丰田汽车制造公司案例分析
丰田八步法实际案例

丰田八步法实际案例【实用版】目录1.丰田八步法简介2.丰田八步法的实际案例3.丰田八步法的效果分析4.丰田八步法的应用建议正文【丰田八步法简介】丰田八步法,又称为 PDCA 循环,是一种以计划(Plan)、执行(Do)、检查(Check)和行动(Act)为核心的管理循环,被广泛应用于各种企业的质量管理中。
这个循环是一个连续不断的过程,通过不断的反馈和修正,达到提升产品质量和效率的目的。
【丰田八步法的实际案例】以丰田汽车公司为例,他们运用丰田八步法,通过不断改进,成为了全球最大的汽车制造商。
具体来说,他们会首先制定目标和计划,然后执行计划,接着检查执行结果,最后根据检查结果进行修正,以达到更好的效果。
例如,他们设定了一个目标:降低某款车型的装配时间。
他们首先进行现状分析,找出了存在的问题,然后制定了改进计划,包括重新设计流程、提高工人的操作技能等。
接着,他们执行这个计划,同时进行检查,看看改进是否达到预期效果。
最后,根据检查结果,他们进行修正,以确保改进的效果能够持续。
【丰田八步法的效果分析】丰田八步法的效果是显著的。
通过这个循环,企业可以发现并解决存在的问题,提高效率,降低成本,提升产品质量,增强竞争力。
丰田汽车公司就是最好的例子,他们的成功,很大程度上得益于丰田八步法的有效运用。
【丰田八步法的应用建议】对于想要应用丰田八步法的企业,我有以下几点建议:首先,要明确目标。
没有明确的目标,就无法进行有效的计划和执行。
其次,要进行现状分析。
只有了解现状,才能找出问题,才能制定出有效的改进计划。
再次,要设定合理的改进目标。
目标过高或过低都无法达到预期的效果。
最后,要坚持执行和检查。
只有持续的执行和检查,才能确保改进的效果能够持续。
丰田公司管理案例分析

丰田公司管理案例分析丰田公司是全球著名的汽车制造公司,其成功的管理模式备受瞩目。
下面将对丰田公司的管理案例进行分析。
首先,丰田公司的成功得益于其创始人丰田喜一郎的领导风格。
丰田喜一郎提倡尊重员工,注重员工的意见和参与,鼓励员工敢于创新和提出改善建议。
这种领导风格创建了一种积极向上的企业文化,员工感到自己的贡献被认可和尊重,从而提高了员工的工作积极性和创造力。
其次,丰田公司以质量为中心的管理理念在汽车行业树立了良好的口碑。
丰田公司一直推崇“精益生产”管理模式,注重生产过程中的细节和品质控制。
丰田公司鼓励员工发现并解决问题,不断改进生产流程和产品质量。
这种质量导向的管理理念使丰田汽车在市场上享有较高的声誉,并赢得了消费者的信任。
另外,丰田公司注重团队合作和横向沟通。
丰田公司采用了“5S”管理方法,即整理、整顿、清洁、清扫、自制。
这种方法强调团队合作,通过组织员工的主动参与来改善工作环境和生产效率。
丰田公司还鼓励员工进行横向沟通,打破部门之间的壁垒,促进信息的自由流动,提高企业的协同效应。
此外,丰田公司不断加强供应链和供应商的管理。
丰田公司着力构建稳定可靠的供应链体系,与供应商建立长期合作关系,共同提高产品质量和供货速度。
丰田公司还通过供应商管理系统来对供应商进行评估和监控,确保供应商符合公司的要求和标准。
最后,丰田公司积极推进可持续发展和环境保护。
丰田公司致力于研发和生产绿色环保的汽车产品,推广可再生能源和节能减排技术。
丰田公司还制定了环境保护的目标和计划,不断提高企业的环境责任和可持续发展能力。
综上所述,丰田公司成功的管理案例得益于其创始人的领导风格、质量导向的管理理念、团队合作和横向沟通、供应链和供应商管理以及可持续发展和环境保护。
这些管理实践使丰田公司成为汽车行业的佼佼者,并在全球范围内树立了良好的企业形象。
成功的企业案例分析
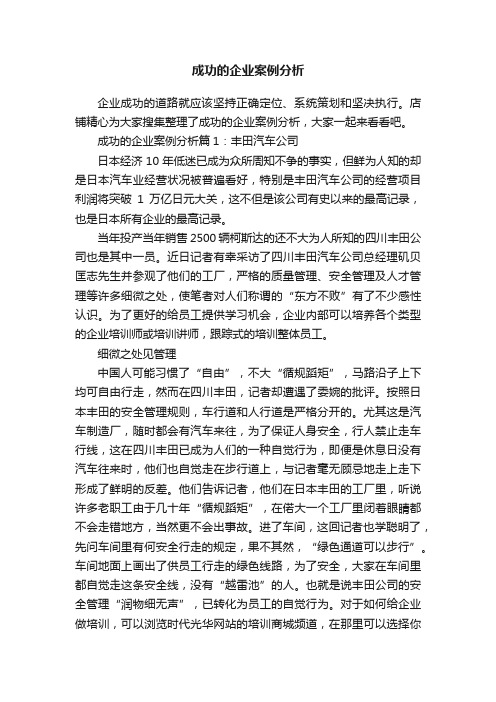
成功的企业案例分析企业成功的道路就应该坚持正确定位、系统策划和坚决执行。
店铺精心为大家搜集整理了成功的企业案例分析,大家一起来看看吧。
成功的企业案例分析篇1:丰田汽车公司日本经济10年低迷已成为众所周知不争的事实,但鲜为人知的却是日本汽车业经营状况被普遍看好,特别是丰田汽车公司的经营项目利润将突破1万亿日元大关,这不但是该公司有史以来的最高记录,也是日本所有企业的最高记录。
当年投产当年销售2500辆柯斯达的还不大为人所知的四川丰田公司也是其中一员。
近日记者有幸采访了四川丰田汽车公司总经理矶贝匡志先生并参观了他们的工厂,严格的质量管理、安全管理及人才管理等许多细微之处,使笔者对人们称谓的“东方不败”有了不少感性认识。
为了更好的给员工提供学习机会,企业内部可以培养各个类型的企业培训师或培训讲师,跟踪式的培训整体员工。
细微之处见管理中国人可能习惯了“自由”,不大“循规蹈矩”,马路沿子上下均可自由行走,然而在四川丰田,记者却遭遇了委婉的批评。
按照日本丰田的安全管理规则,车行道和人行道是严格分开的。
尤其这是汽车制造厂,随时都会有汽车来往,为了保证人身安全,行人禁止走车行线,这在四川丰田已成为人们的一种自觉行为,即便是休息日没有汽车往来时,他们也自觉走在步行道上,与记者毫无顾忌地走上走下形成了鲜明的反差。
他们告诉记者,他们在日本丰田的工厂里,听说许多老职工由于几十年“循规蹈矩”,在偌大一个工厂里闭着眼睛都不会走错地方,当然更不会出事故。
进了车间,这回记者也学聪明了,先问车间里有何安全行走的规定,果不其然,“绿色通道可以步行”。
车间地面上画出了供员工行走的绿色线路,为了安全,大家在车间里都自觉走这条安全线,没有“越雷池”的人。
也就是说丰田公司的安全管理“润物细无声”,已转化为员工的自觉行为。
对于如何给企业做培训,可以浏览时代光华网站的培训商城频道,在那里可以选择你想培训的课题和内容。
在四川丰田每个车间都有一个区域,专门用黑板甚至用绳子挂起一些纸张,多是流程的每一步质量管理,但更吸引记者眼球的是一张张工人们来自生产中的保质增效又降低成本的建议图。
丰田汽车案例分析

一、案例背景P1位于美国肯塔基州的丰田汽车制造公司(美国)(TMM)乔治敦工厂于1988年开始进行大规模生产。
这家工厂所采用生产和管理系统正是丰田独特的丰田生产系统(TPS)。
1992年初,TMM将佳美的两厢版投放市场,使得座椅样式由原来的5种迅速增加为发往北美的8种、发往欧洲的10种、发往日本和中东的18种,合计36种。
此时,乔治敦工厂的装配线经理道格·弗里森遇到了急需解决的座椅问题。
P2TMM公司的独家座椅供应商是肯塔基镶框座椅公司(KFS)。
KFS以顺序拉动式系统与TMM的生产装配线保持同步。
座椅是一个柔软易损部件。
后座的垫子的后面有个钩子用于钩住车身的“眼”,钩子由于由金属材料变更为塑料材料而容易折断,从而导致了这次严重的问题——生产线的产出率在一个月内由95%下降到了85%,离线车辆库存水平激增,并且不能按照承诺准时发货。
但是,在丰田日本工厂曾使用同样的工程设计发生该问题。
二、对TPS及其基于的JIT生产模式和自动化缺陷控制的介绍P1TPS的目标是彻底的消除浪费以降低成本,而它提供了两条指导原则以简化如何识别浪费这个关键过程:一是准时(JIT)生产,二是自动化缺陷控制原则。
P2准时生产方式(Just In Time)简称JIT,是日本丰田汽车公司在20世纪60年代创立的一种生产方式:只生产需要的产品,只生产需要的数量,同时只在需要的时候生产。
JIT采取的是多品种少批量、短周期的生产方式,实现了消除库存、优化生产物流、减少浪费的目的。
它将传统生产过程中前道工序向后道工序送货,改为后道工序根据“看板”向前道工序取货,看板系统是J IT生产现场控制技术的核心,但JIT不仅仅是看板管理。
丰田汽车制造公司案例分析
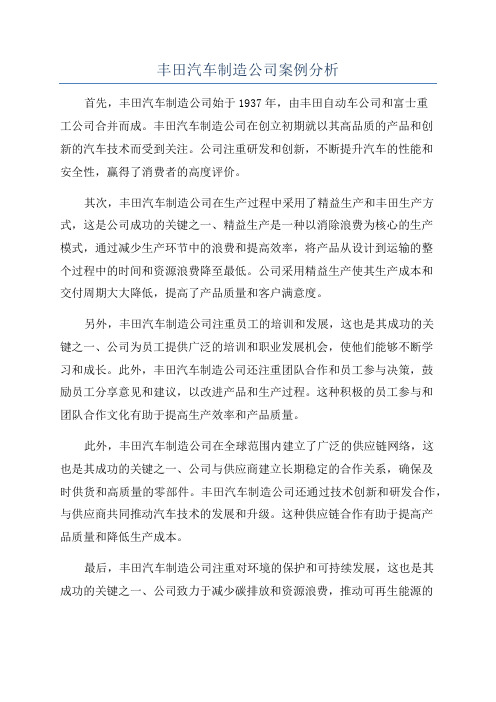
丰田汽车制造公司案例分析首先,丰田汽车制造公司始于1937年,由丰田自动车公司和富士重工公司合并而成。
丰田汽车制造公司在创立初期就以其高品质的产品和创新的汽车技术而受到关注。
公司注重研发和创新,不断提升汽车的性能和安全性,赢得了消费者的高度评价。
其次,丰田汽车制造公司在生产过程中采用了精益生产和丰田生产方式,这是公司成功的关键之一、精益生产是一种以消除浪费为核心的生产模式,通过减少生产环节中的浪费和提高效率,将产品从设计到运输的整个过程中的时间和资源浪费降至最低。
公司采用精益生产使其生产成本和交付周期大大降低,提高了产品质量和客户满意度。
另外,丰田汽车制造公司注重员工的培训和发展,这也是其成功的关键之一、公司为员工提供广泛的培训和职业发展机会,使他们能够不断学习和成长。
此外,丰田汽车制造公司还注重团队合作和员工参与决策,鼓励员工分享意见和建议,以改进产品和生产过程。
这种积极的员工参与和团队合作文化有助于提高生产效率和产品质量。
此外,丰田汽车制造公司在全球范围内建立了广泛的供应链网络,这也是其成功的关键之一、公司与供应商建立长期稳定的合作关系,确保及时供货和高质量的零部件。
丰田汽车制造公司还通过技术创新和研发合作,与供应商共同推动汽车技术的发展和升级。
这种供应链合作有助于提高产品质量和降低生产成本。
最后,丰田汽车制造公司注重对环境的保护和可持续发展,这也是其成功的关键之一、公司致力于减少碳排放和资源浪费,推动可再生能源的使用和环境友好型产品的开发。
丰田汽车制造公司还积极参与社会公益活动和社区发展,回馈社会。
总之,丰田汽车制造公司凭借其高品质的产品、精益生产和丰田生产方式、注重员工培训和发展、建立稳定的供应链网络以及注重环境保护和可持续发展等方面的优势,取得了长期成功。
丰田汽车制造公司的案例告诉我们,通过不断创新和提高生产效率,注重员工和客户的需求,以及积极回馈社会,可以实现持续发展和市场领导地位。
丰田案例分析报告(HBR分析法)

丰田汽车制造公司(美)分析报告2010111040006 付博文1.写作目的对丰田美国工厂座椅问题的分析2.立场陈述JIT本身是一个非常好的生产理念,但是如果没有对临时问题的合理处理办法,一味运用JIT做到准时生产,座椅问题是无法从根本上避免的。
3.证明案例中关键问题是座椅的挂钩出现容易折断的问题,直接影响了汽车的生产速率。
我们先用鱼骨图来分析这个问题。
丰田的高层也是通过这样逐个寻找原因,首先对原材料供应问题来解决,原材料是不存在问题,然后在设计方面,根据日本丰田公司也是运用同样的设计来制作的,但是却没有出现问题,最后基本确定了是生产线的问题,然后再根据生产线了解,那么确定了是员工的操作问题。
但是案例中并没有考虑有没有可能是自然环境造成的,比如湿度,气候抑或是生产线上的温度,在这方面出现问题的概率比较低,可能高层通过了调查,基本确定是人为问题,排除了自然问题。
通过最终确定下来的是原因使生产线上员工的操作问题。
这对于丰田是一个挺致命的问题。
要阐述问题的严重性,先大致了解一下丰田公司的jidoka原则——人工智能自动化质量控制。
一个帮助机器和操作员,发现异常情况并立即停止生产的方法。
它使得各工序能将质量融入生产,并且把人和机器分开,以利于更有效的工作。
jidoka突显出问题,因为当问题一出现的时候,工作就立即被停止下来。
通过消除缺陷的根源,来帮助改进质量。
如果操作员工遵循了jidoka原则,那么挂钩质量问题是可以避免的。
换一句话说,美国丰田公司的生产系统已经偏离了日本总公司的要求,这才是问题的关键。
在操作中,员工发现了这个质量问题,却没有及时停止生产,反而继续生产。
后续的生产并不知道之前的问题,继续生产,导致问题到了成品的时候才解决。
这时所耗损的成本就远远高于及时停止生产的成本,在下面一部分,我们着重来研究jidoka原则。
Jidoka原则是帮助人自动化控制质量,将质量与生产有机融合一起,在生产每个环节中改进质量。
丰田案例
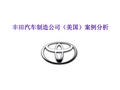
TPS—丰田生产系统
2、 全面质量管理 强调质量是生产出来而非检验出来的,由生产中的质量管理来保证 产品的最终质量。在每道工序进行时均注意质量的检测与控制,保证 及时发现质量问题,培养每位员工的质量意识。如果发现问题,立即 停止生产,直至解决,从而保证不出现对不合格产品的失效加工。 3、 团队工作方法(Team Work) 每位员工在工作中不仅仅是执行上级的命令,更重要的是积极地参与 ,起到决策与辅助决策的作用。组织团队的原则并不完全按行政组织 来划分,而主要根据业务的关系来划分。团队成员强调一专多能,工 作的氛围是信任,以一种长期的监督控制为主,而避免对每一步工作 的稽核,提高工作效率。团队的组织是变动的,针对不同的事物,建 立不同的团队,同一个人可能属于不同的团队。
TPS—丰田生产系统
• 4、 并行工程 在产品设计开发期间,将概念设计、结构设计、工艺设 计、最终需求等结合起来,保证以最快的速度按要求的质 量完成。TPS的另一大理念--零库存,就是随时反馈订 货信息,实现生产与销售的并行化。 • TPS最终目标是企业利润的最大化。管理中的具体目标是 通过消灭一切生产中的浪费来实现成本的最低化。 • TPS通过准时化生产、全面质量管理、并行工程等一系列 方法来消除一切浪费,实现利润最大化。TPS最具特色的 方法是,在组织生产时对消灭物流浪费的无限追求,即对 物流环境的需求和内部的分权决策。 综上所述,基于内部 的团队式工作方式,在外部企业密切合作的环境下,无限 追求物流的平衡是精益生产的核心所在,即TPS的精髓之 所在!
存在问题分析
• 座椅的钩子出了问题,有可能是:1、设计问题;2、KFS 的生产问题;3、TMM安装问题。但TMM和Tsutsumi工厂 使用的是同样的工程设计,却没有发生类似故障,所以问 题可能出在2或3。使用5个WHY去发现问题。
丰田八步法实际案例

丰田八步法实际案例某大型制造企业的生产线存在生产效率低下的问题,为了解决这个问题,企业决定引入丰田生产方式,并采用丰田八步法进行优化。
第一步:明确问题。
企业的目标是提高生产效率,具体指标是降低生产成本、缩短生产周期、提高产品质量。
现状是生产线存在浪费、不平衡、设备故障率高、员工技能水平不一等问题。
理想状态是实现生产线平衡、降低浪费、提高设备利用率和员工技能水平。
第二步:分析现状。
企业收集了生产线相关的数据,包括设备利用率、员工效率、产品质量等信息,并对生产线进行了现场观察。
通过数据分析,企业发现生产线存在严重的浪费问题,包括过度生产、等待时间、运输、不良品等。
同时,设备故障率高也是导致生产效率低下的重要原因。
第三步:确定要因。
经过分析,企业确定了导致生产效率低下的主要原因,包括设备故障率高、生产线不平衡、员工技能水平不一等。
第四步:制定对策。
针对要因,企业制定了相应的对策,包括建立设备维护体系、实施生产线平衡改善、开展员工技能培训等。
第五步:实施对策。
企业按照制定的对策进行了实施,包括建立设备维护体系、对生产线进行重新布局和平衡调整、开展员工技能培训等。
在实施过程中,企业采用了丰田生产方式中的看板管理、标准化作业等工具和方法。
第六步:检查效果。
经过一段时间的实施,企业对改善效果进行了检查。
通过对比改善前后的数据,企业发现生产效率得到了显著提高,生产成本降低了20%,生产周期缩短了30%,产品质量也得到了明显改善。
第七步:标准化。
为了保持改善成果并持续改进,企业将改善过程中形成的经验和方法进行了总结和归纳,形成了标准化的作业流程和规范,并在企业内部进行了推广和实施。
第八步:持续改进。
企业建立了持续改进的机制,定期对生产线进行检查和评估,发现问题及时进行处理和改进。
同时,企业还鼓励员工提出改进意见和建议,并对其进行评估和实施。
丰田汽车成本企划实施案例分析

丰田汽车成本企划实施案例分析丰田汽车公司作为全球知名的汽车制造商,其成功的秘诀在于不断改进和创新。
在成本控制方面,丰田汽车公司同样有着一套独特的成本企划实施案例。
本文将对丰田汽车公司成本企划的实施背景、具体案例以及所带来的启示进行分析。
丰田汽车公司的成本企划始于20世纪70年代,当时正值全球石油危机,汽车行业面临着严峻的挑战。
为了应对这一挑战,丰田汽车公司开始着手实施成本企划,旨在降低生产成本、提高产品竞争力。
丰田汽车公司通过对供应链的优化,实现了对原材料采购、零部件制造等环节的成本控制。
具体措施包括:采用招标方式进行原材料采购,以获取更优的价格;对零部件制造进行精细化管理,减少浪费。
这些措施使得丰田汽车公司在供应链环节降低了成本。
丰田汽车公司通过对生产流程进行优化,提高了生产效率,降低了生产成本。
具体措施包括:采用流水线生产方式,减少生产中的浪费;引入机器人等自动化设备,提高生产效率;实施精益生产理念,持续改进生产过程中的问题。
这些措施使得丰田汽车公司在生产环节进一步降低了成本。
丰田汽车公司通过对研发成本进行控制,实现了对新产品开发成本的降低。
具体措施包括:对产品设计进行模块化处理,减少零配件数量;引入计算机辅助设计技术,提高设计效率;对技术研发进行精细化管理,减少不必要的开支。
这些措施使得丰田汽车公司在研发环节降低了成本。
丰田汽车公司的成本企划实施案例为我们提供了以下几点启示:精细化管理是成本控制的关键。
丰田汽车公司在各个环节都实施了精细化管理,从而减少了浪费,提高了效率。
技术创新是降低成本的重要手段。
丰田汽车公司通过引入新技术、新工艺,提高了生产效率,降低了生产成本。
供应链管理是成本控制的重要环节。
丰田汽车公司通过对供应链的优化,降低了原材料采购和零部件制造的成本。
持续改进是降低成本的核心。
丰田汽车公司通过持续改进生产过程中的问题,不断优化生产流程,提高了生产效率。
丰田汽车公司的成本企划实施案例为我们提供了宝贵的经验。
(运营管理)运营管理之丰田案例分析
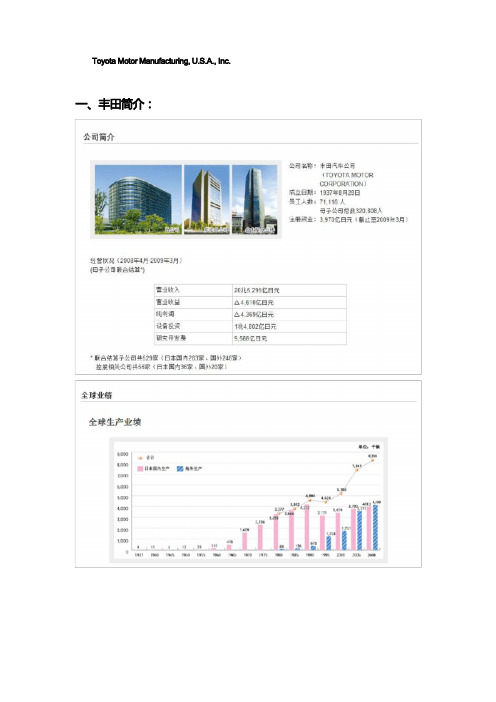
从上图中可以看出,丰田在全球27 个国家和地区(不包括日本本土)总共设有53 家工厂,而这其中,美国一个国家就有10 家工厂,占比接近20%。
下图是丰田在北美地区的工厂列表丰田品质:丰田汽车以其享誉全球的丰田品质备受世界各国人民的信赖与爱慕。
这归功于丰田人“顾客至上”的理念和由此形成的在开辟、生产、销售及服务各领域中的综合实力。
通过下图来简要了解一下丰田的生产方式——TPS。
1、座椅挂钩设计问题;2、供应商供应的座椅挂钩质量存在缺陷;3 、丰田汽车美国公司员工安装操作存在问题。
1、是否是设计问题首先我们需要确认是否是座椅或者座椅挂钩的设计问题导致的。
根据案例可知,KFS 是丰田汽车公司座椅的惟一供应商,地处日本的Tsutsumi 工厂使用同样的设计方式,但是并未遇到类似问题。
因此可以判断美国工厂的座椅问题不是由挂钩的设计问题所导致。
2、是否是质量问题接下来,我们将目标锁定在坐椅或者座椅挂钩本身的质量问题上。
如果确认是产品本身的质量问题,需要迅速与质量管控部门(Quality Control)、进货检查部门、KFS 一起讨论解决问题的方法。
请KFS 限期解决,KFS 方面,认真研究浮现质量问题的关键点所在并试图改进,而丰田工厂的质量管控部门和进货检查部门则需要改进进货审查的标准,保证在产品到货时能第一时间发现潜在质量问题,避免问题的进一步升级。
3、员工安装操作问题不可否认,在安装操作环节,也是有可能发生问题的。
在确保产品质量无问题的基础上,我们需要检查作业人员是否存在误操作问题。
由于Final 2 刚刚接受一批新团队成员,新手操作不熟练非常可能导致浮现座椅问题。
如果确系是该方面的问题,要立刻对作业人员重新进行严格的操作培训,同时加强部门抽查和监管制度,派有经验的老员工在生产线上进行审查和指导。
丰田TPS 生产方式的两大核心是自动化和准时化生产。
准时化生产即JIT (just in time)生产方式。
丰田的生产线优化案例

丰田的生产线优化案例丰田汽车公司作为世界上最大的汽车制造商之一,一直以来都在不断探索和改进生产线的优化方法。
本文将以丰田的生产线优化案例为例,探讨丰田在提高生产效率和质量方面所采取的举措。
1. 引言丰田汽车公司一直以来以其高效、精益的生产线而闻名于世。
丰田不仅仅关注于生产数量的提升,更注重于生产质量的优化。
为了达到这个目标,丰田不断改进和优化其生产线,提高生产效率以及质量控制。
2. 丰田生产方式——精益生产丰田的生产方式基于精益生产原则,即通过最小化浪费和优化生产流程,实现生产效率的最大化。
该生产方式包括以下几个关键要素:- 精确计划:丰田根据市场需求和预测进行精确的生产计划,尽量避免库存过剩或供应不足的情况。
- 拉动式生产:丰田采用拉动式生产方式,根据订单需求进行生产,减少库存和浪费。
- 柔性生产:丰田生产线具备高度柔性,能够根据需求快速调整生产线的布置和产品组装流程。
- 持续改进:丰田通过实施持续改进的措施,包括员工培训、设备更新等,不断提高生产效率和质量。
3. 制定生产计划丰田通过精确的生产计划来确保生产线的运转顺利。
生产计划包括确定产品类型、数量和交付时间等要素。
丰田通过分析市场需求和预测,制定详细的生产计划,并确保生产线按计划进行生产。
4. 流程优化丰田将生产线视为一个整体,通过优化流程来提高生产效率和质量。
丰田通过时间研究和价值流分析等方法,识别出生产过程中的瓶颈和浪费环节,并进行相应的改进。
丰田还使用了一些工具,如交钥匙生产线、单元生产线等,控制生产流程,减少传统生产线上的浪费。
5. 质量控制丰田对生产质量有着严格的控制标准。
丰田通过严谨的质量管理流程,确保每个产品都符合规定的质量要求。
质量管理包括以下几个方面:- 检测设备:丰田使用先进的检测设备来对产品进行检验,确保产品质量符合标准。
- 员工培训:丰田对生产线的操作员进行系统培训,并建立了严格的操作规程,以确保操作的准确性和一致性。
丰田公司管理案例分析

丰田公司管理案例分析丰田公司是世界上最大的汽车制造商之一,以其高质量的产品和创新的管理理念而闻名。
本文将分析丰田公司的管理案例,探讨其成功的原因和可借鉴的经验。
首先,丰田公司秉持着“持续改进”的经营理念。
丰田的创始人丰田喜一郎提出了“丰田生产方式”,主张不断改进和提高生产效率。
丰田实施了“精益生产”模式,通过消除浪费和优化生产流程来提高效率。
这种持续改进的经营理念使丰田能够灵活应对市场需求的变化,并及时进行改进和调整。
第二,丰田公司注重员工的培训和发展。
丰田侧重于培养和激励员工,使他们成为企业的积极参与者。
丰田推行了“人员长期雇佣”政策,鼓励员工长期留在公司并提供培训机会,以提高他们的技能和知识水平。
丰田还采取了“寻求员工意见”的方法,鼓励员工参与决策和改进过程。
通过这种方式,丰田能够激励员工的积极性和创造力,使其为公司做出更大的贡献。
第三,丰田公司注重质量管理。
丰田以其高质量的产品而闻名,这得益于丰田对质量的严格控制和不断改进。
丰田实施了“质量管理圆圈”模式,通过持续的质量改进活动来确保产品的质量。
丰田还注重与供应商的合作,并建立了与供应商共同解决质量问题的机制。
这种注重质量的管理方式使丰田能够提供可靠和高质量的产品,赢得了消费者的信任和支持。
第四,丰田公司注重可持续发展。
丰田将可持续发展纳入其经营战略中,提出了“丰田环境挑战2050”计划。
丰田致力于开发低碳和环保的汽车技术,减少对自然资源的依赖,并改善生态环境。
丰田还注重社会责任,积极参与公益活动和社区建设。
这种以可持续发展为导向的经营理念使丰田在面对日益严峻的环境和资源压力时能够积极应对。
总的来说,丰田公司的管理案例表明其成功的原因在于持续改进的经营理念、注重员工的培训和发展、注重质量管理以及注重可持续发展。
这些经验可以对其他企业提供启示和借鉴:不断改进和提高,培养员工的积极性和创造力,注重质量管理以及注重可持续发展。
这些管理原则对于企业的长期发展和竞争力的提升都具有重要意义。
丰田汽车公司案例讨论分析
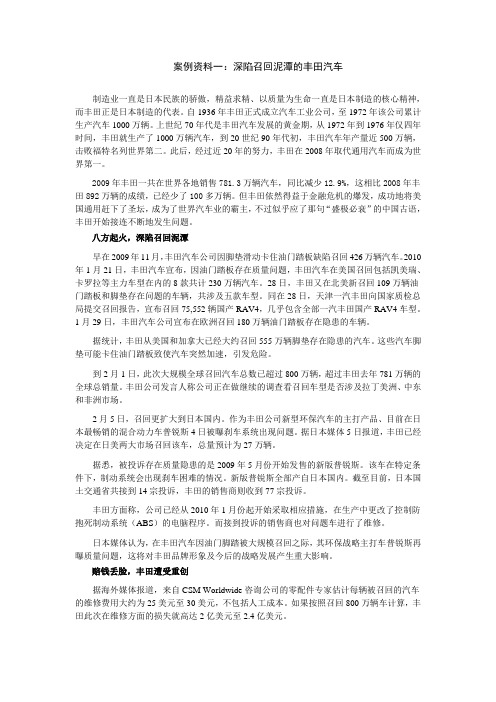
案例资料一:深陷召回泥潭的丰田汽车制造业一直是日本民族的骄傲,精益求精、以质量为生命一直是日本制造的核心精神,而丰田正是日本制造的代表。
自1936年丰田正式成立汽车工业公司,至1972年该公司累计生产汽车1000万辆。
上世纪70年代是丰田汽车发展的黄金期,从1972年到1976年仅四年时间,丰田就生产了1000万辆汽车,到20世纪90年代初,丰田汽车年产量近500万辆,击败福特名列世界第二。
此后,经过近20年的努力,丰田在2008年取代通用汽车而成为世界第一。
2009年丰田一共在世界各地销售781.3万辆汽车,同比减少12.9%,这相比2008年丰田892万辆的成绩,已经少了100多万辆。
但丰田依然得益于金融危机的爆发,成功地将美国通用赶下了圣坛,成为了世界汽车业的霸主,不过似乎应了那句“盛极必衰”的中国古语,丰田开始接连不断地发生问题。
八方起火,深陷召回泥潭早在2009年11月,丰田汽车公司因脚垫滑动卡住油门踏板缺陷召回426万辆汽车。
2010年1月21日,丰田汽车宣布,因油门踏板存在质量问题,丰田汽车在美国召回包括凯美瑞、卡罗拉等主力车型在内的8款共计230万辆汽车。
28日,丰田又在北美新召回109万辆油门踏板和脚垫存在问题的车辆,共涉及五款车型。
同在28日,天津一汽丰田向国家质检总局提交召回报告,宣布召回75,552辆国产RAV4,几乎包含全部一汽丰田国产RAV4车型。
1月29日,丰田汽车公司宣布在欧洲召回180万辆油门踏板存在隐患的车辆。
据统计,丰田从美国和加拿大已经大约召回555万辆脚垫存在隐患的汽车。
这些汽车脚垫可能卡住油门踏板致使汽车突然加速,引发危险。
到2月1日,此次大规模全球召回汽车总数已超过800万辆,超过丰田去年781万辆的全球总销量。
丰田公司发言人称公司正在做继续的调查看召回车型是否涉及拉丁美洲、中东和非洲市场。
2月5日,召回更扩大到日本国内。
作为丰田公司新型环保汽车的主打产品、目前在日本最畅销的混合动力车普锐斯4日被曝刹车系统出现问题。
案例丰田汽车质量管理案例分析
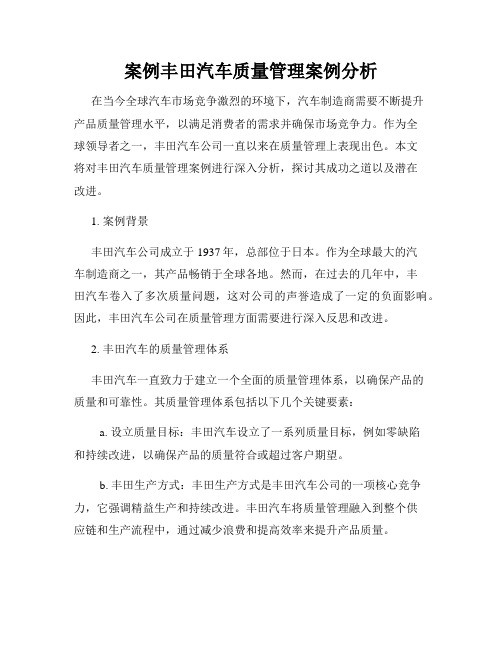
案例丰田汽车质量管理案例分析在当今全球汽车市场竞争激烈的环境下,汽车制造商需要不断提升产品质量管理水平,以满足消费者的需求并确保市场竞争力。
作为全球领导者之一,丰田汽车公司一直以来在质量管理上表现出色。
本文将对丰田汽车质量管理案例进行深入分析,探讨其成功之道以及潜在改进。
1. 案例背景丰田汽车公司成立于1937年,总部位于日本。
作为全球最大的汽车制造商之一,其产品畅销于全球各地。
然而,在过去的几年中,丰田汽车卷入了多次质量问题,这对公司的声誉造成了一定的负面影响。
因此,丰田汽车公司在质量管理方面需要进行深入反思和改进。
2. 丰田汽车的质量管理体系丰田汽车一直致力于建立一个全面的质量管理体系,以确保产品的质量和可靠性。
其质量管理体系包括以下几个关键要素:a. 设立质量目标:丰田汽车设立了一系列质量目标,例如零缺陷和持续改进,以确保产品的质量符合或超过客户期望。
b. 丰田生产方式:丰田生产方式是丰田汽车公司的一项核心竞争力,它强调精益生产和持续改进。
丰田汽车将质量管理融入到整个供应链和生产流程中,通过减少浪费和提高效率来提升产品质量。
c. 供应链管理:丰田汽车与供应商建立了战略合作伙伴关系,共同开展质量管理活动。
通过与供应商的紧密合作和沟通,丰田汽车可以更好地控制供应链中的质量问题。
d. 客户反馈和投诉处理:丰田汽车高度重视客户反馈和投诉,并建立了完善的反馈和投诉处理机制。
通过及时响应和解决客户问题,丰田汽车可以不断改进产品并提高客户满意度。
3. 丰田汽车的成功之处丰田汽车在质量管理方面的成功可以归因于以下几个关键因素:a. 领导力的支持:丰田汽车的高层管理人员高度重视质量管理,并通过持续投资和资源的支持来确保质量管理的有效实施。
b. 员工参与和培训:丰田汽车鼓励员工参与质量管理活动,并为员工提供培训机会,以提高他们的质量意识和技能。
c. 持续改进文化:丰田汽车倡导持续改进的文化,鼓励员工在工作中发现问题并提出改进建议。
丰田汽车案例分析

一、案例背景P1位于美国肯塔基州的丰田汽车制造公司(美国)(TMM)乔治敦工厂于1988年开始进行大规模生产。
这家工厂所采用生产和管理系统正是丰田独特的丰田生产系统(TPS)。
1992年初,TMM将佳美的两厢版投放市场,使得座椅样式由原来的5种迅速增加为发往北美的8种、发往欧洲的10种、发往日本和中东的18种,合计36种。
此时,乔治敦工厂的装配线经理道格·弗里森遇到了急需解决的座椅问题。
P2TMM公司的独家座椅供应商是肯塔基镶框座椅公司(KFS)。
KFS以顺序拉动式系统与TMM的生产装配线保持同步。
座椅是一个柔软易损部件。
后座的垫子的后面有个钩子用于钩住车身的“眼”,钩子由于由金属材料变更为塑料材料而容易折断,从而导致了这次严重的问题——生产线的产出率在一个月内由95%下降到了85%,离线车辆库存水平激增,并且不能按照承诺准时发货。
但是,在丰田日本工厂曾使用同样的工程设计发生该问题。
二、对TPS及其基于的JIT生产模式和自动化缺陷控制的介绍P1TPS的目标是彻底的消除浪费以降低成本,而它提供了两条指导原则以简化如何识别浪费这个关键过程:一是准时(JIT)生产,二是自动化缺陷控制原则。
P2准时生产方式(Just In Time)简称JIT,是日本丰田汽车公司在20世纪60年代创立的一种生产方式:只生产需要的产品,只生产需要的数量,同时只在需要的时候生产。
JIT采取的是多品种少批量、短周期的生产方式,实现了消除库存、优化生产物流、减少浪费的目的。
它将传统生产过程中前道工序向后道工序送货,改为后道工序根据“看板”向前道工序取货,看板系统是JIT生产现场控制技术的核心,但JIT不仅仅是看板管理。
P3自动化缺陷控制(Jidoka)是一种时间化的概念,即发现错误时生产线立即停止,进入生产线停止系统。
“生产线停止系统”是Jidoka的精髓,工人若发现瑕疵,可立刻拉动安灯(andon)线,以告知团队领导速来处理。
丰田汽车案例分析

企业简介:
丰田汽车公司简称“丰田”(TOYOTA),创始人为 丰田喜一郎,是一家总部设在日本爱知县丰田市和东京都 文京区的汽车工业制造公司,前身为日本大井公司,隶属 于日本三井产业财阀。
丰田是世界十大汽车工业公司之一,全球最大的汽车公 司,丰田喜一郎1933年在丰田自动织机制作所成立汽车 部,1937年汽车部正式从丰田自动织机制作所中独立出 来,成立丰田汽车工业公司。早期的丰田牌、皇冠、光冠、 花冠汽车名噪一时,近来的克雷西达、凌志豪华汽车也极 负盛名。TOYOTA在汽车的销售量、销售额、知名度方面 均是世界三强公司之一。TOYOTA生产包括一般大众性汽 车、高档汽车、面包车、跑车、四轮驱动车、商用车在内 的各种汽车。
二、找敌手的错误谬误
丰田定位于美国小型车市场,但该市场也并非没有敌手的赛场, 德国公共公司的小型车就很滞销。丰田招聘美国的查询拜访公司 对公共汽车的用户停止了详细的查询拜访,充实把握了敌手的好 坏,除了车型对劲消费者需要之外,其高效、优良的服务网撤销 了美国人对本国车培修坚苦的疑虑;暖气装备欠好、后座间小、外 部装潢差是浩繁用户对公共车的埋怨。敌手的空子就是本身的机 遇,敌手的错误谬误就是本身的方针。在市场调研的基础上,丰 田公司精确地勾勒出一个按人口统计和心理因素区分的方针市场, 设想出对劲美国顾客需要的美式日制小轿车。花冠车(CORNA), 以其外型玲珑、经济实惠、舒适安稳、培修便利的上风终究敲开 了美国市场的大门,步入成功之路。
丰田汽车市场开辟的营销战略
80年代初,北京机场路四周树起了一块广告牌,全部广告牌以白 色为主色彩,色彩非常艳丽,在四周白纸黑字、色彩繁多的广告牌 群中非常夺目,颠末这里的人们还在老远,眼光就已被它深深吸收,
,看到的是广告牌上一 排清楚的大字“车到山前必有路,有路必有丰田车”。这句广告语 奇妙的借用了中国古语——“车到山前必有路”,而后小题大 作,“有路必有丰田车”,琅琅上口,过目成诵,同时表白了丰田对本 身产物不相上下的决定信念,较之广告牌外观上的过人之处又高超 得多。丰田的这句广告语一出,就遭到媒体和营销界人士的鼎力吹 嘘,丰田汽车的名望也响彻了中国大地。这句广告语以至轰动了那 时并不活泼的中国市场,仅1980-1986年,我国用于入口轿车的 资金就跨越了开国30多年对全部汽车工业的投资!
丰田案例分析
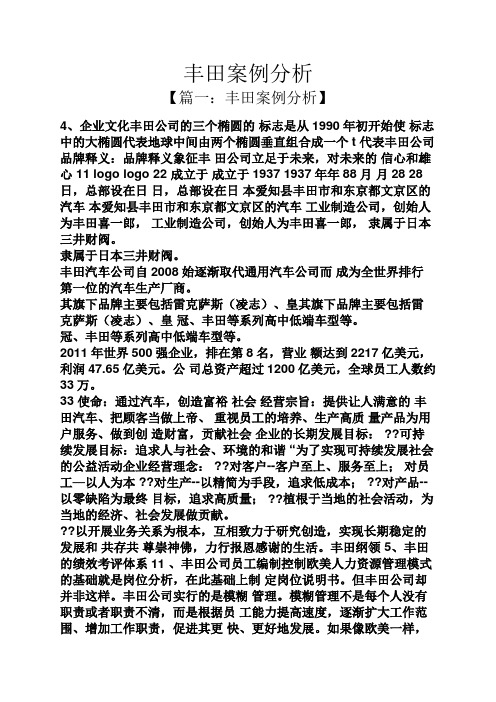
丰田案例分析【篇一:丰田案例分析】4、企业文化丰田公司的三个椭圆的标志是从1990年初开始使标志中的大椭圆代表地球中间由两个椭圆垂直组合成一个t 代表丰田公司品牌释义:品牌释义象征丰田公司立足于未来,对未来的信心和雄心 11 logo logo 22 成立于成立于1937 1937年年88月月28 28日,总部设在日日,总部设在日本爱知县丰田市和东京都文京区的汽车本爱知县丰田市和东京都文京区的汽车工业制造公司,创始人为丰田喜一郎,工业制造公司,创始人为丰田喜一郎,隶属于日本三井财阀。
隶属于日本三井财阀。
丰田汽车公司自2008始逐渐取代通用汽车公司而成为全世界排行第一位的汽车生产厂商。
其旗下品牌主要包括雷克萨斯(凌志)、皇其旗下品牌主要包括雷克萨斯(凌志)、皇冠、丰田等系列高中低端车型等。
冠、丰田等系列高中低端车型等。
2011年世界500强企业,排在第8名,营业额达到2217亿美元,利润47.65亿美元。
公司总资产超过1200亿美元,全球员工人数约33万。
33 使命:通过汽车,创造富裕社会经营宗旨:提供让人满意的丰田汽车、把顾客当做上帝、重视员工的培养、生产高质量产品为用户服务、做到创造财富,贡献社会企业的长期发展目标: ??可持续发展目标:追求人与社会、环境的和谐“为了实现可持续发展社会的公益活动企业经营理念: ??对客户--客户至上、服务至上;对员工—以人为本 ??对生产--以精简为手段,追求低成本; ??对产品--以零缺陷为最终目标,追求高质量; ??植根于当地的社会活动,为当地的经济、社会发展做贡献。
以开展业务关系为根本,互相致力于研究创造,实现长期稳定的发展和共存共尊崇神佛,力行报恩感谢的生活。
丰田纲领 5、丰田的绩效考评体系11 、丰田公司员工编制控制欧美人力资源管理模式的基础就是岗位分析,在此基础上制定岗位说明书。
但丰田公司却并非这样。
丰田公司实行的是模糊管理。
模糊管理不是每个人没有职责或者职责不清,而是根据员工能力提高速度,逐渐扩大工作范围、增加工作职责,促进其更快、更好地发展。
精益项目案例

精益项目案例分析:丰田汽车生产系统1. 背景丰田汽车公司是一家全球知名的汽车制造商,其成功的背后离不开其独特的生产系统——丰田生产方式(Toyota Production System,简称TPS)。
TPS是一种精益制造方法,强调通过消除浪费、提高质量和灵活性来实现高效率的生产。
它被广泛认为是精益项目管理的典范。
2. 过程2.1 浪费的识别和消除在丰田汽车生产过程中,浪费被视为敌人。
TPS强调通过持续改进来减少或消除各种类型的浪费,包括:•运输浪费:减少零部件和成品的运输距离,提高物流效率。
•库存浪费:实施“拉动式”生产模式,根据需求进行生产,降低库存水平。
•过程浪费:优化生产线布局和工艺流程,减少不必要的动作和等待时间。
•缺陷浪费:通过强调质量控制和错误防止来减少产品缺陷。
2.2 持续改进和员工参与TPS强调持续改进和员工参与是实现精益生产的关键。
丰田鼓励每个员工积极参与问题解决和流程改进,通过小组讨论、持续培训和跨职能合作来推动创新。
丰田还实施了一系列激励措施,如奖励制度和晋升机会,以鼓励员工主动参与改进活动。
2.3 价值流分析价值流分析是TPS中的重要工具,用于识别生产过程中的价值增加和非价值增加活动。
通过观察整个价值链,识别并消除非必要的环节和步骤,从而提高生产效率。
2.4 灵活生产灵活生产是TPS的另一个重要特点。
丰田采用“多品种小批量”生产模式,根据市场需求进行灵活调整。
通过减少换线时间、提高设备利用率和优化供应链管理,丰田能够快速响应市场变化,并减少库存积压。
3. 结果丰田汽车公司通过采用TPS实现了显著的业绩提升和竞争优势:•高效率生产:丰田的生产效率远高于其他汽车制造商。
通过消除浪费和持续改进,丰田能够以更低的成本和更短的交付时间生产汽车。
•高质量产品:TPS强调质量控制和错误防止,丰田汽车以其可靠性和耐用性而闻名。
丰田的产品质量指标始终领先于同行业竞争对手。
•灵活供应链:通过灵活生产和优化供应链管理,丰田能够根据市场需求快速调整生产计划,并避免了因库存积压而带来的资金压力。
- 1、下载文档前请自行甄别文档内容的完整性,平台不提供额外的编辑、内容补充、找答案等附加服务。
- 2、"仅部分预览"的文档,不可在线预览部分如存在完整性等问题,可反馈申请退款(可完整预览的文档不适用该条件!)。
- 3、如文档侵犯您的权益,请联系客服反馈,我们会尽快为您处理(人工客服工作时间:9:00-18:30)。
丰田汽车制造公司案例分析
1、座椅问题的背景:
案例讲述了20世纪80年代,丰田汽车公司在美国创建了丰田汽车制造公司(美国)(TMM)。
TMM采用了丰田生产系统(TPS),坚持准时生产(JIT)和自动化缺陷控制两项原则,实现了高效率和高质量的汽车生产装配。
但到了1992年,佳美出了新款车型,座椅样式由原来的5种样式增加到10种,出口到日本和中东的款式更是增加了18种不同的座椅样式。
座椅样式的剧增,导致了座椅组和汽车不相匹配等各种座椅的问题,使产出率降低到不足85%,10个百分点的下降意味着每个班次少生产45辆汽车。
装配部负责人弗里森需要尽快了解并解决座椅问题,并且完善座椅问题修复的系统,使产出率重新提高。
2、座椅问题的归纳:
从案例中,我们可以归纳出座椅问题主要有以下几个:
(1)KFS有时会送来错误的座椅配件,这些座椅配件与任何一辆待返工的汽车都不匹配。
(严重问题,影响产量)
(2)从某个侧面角度上螺栓时,偶尔会出现串线问题,但团队领导应当可以使用螺纹工具在30秒内在线解决该问题。
(容易解决)
(3)有人偶尔因使用手工工具损坏座椅外罩,但他们回忆不起来最近发生的同样情况。
(很少出现)
(4)后座垫子的后面有个突出的钩子,钩子有时会绷断。
但钩子的损坏频率已从每班次7次降低到每班次1次。
(频率较低)
3、根据以上问题,弗里森需要建立问题恢复系统:
当前TMM对座椅问题的处理有标准化的响应措施:
(1)团队成员在安装有缺陷的座椅前,拉一下安灯线将问题报告给团队领导。
(2)团队领导再拉一下安灯线表示收到信息,给相应汽车加上标签以提醒QC检查人员注意座椅问题。
(3)装配有缺陷的座椅的汽车在下线时被送到1号诊断区,检查出现的问题可否在那里得到解决。
如果要更换座椅,那么汽车将转移到溢出停车区,在那里将订购替换座椅,等待KFS的特殊交付。
有缺陷的座椅将被退回至KFS。
该措施能够解决每一台有缺陷座椅的汽车,且无需关闭整条生产线,因此该流程并没有问题。
但措施仅是头痛医头的做法,不能根本性降低座椅的缺陷率,导致产量下降和过多的汽车进入溢出停车区进行离线操作。
因此,建议继续保留上述响应流程的同时,增加以下几项措施:
首先,要解决的问题是,KFS的配送准确率。
与KFS磋商,建立奖惩措施。
有效防止KFS配送不匹配的座椅配件(如一个月出现一次配送问题,KFS应赔偿5万美元影响产量费,如三个月内未出现一次配送问题,可奖励KFS公司1万美元)。
根据双方认同的奖惩措施,大幅提高配送的准确率。
接着,是提高再订购的响应频率。
目前KFS对于再订购是以一天两次的特别更换交付作为响应,建TMM应要求KFS更加灵活,根据当天的再订购数量来确
定特别更换交付的频次,如果再订购数量较多,则以一天三次或者四次的频率来响应,以提高座椅问题维修效率和产量。
然后,需要解决后座钩子问题。
因为改变制造钩子的相关工具将让KFS花费5万美元左右,虽然钩子损坏频率已降低到每班次1次,但是为了提高工作效率和产量,建议由TMM提供费用给KFS改进钩子工艺,从而大幅降低钩子的损坏率。
最后,是减少座椅装配过程中的失误率,提高团队协助效率。
建立惩罚措施,如发现在装配过程中,损坏座椅的,进行相应惩罚,以降低失误率。
对于串线问题,小组领导和团队成员应共同监督团队领导迅速在装配线上解决问题,避免问题的堆积。
通过以上措施,我们相信能够有效地解决座椅问题,同时也是遵循了JIT原则,避免了浪费,保证产量的可持续性。
没有采用自动化缺陷控制原则,因为停止生产将产生很大损失。
我们认为在装配线上处理有缺陷座椅是不合适的,除非是串线等小问题可以在线上解决,其他问题是可以采用以上措施进入溢出停车区解决。
我们认为这个程序是TPS的一个合理的例外,因为座椅问题无法完全杜绝,只能最大限度降低错误率。