车架铆接工艺准则
浅谈现代化重型汽车车架铆接质量控制

浅谈现代化重型汽车车架铆接质量控制摘要车架的铆接工艺是车架制造过程中的关键技术之一,约占汽车车架总成及分总成加工工作的80%以上,在汽车载荷和使用性能方面,车架要求有足够的强度和刚度方可满足车辆的各种运行路况,而铆接质量的控制就显得至关重要。
关键词铆接工艺;铆接质量我公司铆接车间采用2条自动流水作业和1条简易轨道流水线,各工序转运采用自动板链式输送和轨道小车推动式输送,目前可以满足牵引车、自卸车、载货车、专用特种车以及军用越野车等各种车型铆接任务。
1 铆钉材料选用原则铆接的钢结构中,铆钉材料必须具有较高的塑性和不可淬性。
常用钢制的铆钉。
一般钢制铆钉的材料采用以下几种材料制作:普通碳素钢:如Q235、Q215A、BL2、BL3;普通碳素铆接用钢:如ML2、ML3、ML10、ML15、ML20;优质碳素钢:如10、15;我公司车架所用钢制铆钉一般选用普通碳素铆接用钢中的ML10和ML15。
2 铆钉直径选用原则铆钉直径的确定选择是根据结构件的受力情况,考虑铆接件的强度要求,通过力学分析和计算得到的。
铆钉直径的正确选择,主要是根据板料的厚度来确定。
板料厚度又必须依以下三个原则确定:①板料与板料搭接按较厚板料的厚度确定;②厚度相差较大时以较薄板料的厚度确定;③钢板与型材铆接时,以两者的平均厚度确定。
多层板料的总厚度,不应超过铆钉直径的4倍[1]。
铆钉直径也可按下列公式计算:d=式中d—铆钉直径mm;t—板料厚度mm。
3 鉚钉长度的选用原则铆钉钉杆的长度一般是根据被铆接件的总厚度、铆钉直径和铆接工艺等因素来确定的。
对于车架铆钉长度选用原则:铆钉钉杆的体积等于铆接孔的体积加上成形铆头体积[2]。
常用半圆头铆钉的钉杆长度计算公式如下:半圆头铆钉L=(1.65~1.75)d+1.1t式中L—铆钉长度mm;d—铆钉直径mm;t—被铆接件的总厚度mm。
4 铆钉孔径的选用原则铆钉孔直径一般比铆钉直径稍大。
在铆接时,如孔径过大,钉杆容易弯曲,影响铆接质量和铆接强度;如孔径与铆钉直径相等或过小,铆接时铆钉难以插入孔内,或者引起板料凸起和凹入,造成表面不平整,甚至因铆钉膨胀挤坏板料。
载重车架生产工艺课件-铆接

4
T48自卸车
81.41016.6373
车架前宽后窄,变 截面,和 T48牵引 车前段相同
10、工艺文件中的符号、代号及含义
例:AC300N.m 扭力扳手 适用范围:300N.m B16 气扳机 适用范围:最大拧紧螺栓直径M16 S18 套筒 适用于六方为18的螺栓 S-087-171 专用工装代号
DZ9112510140 DZ9100510170 2 S29 DZ9114512710
DZ9114512910 DZ9114515700
9.2德御车系列 为了加宽横梁上、下连接板距离,采用新横梁结构,为了降重心, 横梁位置降低,横梁连接板加高、加宽。横梁连接板上翻,部分 弯梁采用MAN结构形式。
12、铆接工艺知识及铆接标准:
12.1、铆接 车架总成铆接分为冷铆和热铆。 12.1.1、冷铆:铆钉在常温状态下的铆接称为冷铆。 铆接时,所用的铆钉由低碳钢制成,而且要经过退火处理。冷铆时,铆 钉杆不易镦粗,为保证连接强度,钉孔直径和钉杆直径应尽量接近,使钉和 孔严密,防止板料之间有滑动现象,产生冲击应力。一般铆钉孔比铆钉直径 大0.5mm,冷铆铆接力F=20d2(吨),即Φ12铆钉冷铆压力为30吨,Φ14 铆钉冷铆压力为40吨。 冷铆优点:操作过程简化迅速,铆钉孔比热铆填充得紧密。 12.1.2、热铆:铆钉加热后的铆接称为热铆。 铆钉加热温度为1000度以上,铆接力F=10A(A为铆钉截面积cm2), 即Φ16铆钉热铆压力为20吨,Φ18铆钉热铆压力为25吨。 热铆优点:铆钉冷却后,在长度方面的收缩受到板料厚度的限制,钉杆 产生的内应力,作用在板料上,使板料压紧。当铆接件受力时,铆接件和板 料之间产生很大的摩擦阻力,因而提高了铆接件的联接强度。
外六角或内六角 8.8 / 8 Nm 45 45 50 75 75 80 115 125 180 190 260 270 290 10.9 / 10 Nm 65 65 70 105 110 115 170 185 260 280 370 390 410 12.9 / 12 Nm 75 75 85 125 130 135 200 215 310 330 430 450 480
车架铆接通用技术要求

精品资料车架铆接通用技术要求发布精品资料前言车架铆接通用技术要求1 范围本标准规定了我公司客车车架总成及其零部件的铆接技术要求。
本标准适用于公司产品设计、工艺设计、操作与质量检验。
2 引用标准QJ/DD04.3.01-2010 切削加工件通用技术条件3 一般要求3.1 铆钉对应的铆钉孔直径及偏差按表1执行。
表1 单位为毫米3.2 铆钉孔间距偏差按QJ/DD04.3.01-2010执行。
3.3 铆钉、铆接零件表面应清洁,不得有锈层、油垢,铆钉孔不得有毛刺。
3.4 铆接零件装配应相互紧贴,可采用螺栓、定位销或夹子紧固被铆接零件,不允许采用焊接(点焊)的方法紧固。
3.5 铆接操作时,上、下铆头和铆钉应同心,以保证铆钉成形准确。
3.6 车架及其零部件采用冷铆铆接。
当技术文件有明确要求时,可采用热铆铆接。
3.7 热铆铆钉加热温度为800℃~900℃,并在500℃以上完成铆接过程。
3.8 热铆铆钉在装入铆钉孔前,必须清除氧化皮,对烧损、烧细、烧坏的铆钉不允许使用。
3.9 根据设备要求,合理选择铆接压力,保证铆钉成形质量。
3.10 铆接后,不符合要求的铆钉应铲去重铆;铲去铆钉时,不应损坏母体金属及相邻铆钉,其铲入深度不得超过0.5 mm。
3.11 铆接质量技术要求3.11.1 铆接后被铆零件应在铆钉四周3倍铆钉杆直径范围内紧密贴合,其间隙不得超过0.05 mm。
3.11.2 成形铆钉头按附录A《铆接缺陷产生原因分析及缺陷检查表》及铆钉预制头要求执行。
3.11.3 其余铆接质量技术要求按附录A《铆接缺陷产生原因分析及缺陷检查表》执行。
附录A 铆接缺陷产生原因分析及缺陷检查表单位为毫米铆接缺陷简图允许偏差缺陷原因检查方法铆钉头与母材贴合不紧密不允许1、铆钉头与铆钉杆连接处有凸起地方2、铆接时,顶具未顶紧1、外部检查2、用锤敲击3、用0.05 mm塞尺检查铆钉头歪斜不允许1、铆接时粗心大意2、顶具放置偏斜1、外部检查2、用0.05 mm 塞尺检查铆钉头有裂纹不允许1、铆钉材质低劣2、铆钉加热过度外部检查铆钉杆在铆钉孔内弯曲不允许铆钉孔大且铆钉杆长敲击钉头铆钉在铆合件内断开不允许1、零件间有间隙2、装配不正确3、压的不紧敲击铆缝用手锤敲打时,铆钉头振荡或活头不允许1、铆接件压的不紧2、铆钉杆在孔内不严密用手锤敲打两面铆钉头铆钉头有凹痕b≤2但在重要地方不允许顶具松动或疏忽而形成外部检查铆钉头周围有帽缘b≤1.51、铆钉杆长2、铆钉模小外部检查铆钉头中心与铆钉杆中心偏移b≤1.51、铆接时粗心大意2、顶具放置偏斜外部检查铆钉头边缘缺肉b+d≤2c≤1.51、铆钉杆短2、铆钉模大外部检查和用样板检查铆钉头过小b≤0.1d1、铆钉杆短2、铆钉模小外部检查和用样板检查铆钉头周围有硬伤(母材上)h≤11、铆钉模大2、铆钉模安放不正外部检查埋头铆钉的钉头突出h≤0.5时允准许用砂轮磨去1、铆钉杆长2、埋头锥边小外部检查埋头铆钉的钉头凹进h≤0.5铆钉杆长度不够埋头锥边大外部检查_________________________________。
汽车车架的铆接和焊修技术
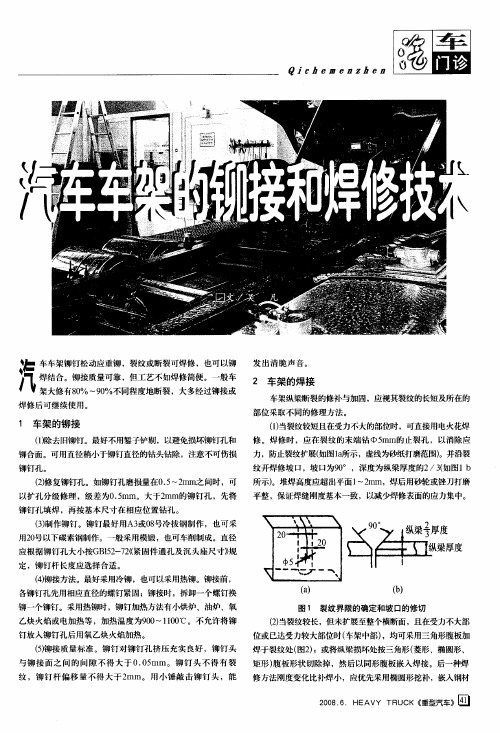
大多经过铆接或
车架纵梁断裂的修补与加固,应视其裂纹的长短及所在的 部位采取不同的修理方法。 () 1当裂纹较短且在受力不大的部位时,可直接用电火花焊
修 。焊修时 ,应在裂纹的末端钻 ①5 mm的止裂孔 ,以消除应
1 车架 的铆 接
() 1 除去旧铆钉。最好不用錾子铲剔,以避免损坏铆钉孔和 铆合面。可 用直径稍小于铆钉直径的钻头钻除 ,注意不可伤损
修方法刚度变化比补焊小 ,应优先采用椭圆形挖补,嵌入钢材
1 71 " 1 7
(铆接质量标 准。铆钉对铆钉 孔挤压充实 良好 ,铆钉头 5 )
与铆接 面 之 间的 间隙 不得 大于 0. 5 m。铆 钉头 不 得 有裂 0r a
纹 ,铆钉 杆偏 移量 不得 大于 2 m。用 小锤敲 击铆 钉头 ,能 a r
() 1 若在受力大的部位焊加强腹板,要注意焊接应力对纵梁 的影响,可采用 图5 的方法。加强板比纵梁边缘宽 出25( .t 为车 t 架纵梁厚度) ,并把焊缝焊成 凹形。
() 2车架上焊缝长度大时 ,应采用断续分段焊法(n 所 I 图6
示) 。每段焊缝长度和间距请参阅下表 。
图2 三角形加强腹板 的厚度 、材质应与纵梁材质相 同。
() 6寒冷季节,应将焊接部位预热至2 ~5  ̄ 0 0 C,以防炸裂; 图 3 角钢切角 图 4 弯角圆弧半径 焊后缓慢冷却,清除焊渣 ,用砂轮、锉刀等工具修整焊缝 。
黼 ■ 鬻 ■ 一 黧 ■ 麓 一 麓 ● 麓 一 麓 ■ 臻 ■ 鞠 ■ ■ 一 ■ 瓣 一 鬃 一 辫 一 鞭 一 一 ■ ■ 一 一 一 一 ■ 一 ■ 一 曩 一 一 ■
为了减小应力集中,加强板的端部应做成逐渐减小的斜角 形( ) 图3。加强板的形状如 图4 所示 ,其弯角圆弧半径应不大于
车架铆接通用技术要求

QJ/DD 03.3.05-2001 车架铆接通用技术要求发布QJ/DD 03.3.05-2001 前言1 范围本标准规定了我公司客车车架总成及其零部件的铆接技术要求。
本标准适用于公司产品设计、工艺设计、操作与质量检验。
2 引用标准QJ/DD04.3.01-2010 切削加工件 通用技术条件 3 一般要求3.1 铆钉对应的铆钉孔直径及偏差按表1执行。
表1 单位为毫米3.2 铆钉孔间距偏差按QJ/DD04.3.01-2010执行。
3.3 铆钉、铆接零件表面应清洁,不得有锈层、油垢,铆钉孔不得有毛刺。
3.4 铆接零件装配应相互紧贴,可采用螺栓、定位销或夹子紧固被铆接零件,不允许采用焊接(点焊)的方法紧固。
3.5 铆接操作时,上、下铆头和铆钉应同心,以保证铆钉成形准确。
3.6 车架及其零部件采用冷铆铆接。
当技术文件有明确要求时,可采用热铆铆接。
3.7 热铆铆钉加热温度为800℃~900℃,并在500℃以上完成铆接过程。
3.8 热铆铆钉在装入铆钉孔前,必须清除氧化皮,对烧损、烧细、烧坏的铆钉不允许使用。
3.9 根据设备要求,合理选择铆接压力,保证铆钉成形质量。
3.10 铆接后,不符合要求的铆钉应铲去重铆;铲去铆钉时,不应损坏母体金属及相邻铆钉,其铲入深度不得超过0.5 mm 。
3.11 铆接质量技术要求3.11.1 铆接后被铆零件应在铆钉四周3倍铆钉杆直径范围内紧密贴合,其间隙不得超过0.05 mm 。
3.11.2 成形铆钉头按附录A 《铆接缺陷产生原因分析及缺陷检查表》及铆钉预制头要求执行。
3.11.3 其余铆接质量技术要求按附录A 《铆接缺陷产生原因分析及缺陷检查表》执行。
附录A 铆接缺陷产生原因分析及缺陷检查表 单位为毫米 车架铆接通用技术要求_________________________________。
铆接工艺守则

SQB42018——2009
我公司车架常用铆钉为精制半圆头铆钉,其编号方法遵循 GB/T 867—1986
中的编号规则。例如:直径 12mm、长 50mm,钢制、氧化的半圆头铆钉编号(图
号)为 Q4501250。我公司车架常用铆钉规格:直径分别为 12、14、16、18mm,
长在 30~55mm 之间。例如:直径 12mm、长 50mm,钢制、氧化的半圆头铆钉
标牌铆 钉
GB/T827—1986① 1.6~5 3~20 用于铆标牌
抽芯铆 钉
GB/T12615~ 12618—1990
3~6
铆接容易,用于汽车车 6~40 身覆盖体、支架等部
位,单面铆接
击芯铆 钉
GB/T1585—1995
① 为商品紧固件产品,应优先选用。
2~5
3~20
用于各种车辆,船舶、 航空、机械制造、电讯 器材和钢木家具等的 单面铆接
将型钢或压型制件与板件用 铆钉连接在一起
3
SQB42018——2009
3.3.3 按照铆钉所受剪切力的情况可分为单剪切、双剪切和多剪切三种连接 形式。 3.3.4 按照每一主板上铆钉的行列可分为单排、双排、三排等连接形式。 3.3.5 按照连接板上铆钉的排列形式可分为平行排列和交错排列两种连接 形式。 3.4 铆钉
7
SQB42018——2009
3.4.3.1 钢结构连接铆钉 常见的钢结构连接铆钉形式有半圆头铆钉、平锥头铆钉、沉头铆钉、半
沉头铆钉、平头铆钉、扁圆头铆钉和扁平头铆钉等(见表 2)。
在各种铆接缝中,半圆头铆钉应用最广泛。特别是强固结合用半圆头铆
钉和密固结合用半圆头铆钉两种铆钉应用更为广泛。常用粗制半圆头铆钉的
车架通用技术条件
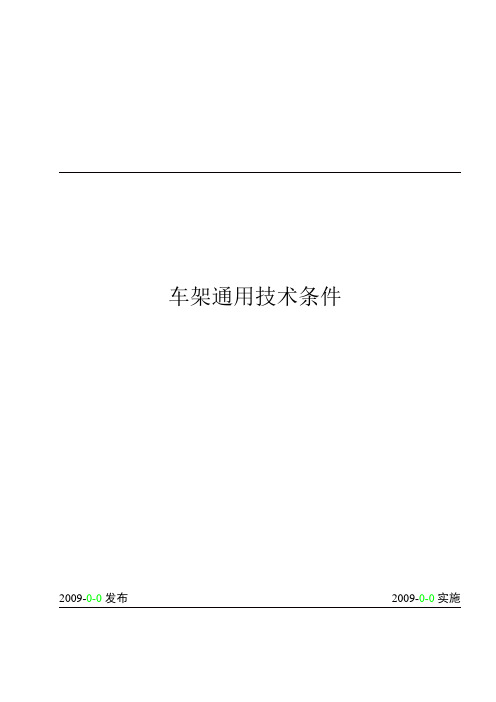
车架通用技术条件前言车架通用技术条件1前言本技术条件是公司车架通用的基本要求,适用于公司车架设计及检验。
2引用标准QJ/DD04.3.23-87 铆接工艺通用技术条件QJ/DD04.3.50-2010 焊接件通用技术条件QJ/DD04.16-2009 客车油漆涂层QJ/DD09.8.10-2009 装配通用技术条件3技术要求3.1车架铆接要求3.1.1铆接要求按QJ/DD04.3.23-87铆接工艺通用技术条件执行。
3.1.2不同心的铆钉孔,允许采用同径铰刀铰孔后铆接。
3.1.3铆接后,不合要求但又在允许偏差范围内的铆钉数,不超过总数的10%,单件上不超过1个。
3.1.4纵梁铆接完成后,对纵梁上下翼面及腹面出现的孔不同心现象,按原孔尺寸引钻。
3.2车架定位焊要求3.2.1槽型梁腹面前后面、上下翼面各焊一段,异型管梁前后腹面各焊一~二段,其余小件每件焊至少两段,每段焊缝长约10 mm,焊角高低于板厚,该焊缝在后续焊接中应被覆盖上。
3.3车架焊接要求3.3.1焊接标准按QJ/DD04.3.50-2010焊接件通用技术条件执行。
3.3.2焊接采用CO2气体保护焊,焊角高度与所焊零件板厚相同。
3.3.3焊接顺序:先焊纵梁联接处→横梁→立柱→其余各支撑梁、小件;焊接中要求由内向外,由中间向前后逐步、对称、交错进行。
3.3.4纵梁搭接、联接处及关键联接件在焊夹具上完成焊接。
3.3.5联接板的塞焊孔≤30mm时,塞焊孔焊平;塞焊孔>30mm时,塞焊孔焊一周;板周边在两孔间断续焊,焊缝长同孔径,焊角高均同板厚。
3.3.6焊接过程中,车架应处于平整状态。
3.4车架检查、修正要求3.4.1车架平面度技术要求3.4.1.1专用焊夹具上生产的老车型车架,平面度≤8mm。
3.4.1.2其余车架平面度≤6mm,每2米≤2mm;带落差车架平面度要求相同,公差按各落差面积分布。
3.4.1.3带行李仓车架在X方向直线度:纵梁≤6mm,每2米≤2mm;支撑梁端头处≤3mm。
车架铆接通用工艺守则(A4)

校对(日期)
审核(日期)
标准化(日期)
会签(日期)
批准(日期)
标记
处数
更改文件号
签字(日期)
长沙仙达实业有限公司
车架铆接通用工艺守则
第4页
共6页
7.5每班每铆第一个铆钉前,应点动操作铆钳,观察动、静铆模是否对中,若不对中,先查明原因,调整或更换铆模使其对中后,再进行铆接。
7.6铆钉头部与尾部应同动、静铆模的端部铆坑对中,若铆钉歪斜,调整后再铆。
6.1铆钉材料为10号或15号优质碳素钢(亦可用ML10、ML15),冷墩加工成型,退火处理,表面氧化(发兰),化学成分、机械性能符合GB6478-86。
6.2严格按照图纸规定选用铆钉规格,铆钉长度理论计算公式:L=1.12∑δ+1.4d其中L为铆钉长度,∑δ为被铆零件厚度之和,d为铆钉直径。
6.3铆钉表面不允许有影响使用的裂缝。
8.2.4铆钉头成形直径不小于1.5倍的钉杆的直径。
8.2.5被铆接零部件结合面要贴合紧密,在小于铆钉直径3倍区域内最大间隙不大于0.2mm。
编制(日期)
校对(日期)
审核(日期)
标准化(日期)
会签(日期)
批准(日期)
标记
处数
更改文件号
签字(日期)
长沙仙达实业有限公司
车架铆接通用工艺守则
第5页
共6页
8.2.6铆钉头与被铆接零部件要贴合紧密,沿铆钉头周围至少有120°范围间隙不大于0.05mm,其余部位间隙不大于0.2mm。
4.6.4铆钉成型后,动铆模不回或回程太短;
4.6.5动铆模下行无力;
4.6.6噪音大,活塞爬行。
4.7设备要定期保养,且有维保记录。
铆工、装配规程

铆工、装配规程铆工(装配)制作规程本工艺(检验)规程使用于公司各类梁柱类、小车架类钢结构铆接工序,包括:起重机主梁、端梁、支腿、横梁、台车架、小车架、走台等起重机钢结构部件及大、小车装配。
一、铆接前的准备工作1.认真阅读图纸,认真分析产品图纸明示和隐含的技术要求,不清楚之处须问清楚;2.依据产品图纸最大轮廓尺寸,确定场地大小,并清理场地内所有与生产无关的物料,使现场地面干净、摆放有序;3.在分析产品图纸和技术要求的前提下,确定需要的平台、工装、辅具、吊具等,并准备到位;注意:吊具要安全可靠,辅具要做到既轻便,又坚固不易变形,平台使用水平仪调整至水平、等高状态;4.按照接到的任务单,收集所需的零件,并检查是否符合要求(外观、平面度、切割面状况、直线度、关键尺寸、折弯角度等),不符合要求的零件及时告知质检员处理;二、部件的拼接工艺1.拼接筋板前,把所需零件集中在平台周围合适的范围内,摆放整齐有序,做到方便取用,又不碍事;2.拼接方框类筋板时应事先在平台上放样,宽度方向按理论尺寸±1,高度方向按理论尺寸-5㎜,在平台上照线点焊定位块,第一件组完后测量对角线之差应小于㎜,确保所有筋板的一致性,避免最后铆下盖板时腹板出现波浪;4.筋板焊接使用J422焊条或混合气体保护焊,焊后要求矫平面度;也可以在焊接时采取措施控制变形量;5.其它类型部件的拼接也须按以上方式执行和保证;三、埋弧焊焊接过程制造工艺及检验程序1.接板前先检查板材直线度,单张板材≤2mm时方可对接;1 3.筋板点固焊只允许点焊所有接缝的两端,焊点长度10㎜左右; 2.拼接错变量超过1㎜,必须返修后方能焊接;3.板材厚度10mm—14mm开V型单面坡口,16mm以上开双面坡口;4.引弧板、熄弧板应与被焊板材的材质、厚度一致;5.要求清理焊接区周边20㎜范围见金属光泽,使用角磨机清理坡口两侧和两端各20㎜范围;6.焊接前对以上5项先自检后找检验员确认,再进行下一项;7.焊接过程中,应保证焊剂纯净,干燥;8.埋弧焊焊缝尺寸:焊高1+δ、宽度2δ±2,δ为板厚; 9.不得出现裂纹、夹渣、气孔、未溶合、未焊透、焊偏等焊接缺陷; 10.焊接完成,清除所有缺陷后自检,自检合格找检验员校检确认;四、主梁、端梁、支腿、横梁、台车架、小车架、走台总成的制造工艺及检验程序1.组立时应先确认盖板和腹板的尺寸,盖板要求拉线检测板边的直线度应小于3㎜、U型梁不超过2mm且禁止出现S弯,腹板要求检测拱度误差小于2㎜,自检合格后,找检验员确认方可点焊筋板;2.找好筋板位置的放线基准,按图示尺寸进行放线,每个间距标明尺寸,便于核查;3.照线安放筋板,仔细调整左右对称度和垂直度,然后点固筋板两侧;4.点固焊要事先设定好位置,不能随意点焊,筋板两端要留出30㎜不能点焊,以免影响腹板的定位;特别是焊接为段焊的部件,大致等距点焊,焊点的焊脚尺寸为3㎜,长度应在10mm~25mm左右,间隔150~300㎜左右(视筋板的宽度而定);注意:不允许点焊成短粗焊点,避免影响焊缝成型;5.筋板点焊完成,应全面自检,自检合格后,找检验员校检确认;6.首检合格后方可焊接筋板焊缝,焊接尺寸按照工艺要求或图纸要求。
铁路货车修理铆接(热铆)技术要求
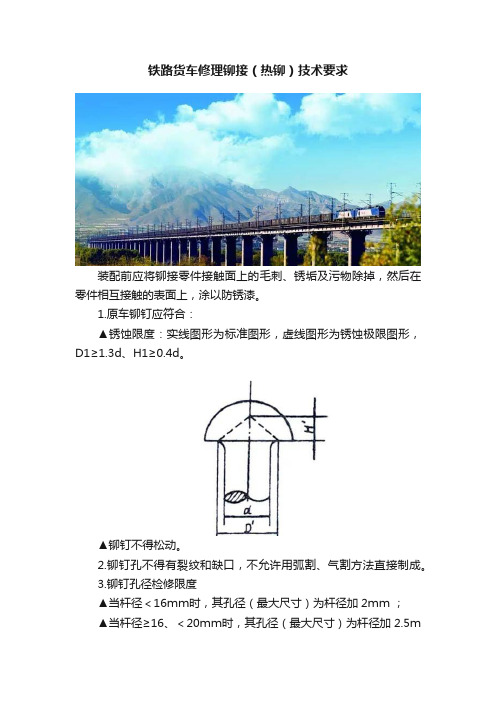
铁路货车修理铆接(热铆)技术要求装配前应将铆接零件接触面上的毛刺、锈垢及污物除掉,然后在零件相互接触的表面上,涂以防锈漆。
1.原车铆钉应符合:▲锈蚀限度:实线图形为标准图形,虚线图形为锈蚀极限图形,D1≥1.3d、H1≥0.4d。
▲铆钉不得松动。
2.铆钉孔不得有裂纹和缺口,不允许用弧割、气割方法直接制成。
3.铆钉孔径检修限度▲当杆径<16mm时,其孔径(最大尺寸)为杆径加2mm;▲当杆径≥16、<20mm时,其孔径(最大尺寸)为杆径加2.5mm;▲当杆径≥20mm时,其孔径(最大尺寸)为杆径加3.5mm;▲当孔径超差时,允许焊后铣孔或堵孔重钻(对可焊性钢材)。
4.钢铆钉一般应加热至800~1100℃,铆接过程应在500℃以前完成。
烧坏之铆钉不准使用(铆钉装入铆钉孔时,必须先将铆钉的氧化皮除掉)。
当铆钉直径不大于10mm时,允许冷铆。
采用液压冷铆时,铆钉直径应不大于12mm。
5.铆接件接触不良,允许烤修。
6.铆接件用螺栓紧固时,数量不少于总孔数的25%,应均匀分布。
对可焊性的钢材,允许将铆接件夹紧后用定位焊紧固(心盘不允许用定位焊紧固),定位焊长度不得大于30mm,定位焊部位应便于检修,不便于检修部位的定位焊应铲除。
定位焊不应有咬肉现象,如有咬肉但深度不超过0.5mm时,允许不进行修补。
7.心盘从板座检修重铆时用0.5mm厚的塞尺测量(重铆后的接触面)不得触及钉杆。
8.新制的钢板压型件与新型钢件铆接后,局部缝隙(指翘边)不得超过1mm,但用0.5mm厚的塞尺测量不得触及钉杆。
9.使用0.25~0.4Kg检查小锤检查和塞尺对铆接质量进行检查,在铆钉头周围1/2范围内用0.1mm(不加工铸件用1mm)塞尺检查不得触及铆钉根部;铆接之残缺须按规定的范围进行处理。
铆接工艺规范

铆接工艺规范一、目的为增强公司的质量管理,完善焊接工艺,提高焊接质量,为顾客提供优质的产质量量,最终提高公司产品的质量和顾客满意度,依据工艺规范及相关规范制定本规范。
二、范围本规范适用于本公司一切的焊接进程三、内容3.1备料3.1.1备料需求矩形管外表无锈蚀,两端无毛刺,无铁屑,发现效果及时反应上道工序停止整改,后按«车间外部索赔考核制度»处置;3.1.2备料要求矩形管长度误差-2mm,角度误差-1°,超出范围制止运用;3.1.3备料要求冲压件必需校平尤其是平板类冲压件,长度误差-2mm,超出范围制止运用;3.1.4如有些件需求现场气割时,要求操作工对气割件按要求停止划线处置后再停止气割,气割公差-1mm,气割后将气割处段面打磨平整;3.1.5如有些件带弧度需求用样板对弧度停止验证,样板与弧度的误差-1mm,确定来件合格后在停止后续工序。
3.1.6如有些件弧度是对接的小料拼焊而成的,在备料时必需用弧板保证对接后的整件弧度,整件长度的误差-2mm。
3.1.7如有两件以上的截面对焊时,这些件料厚均≥5 mm,那么这些件的料厚截面须用砂轮机开坡口。
备料:矩形管外表无锈蚀,两端无毛刺,无铁屑,长度公差-2mm,角度公差-2°3.2拼焊3.2.1铆工应依据焊件的大小厚薄思索到焊接变形,预留出收缩尺寸;3.2.2焊工在无特殊焊件的条件下,焊接工艺参数应将电流坚持在140—220A之间,电压坚持在18—24V之间,铆焊时必需在铆焊任务台上停止;3.2.3铆焊时,要求焊件对接缝隙不大于4mm,严禁操作工对焊缝超出范围的单片停止拼焊,如有特殊需求气割时,需经技术确认后,要求操作工对气割件按要求停止划线处置后再停止气割,另需保证气割后打磨平整;3.2.4依据图纸找长、宽、高三个方向的定位基准件,确定基准件后把这些件在铆焊工装平台上铆焊结实;3.2.5片梁、总成中各矩形管搭焊时以矩形管端面四边角搭焊,不允许在其它面上搭焊,焊接后用检具反省片梁、总成能否平整,各平面误差3 mm ,焊点要结实,要保证在转运进程中不发作位移。
车架铆接工艺准则

车架铆接工艺准则1 目的为加强公司的工艺管理,完善车架铆接工艺,保证车架铆接质量,提高产品竞争力,特制定本准则。
2 范围本规范适用于本公司中重型卡车的车架总成及其零部件。
3 铆钉3.1 铆钉材料、化学成分、机械性能应符合Q450-1995;3.2 铆钉表面一般进行氧化处理。
4 铆钉孔4.1 铆钉孔中心到弯曲边的最小距离(见图1)应符合表1规定。
表1 (单位:mm)4.2 测量点铆钉孔孔边距“X”应从图2所示测量点计起。
4.3 角度偏差纵梁上、下翼面对腹板的角度偏差为±1°或±1.5mm (当翼板宽度为90mm时),见图3.4.4 铆钉孔的直径,见表2.表2 (单位:mm)4.5 去毛刺4.5.1 无论产品图样上是否注明去毛刺,实际加工过程中都必须对孔的两端打磨或倒角,以去除毛刺。
去毛刺后,手指肚划过孔端边沿应感觉平滑、无明显凸兀感,孔内必须无残留铁屑或飞边。
4.5.2 零件装配时铆钉孔允许的最大位移量(错位量)为 1.6mm,为消除位移可采用与孔径对应的铰刀绞孔,以保证铆钉能顺利插入。
4.5.3 铆钉孔位移量不大于1.0mm时,允许使用导正销或其它方法来使铆钉顺利插入铆钉孔, 否则应绞孔至铆钉能顺利插入。
4.5.4 绞孔时铰刀的最大倾斜角为5°,铆钉插入前铆钉孔两端应按4.4.1的要求去毛刺。
5 铆接5.1 铆钉墩头成型应为球冠形(或近似球冠形),其直径dk应不小于铆钉杆直径的1.5倍,其高度K应不小于铆钉预制头高度,见图4。
5.2 铆钉、铆接零件表面应清洁,不得有锈层、油垢,铆钉孔不得有毛刺。
5.3 铆接后,铆钉头与钢板间及各铆接零件间的贴合面必须紧密贴合。
5.3.1 铆钉头(包括成型头及预制头)与被铆钢板间必须紧密贴合,其间隙不得大于0.05mm,见图5。
5.3.2 被铆零件间的贴合面在铆钉沿周3d(3倍铆钉杆直径)范围内必须紧密贴合,其间隙不得大于0.05mm ,见图5。
铆接工艺设计规范方案
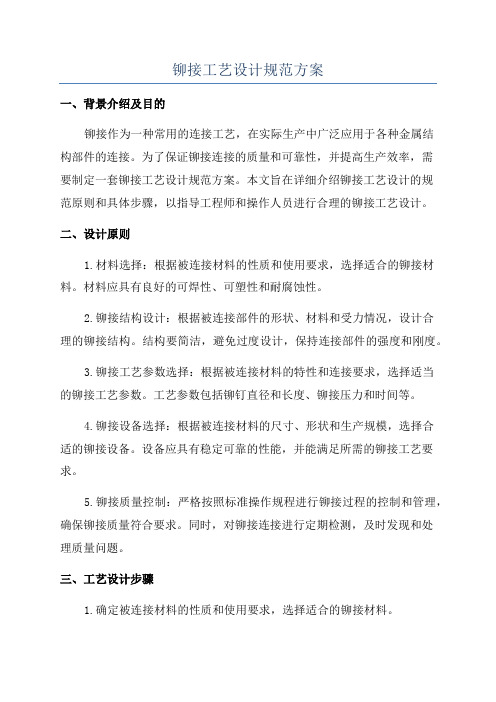
铆接工艺设计规范方案一、背景介绍及目的铆接作为一种常用的连接工艺,在实际生产中广泛应用于各种金属结构部件的连接。
为了保证铆接连接的质量和可靠性,并提高生产效率,需要制定一套铆接工艺设计规范方案。
本文旨在详细介绍铆接工艺设计的规范原则和具体步骤,以指导工程师和操作人员进行合理的铆接工艺设计。
二、设计原则1.材料选择:根据被连接材料的性质和使用要求,选择适合的铆接材料。
材料应具有良好的可焊性、可塑性和耐腐蚀性。
2.铆接结构设计:根据被连接部件的形状、材料和受力情况,设计合理的铆接结构。
结构要简洁,避免过度设计,保持连接部件的强度和刚度。
3.铆接工艺参数选择:根据被连接材料的特性和连接要求,选择适当的铆接工艺参数。
工艺参数包括铆钉直径和长度、铆接压力和时间等。
4.铆接设备选择:根据被连接材料的尺寸、形状和生产规模,选择合适的铆接设备。
设备应具有稳定可靠的性能,并能满足所需的铆接工艺要求。
5.铆接质量控制:严格按照标准操作规程进行铆接过程的控制和管理,确保铆接质量符合要求。
同时,对铆接连接进行定期检测,及时发现和处理质量问题。
三、工艺设计步骤1.确定被连接材料的性质和使用要求,选择适合的铆接材料。
2.根据被连接部件的形状、材料和受力情况,设计合理的铆接结构。
考虑到铆接位,数量和间距等参数。
3.根据被连接材料的特性和连接要求,选择适当的铆接工艺参数。
包括铆钉直径和长度、铆接压力和时间等。
4.根据被连接材料的尺寸、形状和生产规模,选择合适的铆接设备。
确保设备具有稳定可靠的性能,并能满足所需的铆接工艺要求。
5.制定铆接操作规程,明确铆接操作步骤和要求,确保操作人员按照规范进行铆接。
6.进行工艺试验,验证铆接质量和可靠性。
对不合格的铆接进行分析和处理,进行必要的改进措施。
7.对铆接连接进行定期检测,检查连接的强度和可靠性。
发现问题及时处理,确保铆接质量符合要求。
8.对铆接工艺进行持续改进,根据实际生产情况和质量反馈,优化工艺参数和设备选择,提高铆接质量和效率。
车架总成工艺技术标准

28LSA74
第3页
下料尺寸
幅面板厚
板料宽度
主要设备及工装夹具
7×6610×382(外)
5×6610×362(内)
250/7+5
翼面80mm
1200(外)
1150(内)
ቤተ መጻሕፍቲ ባይዱ型号
名称
规格
数量
工艺技术作业指导—装夹成型
1、内、外片梁夹层刷防锈油漆;2、内、外片梁用∅13定位销定位,工装夹具见图A;
3、焊装工艺孔,工艺孔焊点不能高于大梁平面,在0~-1mm范围内;
3、斜尾封板焊缝均匀,封板焊接后不能高于大梁上翼面。
图A
图B
设计
校对
审核
批准
标记
处数
文件号
签字
日期
标记
处数
文件号
签字
日期
****汽车部件有限公司
28LSA74车架总成工艺技术标准
产品名称或产品型号
共5页
28LSA74
第3页
下料尺寸
幅面板厚
板料宽度
主要设备及工装夹具
7×6610×382(外)
5×6610×362(内)
幅面板厚
板料宽度
主要设备及工装夹具
7×6610×382(外)
5×6610×362(内)
250/7+5
翼面80mm
1200(外)
1150(内)
型号
名称
规格
数量
工艺技术作业指导—打磨
1、纵梁外表面“禁磨”:在纵梁外表面禁止使用磨光机打磨,对毛刺的位置只能用铲刀铲掉(铲刀口必须锋利);
2、外表面大孔飞边毛刺无法铲除的,用磨光机(带百叶片)打磨,磨痕距孔边缘不能超过5mm,切不得有较深磨痕;
车架总成通用工艺准则
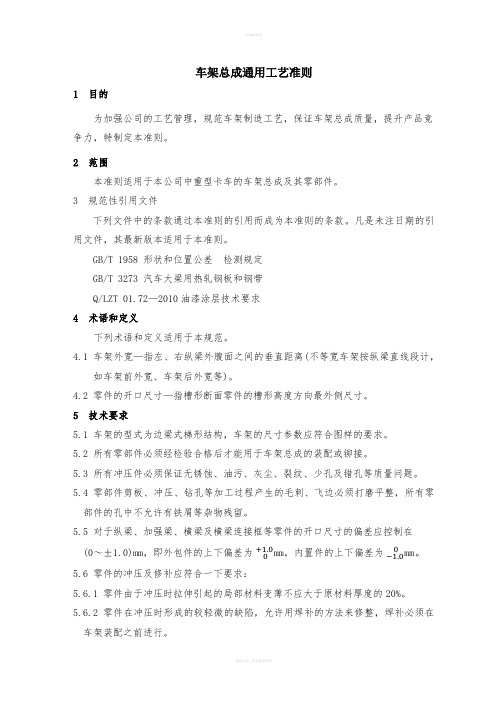
车架总成通用工艺准则1 目的为加强公司的工艺管理,规范车架制造工艺,保证车架总成质量,提升产品竞争力,特制定本准则。
2 范围本准则适用于本公司中重型卡车的车架总成及其零部件。
3 规范性引用文件下列文件中的条款通过本准则的引用而成为本准则的条款。
凡是未注日期的引用文件,其最新版本适用于本准则。
GB/T 1958 形状和位置公差 检测规定GB/T 3273 汽车大梁用热轧钢板和钢带Q/LZT 01.72—2010油漆涂层技术要求4 术语和定义下列术语和定义适用于本规范。
4.1 车架外宽—指左、右纵梁外腹面之间的垂直距离(不等宽车架按纵梁直线段计,如车架前外宽、车架后外宽等)。
4.2 零件的开口尺寸—指槽形断面零件的槽形高度方向最外侧尺寸。
5 技术要求5.1 车架的型式为边梁式梯形结构,车架的尺寸参数应符合图样的要求。
5.2 所有零部件必须经检验合格后才能用于车架总成的装配或铆接。
5.3 所有冲压件必须保证无锈蚀、油污、灰尘、裂纹、少孔及错孔等质量问题。
5.4 零部件剪板、冲压、钻孔等加工过程产生的毛刺、飞边必须打磨平整,所有零部件的孔中不允许有铁屑等杂物残留。
5.5 对于纵梁、加强梁、横梁及横梁连接框等零件的开口尺寸的偏差应控制在(0~±1.0)mm ,即外包件的上下偏差为 0+1.0mm ,内置件的上下偏差为 −1.0 0mm 。
5.6 零件的冲压及修补应符合一下要求:5.6.1 零件由于冲压时拉伸引起的局部材料变薄不应大于原材料厚度的20%。
5.6.2 零件在冲压时形成的较轻微的缺陷,允许用焊补的方法来修整,焊补必须在车架装配之前进行。
5.7 车架总成的铆接应符合《中重型卡车车架铆接工艺准则》的要求。
5.8 装配好的车架总成应符合下表中的各项要求:5.9 车架总成及其零部件的油漆应符合《车架涂装工艺准则》的要求。
5.10 螺栓连接的零件其螺栓拧紧力矩应符合附表1的要求。
6 运输、贮存6.1 涂装后的车架在转挂、吊装、运输过程中应避免磕碰、划伤。
车架铆接工艺流程
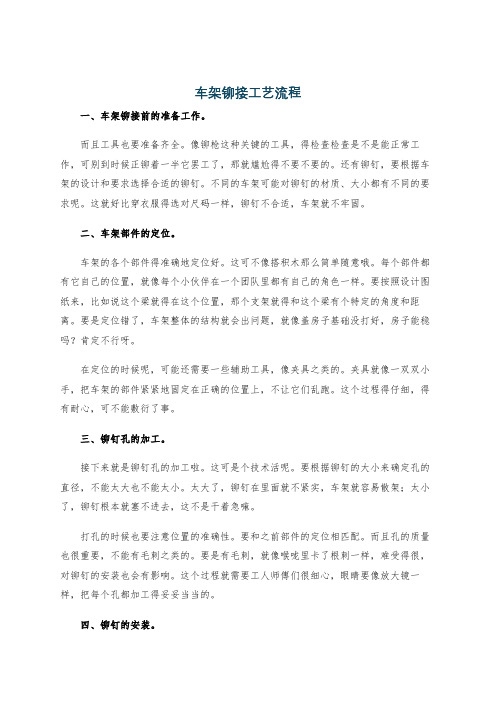
车架铆接工艺流程一、车架铆接前的准备工作。
而且工具也要准备齐全。
像铆枪这种关键的工具,得检查检查是不是能正常工作,可别到时候正铆着一半它罢工了,那就尴尬得不要不要的。
还有铆钉,要根据车架的设计和要求选择合适的铆钉。
不同的车架可能对铆钉的材质、大小都有不同的要求呢。
这就好比穿衣服得选对尺码一样,铆钉不合适,车架就不牢固。
二、车架部件的定位。
车架的各个部件得准确地定位好。
这可不像搭积木那么简单随意哦。
每个部件都有它自己的位置,就像每个小伙伴在一个团队里都有自己的角色一样。
要按照设计图纸来,比如说这个梁就得在这个位置,那个支架就得和这个梁有个特定的角度和距离。
要是定位错了,车架整体的结构就会出问题,就像盖房子基础没打好,房子能稳吗?肯定不行呀。
在定位的时候呢,可能还需要一些辅助工具,像夹具之类的。
夹具就像一双双小手,把车架的部件紧紧地固定在正确的位置上,不让它们乱跑。
这个过程得仔细,得有耐心,可不能敷衍了事。
三、铆钉孔的加工。
接下来就是铆钉孔的加工啦。
这可是个技术活呢。
要根据铆钉的大小来确定孔的直径,不能太大也不能太小。
太大了,铆钉在里面就不紧实,车架就容易散架;太小了,铆钉根本就塞不进去,这不是干着急嘛。
打孔的时候也要注意位置的准确性。
要和之前部件的定位相匹配。
而且孔的质量也很重要,不能有毛刺之类的。
要是有毛刺,就像喉咙里卡了根刺一样,难受得很,对铆钉的安装也会有影响。
这个过程就需要工人师傅们很细心,眼睛要像放大镜一样,把每个孔都加工得妥妥当当的。
四、铆钉的安装。
好啦,到了铆钉安装这个关键步骤啦。
把铆钉塞进之前加工好的孔里,就像把钥匙插进锁孔一样。
不过这可比插钥匙难多啦。
然后就用铆枪开始工作啦。
铆枪发出“哒哒哒”的声音,就像在唱歌一样,但是这个歌声可是很有力量的。
铆枪把铆钉的一端给挤压变形,让它紧紧地咬住车架的部件。
这个过程要控制好力度,力度小了,铆钉咬不紧;力度大了,可能会把车架部件给弄变形或者把铆钉弄断。
铆接工艺技术要求

铆接工艺技术要求铆接工艺技术要求铆接是一种通过利用铆钉的伸缩性,将两个或多个工件连接在一起的方法。
铆接工艺技术要求对于铆接质量和工作效率至关重要。
下面是一些铆接工艺技术要求。
1. 合适的铆接材料:选择合适的铆接材料对于铆接工艺的成功非常重要。
通常情况下,铆接使用的材料应与要连接的工件材料相似或具有相似的力学性能。
这样可以避免因材料不匹配而导致的连接失效。
2. 适当的铆接设备:铆接设备的选择和使用对于铆接工艺的成功至关重要。
合适的铆接设备能够提供足够的力量和压力来确保连接的牢固性。
此外,设备还应具备调节功能,以便根据不同的工件材料和尺寸进行调整。
3. 正确的铆接方法:不同的铆接方法适用于不同的工件连接。
常用的铆接方法包括挤压铆接、钻孔铆接和铆接针。
选择适当的铆接方法对于保证连接的强度和可靠性非常重要。
4. 合适的铆接标准:铆接工艺需要符合相应的铆接标准和规范。
这些标准和规范确保了铆接工艺的质量和一致性,以及连接的可靠性。
同时,铆接工艺需要进行适当的质量检验和测试,以确保连接的质量。
5. 适当的培训和技能:铆接工艺需要经过适当的培训和技能才能掌握。
铆接工人需要具备相关的铆接知识和技能,以确保正确地执行铆接工艺。
高质量的铆接技术需要经过长期实践和经验的积累。
总之,铆接工艺技术要求对于铆接工艺的成功非常重要。
选择合适的材料和设备,采用适当的铆接方法,遵守相关的铆接标准和规范,以及具备相关的培训和技能,这些都是铆接工艺技术要求需要重视的方面。
只有通过正确的铆接工艺技术要求,才能实现高质量的铆接连接。
- 1、下载文档前请自行甄别文档内容的完整性,平台不提供额外的编辑、内容补充、找答案等附加服务。
- 2、"仅部分预览"的文档,不可在线预览部分如存在完整性等问题,可反馈申请退款(可完整预览的文档不适用该条件!)。
- 3、如文档侵犯您的权益,请联系客服反馈,我们会尽快为您处理(人工客服工作时间:9:00-18:30)。
车架铆接工艺准则
1 目的
为加强公司的工艺管理,完善车架铆接工艺,保证车架铆接质量,提高产品竞争力,特制定本准则。
2 范围
本规范适用于本公司中重型卡车的车架总成及其零部件。
3 铆钉
3.1 铆钉材料、化学成分、机械性能应符合Q450-1995;
3.2 铆钉表面一般进行氧化处理。
4 铆钉孔
4.1 铆钉孔中心到弯曲边的最小距离(见图1)应符合表1规定。
表1 (单位:mm)
4.2 测量点
铆钉孔孔边距“X”应从图2所示测量点计起。
4.3 角度偏差
纵梁上、下翼面对腹板的角度偏差为±1°或±1.5mm (当翼板宽度为90mm时),见图3.
4.4 铆钉孔的直径,见表2.
表2 (单位:mm)
4.5 去毛刺
4.5.1 无论产品图样上是否注明去毛刺,实际加工过程中都必须对孔的两端打磨或倒角,以去除毛刺。
去毛刺后,手指肚划过孔端边沿应感觉平滑、无明显凸兀感,孔内必须无残留铁屑或飞边。
4.5.2 零件装配时铆钉孔允许的最大位移量(错位量)为 1.6mm,为消除位移可采用与孔径对应的铰刀绞孔,以保证铆钉能顺利插入。
4.5.3 铆钉孔位移量不大于1.0mm时,允许使用导正销或其它方法来使铆钉顺利插入铆钉孔, 否则应绞孔至铆钉能顺利插入。
4.5.4 绞孔时铰刀的最大倾斜角为5°,铆钉插入前铆钉孔两端应按4.4.1的要求去毛刺。
5 铆接
5.1 铆钉墩头成型应为球冠形(或近似球冠形),其直径dk应不小于铆钉杆直径的
1.5倍,其高度K应不小于铆钉预制头高度,见图4。
5.2 铆钉、铆接零件表面应清洁,不得有锈层、油垢,铆钉孔不得有毛刺。
5.3 铆接后,铆钉头与钢板间及各铆接零件间的贴合面必须紧密贴合。
5.3.1 铆钉头(包括成型头及预制头)与被铆钢板间必须紧密贴合,其间隙不得大于0.05mm,见图5。
5.3.2 被铆零件间的贴合面在铆钉沿周3d(3倍铆钉杆直径)范围内必须紧密贴合,其间隙不得大于0.05mm ,见图5。
5.3.3 铆钉孔到弯边距离小于3d时,圆角部分不做上述要求。
5.4 铆接操作时,上、下铆头和铆钉应同心,以保证铆钉成形准确。
5.5 车架及其零部件采用冷铆铆接。
当技术文件有明确要求时,可采用热铆铆接。
5.6 热铆铆钉加热温度为800℃~900℃,并在500℃以上完成铆接过程。
5.7 热铆铆钉在装入铆钉孔前,必须清除氧化皮,对烧损、烧细、烧坏的铆钉不允许使用。
5.8 铆接后,不符合要求的铆钉应铲去重铆;铲去铆钉时,不应损坏母体金属及相邻铆钉,其铲入深度不得超过0.5 mm。
6 铆接压力
铆接压力见表3。
表3 铆接压力
7 其余铆接技术要求按附录A《铆接缺陷产生原因分析及缺陷检查表》执行。
附录A 铆接缺陷产生原因分析及缺陷检查表
铆钉头与母
材贴合不紧不允许
铆钉头歪斜不允许
铆钉头有裂
不允许
铆钉杆在铆
不允许
钉孔内弯曲
铆钉在铆合
不允许用手锤敲打
铆钉头有凹b
重
不允许
铆钉头周围
b
铆钉头中心
与铆钉杆中b
铆钉头边缘残缺或外形b+d c
铆钉头过小b
铆钉头周围
有硬伤(母h
埋头铆钉的h
允
轮磨去
埋头铆钉的
h。