磷化机理
火山岩型磷化作用机理与成岩环境分析
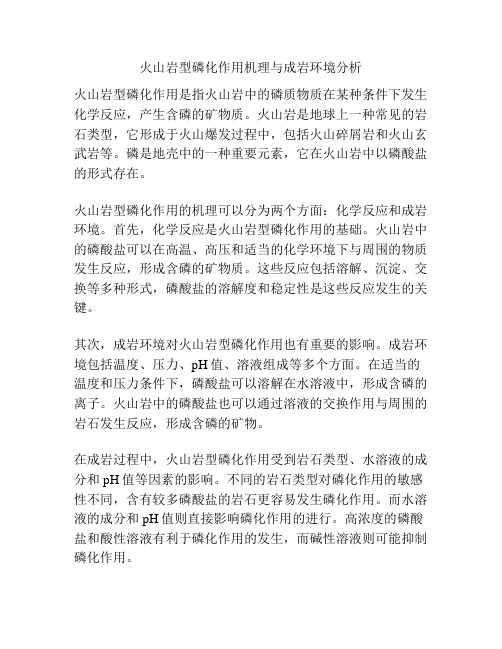
火山岩型磷化作用机理与成岩环境分析火山岩型磷化作用是指火山岩中的磷质物质在某种条件下发生化学反应,产生含磷的矿物质。
火山岩是地球上一种常见的岩石类型,它形成于火山爆发过程中,包括火山碎屑岩和火山玄武岩等。
磷是地壳中的一种重要元素,它在火山岩中以磷酸盐的形式存在。
火山岩型磷化作用的机理可以分为两个方面:化学反应和成岩环境。
首先,化学反应是火山岩型磷化作用的基础。
火山岩中的磷酸盐可以在高温、高压和适当的化学环境下与周围的物质发生反应,形成含磷的矿物质。
这些反应包括溶解、沉淀、交换等多种形式,磷酸盐的溶解度和稳定性是这些反应发生的关键。
其次,成岩环境对火山岩型磷化作用也有重要的影响。
成岩环境包括温度、压力、pH值、溶液组成等多个方面。
在适当的温度和压力条件下,磷酸盐可以溶解在水溶液中,形成含磷的离子。
火山岩中的磷酸盐也可以通过溶液的交换作用与周围的岩石发生反应,形成含磷的矿物。
在成岩过程中,火山岩型磷化作用受到岩石类型、水溶液的成分和pH值等因素的影响。
不同的岩石类型对磷化作用的敏感性不同,含有较多磷酸盐的岩石更容易发生磷化作用。
而水溶液的成分和pH值则直接影响磷化作用的进行。
高浓度的磷酸盐和酸性溶液有利于磷化作用的发生,而碱性溶液则可能抑制磷化作用。
火山岩型磷化作用在地质历史中具有重要的意义。
它是磷矿床形成的主要途径之一,也是磷肥资源的重要来源。
在岩石圈的构造作用下,磷酸盐通过地下水和热液等途径进入火山岩中,形成含磷的矿物质。
随着地壳的抬升和侵蚀,这些含磷的矿物质被暴露在地表,形成磷矿床。
由于磷是植物生长的必需元素,磷矿床是磷肥资源的重要来源。
火山岩型磷化作用的认识对于磷资源的勘探和利用具有重要的指导意义。
总之,火山岩型磷化作用是火山岩中的磷酸盐在特定的化学环境下发生反应,形成含磷的矿物质的过程。
化学反应和成岩环境是火山岩型磷化作用的机理,岩石类型、水溶液的成分和pH值等因素对其影响很大。
火山岩型磷化作用在地质历史中起着重要的作用,是磷矿床形成和磷肥资源开发的重要途径。
磷化钝化膜形成原理
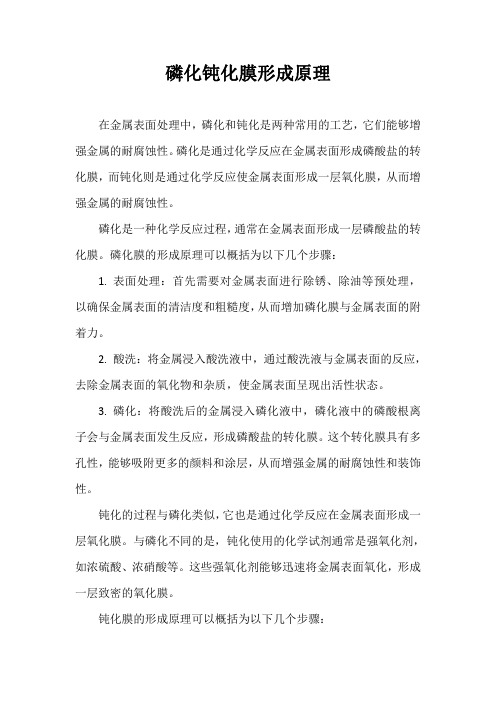
磷化钝化膜形成原理在金属表面处理中,磷化和钝化是两种常用的工艺,它们能够增强金属的耐腐蚀性。
磷化是通过化学反应在金属表面形成磷酸盐的转化膜,而钝化则是通过化学反应使金属表面形成一层氧化膜,从而增强金属的耐腐蚀性。
磷化是一种化学反应过程,通常在金属表面形成一层磷酸盐的转化膜。
磷化膜的形成原理可以概括为以下几个步骤:1.表面处理:首先需要对金属表面进行除锈、除油等预处理,以确保金属表面的清洁度和粗糙度,从而增加磷化膜与金属表面的附着力。
2.酸洗:将金属浸入酸洗液中,通过酸洗液与金属表面的反应,去除金属表面的氧化物和杂质,使金属表面呈现出活性状态。
3.磷化:将酸洗后的金属浸入磷化液中,磷化液中的磷酸根离子会与金属表面发生反应,形成磷酸盐的转化膜。
这个转化膜具有多孔性,能够吸附更多的颜料和涂层,从而增强金属的耐腐蚀性和装饰性。
钝化的过程与磷化类似,它也是通过化学反应在金属表面形成一层氧化膜。
与磷化不同的是,钝化使用的化学试剂通常是强氧化剂,如浓硫酸、浓硝酸等。
这些强氧化剂能够迅速将金属表面氧化,形成一层致密的氧化膜。
钝化膜的形成原理可以概括为以下几个步骤:1.表面处理:同样需要对金属表面进行除锈、除油等预处理,以提高钝化膜与金属表面的附着力。
2.酸洗:将金属浸入酸洗液中,去除金属表面的氧化物和杂质,使金属表面呈现出活性状态。
3.钝化:将酸洗后的金属浸入钝化液中,钝化液中的强氧化剂会迅速将金属表面氧化,形成一层致密的氧化膜。
这个氧化膜能够阻挡腐蚀介质对金属的侵蚀,从而提高金属的耐腐蚀性。
通过磷化和钝化处理,金属表面的耐腐蚀性能得到了显著提高。
同时,这两种处理方法还可以增强金属的装饰性能,使其具有更美观的外观。
在实际应用中,应根据不同的需求选择合适的处理方法。
总的来说,磷化、钝化都是通过化学反应在金属表面形成一层保护膜,从而提高金属的耐腐蚀性。
虽然它们的化学反应机理和所用试剂有所不同,但它们的表面处理和反应过程是相似的。
磷化成膜机理

磷化成膜机理1、化学转化过程所用的磷化液都是由磷酸、碱金属或重金属的磷酸二氢盐及氧化性促进剂组成的酸性溶液。
因此,整个磷化过程都包括含有基体金属的溶解反应、难溶磷酸盐结晶沉积的成膜过程及氧化性促进剂的去极化作用。
①基体金属的溶解磷化液的PH 值一般都在2~5.5之间,呈酸性。
因此当金属和此酸性溶液接触时,必然发生由局部阳极和局部阴极反应组成的金属溶解过程:局部阳极 Me Me 2++2e 局部阴极 2H ++2e H 2↑ ②成膜反应由于局部阴极区域H +被还原而消耗,酸度下降,使得在第一阶段形成的可溶性二价金属磷酸二氢盐离解成溶解度较小的磷酸一氢盐:Me (H 2PO 4)2 MeHPO 4+H 3PO 4只要PH 上升到一定程度,则主要离解成不溶性二价金属磷酸盐。
此离解则比较迅速:Me (H 2PO 4)2 MeHPO 4+4H 3PO 4同时 MeHPO 4 Me 3(PO 4)2+H 3PO 4难溶的Me 3(PO 4)2在金属表面的阴极区域沉积析出。
当整个阴极区域都被沉积物覆盖时,成膜反应结束,从而在金属表面形成完整的磷化膜覆盖。
由于成膜反应的可溶性二价金属磷酸二氢盐可以是金属溶解生成的,也可以是溶液中原有的配方组成。
除磷酸铁盐膜外,其他所有的磷化膜的成膜物质都是添加配方中的原料。
难溶性磷酸盐的溶积度如表:氧化性促进剂的去极化作用和对金属溶解的促进金属溶解时产生的氢气易吸附于阴极的金属表面,从而阻碍水解产生的二价金属磷酸盐在阴极区域的沉积,不能形成磷化膜。
水解产物则于溶液中析出成为渣,即浪费成膜原料,也使渣量大大增加。
这样在工艺方面将造成困难,对膜的性能也不能保证,因为孔隙率很大。
氧化剂的去极化作用是将还原形成的初生态氢氧化成水;2[H]+[O] H2O与去极化作用密切相关的是促进剂对金属溶解的促进。
它是通过促进剂对H2的氧化和沉积作用,导致阳极电流密度增加而提高溶解速率,即提高可溶性二价金属磷酸二氢盐的生成速率。
钢铁的锌系磷化
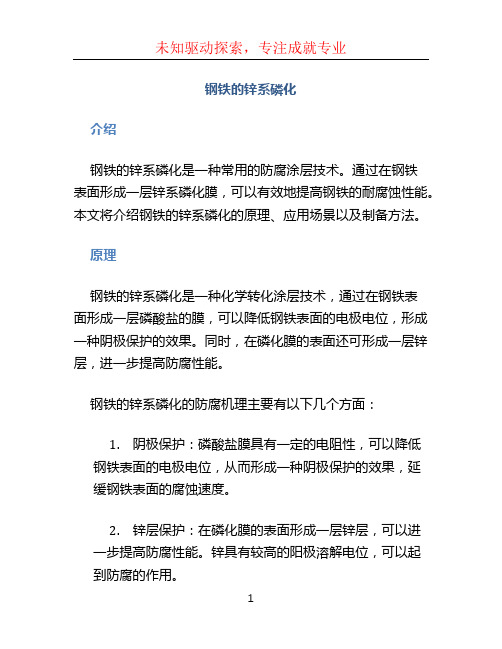
钢铁的锌系磷化介绍钢铁的锌系磷化是一种常用的防腐涂层技术。
通过在钢铁表面形成一层锌系磷化膜,可以有效地提高钢铁的耐腐蚀性能。
本文将介绍钢铁的锌系磷化的原理、应用场景以及制备方法。
原理钢铁的锌系磷化是一种化学转化涂层技术,通过在钢铁表面形成一层磷酸盐的膜,可以降低钢铁表面的电极电位,形成一种阴极保护的效果。
同时,在磷化膜的表面还可形成一层锌层,进一步提高防腐性能。
钢铁的锌系磷化的防腐机理主要有以下几个方面:1.阴极保护:磷酸盐膜具有一定的电阻性,可以降低钢铁表面的电极电位,从而形成一种阴极保护的效果,延缓钢铁表面的腐蚀速度。
2.锌层保护:在磷化膜的表面形成一层锌层,可以进一步提高防腐性能。
锌具有较高的阳极溶解电位,可以起到防腐的作用。
3.磷酸盐膜的吸附能力:磷酸盐膜具有良好的吸附能力,可以与钢铁表面的氧化铁发生反应,形成一个致密的磷酸盐膜。
这种膜具有很好的附着力和耐腐蚀性能。
应用场景钢铁的锌系磷化技术广泛应用于钢结构、汽车零部件、船舶、建筑材料等领域。
主要用于提高钢铁材料的耐腐蚀性能,延长使用寿命。
具体应用场景包括:1.钢结构:钢结构在室内外环境下易受到腐蚀,通过施加锌系磷化涂层可以有效延缓腐蚀速度,提高钢结构的耐久性。
2.汽车零部件:汽车零部件常暴露在潮湿、多灰尘的环境中,易受到腐蚀影响。
通过施加锌系磷化涂层可以提高零部件的耐腐蚀性能,延长使用寿命。
3.船舶:船舶在海洋环境中容易受到海水腐蚀。
通过施加锌系磷化涂层可以提高船舶的耐腐蚀性能,延长使用寿命。
4.建筑材料:建筑材料在室外环境下易受到大气环境和酸雨的腐蚀。
通过施加锌系磷化涂层可以提高建筑材料的耐腐蚀性能,延长使用寿命。
制备方法钢铁的锌系磷化有多种制备方法,常用的方法包括酸洗法、电化学法和浸泡法等。
1.酸洗法:将钢铁表面经过酸洗处理,去除表面的氧化铁和杂质,然后放入磷酸盐溶液中进行磷化反应。
这种方法制备的锌系磷化膜结构致密,耐腐蚀性能较好。
磷化基本原理
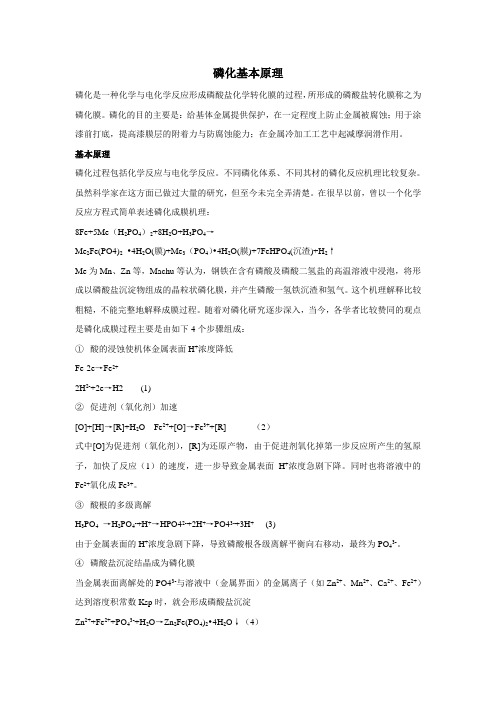
磷化基本原理磷化是一种化学与电化学反应形成磷酸盐化学转化膜的过程,所形成的磷酸盐转化膜称之为磷化膜。
磷化的目的主要是:给基体金属提供保护,在一定程度上防止金属被腐蚀;用于涂漆前打底,提高漆膜层的附着力与防腐蚀能力;在金属冷加工工艺中起减摩润滑作用。
基本原理磷化过程包括化学反应与电化学反应。
不同磷化体系、不同其材的磷化反应机理比较复杂。
虽然科学家在这方面已做过大量的研究,但至今未完全弄清楚。
在很早以前,曾以一个化学反应方程式简单表述磷化成膜机理:8Fe+5Me(H2PO4)2+8H2O+H3PO4→Me2Fe(PO4)2•4H2O(膜)+Me3(PO4)•4H2O(膜)+7FeHPO4(沉渣)+H2↑Me为Mn、Zn等,Machu等认为,钢铁在含有磷酸及磷酸二氢盐的高温溶液中浸泡,将形成以磷酸盐沉淀物组成的晶粒状磷化膜,并产生磷酸一氢铁沉渣和氢气。
这个机理解释比较粗糙,不能完整地解释成膜过程。
随着对磷化研究逐步深入,当今,各学者比较赞同的观点是磷化成膜过程主要是由如下4个步骤组成:①酸的浸蚀使机体金属表面H+浓度降低Fe-2e→Fe2+2H2-+2e→H2 (1)②促进剂(氧化剂)加速[O]+[H]→[R]+H2O Fe2++[O]→Fe3++[R] (2)式中[O]为促进剂(氧化剂),[R]为还原产物,由于促进剂氧化掉第一步反应所产生的氢原子,加快了反应(1)的速度,进一步导致金属表面H+浓度急剧下降。
同时也将溶液中的Fe2+氧化成Fe3+。
③酸根的多级离解H3PO4→H2PO4-+H+→HPO42-+2H+→PO43-+3H+ (3)由于金属表面的H+浓度急剧下降,导致磷酸根各级离解平衡向右移动,最终为PO43-。
④磷酸盐沉淀结晶成为磷化膜当金属表面离解处的PO43-与溶液中(金属界面)的金属离子(如Zn2+、Mn2+、Ca2+、Fe2+)达到溶度积常数Ksp时,就会形成磷酸盐沉淀Zn2++Fe2++PO43-+H2O→Zn2Fe(PO4)2•4H2O↓(4)3Zn2++2PO43-+4H2O→Zn3(PO4)2••4H2O↓(5)磷酸盐沉淀与水分子一起形成磷化晶核,晶核继续长大成为磷化晶粒,无数个晶粒紧密堆集形成磷化膜。
钢板的磷化
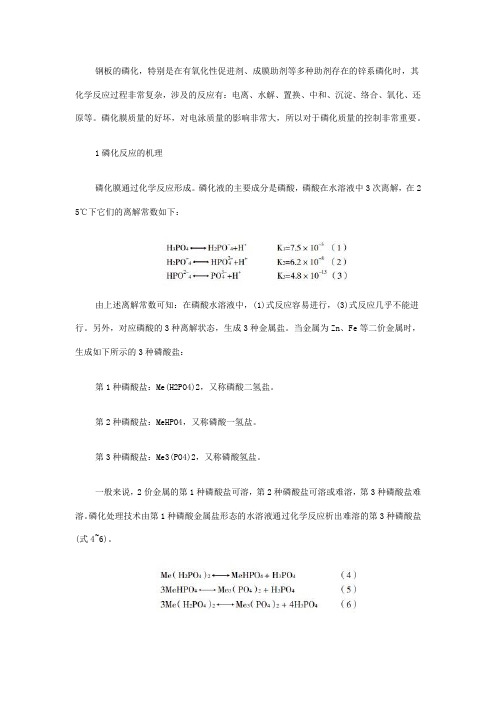
钢板的磷化,特别是在有氧化性促进剂、成膜助剂等多种助剂存在的锌系磷化时,其化学反应过程非常复杂,涉及的反应有:电离、水解、置换、中和、沉淀、络合、氧化、还原等。
磷化膜质量的好坏,对电泳质量的影响非常大,所以对于磷化质量的控制非常重要。
1磷化反应的机理磷化膜通过化学反应形成。
磷化液的主要成分是磷酸,磷酸在水溶液中3次离解,在2 5℃下它们的离解常数如下:由上述离解常数可知:在磷酸水溶液中,(1)式反应容易进行,(3)式反应几乎不能进行。
另外,对应磷酸的3种离解状态,生成3种金属盐。
当金属为Zn、Fe等二价金属时,生成如下所示的3种磷酸盐:第1种磷酸盐:Me(H2PO4)2,又称磷酸二氢盐。
第2种磷酸盐:MeHPO4,又称磷酸一氢盐。
第3种磷酸盐:Me3(PO4)2,又称磷酸氢盐。
一般来说,2价金属的第1种磷酸盐可溶,第2种磷酸盐可溶或难溶,第3种磷酸盐难溶。
磷化处理技术由第1种磷酸金属盐形态的水溶液通过化学反应析出难溶的第3种磷酸盐(式4~6)。
汽车涂装前的磷化处理以锌盐磷化处理为代表。
(7)式和(8)式所示的是生成锌盐磷化膜的平衡反应:(7)式反应在被处理物上进行,钢板界面上的Fe(H2PO4)2浓度增高。
将氧化促进剂亚硝酸盐添加到锌盐磷化液中后,(7)式中Fe(H2PO4)2就成为FePO4,H2变成H2O除去。
根据(7)式的反应,在磷化槽液内的钢板表面上,靠促进剂的作用,氢离子浓度下降,引发(9)式的反应:Fe的浓度高时就生成磷酸二锌铁:2磷化的加速反应2.1磷化反应的加速(1)磷化反应是一个吸热过程,加热有利于反应的进行。
(2)加入氧化性物质(如NO2-、H2O2等)作为去极化剂,其作用是使晶核能够暴露,而不被氢气覆盖;在有氧化性促进剂时,氢原子直接被氧化成水,不影响离子的扩散,形成磷化膜。
2.2磷化膜沉积过程的加速实现反应加速的方法一般是引入结晶晶核。
磷化前的钛盐表面调整,在工件表面形成晶核活性中心,使磷化结晶能够沿晶核生长。
关于磷化工序的浅解

关于钢丝〔盘条〕磷化的浅解1.0磷化的目的和基本原理:1.1钢丝表面涂着物的特性:钢丝的加工和使用,要求材料在保存或加工过程和加工结束后的一定时间段内,材料表面不产生锈蚀或表面涂着物不产生潮解;在加工过程中得到低的摩擦系数。
钢丝因再加工和使用的需要,钢丝表面选择的涂着物有:涂石灰、涂硼砂或其类似物、电镀金属、磷化等。
电镀金属仅是在一些特殊产品的要求而使用。
涂石灰是早期钢丝生产工艺中广泛使用的方式,它成本低;但是这种方式在再加工时产生粉尘有害健康且不适应高速拉拔。
涂硼砂是适用于高速拉拔且成本低廉的方式。
虽然它易于潮解,但对涂后的中间品有适当的管理措施是可以避免的。
且特别在涂后直接拉拔的工艺是被广泛选用。
目前国外虽开始限制使用硼砂产品,因此出现其类似物。
但是这种涂层只适用于中间产品的表面而不适用于最终产品的表面;因为它抗锈蚀能力差,但强于石灰涂层。
磷化的涂着层具有一定的抗锈蚀能力,和具有一定的电抗;在后加工过程中得到低的摩擦系数。
好的磷化膜本身具有很好的塑性,在变形中能够很好地保持其连续性;同时,它不仅能和皂——硬脂酸钠,发生反应产生更有利于润滑的金属皂类,而且其表面又可以很好地附着皂液和润滑剂;这有利减小变形摩擦因数、减少模具磨损。
1.2 磷化膜的形成和特性:1.2.1 磷化技术的机理:磷化处理过程是化学与电化学反应过程,主要是由下述步骤组成:a.酸的浸蚀使基体金属表面 H+ 离子浓度降低。
当金属表面与酸性磷化液接触时,钢丝表面被溶解,使金属与溶液中酸反应产生氢,从而使界面的 PH 值上升,以致磷酸锌〔以锌系为例〕沉积于钢丝表面。
由于亚铁在溶液中的存在,不论因酸后的带入还是在槽内反应产生,磷酸铁锌也同时沉积于钢丝表面。
其总反应方程如下:5Zn(H2P04)2+Fe(H2P04)2+8H20--+ Zn 3(P04)2。
4H20+ Zn 2Fe(P04)2。
4H20+ 8 H3P04磷酸盐沉淀的副反应将形成磷化沉渣,即亚铁离子被氧化后同磷酸反应生成磷酸铁在溶液中沉淀:Fe³¯+ P04³¯==FeP04但是在这钢丝表面的二种磷膜沉积物有不同的特性;称前者Zn 3(P04)2。
磷化(I)——基本原理及分类
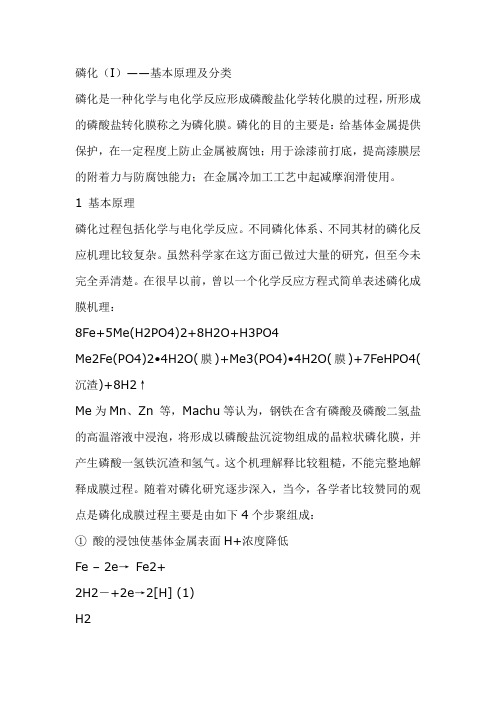
磷化(I)——基本原理及分类磷化是一种化学与电化学反应形成磷酸盐化学转化膜的过程,所形成的磷酸盐转化膜称之为磷化膜。
磷化的目的主要是:给基体金属提供保护,在一定程度上防止金属被腐蚀;用于涂漆前打底,提高漆膜层的附着力与防腐蚀能力;在金属冷加工工艺中起减摩润滑使用。
1 基本原理磷化过程包括化学与电化学反应。
不同磷化体系、不同其材的磷化反应机理比较复杂。
虽然科学家在这方面已做过大量的研究,但至今未完全弄清楚。
在很早以前,曾以一个化学反应方程式简单表述磷化成膜机理:8Fe+5Me(H2PO4)2+8H2O+H3PO4Me2Fe(PO4)2•4H2O(膜)+Me3(PO4)•4H2O(膜)+7FeHPO4(沉渣)+8H2↑Me为Mn、Zn 等,Machu等认为,钢铁在含有磷酸及磷酸二氢盐的高温溶液中浸泡,将形成以磷酸盐沉淀物组成的晶粒状磷化膜,并产生磷酸一氢铁沉渣和氢气。
这个机理解释比较粗糙,不能完整地解释成膜过程。
随着对磷化研究逐步深入,当今,各学者比较赞同的观点是磷化成膜过程主要是由如下4个步聚组成:①酸的浸蚀使基体金属表面H+浓度降低Fe – 2e→Fe2+2H2-+2e→2[H] (1)H2②促进剂(氧化剂)加速[O]+[H] →[R]+H2OFe2++[O] →Fe3++[R]式中[O]为促进剂(氧化剂),[R]为还原产物,由于促进剂氧化掉第一步反应所产生的氢原子,加快了反应(1)的速度,进一步导致金属表面H+浓度急剧下降。
同时也将溶液中的Fe2+氧化成为Fe3+。
③磷酸根的多级离解H3PO4 H2PO4-+H+ HPO42-+2H+ PO43-+3H-(3)由于金属表面的H+浓度急剧下降,导致磷酸根各级离解平衡向右移动,最终为PO43-。
④磷酸盐沉淀结晶成为磷化膜当金属表面离解出的PO43-与溶液中(金属界面)的金属离子(如Zn2+、Mn2+、Ca2+、Fe2+)达到溶度积常数Ksp时,就会形成磷酸盐沉淀Zn2++Fe2++PO43-+H2O→Zn2Fe(PO4)2•4H2O↓(4)3Zn2++2PO43-+4H2O=Zn3(PO4)2•4H2O↓(5)磷酸盐沉淀与水分子一起形成磷化晶核,晶核继续长大成为磷化晶粒,无数个晶粒紧密堆集形而上学成磷化膜。
磷化与钝化处理的区别

磷化处理和钝化处理的区别点击次数:711??? 时间:2009-11-10磷化处理:??? 磷化是金属材料防腐蚀的重要方法之一,其目的在于给基体金属提供防腐蚀保护、用于喷漆前打底、提高覆膜层的附着力与防腐蚀能力及在金属加工中起减摩润滑作用等。
按用途可分为三类:1、涂装性磷化2、冷挤压润滑磷化3、装饰性磷化。
按所用的磷酸盐分类有:磷酸锌系、磷酸锌钙系、磷酸铁系、磷酸锌锰系、磷酸锰系。
根据磷化的温度分类有:高温(80 ℃以上)磷化、中温(50~70 ℃)磷化、低温磷化(40 ℃左右)和常温磷化(10~30 ℃)。
一、磷化成膜机理磷化主要有以下过程:(1)金属的溶解过程即金属与磷化液中的游离酸发生反应:M+H3PO4 = M(H2PO4)2+H2↑(2)促进剂的加速过程为:M(H2PO4)2+Fe+[O]→M3(PO4)2+FePO由于氧化剂的氧化作用,加速了不溶性盐的逐步沉积,使金属基体与槽液隔离,会限制甚至停止酸蚀的进行。
(3)磷酸及盐的水解磷化液的基本成分是一种或多种重金属的酸式磷酸盐, 其分子式为Me(H2PO4)2,这些酸式磷酸盐溶于水,在一定浓度及pH值下发生水解,产生游离磷酸:Me(H2PO4)2=MeHPO4+H3PO43MeHPO4=Me3(PO4)2+H3PO4H3PO4=H2PO4-+H+= HPO2-4 + 2H+ =PO3-4 + 3H+由于金属工件表面的H+浓度急剧下降,导致磷酸根各级离解平衡向右移动,最终成为磷酸根。
(4 ) 磷化膜的形成当金属表面离解出的PO3-4与磷化槽液中的金属离子Zn2+、Mn2+、Fe2+达到饱和时,即结晶沉积在金属工件表面,晶粒持续增长,直到在金属工件表面生成连续不溶于水的牢固的磷化膜:3M2 + + 2PO3 -4 + 4H2O = M3 ( PO4 ) 2·4H2O ↓2 M2 + + Fe2 + + 2PO3 -4 + 4H2O= M2 Fe ( PO4 ) 2· 4H2O金属工件溶解出的Fe2+一部分作为磷化膜的组成部分被消耗掉,而残留在磷化槽液中的Fe2+则氧化成Fe3+,生成FePO4沉淀,即磷化沉渣的主要成分之一。
磷化原理及工艺

磷化原理及⼯艺中⽂名称:磷化英⽂名称:phosphatizing其他名称:磷酸盐处理定义:把⼯件浸⼊磷酸盐溶液中,使⼯件表⾯获得⼀层不溶于⽔的磷酸盐薄膜的⼯艺。
所属学科:机械⼯程(⼀级学科);机械⼯程(2)_热处理(⼆级学科);化学热处理(三级学科)磷化(phosphorization)是⼀种化学与电化学反应形成磷酸盐化学转化膜的过程,所形成的磷酸盐转化膜称之为磷化膜。
磷化的⽬的主要是:给基体⾦属提供保护,在⼀定程度上防⽌⾦属被腐蚀;⽤于涂漆前打底,提⾼漆膜层的附着⼒与防腐蚀能⼒;在⾦属冷加⼯⼯艺中起减摩润滑使⽤。
磷化处理⼯艺应⽤于⼯业⼰有90多年的历史,⼤致可以分为三个时期:奠定磷化技术基础时期、磷化技术迅速发展时期和⼴泛应⽤时期。
磷化膜⽤作钢铁的防腐蚀保护膜,最早的可靠记载是英国Charles Ross 于1869年获得的专利(B.P. N o.3119)。
从此,磷化⼯艺应⽤于⼯业⽣产。
在近⼀个世纪的漫长岁⽉中,磷化处理技术积累了丰富的经验,有了许多重⼤的发现。
⼀战期间,磷化技术的发展中⼼由英国转移⾄美国。
1909年美国T.W.Coslet将锌、氧化锌或磷酸锌盐溶于磷酸中制成了第⼀个锌系磷化液。
这⼀研究成果⼤⼤促进了磷化⼯艺的发展,拓宽了磷化⼯艺的发展前途。
Parker防锈公司研究开发的Parco Power配制磷化液,克服T许多缺点,将磷化处理时间提⾼到lho 1929年Bonderizing磷化⼯艺将磷化时间缩短⾄10min, 1934年磷化处理技术在⼯业上取得了⾰命性的发展,即采⽤了将磷化液喷射到⼯件上的⽅法。
⼆战结束以后,磷化技术很少有突破性进展,只是稳步的发展和完善。
磷化⼴泛应⽤于防蚀技术,⾦属冷变形加⼯⼯业。
这个时期磷化处理技术重要改进主要有:低温磷化、各种控制磷化膜膜重的⽅法、连续钢带⾼速磷化。
当前,磷化技术领域的研究⽅向主要是围绕提⾼质量、减少环境污染、节省能源进⾏。
原理及应⽤磷化是常⽤的前处理技术,原理上应属于化学转换膜处理,主要应⽤于钢铁表⾯磷化,有⾊⾦属(如铝、锌)件也可应⽤磷化。
磷化处理
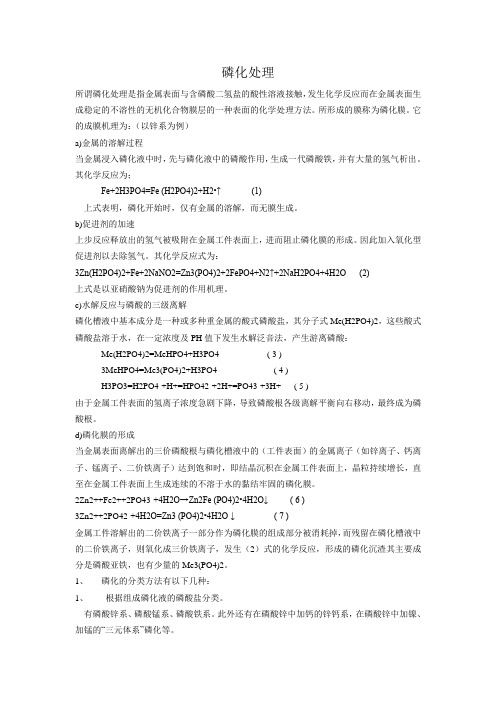
磷化处理所谓磷化处理是指金属表面与含磷酸二氢盐的酸性溶液接触,发生化学反应而在金属表面生成稳定的不溶性的无机化合物膜层的一种表面的化学处理方法。
所形成的膜称为磷化膜。
它的成膜机理为:(以锌系为例)a)金属的溶解过程当金属浸入磷化液中时,先与磷化液中的磷酸作用,生成一代磷酸铁,并有大量的氢气析出。
其化学反应为;Fe+2H3PO4=Fe (H2PO4)2+H2•↑ (1)上式表明,磷化开始时,仅有金属的溶解,而无膜生成。
b)促进剂的加速上步反应释放出的氢气被吸附在金属工件表面上,进而阻止磷化膜的形成。
因此加入氧化型促进剂以去除氢气。
其化学反应式为:3Zn(H2PO4)2+Fe+2NaNO2=Zn3(PO4)2+2FePO4+N2↑+2NaH2PO4+4H2O (2)上式是以亚硝酸钠为促进剂的作用机理。
c)水解反应与磷酸的三级离解磷化槽液中基本成分是一种或多种重金属的酸式磷酸盐,其分子式Me(H2PO4)2,这些酸式磷酸盐溶于水,在一定浓度及PH值下发生水解泛音法,产生游离磷酸:Me(H2PO4)2=MeHPO4+H3PO4 ( 3 )3MeHPO4=Me3(PO4)2+H3PO4 ( 4 )H3PO3=H2PO4-+H+=HPO42-+2H+=PO43-+3H+ ( 5 )由于金属工件表面的氢离子浓度急剧下降,导致磷酸根各级离解平衡向右移动,最终成为磷酸根。
d)磷化膜的形成当金属表面离解出的三价磷酸根与磷化槽液中的(工件表面)的金属离子(如锌离子、钙离子、锰离子、二价铁离子)达到饱和时,即结晶沉积在金属工件表面上,晶粒持续增长,直至在金属工件表面上生成连续的不溶于水的黏结牢固的磷化膜。
2Zn2++Fe2++2PO43-+4H2O→Zn2Fe (PO4)2•4H2O↓ ( 6 )3Zn2++2PO42-+4H2O=Zn3 (PO4)2•4H2O ↓ ( 7 )金属工件溶解出的二价铁离子一部分作为磷化膜的组成部分被消耗掉,而残留在磷化槽液中的二价铁离子,则氧化成三价铁离子,发生(2)式的化学反应,形成的磷化沉渣其主要成分是磷酸亚铁,也有少量的Me3(PO4)2。
钢铁常温彩色磷化工艺与成膜机理
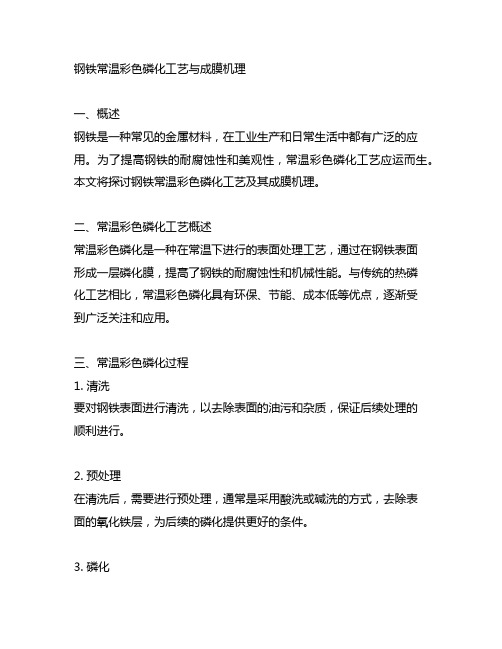
钢铁常温彩色磷化工艺与成膜机理一、概述钢铁是一种常见的金属材料,在工业生产和日常生活中都有广泛的应用。
为了提高钢铁的耐腐蚀性和美观性,常温彩色磷化工艺应运而生。
本文将探讨钢铁常温彩色磷化工艺及其成膜机理。
二、常温彩色磷化工艺概述常温彩色磷化是一种在常温下进行的表面处理工艺,通过在钢铁表面形成一层磷化膜,提高了钢铁的耐腐蚀性和机械性能。
与传统的热磷化工艺相比,常温彩色磷化具有环保、节能、成本低等优点,逐渐受到广泛关注和应用。
三、常温彩色磷化过程1. 清洗要对钢铁表面进行清洗,以去除表面的油污和杂质,保证后续处理的顺利进行。
2. 预处理在清洗后,需要进行预处理,通常是采用酸洗或碱洗的方式,去除表面的氧化铁层,为后续的磷化提供更好的条件。
3. 磷化将经过清洗和预处理的钢铁件浸入含有磷酸盐的磷酸盐磷化液中,经过一定时间的处理,形成磷化膜。
4. 彩色处理经过磷化的钢铁件需要进行彩色处理,通常是在染色液中进行处理,不同的染色液可以形成不同的颜色。
彩色处理不仅提高了钢铁的美观性,也能进一步增强其耐腐蚀性。
5. 封孔需要对彩色处理后的钢铁进行封孔处理,以增强磷化膜的密封性和耐腐蚀性。
四、磷化膜的成膜机理1. 化学反应磷化膜的形成主要是通过磷酸盐磷化液中的化学物质与钢铁表面发生化学反应,生成磷化膜。
2. 微观结构磷化膜是由磷化物、氢氧化物和碳酸盐等多种物质组成的复合物,具有较为复杂的微观结构。
磷化膜的形成和组成直接影响其性能和应用。
3. 彩色效应通过对磷化膜进行彩色处理,可以形成不同颜色的磷化膜,这是由于染色液中的染色剂与磷化膜的微观结构之间的相互作用所致。
五、磷化膜的性能1. 耐腐蚀性磷化膜具有良好的耐腐蚀性,能够有效地保护钢铁表面不受环境气氛的侵蚀。
2. 机械性能磷化膜具有一定的硬度和耐磨性,可以提高钢铁表面的机械性能。
3. 色泽经过彩色处理后的磷化膜具有丰富的色彩,可以满足不同客户对钢铁表面颜色的需求。
六、常温彩色磷化在工业中的应用常温彩色磷化工艺在汽车制造、建筑、家居用品等领域都有着广泛的应用。
关于磷化处理原理
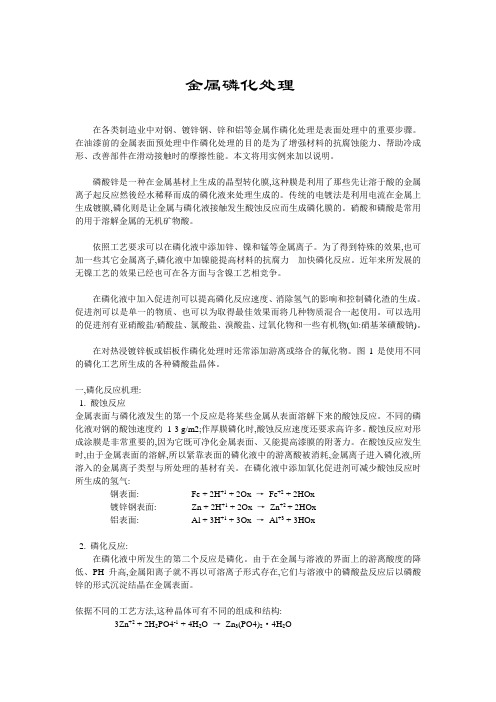
金属磷化处理在各类制造业中对钢、镀锌钢、锌和铝等金属作磷化处理是表面处理中的重要步骤。
在油漆前的金属表面预处理中作磷化处理的目的是为了增强材料的抗腐蚀能力、帮助冷成形、改善部件在滑动接触时的摩擦性能。
本文将用实例来加以说明。
磷酸锌是一种在金属基材上生成的晶型转化膜,这种膜是利用了那些先让溶于酸的金属离子起反应然後经水稀释而成的磷化液来处理生成的。
传统的电镀法是利用电流在金属上生成镀膜,磷化则是让金属与磷化液接触发生酸蚀反应而生成磷化膜的。
硝酸和磷酸是常用的用于溶解金属的无机矿物酸。
依照工艺要求可以在磷化液中添加锌、镍和锰等金属离子。
为了得到特殊的效果,也可加一些其它金属离子,磷化液中加镍能提高材料的抗腐力 加快磷化反应。
近年来所发展的无镍工艺的效果已经也可在各方面与含镍工艺相竞争。
在磷化液中加入促进剂可以提高磷化反应速度、消除氢气的影响和控制磷化渣的生成。
促进剂可以是单一的物质、也可以为取得最佳效果而将几种物质混合一起使用。
可以选用的促进剂有亚硝酸盐/硝酸盐、氯酸盐、溴酸盐、过氧化物和一些有机物(如:硝基苯磺酸钠)。
在对热浸镀锌板或铝板作磷化处理时还常添加游离或络合的氟化物。
图1是使用不同的磷化工艺所生成的各种磷酸盐晶体。
一,磷化反应机理:1. 酸蚀反应金属表面与磷化液发生的第一个反应是将某些金属从表面溶解下来的酸蚀反应。
不同的磷化液对钢的酸蚀速度约1-3 g/m2;作厚膜磷化时,酸蚀反应速度还要求高许多。
酸蚀反应对形成涂膜是非常重要的,因为它既可净化金属表面、又能提高漆膜的附著力。
在酸蚀反应发生时,由于金属表面的溶解,所以紧靠表面的磷化液中的游离酸被消耗,金属离子进入磷化液,所溶入的金属离子类型与所处理的基材有关。
在磷化液中添加氧化促进剂可减少酸蚀反应时所生成的氢气:钢表面: Fe + 2H+1 + 2Ox →Fe+2 + 2HOx镀锌钢表面: Zn + 2H+1 + 2Ox →Zn+2 + 2HOx铝表面: Al + 3H+1 + 3Ox →Al+3 + 3HOx2. 磷化反应:在磷化液中所发生的第二个反应是磷化。
碳酸盐型和火山岩型磷化作用机理与成岩环境分析

碳酸盐型和火山岩型磷化作用机理与成岩环境分析碳酸盐型和火山岩型磷化作用机理与成岩环境分析磷是地壳中第十五丰度最高的元素,广泛存在于岩石、矿物、土壤和水体中,是生命活动中不可或缺的元素。
磷的存在形态主要包括磷酸盐、磷酸铵、有机磷等多种化合物。
磷酸盐主要存在于碳酸盐型和火山岩型中,而其成岩机理和成岩环境则各有特点。
碳酸盐型磷化作用机理主要涉及到碳酸盐的溶解、沉积和同位素交换等过程。
在碳酸盐岩的成岩过程中,碳酸盐矿物晶体中的钙离子可以被磷酸根等离子置换,形成磷酸钙矿物,如磷灰石。
这一过程通常发生在碳酸盐岩的溶解和溶蚀作用区域,磷酸盐溶解后再沉积的过程叫做原位磷化作用。
此外,还存在有磷酸盐的同位素交换作用,如氧同位素交换和碳同位素交换。
氧同位素交换发生在碳酸盐矿物和水体中的溶解和析出过程中,而碳同位素交换则发生在有机质和溶解碳酸盐矿物之间。
碳酸盐型磷化作用通常在还原环境下发生,主要包括富含有机质的沉积环境、潮湿环境和富含还原剂的流体环境。
这些环境中有机质可以提供还原剂,促使碳酸盐矿物中的钙离子被磷酸根离子置换,形成磷酸钙矿物。
此外,还存在有机质在溶解碳酸盐矿物的同时,产生的CO2与磷酸根离子发生碳同位素交换作用,进而形成具有特殊碳同位素组成的磷酸钙矿物。
因此,碳酸盐型的磷化作用主要受到有机质的影响,环境中含有丰富的有机质,利于磷化作用的发生。
火山岩型的磷化作用机理与碳酸盐型有所不同。
火山岩型磷化作用主要发生在火山岩熔融、喷发和沉积过程中。
火山岩中主要存在的是含磷矿物,如磷灰石、辉石、黑云母等。
这些含磷矿物在火山岩熔融、喷发的过程中形成,随着火山岩的深度增加和温度下降,磷酸盐矿物会发生分解,释放出磷酸根等离子。
在火山岩的沉积过程中,这些磷酸根等离子可以通过溶解和沉积,与周围的结晶硅酸岩石发生反应,形成含磷的硅酸盐矿物。
火山岩型磷化作用的机理与火山岩的形成有密切关系,火山岩喷发和沉积环境中存在高温、高压和富含磷酸根等离子的流体,有利于磷化作用的发生。
磷化成膜机理

磷化成膜机理1、化学转化过程所用的磷化液都是由磷酸、碱金属或重金属的磷酸二氢盐及氧化性促进剂组成的酸性溶液。
因此,整个磷化过程都包括含有基体金属的溶解反应、难溶磷酸盐结晶沉积的成膜过程及氧化性促进剂的去极化作用。
基体金属的溶解磷化液的PH 值一般都在2~之间,呈酸性。
因此当金属和此酸性溶液接触时,必然发生由局部阳极和局部阴极反应组成的金属溶解过程:局部阳极 Me Me 2++2e 局部阴极 2H ++2e H 2↑成膜反应由于局部阴极区域H +被还原而消耗,酸度下降,使得在第一阶段形成的可溶性二价金属磷酸二氢盐离解成溶解度较小的磷酸一氢盐:Me (H 2PO 4)2 MeHPO 4+H 3PO 4只要PH 上升到一定程度,则主要离解成不溶性二价金属磷酸盐。
此离解则比较迅速: Me (H 2PO 4)2 MeHPO 4+4H 3PO 4同时 MeHPO 4 Me 3(PO 4)2+H 3PO 4难溶的Me 3(PO 4)2在金属表面的阴极区域沉积析出。
当整个阴极区域都被沉积物覆盖时,成膜反应结束,从而在金属表面形成完整的磷化膜覆盖。
由于成膜反应的可溶性二价金属磷酸二氢盐可以是金属溶解生成的,也可以是溶液中原有的配方组成。
除磷酸铁盐膜外,其他所有的磷化膜的成膜物质都是添加配方中的原料。
难溶性磷酸盐的溶积度如表:氧化性促进剂的去极化作用和对金属溶解的促进金属溶解时产生的氢气易吸附于阴极的金属表面,从而阻碍水解产生的二价金属磷酸盐在阴极区域的沉积,不能形成磷化膜。
水解产物则于溶液中析出成为渣,即浪费成膜原料,也使渣量大大增加。
这样在工艺方面将造成困难,对膜的性能也不能保证,因为孔隙率很大。
氧化剂的去极化作用是将还原形成的初生态氢氧化成水;2[H]+[O] H 2O与去极化作用密切相关的是促进剂对金属溶解的促进。
它是通过促进剂对H 2的氧化和沉积作用,导致阳极电流密度增加而提高溶解速率,即提高可溶性二价金属磷酸二氢盐的生成速率。
化学反应中的有机磷化学反应

有机磷化学反应是一类在有机化学中重要的反应类型,涵盖了包括磷化反应、磷氧化还原反应、磷碳键形成反应等多个方面。
有机磷化学反应在药物、农药及聚合物领域有着广泛的应用,并且对于有机合成化学的发展起到了重要的推动作用。
在有机磷化学反应中,磷元素的化学性质和它在有机化合物中的应用起到了关键的作用。
磷元素作为一种特殊的元素,在有机化学中广泛存在于磷酸酯、亚磷酸酯、磷酸酐等化合物中。
磷元素具有独特的电子结构,它的单个孤对电子和一个弱键参与到反应中,影响了反应的速率和机理。
有机磷化学反应中的一种重要反应类型是磷化反应。
磷化反应是指将有机化合物中的磷原子与其他原子或分子结合形成磷原子的单键或多键。
磷化反应通常有选择性和高效性,可以合成一系列具有重要生物活性的磷化合物。
例如,磷化反应可以将无机磷化合物转化为有机磷化合物,形成具有独特化学性质和应用的新型有机磷化合物。
另一个重要的有机磷化学反应是磷氧化还原反应。
磷氧化还原反应是指磷化合物中的磷原子与氧原子发生电子转移或共用电子对,从而引发物质的氧化或还原。
例如,有机酯的加热可以发生醇与三乙基氧化膦的磷氧化还原反应,经过一系列反应过程形成磷酸酯。
磷氧化还原反应在有机合成中广泛应用,可以合成具有多种化学性质和应用的磷化合物。
此外,有机磷化学反应还包括多种磷碳键形成反应。
磷碳键形成反应是指磷元素与碳原子发生共价键键合,从而形成磷碳链或环。
磷碳键形成反应可以通过不同的反应条件和催化剂实现,如烯醇磷仿π醇磷反应、草酰亚胺磷仿羰磷反应等。
这些反应能够为有机合成提供多种磷碳键构建策略,为合成复杂有机分子提供了很大的便利。
综上所述,有机磷化学反应作为一类重要的有机化学反应类型,在有机合成领域具有重要的应用和发展潜力。
研究和应用有机磷化学反应不仅可以帮助我们更好地理解和探索有机化学的规律,还可以为有机化学的发展和应用提供新的方向和思路。
希望随着对有机磷化学反应的深入研究和理解,能够进一步推动有机化学的发展和创新。
高品位火山岩型和沉积型磷化作用机理比较与分析——以某地区为例

高品位火山岩型和沉积型磷化作用机理比较与分析——以某地区为例高品位火山岩型和沉积型磷化作用是两种不同的磷化过程,它们在形成机制、地质环境和矿床类型等方面存在较大差异。
本篇文章将以某地区为例,对这两种类型的磷化作用进行比较与分析。
首先,我们先来了解高品位火山岩型磷化作用。
高品位火山岩型磷化矿床多分布于火山喷发岩带中,是由火山喷发和火山喷发过程中的气体、液体和固体相互作用造成的。
火山岩熔融后,富集于磷的气相在岩浆体系中扩散并以液相的形式被固态酸硅铝矿物包围。
当火山岩冷却固化后,这些磷酸盐的富集度就对应于磷化矿床的矿石品位。
由于火山岩的高品位磷化矿床多富含可经济利用的磷酸钙矿石,因此成为重要的磷矿资源。
与高品位火山岩型磷化作用相比,沉积型磷化作用的机理有所不同。
沉积型磷化矿床多分布于古代的海洋沉积盆地中,磷化物主要以磷灰石和磷酸石的形式存在,并与泥质沉积物和有机质一起被掩埋和封闭在地下。
沉积型磷化作用主要是在海洋中以生物和非生物过程结合产生的。
生物作用主要包括浮游生物、底栖生物以及富含磷的有机质在海洋生态系统中的循环过程;而非生物过程包括海水中磷的迁移和沉积、海底地质和地球化学过程等。
在长时间的沉积和地质作用下,沉积型磷化矿床逐渐形成并且富含高品位的磷化矿石。
从地质环境的角度来看,高品位火山岩型磷化矿床多分布在火山地区,如环太平洋火山带、中美洲火山带等;而沉积型磷化矿床则主要分布于海洋沉积盆地,如北美大陆陆棚、非洲大陆陆棚等。
这意味着高品位火山岩型磷化矿床与火山活动有关,而沉积型磷化矿床与海洋环境有关。
最后,我们来分析这两种磷化作用的矿床特点。
高品位火山岩型磷化矿床通常具有品位较高、矿石层位清晰、储量大的特点。
矿石中的磷酸钙矿物易于开采和加工,因此具有较高的经济价值。
而沉积型磷化矿床则具有品位较低、矿物种类丰富、矿石层位复杂的特点。
矿石中的磷酸钙矿物与其他矿物颗粒混杂在一起,需要经过破碎、浮选等多道工艺才能获得高品位的矿石。
- 1、下载文档前请自行甄别文档内容的完整性,平台不提供额外的编辑、内容补充、找答案等附加服务。
- 2、"仅部分预览"的文档,不可在线预览部分如存在完整性等问题,可反馈申请退款(可完整预览的文档不适用该条件!)。
- 3、如文档侵犯您的权益,请联系客服反馈,我们会尽快为您处理(人工客服工作时间:9:00-18:30)。
化学元素磷能生成氧化态为+1、+3和+5的各种含氧酸,其中P(+5)的含氧酸和含氧酸盐是磷的重要化合物,而正磷酸就是磷的五价含氧酸。
正磷酸简称磷酸,是由一个单一的磷氧四面体构成的,磷原子位于四面体的中心。
磷酸的分子式为H3PO4,相对分子质量为97.99。
纯磷酸是无色透明的固体,熔点是42.3°C,它的半水化合物H3PO4·1/2H2O的熔点是29.35°C。
它在水溶液中从红磷、H2和O2的生成热是1264.4kJ/mol。
磷酸是一种无氧化性的不挥发酸,市售的磷酸是含85%H2PO4或含75%H3PO4的水溶液。
磷酸是一个三元酸,在水溶液中按下式分三步电离:H3PO4一H2PO4-+H+H2PO4-一HPO42-一+H+HPO42-一PO43-+H+而逐级电离常数是K1=7.5×l0-3(25°C时为7.101×l0-3)K2=6.2×10-8(25°C时为7.99×l0-8)K3×10-13(25°C时为4 8×10-13)电离常数越大,说明其越易电离。
对于酸来说,越易电离说明其给出质子的能力越强,酸性就越强。
磷酸的K1比一般的弱酸如碳酸(K1=4.30×10-7)、醋酸(K1=1.76×10-5)都大,所以说磷酸是中强度的酸。
由于磷酸含有三个可以被置换的氢原子,因而可以形成三种形式的盐,即磷酸二氢盐(二酸式盐)、磷酸氢盐(一酸式盐)和磷酸正盐。
一价金属的三种形式的磷酸盐如下:MH2PO4M2HPO4M3PO4M=K+、Na+、NH4+…还有其他形式的酸式和碱式盐,如多聚磷酸盐等,二价金属三种形式的磷酸盐如下:M(H2PO4) 2MHPO4M3 (PO4) 2M=Fe2+、Zn2+、Mn2+等在这些盐中磷酸根是以磷氧四面体的形式存在的。
碱金属的磷酸二氢盐的水解呈酸性,磷酸氢盐的水解呈弱碱性,正磷酸盐的水解呈强碱性,例如钠的三种磷酸盐在25°C、10g/L的条件下所显示的pH值如下:NaH2PO3 pH=5.6NaHPO4 pH=8.3Na3PO4 pH=11.9二价金属的所有磷酸二氢盐(二酸式盐)都易溶于水,而磷酸氢盐(一酸式盐)呈不稳定性或不溶解性,二价金属的所有正磷酸盐都不溶于水。
而磷化正是利用了磷酸盐的这种性质,绝大多数磷化剂都是二价金属的磷酸二氖盐(铁系磷化液、锌系磷化液、锰系磷化液、锌钙系磷化液等),它们均可溶于水而配成磷化液,金属用它们磷化处理获得的磷化膜是不溶于水的正磷酸盐。
磷化成膜机理比较复杂,至今尚没有统一完整的理论,不同的磷化体系,不同材质的磷化,反应原理不同。
首先,磷化剂在水溶液中发生电离,随温度的升高,离解度增大。
在一定的温度下处于平衡状态。
当金属与磷化液接触时,钢铁受游离酸的侵蚀而发生反应,产生的氢气被溶液中的氧化剂氧化成水,同时部分Fe2+离子也被溶液中的氧化剂氧化成Fe3+,Fe3+与PO43-生成FePO4成为残渣,部分Fe2+参与成膜反应。
这些反应都是发生在金属表面。
由于反应式的发生,反应式的平衡被打破,平衡向右移动,同时,反应式的发生加速了式的电离,电离出越来越多的Zn2+和PO43-使得金属表面附近的Zn2+、PO43-和Fe2+的浓度过饱和,当大于Zn3(PO4) 2或Zn2Fe(PO4) 2的溶度积时,不溶性的磷酸正盐就沉积在溶液与金属的界面上,由此形成磷化膜。
在生成磷化膜的同时,由于消耗掉zn2+及PO43-使得反应平衡继续右移,这样,从Zn(H2PO4) 2中又电离出H+、Zn2+PO43-等离子,溶液又处于新的平衡中。
可以看出,磷化液就是一种缓冲溶液,在生产中,它一直处于一种动态平衡状态中,金属表面的活性点增多,即晶核增多,有利于磷化膜的结晶,这也是表面调整的理论基础。
实际的磷化反应比上面描述的过程复杂得多,因为磷化液中有木同的氧化剂、催化剂、络合剂等,还有许多副反应发生。
磷化实际上也是一种电化学现象。
磷化过程中,微阳极发生金属溶解,而微阴极释放出氢气,并随着出现不溶性磷酸盐的水解和沉积。
过电位测定,可以检测到磷化膜的生长过程。
1.钢铁工件刚接触到磷化液时,首先受到磷化液中游离磷酸的侵蚀,发生电化学阳极溶解,这时对应的图中的电位升高。
2.由于溶解很快,在局部阳极区域,产生Fe(H2PO4) 2浓度迅速增加而达到饱和,并在局部阴极以溶解不可逆的无定型形态沉积于金属表面,导致电位图上的电位急剧下降,此时,含铁的磷化膜生成,构成了非晶态的底层,这叫非晶态沉积,由于最先生成的无定型沉淀膜具有钝化作用,随后电位变化趋势较平坦。
3.重新上移,说明钢铁基体的电化学阳极溶解继续进行。
4.随着Zn3(PO4) 2、ZnFe(PO4) 2沉积量增加,磷化膜增厚,图中电位缓慢下移。
5.(Ghali盖利)用附加恒电位进行磷化处理时,同时测定阳极极化电流随时问的变化,汪明了重结晶现象的存在。
磷化速率就是磷化膜的生成速率,可以用单位面积磷化膜质量随时间增长来表示,也可以用空隙率,更确切地说是以阳极面积百分数随磷化时间下降来表示,其数学表达式为ln(F ao/F a)=k式中k ——速度常数;T ——磷化时间;F ao——初始自由阳极面积(cm2);F a——t时残留的阳极面积(cm2)。
显然,速度常数☆值越大,成膜越快,否则,形成一定厚度的磷化膜就需要相当长的时间。
由电化学反应动力学理论知,速度常数k是温度的函数,即K=k0-E/RT式中k0——活化能等于零时的速度常数R——气体常数;。
E——活化能;T——温度(K)。
因此,速度常数k只是温度和活化能的函数,温度升高,k值增大,反应加快。
活化能则与被磷化金属的化学性能及其表而的物理状态、磷化药液的各种成分及其性能等因索有关。
磷化液的性能主要由氧化性促进剂决定,它降低活化能使k值增大,磷化加快。
此外,成膜物质的浓度、物质在界面处的扩散、成膜时的晶核生成及结晶排列等也化液的性能,通常情况下,各种因素是彼此相关的金属溶解反应导致局部阴极区域界面液的酸度下降,从而形成过饱和溶液,在pH=4~5时,出现磷化液中磷酸盐的起始沉淀点(PIP),出现起始沉淀点的pH值随溶液中PO43-/zn2+比值的升高而提高。
最先形成的不完善的磷酸铁、氧化铁混合物组成的钝化膜,也可作为供磷酸锌增长的晶核。
由金属表面结构来看,表面存在着供磷化膜生产的“活性中心”,该活性中心具有一定的能级、数量和表面分布,活性中心的能级决定晶核生成的难易程度,活性中心的数量和表面分布影响到晶核的数量和分布,从而影响磷化膜的粗细和致密性,晶核生成速率随活性中心数量而增加,但主要的制约因素还是活性中心的能级。
磷化膜在金属晶格基础上的取向和排列同金属晶体相似,即晶格周期相一致,如磷化膜晶体的取向、接长规律。
磷化膜晶格在金属晶体上排列整齐,且两者之间又有较强的作用力,形成的磷化膜就致密,附着力强。
晶核都是在反应开始后不久生成的,随后的结晶过程只是品粒的长大,而晶粒数并不增加,一般情况下,单位面积(cm2)的钢铁表面,有几十万至几百万个晶粒。
钢铁表面晶粒界面处都是晶粒形成的活性中心,所以钢铁晶粒组织越小,磷酸盐结晶的析出度就越大。
喷淋磷化和浸渍磷化的晶核生成数有很大的差别,一般喷淋磷化生成的晶核多,磷化膜细致。
金属表面的状态,可以用化学表面调整剂进行表面调整,如用磷酸钛胶体溶液、锰盐悬浮液等调整以后,改善了金属表面活性中心的密度,有助于提高磷化膜的质量和生成速率。
另外,还可通过机械活化手段,如砂纸打磨、擦拭来提高晶核的数量,来加快成膜速度。
因为晶核数量与金属表面粗糙度成正比,打磨可增加金属表面的粗糙度,使得到的磷化膜细致;而擦拭作用则给予金属表面能快。
以下还可以了解:磷化膜可以在不含有金属离子,而只含有钠离子、钾离子、铵离子的磷酸盐溶液中形成。
由于没有碱金属进入磷化膜中,因而对这种磷化的命名就比较模糊,但是,用这类磷化得到的磷化膜的主要成分仍含有大量的磷酸铁,因而这类磷化也被认为铁系磷化,不过,碱金属磷酸盐与以磷酸二氢铁为主要成分的、真正的铁系磷化液磷化是不同的,为了加以区分不至于混淆,将此类磷化称为碱金属磷化或轻型铁系磷化比较合适。
钢铁材质在碱金属磷化处理液中的成膜机理与在重金属磷化处理液中的成膜机理具有明显的区别,碱金属的正磷酸盐全部易溶于水,它们的水溶液不存在电离平衡,相对于重金属磷化处理液的pH值为1.5~3.5的情况,碱金属磷化处理的最佳pH值范围为4.O~6.0。
有人认为,当钢铁工件与磷化液接触时,首先发生腐蚀反应,但该反应中产生的氢尚在初生状态时即被迅速氧化了,见下式:2Fe+4NaH2PO4+2H2O+O2—2Fe(H2PO4) 2+4NaOH (5-8)接着磷酸亚铁被氧化成三价铁,部分成为磷酸铁,见式(5-9),部分成为氢氧化铁,见式(5-10)。
4Fe(H2PO4) 2+4NaOH4+O2——4FePO4+4NaH2PO4+6H2O (5-9)4Fe(H2PO4) 2十12NaOH+O2—2Fe(0H) 3+4NaH2PO4+4NaHPO4+2H2O (5-10)在烘干过程中氢氧化铁不稳定,分解为Fe2O3见下式:2Fe(OH) 3—Fe2O3+3H2O (5-11)综合式(5-8)~式(5-11)的反应,得4Fe + 4NaH2PO4 + 3O2 →2FePO4+Fe2O3+2Na2HPO4+3H2 O (5-12)(被处理金属) (磷化液主要成分) (氧化剂) (磷化膜)但也有人认为,这类磷化膜的形成有两种过程,即磷酸盐的沉积和金属的直接氧化,见如下两式:4Fe+8NaH2PO4+3O2—4FePO4+4Na2HPO4+6H2O (5-13)4Fe+3O2→2Fe2O3 (5一14)综合式(5—13)、式(5一14),得4Fe + 4NaH2PO4 + 3O2→2FePO4+Fe2O3+2Na2HPO4+3H2O (5-15) (被处理金属) (磷化液主要成分) (氧化剂) (磷化膜)可以看出,以上两种理论过程不同,结果是一样的,所有的不溶性产物均进入磷化膜中,溶液中无残渣,反应中仅有盼可溶性产物是磷酸氢钠。
氧化促进剂,尤其是氯酸盐、钼酸盐等常被应用于此类磷化处理。
但也有人认为加入它们的必要性不大,特别是在喷淋方式处理的情况下,空气中的氧气足够起到氧化剂的作用。
但是,磷化处理液中的氧化剂的种类、用量对磷化膜中的氧化铁的比例,甚至对磷化膜的性能还是有很大影响的。