v r r a ai e T s t g t o o t a a e n Mo a te sRe o ey t
s n Ho g h u n z u,Co g Na n n,S a g Ja z o g& Lu Ja pn h n in h n in i g
C lg ol efMe urnc n i e n n uo ai , t nU i r o DfneTcnl y h nsa e o ct oiE gn r gadA tm t n Nai nv s f e s ehoo ,C a h 410 3 h ei o o e e g g 0 7
490柴油机曲轴应力应变有限元仿真
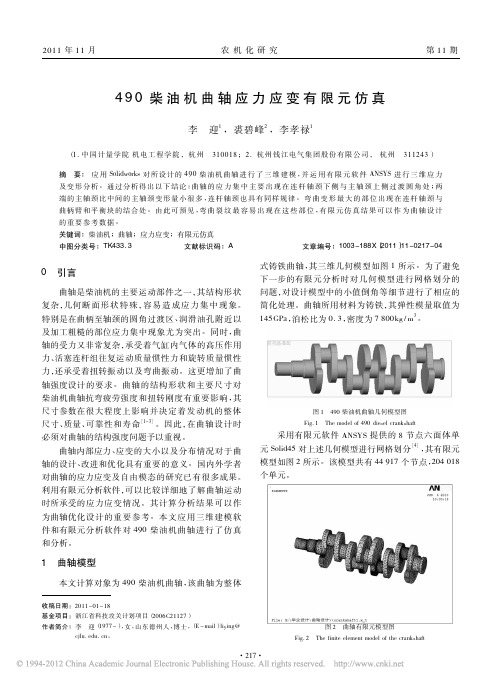
1 曲轴模型
本文计算对象为 490 柴油机曲轴,该曲轴为整体
收稿日期: 2011-01-18 基金项目: 浙江省科技攻关计划项目( 2006C21127) 作者简介: 李 迎( 1977 -) ,女,山东德州人,博士,( E - mail) liying @
式铸铁曲轴,其三维几何模型如图 1 所示。为了避免 下一步的有限元分析时对几何模型进行网格划分的 问题,对设计模型中的小值倒角等细节进行了相应的 简化处理。曲轴所用材料为铸铁,其弹性模量取值为 145GPa,泊松比为 0. 3,密度为 7 800kg / m3 。
图 1 490 柴油机曲轴几何模型图 Fig. 1 The model of 490 diesel crankshaft
2) 最大应力出现在第 1 缸处于最大爆发压力时, 而连杆轴颈的最大应力出现在第 2 缸对应的连杆轴径 处; 主轴颈的最大应力出现在第 4 缸对应的主轴径处。
图 3 490 柴油机缸内压力曲线图
Fig. 3 The pressure in cylinder curve of 490 diesel
气体压力通 过 活 塞 和 连 杆 传 递 到 曲 轴 上,其 分 量
由图 8 ~ 图 11 可以看出,曲轴发生变形的位置及 量值具有如下规律:
1) 最小变形出现在曲轴的两端,最大变形出现在 曲轴第 3 缸左边曲柄臂的过渡圆角处;
2) 各个气缸处于最大爆发压力时曲轴的变形分
·219·
2011 年 11 月
农机化研究
汽车轮毂轴承有限元仿真分析

预设多种凸度匹配关系,分析其在不同载荷作用下,最大主应力,接触长度的变 化情况,综合总体分析结果,确定最佳凸度及匹配关系。通过理论计算,给出凸 度控制方程。 这种方法的优点是考虑整体应力、 变形情况, 确定的凸度更为合理; 缺点是模型复杂,计算量大,收敛性差。 (3)凸度混合有限元分析 凸度混合有限元分析采用凸度局部有限元分析确定若干组凸度, 用凸度整体 有限元分析对所确定的凸度进行分析,综合优化分析结果,确定最终凸度方程。 这种方法模型相对简化, 减小了计算量、 提高了收敛性, 凸度计算结果更趋合理。 2. 第二代圆锥滚子轮毂轴承凸度局部有限元分析 分析对象为轿车前轮毂双列圆锥滚子轴承,结构型式为;内圈分离,外圈整 体结构,带法兰盘,属第二代产品。 2.1 滚子与滚道凸型和凸度量的确定 根据国内外轴承样品的对比分析结果及在滚子与滚道多种设计方案进行分 析的基础上, 仅对滚子与内圈有凸度的情况进行仿真分析,并提出如下滚子与滚 道凸度设计原则,在轻载时,滚子的有效接触长度为滚子长度的 60%-70%,重载 时,不出现应力集中。在此选择的凸型为修正对数曲线,采用滚子、内圈滚道带 凸度的“2 凸”设计,并对四种情况的凸度匹配关系进行对比分析。 四种情况所给出的凸度量分别为: 滚子和滚道无凸度; 滚子凸度: 2.4μm, 内 圈滚道凸度:5μm;滚子凸度:8μm, 内圈滚道凸度:10μm;滚子凸度:15μ m, 内圈滚道凸度:15μm。 2.2 滚子和滚道凸度有限元模型及仿真分析 在轴承中, 由于滚子和滚道的接触特征完全一致,因此用一个滚子和滚道接 触的局部模型就能够进行整体的凸度仿真分析。采用 ANSYS 有限元分析软件进 行分析,图 2.1 给出了有限元分析网格划分模型。 2.3 分析结果
(轴承承受的径向载荷为 0.3Cr,滚
汽车传动轴系应力应变测试方法分析

汽车传动轴系应力应变测试方法分析作者:李静来源:《科技与创新》2016年第06期摘要:随着社会经济的发展,汽车行业也朝着高功率、高扭矩的方向发展。
当汽车驱动轴系承受扭矩波动后,就会引起汽车驱动轴系的扭剪应力应变。
这些都会严重影响汽车的行驶安全。
简要分析了汽车驱动轴系应力应变测试方法,旨在为提高汽车行驶的安全性提供参考依据。
关键词:汽车传动轴系;应力应变;测试方法;行驶安全中图分类号:U467.3 文献标识码:A DOI:10.15913/ki.kjycx.2016.06.106随着经济的发展和人们生活水平的提高,汽车成为了人们生活中必不可少的交通工具,人们对汽车功率和速度的要求也在不断提高。
汽油机的应用使得汽车驱动轴系的受力情况变得越来越复杂,进而影响汽车的行驶安全。
1 应变片电测法应变片电测法主要是利用电阻应变计完成对汽车驱动轴系应变的测量,之后根据应变与应力的关系确定汽车驱动轴系表面的应力状态。
在测量过程中,可将电阻应变片粘贴在汽车传动轴系的被测点表面,一旦汽车驱动轴系的相关零件在荷载作用下发生应变,电阻应变片的电阻值就会发生变化。
这时,就可以计算出汽车传驱动系被测点的应力应变情况。
应变片电测法具有灵敏度高、精度高、尺寸小等特点,但是,应变片的测量原理也决定了其固有的缺陷。
具体包括以下2点:①应变片电测法属于一种接触式测量方法,它只能测量汽车驱动轴系表面的应变,不能测量其内部结构应变;②应变片电测法是一种电测量方法,需要使用带有导线的测量回路,因此,在利用应变片测试汽车驱动轴系应力应变时,要采取特殊的增强系统措施抵御电磁的干扰。
2 光弹性法光弹性法主要是利用双折射效应测试其应力应变情况。
当非晶体材料受到荷载作用时,会像晶体一样产生光学各向异性,从而发生双折射现象。
但是,采用这种方法时,一旦去掉荷载,双折射现象就会消失。
因此,可以将具有双折射效应的透明塑料按照一定比例制成汽车驱动轴系模型,或者直接在汽车驱动轴系上进行光贴片处理,之后再将模型或汽车传动轴系置于偏振光场中。
大客车车身骨架结构动应力仿真计算

[ 要] 运用模态综合 技术和弹性力学理论 , 摘 研究 了由路 面不平度 引起 的车身动应 力的形成机 理及其仿 真计 算方法 。将其应用 于样车车身骨架结构 的动态强度分析与设计 , 从底 盘与车 身的模态参 数和路 面激励 两方 面分 析 了样车动应力 的特征 。样 车的动态强度试验 , 验证 了仿真分析结果 的正确性。
研 究 了车 身动应 力 的仿 真计 算方 法 … 。
日 吾 J I
1 系统动力 学方程
大客车车身骨架是整车 的基体 , 承受着客车 的
所有 动 、 静态 载荷 , 结构 设计 对 于整 车 的性 能 起 着 其 举足 轻 重 的作 用 。 目前车 身 结构 动 态强 度 的校 核 主
划 分 为 簧 上 和 簧 下 两 部 分 ( l 示 系统 I和系 图 所 统 Ⅱ) 所 分 析 的 振 动 系 , 统 包 括 簧 上 结 构 和 悬 架
. 。 ; /
两部 分。将 车 桥传 到 悬 架 的载 荷 Z() 为 系 统 t作
_
振 动激 励 , 车身 骨 架 上 各 图 1 振动系统分析简图 节 点 的动态 响应 作 为输 出 。
汽
车
ቤተ መጻሕፍቲ ባይዱ
工
程
21 0 1年( 3 ) 5期 第 3卷 第
Au o t e E g n e i g t moi ‘ n ie r v n
2 1 8 01 0 9
大 客 车 车 身 骨 架 结 构 动 应 力 仿 真 计 算
石 琴, 王 涛, 张代胜 , 李宏玲
2 00 ) 30 9 ( 合肥 工业 大学机械 与汽车工程 学院, 合肥
S i n W a gT o Z a gD i e g& L n l g h , Qi n a , h n as n h i Ho gi n
应力应变分析及仿真实验【精选】

壳单元应力应变分析一、壳单元1.1 什么是壳单元应用壳单元可以模拟结构,该结构一个方向的尺度(厚度)远小于其它方向的尺度,并忽略沿厚度方向的应力。
没强调厚度方向的应变。
1.2 ANSYS 帮助文件中的应力应变关系在线性材料中,Stress 和Strain的关系为:(1)是包含6个方向的应力向量;{σ},是弹性应变,是引起应力的应变;{εel }={ε}‒{εtℎ}是总应变,是应变计测量的应变。
{ε}是热膨胀应变。
{εtℎ}通过逆运算,我们可以得到:(2)(3){εel }=D ‒1{σ} (4){ε}={εtℎ}+D ‒1{σ}由于热膨胀应变为0,所以。
下面的数据是从ansys 中导出的数{εel}={ε}据,从数据中可以看出总应变和弹性应变相等。
1.3 由应力求应变D D‒1对于某一特定材料,矩阵和是确定值。
对于各向同性材料,D矩阵是对称相等的,可以参考式(2)。
选取ansys中一些点的应力值如下,Z方向数量级非常小,几乎是0;YZ和XZ也相对小了十几个数量级,也几乎为0.NODE SX SY SZ SXY SYZ SXZ173 -0.32807E+08-0.55022E+07-0.82519E-25 0.85531E+06-0.67382E-09 0.10475E-09181 -0.32141E+08-0.53462E+07-0.80179E-25 0.12071E+06-0.65471E-09 0.14783E-102411 -0.40767E+08-0.24179E+07-0.36262E-25 0.10070E+06-0.29610E-09 0.12332E-10 D‒1通过求解得到相应点的应变值如下:X Y Z YZ ZX XY-1.5963465e-003 -1.2649597e-005 3.0647545e-004 0.0000000e+000 0.0000000e+000 9.9215956e-005-1.5642989e-003 -1.0176668e-005 2.9990011e-004 0.0000000e+000 0.0000000e+000 1.4002894e-005-2.0189921e-003 2.0524013e-004 3.4547657e-004 0.0000000e+000 0.0000000e+000 1.1681068e-005通过ansys直接读取的应变值如下:NODE EPELX EPELY EPELZ EPELXY EPELYZ EPELXZ173 -0.15963E-02-0.12650E-04 0.30648E-03 0.99216E-04-0.78163E-19 0.12150E-19181 -0.15643E-02-0.10177E-04 0.29990E-03 0.14003E-04-0.75947E-19 0.17149E-202411 -0.20190E-02 0.20524E-03 0.34548E-03 0.11681E-04-0.34348E-19 0.14305E-20从上面三个点的应变值可以看出,通过D矩阵算出来的应变值就是ansys中EPEL的值。
基于显式动力学的滚动轴承接触应力有限元分析

( 3)
中心差分算法解的稳定性条件是 τn Δt ≤ Δ t cr = π
( 4)
式中 ,τn 是有限元系统的最小固有振动周期 ,Δ t cr 为 某个临界值 , 如采用壳单元时 , Δ t cr = l min /
110
北 京 交 通 大 学 学 报 第 30 卷
¨ at =
at =
1 ( a Δ - 2 a t + a t +Δ t ) Δt 2 t - t
Δt 2
1
( 2)
17 mm ,外径为 35 mm ,滚子直径为 5. 5 mm ,滚子个 数为 10. 在 Solid edge 软件中建立实体模型 ,再将建
K = V f s ×S ×k ( 5)
考虑到滚动体的应变是最大的 ,相对而言 ,内外 圈和保持架的变形可以忽略 ,因此 ,在选择材料模型 时 ,定义内外圈和保持架为刚体 , 滚动体为弹塑性 体 . 定义刚体材料模型 , 可以大大减少计算时间 , 这 是因为刚体内的所有节点的自由度都耦合到刚体的 质量中心上 ,不论有限元模型定义了多少节点 ,刚体 仅有 6 个自由度 ,刚体的运动通过质心计算而得 ,并 把相应的位移值传递给节点 . 这里的弹塑性模型选择了用于金属和塑性成形 分析的幂指数硬化塑性模型 . 该模型考虑应变率影 响 ,带有强度和硬化系数的 Cowper- Symonds 模型 , 其应力- 应变关系为 σ 1 + y = ε
第 30 卷 第 4 期 北 京 交 通 大 学 学 报 Vol. 30 No. 4 2006 年 8 月 J OU RNAL OF B EIJ IN G J IAO TON G UN IV ERSIT Y Aug. 2006 文章编号 :167320291 ( 2006) 0420109204
模态分析方法综述-闫文飞-2015-03-30

模态分析方法综述闫文飞(北京信息科技大学机电工程院,北京100192)摘要--专业模态分析,包含多种经典和最新理论方法,支持各种模态试验方法。
目前已经在国防军工、教学科研、土木建筑、机械、铁路交通等各行业得到了非常广泛的应用,成功完成了大量的模态试验任务,包括航天器、军械、卫星、汽车、桥梁、井架、楼房等等,受到广大用户的高度评价。
专业模态分析可完成位移模态和应变模态的试验分析,可直接输出含有模态质量、刚度、阻尼、留数、振型、相关矩阵校验系数的模态分析报告。
模态分析有各种试验方法,SIMO(单输入多输出)、MISO(多输入单输出)、MIMO(多输入多输出)、ODS(运行状态变形)、OMA(环境激励模态)等。
关键词模态分析;实验模态分析法。
Abstract--Professional modal analysis, which contains a variety of classical methods and the modern theories, supports a variety of modal test methods. It has been widely used in many industries ,such as national defense, teaching, scientific research, civil construction, machinery and railway transportation.Professional modal analysis successfully completed a large number of modal test tasks, including aircraft, weapons, satellite, automobile, bridges, derrick, buildings and so on, which is spoken highly of.Professional modal analysis can not only complete displacement mode and strain modal test analysis, but also directly output the modal analysis reports that contains modal mass, stiffness, damping, residue, vibration mode and so on.There are all kinds of test modal analysis methods, such as the SIMO (single input multiple output), MISO (multiple input single output), MIMO (multiple input multiple output), ODS (deformation) running state, OMA (environmental incentive mode), etc.Key words Modal analysis;The experimental modal analysis method.0 引言振动模态分析与参数辨识是振动工程中最活跃的分支,是结构动态设汁、减振消振、振动控制、以及利用振动信号的状态检测和故障诊断的基础。
关于静强度仿真计算中车体不连续部位高应力的修正

关于静强度仿真计算中车体不连续部位高应力的修正1 问题的提出铁路货车车体静强度仿真计算一般采用线性算法,对超出材料屈服强度的应力仍按材料的弹性模量进行计算,没有考虑材料非线性的影响,这样会导致车体结构不连续部位在载荷作用下出现很高的应力,远超出材料的许用应力,但这样的应力是不真实的,在现实结构中不会出现,对于这种由于计算方法的局限而造成的高应力到底应该如何进行评价,给我们提出了一个问题。
2 国内外的相关规定2.1 国内的处理方法目前国内铁路货车车体静强度计算及试验标准没有对上述问题给出明确的说法,各公司对该问题的一般做法是对车体结构不连续部位出现超出标准规定许用应力的情况,通过不断优化结构来降低这些部位的应力,直至计算出来的应力达到标准规定的要求。
在我公司80t 级轻粘油铁路罐车设计过程中,车体静强度仿真计算出牵引梁立焊缝起始处应力比较大,超出了TB/T1335-1996 的要求,为此我们对该部位结构优化进行了大量的工作,最后确定采用在该部位增加两个圆弧形的连接板,连接板分别与枕梁腹板、牵引梁腹板焊接在一起,优化后的结构计算应力满足TB/T1335-1996 的要求。
2.2 AAR 标准中的规定AAR 标准(2007 版)CⅡ分册第7 章7.7.7.4 中指出,由于车体中必然包括结构非常不连续部位,这些部位在载荷的作用下可能会出现局部的材料屈服,在线性有限元分析中没有包括这些部位实际结构中会发生的材料屈服的影响,因此会计算出非常高的应力,但在实际结构中并没有发生很高的应力集中,输出这些高的计算应力是不真实的,因为它们是受分析方法限制的结果而不是结构本身引起的,可以用Neuber 法则(《用任意非线性应力-应变法则的剪应变柱体的应力集中理论》做一个真实应力的估算。
AAR 标准中给出了屈服强度为345MPa 材料的修正曲线,如图1 所示,很明显,应力可以转化为可以与材料的屈服强度相比较的等效应力。
分析时应该用等效应力进行评定。
机械结构随机振动动态应力高精度计算方法[发明专利]
![机械结构随机振动动态应力高精度计算方法[发明专利]](https://img.taocdn.com/s3/m/f0f85e9aa26925c52dc5bf2a.png)
专利名称:机械结构随机振动动态应力高精度计算方法专利类型:发明专利
发明人:谢慈航,薛璞,吴媛,谭邵毅,虞泽亮,陈欢欢,李玉龙申请号:CN201510282177.X
申请日:20150528
公开号:CN104850713A
公开日:
20150819
专利内容由知识产权出版社提供
摘要:本发明公开了一种机械结构随机振动动态应力高精度计算方法,将随机激励转化为确定性激励,在完全考虑模态耦合效应的同时,提高计算效率;采用模态应力系数计算,避免从位移求导计算应力时精度的损失;进行静力修正,考虑模态截取时忽略的高阶模态的影响,提高随机动态应力的计算精度。
本发明在计算时包含了全部参振模态之间的互相关项,得到的是精确解。
对于大型复杂工程结构,本发明易于操作实践,其计算效率与传统算法相比有较大提高,并且由于应力模态矩阵和高阶模态静力修正项的引入,提高了计算精度。
申请人:西北工业大学
地址:710072 陕西省西安市友谊西路127号
国籍:CN
代理机构:西北工业大学专利中心
代理人:陈星
更多信息请下载全文后查看。
基于应变模态的车轴动应力仿真计算

文章编号:1673-0291(2011)04-0130-04基于应变模态的车轴动应力仿真计算刘志明,马跃峰(北京交通大学机械与电子控制工程学院,北京100044)摘 要:基于动车组的动车车轴和拖车车轴的应变模态分析结果,结合线路实测数据,运用模态叠加法对动车组车轴进行了动应力的仿真计算,得出了两种车轴上相应测点的应力时间历程,并与线路测试数据进行了比较.结果表明:经过仿真计算得到的测点应力时间历程与实测结果比较吻合,从而验证了将应变模态与测试数据结合计算动应力的可行性,可以进一步开展疲劳强度分析.关键词:车轴;应变模态;模态叠加法;动应力;振动中图分类号:U2601111 文献标志码:ASimulation and calculation of dynamic stress to axlesbased on strain modalLI U Zhiming,M A Yue f eng(School o f M echanical,Electronic and Contr ol Engineer ing ,Beijing Jiaotong U niversity ,Beijing 100044,China)Abstract:Based on the strain modal analysis results of EMU .s motor -car ax le and trai-l car axle,and combined w ith actual line test data,simulation and calculation of dynam ic stress to EM U .s axles was done w ith modal superposition method.Stress -time history of the corresponding point on motor -car axle and trai-l car axle w as obtained,and comparison w ith the line test data w as also performed.The results show that:stress -time history of the measured points got by simulation and calculation was in g ood ag reement with the test results.Therefore,the feasibility of calculating dynamic stress w ith strain modal and test data w as verified,and it is doable to make further research on the fatigue strength analysis.Key words:axle;strain modal;modal superposition method;dynam ic stress;vibration 收稿日期:2009-11-27基金项目:国家科技支撑项目资助(M 10B300140)作者简介:刘志明(1966)),男,江西南昌人,教授,博士,博士生导师,主要从事结构疲劳可靠性研究.email:zhmliul@.在复杂结构的动态设计中,分析结构在动态载荷下的应力状态是进行强度设计和疲劳寿命评估的基础和关键,分析车轴疲劳强度的关键是得到车轴在实际运用状态下的动应力.对结构动态特性的研究主要有有限元方法和实验模态分析技术,根据所测物理量的不同,实验模态分析又分为位移模态分析和应变模态分析.位移模态分析是以位移响应(加速度)为基本参数,该技术已经在工程上广泛应用,但位移模态分析结果不能直接用于结构的疲劳设计,在运动机械和承受动载荷结构的设计校核中,从强度和疲劳的观点出发,更侧重于对结构的应力、应变分布情况的研究.应变模态分析是以结构的应变响应为基本参数,从而确定结构的应变最大点和共振疲劳点[1-2].目前对应变模态的分析一般是基于简单的梁和板,针对应变模态运用模态叠加法对结构响应进行计算分析的文献比较少.本文作者以有限元仿真的方法对高速动车组车轴进行应变模态分析,结合线路实测数据,运用模态叠加法对车轴进行动应力仿真计算.第35卷第4期2011年8月北 京 交 通 大 学 学 报JOU RNAL OF BEIJING JIA OT ON G U N IV ERSIT YVol.35No.4Aug.20111应变模态叠加法分析原理[3-5]无论是自由振动,还是受迫振动,其位移和应变响应都可以表示为各阶位移模态和应变模态的线性叠加.对于N个自由度的强迫振动系统,其位移和应变响应可表示为{X}=E N r=1q r[5r]=E N r=1G r[5r]k r-w m r+j w c re j wt(1){E}=E N r=1q r[U r]=E N r=1[U r]G rk r-w2m r+j w c re j wt(2)式中:{X}和{E}分别为位移和应变向量;[5r]和[U r]分别为第r阶位移和应变振型;q r为第r阶广义坐标;G r为第r阶广义力;w为激振频率;k r、m r 和c r为第r阶刚度、质量和阻尼矩阵.于是动车组车轴的应变可以表示为前n阶应变模态的线性叠加.本文是基于用模态分析与线路实测数据相结合来求解车轴的动应变,在测试过程中一般使用应变片测试有限个点的动应变,根据模态叠加法的原理,可以取车轴上的n个测点,提取这n个测点在某一时刻的实测动应变,组成n@1矩阵[E i],将其作为叠加后的应变向量;在有限元计算结果中提取出车轴振动时这n个点的前n阶应变模态,每个点的前n阶应变模态组成一行,n个点就可组成n@n矩阵[E ij],也就是模态叠加法中的应变振型向量.最后假设一个系数矩阵[k i],即公式中的广义坐标,用n@n的模态矩阵乘以n@1的系数矩阵[k i],所得结果等于n@1的实测动应变矩阵[E i],即E1E2sE n=E11E12,E1nE21E22,E2ns s w sE n1E n2,E nnk1k2sk n(3)式(3)中,等式左侧应变值为线路实测动应变,右侧n@n矩阵[E ij]的行代表一个测点的前n阶应变模态,乘以系数列阵后所得结果对应于左侧应变列阵中相应行的应变值.这是符合模态叠加法原理的,所以式(3)中只有系数矩阵[k i]未知,比较容易解出.求出系数矩阵后,可以在应变模态分析结果中提取其他点的前n阶应变模态,组成模态振型向量,模态振型向量与系数矩阵相乘后即可求出其对应的应变值.依据此原理,可以提取n个测点的一段应变时间历程,用模态叠加法计算对应的随时间变化的系数矩阵,再将车轴上其他点的前n阶应变模态与系数矩阵相乘,即可计算出车轴上任何一点的应变时间历程.通过对车轴的仿真分析可以得出车轴的弯曲应力以轴向为主,一般对动应力的线路测试也是以轴向动应力为主.由力学理论可知,弯曲应力与应变满足虎克定律,即R=E E(4)式中:R为应力;E为材料弹性模量;E为应变.在有限元计算结果中可以直接提取车轴的模态应力,线路实测的数据结果也可以转换为应力值,因此文中后面的计算采用应力叠加法,思路方法都与上述相同,最后可以直接得出车轴的应力时间历程.2动车车轴动应力仿真计算北京交通大学结构强度检测实验室在实际线路上对某列动车组的动车车轴和拖车车轴进行了动应力测试,得出了在各种工况下空车和重车的车轴动应力数据.在动车车轴上共分布有9个弯曲应力测点,分别位于车轴的4个断面上,左侧2个断面测点呈90b布置,右侧断面3上的3个测点呈120b布置,断面4上2个测点呈90b布置.将测点分别命名为M L1~ML4、M R1~MR5,如图1所示.(a)测点总体布置图1动车车轴测点图F ig.1F igur e of tested points of motor-car axle用有限元分析软件ANSYS对车轴进行模态分析,在后处理器中提取出各测点的各阶模态应力.这里主要为了验证所用方法的适用性,故在分析动车车轴时,由其中8个测点的动应力数据推断第9个测点的应力时间历程,最后绘制出第9个测点的应力时间历程曲线,以便与线路实测的应力时间历程进行对比.选取图1中断面1上的ML2测点进行动应力仿真计算.131第4期刘志明等:基于应变模态的车轴动应力仿真计算在模态分析结果中提取出了动车车轴上所有9个测点的前8阶模态应力,如表1所示.表1 动车车轴测点前八阶模态应力T ab.1 First eight orders of modal stress of motor -car ax leM L 1M R1M R2M L4M L 3M R4M R3M R5M L2151607-15123801997191939-2441117-1515262011025-1901465-11421-7251473-82512760100318-5104E-04-481821-4123E-043581476405195-01078-591366-64157151264-2301496928125-24414788581296-7991976171826-471005611422-1261298-163073512592020-832173280414911041241-136517403100E-01-010241-9116132110E-02-764126-8641215-0328-011137011086-3342-6175E-04-010073-1971474-01173-011807-9176E-501146-011831175E-04-19813-01001-8128E-04010*******-3210-11074-291436-11271105-2112101982-215116231129-11294依据模态叠加法,将表1中除M L2外的每个测点的前8阶模态应力组成一行,8个测点的模态应力组成8@8矩阵[R ij ],假设8@1的系数矩阵为[k i ],由[R i j ]乘以系数矩阵[k i ],得到8@1的应力响应矩阵[R i ],而[R i ]从线路测试数据提取,为已知,故可采用MAT LAB 软件求解出对应的系数矩阵.解出系数矩阵后,将M L2点的各阶模态应力与系数矩阵中对应阶数的数值相乘,可以求出M L2在该时刻的应力值.图2 M L2点实测与计算动应力波形Fig.2 T ested and calculated dy namic stress wave of M L2采用抽样的方法在测试数据中等间隔地抽出20组数据表示测点的一段应力时间历程,依次将所提取的20组数据代入求解,求得20组系数矩阵.然后结合ML2点的前8阶模态应力再进行计算,可以得出20个应力值,于是可以绘制出ML2点对应的一段应力时间历程.M L2点的计算应力时间历程曲线和实测应力时间历程曲线如图2所示.可以看出,M L2点的计算应力与实测应力变化趋势相同,但在个别点偏差值较大,最大达到4M Pa,这是由于在有限元建模中未考虑车轴上的齿轮箱等相关部件,且在模态分析中对车轴的约束设置不可能和现实运行中完全一致,因此造成了计算和实测应力时间历程曲线的偏差.后半段两者基本重合.3 拖车车轴动应力仿真计算拖车车轴分布有10个弯曲应力测点,分布于4个断面.断面1和断面4上分别有2个测点,呈90b 布置,断面2和断面3上分别有3个测点,呈120b 布置,如图3所示.(a)测点总体布置图3 拖车车轴测点图Fig.3 F igure o f tested points of tr ai -l car ax le将拖车车轴上9个测点的测试数据与模态应力结合,计算第10个测点的应力值,最后得出应力时间历程.选取图3中车轴断面2上的M R5点进行动应力仿真计算.运用模态叠加法,用模态应力的9@9矩阵和实测应力的9@1矩阵计算出一个9@1的系数矩阵,再将提取出的M R5点的前9阶模态应力矩阵乘以系数矩阵计算其对应的应力值.拖车车轴的前9阶模态应力如表2所示.同样从测试数据中抽样出20组数据,最后计算出MR5点的应力时间历程.将计算和实测应力数据绘成曲线,如图4所示.132北 京 交 通 大 学 学 报 第35卷表2 拖车车轴测点前9阶模态应力T ab.2 F irst nine or ders of modal str ess of tr ai -l car ax leM L2M L1M R1M R2M L4M R4M L3M R3M L5M R511922-151834151064-11671-2512712419762081271-1961314-176191718314-01003552-8161843-7981975-01006-4106E-04-010037130513142901835446101542613-61188512818111221826-56140141711414221839-8291733-8131151763190475812130E-060101758-010547-3644-1180E-05-4721805-0100764-011055-010106-010*********-851974671777-3741805-18252816581126-4641936-539188443111-3943-01030901008898-1137E-06-2192E+026179E-06-5195E-02-3184E-03-5153E-2-5132E-3-239153911405-231245-136149432702065-301165299158928120728014-010********-175********-3159E-043120E-04-78214753-88511385311-11526-25105-271705-110911122101705-1901235-18718742071055214113由图4可以看出,MR5点的计算应力与实测应力变化趋势一致,两者之间始终有一个2MPa 左右的差值,造成误差的原因与动车车轴相似.可见实测与计算动应力波形比较吻合,两者有较好的一致性.图4 MR5点实测与计算动应力波形F ig.4 T ested and calculated dynamic str ess wave of M R54 小结1)在基于有限元的应变模态分析结果中提取所需阶数的模态应力,结合线路实测数据,运用模态叠加法对动车组车轴进行动应力仿真计算,可以得出高速动车组动车车轴和拖车车轴上相应测点的应力时间历程.将得出的数据结果与线路测试数据进行对比分析,验证了所用方法的可行性.2)运用文中的方法和思路,可以计算出车轴上所有未测试点在实际运用工况下的动应力,由此可以编制应力谱,开展疲劳强度分析,也可以进一步开展载荷谱研究.3)运用模态叠加法计算结构的动态响应时,需要考虑对截断模态的选取,以求达到满足精度的条件下用最少的模态阶数进行计算.文中选取了较多的模态阶数,所以更能满足计算精度.在今后的研究中还需要对模态叠加中所用的模态阶数进行讨论,此外还需要对有限元模型的细化和模态分析的约束设置进行研究,从而最大限度地缩小误差.参考文献(References):[1]王文静,刘志明,缪龙秀.基于实验模态的结构应变模态分析[J].北方交通大学学报,2000,24(4):20-24.WA NG Wenjing ,L IU Z himing,M IAO Longx iu.T he strain modal analysis of structure based on modal test ing [J].Journal of Northern Jiaotong U niversity ,2000,24(4):20-24.(in Chinese)[2]许本文,焦群英.机械振动与模态分析基础[M ].北京:机械工业出版社,1998:15-40.XU Benwen,JIAO Q unying.M echanical v ibration and modal analysis basis[M ].Beijing:China M achine Press,1998:15-40.(in Chinese)[3]秦文科,鲁丽君,查小鹏.结构应变模态获取途径的理论与仿真研究[J].国外建材科技,2008,29(3):81-83.Q IN Wenke,L U L ijun,ZHA Xiaopeng.T heory and sim -ulation on the access to the strain mo de [J].Science and T echnology of Ov erseas Building M aterials,2008,29(3):81-83.(in Chinese)[4]Yam L H,L eung T P,Li D B,et al.T heoretical and ex per -imental study of modal strain analysis[J].Jour nal o f Sound and Vibration,1996,191(2):251-260.[5]Grubisic V,Fischer ag e related desig n and validationof wheel set ax les[C]M Structur al Durability in Railw ay Engineer ing,Darmstadt ,4th F raunhofer L BF -M eeting,2006.133第4期 刘志明等:基于应变模态的车轴动应力仿真计算。
基于总应变能的多轴疲劳模型研究

第19卷第4期船舶力学Vol.19No.4 2015年4月Journal of Ship Mechanics Apr.2015文章编号:1007-7294(2015)04-0405-06基于总应变能的多轴疲劳模型研究孙楠楠1,李国祥1,白书战1,王洋2,魏涛2(1山东大学能源与动力工程学院,济南250061;2潍柴动力股份有限公司技术中心,山东潍坊261205)摘要:该研究提出一种多轴疲劳寿命预测模型。
结合现有的几种多轴疲劳模型的优点和不足之处,分别对正应变能部分和剪应变能部分做出了修正,提出了一个能够适用于多种载荷形式的多轴疲劳寿命预测模型。
该模型通过求解莫尔圆把剪应变幅作为临界面判定参量,把临界面上的总应变能作为损伤参量。
运用SNCM630合金钢、纯钛和钛合金等4种材料的疲劳试验数据对提出的模型进行评估和验证,尽管材料特性和载荷形式各异,但所有的预测寿命基本都落在了试验寿命两倍的公差带以内,这证明提出的新模型具有较高的预测精度。
关键词:多轴疲劳;能量准则;临界面;多轴比例—非比例载荷中图分类号:TK4TG1文献标识码:A doi:10.3969/j.issn.1007-7294.2015.04.008Study on multiaxial fatigue criterion based ontotal strain energySUN Nan-nan1,LI Guo-xiang1,BAI Shu-zhan1,WANG Yang2,WEI Tao2(1School of Energy&Power Engineering,Shandong University,Jinan250061,China;2R&D Center,Weichai Power Co.,Ltd,Weifang261205,China)Abstract:A new multi-axial model fatigue criterion is proposed.Taking into account the advantage and shortage of several existing multi-axial fatigue criteria,modifications are made on the normal energy and shear energy part,and a new multiaxial fatigue criterion is proposed to predict fatigue life under proportion-al and non-proportional loadings.Through the calculation of Mohr’s circle,shear strain amplitude is taken as the parameter to determine the critical plane and total strain energy is taken as the damage parameter of the new model.The model is evaluated by the multiaxial fatigue test data of SNCM630steel,pure titani-um,titanium alloy BT9,and titanium alloy TC4.Although loadings are complex and various,the predicted data are almost within a factor of2scatter band of the test results.The results show that the new model has a higher predicted accuracy.Key words:multi-axial fatigue;energy criterion;critical plane;proportional and non-proportional loading0引言随着对弹塑性力学和疲劳裂纹萌生机理的深入研究,基于应变的疲劳寿命模型研究得到了很好的发展,弥补了S-N方法只基于统计数据但缺乏深入的理论基础的弊端。
零件局部应力—应变计算新方法
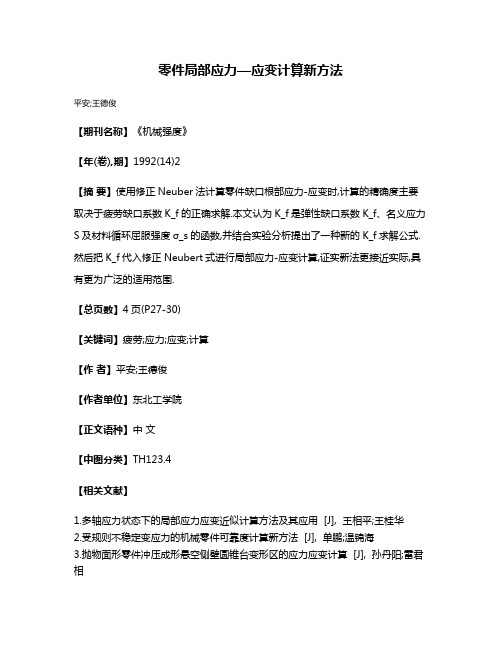
零件局部应力—应变计算新方法
平安;王德俊
【期刊名称】《机械强度》
【年(卷),期】1992(14)2
【摘要】使用修正Neuber法计算零件缺口根部应力-应变时,计算的精确度主要取决于疲劳缺口系数K_f的正确求解.本文认为K_f是弹性缺口系数K_f、名义应力S及材料循环屈服强度σ_s的函数,并结合实验分析提出了一种新的K_f求解公式.然后把K_f代入修正Neubert式进行局部应力-应变计算,证实新法更接近实际,具有更为广泛的适用范围.
【总页数】4页(P27-30)
【关键词】疲劳;应力;应变;计算
【作者】平安;王德俊
【作者单位】东北工学院
【正文语种】中文
【中图分类】TH123.4
【相关文献】
1.多轴应力状态下的局部应力应变近似计算方法及其应用 [J], 王相平;王桂华
2.受规则不稳定变应力的机械零件可靠度计算新方法 [J], 单鹏;温锦海
3.抛物面形零件冲压成形悬空侧壁圆锥台变形区的应力应变计算 [J], 孙丹阳;雷君相
4.圆锥形零件冲压成形悬空侧壁圆锥台变形区的应力应变计算 [J], 雷君相
5.应用解理断裂局部法预测任意应力—应变关系材料断裂韧度K_(IC)的新方法 [J], 惠虎;李培宁;轩福贞;刘长军;曲家棣
因版权原因,仅展示原文概要,查看原文内容请购买。
- 1、下载文档前请自行甄别文档内容的完整性,平台不提供额外的编辑、内容补充、找答案等附加服务。
- 2、"仅部分预览"的文档,不可在线预览部分如存在完整性等问题,可反馈申请退款(可完整预览的文档不适用该条件!)。
- 3、如文档侵犯您的权益,请联系客服反馈,我们会尽快为您处理(人工客服工作时间:9:00-18:30)。
文章编号:1673-0291(2011)04-0130-04基于应变模态的车轴动应力仿真计算刘志明,马跃峰(北京交通大学机械与电子控制工程学院,北京100044)摘 要:基于动车组的动车车轴和拖车车轴的应变模态分析结果,结合线路实测数据,运用模态叠加法对动车组车轴进行了动应力的仿真计算,得出了两种车轴上相应测点的应力时间历程,并与线路测试数据进行了比较.结果表明:经过仿真计算得到的测点应力时间历程与实测结果比较吻合,从而验证了将应变模态与测试数据结合计算动应力的可行性,可以进一步开展疲劳强度分析.关键词:车轴;应变模态;模态叠加法;动应力;振动中图分类号:U2601111 文献标志码:ASimulation and calculation of dynamic stress to axlesbased on strain modalLI U Zhiming,M A Yue f eng(School o f M echanical,Electronic and Contr ol Engineer ing ,Beijing Jiaotong U niversity ,Beijing 100044,China)Abstract:Based on the strain modal analysis results of EMU .s motor -car ax le and trai-l car axle,and combined w ith actual line test data,simulation and calculation of dynam ic stress to EM U .s axles was done w ith modal superposition method.Stress -time history of the corresponding point on motor -car axle and trai-l car axle w as obtained,and comparison w ith the line test data w as also performed.The results show that:stress -time history of the measured points got by simulation and calculation was in g ood ag reement with the test results.Therefore,the feasibility of calculating dynamic stress w ith strain modal and test data w as verified,and it is doable to make further research on the fatigue strength analysis.Key words:axle;strain modal;modal superposition method;dynam ic stress;vibration 收稿日期:2009-11-27基金项目:国家科技支撑项目资助(M 10B300140)作者简介:刘志明(1966)),男,江西南昌人,教授,博士,博士生导师,主要从事结构疲劳可靠性研究.email:zhmliul@.在复杂结构的动态设计中,分析结构在动态载荷下的应力状态是进行强度设计和疲劳寿命评估的基础和关键,分析车轴疲劳强度的关键是得到车轴在实际运用状态下的动应力.对结构动态特性的研究主要有有限元方法和实验模态分析技术,根据所测物理量的不同,实验模态分析又分为位移模态分析和应变模态分析.位移模态分析是以位移响应(加速度)为基本参数,该技术已经在工程上广泛应用,但位移模态分析结果不能直接用于结构的疲劳设计,在运动机械和承受动载荷结构的设计校核中,从强度和疲劳的观点出发,更侧重于对结构的应力、应变分布情况的研究.应变模态分析是以结构的应变响应为基本参数,从而确定结构的应变最大点和共振疲劳点[1-2].目前对应变模态的分析一般是基于简单的梁和板,针对应变模态运用模态叠加法对结构响应进行计算分析的文献比较少.本文作者以有限元仿真的方法对高速动车组车轴进行应变模态分析,结合线路实测数据,运用模态叠加法对车轴进行动应力仿真计算.第35卷第4期2011年8月北 京 交 通 大 学 学 报JOU RNAL OF BEIJING JIA OT ON G U N IV ERSIT YVol.35No.4Aug.20111应变模态叠加法分析原理[3-5]无论是自由振动,还是受迫振动,其位移和应变响应都可以表示为各阶位移模态和应变模态的线性叠加.对于N个自由度的强迫振动系统,其位移和应变响应可表示为{X}=E N r=1q r[5r]=E N r=1G r[5r]k r-w m r+j w c re j wt(1){E}=E N r=1q r[U r]=E N r=1[U r]G rk r-w2m r+j w c re j wt(2)式中:{X}和{E}分别为位移和应变向量;[5r]和[U r]分别为第r阶位移和应变振型;q r为第r阶广义坐标;G r为第r阶广义力;w为激振频率;k r、m r 和c r为第r阶刚度、质量和阻尼矩阵.于是动车组车轴的应变可以表示为前n阶应变模态的线性叠加.本文是基于用模态分析与线路实测数据相结合来求解车轴的动应变,在测试过程中一般使用应变片测试有限个点的动应变,根据模态叠加法的原理,可以取车轴上的n个测点,提取这n个测点在某一时刻的实测动应变,组成n@1矩阵[E i],将其作为叠加后的应变向量;在有限元计算结果中提取出车轴振动时这n个点的前n阶应变模态,每个点的前n阶应变模态组成一行,n个点就可组成n@n矩阵[E ij],也就是模态叠加法中的应变振型向量.最后假设一个系数矩阵[k i],即公式中的广义坐标,用n@n的模态矩阵乘以n@1的系数矩阵[k i],所得结果等于n@1的实测动应变矩阵[E i],即E1E2sE n=E11E12,E1nE21E22,E2ns s w sE n1E n2,E nnk1k2sk n(3)式(3)中,等式左侧应变值为线路实测动应变,右侧n@n矩阵[E ij]的行代表一个测点的前n阶应变模态,乘以系数列阵后所得结果对应于左侧应变列阵中相应行的应变值.这是符合模态叠加法原理的,所以式(3)中只有系数矩阵[k i]未知,比较容易解出.求出系数矩阵后,可以在应变模态分析结果中提取其他点的前n阶应变模态,组成模态振型向量,模态振型向量与系数矩阵相乘后即可求出其对应的应变值.依据此原理,可以提取n个测点的一段应变时间历程,用模态叠加法计算对应的随时间变化的系数矩阵,再将车轴上其他点的前n阶应变模态与系数矩阵相乘,即可计算出车轴上任何一点的应变时间历程.通过对车轴的仿真分析可以得出车轴的弯曲应力以轴向为主,一般对动应力的线路测试也是以轴向动应力为主.由力学理论可知,弯曲应力与应变满足虎克定律,即R=E E(4)式中:R为应力;E为材料弹性模量;E为应变.在有限元计算结果中可以直接提取车轴的模态应力,线路实测的数据结果也可以转换为应力值,因此文中后面的计算采用应力叠加法,思路方法都与上述相同,最后可以直接得出车轴的应力时间历程.2动车车轴动应力仿真计算北京交通大学结构强度检测实验室在实际线路上对某列动车组的动车车轴和拖车车轴进行了动应力测试,得出了在各种工况下空车和重车的车轴动应力数据.在动车车轴上共分布有9个弯曲应力测点,分别位于车轴的4个断面上,左侧2个断面测点呈90b布置,右侧断面3上的3个测点呈120b布置,断面4上2个测点呈90b布置.将测点分别命名为M L1~ML4、M R1~MR5,如图1所示.(a)测点总体布置图1动车车轴测点图F ig.1F igur e of tested points of motor-car axle用有限元分析软件ANSYS对车轴进行模态分析,在后处理器中提取出各测点的各阶模态应力.这里主要为了验证所用方法的适用性,故在分析动车车轴时,由其中8个测点的动应力数据推断第9个测点的应力时间历程,最后绘制出第9个测点的应力时间历程曲线,以便与线路实测的应力时间历程进行对比.选取图1中断面1上的ML2测点进行动应力仿真计算.131第4期刘志明等:基于应变模态的车轴动应力仿真计算在模态分析结果中提取出了动车车轴上所有9个测点的前8阶模态应力,如表1所示.表1 动车车轴测点前八阶模态应力T ab.1 First eight orders of modal stress of motor -car ax leM L 1M R1M R2M L4M L 3M R4M R3M R5M L2151607-15123801997191939-2441117-1515262011025-1901465-11421-7251473-82512760100318-5104E-04-481821-4123E-043581476405195-01078-591366-64157151264-2301496928125-24414788581296-7991976171826-471005611422-1261298-163073512592020-832173280414911041241-136517403100E-01-010241-9116132110E-02-764126-8641215-0328-011137011086-3342-6175E-04-010073-1971474-01173-011807-9176E-501146-011831175E-04-19813-01001-8128E-04010*******-3210-11074-291436-11271105-2112101982-215116231129-11294依据模态叠加法,将表1中除M L2外的每个测点的前8阶模态应力组成一行,8个测点的模态应力组成8@8矩阵[R ij ],假设8@1的系数矩阵为[k i ],由[R i j ]乘以系数矩阵[k i ],得到8@1的应力响应矩阵[R i ],而[R i ]从线路测试数据提取,为已知,故可采用MAT LAB 软件求解出对应的系数矩阵.解出系数矩阵后,将M L2点的各阶模态应力与系数矩阵中对应阶数的数值相乘,可以求出M L2在该时刻的应力值.图2 M L2点实测与计算动应力波形Fig.2 T ested and calculated dy namic stress wave of M L2采用抽样的方法在测试数据中等间隔地抽出20组数据表示测点的一段应力时间历程,依次将所提取的20组数据代入求解,求得20组系数矩阵.然后结合ML2点的前8阶模态应力再进行计算,可以得出20个应力值,于是可以绘制出ML2点对应的一段应力时间历程.M L2点的计算应力时间历程曲线和实测应力时间历程曲线如图2所示.可以看出,M L2点的计算应力与实测应力变化趋势相同,但在个别点偏差值较大,最大达到4M Pa,这是由于在有限元建模中未考虑车轴上的齿轮箱等相关部件,且在模态分析中对车轴的约束设置不可能和现实运行中完全一致,因此造成了计算和实测应力时间历程曲线的偏差.后半段两者基本重合.3 拖车车轴动应力仿真计算拖车车轴分布有10个弯曲应力测点,分布于4个断面.断面1和断面4上分别有2个测点,呈90b 布置,断面2和断面3上分别有3个测点,呈120b 布置,如图3所示.(a)测点总体布置图3 拖车车轴测点图Fig.3 F igure o f tested points of tr ai -l car ax le将拖车车轴上9个测点的测试数据与模态应力结合,计算第10个测点的应力值,最后得出应力时间历程.选取图3中车轴断面2上的M R5点进行动应力仿真计算.运用模态叠加法,用模态应力的9@9矩阵和实测应力的9@1矩阵计算出一个9@1的系数矩阵,再将提取出的M R5点的前9阶模态应力矩阵乘以系数矩阵计算其对应的应力值.拖车车轴的前9阶模态应力如表2所示.同样从测试数据中抽样出20组数据,最后计算出MR5点的应力时间历程.将计算和实测应力数据绘成曲线,如图4所示.132北 京 交 通 大 学 学 报 第35卷表2 拖车车轴测点前9阶模态应力T ab.2 F irst nine or ders of modal str ess of tr ai -l car ax leM L2M L1M R1M R2M L4M R4M L3M R3M L5M R511922-151834151064-11671-2512712419762081271-1961314-176191718314-01003552-8161843-7981975-01006-4106E-04-010037130513142901835446101542613-61188512818111221826-56140141711414221839-8291733-8131151763190475812130E-060101758-010547-3644-1180E-05-4721805-0100764-011055-010106-010*********-851974671777-3741805-18252816581126-4641936-539188443111-3943-01030901008898-1137E-06-2192E+026179E-06-5195E-02-3184E-03-5153E-2-5132E-3-239153911405-231245-136149432702065-301165299158928120728014-010********-175********-3159E-043120E-04-78214753-88511385311-11526-25105-271705-110911122101705-1901235-18718742071055214113由图4可以看出,MR5点的计算应力与实测应力变化趋势一致,两者之间始终有一个2MPa 左右的差值,造成误差的原因与动车车轴相似.可见实测与计算动应力波形比较吻合,两者有较好的一致性.图4 MR5点实测与计算动应力波形F ig.4 T ested and calculated dynamic str ess wave of M R54 小结1)在基于有限元的应变模态分析结果中提取所需阶数的模态应力,结合线路实测数据,运用模态叠加法对动车组车轴进行动应力仿真计算,可以得出高速动车组动车车轴和拖车车轴上相应测点的应力时间历程.将得出的数据结果与线路测试数据进行对比分析,验证了所用方法的可行性.2)运用文中的方法和思路,可以计算出车轴上所有未测试点在实际运用工况下的动应力,由此可以编制应力谱,开展疲劳强度分析,也可以进一步开展载荷谱研究.3)运用模态叠加法计算结构的动态响应时,需要考虑对截断模态的选取,以求达到满足精度的条件下用最少的模态阶数进行计算.文中选取了较多的模态阶数,所以更能满足计算精度.在今后的研究中还需要对模态叠加中所用的模态阶数进行讨论,此外还需要对有限元模型的细化和模态分析的约束设置进行研究,从而最大限度地缩小误差.参考文献(References):[1]王文静,刘志明,缪龙秀.基于实验模态的结构应变模态分析[J].北方交通大学学报,2000,24(4):20-24.WA NG Wenjing ,L IU Z himing,M IAO Longx iu.T he strain modal analysis of structure based on modal test ing [J].Journal of Northern Jiaotong U niversity ,2000,24(4):20-24.(in Chinese)[2]许本文,焦群英.机械振动与模态分析基础[M ].北京:机械工业出版社,1998:15-40.XU Benwen,JIAO Q unying.M echanical v ibration and modal analysis basis[M ].Beijing:China M achine Press,1998:15-40.(in Chinese)[3]秦文科,鲁丽君,查小鹏.结构应变模态获取途径的理论与仿真研究[J].国外建材科技,2008,29(3):81-83.Q IN Wenke,L U L ijun,ZHA Xiaopeng.T heory and sim -ulation on the access to the strain mo de [J].Science and T echnology of Ov erseas Building M aterials,2008,29(3):81-83.(in Chinese)[4]Yam L H,L eung T P,Li D B,et al.T heoretical and ex per -imental study of modal strain analysis[J].Jour nal o f Sound and Vibration,1996,191(2):251-260.[5]Grubisic V,Fischer ag e related desig n and validationof wheel set ax les[C]M Structur al Durability in Railw ay Engineer ing,Darmstadt ,4th F raunhofer L BF -M eeting,2006.133第4期 刘志明等:基于应变模态的车轴动应力仿真计算。